Thermal Shield Update Niklas Templeton 150216 final update
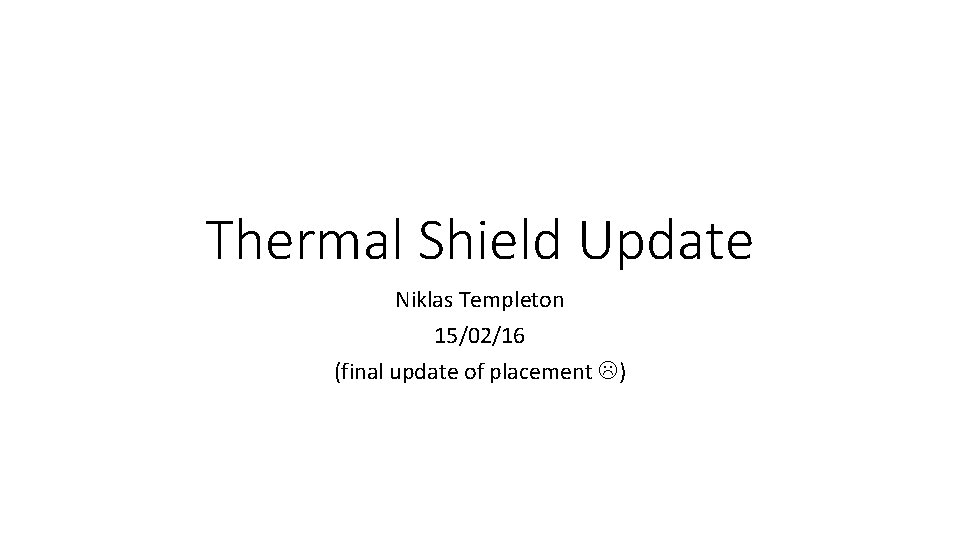
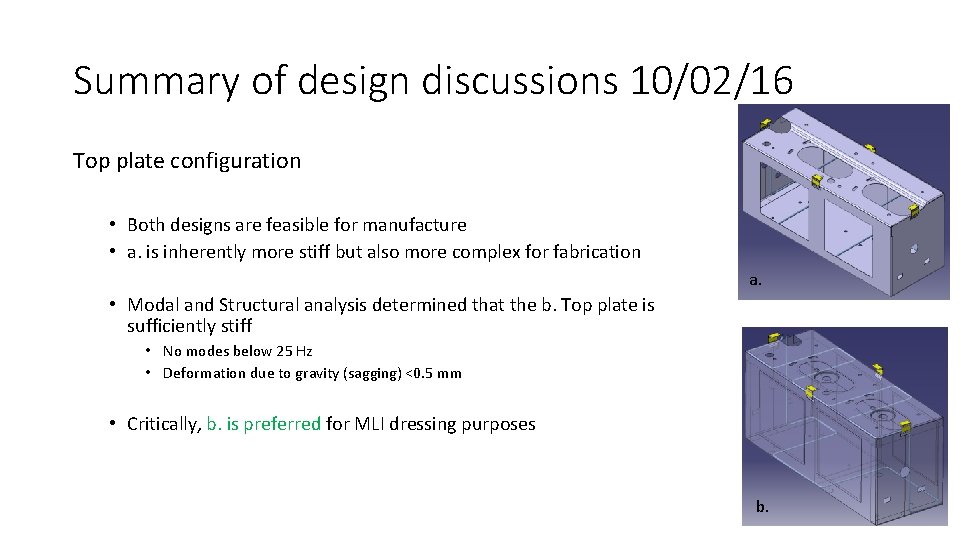
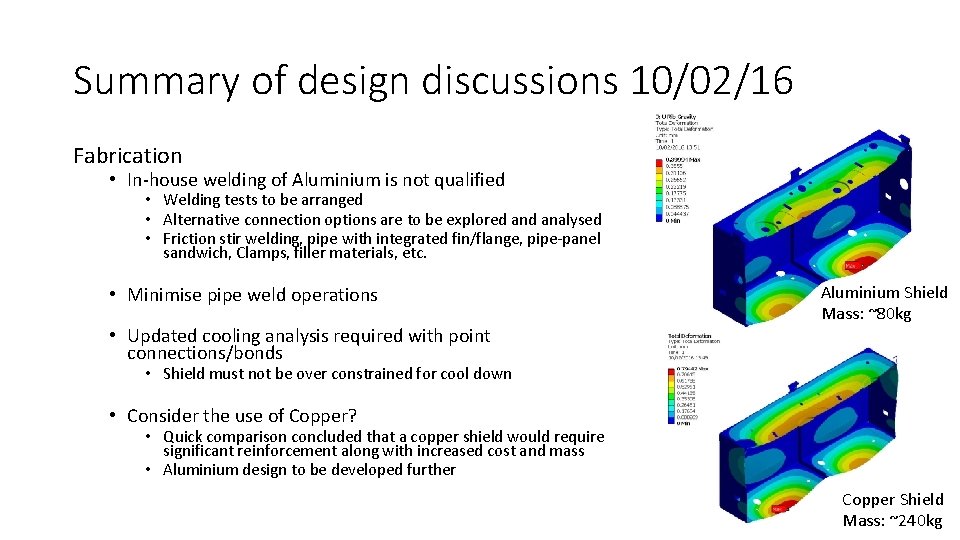
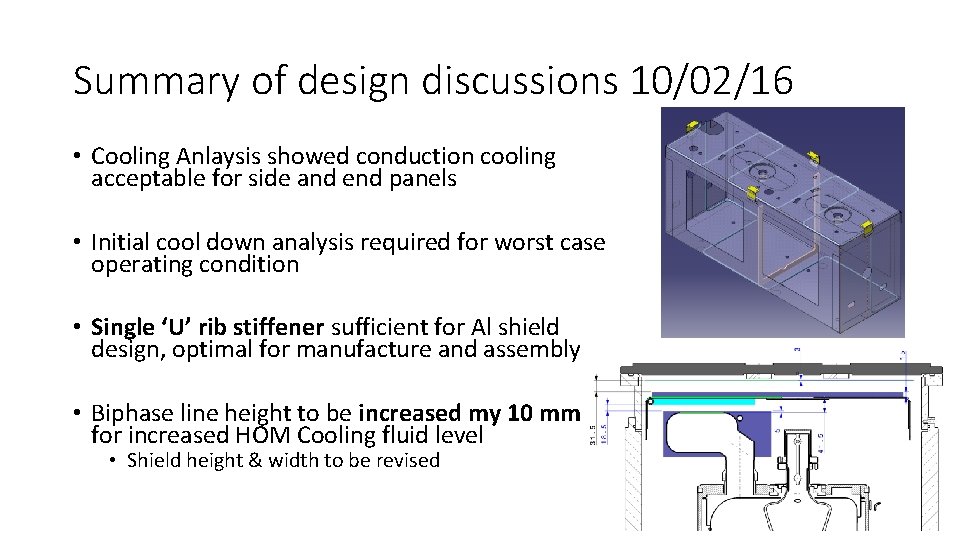
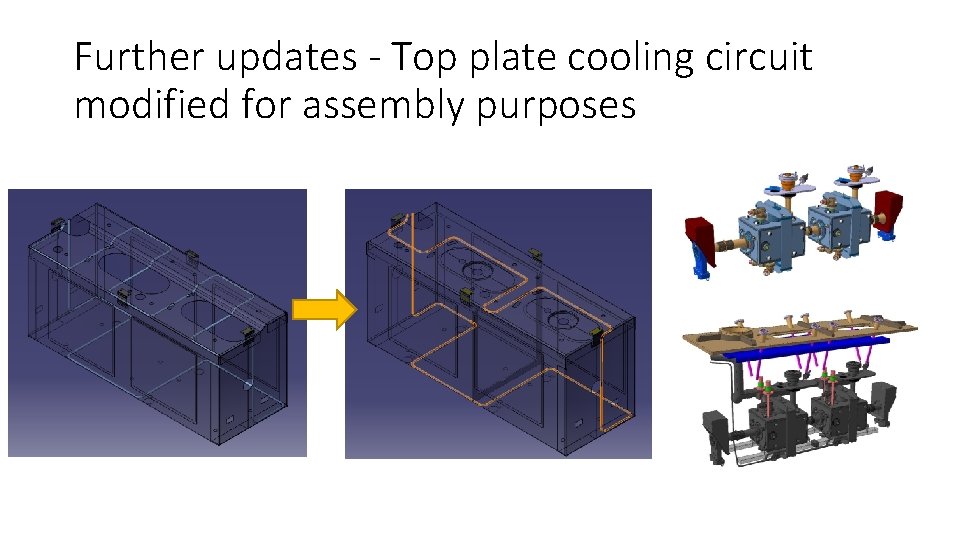
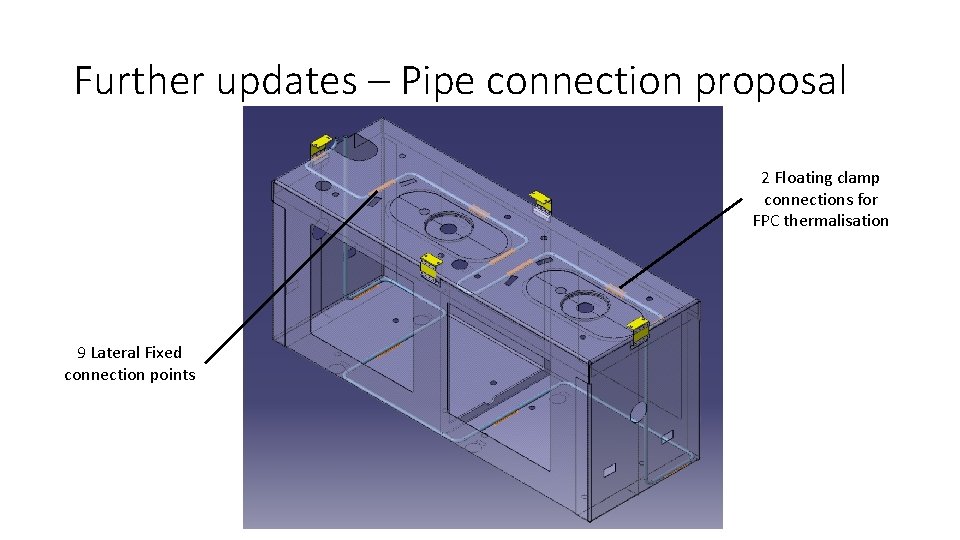
- Slides: 6
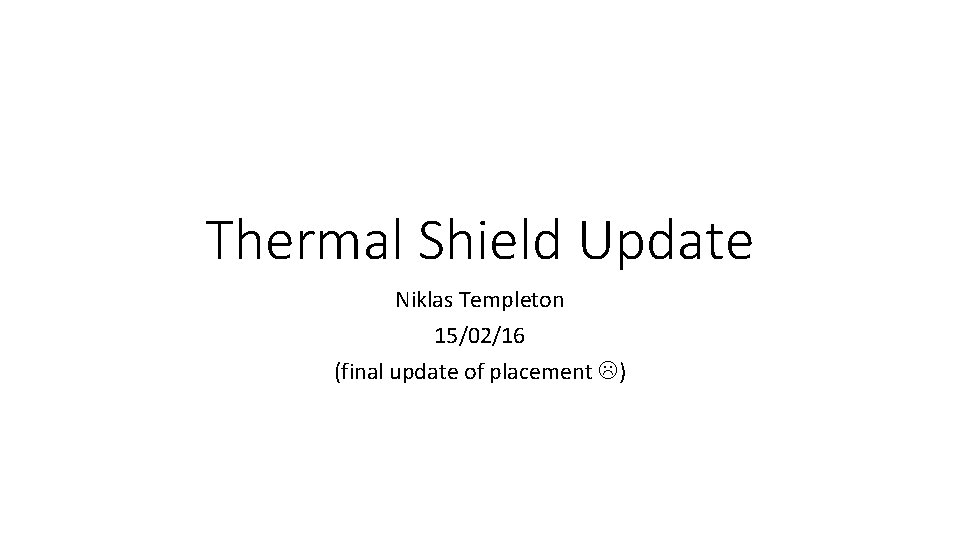
Thermal Shield Update Niklas Templeton 15/02/16 (final update of placement )
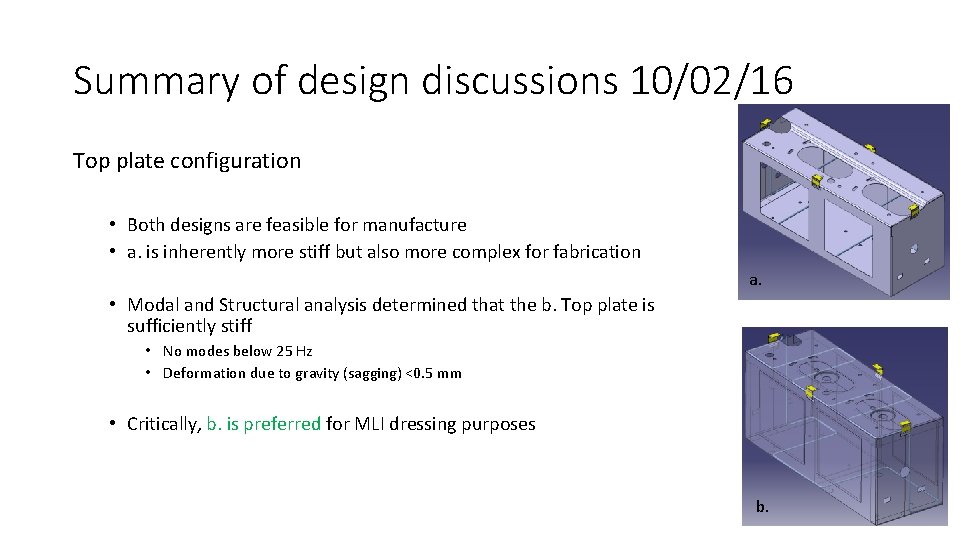
Summary of design discussions 10/02/16 Top plate configuration • Both designs are feasible for manufacture • a. is inherently more stiff but also more complex for fabrication a. • Modal and Structural analysis determined that the b. Top plate is sufficiently stiff • No modes below 25 Hz • Deformation due to gravity (sagging) <0. 5 mm • Critically, b. is preferred for MLI dressing purposes b.
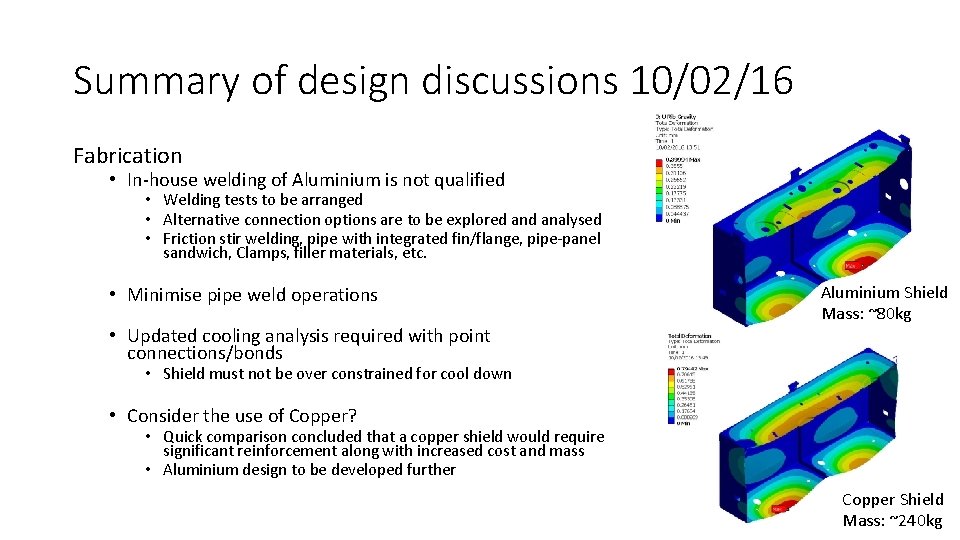
Summary of design discussions 10/02/16 Fabrication • In-house welding of Aluminium is not qualified • Welding tests to be arranged • Alternative connection options are to be explored analysed • Friction stir welding, pipe with integrated fin/flange, pipe-panel sandwich, Clamps, filler materials, etc. • Minimise pipe weld operations • Updated cooling analysis required with point connections/bonds Aluminium Shield Mass: ~80 kg • Shield must not be over constrained for cool down • Consider the use of Copper? • Quick comparison concluded that a copper shield would require significant reinforcement along with increased cost and mass • Aluminium design to be developed further Copper Shield Mass: ~240 kg
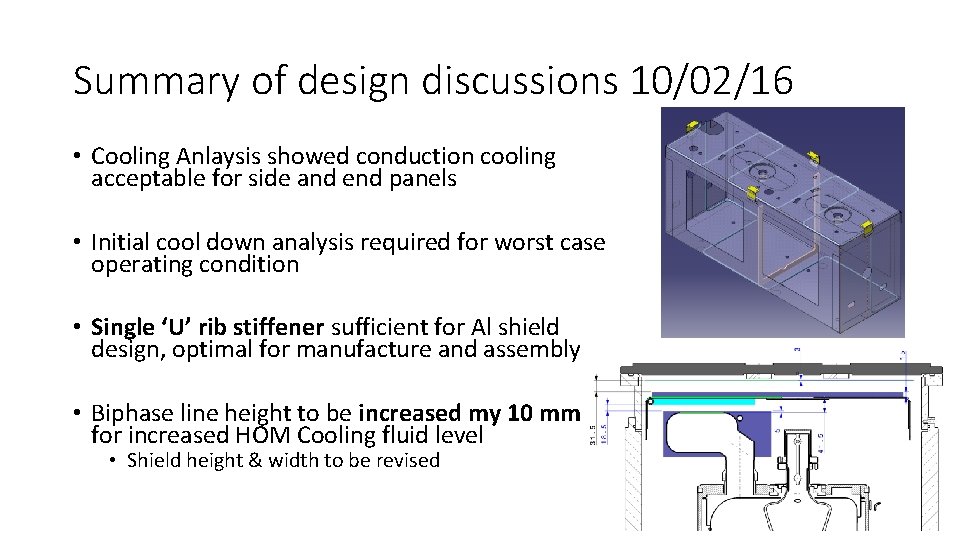
Summary of design discussions 10/02/16 • Cooling Anlaysis showed conduction cooling acceptable for side and end panels • Initial cool down analysis required for worst case operating condition • Single ‘U’ rib stiffener sufficient for Al shield design, optimal for manufacture and assembly • Biphase line height to be increased my 10 mm for increased HOM Cooling fluid level • Shield height & width to be revised
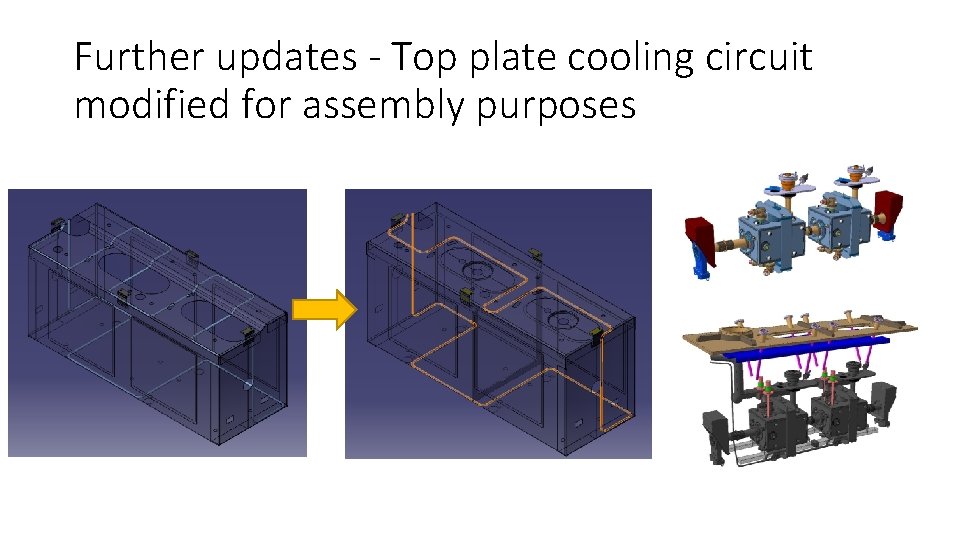
Further updates - Top plate cooling circuit modified for assembly purposes
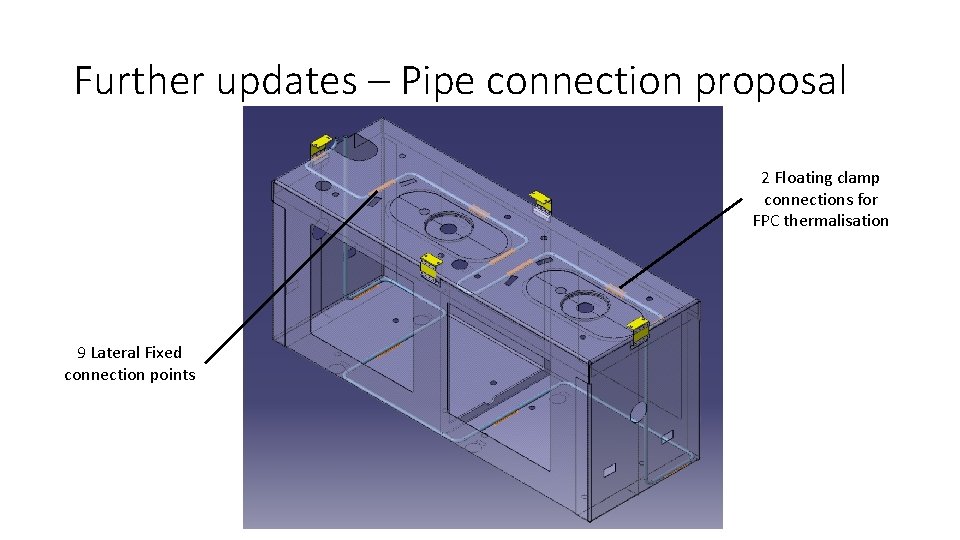
Further updates – Pipe connection proposal 2 Floating clamp connections for FPC thermalisation 9 Lateral Fixed connection points