DFHx Conceptual Design Review 3 D Design and
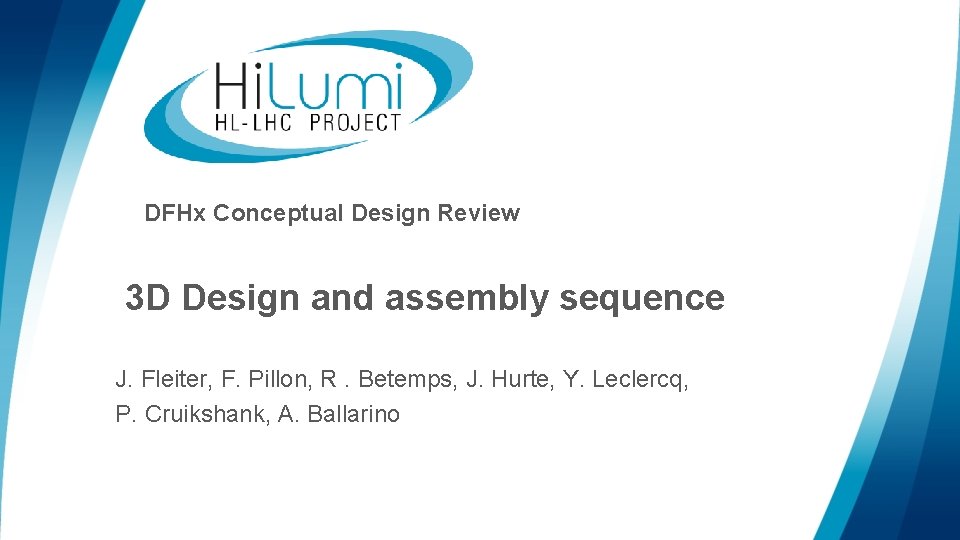
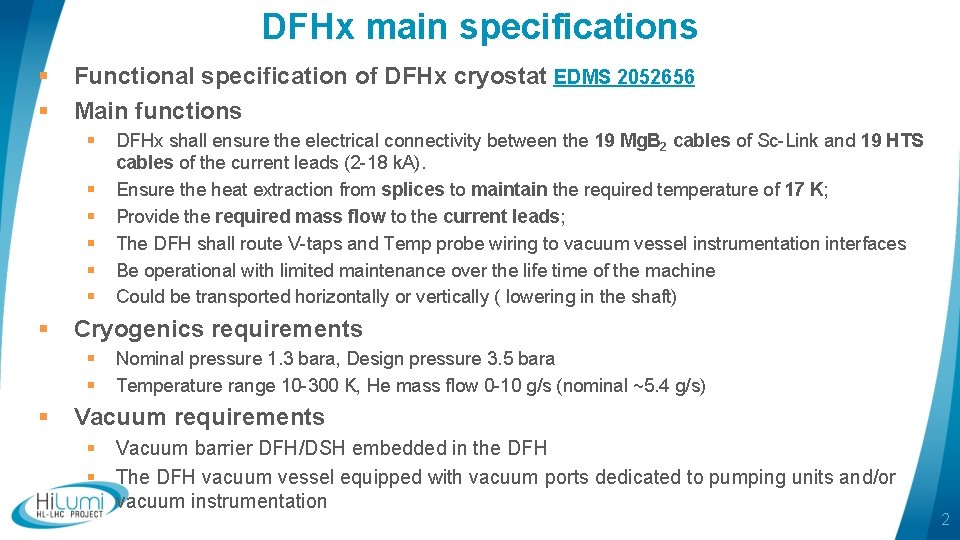
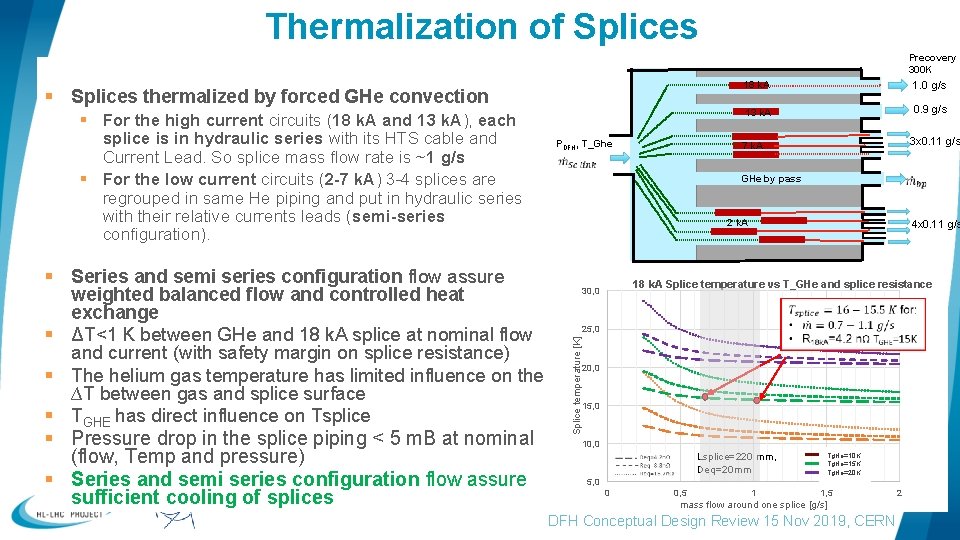
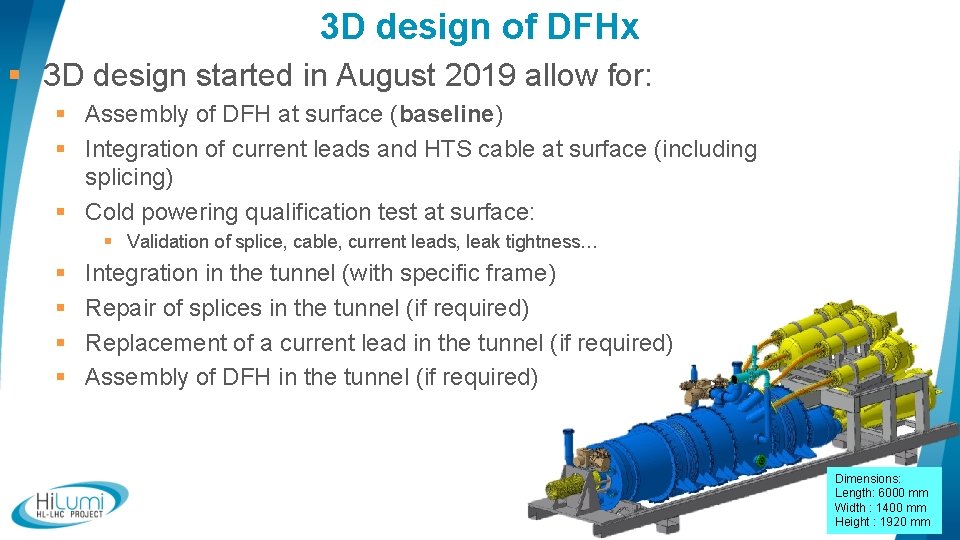
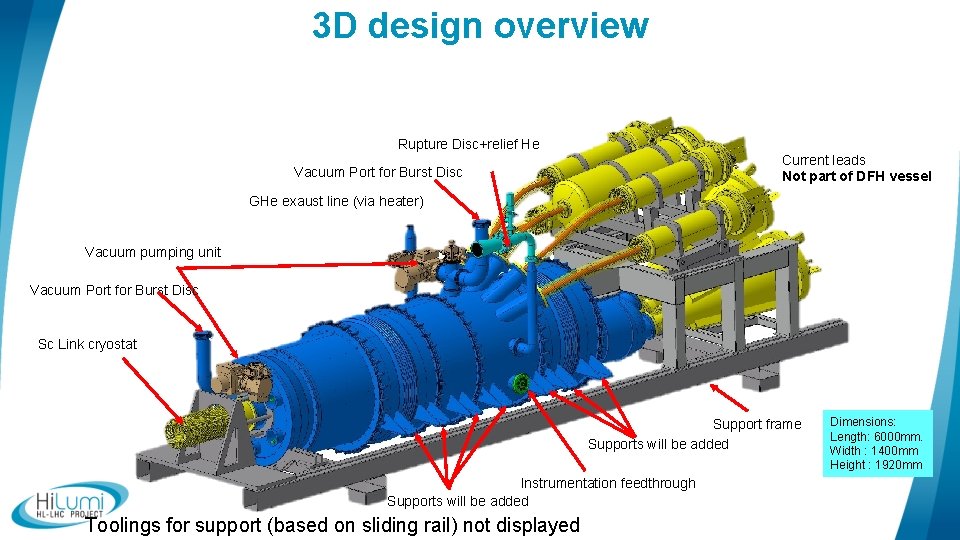
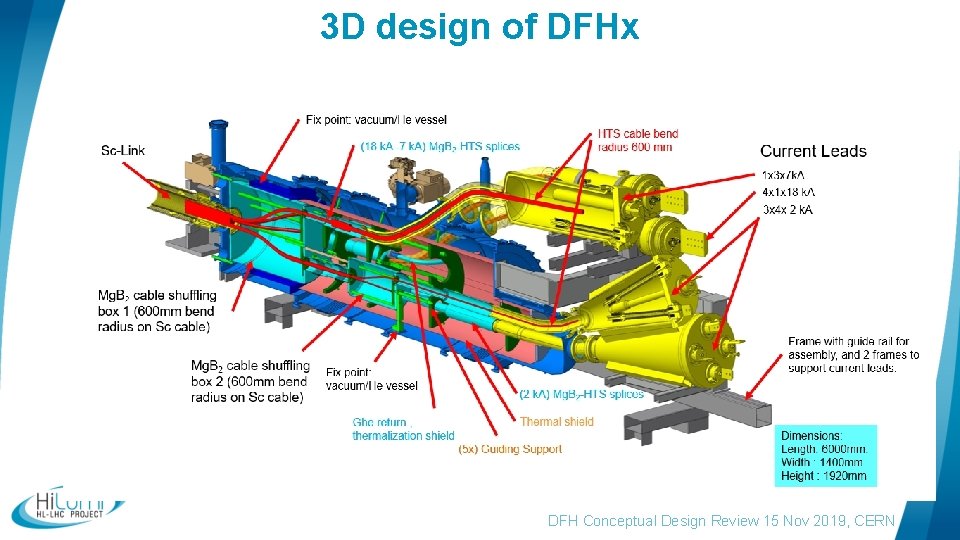
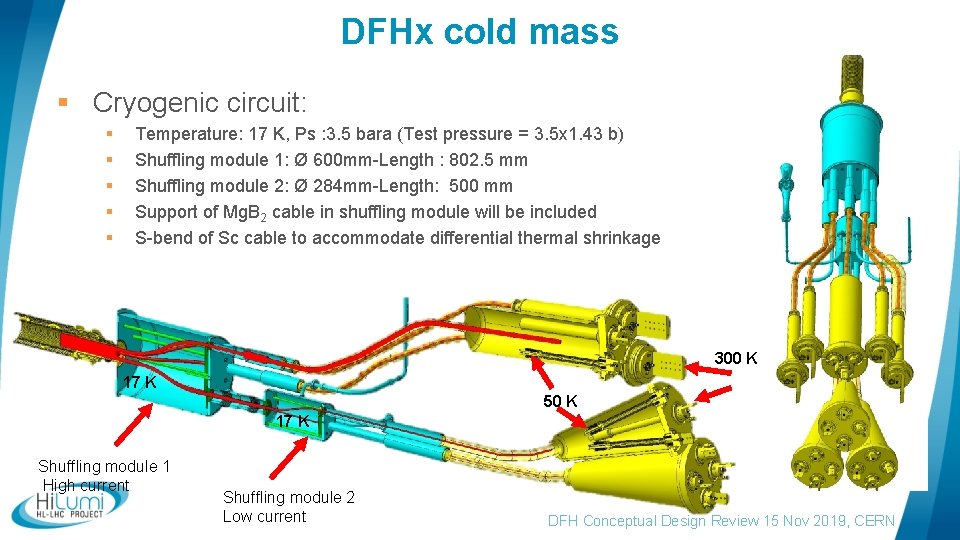
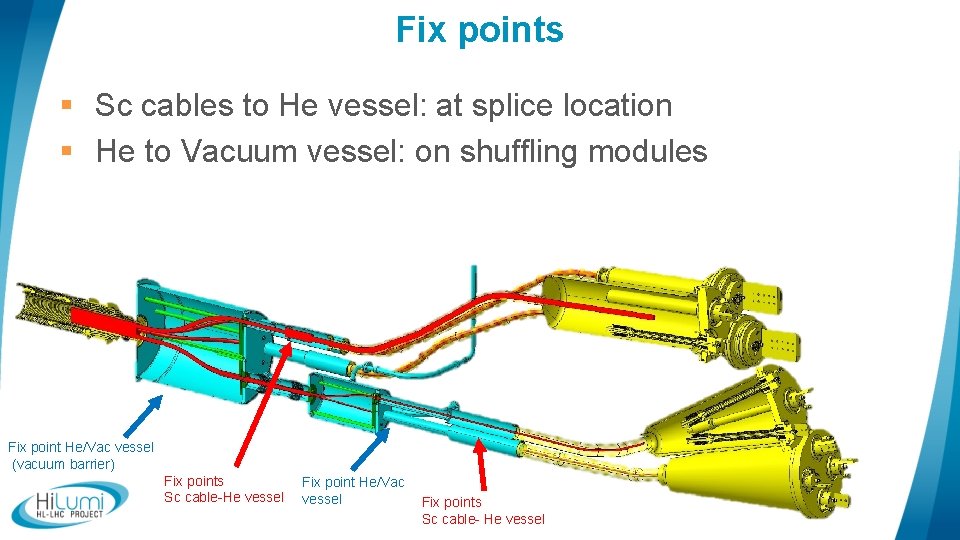
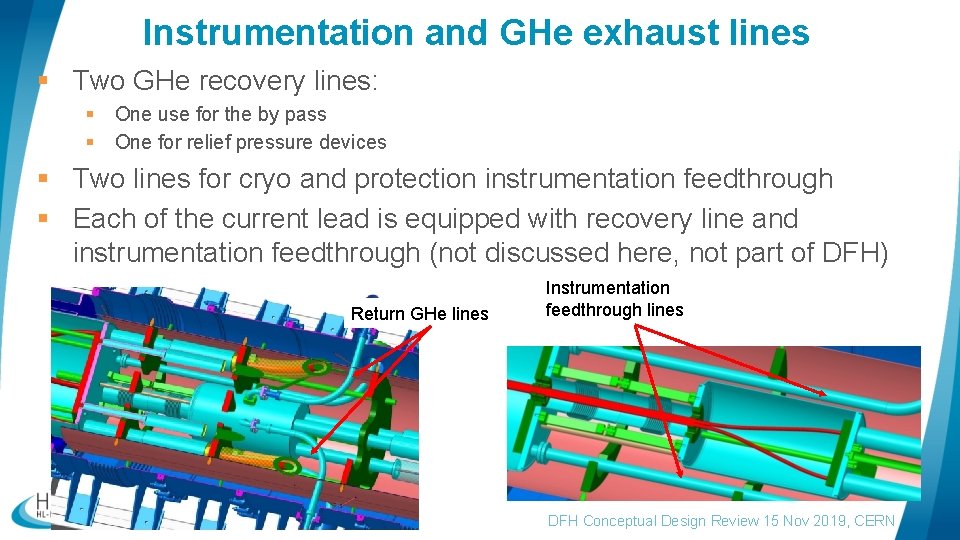
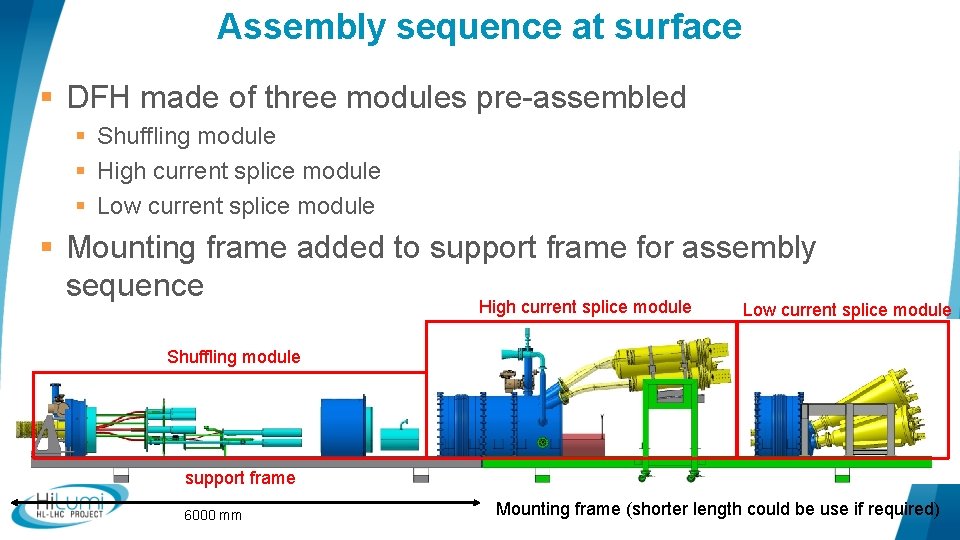
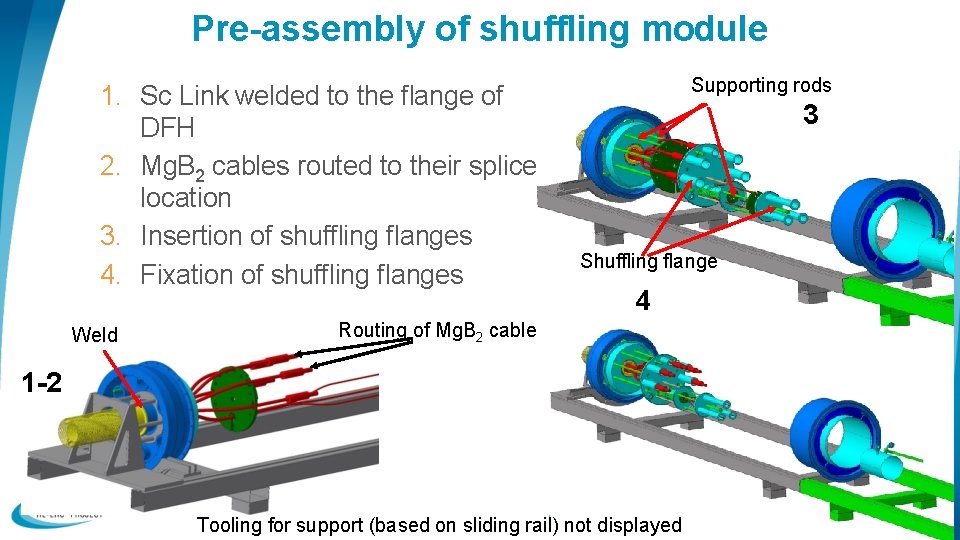
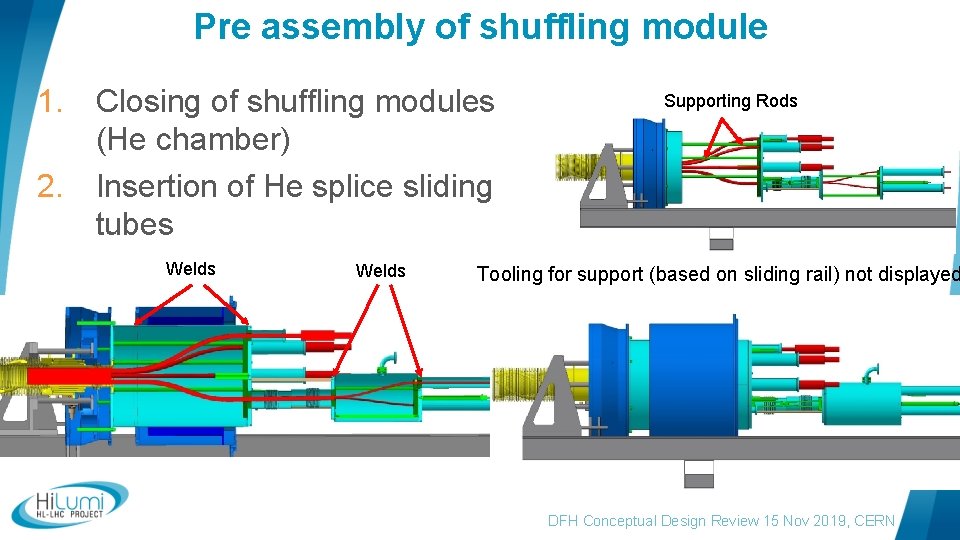
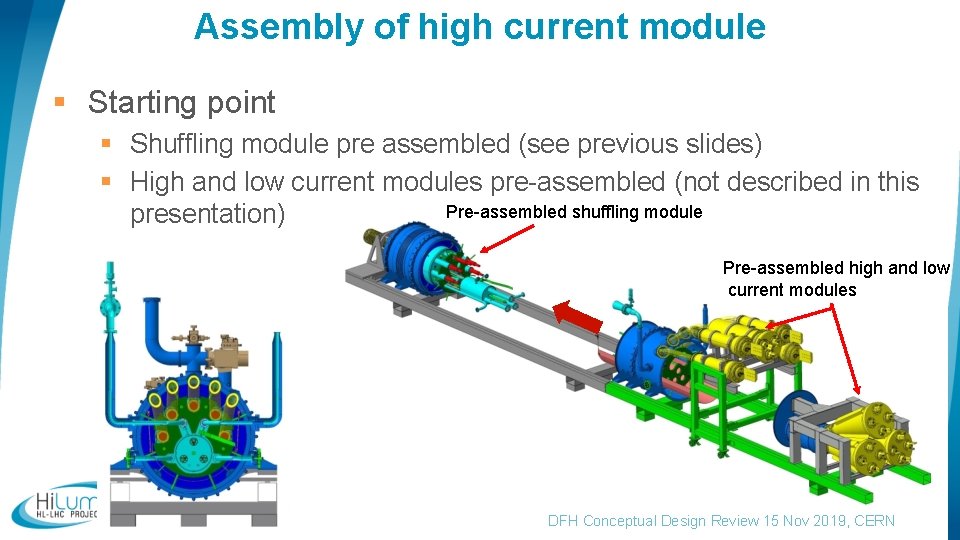
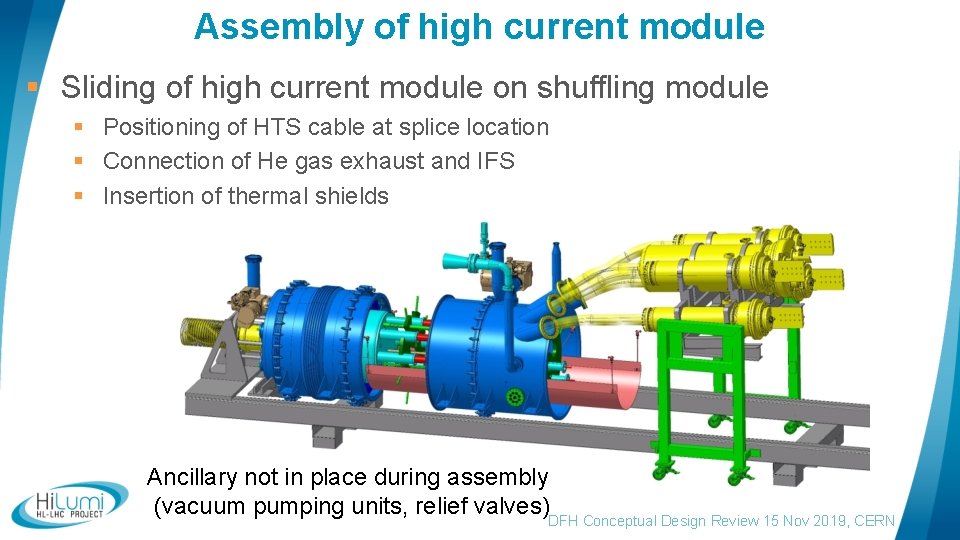
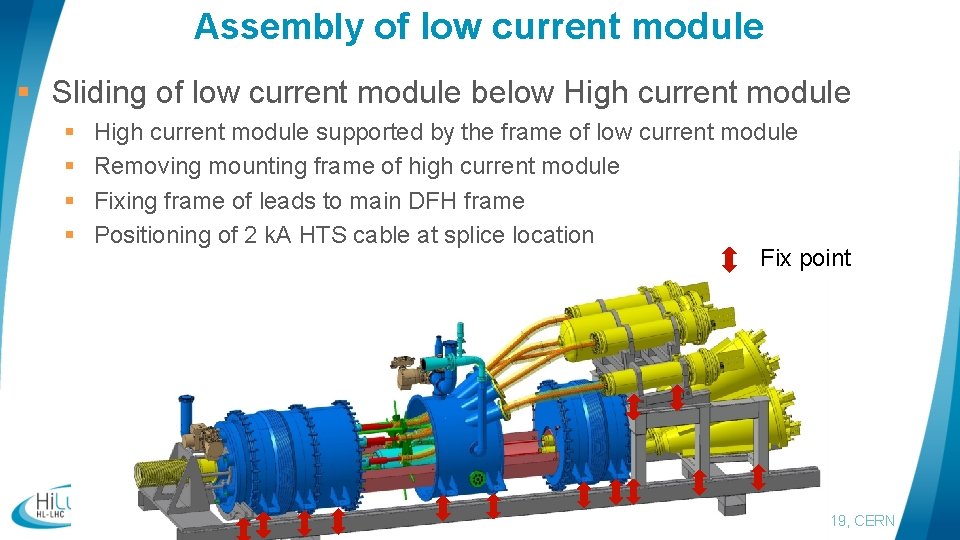
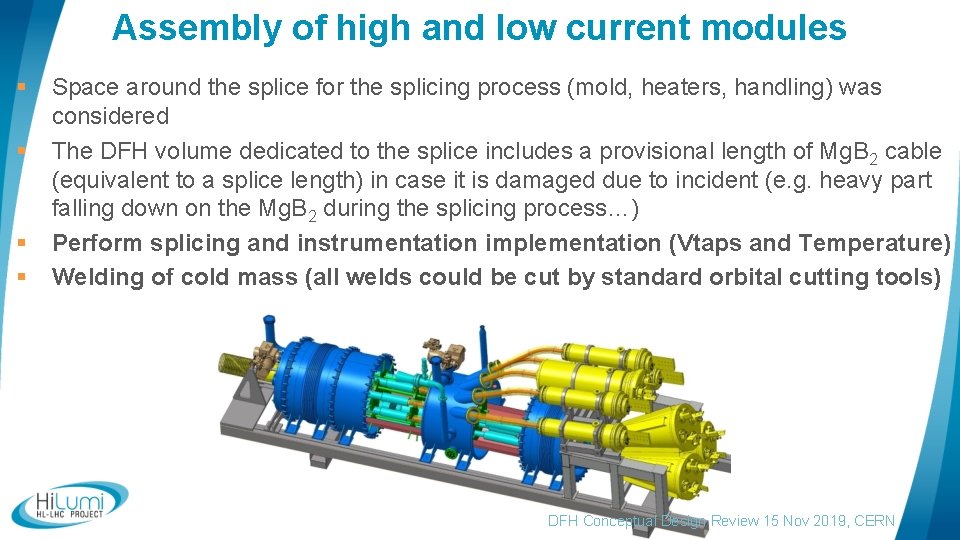
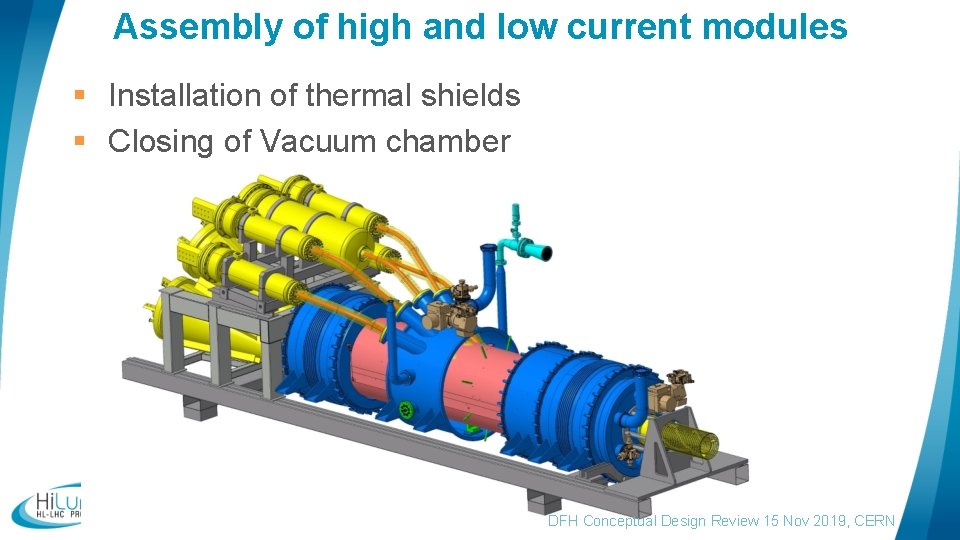
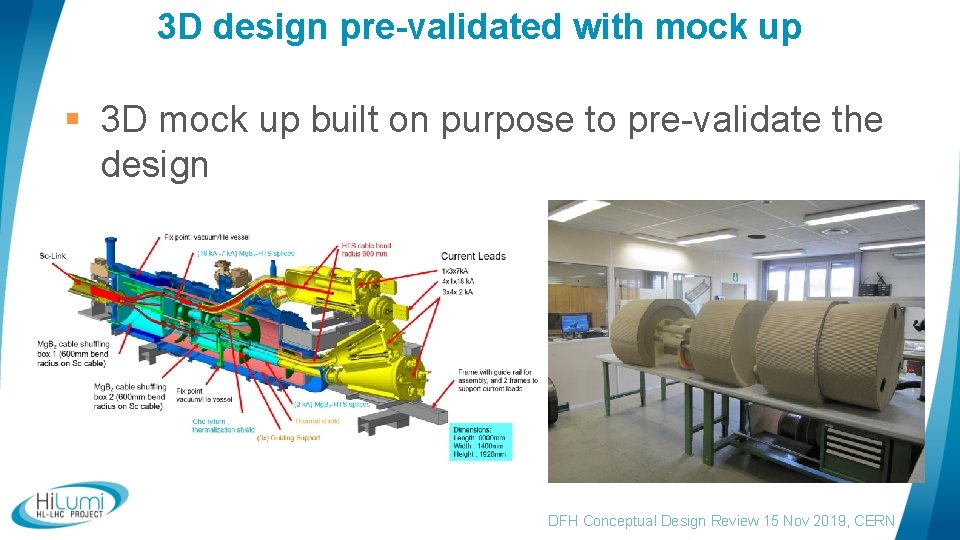
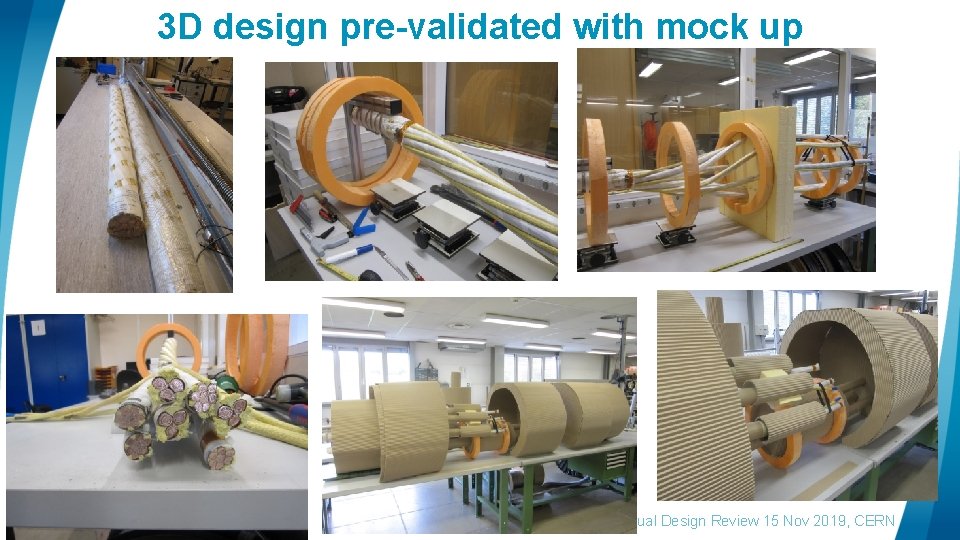
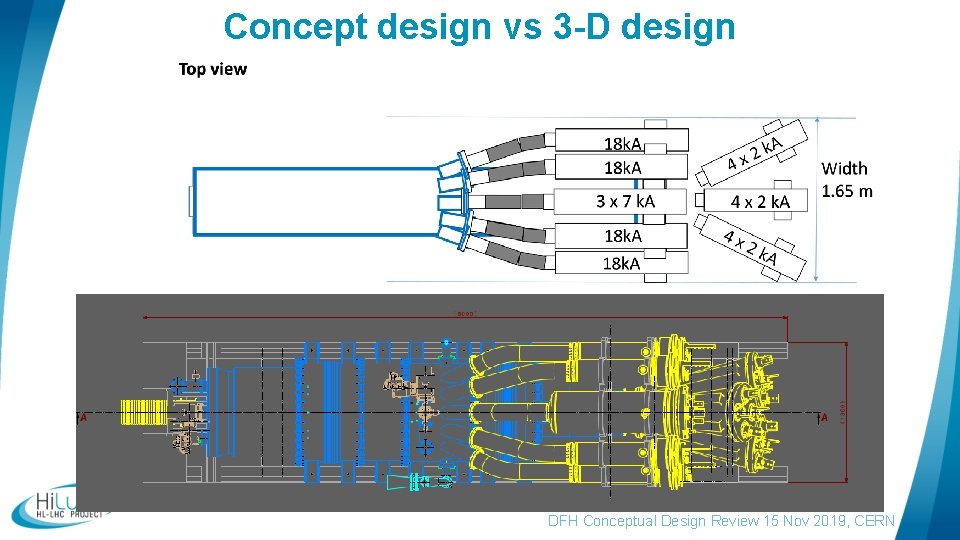
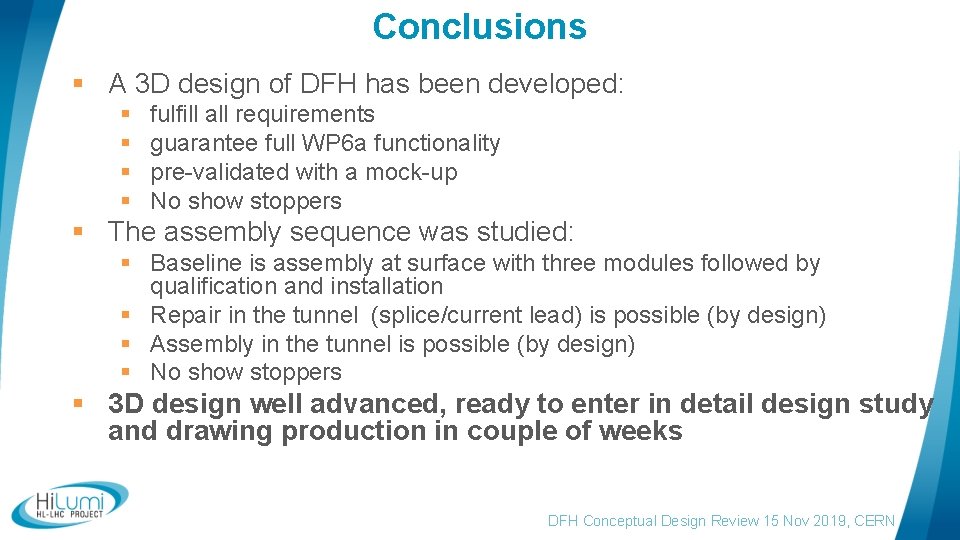
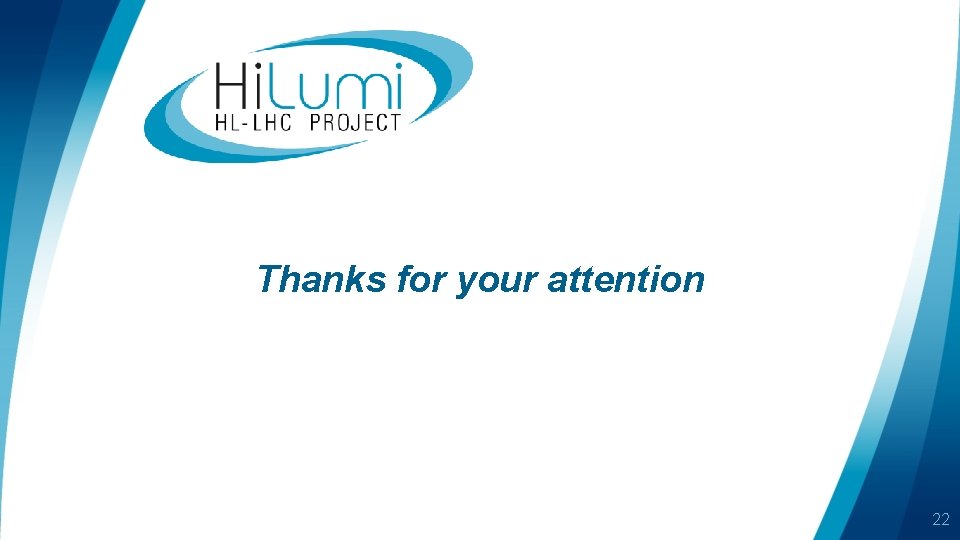
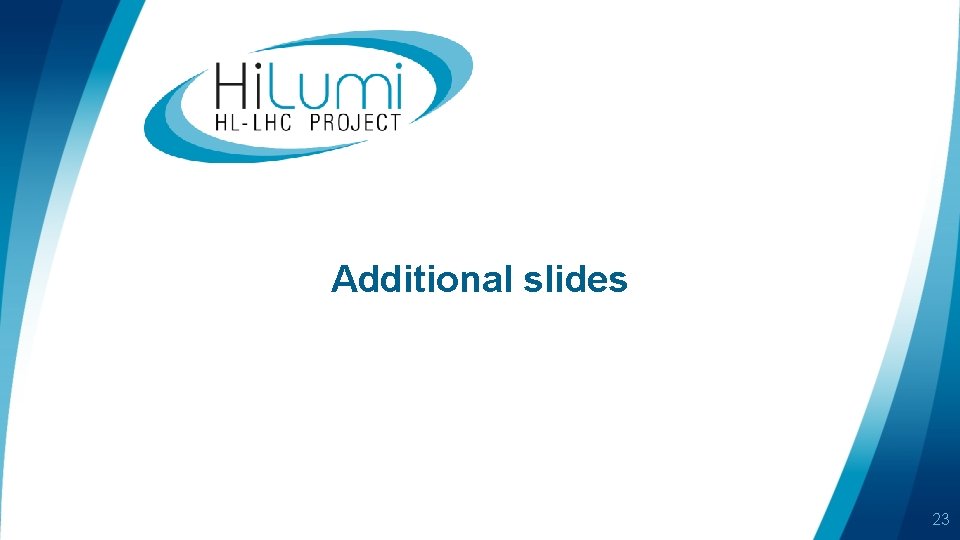
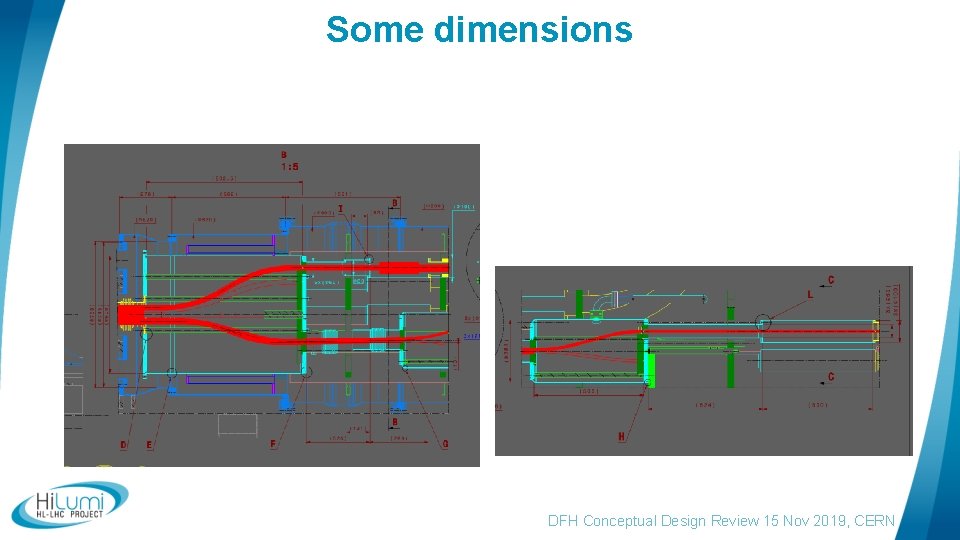
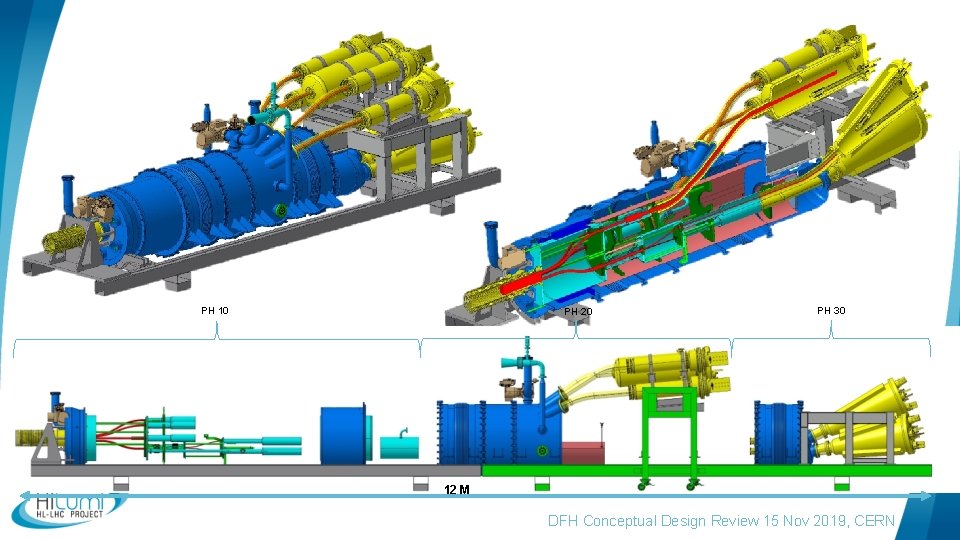
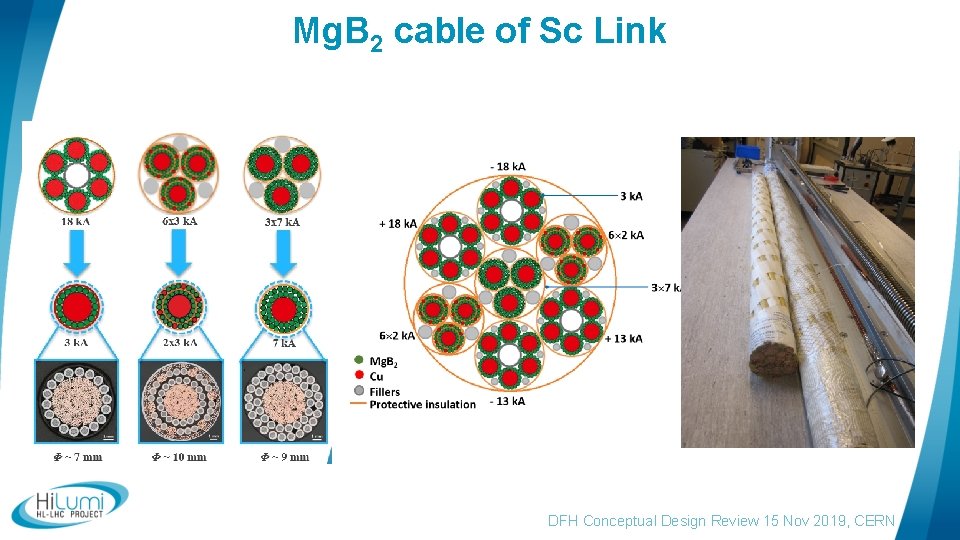
- Slides: 26
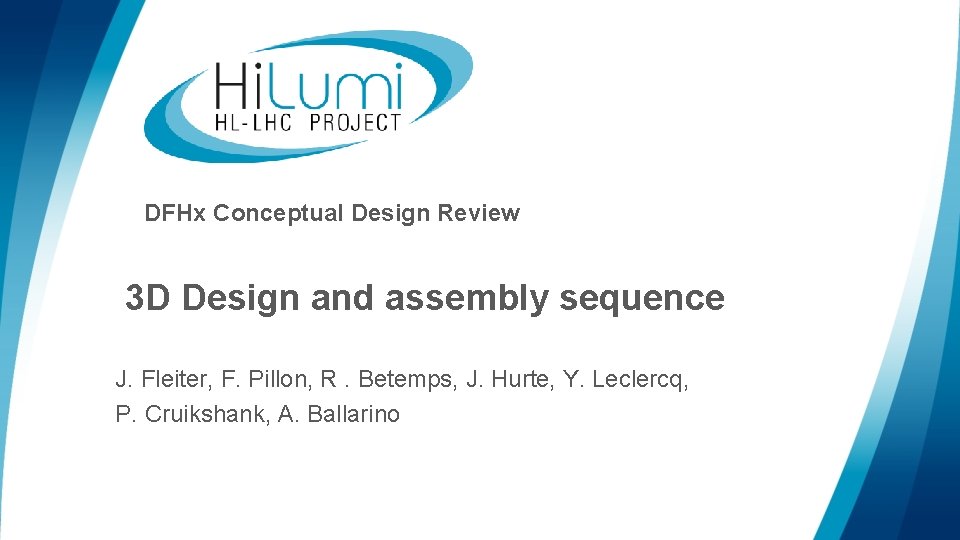
DFHx Conceptual Design Review 3 D Design and assembly sequence J. Fleiter, F. Pillon, R. Betemps, J. Hurte, Y. Leclercq, P. Cruikshank, A. Ballarino
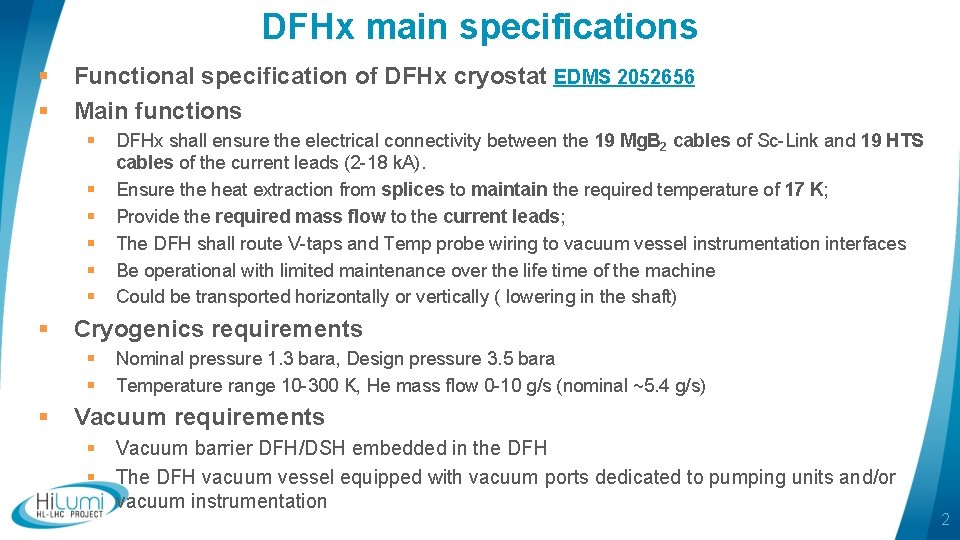
DFHx main specifications § § Functional specification of DFHx cryostat EDMS 2052656 Main functions § § § § Cryogenics requirements § § § DFHx shall ensure the electrical connectivity between the 19 Mg. B 2 cables of Sc-Link and 19 HTS cables of the current leads (2 -18 k. A). Ensure the heat extraction from splices to maintain the required temperature of 17 K; Provide the required mass flow to the current leads; The DFH shall route V-taps and Temp probe wiring to vacuum vessel instrumentation interfaces Be operational with limited maintenance over the life time of the machine Could be transported horizontally or vertically ( lowering in the shaft) Nominal pressure 1. 3 bara, Design pressure 3. 5 bara Temperature range 10 -300 K, He mass flow 0 -10 g/s (nominal ~5. 4 g/s) Vacuum requirements § § Vacuum barrier DFH/DSH embedded in the DFH The DFH vacuum vessel equipped with vacuum ports dedicated to pumping units and/or vacuum instrumentation 2
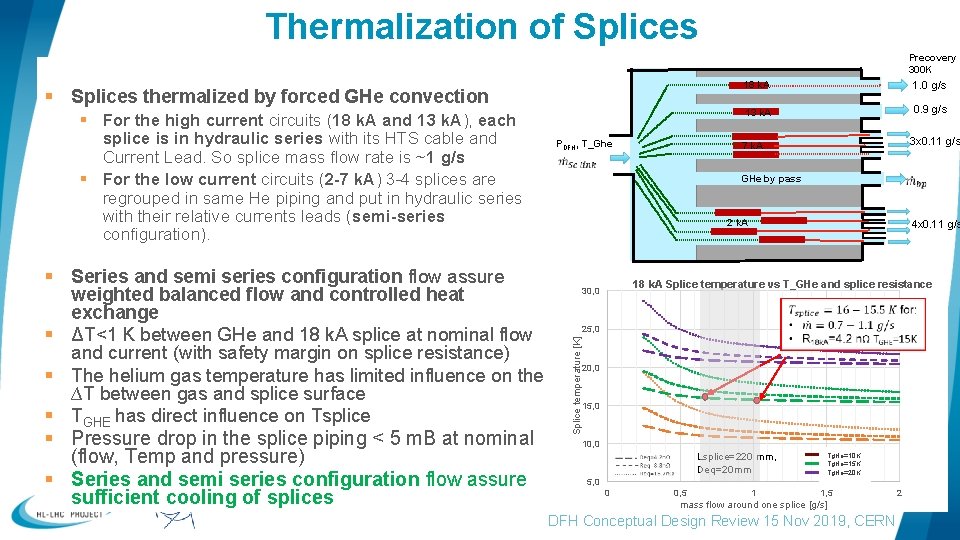
Thermalization of Splices Precovery 300 K § Splices thermalized by forced GHe convection § Series and semi series configuration flow assure weighted balanced flow and controlled heat exchange § ΔT<1 K between GHe and 18 k. A splice at nominal flow and current (with safety margin on splice resistance) § The helium gas temperature has limited influence on the ∆T between gas and splice surface § TGHE has direct influence on Tsplice § Pressure drop in the splice piping < 5 m. B at nominal (flow, Temp and pressure) § Series and semi series configuration flow assure sufficient cooling of splices PDFH, T_Ghe 1. 0 g/s 13 k. A 0. 9 g/s 3 x 0. 11 g/s 7 k. A GHe by pass 2 k. A 4 x 0. 11 g/s 18 k. A Splice temperature vs T_GHe and splice resistance 30, 0 25, 0 Splice temperature [K] § For the high current circuits (18 k. A and 13 k. A), each splice is in hydraulic series with its HTS cable and Current Lead. So splice mass flow rate is ~1 g/s § For the low current circuits (2 -7 k. A) 3 -4 splices are regrouped in same He piping and put in hydraulic series with their relative currents leads (semi-series configuration). 18 k. A 20, 0 15, 0 10, 0 Lsplice=220 mm, Deq=20 mm Tg. He=10 K Tg. He=15 K Tg. He=20 K 5, 0 0 0, 5 1 1, 5 mass flow around one splice [g/s] DFH Conceptual Design Review 15 Nov 2019, CERN 2
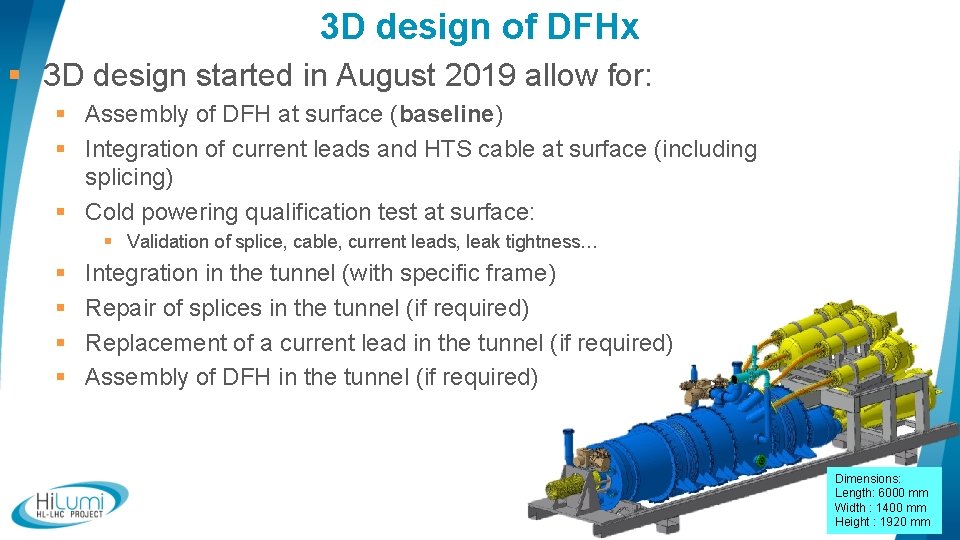
3 D design of DFHx § 3 D design started in August 2019 allow for: § Assembly of DFH at surface (baseline) § Integration of current leads and HTS cable at surface (including splicing) § Cold powering qualification test at surface: § Validation of splice, cable, current leads, leak tightness… § § Integration in the tunnel (with specific frame) Repair of splices in the tunnel (if required) Replacement of a current lead in the tunnel (if required) Assembly of DFH in the tunnel (if required) Dimensions: Length: 6000 mm Width : 1400 mm Height : 1920 mm
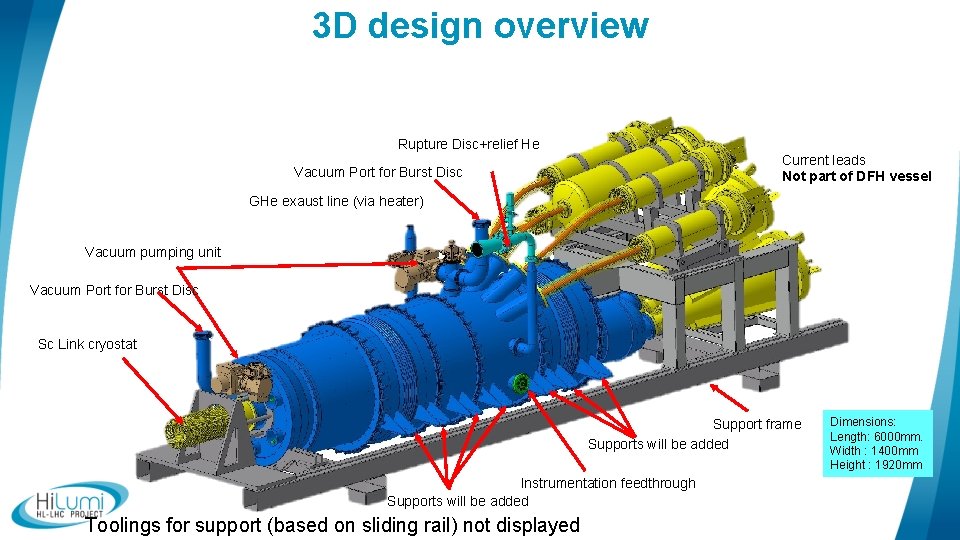
3 D design overview Rupture Disc+relief He Current leads Not part of DFH vessel Vacuum Port for Burst Disc GHe exaust line (via heater) Vacuum pumping unit Vacuum Port for Burst Disc Sc Link cryostat Support frame Supports will be added Instrumentation feedthrough Supports will be added Toolings for support (based on sliding rail) not displayed Dimensions: Length: 6000 mm. Width : 1400 mm Height : 1920 mm
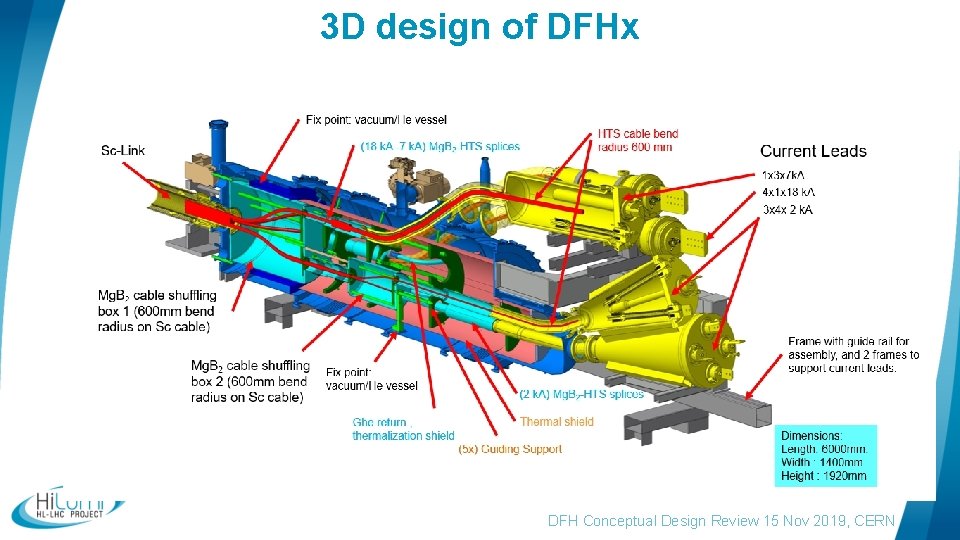
3 D design of DFHx DFH Conceptual Design Review 15 Nov 2019, CERN
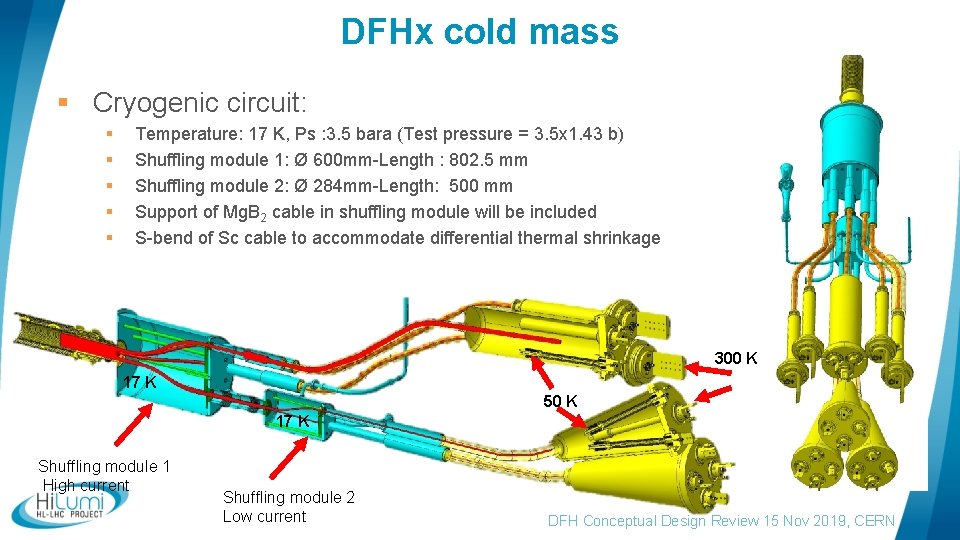
DFHx cold mass § Cryogenic circuit: § § § Temperature: 17 K, Ps : 3. 5 bara (Test pressure = 3. 5 x 1. 43 b) Shuffling module 1: Ø 600 mm-Length : 802. 5 mm Shuffling module 2: Ø 284 mm-Length: 500 mm Support of Mg. B 2 cable in shuffling module will be included S-bend of Sc cable to accommodate differential thermal shrinkage 300 K 17 K 50 K 17 K Shuffling module 1 High current Shuffling module 2 Low current DFH Conceptual Design Review 15 Nov 2019, CERN
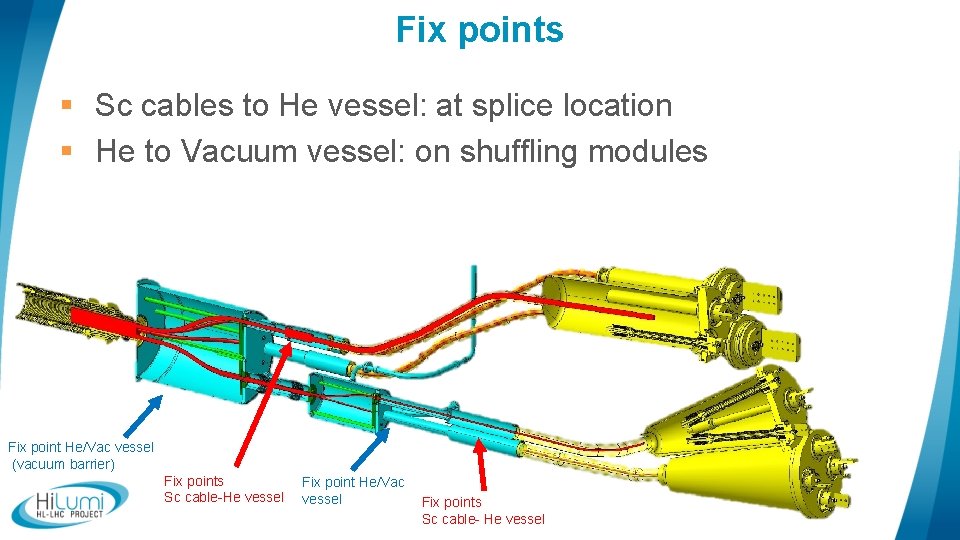
Fix points § Sc cables to He vessel: at splice location § He to Vacuum vessel: on shuffling modules Fix point He/Vac vessel (vacuum barrier) Fix points Sc cable-He vessel Fix point He/Vac vessel Fix points Sc cable- He vessel
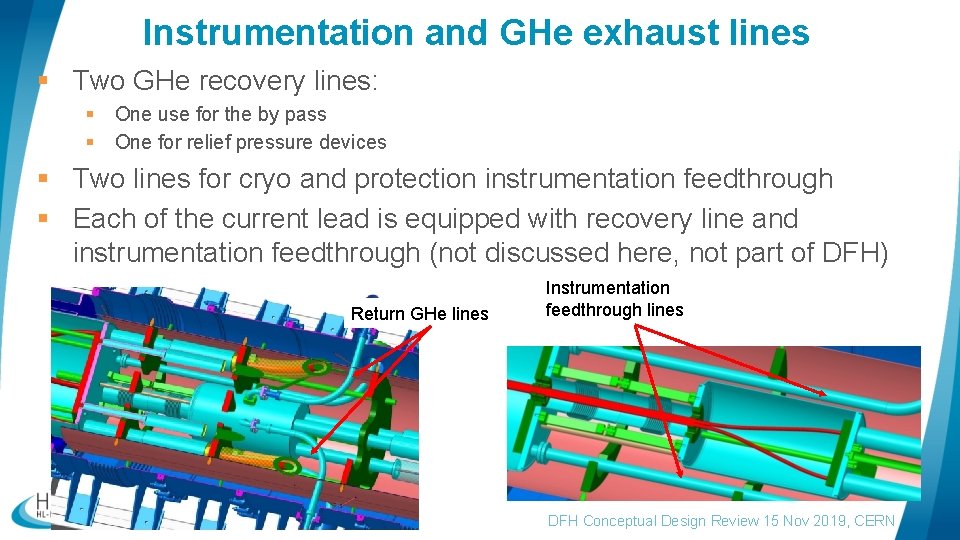
Instrumentation and GHe exhaust lines § Two GHe recovery lines: § § One use for the by pass One for relief pressure devices § Two lines for cryo and protection instrumentation feedthrough § Each of the current lead is equipped with recovery line and instrumentation feedthrough (not discussed here, not part of DFH) Return GHe lines Instrumentation feedthrough lines DFH Conceptual Design Review 15 Nov 2019, CERN
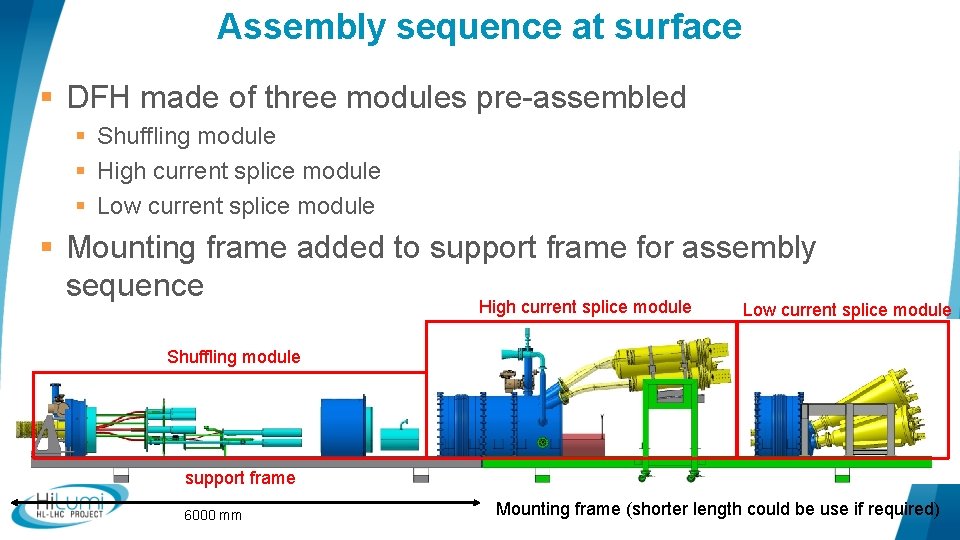
Assembly sequence at surface § DFH made of three modules pre-assembled § Shuffling module § High current splice module § Low current splice module § Mounting frame added to support frame for assembly sequence High current splice module Low current splice module Shuffling module support frame 6000 mm Mounting frame (shorter length could be use if required)
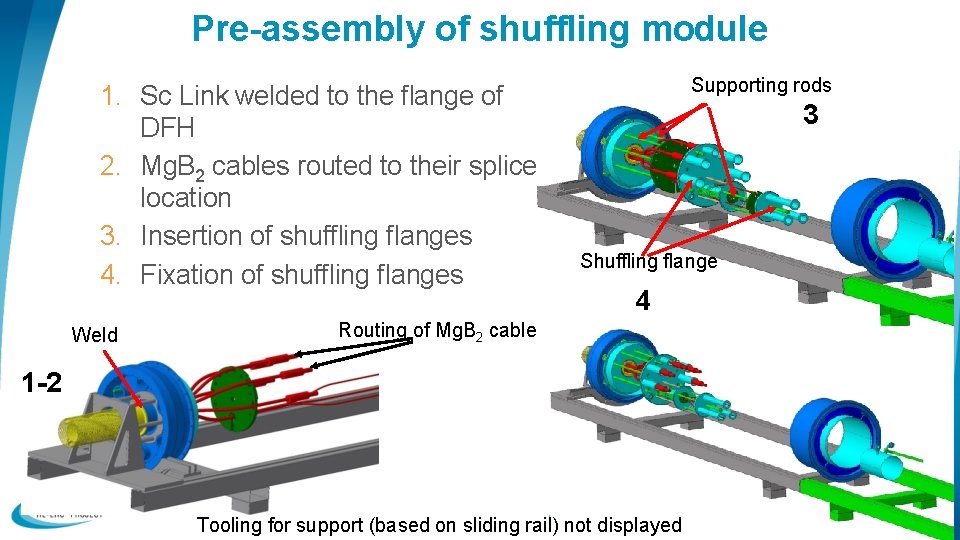
Pre-assembly of shuffling module 1. Sc Link welded to the flange of DFH 2. Mg. B 2 cables routed to their splice location 3. Insertion of shuffling flanges 4. Fixation of shuffling flanges Weld Supporting rods 3 Shuffling flange 4 Routing of Mg. B 2 cable 1 -2 DFH Design Review 15 Nov 2019, CERN Tooling for support (based on sliding rail) not. Conceptual displayed
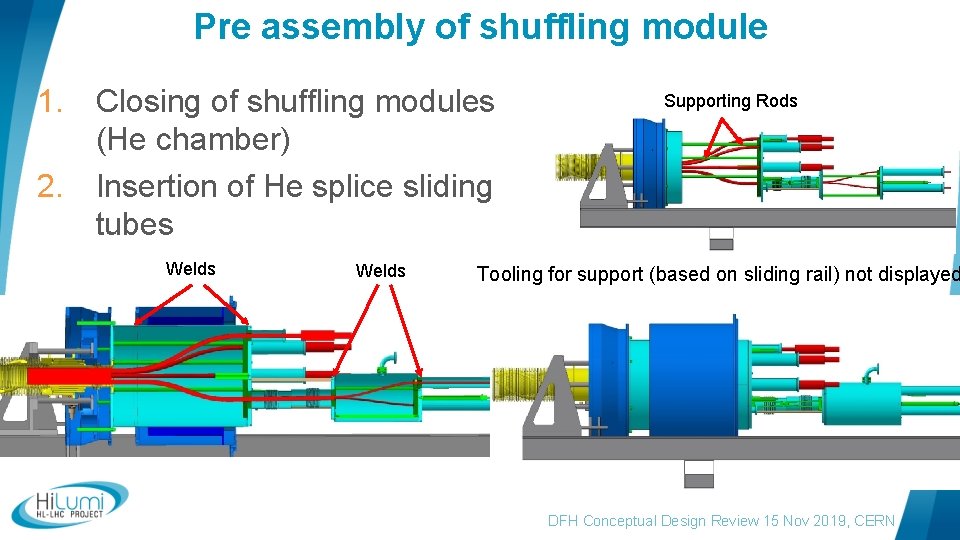
Pre assembly of shuffling module 1. Closing of shuffling modules (He chamber) 2. Insertion of He splice sliding tubes Welds Supporting Rods Tooling for support (based on sliding rail) not displayed DFH Conceptual Design Review 15 Nov 2019, CERN
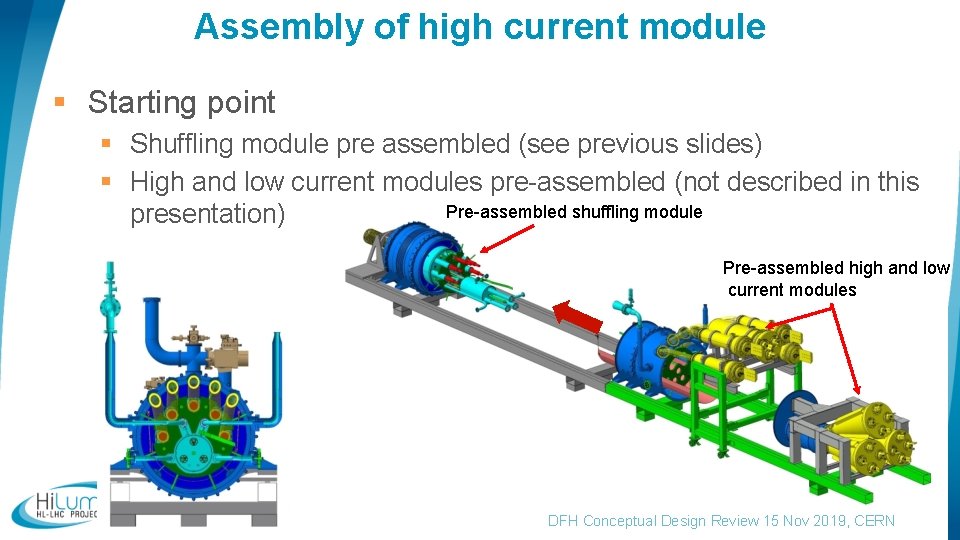
Assembly of high current module § Starting point § Shuffling module pre assembled (see previous slides) § High and low current modules pre-assembled (not described in this Pre-assembled shuffling module presentation) Pre-assembled high and low current modules DFH Conceptual Design Review 15 Nov 2019, CERN
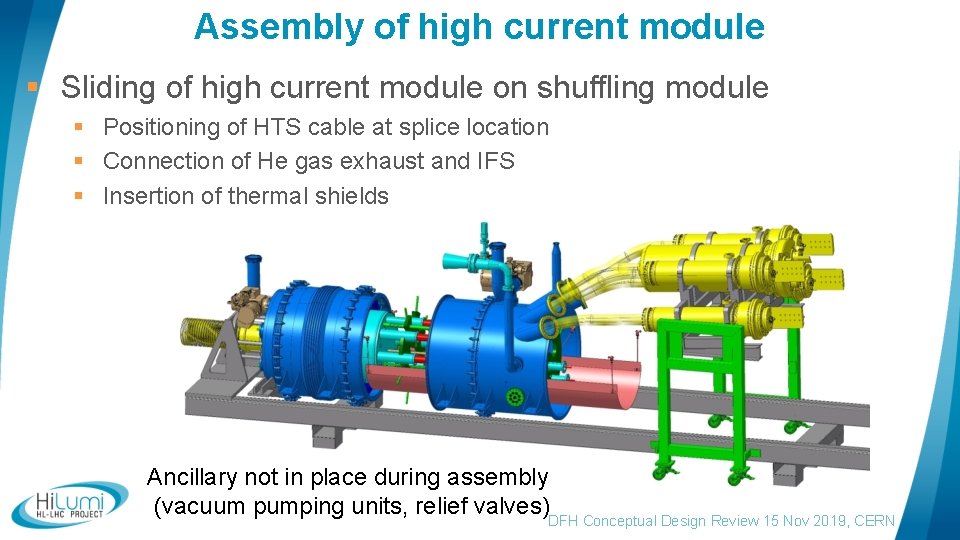
Assembly of high current module § Sliding of high current module on shuffling module § Positioning of HTS cable at splice location § Connection of He gas exhaust and IFS § Insertion of thermal shields Ancillary not in place during assembly (vacuum pumping units, relief valves)DFH Conceptual Design Review 15 Nov 2019, CERN
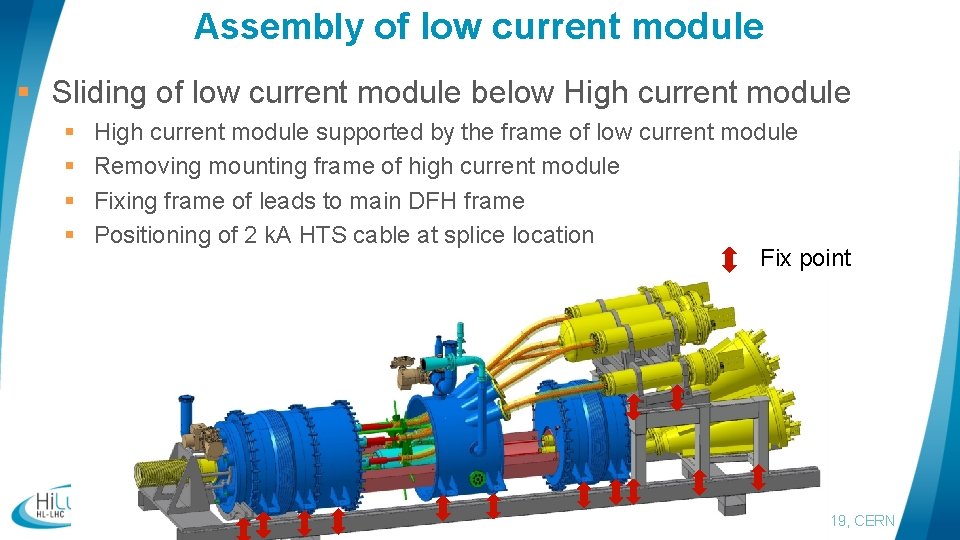
Assembly of low current module § Sliding of low current module below High current module § § High current module supported by the frame of low current module Removing mounting frame of high current module Fixing frame of leads to main DFH frame Positioning of 2 k. A HTS cable at splice location Fix point DFH Conceptual Design Review 15 Nov 2019, CERN
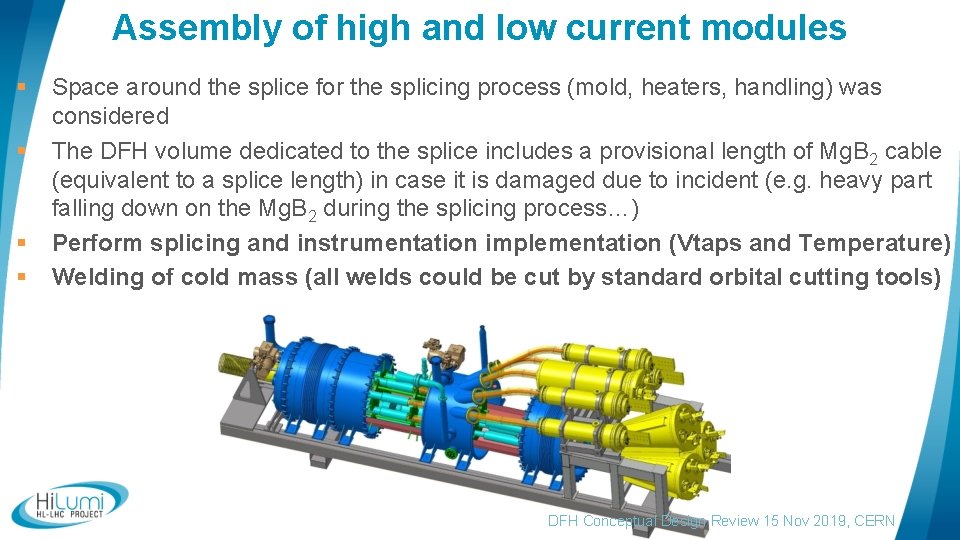
Assembly of high and low current modules § § Space around the splice for the splicing process (mold, heaters, handling) was considered The DFH volume dedicated to the splice includes a provisional length of Mg. B 2 cable (equivalent to a splice length) in case it is damaged due to incident (e. g. heavy part falling down on the Mg. B 2 during the splicing process…) Perform splicing and instrumentation implementation (Vtaps and Temperature) Welding of cold mass (all welds could be cut by standard orbital cutting tools) DFH Conceptual Design Review 15 Nov 2019, CERN
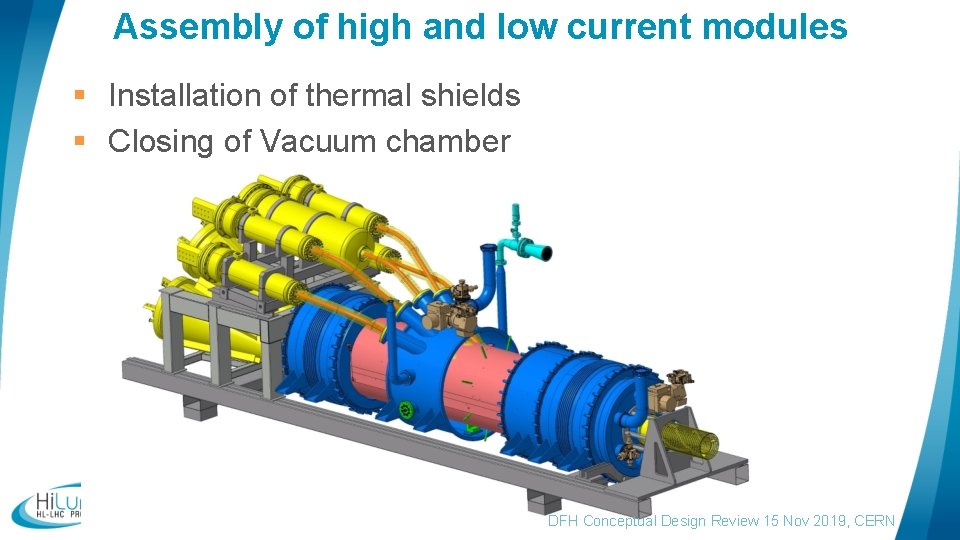
Assembly of high and low current modules § Installation of thermal shields § Closing of Vacuum chamber DFH Conceptual Design Review 15 Nov 2019, CERN
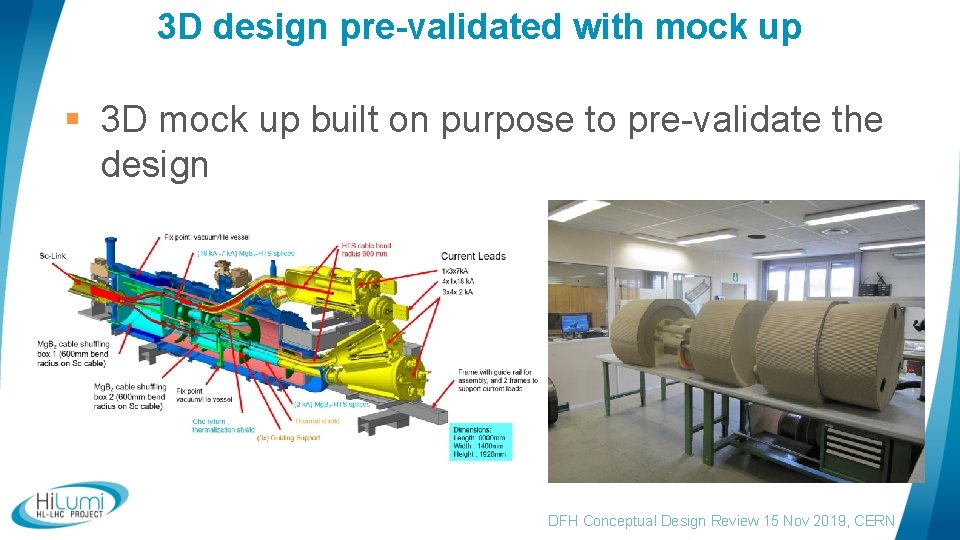
3 D design pre-validated with mock up § 3 D mock up built on purpose to pre-validate the design DFH Conceptual Design Review 15 Nov 2019, CERN
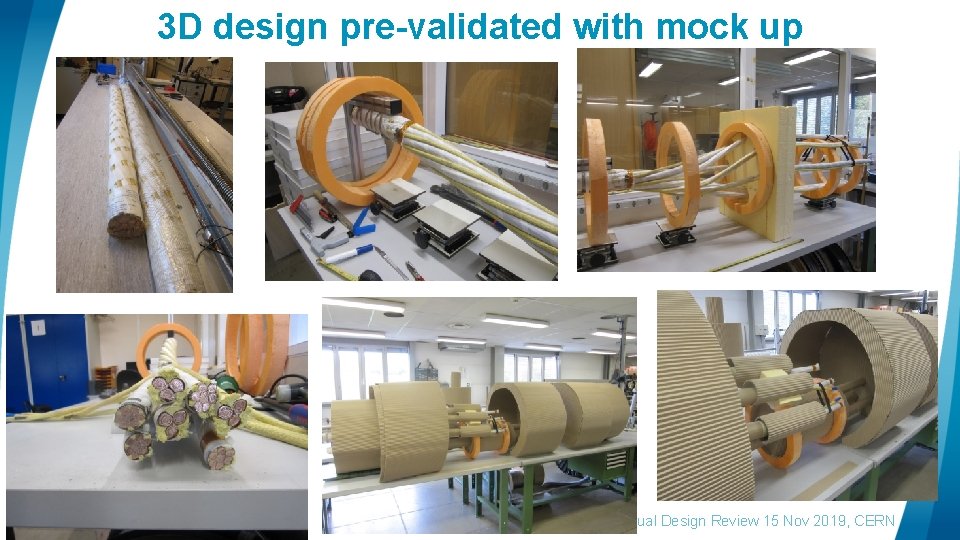
3 D design pre-validated with mock up DFH Conceptual Design Review 15 Nov 2019, CERN
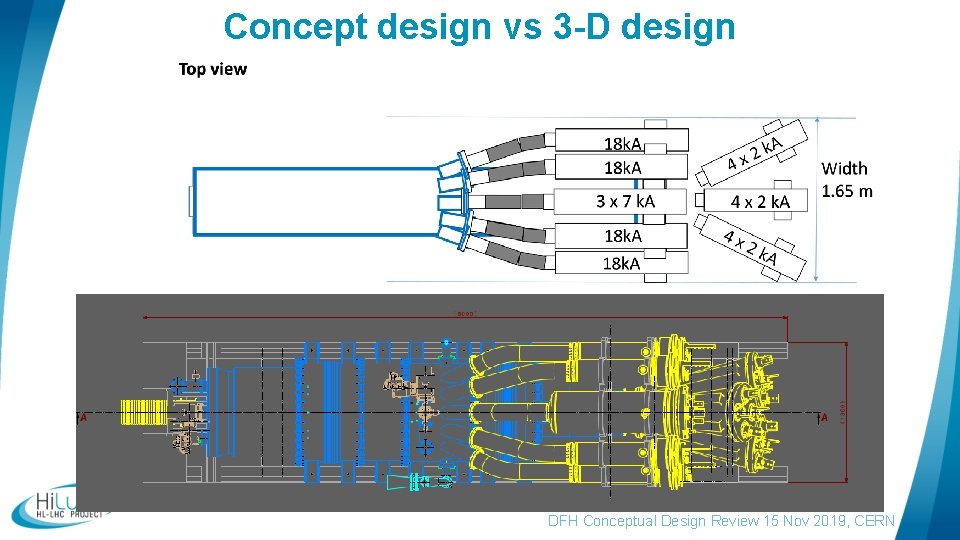
Concept design vs 3 -D design DFH Conceptual Design Review 15 Nov 2019, CERN
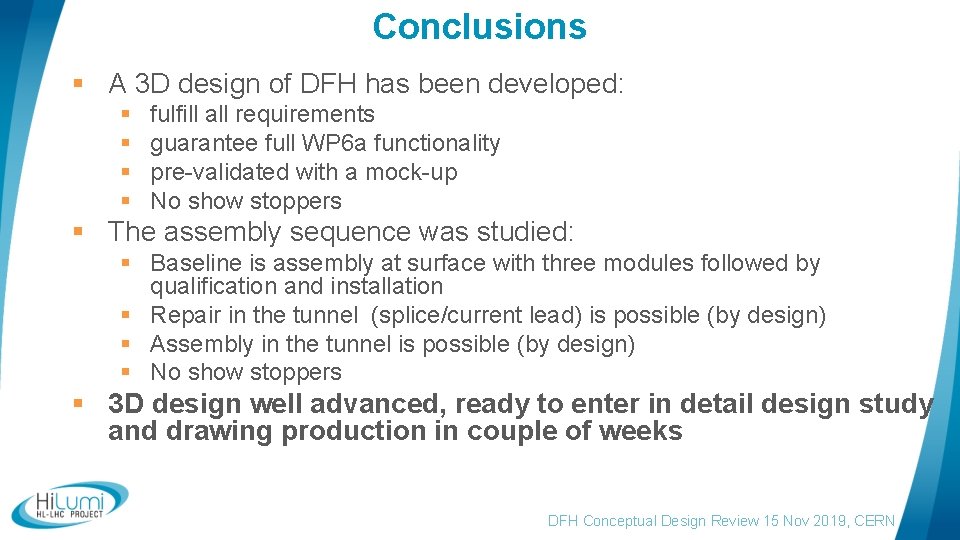
Conclusions § A 3 D design of DFH has been developed: § § fulfill all requirements guarantee full WP 6 a functionality pre-validated with a mock-up No show stoppers § The assembly sequence was studied: § Baseline is assembly at surface with three modules followed by qualification and installation § Repair in the tunnel (splice/current lead) is possible (by design) § Assembly in the tunnel is possible (by design) § No show stoppers § 3 D design well advanced, ready to enter in detail design study and drawing production in couple of weeks DFH Conceptual Design Review 15 Nov 2019, CERN
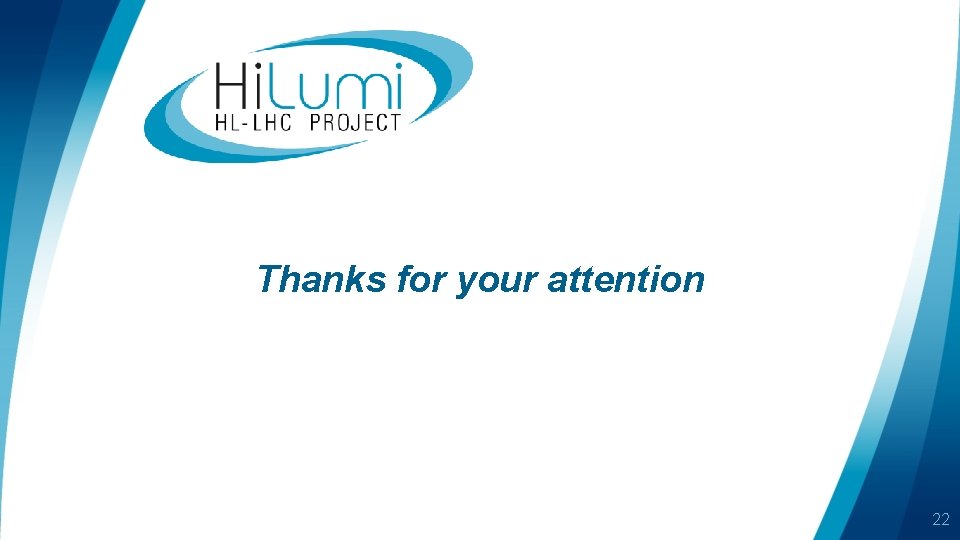
Thanks for your attention 22
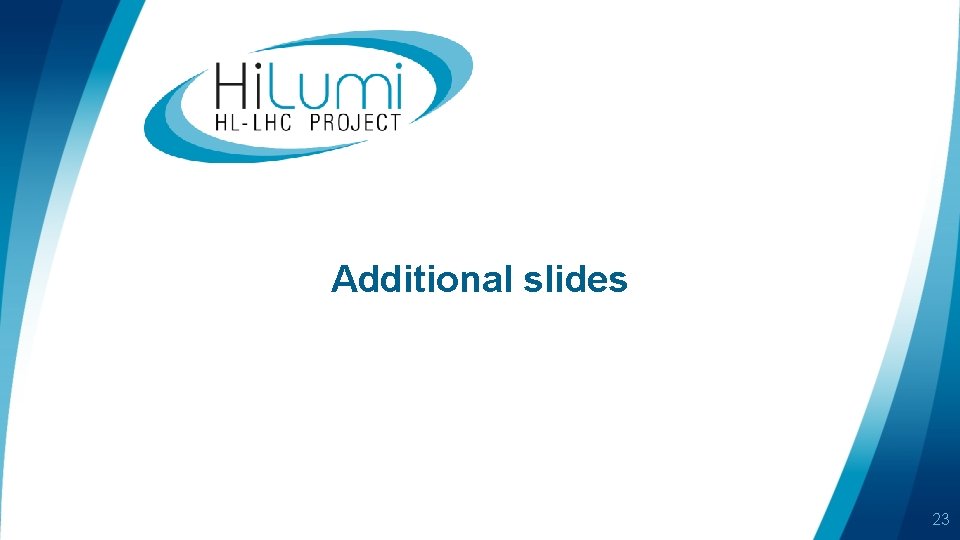
Additional slides 23
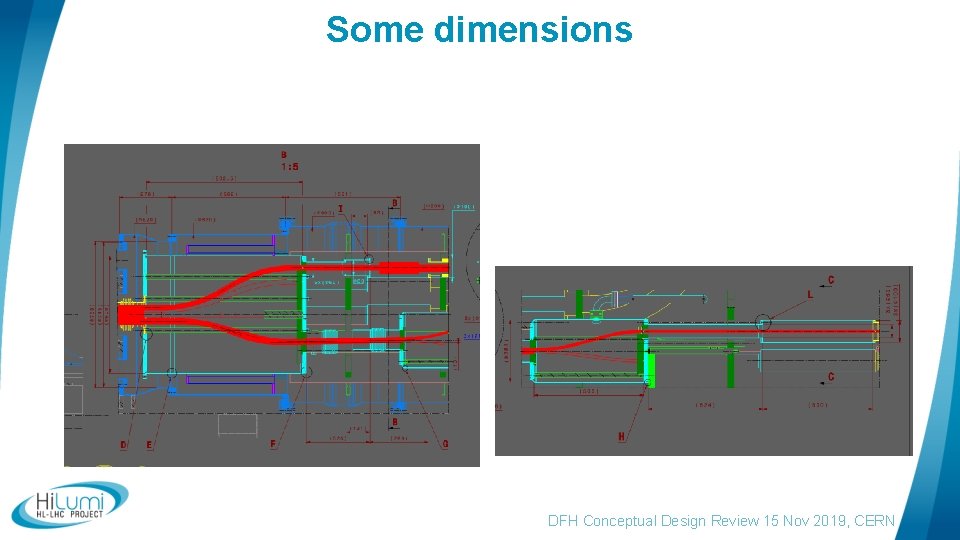
Some dimensions DFH Conceptual Design Review 15 Nov 2019, CERN
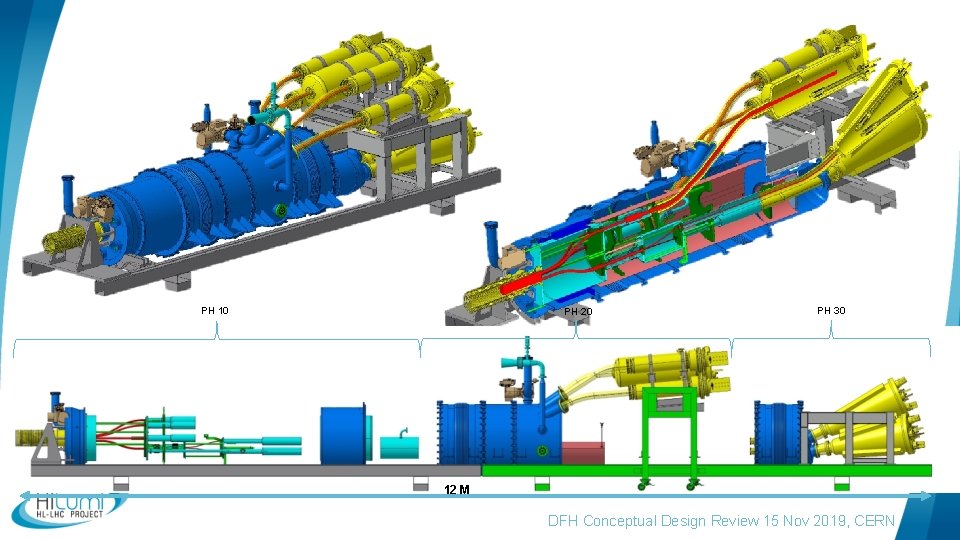
PH 10 PH 20 PH 30 12 M DFH Conceptual Design Review 15 Nov 2019, CERN
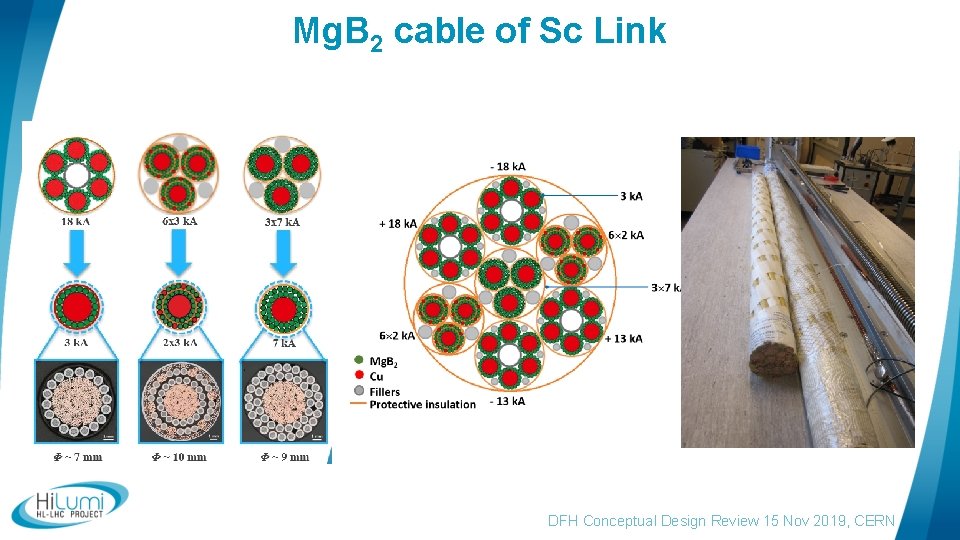
Mg. B 2 cable of Sc Link DFH Conceptual Design Review 15 Nov 2019, CERN
Dfh circuit
Conceptual design review template
Conceptual design review
Conceptual design vs physical design
Chapter 25 conceptual physics
Chapter review motion part a vocabulary review answer key
Ap gov review final exam review
Nader amin-salehi
Prisma diagram example
Narrative review vs systematic review
Outside corner weld symbol
Conceptual design examples
Contoh conceptual database design
High level conceptual data model
Conceptual design database
Conceptual database design
Bubble matching digital logic
Preliminary design review example
Formal design review
Critical design review
Critical design review
Critical design review
Critical design review
Gmp design review
Billy blue college of design reviews
Oht design
Design review example