Mechanical Realignment of Modular Coils to Mitigate Field
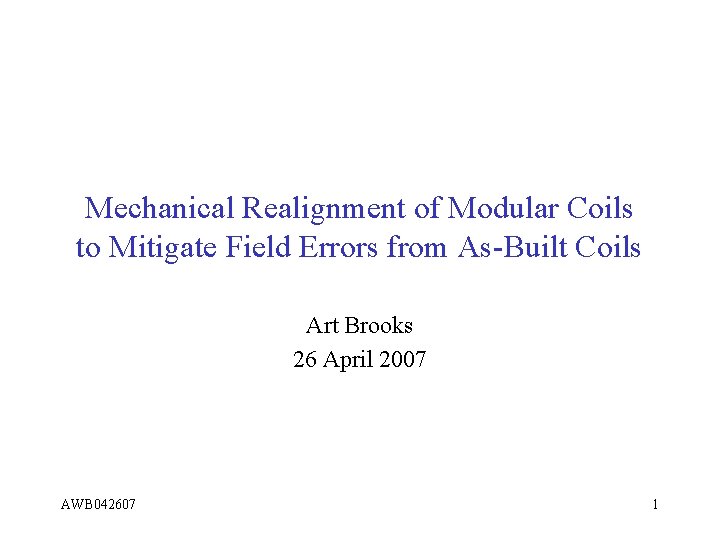
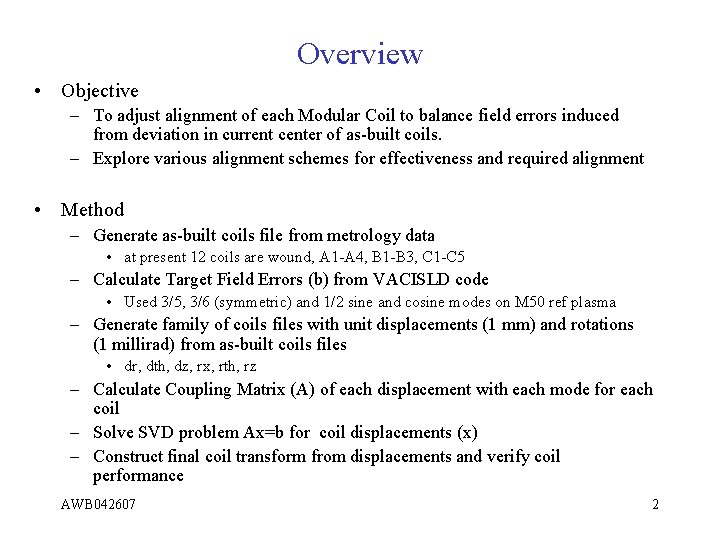
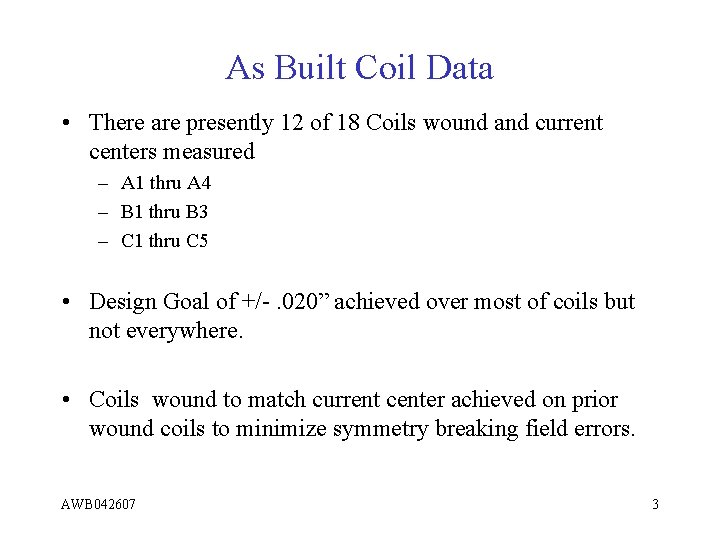
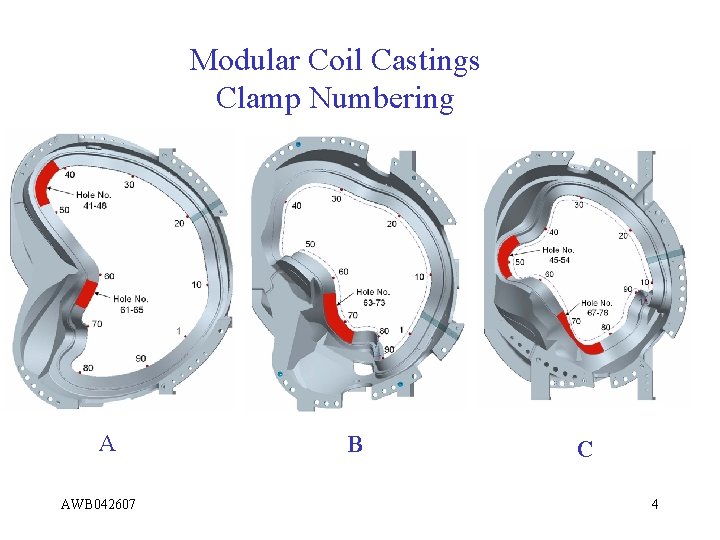
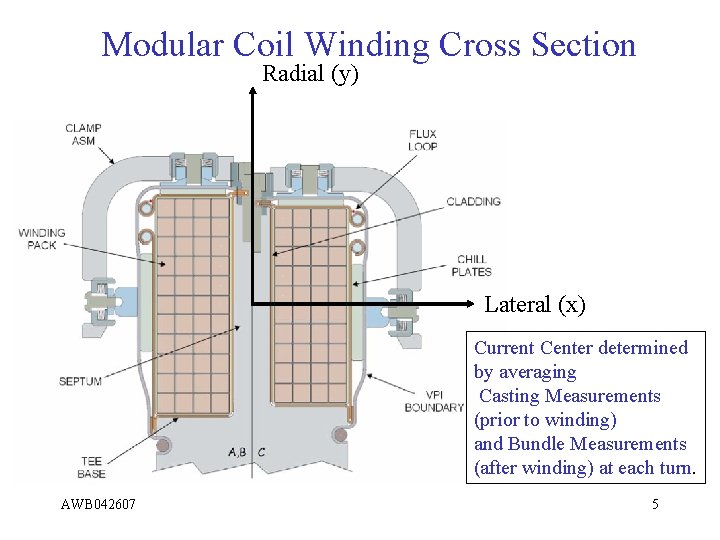
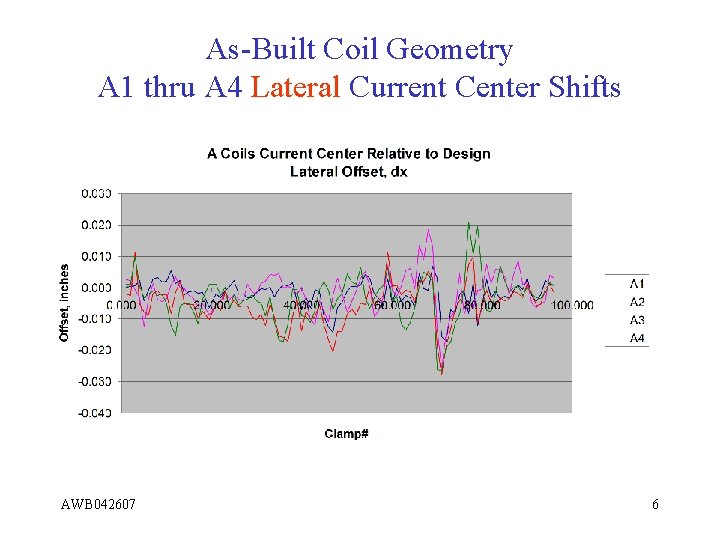
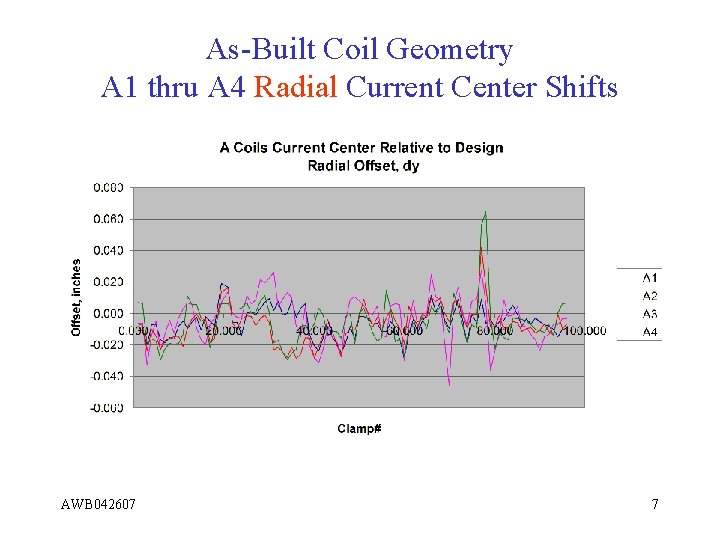
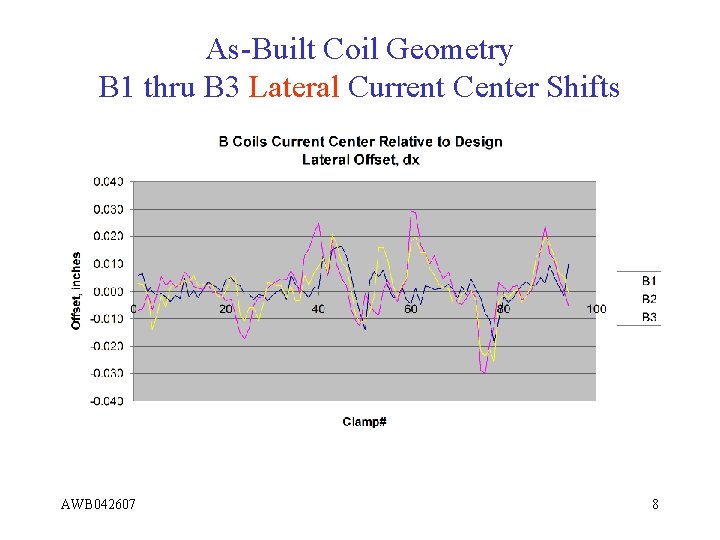
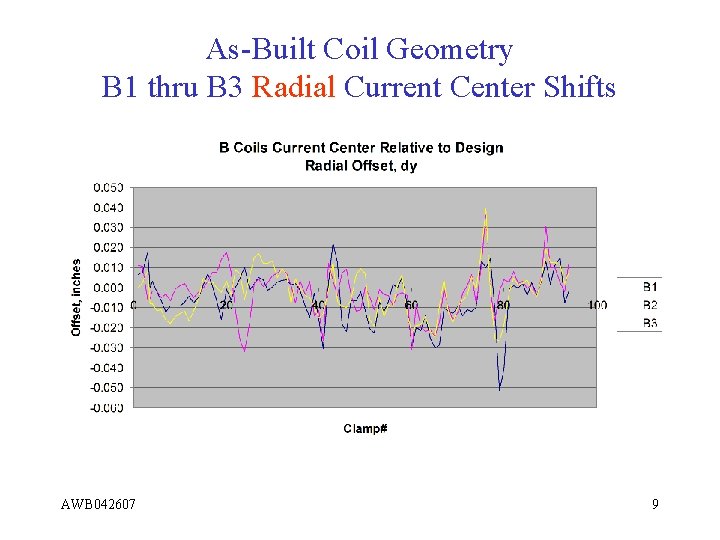
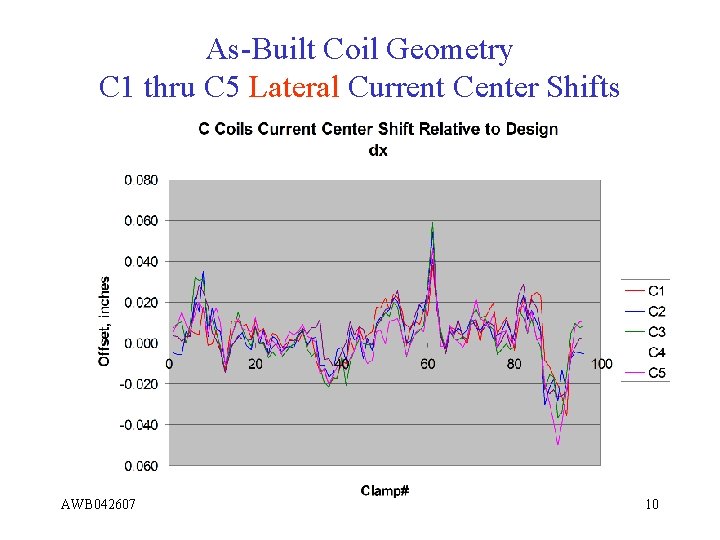
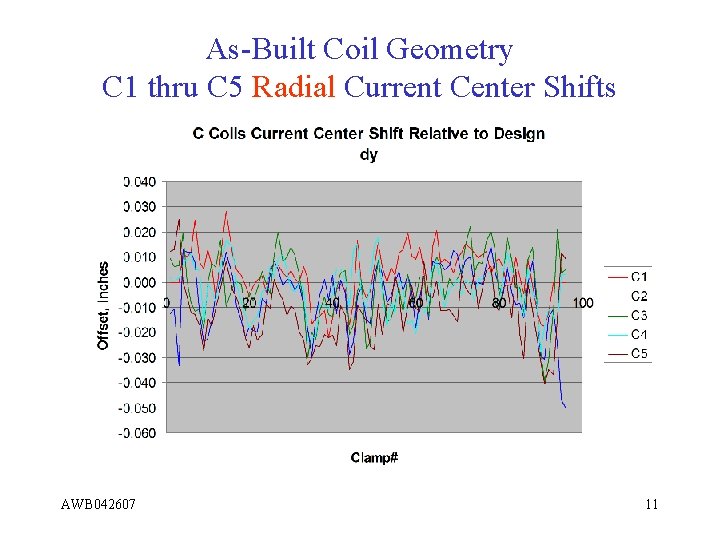
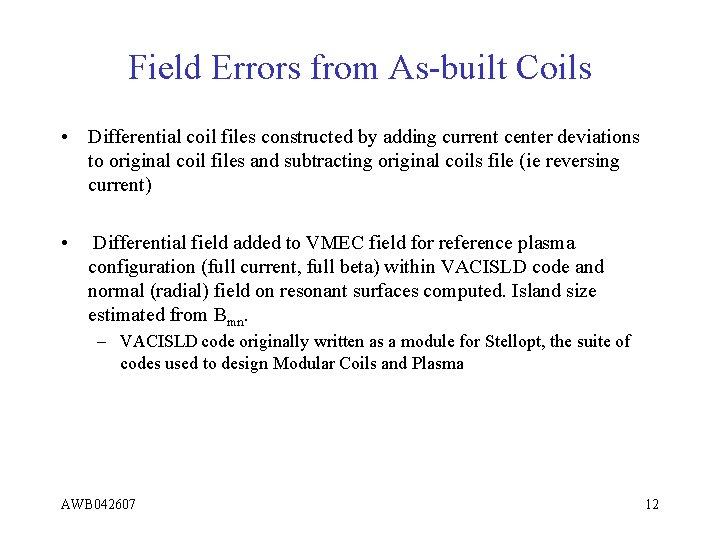
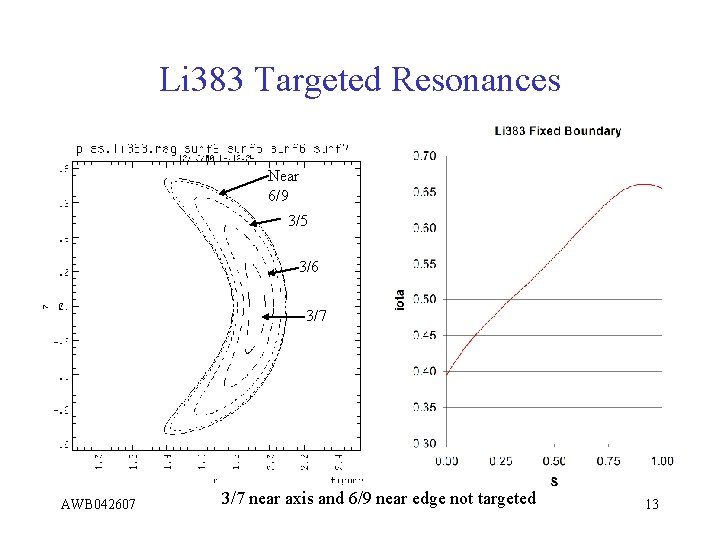
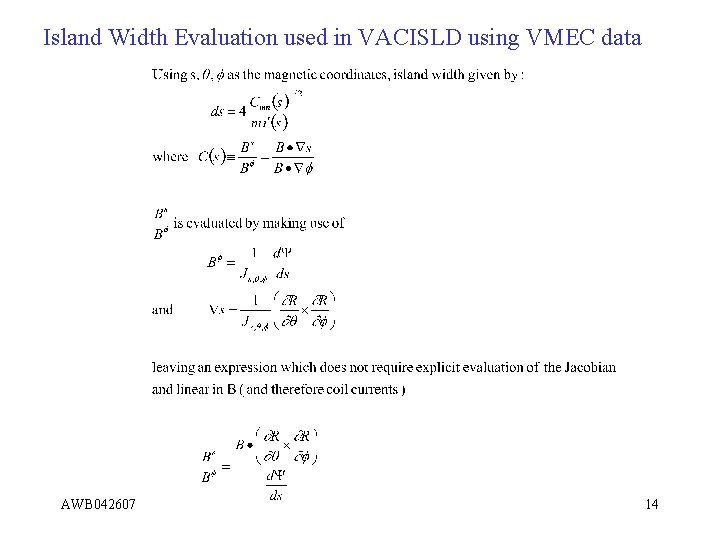
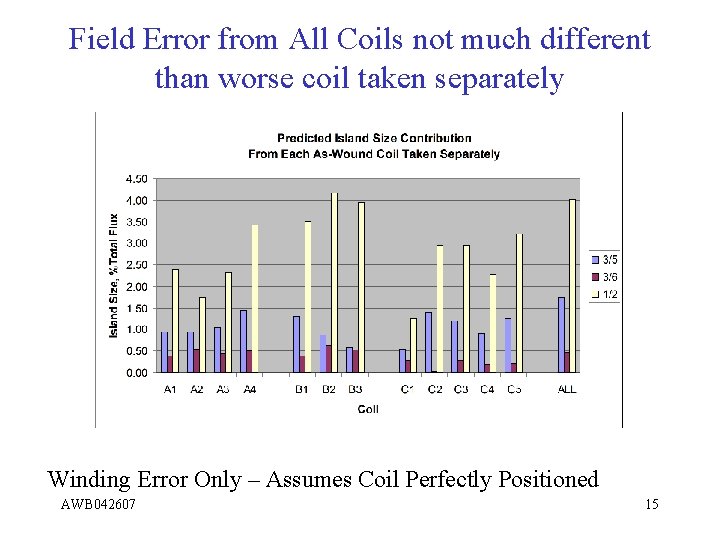
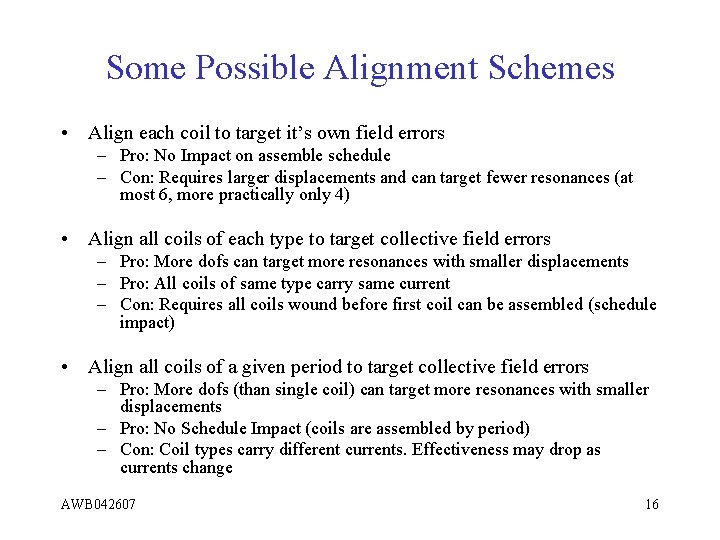
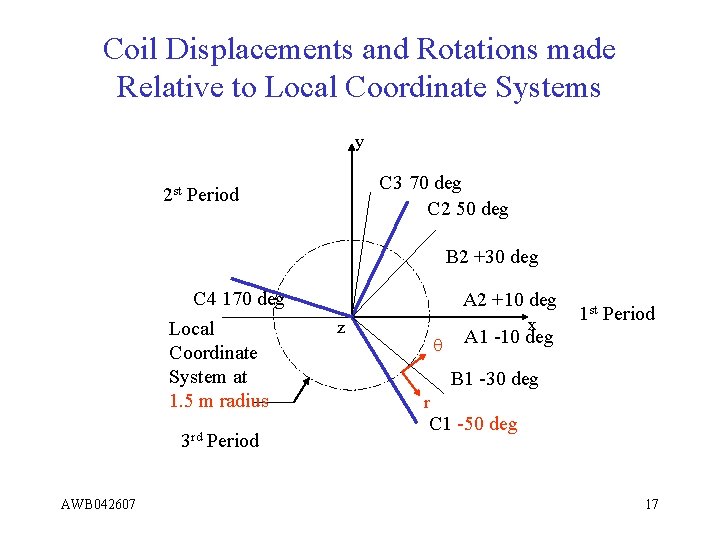
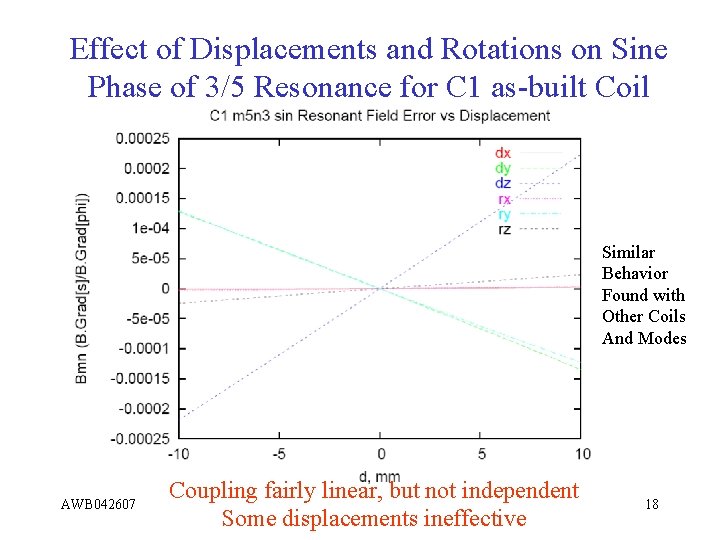
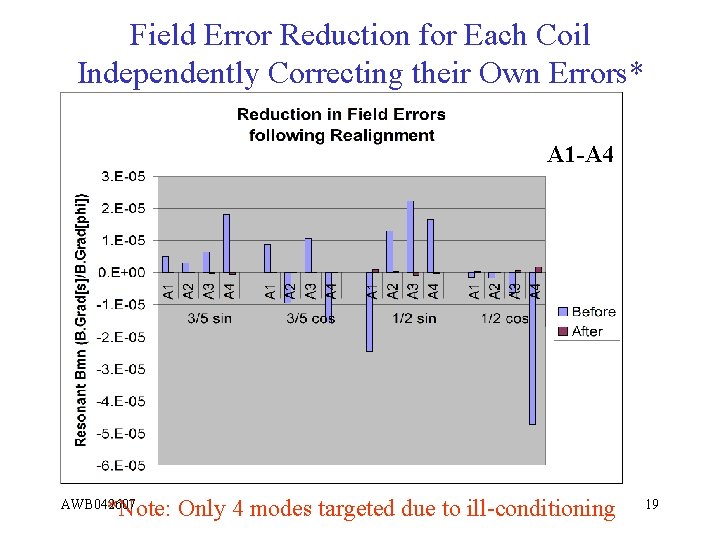
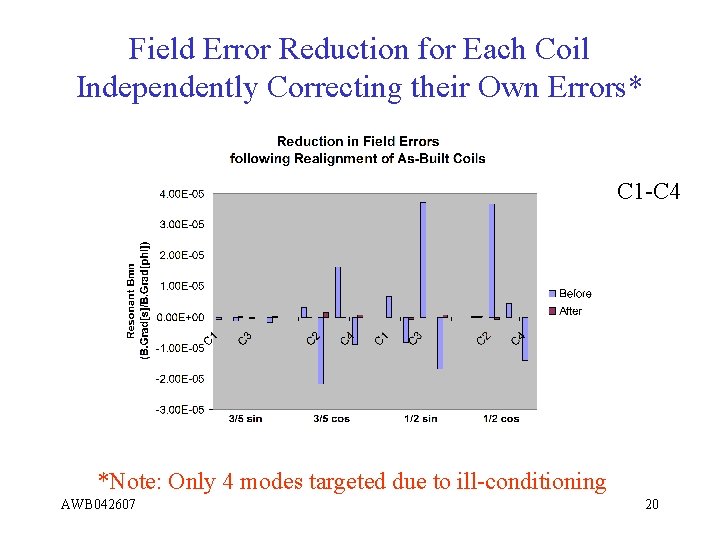
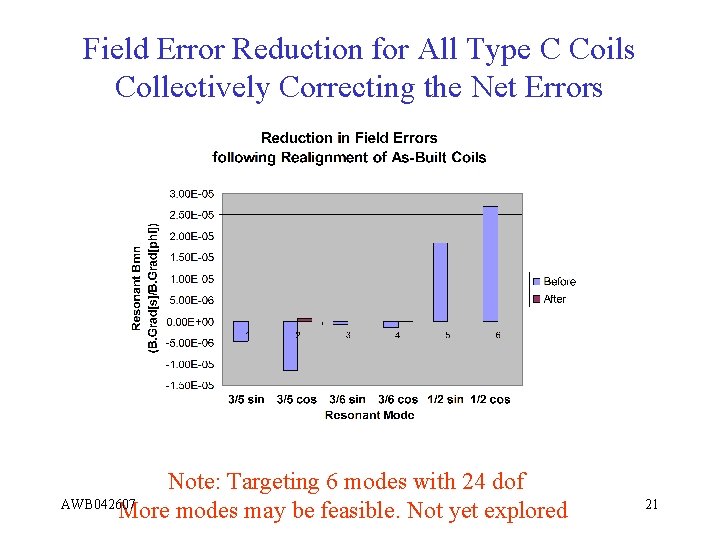
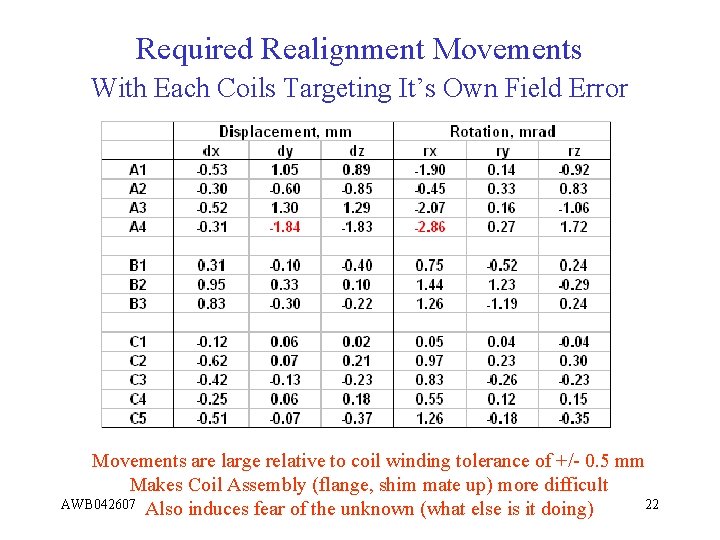
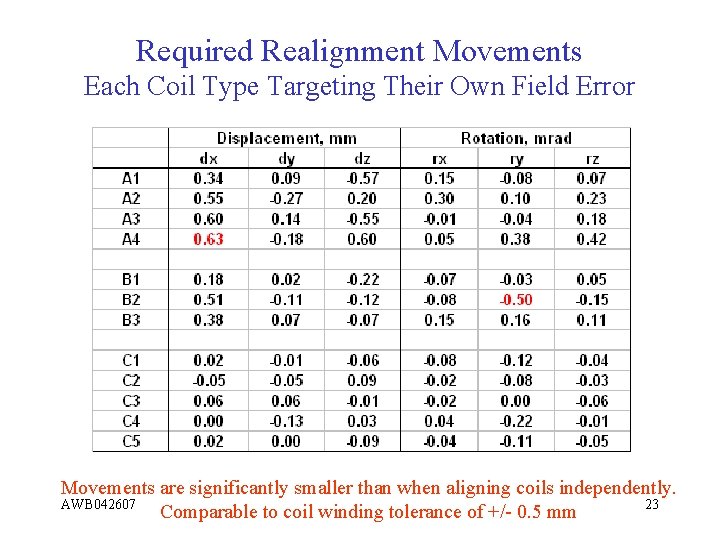
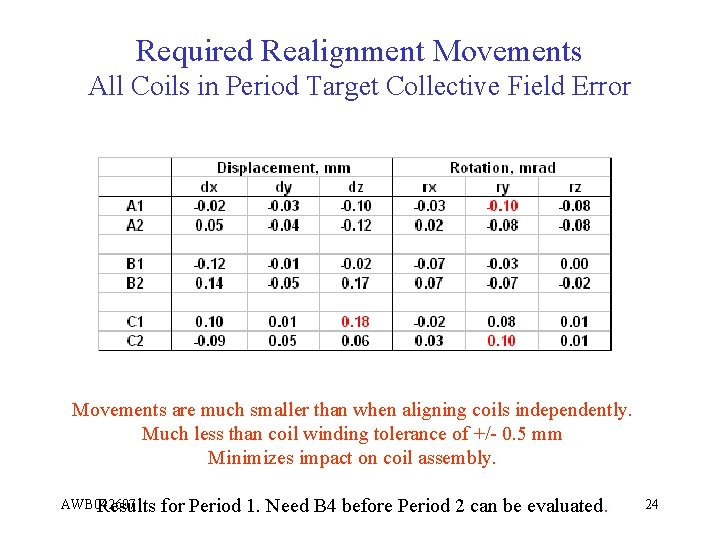
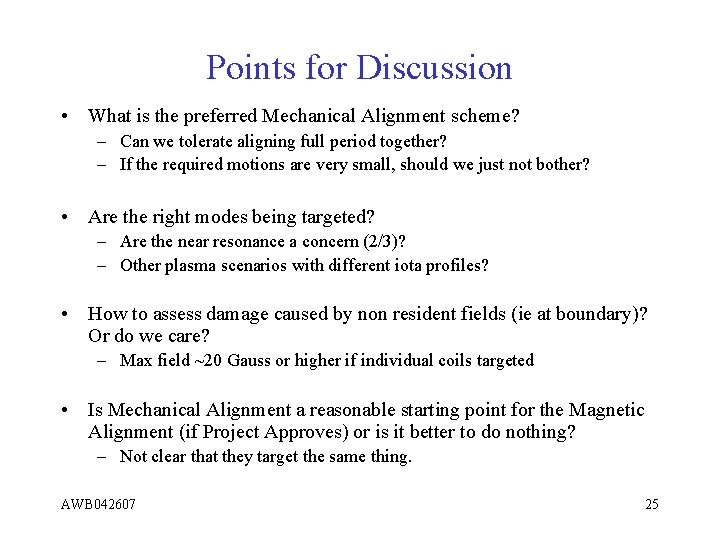
- Slides: 25
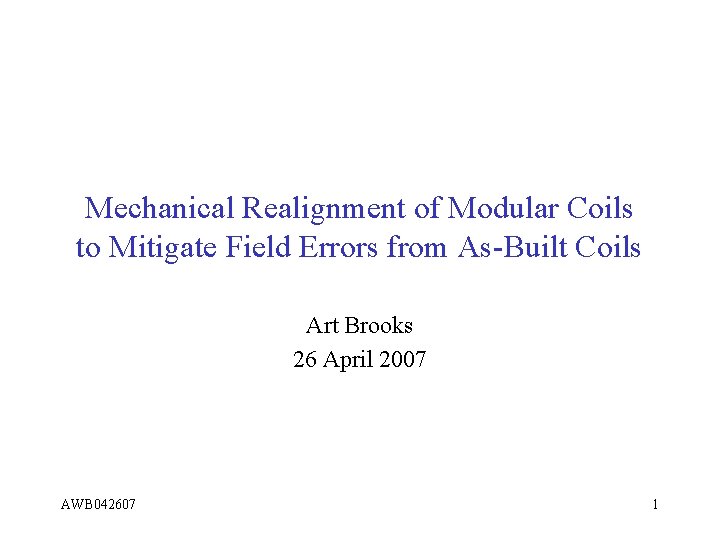
Mechanical Realignment of Modular Coils to Mitigate Field Errors from As-Built Coils Art Brooks 26 April 2007 AWB 042607 1
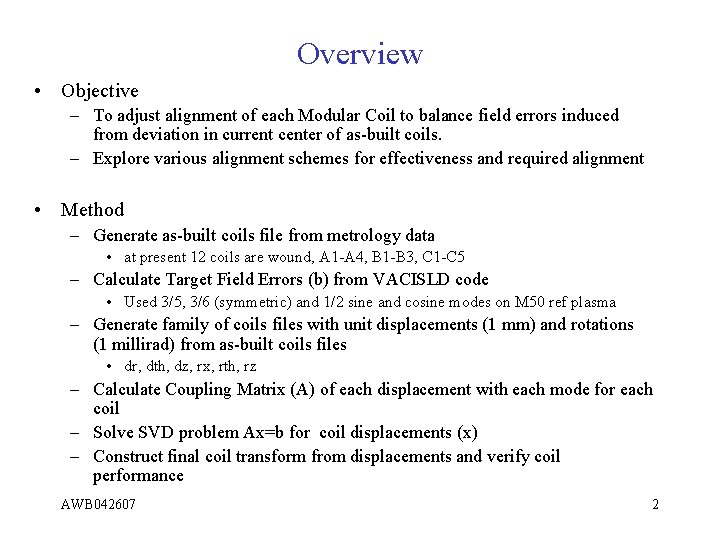
Overview • Objective – To adjust alignment of each Modular Coil to balance field errors induced from deviation in current center of as-built coils. – Explore various alignment schemes for effectiveness and required alignment • Method – Generate as-built coils file from metrology data • at present 12 coils are wound, A 1 -A 4, B 1 -B 3, C 1 -C 5 – Calculate Target Field Errors (b) from VACISLD code • Used 3/5, 3/6 (symmetric) and 1/2 sine and cosine modes on M 50 ref plasma – Generate family of coils files with unit displacements (1 mm) and rotations (1 millirad) from as-built coils files • dr, dth, dz, rx, rth, rz – Calculate Coupling Matrix (A) of each displacement with each mode for each coil – Solve SVD problem Ax=b for coil displacements (x) – Construct final coil transform from displacements and verify coil performance AWB 042607 2
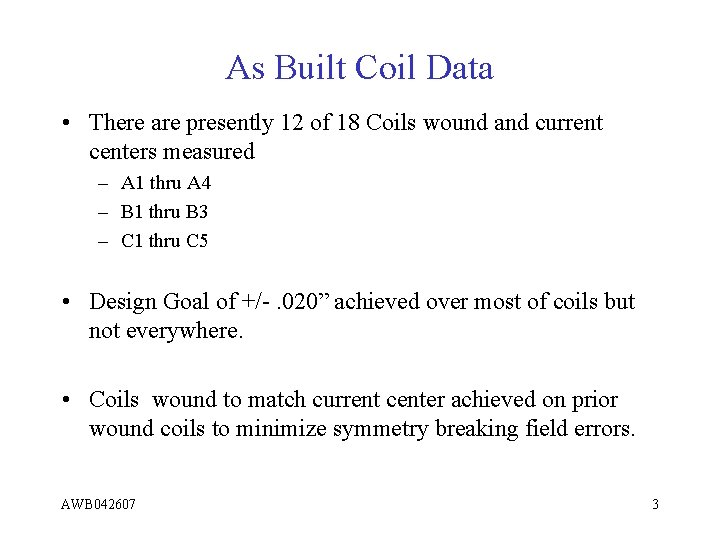
As Built Coil Data • There are presently 12 of 18 Coils wound and current centers measured – A 1 thru A 4 – B 1 thru B 3 – C 1 thru C 5 • Design Goal of +/-. 020” achieved over most of coils but not everywhere. • Coils wound to match current center achieved on prior wound coils to minimize symmetry breaking field errors. AWB 042607 3
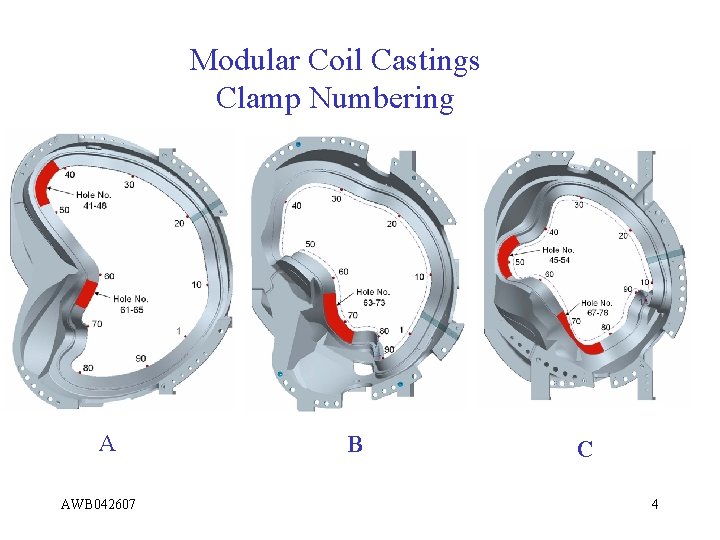
Modular Coil Castings Clamp Numbering A AWB 042607 B C 4
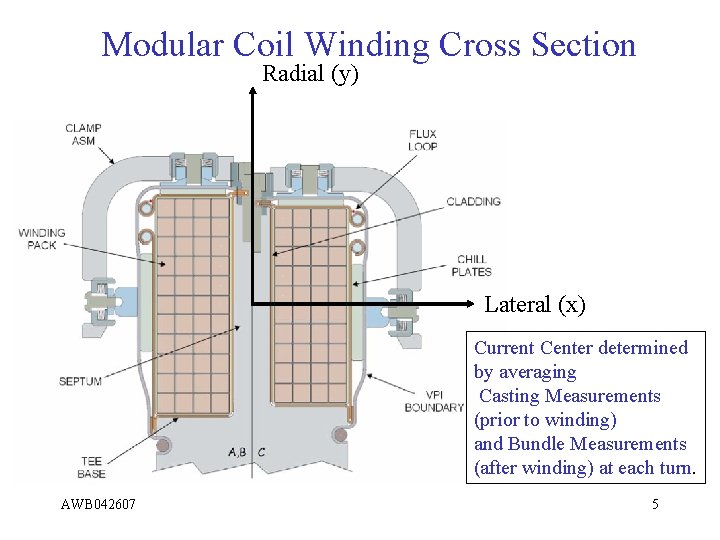
Modular Coil Winding Cross Section Radial (y) Lateral (x) Current Center determined by averaging Casting Measurements (prior to winding) and Bundle Measurements (after winding) at each turn. AWB 042607 5
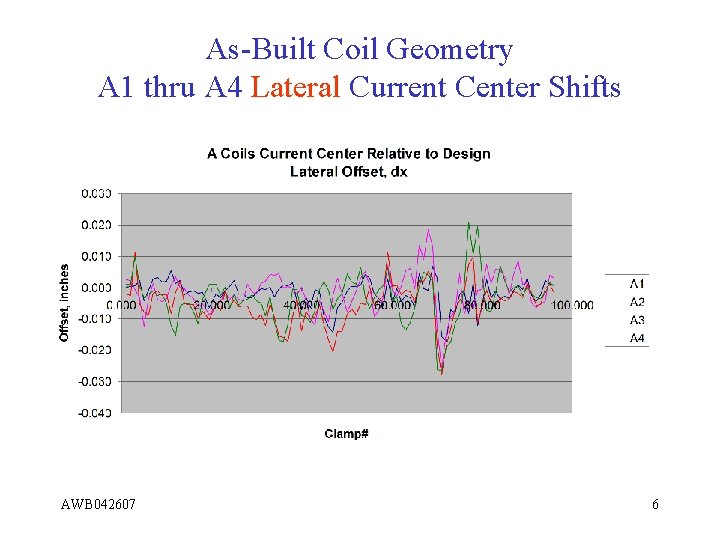
As-Built Coil Geometry A 1 thru A 4 Lateral Current Center Shifts AWB 042607 6
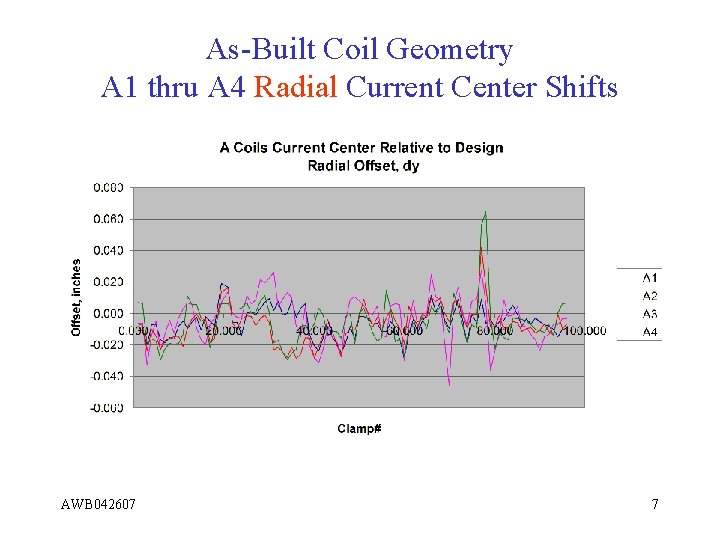
As-Built Coil Geometry A 1 thru A 4 Radial Current Center Shifts AWB 042607 7
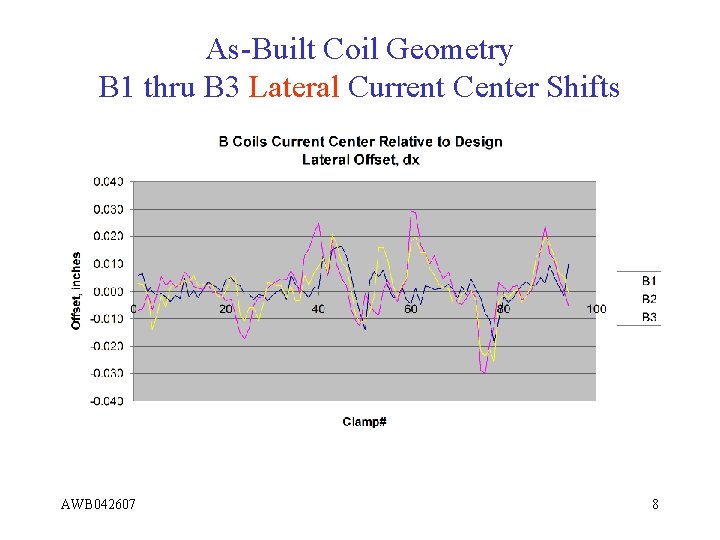
As-Built Coil Geometry B 1 thru B 3 Lateral Current Center Shifts AWB 042607 8
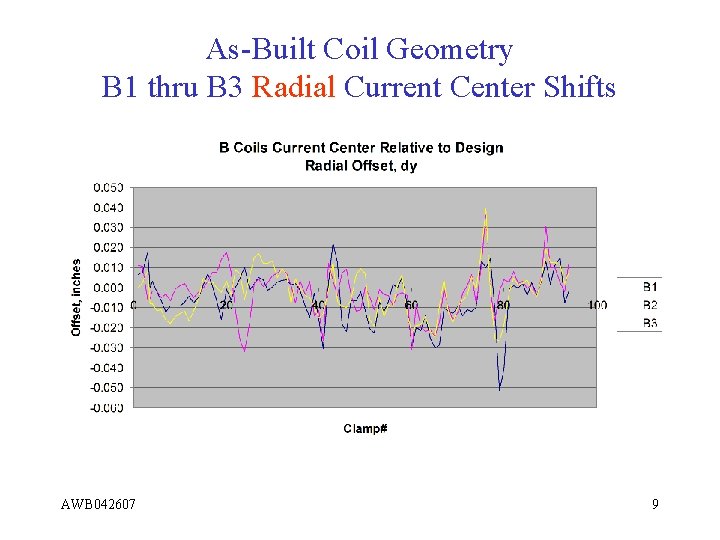
As-Built Coil Geometry B 1 thru B 3 Radial Current Center Shifts AWB 042607 9
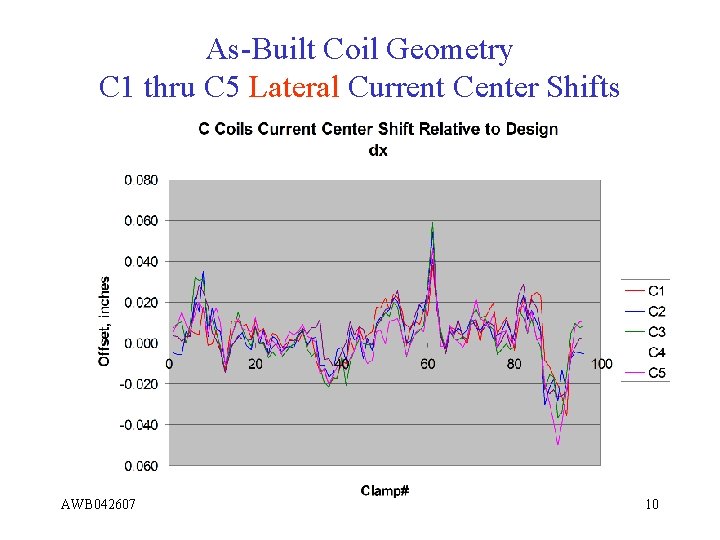
As-Built Coil Geometry C 1 thru C 5 Lateral Current Center Shifts AWB 042607 10
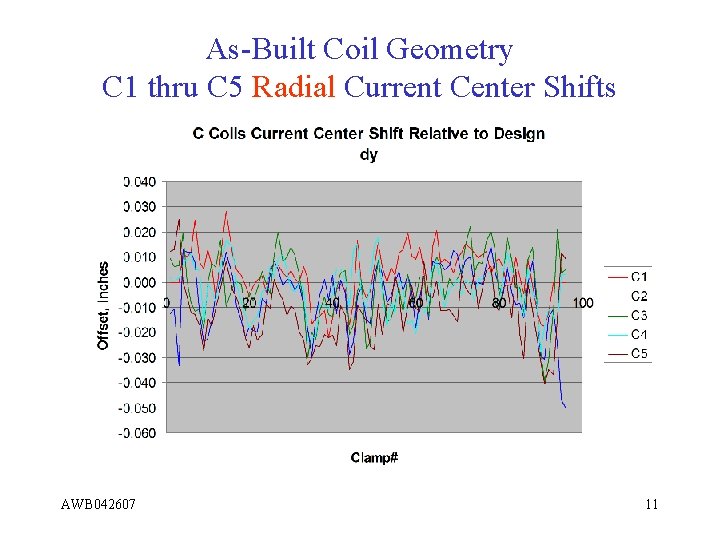
As-Built Coil Geometry C 1 thru C 5 Radial Current Center Shifts AWB 042607 11
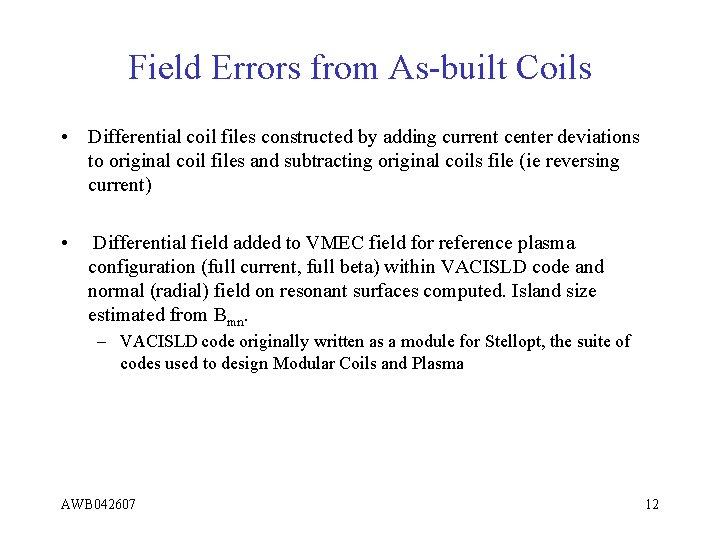
Field Errors from As-built Coils • Differential coil files constructed by adding current center deviations to original coil files and subtracting original coils file (ie reversing current) • Differential field added to VMEC field for reference plasma configuration (full current, full beta) within VACISLD code and normal (radial) field on resonant surfaces computed. Island size estimated from Bmn. – VACISLD code originally written as a module for Stellopt, the suite of codes used to design Modular Coils and Plasma AWB 042607 12
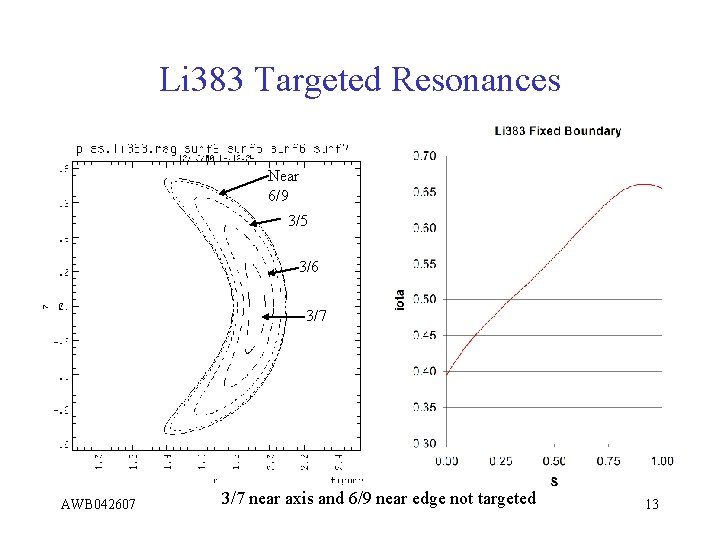
Li 383 Targeted Resonances Near 6/9 3/5 3/6 3/7 AWB 042607 3/7 near axis and 6/9 near edge not targeted 13
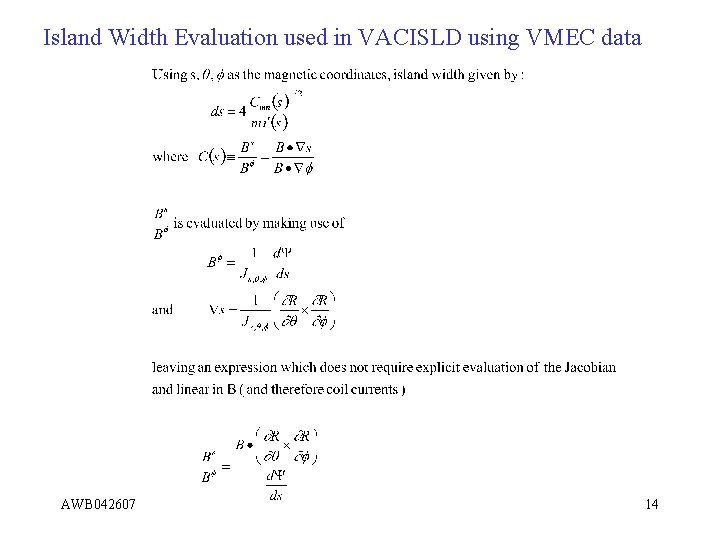
Island Width Evaluation used in VACISLD using VMEC data AWB 042607 14
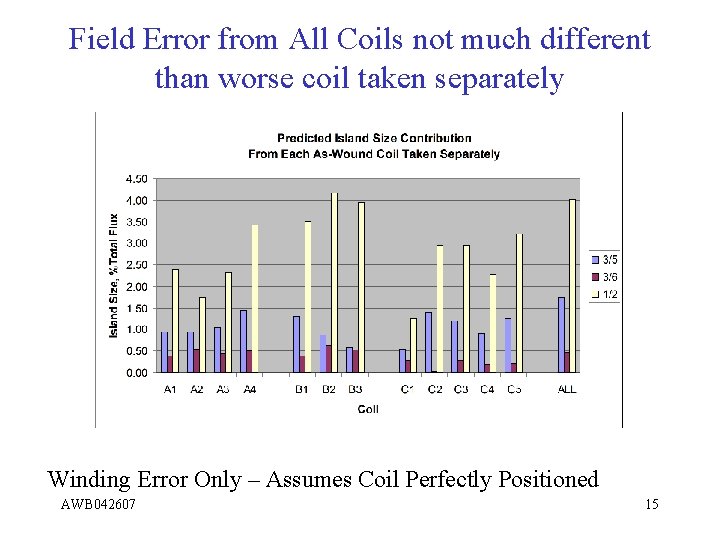
Field Error from All Coils not much different than worse coil taken separately Winding Error Only – Assumes Coil Perfectly Positioned AWB 042607 15
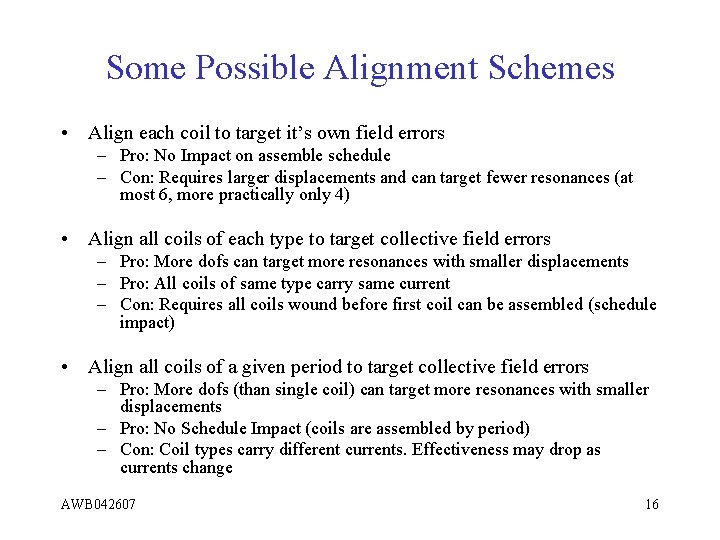
Some Possible Alignment Schemes • Align each coil to target it’s own field errors – Pro: No Impact on assemble schedule – Con: Requires larger displacements and can target fewer resonances (at most 6, more practically only 4) • Align all coils of each type to target collective field errors – Pro: More dofs can target more resonances with smaller displacements – Pro: All coils of same type carry same current – Con: Requires all coils wound before first coil can be assembled (schedule impact) • Align all coils of a given period to target collective field errors – Pro: More dofs (than single coil) can target more resonances with smaller displacements – Pro: No Schedule Impact (coils are assembled by period) – Con: Coil types carry different currents. Effectiveness may drop as currents change AWB 042607 16
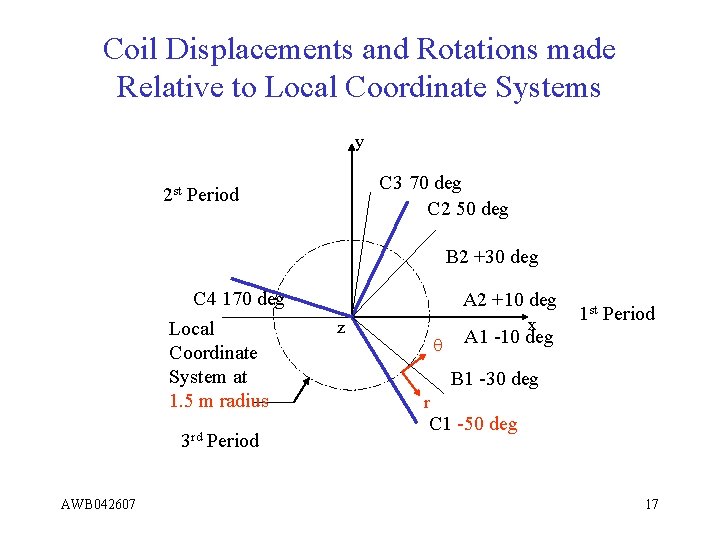
Coil Displacements and Rotations made Relative to Local Coordinate Systems y C 3 70 deg C 2 50 deg 2 st Period B 2 +30 deg C 4 170 deg Local Coordinate System at 1. 5 m radius 3 rd AWB 042607 Period A 2 +10 deg z q x 1 st Period A 1 -10 deg B 1 -30 deg r C 1 -50 deg 17
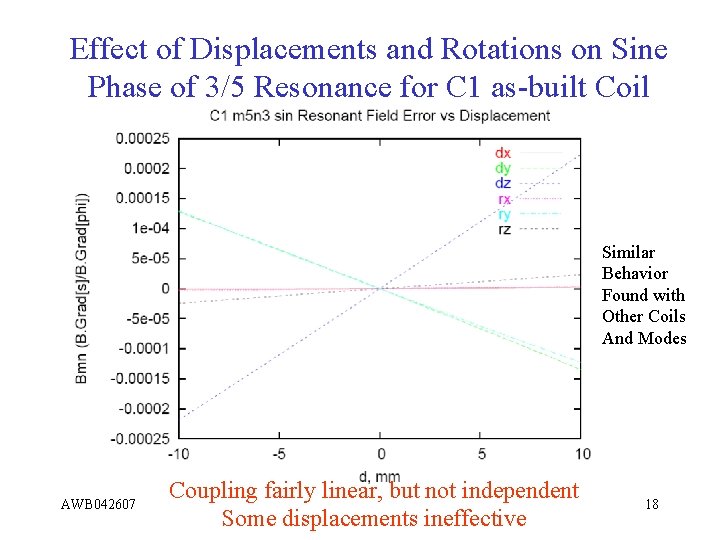
Effect of Displacements and Rotations on Sine Phase of 3/5 Resonance for C 1 as-built Coil Similar Behavior Found with Other Coils And Modes AWB 042607 Coupling fairly linear, but not independent Some displacements ineffective 18
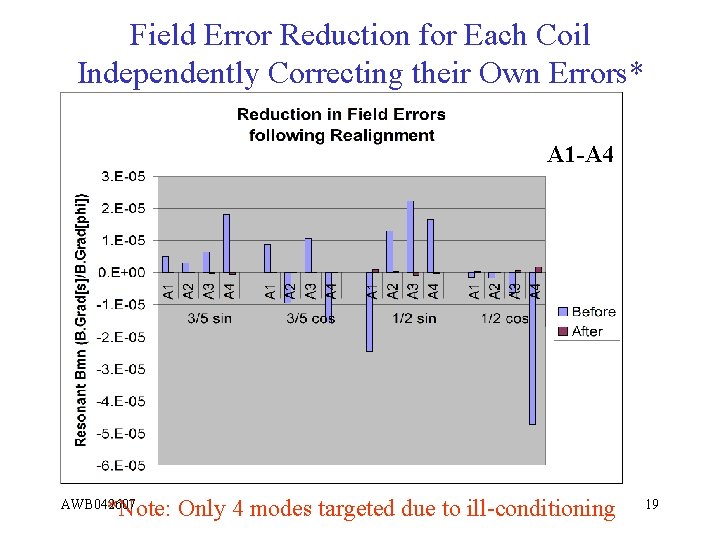
Field Error Reduction for Each Coil Independently Correcting their Own Errors* A 1 -A 4 *Note: Only 4 modes targeted due to ill-conditioning AWB 042607 19
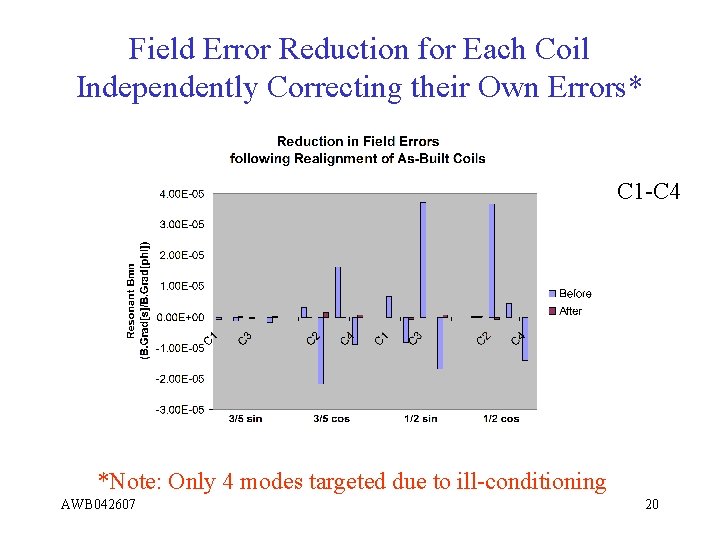
Field Error Reduction for Each Coil Independently Correcting their Own Errors* C 1 -C 4 *Note: Only 4 modes targeted due to ill-conditioning AWB 042607 20
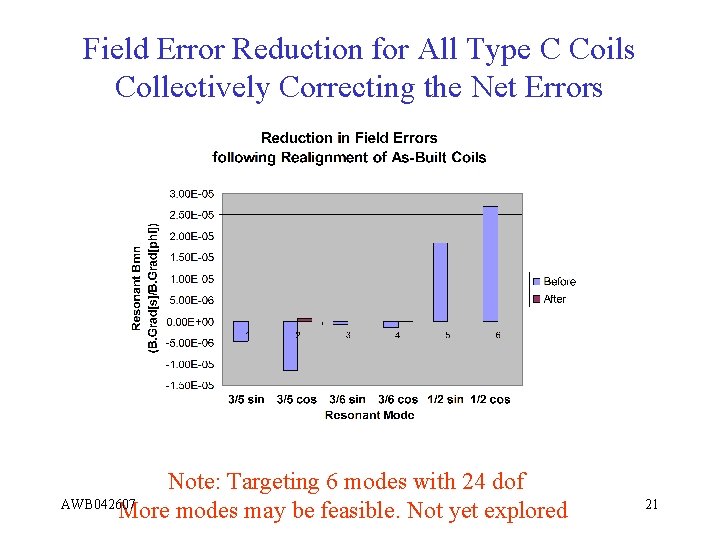
Field Error Reduction for All Type C Coils Collectively Correcting the Net Errors Note: Targeting 6 modes with 24 dof AWB 042607 More modes may be feasible. Not yet explored 21
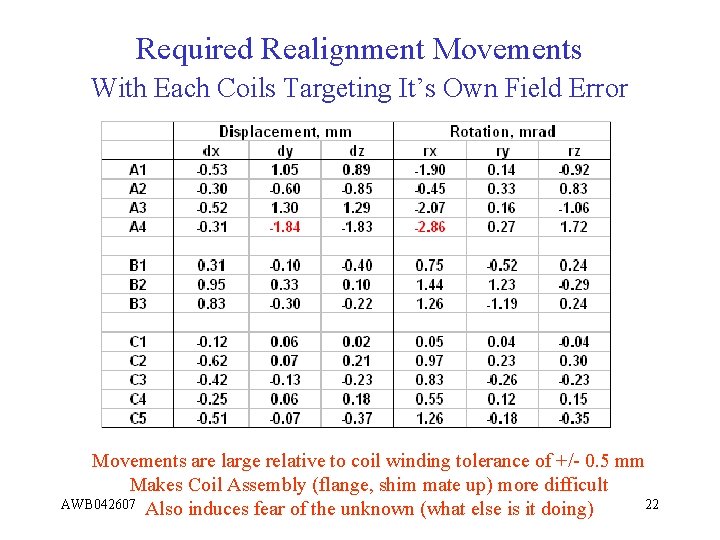
Required Realignment Movements With Each Coils Targeting It’s Own Field Error Movements are large relative to coil winding tolerance of +/- 0. 5 mm Makes Coil Assembly (flange, shim mate up) more difficult AWB 042607 Also induces fear of the unknown (what else is it doing) 22
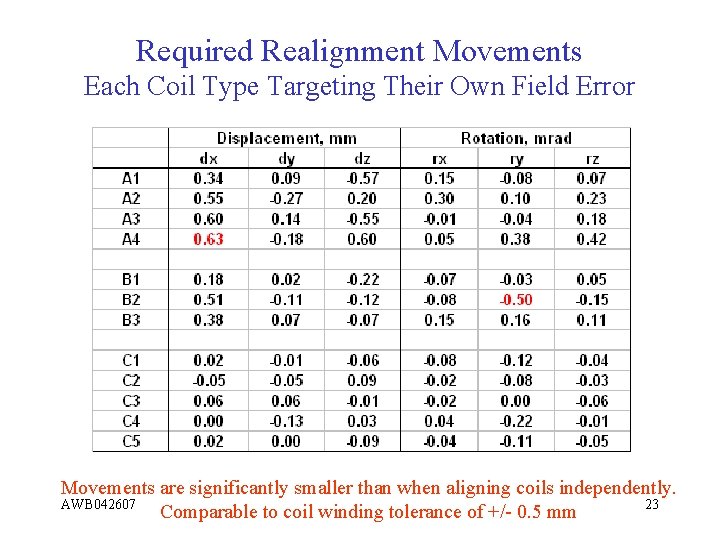
Required Realignment Movements Each Coil Type Targeting Their Own Field Error Movements are significantly smaller than when aligning coils independently. AWB 042607 23 Comparable to coil winding tolerance of +/- 0. 5 mm
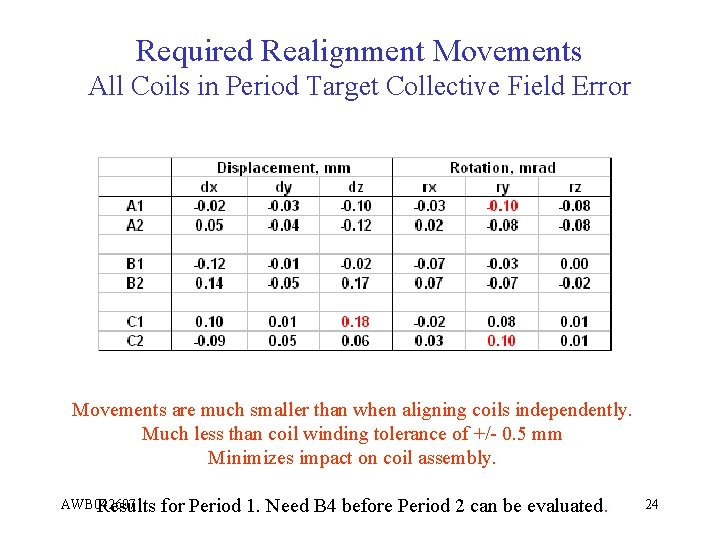
Required Realignment Movements All Coils in Period Target Collective Field Error Movements are much smaller than when aligning coils independently. Much less than coil winding tolerance of +/- 0. 5 mm Minimizes impact on coil assembly. AWB 042607 Results for Period 1. Need B 4 before Period 2 can be evaluated. 24
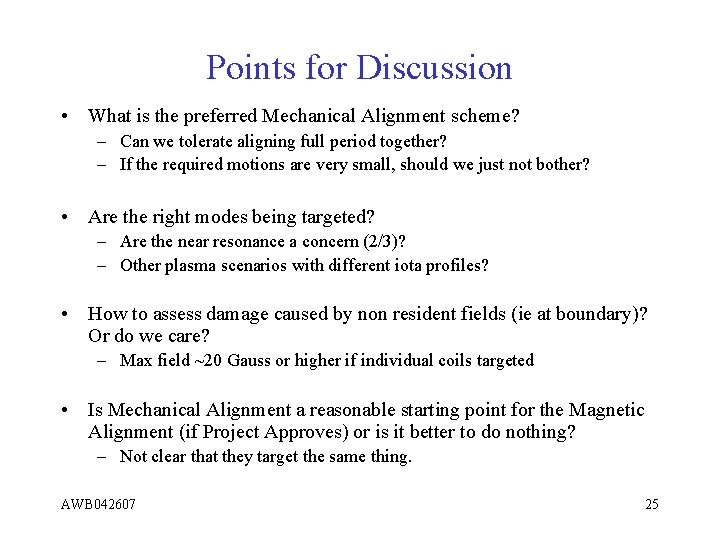
Points for Discussion • What is the preferred Mechanical Alignment scheme? – Can we tolerate aligning full period together? – If the required motions are very small, should we just not bother? • Are the right modes being targeted? – Are the near resonance a concern (2/3)? – Other plasma scenarios with different iota profiles? • How to assess damage caused by non resident fields (ie at boundary)? Or do we care? – Max field ~20 Gauss or higher if individual coils targeted • Is Mechanical Alignment a reasonable starting point for the Magnetic Alignment (if Project Approves) or is it better to do nothing? – Not clear that they target the same thing. AWB 042607 25
Apex distance of curve formula
1991 realignment
Prepare mitigate respond recover
Mitigate buffer overflow
"risk management workflow" mitigate transfer
Iter coils
Left anterior lobe frog
Magnetic field drift
Coupled circuits
Iter coils
Coils
Lordan coils
Actual mechanical advantage vs ideal mechanical advantage
Electric field and magnetic field difference
Difference between electric field and magnetic field
Waveguide cutoff frequency
Electric field and magnetic field difference
Database field types and field properties
Field dependent vs field independent
Field dependent vs field independent
Field dependent and field independent
Modular design programming
Modular arithmetic
Modular approach adalah
Modular object-oriented dynamic learning environment
Solaris modular approach