Lecture 23 Switch Mode Power Supplies Pulse Width
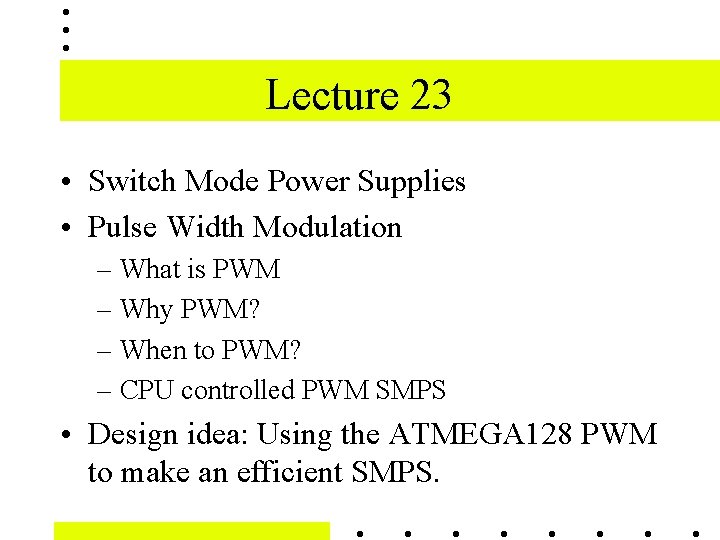
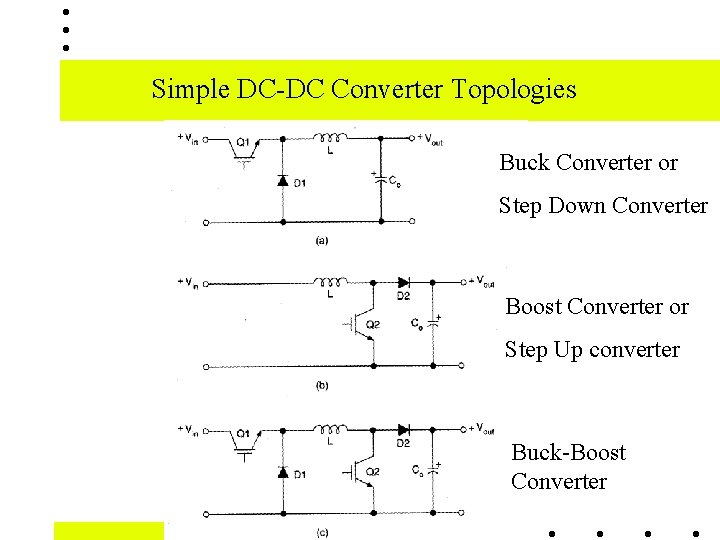
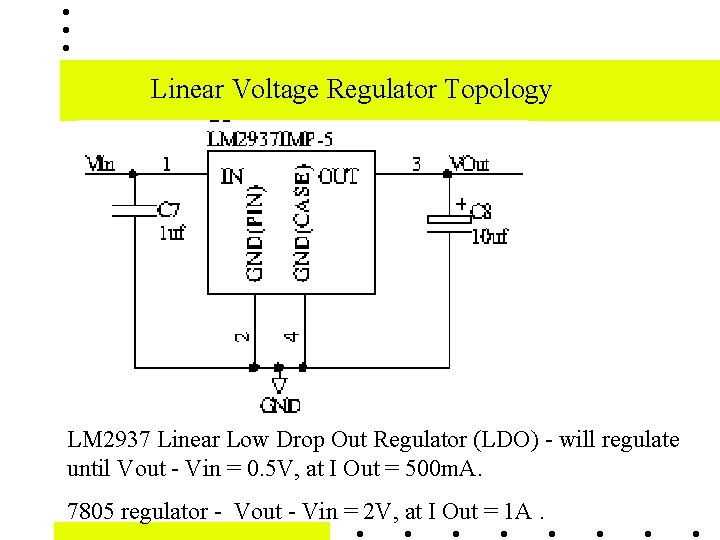
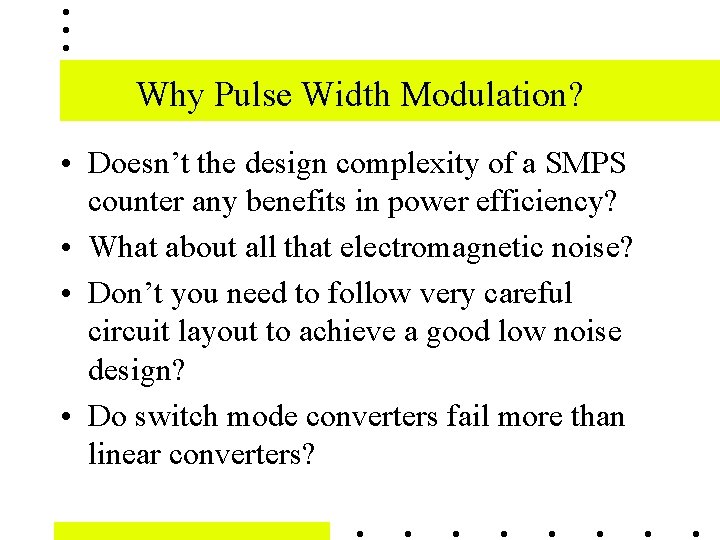
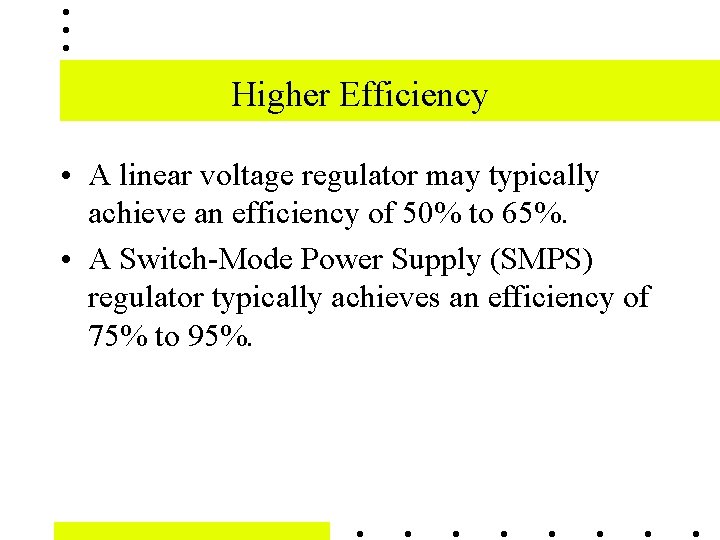
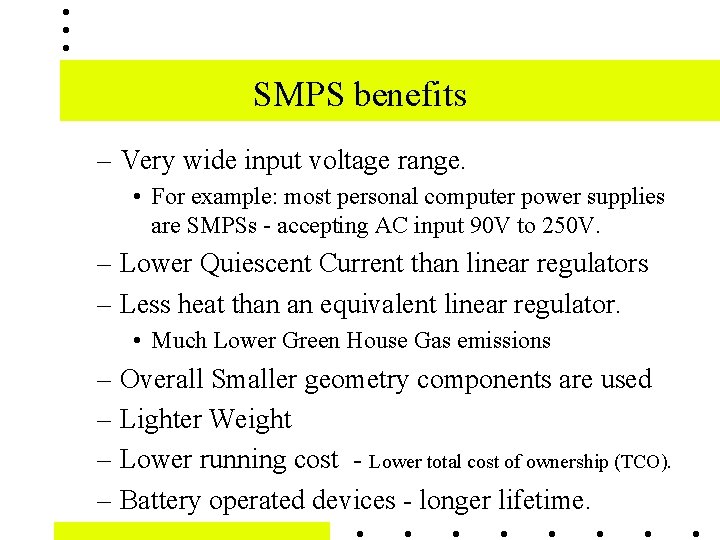
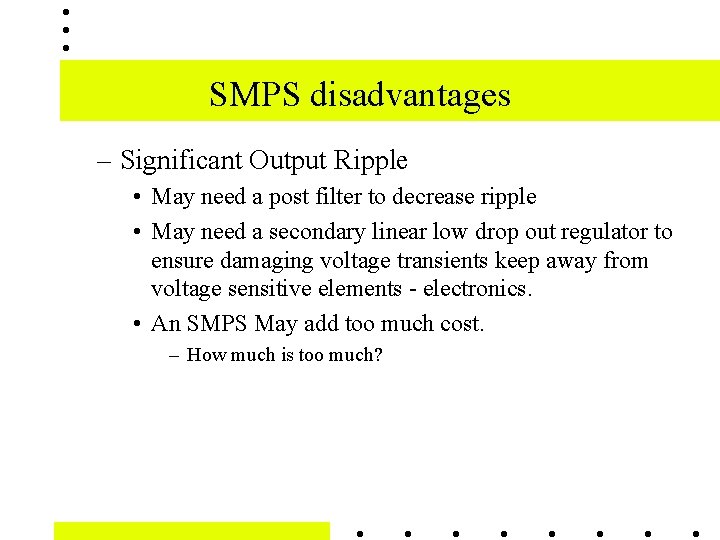
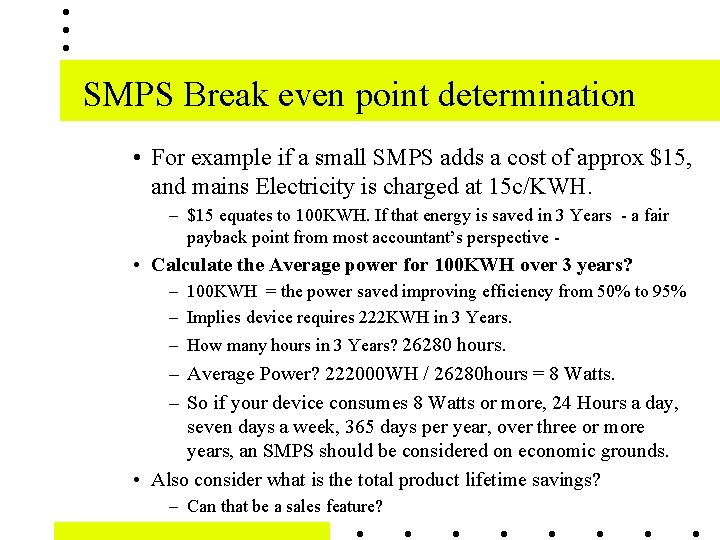
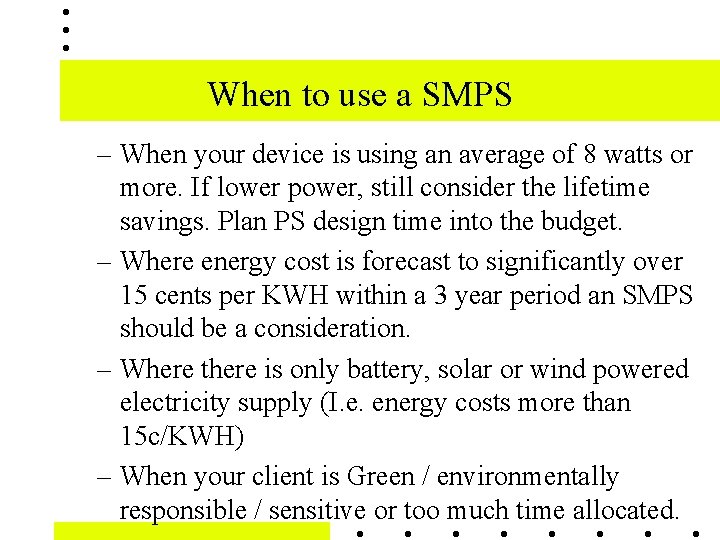
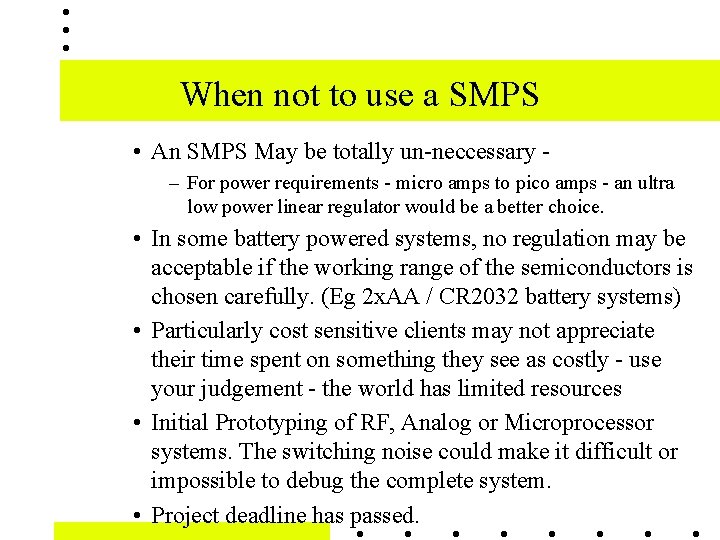
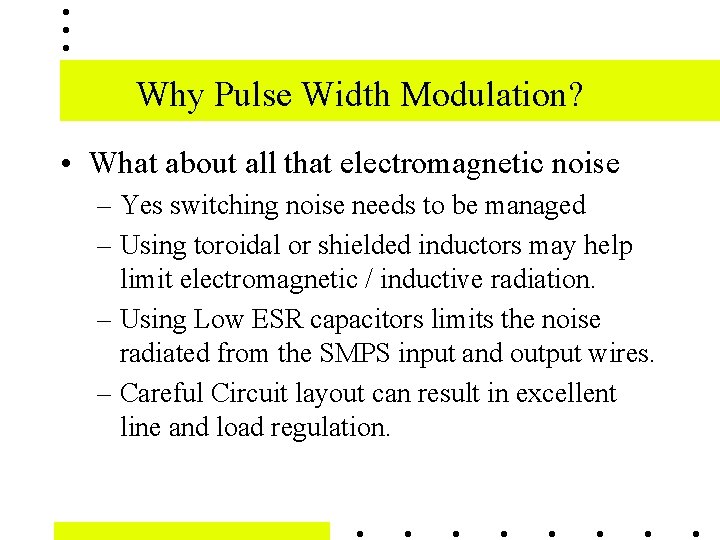
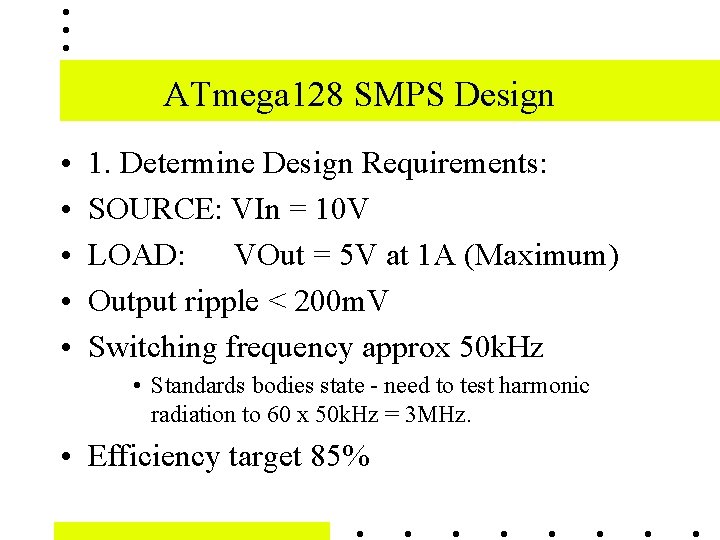
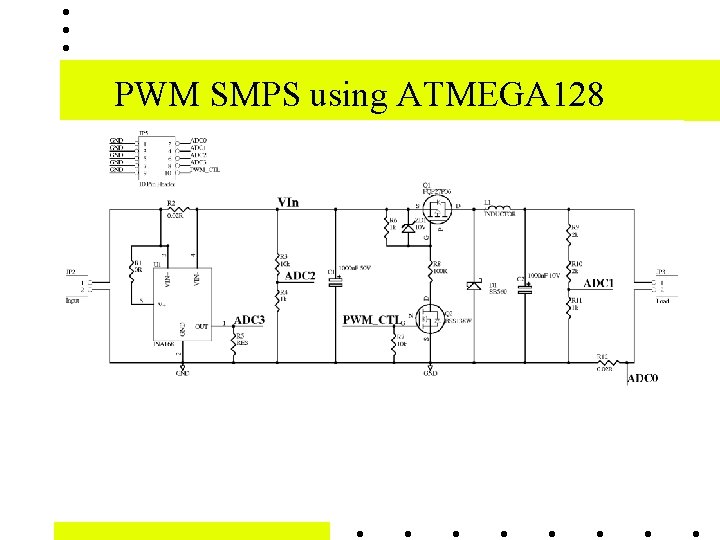
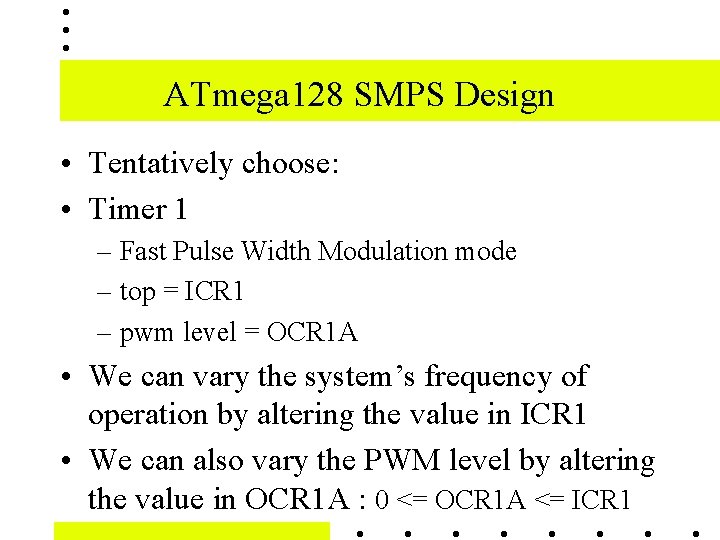
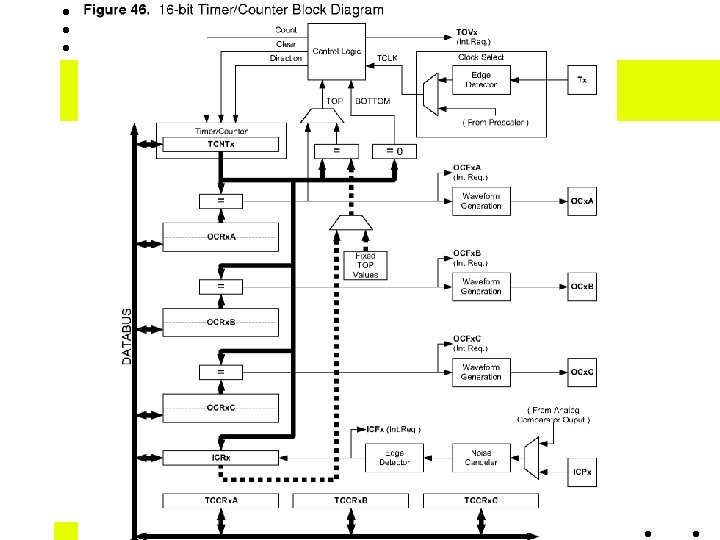
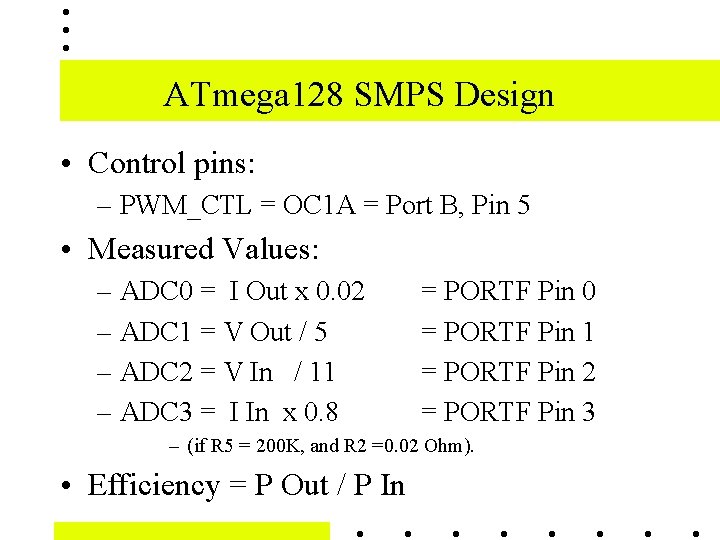

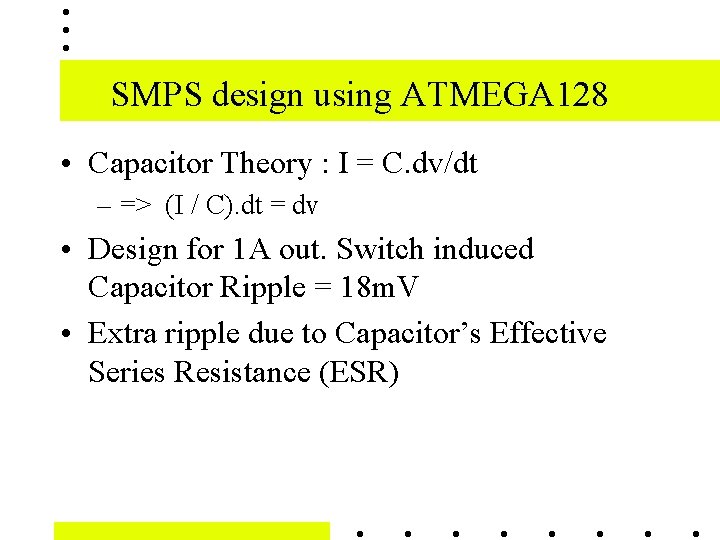
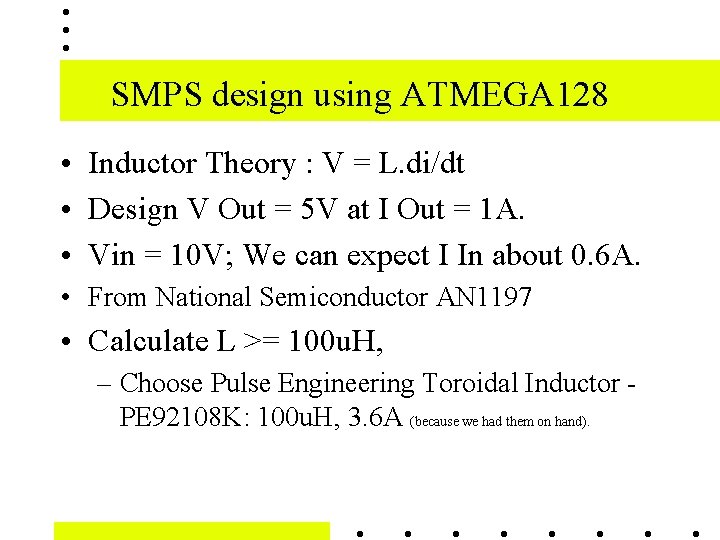

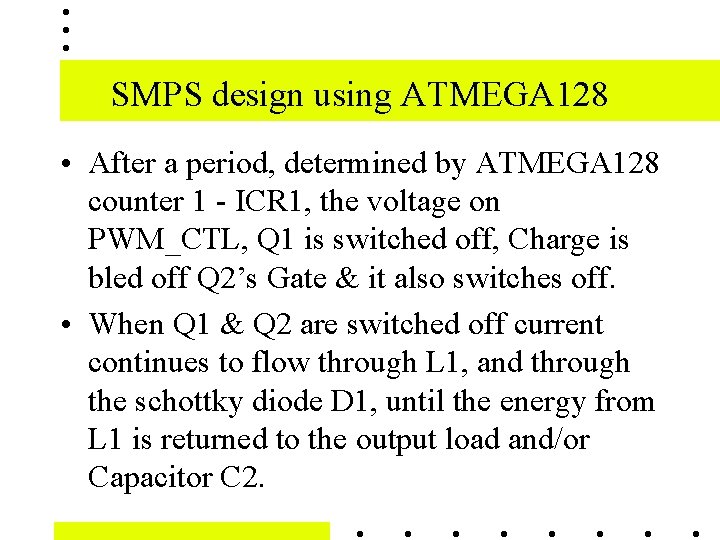
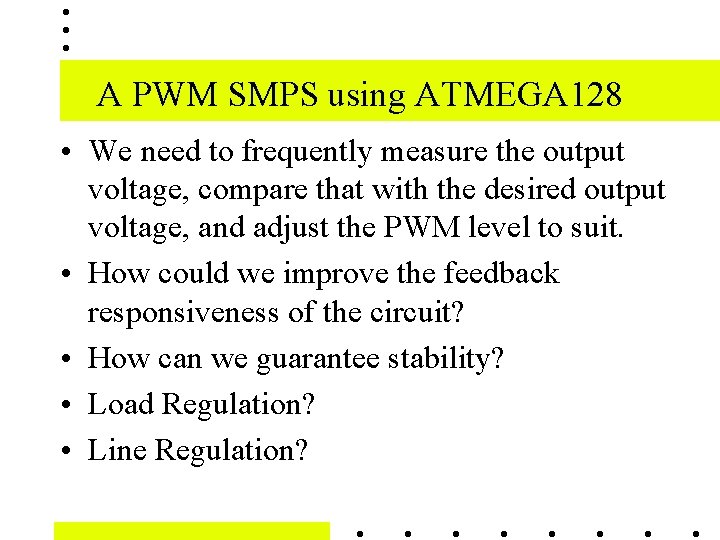
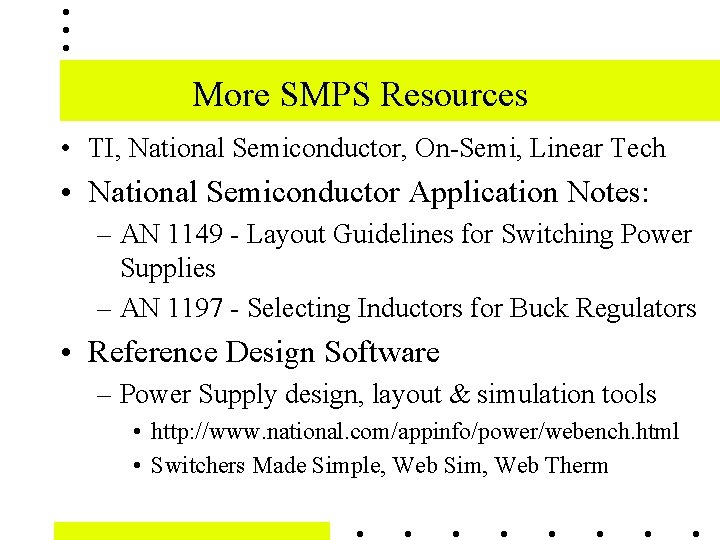
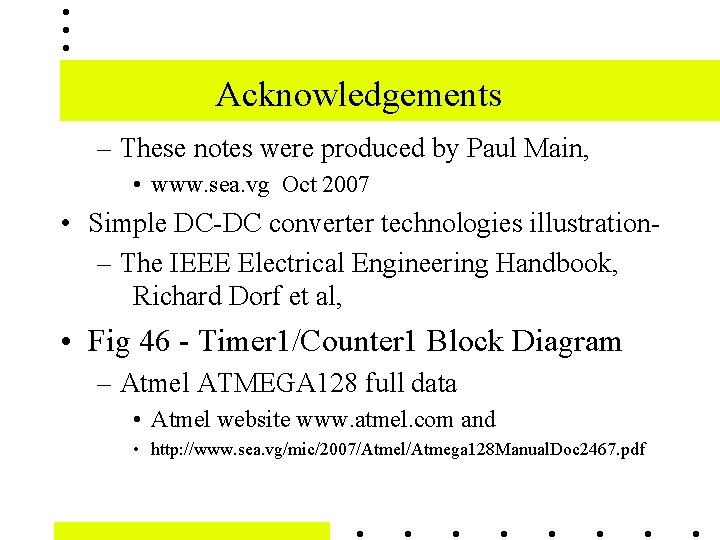
- Slides: 24
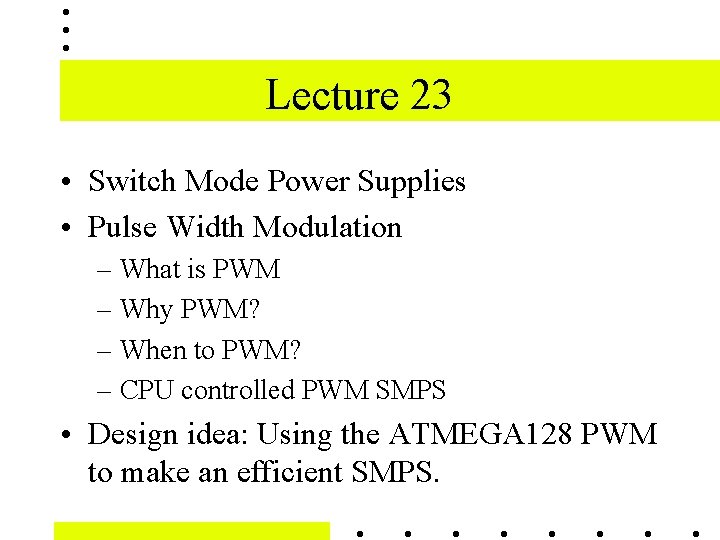
Lecture 23 • Switch Mode Power Supplies • Pulse Width Modulation – What is PWM – Why PWM? – When to PWM? – CPU controlled PWM SMPS • Design idea: Using the ATMEGA 128 PWM to make an efficient SMPS.
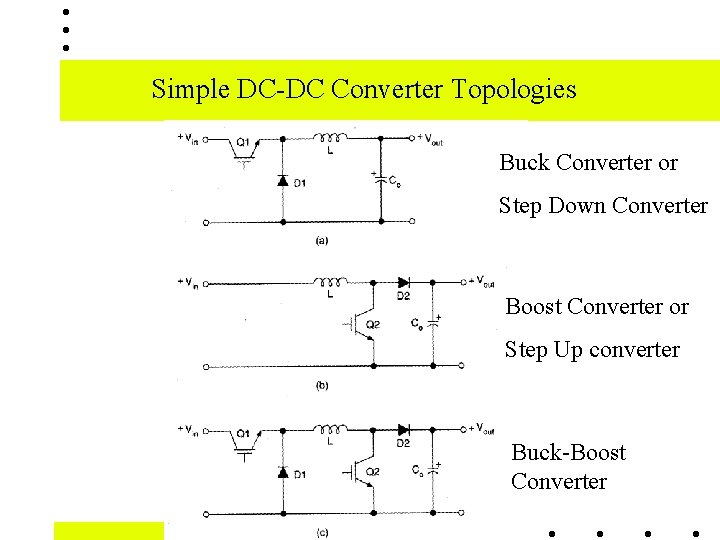
Simple DC-DC Converter Topologies Buck Converter or Step Down Converter Boost Converter or Step Up converter Buck-Boost Converter
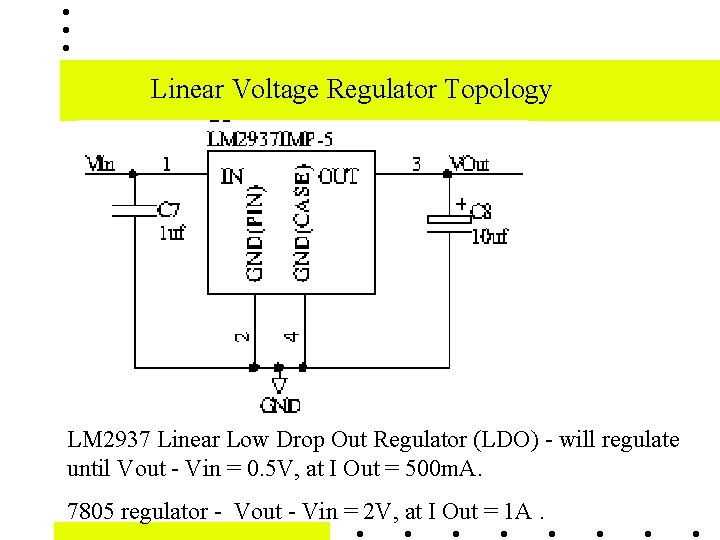
Linear Voltage Regulator Topology LM 2937 Linear Low Drop Out Regulator (LDO) - will regulate until Vout - Vin = 0. 5 V, at I Out = 500 m. A. 7805 regulator - Vout - Vin = 2 V, at I Out = 1 A.
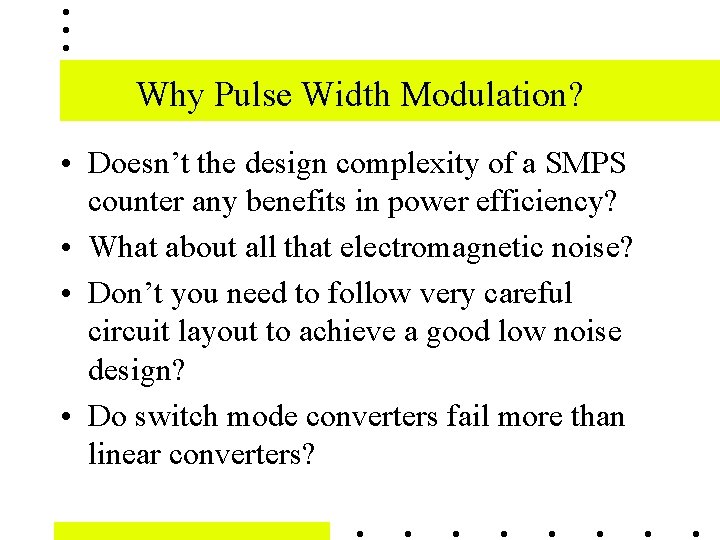
Why Pulse Width Modulation? • Doesn’t the design complexity of a SMPS counter any benefits in power efficiency? • What about all that electromagnetic noise? • Don’t you need to follow very careful circuit layout to achieve a good low noise design? • Do switch mode converters fail more than linear converters?
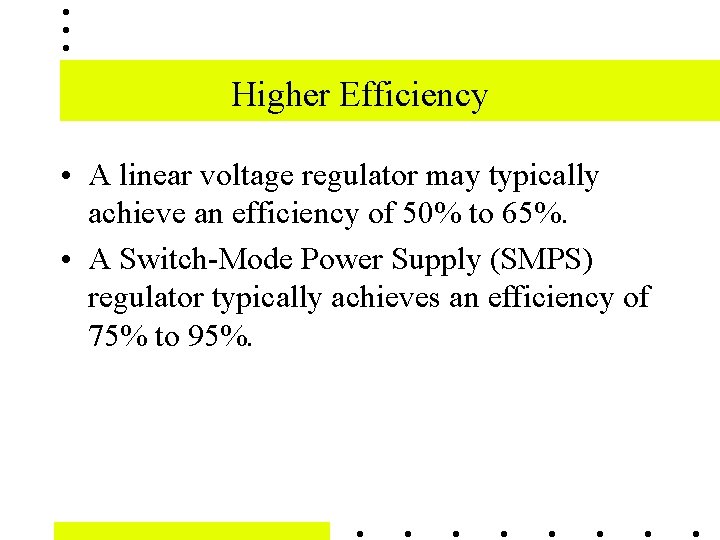
Higher Efficiency • A linear voltage regulator may typically achieve an efficiency of 50% to 65%. • A Switch-Mode Power Supply (SMPS) regulator typically achieves an efficiency of 75% to 95%.
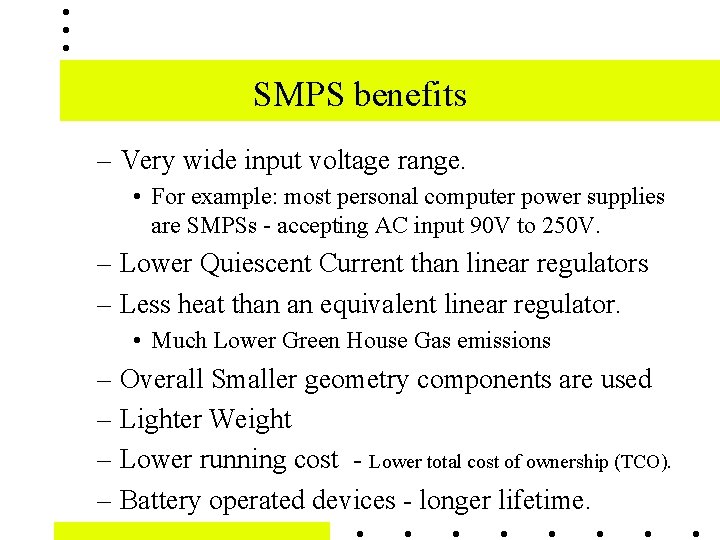
SMPS benefits – Very wide input voltage range. • For example: most personal computer power supplies are SMPSs - accepting AC input 90 V to 250 V. – Lower Quiescent Current than linear regulators – Less heat than an equivalent linear regulator. • Much Lower Green House Gas emissions – Overall Smaller geometry components are used – Lighter Weight – Lower running cost - Lower total cost of ownership (TCO). – Battery operated devices - longer lifetime.
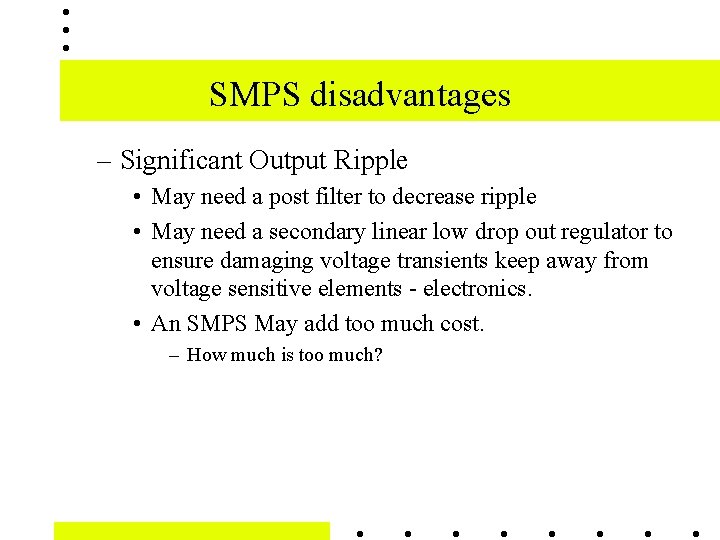
SMPS disadvantages – Significant Output Ripple • May need a post filter to decrease ripple • May need a secondary linear low drop out regulator to ensure damaging voltage transients keep away from voltage sensitive elements - electronics. • An SMPS May add too much cost. – How much is too much?
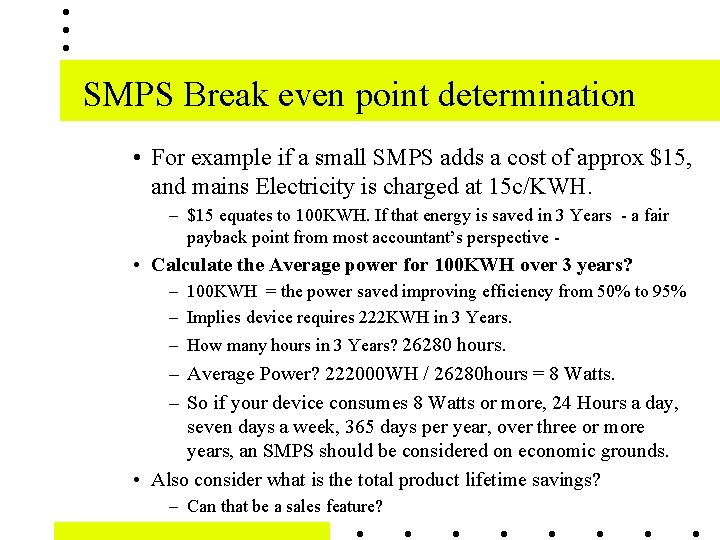
SMPS Break even point determination • For example if a small SMPS adds a cost of approx $15, and mains Electricity is charged at 15 c/KWH. – $15 equates to 100 KWH. If that energy is saved in 3 Years - a fair payback point from most accountant’s perspective - • Calculate the Average power for 100 KWH over 3 years? – 100 KWH = the power saved improving efficiency from 50% to 95% – Implies device requires 222 KWH in 3 Years. – How many hours in 3 Years? 26280 hours. – Average Power? 222000 WH / 26280 hours = 8 Watts. – So if your device consumes 8 Watts or more, 24 Hours a day, seven days a week, 365 days per year, over three or more years, an SMPS should be considered on economic grounds. • Also consider what is the total product lifetime savings? – Can that be a sales feature?
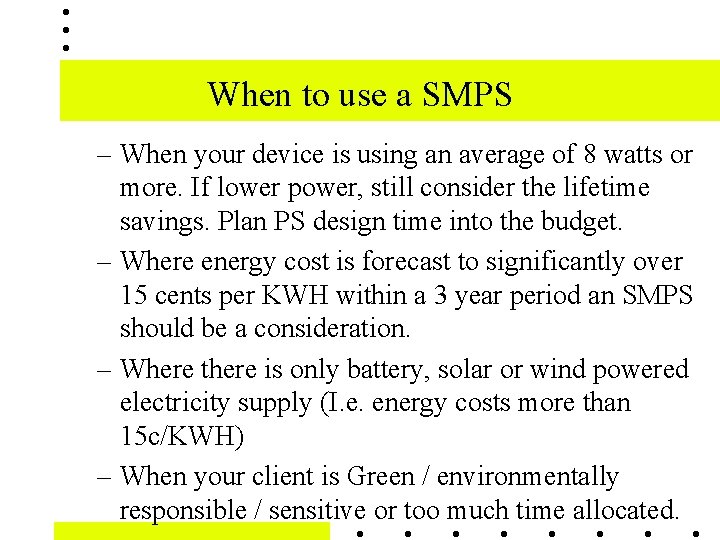
When to use a SMPS – When your device is using an average of 8 watts or more. If lower power, still consider the lifetime savings. Plan PS design time into the budget. – Where energy cost is forecast to significantly over 15 cents per KWH within a 3 year period an SMPS should be a consideration. – Where there is only battery, solar or wind powered electricity supply (I. e. energy costs more than 15 c/KWH) – When your client is Green / environmentally responsible / sensitive or too much time allocated.
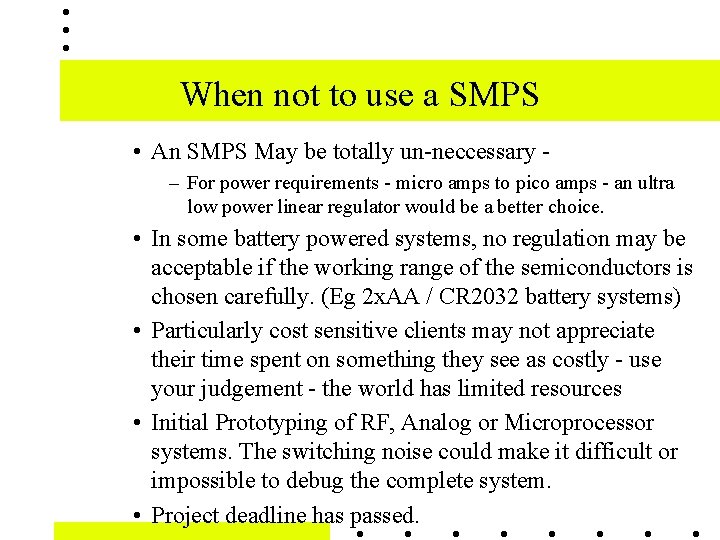
When not to use a SMPS • An SMPS May be totally un-neccessary – For power requirements - micro amps to pico amps - an ultra low power linear regulator would be a better choice. • In some battery powered systems, no regulation may be acceptable if the working range of the semiconductors is chosen carefully. (Eg 2 x. AA / CR 2032 battery systems) • Particularly cost sensitive clients may not appreciate their time spent on something they see as costly - use your judgement - the world has limited resources • Initial Prototyping of RF, Analog or Microprocessor systems. The switching noise could make it difficult or impossible to debug the complete system. • Project deadline has passed.
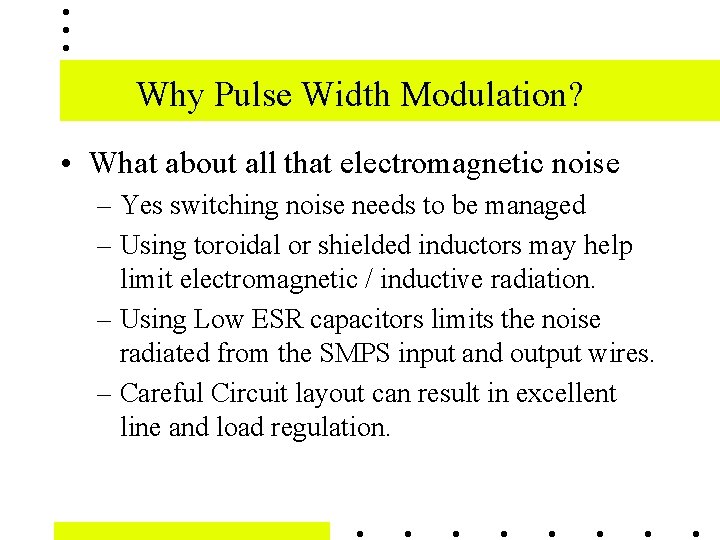
Why Pulse Width Modulation? • What about all that electromagnetic noise – Yes switching noise needs to be managed – Using toroidal or shielded inductors may help limit electromagnetic / inductive radiation. – Using Low ESR capacitors limits the noise radiated from the SMPS input and output wires. – Careful Circuit layout can result in excellent line and load regulation.
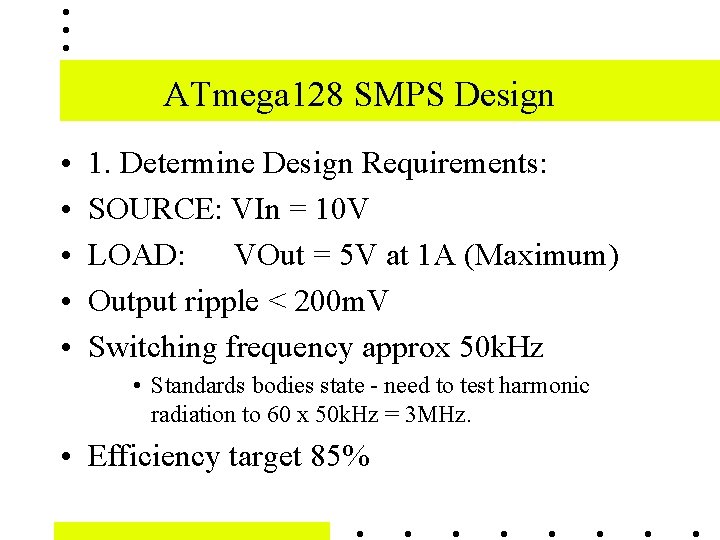
ATmega 128 SMPS Design • • • 1. Determine Design Requirements: SOURCE: VIn = 10 V LOAD: VOut = 5 V at 1 A (Maximum) Output ripple < 200 m. V Switching frequency approx 50 k. Hz • Standards bodies state - need to test harmonic radiation to 60 x 50 k. Hz = 3 MHz. • Efficiency target 85%
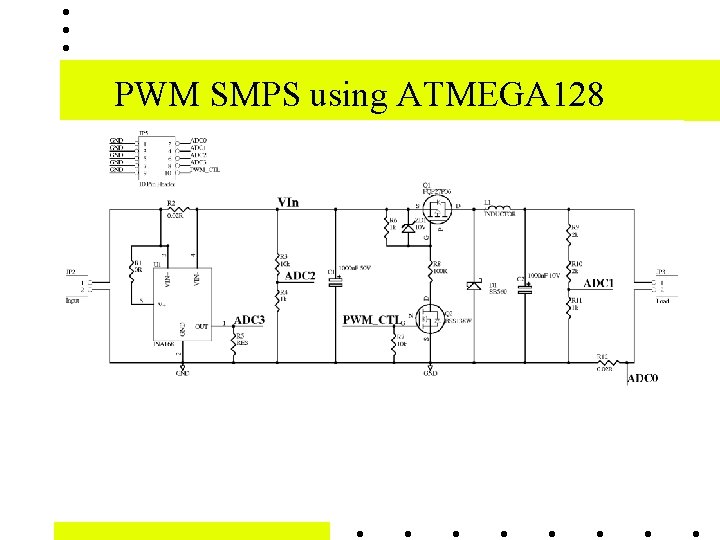
PWM SMPS using ATMEGA 128
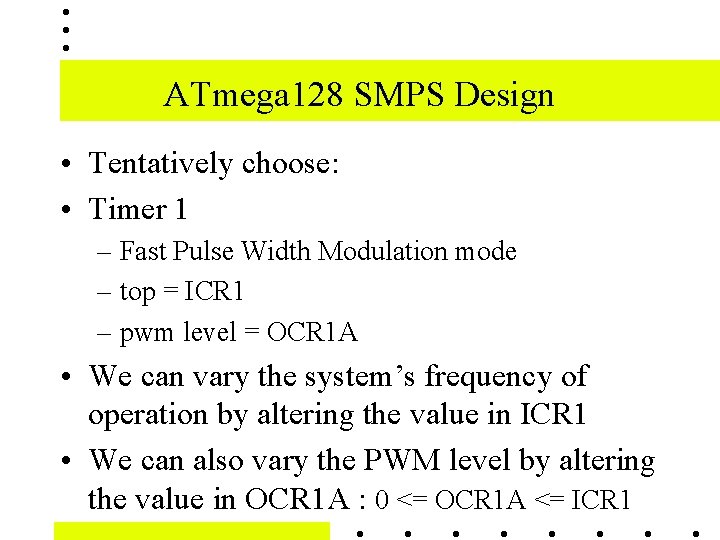
ATmega 128 SMPS Design • Tentatively choose: • Timer 1 – Fast Pulse Width Modulation mode – top = ICR 1 – pwm level = OCR 1 A • We can vary the system’s frequency of operation by altering the value in ICR 1 • We can also vary the PWM level by altering the value in OCR 1 A : 0 <= OCR 1 A <= ICR 1
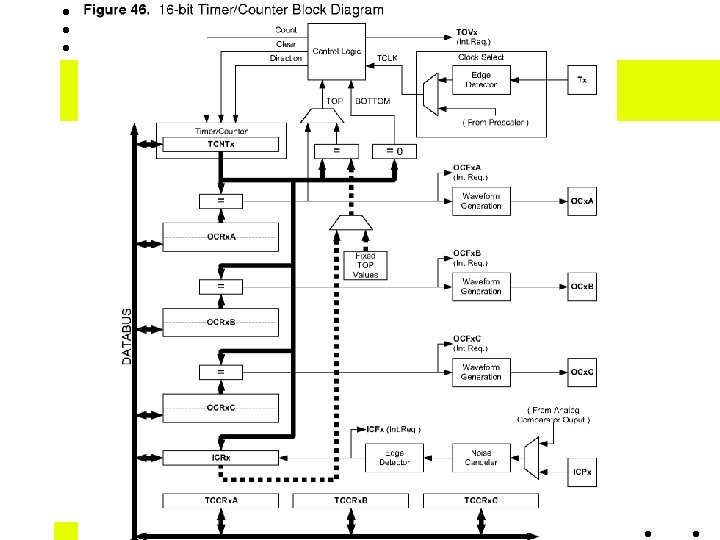
PWM SMPS using ATMEGA 128
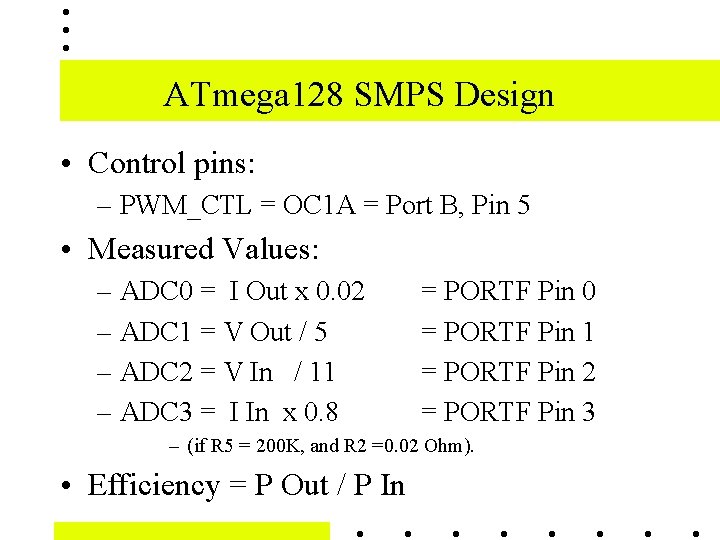
ATmega 128 SMPS Design • Control pins: – PWM_CTL = OC 1 A = Port B, Pin 5 • Measured Values: – ADC 0 = I Out x 0. 02 – ADC 1 = V Out / 5 – ADC 2 = V In / 11 – ADC 3 = I In x 0. 8 = PORTF Pin 0 = PORTF Pin 1 = PORTF Pin 2 = PORTF Pin 3 – (if R 5 = 200 K, and R 2 =0. 02 Ohm). • Efficiency = P Out / P In

PWM SMPS using ATMEGA 128
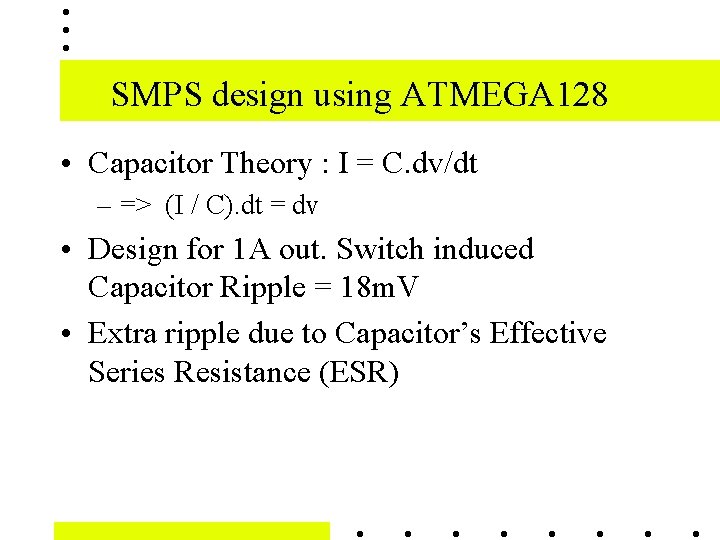
SMPS design using ATMEGA 128 • Capacitor Theory : I = C. dv/dt – => (I / C). dt = dv • Design for 1 A out. Switch induced Capacitor Ripple = 18 m. V • Extra ripple due to Capacitor’s Effective Series Resistance (ESR)
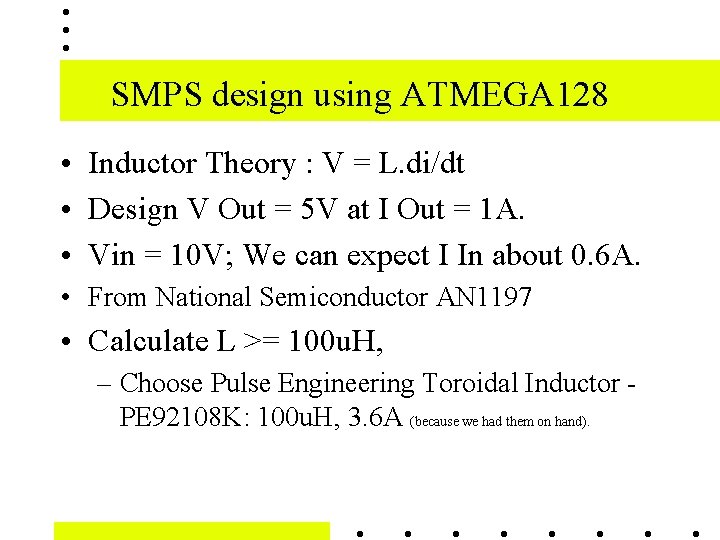
SMPS design using ATMEGA 128 • Inductor Theory : V = L. di/dt • Design V Out = 5 V at I Out = 1 A. • Vin = 10 V; We can expect I In about 0. 6 A. • From National Semiconductor AN 1197 • Calculate L >= 100 u. H, – Choose Pulse Engineering Toroidal Inductor PE 92108 K: 100 u. H, 3. 6 A (because we had them on hand).

SMPS design using ATMEGA 128 • So the circuit works by initially switching on transistor Q 2 (via node PWM_CTL) which in turn switches on Q 1. • Current flows through inductor L 1, and charges capacitor C 2, and provides the load on JP 3 with current. • Energy is stored in L 1’s magnetic core as current starts to rise. If the core saturates, current plateaus, and no more energy is stored.
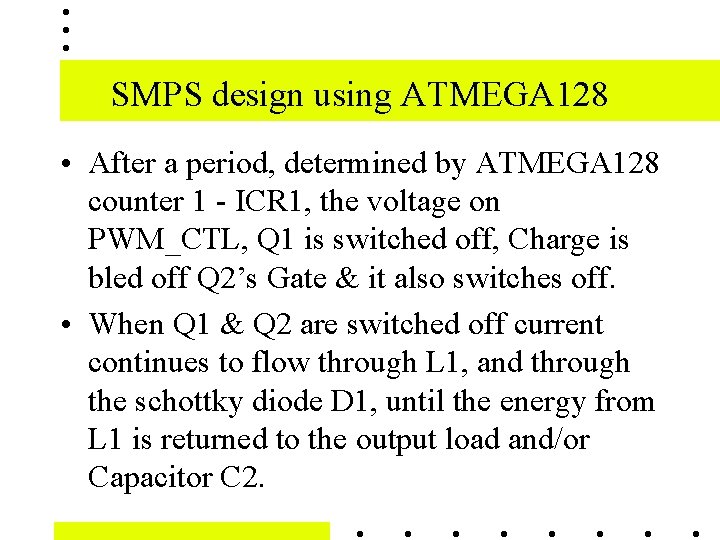
SMPS design using ATMEGA 128 • After a period, determined by ATMEGA 128 counter 1 - ICR 1, the voltage on PWM_CTL, Q 1 is switched off, Charge is bled off Q 2’s Gate & it also switches off. • When Q 1 & Q 2 are switched off current continues to flow through L 1, and through the schottky diode D 1, until the energy from L 1 is returned to the output load and/or Capacitor C 2.
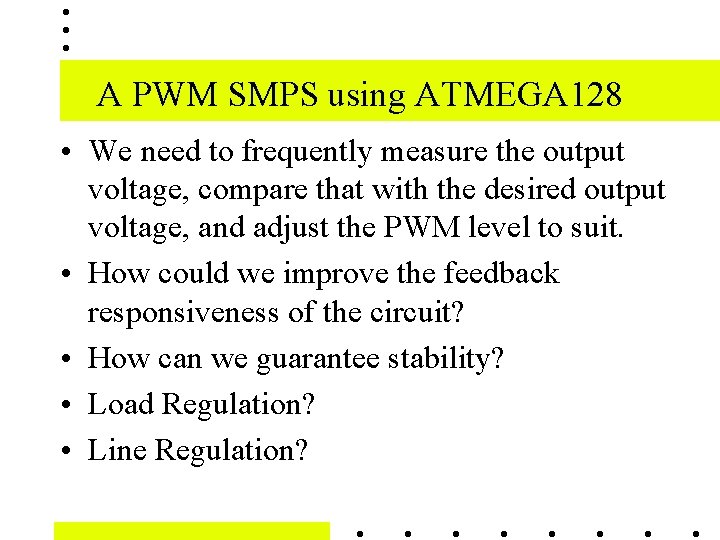
A PWM SMPS using ATMEGA 128 • We need to frequently measure the output voltage, compare that with the desired output voltage, and adjust the PWM level to suit. • How could we improve the feedback responsiveness of the circuit? • How can we guarantee stability? • Load Regulation? • Line Regulation?
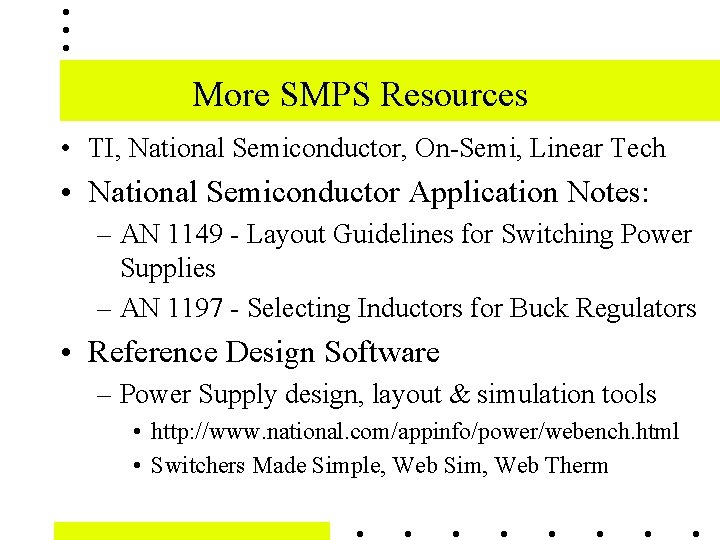
More SMPS Resources • TI, National Semiconductor, On-Semi, Linear Tech • National Semiconductor Application Notes: – AN 1149 - Layout Guidelines for Switching Power Supplies – AN 1197 - Selecting Inductors for Buck Regulators • Reference Design Software – Power Supply design, layout & simulation tools • http: //www. national. com/appinfo/power/webench. html • Switchers Made Simple, Web Sim, Web Therm
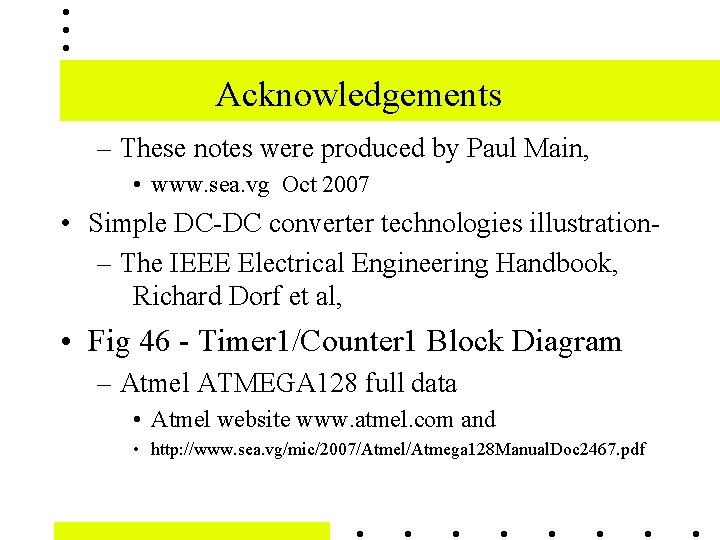
Acknowledgements – These notes were produced by Paul Main, • www. sea. vg Oct 2007 • Simple DC-DC converter technologies illustration– The IEEE Electrical Engineering Handbook, Richard Dorf et al, • Fig 46 - Timer 1/Counter 1 Block Diagram – Atmel ATMEGA 128 full data • Atmel website www. atmel. com and • http: //www. sea. vg/mic/2007/Atmel/Atmega 128 Manual. Doc 2467. pdf
Switch mode power supply lecture notes
What is a mode ultrasound
Buck switch mode power supply
Advantage of pulse width modulation
Duty cycle formula
Multiple pulse width modulation
What is pulse width modulation
In a banyan switch micro switch
Go switch working principle
Axial spray metal transfer definition
Commercial power supplies
Automated business power
01:640:244 lecture notes - lecture 15: plat, idah, farad
Switch mode converter
Power traiangle
Focus mode and diffuse mode
Mode địa chỉ tức thì là mode
Difference between real mode and virtual mode of 80386
Timer modes of 8051
Gartner mode 1 mode 2
Perbedaan (planning mode) dan (evolutionary mode)
8088 vs 8086
Vni4140
Power system dynamics and stability lecture notes
Zline 667-36