Intro to Mapo Resource Recovery Facility 2012 11
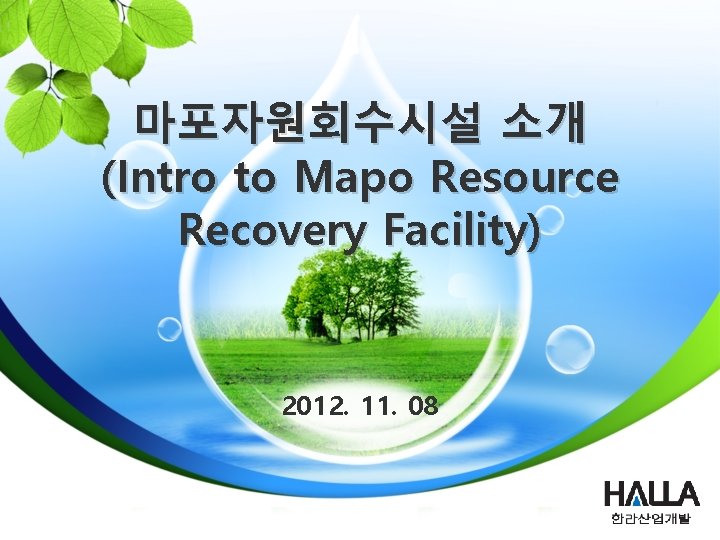
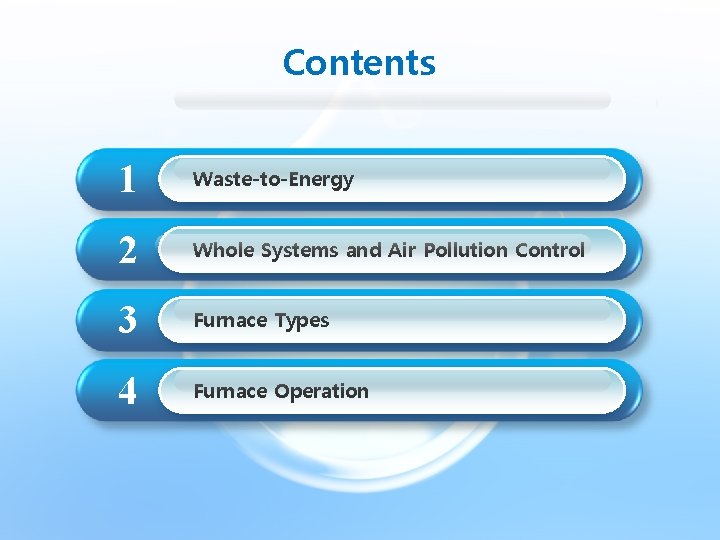
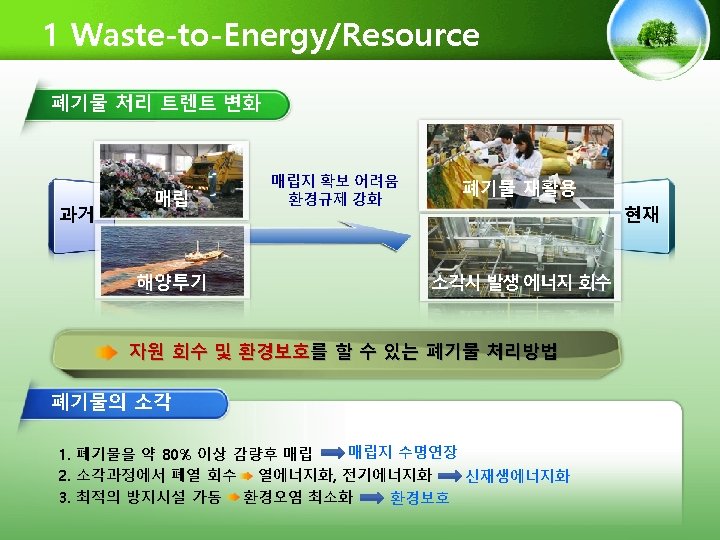
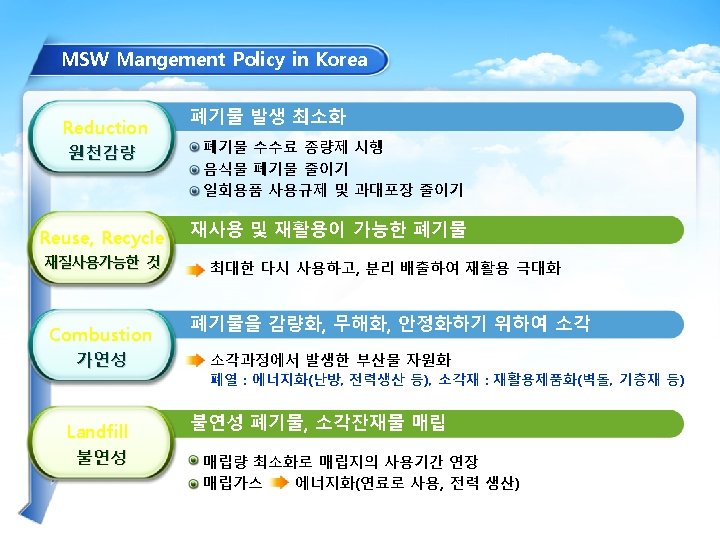
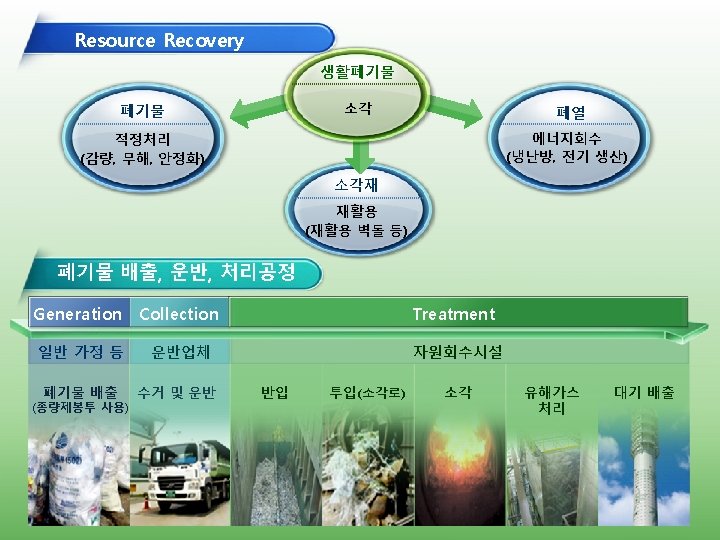
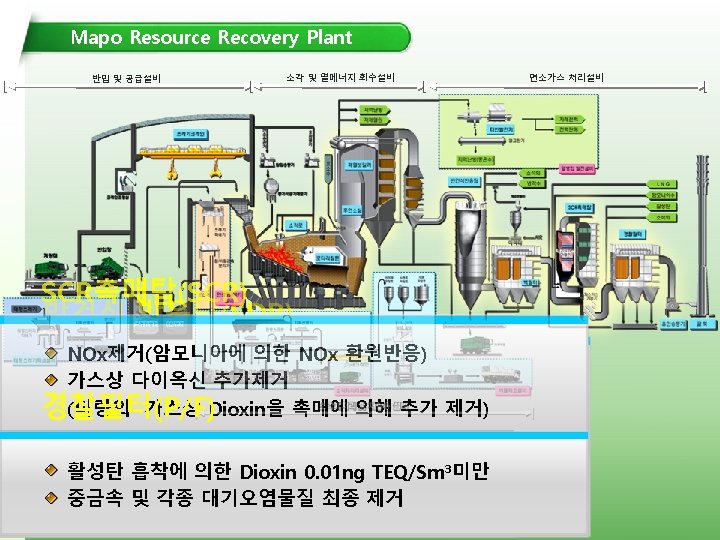
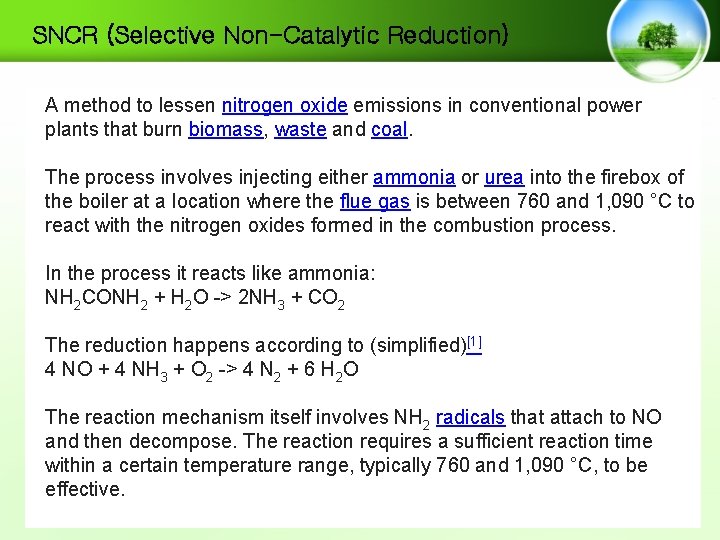
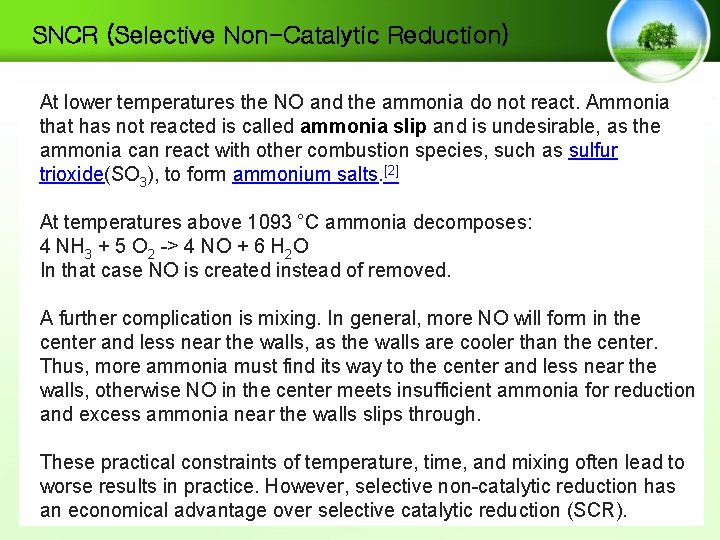
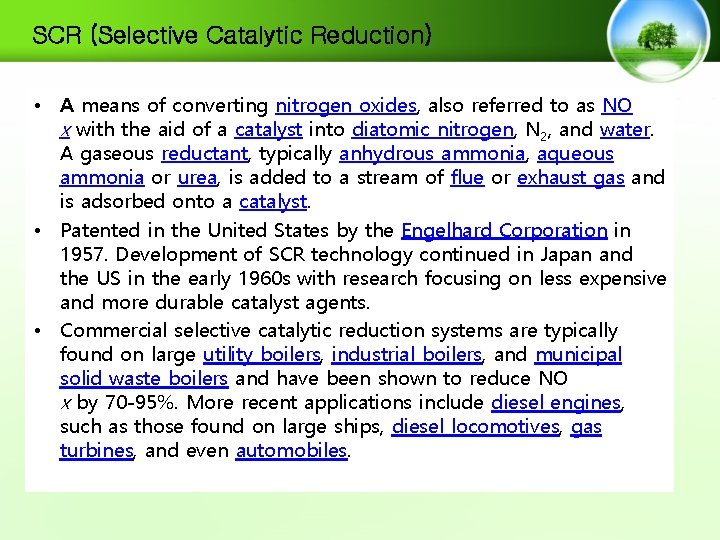
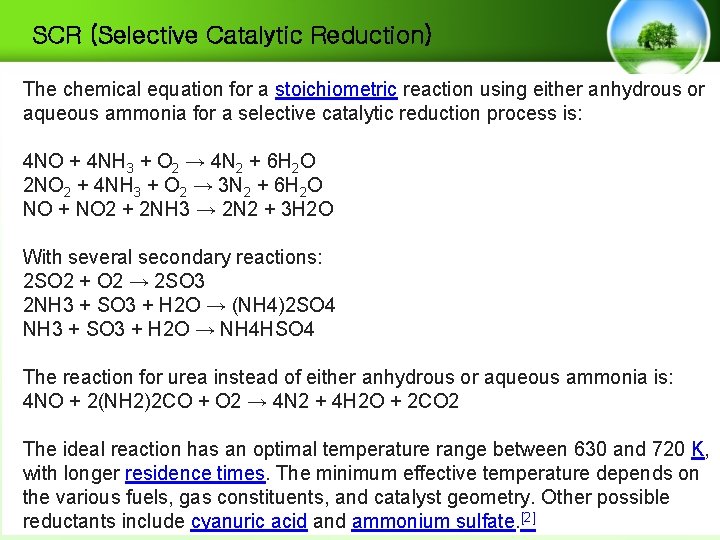
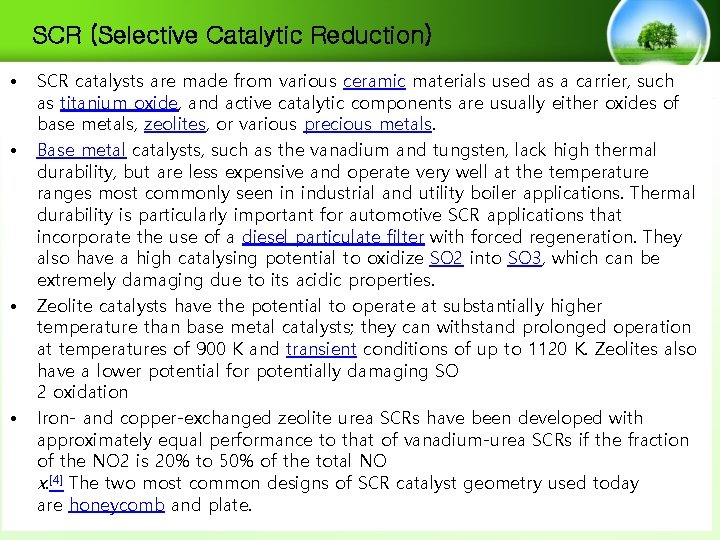
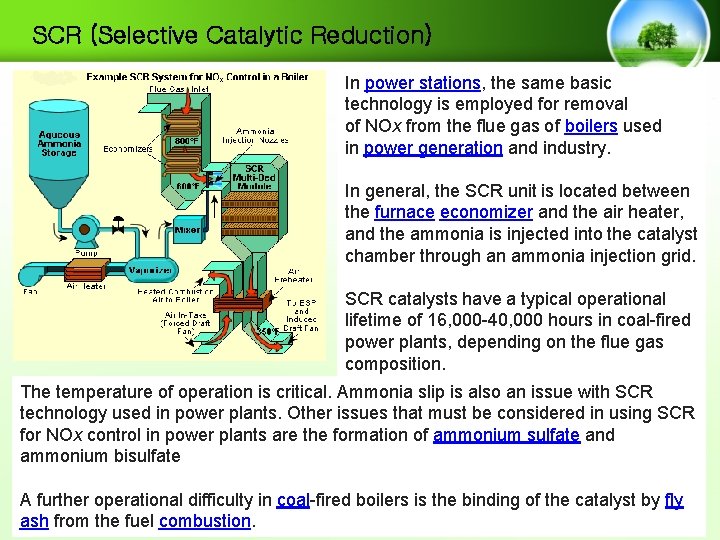
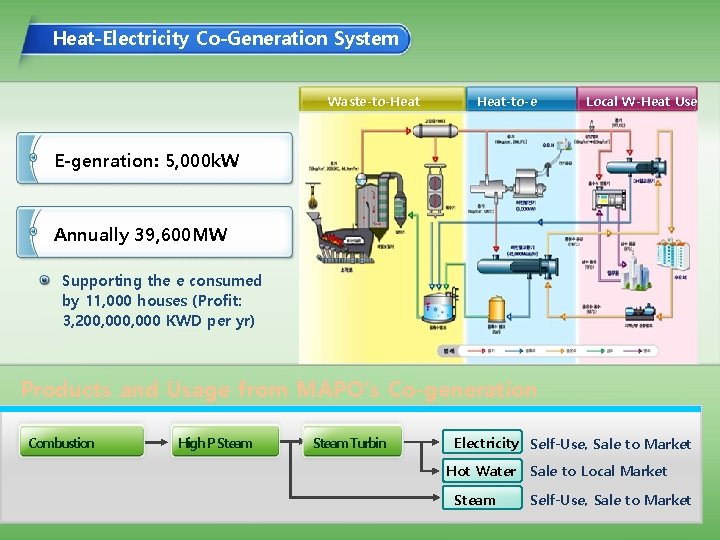
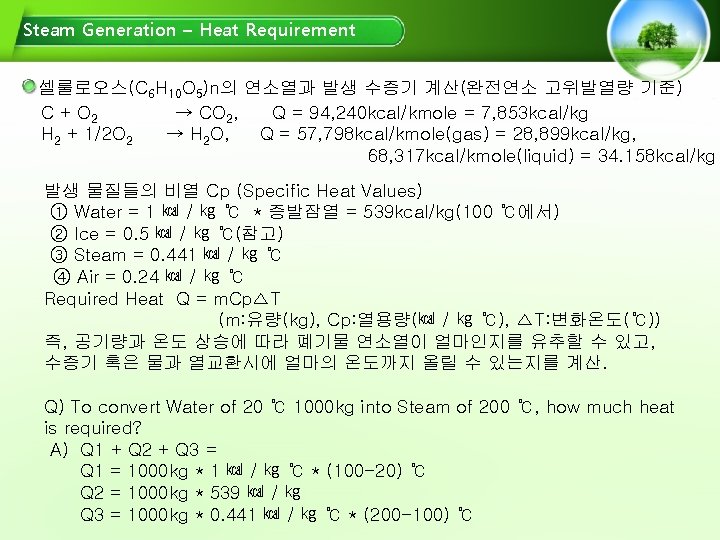
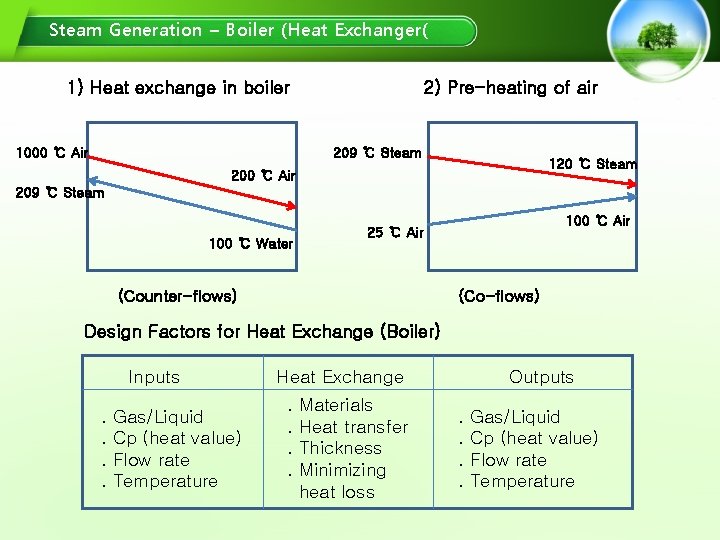
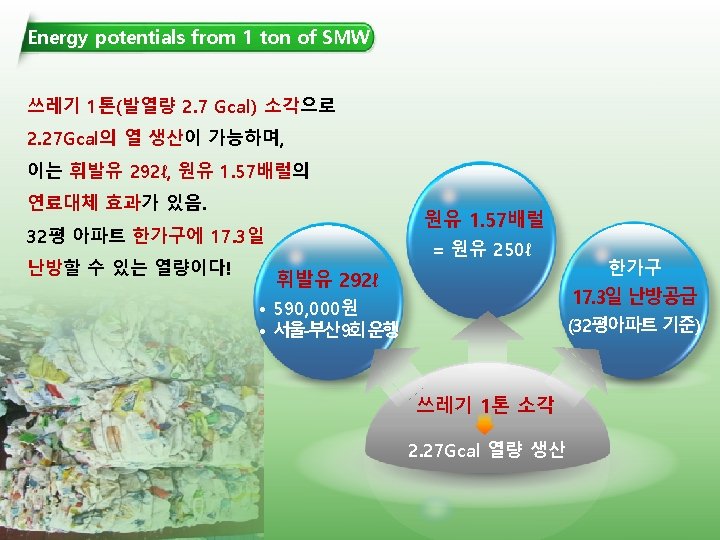
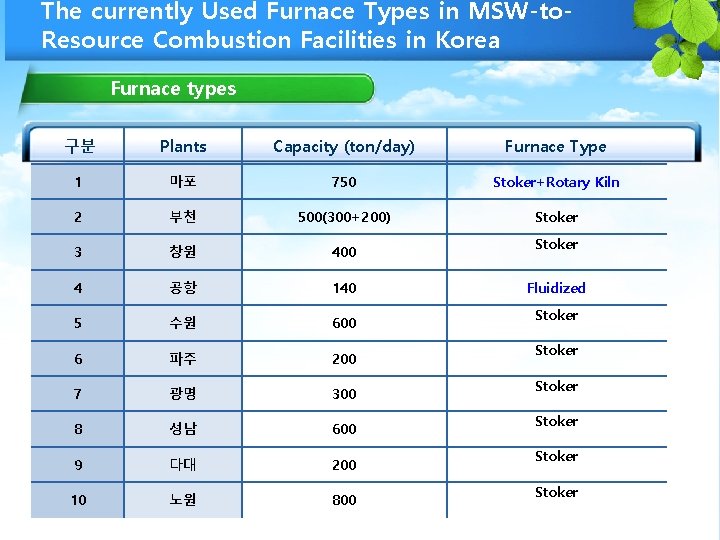
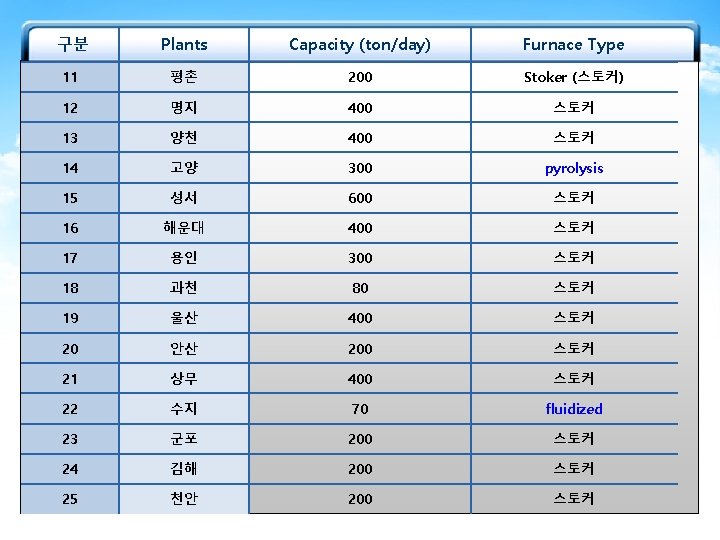
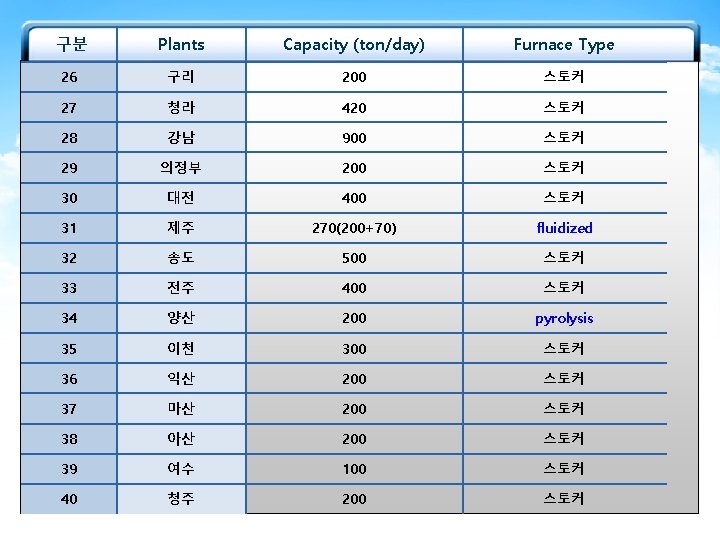
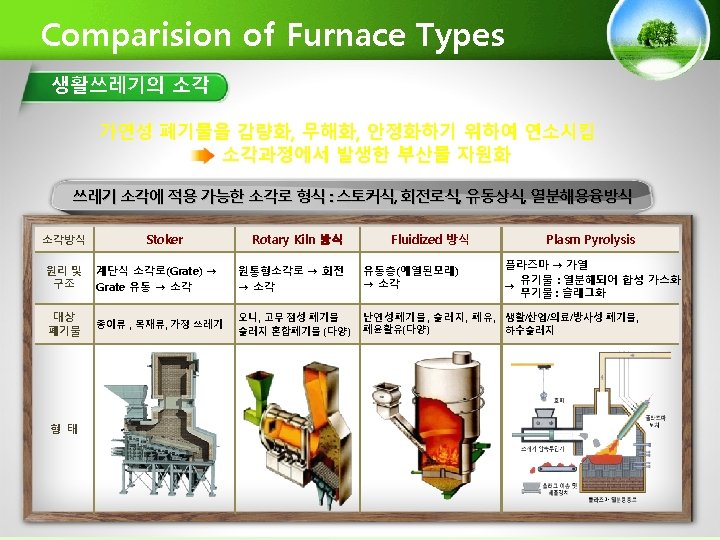

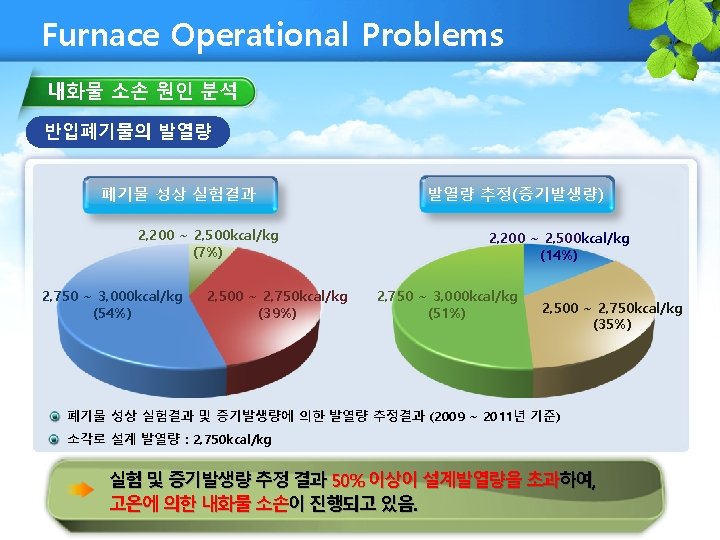
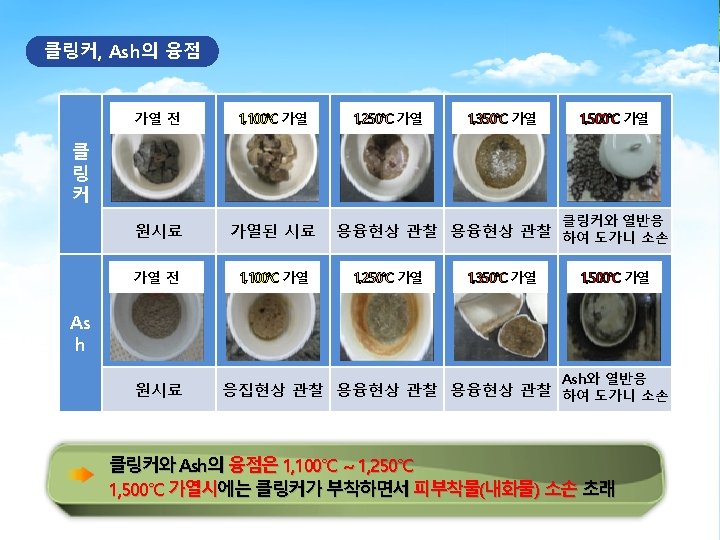
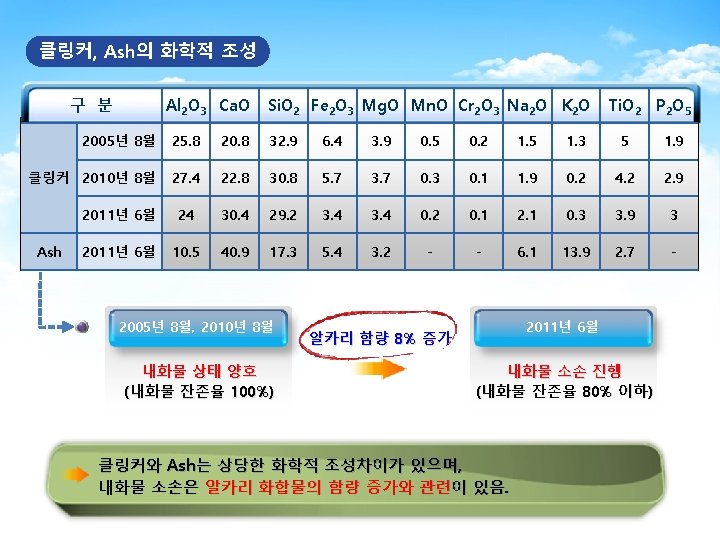
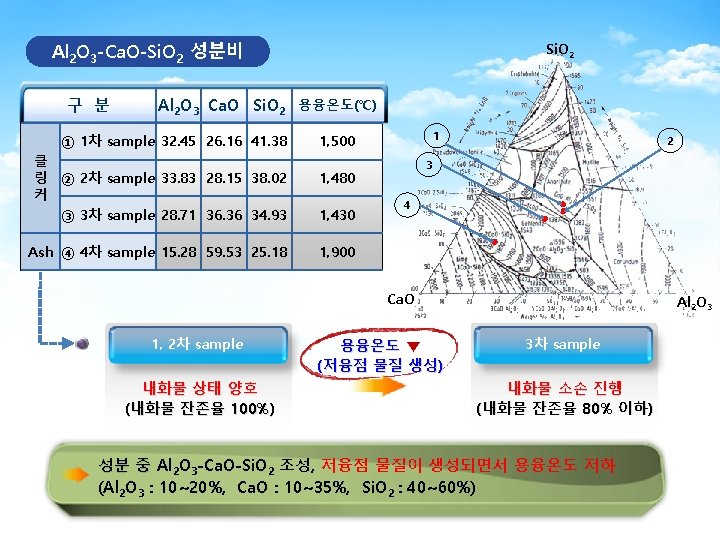
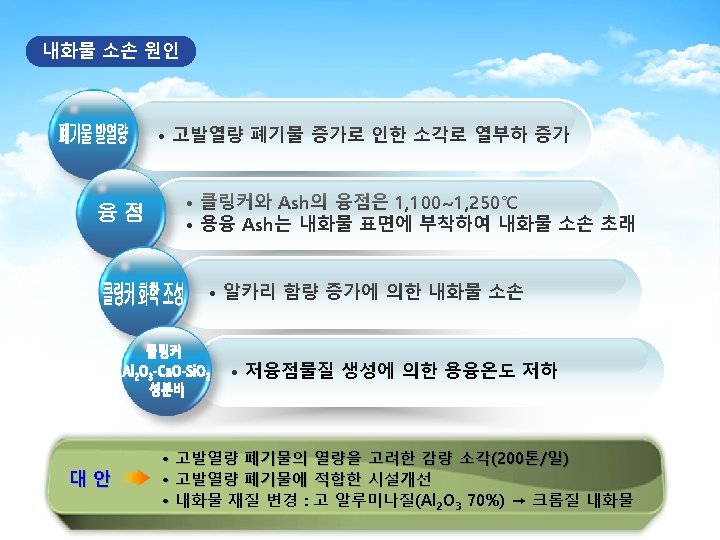

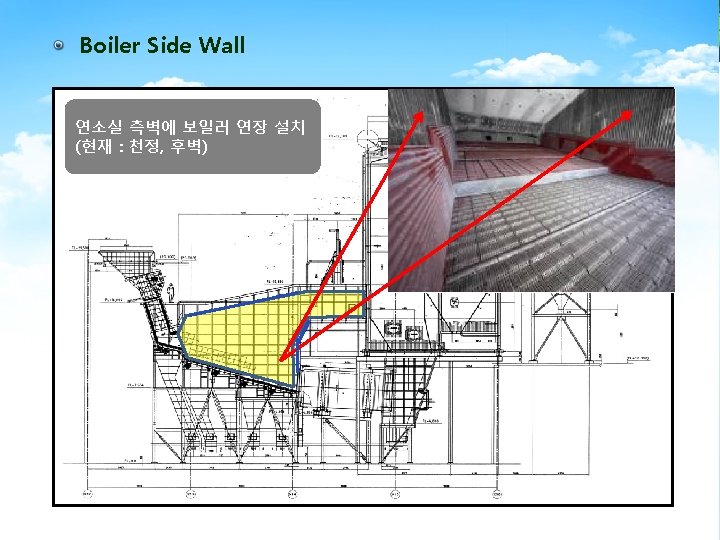
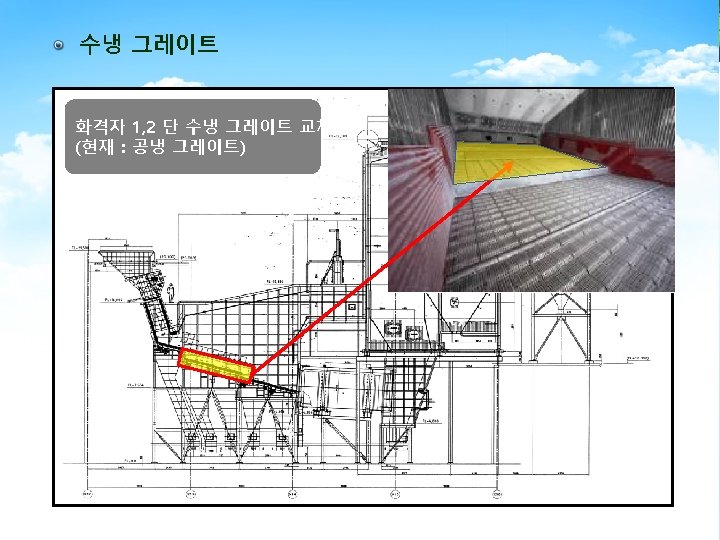
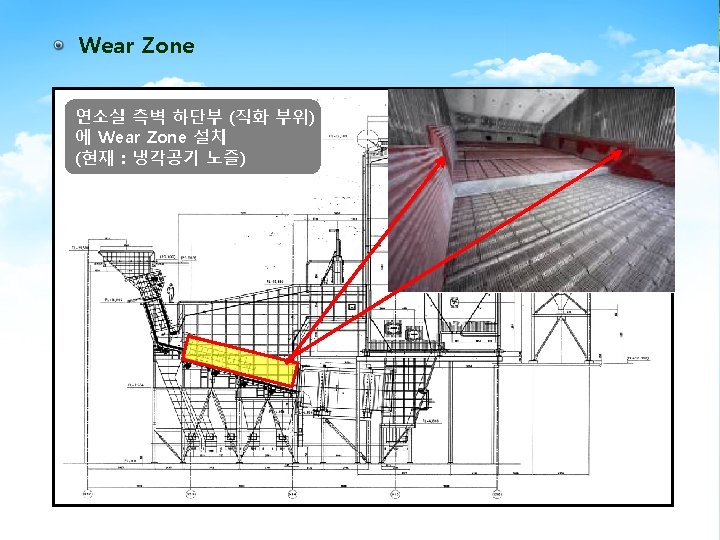
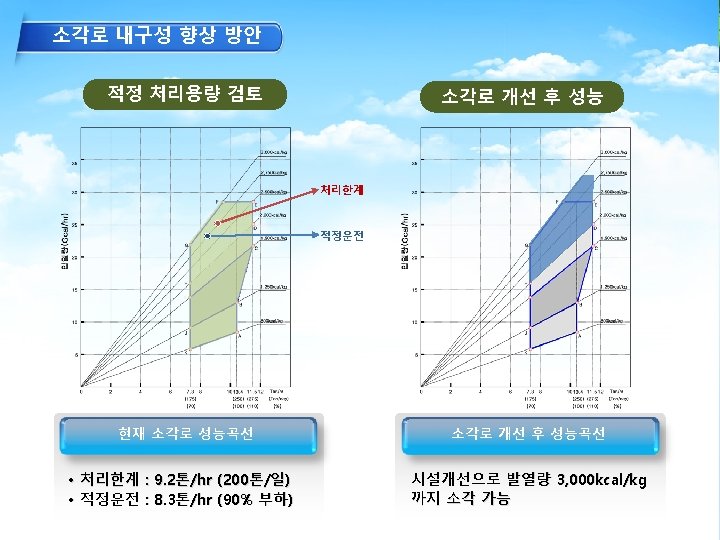
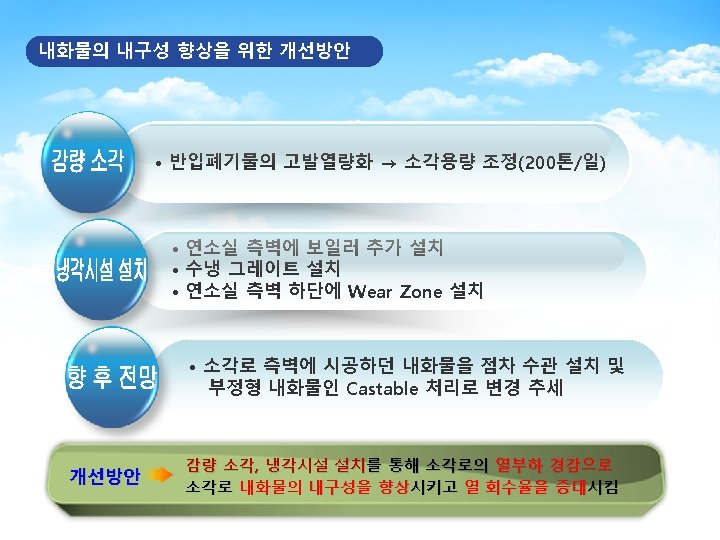
- Slides: 32
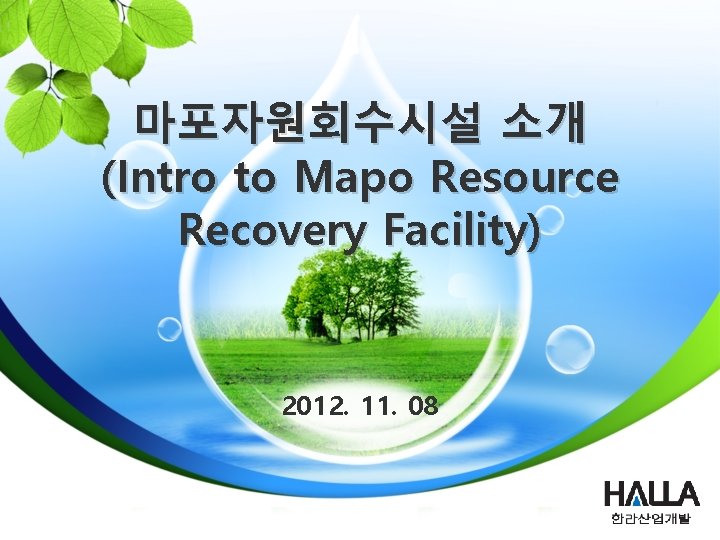
마포자원회수시설 소개 (Intro to Mapo Resource Recovery Facility) 2012. 11. 08
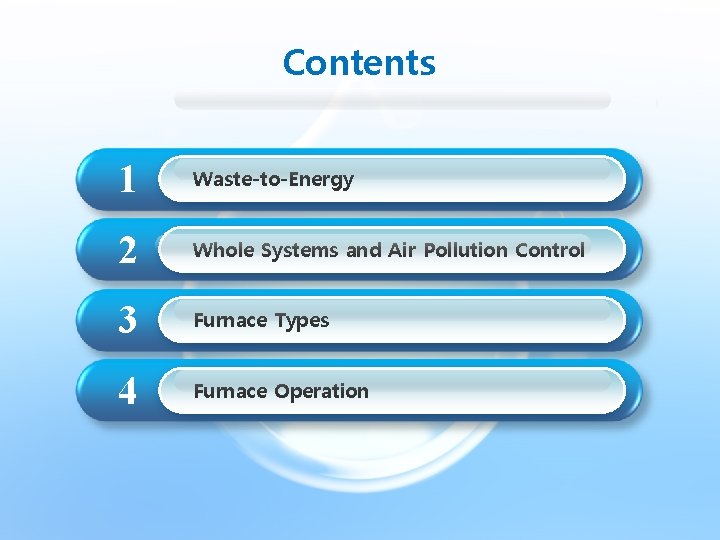
Contents 1 Waste-to-Energy 2 Whole Systems and Air Pollution Control 3 Furnace Types 4 Furnace Operation
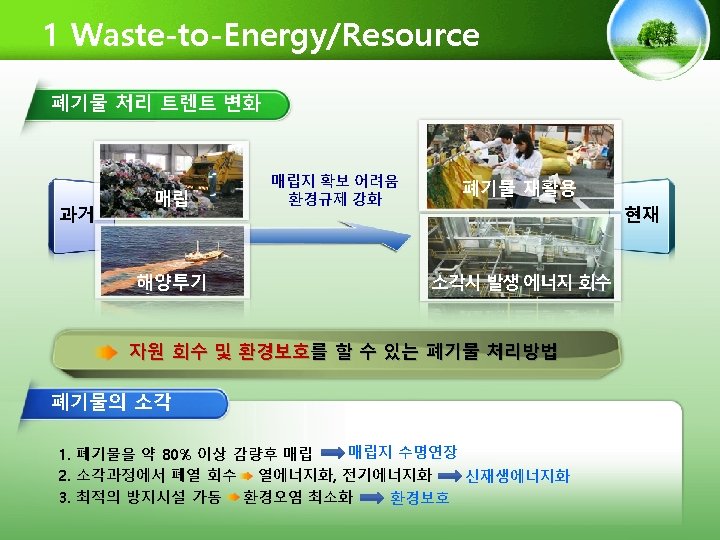
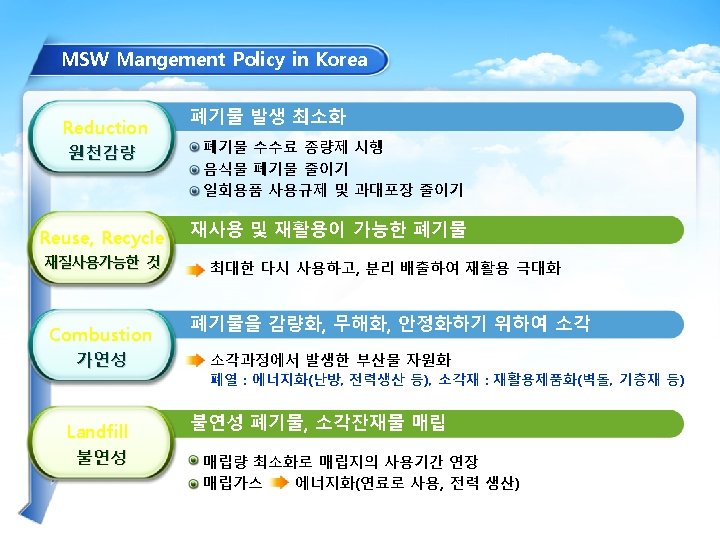
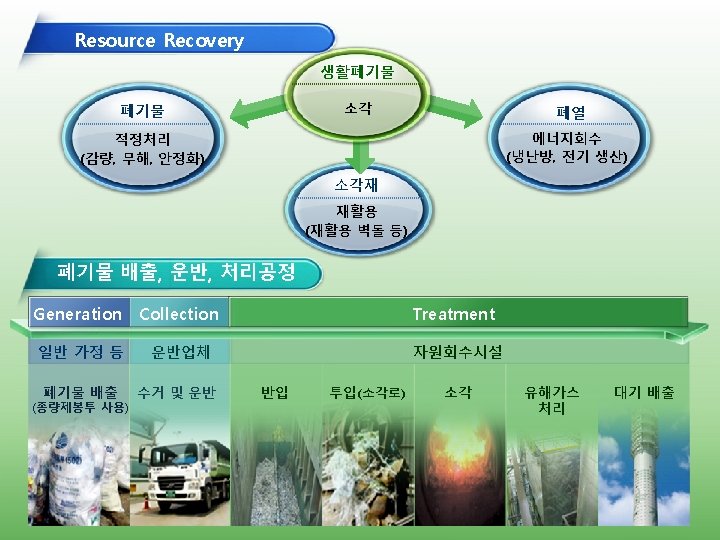
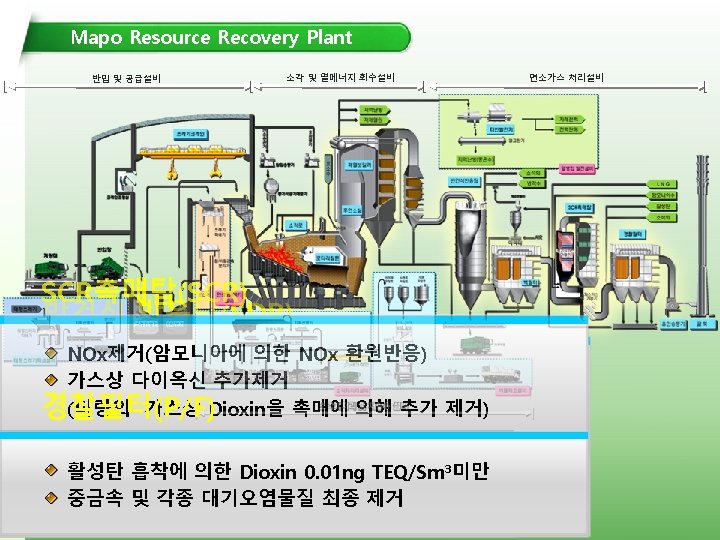
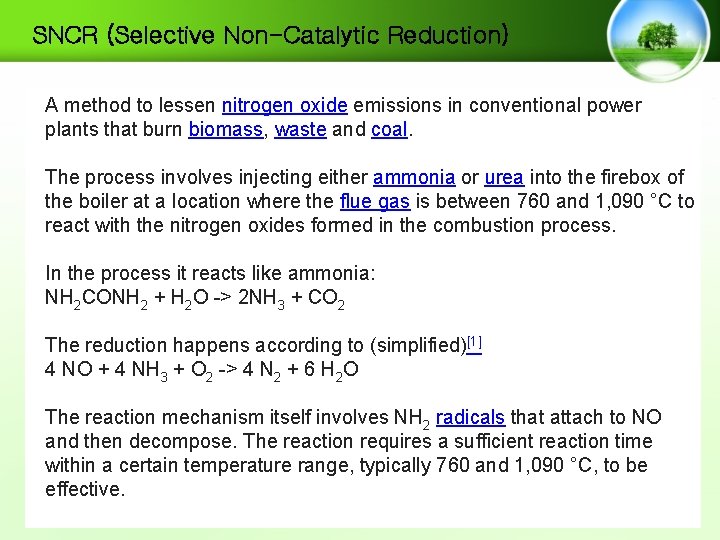
SNCR (Selective Non-Catalytic Reduction) A method to lessen nitrogen oxide emissions in conventional power plants that burn biomass, waste and coal. The process involves injecting either ammonia or urea into the firebox of the boiler at a location where the flue gas is between 760 and 1, 090 °C to react with the nitrogen oxides formed in the combustion process. In the process it reacts like ammonia: NH 2 CONH 2 + H 2 O -> 2 NH 3 + CO 2 The reduction happens according to (simplified)[1] 4 NO + 4 NH 3 + O 2 -> 4 N 2 + 6 H 2 O The reaction mechanism itself involves NH 2 radicals that attach to NO and then decompose. The reaction requires a sufficient reaction time within a certain temperature range, typically 760 and 1, 090 °C, to be effective.
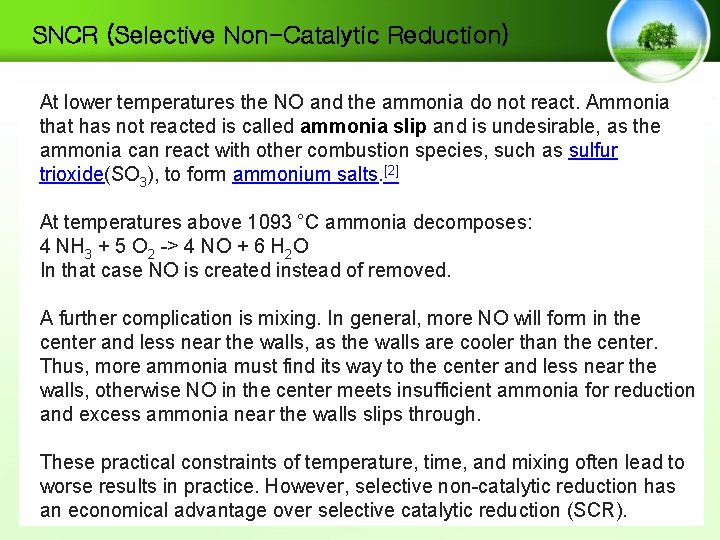
SNCR (Selective Non-Catalytic Reduction) At lower temperatures the NO and the ammonia do not react. Ammonia that has not reacted is called ammonia slip and is undesirable, as the ammonia can react with other combustion species, such as sulfur trioxide(SO 3), to form ammonium salts. [2] At temperatures above 1093 °C ammonia decomposes: 4 NH 3 + 5 O 2 -> 4 NO + 6 H 2 O In that case NO is created instead of removed. A further complication is mixing. In general, more NO will form in the center and less near the walls, as the walls are cooler than the center. Thus, more ammonia must find its way to the center and less near the walls, otherwise NO in the center meets insufficient ammonia for reduction and excess ammonia near the walls slips through. These practical constraints of temperature, time, and mixing often lead to worse results in practice. However, selective non-catalytic reduction has an economical advantage over selective catalytic reduction (SCR).
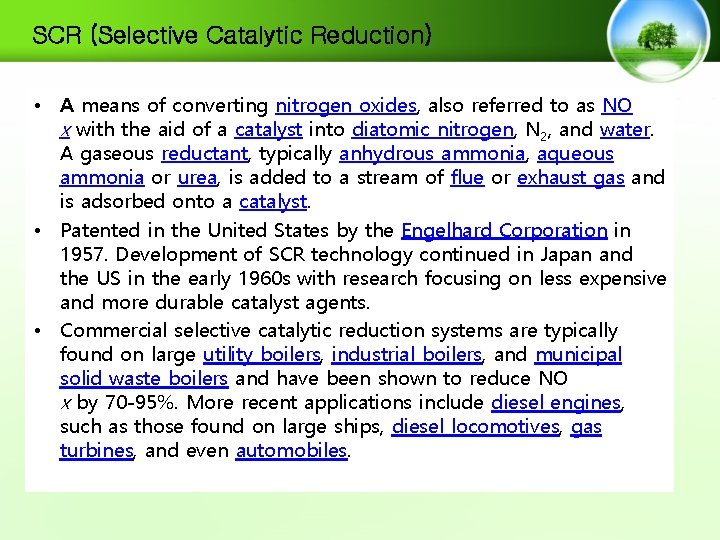
SCR (Selective Catalytic Reduction) • A means of converting nitrogen oxides, also referred to as NO x with the aid of a catalyst into diatomic nitrogen, N 2, and water. A gaseous reductant, typically anhydrous ammonia, aqueous ammonia or urea, is added to a stream of flue or exhaust gas and is adsorbed onto a catalyst. • Patented in the United States by the Engelhard Corporation in 1957. Development of SCR technology continued in Japan and the US in the early 1960 s with research focusing on less expensive and more durable catalyst agents. • Commercial selective catalytic reduction systems are typically found on large utility boilers, industrial boilers, and municipal solid waste boilers and have been shown to reduce NO x by 70 -95%. More recent applications include diesel engines, such as those found on large ships, diesel locomotives, gas turbines, and even automobiles.
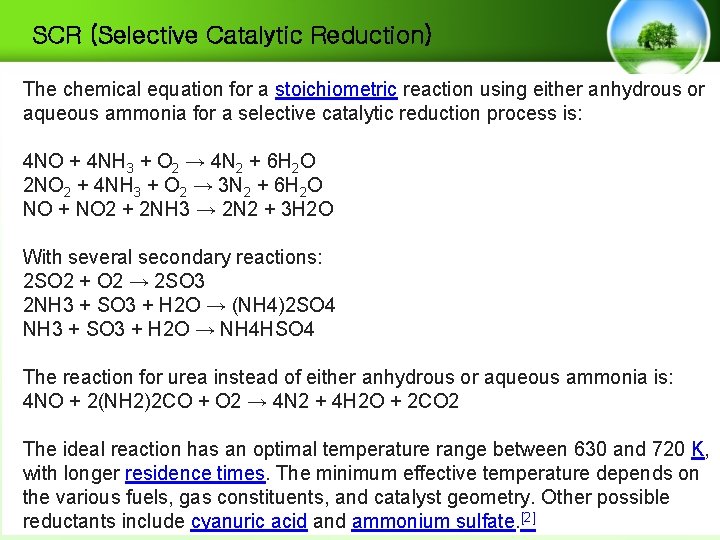
SCR (Selective Catalytic Reduction) The chemical equation for a stoichiometric reaction using either anhydrous or aqueous ammonia for a selective catalytic reduction process is: 4 NO + 4 NH 3 + O 2 → 4 N 2 + 6 H 2 O 2 NO 2 + 4 NH 3 + O 2 → 3 N 2 + 6 H 2 O NO + NO 2 + 2 NH 3 → 2 N 2 + 3 H 2 O With several secondary reactions: 2 SO 2 + O 2 → 2 SO 3 2 NH 3 + SO 3 + H 2 O → (NH 4)2 SO 4 NH 3 + SO 3 + H 2 O → NH 4 HSO 4 The reaction for urea instead of either anhydrous or aqueous ammonia is: 4 NO + 2(NH 2)2 CO + O 2 → 4 N 2 + 4 H 2 O + 2 CO 2 The ideal reaction has an optimal temperature range between 630 and 720 K, with longer residence times. The minimum effective temperature depends on the various fuels, gas constituents, and catalyst geometry. Other possible reductants include cyanuric acid and ammonium sulfate. [2]
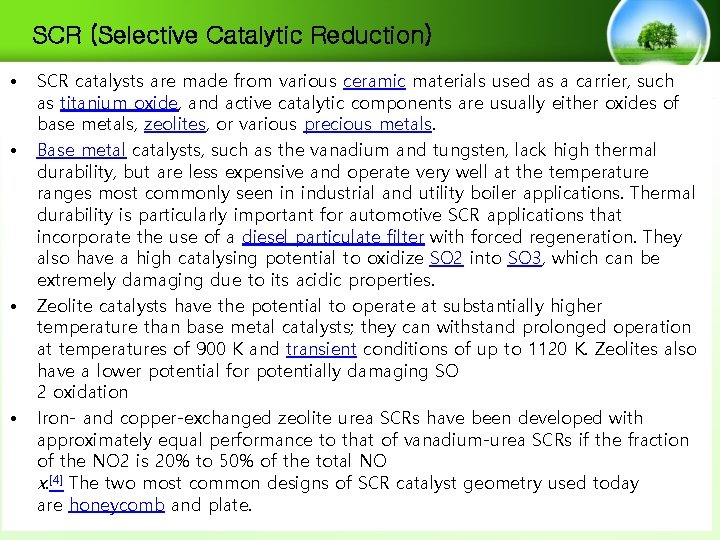
SCR (Selective Catalytic Reduction) • • SCR catalysts are made from various ceramic materials used as a carrier, such as titanium oxide, and active catalytic components are usually either oxides of base metals, zeolites, or various precious metals. Base metal catalysts, such as the vanadium and tungsten, lack high thermal durability, but are less expensive and operate very well at the temperature ranges most commonly seen in industrial and utility boiler applications. Thermal durability is particularly important for automotive SCR applications that incorporate the use of a diesel particulate filter with forced regeneration. They also have a high catalysing potential to oxidize SO 2 into SO 3, which can be extremely damaging due to its acidic properties. Zeolite catalysts have the potential to operate at substantially higher temperature than base metal catalysts; they can withstand prolonged operation at temperatures of 900 K and transient conditions of up to 1120 K. Zeolites also have a lower potential for potentially damaging SO 2 oxidation Iron- and copper-exchanged zeolite urea SCRs have been developed with approximately equal performance to that of vanadium-urea SCRs if the fraction of the NO 2 is 20% to 50% of the total NO x. [4] The two most common designs of SCR catalyst geometry used today are honeycomb and plate.
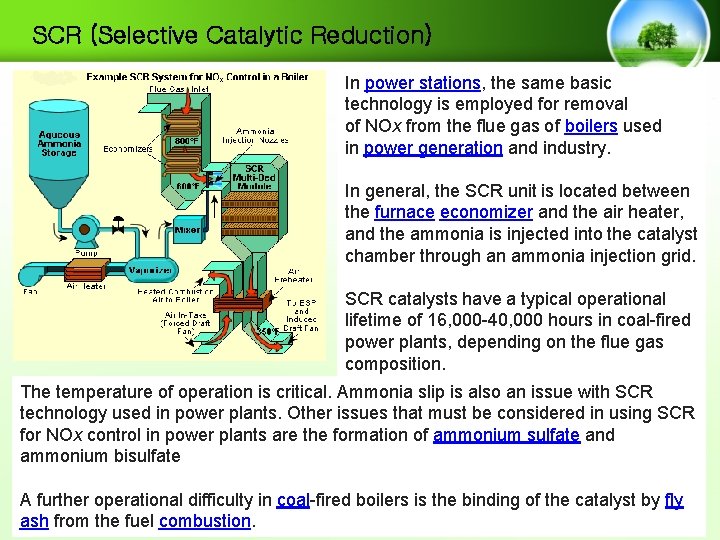
SCR (Selective Catalytic Reduction) In power stations, the same basic technology is employed for removal of NOx from the flue gas of boilers used in power generation and industry. In general, the SCR unit is located between the furnace economizer and the air heater, and the ammonia is injected into the catalyst chamber through an ammonia injection grid. SCR catalysts have a typical operational lifetime of 16, 000 -40, 000 hours in coal-fired power plants, depending on the flue gas composition. The temperature of operation is critical. Ammonia slip is also an issue with SCR technology used in power plants. Other issues that must be considered in using SCR for NOx control in power plants are the formation of ammonium sulfate and ammonium bisulfate A further operational difficulty in coal-fired boilers is the binding of the catalyst by fly ash from the fuel combustion.
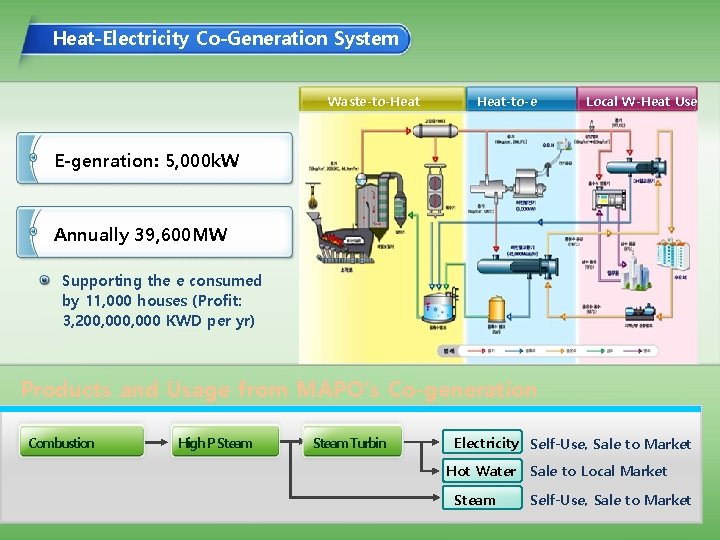
Heat-Electricity Co-Generation System Waste-to-Heat-to-e Local W-Heat Use E-genration: 5, 000 k. W Annually 39, 600 MW Supporting the e consumed by 11, 000 houses (Profit: 3, 200, 000 KWD per yr) Products and Usage from MAPO’s Co-generation Combustion High P Steam Turbin Electricity Self-Use, Sale to Market Hot Water Steam Sale to Local Market Self-Use, Sale to Market
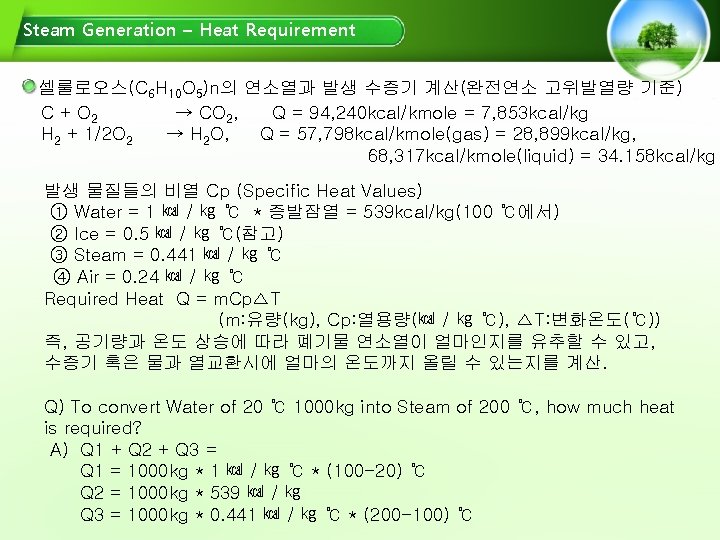
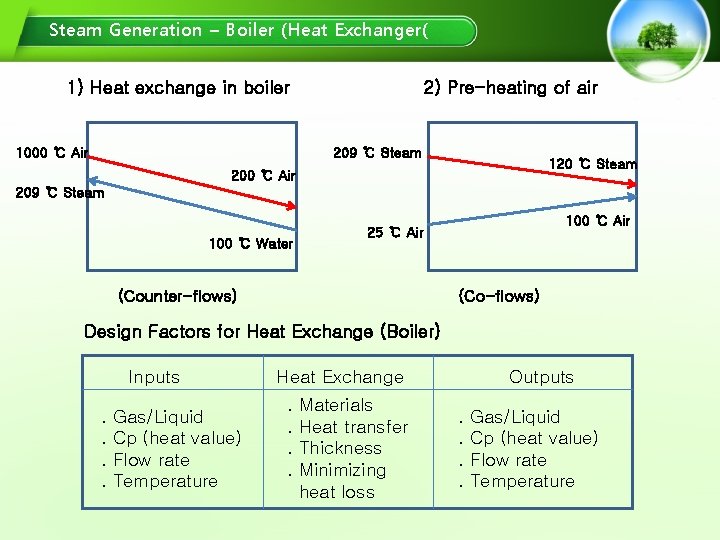
Steam Generation – Boiler (Heat Exchanger( 1) Heat exchange in boiler 1000 ℃ Air 2) Pre-heating of air 209 ℃ Steam 120 ℃ Steam 200 ℃ Air 209 ℃ Steam 100 ℃ Water 100 ℃ Air 25 ℃ Air (Counter-flows) (Co-flows) Design Factors for Heat Exchange (Boiler) Inputs. . Gas/Liquid Cp (heat value) Flow rate Temperature Heat Exchange. . Materials Heat transfer Thickness Minimizing heat loss Outputs. . Gas/Liquid Cp (heat value) Flow rate Temperature
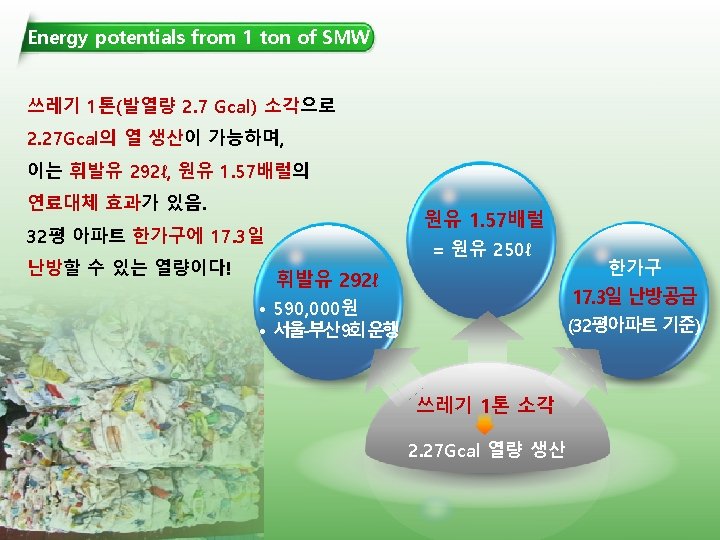
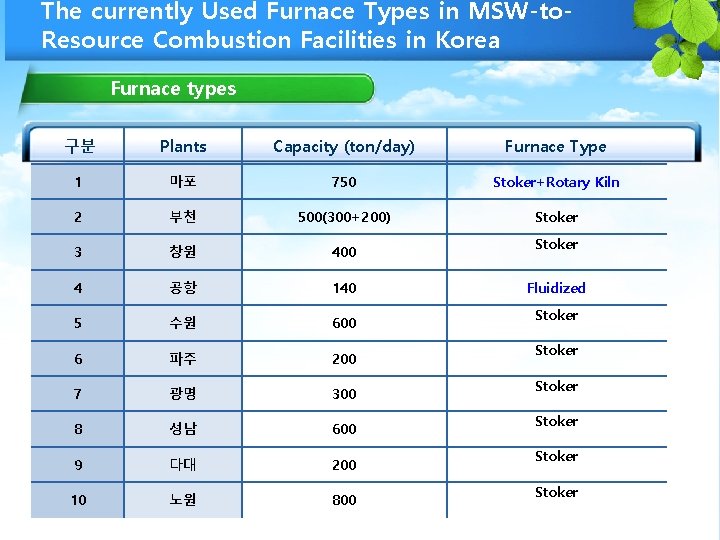
The currently Used Furnace Types in MSW-to. Resource Combustion Facilities in Korea Furnace types 구분 Plants Capacity (ton/day) Furnace Type 1 마포 750 Stoker+Rotary Kiln 2 부천 500(300+200) Stoker 3 창원 400 4 공항 140 5 수원 600 6 파주 200 7 광명 300 8 성남 600 9 다대 200 10 노원 800 Stoker Fluidized Stoker Stoker
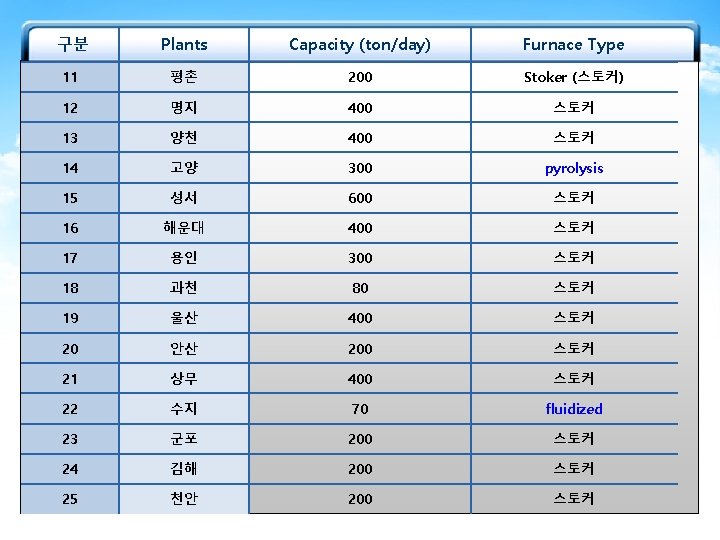
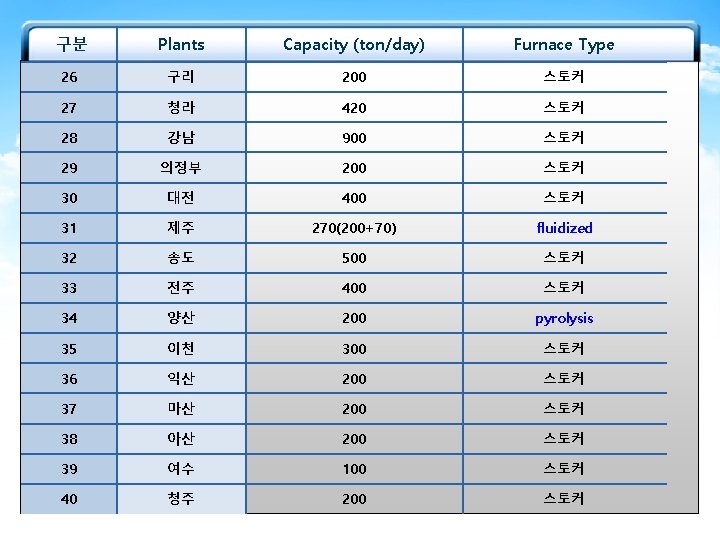
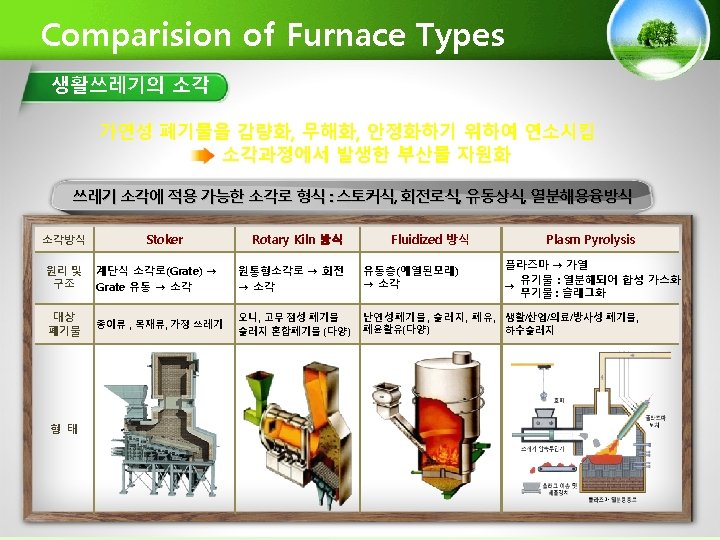

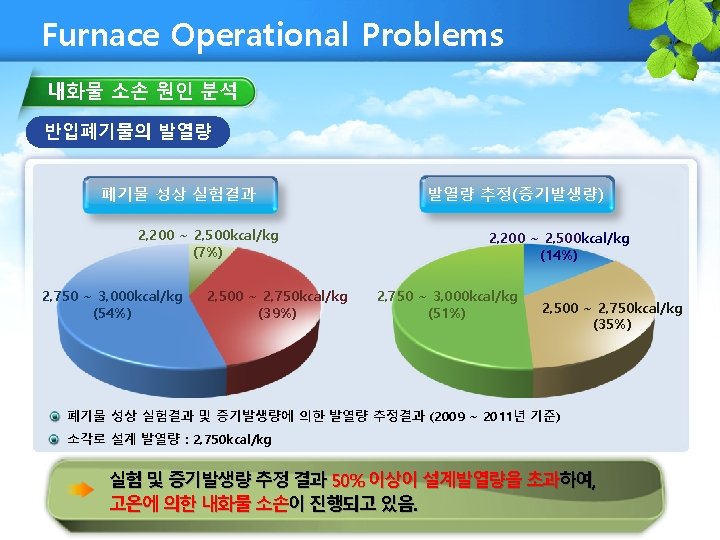
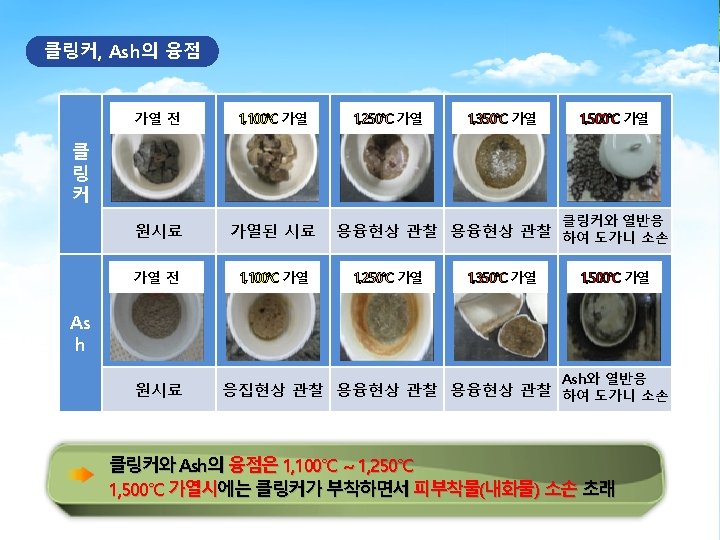
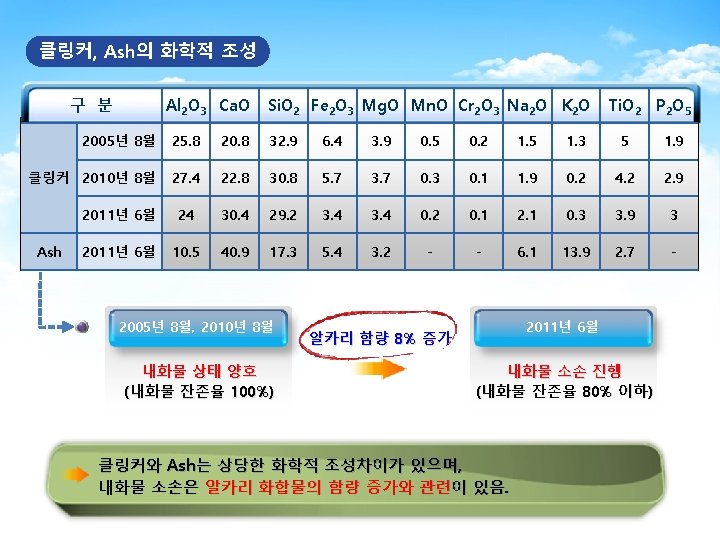
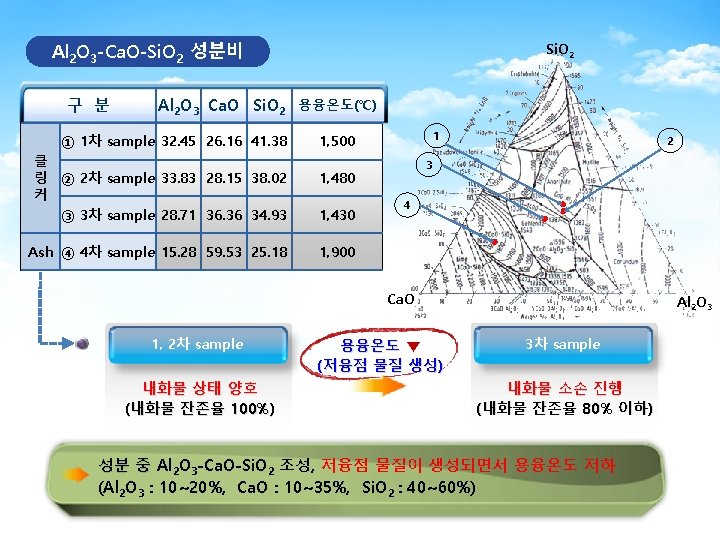
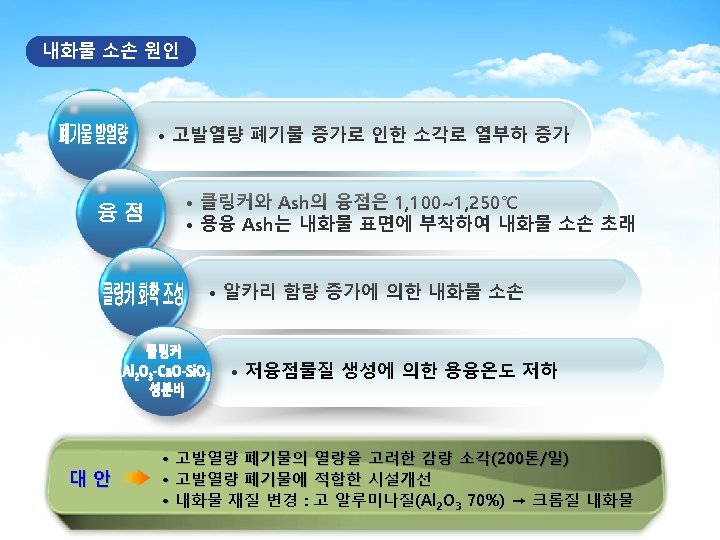

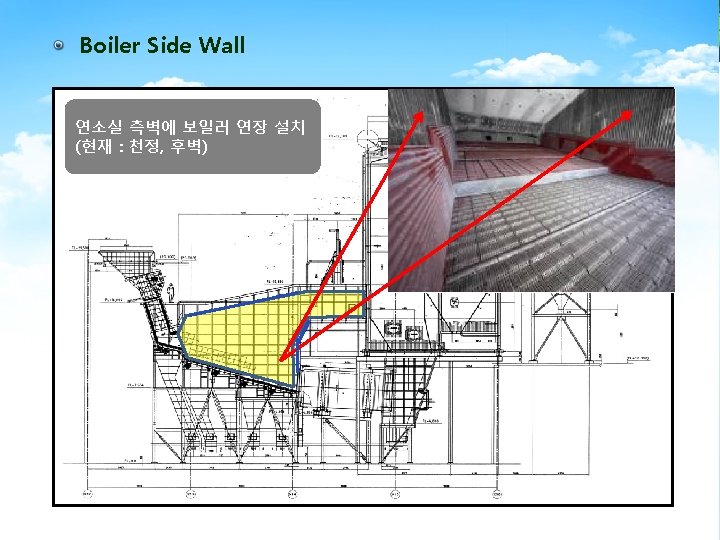
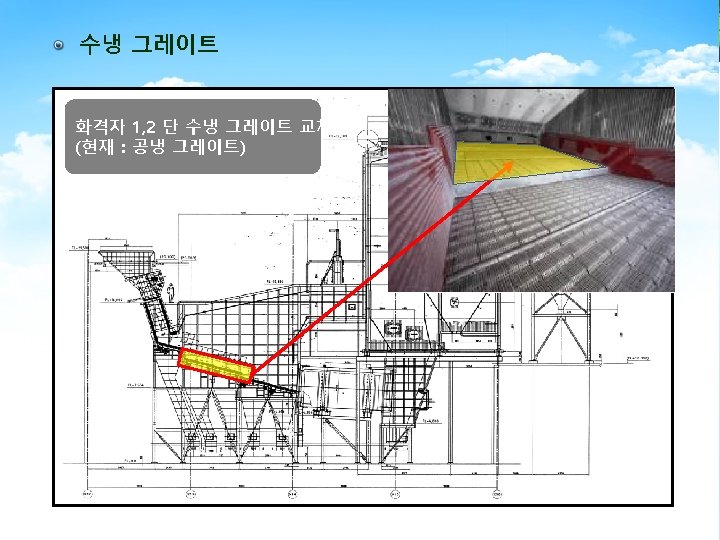
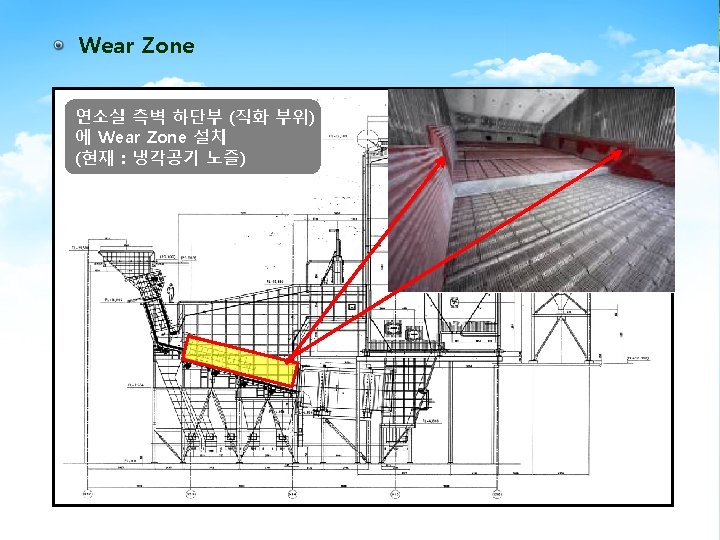
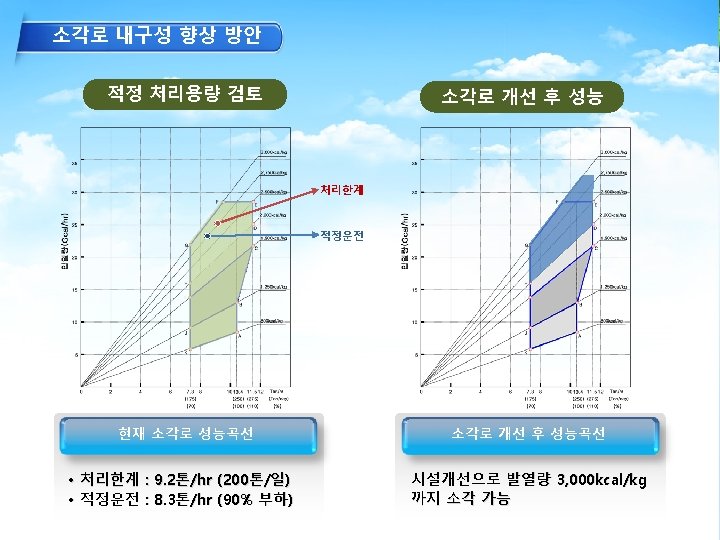
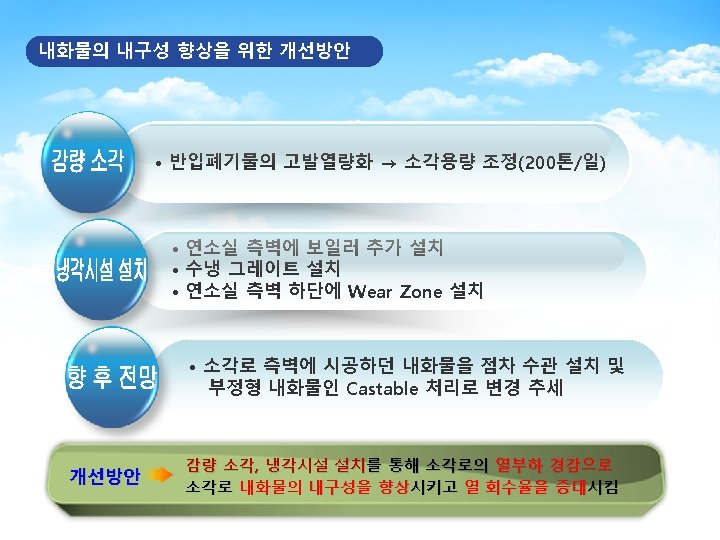
Mapo a
Scheda rilevazione mapo
Mapo movimentazione
Global facility for disaster reduction and recovery
Overview of hrm
Human resource management chapter 1
Resource leveling is the approach to even out the peaks of
Perbedaan antara resource loading dan resource levelling
Solar system intro
Intro to polynomials
Intro
Prefix and suffix examples
Intro to business chapter 10
Goodguysww.
Oliver twist summary
Background kfc company
Introduction to assembly
Half adder
Jane schaffer
Intro paragraph format
Thematic essay example
Fable leather armor
Introduction to machine learning andrew ng
Intro.php?aid=
Huckleberry finn intro
Leq format
Captcha crowdsourcing
Introduction body and conclusion
Rhythm in floral design
Peristalsis in digestive system
Prog10082
Bd max intro
Example of introduction title