Target Costing Cost plus pricing is more appropriate
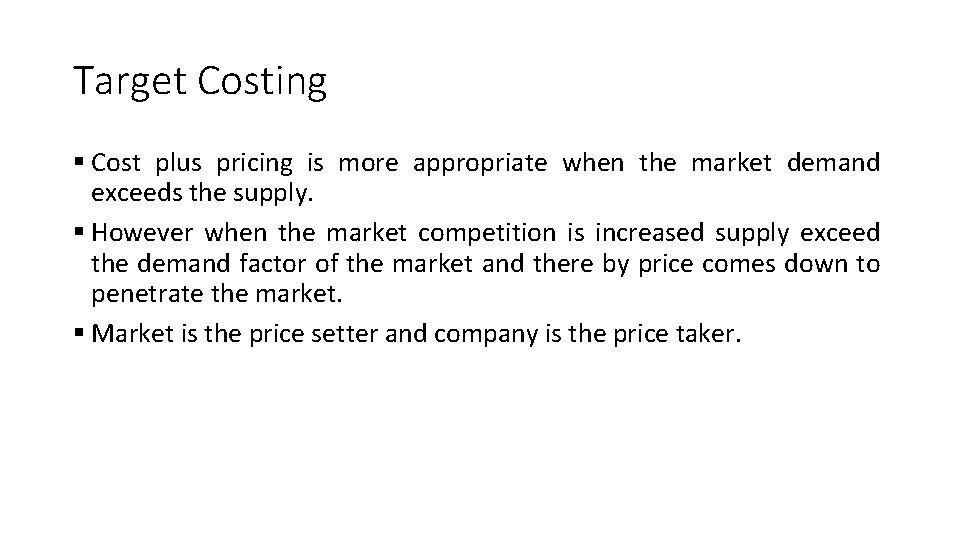
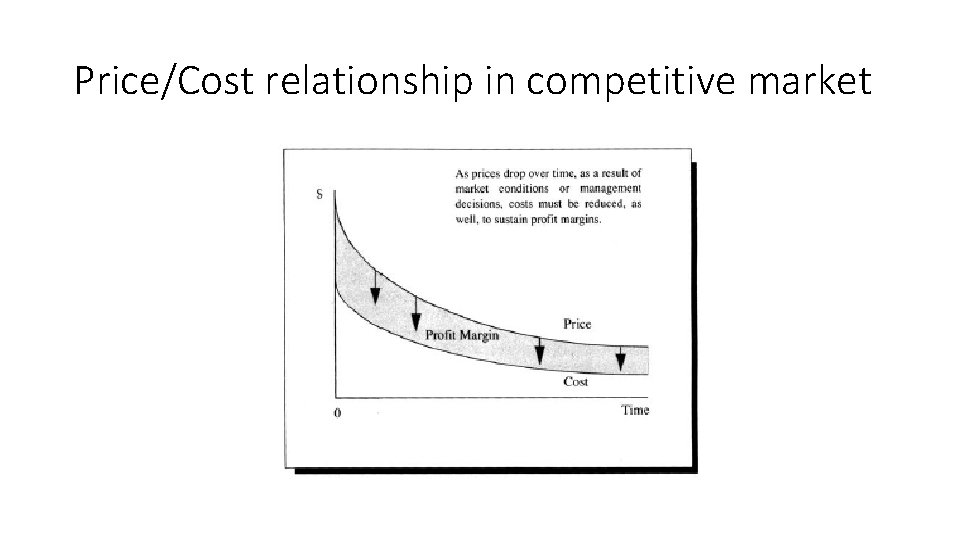
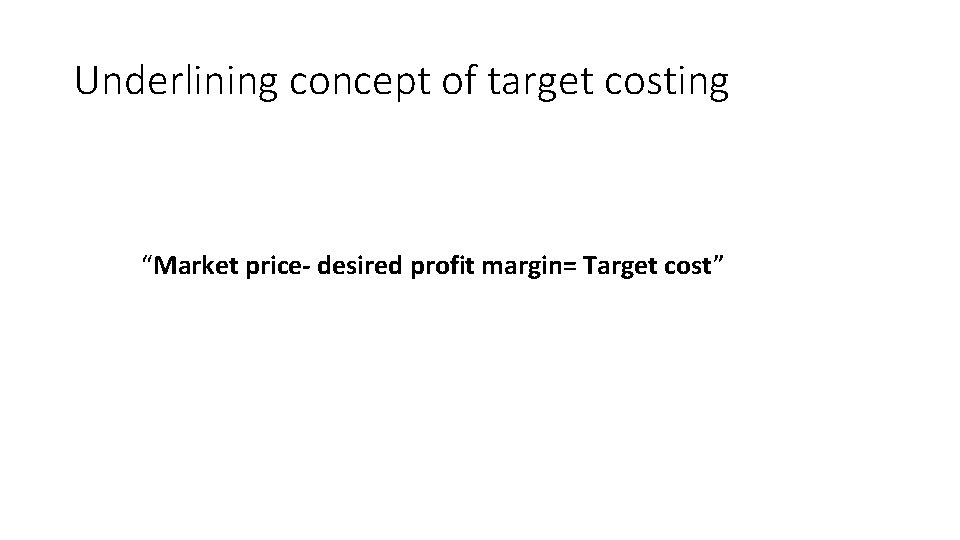
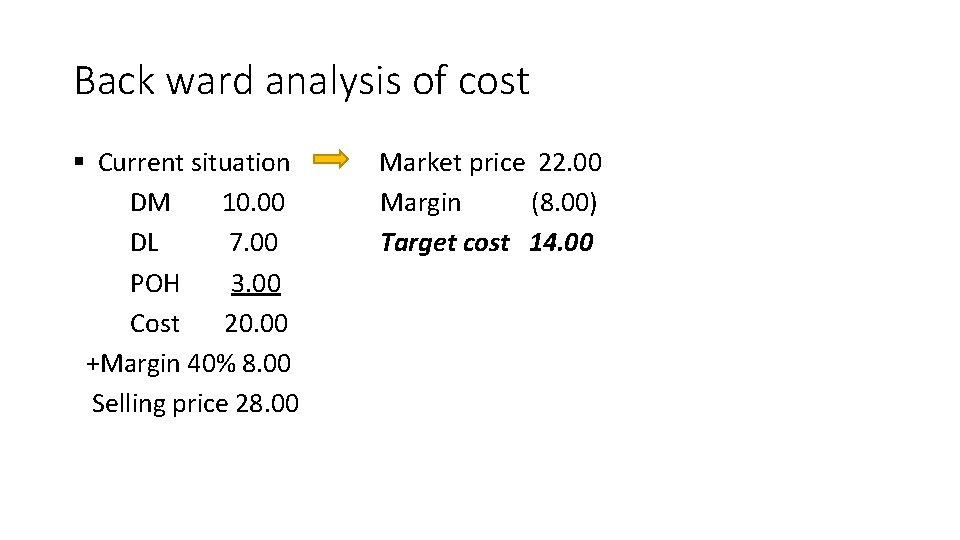
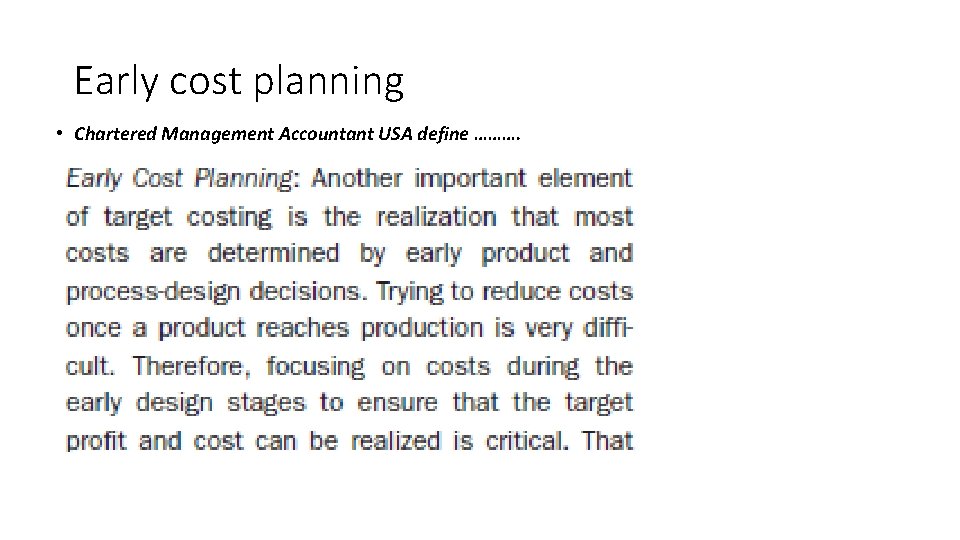
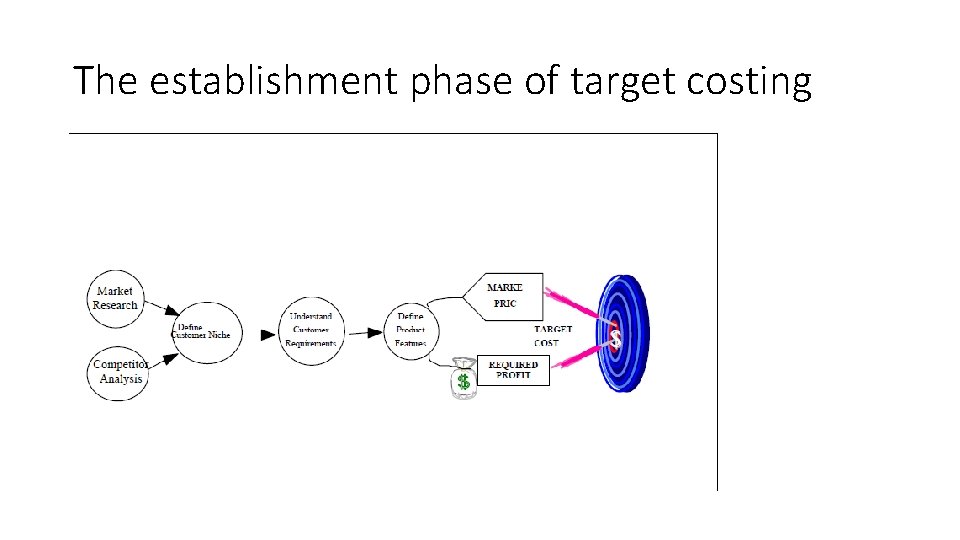
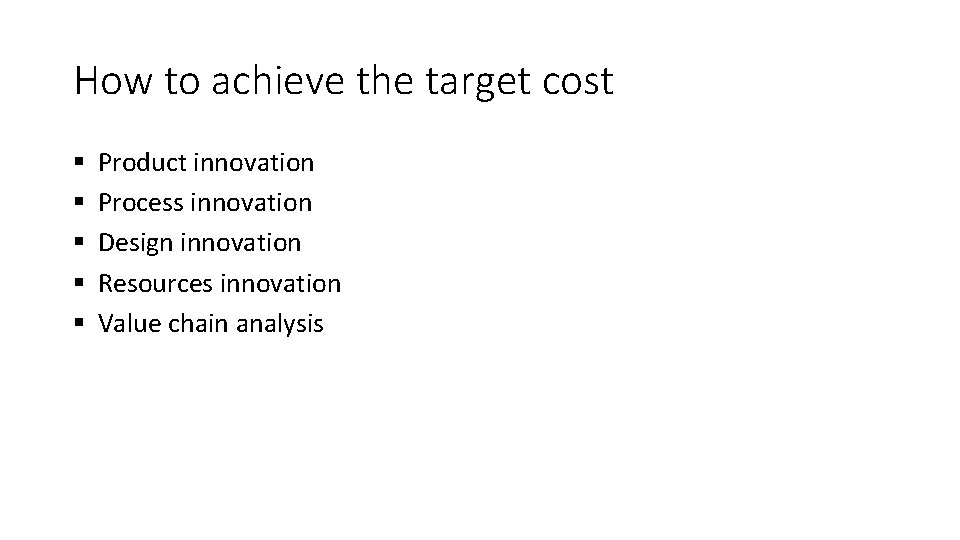
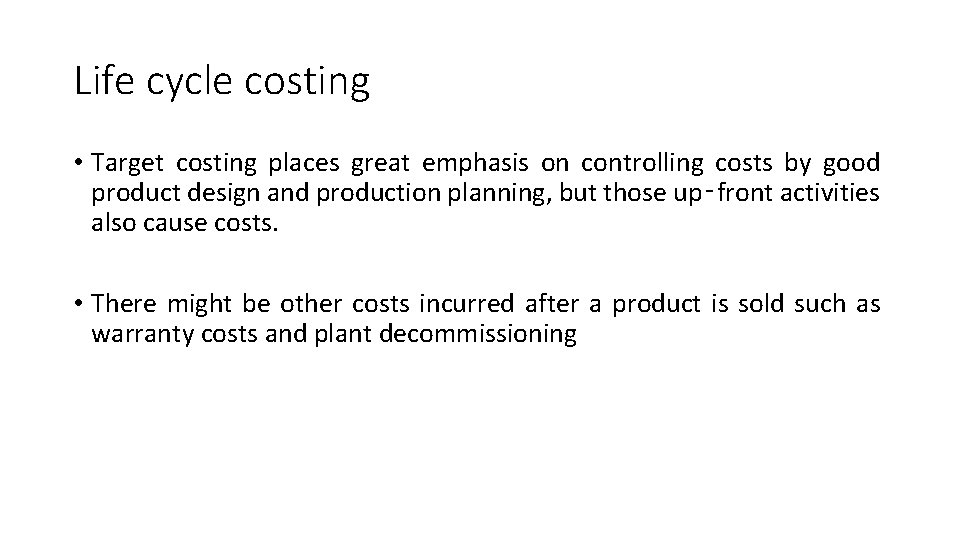
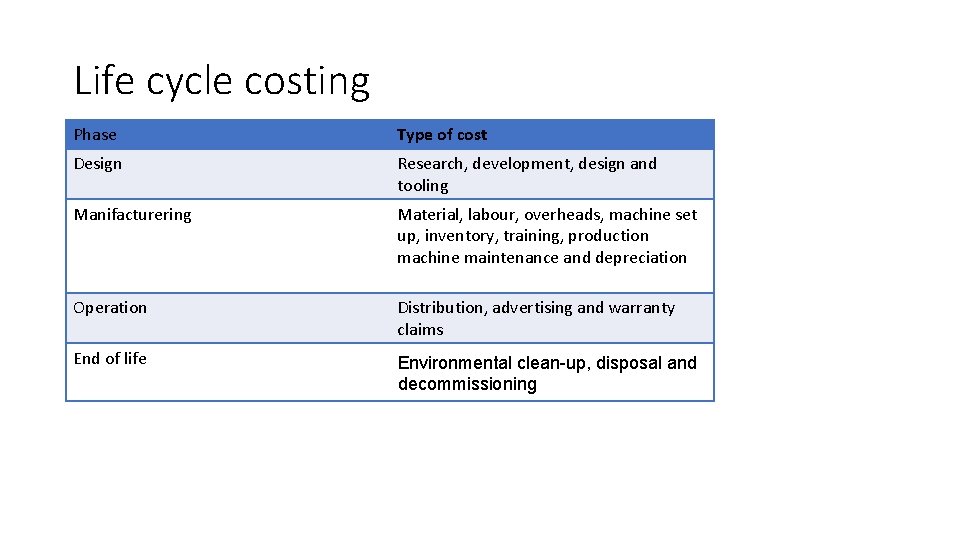
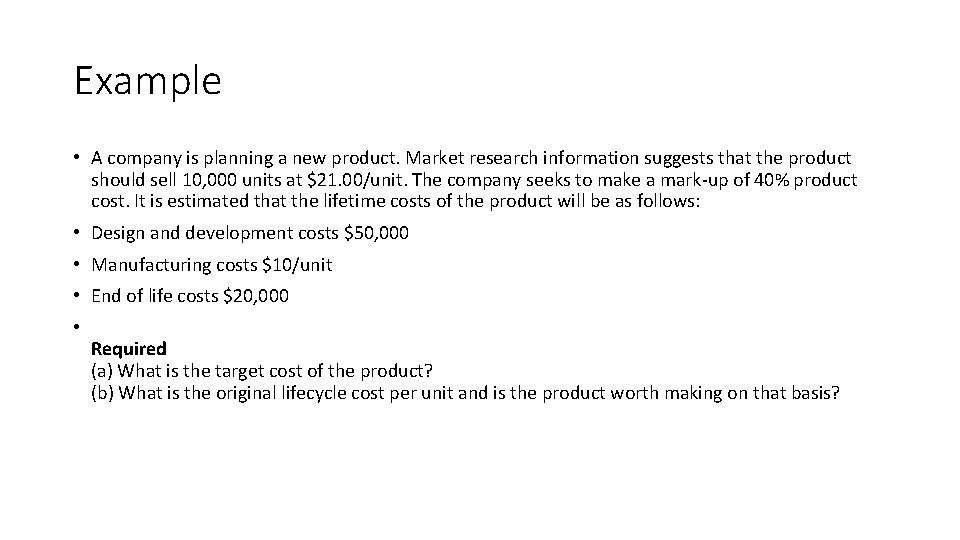
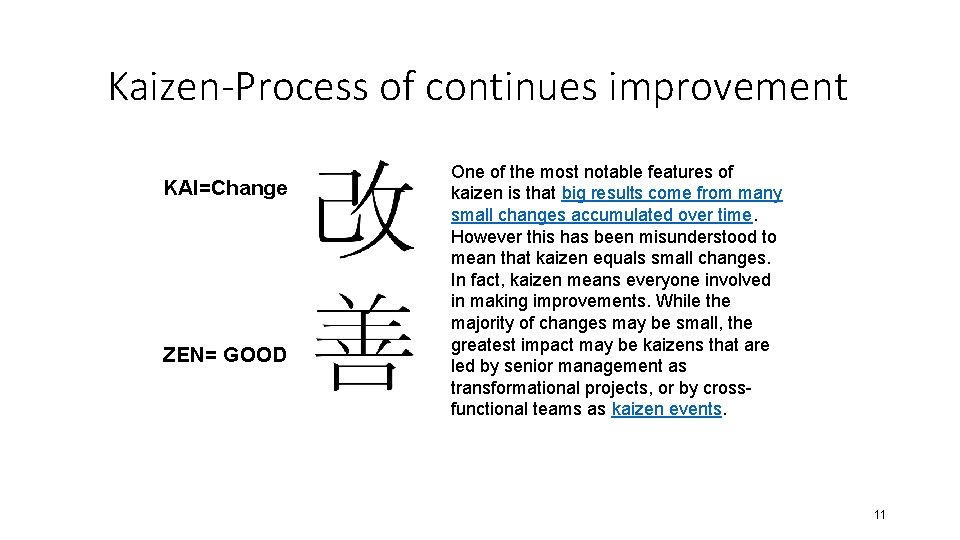
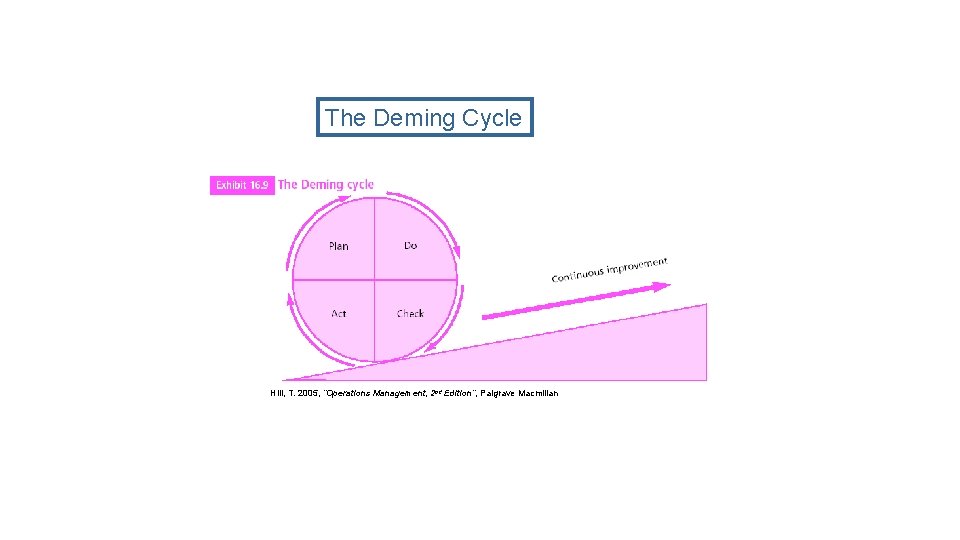
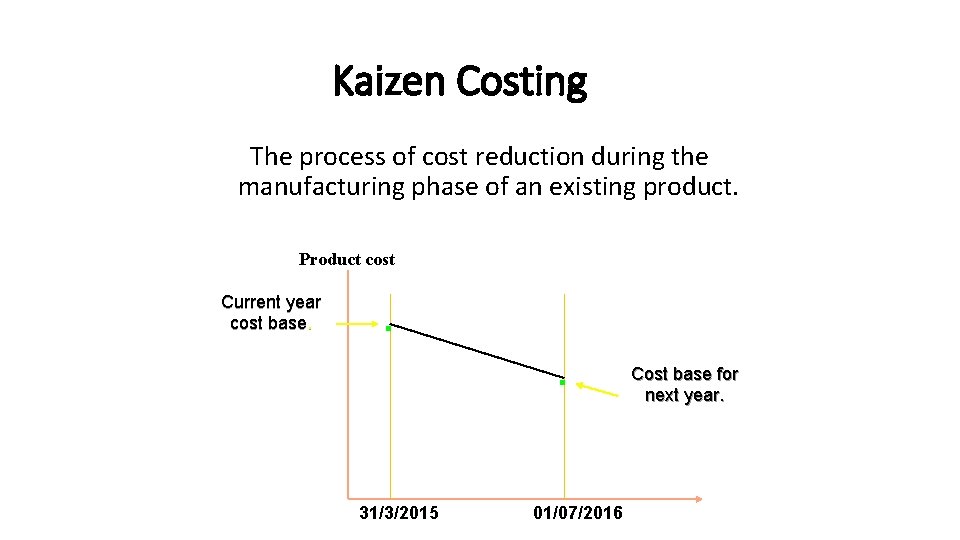
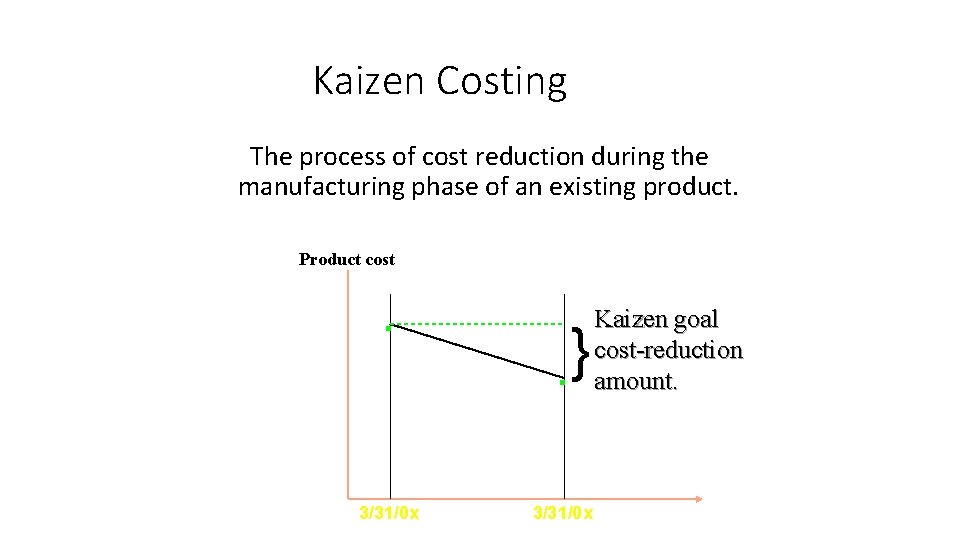
- Slides: 14
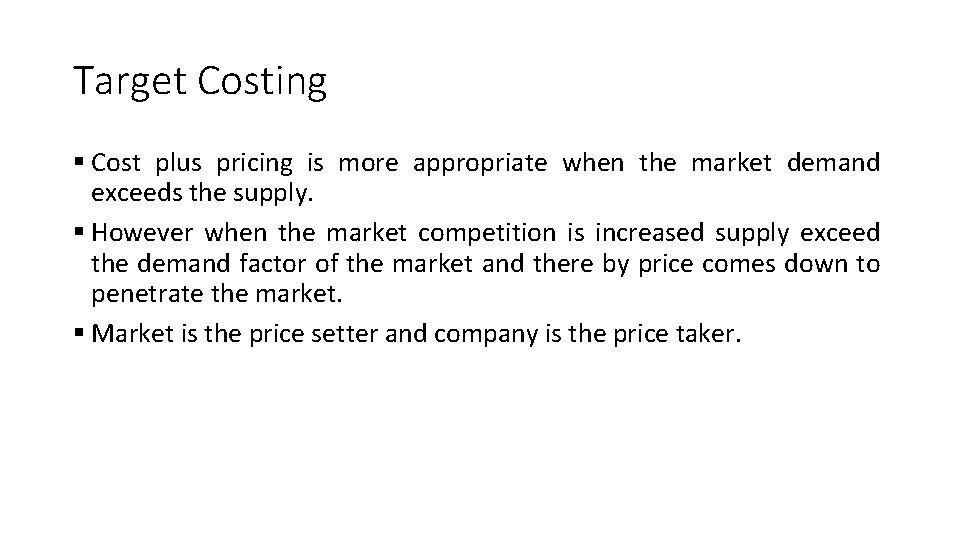
Target Costing § Cost plus pricing is more appropriate when the market demand exceeds the supply. § However when the market competition is increased supply exceed the demand factor of the market and there by price comes down to penetrate the market. § Market is the price setter and company is the price taker.
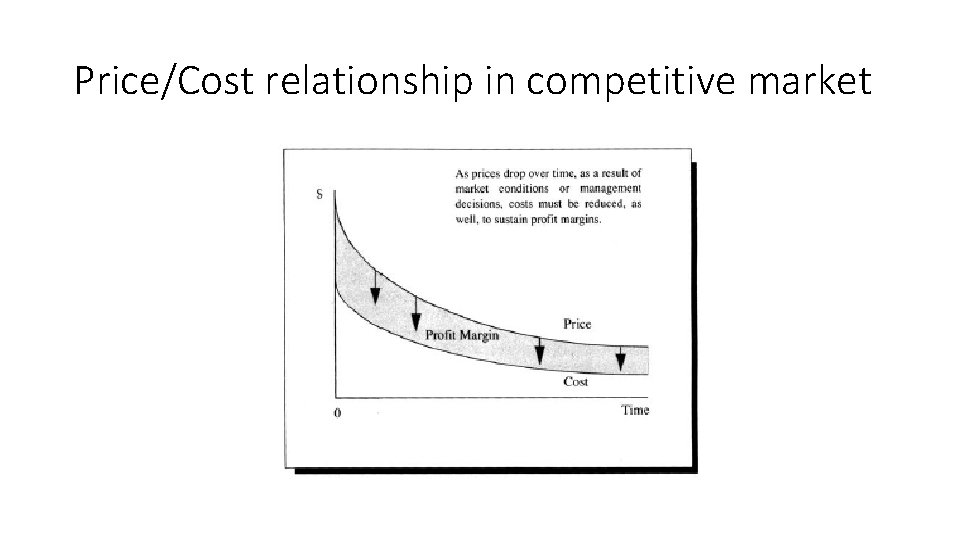
Price/Cost relationship in competitive market
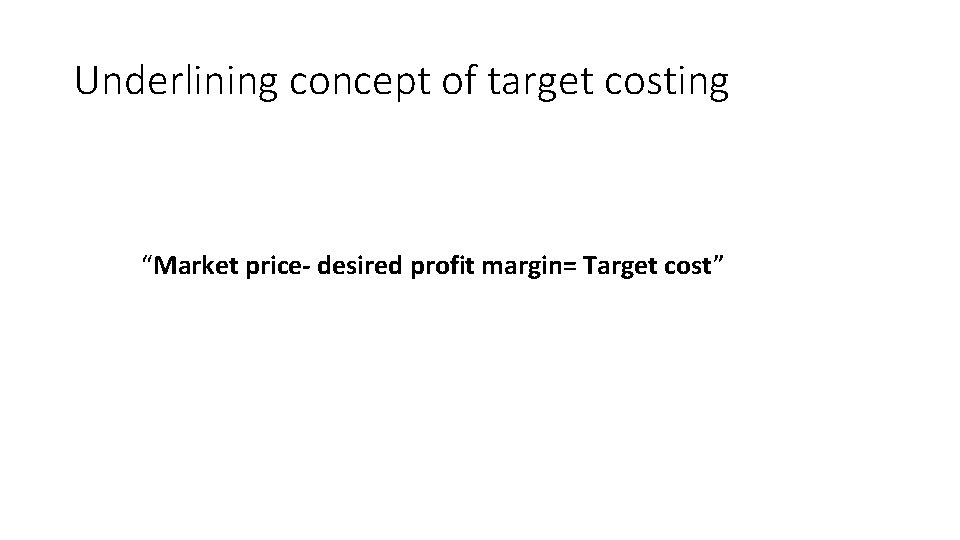
Underlining concept of target costing “Market price- desired profit margin= Target cost”
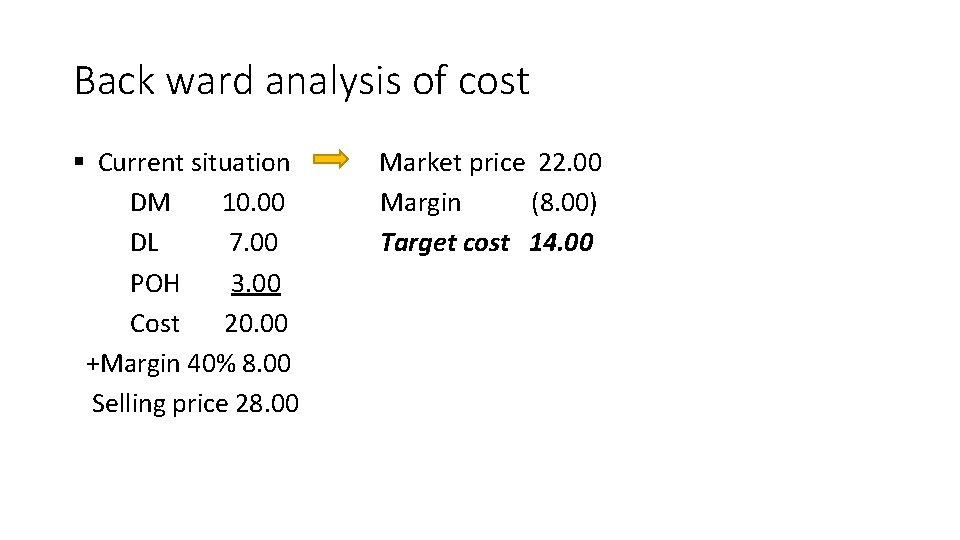
Back ward analysis of cost § Current situation DM 10. 00 DL 7. 00 POH 3. 00 Cost 20. 00 +Margin 40% 8. 00 Selling price 28. 00 Market price 22. 00 Margin (8. 00) Target cost 14. 00
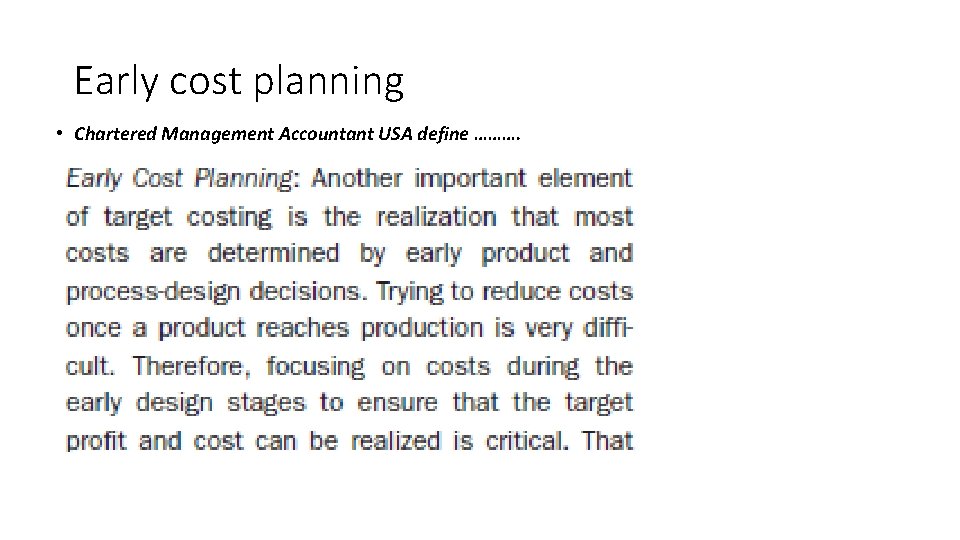
Early cost planning • Chartered Management Accountant USA define ……….
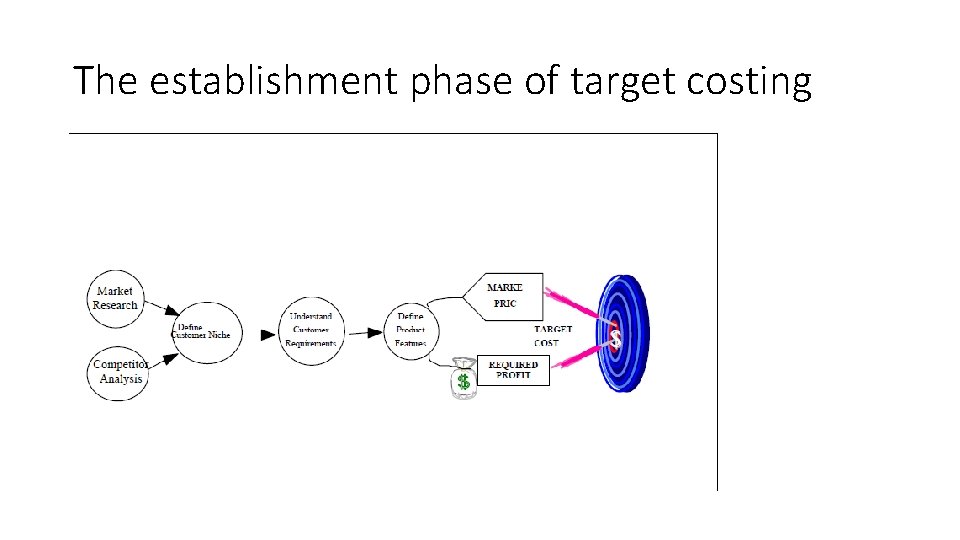
The establishment phase of target costing
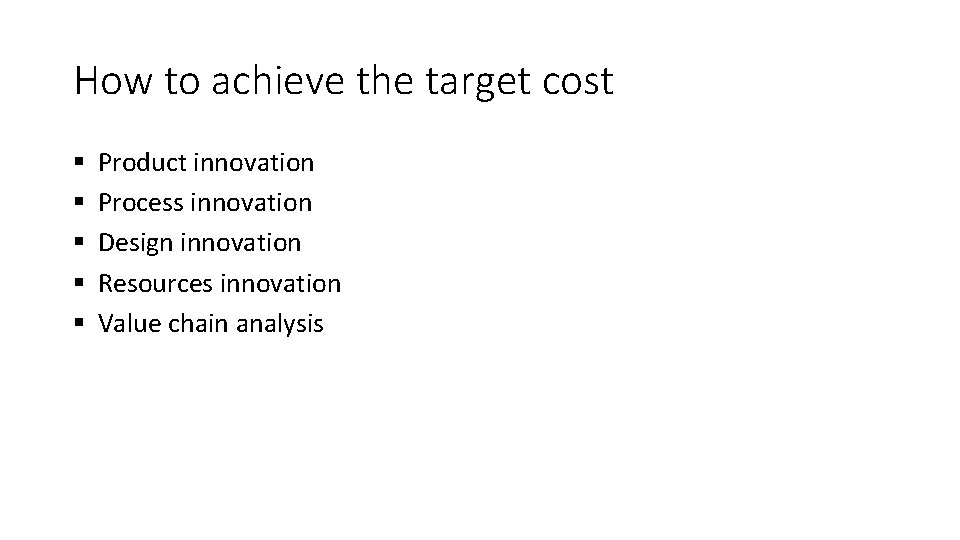
How to achieve the target cost § § § Product innovation Process innovation Design innovation Resources innovation Value chain analysis
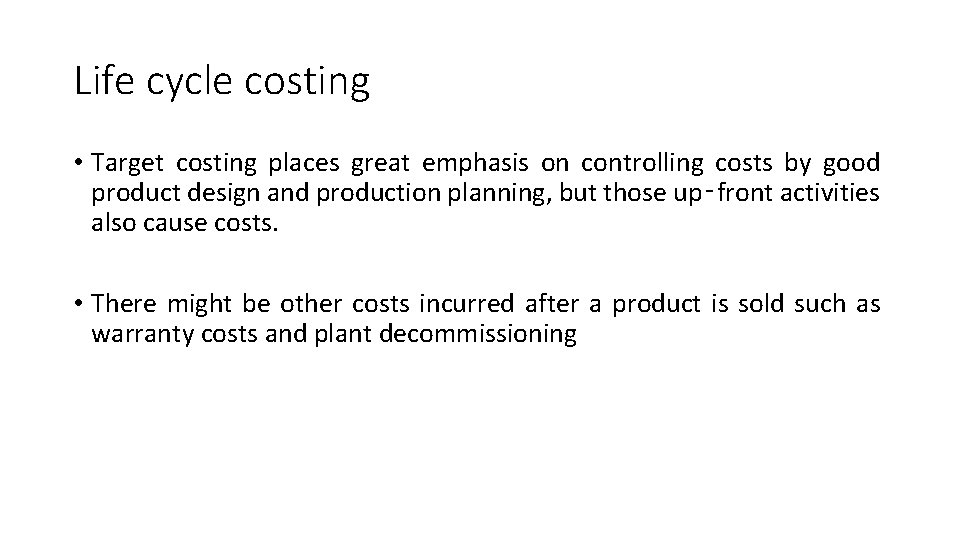
Life cycle costing • Target costing places great emphasis on controlling costs by good product design and production planning, but those up‑front activities also cause costs. • There might be other costs incurred after a product is sold such as warranty costs and plant decommissioning
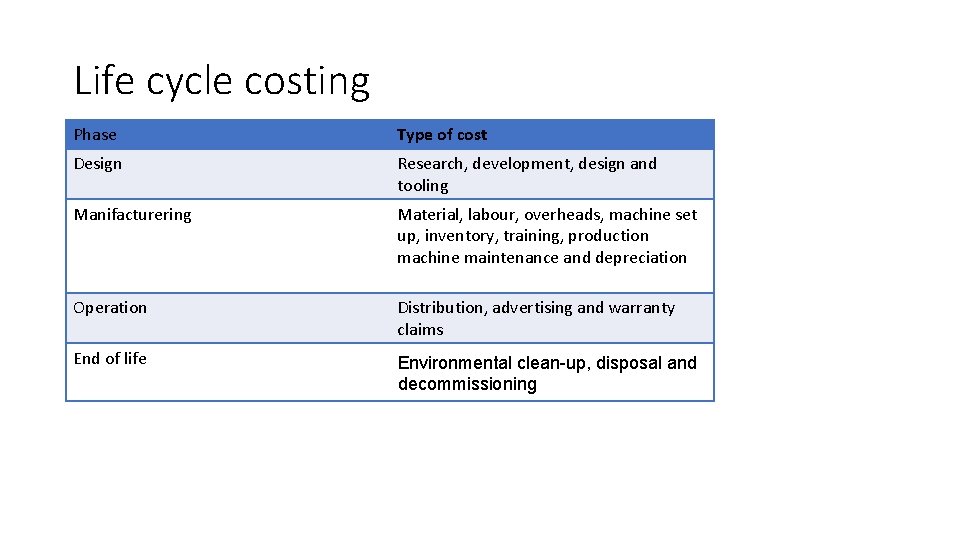
Life cycle costing Phase Type of cost Design Research, development, design and tooling Manifacturering Material, labour, overheads, machine set up, inventory, training, production machine maintenance and depreciation Operation Distribution, advertising and warranty claims End of life Environmental clean-up, disposal and decommissioning
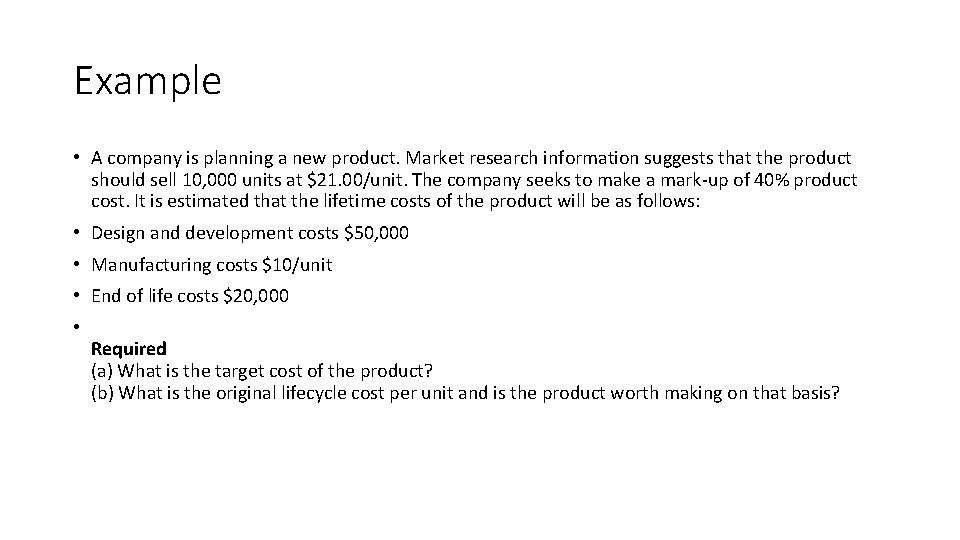
Example • A company is planning a new product. Market research information suggests that the product should sell 10, 000 units at $21. 00/unit. The company seeks to make a mark-up of 40% product cost. It is estimated that the lifetime costs of the product will be as follows: • Design and development costs $50, 000 • Manufacturing costs $10/unit • End of life costs $20, 000 • Required (a) What is the target cost of the product? (b) What is the original lifecycle cost per unit and is the product worth making on that basis?
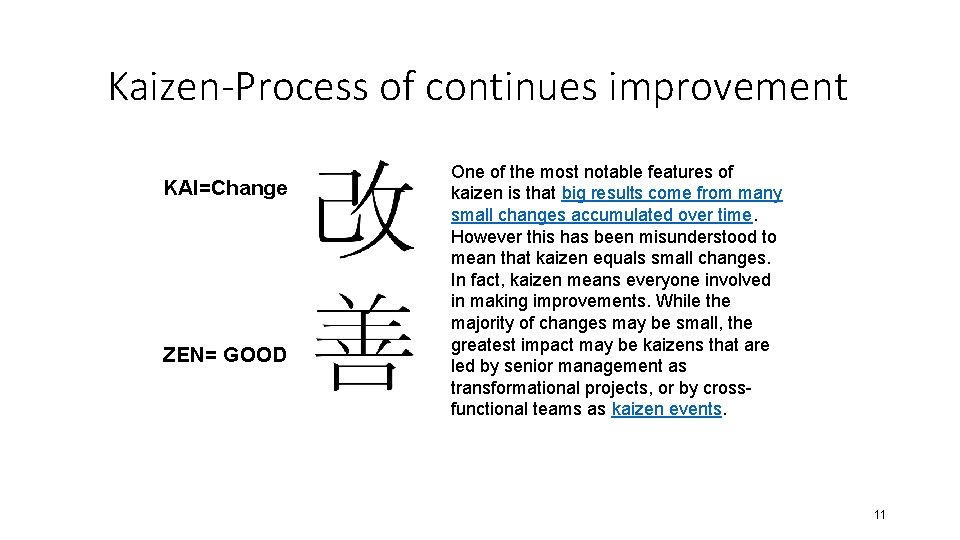
Kaizen-Process of continues improvement KAI=Change ZEN= GOOD One of the most notable features of kaizen is that big results come from many small changes accumulated over time. However this has been misunderstood to mean that kaizen equals small changes. In fact, kaizen means everyone involved in making improvements. While the majority of changes may be small, the greatest impact may be kaizens that are led by senior management as transformational projects, or by crossfunctional teams as kaizen events. 11
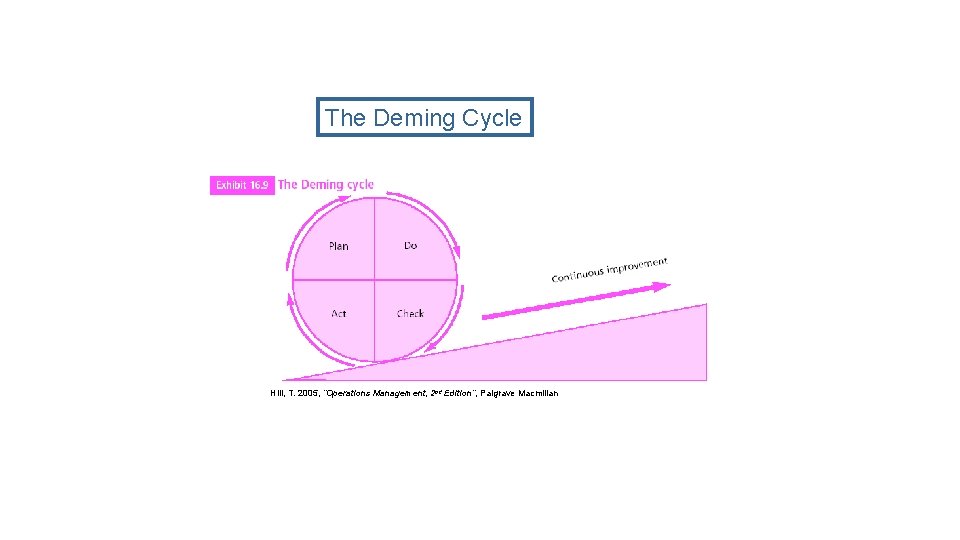
The Deming Cycle Hill, T. 2005, “Operations Management, 2 nd Edition”, Palgrave Macmillan
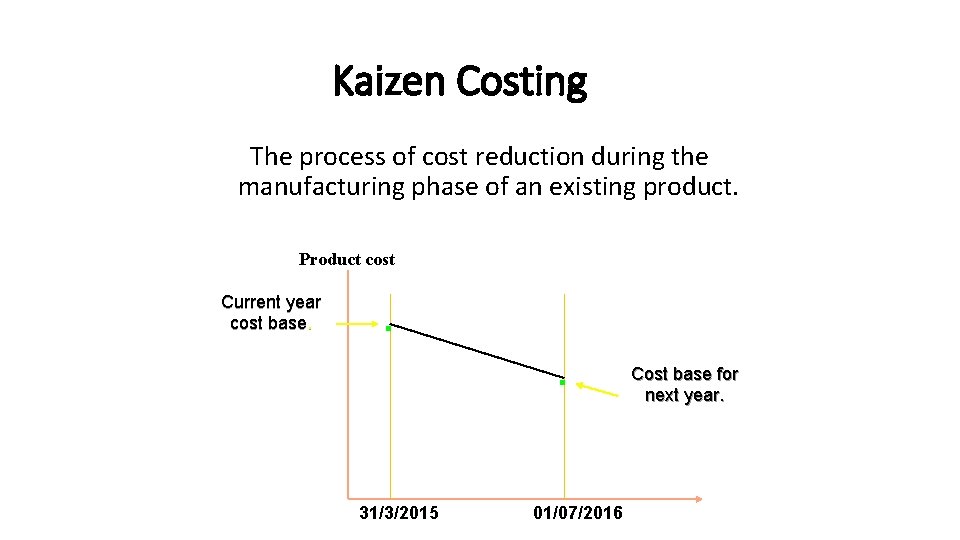
Kaizen Costing The process of cost reduction during the manufacturing phase of an existing product. Product cost Current year cost base. . 31/3/2015 . 01/07/2016 Cost base for next year.
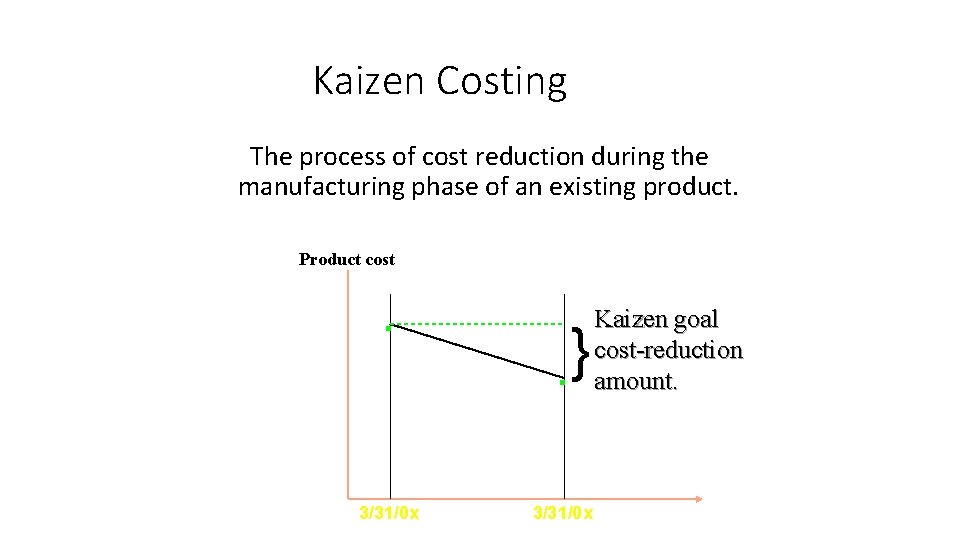
Kaizen Costing The process of cost reduction during the manufacturing phase of an existing product. Product cost . 3/31/0 x }. 3/31/0 x Kaizen goal cost-reduction amount.
More more more i want more more more more we praise you
More more more i want more more more more we praise you
Target pricing vs cost plus
Target costing and activity based costing
Cost plus pricing formula
Reverse cost plus pricing
Cost plus loan pricing model
Costing and pricing
Cost plus pricing
Job order costing and process costing
Job order cost flow
Differences between service costing and product costing
Absorption costing vs marginal costing
Job costing with process costing
Difference between job order costing and process costing