Euro Cir Col WP 5 CEA Activities FCC
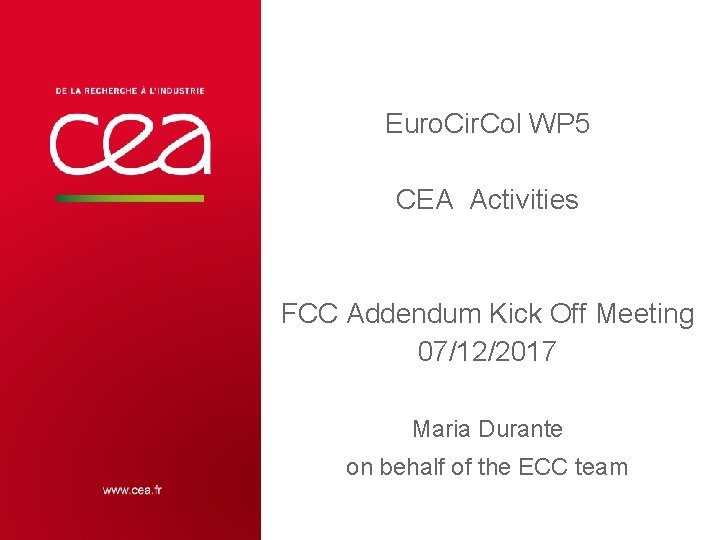
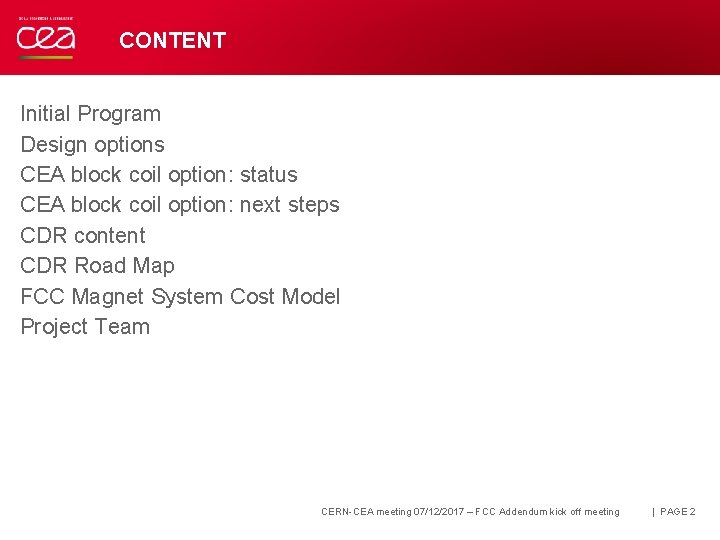
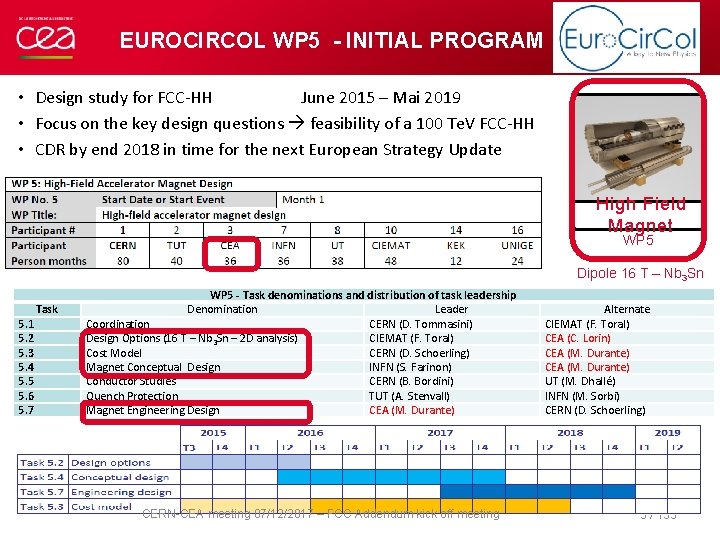
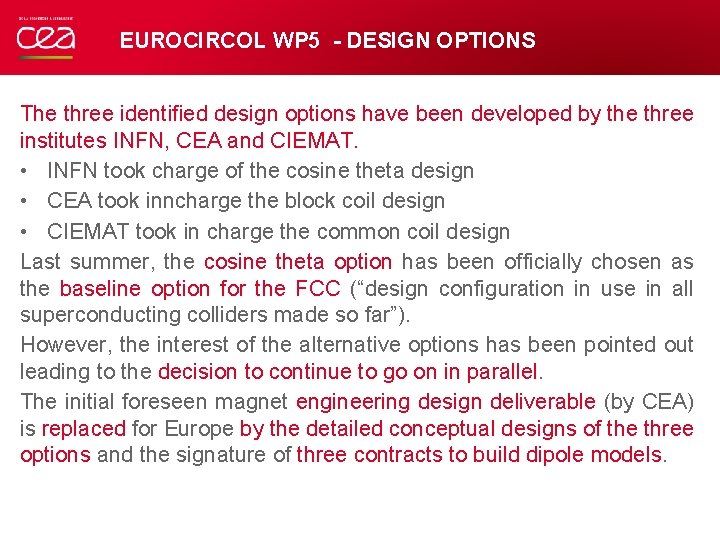
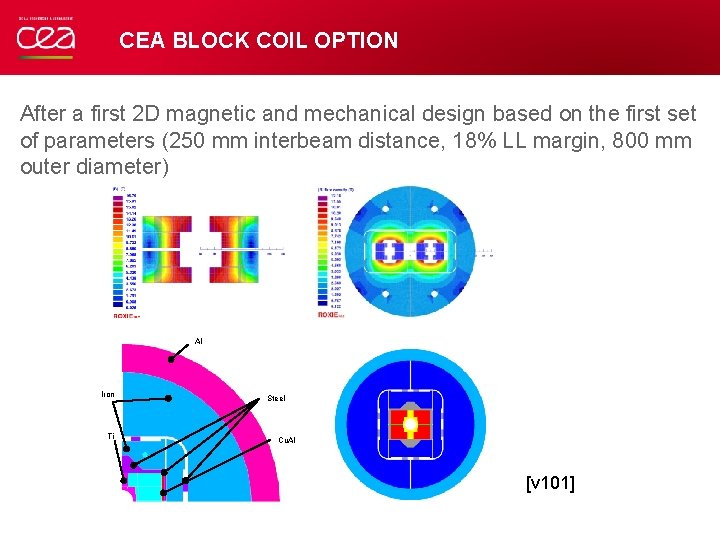
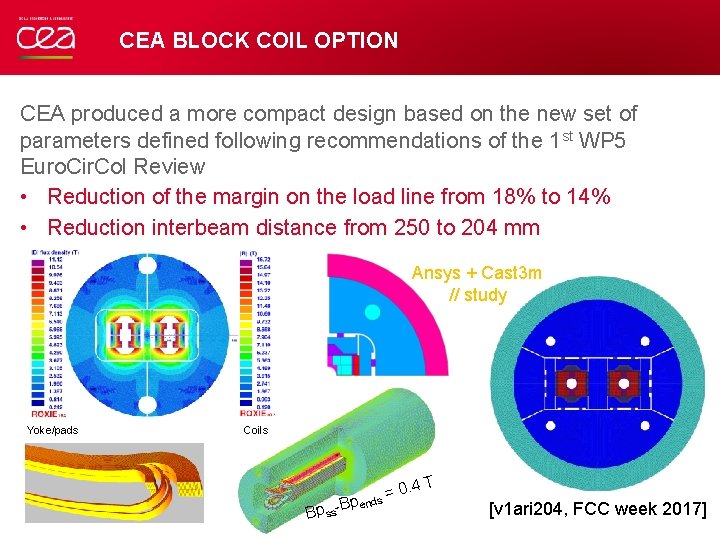
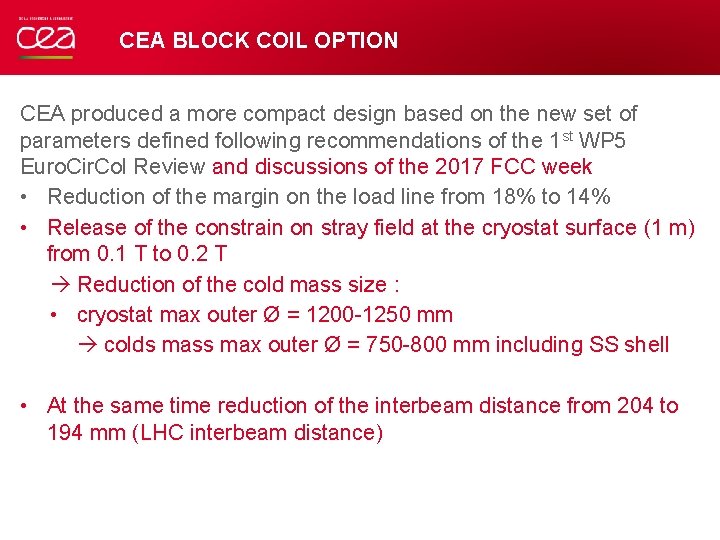
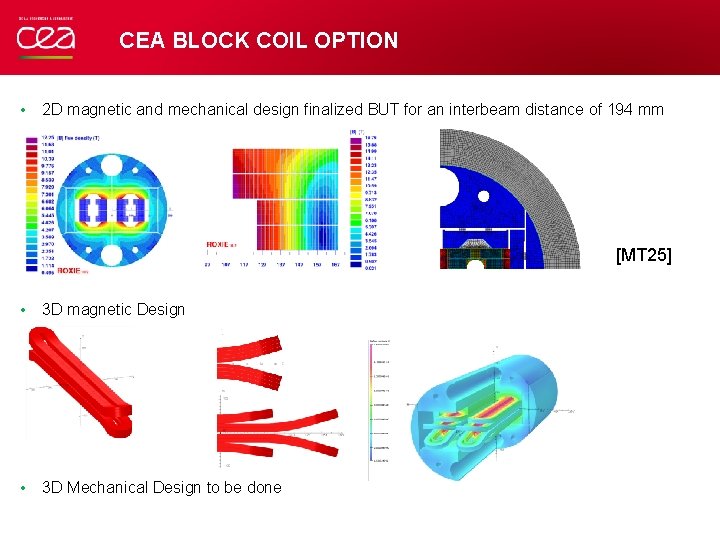
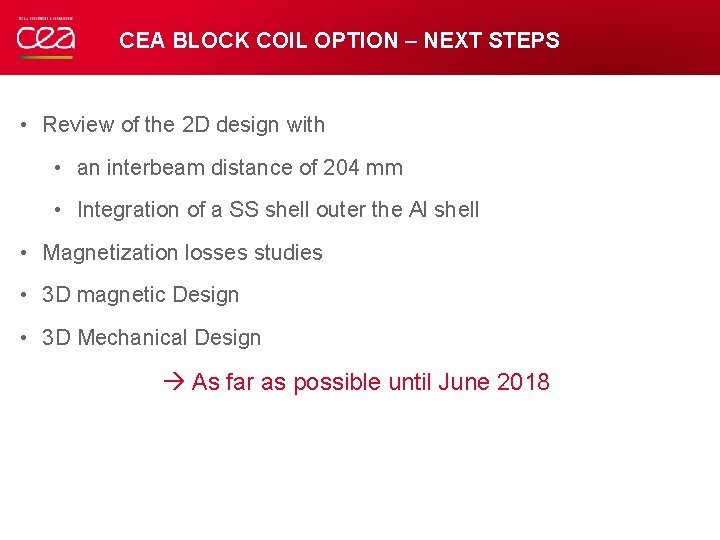
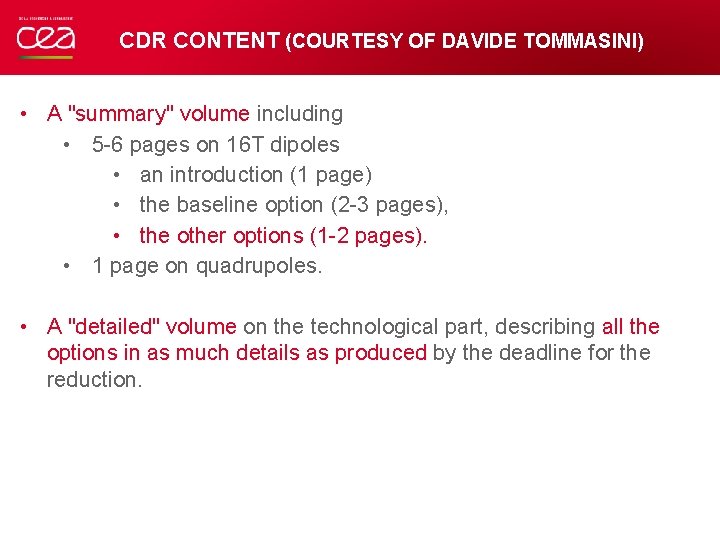

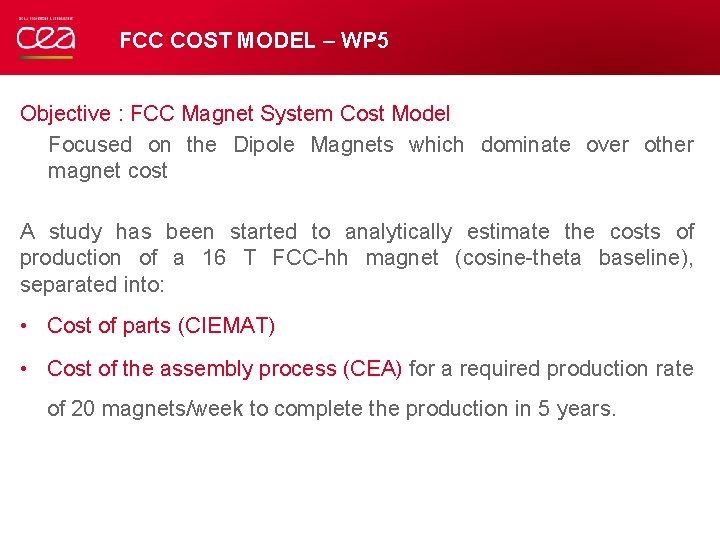
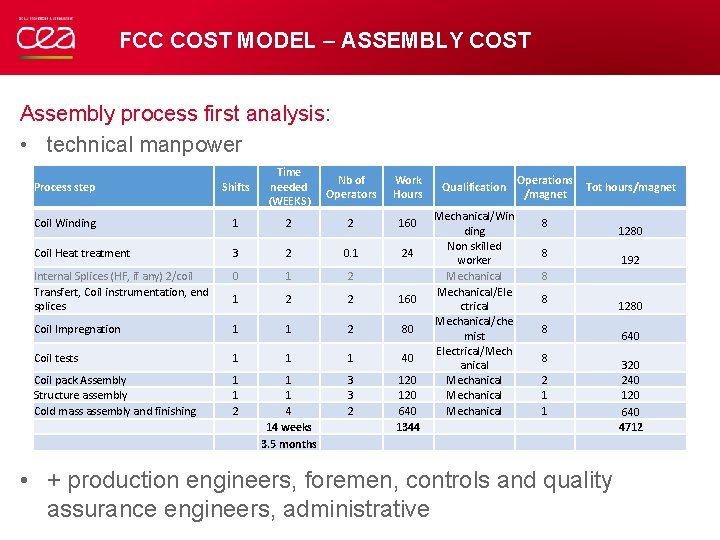
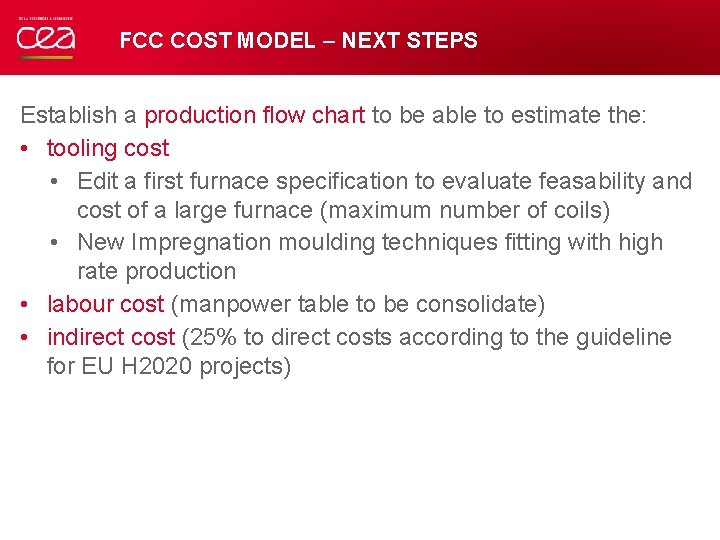
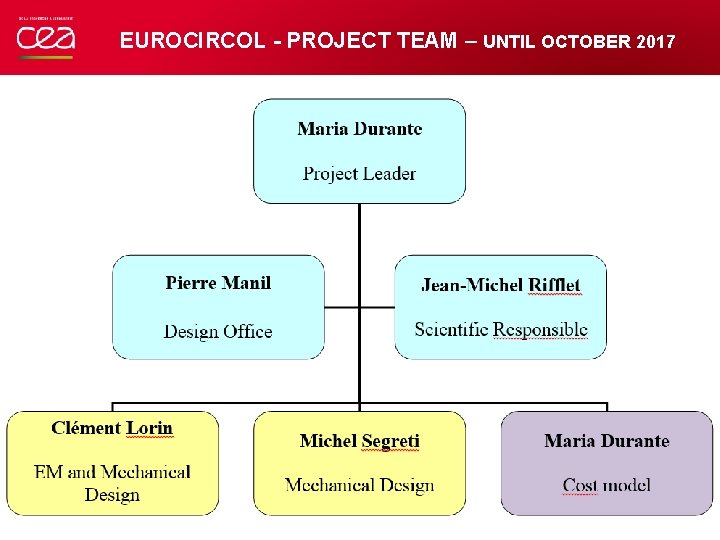
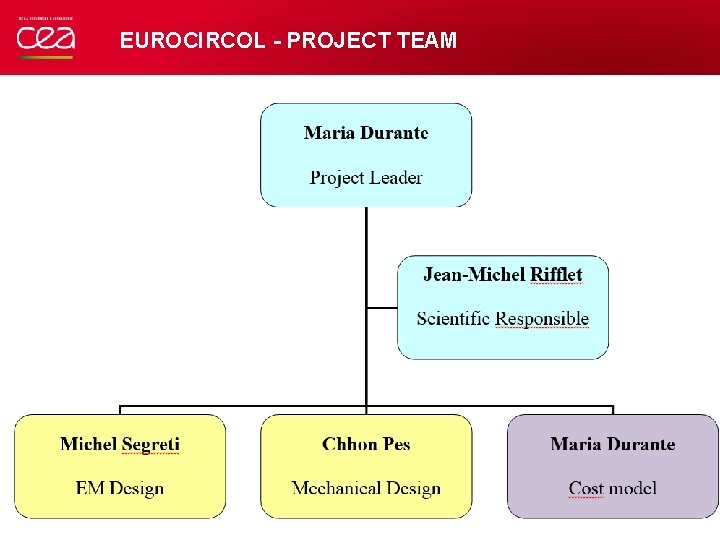
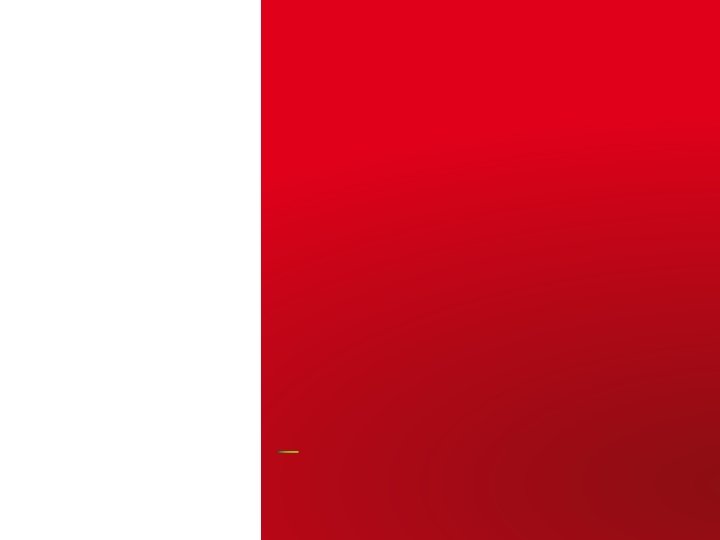
- Slides: 17
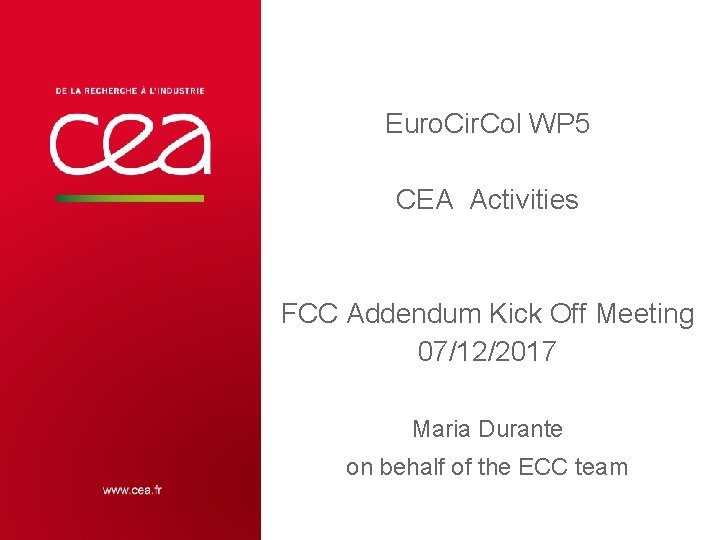
Euro. Cir. Col WP 5 CEA Activities FCC Addendum Kick Off Meeting 07/12/2017 Maria Durante on behalf of the ECC team
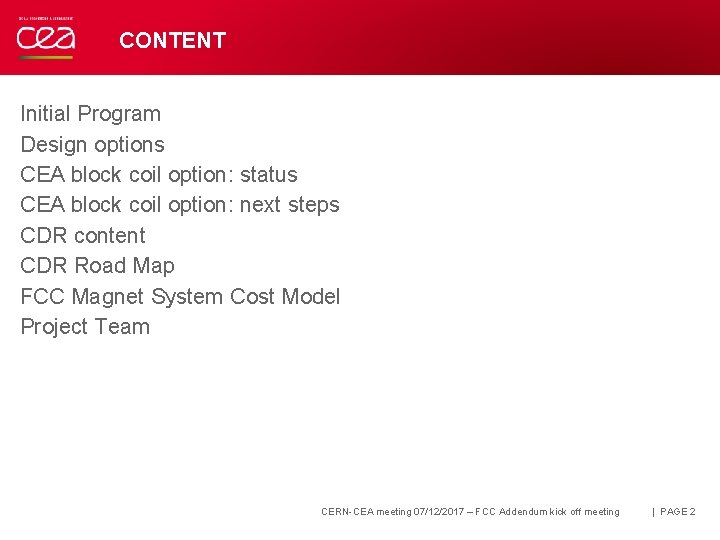
CONTENT Initial Program Design options CEA block coil option: status CEA block coil option: next steps CDR content CDR Road Map FCC Magnet System Cost Model Project Team CERN-CEA meeting 07/12/2017 – FCC Addendum kick off meeting | PAGE 2
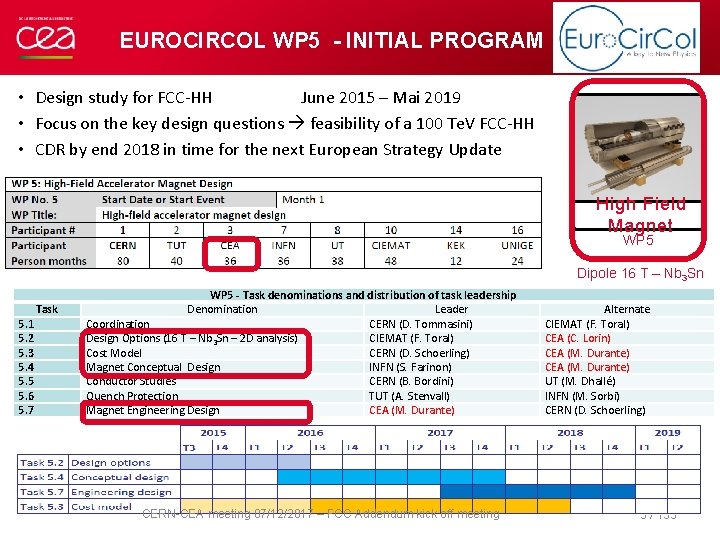
EUROCIRCOL WP 5 - INITIAL PROGRAM • Design study for FCC-HH June 2015 – Mai 2019 • Focus on the key design questions feasibility of a 100 Te. V FCC-HH • CDR by end 2018 in time for the next European Strategy Update High Field Magnet WP 5 Dipole 16 T – Nb 3 Sn 5. 1 5. 2 5. 3 5. 4 5. 5 5. 6 5. 7 Task WP 5 - Task denominations and distribution of task leadership Denomination Leader Coordination CERN (D. Tommasini) Design Options (16 T – Nb 3 Sn – 2 D analysis) CIEMAT (F. Toral) Cost Model CERN (D. Schoerling) Magnet Conceptual Design INFN (S. Farinon) Conductor Studies CERN (B. Bordini) Quench Protection TUT (A. Stenvall) Magnet Engineering Design CEA (M. Durante) CERN-CEA meeting 07/12/2017 – FCC Addendum kick off meeting Alternate CIEMAT (F. Toral) CEA (C. Lorin) CEA (M. Durante) UT (M. Dhallé) INFN (M. Sorbi) CERN (D. Schoerling) 3 / 153
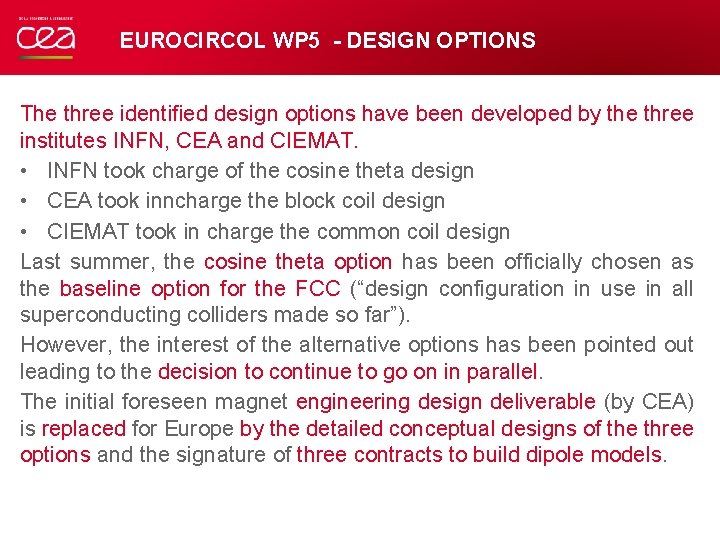
EUROCIRCOL WP 5 - DESIGN OPTIONS The three identified design options have been developed by the three institutes INFN, CEA and CIEMAT. • INFN took charge of the cosine theta design • CEA took inncharge the block coil design • CIEMAT took in charge the common coil design Last summer, the cosine theta option has been officially chosen as the baseline option for the FCC (“design configuration in use in all superconducting colliders made so far”). However, the interest of the alternative options has been pointed out leading to the decision to continue to go on in parallel. The initial foreseen magnet engineering design deliverable (by CEA) is replaced for Europe by the detailed conceptual designs of the three options and the signature of three contracts to build dipole models.
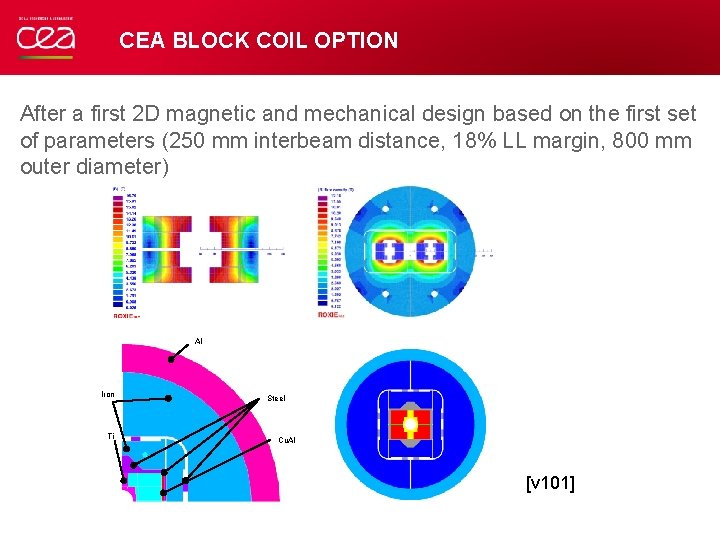
CEA BLOCK COIL OPTION After a first 2 D magnetic and mechanical design based on the first set of parameters (250 mm interbeam distance, 18% LL margin, 800 mm outer diameter) Al Iron Ti Steel Cu. Al [v 101]
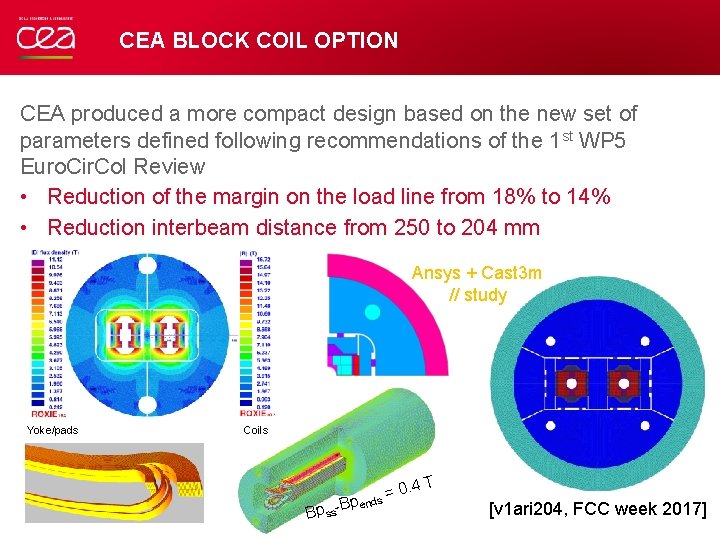
CEA BLOCK COIL OPTION CEA produced a more compact design based on the new set of parameters defined following recommendations of the 1 st WP 5 Euro. Cir. Col Review • Reduction of the margin on the load line from 18% to 14% • Reduction interbeam distance from 250 to 204 mm Ansys + Cast 3 m // study Yoke/pads Coils 0. 4 T = ds Bp en Bp ss- [v 1 ari 204, FCC week 2017]
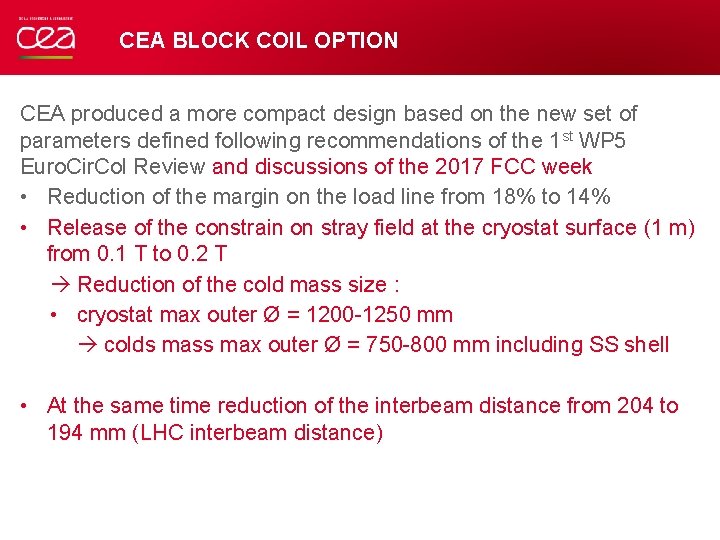
CEA BLOCK COIL OPTION CEA produced a more compact design based on the new set of parameters defined following recommendations of the 1 st WP 5 Euro. Cir. Col Review and discussions of the 2017 FCC week • Reduction of the margin on the load line from 18% to 14% • Release of the constrain on stray field at the cryostat surface (1 m) from 0. 1 T to 0. 2 T Reduction of the cold mass size : • cryostat max outer Ø = 1200 -1250 mm colds mass max outer Ø = 750 -800 mm including SS shell • At the same time reduction of the interbeam distance from 204 to 194 mm (LHC interbeam distance)
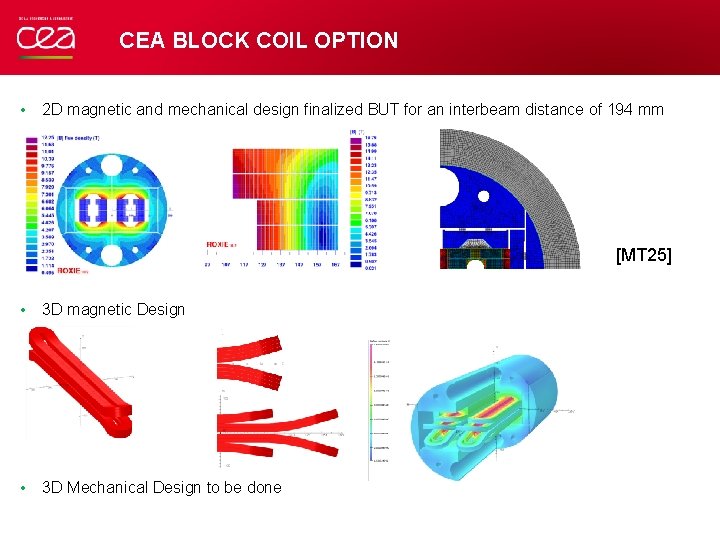
CEA BLOCK COIL OPTION • 2 D magnetic and mechanical design finalized BUT for an interbeam distance of 194 mm [MT 25] • 3 D magnetic Design • 3 D Mechanical Design to be done
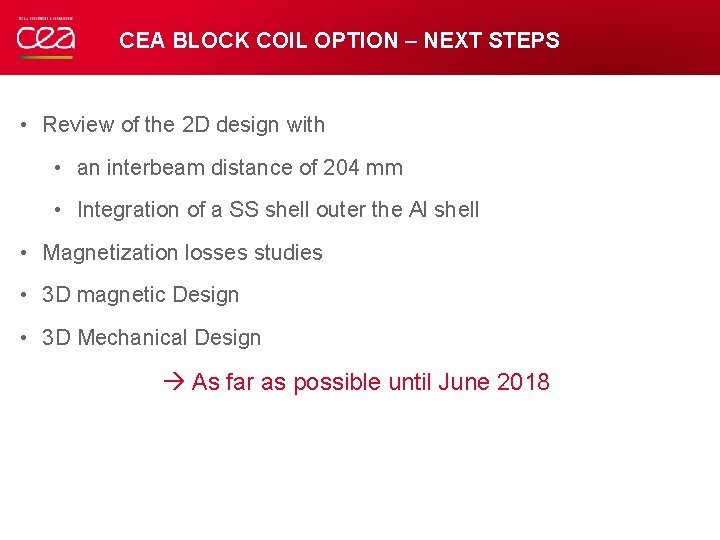
CEA BLOCK COIL OPTION – NEXT STEPS • Review of the 2 D design with • an interbeam distance of 204 mm • Integration of a SS shell outer the Al shell • Magnetization losses studies • 3 D magnetic Design • 3 D Mechanical Design As far as possible until June 2018
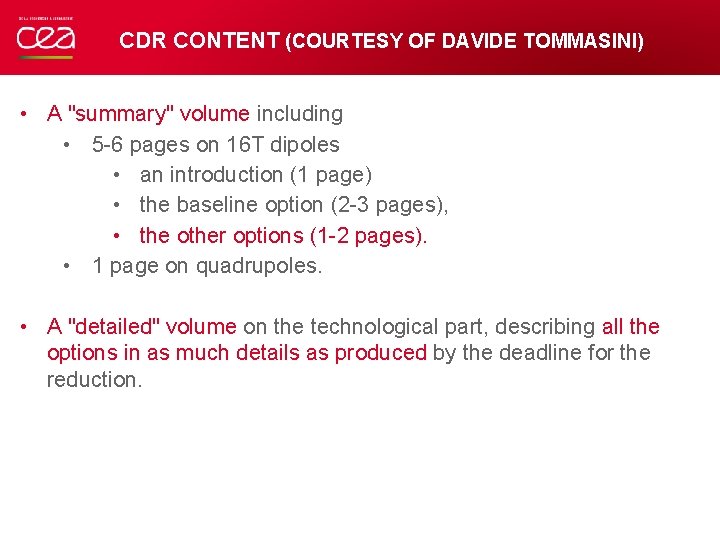
CDR CONTENT (COURTESY OF DAVIDE TOMMASINI) • A "summary" volume including • 5 -6 pages on 16 T dipoles • an introduction (1 page) • the baseline option (2 -3 pages), • the other options (1 -2 pages). • 1 page on quadrupoles. • A "detailed" volume on the technological part, describing all the options in as much details as produced by the deadline for the reduction.

CDR ROAD MAP (COURTESY OF DAVIDE TOMMASINI) • Dec 2017: First draft of summary FCC CDR book chapter on 16 T. • 2 D designs of all design options • April 2018: FCC Week • • 2 D EM and mech design finalized (with SS shell, 204 interbeam) conceptual 3 D EM study (EM model + artistical picture) integration in the cryostat (by CERN) Status of the 3 D Mechanical study report for Task 5. 3 Cost model report for Task 5. 5 Conductor studies report for Task 5. 6 Quench protection • • • June 2018: first draft of detailed FCC CDR book chapter on 16 T dipole • Dec 2018: compilation of FCC CDR • April 2019: final report for EU
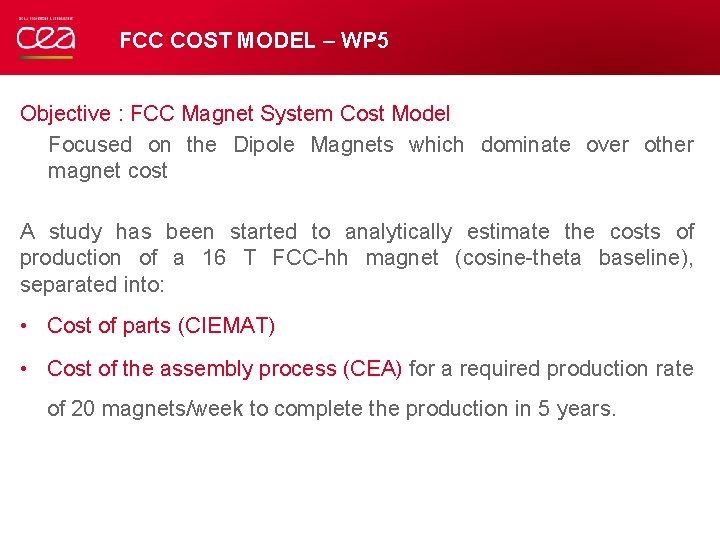
FCC COST MODEL – WP 5 Objective : FCC Magnet System Cost Model Focused on the Dipole Magnets which dominate over other magnet cost A study has been started to analytically estimate the costs of production of a 16 T FCC-hh magnet (cosine-theta baseline), separated into: • Cost of parts (CIEMAT) • Cost of the assembly process (CEA) for a required production rate of 20 magnets/week to complete the production in 5 years.
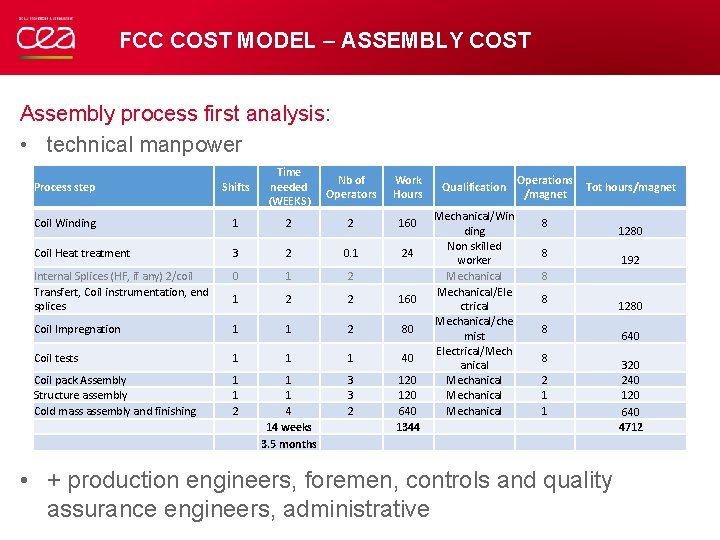
FCC COST MODEL – ASSEMBLY COST Assembly process first analysis: • technical manpower Process step Shifts Time needed (WEEKS) Nb of Operators Work Hours Coil Winding 1 2 2 160 Coil Heat treatment 3 2 0. 1 24 Internal Splices (HF, if any) 2/coil Transfert, Coil instrumentation, end splices 0 1 2 2 160 Coil Impregnation 1 1 2 80 Coil tests 1 1 1 40 Coil pack Assembly Structure assembly Cold mass assembly and finishing 1 1 2 1 1 4 14 weeks 3. 5 months 3 3 2 120 640 1344 Qualification Mechanical/Win ding Non skilled worker Mechanical/Ele ctrical Mechanical/che mist Electrical/Mech anical Mechanical Operations /magnet Tot hours/magnet 8 8 8 2 1 1 • + production engineers, foremen, controls and quality assurance engineers, administrative 1280 192 1280 640 320 240 120 640 4712
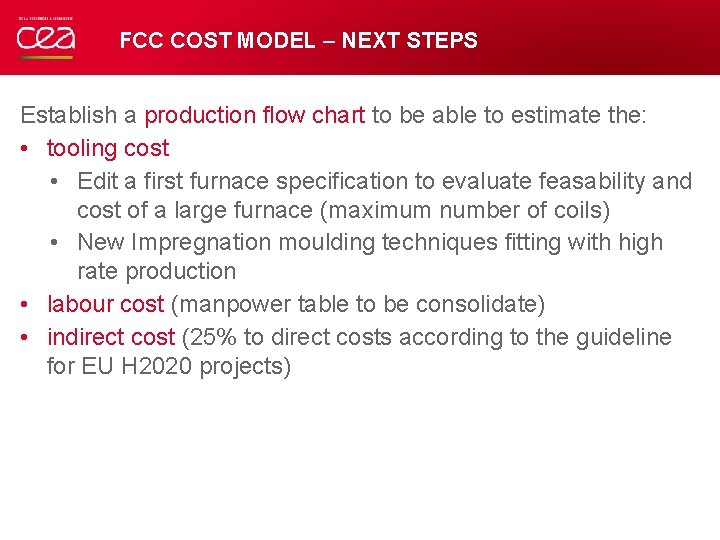
FCC COST MODEL – NEXT STEPS Establish a production flow chart to be able to estimate the: • tooling cost • Edit a first furnace specification to evaluate feasability and cost of a large furnace (maximum number of coils) • New Impregnation moulding techniques fitting with high rate production • labour cost (manpower table to be consolidate) • indirect cost (25% to direct costs according to the guideline for EU H 2020 projects)
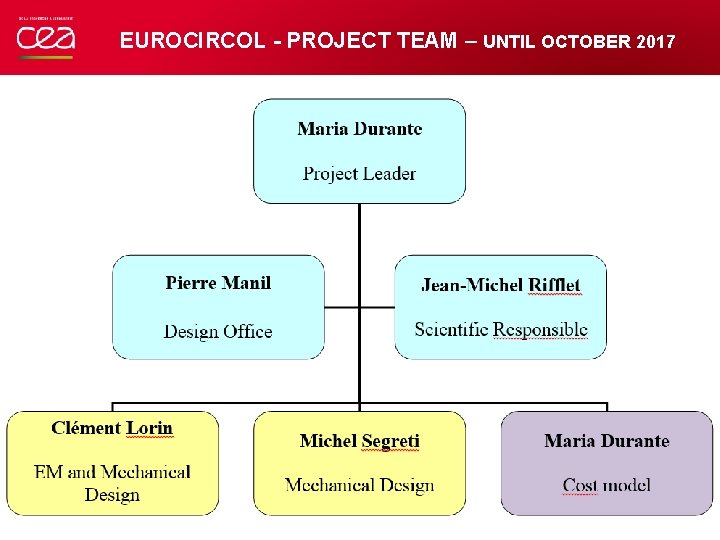
EUROCIRCOL - PROJECT TEAM – UNTIL OCTOBER 2017
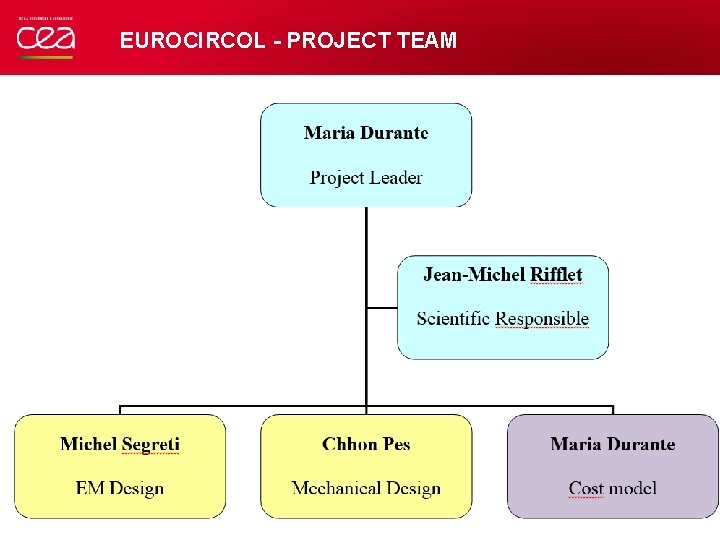
EUROCIRCOL - PROJECT TEAM
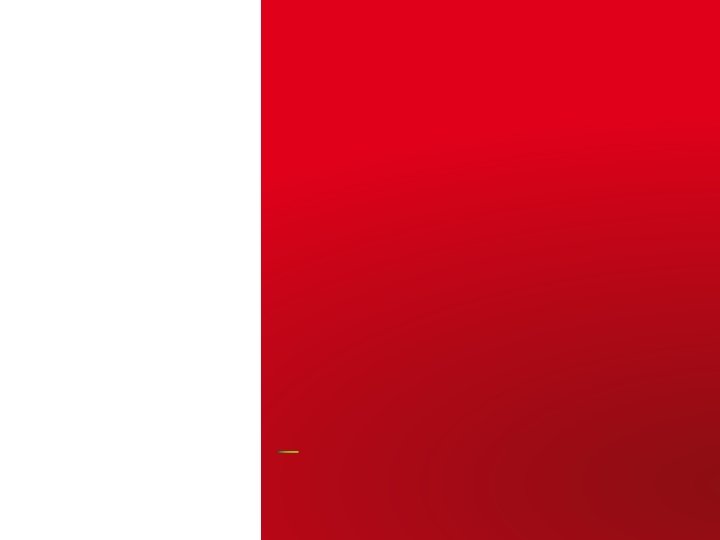
| PAGE 17 CERN-CEA meeting 07/12/2017 – FCC Addendum kick off meeting
Mnuo
Caracol col col sal de tu casita
Cir immunization registry
Cir registry
Computer organization
Cops monitoring 10024 vanderbilt cir. #4 rockville md 20850
The statement of cash flows helps users
Indoor sports and outdoor sports
Support activities and primary activities
Primary activities and tertiary activities
Care sunt formele comunicarii
Cea vega media
Cea nedir
Sceneta de 8 martie inima mamei
Vpn ssl cea
Fotografie 1826
Cua vs cea
Ag carcino embrionale cea