Engineer Training XL 1200 Motion Control System Motion
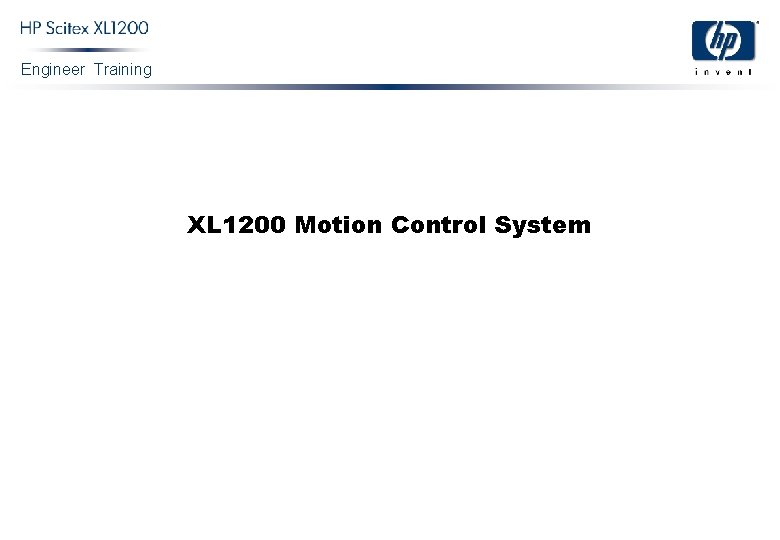
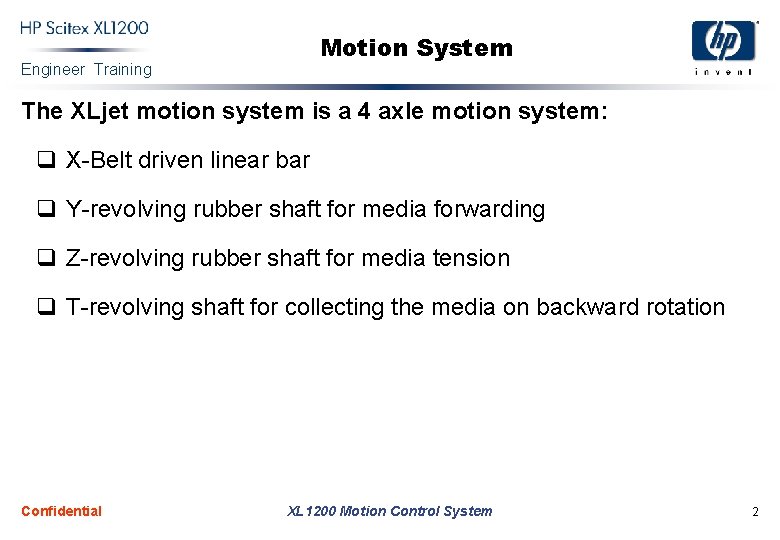
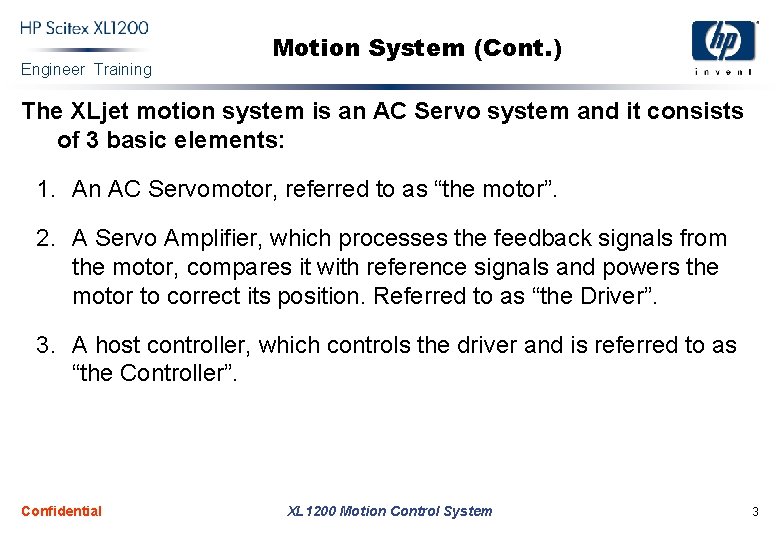
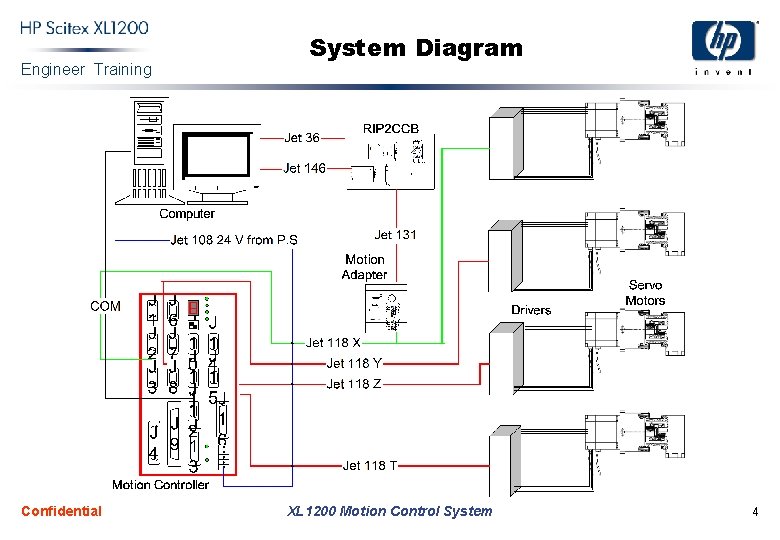
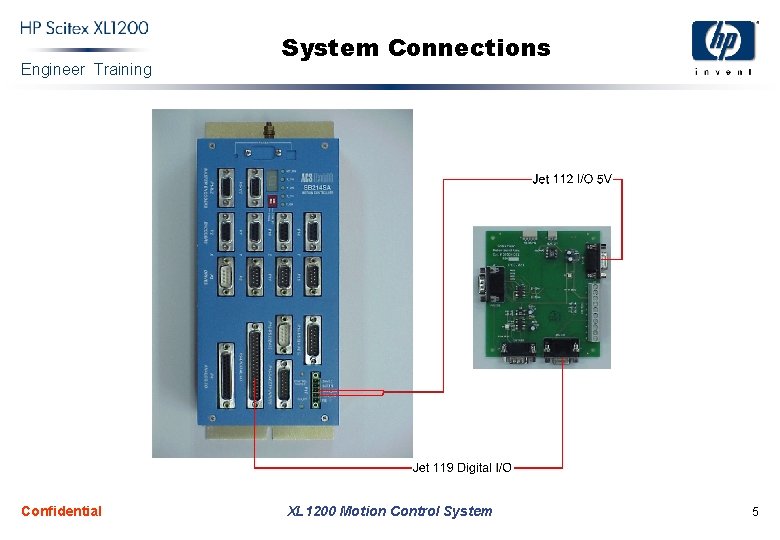
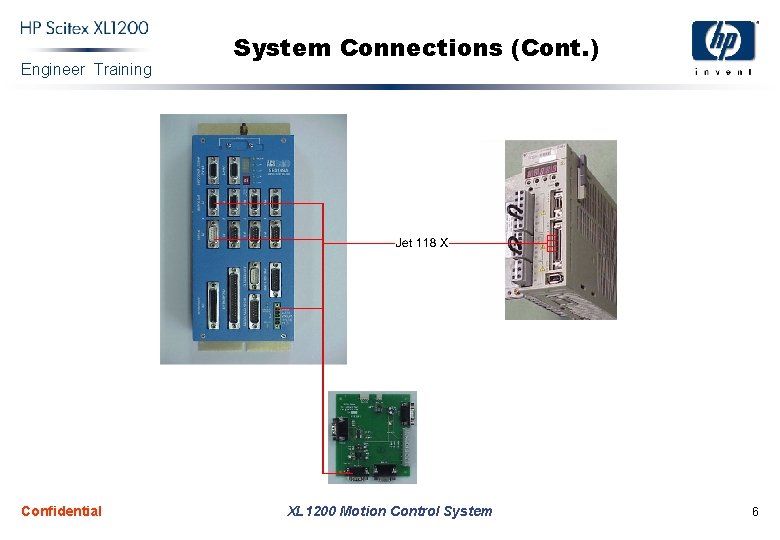
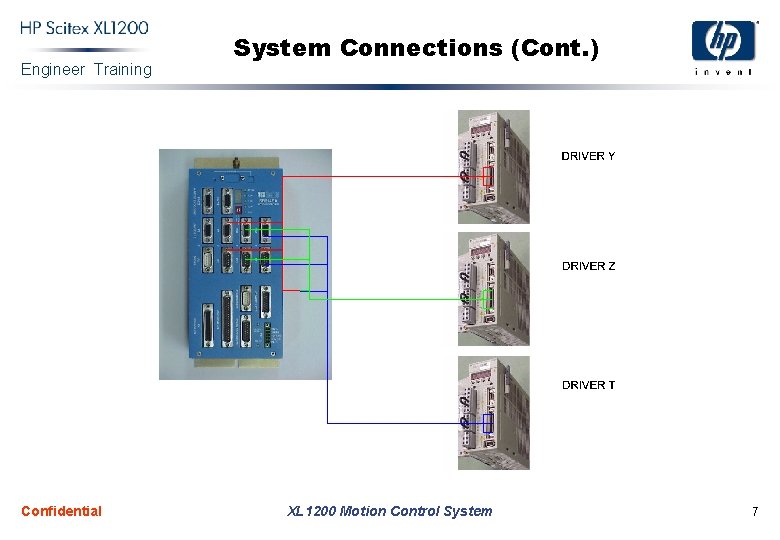
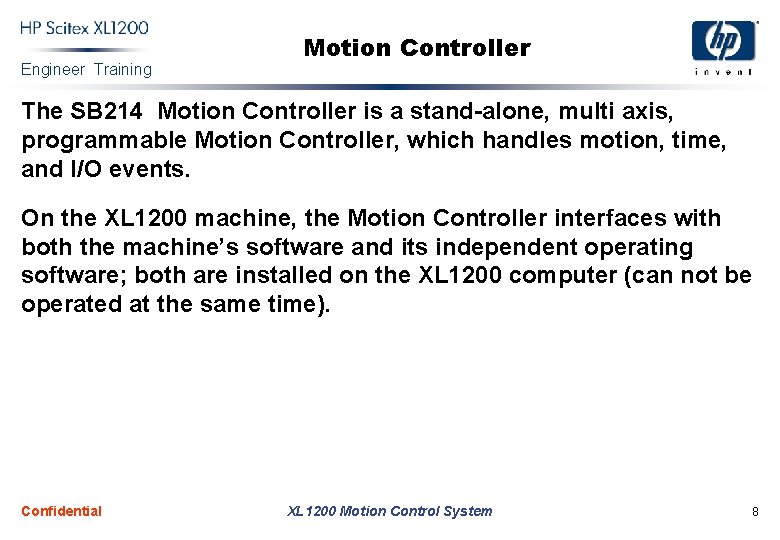
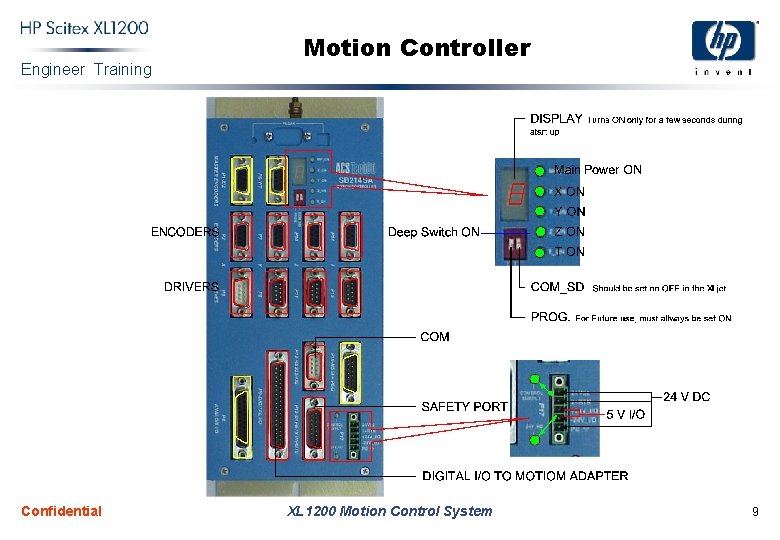
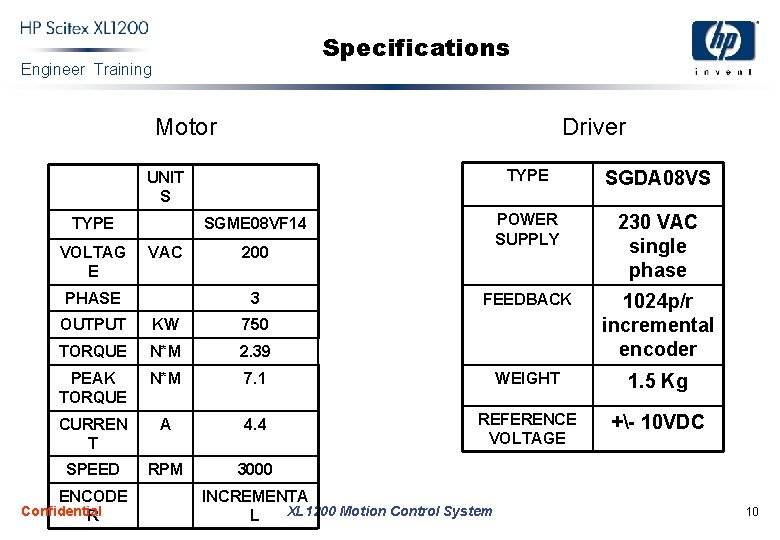
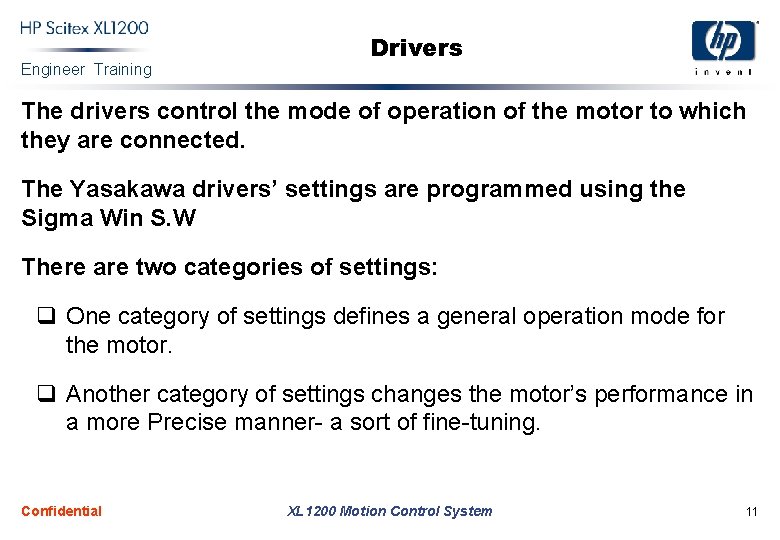
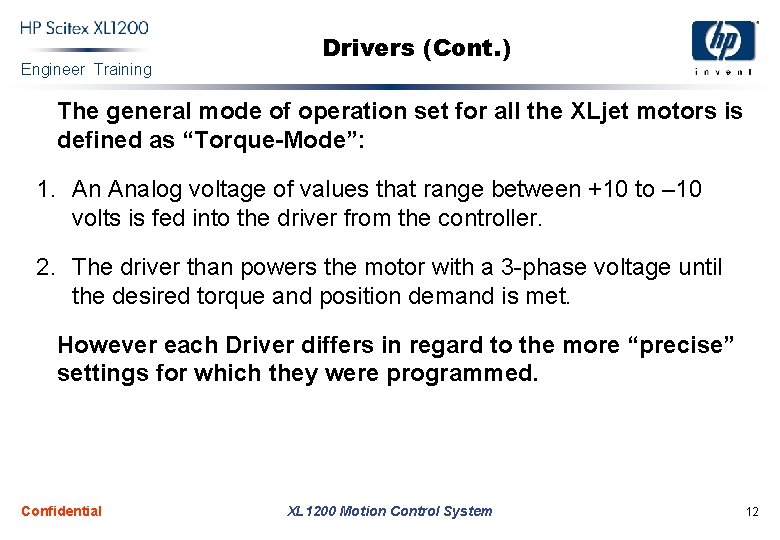
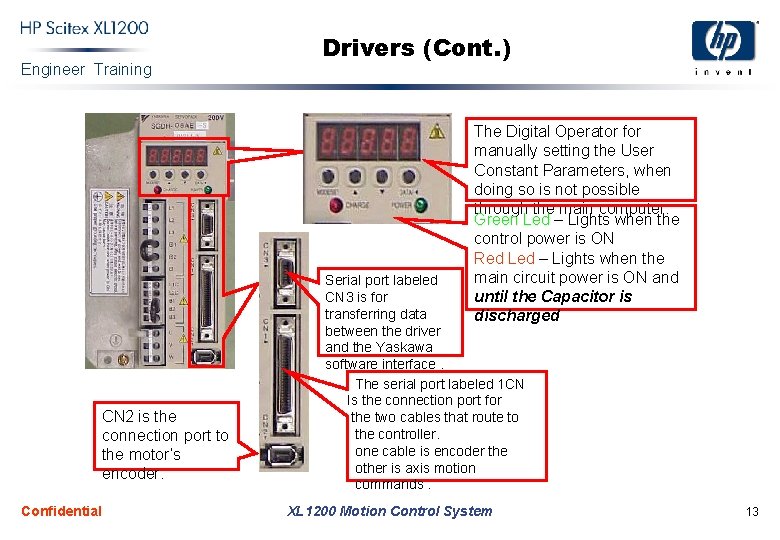
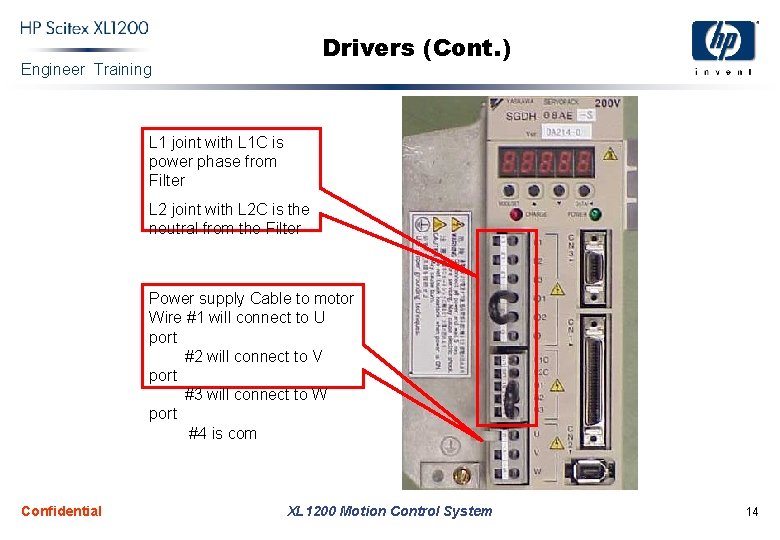
- Slides: 14
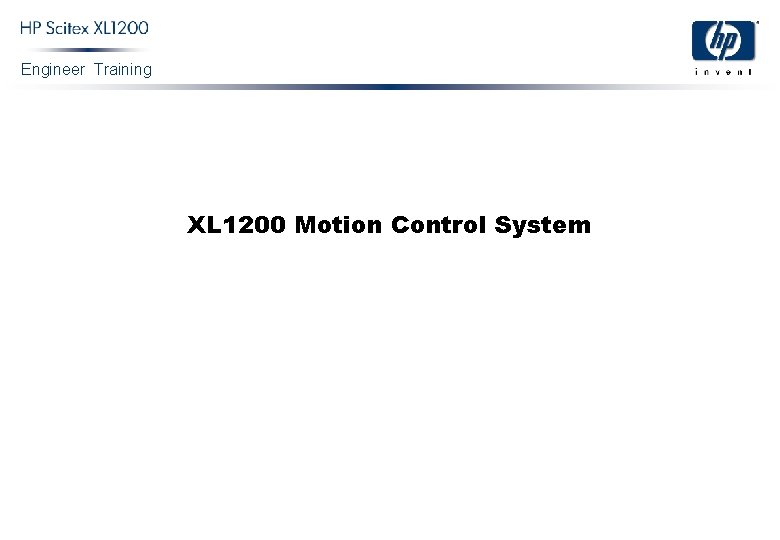
Engineer Training XL 1200 Motion Control System
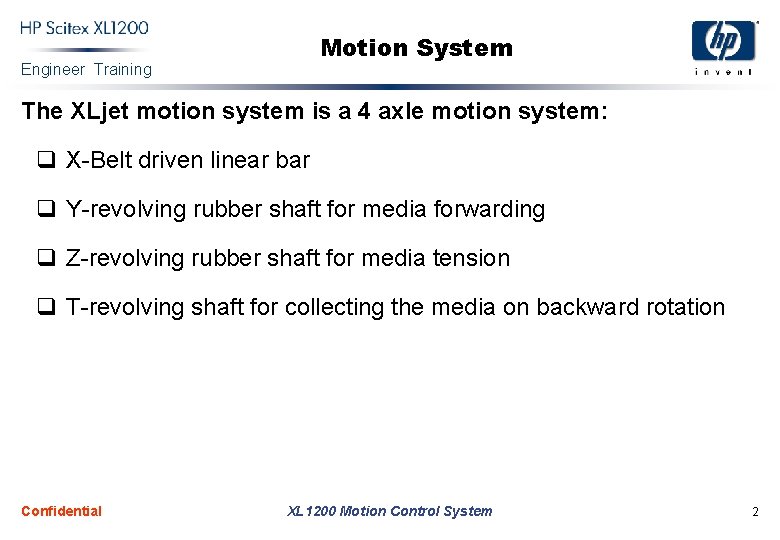
Motion System Engineer Training The XLjet motion system is a 4 axle motion system: q X-Belt driven linear bar q Y-revolving rubber shaft for media forwarding q Z-revolving rubber shaft for media tension q T-revolving shaft for collecting the media on backward rotation Confidential XL 1200 Motion Control System 2
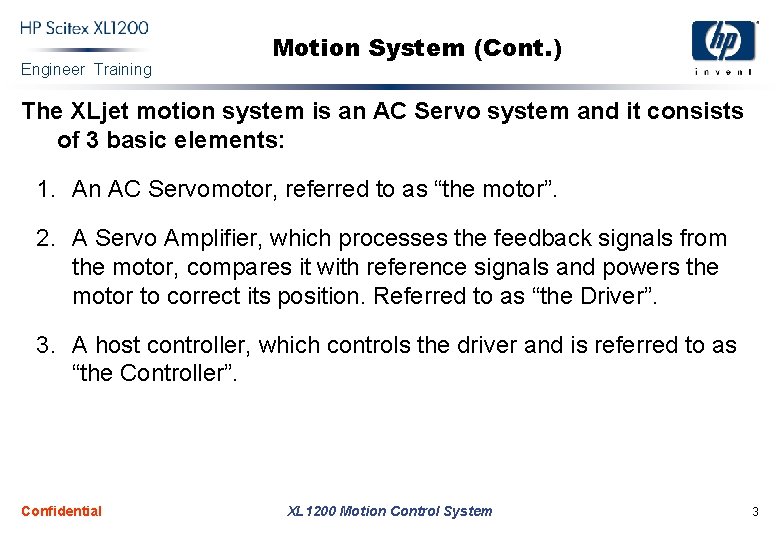
Engineer Training Motion System (Cont. ) The XLjet motion system is an AC Servo system and it consists of 3 basic elements: 1. An AC Servomotor, referred to as “the motor”. 2. A Servo Amplifier, which processes the feedback signals from the motor, compares it with reference signals and powers the motor to correct its position. Referred to as “the Driver”. 3. A host controller, which controls the driver and is referred to as “the Controller”. Confidential XL 1200 Motion Control System 3
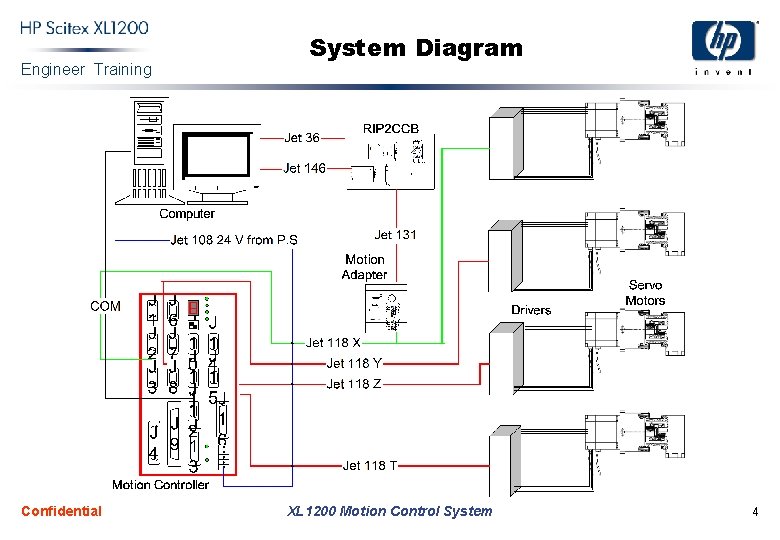
Engineer Training Confidential System Diagram XL 1200 Motion Control System 4
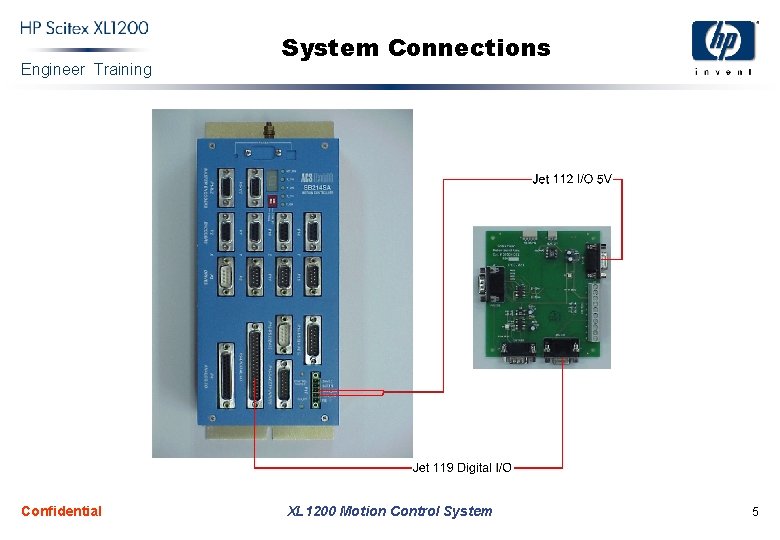
Engineer Training Confidential System Connections XL 1200 Motion Control System 5
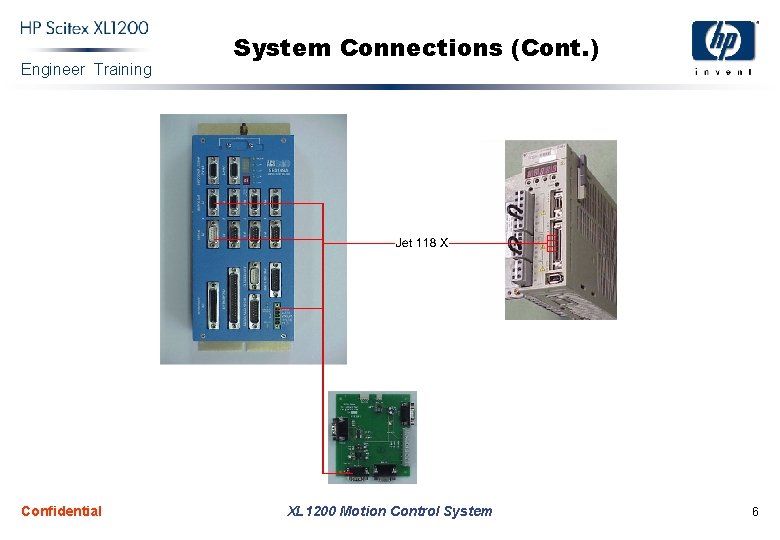
Engineer Training Confidential System Connections (Cont. ) XL 1200 Motion Control System 6
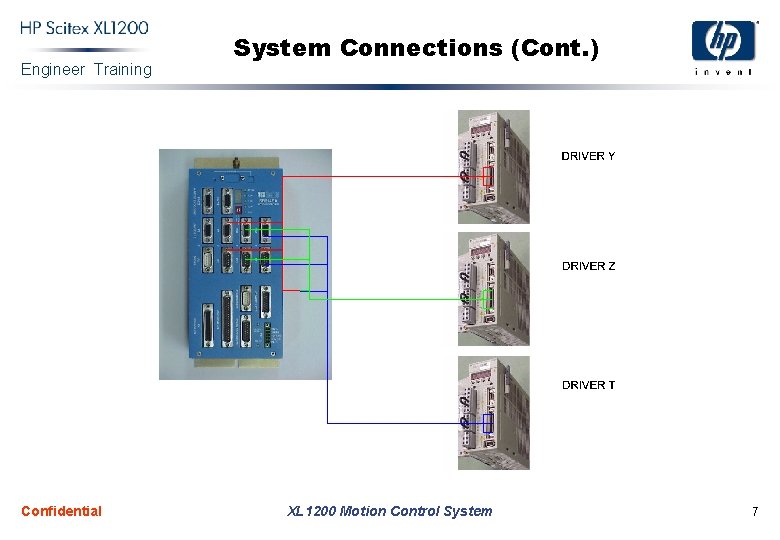
Engineer Training Confidential System Connections (Cont. ) XL 1200 Motion Control System 7
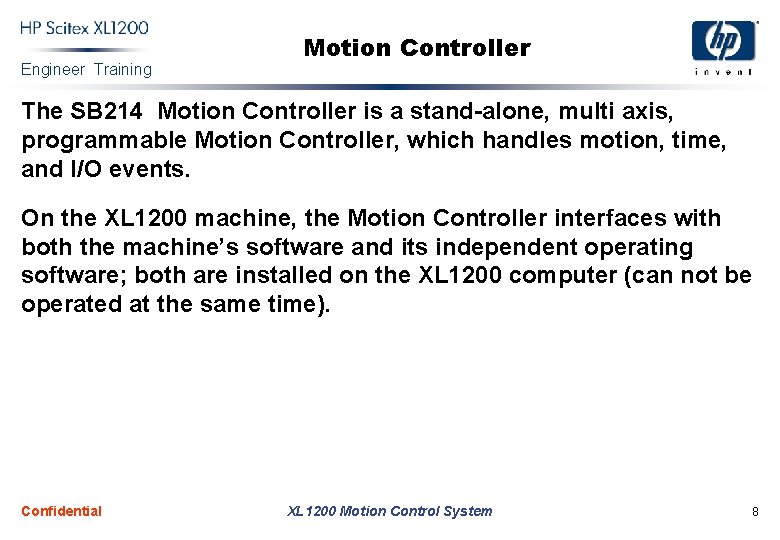
Engineer Training Motion Controller The SB 214 Motion Controller is a stand-alone, multi axis, programmable Motion Controller, which handles motion, time, and I/O events. On the XL 1200 machine, the Motion Controller interfaces with both the machine’s software and its independent operating software; both are installed on the XL 1200 computer (can not be operated at the same time). Confidential XL 1200 Motion Control System 8
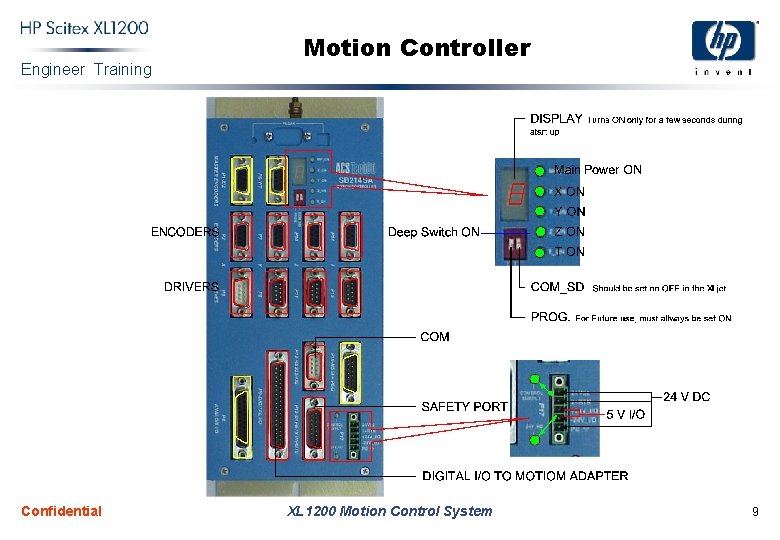
Engineer Training Confidential Motion Controller XL 1200 Motion Control System 9
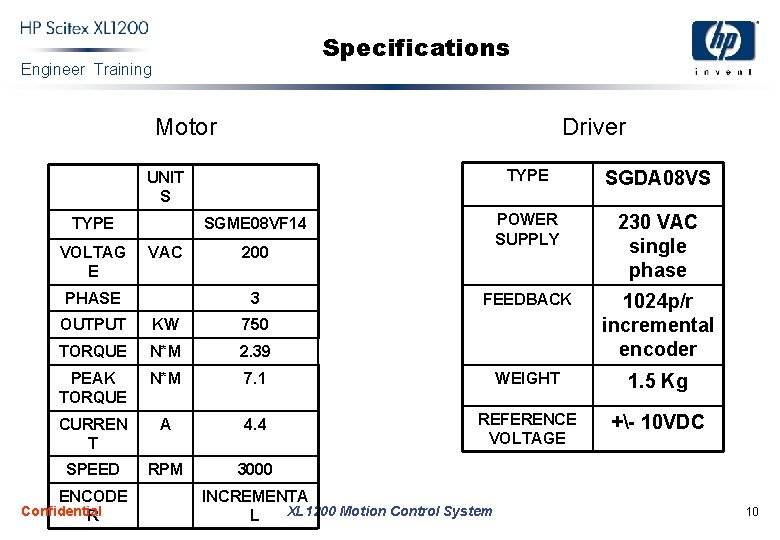
Specifications Engineer Training Motor Driver UNIT S TYPE SGDA 08 VS TYPE SGME 08 VF 14 VOLTAG E VAC 200 POWER SUPPLY 230 VAC single phase PHASE 3 FEEDBACK OUTPUT KW 750 TORQUE N*M 2. 39 1024 p/r incremental encoder PEAK TORQUE N*M 7. 1 WEIGHT 1. 5 Kg CURREN T A 4. 4 REFERENCE VOLTAGE +- 10 VDC SPEED RPM 3000 ENCODE Confidential R INCREMENTA XL 1200 Motion Control System L 10
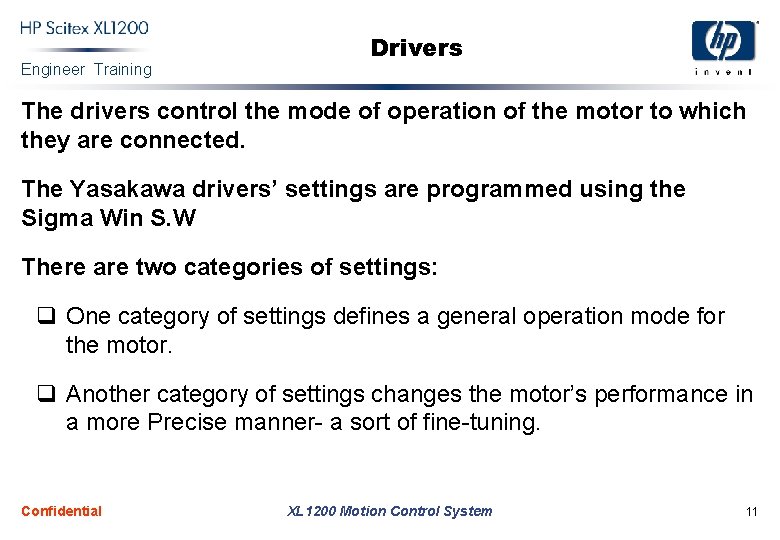
Engineer Training Drivers The drivers control the mode of operation of the motor to which they are connected. The Yasakawa drivers’ settings are programmed using the Sigma Win S. W There are two categories of settings: q One category of settings defines a general operation mode for the motor. q Another category of settings changes the motor’s performance in a more Precise manner- a sort of fine-tuning. Confidential XL 1200 Motion Control System 11
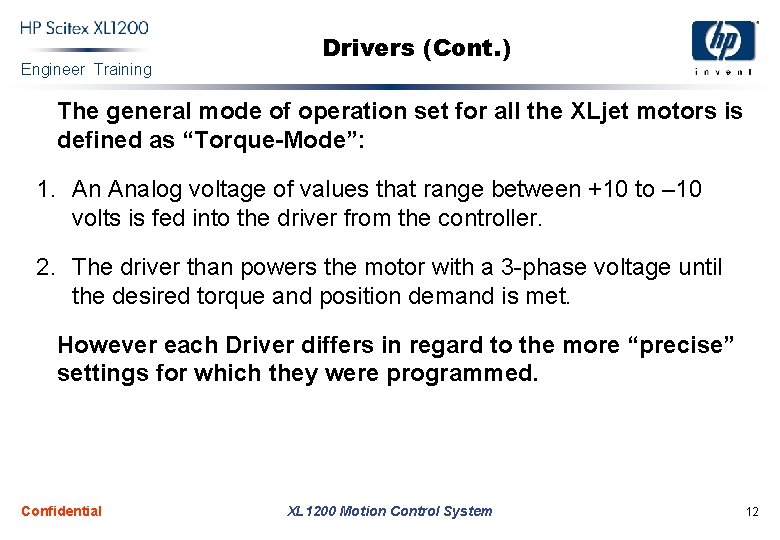
Engineer Training Drivers (Cont. ) The general mode of operation set for all the XLjet motors is defined as “Torque-Mode”: 1. An Analog voltage of values that range between +10 to – 10 volts is fed into the driver from the controller. 2. The driver than powers the motor with a 3 -phase voltage until the desired torque and position demand is met. However each Driver differs in regard to the more “precise” settings for which they were programmed. Confidential XL 1200 Motion Control System 12
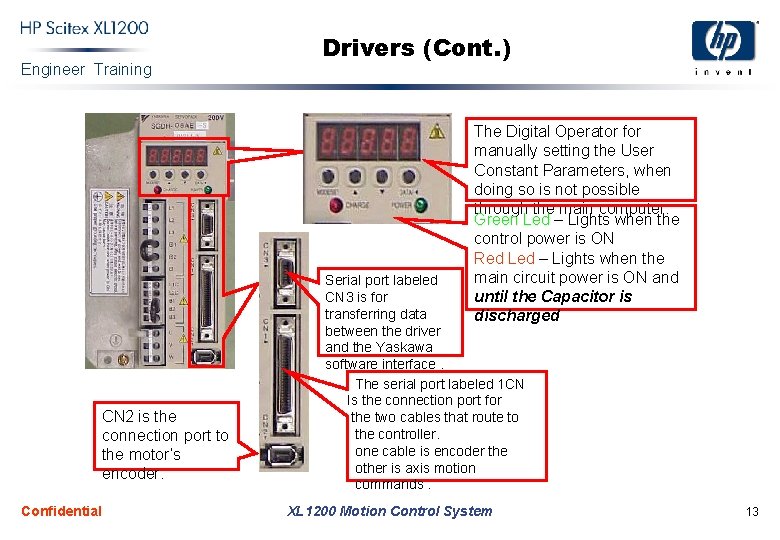
Engineer Training Drivers (Cont. ) The Digital Operator for manually setting the User Constant Parameters, when doing so is not possible through the main computer. Green Led – Lights when the control power is ON Red Led – Lights when the main circuit power is ON and until the Capacitor is discharged CN 2 is the connection port to the motor’s encoder. Confidential Serial port labeled CN 3 is for transferring data between the driver and the Yaskawa software interface. The serial port labeled 1 CN Is the connection port for the two cables that route to the controller. one cable is encoder the other is axis motion commands. XL 1200 Motion Control System 13
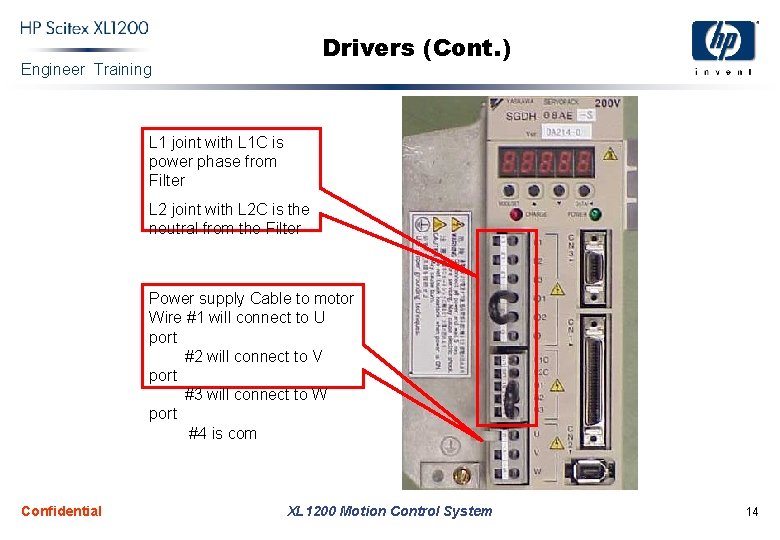
Drivers (Cont. ) Engineer Training L 1 joint with L 1 C is power phase from Filter L 2 joint with L 2 C is the neutral from the Filter Power supply Cable to motor Wire #1 will connect to U port #2 will connect to V port #3 will connect to W port #4 is com Confidential XL 1200 Motion Control System 14
A traffic control engineer reports that 75
System install engineer asml
System engineer chap 1
Mycin advantages and disadvantages
System engineer chapter 36
The three age system
Dardel ion exchange
Yucatan peninsula on north america map
Military time conversion
Anatolia map 1200
1200 alloy
Interface wien 1200
29cfr1910.1200
29 cfr 1910 section 1200
29 cfr 1200