F16 Production NonCr 6 Implementation USAF NonChrome TIM
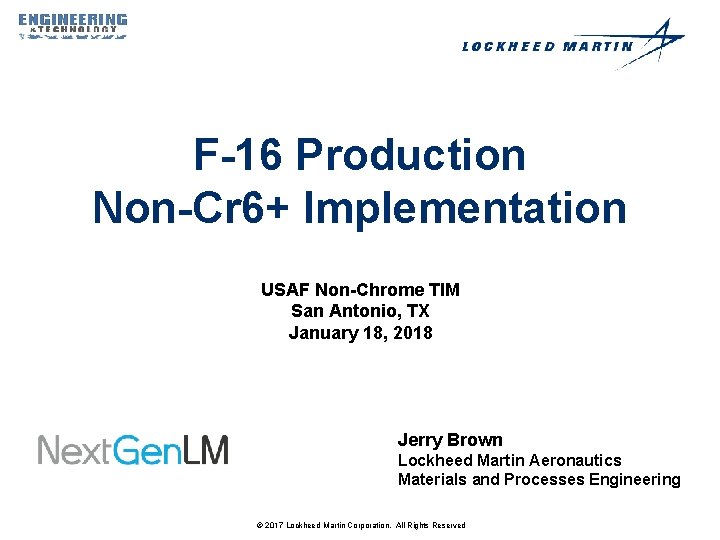
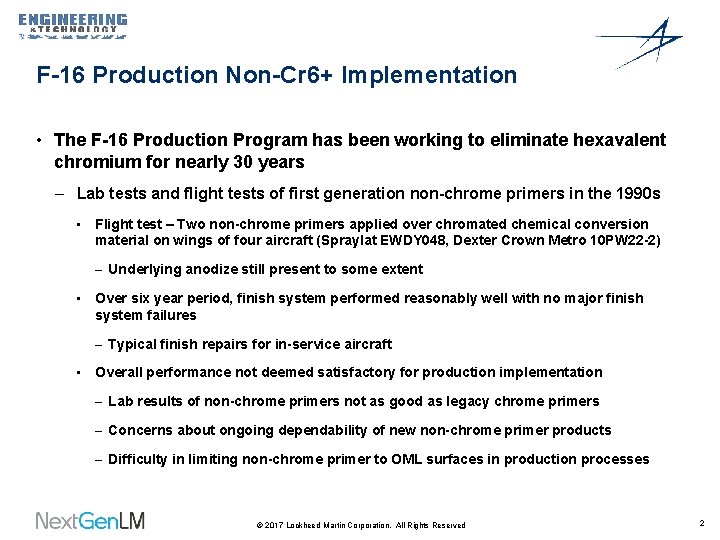
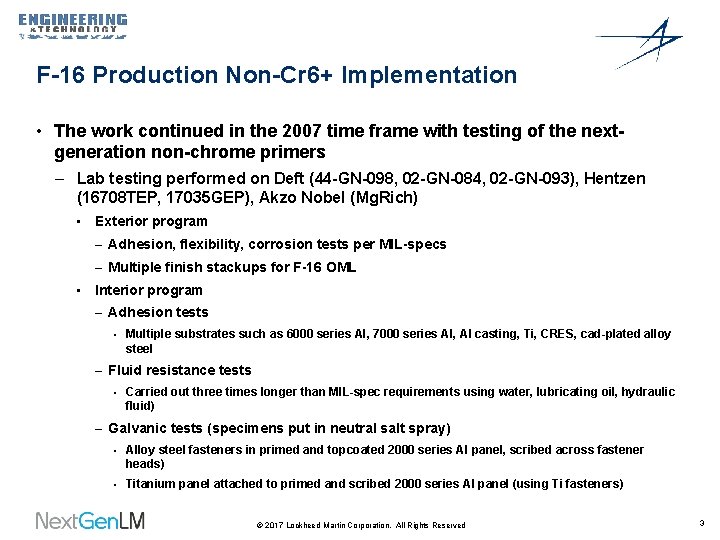
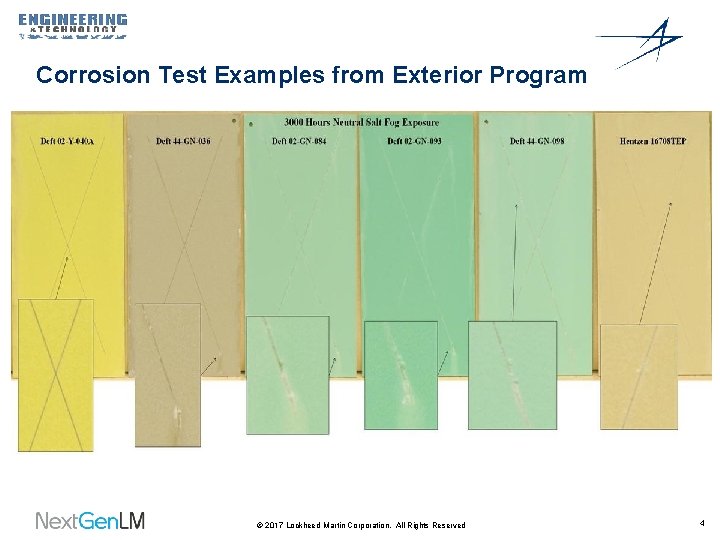
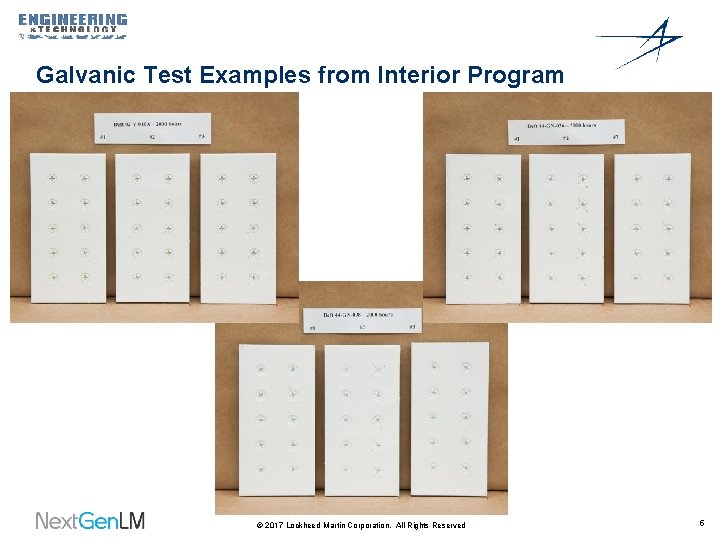
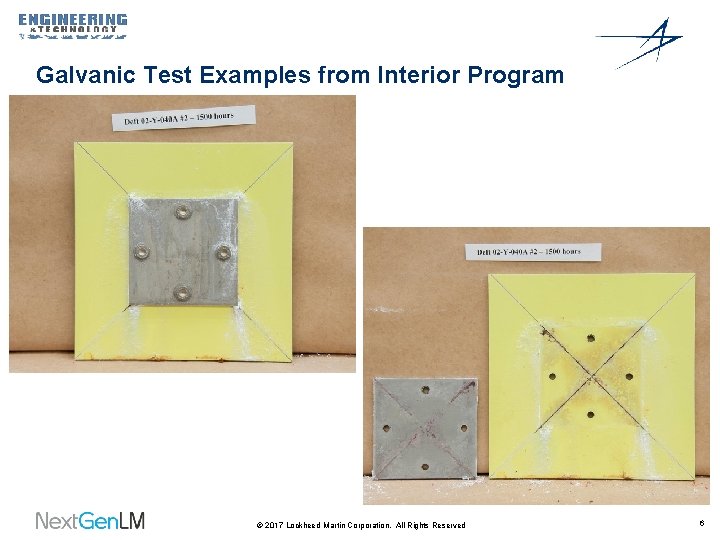
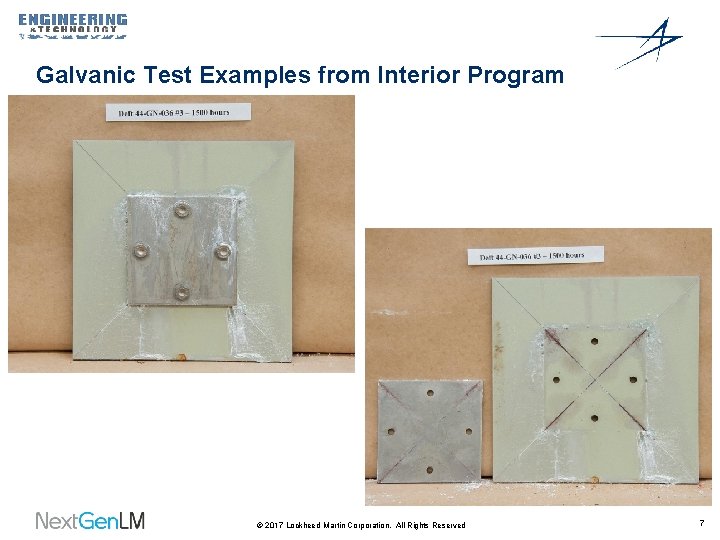
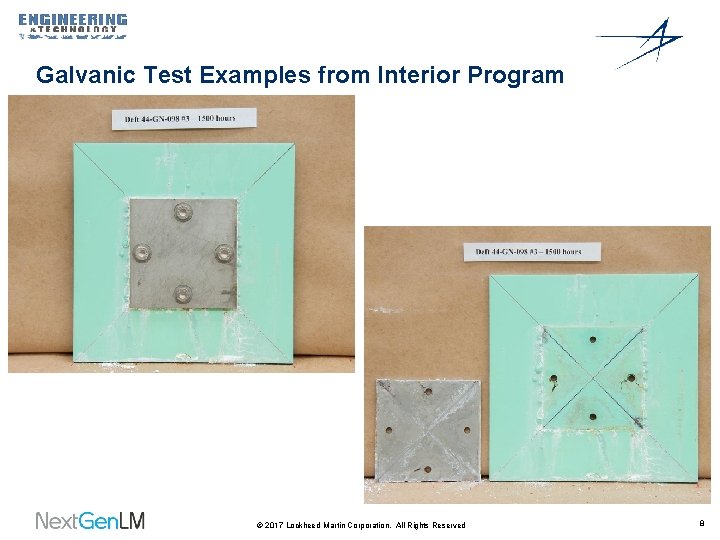
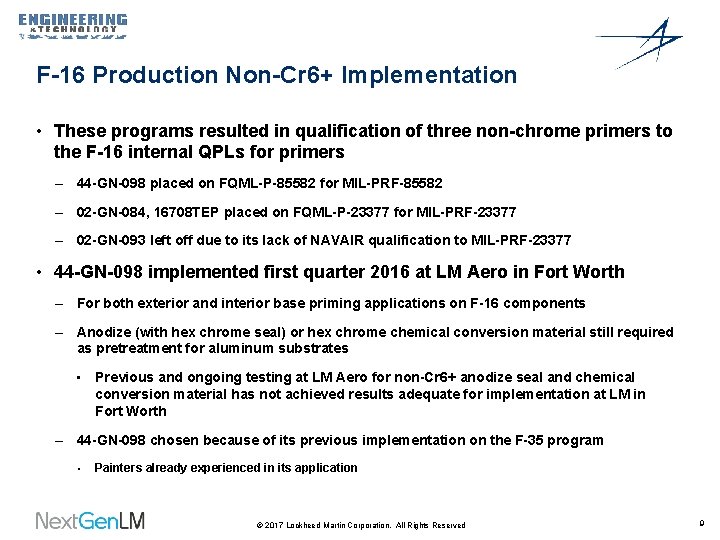
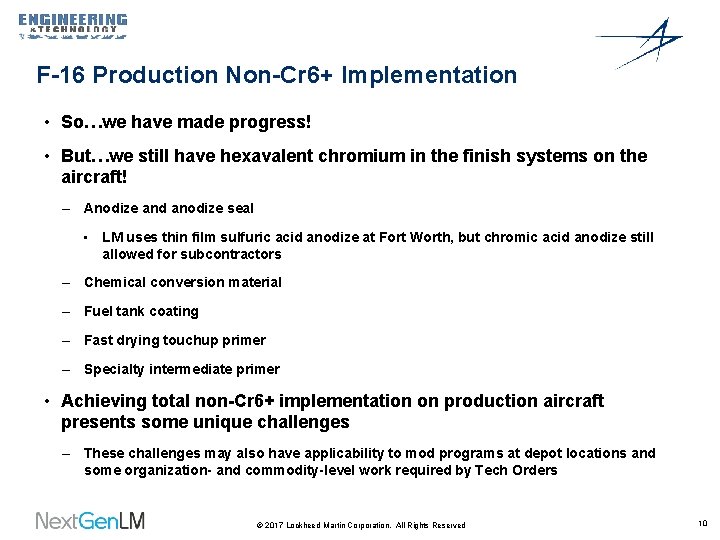
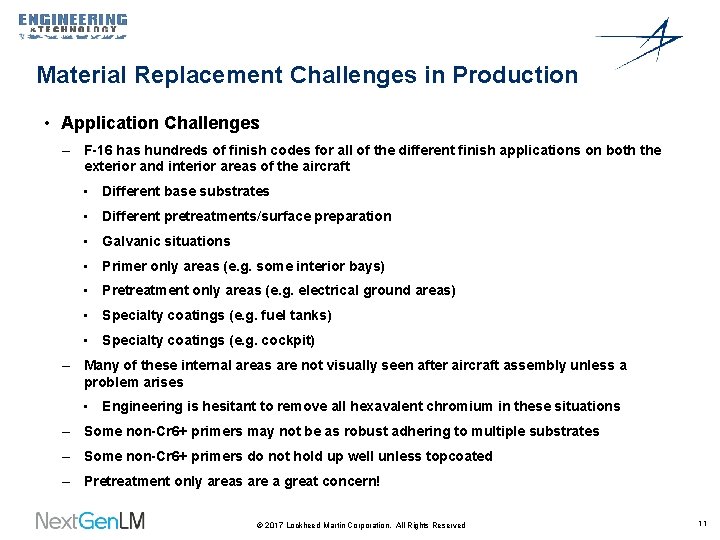
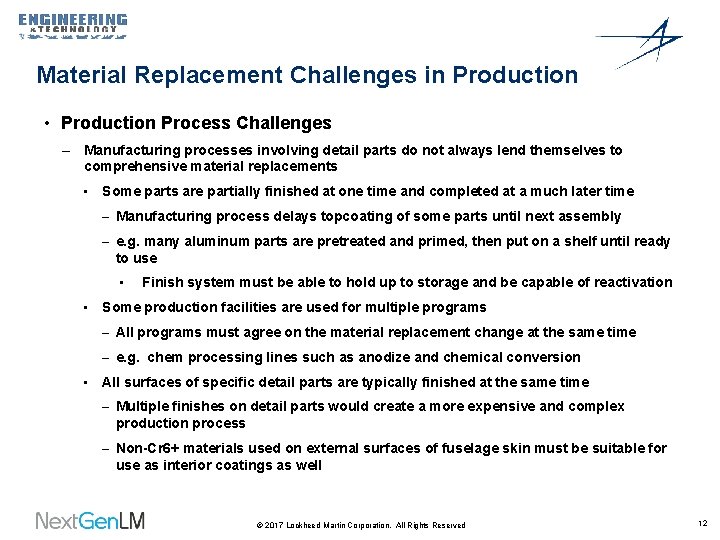
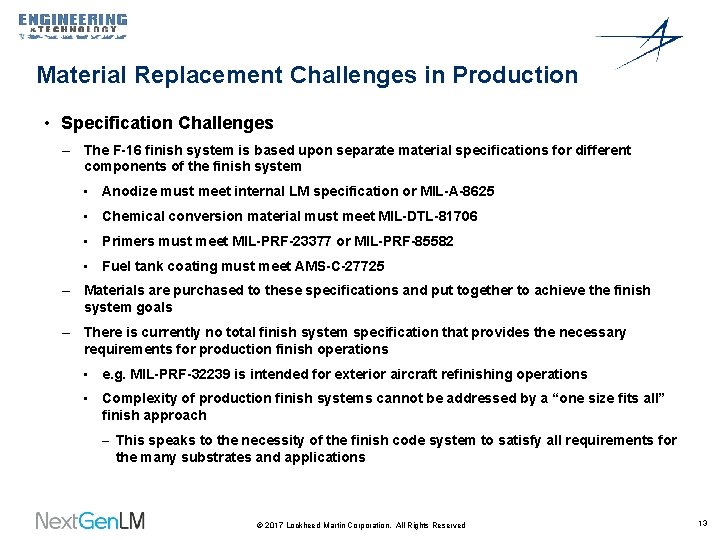
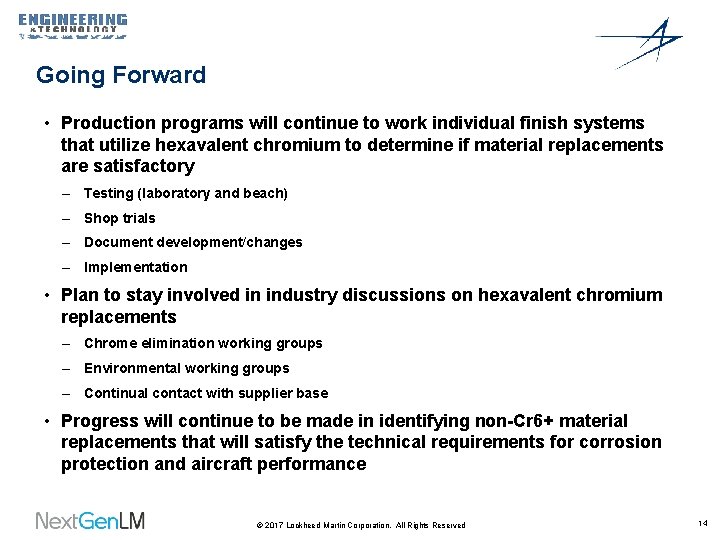
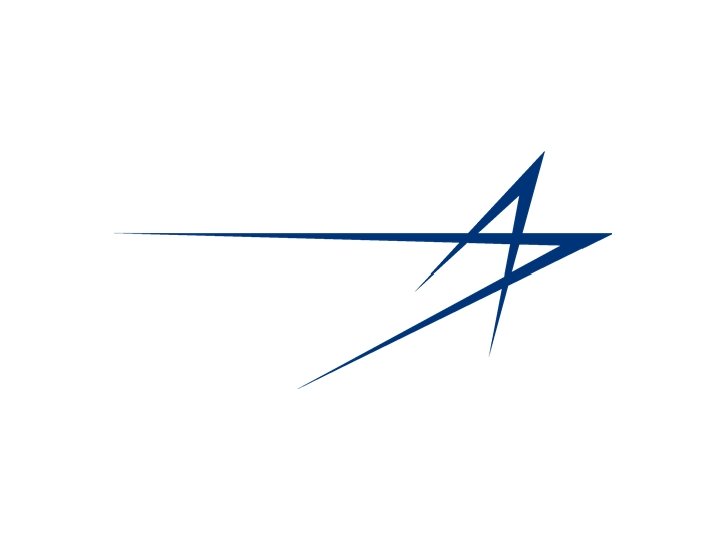
- Slides: 15
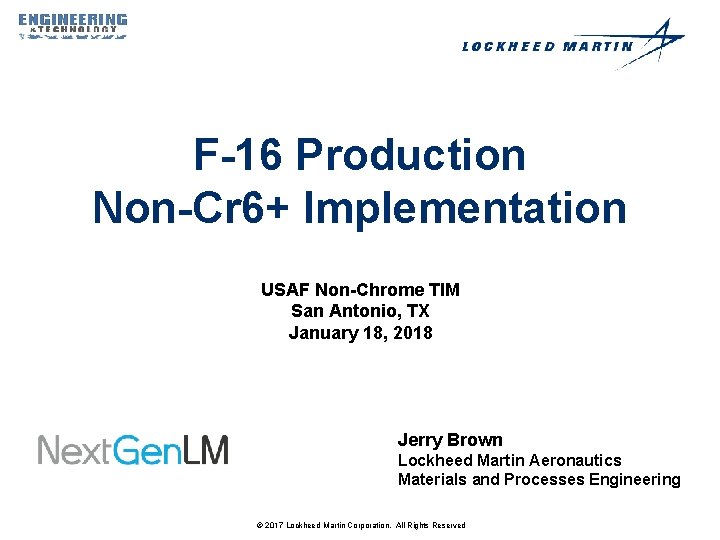
F-16 Production Non-Cr 6+ Implementation USAF Non-Chrome TIM San Antonio, TX January 18, 2018 Jerry Brown Lockheed Martin Aeronautics Materials and Processes Engineering © 2017 Lockheed Martin Corporation. All Rights Reserved
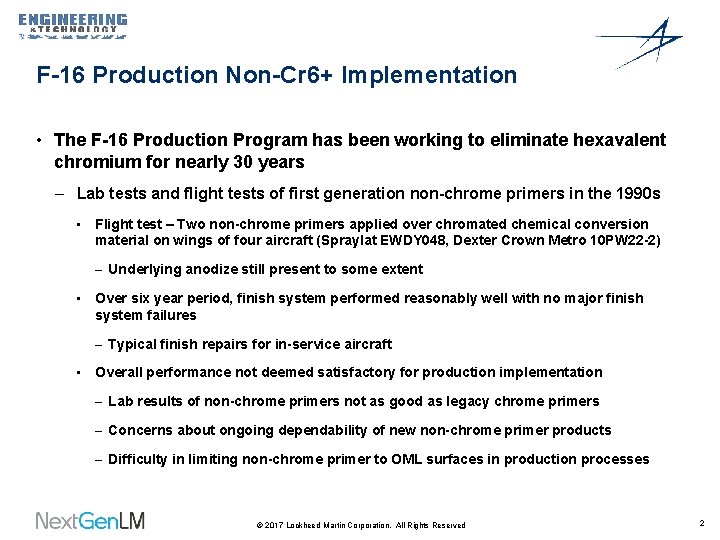
F-16 Production Non-Cr 6+ Implementation • The F-16 Production Program has been working to eliminate hexavalent chromium for nearly 30 years – Lab tests and flight tests of first generation non-chrome primers in the 1990 s • Flight test – Two non-chrome primers applied over chromated chemical conversion material on wings of four aircraft (Spraylat EWDY 048, Dexter Crown Metro 10 PW 22 -2) – Underlying anodize still present to some extent • Over six year period, finish system performed reasonably well with no major finish system failures – Typical finish repairs for in-service aircraft • Overall performance not deemed satisfactory for production implementation – Lab results of non-chrome primers not as good as legacy chrome primers – Concerns about ongoing dependability of new non-chrome primer products – Difficulty in limiting non-chrome primer to OML surfaces in production processes © 2017 Lockheed Martin Corporation. All Rights Reserved 2
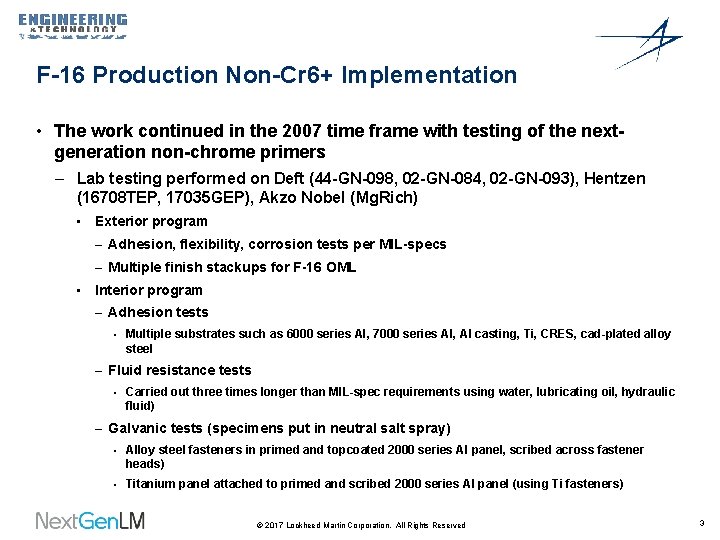
F-16 Production Non-Cr 6+ Implementation • The work continued in the 2007 time frame with testing of the nextgeneration non-chrome primers – Lab testing performed on Deft (44 -GN-098, 02 -GN-084, 02 -GN-093), Hentzen (16708 TEP, 17035 GEP), Akzo Nobel (Mg. Rich) • Exterior program – Adhesion, flexibility, corrosion tests per MIL-specs – Multiple finish stackups for F-16 OML • Interior program – Adhesion tests • Multiple substrates such as 6000 series Al, 7000 series Al, Al casting, Ti, CRES, cad-plated alloy steel – Fluid resistance tests • Carried out three times longer than MIL-spec requirements using water, lubricating oil, hydraulic fluid) – Galvanic tests (specimens put in neutral salt spray) • Alloy steel fasteners in primed and topcoated 2000 series Al panel, scribed across fastener heads) • Titanium panel attached to primed and scribed 2000 series Al panel (using Ti fasteners) © 2017 Lockheed Martin Corporation. All Rights Reserved 3
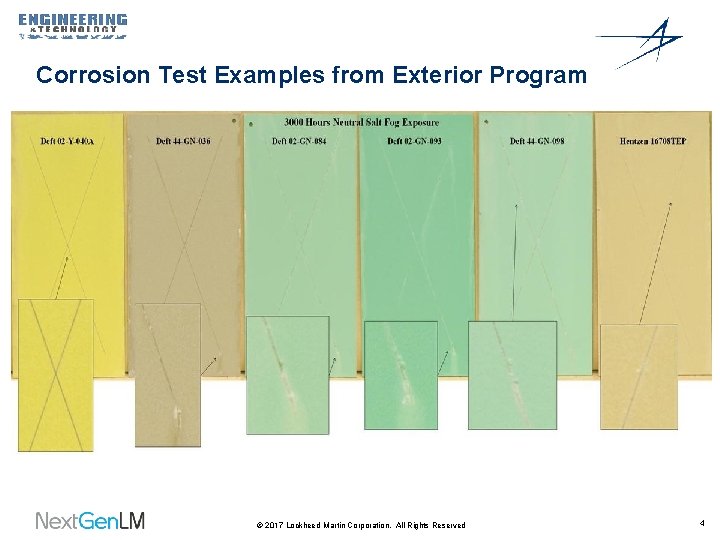
Corrosion Test Examples from Exterior Program © 2017 Lockheed Martin Corporation. All Rights Reserved 4
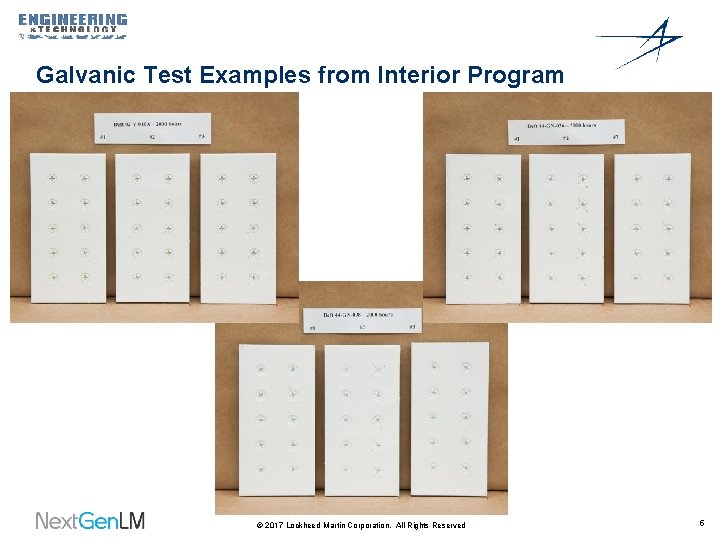
Galvanic Test Examples from Interior Program © 2017 Lockheed Martin Corporation. All Rights Reserved 5
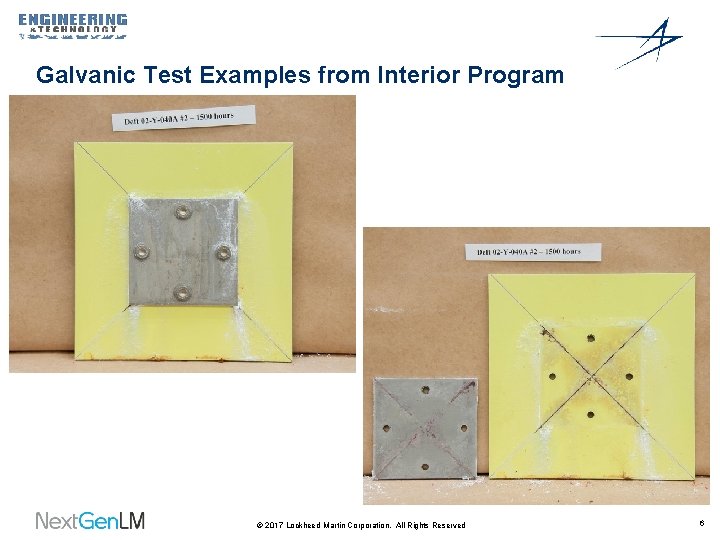
Galvanic Test Examples from Interior Program © 2017 Lockheed Martin Corporation. All Rights Reserved 6
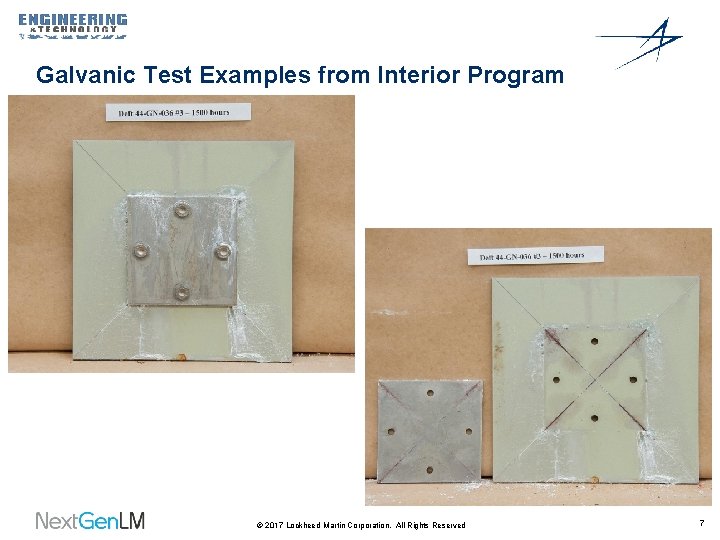
Galvanic Test Examples from Interior Program © 2017 Lockheed Martin Corporation. All Rights Reserved 7
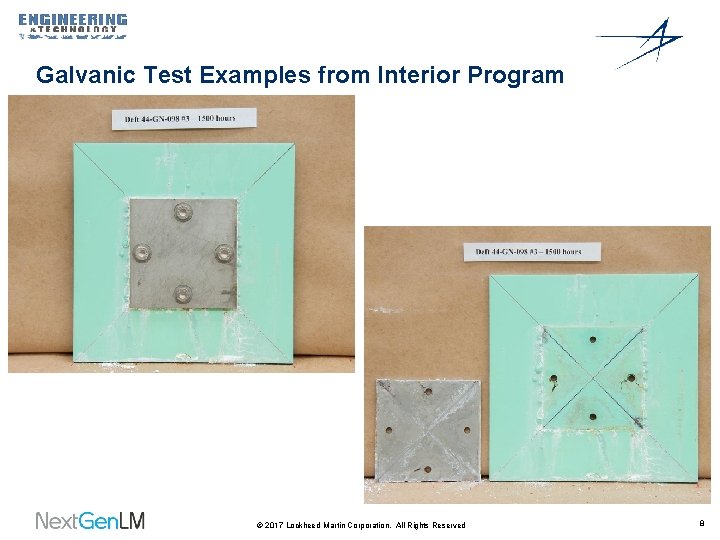
Galvanic Test Examples from Interior Program © 2017 Lockheed Martin Corporation. All Rights Reserved 8
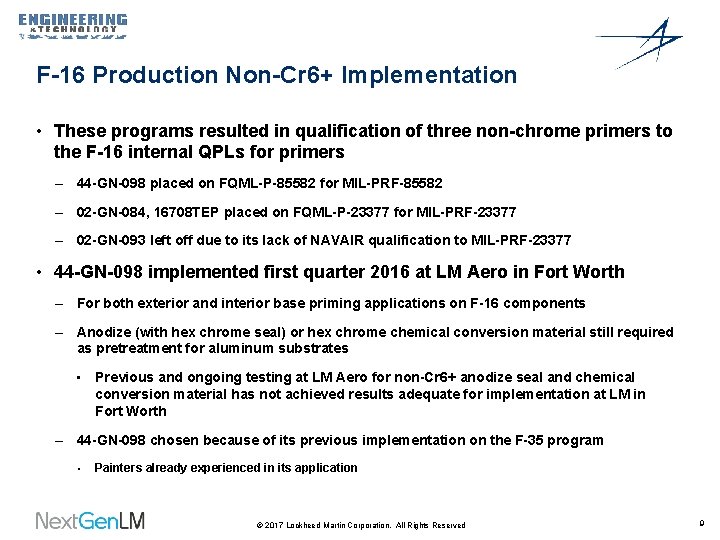
F-16 Production Non-Cr 6+ Implementation • These programs resulted in qualification of three non-chrome primers to the F-16 internal QPLs for primers – 44 -GN-098 placed on FQML-P-85582 for MIL-PRF-85582 – 02 -GN-084, 16708 TEP placed on FQML-P-23377 for MIL-PRF-23377 – 02 -GN-093 left off due to its lack of NAVAIR qualification to MIL-PRF-23377 • 44 -GN-098 implemented first quarter 2016 at LM Aero in Fort Worth – For both exterior and interior base priming applications on F-16 components – Anodize (with hex chrome seal) or hex chrome chemical conversion material still required as pretreatment for aluminum substrates • Previous and ongoing testing at LM Aero for non-Cr 6+ anodize seal and chemical conversion material has not achieved results adequate for implementation at LM in Fort Worth – 44 -GN-098 chosen because of its previous implementation on the F-35 program • Painters already experienced in its application © 2017 Lockheed Martin Corporation. All Rights Reserved 9
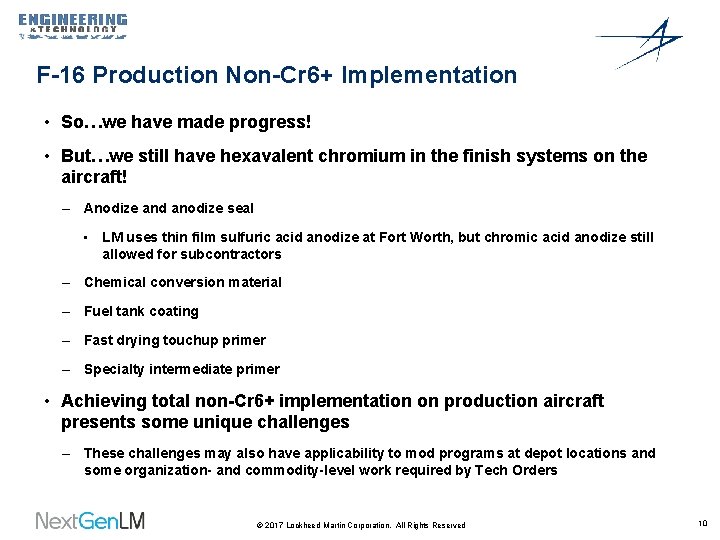
F-16 Production Non-Cr 6+ Implementation • So…we have made progress! • But…we still have hexavalent chromium in the finish systems on the aircraft! – Anodize and anodize seal • LM uses thin film sulfuric acid anodize at Fort Worth, but chromic acid anodize still allowed for subcontractors – Chemical conversion material – Fuel tank coating – Fast drying touchup primer – Specialty intermediate primer • Achieving total non-Cr 6+ implementation on production aircraft presents some unique challenges – These challenges may also have applicability to mod programs at depot locations and some organization- and commodity-level work required by Tech Orders © 2017 Lockheed Martin Corporation. All Rights Reserved 10
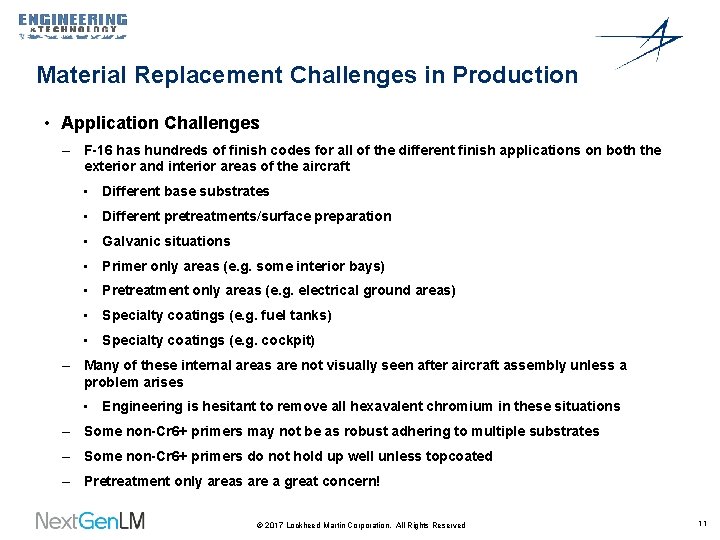
Material Replacement Challenges in Production • Application Challenges – F-16 has hundreds of finish codes for all of the different finish applications on both the exterior and interior areas of the aircraft • Different base substrates • Different pretreatments/surface preparation • Galvanic situations • Primer only areas (e. g. some interior bays) • Pretreatment only areas (e. g. electrical ground areas) • Specialty coatings (e. g. fuel tanks) • Specialty coatings (e. g. cockpit) – Many of these internal areas are not visually seen after aircraft assembly unless a problem arises • Engineering is hesitant to remove all hexavalent chromium in these situations – Some non-Cr 6+ primers may not be as robust adhering to multiple substrates – Some non-Cr 6+ primers do not hold up well unless topcoated – Pretreatment only areas are a great concern! © 2017 Lockheed Martin Corporation. All Rights Reserved 11
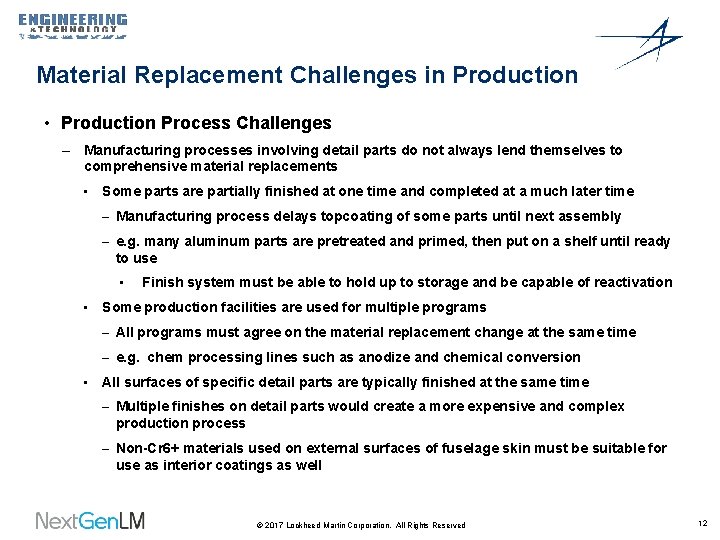
Material Replacement Challenges in Production • Production Process Challenges – Manufacturing processes involving detail parts do not always lend themselves to comprehensive material replacements • Some parts are partially finished at one time and completed at a much later time – Manufacturing process delays topcoating of some parts until next assembly – e. g. many aluminum parts are pretreated and primed, then put on a shelf until ready to use • • Finish system must be able to hold up to storage and be capable of reactivation Some production facilities are used for multiple programs – All programs must agree on the material replacement change at the same time – e. g. chem processing lines such as anodize and chemical conversion • All surfaces of specific detail parts are typically finished at the same time – Multiple finishes on detail parts would create a more expensive and complex production process – Non-Cr 6+ materials used on external surfaces of fuselage skin must be suitable for use as interior coatings as well © 2017 Lockheed Martin Corporation. All Rights Reserved 12
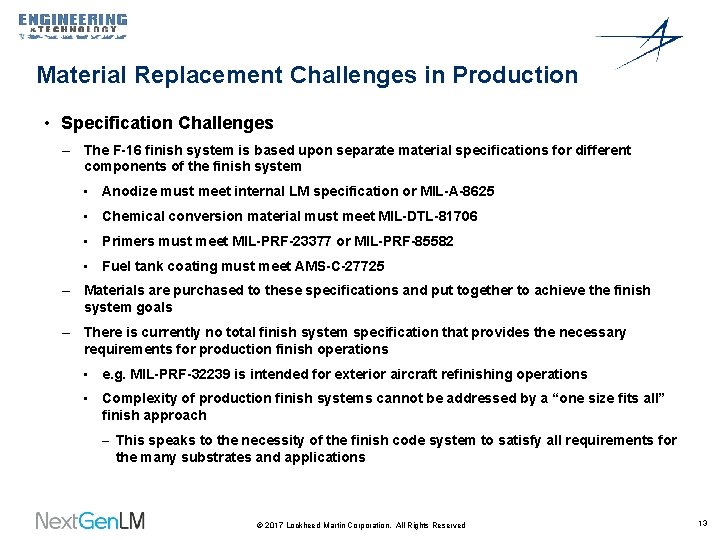
Material Replacement Challenges in Production • Specification Challenges – The F-16 finish system is based upon separate material specifications for different components of the finish system • Anodize must meet internal LM specification or MIL-A-8625 • Chemical conversion material must meet MIL-DTL-81706 • Primers must meet MIL-PRF-23377 or MIL-PRF-85582 • Fuel tank coating must meet AMS-C-27725 – Materials are purchased to these specifications and put together to achieve the finish system goals – There is currently no total finish system specification that provides the necessary requirements for production finish operations • e. g. MIL-PRF-32239 is intended for exterior aircraft refinishing operations • Complexity of production finish systems cannot be addressed by a “one size fits all” finish approach – This speaks to the necessity of the finish code system to satisfy all requirements for the many substrates and applications © 2017 Lockheed Martin Corporation. All Rights Reserved 13
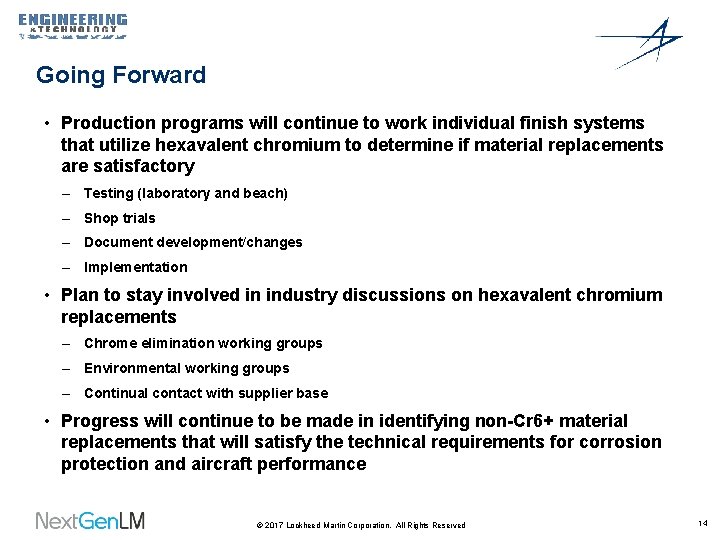
Going Forward • Production programs will continue to work individual finish systems that utilize hexavalent chromium to determine if material replacements are satisfactory – Testing (laboratory and beach) – Shop trials – Document development/changes – Implementation • Plan to stay involved in industry discussions on hexavalent chromium replacements – Chrome elimination working groups – Environmental working groups – Continual contact with supplier base • Progress will continue to be made in identifying non-Cr 6+ material replacements that will satisfy the technical requirements for corrosion protection and aircraft performance © 2017 Lockheed Martin Corporation. All Rights Reserved 14
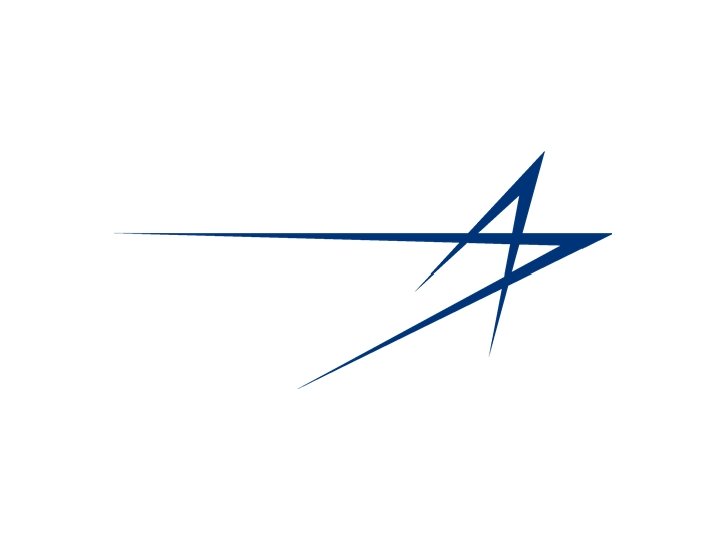
Noncr
Alir proses produksi produk multimedia
Sfw f16
F16 net
F16 mc
Air force progressive discipline chart
Usaf first sergeant afi
Usaf 2 line prf examples
Progressive discipline air force
Promotions afi
Usaf first sergeant afi
Afi 36-2908
Ehr implementation work breakdown structure
How to create a pmo implementation plan
Implementation design principles
Buddy memory allocation implementation