The Green Coil Cleaner Coil Cleaning Demo At
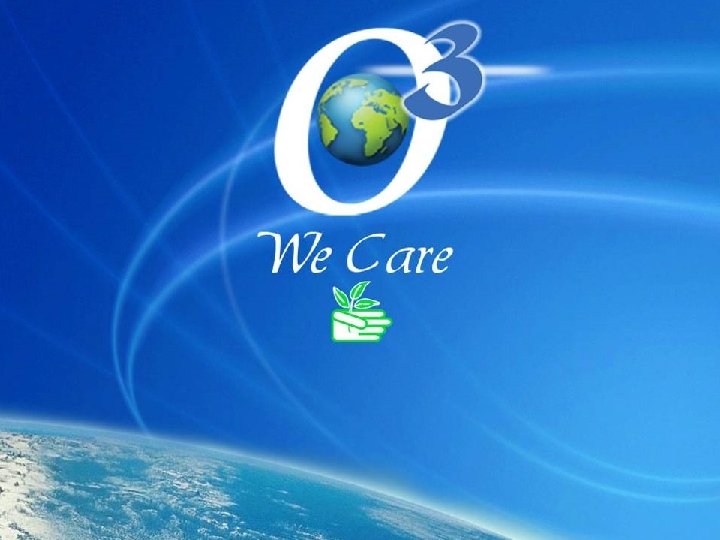
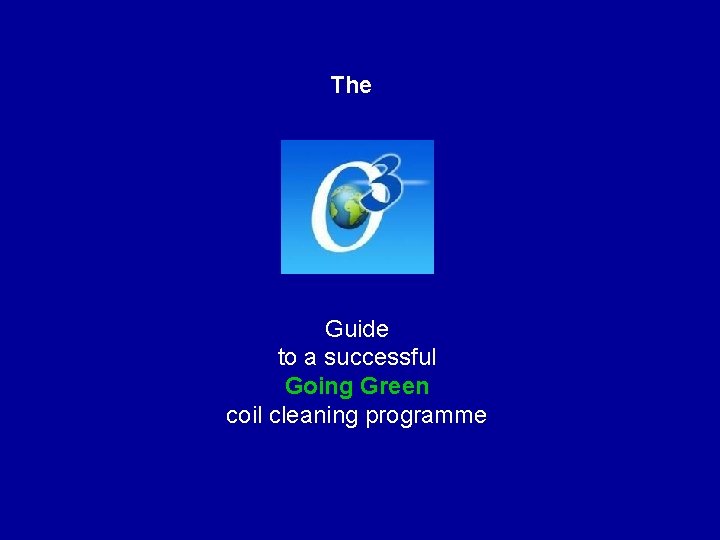
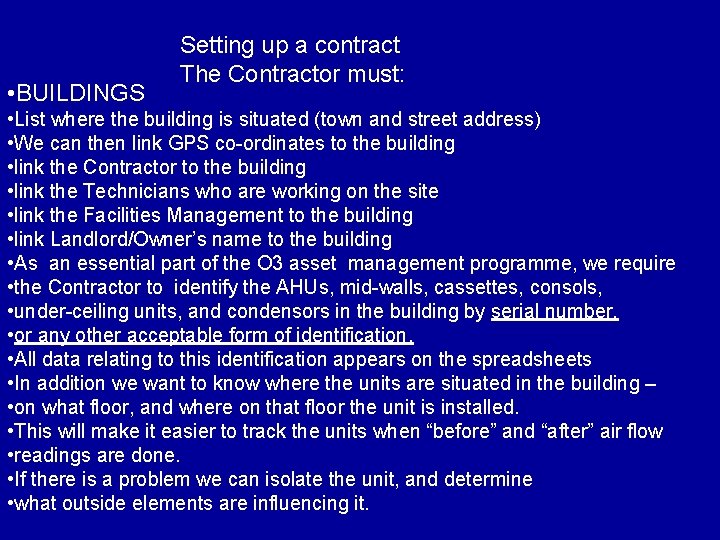
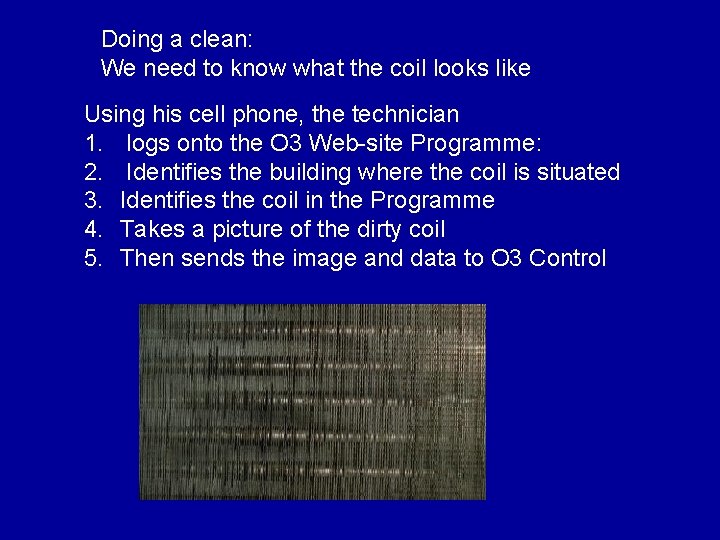
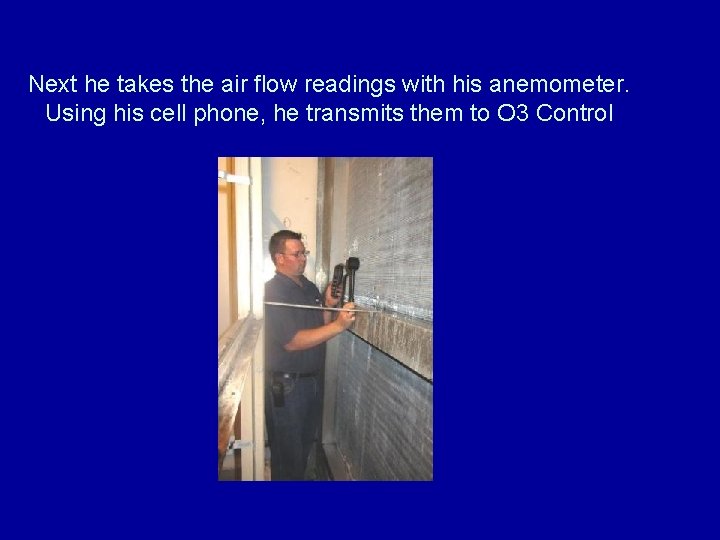
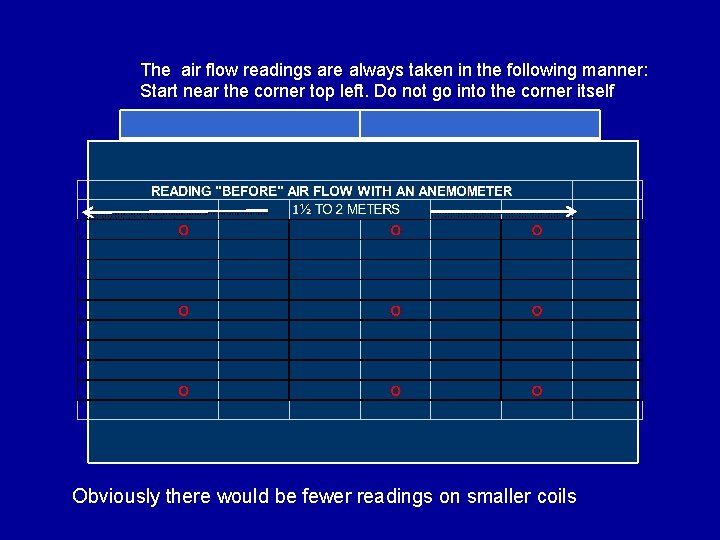
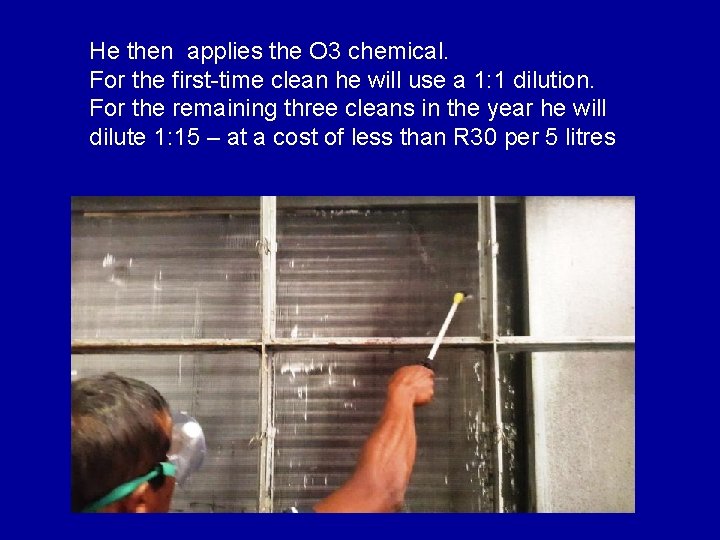
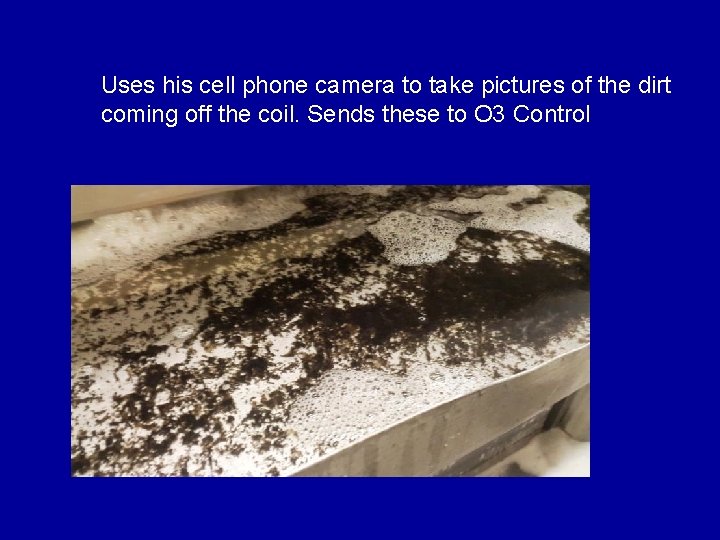
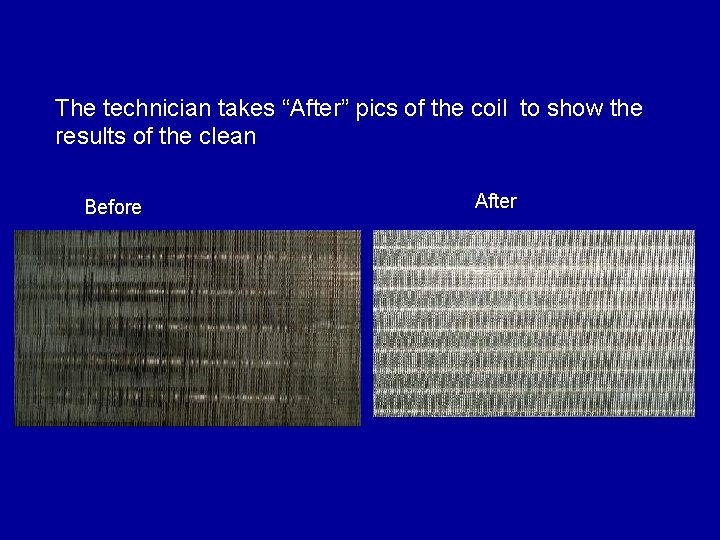
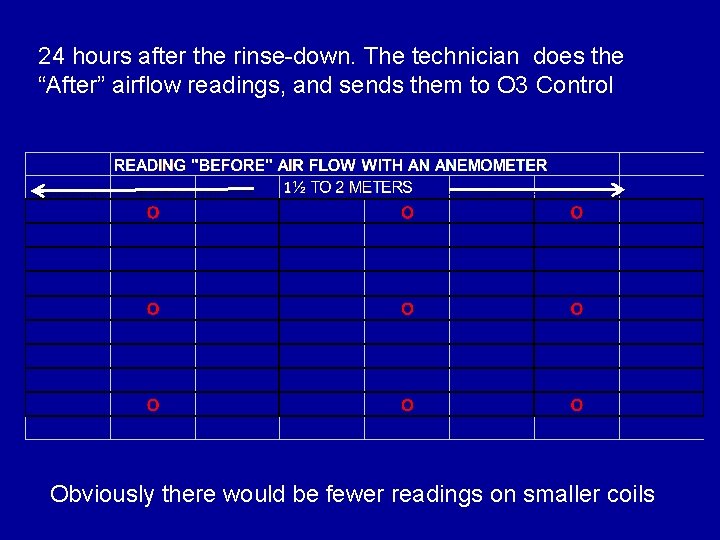
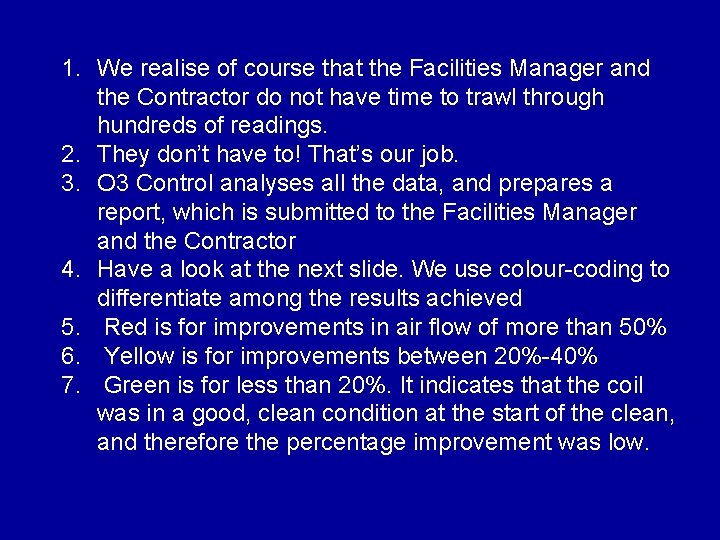
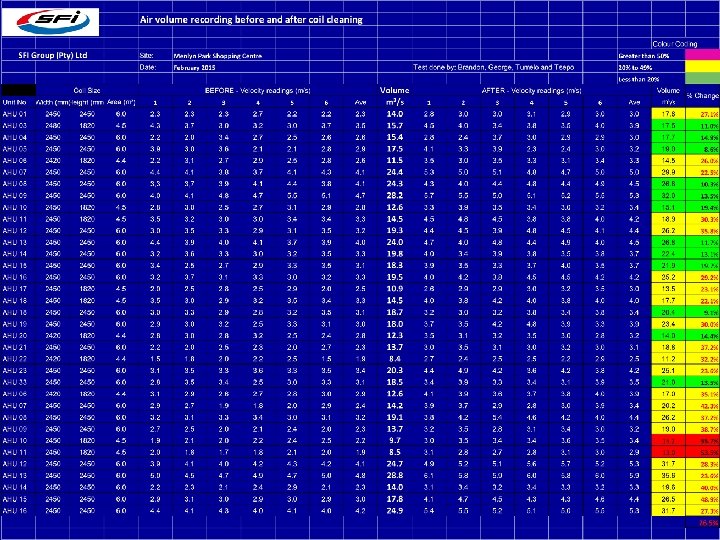
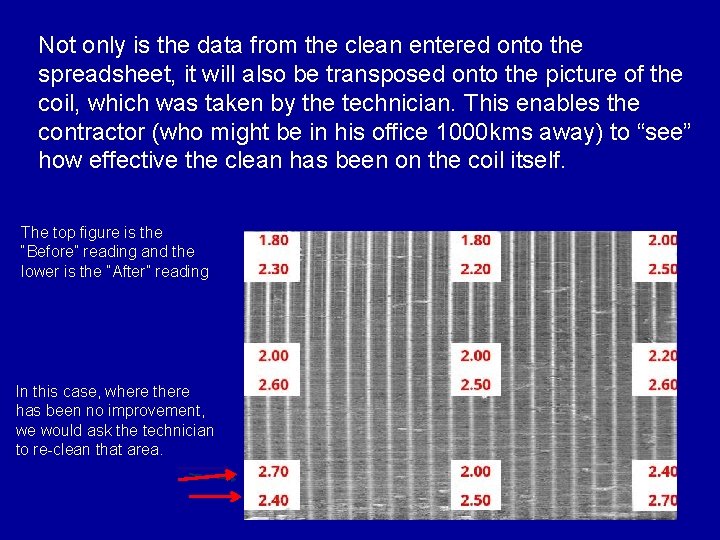
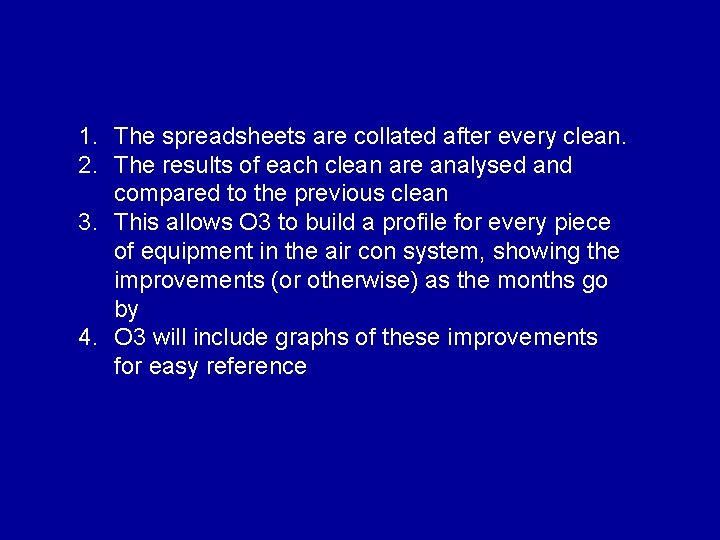
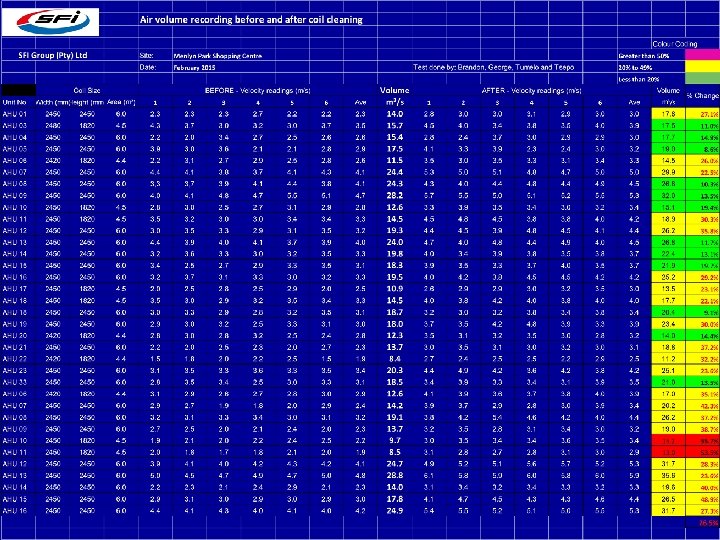
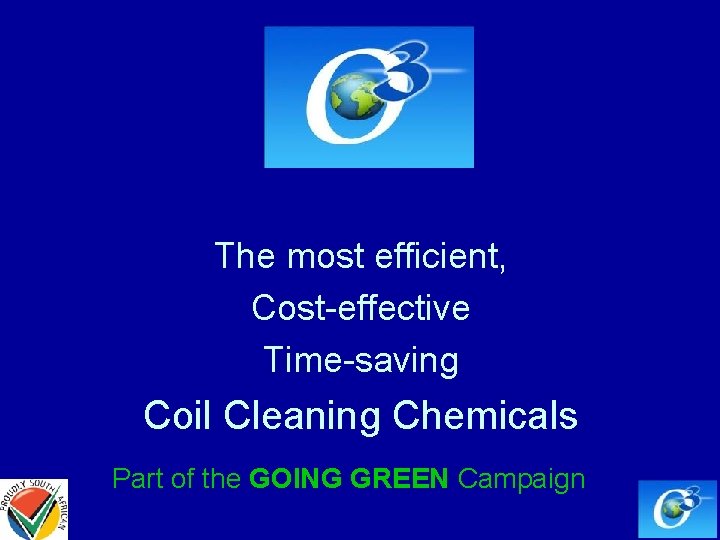
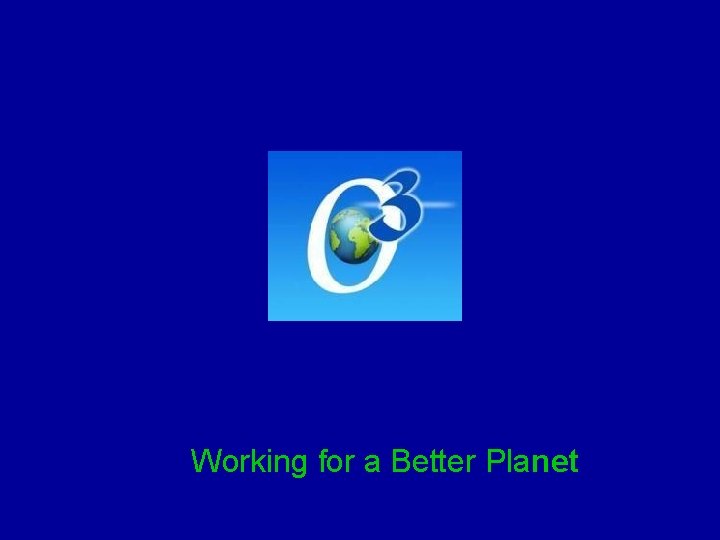
- Slides: 17
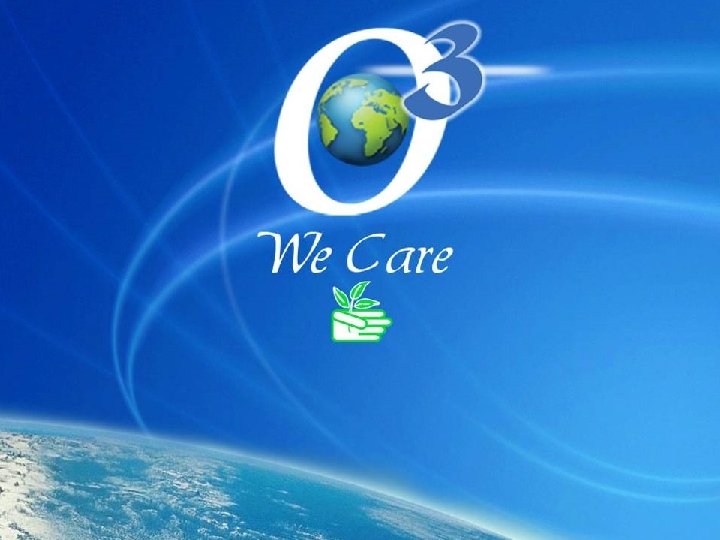
The Green Coil Cleaner Coil Cleaning Demo At V & A Waterfront in Cape Town
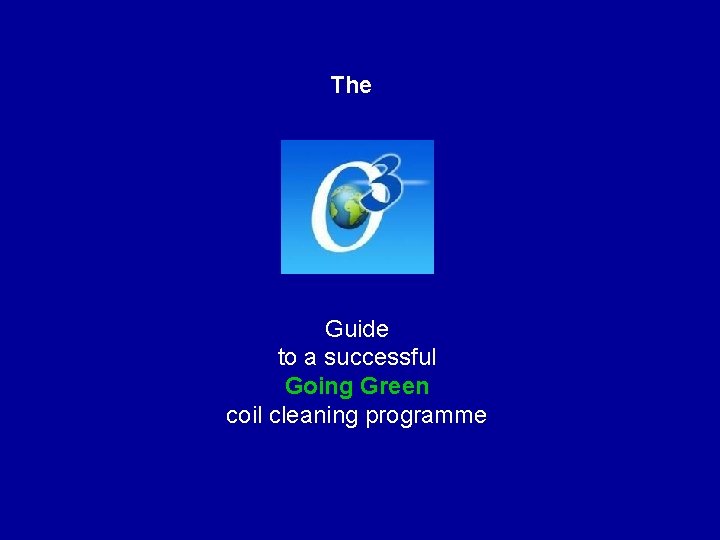
The Guide to a successful Going Green coil cleaning programme
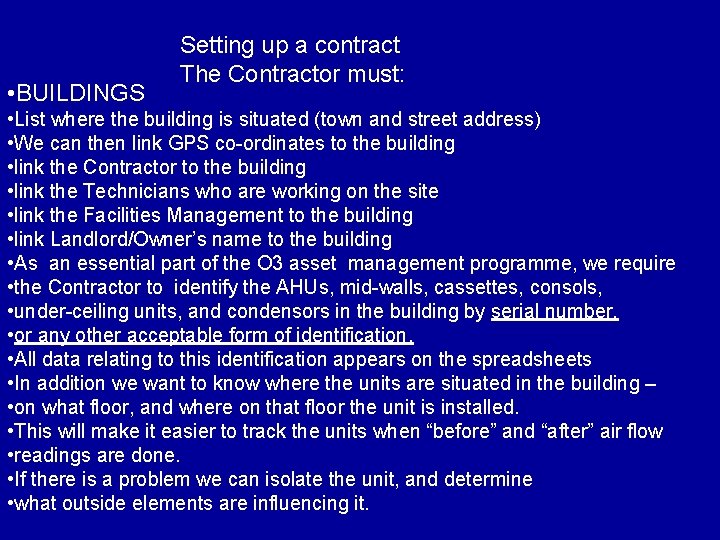
• BUILDINGS Setting up a contract The Contractor must: • List where the building is situated (town and street address) • We can then link GPS co-ordinates to the building • link the Contractor to the building • link the Technicians who are working on the site • link the Facilities Management to the building • link Landlord/Owner’s name to the building • As an essential part of the O 3 asset management programme, we require • the Contractor to identify the AHUs, mid-walls, cassettes, consols, • under-ceiling units, and condensors in the building by serial number, • or any other acceptable form of identification. • All data relating to this identification appears on the spreadsheets • In addition we want to know where the units are situated in the building – • on what floor, and where on that floor the unit is installed. • This will make it easier to track the units when “before” and “after” air flow • readings are done. • If there is a problem we can isolate the unit, and determine • what outside elements are influencing it.
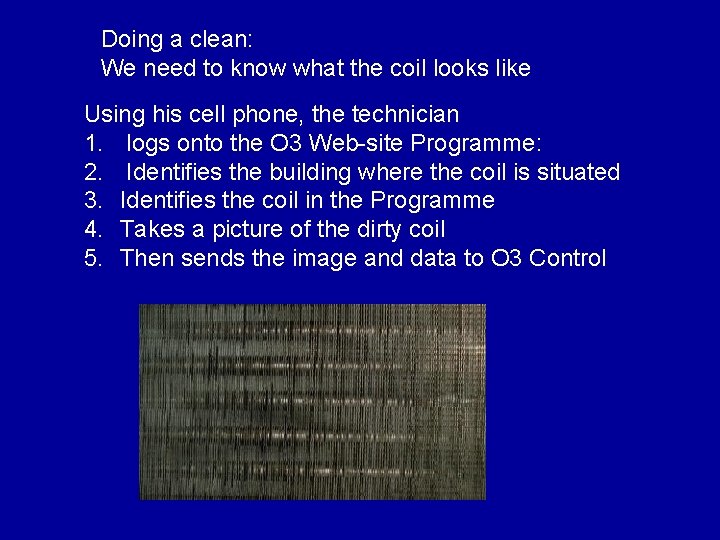
Doing a clean: We need to know what the coil looks like Using his cell phone, the technician 1. logs onto the O 3 Web-site Programme: 2. Identifies the building where the coil is situated 3. Identifies the coil in the Programme 4. Takes a picture of the dirty coil 5. Then sends the image and data to O 3 Control
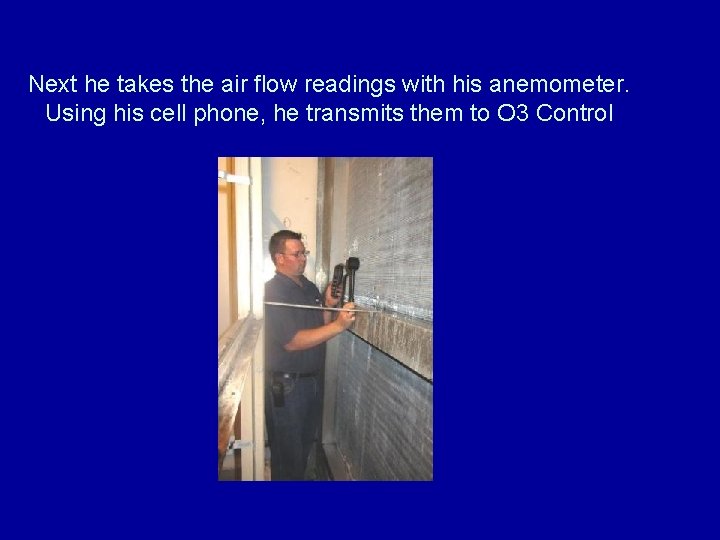
Next he takes the air flow readings with his anemometer. Using his cell phone, he transmits them to O 3 Control
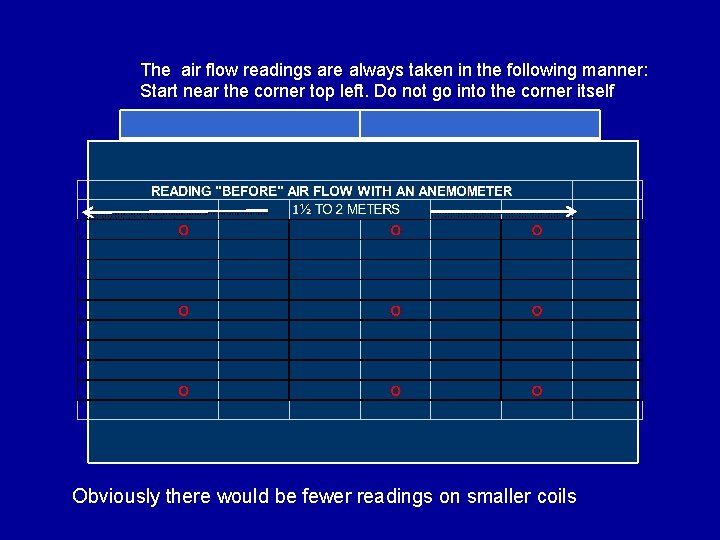
The air flow readings are always taken in the following manner: Start near the corner top left. Do not go into the corner itself Obviously there would be fewer readings on smaller coils
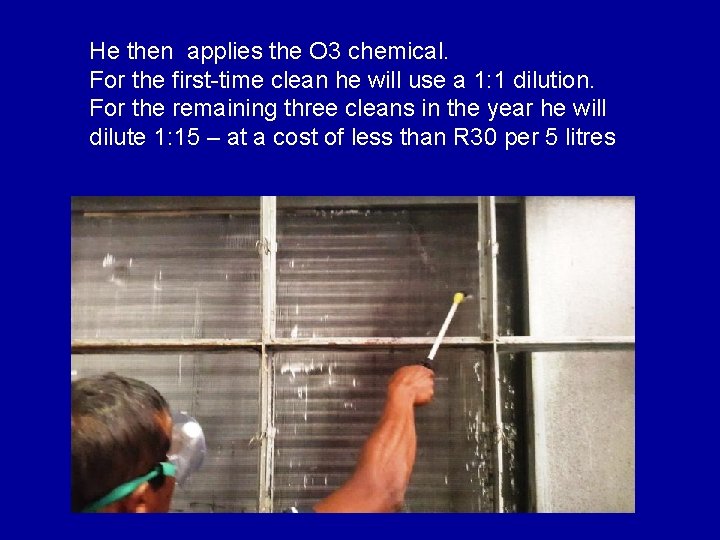
He then applies the O 3 chemical. For the first-time clean he will use a 1: 1 dilution. For the remaining three cleans in the year he will dilute 1: 15 – at a cost of less than R 30 per 5 litres
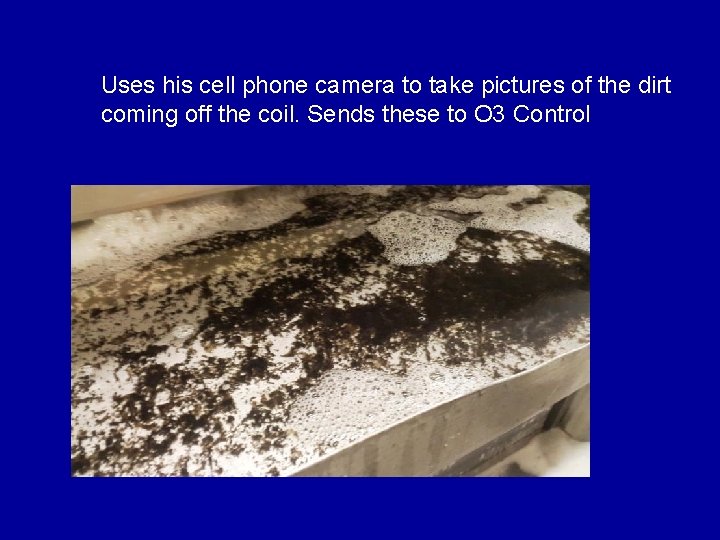
Uses his cell phone camera to take pictures of the dirt coming off the coil. Sends these to O 3 Control
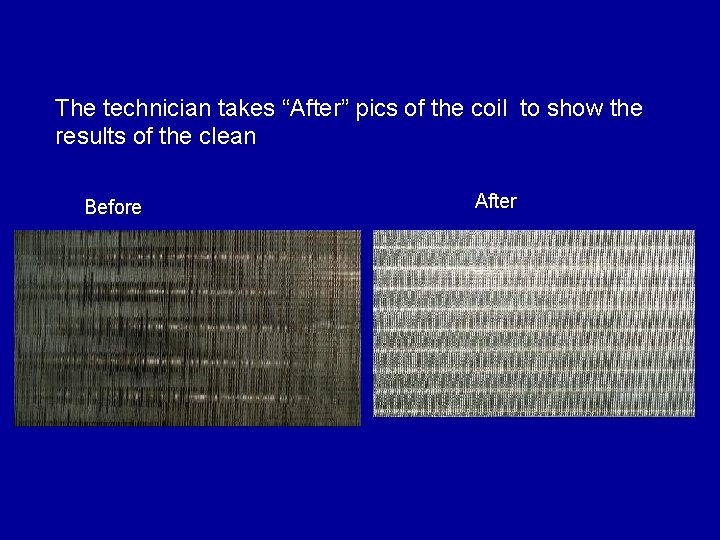
The technician takes “After” pics of the coil to show the results of the clean Before After
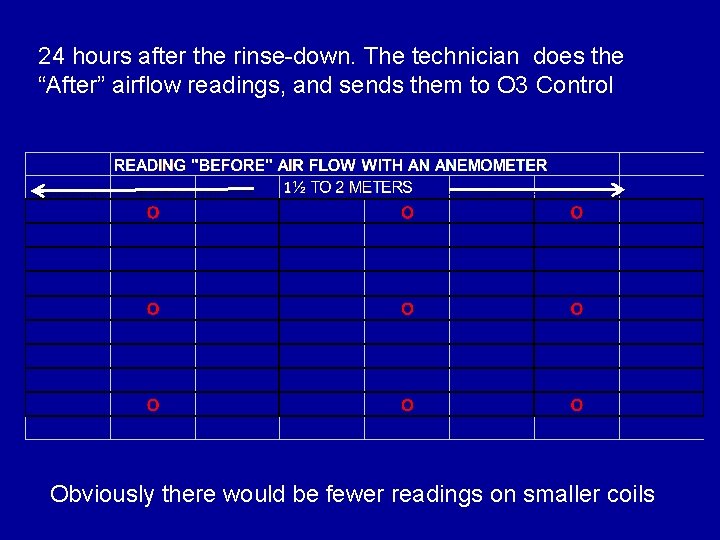
24 hours after the rinse-down. The technician does the “After” airflow readings, and sends them to O 3 Control Obviously there would be fewer readings on smaller coils
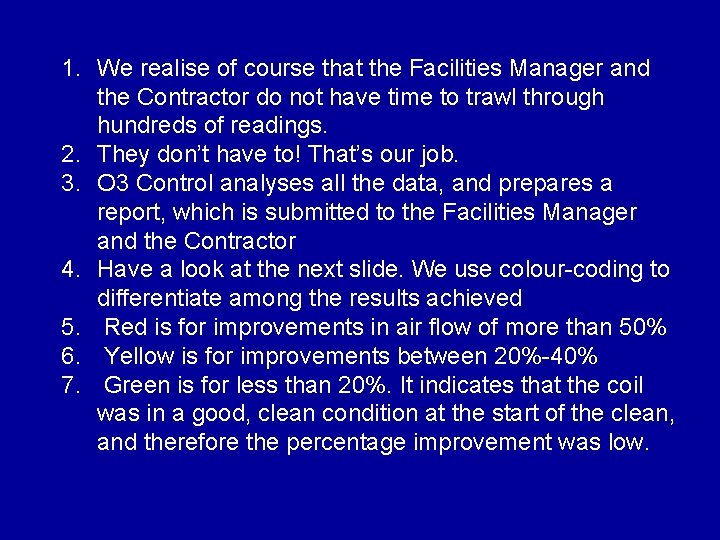
1. We realise of course that the Facilities Manager and the Contractor do not have time to trawl through hundreds of readings. 2. They don’t have to! That’s our job. 3. O 3 Control analyses all the data, and prepares a report, which is submitted to the Facilities Manager and the Contractor 4. Have a look at the next slide. We use colour-coding to differentiate among the results achieved 5. Red is for improvements in air flow of more than 50% 6. Yellow is for improvements between 20%-40% 7. Green is for less than 20%. It indicates that the coil was in a good, clean condition at the start of the clean, and therefore the percentage improvement was low.
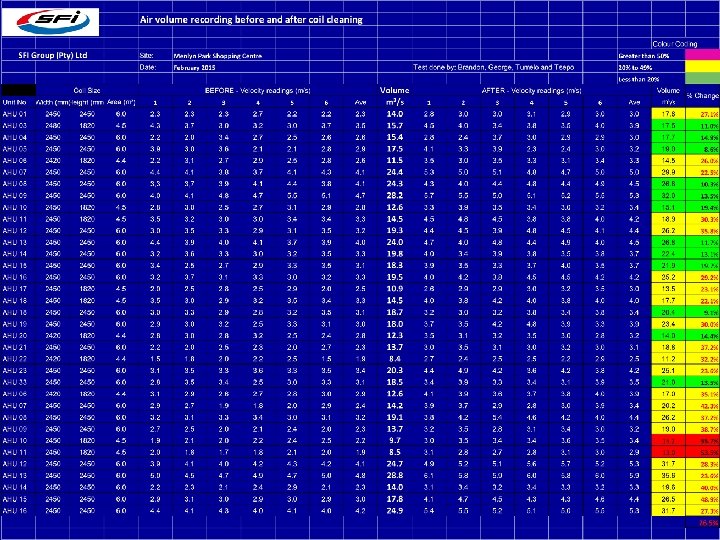
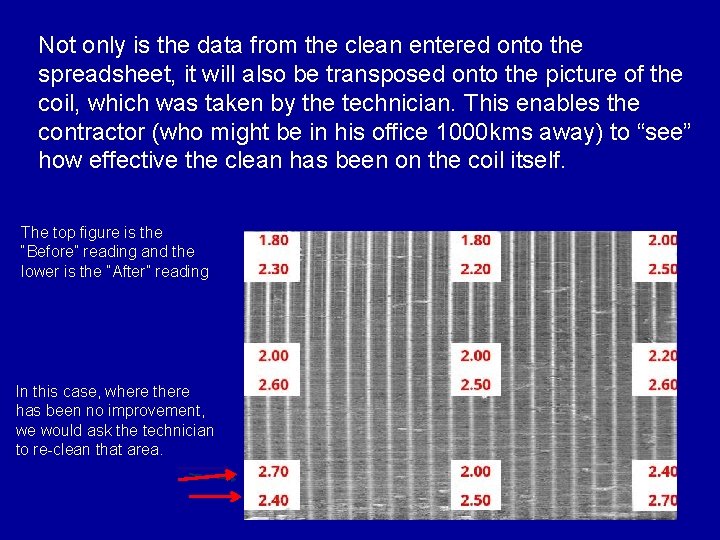
Not only is the data from the clean entered onto the spreadsheet, it will also be transposed onto the picture of the coil, which was taken by the technician. This enables the contractor (who might be in his office 1000 kms away) to “see” how effective the clean has been on the coil itself. The top figure is the “Before” reading and the lower is the “After” reading In this case, where there has been no improvement, we would ask the technician to re-clean that area.
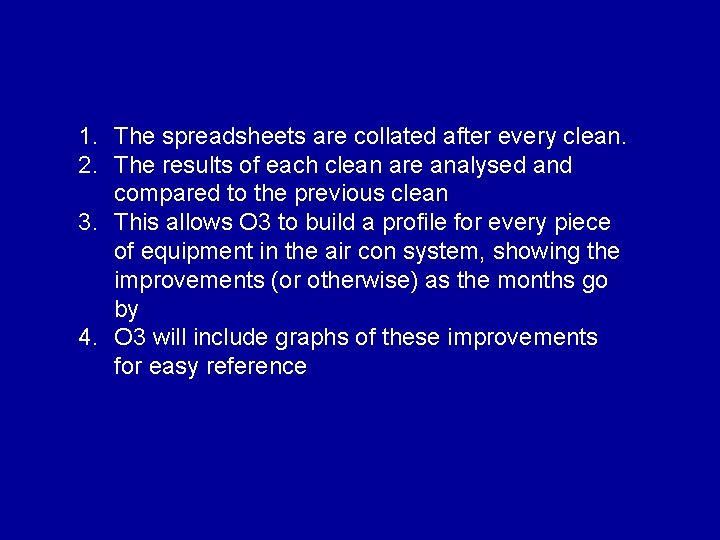
1. The spreadsheets are collated after every clean. 2. The results of each clean are analysed and compared to the previous clean 3. This allows O 3 to build a profile for every piece of equipment in the air con system, showing the improvements (or otherwise) as the months go by 4. O 3 will include graphs of these improvements for easy reference
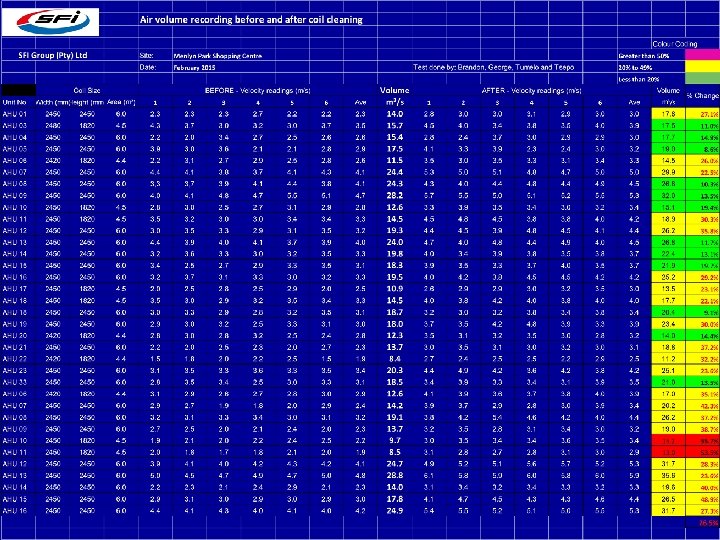
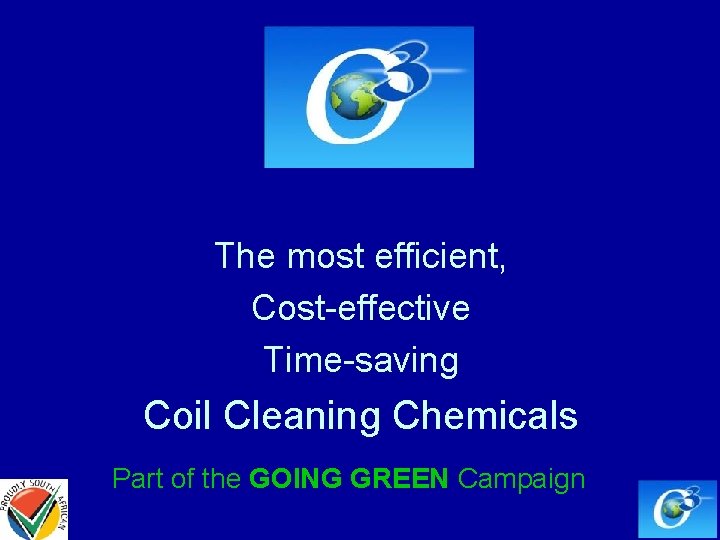
The most efficient, Cost-effective Time-saving Coil Cleaning Chemicals Part of the GOING GREEN Campaign
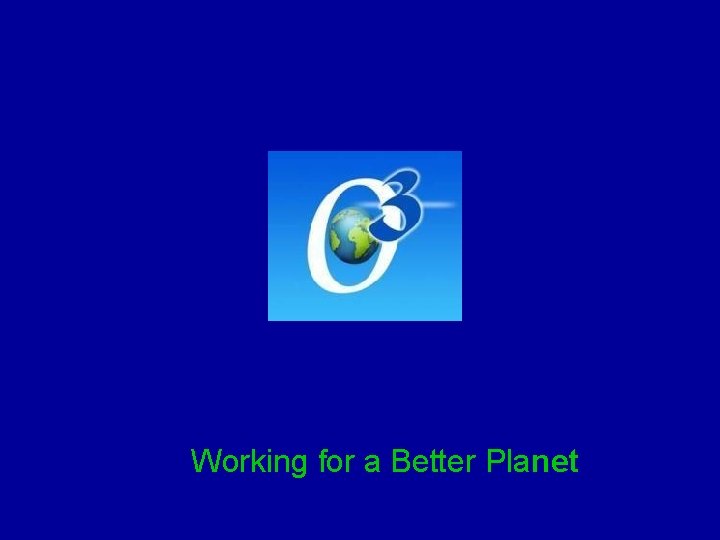
Working for a Better Planet
Green coil cleaner
Draw hta for home cleaning task using vacuum cleaner.
Concur task tree
Alkaline coil cleaner
Series coil and multi-turn coil
Yellow light
Green air cleaning
Lernpyramide von green & green (2005)
Red + green = yellow = white - blue
Frc control system
Ism grain cleaner
Marine fabre
Diener plasma cleaner
Sewa vacuum cleaner
Charging toward cleaner air in london
Menicare gp cds
Kitchen exhaust cleaning pittsburgh
Microbe drain cleaner