Compact Integration of Aerodynamic Control and Thrust Vector
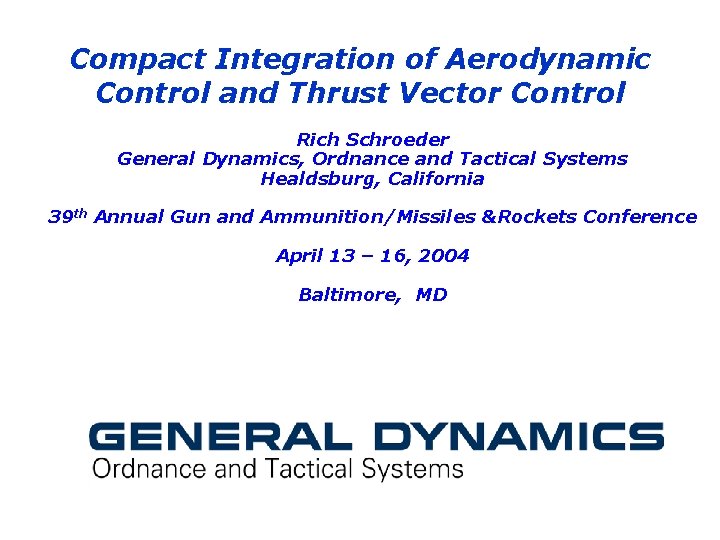
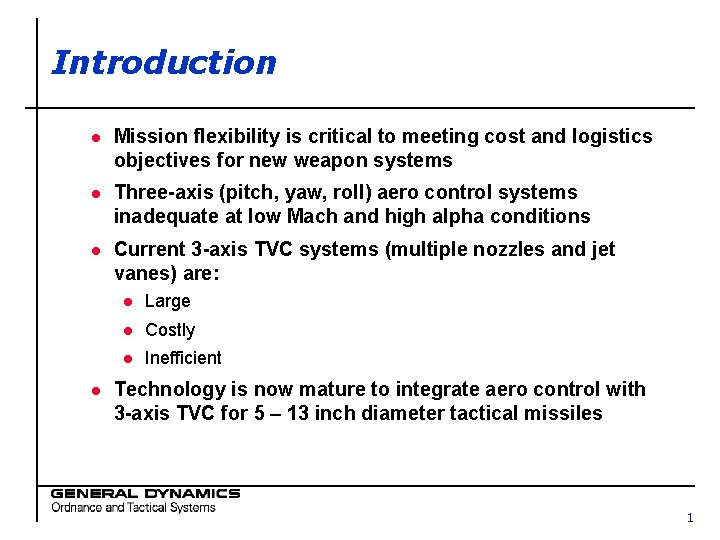
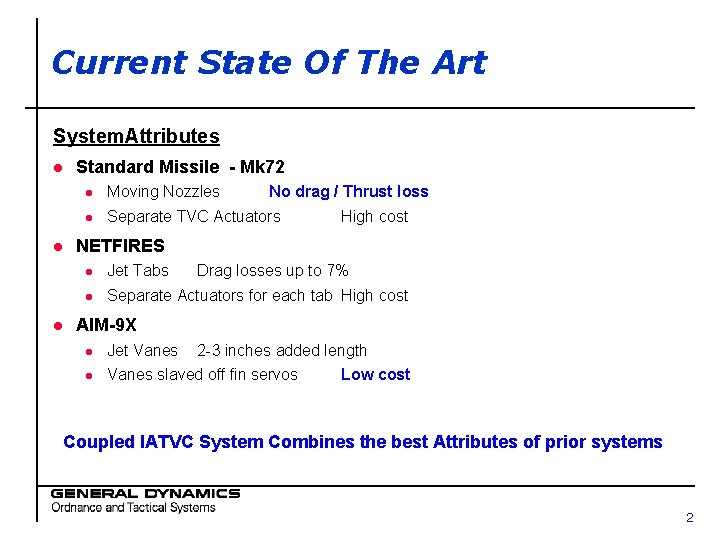
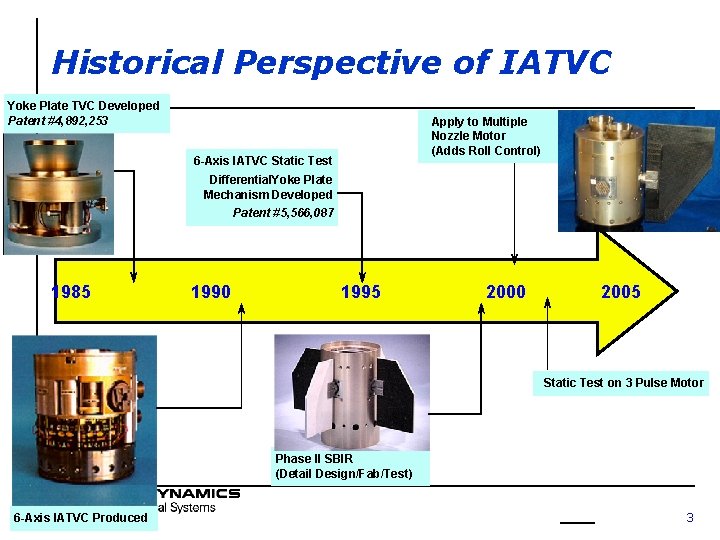
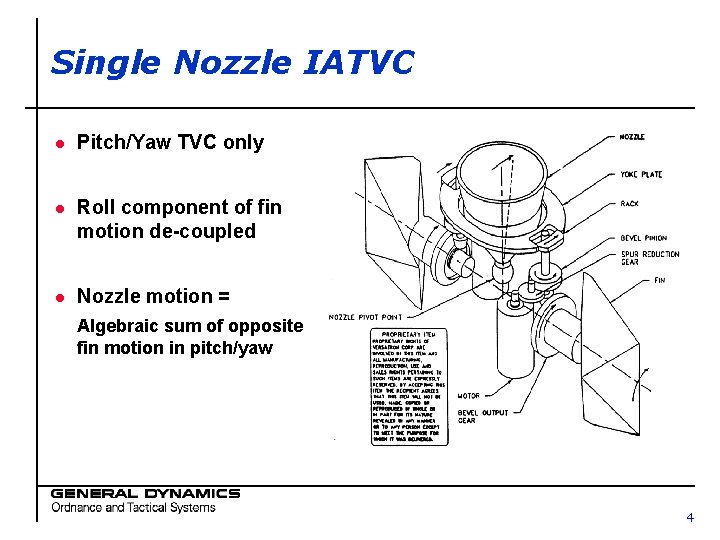
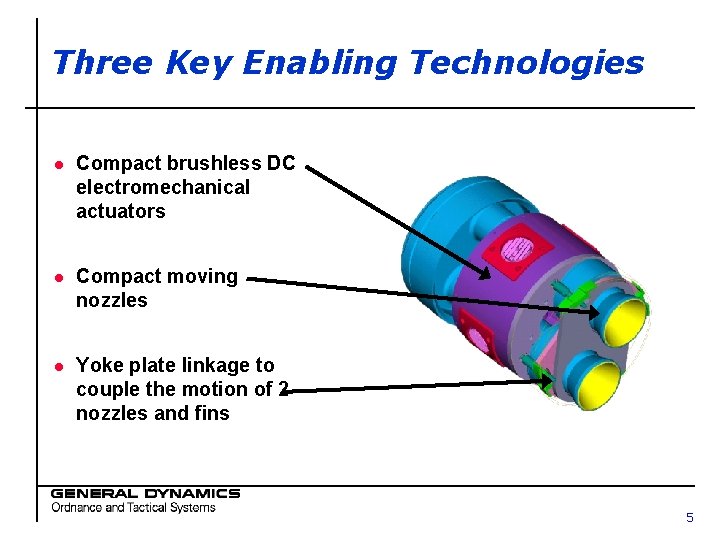
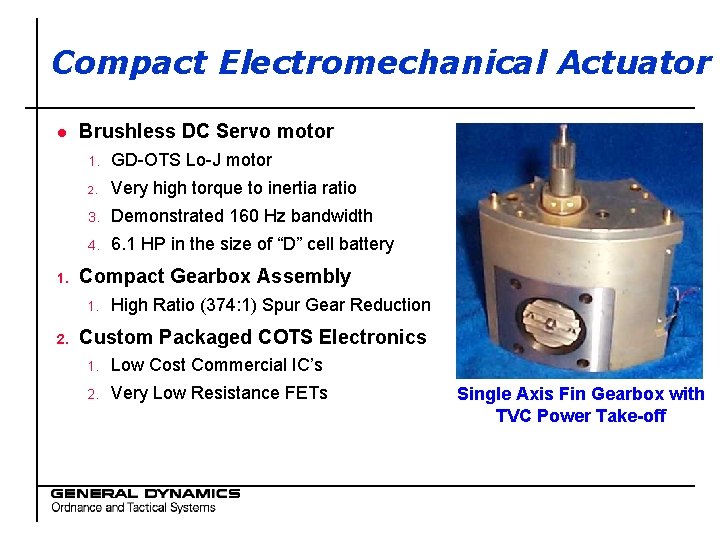
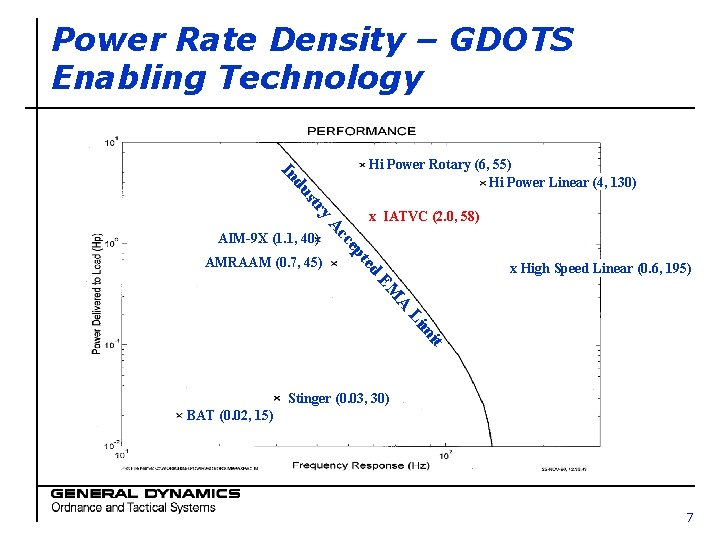
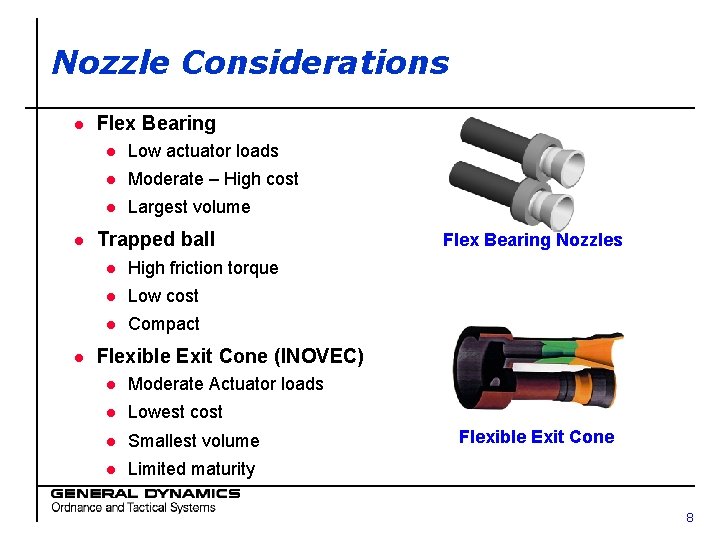
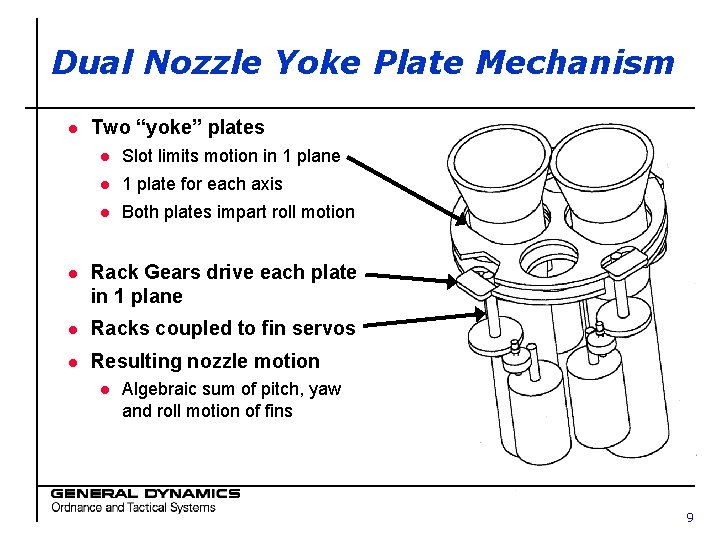
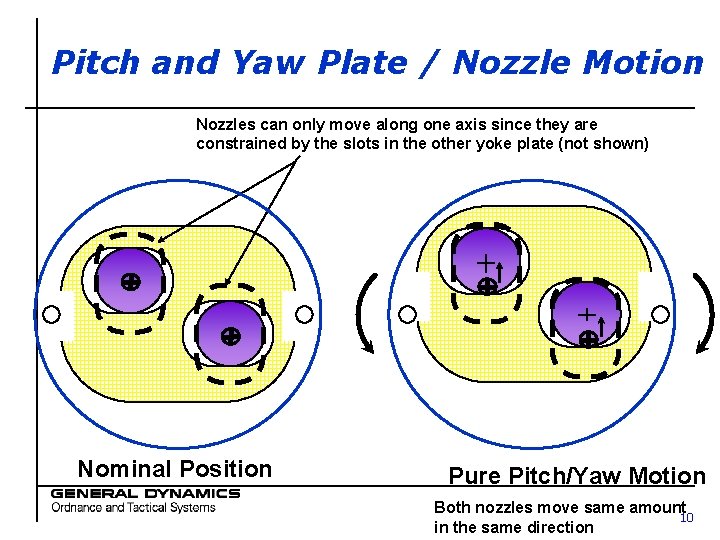
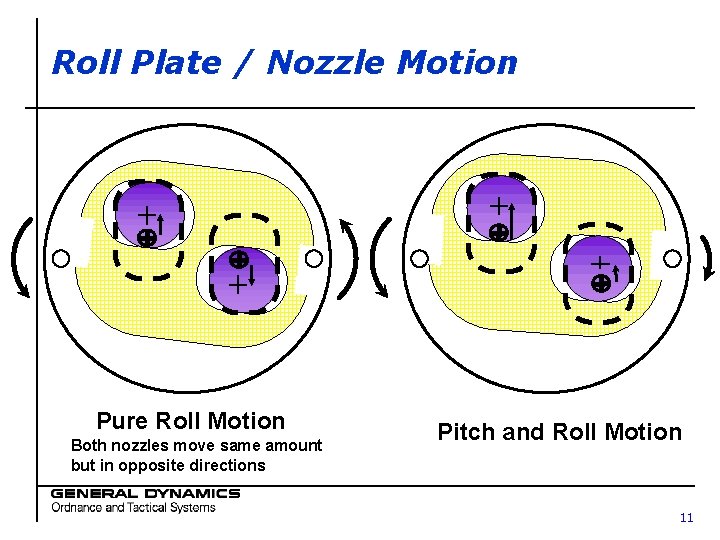
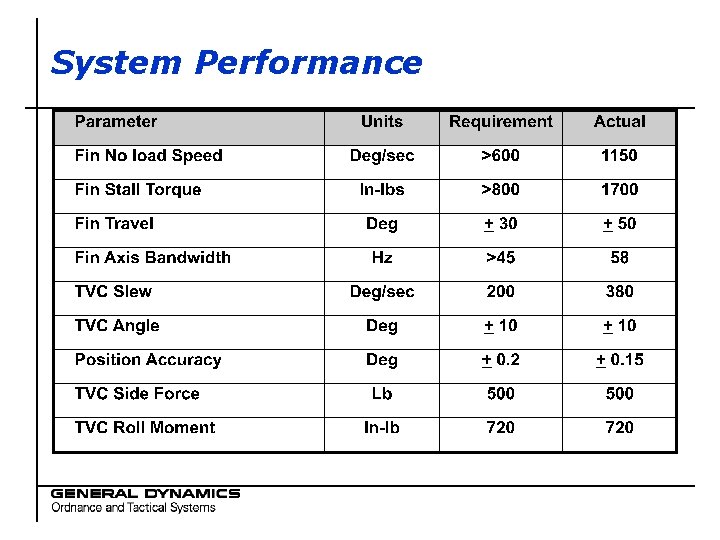
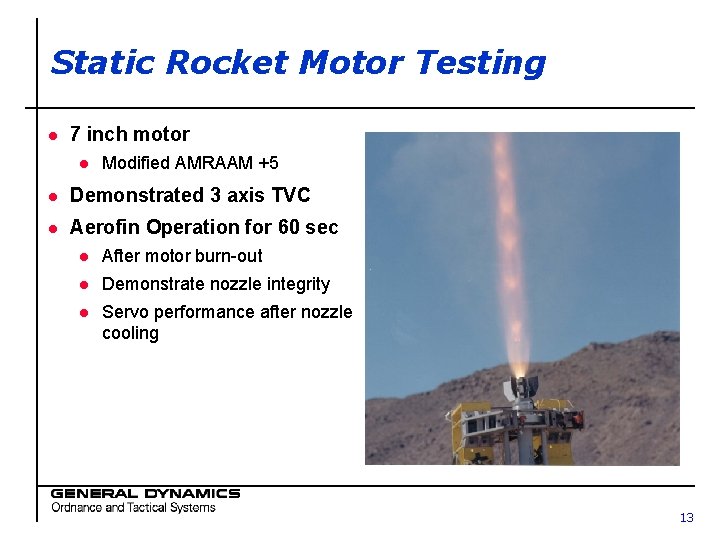
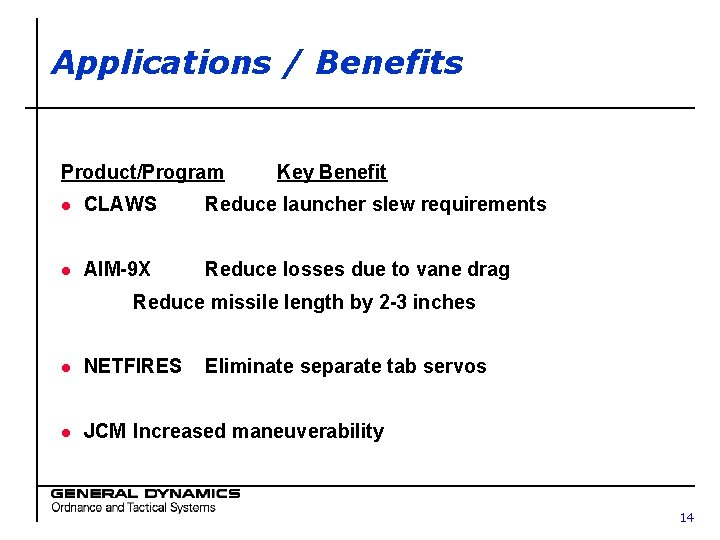
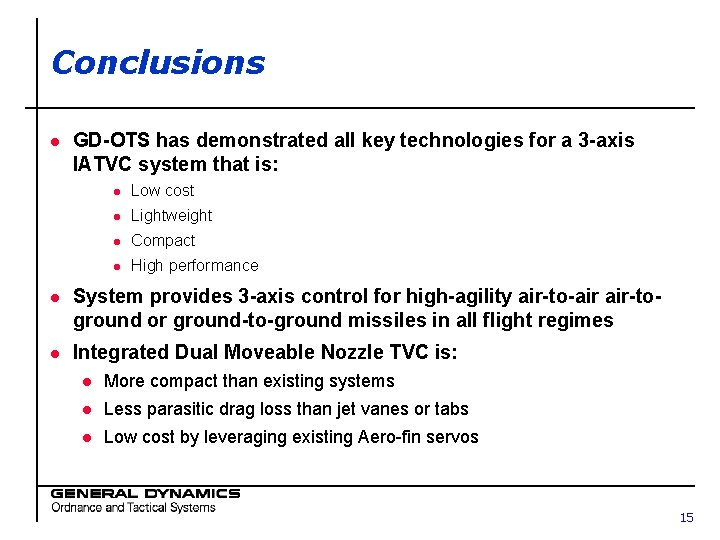
- Slides: 16
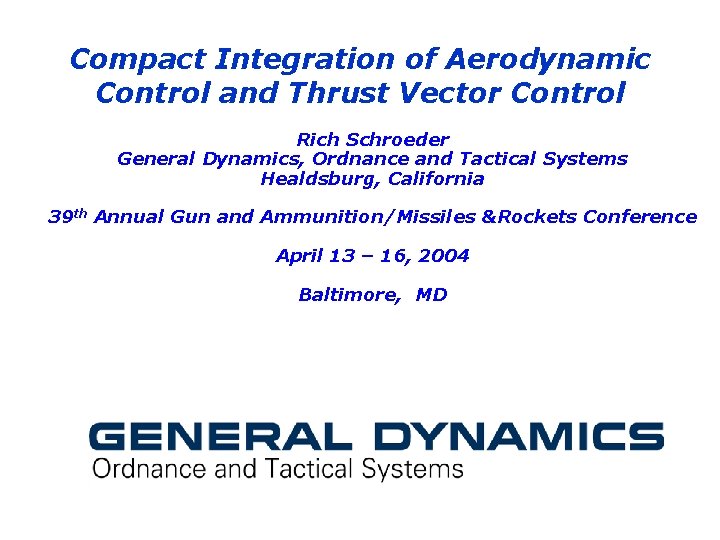
Compact Integration of Aerodynamic Control and Thrust Vector Control Rich Schroeder General Dynamics, Ordnance and Tactical Systems Healdsburg, California 39 th Annual Gun and Ammunition/Missiles &Rockets Conference April 13 – 16, 2004 Baltimore, MD
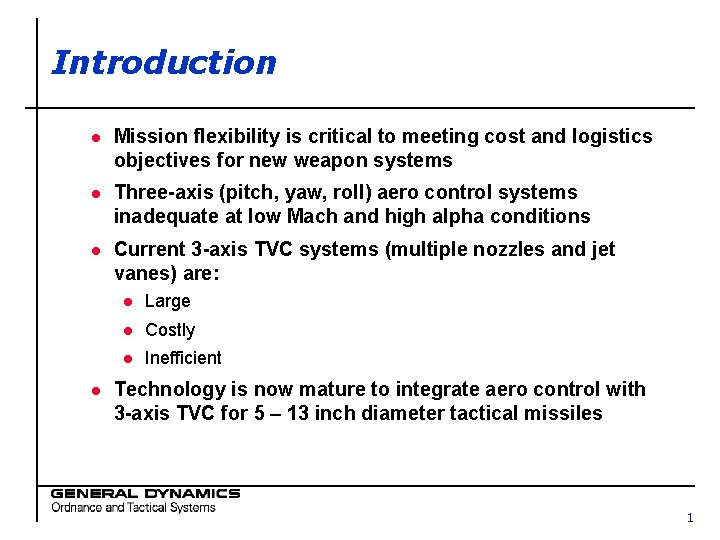
Introduction l Mission flexibility is critical to meeting cost and logistics objectives for new weapon systems l Three-axis (pitch, yaw, roll) aero control systems inadequate at low Mach and high alpha conditions l Current 3 -axis TVC systems (multiple nozzles and jet vanes) are: l l Large l Costly l Inefficient Technology is now mature to integrate aero control with 3 -axis TVC for 5 – 13 inch diameter tactical missiles 1
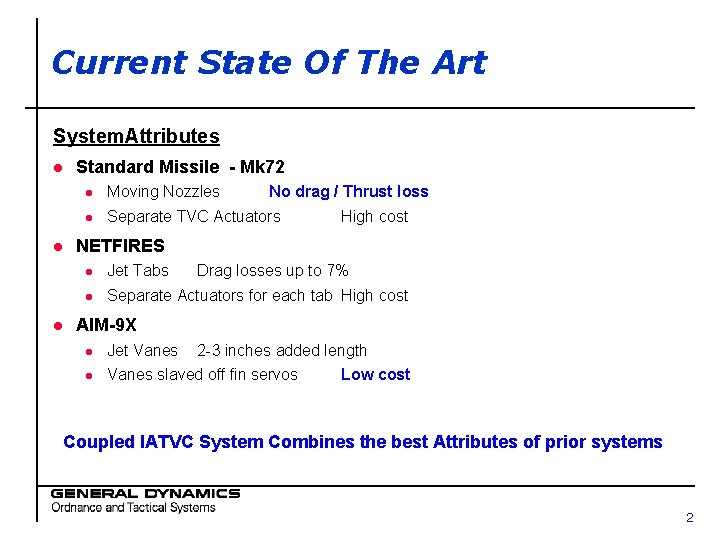
Current State Of The Art System. Attributes l l l Standard Missile - Mk 72 l Moving Nozzles No drag / Thrust loss l Separate TVC Actuators High cost NETFIRES l Jet Tabs Drag losses up to 7% l Separate Actuators for each tab High cost AIM-9 X l Jet Vanes 2 -3 inches added length l Vanes slaved off fin servos Low cost Coupled IATVC System Combines the best Attributes of prior systems 2
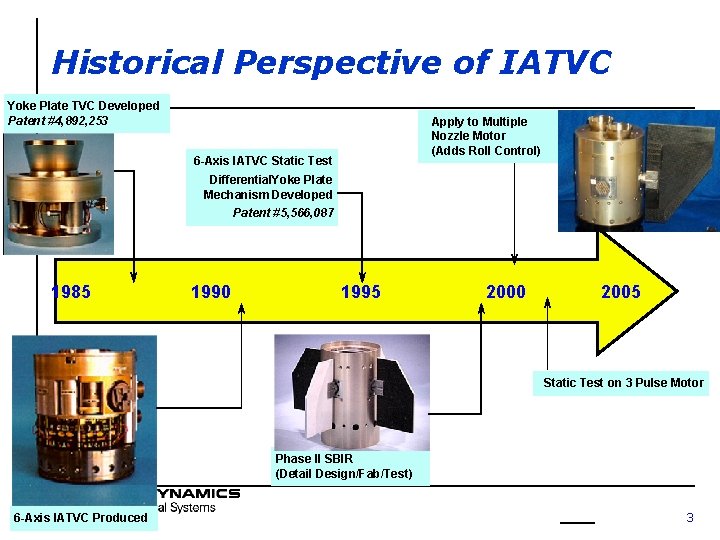
Historical Perspective of IATVC Yoke Plate TVC Developed Patent #4, 892, 253 Apply to Multiple Nozzle Motor (Adds Roll Control) 6 -Axis IATVC Static Test Differential. Yoke Plate Mechanism Developed Patent #5, 566, 087 1985 1990 1995 2000 2005 Static Test on 3 Pulse Motor Phase II SBIR (Detail Design/Fab/Test) 6 -Axis IATVC Produced 3
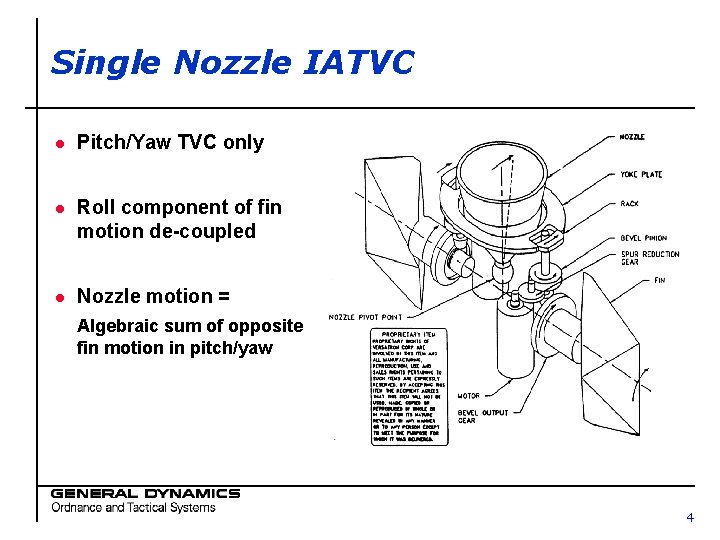
Single Nozzle IATVC l Pitch/Yaw TVC only l Roll component of fin motion de-coupled l Nozzle motion = Algebraic sum of opposite fin motion in pitch/yaw 4
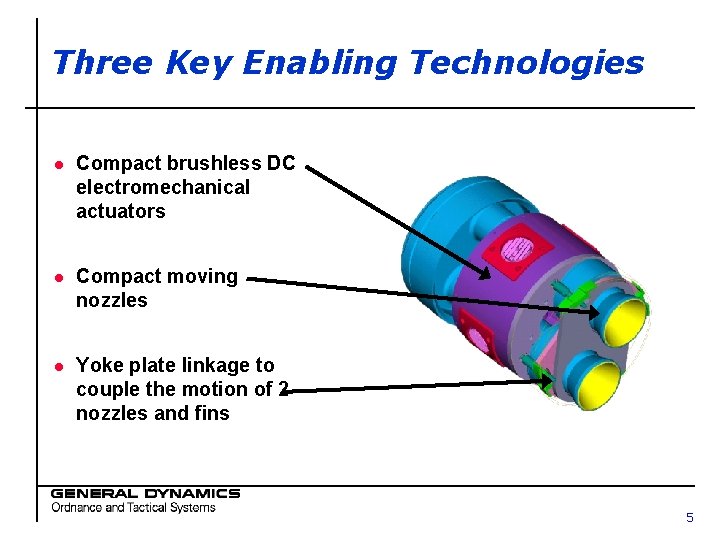
Three Key Enabling Technologies l Compact brushless DC electromechanical actuators l Compact moving nozzles l Yoke plate linkage to couple the motion of 2 nozzles and fins 5
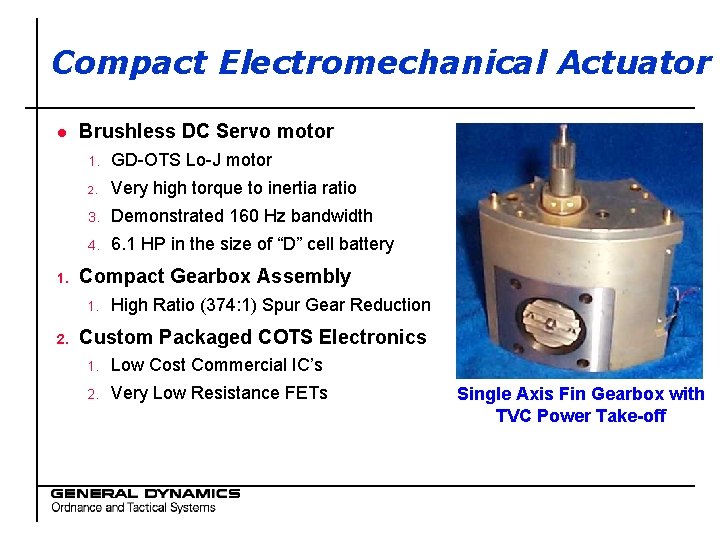
Compact Electromechanical Actuator l 1. Brushless DC Servo motor 1. GD-OTS Lo-J motor 2. Very high torque to inertia ratio 3. Demonstrated 160 Hz bandwidth 4. 6. 1 HP in the size of “D” cell battery Compact Gearbox Assembly 1. 2. High Ratio (374: 1) Spur Gear Reduction Custom Packaged COTS Electronics 1. Low Cost Commercial IC’s 2. Very Low Resistance FETs Single Axis Fin Gearbox with TVC Power Take-off
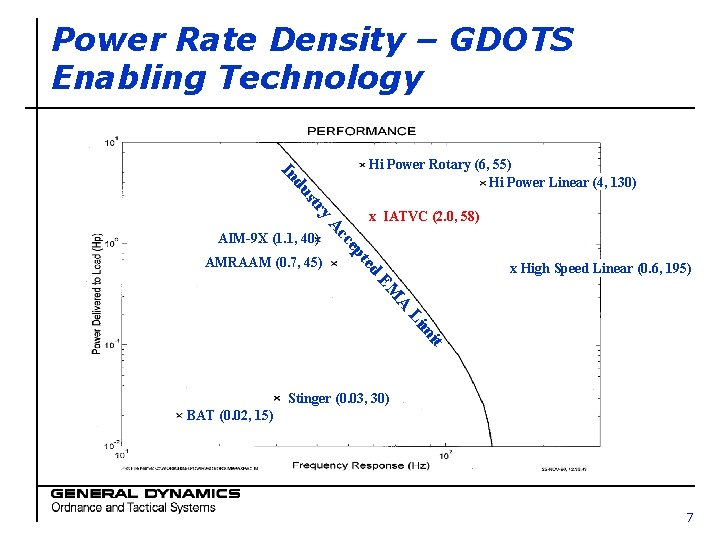
Power Rate Density – GDOTS Enabling Technology du In Hi Power Rotary (6, 55) Hi Power Linear (4, 130) x High Speed Linear (0. 6, 195) d AMRAAM (0. 7, 45) te ep cc y. A str AIM-9 X (1. 1, 40) x IATVC (2. 0, 58) A EM it m Li Stinger (0. 03, 30) BAT (0. 02, 15) 7
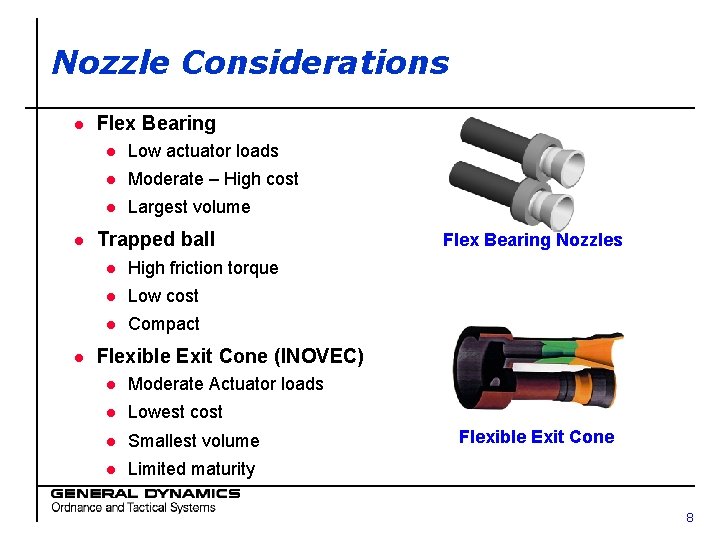
Nozzle Considerations l l l Flex Bearing l Low actuator loads l Moderate – High cost l Largest volume Trapped ball l High friction torque l Low cost l Compact Flex Bearing Nozzles Flexible Exit Cone (INOVEC) l Moderate Actuator loads l Lowest cost l Smallest volume l Limited maturity Flexible Exit Cone 8
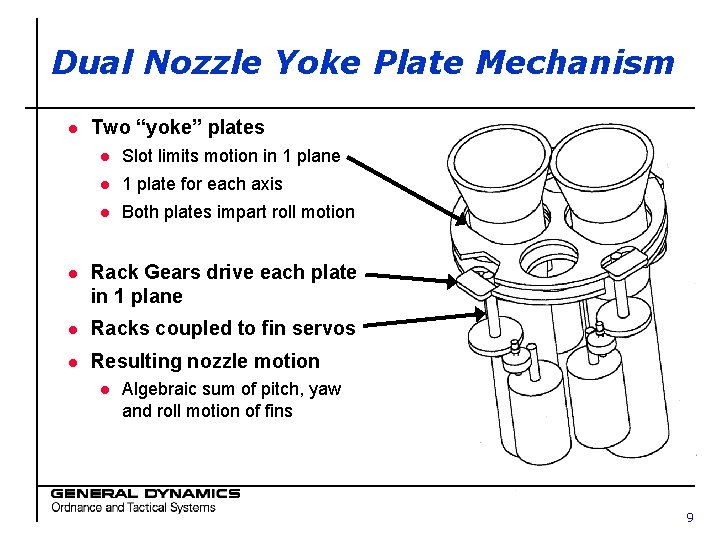
Dual Nozzle Yoke Plate Mechanism l Two “yoke” plates l Slot limits motion in 1 plane l 1 plate for each axis l Both plates impart roll motion l Rack Gears drive each plate in 1 plane l Racks coupled to fin servos l Resulting nozzle motion l Algebraic sum of pitch, yaw and roll motion of fins 9
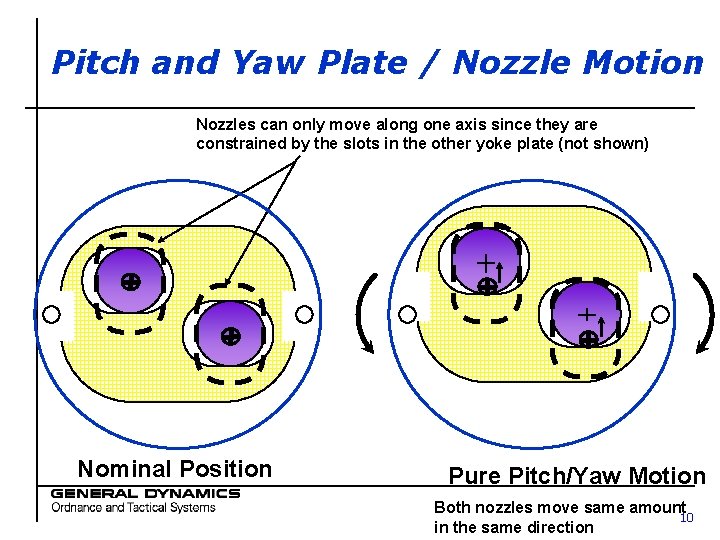
Pitch and Yaw Plate / Nozzle Motion Nozzles can only move along one axis since they are constrained by the slots in the other yoke plate (not shown) Nominal Position Pure Pitch/Yaw Motion Both nozzles move same amount 10 in the same direction
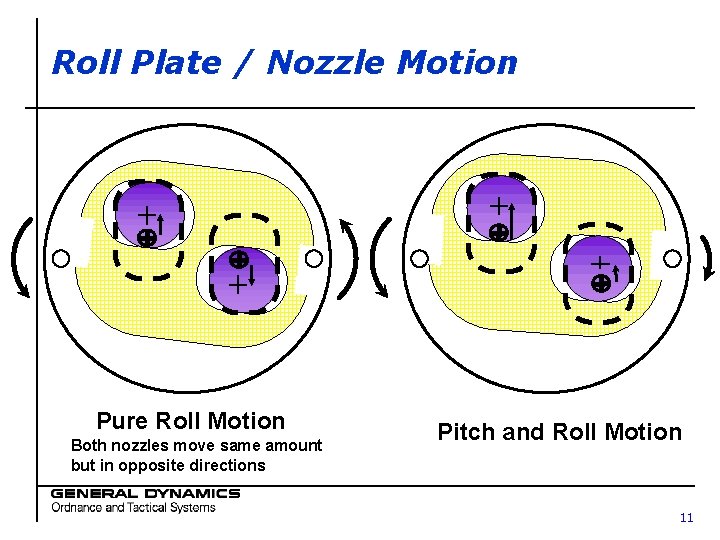
Roll Plate / Nozzle Motion Pure Roll Motion Both nozzles move same amount but in opposite directions Pitch and Roll Motion 11
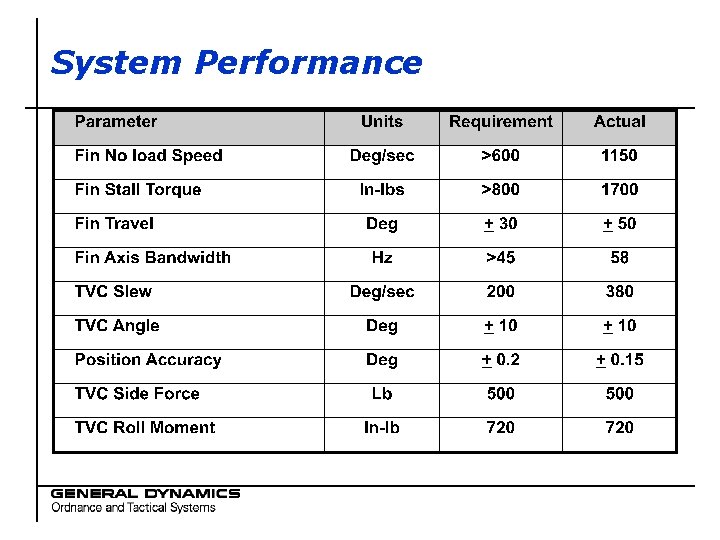
System Performance
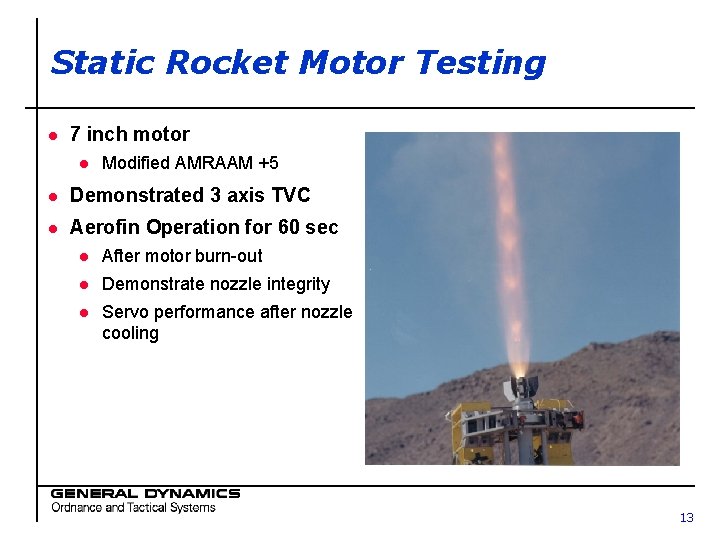
Static Rocket Motor Testing l 7 inch motor l Modified AMRAAM +5 l Demonstrated 3 axis TVC l Aerofin Operation for 60 sec l After motor burn-out l Demonstrate nozzle integrity l Servo performance after nozzle cooling 13
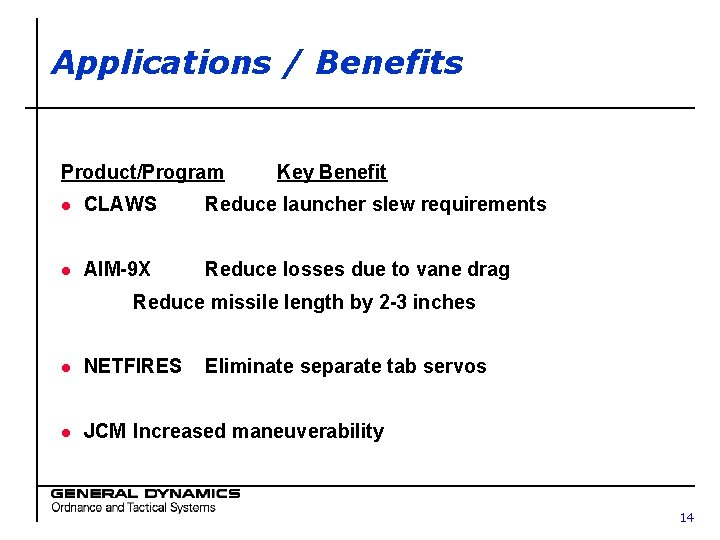
Applications / Benefits Product/Program Key Benefit l CLAWS Reduce launcher slew requirements l AIM-9 X Reduce losses due to vane drag Reduce missile length by 2 -3 inches l NETFIRES Eliminate separate tab servos l JCM Increased maneuverability 14
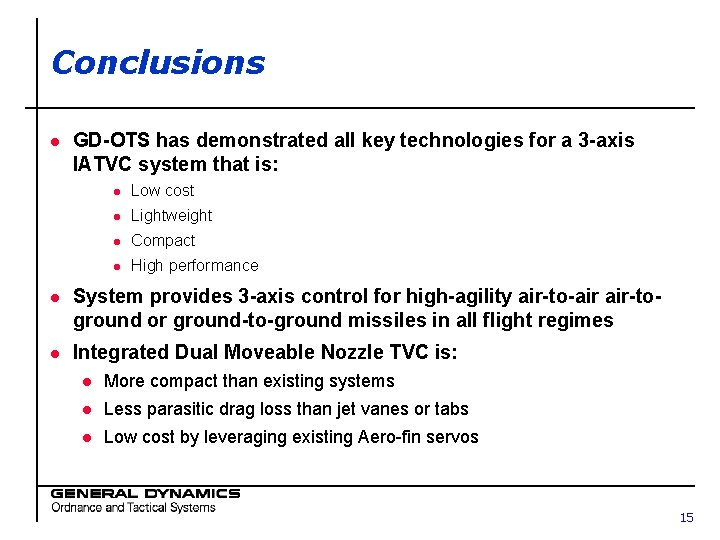
Conclusions l GD-OTS has demonstrated all key technologies for a 3 -axis IATVC system that is: l Low cost l Lightweight l Compact l High performance l System provides 3 -axis control for high-agility air-to-air air-toground or ground-to-ground missiles in all flight regimes l Integrated Dual Moveable Nozzle TVC is: l More compact than existing systems l Less parasitic drag loss than jet vanes or tabs l Low cost by leveraging existing Aero-fin servos 15
Plastic compact semi compact slender
Thrust device vector example
Aerodynamics of a water bottle rocket
Mean aerodynamic chord
Missile aerodynamics
Least aerodynamic shape
Co2 dragster aerodynamics
Airfoil nomenclature
Aerodynamic devices
Drag equation physics
Sectional drive
Forward integration and backward integration
Forward integration and backward integration
Simultaneous integration example
Directed line segment definition
Vector unitario de un vector
Vector resolution