Attitude Determination and Control Preliminary Design Review Stephen
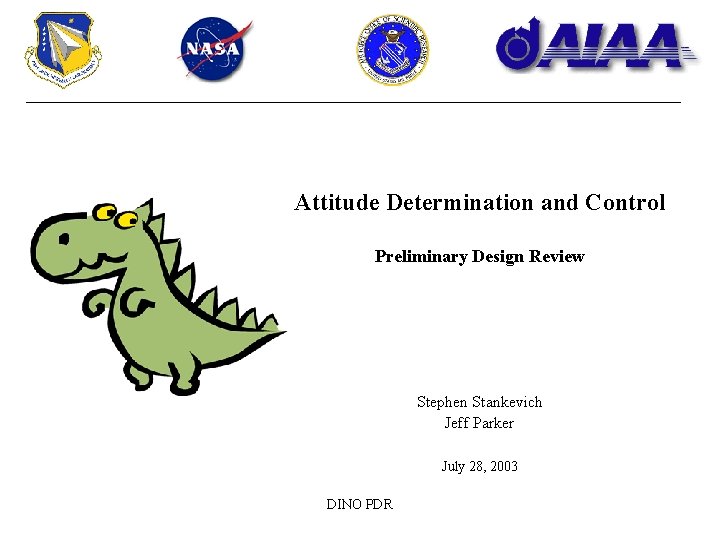
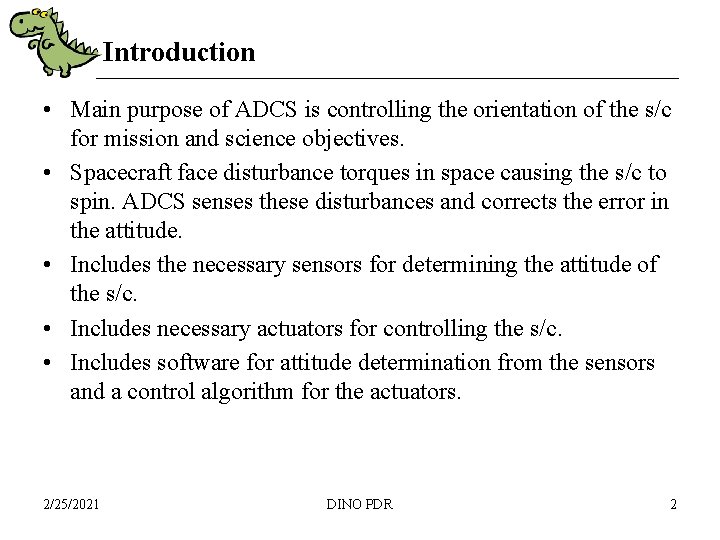
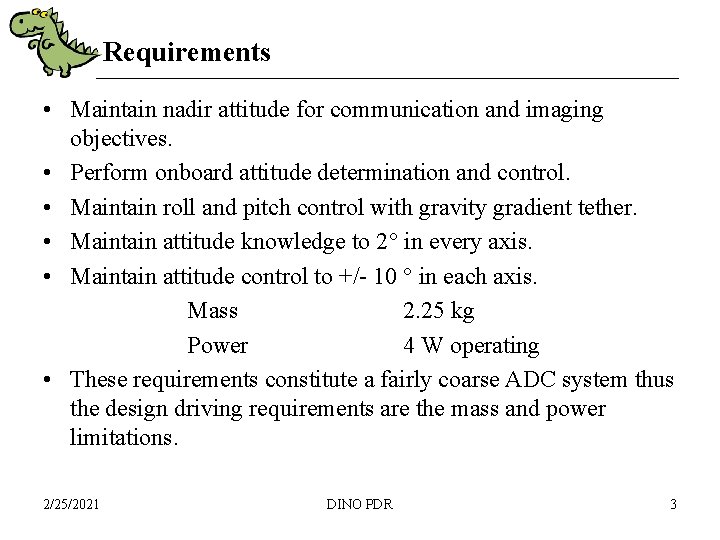
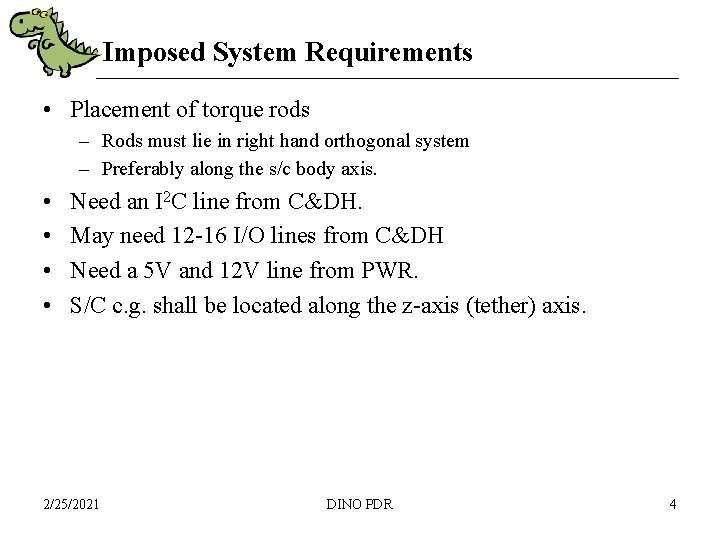
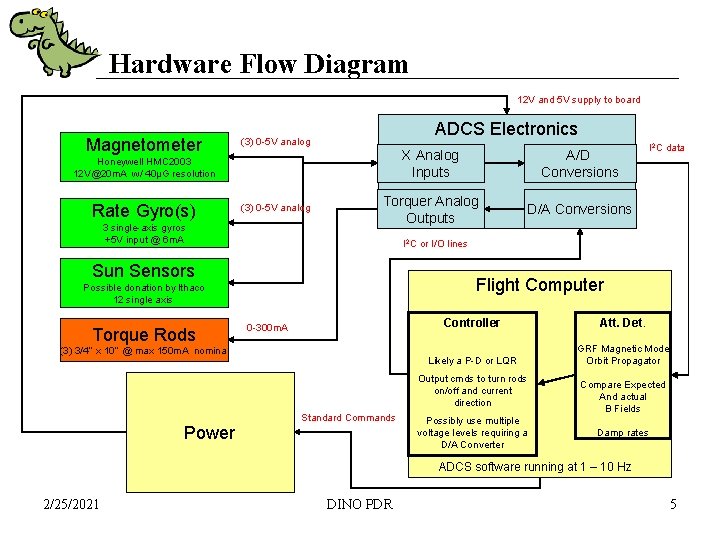
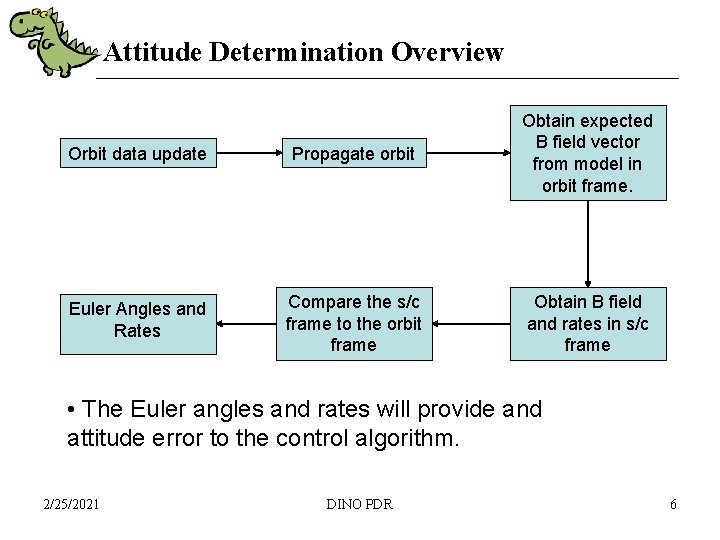
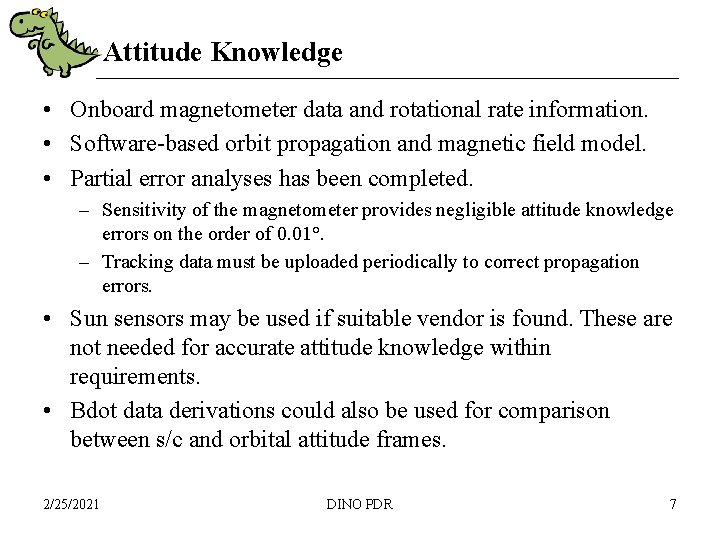
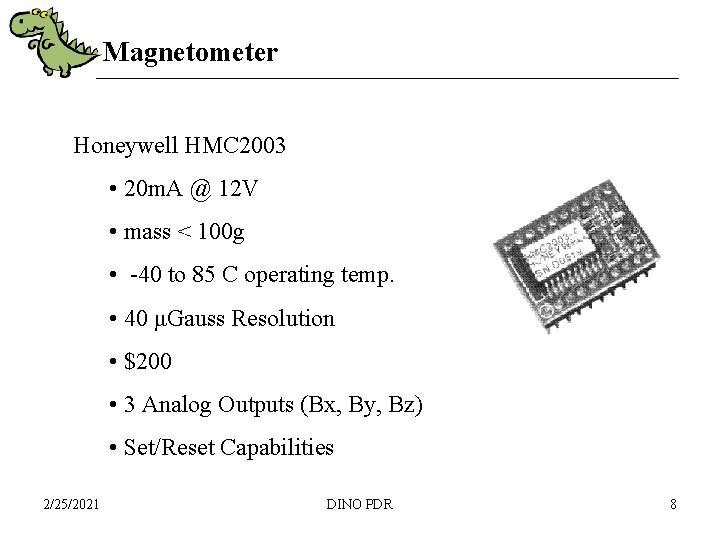
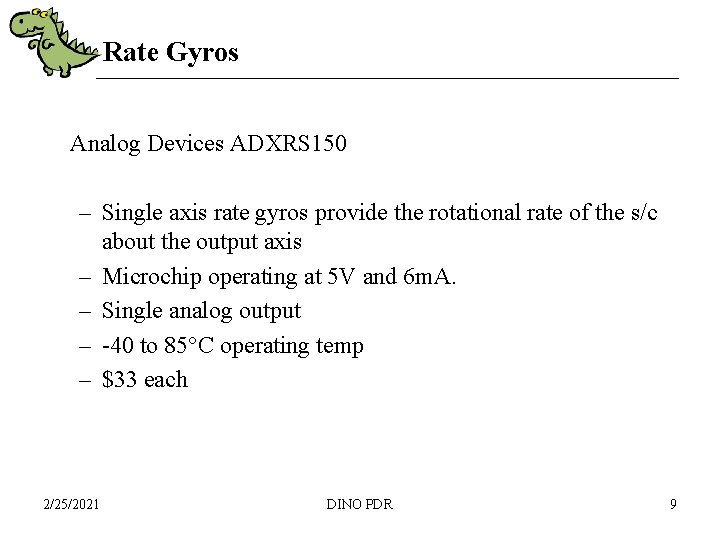
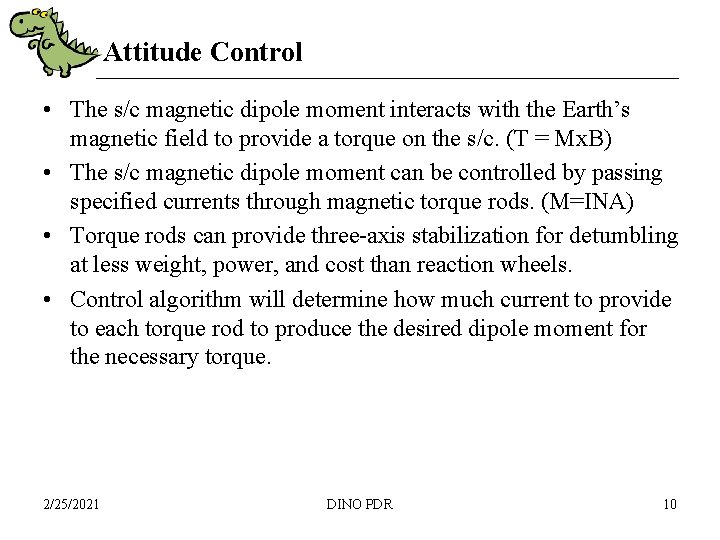
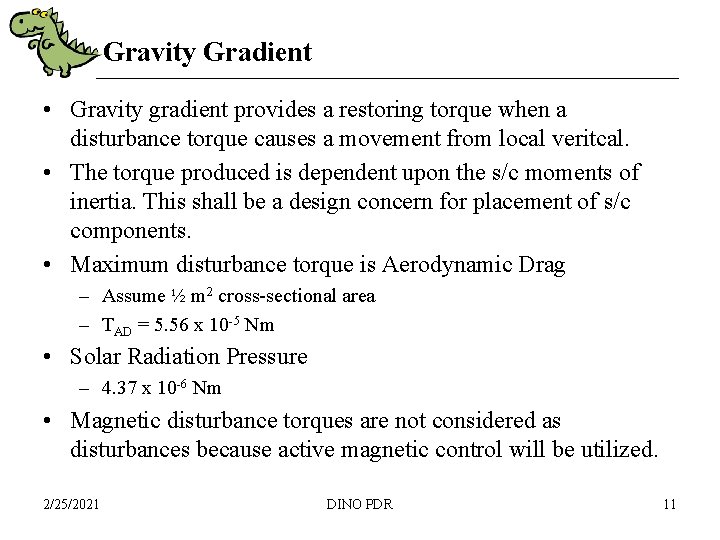
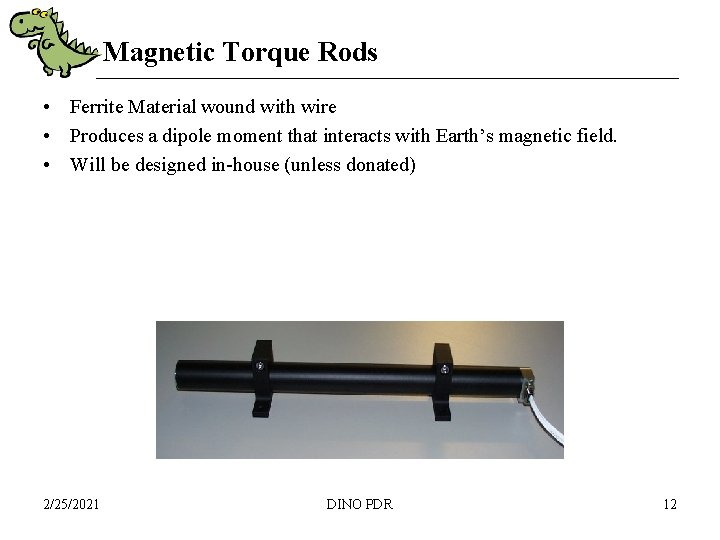
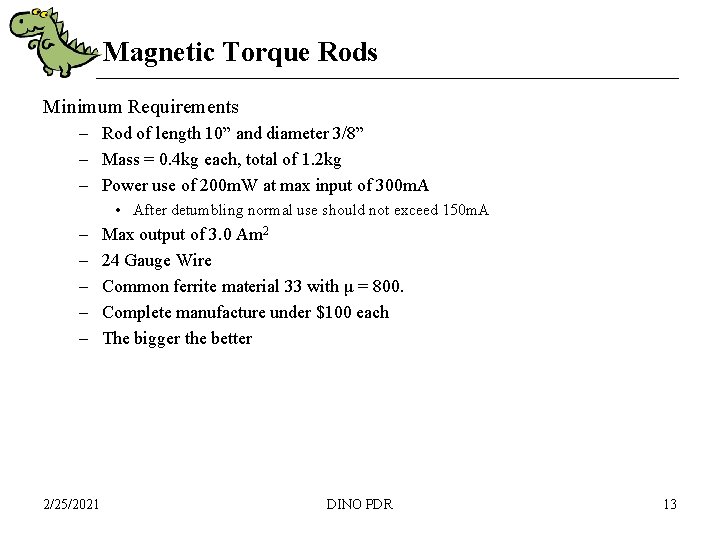
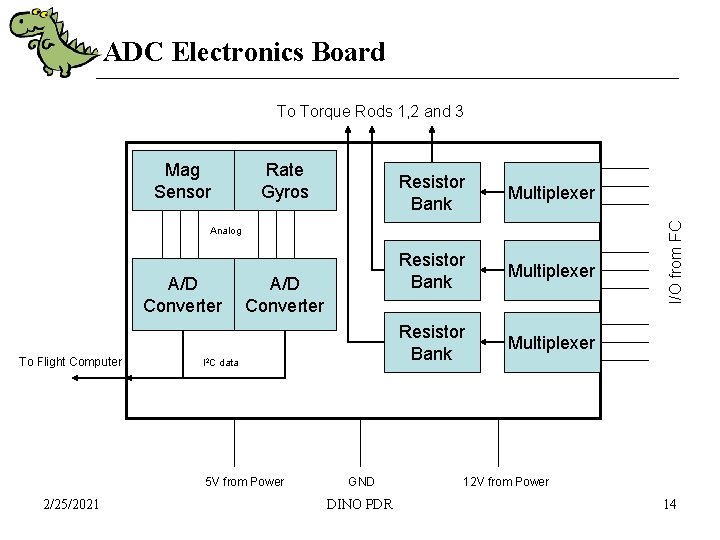
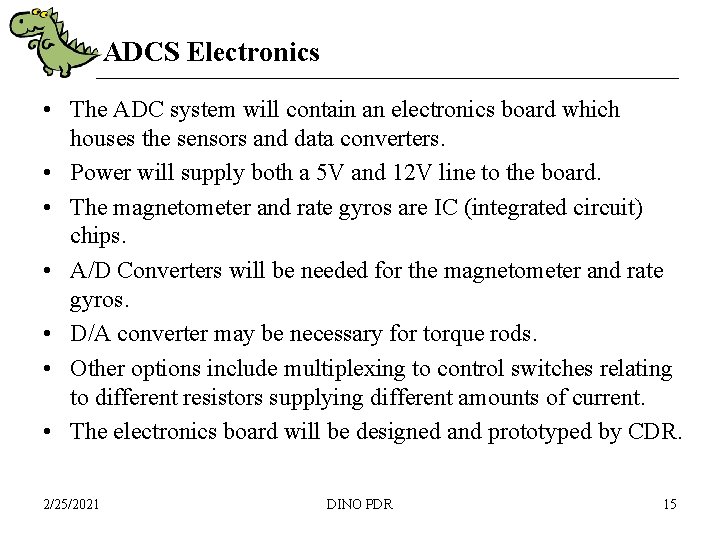
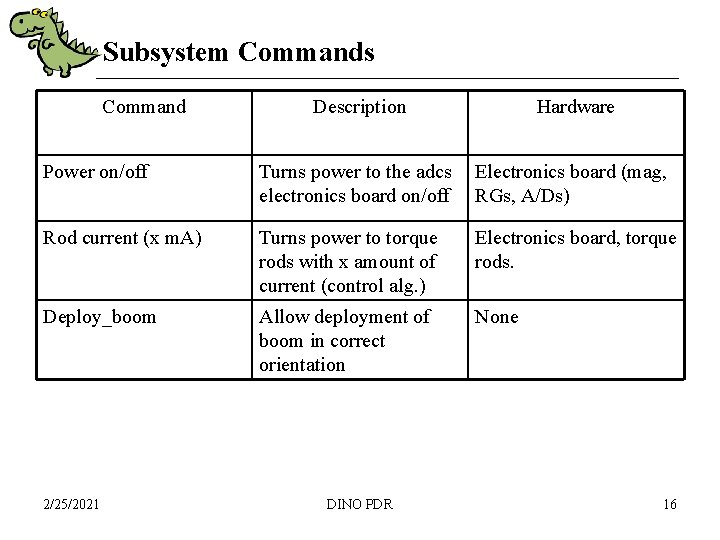
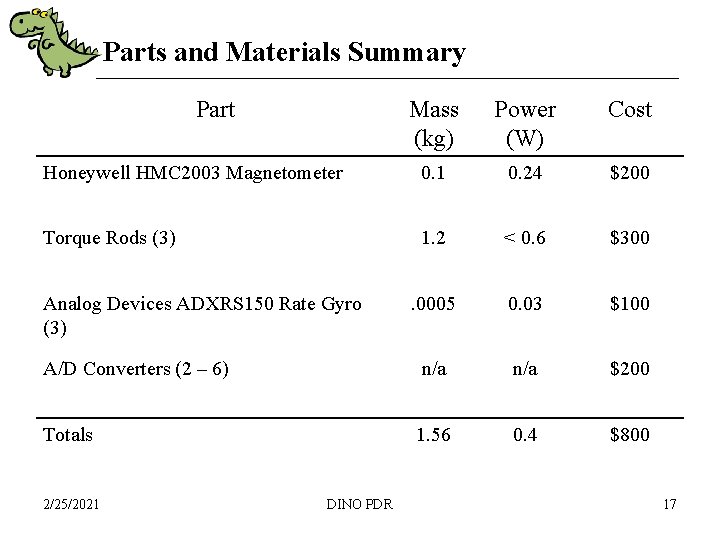
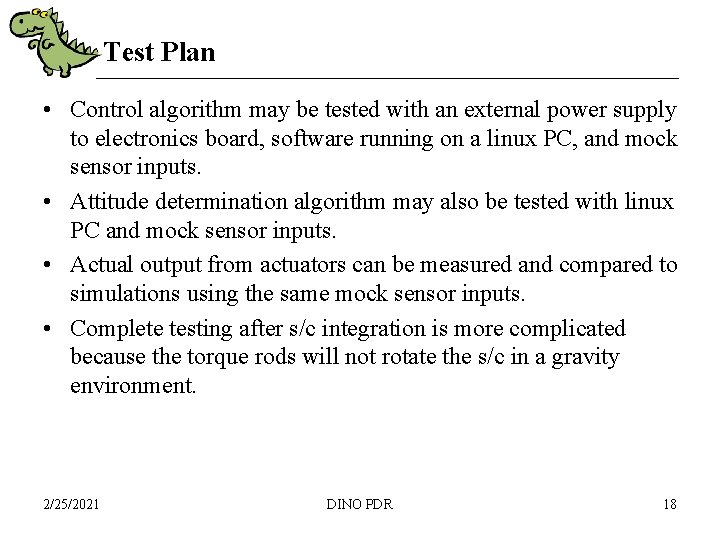
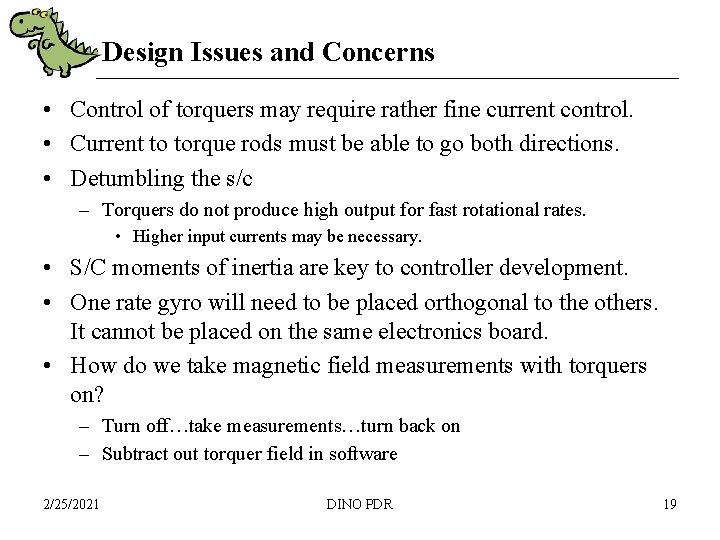
- Slides: 19
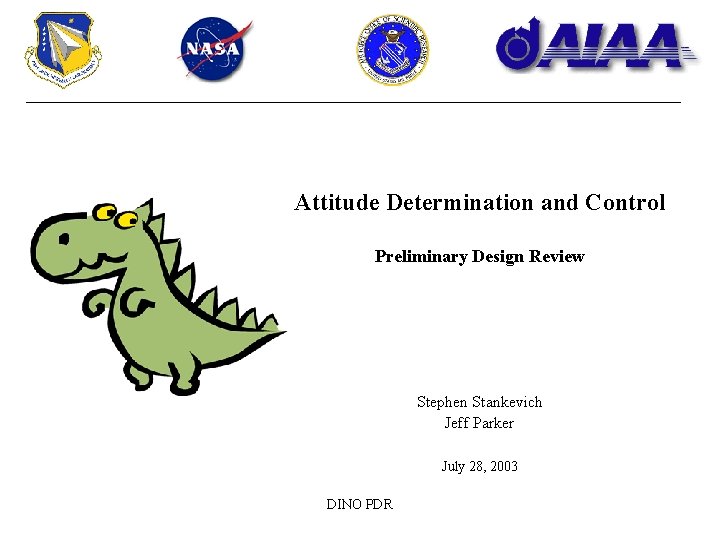
Attitude Determination and Control Preliminary Design Review Stephen Stankevich Jeff Parker July 28, 2003 DINO PDR
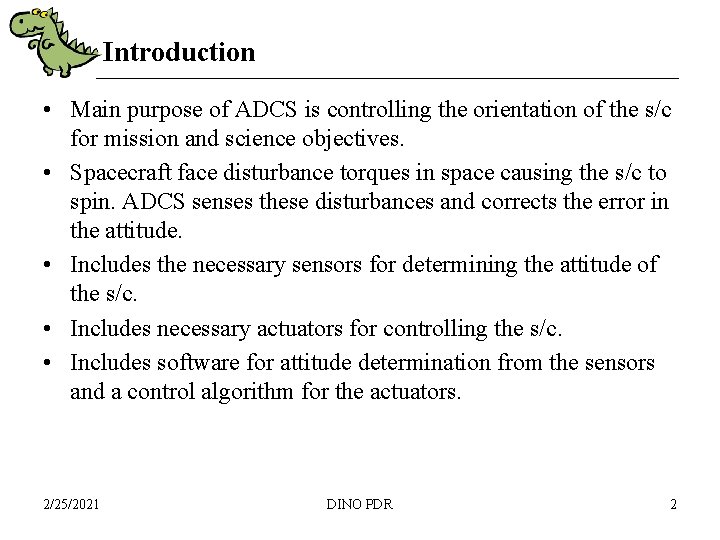
Introduction • Main purpose of ADCS is controlling the orientation of the s/c for mission and science objectives. • Spacecraft face disturbance torques in space causing the s/c to spin. ADCS senses these disturbances and corrects the error in the attitude. • Includes the necessary sensors for determining the attitude of the s/c. • Includes necessary actuators for controlling the s/c. • Includes software for attitude determination from the sensors and a control algorithm for the actuators. 2/25/2021 DINO PDR 2
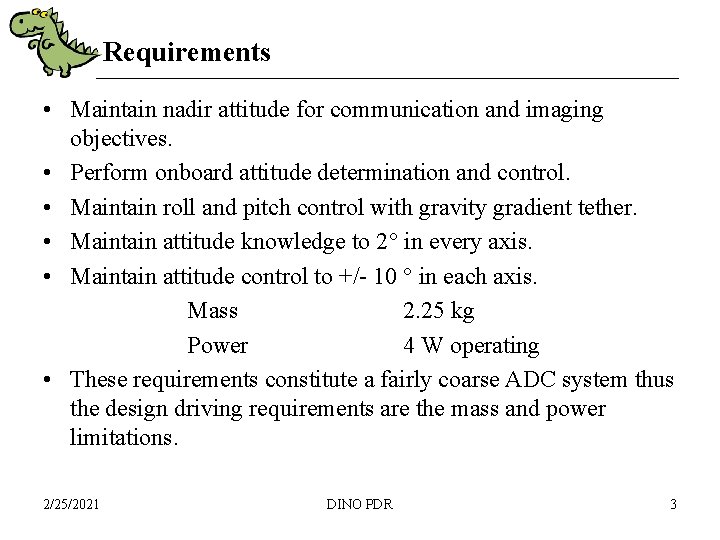
Requirements • Maintain nadir attitude for communication and imaging objectives. • Perform onboard attitude determination and control. • Maintain roll and pitch control with gravity gradient tether. • Maintain attitude knowledge to 2° in every axis. • Maintain attitude control to +/- 10 ° in each axis. Mass 2. 25 kg Power 4 W operating • These requirements constitute a fairly coarse ADC system thus the design driving requirements are the mass and power limitations. 2/25/2021 DINO PDR 3
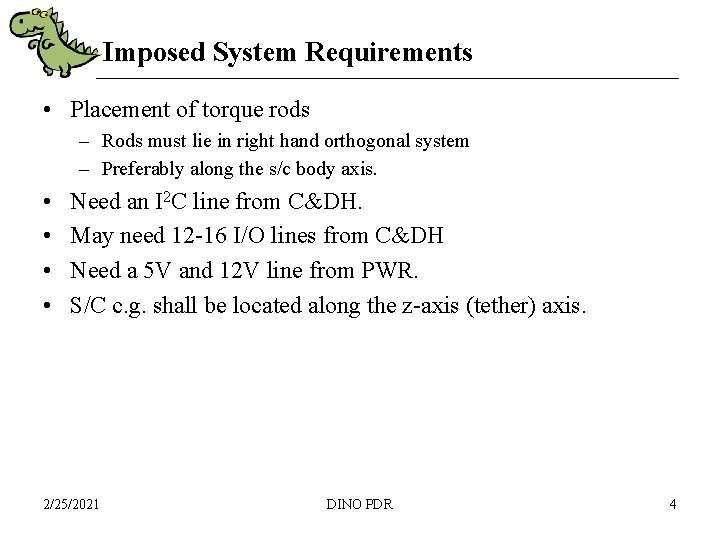
Imposed System Requirements • Placement of torque rods – Rods must lie in right hand orthogonal system – Preferably along the s/c body axis. • • Need an I 2 C line from C&DH. May need 12 -16 I/O lines from C&DH Need a 5 V and 12 V line from PWR. S/C c. g. shall be located along the z-axis (tether) axis. 2/25/2021 DINO PDR 4
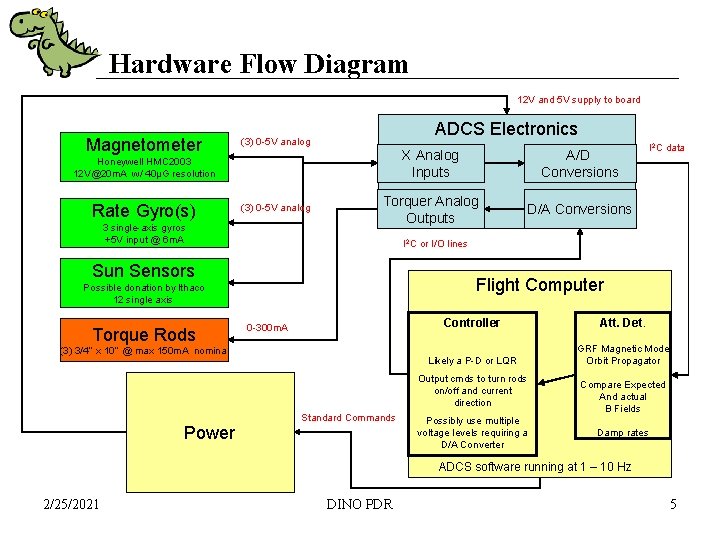
Hardware Flow Diagram 12 V and 5 V supply to board Magnetometer ADCS Electronics (3) 0 -5 V analog X Analog Inputs A/D Conversions Torquer Analog Outputs D/A Conversions Honeywell HMC 2003 12 V@20 m. A w/ 40μG resolution Rate Gyro(s) (3) 0 -5 V analog 3 single-axis gyros +5 V input @ 6 m. A I 2 C or I/O lines Sun Sensors Flight Computer Possible donation by Ithaco 12 single axis Torque Rods 0 -300 m. A (3) 3/4’’ x 10’’ @ max 150 m. A nominal Controller Att. Det. Likely a P-D or LQR IGRF Magnetic Model Orbit Propagator Output cmds to turn rods on/off and current direction Power I 2 C data Standard Commands Possibly use multiple voltage levels requiring a D/A Converter Compare Expected And actual B Fields Damp rates ADCS software running at 1 – 10 Hz 2/25/2021 DINO PDR 5
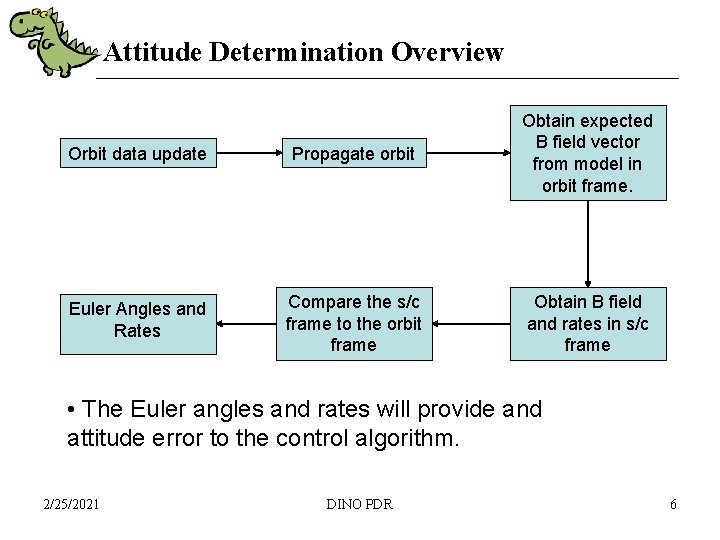
Attitude Determination Overview Orbit data update Propagate orbit Obtain expected B field vector from model in orbit frame. Euler Angles and Rates Compare the s/c frame to the orbit frame Obtain B field and rates in s/c frame • The Euler angles and rates will provide and attitude error to the control algorithm. 2/25/2021 DINO PDR 6
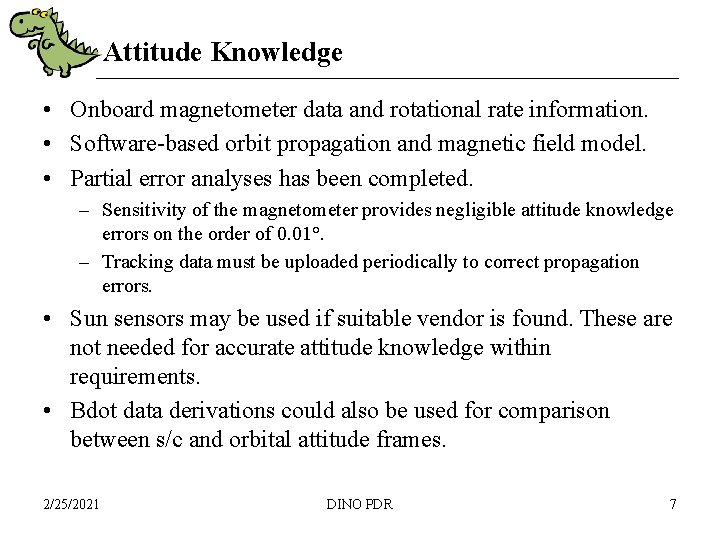
Attitude Knowledge • Onboard magnetometer data and rotational rate information. • Software-based orbit propagation and magnetic field model. • Partial error analyses has been completed. – Sensitivity of the magnetometer provides negligible attitude knowledge errors on the order of 0. 01°. – Tracking data must be uploaded periodically to correct propagation errors. • Sun sensors may be used if suitable vendor is found. These are not needed for accurate attitude knowledge within requirements. • Bdot data derivations could also be used for comparison between s/c and orbital attitude frames. 2/25/2021 DINO PDR 7
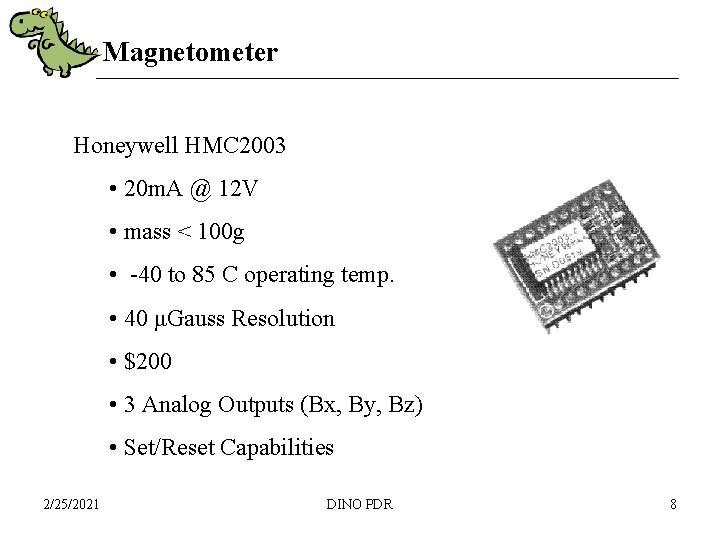
Magnetometer Honeywell HMC 2003 • 20 m. A @ 12 V • mass < 100 g • -40 to 85 C operating temp. • 40 μGauss Resolution • $200 • 3 Analog Outputs (Bx, By, Bz) • Set/Reset Capabilities 2/25/2021 DINO PDR 8
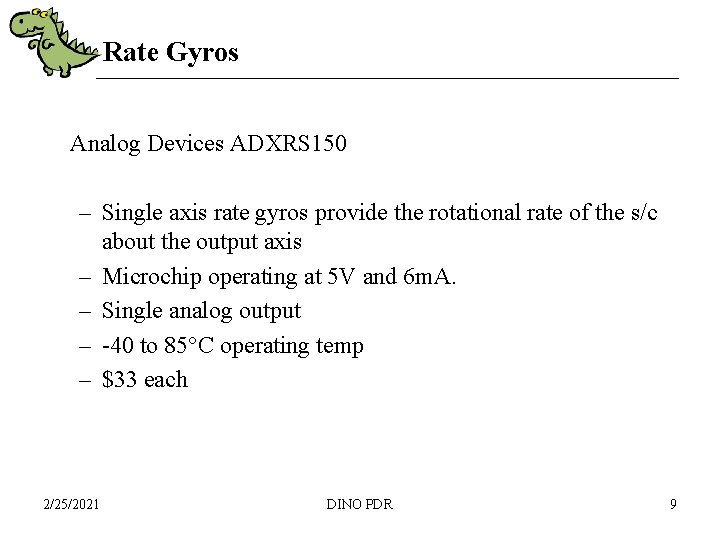
Rate Gyros Analog Devices ADXRS 150 – Single axis rate gyros provide the rotational rate of the s/c about the output axis – Microchip operating at 5 V and 6 m. A. – Single analog output – -40 to 85°C operating temp – $33 each 2/25/2021 DINO PDR 9
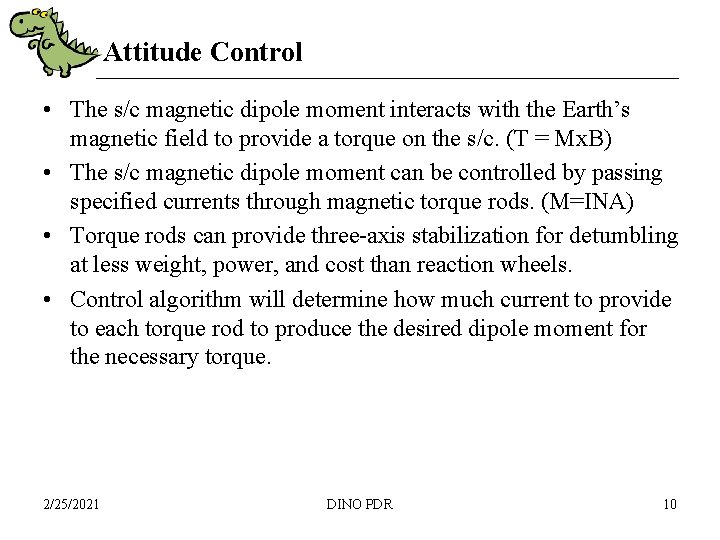
Attitude Control • The s/c magnetic dipole moment interacts with the Earth’s magnetic field to provide a torque on the s/c. (T = Mx. B) • The s/c magnetic dipole moment can be controlled by passing specified currents through magnetic torque rods. (M=INA) • Torque rods can provide three-axis stabilization for detumbling at less weight, power, and cost than reaction wheels. • Control algorithm will determine how much current to provide to each torque rod to produce the desired dipole moment for the necessary torque. 2/25/2021 DINO PDR 10
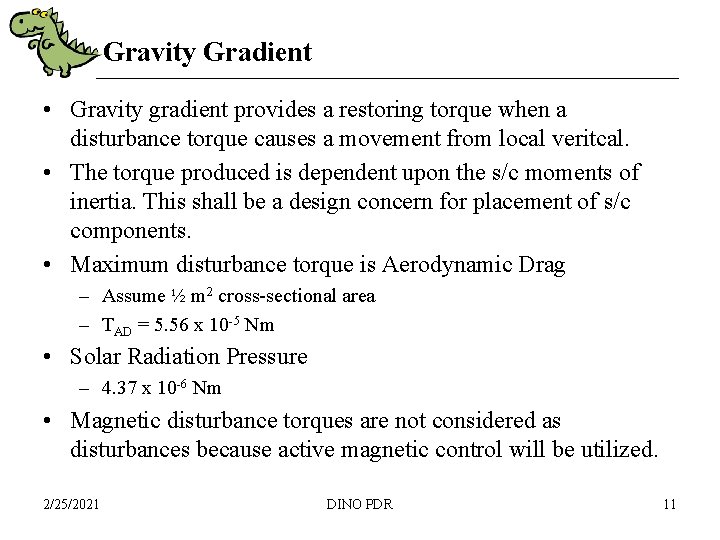
Gravity Gradient • Gravity gradient provides a restoring torque when a disturbance torque causes a movement from local veritcal. • The torque produced is dependent upon the s/c moments of inertia. This shall be a design concern for placement of s/c components. • Maximum disturbance torque is Aerodynamic Drag – Assume ½ m 2 cross-sectional area – TAD = 5. 56 x 10 -5 Nm • Solar Radiation Pressure – 4. 37 x 10 -6 Nm • Magnetic disturbance torques are not considered as disturbances because active magnetic control will be utilized. 2/25/2021 DINO PDR 11
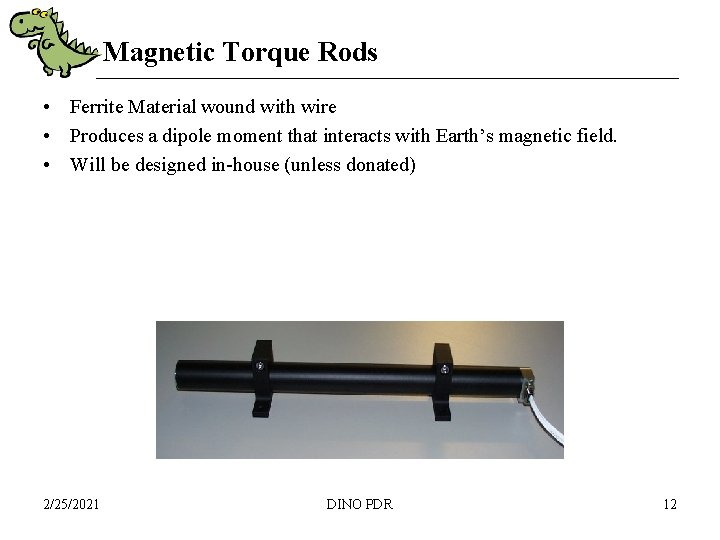
Magnetic Torque Rods • Ferrite Material wound with wire • Produces a dipole moment that interacts with Earth’s magnetic field. • Will be designed in-house (unless donated) 2/25/2021 DINO PDR 12
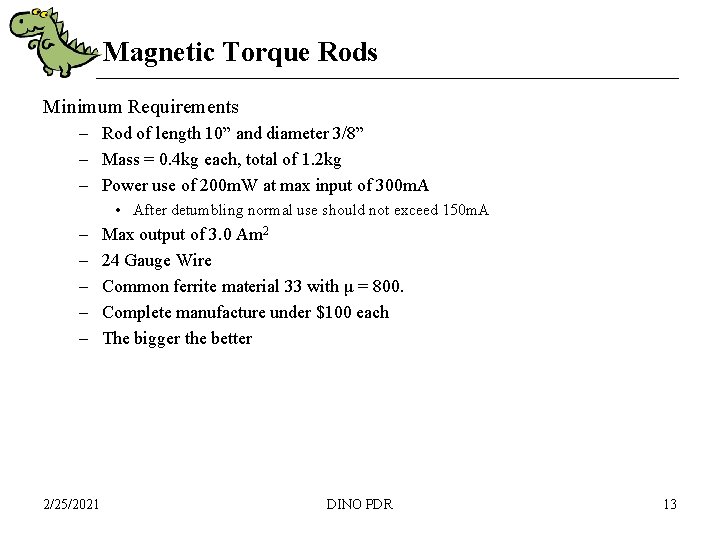
Magnetic Torque Rods Minimum Requirements – Rod of length 10” and diameter 3/8” – Mass = 0. 4 kg each, total of 1. 2 kg – Power use of 200 m. W at max input of 300 m. A • After detumbling normal use should not exceed 150 m. A – – – 2/25/2021 Max output of 3. 0 Am 2 24 Gauge Wire Common ferrite material 33 with μ = 800. Complete manufacture under $100 each The bigger the better DINO PDR 13
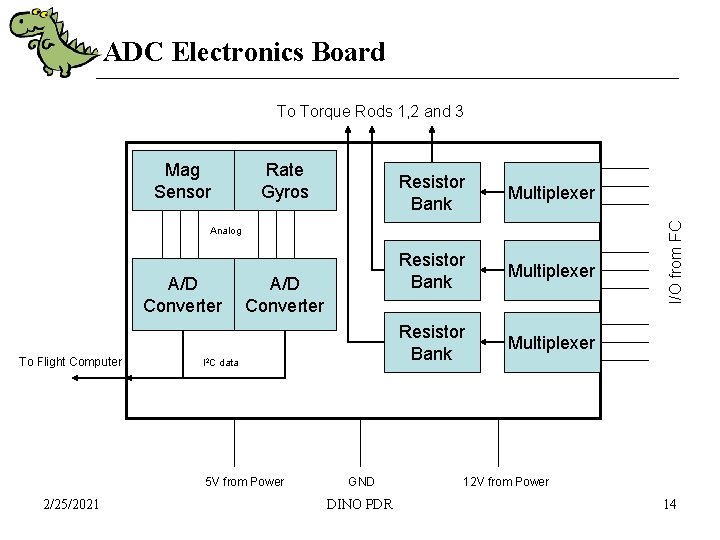
ADC Electronics Board Mag Sensor Rate Gyros Resistor Bank Multiplexer Analog A/D Converter To Flight Computer I 2 C A/D Converter data 5 V from Power 2/25/2021 GND DINO PDR I/O from FC To Torque Rods 1, 2 and 3 12 V from Power 14
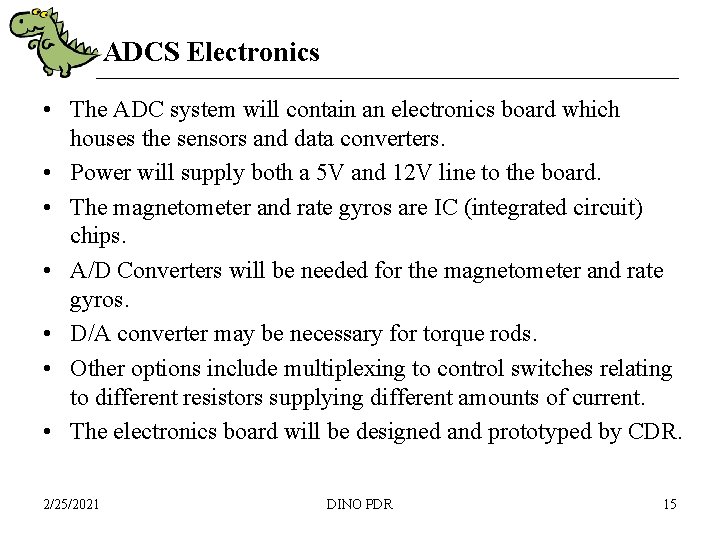
ADCS Electronics • The ADC system will contain an electronics board which houses the sensors and data converters. • Power will supply both a 5 V and 12 V line to the board. • The magnetometer and rate gyros are IC (integrated circuit) chips. • A/D Converters will be needed for the magnetometer and rate gyros. • D/A converter may be necessary for torque rods. • Other options include multiplexing to control switches relating to different resistors supplying different amounts of current. • The electronics board will be designed and prototyped by CDR. 2/25/2021 DINO PDR 15
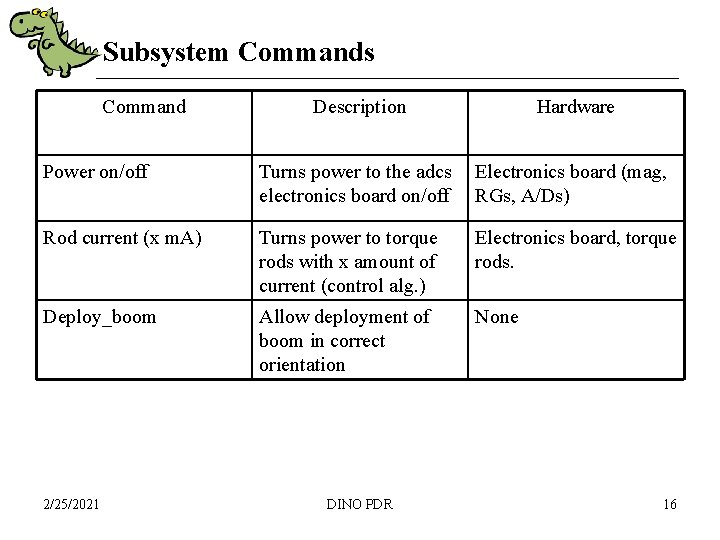
Subsystem Commands Command Description Hardware Power on/off Turns power to the adcs electronics board on/off Electronics board (mag, RGs, A/Ds) Rod current (x m. A) Turns power to torque rods with x amount of current (control alg. ) Electronics board, torque rods. Deploy_boom Allow deployment of boom in correct orientation None 2/25/2021 DINO PDR 16
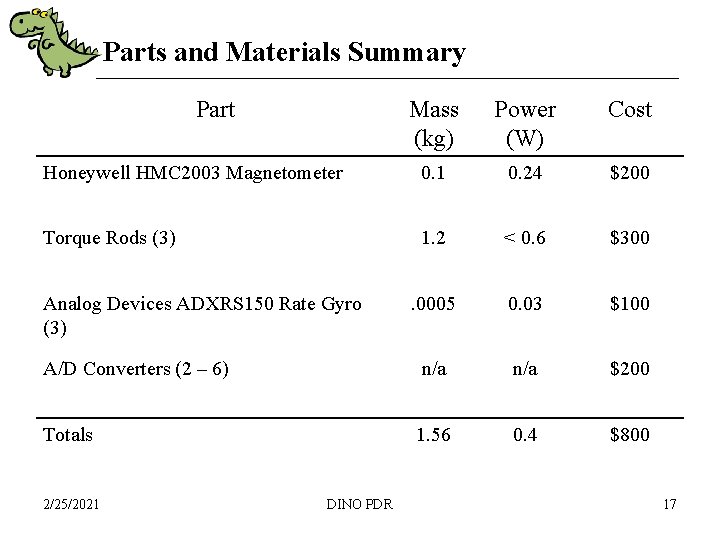
Parts and Materials Summary Part Mass (kg) Power (W) Cost Honeywell HMC 2003 Magnetometer 0. 1 0. 24 $200 Torque Rods (3) 1. 2 < 0. 6 $300 . 0005 0. 03 $100 A/D Converters (2 – 6) n/a $200 Totals 1. 56 0. 4 $800 Analog Devices ADXRS 150 Rate Gyro (3) 2/25/2021 DINO PDR 17
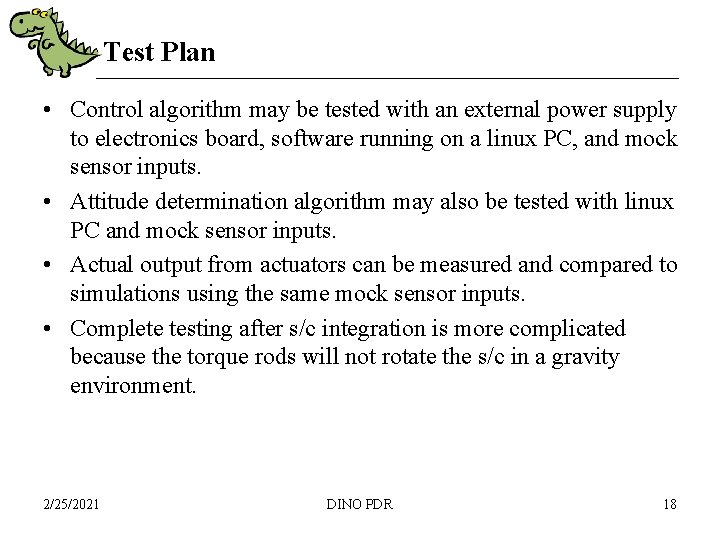
Test Plan • Control algorithm may be tested with an external power supply to electronics board, software running on a linux PC, and mock sensor inputs. • Attitude determination algorithm may also be tested with linux PC and mock sensor inputs. • Actual output from actuators can be measured and compared to simulations using the same mock sensor inputs. • Complete testing after s/c integration is more complicated because the torque rods will not rotate the s/c in a gravity environment. 2/25/2021 DINO PDR 18
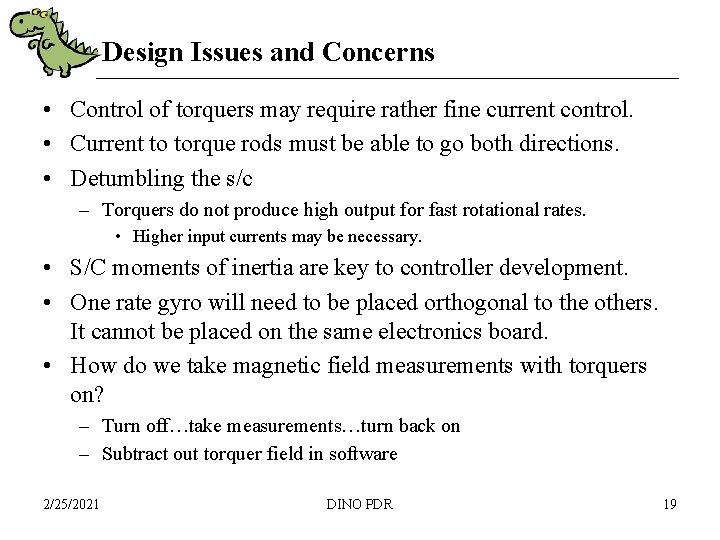
Design Issues and Concerns • Control of torquers may require rather fine current control. • Current to torque rods must be able to go both directions. • Detumbling the s/c – Torquers do not produce high output for fast rotational rates. • Higher input currents may be necessary. • S/C moments of inertia are key to controller development. • One rate gyro will need to be placed orthogonal to the others. It cannot be placed on the same electronics board. • How do we take magnetic field measurements with torquers on? – Turn off…take measurements…turn back on – Subtract out torquer field in software 2/25/2021 DINO PDR 19
Preliminary design review example
Pdr preliminary design review
Preliminary design review example
ñporo
Quality determination
Process design and control design should always be in
Waterfall and sprinkler strategy
Preliminary cooking and flavoring
Acs attitude control system
Lain peterson
Preliminary budget
Preliminary treatment adalah
Preliminary survey audit
P 波
Preliminary materials
Preliminary outline example
Preliminary interview
Broad problem examples
Hopi corporation expects the following
Blangkong pahina bago ang katawan ng pamanahong-papel. *