Introduction to Foamed Asphalt How is Foamed Asphalt
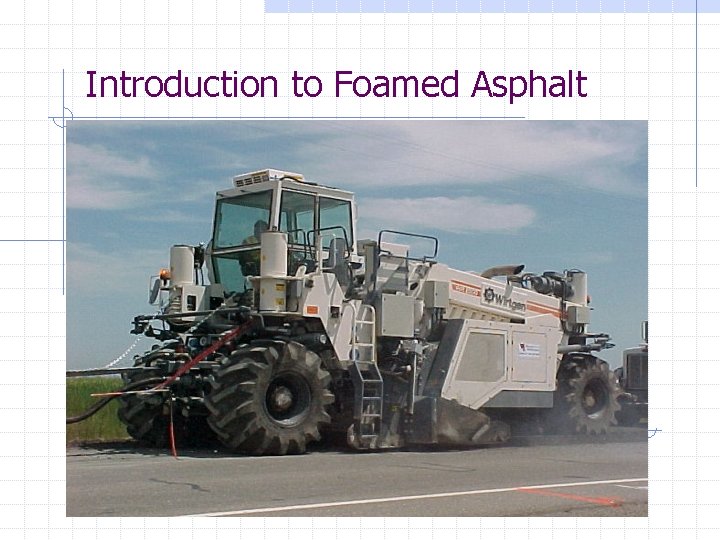
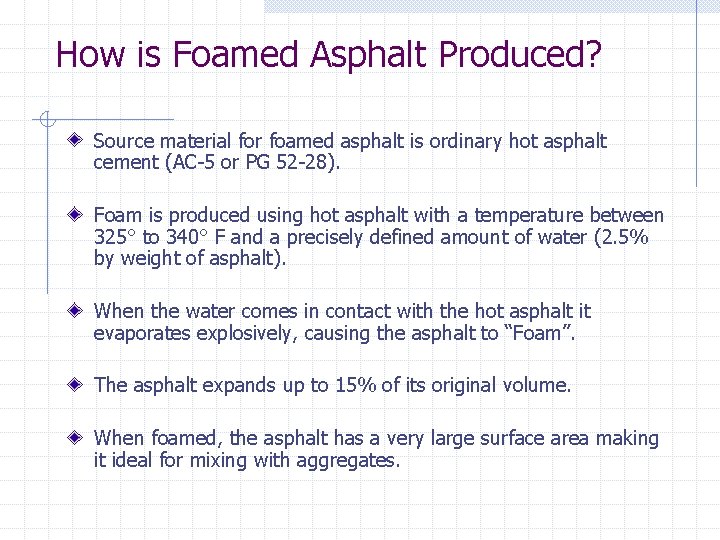
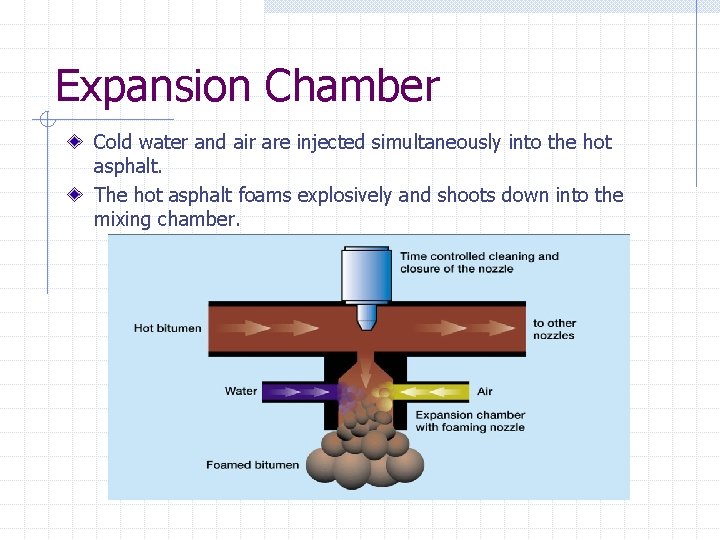
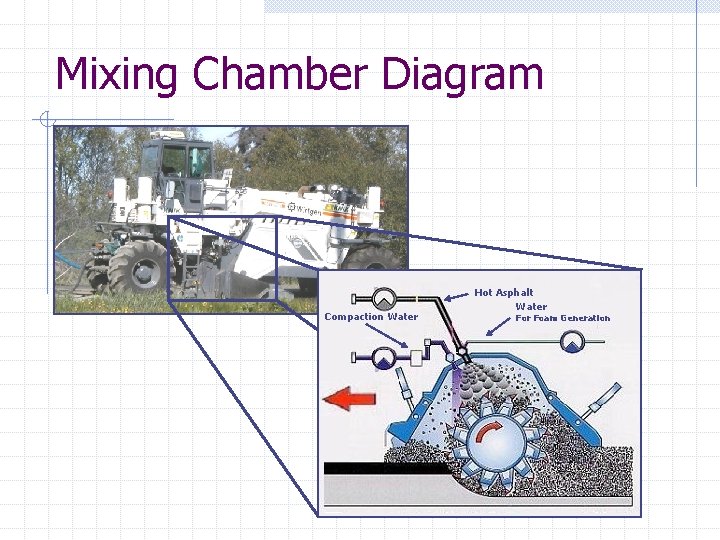
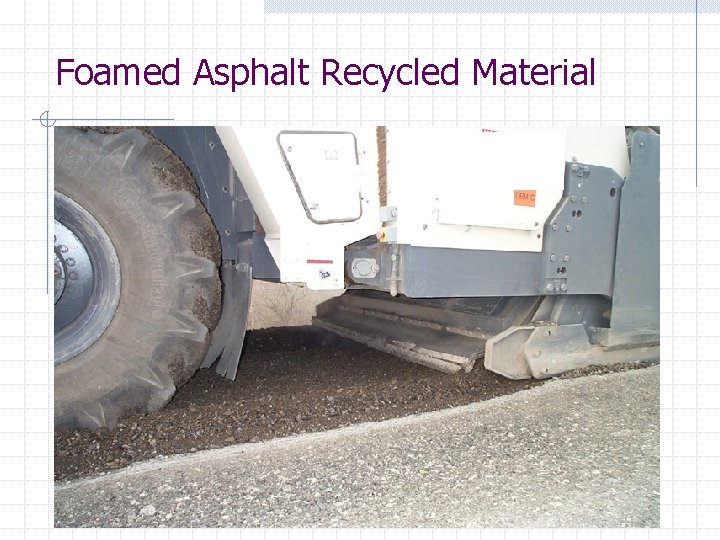
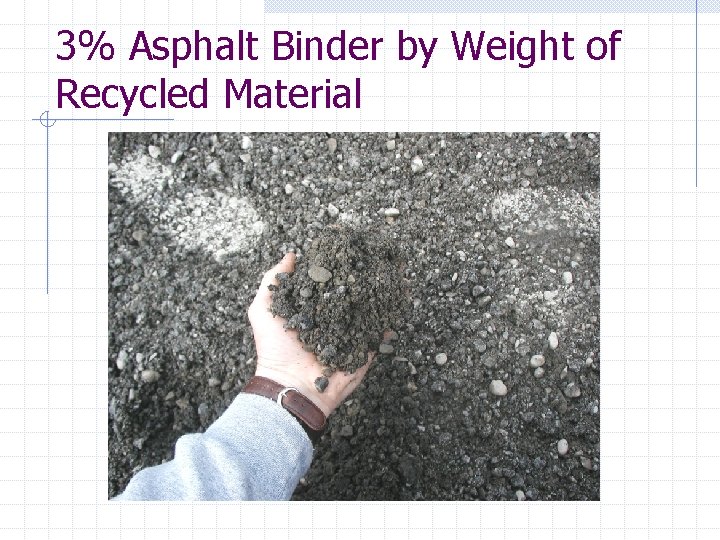
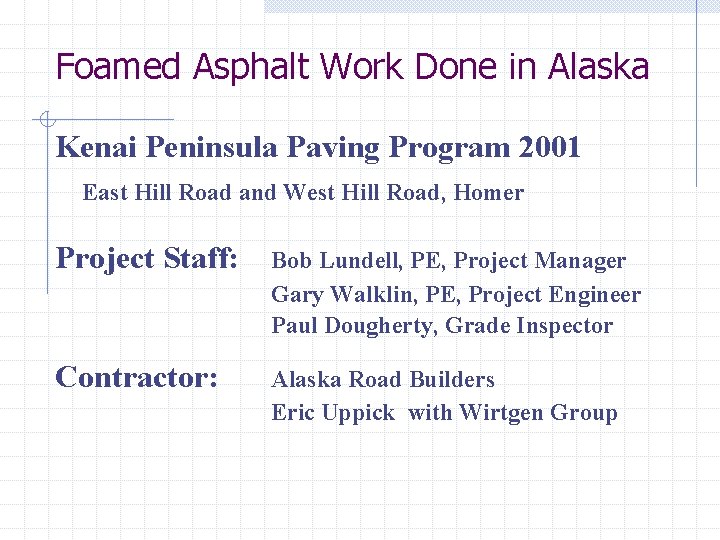
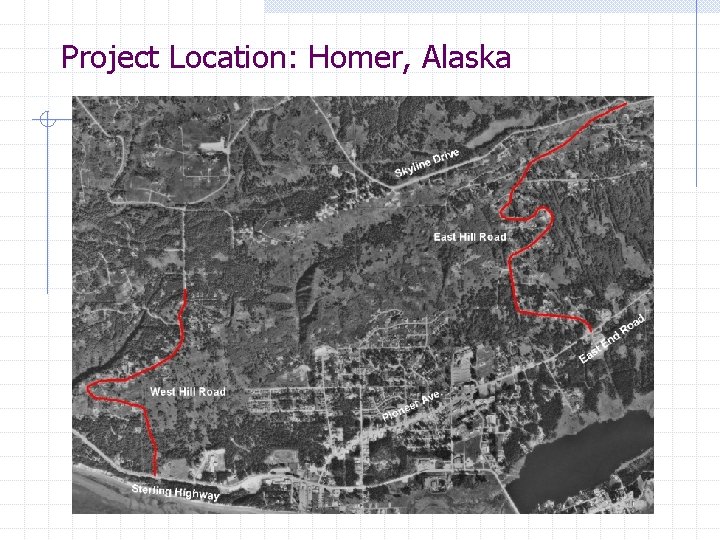
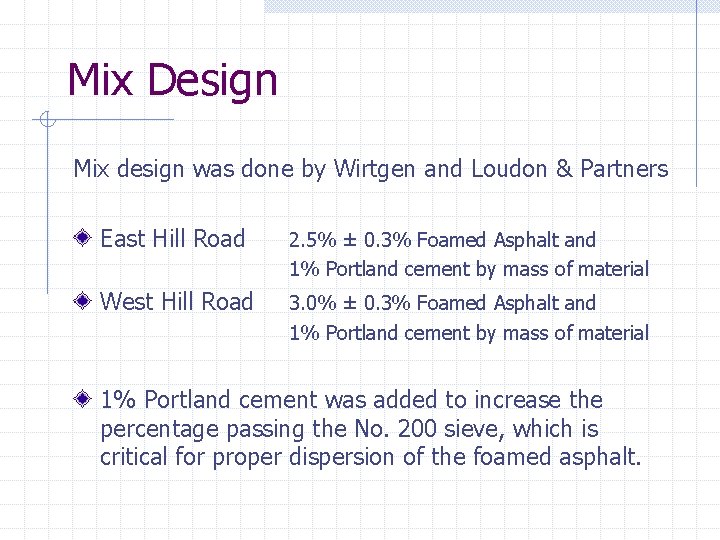
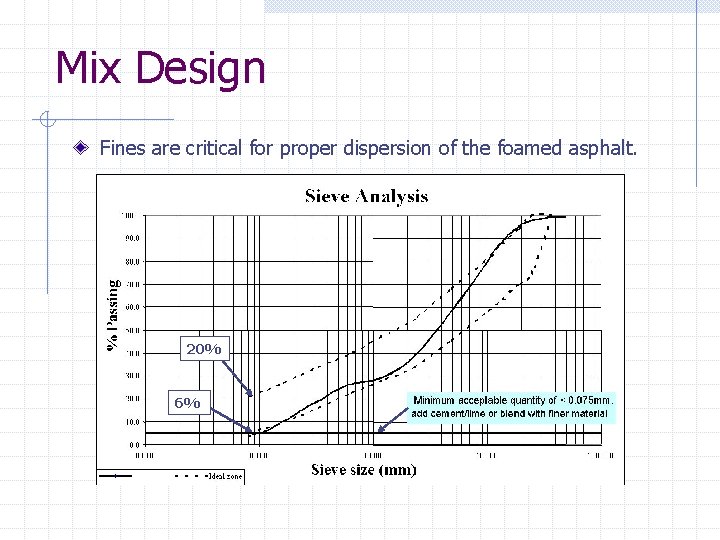
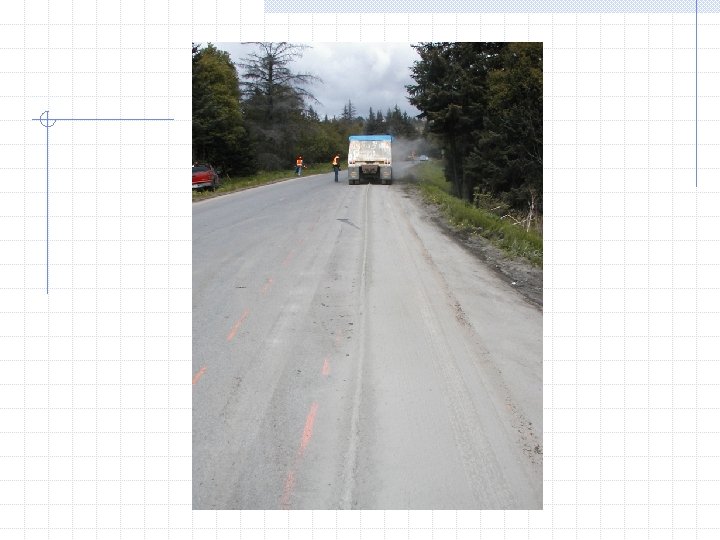
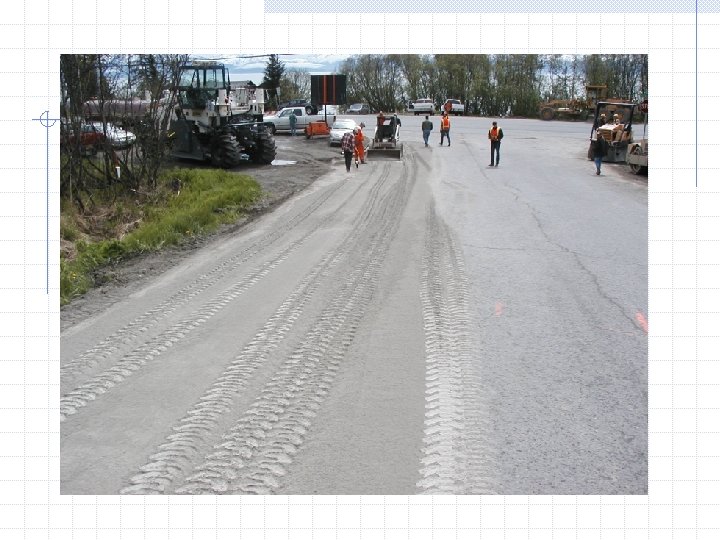
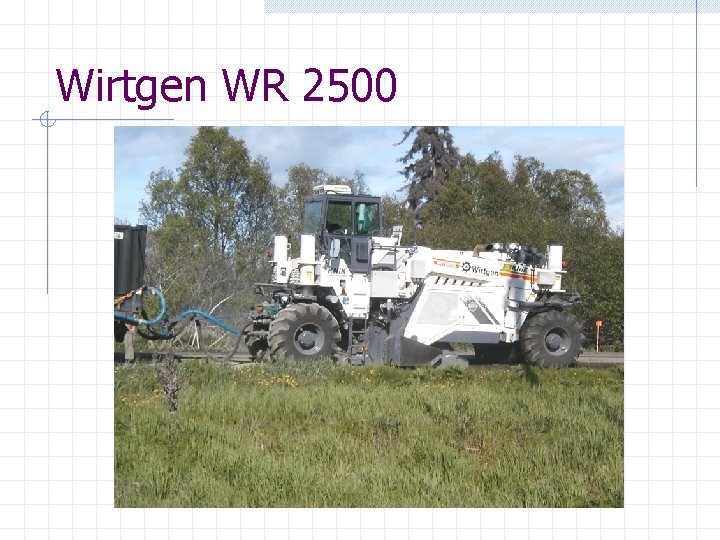
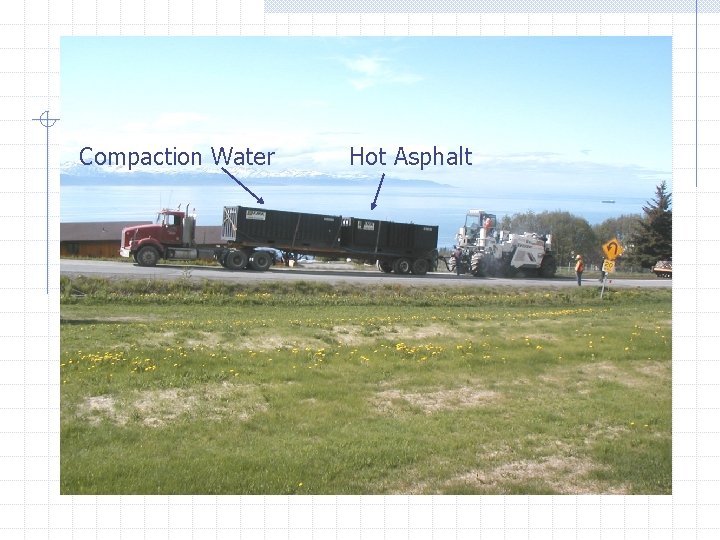
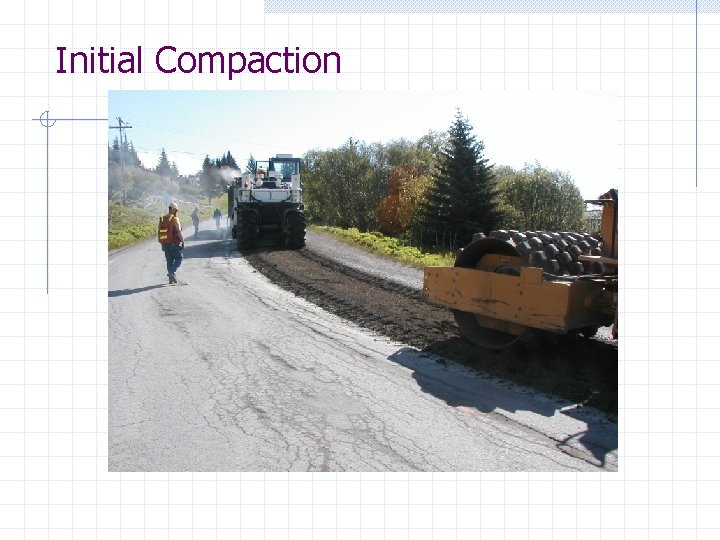
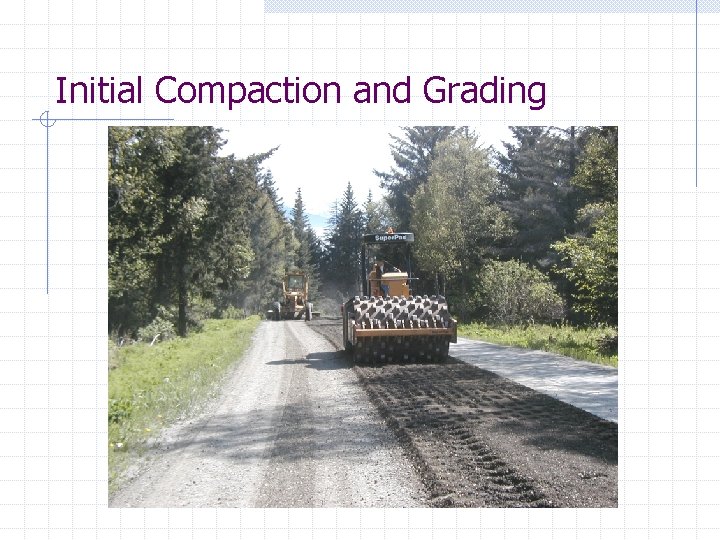
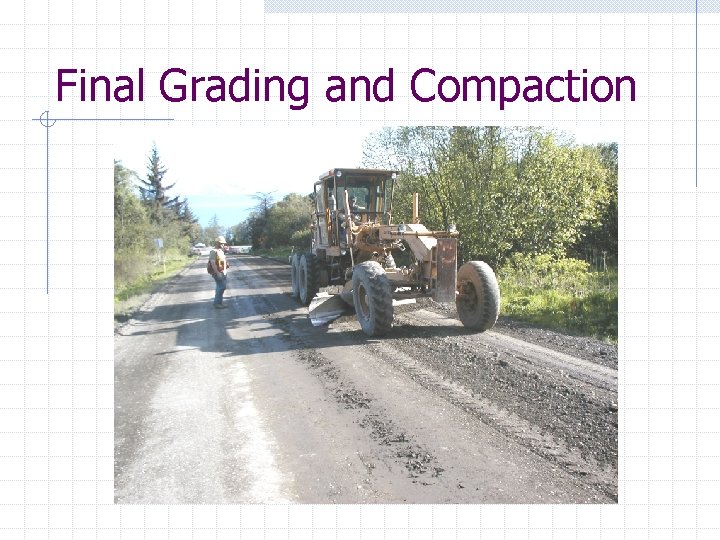
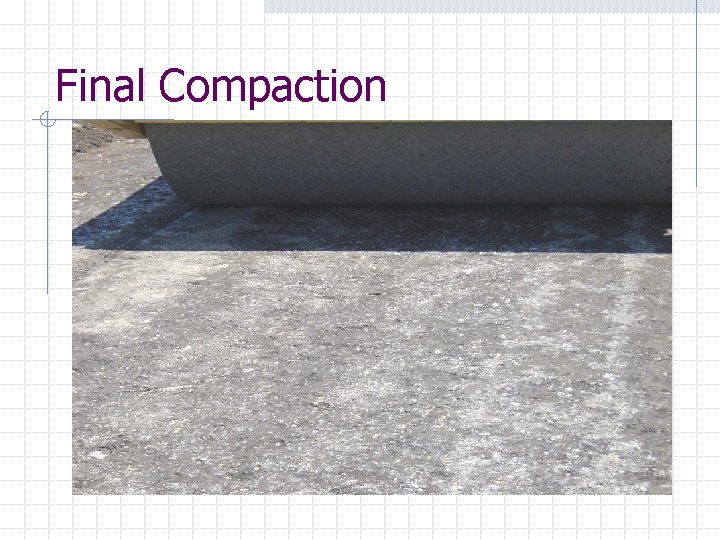
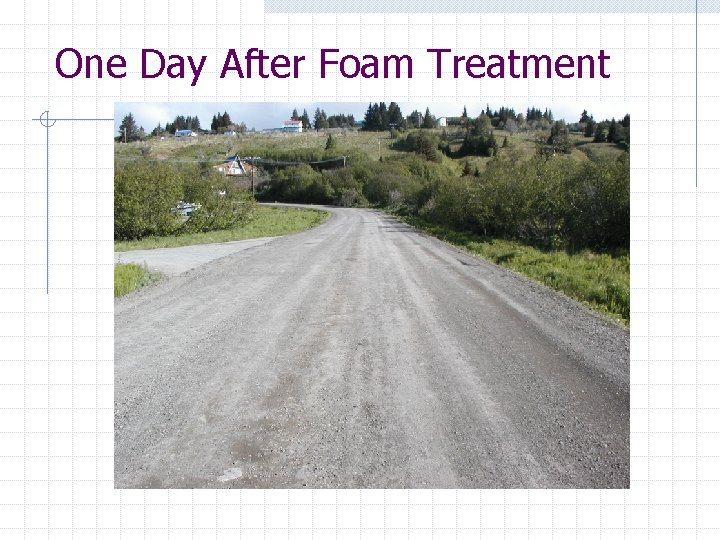
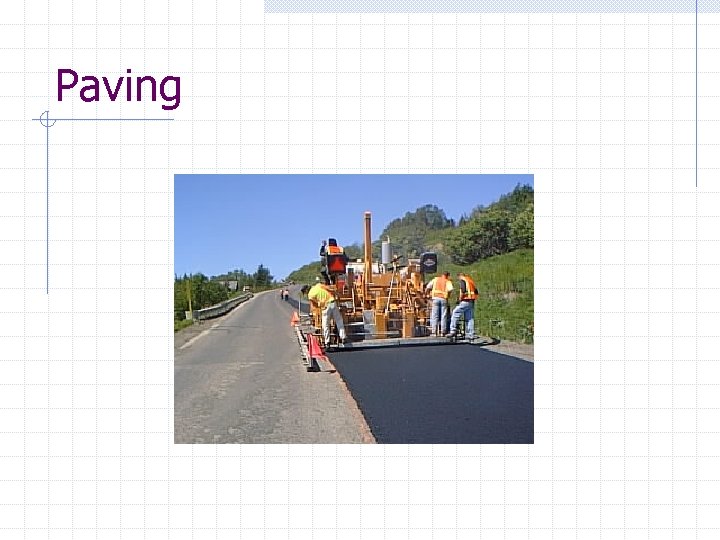
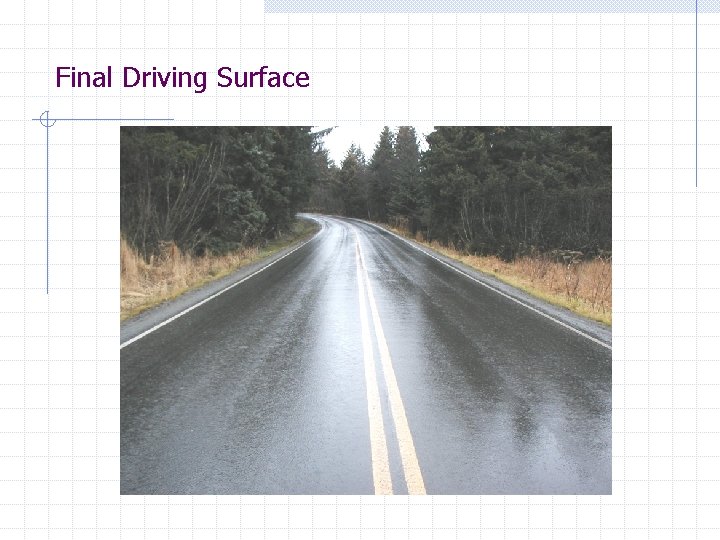
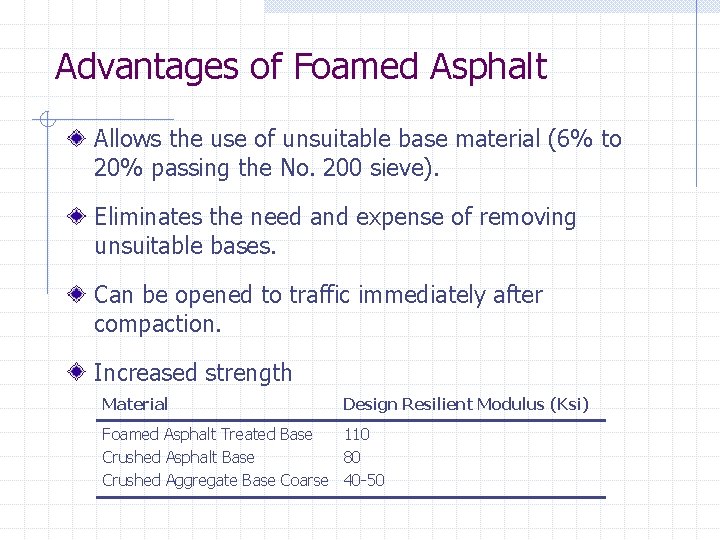
- Slides: 22
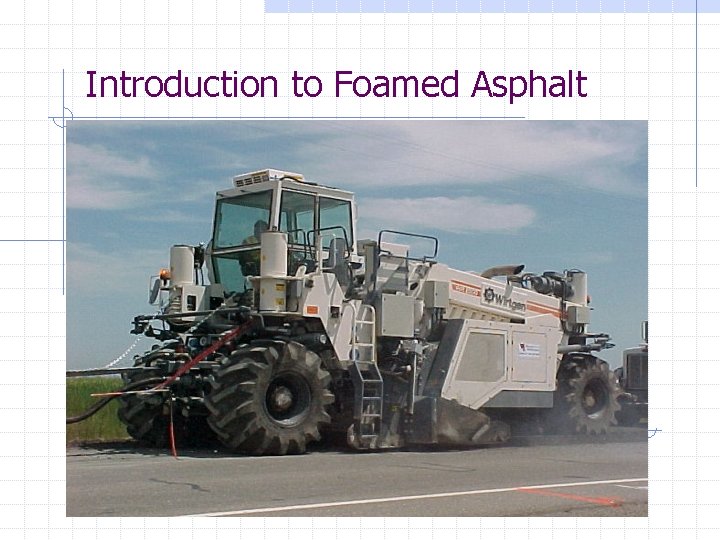
Introduction to Foamed Asphalt
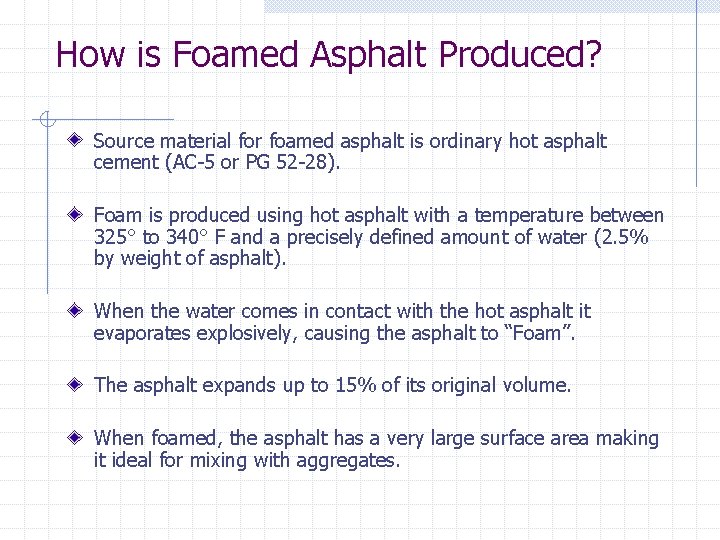
How is Foamed Asphalt Produced? Source material for foamed asphalt is ordinary hot asphalt cement (AC-5 or PG 52 -28). Foam is produced using hot asphalt with a temperature between 325° to 340° F and a precisely defined amount of water (2. 5% by weight of asphalt). When the water comes in contact with the hot asphalt it evaporates explosively, causing the asphalt to “Foam”. The asphalt expands up to 15% of its original volume. When foamed, the asphalt has a very large surface area making it ideal for mixing with aggregates.
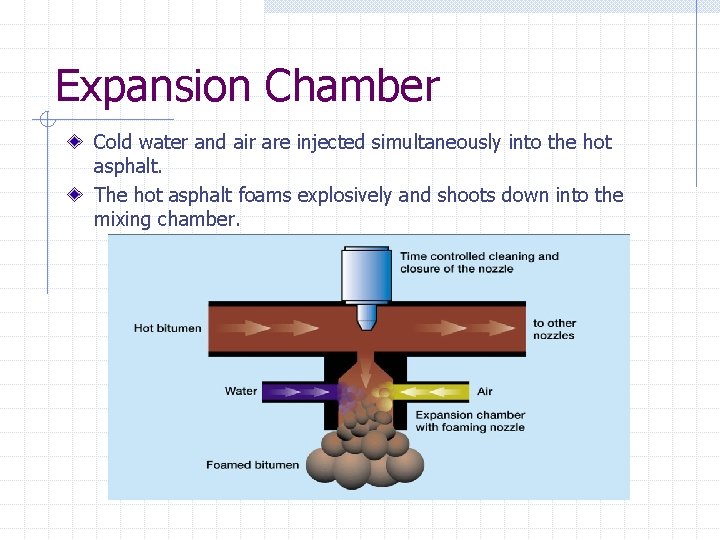
Expansion Chamber Cold water and air are injected simultaneously into the hot asphalt. The hot asphalt foams explosively and shoots down into the mixing chamber.
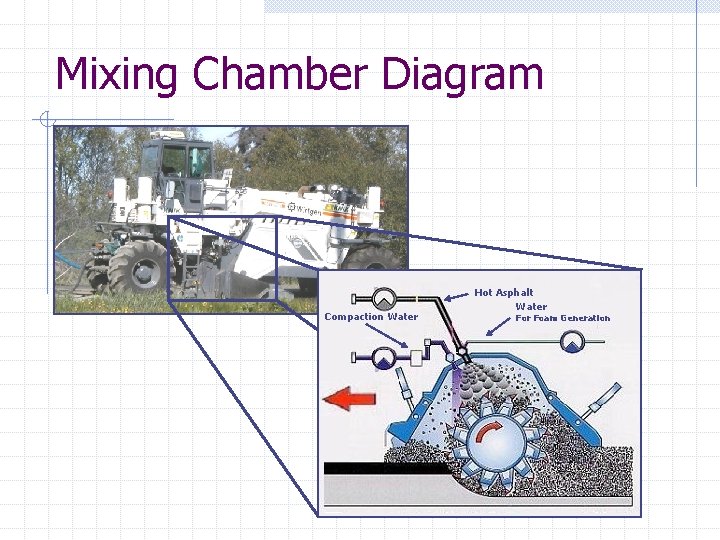
Mixing Chamber Diagram Compaction Water Hot Asphalt Water Foam Generation
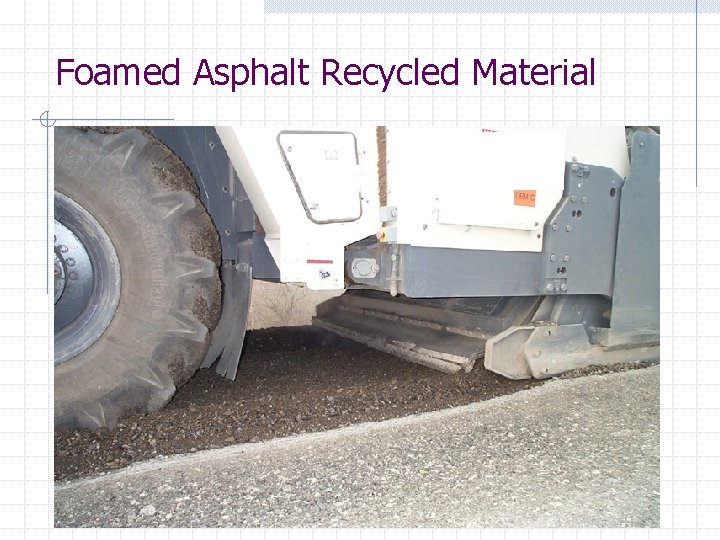
Foamed Asphalt Recycled Material
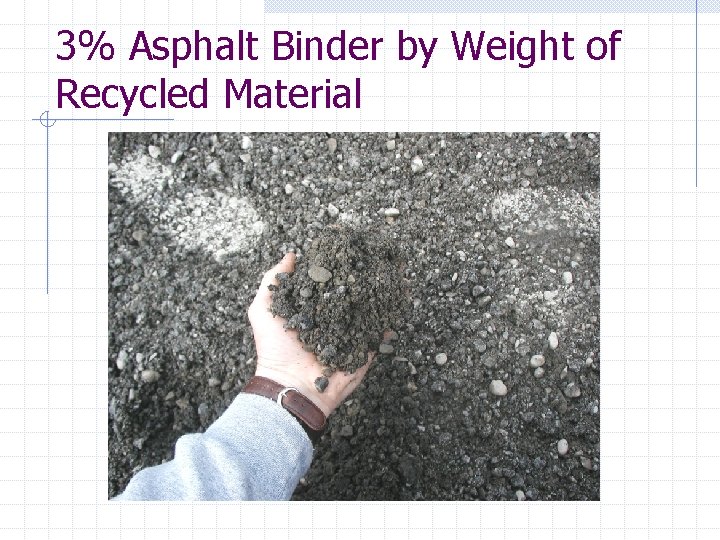
3% Asphalt Binder by Weight of Recycled Material
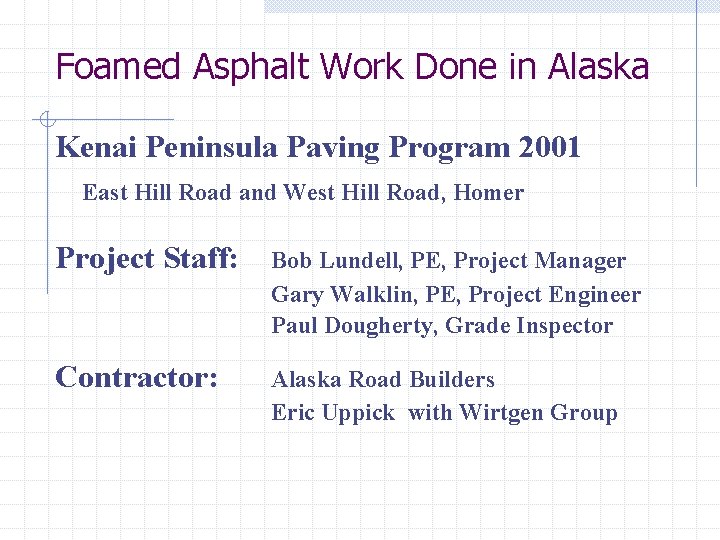
Foamed Asphalt Work Done in Alaska Kenai Peninsula Paving Program 2001 East Hill Road and West Hill Road, Homer Project Staff: Bob Lundell, PE, Project Manager Gary Walklin, PE, Project Engineer Paul Dougherty, Grade Inspector Contractor: Alaska Road Builders Eric Uppick with Wirtgen Group
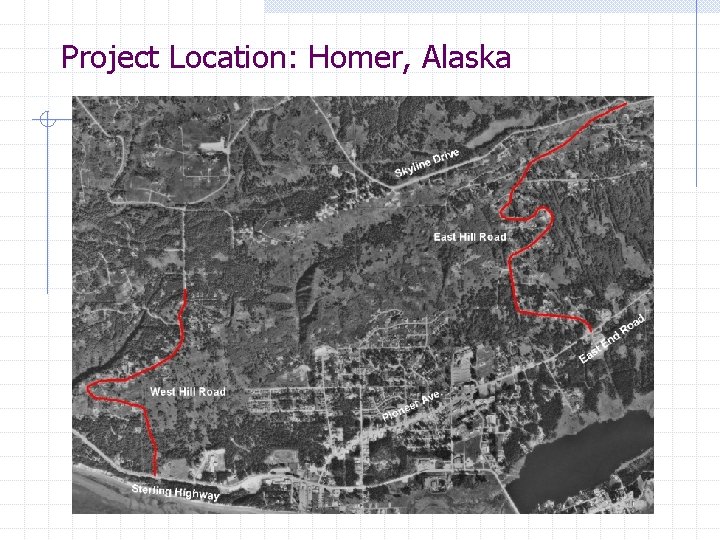
Project Location: Homer, Alaska
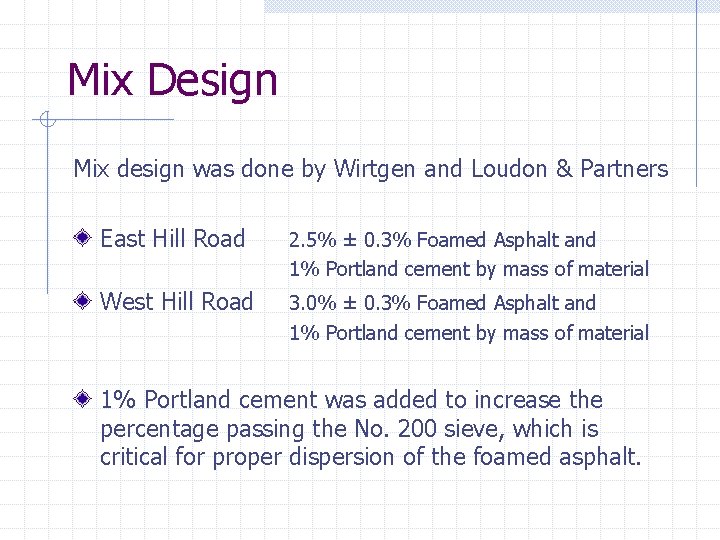
Mix Design Mix design was done by Wirtgen and Loudon & Partners East Hill Road 2. 5% ± 0. 3% Foamed Asphalt and 1% Portland cement by mass of material West Hill Road 3. 0% ± 0. 3% Foamed Asphalt and 1% Portland cement by mass of material 1% Portland cement was added to increase the percentage passing the No. 200 sieve, which is critical for proper dispersion of the foamed asphalt.
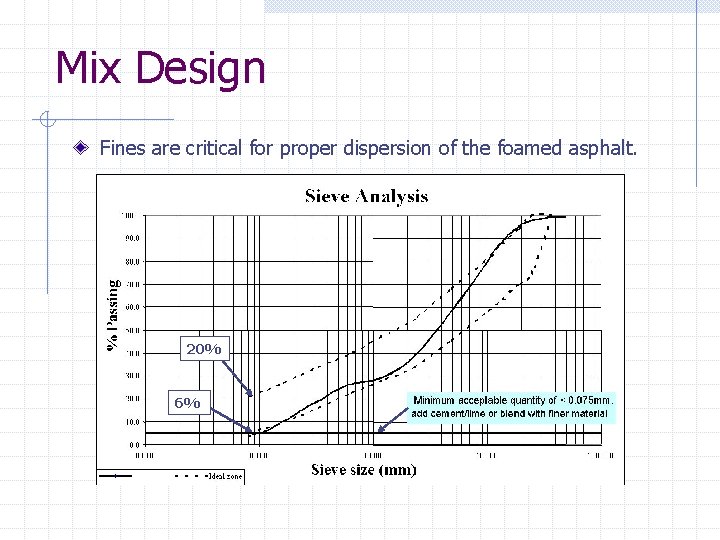
Mix Design Fines are critical for proper dispersion of the foamed asphalt. 20% 6%
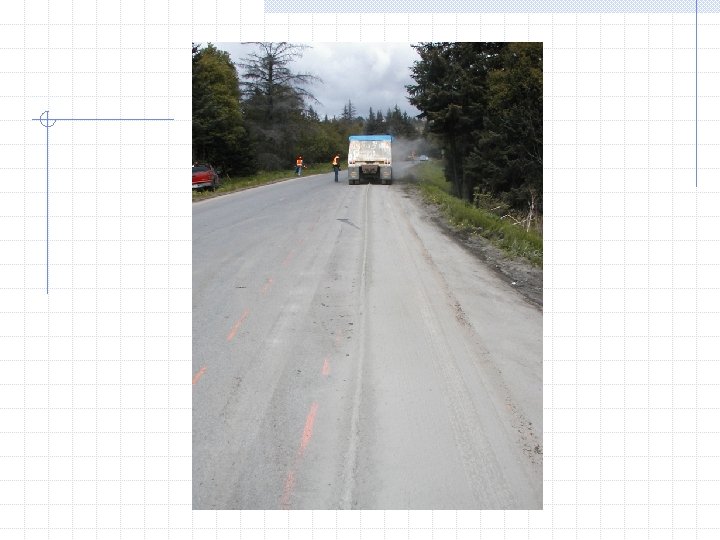
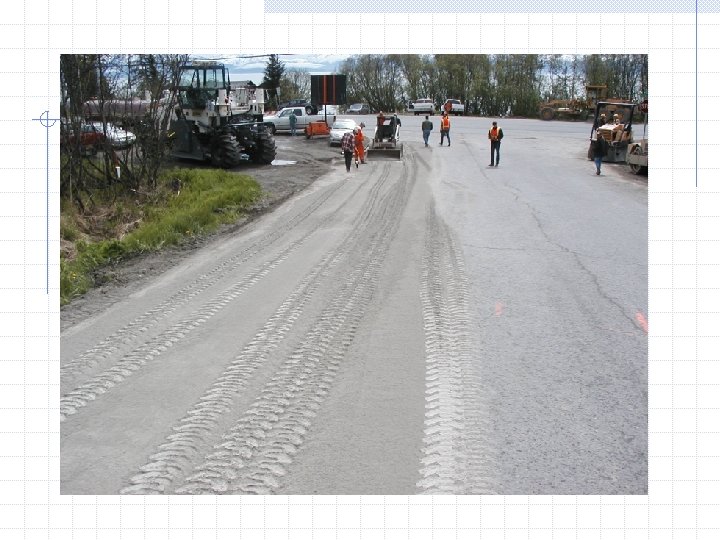
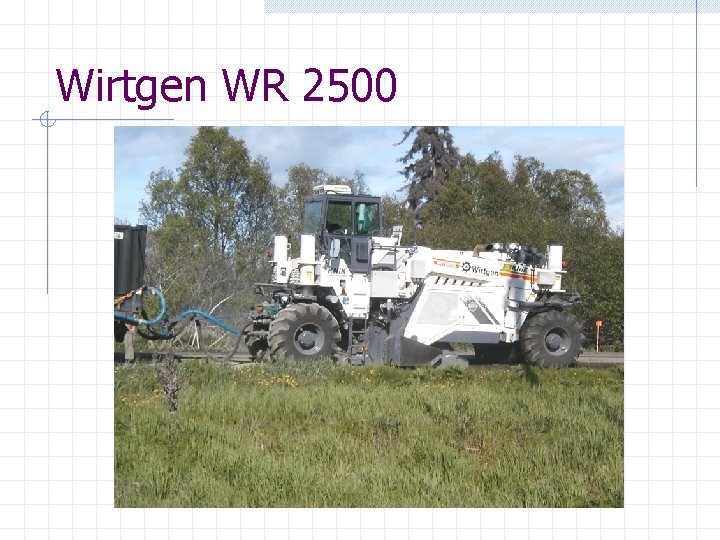
Wirtgen WR 2500
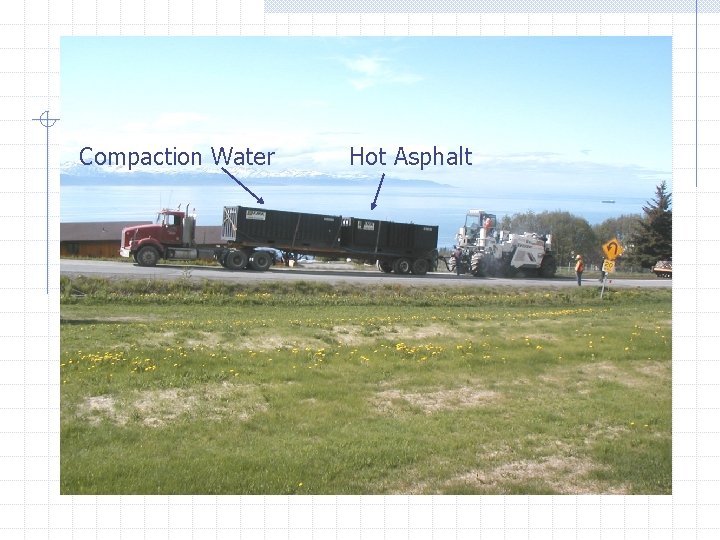
Compaction Water Hot Asphalt
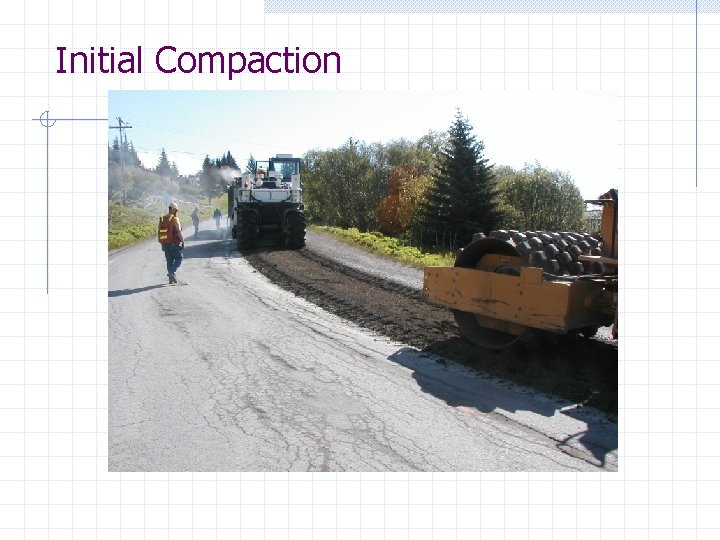
Initial Compaction
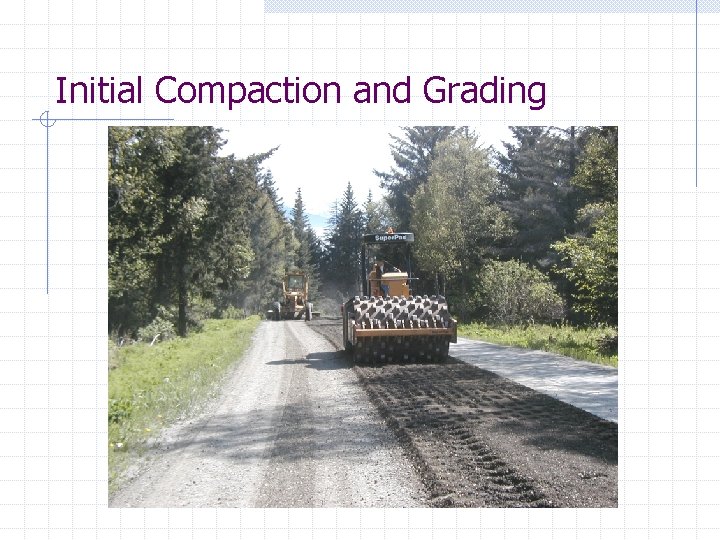
Initial Compaction and Grading
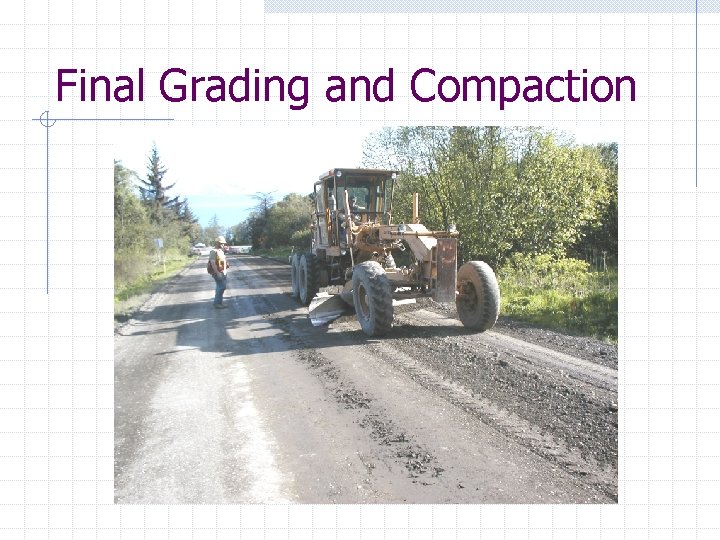
Final Grading and Compaction
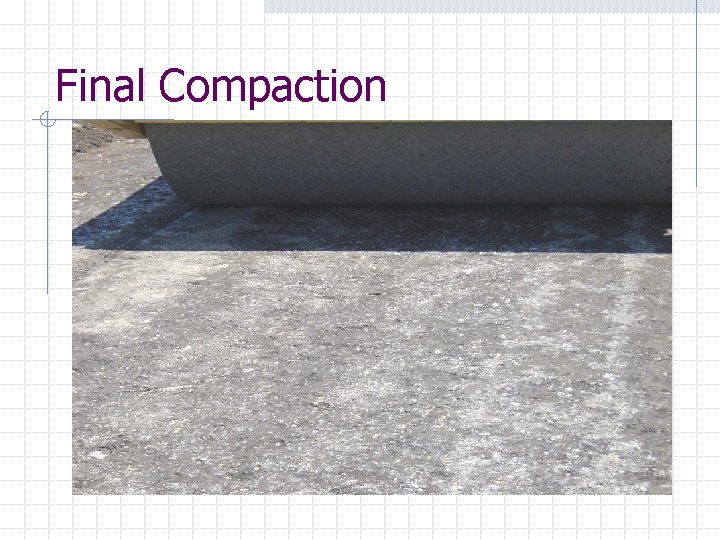
Final Compaction
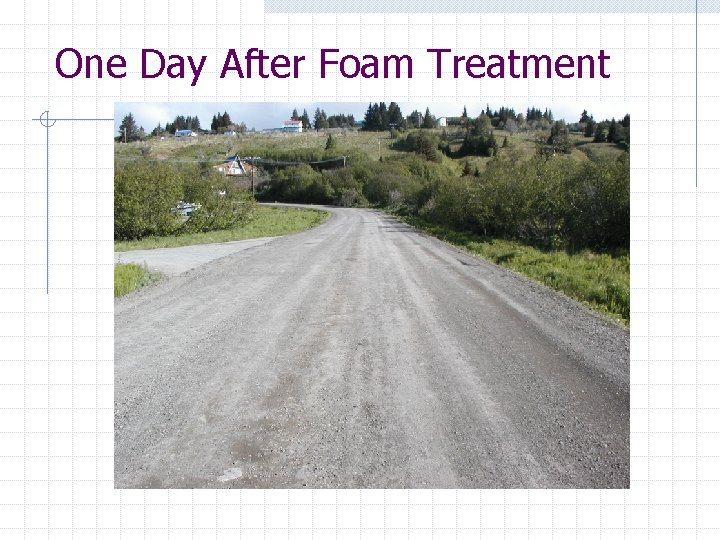
One Day After Foam Treatment
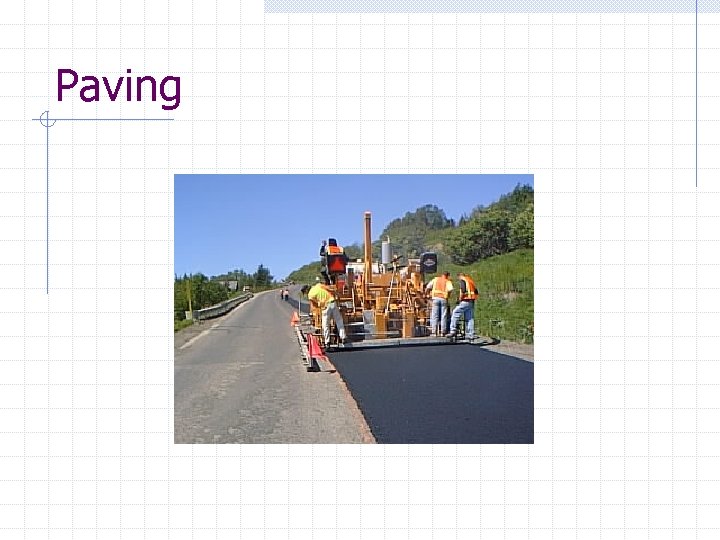
Paving
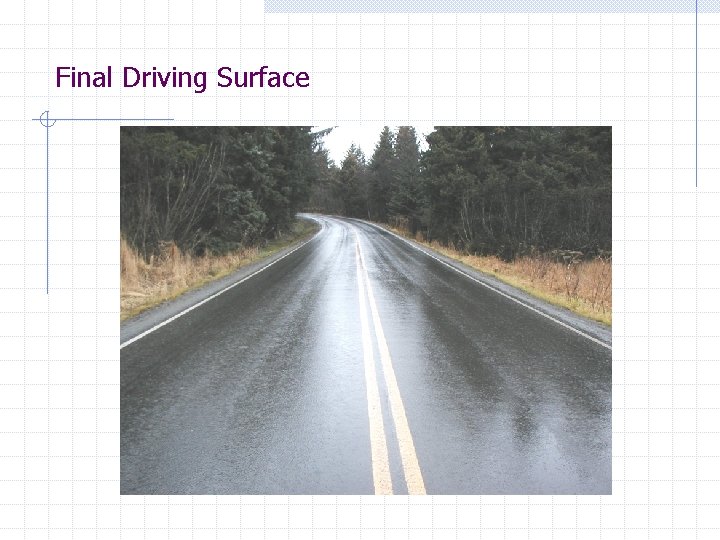
Final Driving Surface
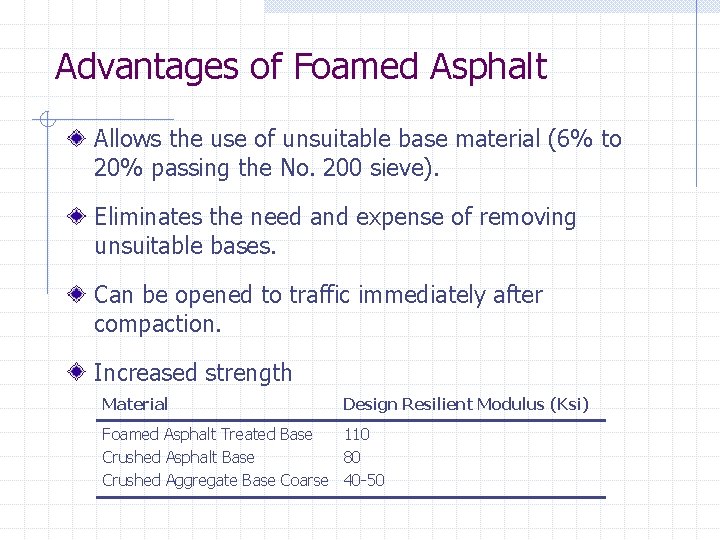
Advantages of Foamed Asphalt Allows the use of unsuitable base material (6% to 20% passing the No. 200 sieve). Eliminates the need and expense of removing unsuitable bases. Can be opened to traffic immediately after compaction. Increased strength Material Design Resilient Modulus (Ksi) Foamed Asphalt Treated Base 110 Crushed Asphalt Base 80 Crushed Aggregate Base Coarse 40 -50
Eabassoc
Asphalt pavement design example
Asphalt pavement design example
Asphalt institute
Asphalt pavement design example
Asphalt pavement design example
Airport mix asphalt
Asphalt rolling pattern
Capa asphalt
Warm mix asphalt
Core
Quiet pavement
Pete's absolute asphalt
Alabama asphalt pavement association
Bulldosing
Contained rock asphalt mat
What is this sing
China nonionic asphalt emulsifier
Asphalt base layer
Nchrp 9-60
S&b asphalt
Determann asphalt
Shingle recycling near me