CHEME 7160 Fluid Flow in Process Units Project
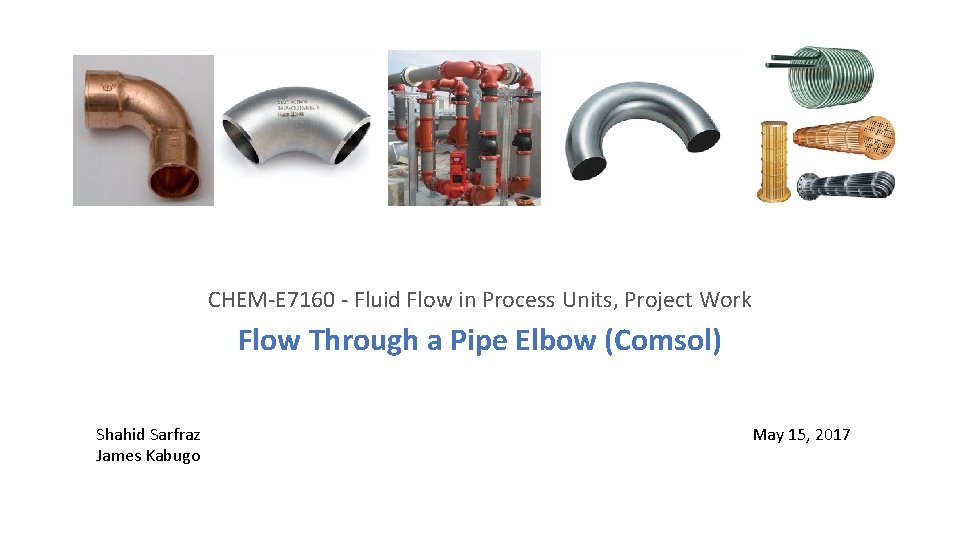
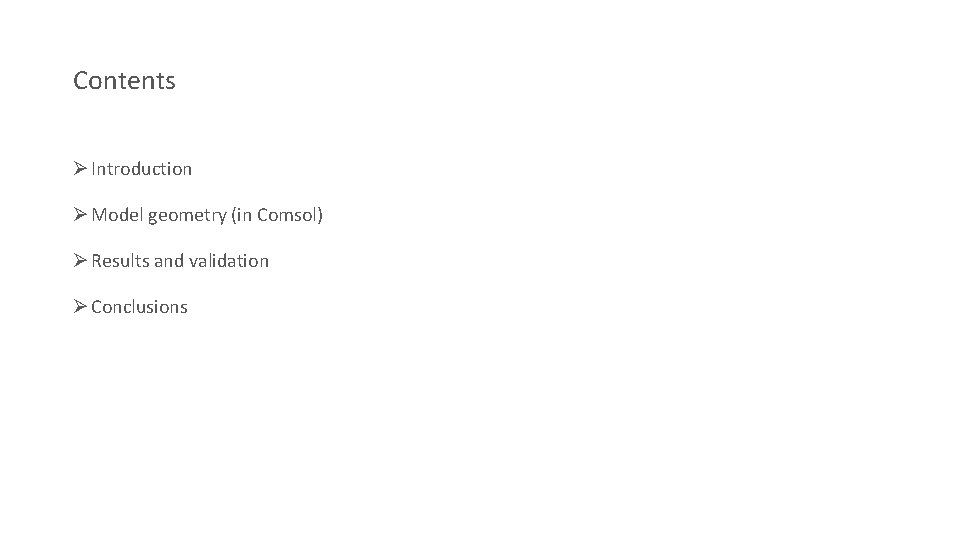
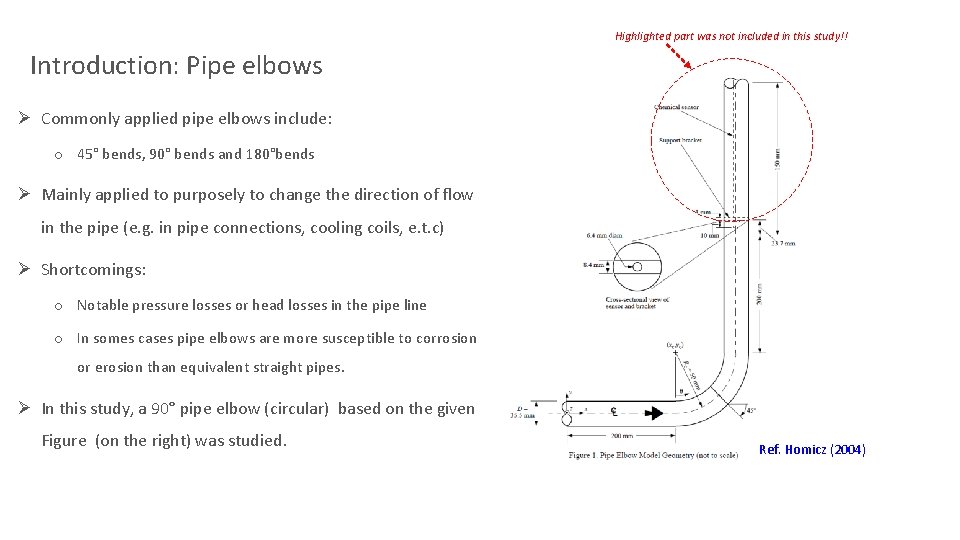
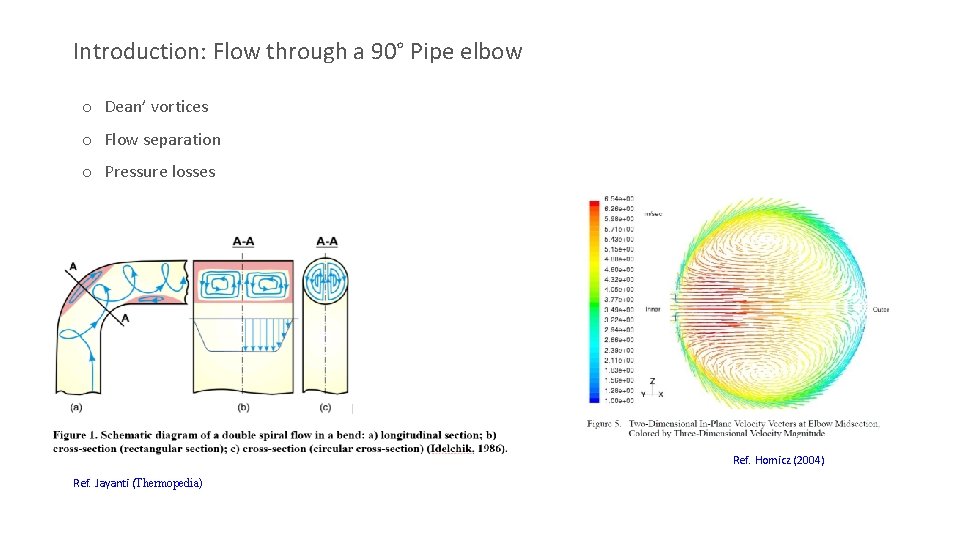
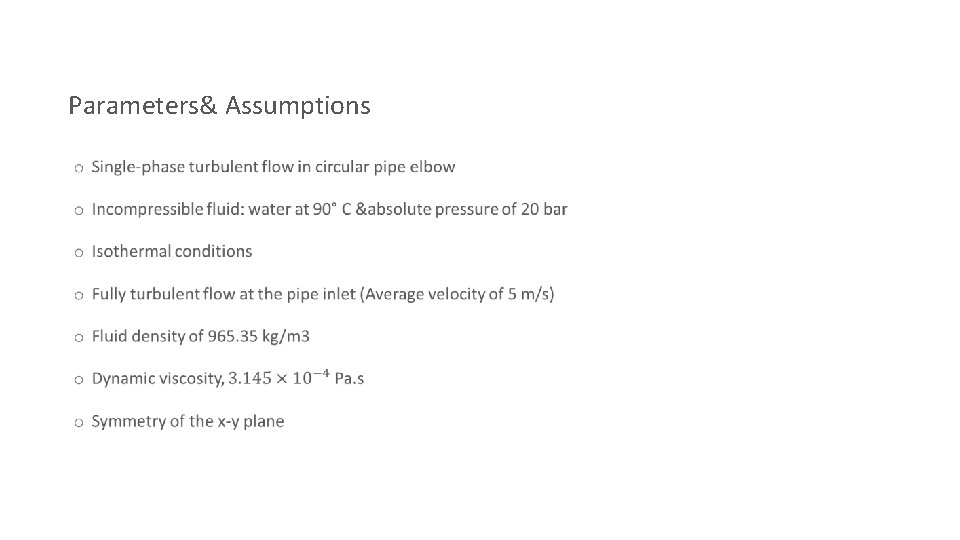
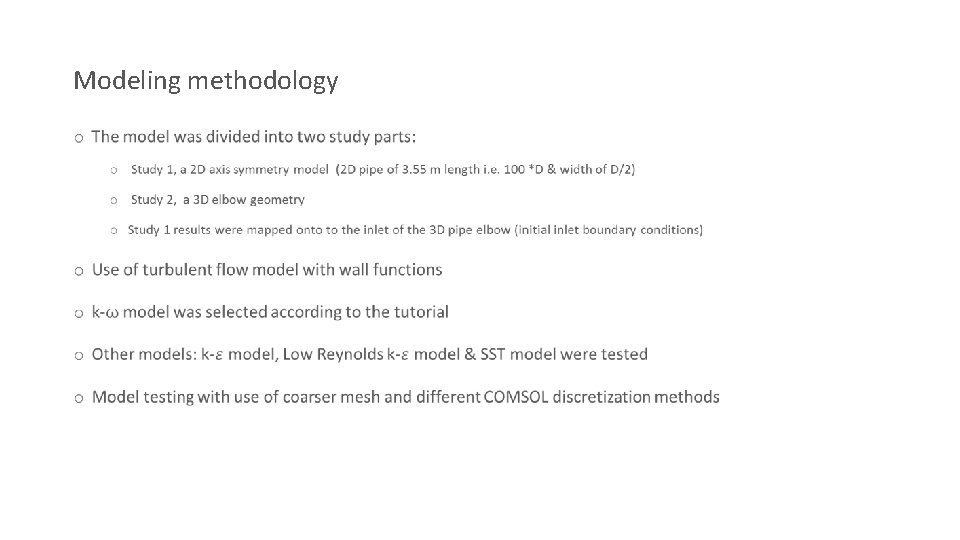
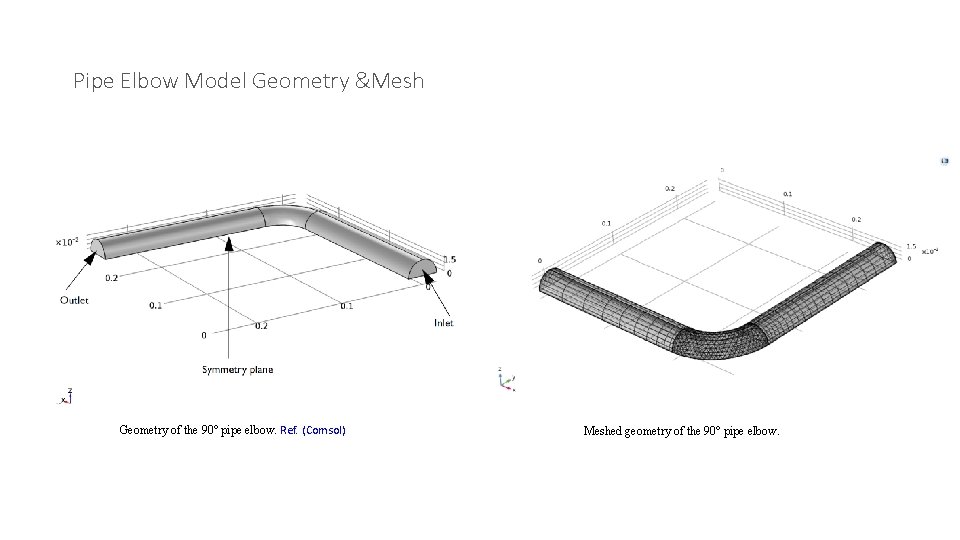
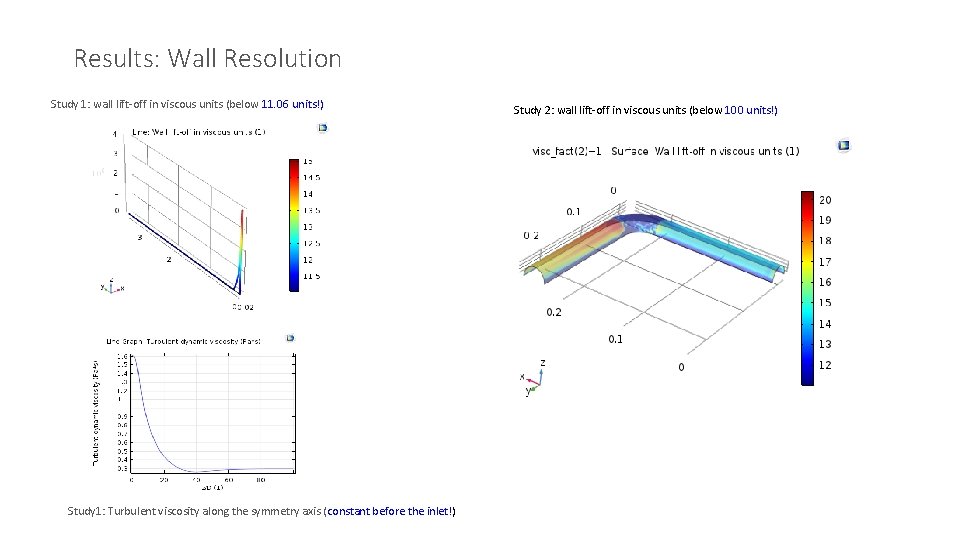
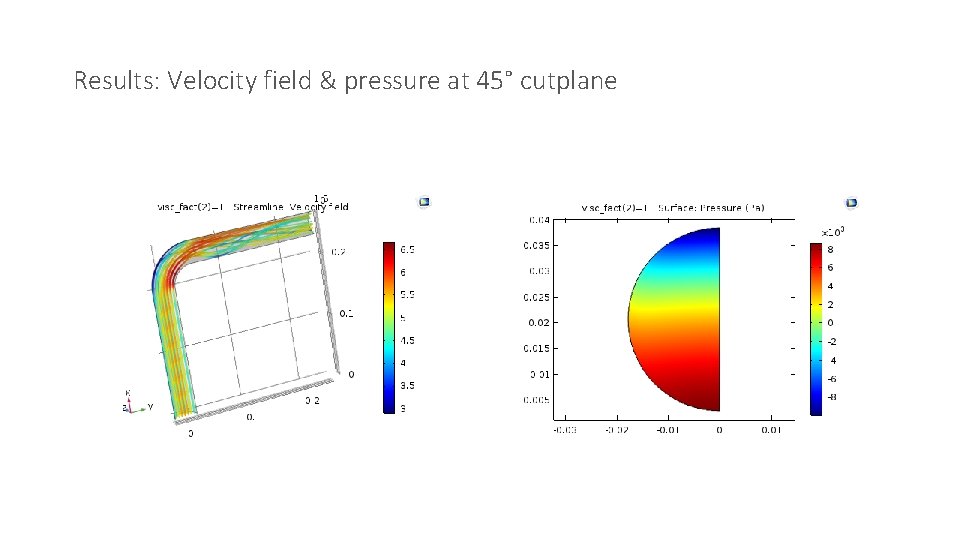
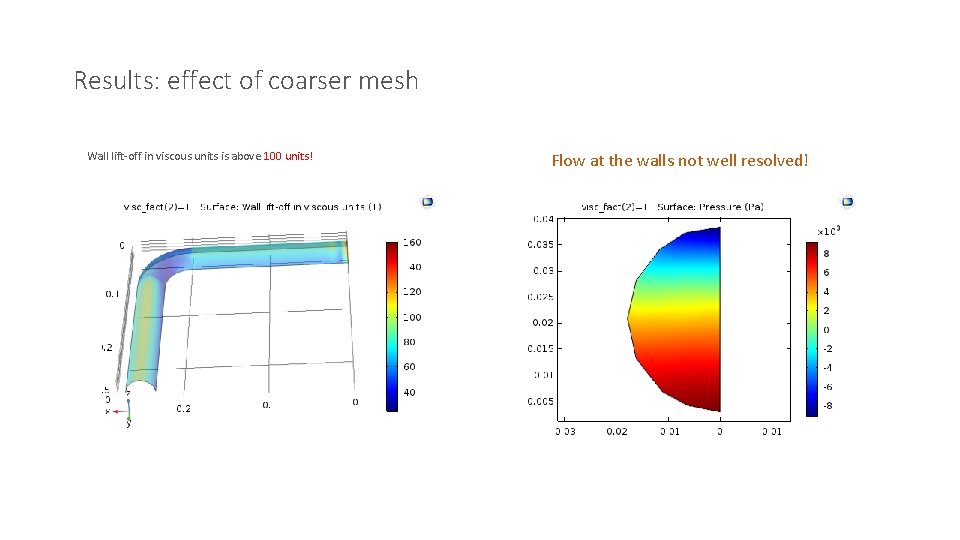
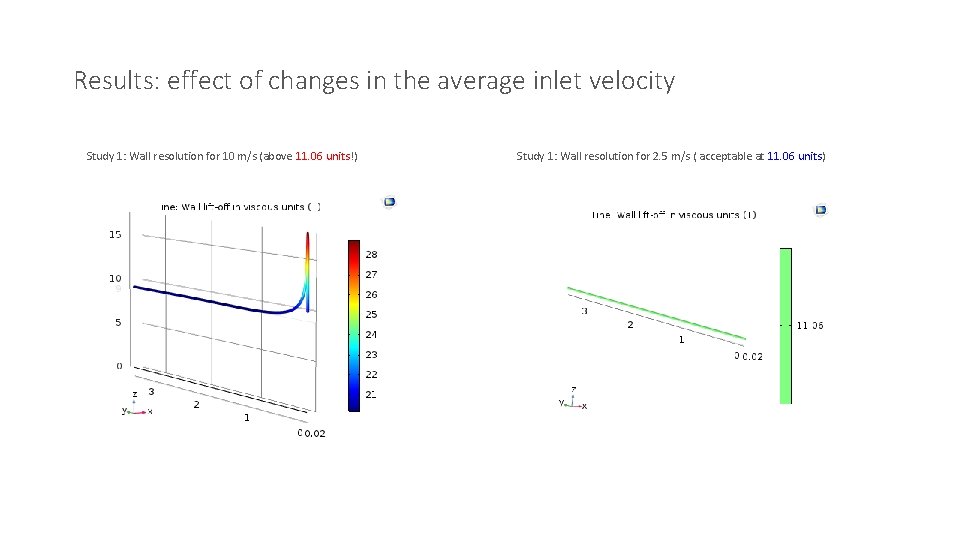
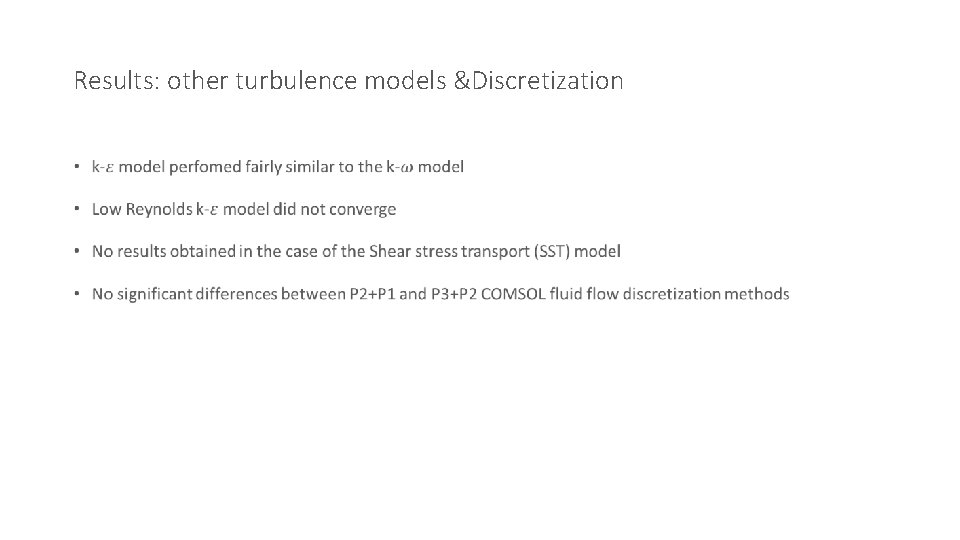
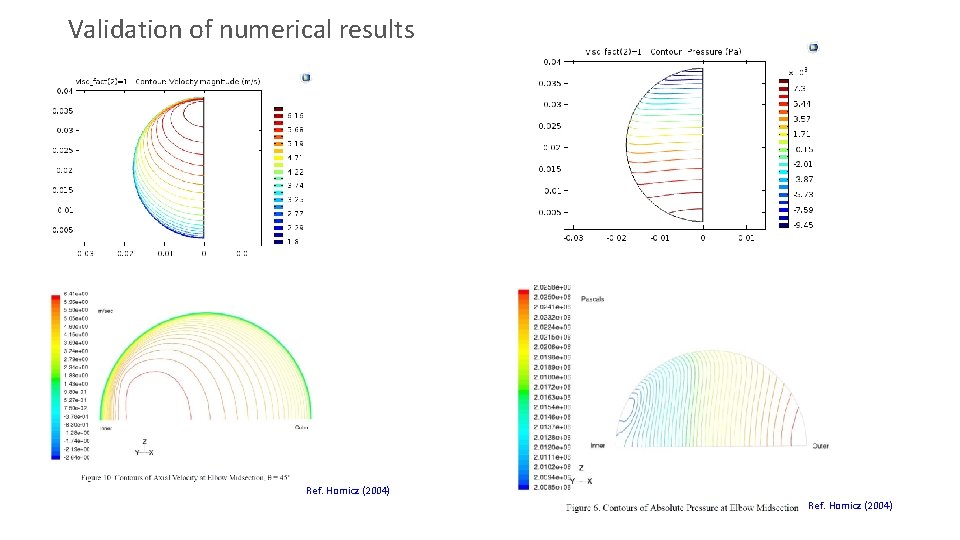
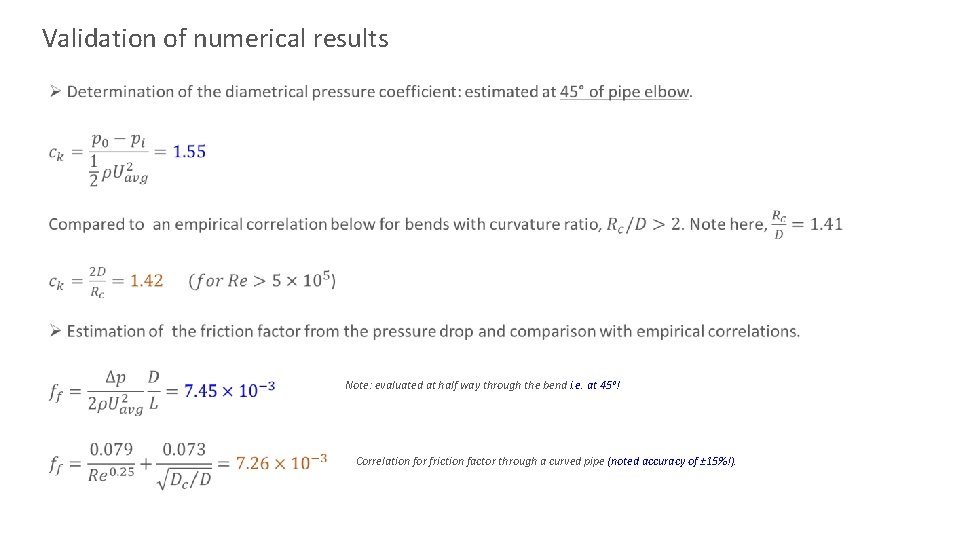

- Slides: 15
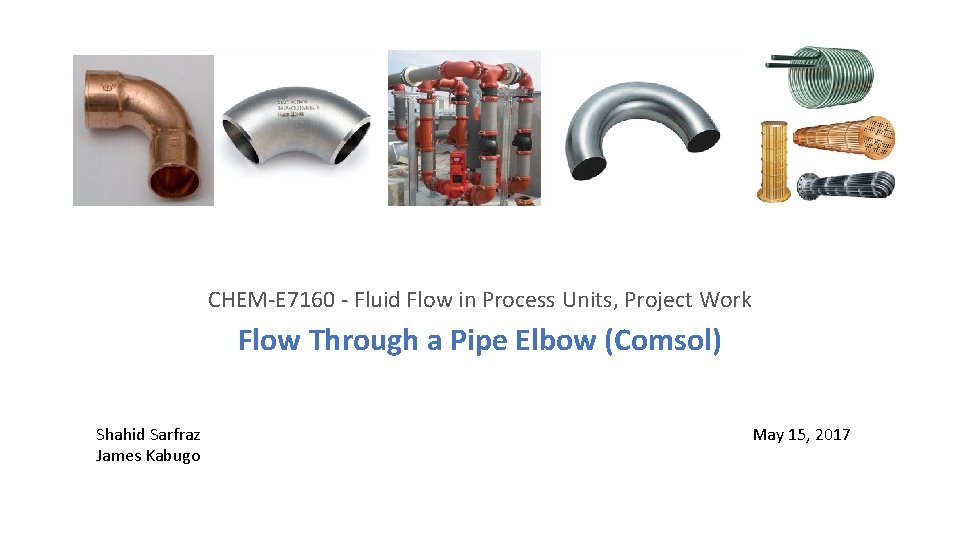
CHEM-E 7160 - Fluid Flow in Process Units, Project Work Flow Through a Pipe Elbow (Comsol) Shahid Sarfraz James Kabugo May 15, 2017
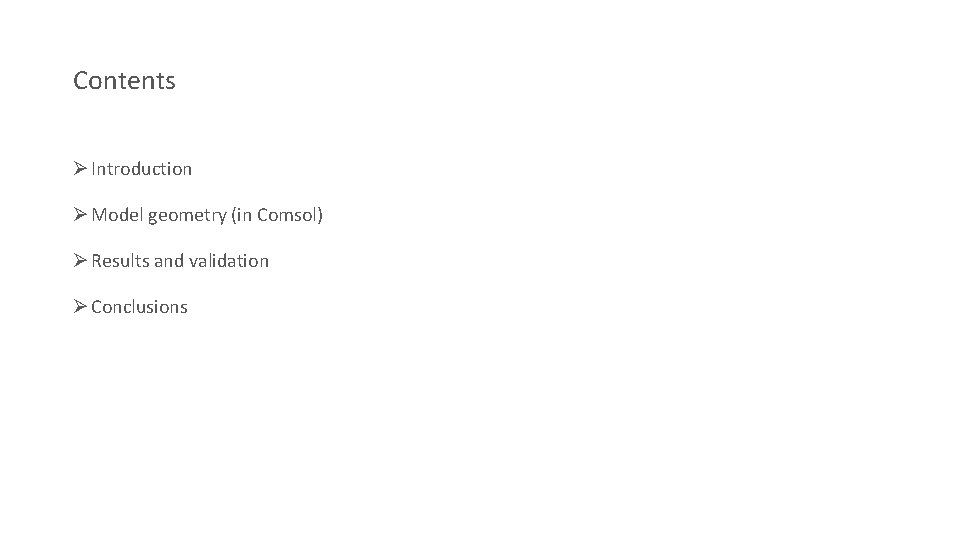
Contents Ø Introduction Ø Model geometry (in Comsol) Ø Results and validation Ø Conclusions
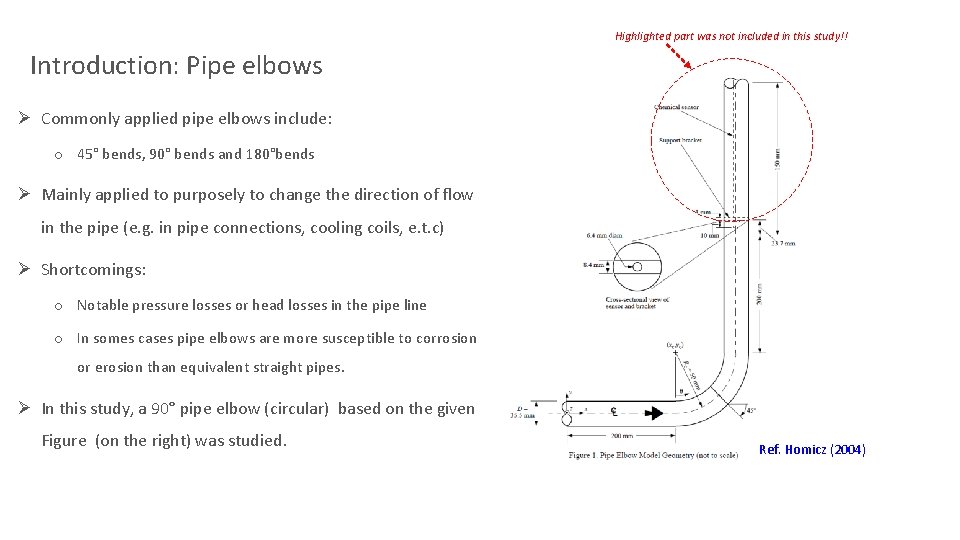
Highlighted part was not included in this study!! Introduction: Pipe elbows Ø Commonly applied pipe elbows include: o 45° bends, 90° bends and 180°bends Ø Mainly applied to purposely to change the direction of flow in the pipe (e. g. in pipe connections, cooling coils, e. t. c) Ø Shortcomings: o Notable pressure losses or head losses in the pipe line o In somes cases pipe elbows are more susceptible to corrosion or erosion than equivalent straight pipes. Ø In this study, a 90° pipe elbow (circular) based on the given Figure (on the right) was studied. Ref. Homicz (2004)
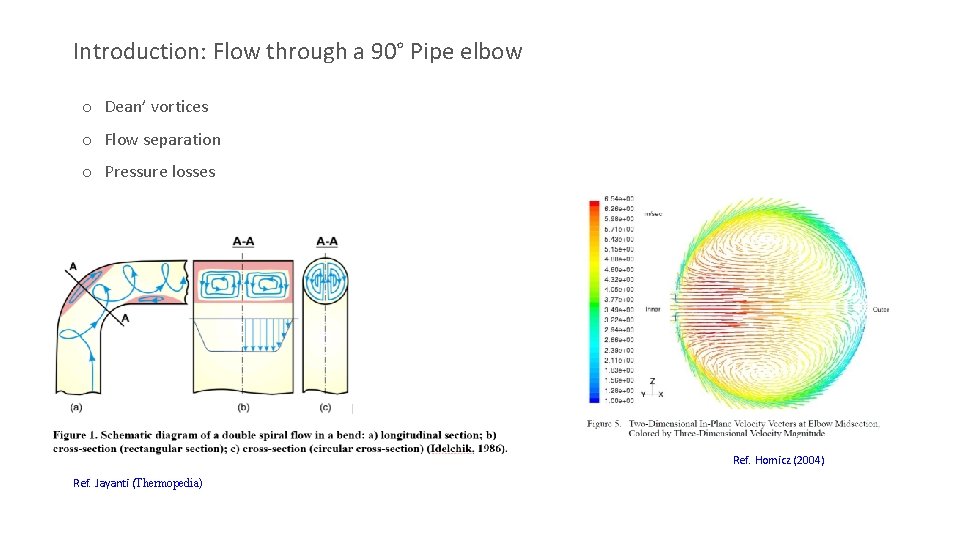
Introduction: Flow through a 90° Pipe elbow o Dean’ vortices o Flow separation o Pressure losses Ref. Homicz (2004) Ref. Jayanti (Thermopedia)
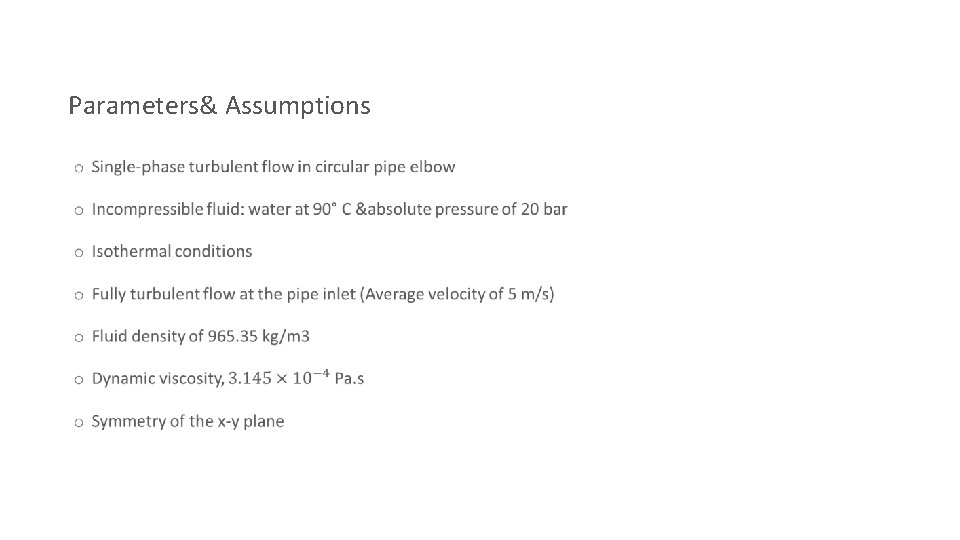
Parameters& Assumptions •
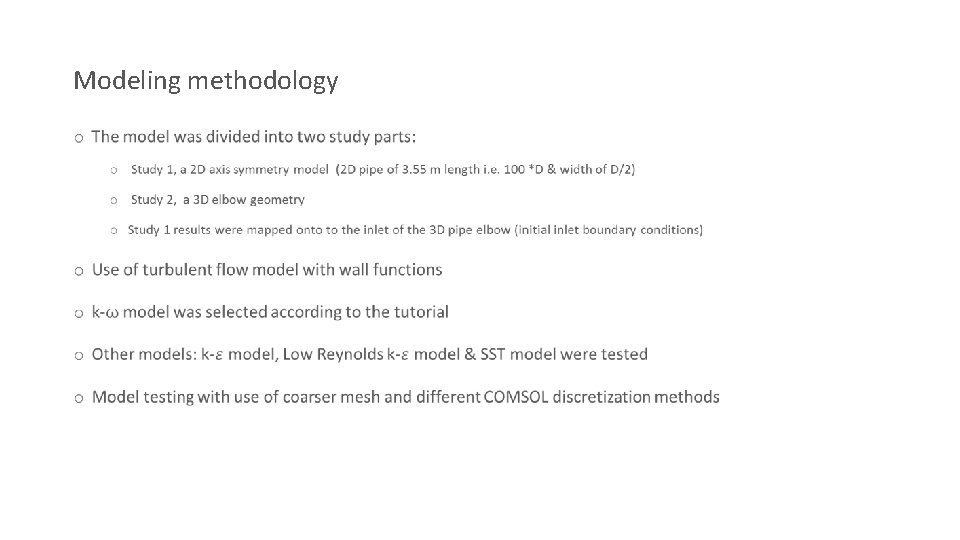
Modeling methodology •
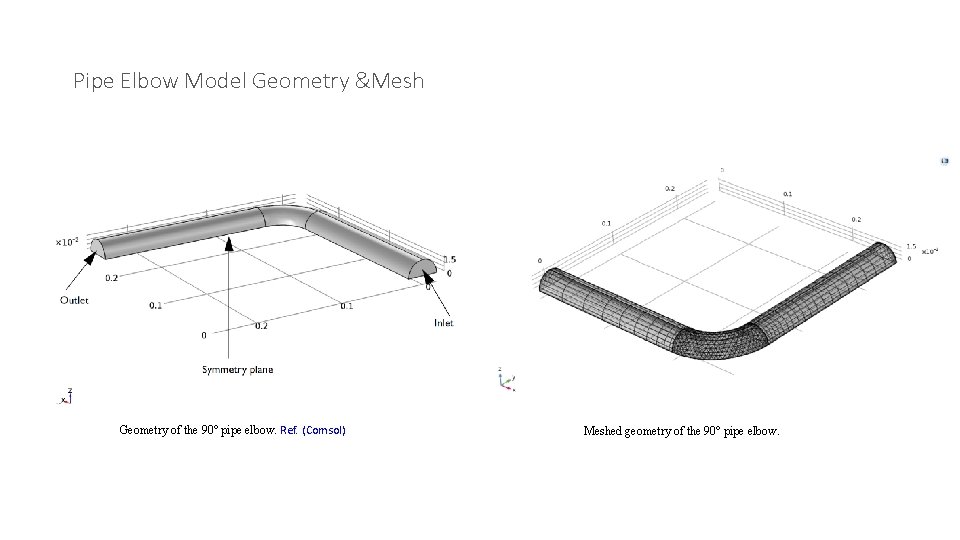
Pipe Elbow Model Geometry &Mesh Geometry of the 90° pipe elbow. Ref. (Comsol) Meshed geometry of the 90° pipe elbow.
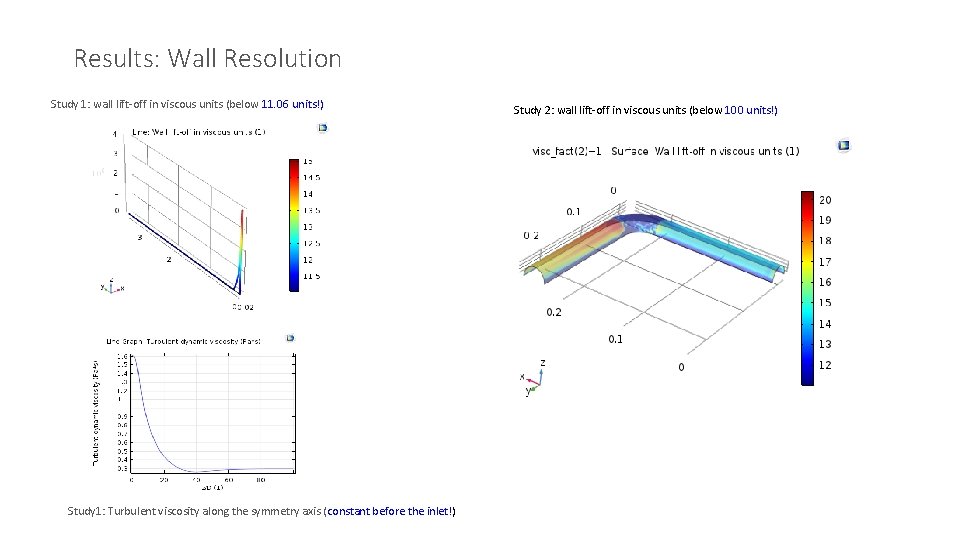
Results: Wall Resolution Study 1: wall lift-off in viscous units (below 11. 06 units!) Study 1: Turbulent viscosity along the symmetry axis (constant before the inlet!) Study 2: wall lift-off in viscous units (below 100 units!)
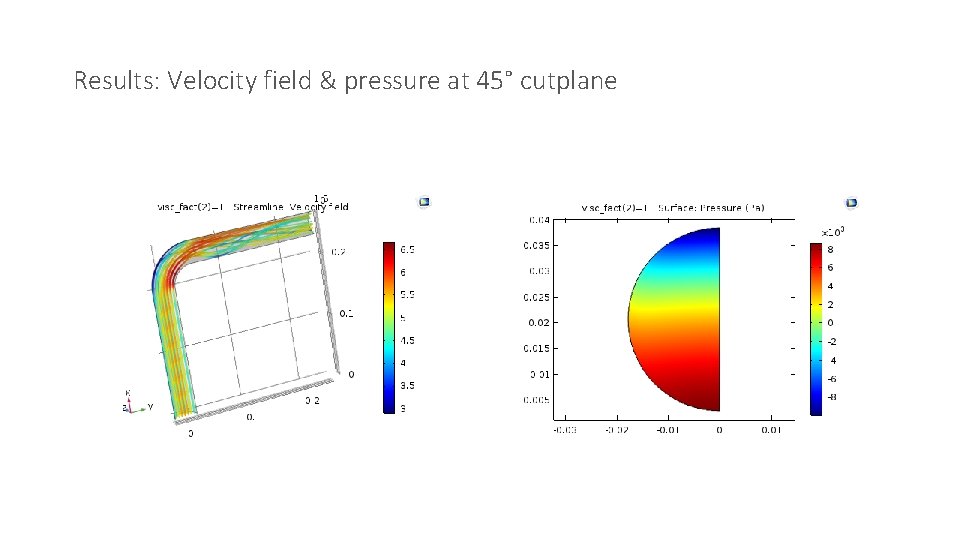
Results: Velocity field & pressure at 45° cutplane
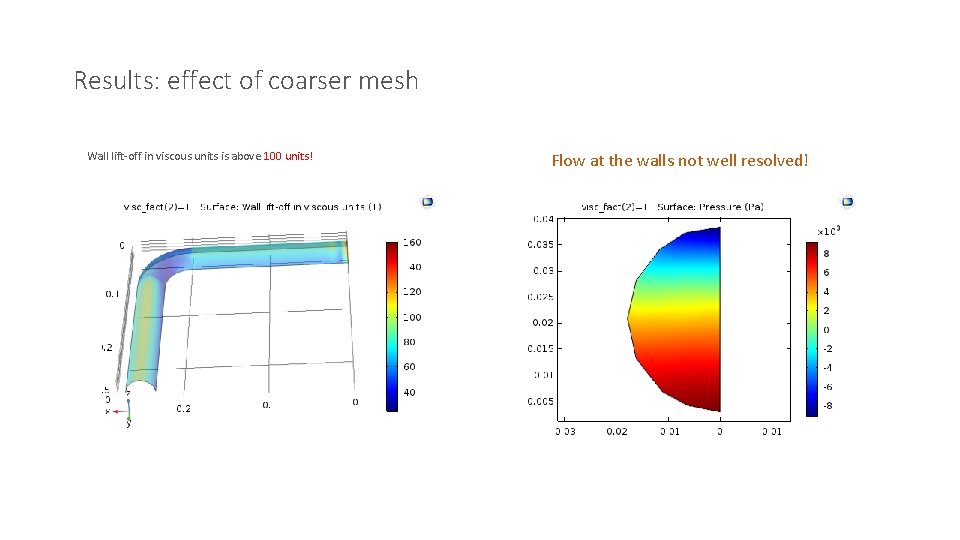
Results: effect of coarser mesh Wall lift-off in viscous units is above 100 units! Flow at the walls not well resolved!
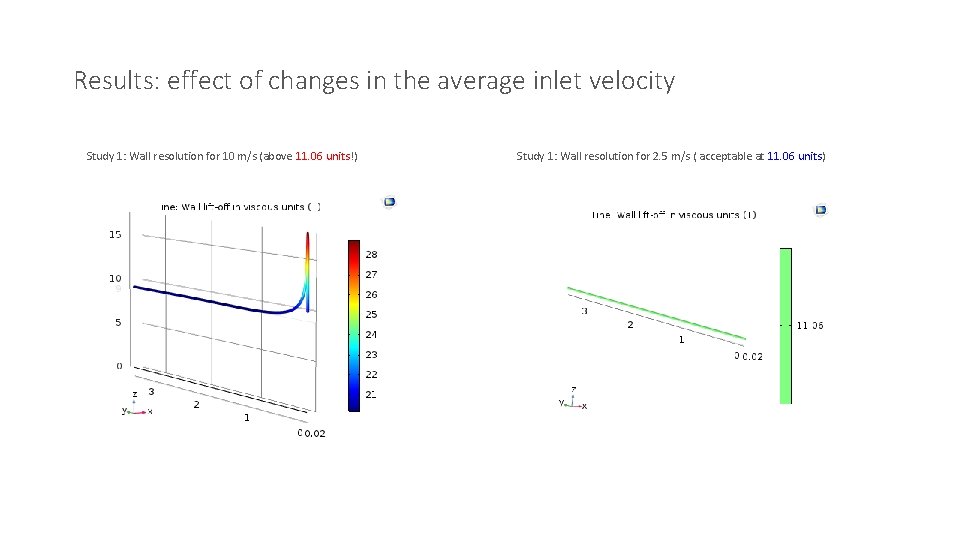
Results: effect of changes in the average inlet velocity Study 1: Wall resolution for 10 m/s (above 11. 06 units!) Study 1: Wall resolution for 2. 5 m/s ( acceptable at 11. 06 units)
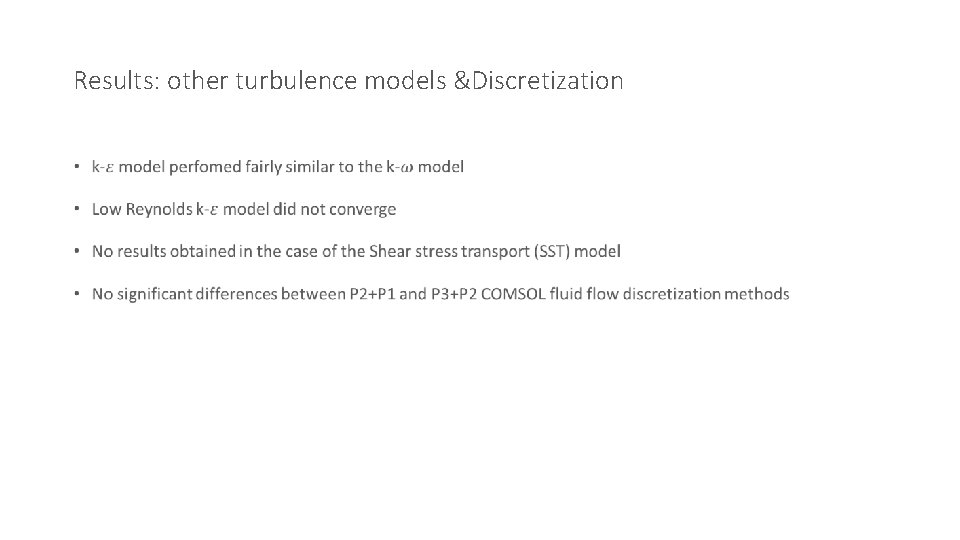
Results: other turbulence models &Discretization •
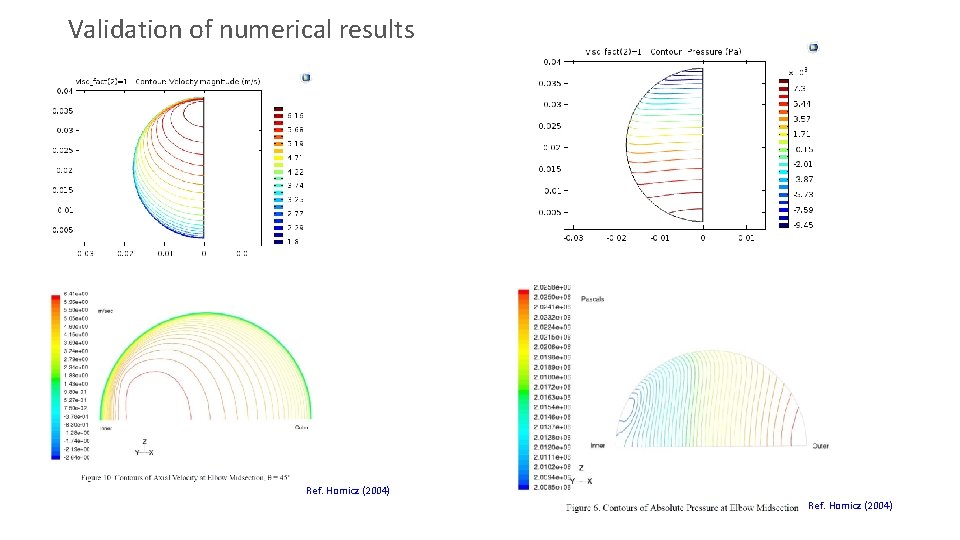
Validation of numerical results Ref. Homicz (2004)
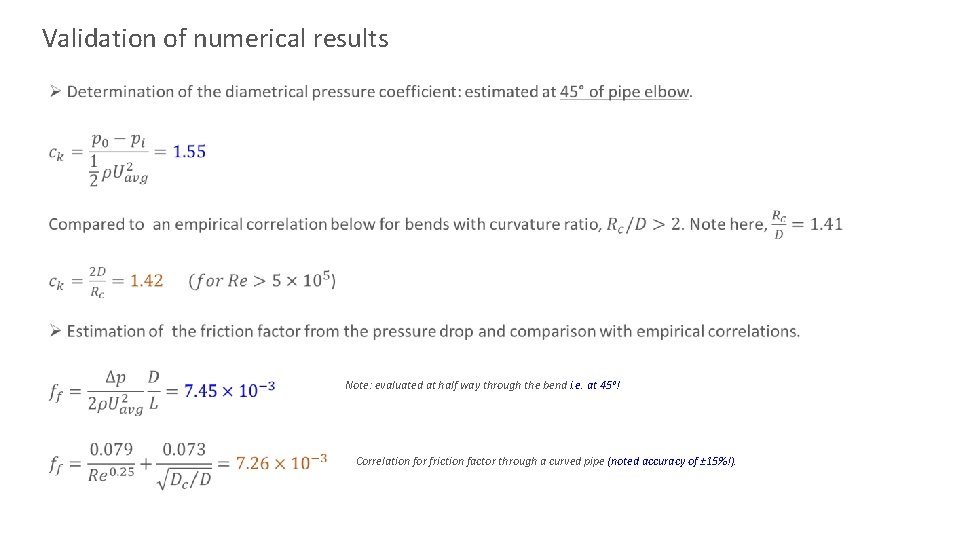
Validation of numerical results • Note: evaluated at half way through the bend i. e. at 45°! Correlation for friction factor through a curved pipe (noted accuracy of ± 15%!).

Conclusions • Higher pressure development on the outer wall of the curvature • Increase in flow velocity and maximum velocity observed along the centerline • Formation of two counteracting vortices (swirling behaviour) • Separation of the flow as it leaves the pipe elbow • Pressure or head losses are experienced in the pipe elbow • With a coarser grid, flow near the walls was poorly modeled
Viscoseal
P1-p2
Fluid statics deals with fluid at rest
Transcellular fluid compartment
Ecf icf and interstitial fluid
Interstitial vs intracellular
Timeline fluid mechanics
Extracellular fluid and interstitial fluid
Amount of fluid for fluid thrill
Speywood units vs botox units
Variable costing income statement
Close procurement process output
Nasa project life-cycle process flow poster
Cerebrospinal fluid
Bernoulli equation and conservation of energy
Critical reynolds number