Managing Finance in a Digital World Chapter 9
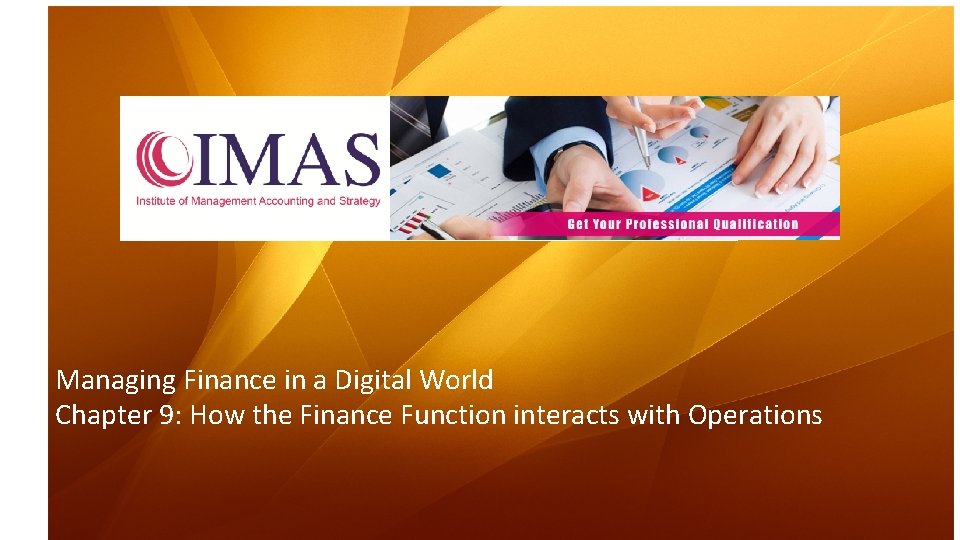
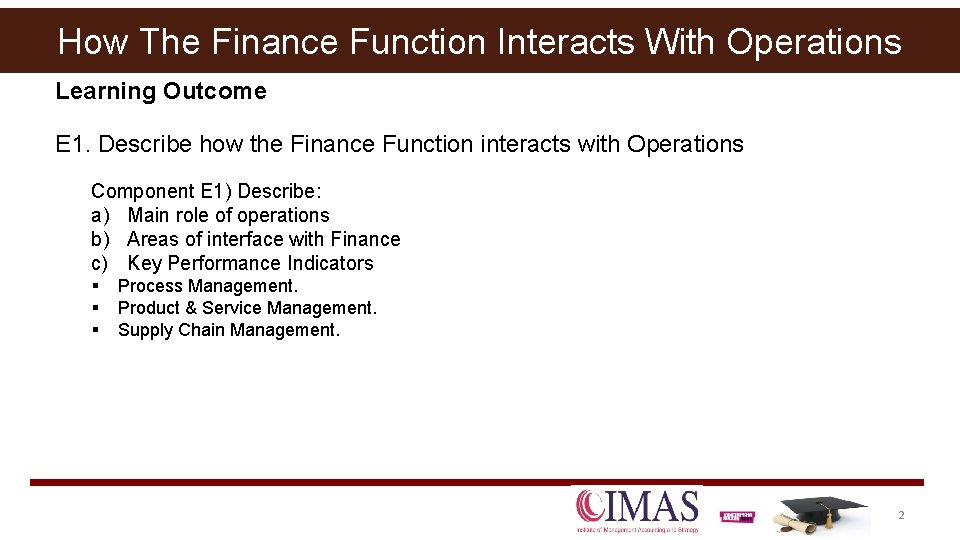
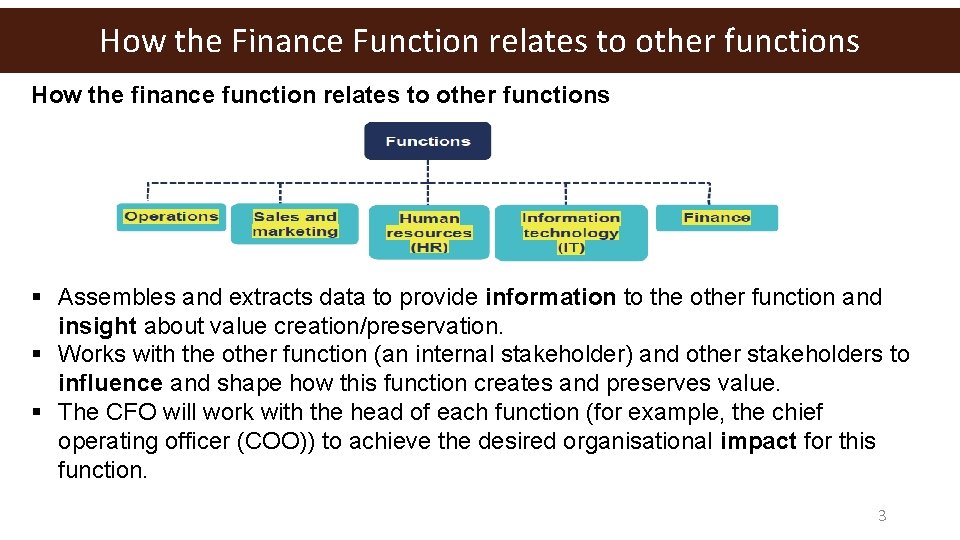
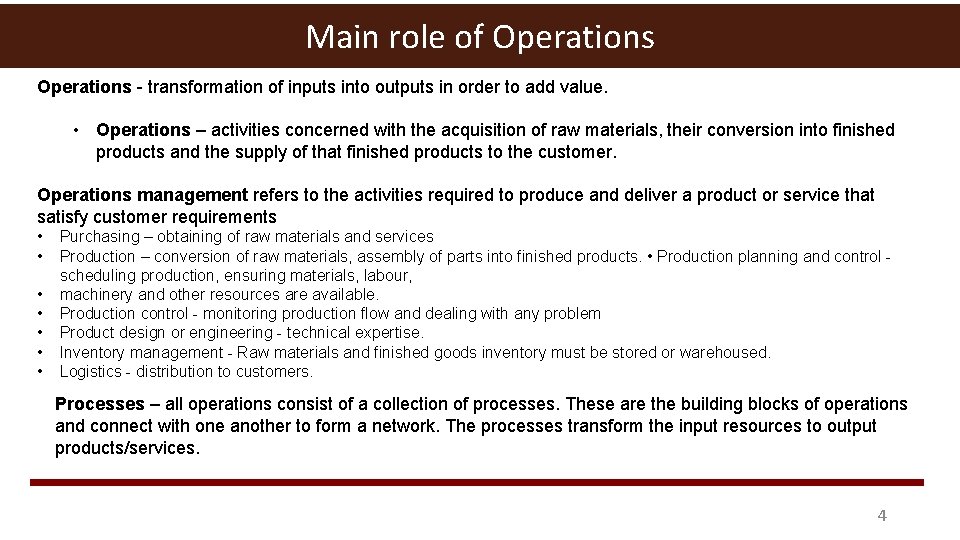
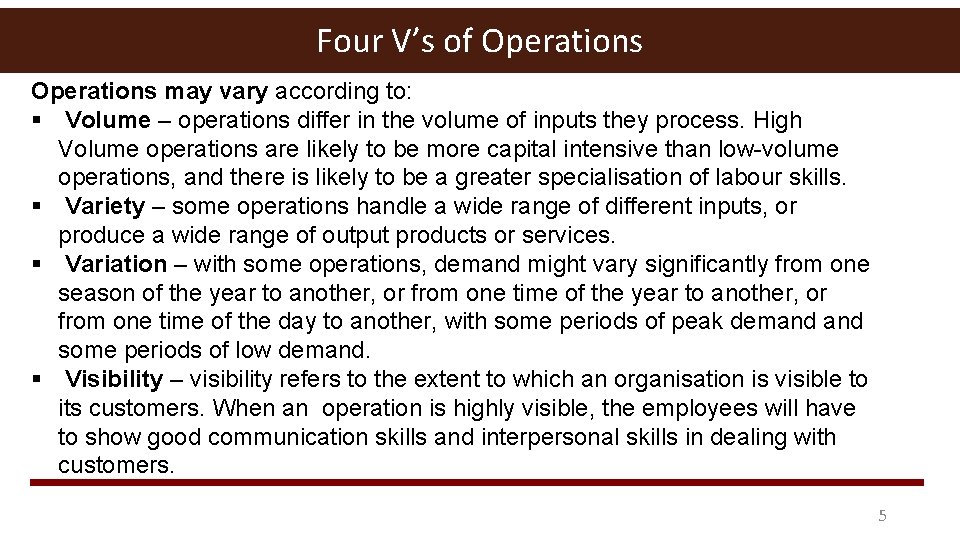
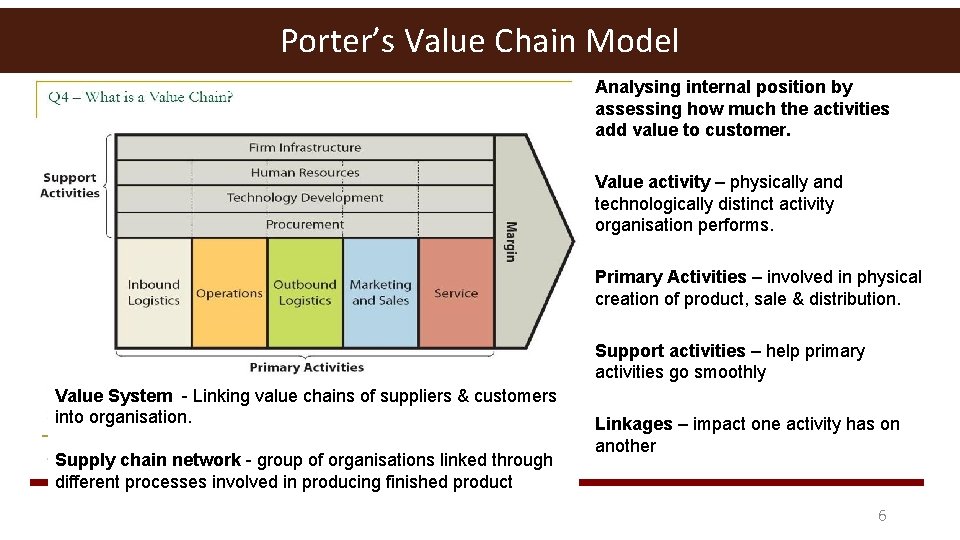
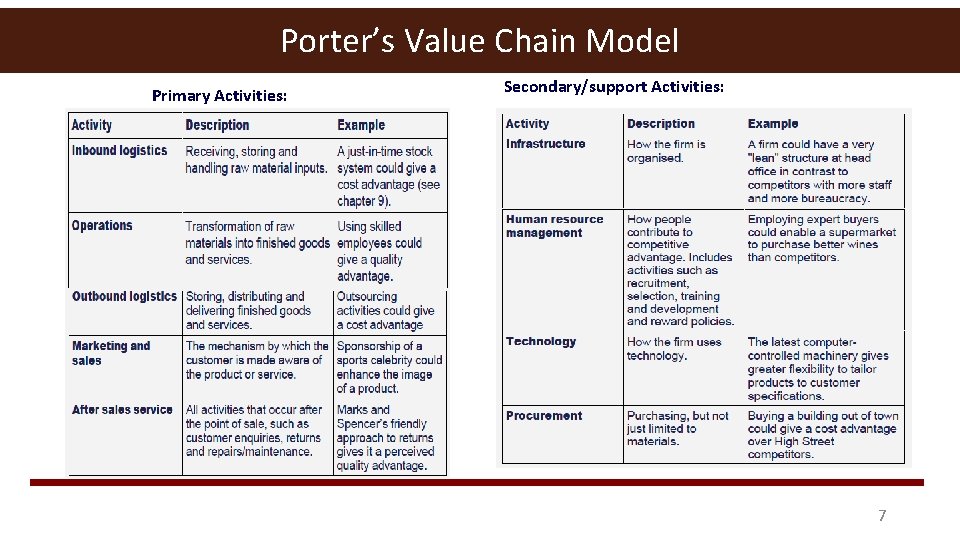
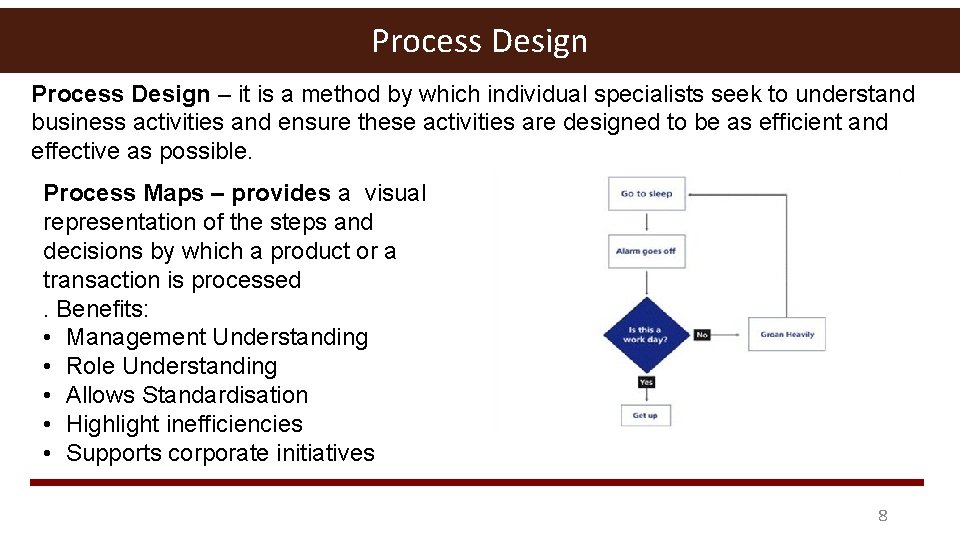
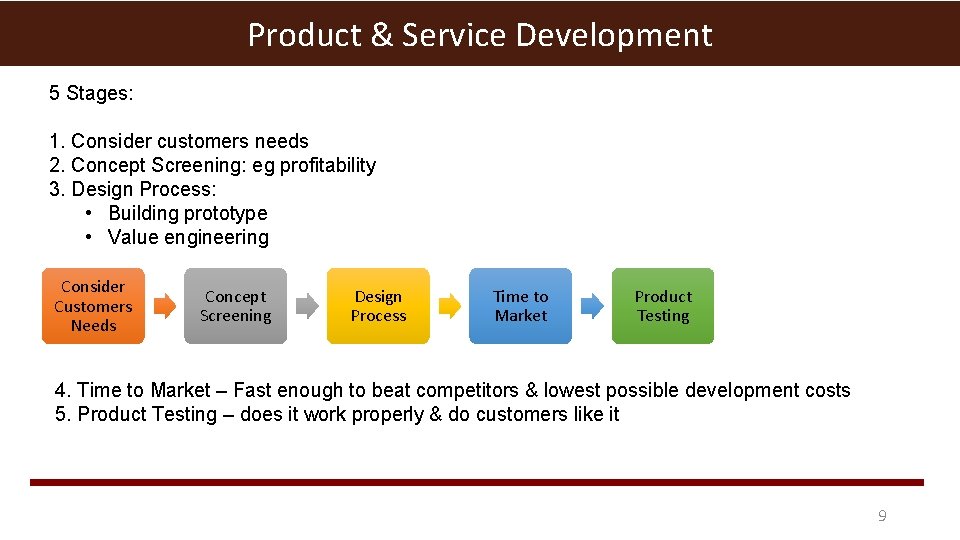
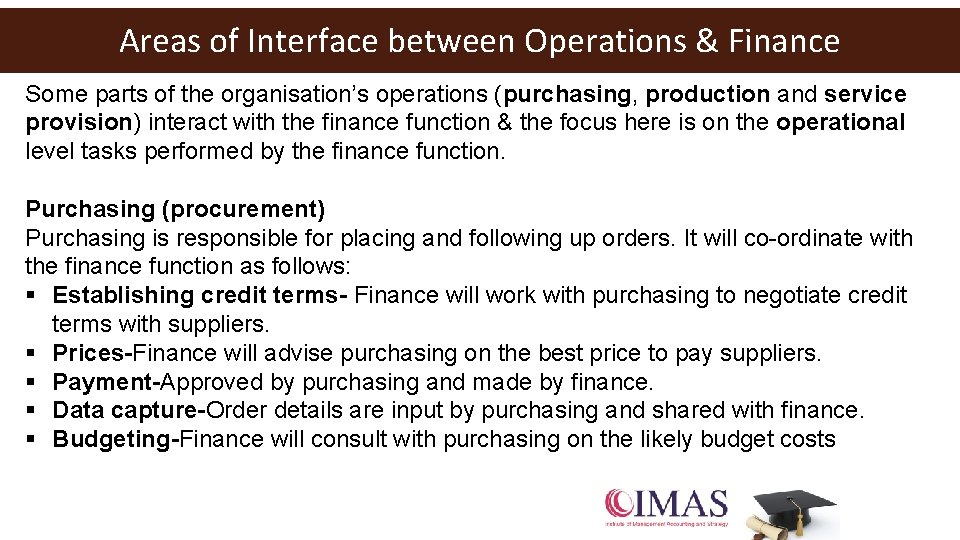
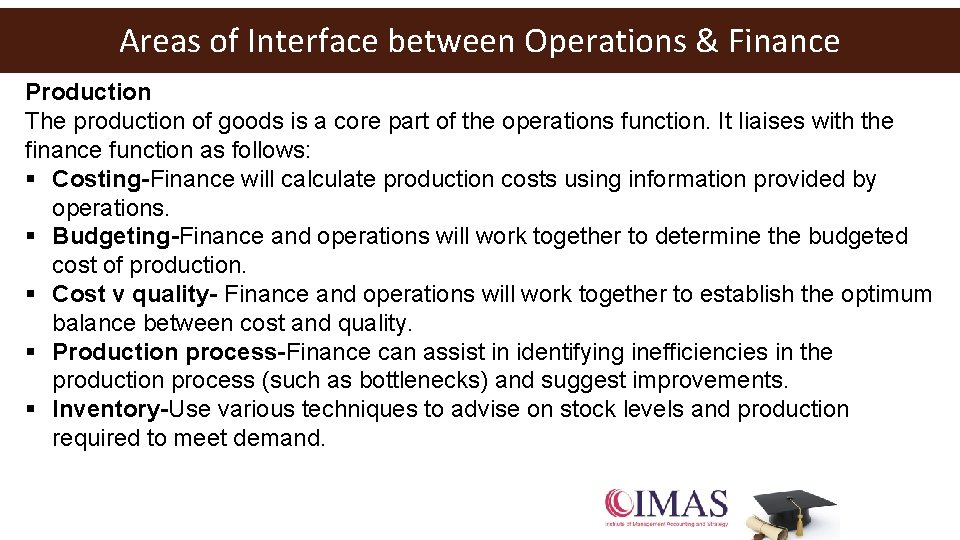
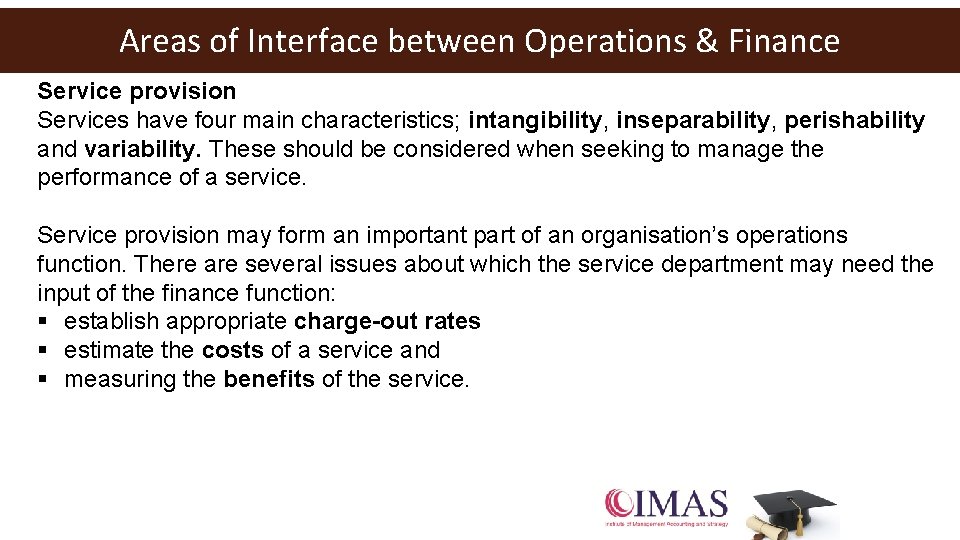
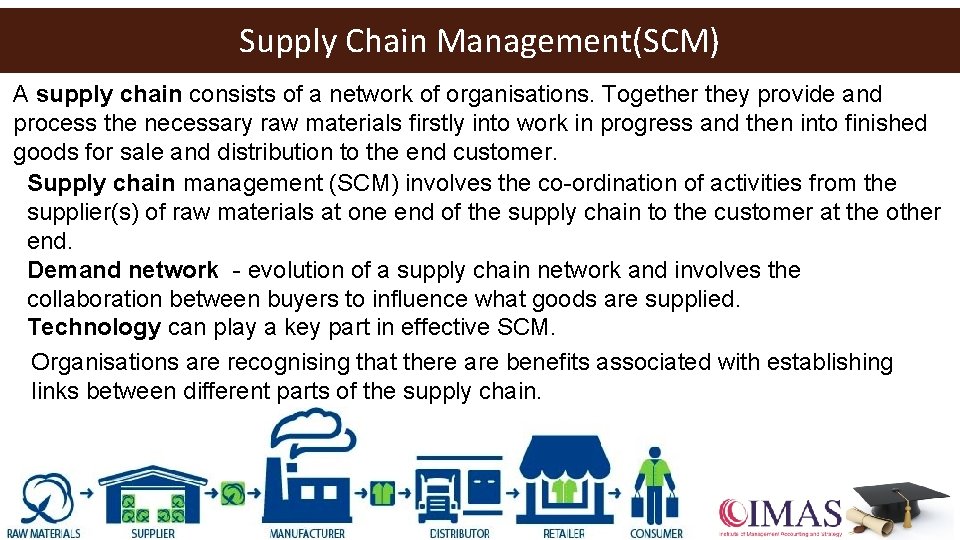
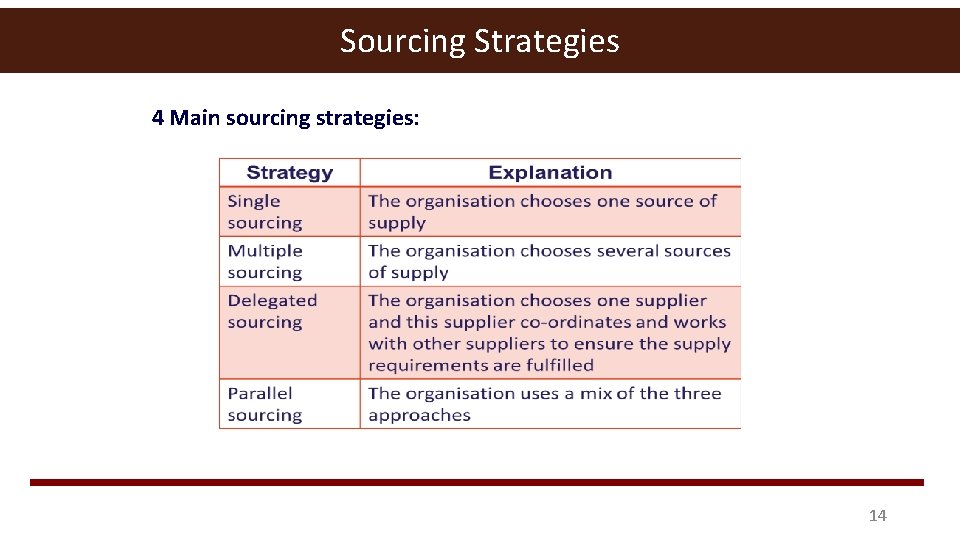
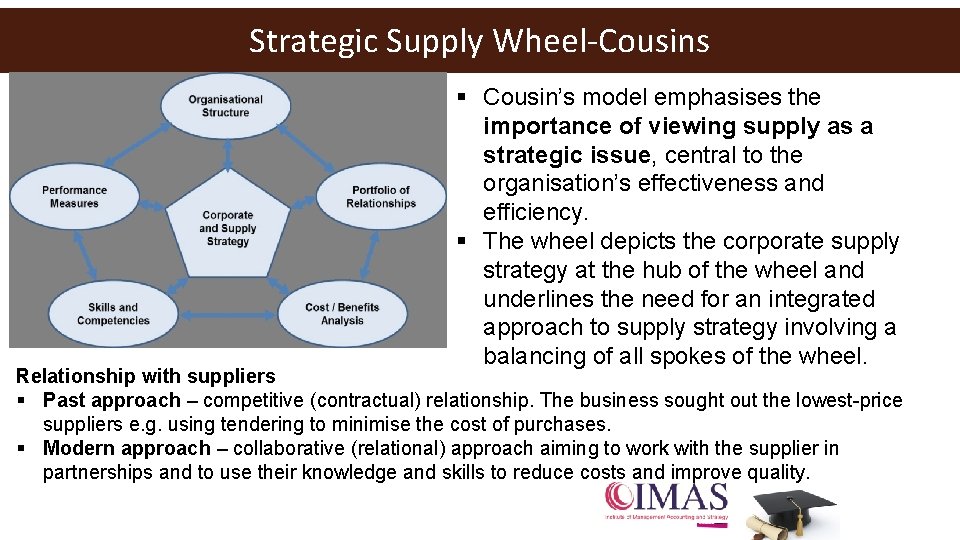
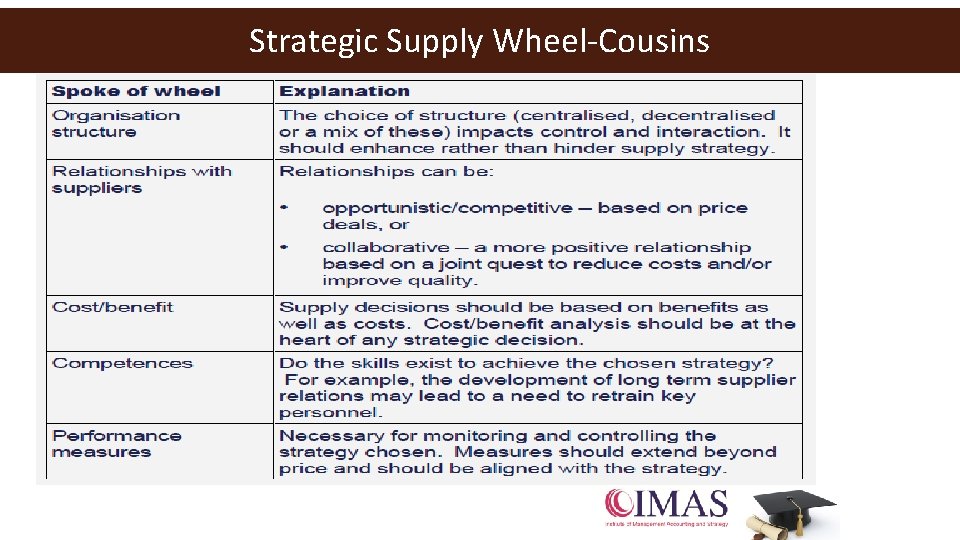
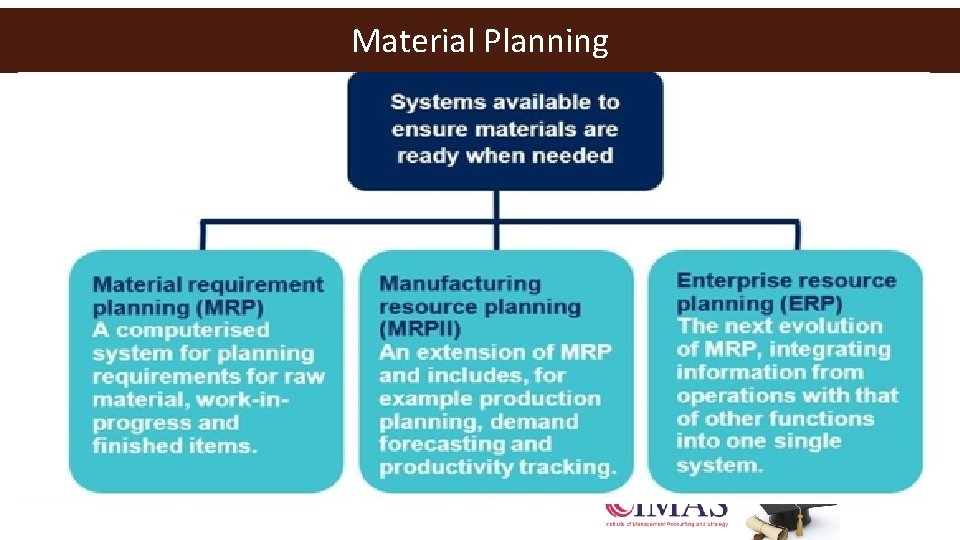
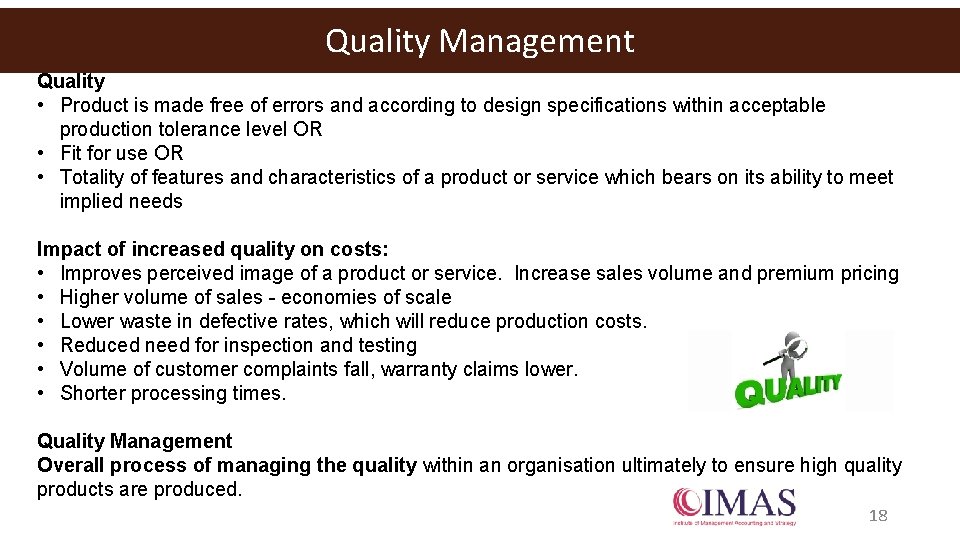
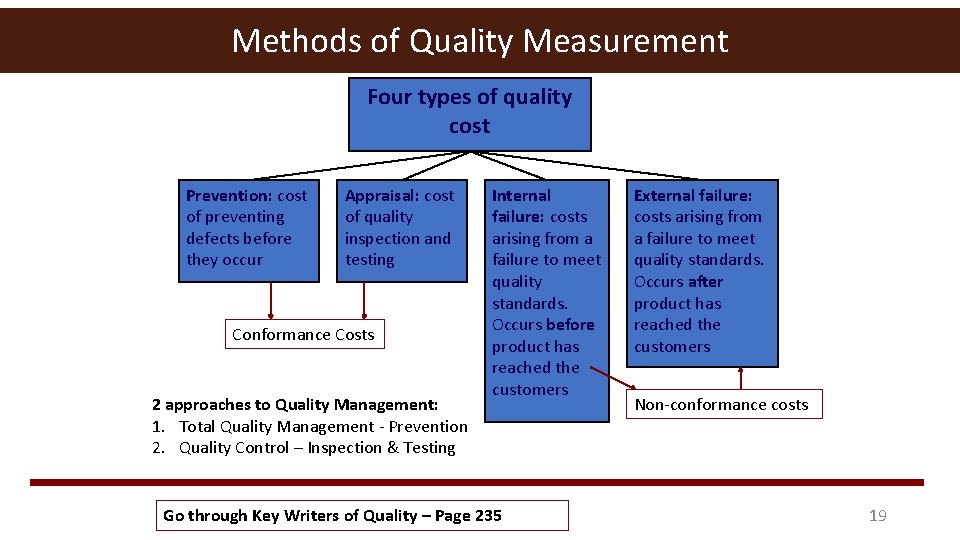
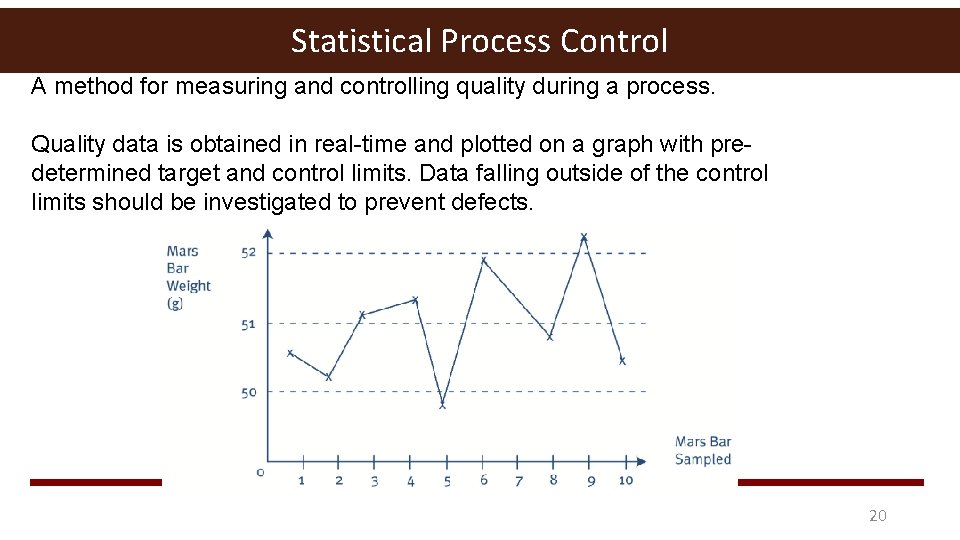
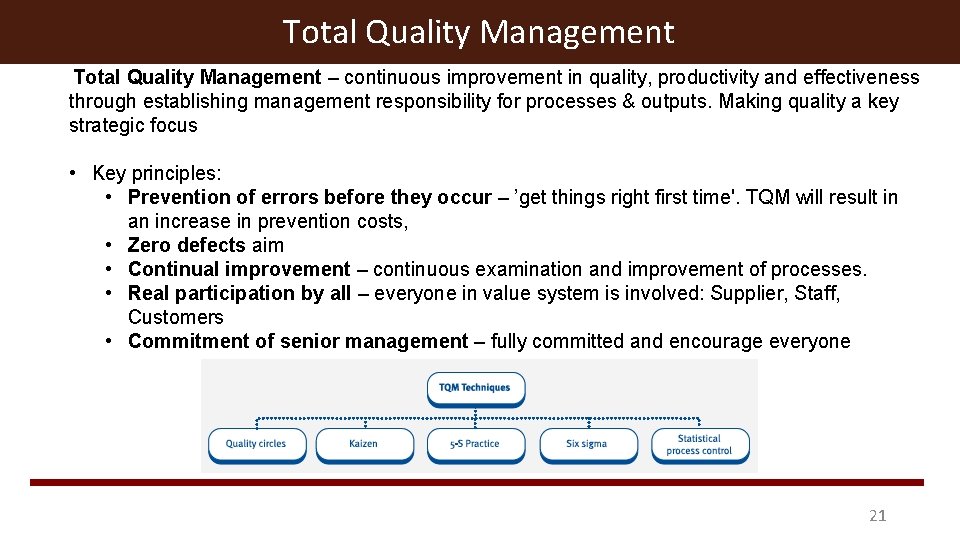
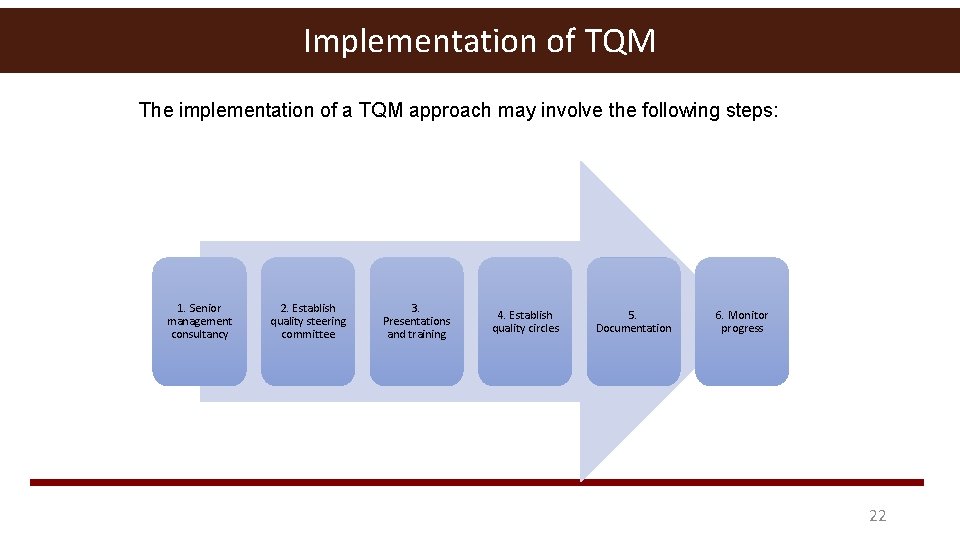
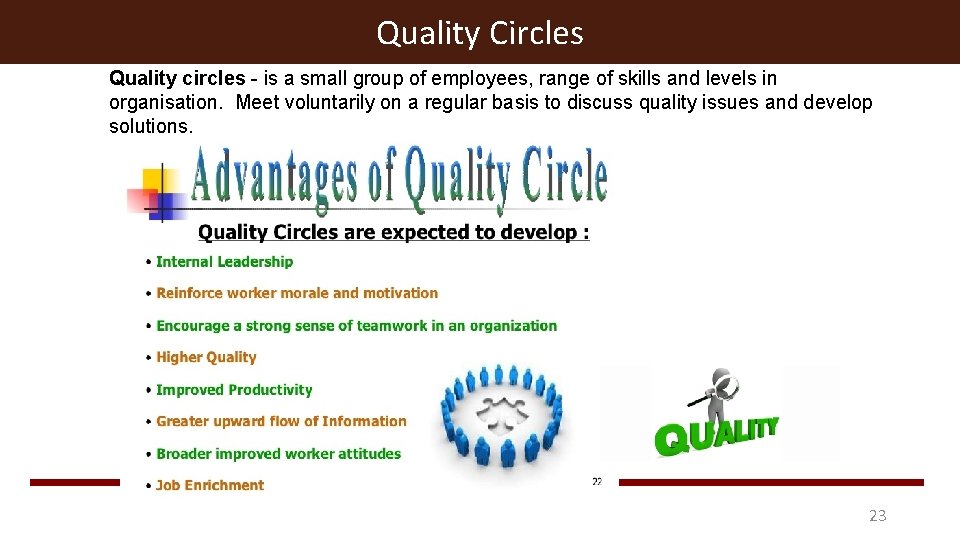
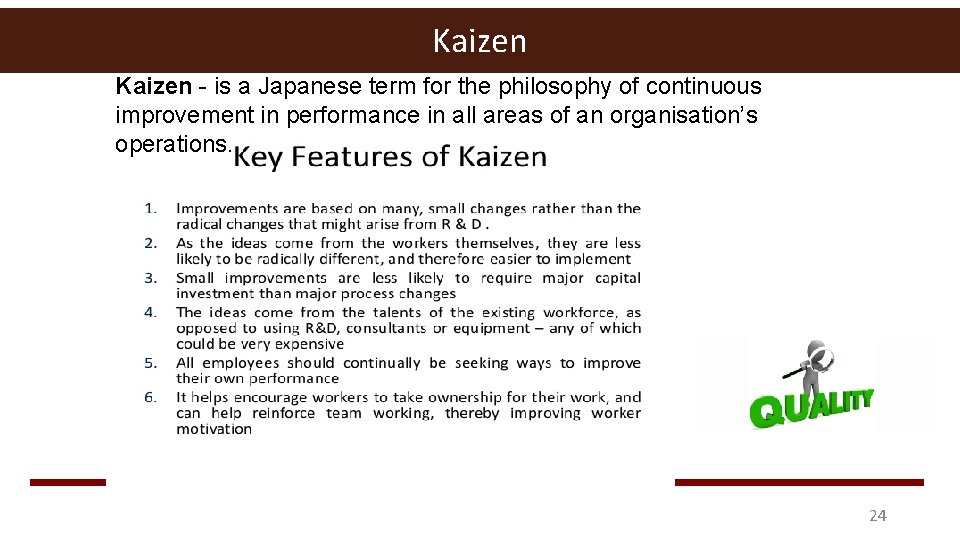
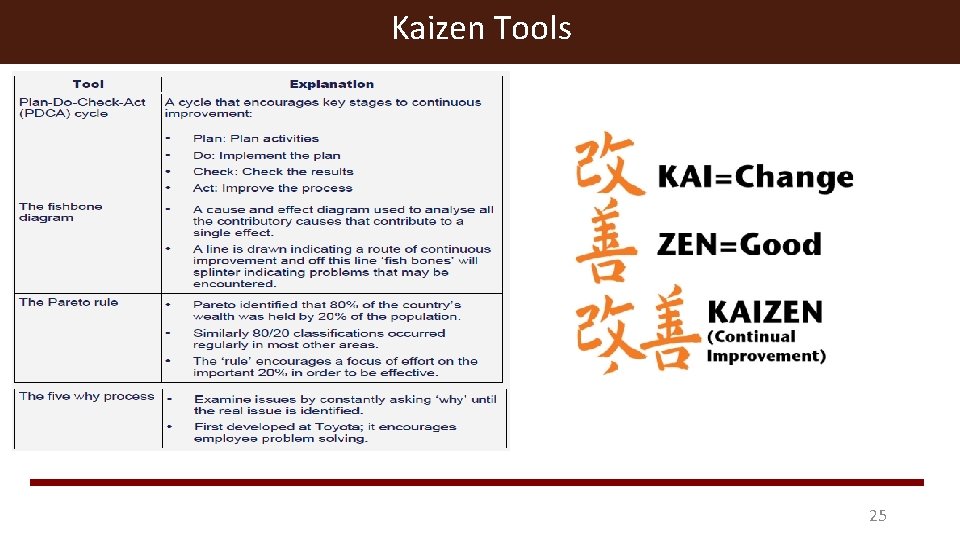
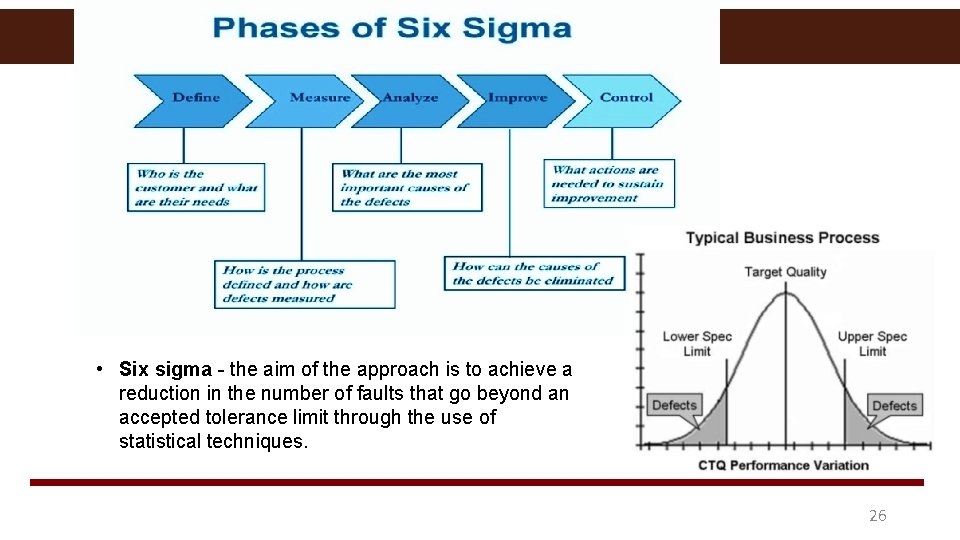
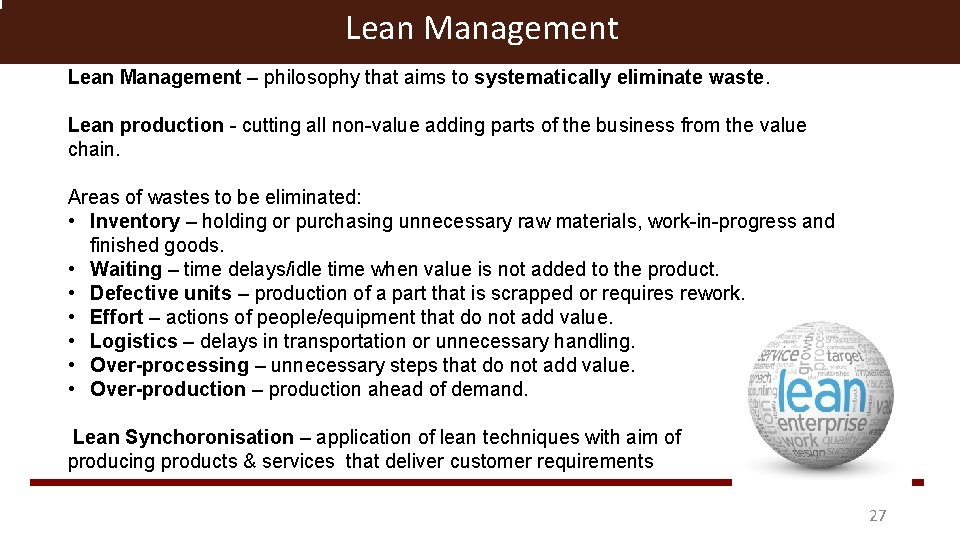
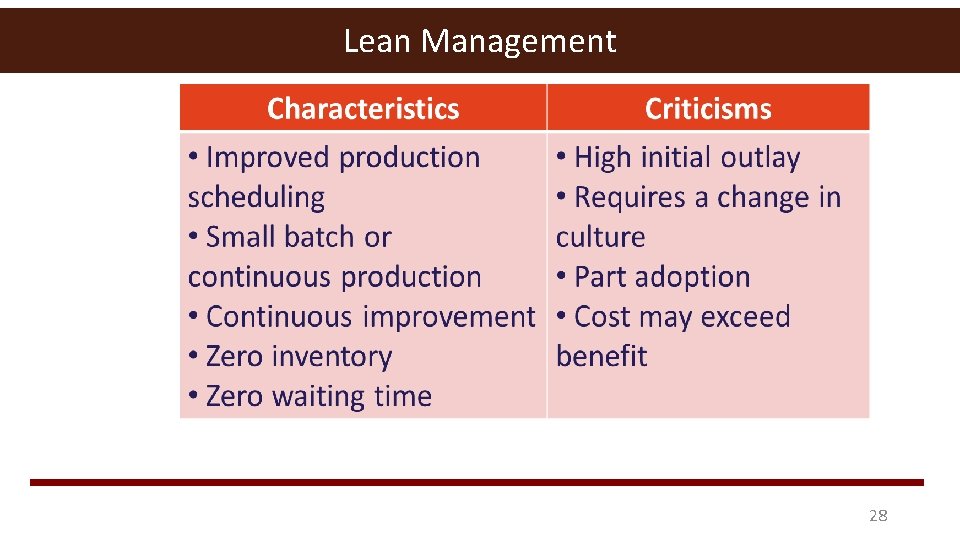
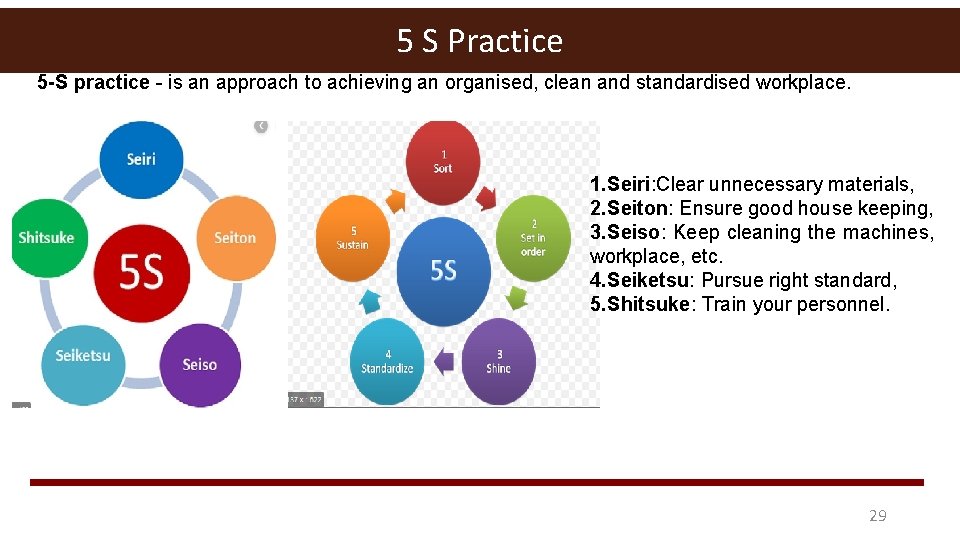
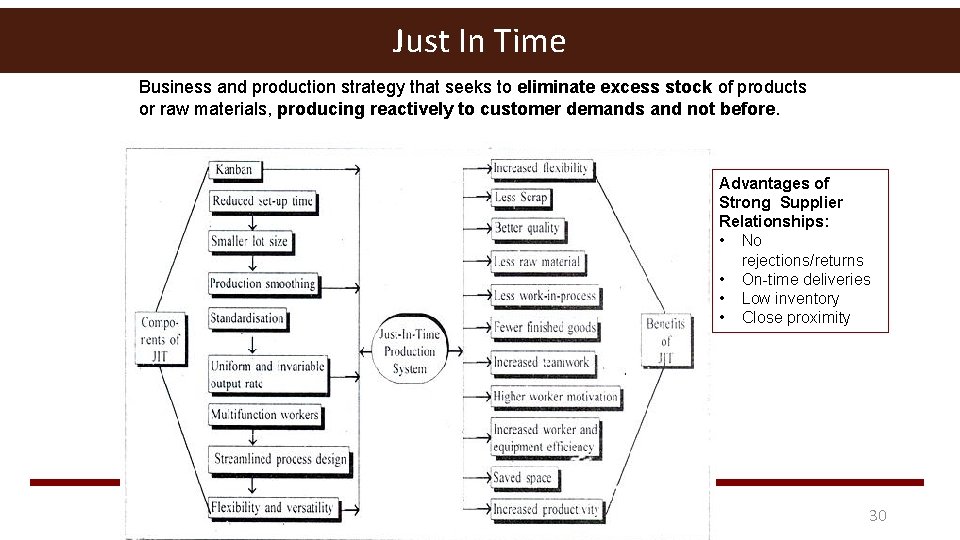
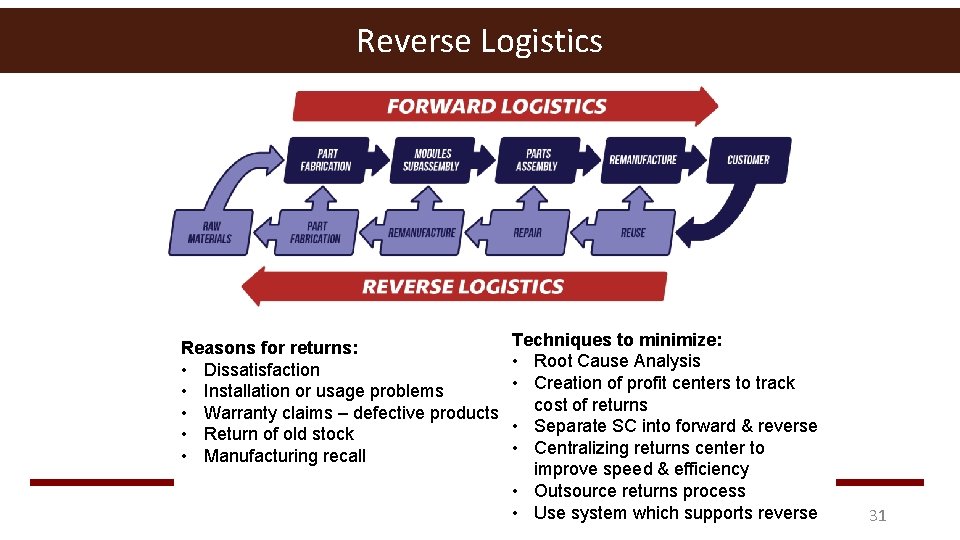
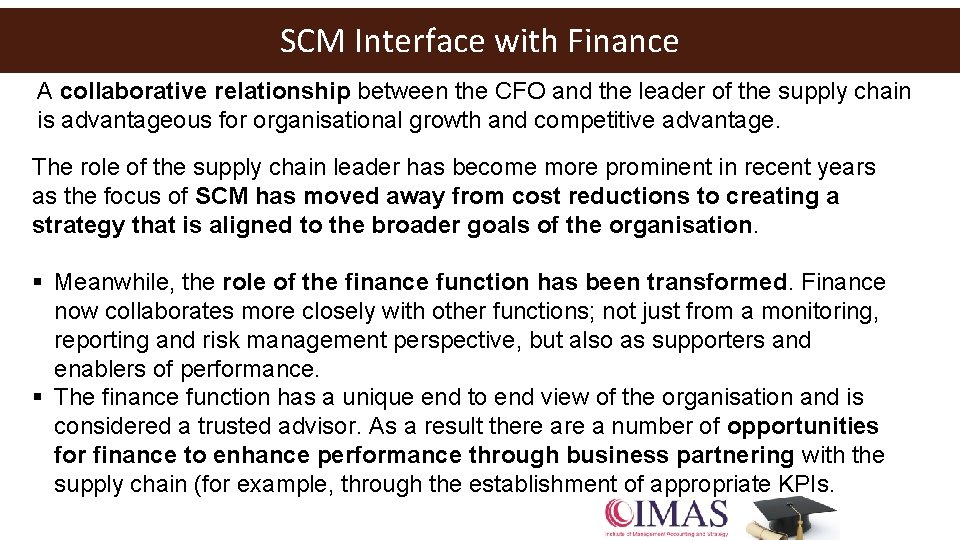
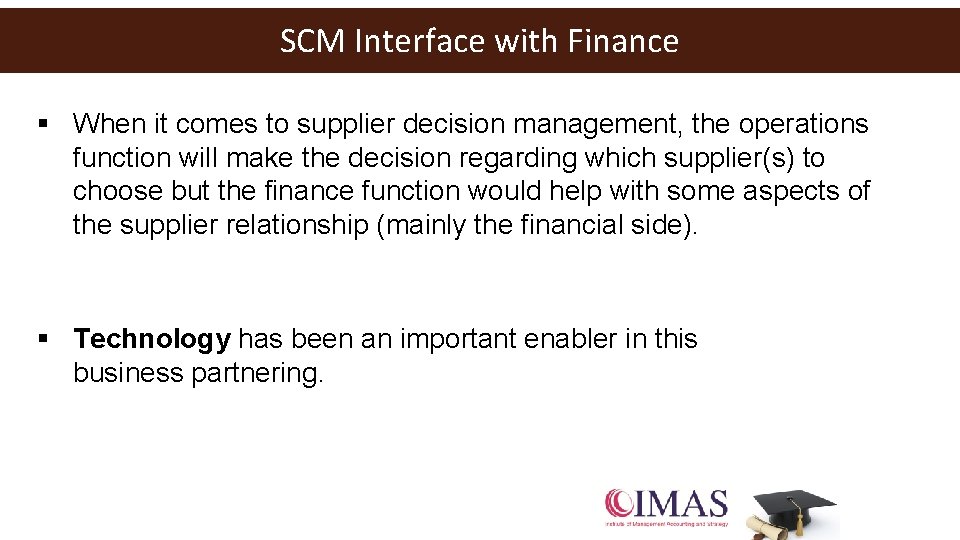
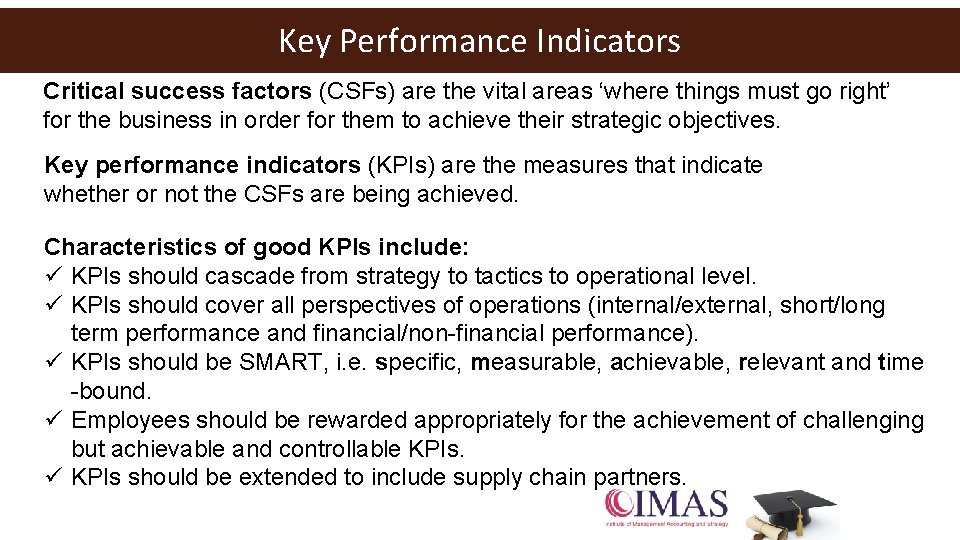
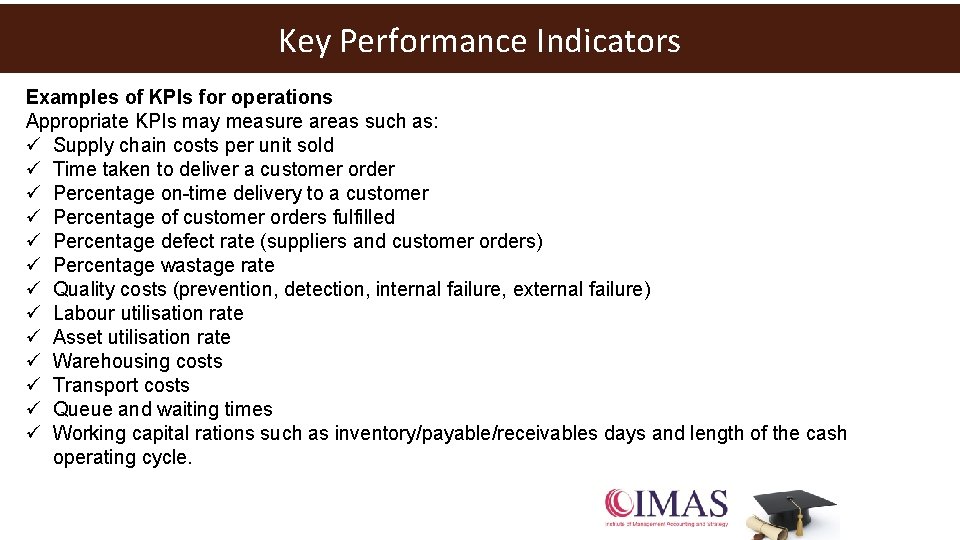
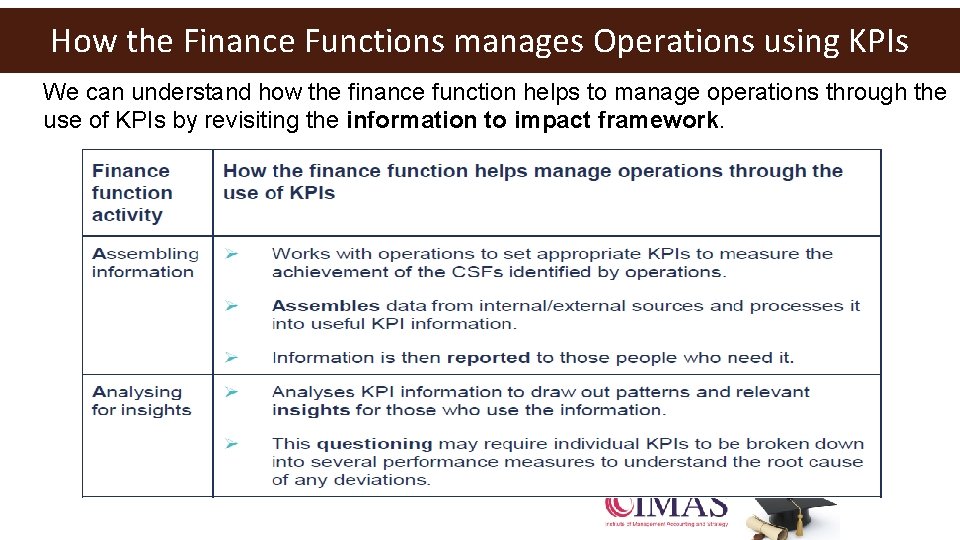
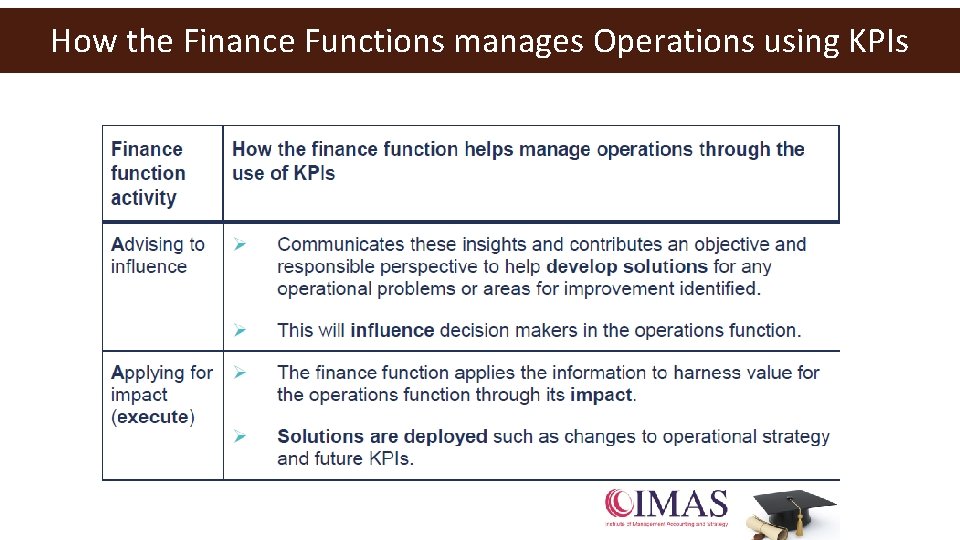
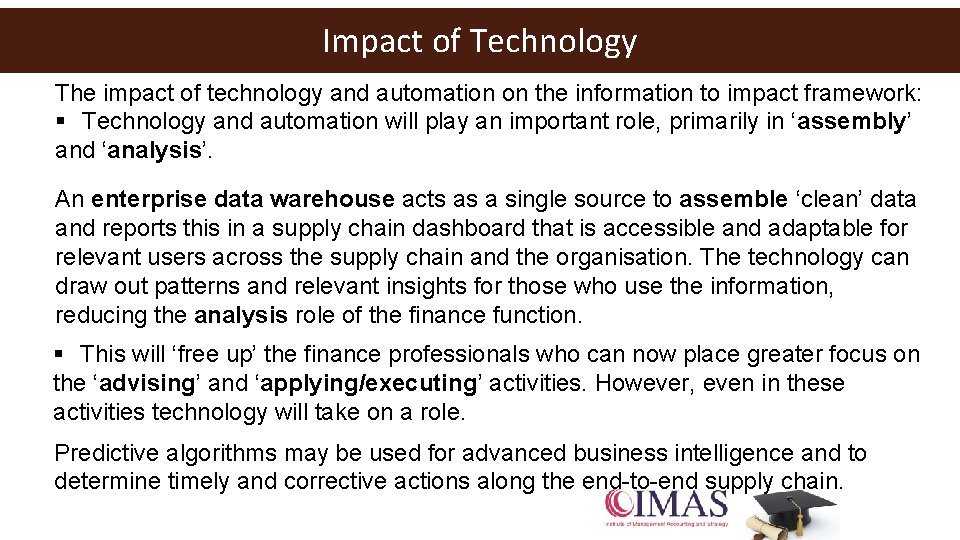
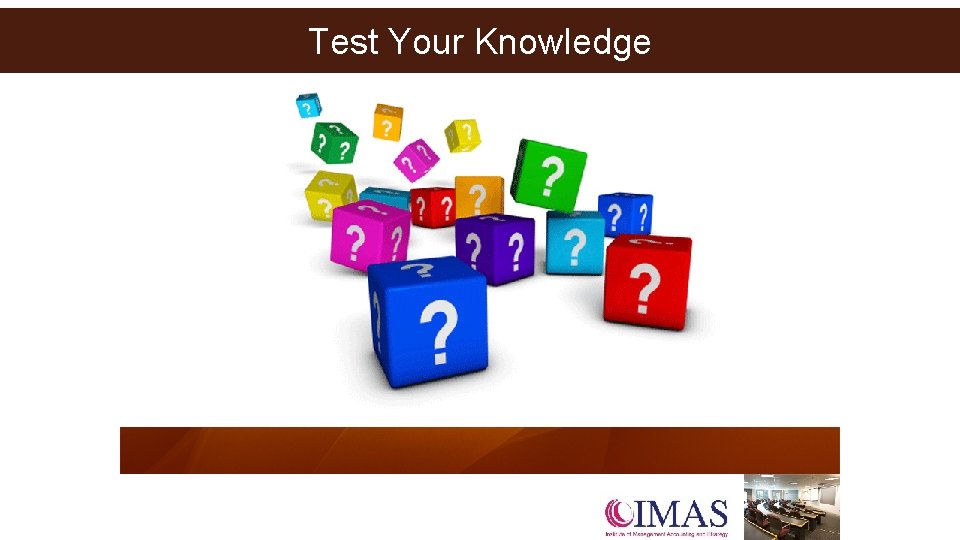
- Slides: 39
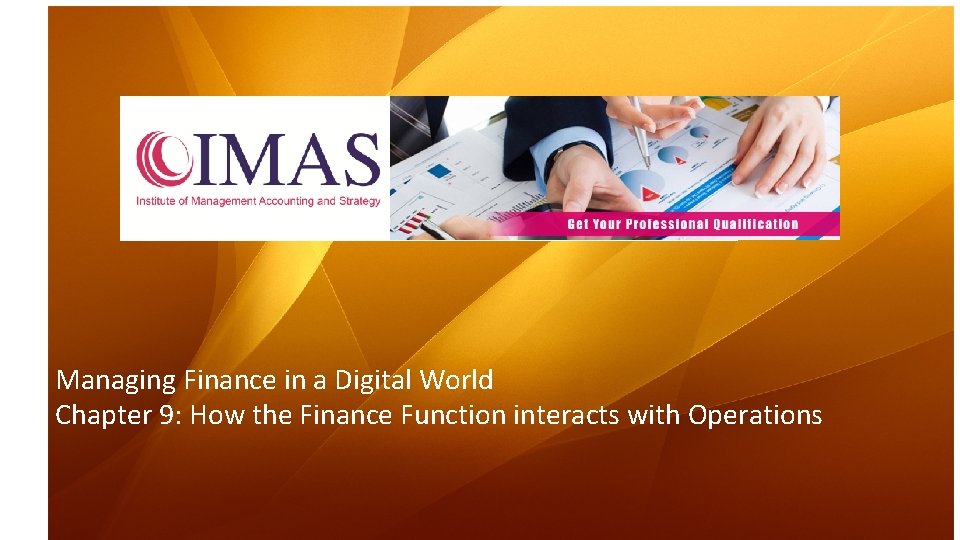
Managing Finance in a Digital World Chapter 9: How the Finance Function interacts with Operations
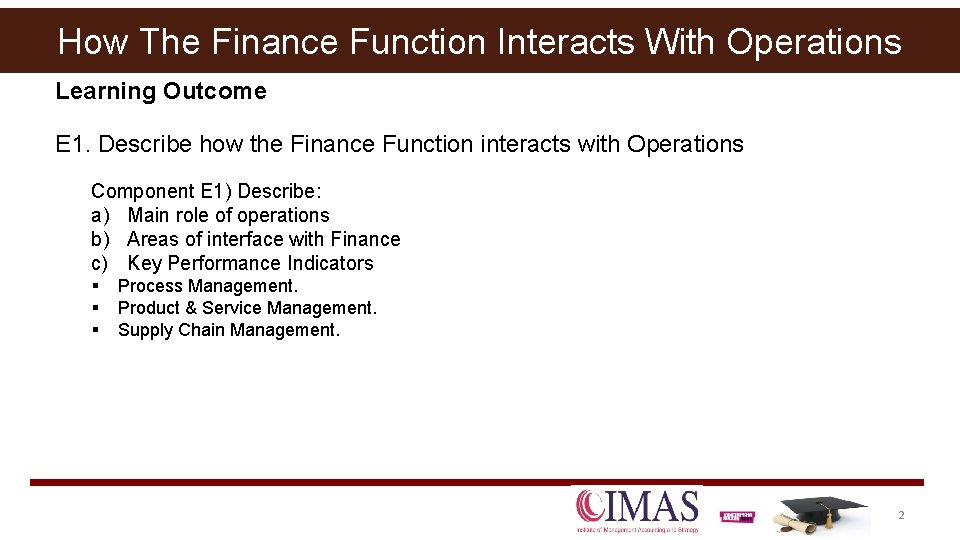
How The Finance Function Interacts With Operations Learning Outcome E 1. Describe how the Finance Function interacts with Operations Component E 1) Describe: a) Main role of operations b) Areas of interface with Finance c) Key Performance Indicators § § § Process Management. Product & Service Management. Supply Chain Management. 2
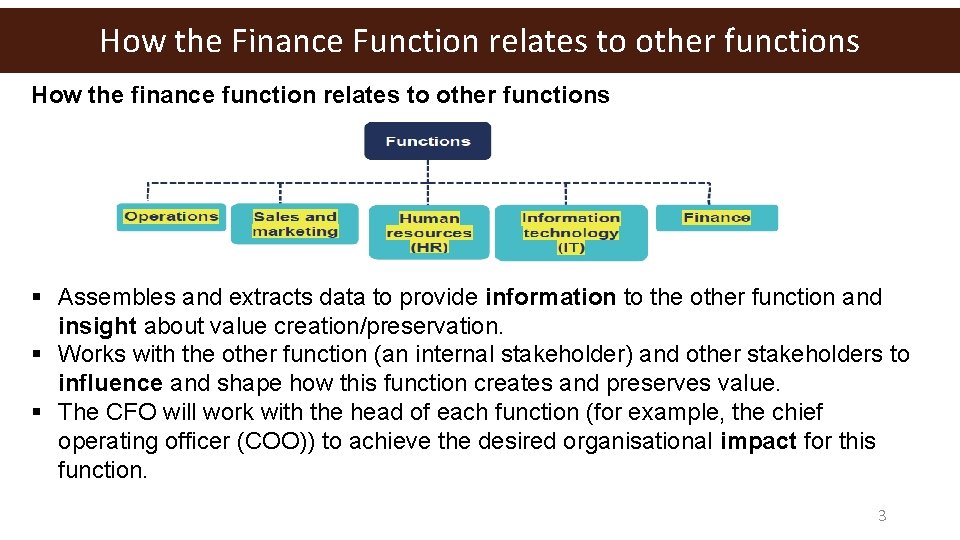
How the Finance Function relates to other functions How the finance function relates to other functions § Assembles and extracts data to provide information to the other function and insight about value creation/preservation. § Works with the other function (an internal stakeholder) and other stakeholders to influence and shape how this function creates and preserves value. § The CFO will work with the head of each function (for example, the chief operating officer (COO)) to achieve the desired organisational impact for this function. 3
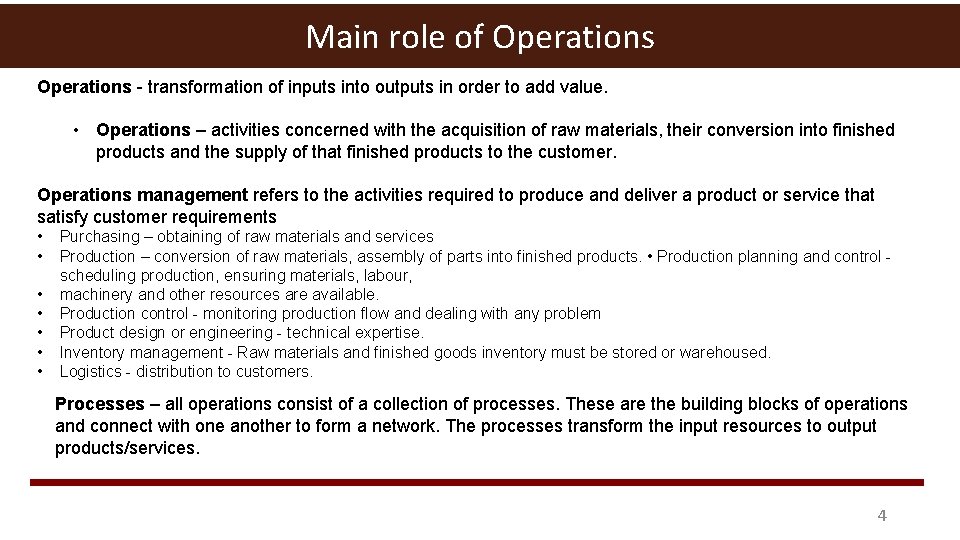
Main role of Operations - transformation of inputs into outputs in order to add value. • Operations – activities concerned with the acquisition of raw materials, their conversion into finished products and the supply of that finished products to the customer. Operations management refers to the activities required to produce and deliver a product or service that satisfy customer requirements • • Purchasing – obtaining of raw materials and services Production – conversion of raw materials, assembly of parts into finished products. • Production planning and control scheduling production, ensuring materials, labour, machinery and other resources are available. Production control - monitoring production flow and dealing with any problem Product design or engineering - technical expertise. Inventory management - Raw materials and finished goods inventory must be stored or warehoused. Logistics - distribution to customers. Processes – all operations consist of a collection of processes. These are the building blocks of operations and connect with one another to form a network. The processes transform the input resources to output products/services. 4
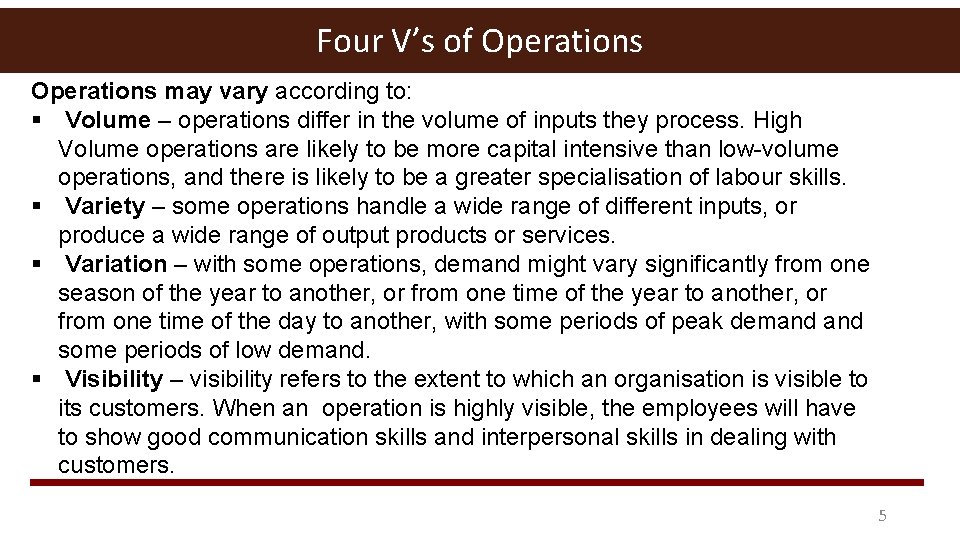
Four V’s of Four of Operations may vary according to: § Volume – operations differ in the volume of inputs they process. High Volume operations are likely to be more capital intensive than low-volume operations, and there is likely to be a greater specialisation of labour skills. § Variety – some operations handle a wide range of different inputs, or produce a wide range of output products or services. § Variation – with some operations, demand might vary significantly from one season of the year to another, or from one time of the day to another, with some periods of peak demand some periods of low demand. § Visibility – visibility refers to the extent to which an organisation is visible to its customers. When an operation is highly visible, the employees will have to show good communication skills and interpersonal skills in dealing with customers. 5
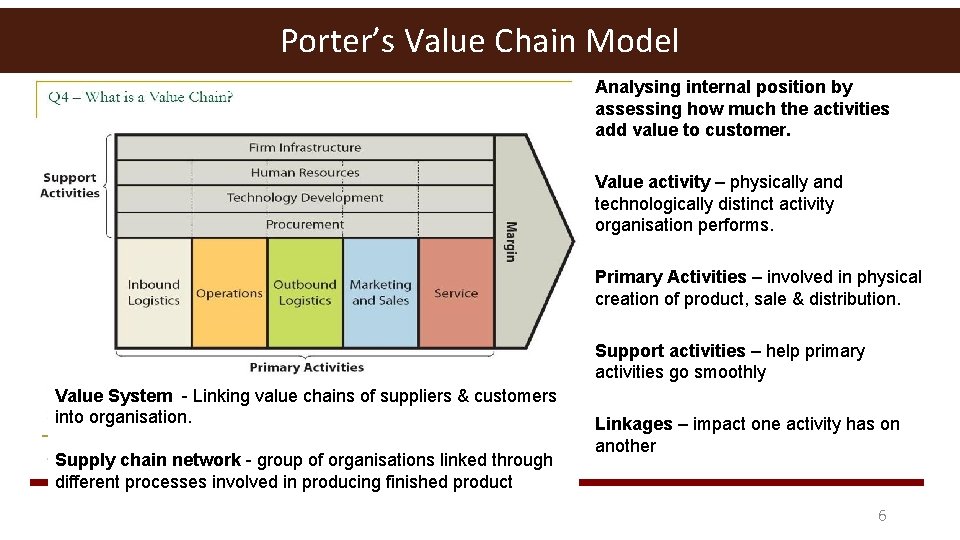
Porter’s Value Chain Model Analysing internal position by assessing how much the activities add value to customer. Value activity – physically and technologically distinct activity organisation performs. Primary Activities – involved in physical creation of product, sale & distribution. Support activities – help primary activities go smoothly Value System - Linking value chains of suppliers & customers into organisation. Supply chain network - group of organisations linked through different processes involved in producing finished product Linkages – impact one activity has on another 6
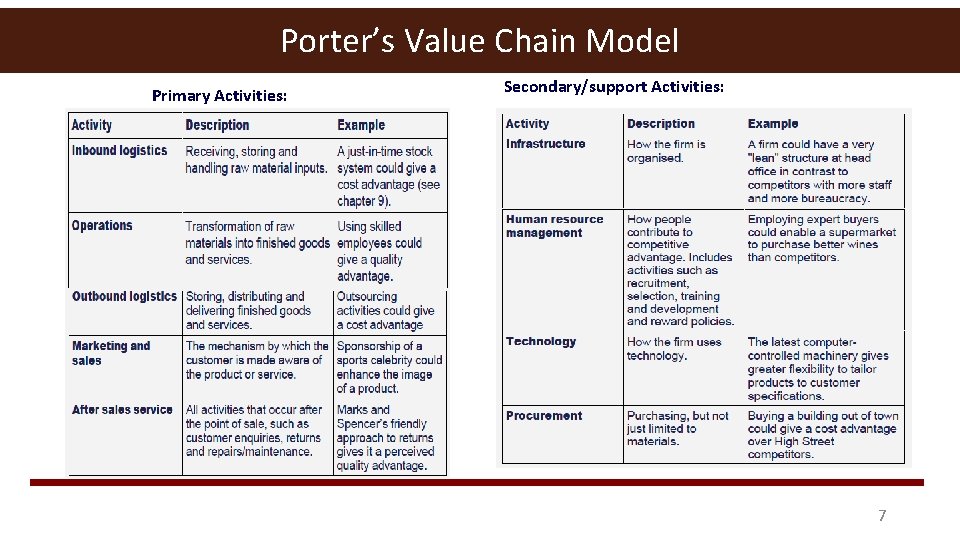
Porter’s Value Chain Model Primary Activities: Secondary/support Activities: 7
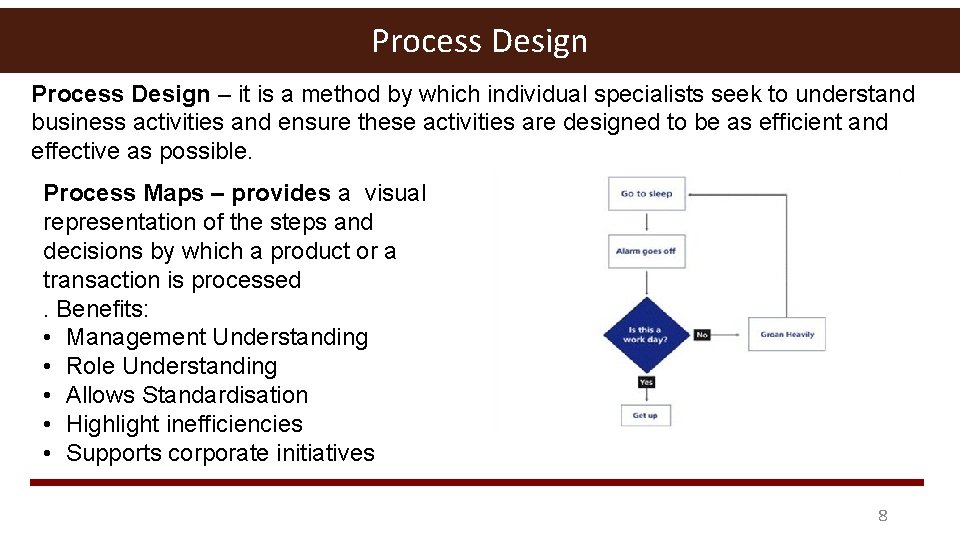
Process Design – it is a method by which individual specialists seek to understand business activities and ensure these activities are designed to be as efficient and effective as possible. Process Maps – provides a visual representation of the steps and decisions by which a product or a transaction is processed. Benefits: • Management Understanding • Role Understanding • Allows Standardisation • Highlight inefficiencies • Supports corporate initiatives 8
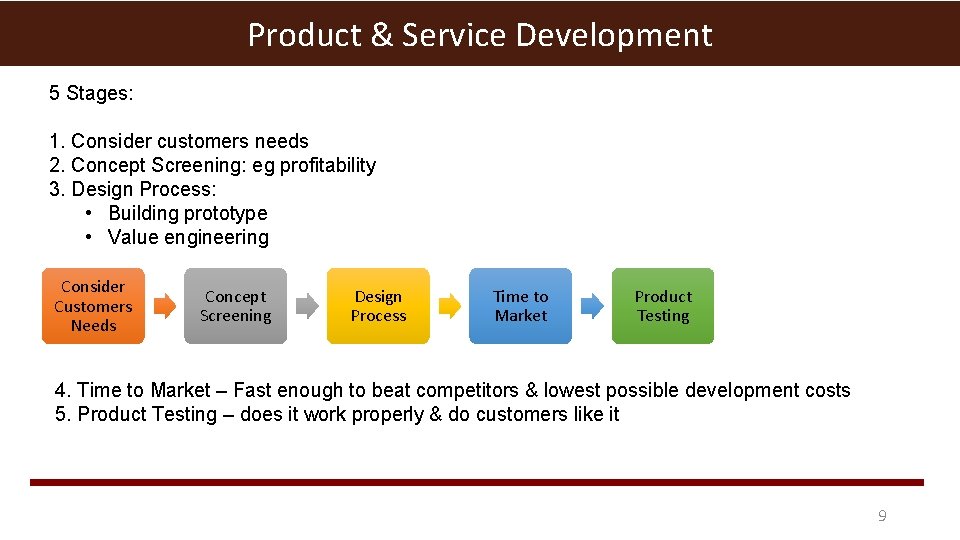
Product & Service Development 5 Stages: 1. Consider customers needs 2. Concept Screening: eg profitability 3. Design Process: • Building prototype • Value engineering Consider Customers Needs Concept Screening Design Process Time to Market Product Testing 4. Time to Market – Fast enough to beat competitors & lowest possible development costs 5. Product Testing – does it work properly & do customers like it 9
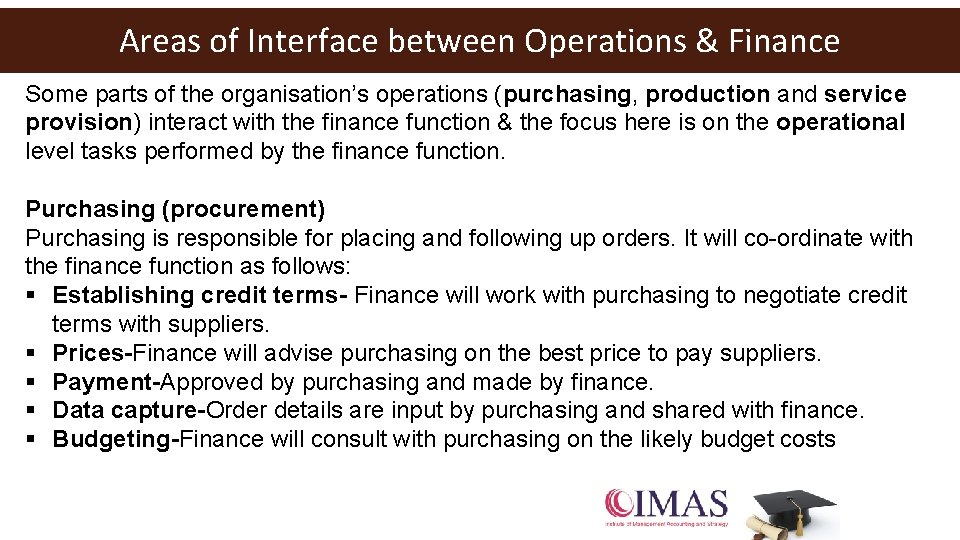
Areas of Interface between Operations & Finance Some parts of the organisation’s operations (purchasing, production and service provision) interact with the finance function & the focus here is on the operational level tasks performed by the finance function. Purchasing (procurement) Purchasing is responsible for placing and following up orders. It will co-ordinate with the finance function as follows: § Establishing credit terms- Finance will work with purchasing to negotiate credit terms with suppliers. § Prices-Finance will advise purchasing on the best price to pay suppliers. § Payment-Approved by purchasing and made by finance. § Data capture-Order details are input by purchasing and shared with finance. § Budgeting-Finance will consult with purchasing on the likely budget costs
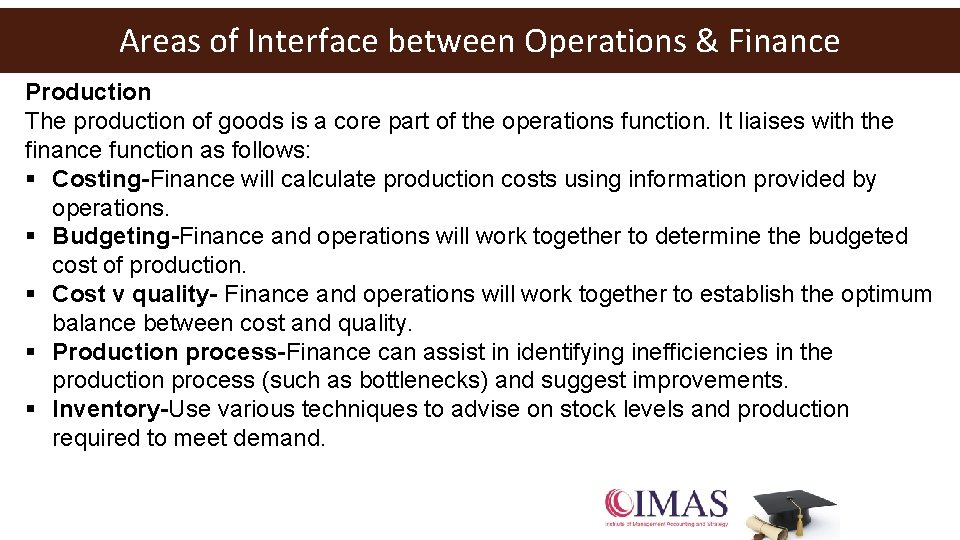
Areas of Interface between Operations & Finance Production The production of goods is a core part of the operations function. It liaises with the finance function as follows: § Costing-Finance will calculate production costs using information provided by operations. § Budgeting-Finance and operations will work together to determine the budgeted cost of production. § Cost v quality- Finance and operations will work together to establish the optimum balance between cost and quality. § Production process-Finance can assist in identifying inefficiencies in the production process (such as bottlenecks) and suggest improvements. § Inventory-Use various techniques to advise on stock levels and production required to meet demand.
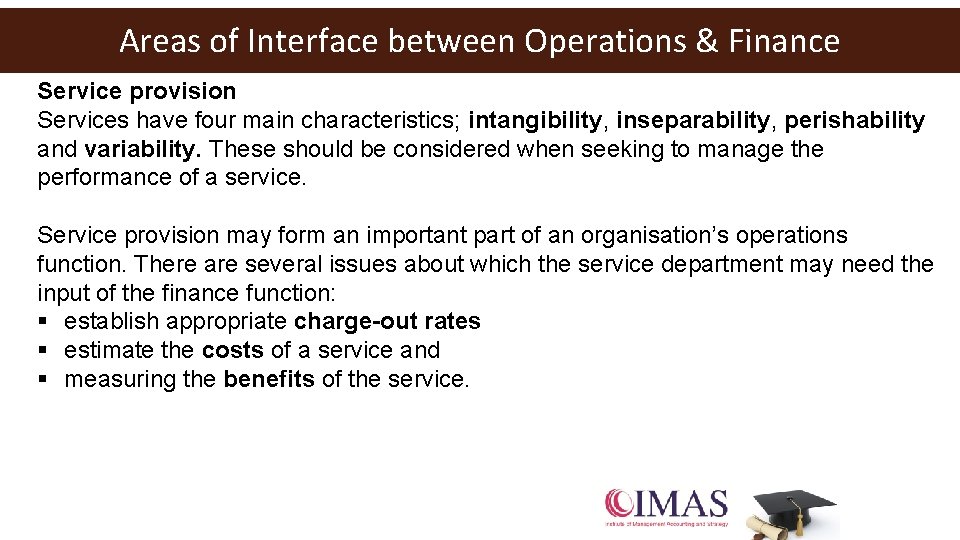
Areas of Interface between Operations & Finance Service provision Services have four main characteristics; intangibility, inseparability, perishability and variability. These should be considered when seeking to manage the performance of a service. Service provision may form an important part of an organisation’s operations function. There are several issues about which the service department may need the input of the finance function: § establish appropriate charge-out rates § estimate the costs of a service and § measuring the benefits of the service.
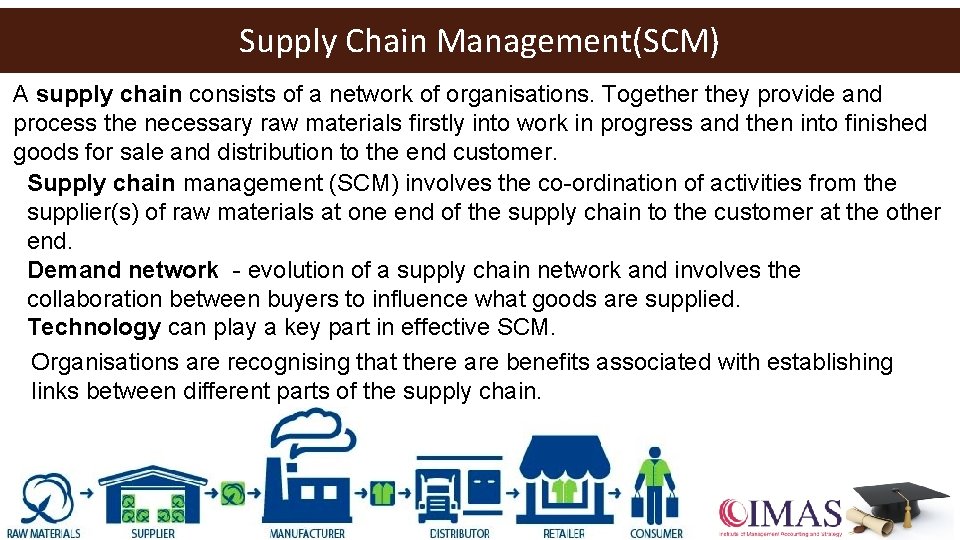
Supply Chain Management(SCM) A supply chain consists of a network of organisations. Together they provide and process the necessary raw materials firstly into work in progress and then into finished goods for sale and distribution to the end customer. Supply chain management (SCM) involves the co-ordination of activities from the supplier(s) of raw materials at one end of the supply chain to the customer at the other end. Demand network - evolution of a supply chain network and involves the collaboration between buyers to influence what goods are supplied. Technology can play a key part in effective SCM. Organisations are recognising that there are benefits associated with establishing links between different parts of the supply chain.
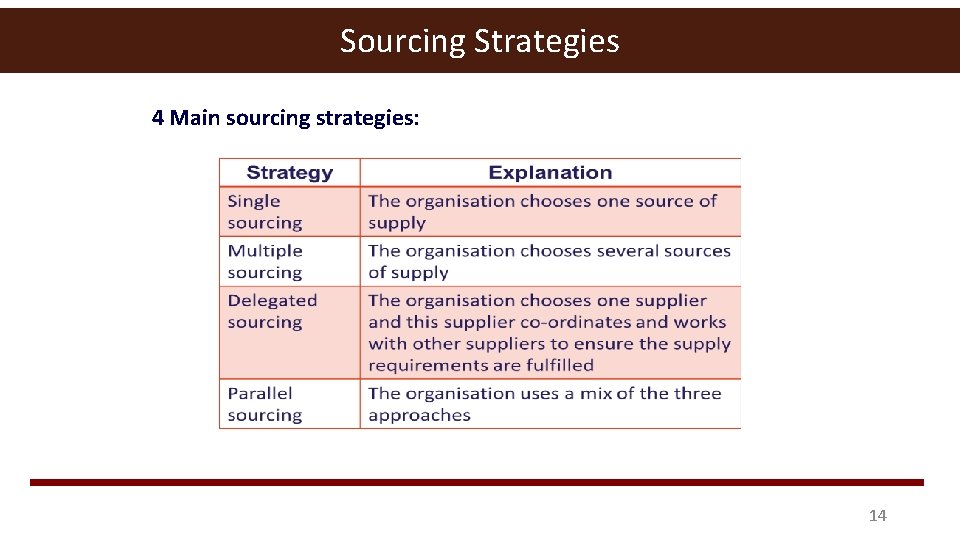
Sourcing Strategies 4 Main sourcing strategies: 14
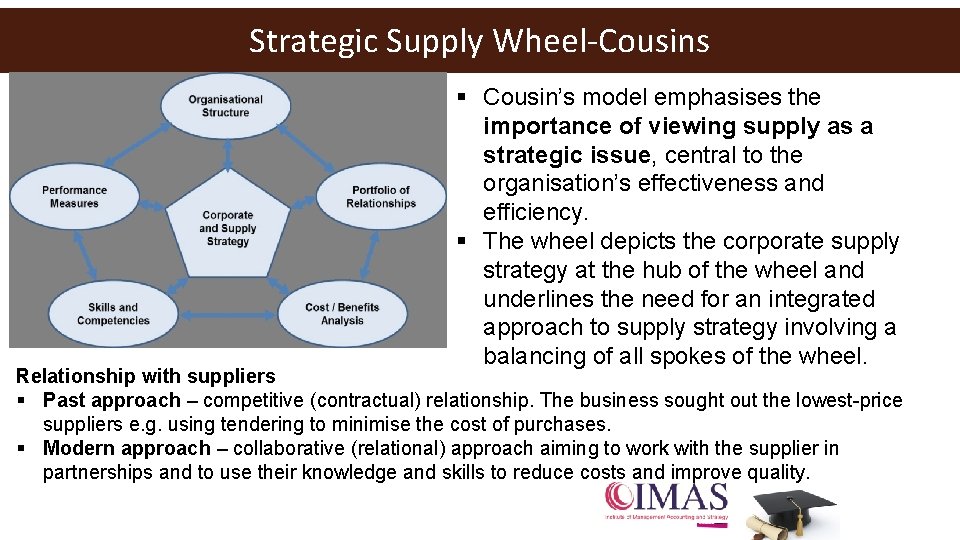
Strategic Supply Wheel-Cousins § Cousin’s model emphasises the importance of viewing supply as a strategic issue, central to the organisation’s effectiveness and efficiency. § The wheel depicts the corporate supply strategy at the hub of the wheel and underlines the need for an integrated approach to supply strategy involving a balancing of all spokes of the wheel. Relationship with suppliers § Past approach – competitive (contractual) relationship. The business sought out the lowest-price suppliers e. g. using tendering to minimise the cost of purchases. § Modern approach – collaborative (relational) approach aiming to work with the supplier in partnerships and to use their knowledge and skills to reduce costs and improve quality.
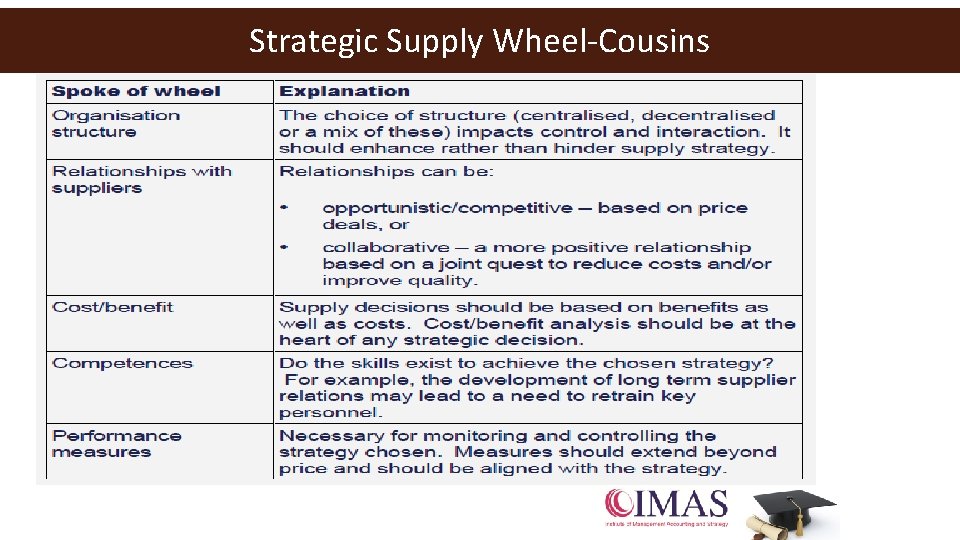
Strategic Supply Wheel-Cousins
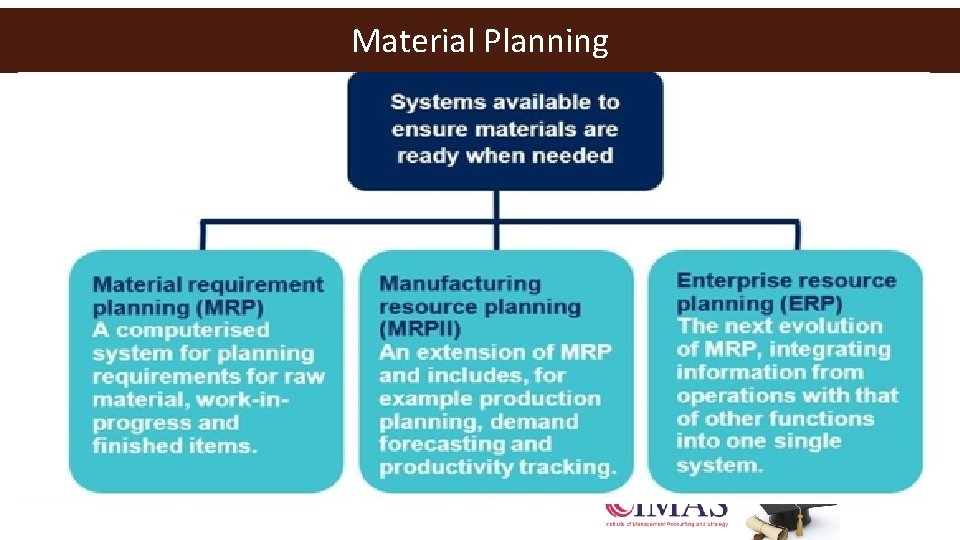
Material Planning
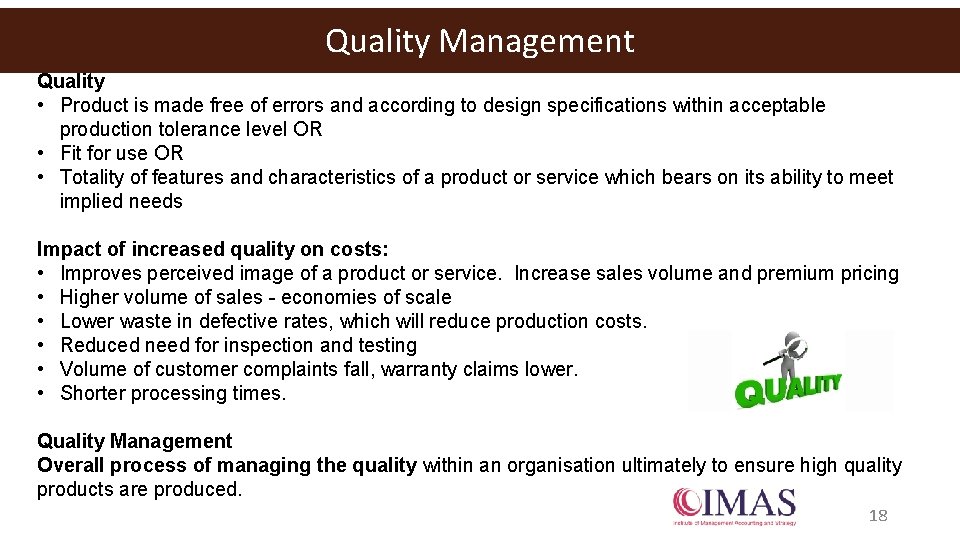
Quality Management Quality • Product is made free of errors and according to design specifications within acceptable production tolerance level OR • Fit for use OR • Totality of features and characteristics of a product or service which bears on its ability to meet implied needs Impact of increased quality on costs: • Improves perceived image of a product or service. Increase sales volume and premium pricing • Higher volume of sales - economies of scale • Lower waste in defective rates, which will reduce production costs. • Reduced need for inspection and testing • Volume of customer complaints fall, warranty claims lower. • Shorter processing times. Quality Management Overall process of managing the quality within an organisation ultimately to ensure high quality products are produced. 18
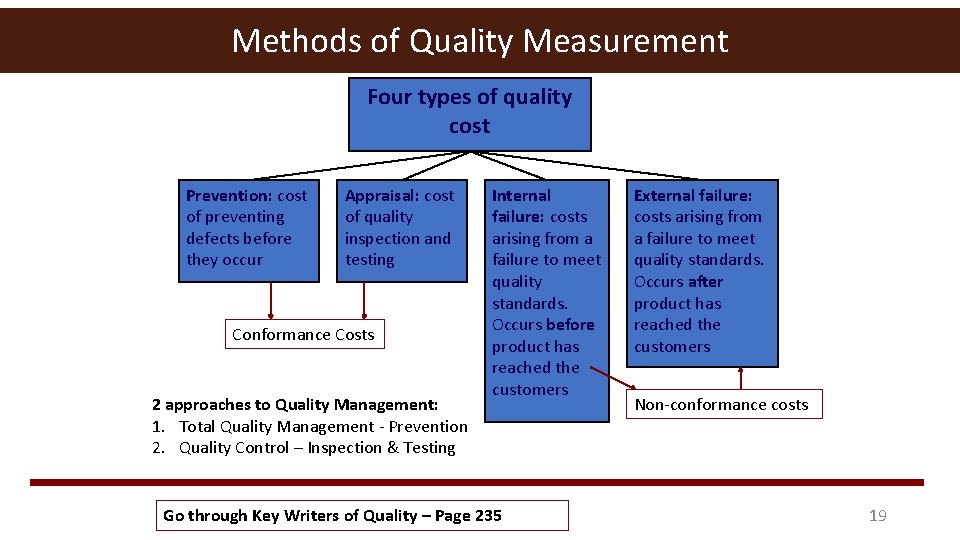
Methods of Quality Measurement Four types of quality cost Prevention: cost of preventing defects before they occur Appraisal: cost of quality inspection and testing Conformance Costs 2 approaches to Quality Management: 1. Total Quality Management - Prevention 2. Quality Control – Inspection & Testing Internal failure: costs arising from a failure to meet quality standards. Occurs before product has reached the customers Go through Key Writers of Quality – Page 235 External failure: costs arising from a failure to meet quality standards. Occurs after product has reached the customers Non-conformance costs 19
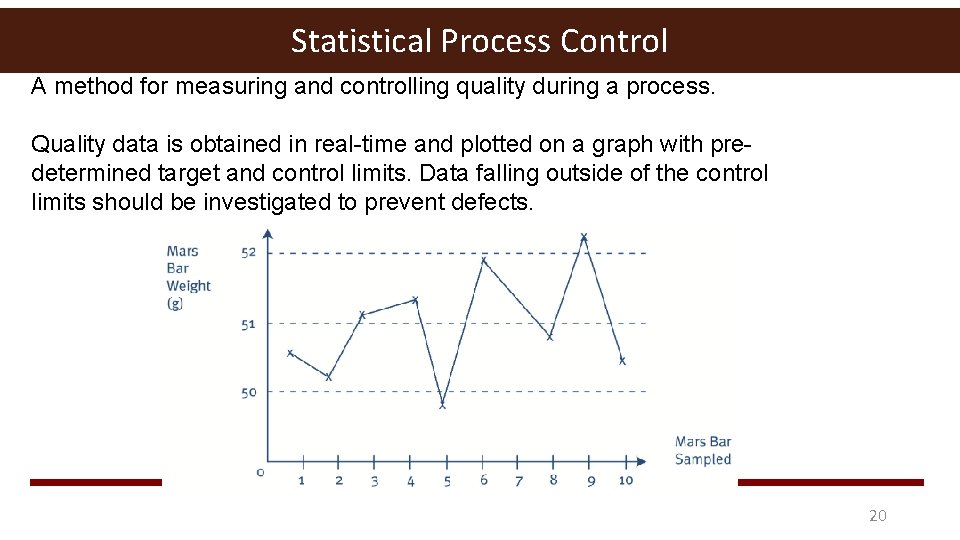
Statistical Process Control A method for measuring and controlling quality during a process. Quality data is obtained in real-time and plotted on a graph with predetermined target and control limits. Data falling outside of the control limits should be investigated to prevent defects. 20
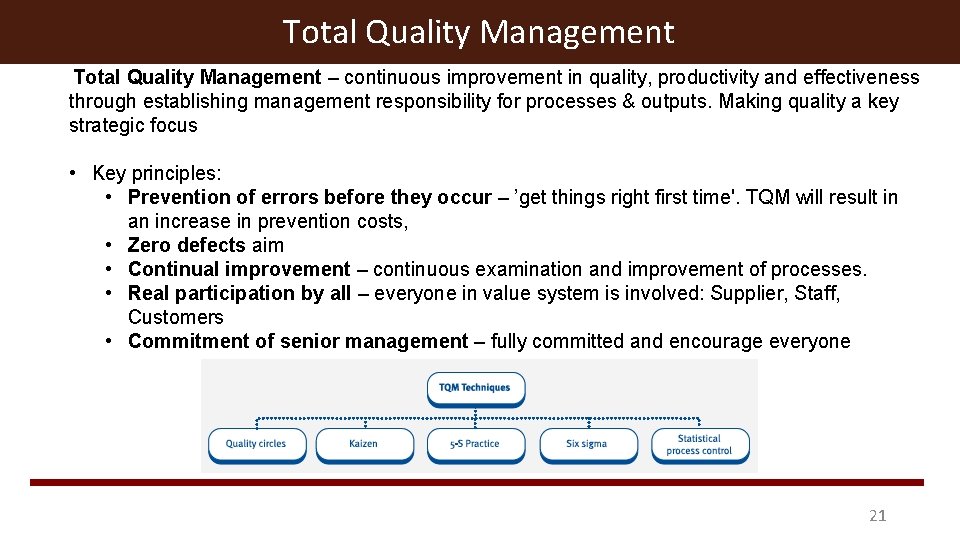
Total Quality Management – continuous improvement in quality, productivity and effectiveness through establishing management responsibility for processes & outputs. Making quality a key strategic focus • Key principles: • Prevention of errors before they occur – ’get things right first time'. TQM will result in an increase in prevention costs, • Zero defects aim • Continual improvement – continuous examination and improvement of processes. • Real participation by all – everyone in value system is involved: Supplier, Staff, Customers • Commitment of senior management – fully committed and encourage everyone 21
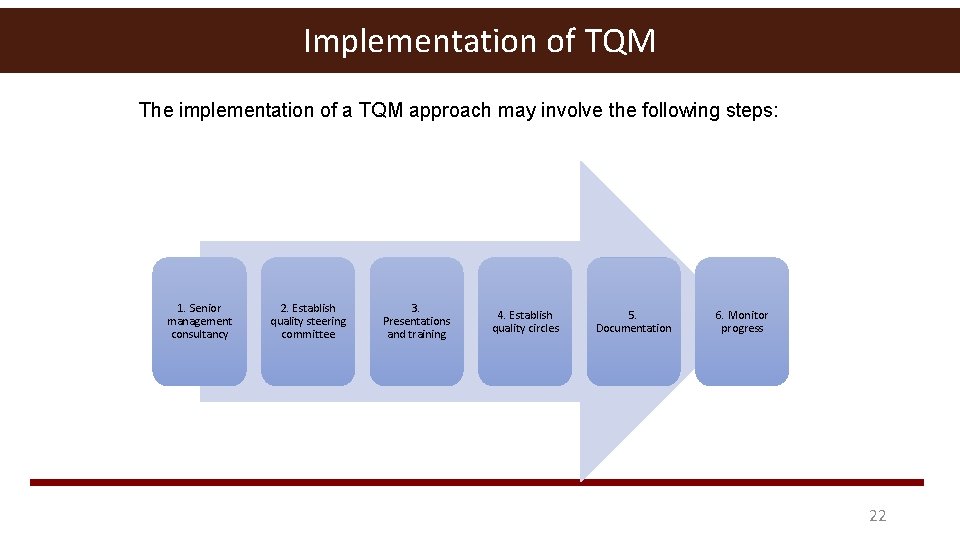
Implementation of TQM The implementation of a TQM approach may involve the following steps: 1. Senior management consultancy 2. Establish quality steering committee 3. Presentations and training 4. Establish quality circles 5. Documentation 6. Monitor progress 22
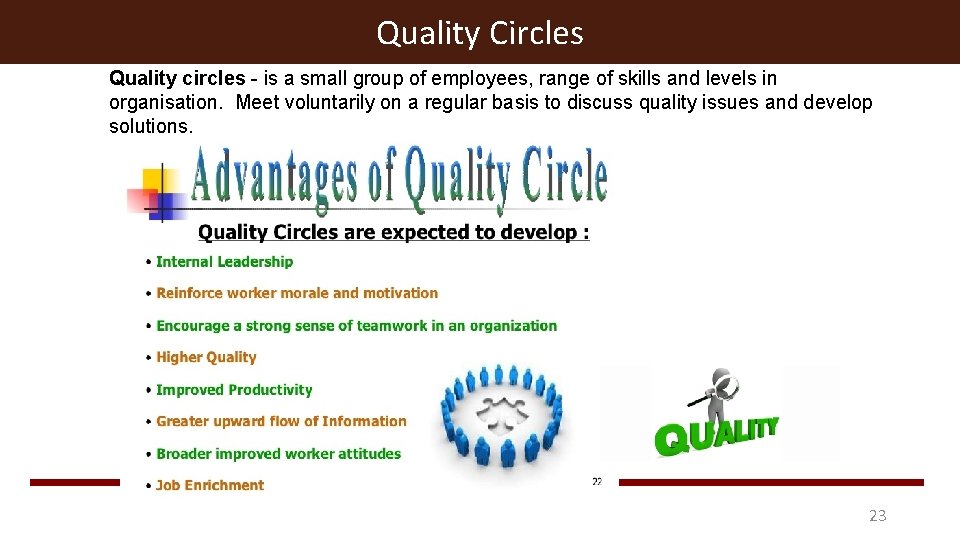
Quality Circles Quality circles - is a small group of employees, range of skills and levels in organisation. Meet voluntarily on a regular basis to discuss quality issues and develop solutions. 23
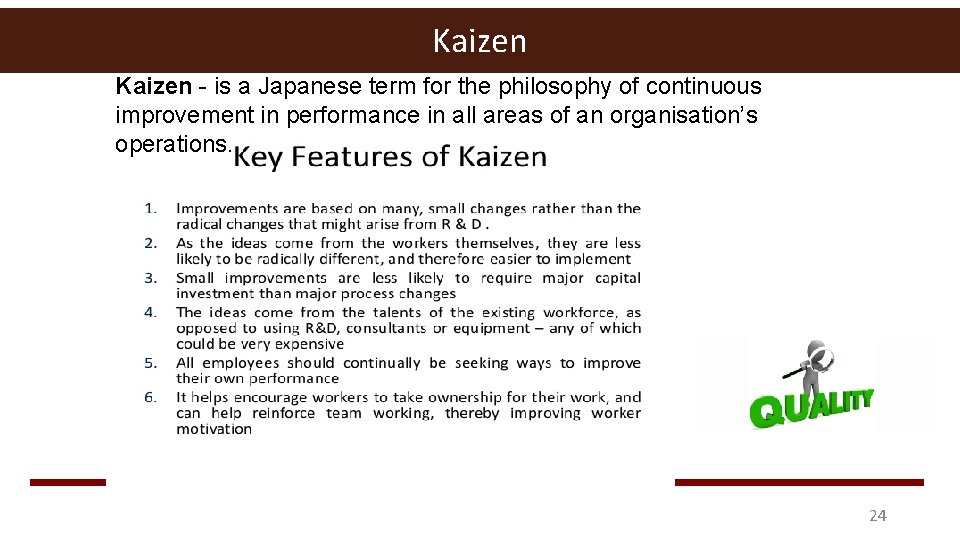
Kaizen - is a Japanese term for the philosophy of continuous improvement in performance in all areas of an organisation’s operations. 24
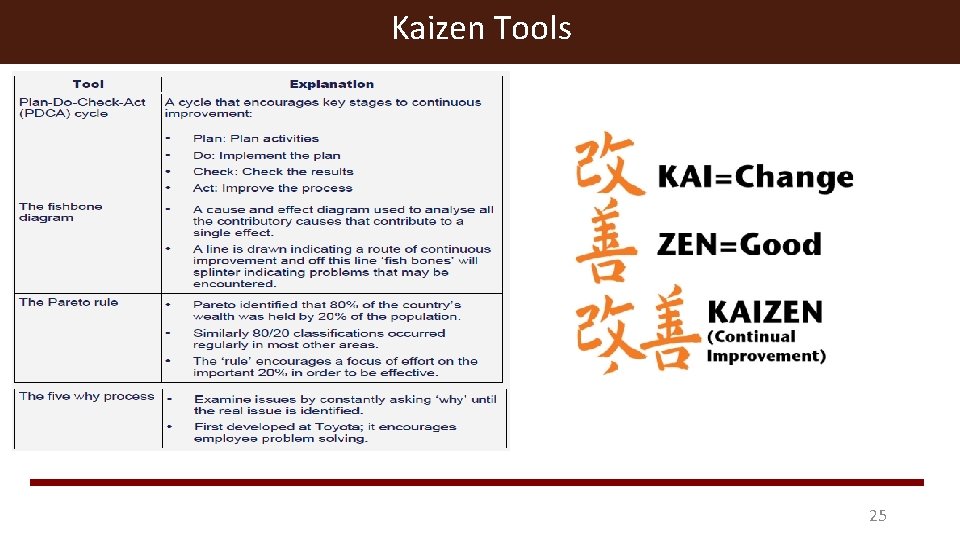
Kaizen Tools 25
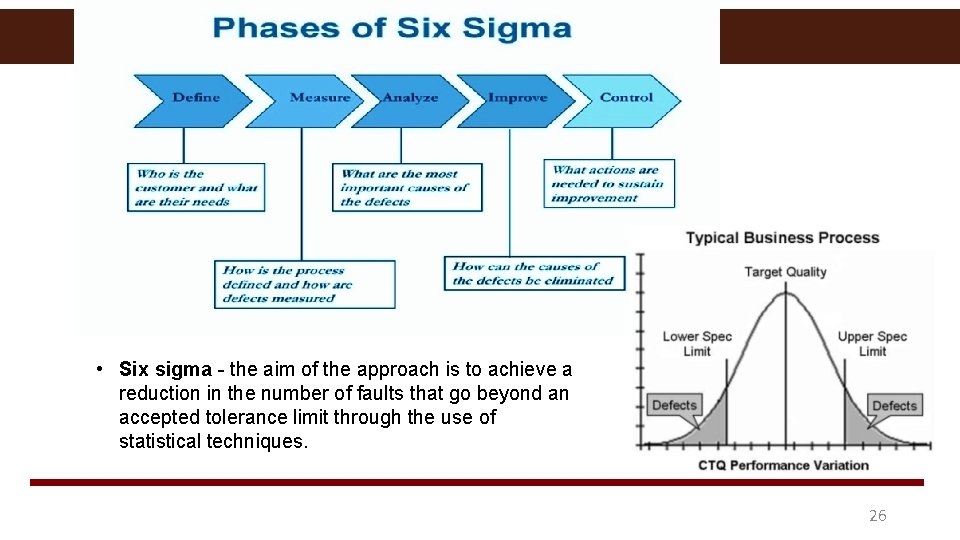
Six Sigma • Six sigma - the aim of the approach is to achieve a reduction in the number of faults that go beyond an accepted tolerance limit through the use of statistical techniques. 26
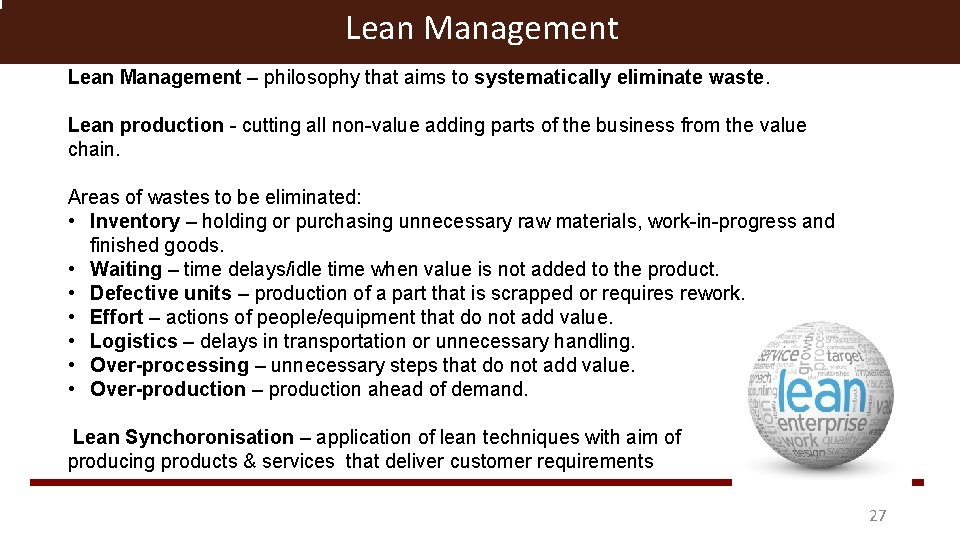
Lean Management – philosophy that aims to systematically eliminate waste. Lean production - cutting all non-value adding parts of the business from the value chain. Areas of wastes to be eliminated: • Inventory – holding or purchasing unnecessary raw materials, work-in-progress and finished goods. • Waiting – time delays/idle time when value is not added to the product. • Defective units – production of a part that is scrapped or requires rework. • Effort – actions of people/equipment that do not add value. • Logistics – delays in transportation or unnecessary handling. • Over-processing – unnecessary steps that do not add value. • Over-production – production ahead of demand. Lean Synchoronisation – application of lean techniques with aim of producing products & services that deliver customer requirements 27
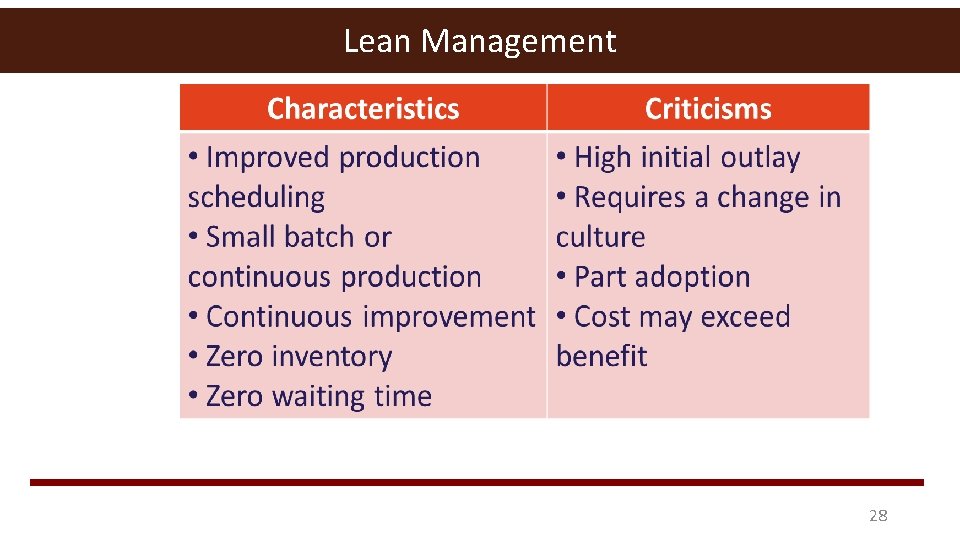
Lean Management 28
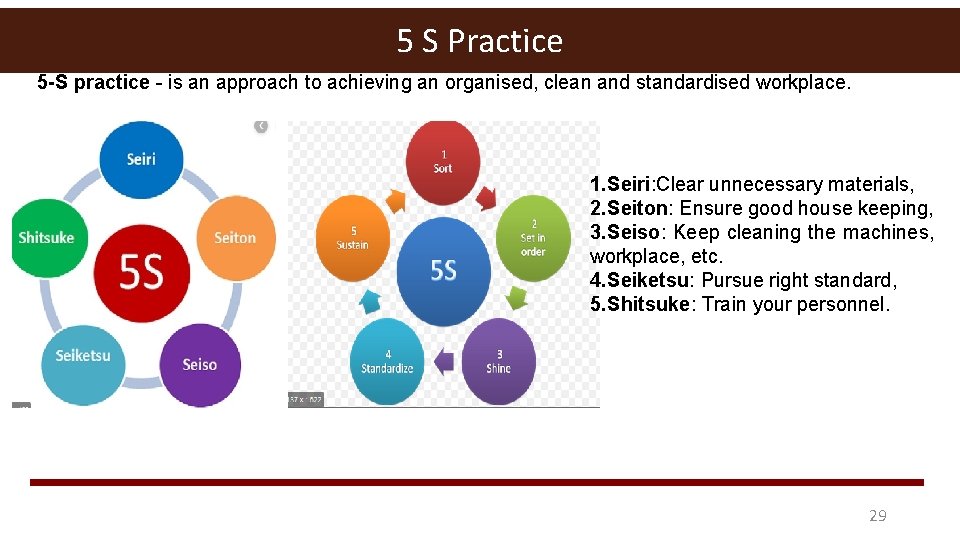
5 S Practice 5 -S practice - is an approach to achieving an organised, clean and standardised workplace. 1. Seiri: Clear unnecessary materials, 2. Seiton: Ensure good house keeping, 3. Seiso: Keep cleaning the machines, workplace, etc. 4. Seiketsu: Pursue right standard, 5. Shitsuke: Train your personnel. 29
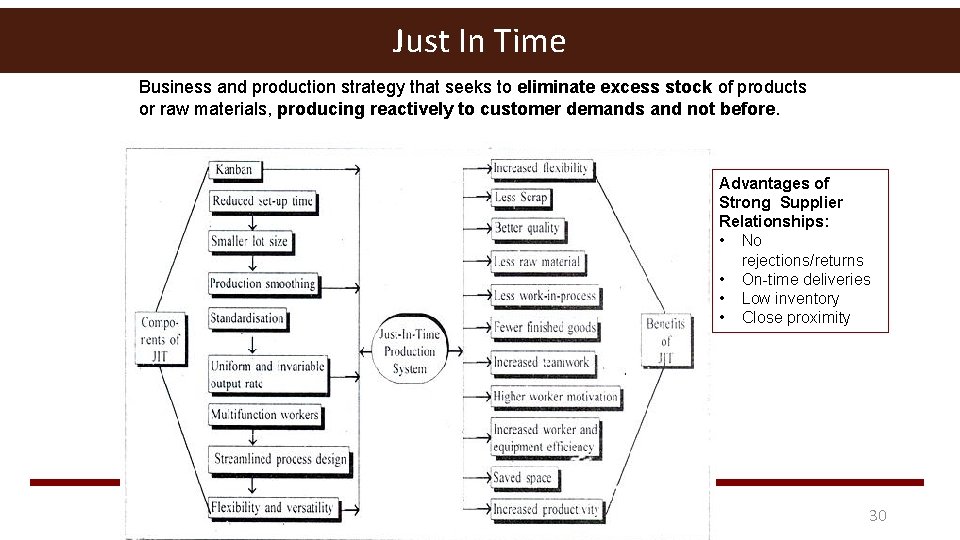
Just In Time Business and production strategy that seeks to eliminate excess stock of products or raw materials, producing reactively to customer demands and not before. Advantages of Strong Supplier Relationships: • No rejections/returns • On-time deliveries • Low inventory • Close proximity 30
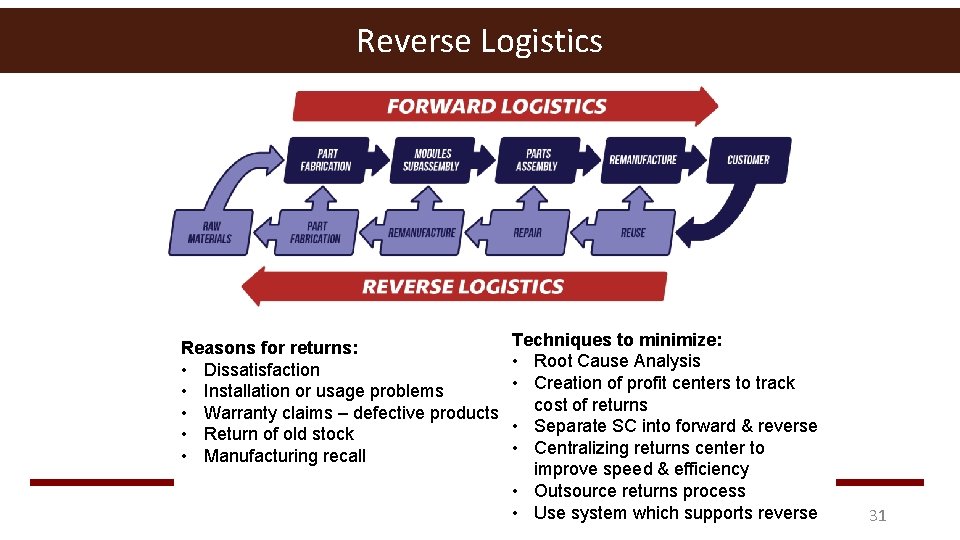
Reverse Logistics Reasons for returns: • Dissatisfaction • Installation or usage problems • Warranty claims – defective products • Return of old stock • Manufacturing recall Techniques to minimize: • Root Cause Analysis • Creation of profit centers to track cost of returns • Separate SC into forward & reverse • Centralizing returns center to improve speed & efficiency • Outsource returns process • Use system which supports reverse 31
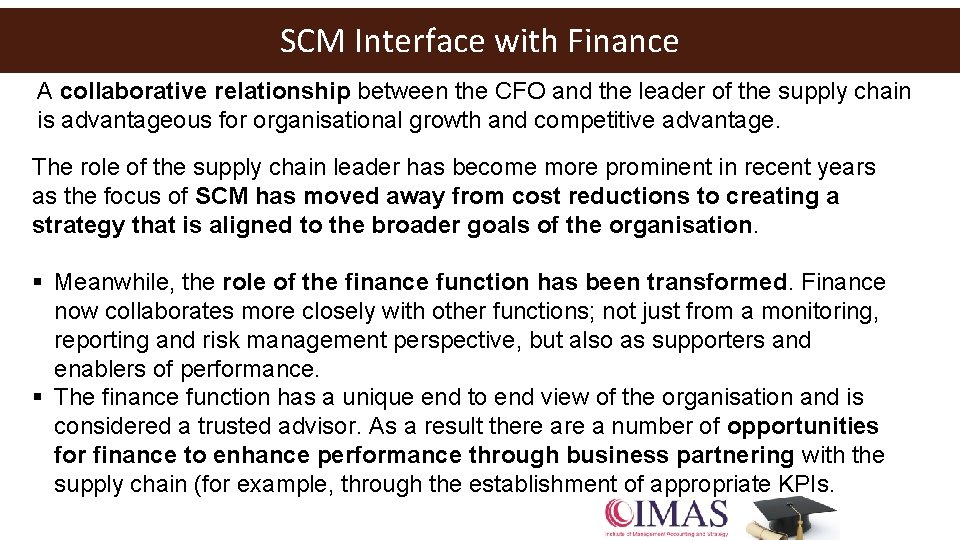
SCM Interface with Finance A collaborative relationship between the CFO and the leader of the supply chain is advantageous for organisational growth and competitive advantage. The role of the supply chain leader has become more prominent in recent years as the focus of SCM has moved away from cost reductions to creating a strategy that is aligned to the broader goals of the organisation. § Meanwhile, the role of the finance function has been transformed. Finance now collaborates more closely with other functions; not just from a monitoring, reporting and risk management perspective, but also as supporters and enablers of performance. § The finance function has a unique end to end view of the organisation and is considered a trusted advisor. As a result there a number of opportunities for finance to enhance performance through business partnering with the supply chain (for example, through the establishment of appropriate KPIs.
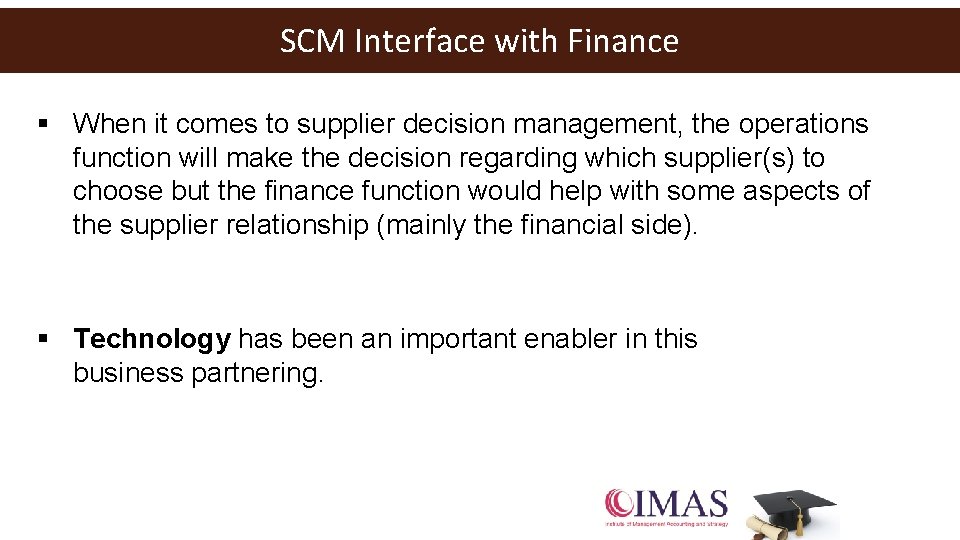
SCM Interface with Finance § When it comes to supplier decision management, the operations function will make the decision regarding which supplier(s) to choose but the finance function would help with some aspects of the supplier relationship (mainly the financial side). § Technology has been an important enabler in this business partnering.
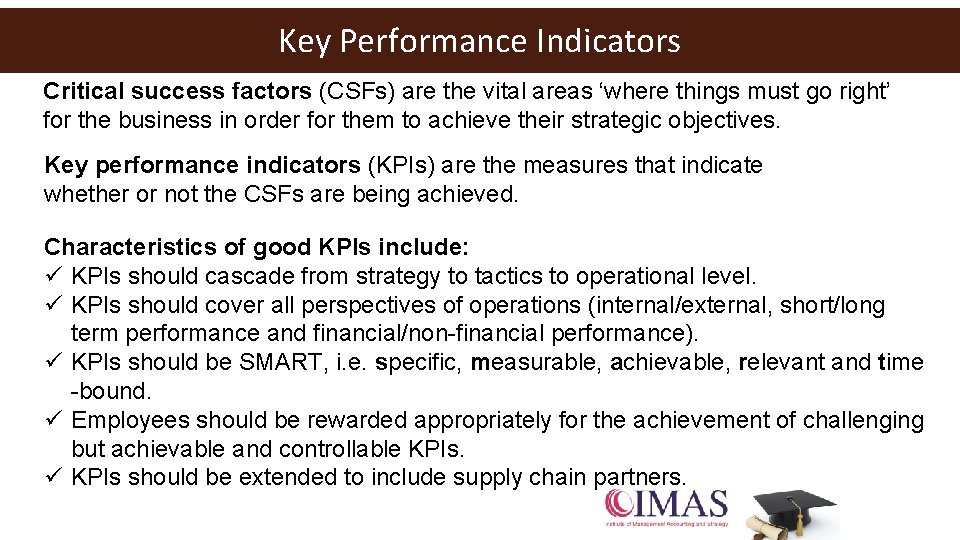
Key Performance Indicators Critical success factors (CSFs) are the vital areas ‘where things must go right’ for the business in order for them to achieve their strategic objectives. Key performance indicators (KPIs) are the measures that indicate whether or not the CSFs are being achieved. Characteristics of good KPIs include: ü KPIs should cascade from strategy to tactics to operational level. ü KPIs should cover all perspectives of operations (internal/external, short/long term performance and financial/non-financial performance). ü KPIs should be SMART, i. e. specific, measurable, achievable, relevant and time -bound. ü Employees should be rewarded appropriately for the achievement of challenging but achievable and controllable KPIs. ü KPIs should be extended to include supply chain partners.
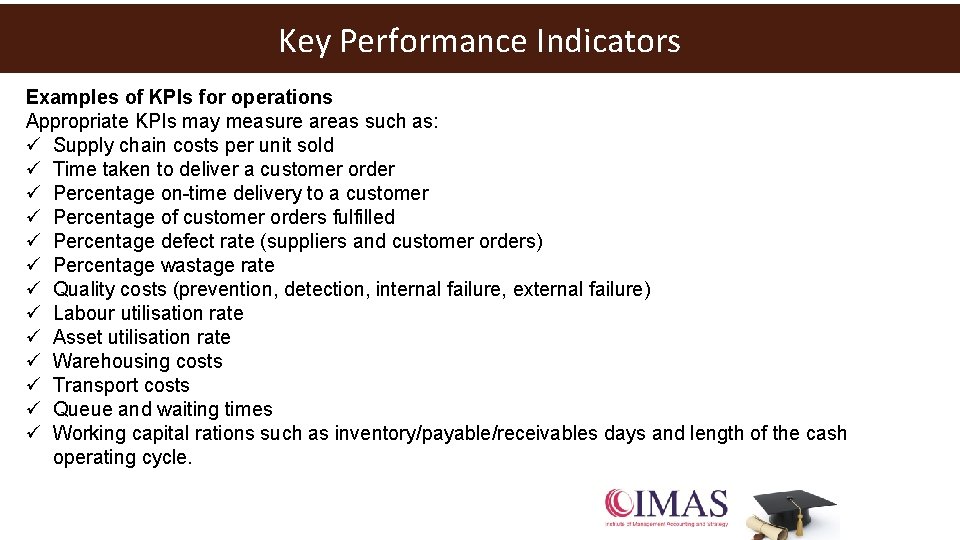
Key Performance Indicators Examples of KPIs for operations Appropriate KPIs may measure areas such as: ü Supply chain costs per unit sold ü Time taken to deliver a customer order ü Percentage on-time delivery to a customer ü Percentage of customer orders fulfilled ü Percentage defect rate (suppliers and customer orders) ü Percentage wastage rate ü Quality costs (prevention, detection, internal failure, external failure) ü Labour utilisation rate ü Asset utilisation rate ü Warehousing costs ü Transport costs ü Queue and waiting times ü Working capital rations such as inventory/payable/receivables days and length of the cash operating cycle.
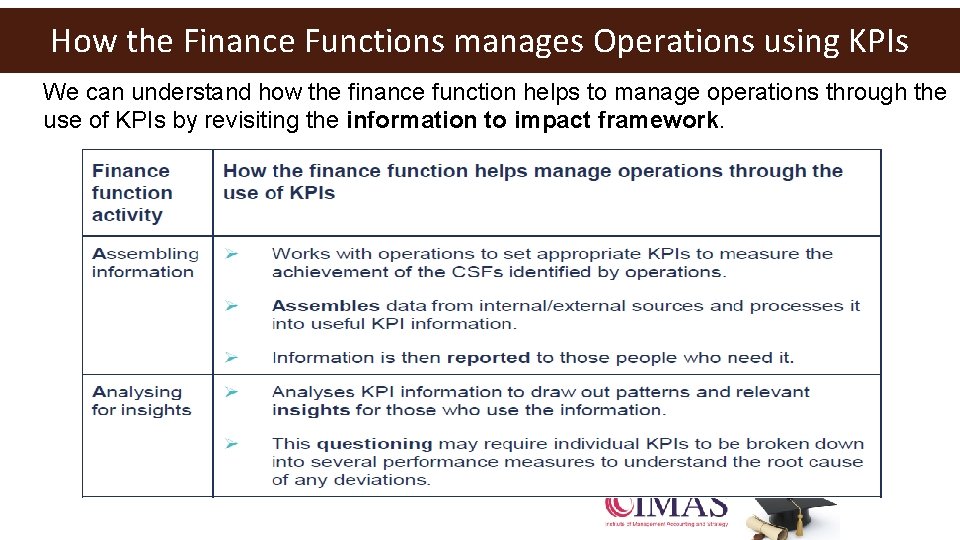
How the Finance Functions manages Operations using KPIs We can understand how the finance function helps to manage operations through the use of KPIs by revisiting the information to impact framework.
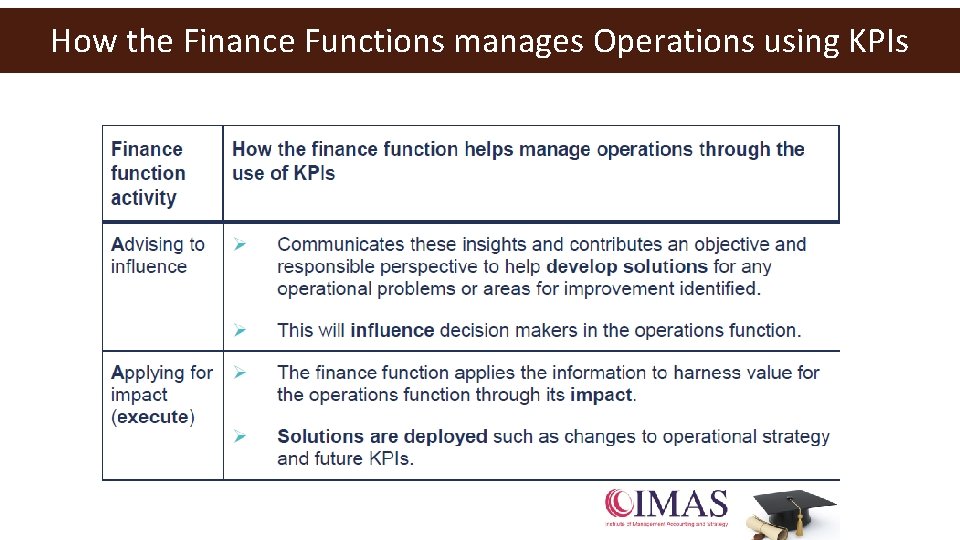
How the Finance Functions manages Operations using KPIs
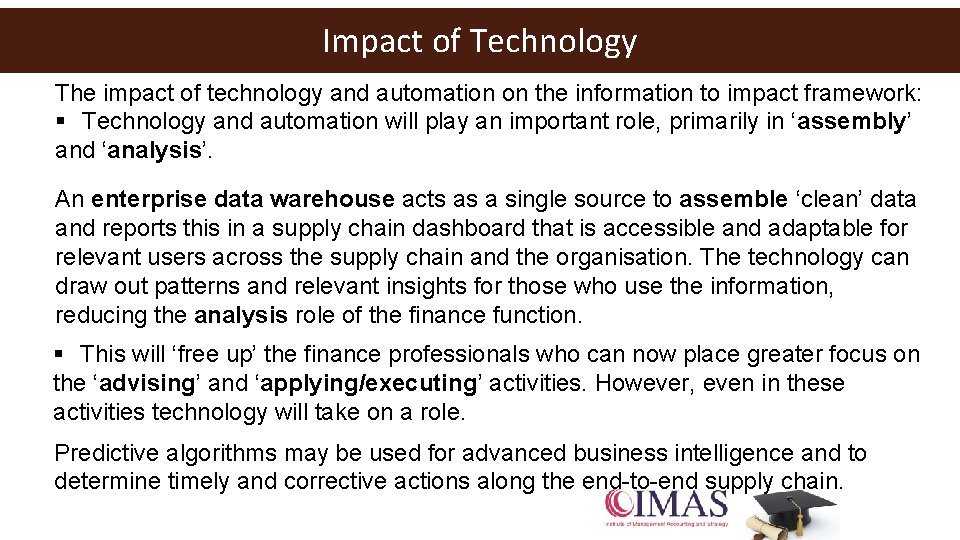
Impact of Technology The impact of technology and automation on the information to impact framework: § Technology and automation will play an important role, primarily in ‘assembly’ and ‘analysis’. An enterprise data warehouse acts as a single source to assemble ‘clean’ data and reports this in a supply chain dashboard that is accessible and adaptable for relevant users across the supply chain and the organisation. The technology can draw out patterns and relevant insights for those who use the information, reducing the analysis role of the finance function. § This will ‘free up’ the finance professionals who can now place greater focus on the ‘advising’ and ‘applying/executing’ activities. However, even in these activities technology will take on a role. Predictive algorithms may be used for advanced business intelligence and to determine timely and corrective actions along the end-to-end supply chain.
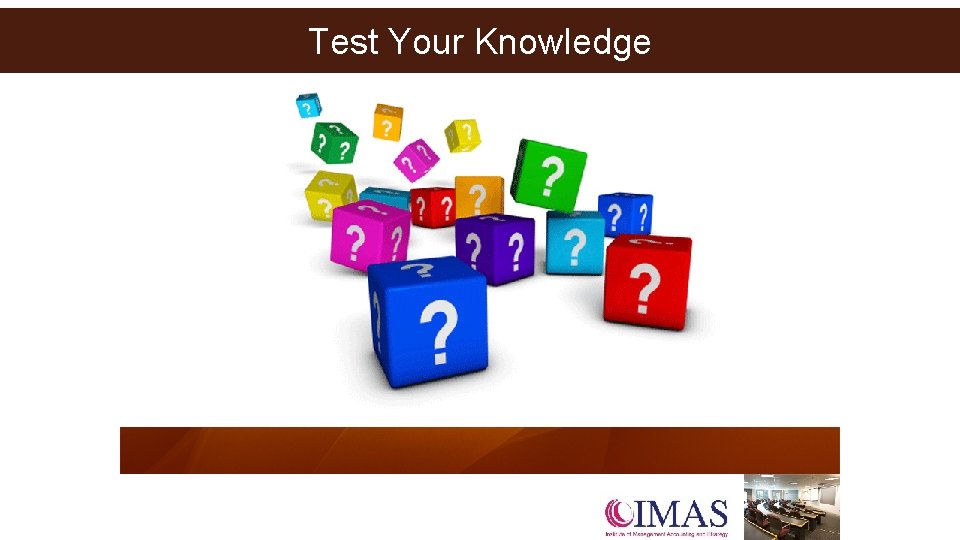
Test Your Knowledge ?
Finance in a digital world
Managing in a digital world
Managing in a digital world
Diamond shape finance function
Finance for executives: managing for value creation
Real world vs digital world
Managing digital marketing
Managing digital communications
Management information system managing the digital firm
Management information systems managing the digital firm
Managing the digital firm
Managing knowledge in the digital firm
Sffcu auto loan rates
Digital trade
Ap world history chapter 25 africa and the atlantic world
Apa yang dimaksud warga digital
Unique features of digital markets
Digital data digital signals
Digital data transmission
E-commerce: digital markets, digital goods
Data encoding techniques in computer networks
"euro digital partners" "digital marketing"
E-commerce digital markets digital goods
Chapter 1 managing risk when driving
Chapter 8 managing stress and anxiety
Leasiest
Auditory distraction while driving
Chapter 8 managing distractions answers
Chapter 6 managing weight and body composition
Managing risk with the ipde process
Ipde process examples
Chapter 4 managing stress and coping with loss
Chapter 4 managing risk with the ipde process
Chapter 4 managing in a global environment
Chapter 18 managing anxiety
Chapter 17 managing personal finances
Chapter 17 managing business finances
Chapter 16 managing the stress in your life
Chapter 13 medical records management
Chapter 11 managing weight and eating behaviors