Gauteng Department of Education Further Education and Training
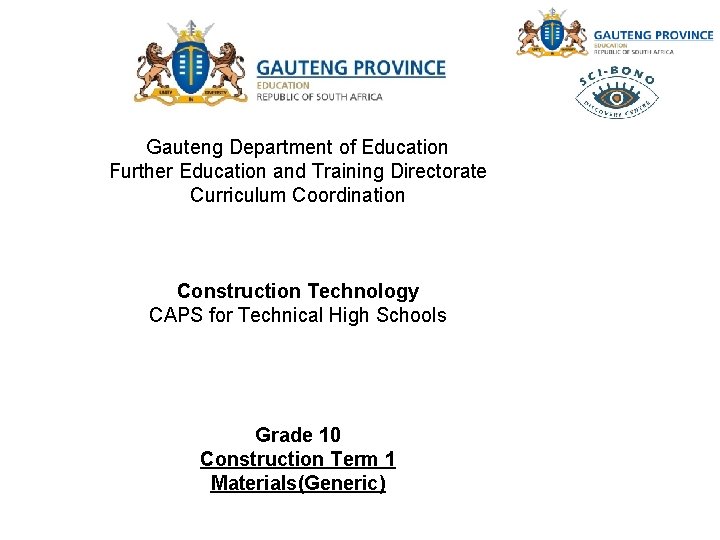
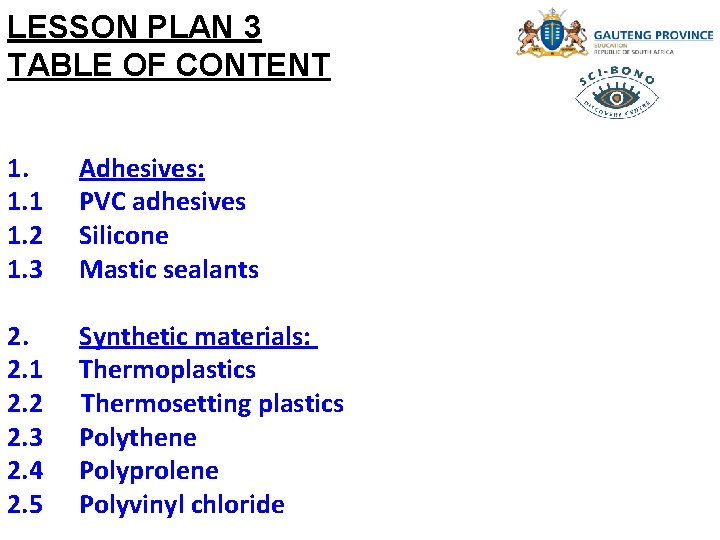
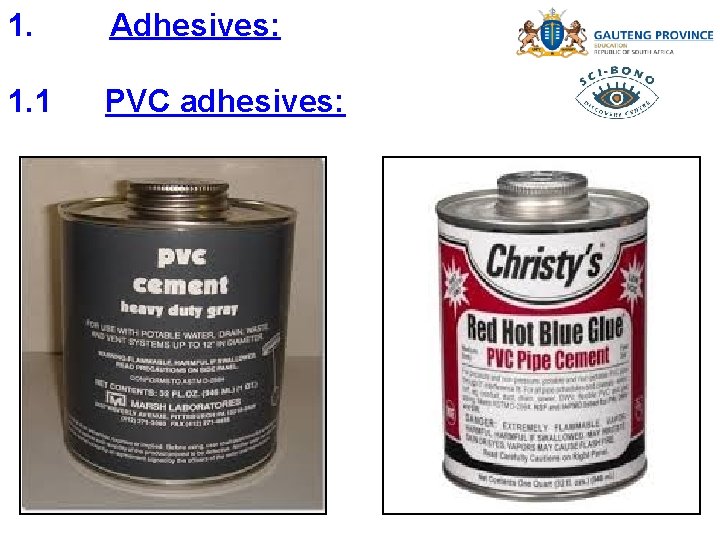
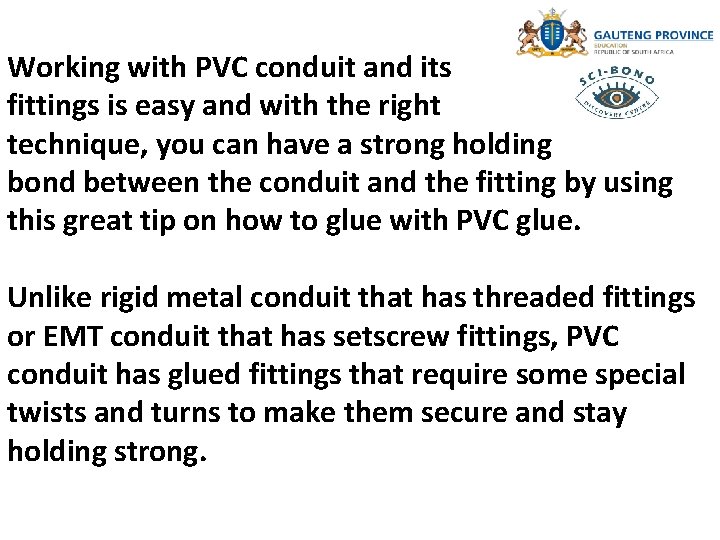
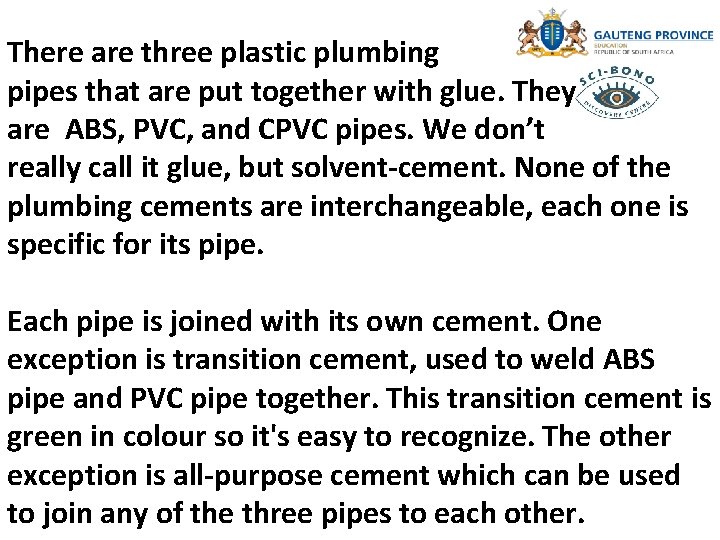
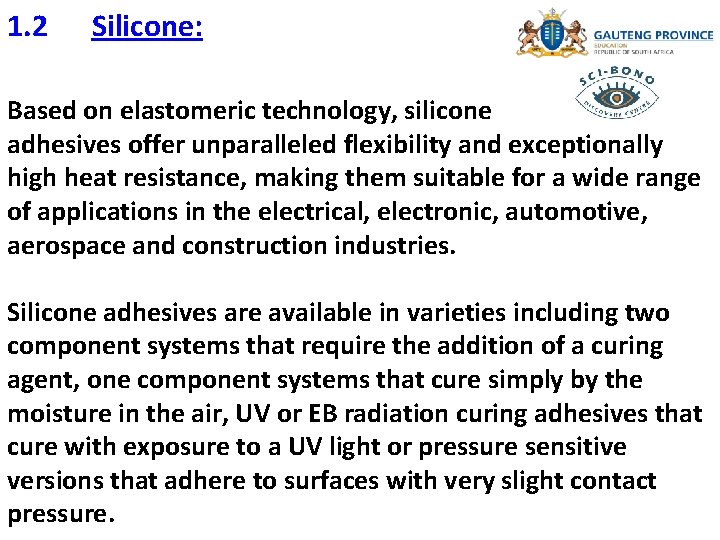

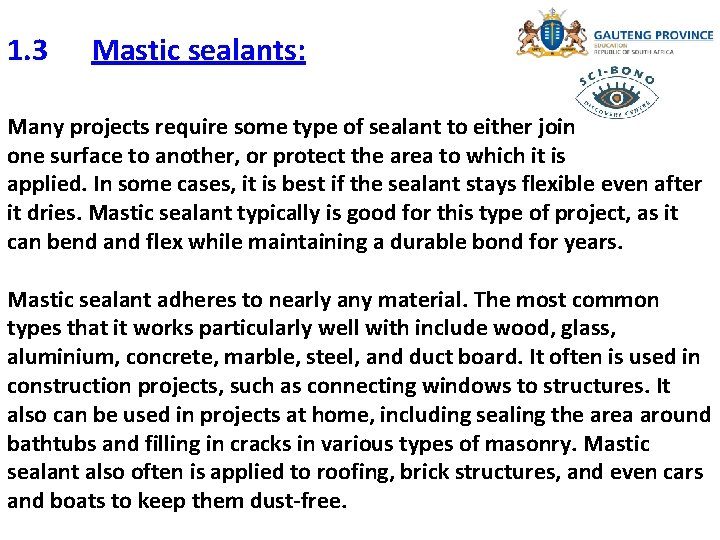
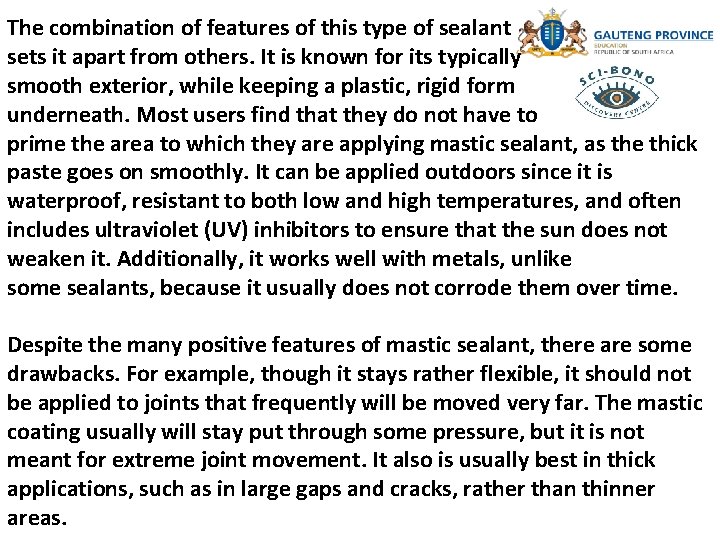
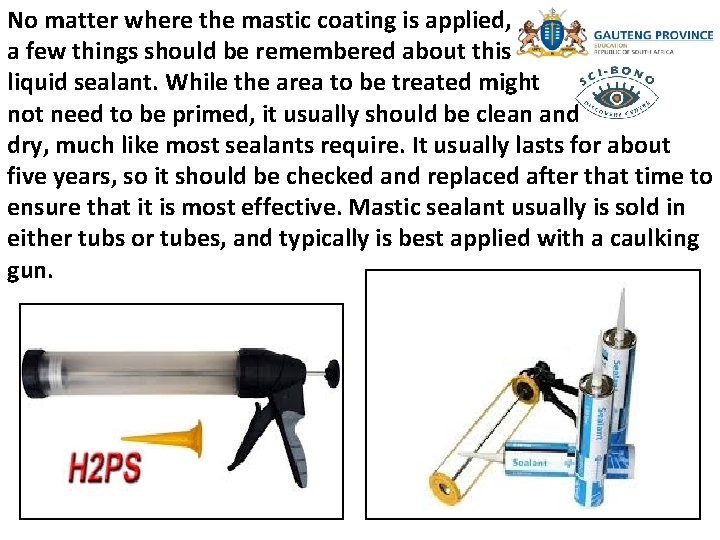
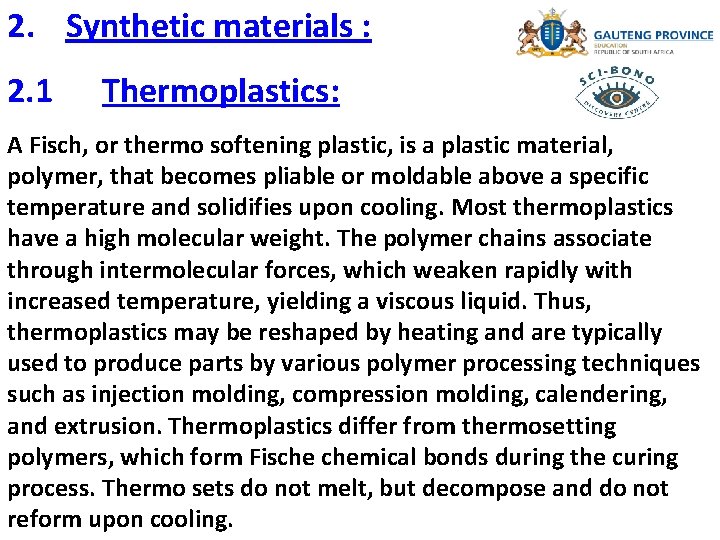
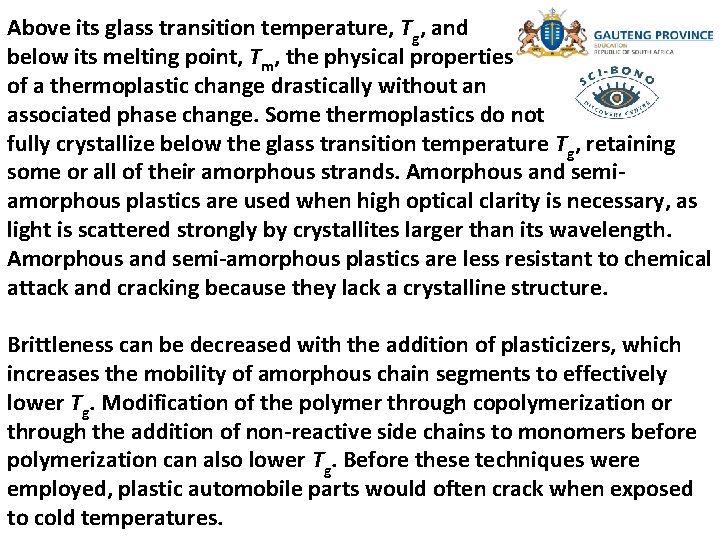
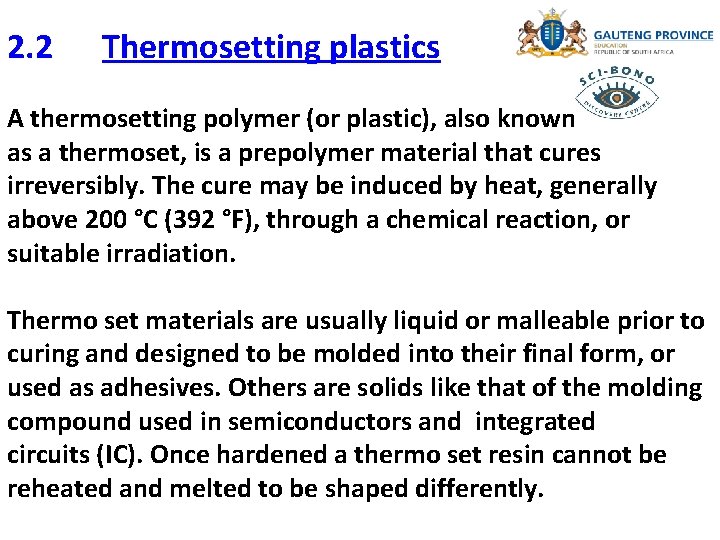
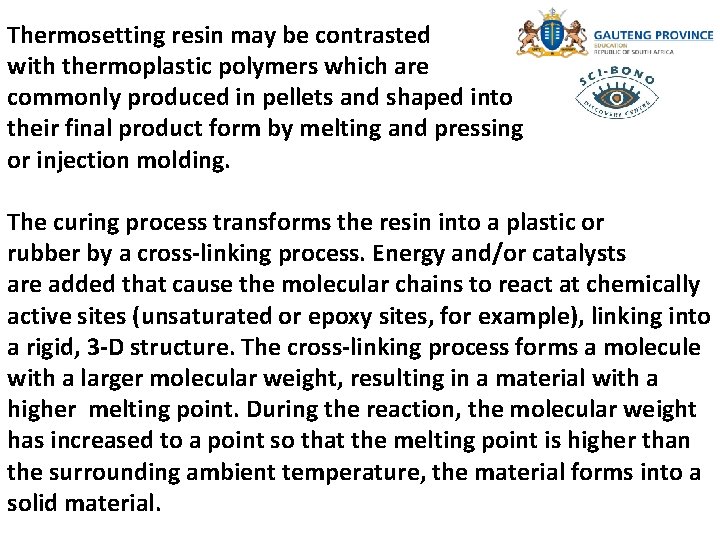
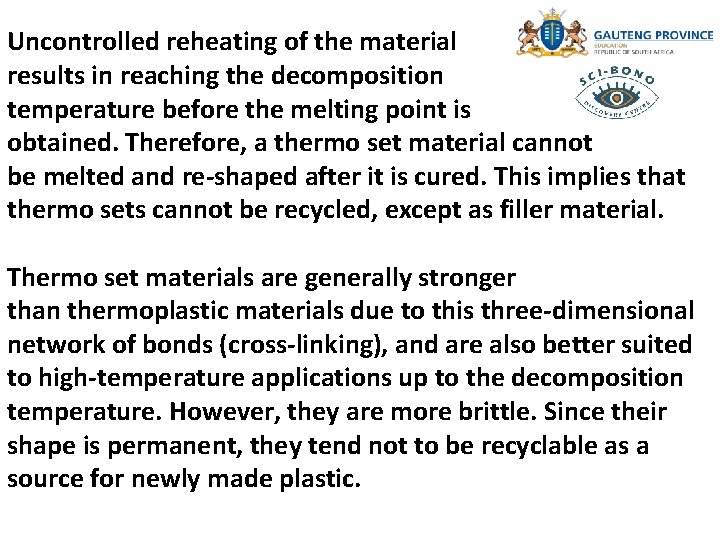
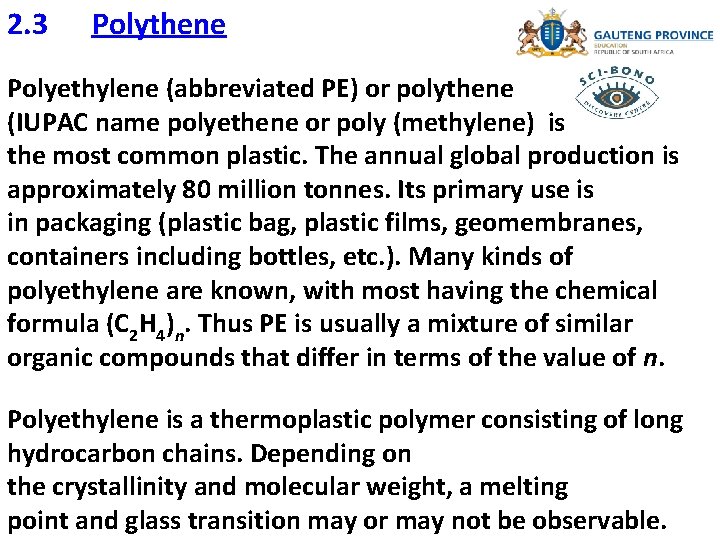
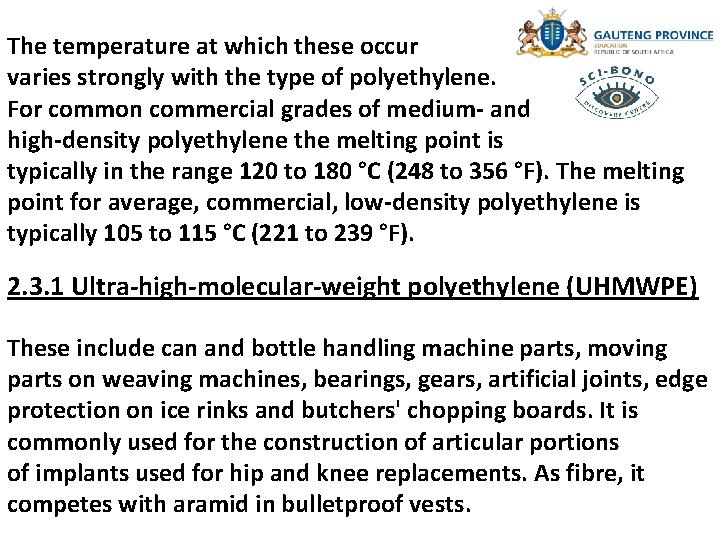
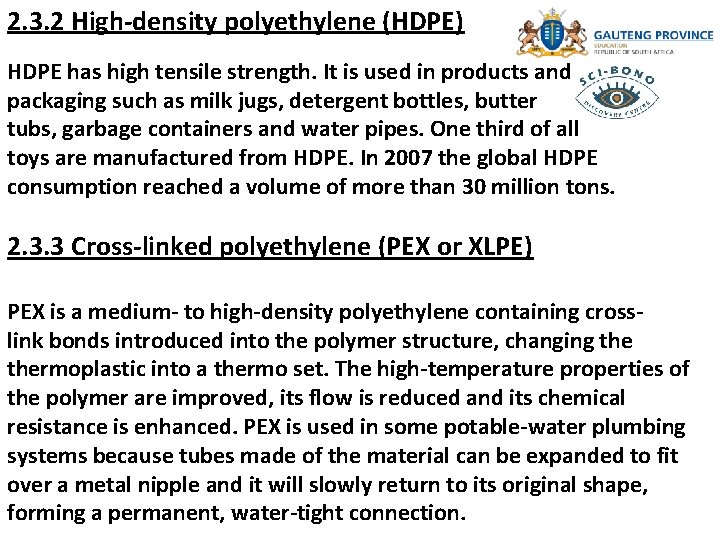
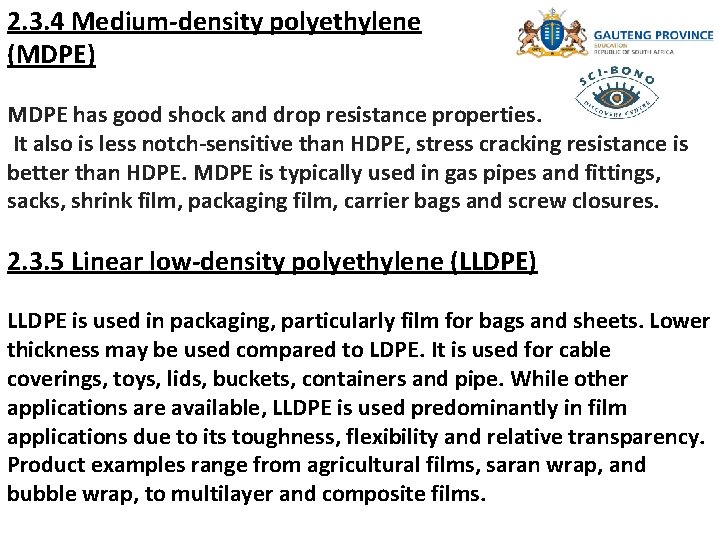
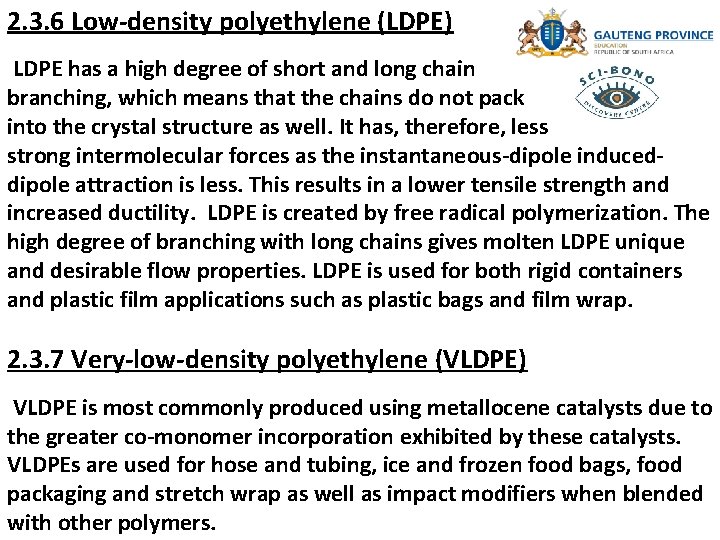
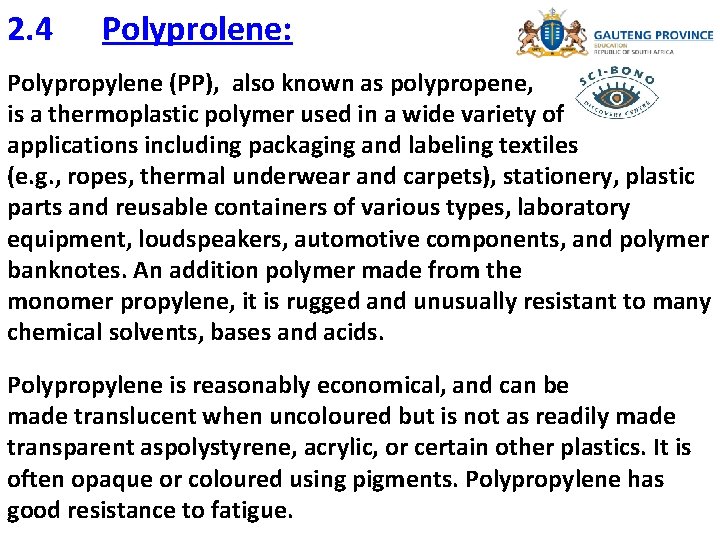
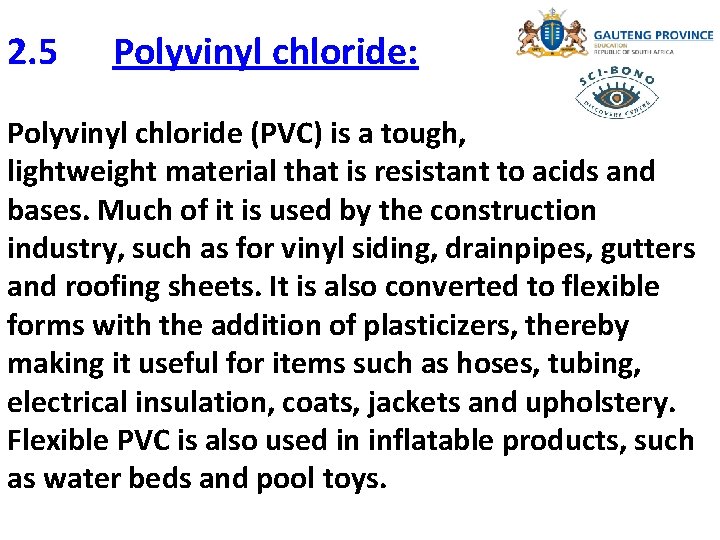
- Slides: 22
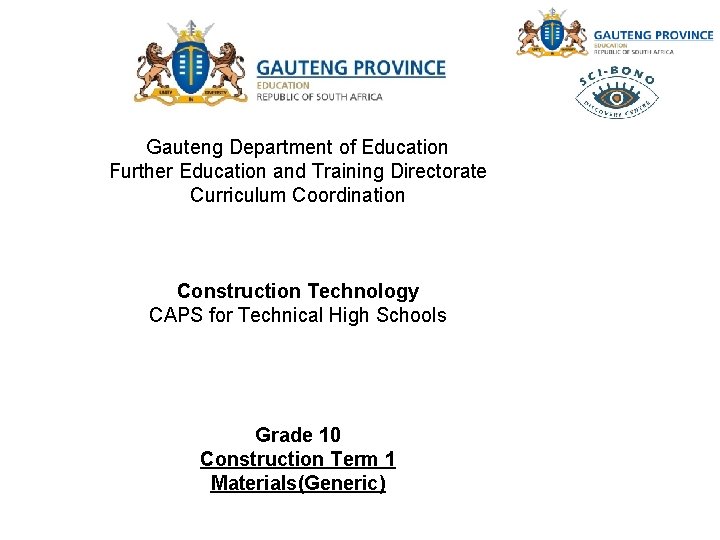
Gauteng Department of Education Further Education and Training Directorate Curriculum Coordination Construction Technology CAPS for Technical High Schools Grade 10 Construction Term 1 Materials(Generic)
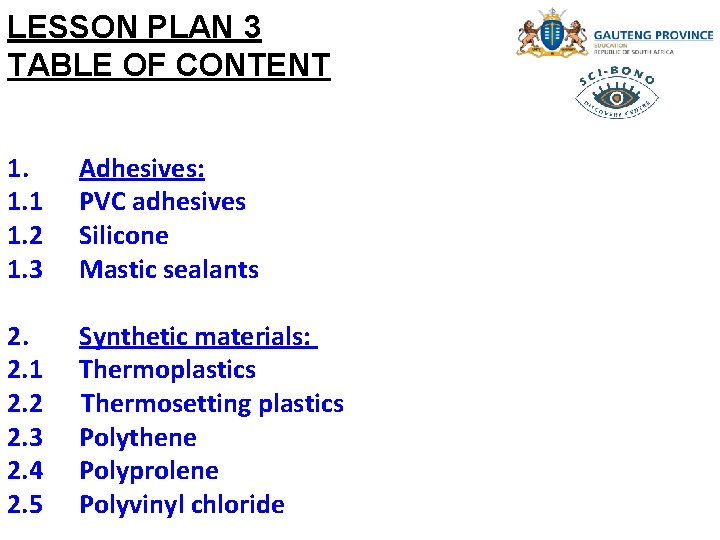
LESSON PLAN 3 TABLE OF CONTENT 1. 1 1. 2 1. 3 Adhesives: PVC adhesives Silicone Mastic sealants 2. Synthetic materials: 2. 1 Thermoplastics 2. 2 Thermosetting plastics 2. 3 Polythene 2. 4 Polyprolene 2. 5 Polyvinyl chloride
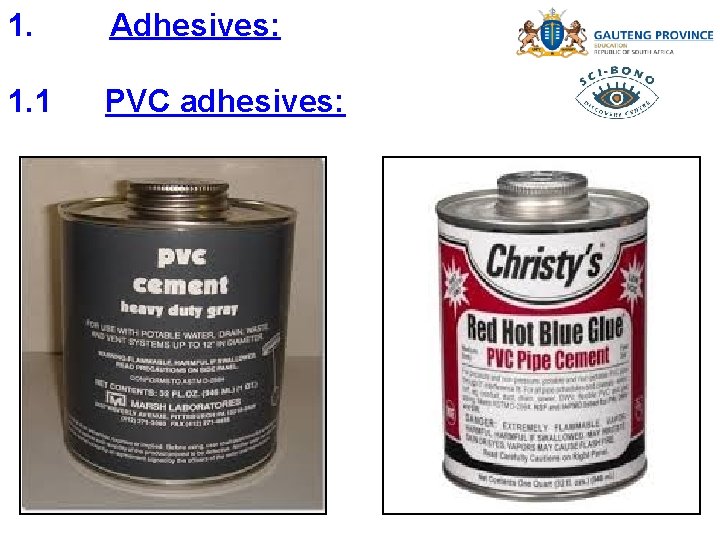
1. Adhesives: 1. 1 PVC adhesives:
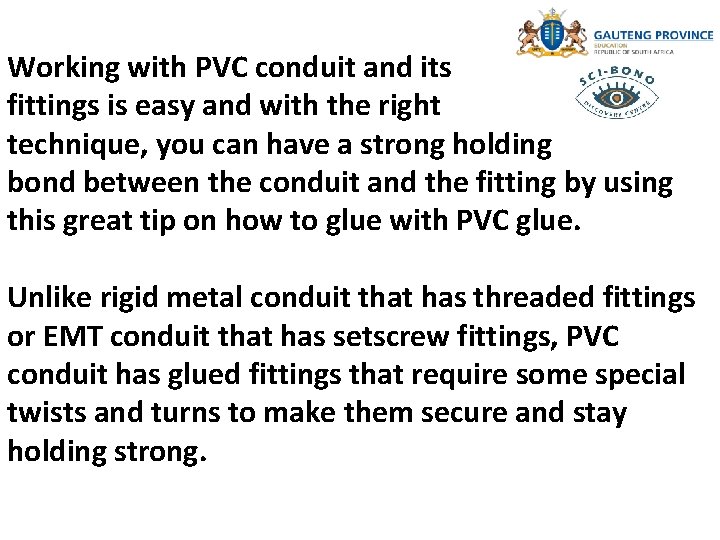
Working with PVC conduit and its fittings is easy and with the right technique, you can have a strong holding bond between the conduit and the fitting by using this great tip on how to glue with PVC glue. Unlike rigid metal conduit that has threaded fittings or EMT conduit that has setscrew fittings, PVC conduit has glued fittings that require some special twists and turns to make them secure and stay holding strong.
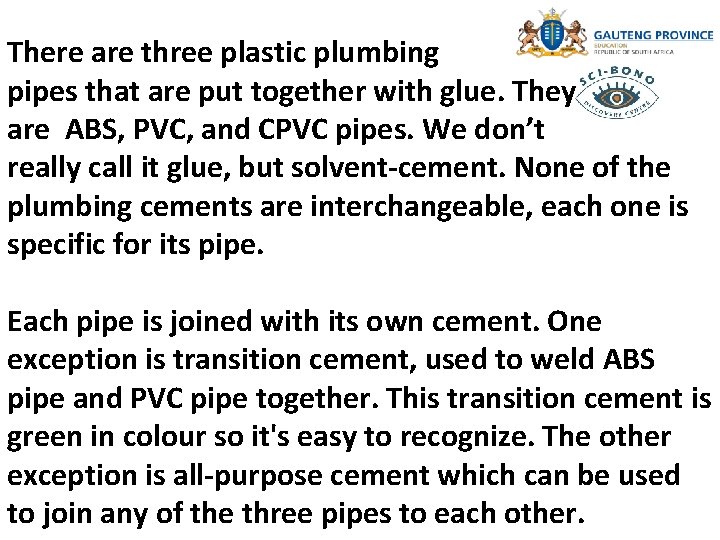
There are three plastic plumbing pipes that are put together with glue. They are ABS, PVC, and CPVC pipes. We don’t really call it glue, but solvent-cement. None of the plumbing cements are interchangeable, each one is specific for its pipe. Each pipe is joined with its own cement. One exception is transition cement, used to weld ABS pipe and PVC pipe together. This transition cement is green in colour so it's easy to recognize. The other exception is all-purpose cement which can be used to join any of the three pipes to each other.
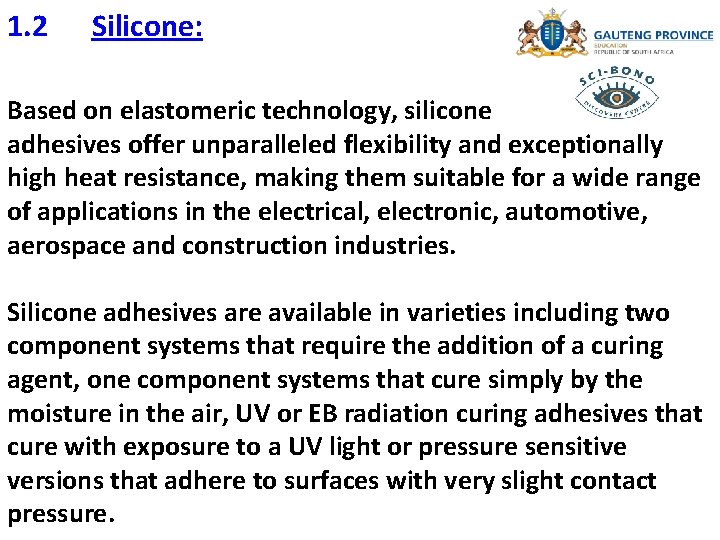
1. 2 Silicone: Based on elastomeric technology, silicone adhesives offer unparalleled flexibility and exceptionally high heat resistance, making them suitable for a wide range of applications in the electrical, electronic, automotive, aerospace and construction industries. Silicone adhesives are available in varieties including two component systems that require the addition of a curing agent, one component systems that cure simply by the moisture in the air, UV or EB radiation curing adhesives that cure with exposure to a UV light or pressure sensitive versions that adhere to surfaces with very slight contact pressure.

In general, users can count on silicone adhesives to produce bonds that can withstand high temperatures (in some cases up to 600°F), remain flexible even after curing and resist chemicals including water. With their ability to resist water and other chemicals, silicone systems are used for sealing gaskets and engines in the transportation industry. They are also used for potting and heat sink attachment in electronic applications.
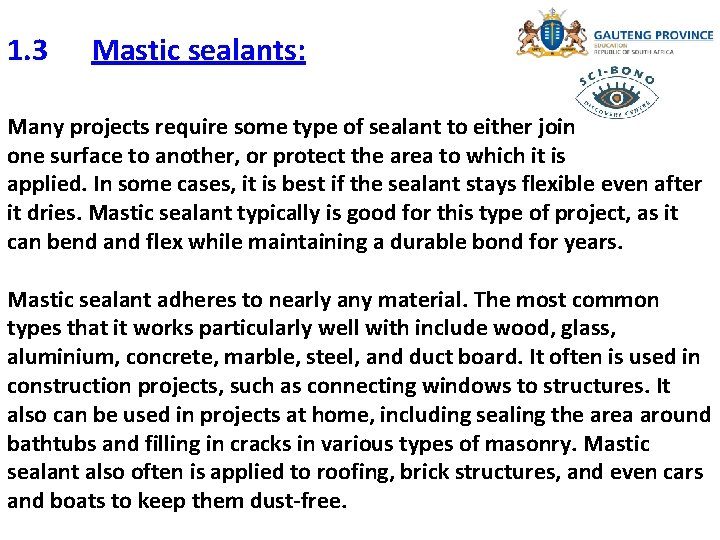
1. 3 Mastic sealants: Many projects require some type of sealant to either join one surface to another, or protect the area to which it is applied. In some cases, it is best if the sealant stays flexible even after it dries. Mastic sealant typically is good for this type of project, as it can bend and flex while maintaining a durable bond for years. Mastic sealant adheres to nearly any material. The most common types that it works particularly well with include wood, glass, aluminium, concrete, marble, steel, and duct board. It often is used in construction projects, such as connecting windows to structures. It also can be used in projects at home, including sealing the area around bathtubs and filling in cracks in various types of masonry. Mastic sealant also often is applied to roofing, brick structures, and even cars and boats to keep them dust-free.
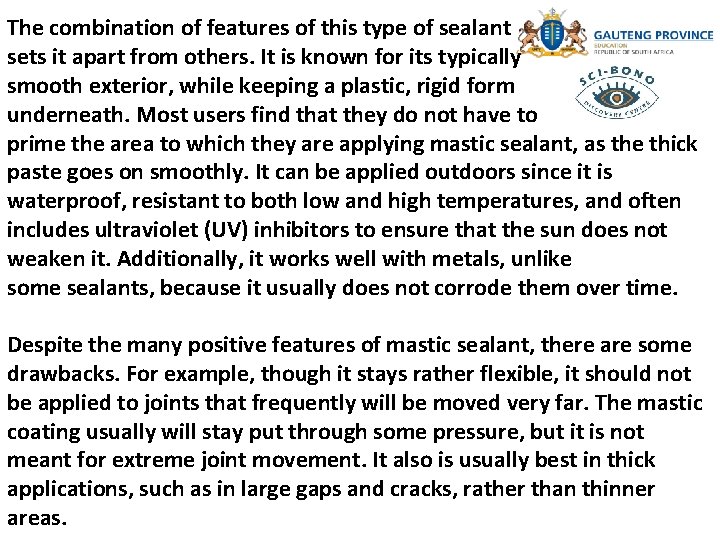
The combination of features of this type of sealant sets it apart from others. It is known for its typically smooth exterior, while keeping a plastic, rigid form underneath. Most users find that they do not have to prime the area to which they are applying mastic sealant, as the thick paste goes on smoothly. It can be applied outdoors since it is waterproof, resistant to both low and high temperatures, and often includes ultraviolet (UV) inhibitors to ensure that the sun does not weaken it. Additionally, it works well with metals, unlike some sealants, because it usually does not corrode them over time. Despite the many positive features of mastic sealant, there are some drawbacks. For example, though it stays rather flexible, it should not be applied to joints that frequently will be moved very far. The mastic coating usually will stay put through some pressure, but it is not meant for extreme joint movement. It also is usually best in thick applications, such as in large gaps and cracks, rather than thinner areas.
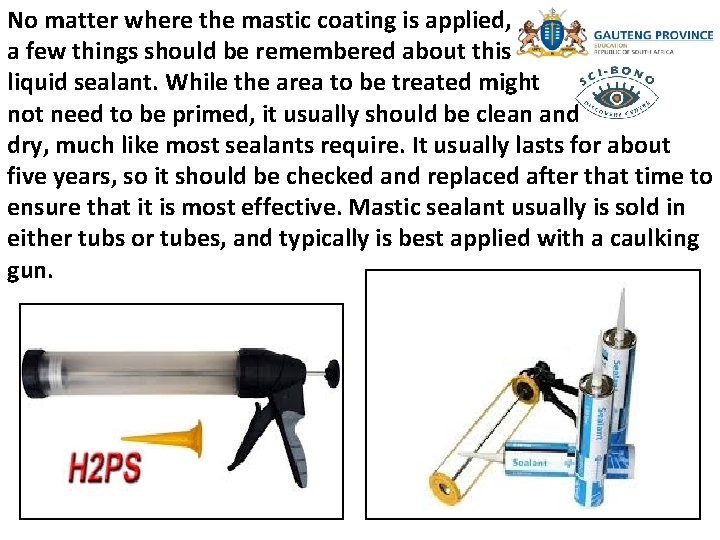
No matter where the mastic coating is applied, a few things should be remembered about this liquid sealant. While the area to be treated might not need to be primed, it usually should be clean and dry, much like most sealants require. It usually lasts for about five years, so it should be checked and replaced after that time to ensure that it is most effective. Mastic sealant usually is sold in either tubs or tubes, and typically is best applied with a caulking gun.
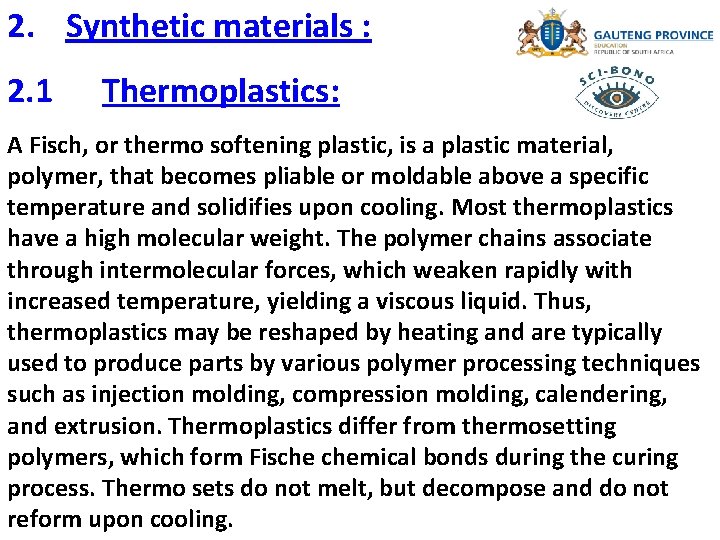
2. Synthetic materials : 2. 1 Thermoplastics: A Fisch, or thermo softening plastic, is a plastic material, polymer, that becomes pliable or moldable above a specific temperature and solidifies upon cooling. Most thermoplastics have a high molecular weight. The polymer chains associate through intermolecular forces, which weaken rapidly with increased temperature, yielding a viscous liquid. Thus, thermoplastics may be reshaped by heating and are typically used to produce parts by various polymer processing techniques such as injection molding, compression molding, calendering, and extrusion. Thermoplastics differ from thermosetting polymers, which form Fische chemical bonds during the curing process. Thermo sets do not melt, but decompose and do not reform upon cooling.
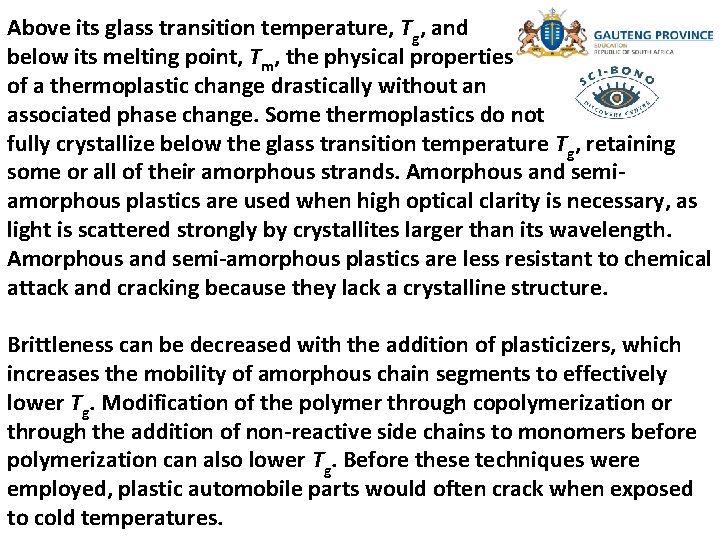
Above its glass transition temperature, Tg, and below its melting point, Tm, the physical properties of a thermoplastic change drastically without an associated phase change. Some thermoplastics do not fully crystallize below the glass transition temperature Tg, retaining some or all of their amorphous strands. Amorphous and semiamorphous plastics are used when high optical clarity is necessary, as light is scattered strongly by crystallites larger than its wavelength. Amorphous and semi-amorphous plastics are less resistant to chemical attack and cracking because they lack a crystalline structure. Brittleness can be decreased with the addition of plasticizers, which increases the mobility of amorphous chain segments to effectively lower Tg. Modification of the polymer through copolymerization or through the addition of non-reactive side chains to monomers before polymerization can also lower Tg. Before these techniques were employed, plastic automobile parts would often crack when exposed to cold temperatures.
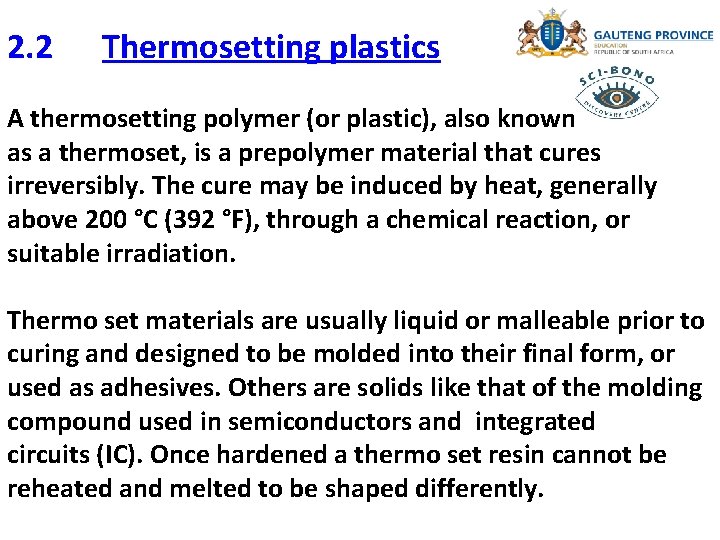
2. 2 Thermosetting plastics A thermosetting polymer (or plastic), also known as a thermoset, is a prepolymer material that cures irreversibly. The cure may be induced by heat, generally above 200 °C (392 °F), through a chemical reaction, or suitable irradiation. Thermo set materials are usually liquid or malleable prior to curing and designed to be molded into their final form, or used as adhesives. Others are solids like that of the molding compound used in semiconductors and integrated circuits (IC). Once hardened a thermo set resin cannot be reheated and melted to be shaped differently.
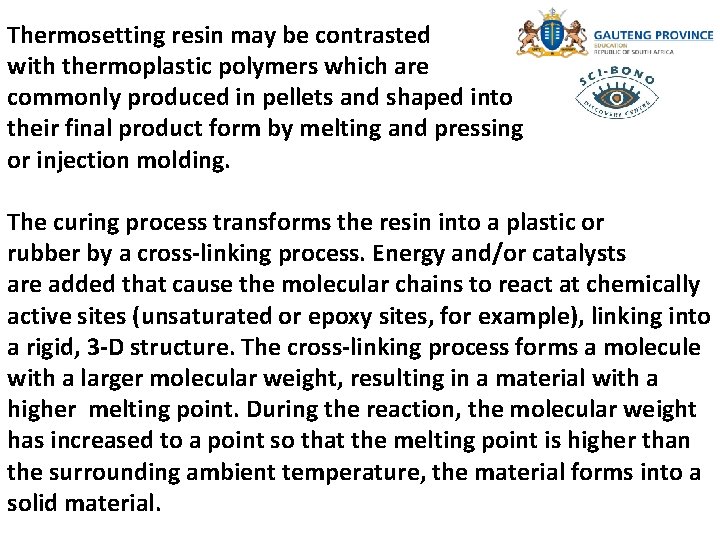
Thermosetting resin may be contrasted with thermoplastic polymers which are commonly produced in pellets and shaped into their final product form by melting and pressing or injection molding. The curing process transforms the resin into a plastic or rubber by a cross-linking process. Energy and/or catalysts are added that cause the molecular chains to react at chemically active sites (unsaturated or epoxy sites, for example), linking into a rigid, 3 -D structure. The cross-linking process forms a molecule with a larger molecular weight, resulting in a material with a higher melting point. During the reaction, the molecular weight has increased to a point so that the melting point is higher than the surrounding ambient temperature, the material forms into a solid material.
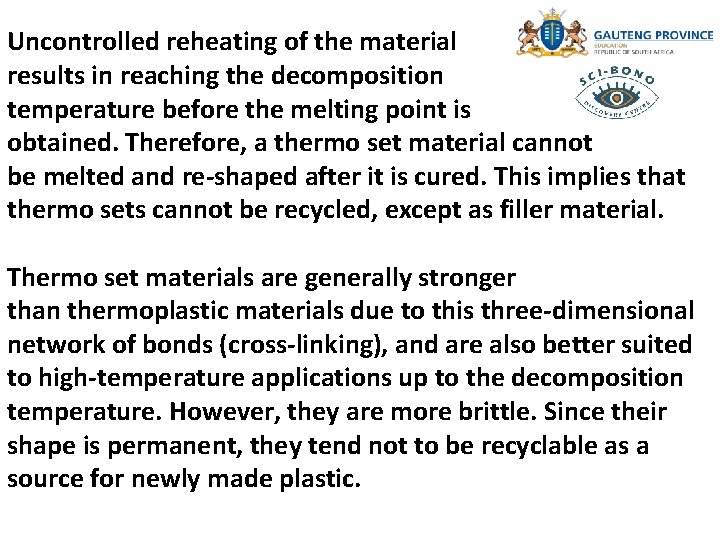
Uncontrolled reheating of the material results in reaching the decomposition temperature before the melting point is obtained. Therefore, a thermo set material cannot be melted and re-shaped after it is cured. This implies that thermo sets cannot be recycled, except as filler material. Thermo set materials are generally stronger than thermoplastic materials due to this three-dimensional network of bonds (cross-linking), and are also better suited to high-temperature applications up to the decomposition temperature. However, they are more brittle. Since their shape is permanent, they tend not to be recyclable as a source for newly made plastic.
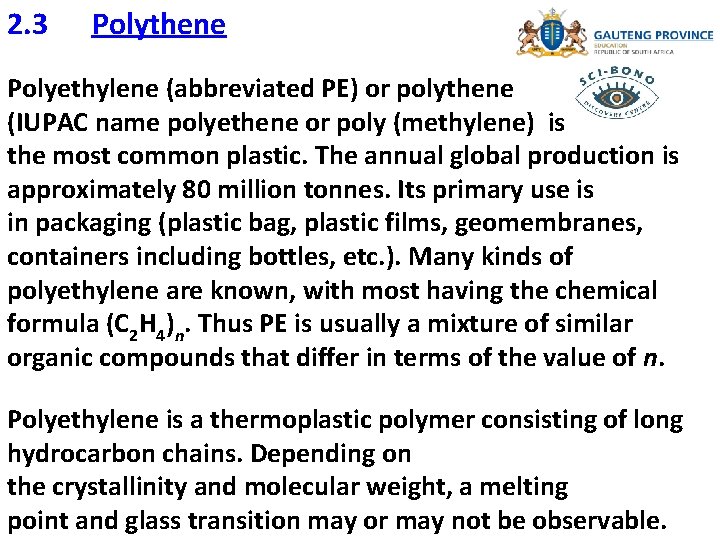
2. 3 Polythene Polyethylene (abbreviated PE) or polythene (IUPAC name polyethene or poly (methylene) is the most common plastic. The annual global production is approximately 80 million tonnes. Its primary use is in packaging (plastic bag, plastic films, geomembranes, containers including bottles, etc. ). Many kinds of polyethylene are known, with most having the chemical formula (C 2 H 4)n. Thus PE is usually a mixture of similar organic compounds that differ in terms of the value of n. Polyethylene is a thermoplastic polymer consisting of long hydrocarbon chains. Depending on the crystallinity and molecular weight, a melting point and glass transition may or may not be observable.
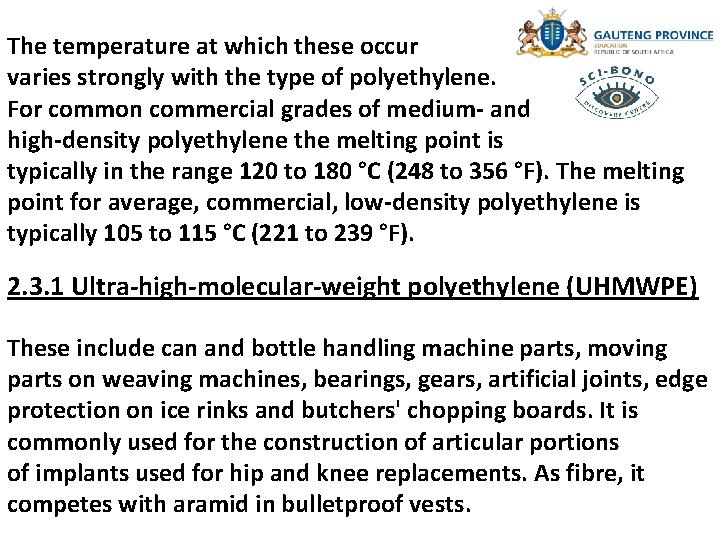
The temperature at which these occur varies strongly with the type of polyethylene. For common commercial grades of medium- and high-density polyethylene the melting point is typically in the range 120 to 180 °C (248 to 356 °F). The melting point for average, commercial, low-density polyethylene is typically 105 to 115 °C (221 to 239 °F). 2. 3. 1 Ultra-high-molecular-weight polyethylene (UHMWPE) These include can and bottle handling machine parts, moving parts on weaving machines, bearings, gears, artificial joints, edge protection on ice rinks and butchers' chopping boards. It is commonly used for the construction of articular portions of implants used for hip and knee replacements. As fibre, it competes with aramid in bulletproof vests.
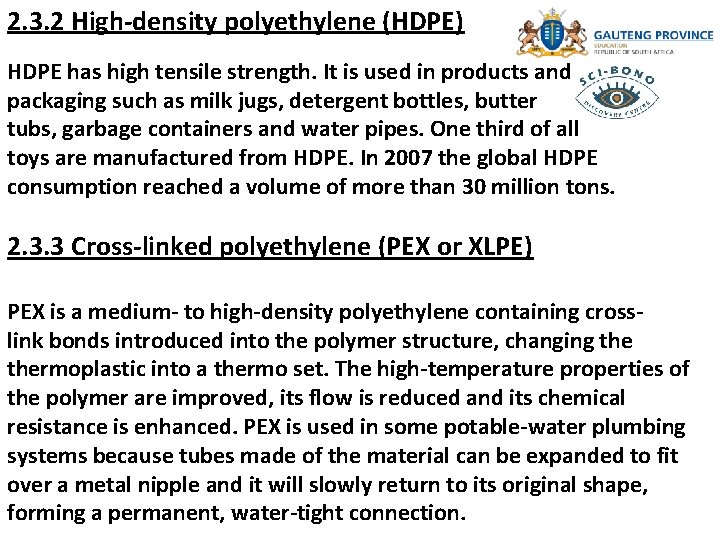
2. 3. 2 High-density polyethylene (HDPE) HDPE has high tensile strength. It is used in products and packaging such as milk jugs, detergent bottles, butter tubs, garbage containers and water pipes. One third of all toys are manufactured from HDPE. In 2007 the global HDPE consumption reached a volume of more than 30 million tons. 2. 3. 3 Cross-linked polyethylene (PEX or XLPE) PEX is a medium- to high-density polyethylene containing crosslink bonds introduced into the polymer structure, changing thermoplastic into a thermo set. The high-temperature properties of the polymer are improved, its flow is reduced and its chemical resistance is enhanced. PEX is used in some potable-water plumbing systems because tubes made of the material can be expanded to fit over a metal nipple and it will slowly return to its original shape, forming a permanent, water-tight connection.
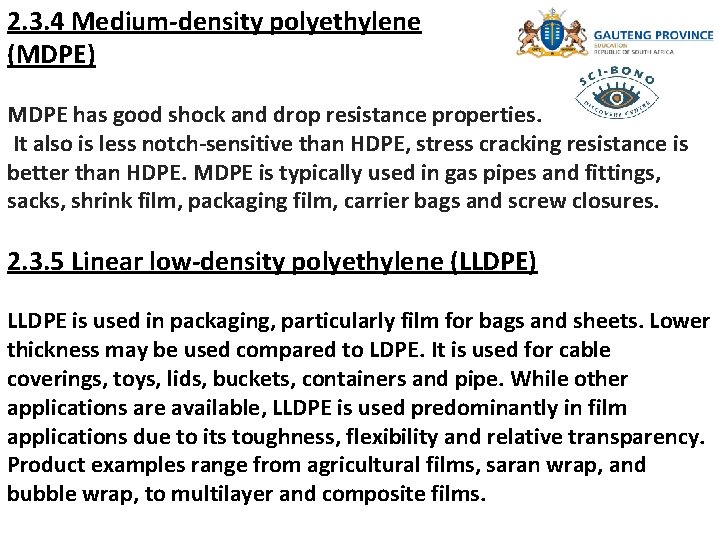
2. 3. 4 Medium-density polyethylene (MDPE) MDPE has good shock and drop resistance properties. It also is less notch-sensitive than HDPE, stress cracking resistance is better than HDPE. MDPE is typically used in gas pipes and fittings, sacks, shrink film, packaging film, carrier bags and screw closures. 2. 3. 5 Linear low-density polyethylene (LLDPE) LLDPE is used in packaging, particularly film for bags and sheets. Lower thickness may be used compared to LDPE. It is used for cable coverings, toys, lids, buckets, containers and pipe. While other applications are available, LLDPE is used predominantly in film applications due to its toughness, flexibility and relative transparency. Product examples range from agricultural films, saran wrap, and bubble wrap, to multilayer and composite films.
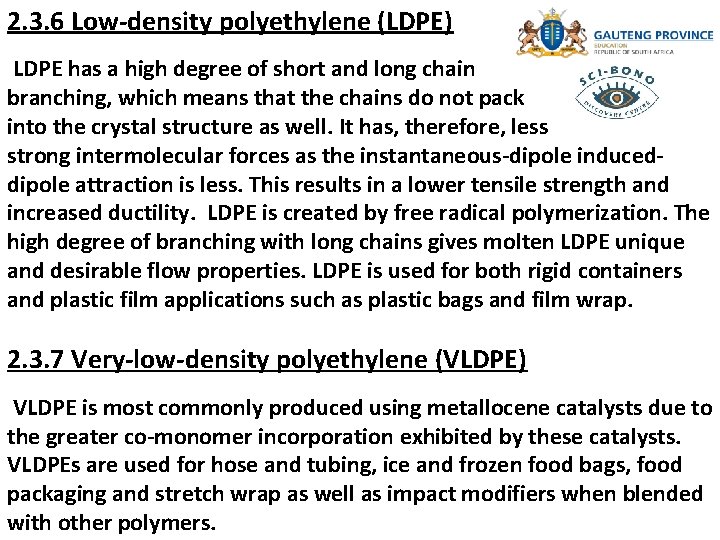
2. 3. 6 Low-density polyethylene (LDPE) LDPE has a high degree of short and long chain branching, which means that the chains do not pack into the crystal structure as well. It has, therefore, less strong intermolecular forces as the instantaneous-dipole induceddipole attraction is less. This results in a lower tensile strength and increased ductility. LDPE is created by free radical polymerization. The high degree of branching with long chains gives molten LDPE unique and desirable flow properties. LDPE is used for both rigid containers and plastic film applications such as plastic bags and film wrap. 2. 3. 7 Very-low-density polyethylene (VLDPE) VLDPE is most commonly produced using metallocene catalysts due to the greater co-monomer incorporation exhibited by these catalysts. VLDPEs are used for hose and tubing, ice and frozen food bags, food packaging and stretch wrap as well as impact modifiers when blended with other polymers.
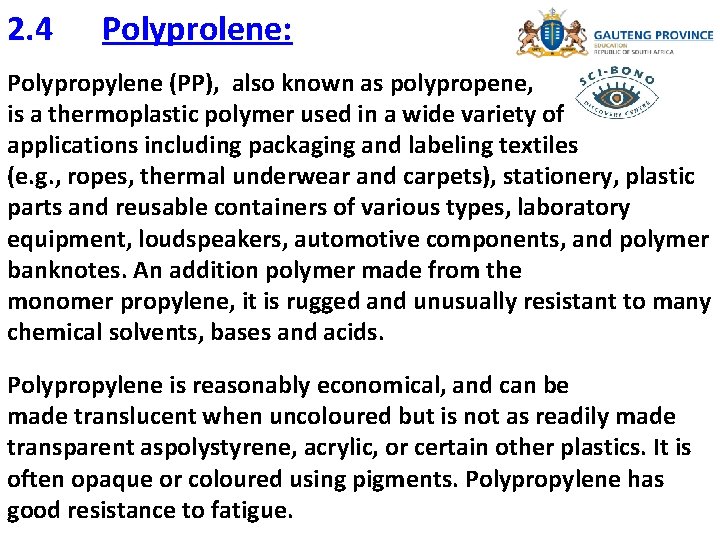
2. 4 Polyprolene: Polypropylene (PP), also known as polypropene, is a thermoplastic polymer used in a wide variety of applications including packaging and labeling textiles (e. g. , ropes, thermal underwear and carpets), stationery, plastic parts and reusable containers of various types, laboratory equipment, loudspeakers, automotive components, and polymer banknotes. An addition polymer made from the monomer propylene, it is rugged and unusually resistant to many chemical solvents, bases and acids. Polypropylene is reasonably economical, and can be made translucent when uncoloured but is not as readily made transparent aspolystyrene, acrylic, or certain other plastics. It is often opaque or coloured using pigments. Polypropylene has good resistance to fatigue.
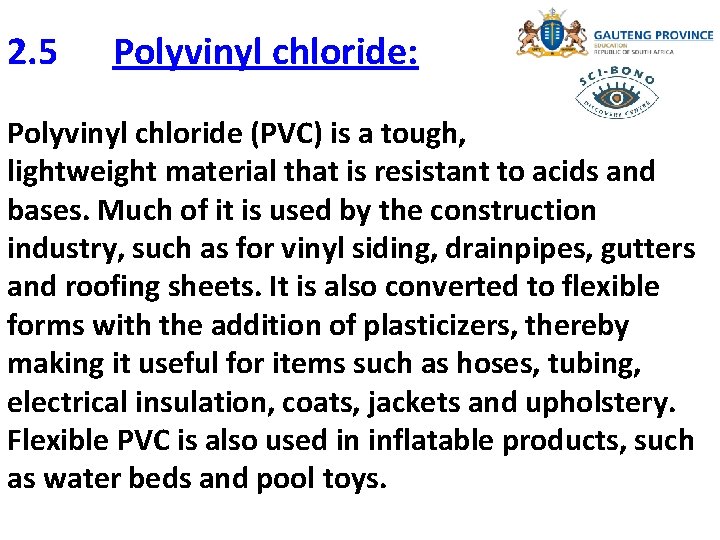
2. 5 Polyvinyl chloride: Polyvinyl chloride (PVC) is a tough, lightweight material that is resistant to acids and bases. Much of it is used by the construction industry, such as for vinyl siding, drainpipes, gutters and roofing sheets. It is also converted to flexible forms with the addition of plasticizers, thereby making it useful for items such as hoses, tubing, electrical insulation, coats, jackets and upholstery. Flexible PVC is also used in inflatable products, such as water beds and pool toys.
Ekurhuleni department of education
Department of education revised curriculum 2020
10 pillars of education in gauteng
Havering college of further and higher education
Department of higher education and training
Further education support service
Webdhis
Learner attainment improvement plan 2020
Dbe moodle
Gauteng rapid land release programme
Difference between further and furthermore
Springs and strings
Metaphor definition
Simplification of a force and couple system
Further mechanics 1 unit test 1 momentum and impulse
Department of labor and training
Further study design
Starboard and port side
Dr frost further kinematics
"not for distribution" confidential
Kali jelen
Further applications of integration
Further applications of integration