MATSE 259 EXAM 3 REVIEW SESSION 1 Exam
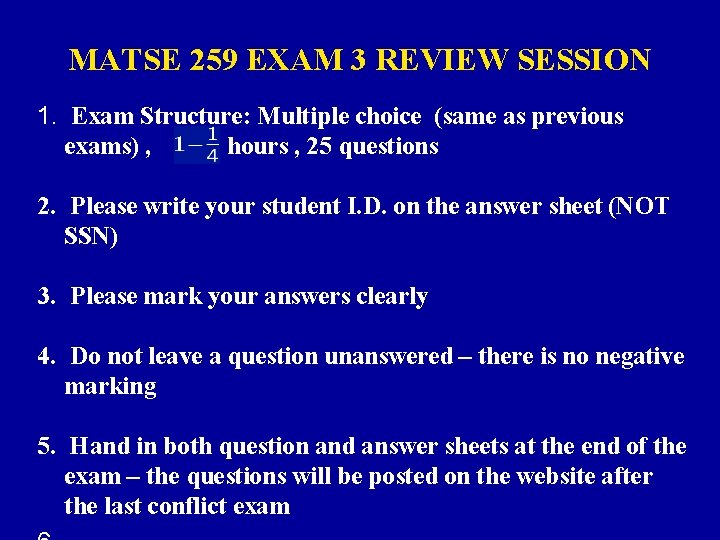
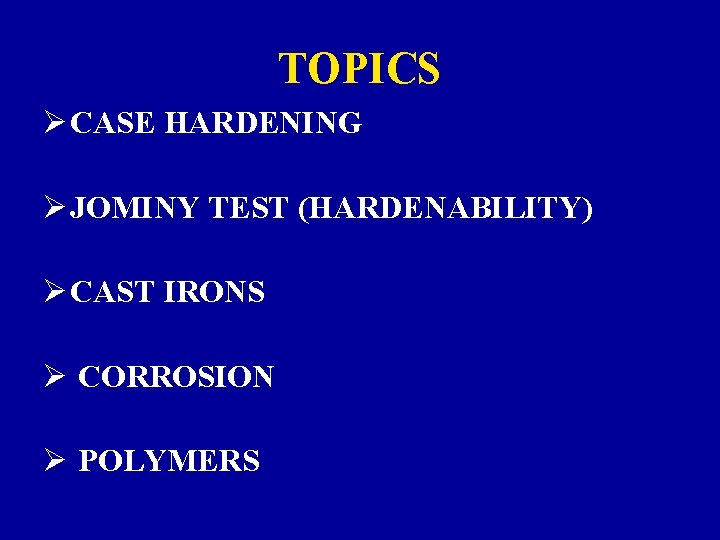
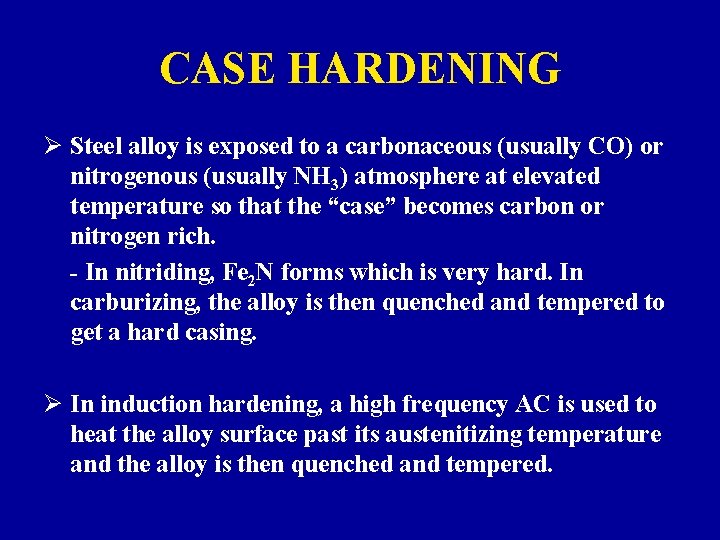
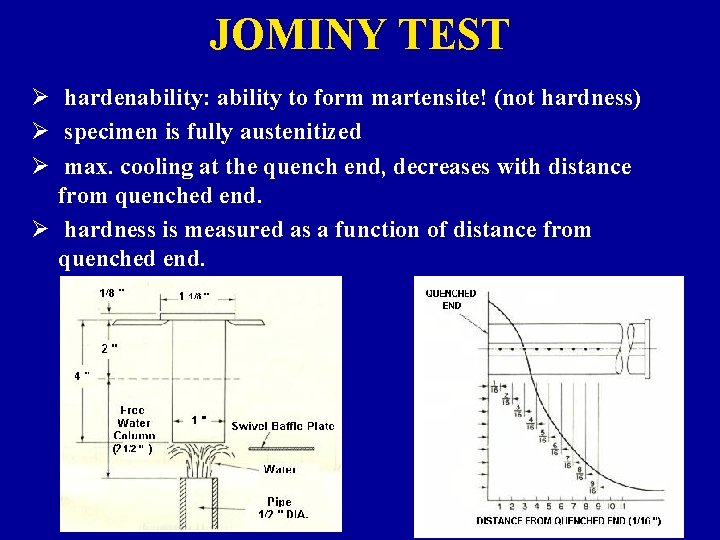
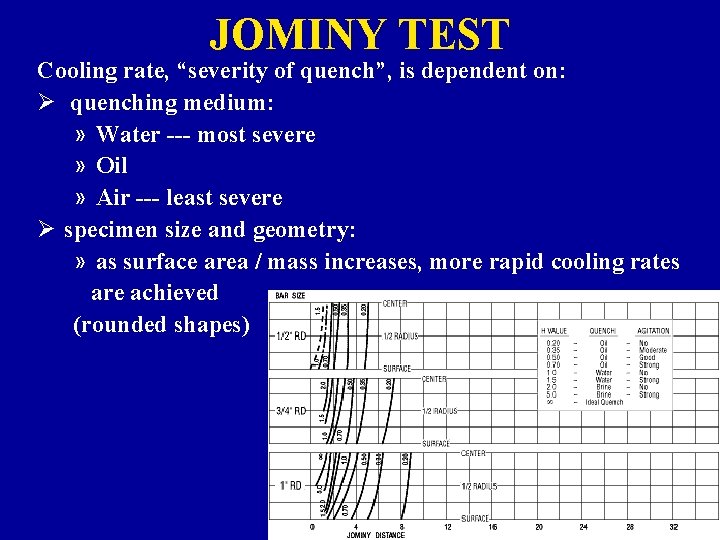
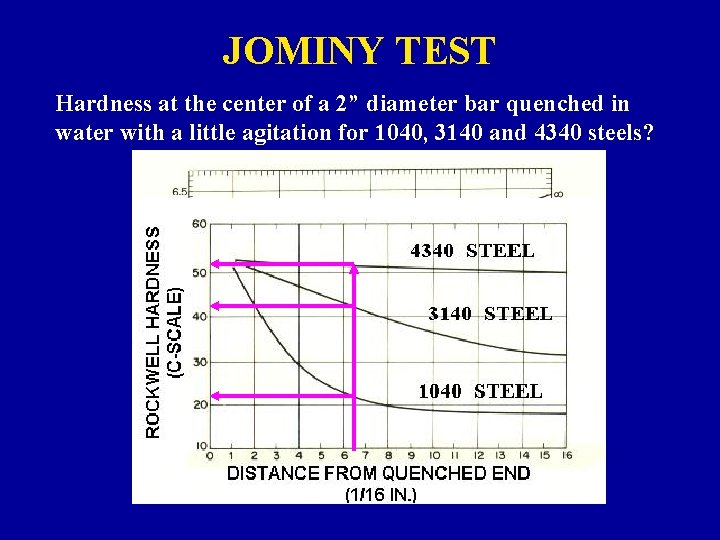
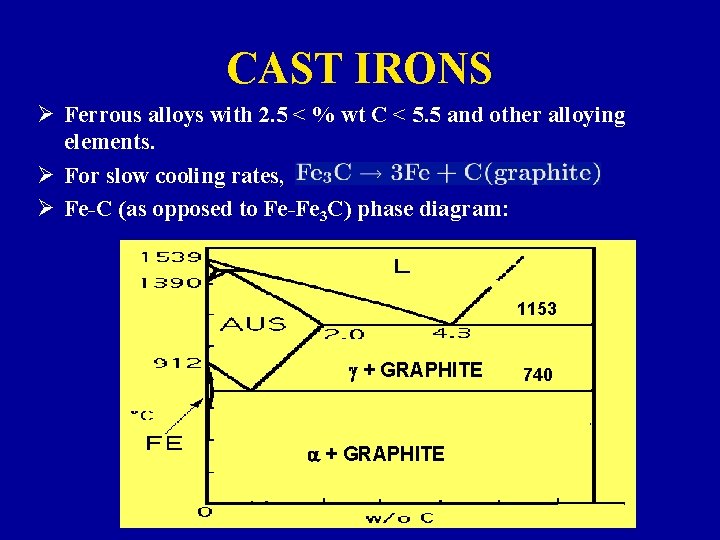
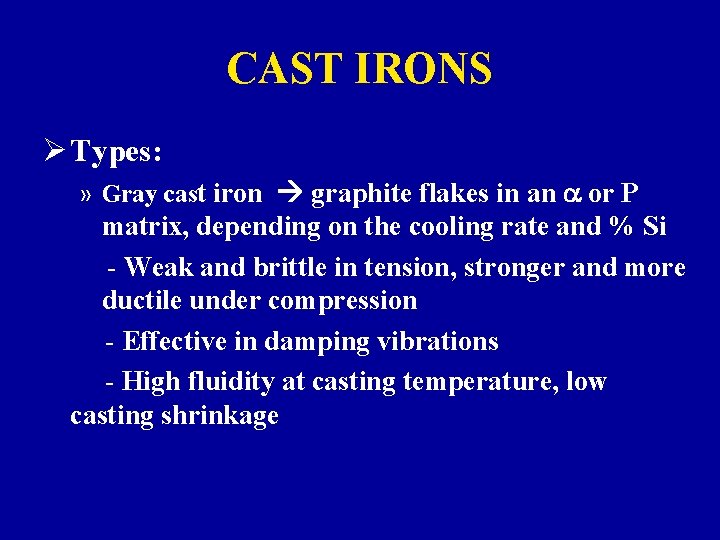
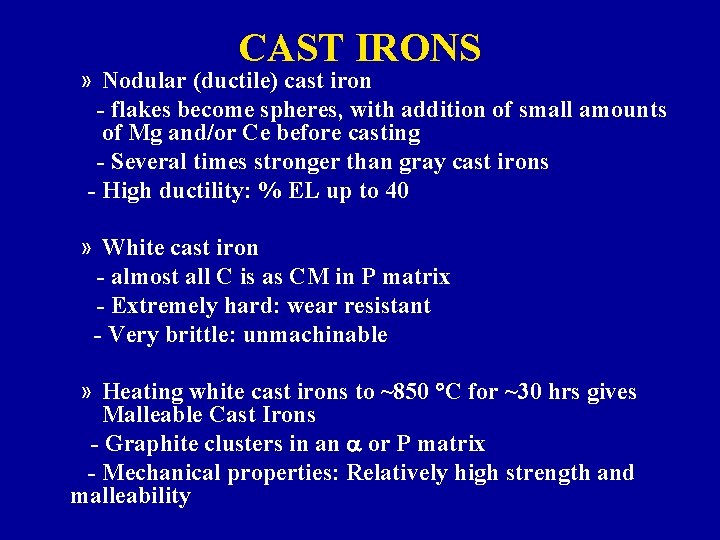
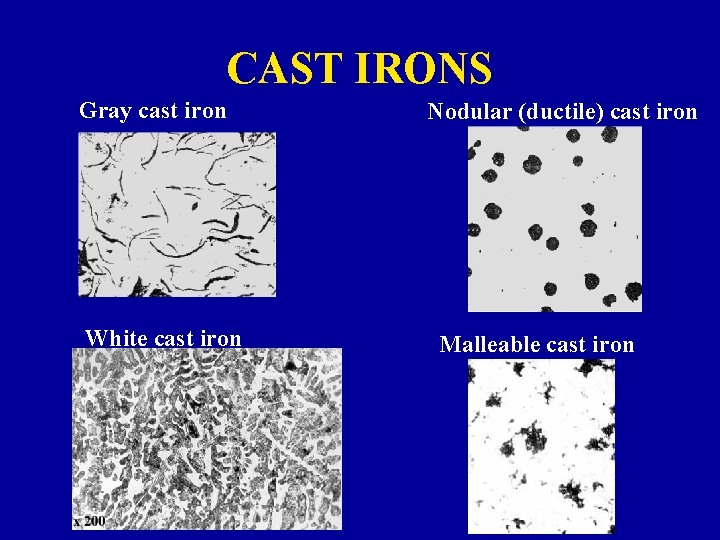
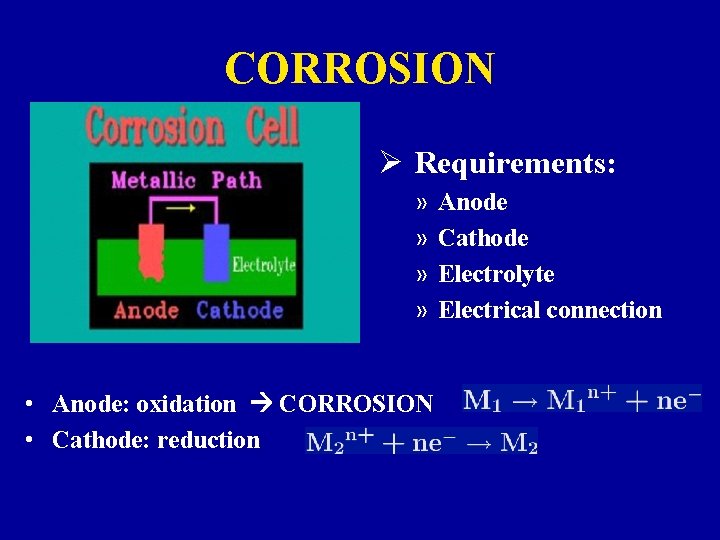
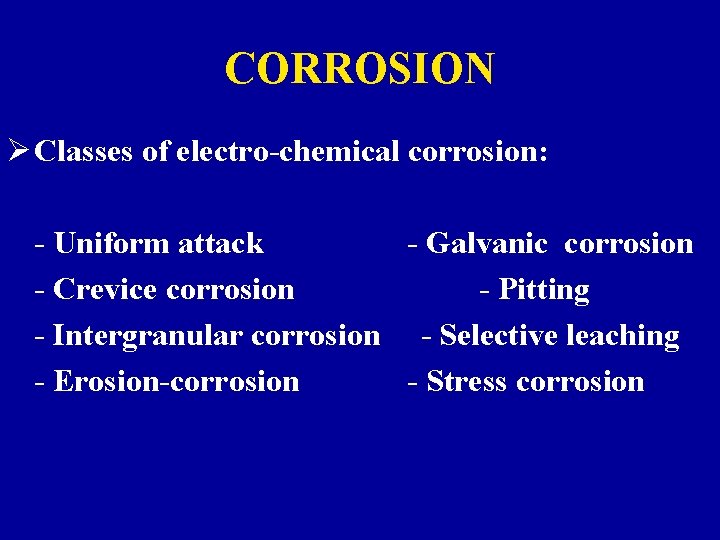
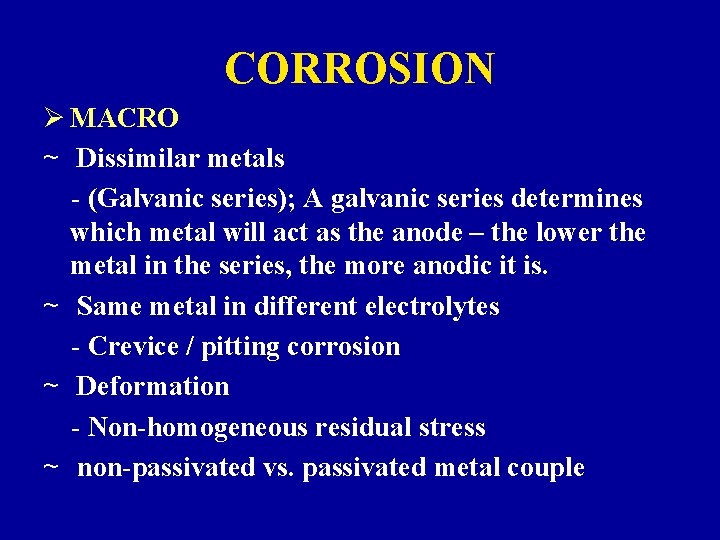
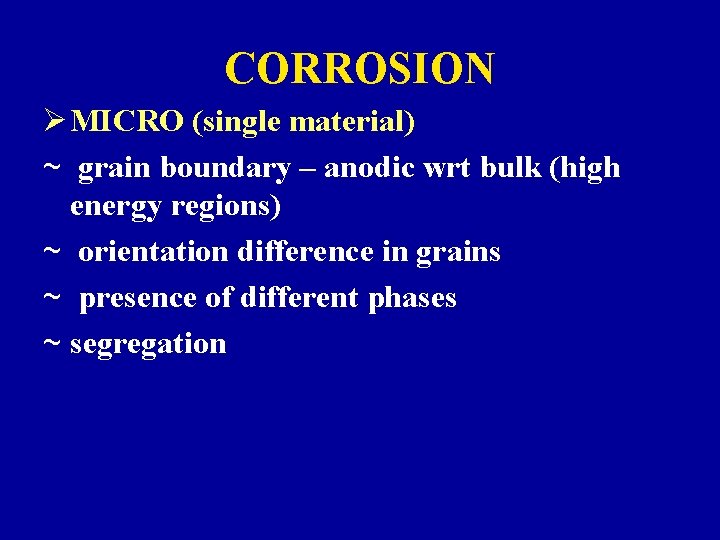
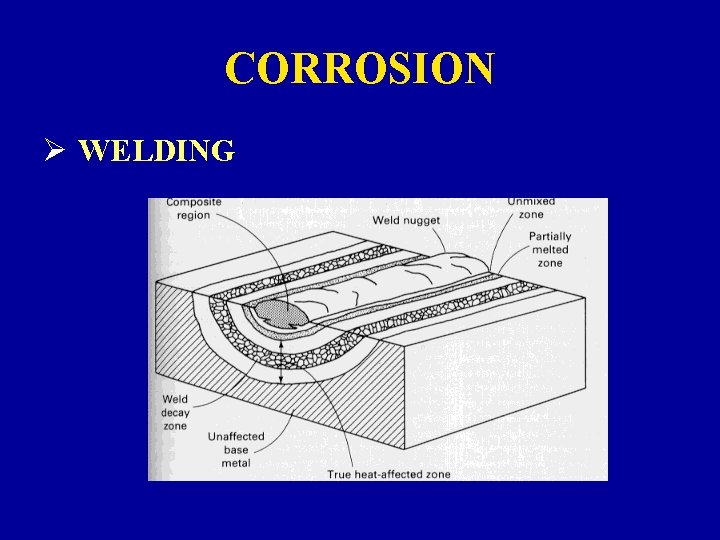
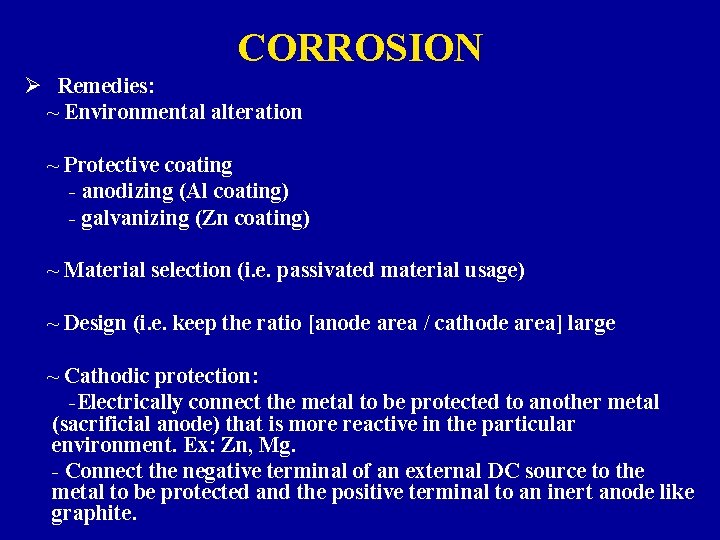
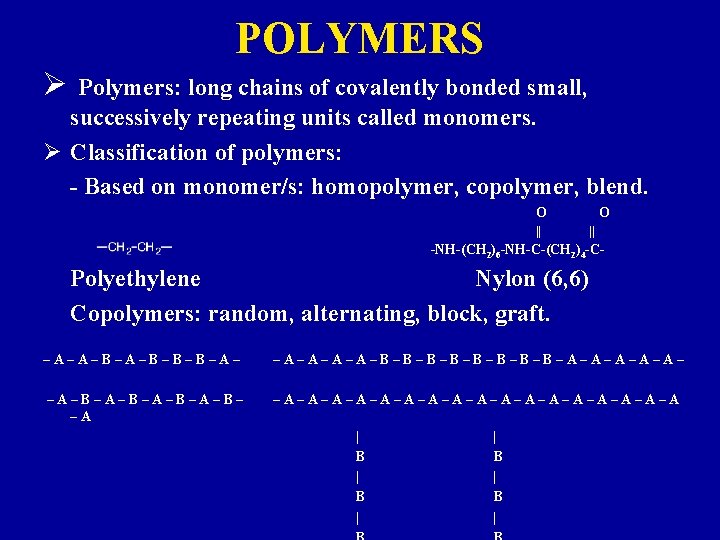
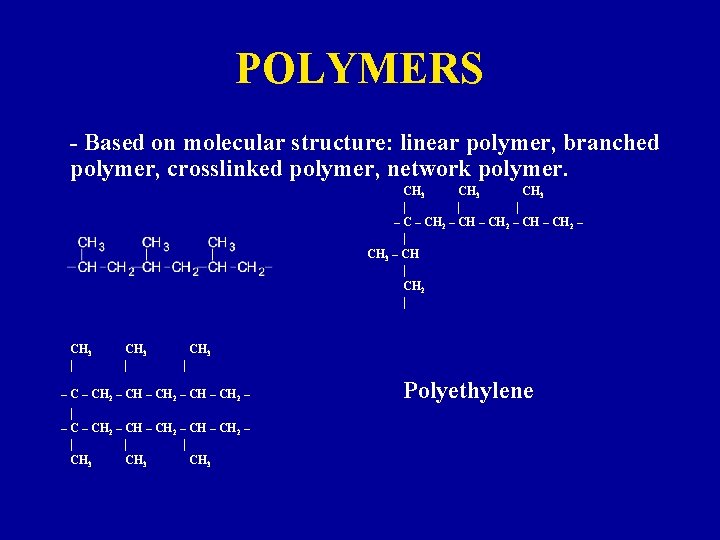
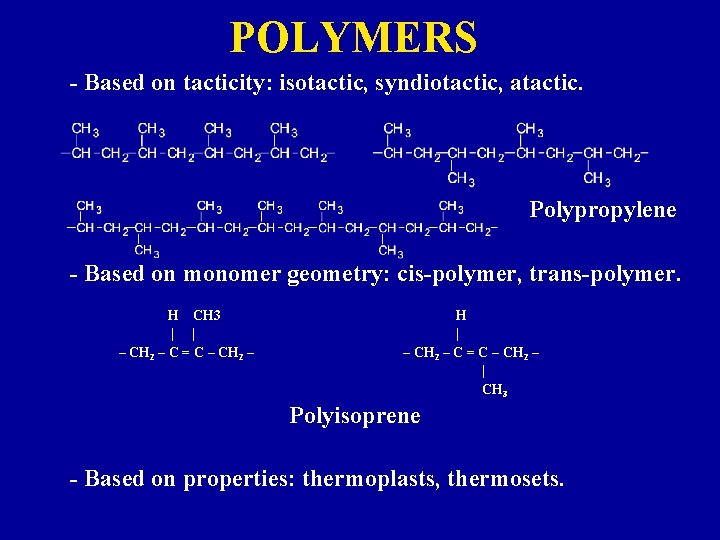
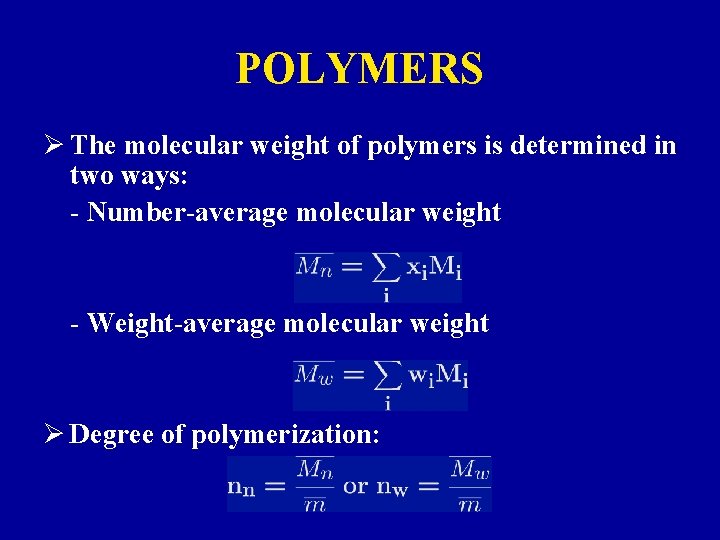
- Slides: 20
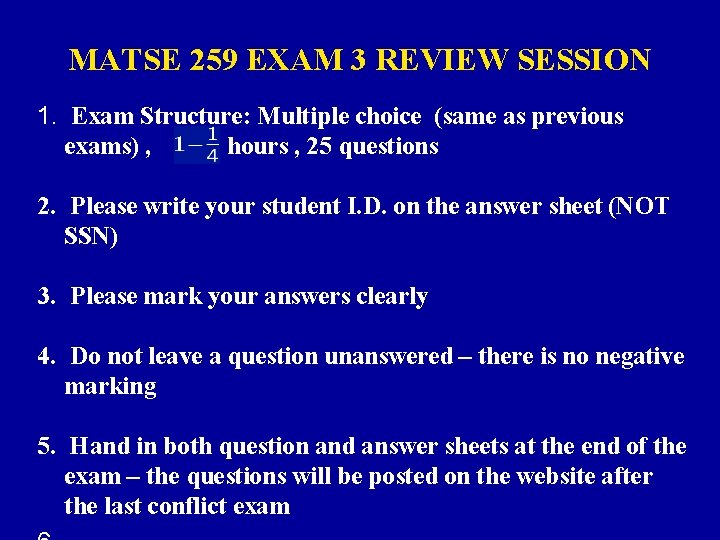
MATSE 259 EXAM 3 REVIEW SESSION 1. Exam Structure: Multiple choice (same as previous exams) , hours , 25 questions 2. Please write your student I. D. on the answer sheet (NOT SSN) 3. Please mark your answers clearly 4. Do not leave a question unanswered – there is no negative marking 5. Hand in both question and answer sheets at the end of the exam – the questions will be posted on the website after the last conflict exam
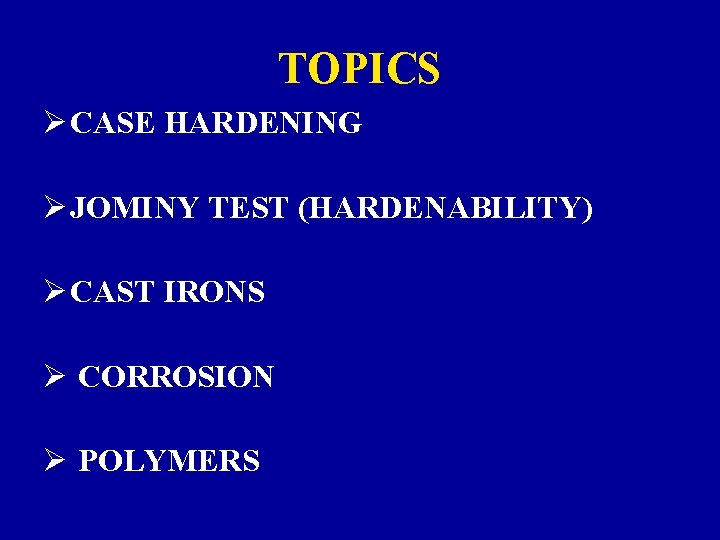
TOPICS Ø CASE HARDENING Ø JOMINY TEST (HARDENABILITY) Ø CAST IRONS Ø CORROSION Ø POLYMERS
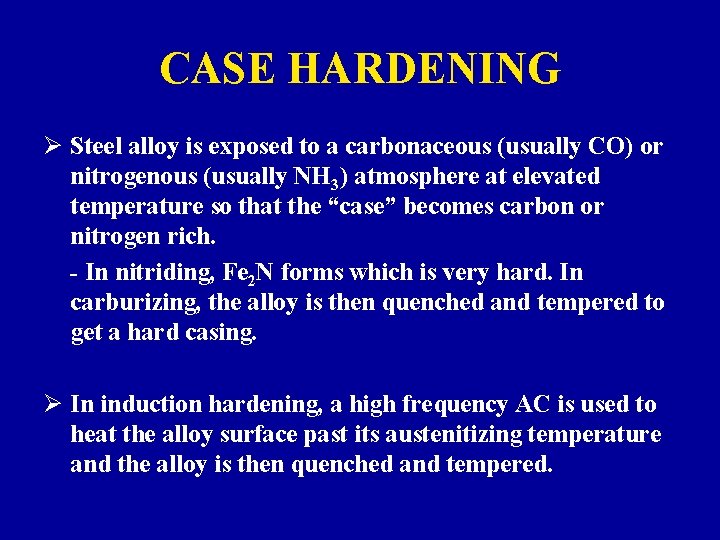
CASE HARDENING Ø Steel alloy is exposed to a carbonaceous (usually CO) or nitrogenous (usually NH 3) atmosphere at elevated temperature so that the “case” becomes carbon or nitrogen rich. - In nitriding, Fe 2 N forms which is very hard. In carburizing, the alloy is then quenched and tempered to get a hard casing. Ø In induction hardening, a high frequency AC is used to heat the alloy surface past its austenitizing temperature and the alloy is then quenched and tempered.
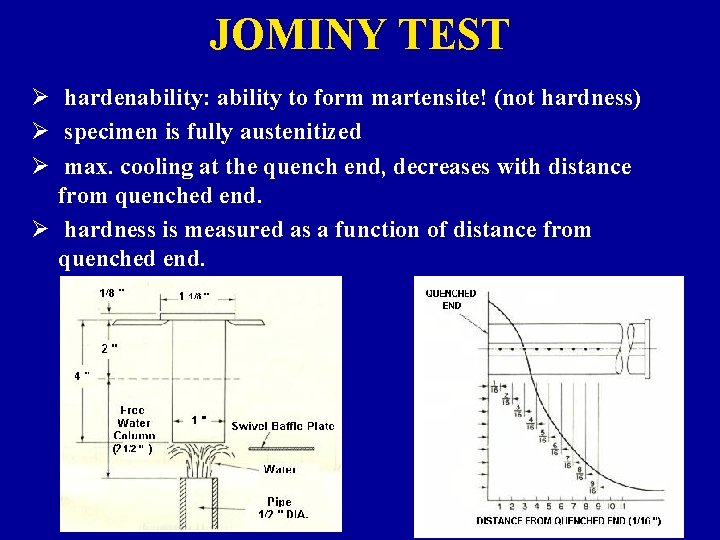
JOMINY TEST Ø hardenability: ability to form martensite! (not hardness) Ø specimen is fully austenitized Ø max. cooling at the quench end, decreases with distance from quenched end. Ø hardness is measured as a function of distance from quenched end.
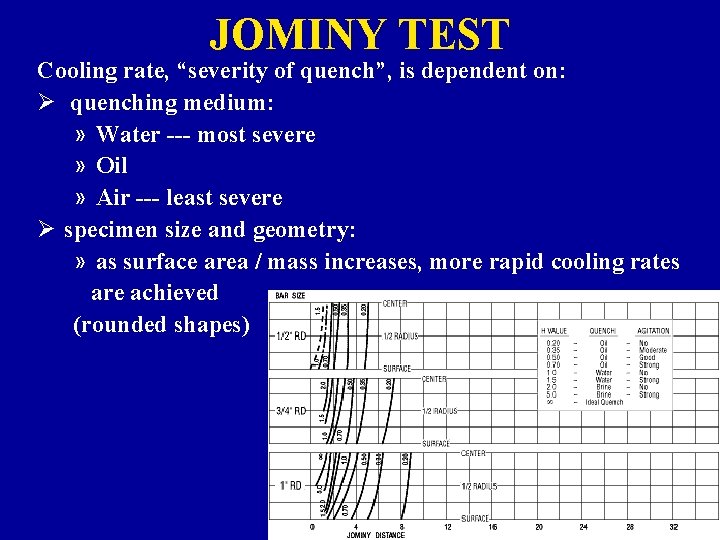
JOMINY TEST Cooling rate, “severity of quench”, is dependent on: Ø quenching medium: » Water --- most severe » Oil » Air --- least severe Ø specimen size and geometry: » as surface area / mass increases, more rapid cooling rates are achieved (rounded shapes)
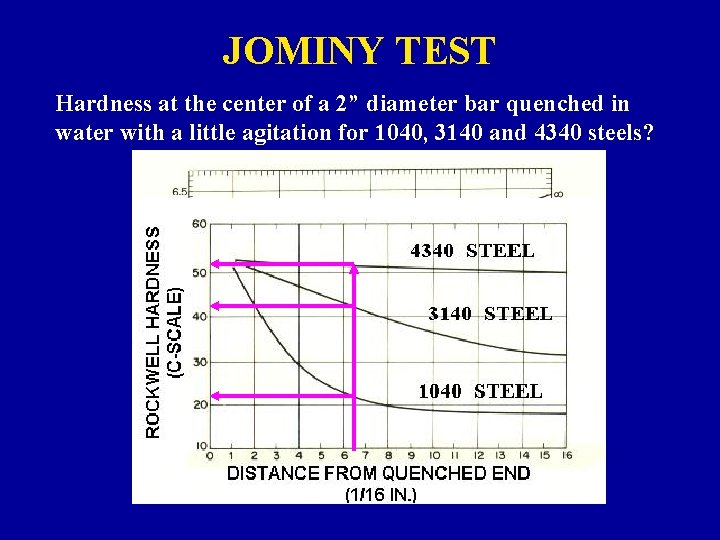
JOMINY TEST Hardness at the center of a 2” diameter bar quenched in water with a little agitation for 1040, 3140 and 4340 steels?
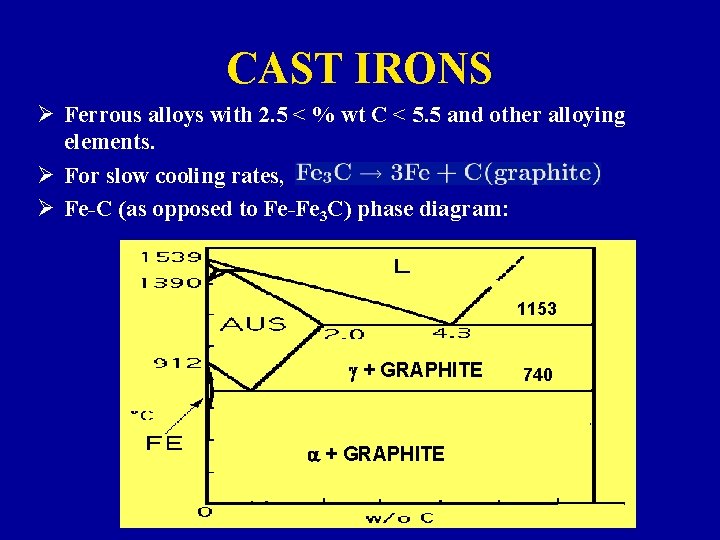
CAST IRONS Ø Ferrous alloys with 2. 5 < % wt C < 5. 5 and other alloying elements. Ø For slow cooling rates, Ø Fe-C (as opposed to Fe-Fe 3 C) phase diagram: 1153 g + GRAPHITE a + GRAPHITE 740
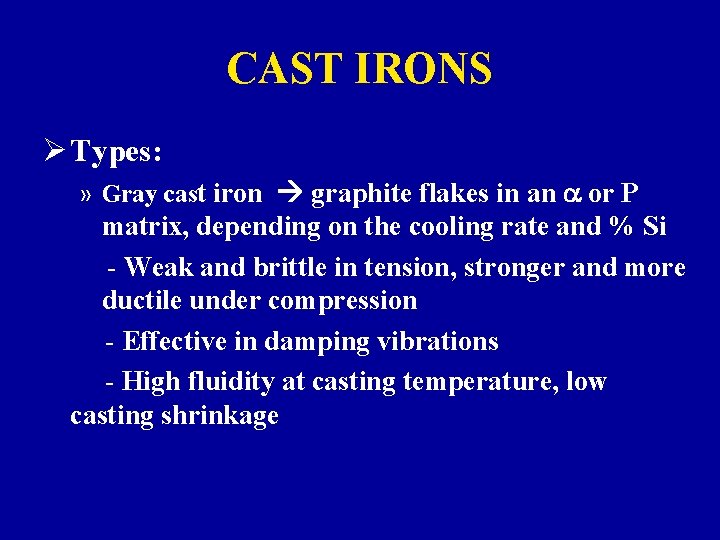
CAST IRONS Ø Types: » Gray cast iron graphite flakes in an a or P matrix, depending on the cooling rate and % Si - Weak and brittle in tension, stronger and more ductile under compression - Effective in damping vibrations - High fluidity at casting temperature, low casting shrinkage
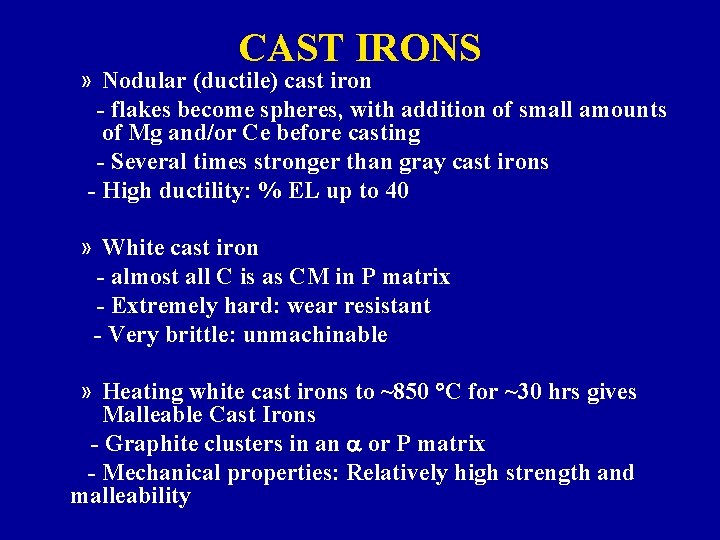
CAST IRONS » Nodular (ductile) cast iron - flakes become spheres, with addition of small amounts of Mg and/or Ce before casting - Several times stronger than gray cast irons - High ductility: % EL up to 40 » White cast iron - almost all C is as CM in P matrix - Extremely hard: wear resistant - Very brittle: unmachinable » Heating white cast irons to ~850 C for ~30 hrs gives Malleable Cast Irons - Graphite clusters in an a or P matrix - Mechanical properties: Relatively high strength and malleability
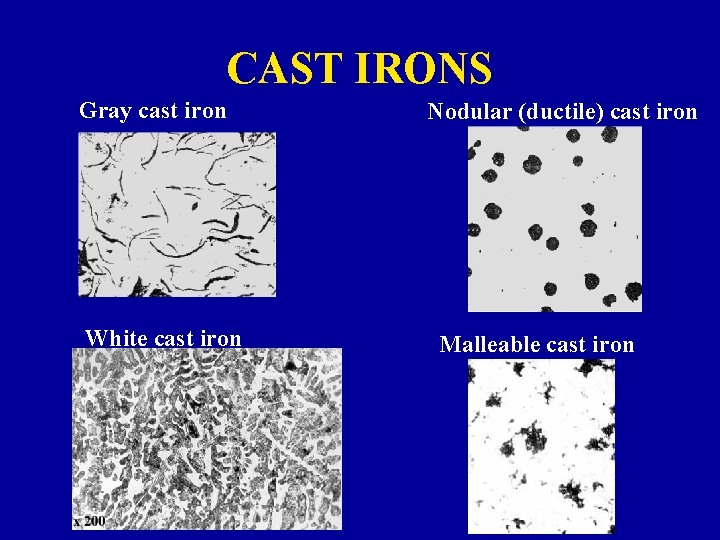
CAST IRONS Gray cast iron White cast iron Nodular (ductile) cast iron Malleable cast iron
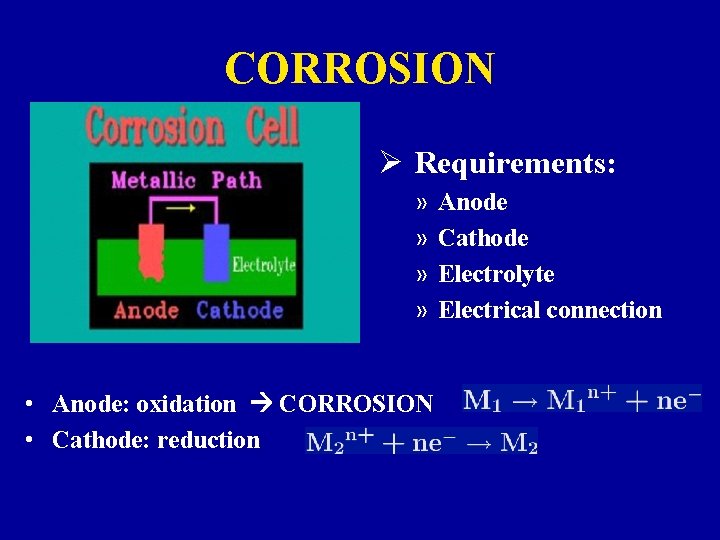
CORROSION Ø Requirements: » » • Anode: oxidation CORROSION • Cathode: reduction Anode Cathode Electrolyte Electrical connection
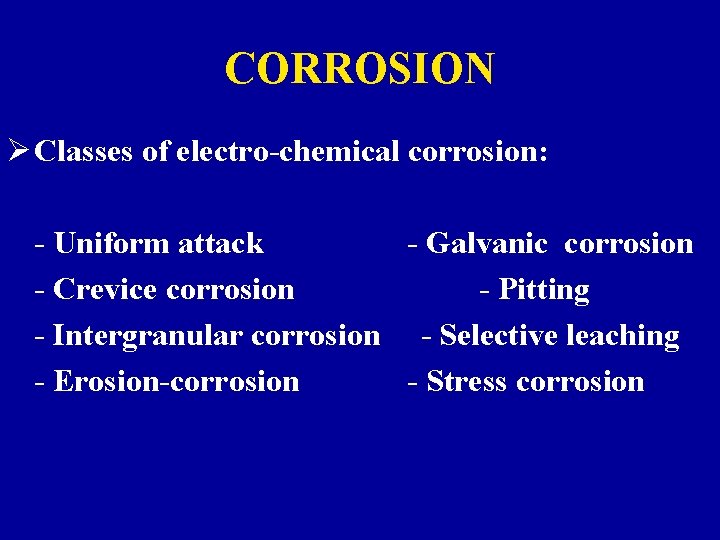
CORROSION Ø Classes of electro-chemical corrosion: - Uniform attack - Galvanic corrosion - Crevice corrosion - Pitting - Intergranular corrosion - Selective leaching - Erosion-corrosion - Stress corrosion
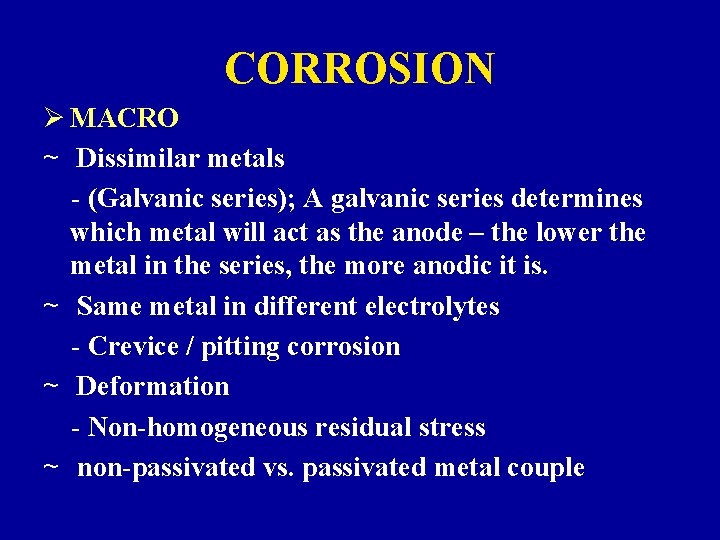
CORROSION Ø MACRO ~ Dissimilar metals - (Galvanic series); A galvanic series determines which metal will act as the anode – the lower the metal in the series, the more anodic it is. ~ Same metal in different electrolytes - Crevice / pitting corrosion ~ Deformation - Non-homogeneous residual stress ~ non-passivated vs. passivated metal couple
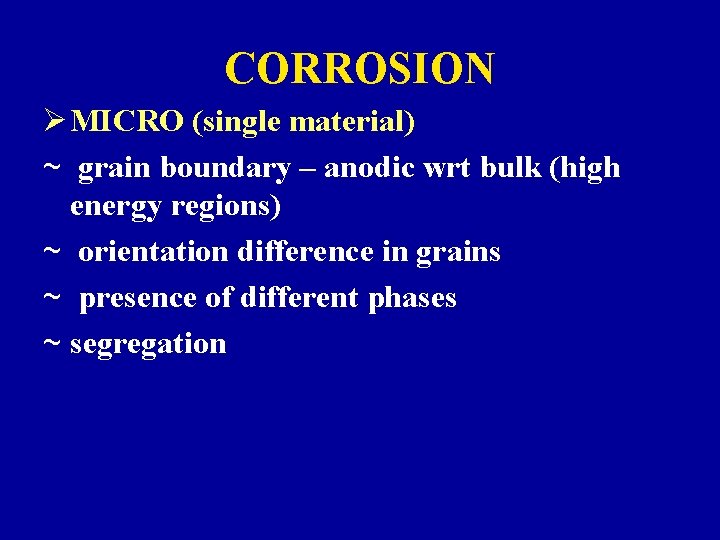
CORROSION Ø MICRO (single material) ~ grain boundary – anodic wrt bulk (high energy regions) ~ orientation difference in grains ~ presence of different phases ~ segregation
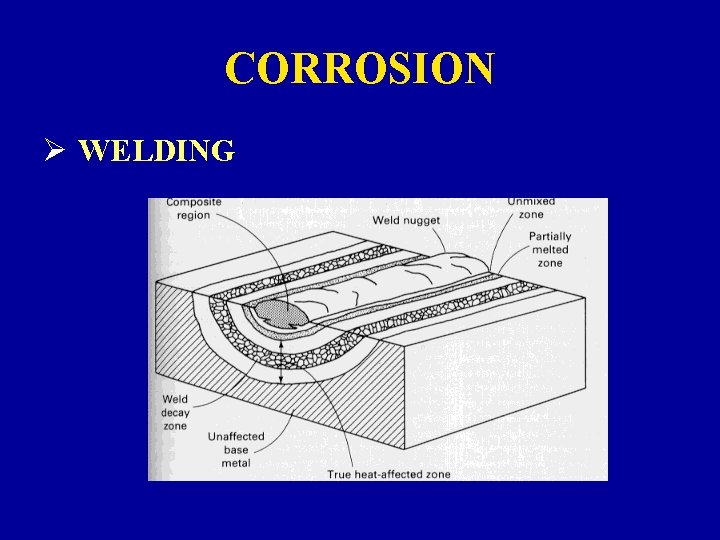
CORROSION Ø WELDING
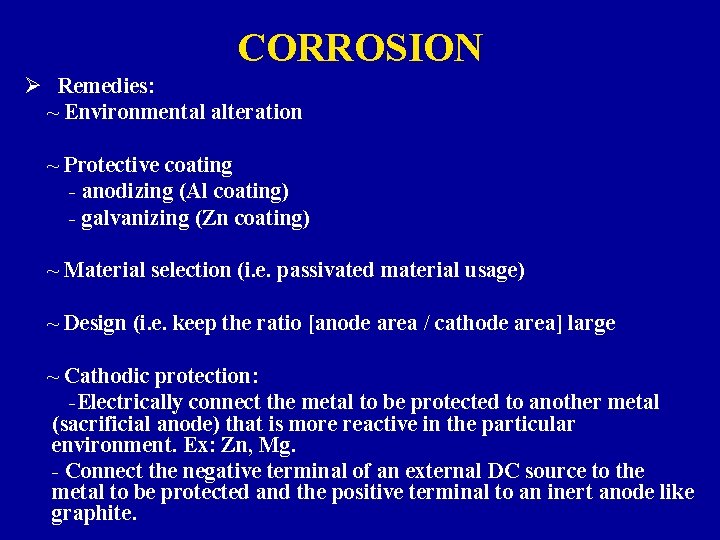
CORROSION Ø Remedies: ~ Environmental alteration ~ Protective coating - anodizing (Al coating) - galvanizing (Zn coating) ~ Material selection (i. e. passivated material usage) ~ Design (i. e. keep the ratio [anode area / cathode area] large ~ Cathodic protection: -Electrically connect the metal to be protected to another metal (sacrificial anode) that is more reactive in the particular environment. Ex: Zn, Mg. - Connect the negative terminal of an external DC source to the metal to be protected and the positive terminal to an inert anode like graphite.
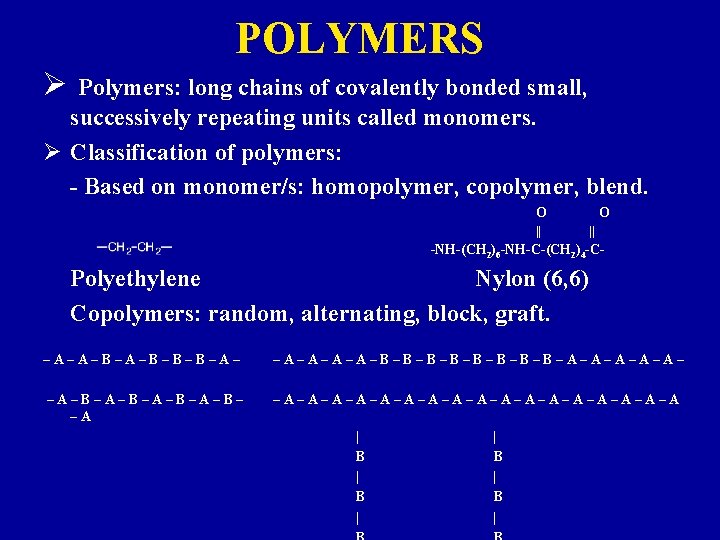
POLYMERS Ø Polymers: long chains of covalently bonded small, successively repeating units called monomers. Ø Classification of polymers: - Based on monomer/s: homopolymer, copolymer, blend. O || -NH-(CH 2)6 -NH-C-(CH 2)4 -C- Polyethylene Nylon (6, 6) Copolymers: random, alternating, block, graft. –A–A–B–B–B–A– –A–A–B–B–B–B–A–A–A– –A–B–A–B– –A –A–A–A–A–A–A–A–A–A | B | B |
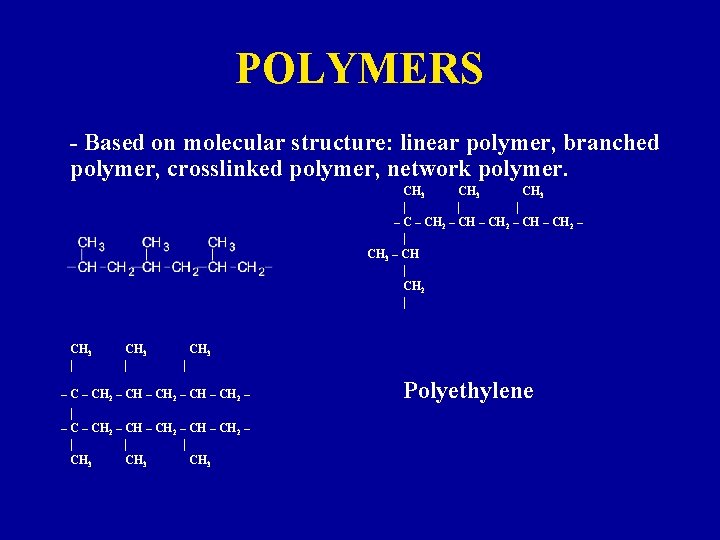
POLYMERS - Based on molecular structure: linear polymer, branched polymer, crosslinked polymer, network polymer. CH 3 | | | – CH 2 – CH 2 – | CH 3 – CH | CH 2 | CH 3 | – C – CH 2 – CH – CH 2 – | | | CH 3 Polyethylene
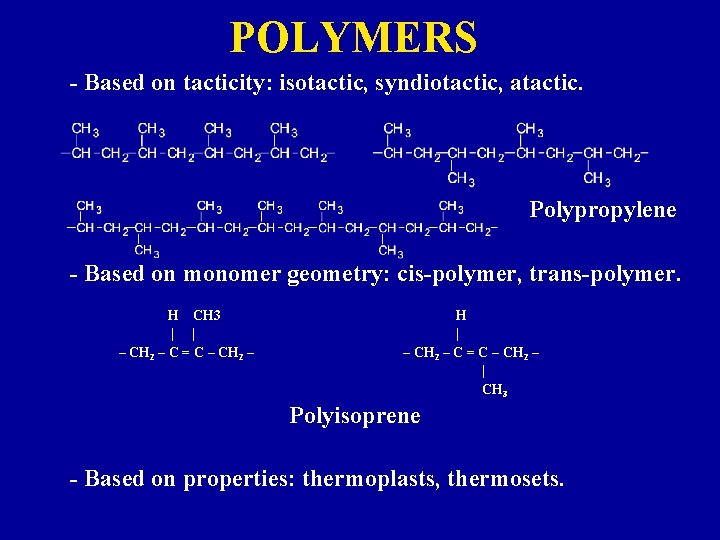
POLYMERS - Based on tacticity: isotactic, syndiotactic, atactic. Polypropylene - Based on monomer geometry: cis-polymer, trans-polymer. H CH 3 | | – CH 2 – C = C – CH 2 – H | – CH 2 – C = C – CH 2 – | CH 3 Polyisoprene - Based on properties: thermoplasts, thermosets.
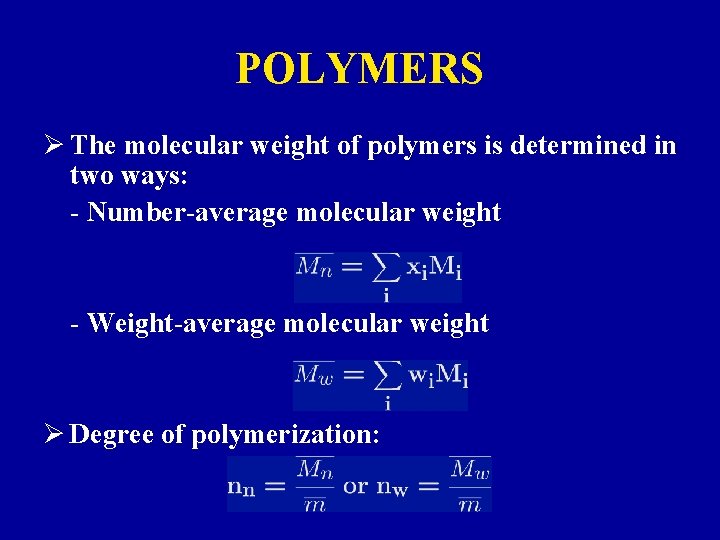
POLYMERS Ø The molecular weight of polymers is determined in two ways: - Number-average molecular weight - Weight-average molecular weight Ø Degree of polymerization:
Uncontrollable spending ap gov
Usd259 portal
Omis 259
Homework 259
Geoffrey tien ubc
Physics 259
Asw-259
Rapidity usd 259
Sccs library
Srmnea
Hkn review session
Hkn review session
Hkn review session
Ece 329 uiuc
Ece 329
Ece391
Uiuc ece 329
Chapter review motion part a vocabulary review answer key
Narrative review vs systematic review
Systematic review definition
Narrative review vs systematic review