Deactivating Decontaminating Cleaning and Disinfecting Overview Training DATE
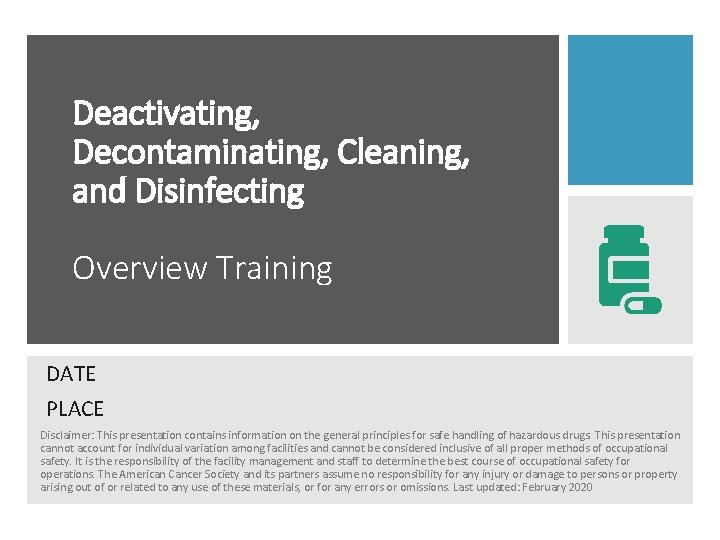
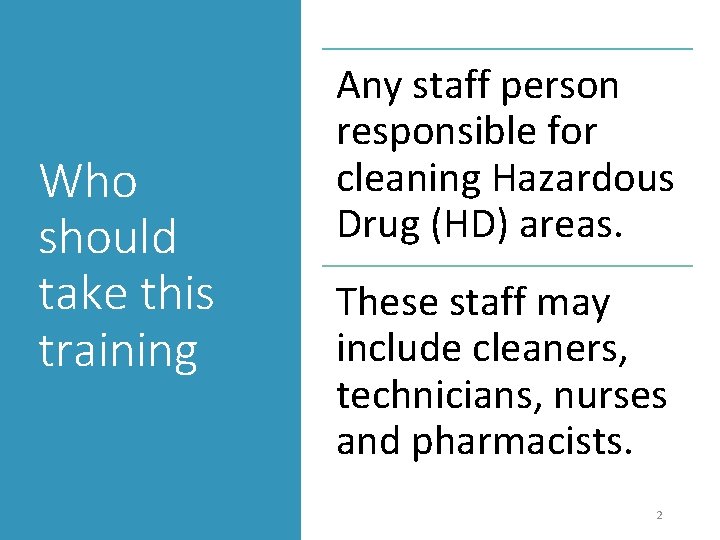
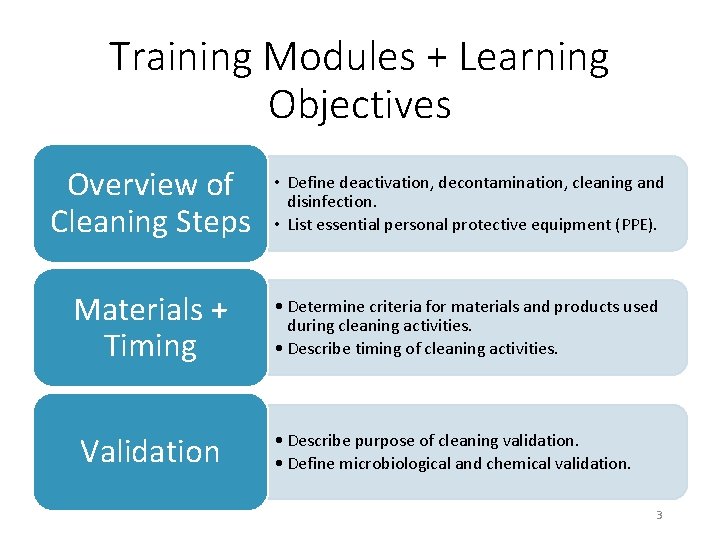
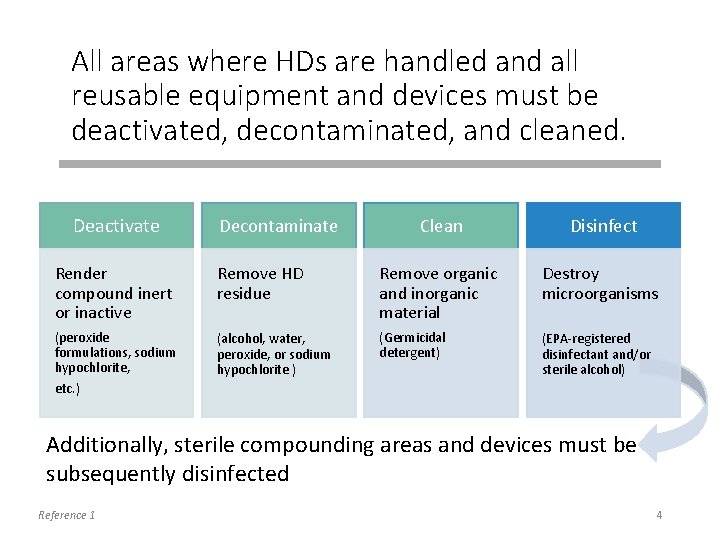
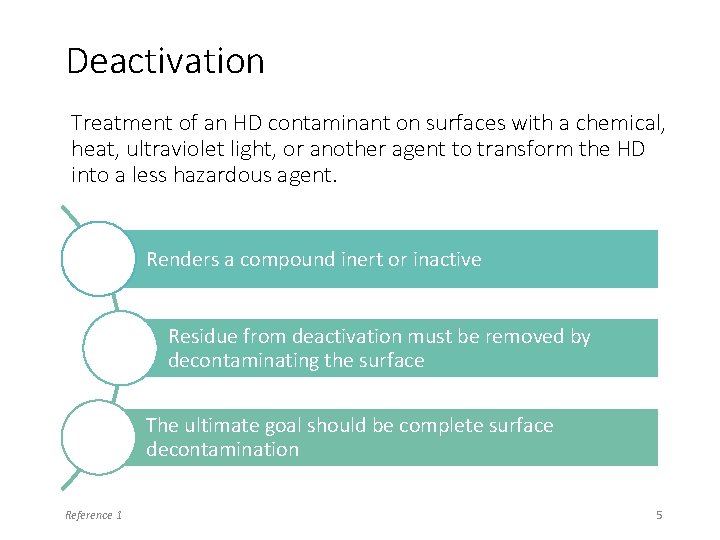
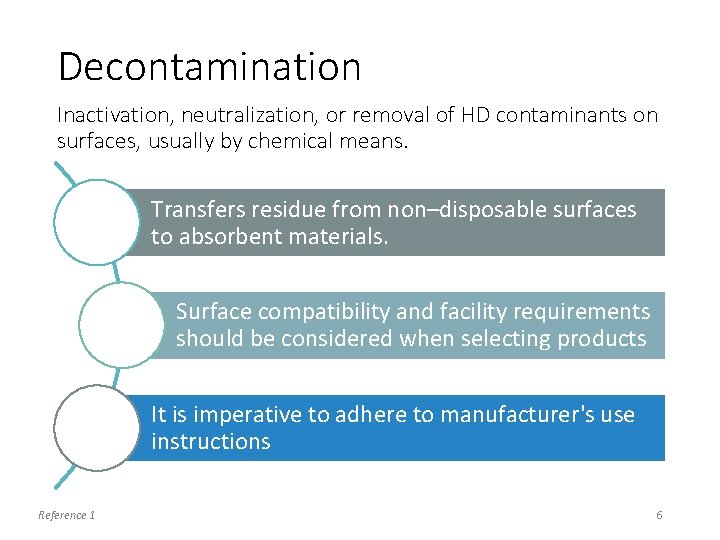
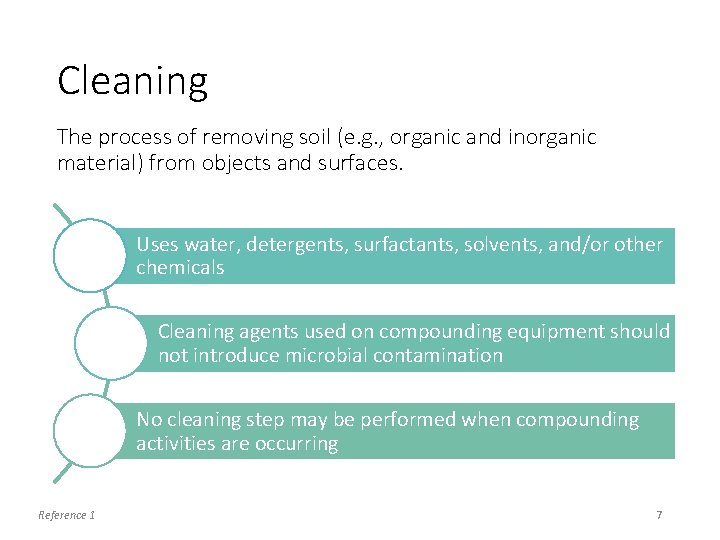
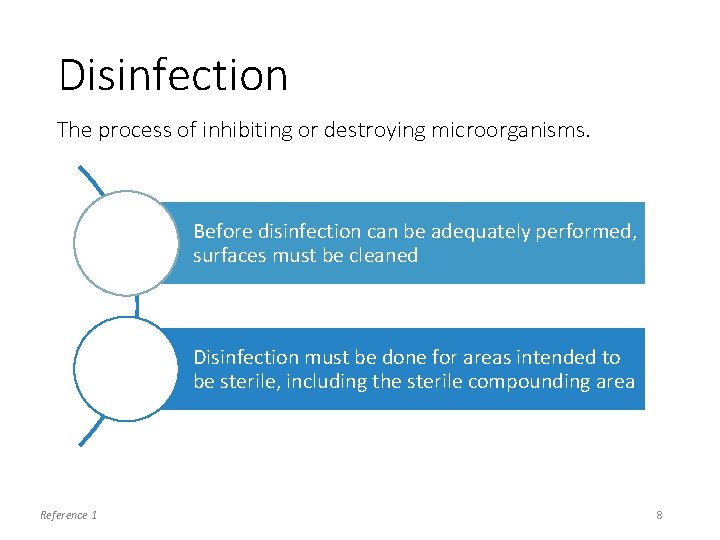
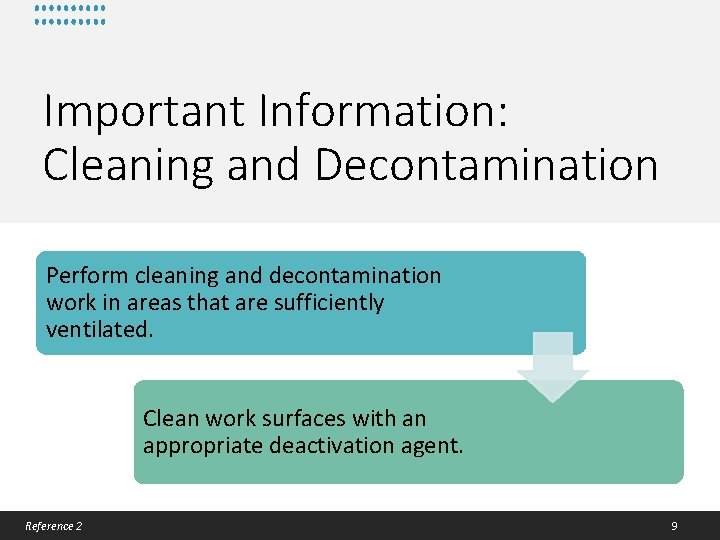
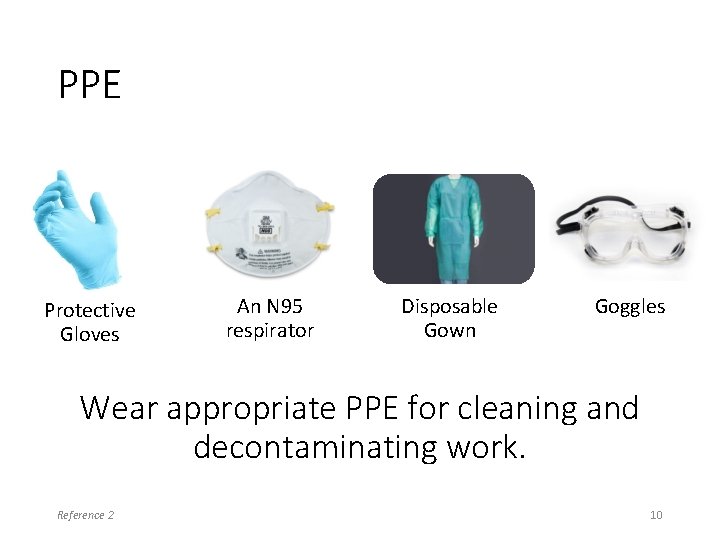
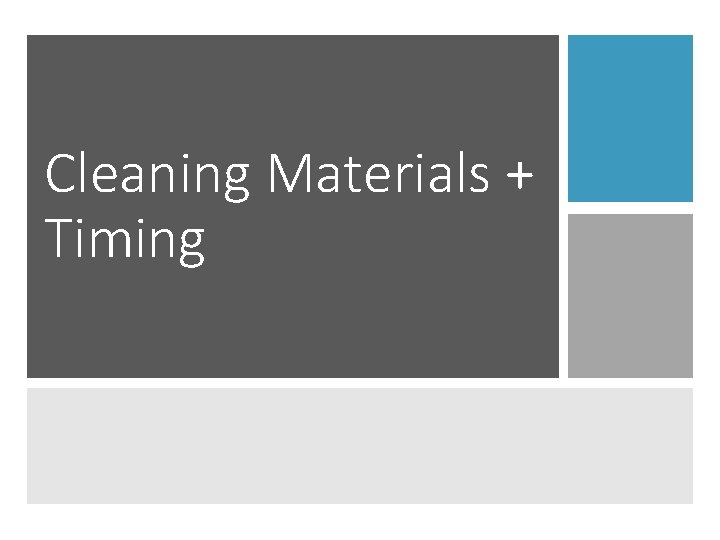
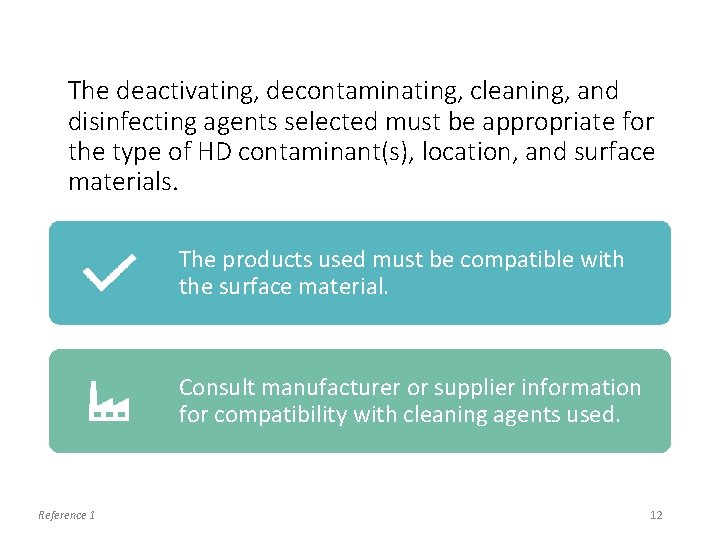
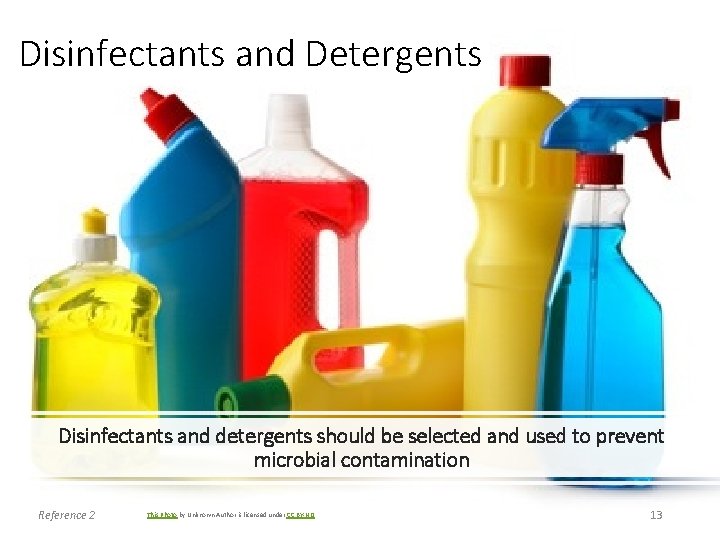
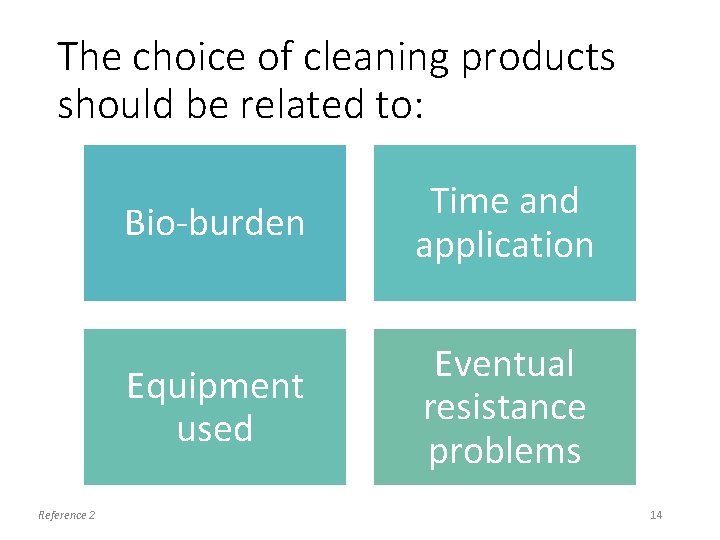
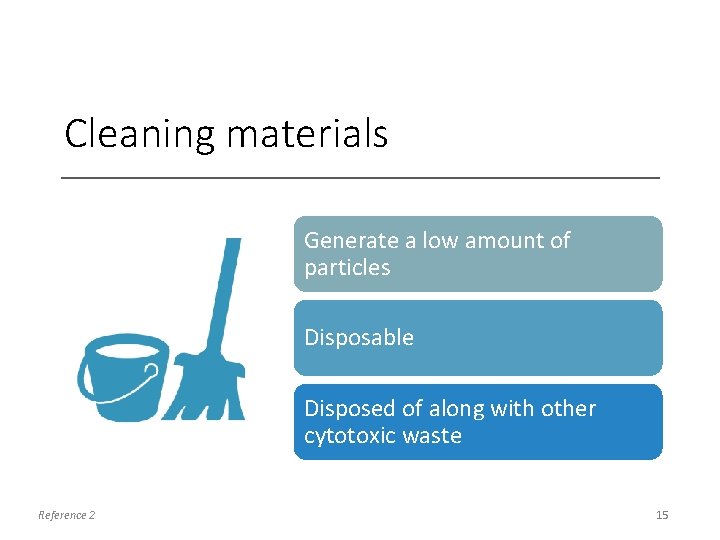
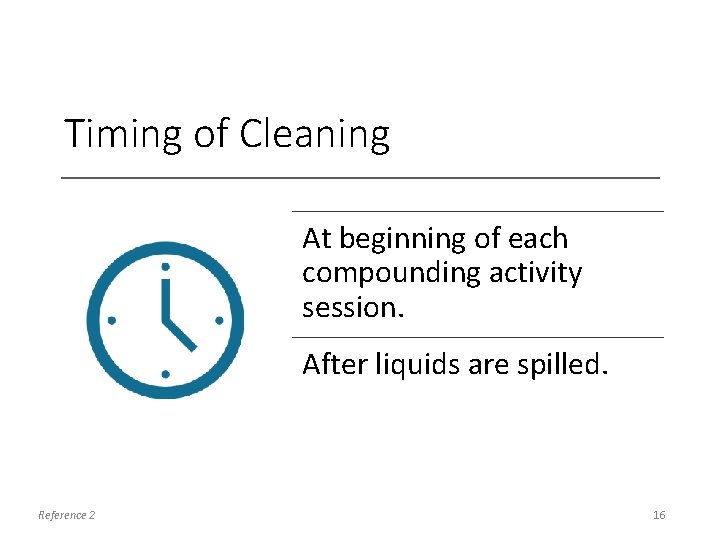
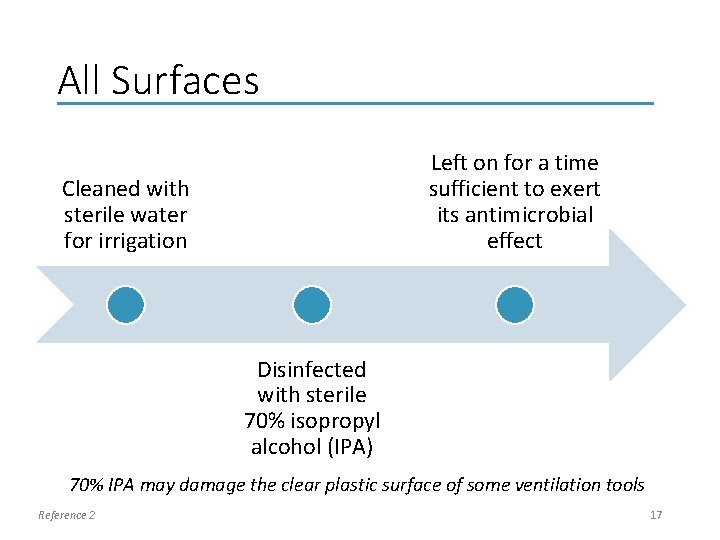
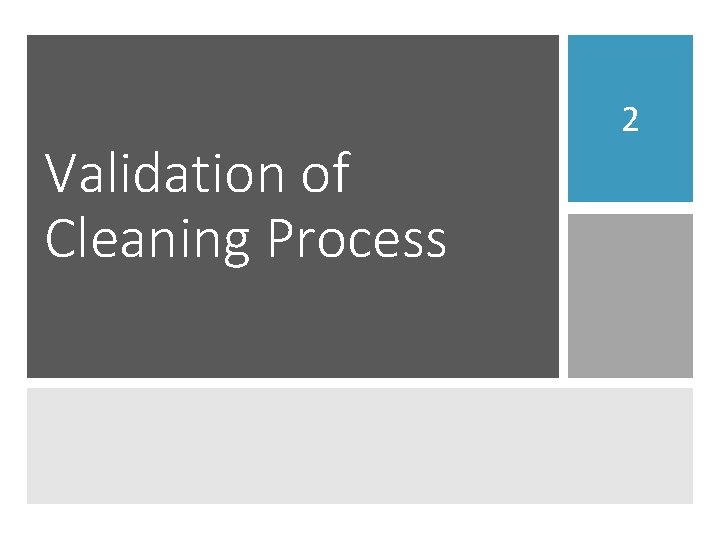
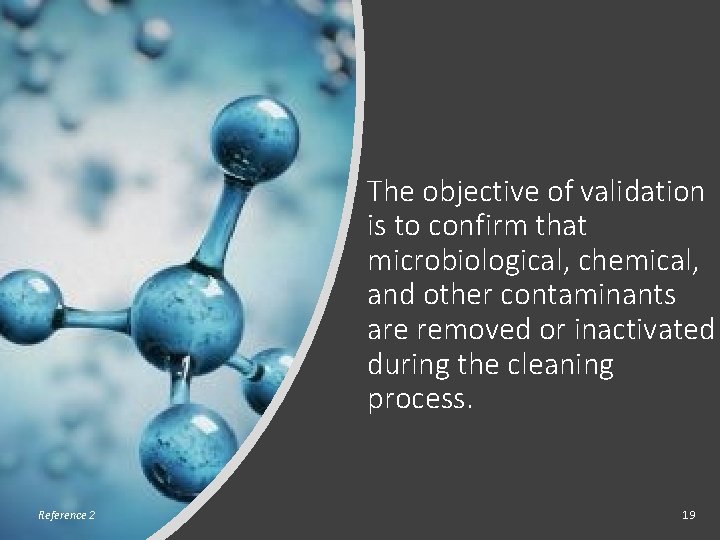
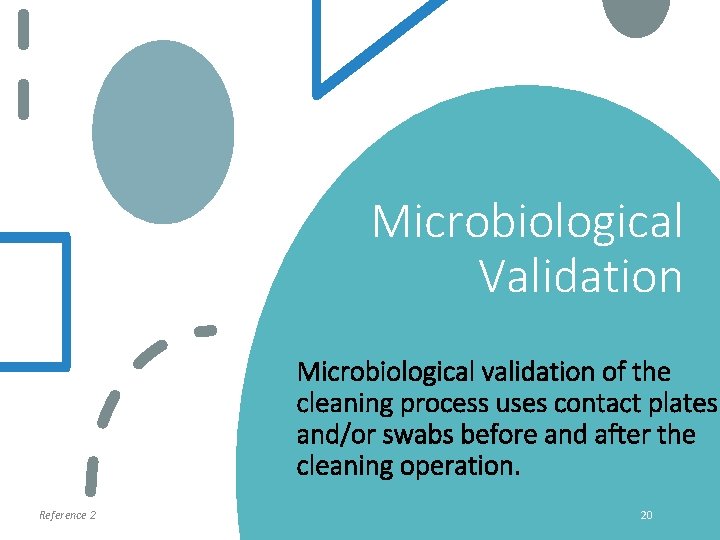
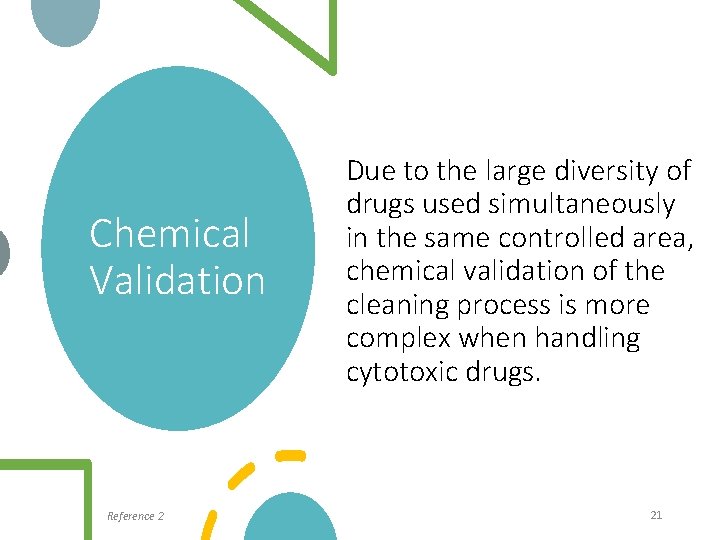
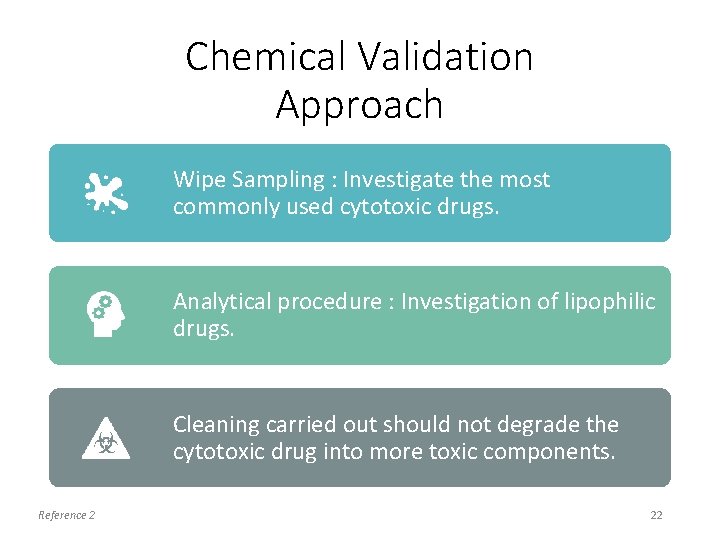
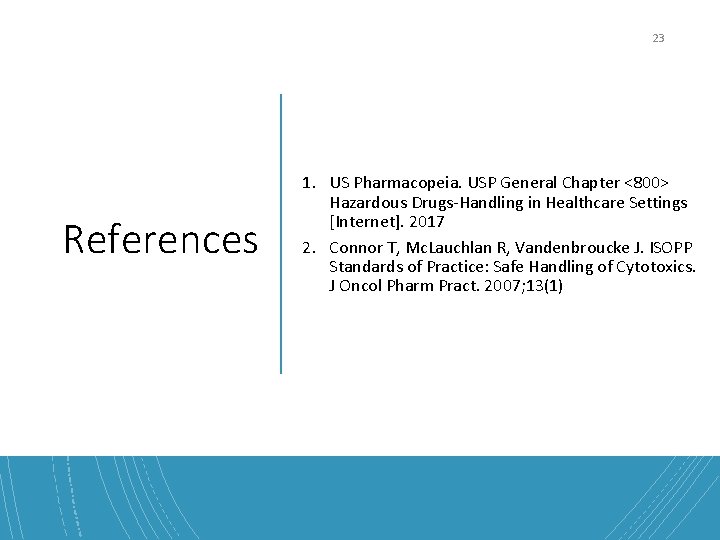
- Slides: 23
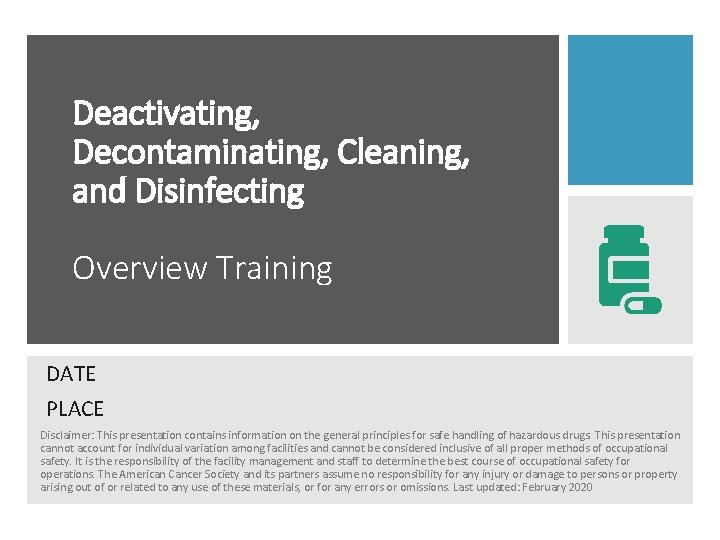
Deactivating, Decontaminating, Cleaning, and Disinfecting Overview Training DATE PLACE Disclaimer: This presentation contains information on the general principles for safe handling of hazardous drugs. This presentation cannot account for individual variation among facilities and cannot be considered inclusive of all proper methods of occupational safety. It is the responsibility of the facility management and staff to determine the best course of occupational safety for operations. The American Cancer Society and its partners assume no responsibility for any injury or damage to persons or property arising out of or related to any use of these materials, or for any errors or omissions. Last updated: February 2020
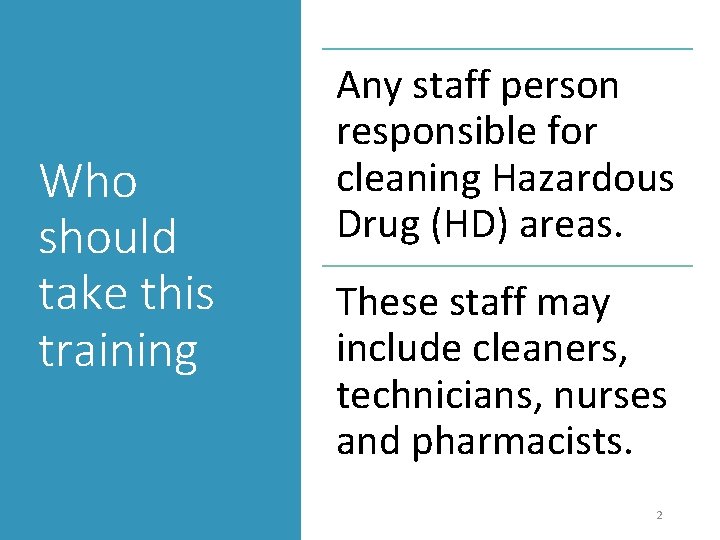
Who should take this training Any staff person responsible for cleaning Hazardous Drug (HD) areas. These staff may include cleaners, technicians, nurses and pharmacists. 2
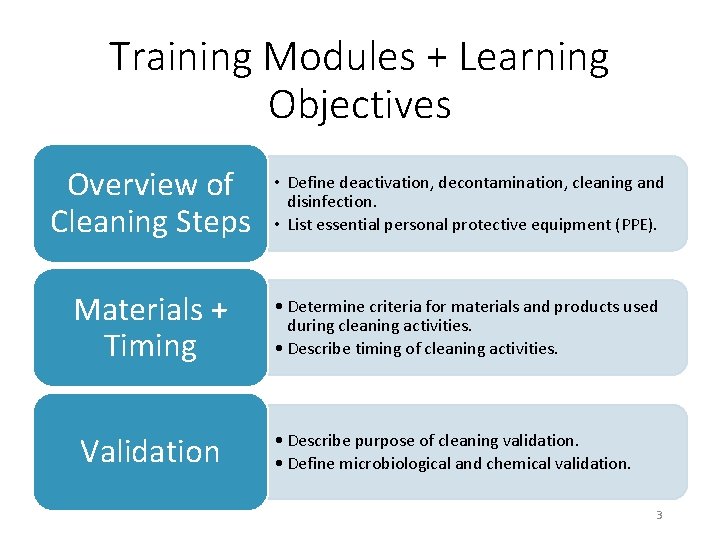
Training Modules + Learning Objectives Overview of Cleaning Steps • Define deactivation, decontamination, cleaning and disinfection. • List essential personal protective equipment (PPE). Materials + Timing • Determine criteria for materials and products used during cleaning activities. • Describe timing of cleaning activities. Validation • Describe purpose of cleaning validation. • Define microbiological and chemical validation. 3
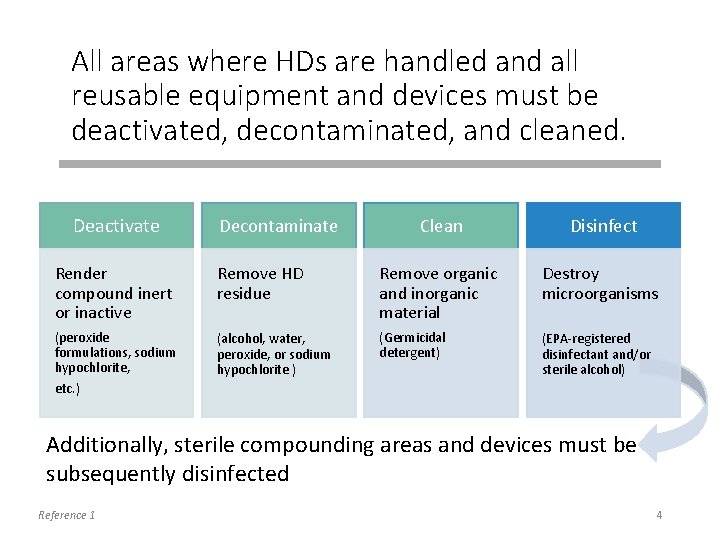
All areas where HDs are handled and all reusable equipment and devices must be deactivated, decontaminated, and cleaned. Deactivate Decontaminate Clean Disinfect Render compound inert or inactive Remove HD residue Remove organic and inorganic material Destroy microorganisms (peroxide formulations, sodium hypochlorite, (alcohol, water, peroxide, or sodium hypochlorite ) (Germicidal detergent) (EPA-registered disinfectant and/or sterile alcohol) etc. ) Additionally, sterile compounding areas and devices must be subsequently disinfected Reference 1 4
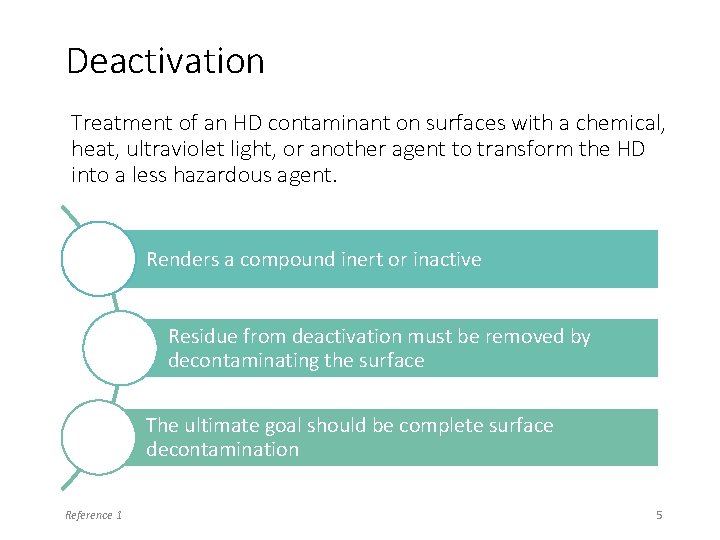
Deactivation Treatment of an HD contaminant on surfaces with a chemical, heat, ultraviolet light, or another agent to transform the HD into a less hazardous agent. Renders a compound inert or inactive Residue from deactivation must be removed by decontaminating the surface The ultimate goal should be complete surface decontamination Reference 1 5
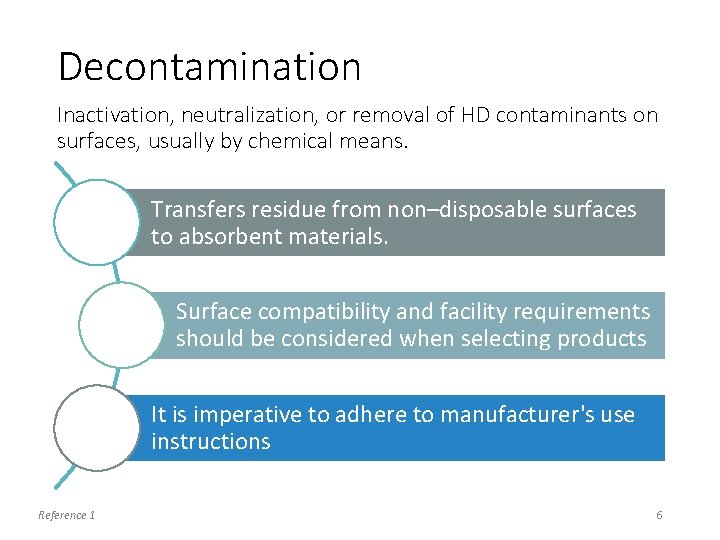
Decontamination Inactivation, neutralization, or removal of HD contaminants on surfaces, usually by chemical means. Transfers residue from non–disposable surfaces to absorbent materials. Surface compatibility and facility requirements should be considered when selecting products It is imperative to adhere to manufacturer's use instructions Reference 1 6
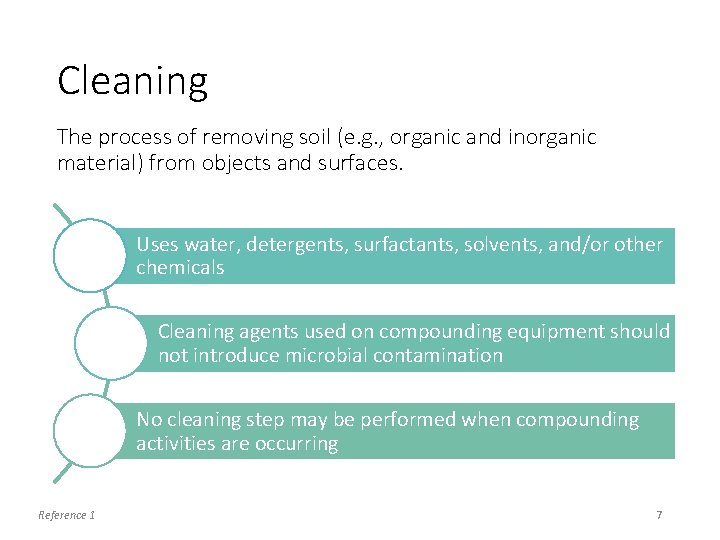
Cleaning The process of removing soil (e. g. , organic and inorganic material) from objects and surfaces. Uses water, detergents, surfactants, solvents, and/or other chemicals Cleaning agents used on compounding equipment should not introduce microbial contamination No cleaning step may be performed when compounding activities are occurring Reference 1 7
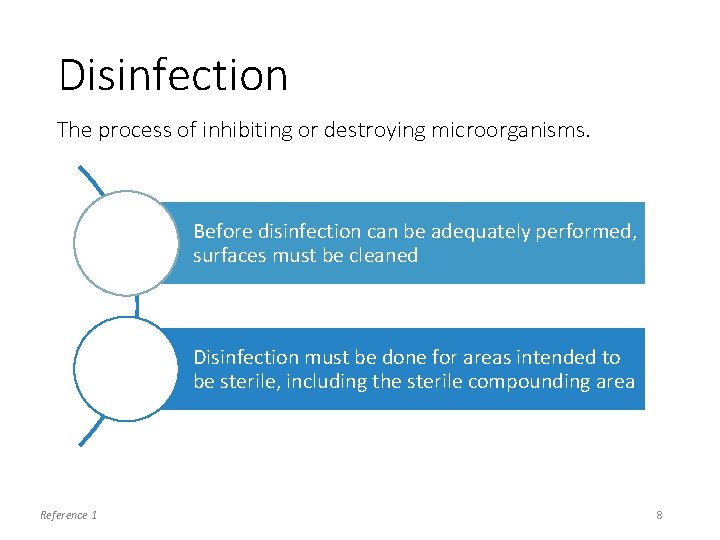
Disinfection The process of inhibiting or destroying microorganisms. Before disinfection can be adequately performed, surfaces must be cleaned Disinfection must be done for areas intended to be sterile, including the sterile compounding area Reference 1 8
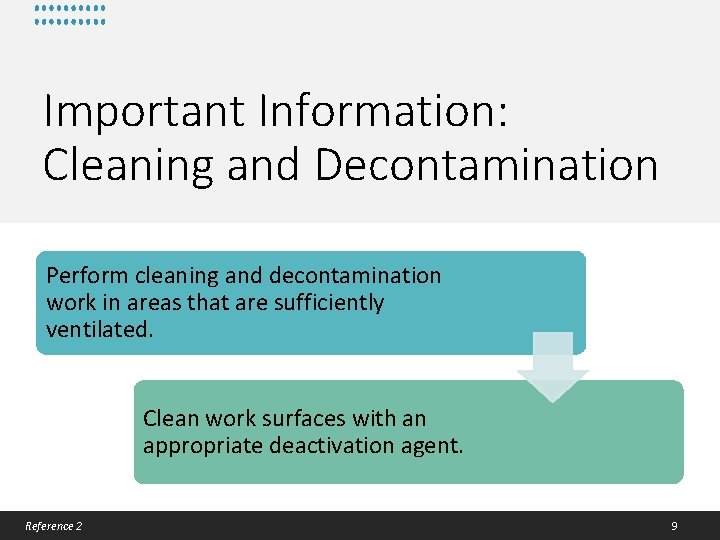
Important Information: Cleaning and Decontamination Perform cleaning and decontamination work in areas that are sufficiently ventilated. Clean work surfaces with an appropriate deactivation agent. Reference 2 9
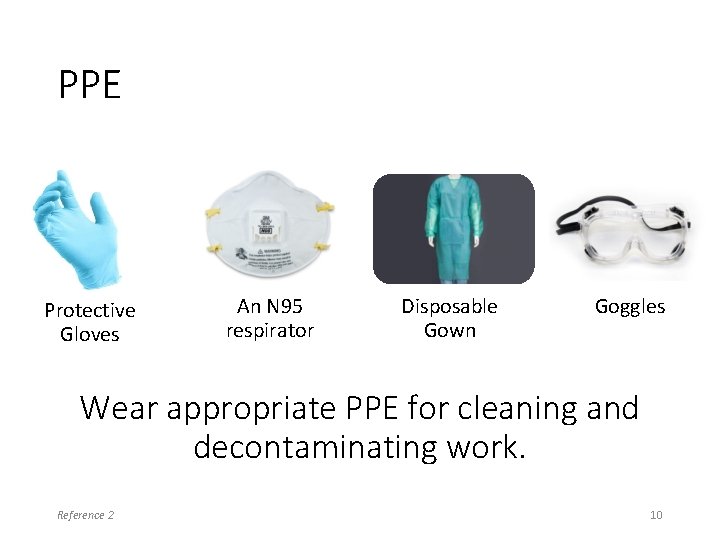
PPE Protective Gloves An N 95 respirator Disposable Gown Goggles Wear appropriate PPE for cleaning and decontaminating work. Reference 2 10
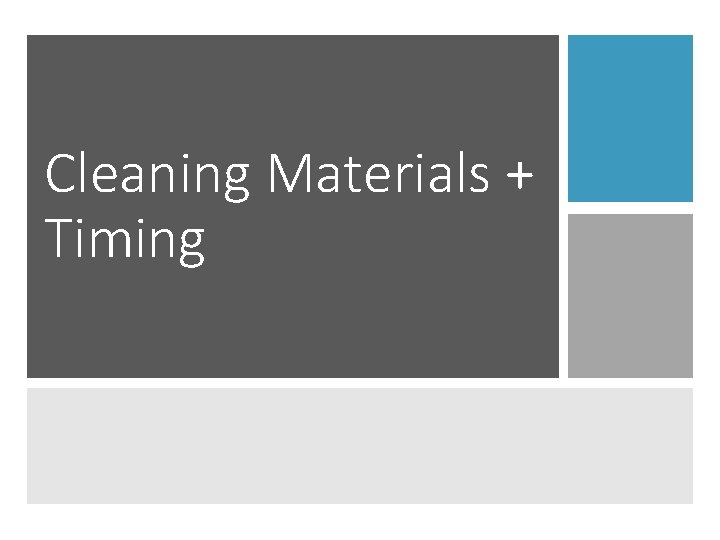
Cleaning Materials + Timing
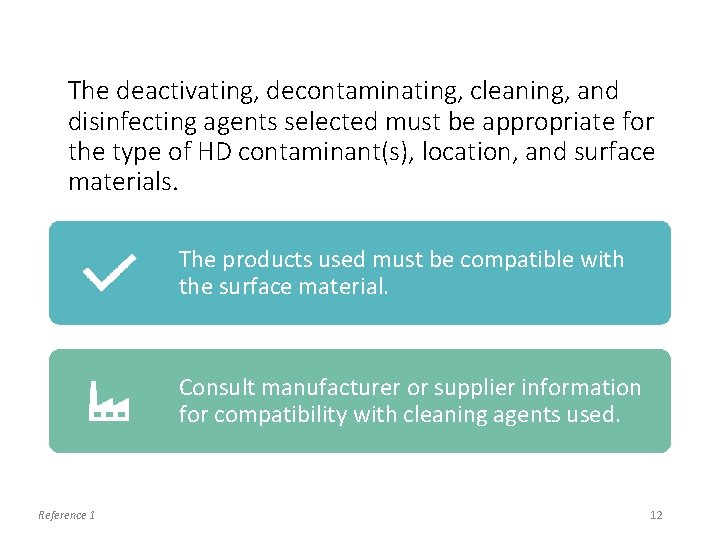
The deactivating, decontaminating, cleaning, and disinfecting agents selected must be appropriate for the type of HD contaminant(s), location, and surface materials. The products used must be compatible with the surface material. Consult manufacturer or supplier information for compatibility with cleaning agents used. Reference 1 12
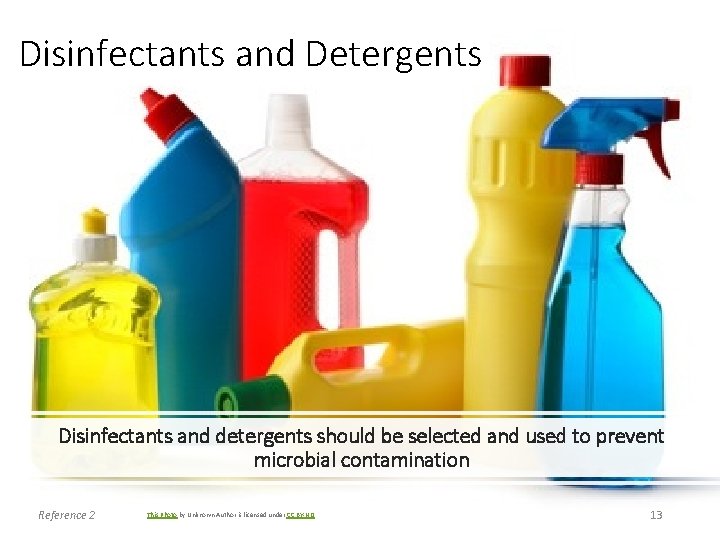
Disinfectants and Detergents Disinfectants and detergents should be selected and used to prevent microbial contamination Reference 2 This Photo by Unknown Author is licensed under CC BY-ND 13 13
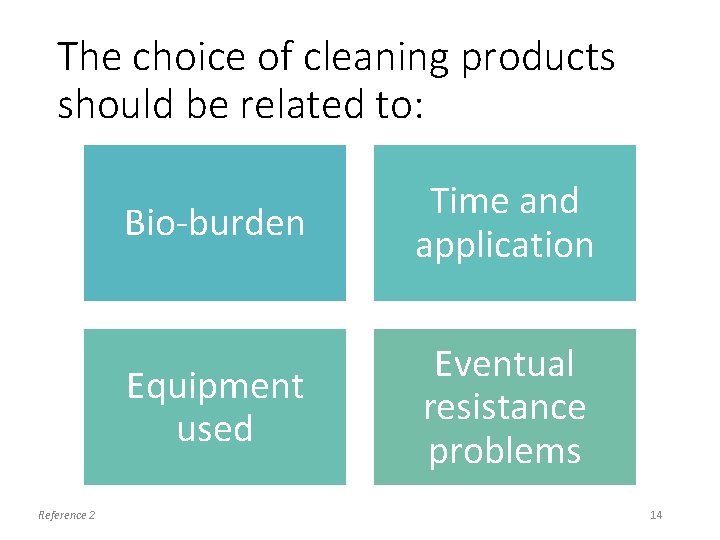
The choice of cleaning products should be related to: Reference 2 Bio-burden Time and application Equipment used Eventual resistance problems 14
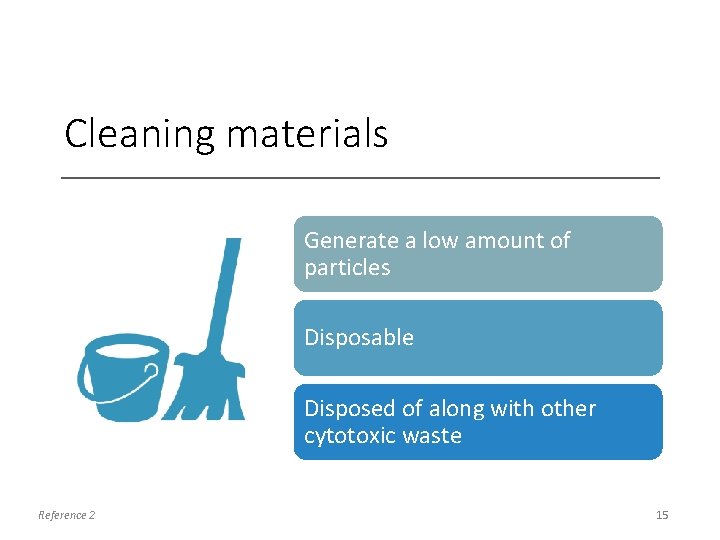
Cleaning materials Generate a low amount of particles Disposable Disposed of along with other cytotoxic waste Reference 2 15
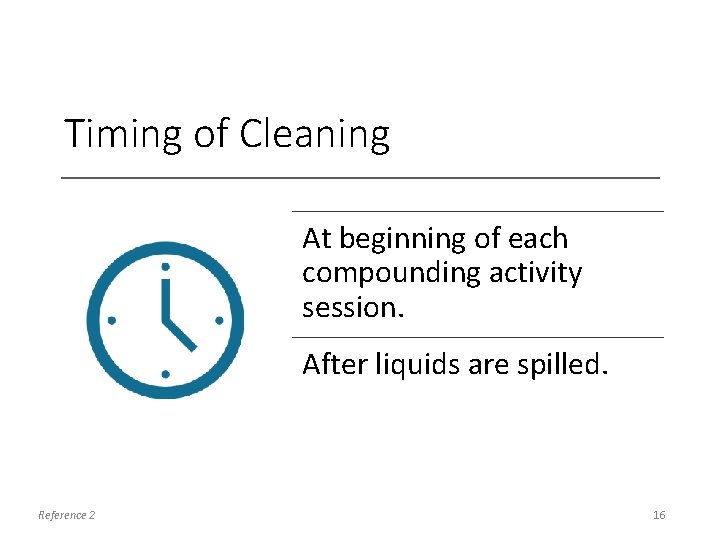
Timing of Cleaning At beginning of each compounding activity session. After liquids are spilled. Reference 2 16
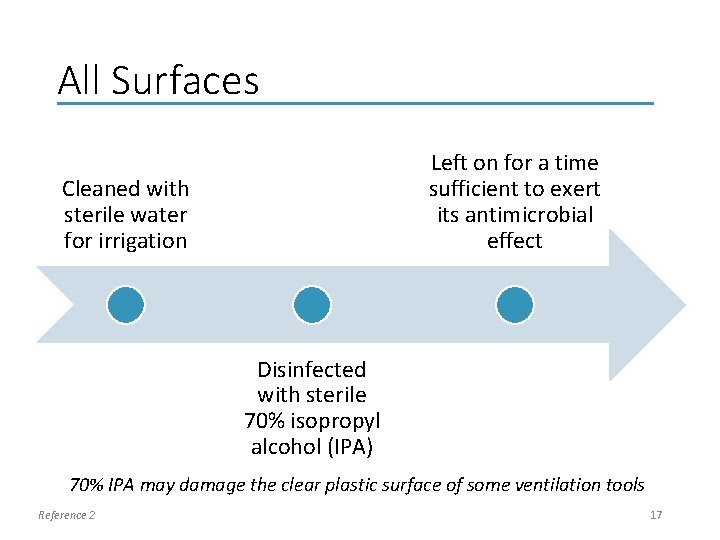
All Surfaces Left on for a time sufficient to exert its antimicrobial effect Cleaned with sterile water for irrigation Disinfected with sterile 70% isopropyl alcohol (IPA) 70% IPA may damage the clear plastic surface of some ventilation tools Reference 2 17
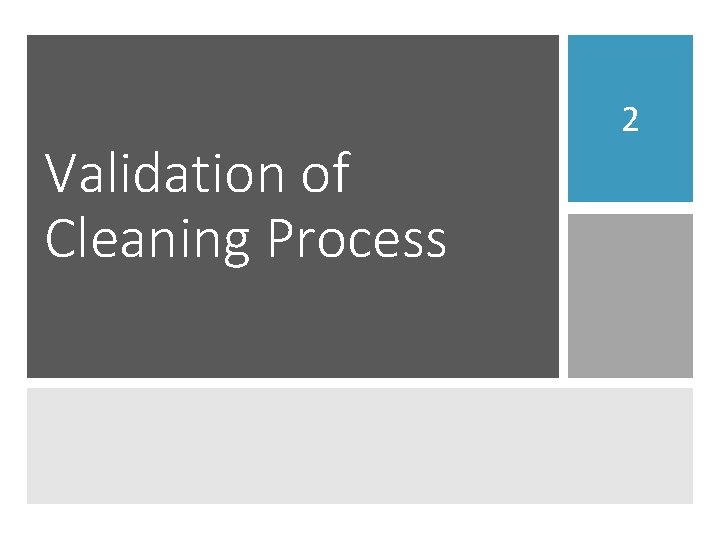
Validation of Cleaning Process 2
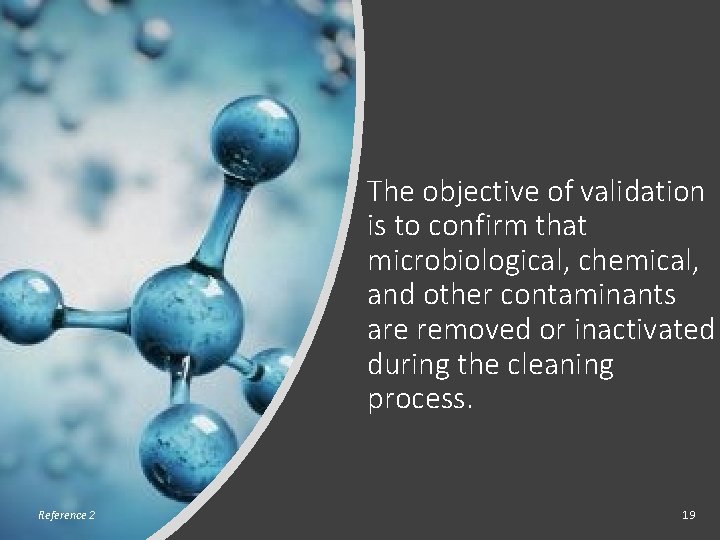
The objective of validation is to confirm that microbiological, chemical, and other contaminants are removed or inactivated during the cleaning process. Reference 2 19
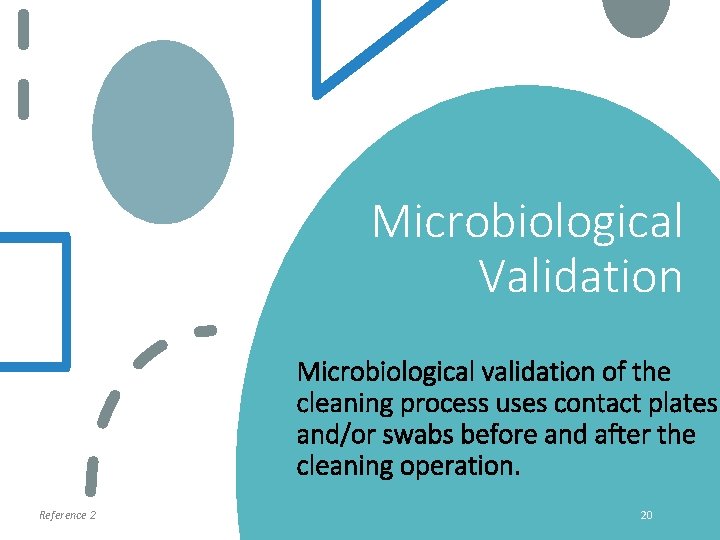
Microbiological Validation Microbiological validation of the cleaning process uses contact plates and/or swabs before and after the cleaning operation. Reference 2 20
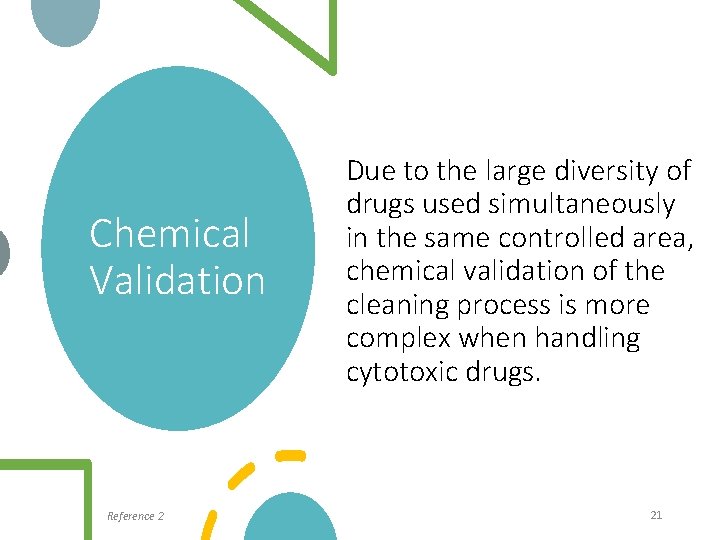
Chemical Validation Reference 2 Due to the large diversity of drugs used simultaneously in the same controlled area, chemical validation of the cleaning process is more complex when handling cytotoxic drugs. 21
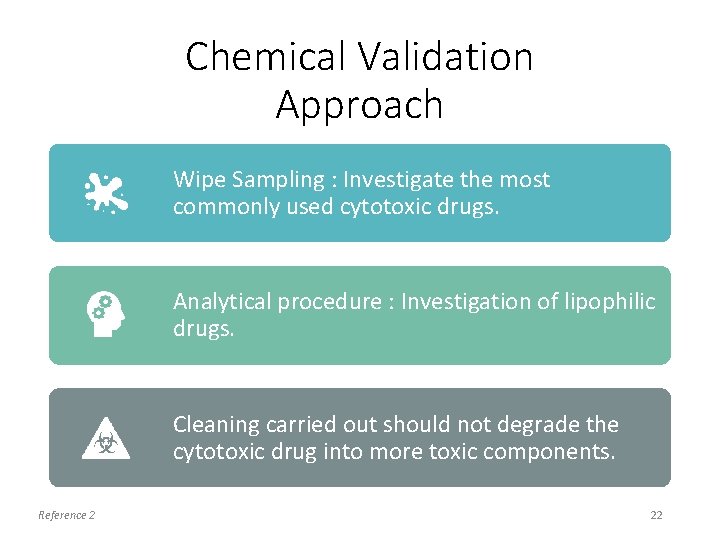
Chemical Validation Approach Wipe Sampling : Investigate the most commonly used cytotoxic drugs. Analytical procedure : Investigation of lipophilic drugs. Cleaning carried out should not degrade the cytotoxic drug into more toxic components. Reference 2 22
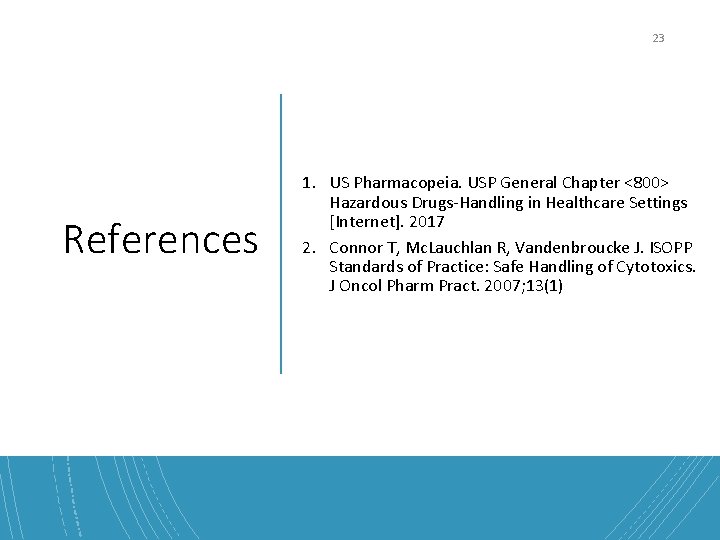
23 References 1. US Pharmacopeia. USP General Chapter <800> Hazardous Drugs-Handling in Healthcare Settings [Internet]. 2017 2. Connor T, Mc. Lauchlan R, Vandenbroucke J. ISOPP Standards of Practice: Safe Handling of Cytotoxics. J Oncol Pharm Pract. 2007; 13(1)
Deactivating group
Ester activating or deactivating
Data quality and data cleaning an overview
Data quality and data cleaning an overview
Data quality and data cleaning an overview
Record date ex dividend date
Record date for dividend
Restroom cleaning training
Clean public areas facilities and equipment
Things we use to clean utensils
What is the definition of sanitizing servsafe
Data integration in data preprocessing
Cleaning and sanitation manual for breweries
What the things you in cleaning kitchen premises
Cleaning the tides of san diego and tijuana
Tru count planter clutches
Power tool cleaning
Standard cost model
Sedimclean
What are three types of hazards that make food unsafe
Pengolahan data editing, coding processing cleaning
Pt among kampung rambutan
Hospital patient room cleaning procedures
Room cleaning procedure