DYNAPAC F 1000 TW Paver Controller System Propel
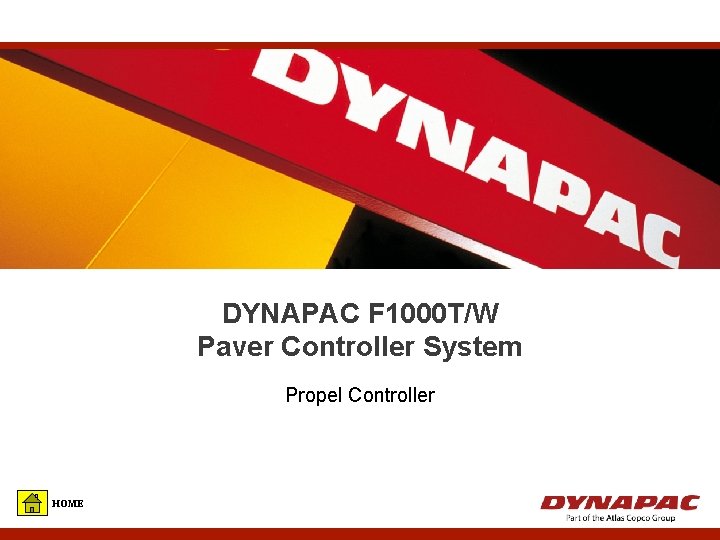
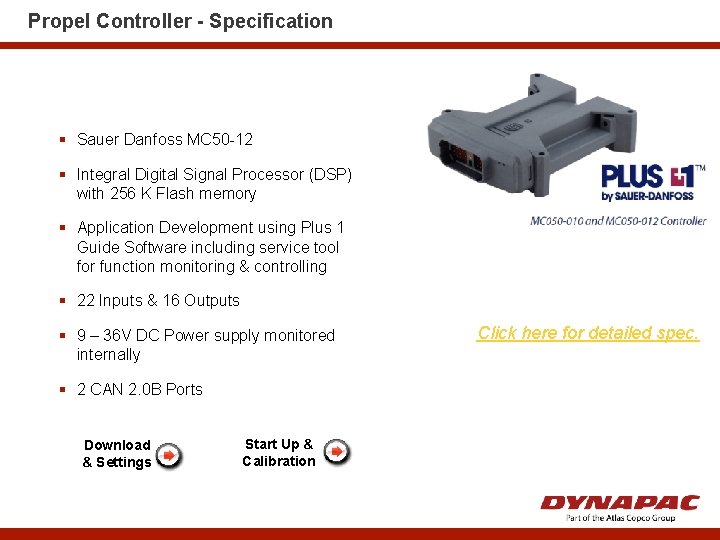
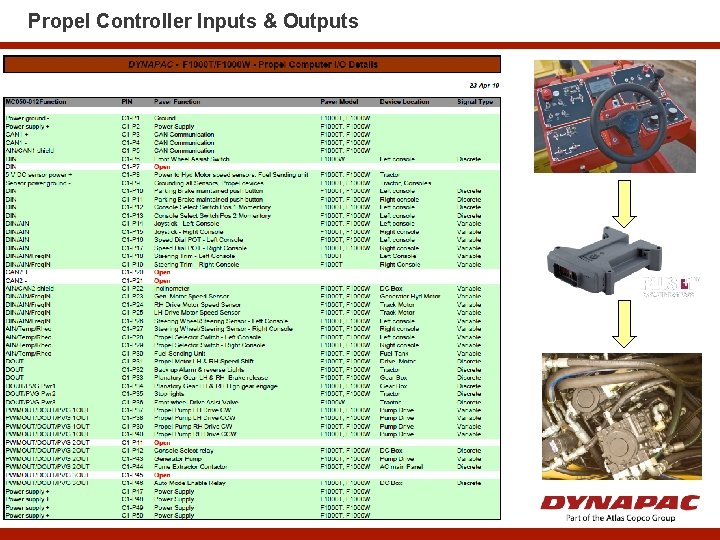
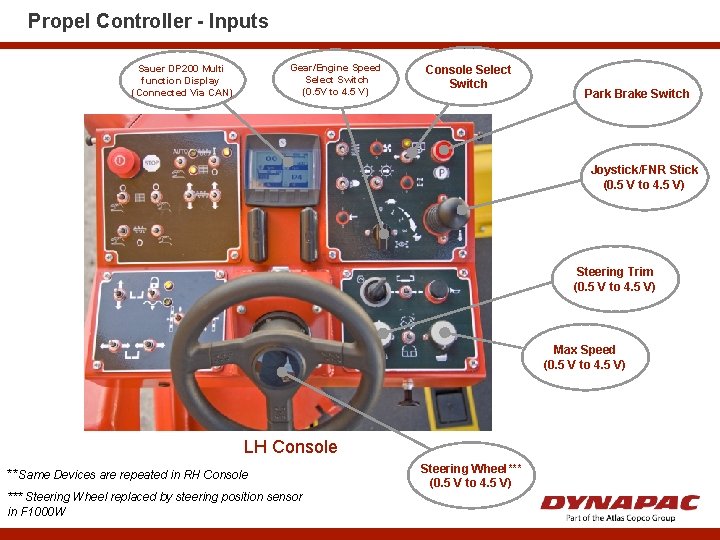
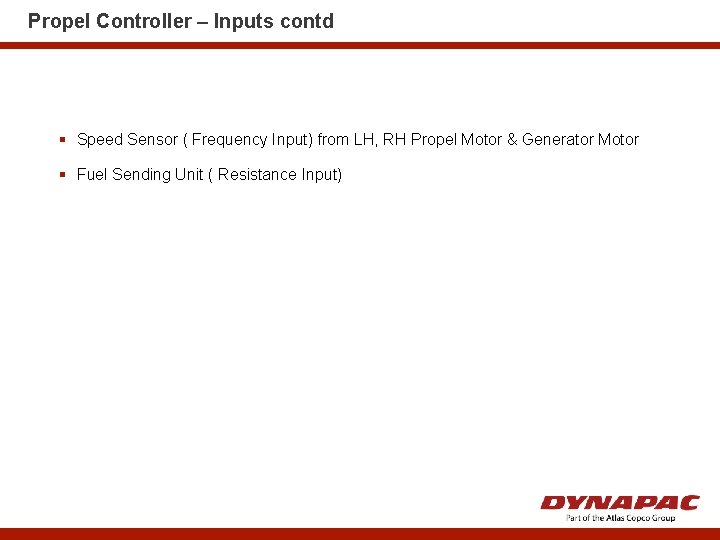
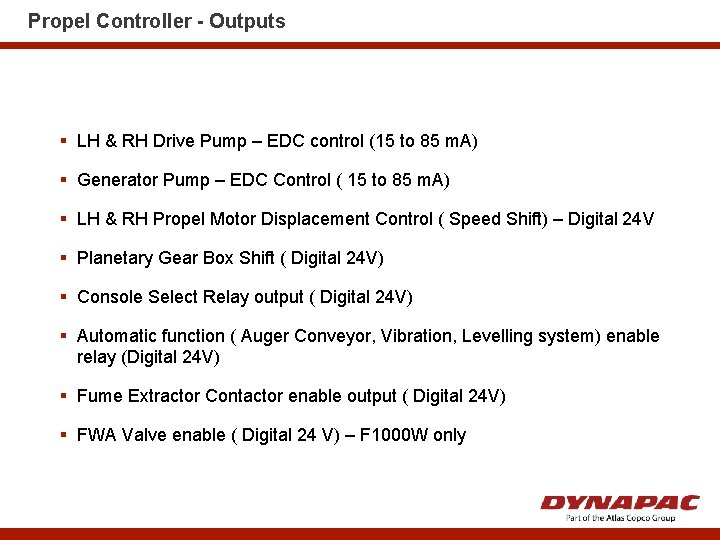
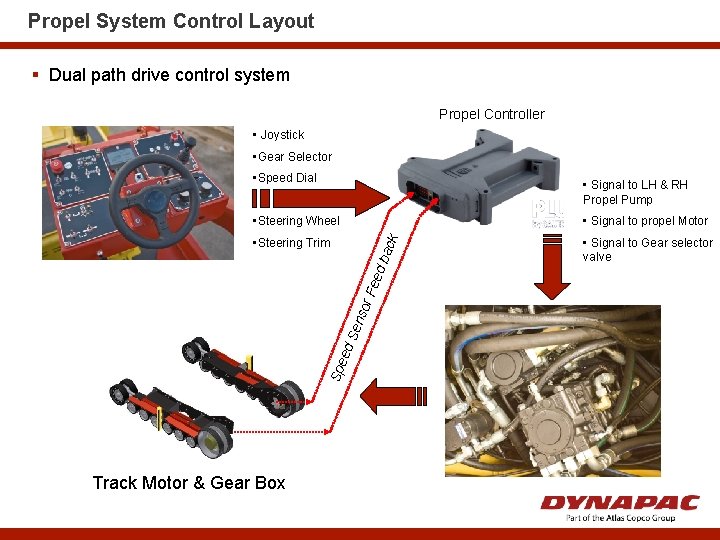
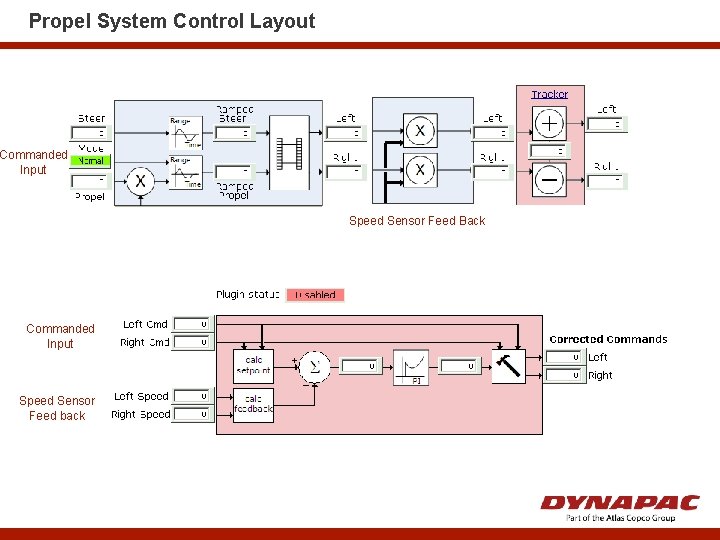
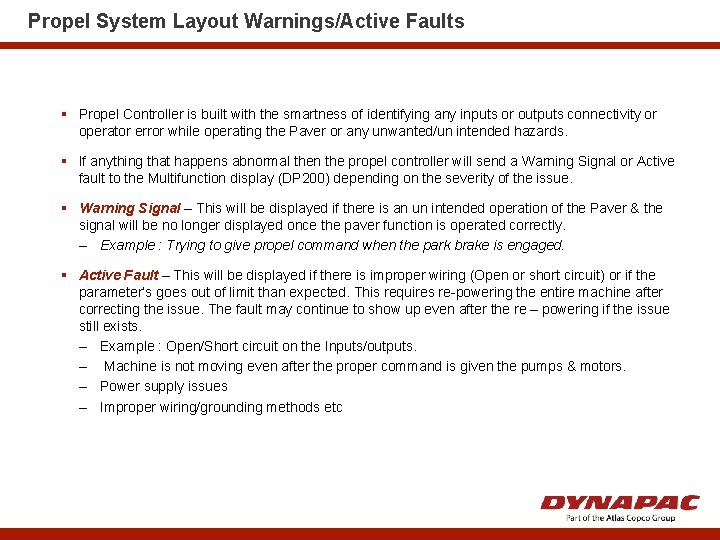
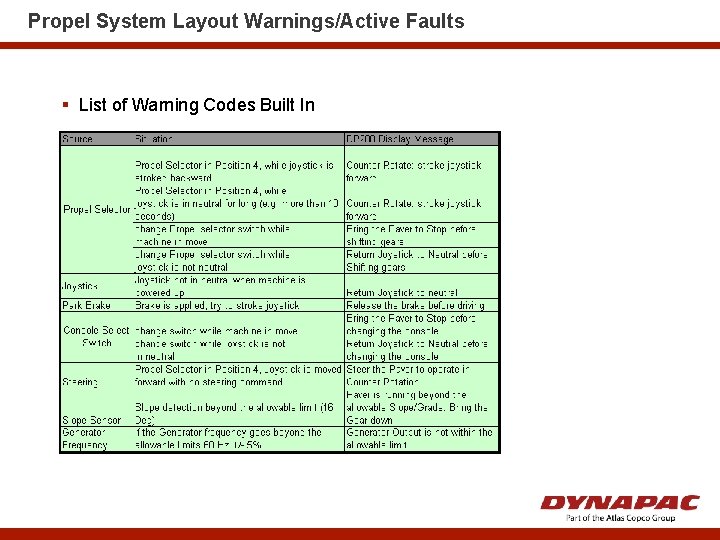
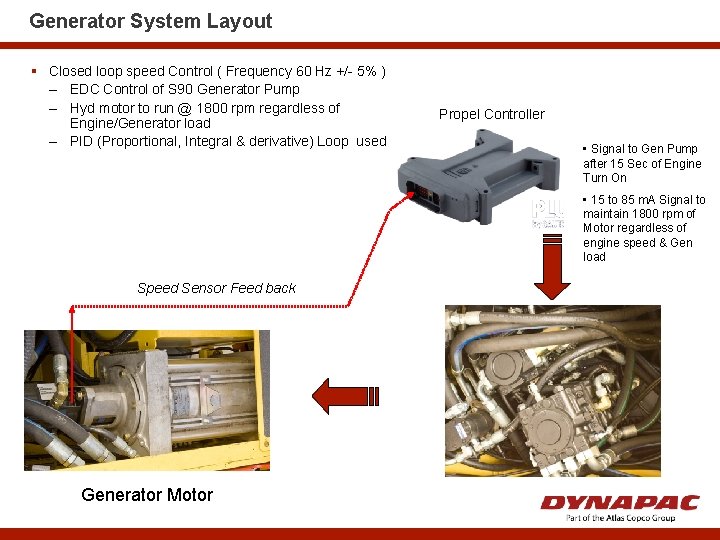
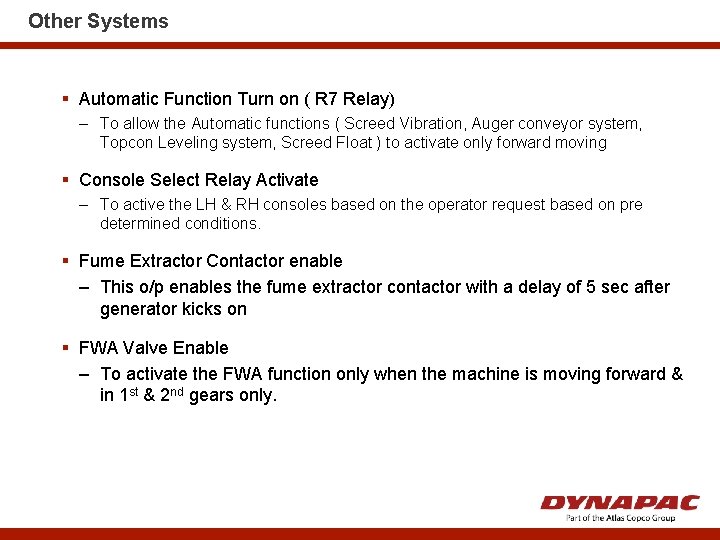
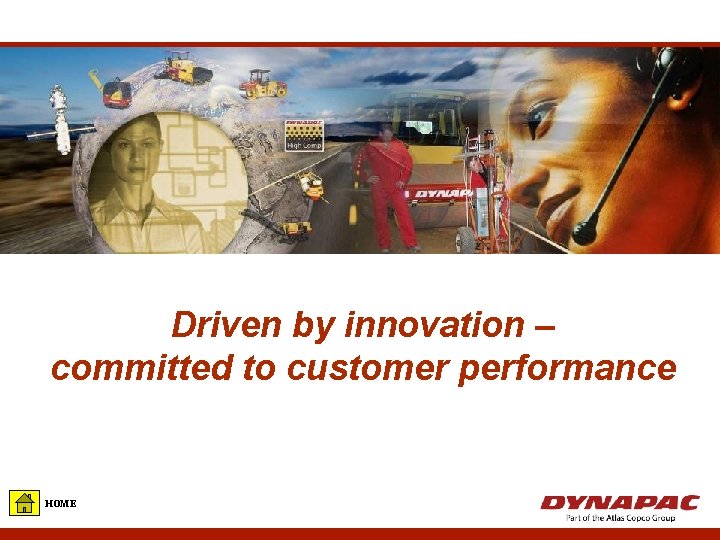
- Slides: 13
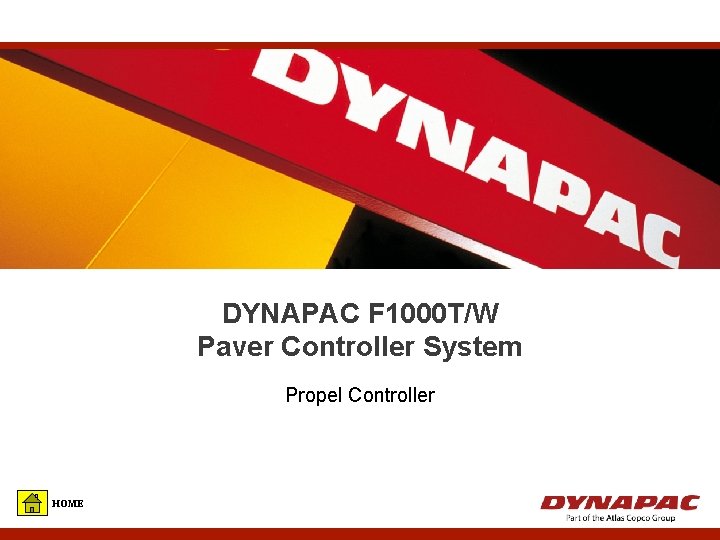
DYNAPAC F 1000 T/W Paver Controller System Propel Controller HOME
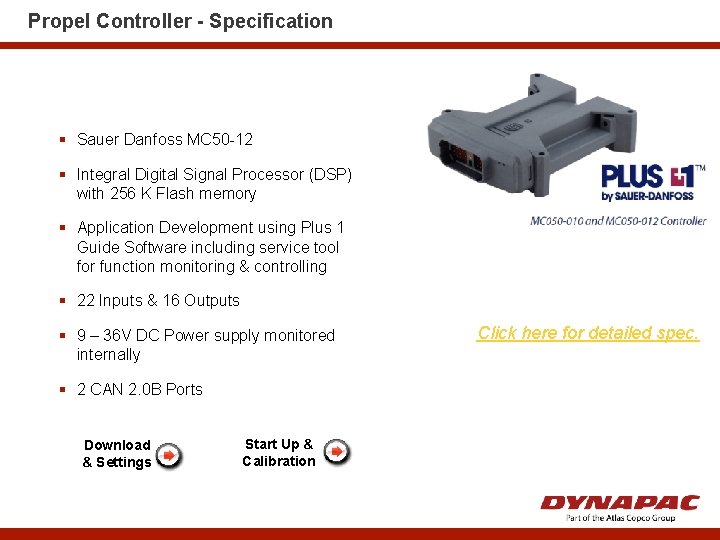
Propel Controller - Specification § Sauer Danfoss MC 50 -12 § Integral Digital Signal Processor (DSP) with 256 K Flash memory § Application Development using Plus 1 Guide Software including service tool for function monitoring & controlling § 22 Inputs & 16 Outputs § 9 – 36 V DC Power supply monitored internally § 2 CAN 2. 0 B Ports Download & Settings Start Up & Calibration Click here for detailed spec.
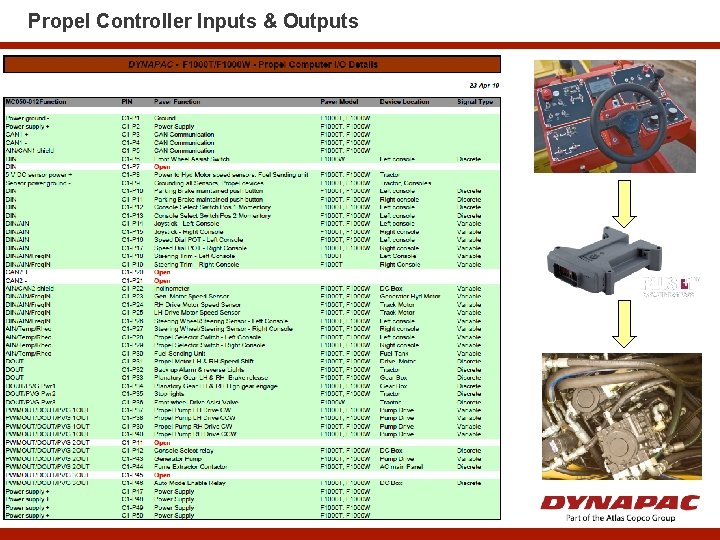
Propel Controller Inputs & Outputs
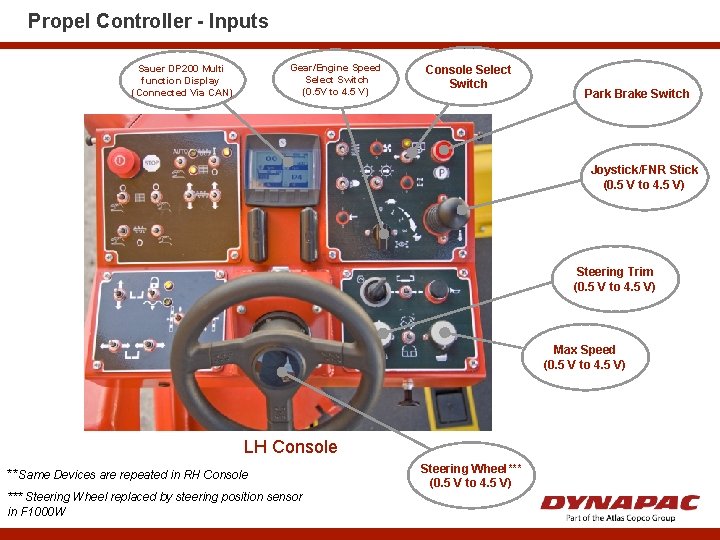
Propel Controller - Inputs Gear/Engine Speed Select Switch (0. 5 V to 4. 5 V) Sauer DP 200 Multi function Display (Connected Via CAN) Console Select Switch Park Brake Switch Joystick/FNR Stick (0. 5 V to 4. 5 V) Steering Trim (0. 5 V to 4. 5 V) Max Speed (0. 5 V to 4. 5 V) LH Console **Same Devices are repeated in RH Console *** Steering Wheel replaced by steering position sensor in F 1000 W Steering Wheel*** (0. 5 V to 4. 5 V)
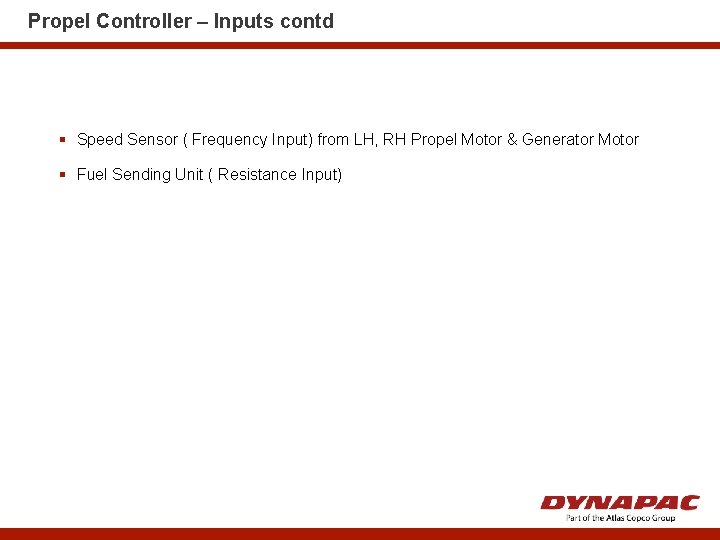
Propel Controller – Inputs contd § Speed Sensor ( Frequency Input) from LH, RH Propel Motor & Generator Motor § Fuel Sending Unit ( Resistance Input)
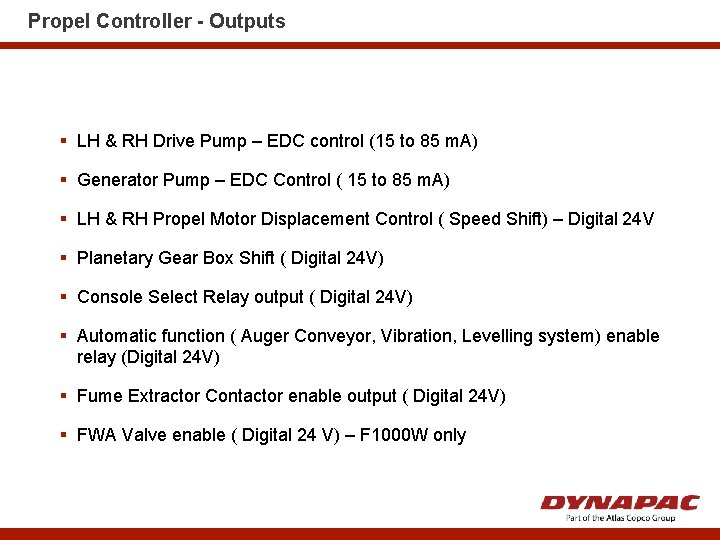
Propel Controller - Outputs § LH & RH Drive Pump – EDC control (15 to 85 m. A) § Generator Pump – EDC Control ( 15 to 85 m. A) § LH & RH Propel Motor Displacement Control ( Speed Shift) – Digital 24 V § Planetary Gear Box Shift ( Digital 24 V) § Console Select Relay output ( Digital 24 V) § Automatic function ( Auger Conveyor, Vibration, Levelling system) enable relay (Digital 24 V) § Fume Extractor Contactor enable output ( Digital 24 V) § FWA Valve enable ( Digital 24 V) – F 1000 W only
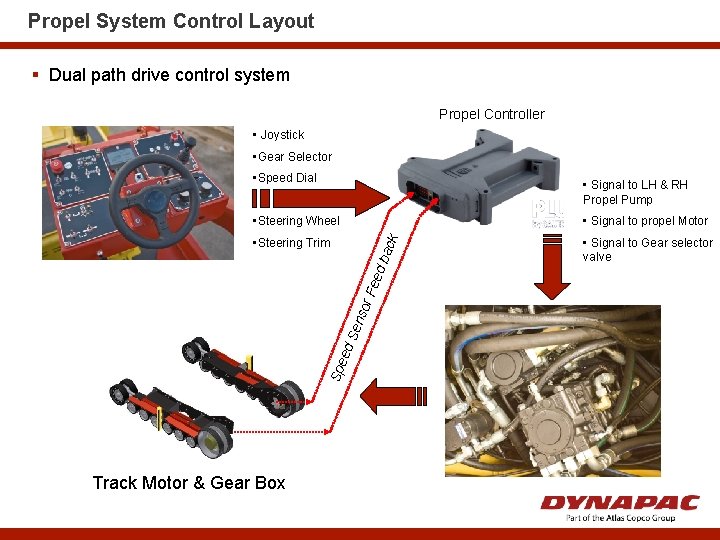
Propel System Control Layout § Dual path drive control system Propel Controller • Joystick • Gear Selector • Speed Dial • Signal to LH & RH Propel Pump • Signal to propel Motor • Steering Trim • Signal to Gear selector valve Spe ed S ens or F eed bac k • Steering Wheel Track Motor & Gear Box
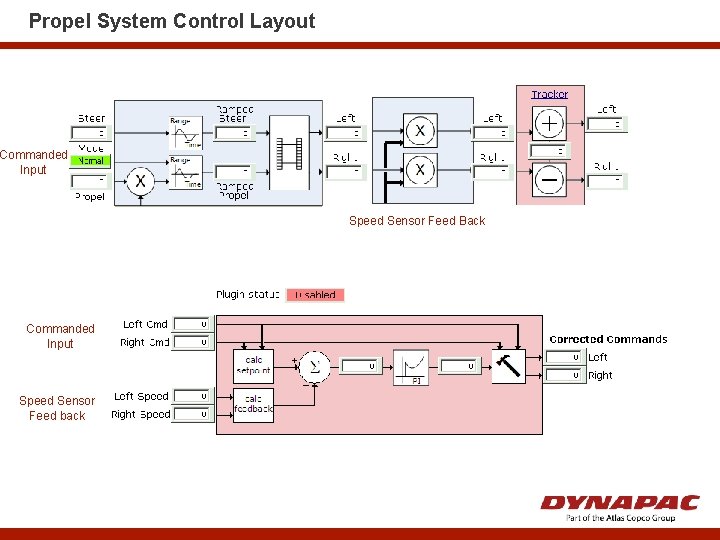
Propel System Control Layout Commanded Input Speed Sensor Feed Back Commanded Input Speed Sensor Feed back
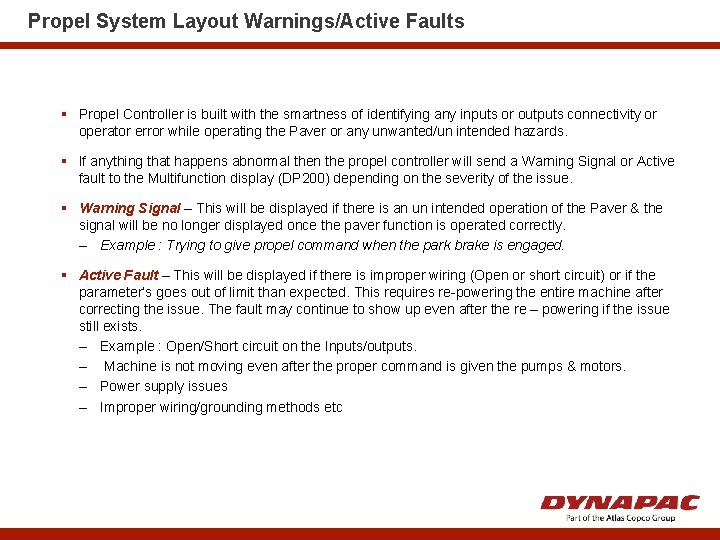
Propel System Layout Warnings/Active Faults § Propel Controller is built with the smartness of identifying any inputs or outputs connectivity or operator error while operating the Paver or any unwanted/un intended hazards. § If anything that happens abnormal then the propel controller will send a Warning Signal or Active fault to the Multifunction display (DP 200) depending on the severity of the issue. § Warning Signal – This will be displayed if there is an un intended operation of the Paver & the signal will be no longer displayed once the paver function is operated correctly. – Example : Trying to give propel command when the park brake is engaged. § Active Fault – This will be displayed if there is improper wiring (Open or short circuit) or if the parameter’s goes out of limit than expected. This requires re-powering the entire machine after correcting the issue. The fault may continue to show up even after the re – powering if the issue still exists. – Example : Open/Short circuit on the Inputs/outputs. – Machine is not moving even after the proper command is given the pumps & motors. – Power supply issues – Improper wiring/grounding methods etc
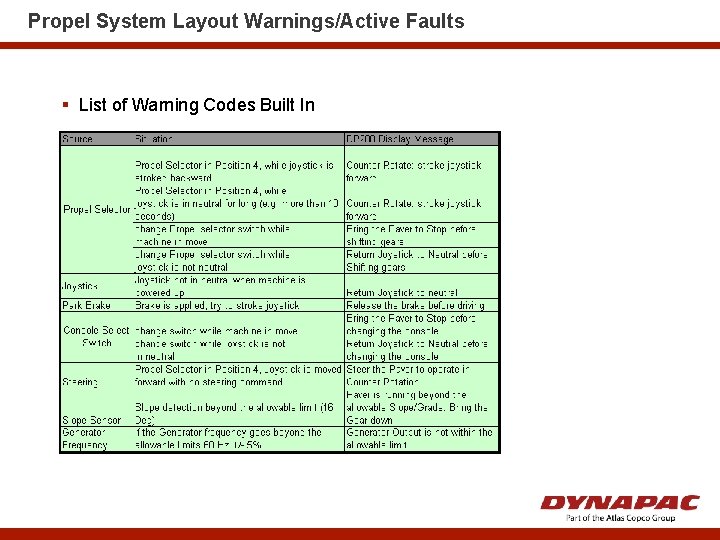
Propel System Layout Warnings/Active Faults § List of Warning Codes Built In
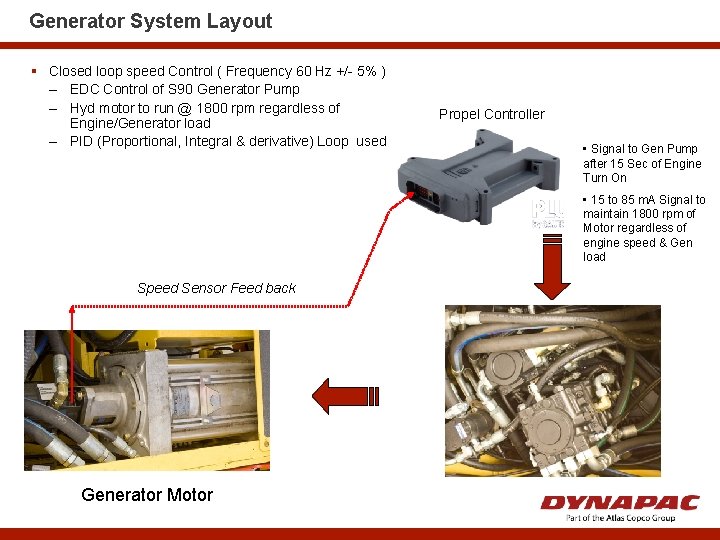
Generator System Layout § Closed loop speed Control ( Frequency 60 Hz +/- 5% ) – EDC Control of S 90 Generator Pump – Hyd motor to run @ 1800 rpm regardless of Engine/Generator load – PID (Proportional, Integral & derivative) Loop used Propel Controller • Signal to Gen Pump after 15 Sec of Engine Turn On • 15 to 85 m. A Signal to maintain 1800 rpm of Motor regardless of engine speed & Gen load Speed Sensor Feed back Generator Motor
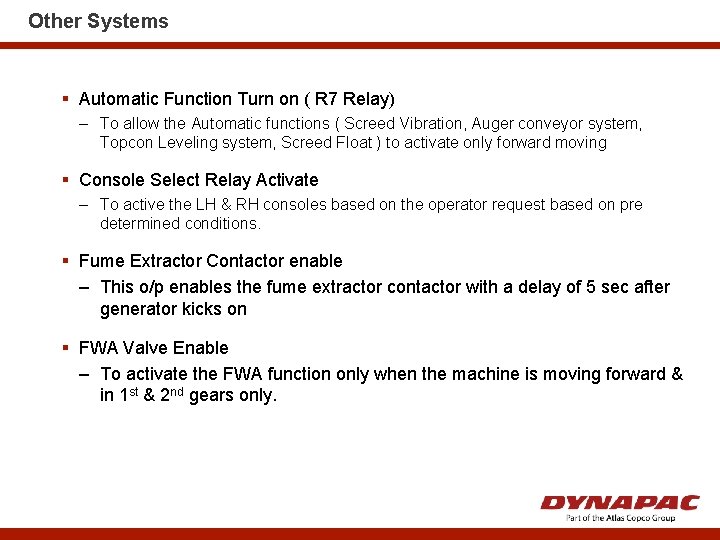
Other Systems § Automatic Function Turn on ( R 7 Relay) – To allow the Automatic functions ( Screed Vibration, Auger conveyor system, Topcon Leveling system, Screed Float ) to activate only forward moving § Console Select Relay Activate – To active the LH & RH consoles based on the operator request based on pre determined conditions. § Fume Extractor Contactor enable – This o/p enables the fume extractor contactor with a delay of 5 sec after generator kicks on § FWA Valve Enable – To activate the FWA function only when the machine is moving forward & in 1 st & 2 nd gears only.
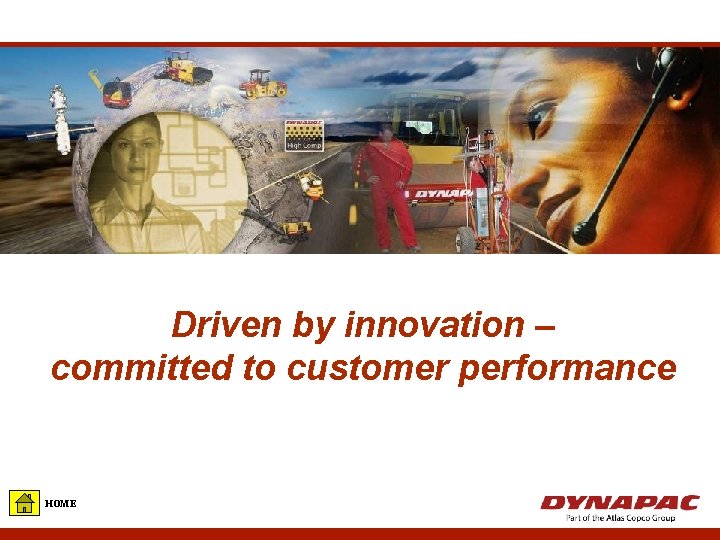
Driven by innovation – committed to customer performance HOME
Paver grate
Repeater link controller
Propel php tutorial
Dangerous propel lacrosse
Propel marketing
Terminal access controller access-control system
I/o devices
Terminal access controller access-control system
System center app controller
System center app controller
Raster scan display and vector scan display
Av system controller
Embedded controller program
Vex controller code