Shallow cavities Deep cavities Filiform corrosion Figure 23
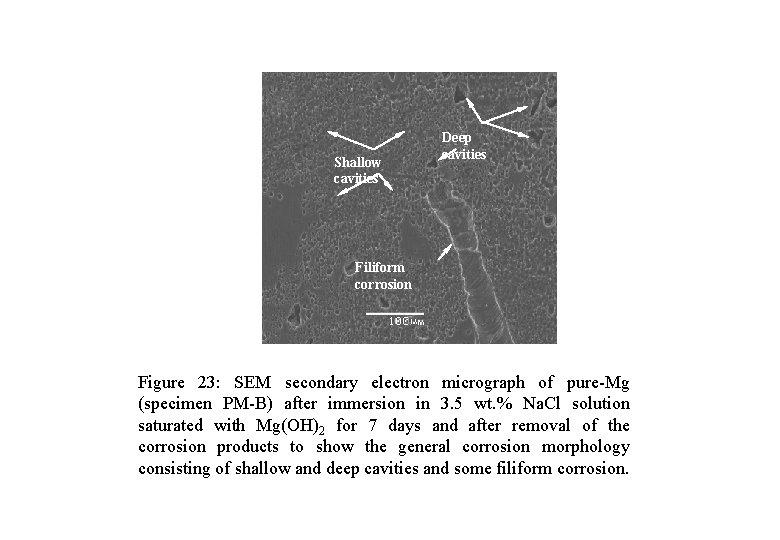
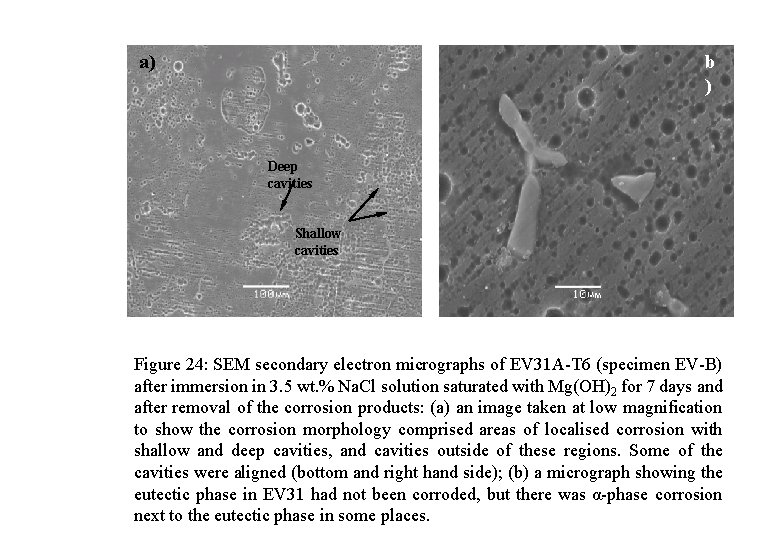
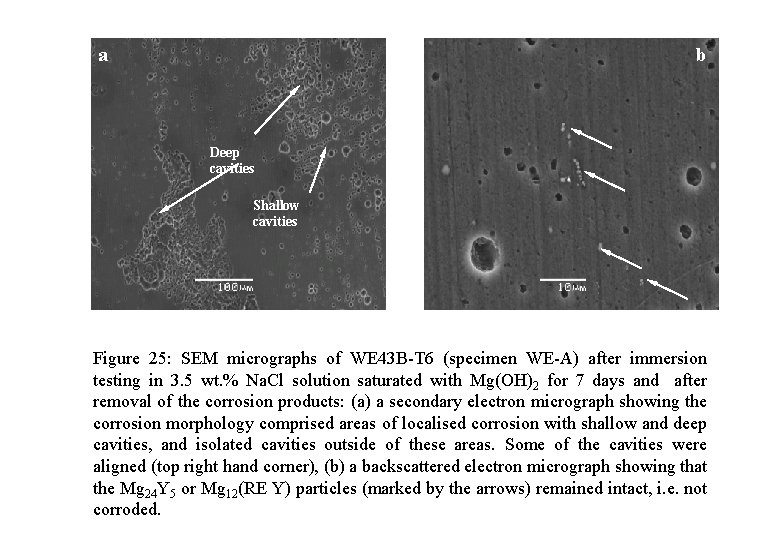
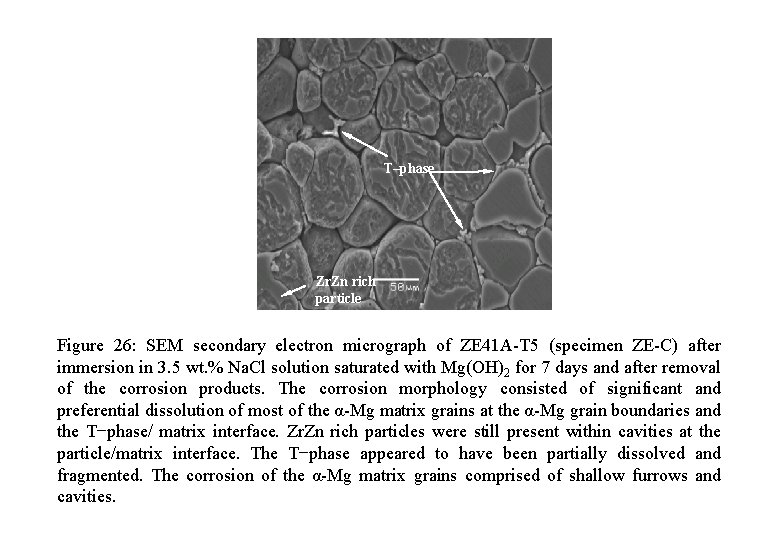
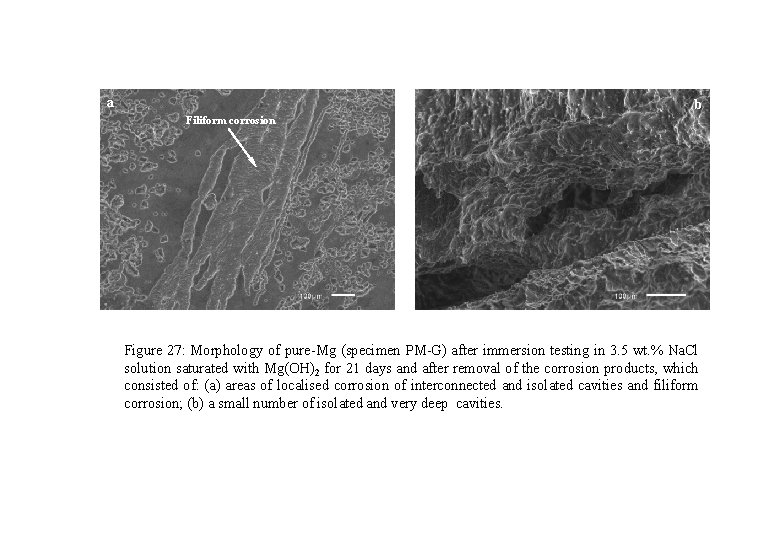
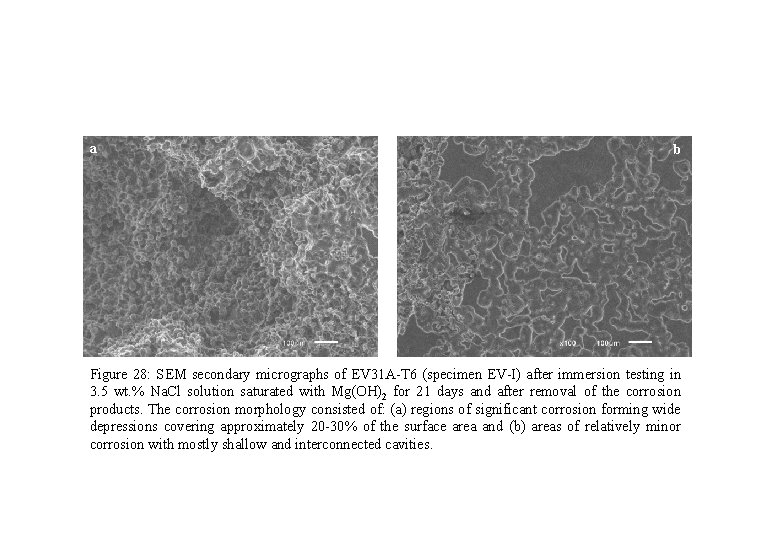
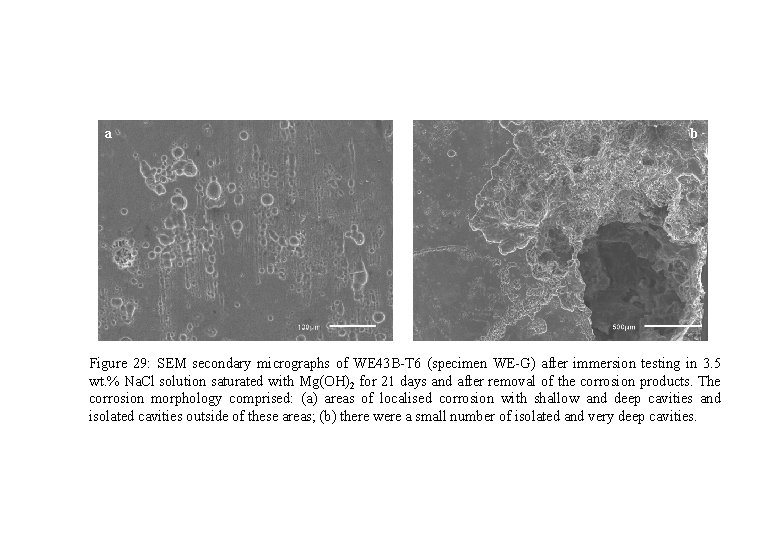
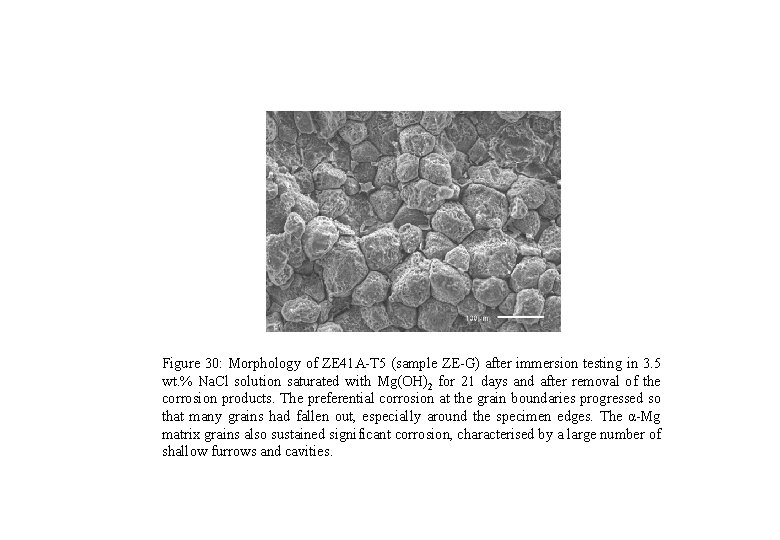
- Slides: 8
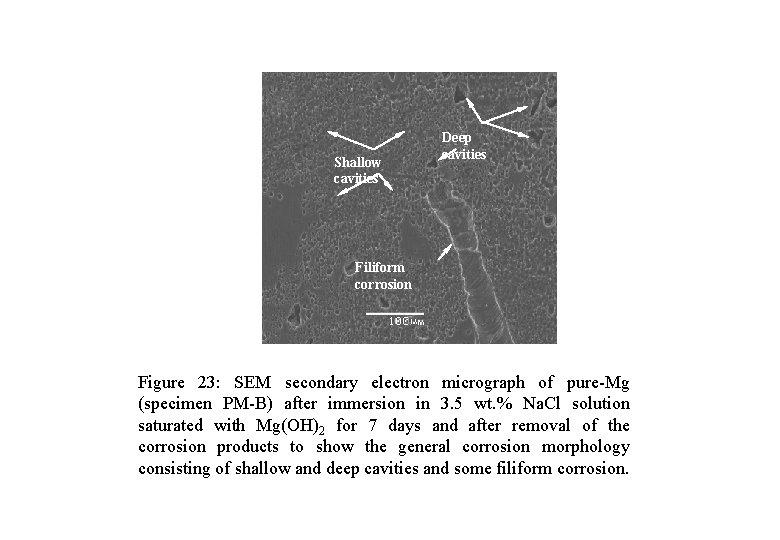
Shallow cavities Deep cavities Filiform corrosion Figure 23: SEM secondary electron micrograph of pure-Mg (specimen PM-B) after immersion in 3. 5 wt. % Na. Cl solution saturated with Mg(OH)2 for 7 days and after removal of the corrosion products to show the general corrosion morphology consisting of shallow and deep cavities and some filiform corrosion.
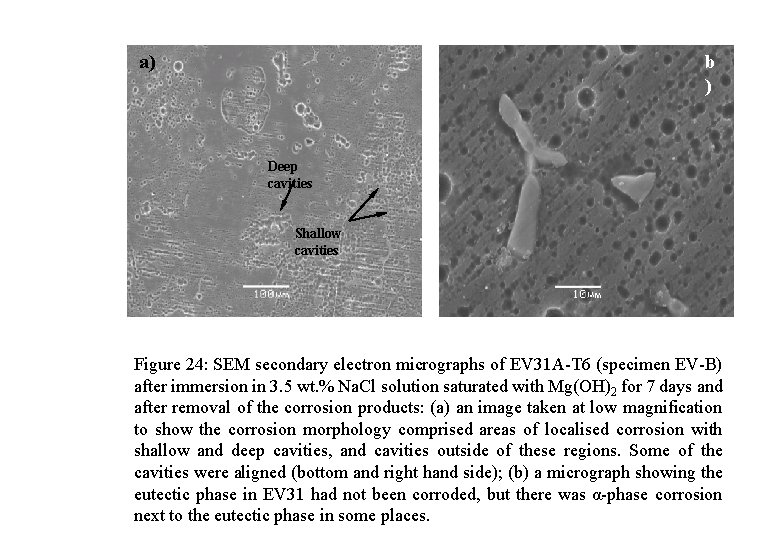
b ) a) Deep cavities Shallow cavities Figure 24: SEM secondary electron micrographs of EV 31 A-T 6 (specimen EV-B) after immersion in 3. 5 wt. % Na. Cl solution saturated with Mg(OH)2 for 7 days and after removal of the corrosion products: (a) an image taken at low magnification to show the corrosion morphology comprised areas of localised corrosion with shallow and deep cavities, and cavities outside of these regions. Some of the cavities were aligned (bottom and right hand side); (b) a micrograph showing the eutectic phase in EV 31 had not been corroded, but there was α-phase corrosion next to the eutectic phase in some places.
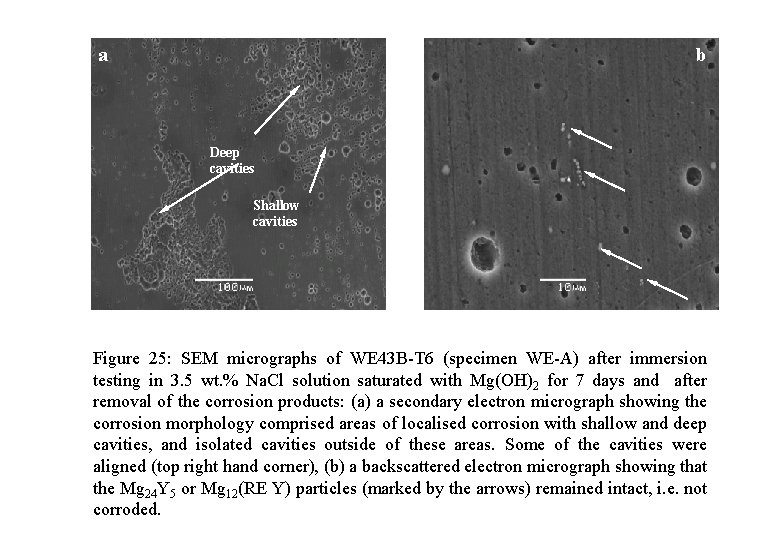
a b Deep cavities Shallow cavities Figure 25: SEM micrographs of WE 43 B-T 6 (specimen WE-A) after immersion testing in 3. 5 wt. % Na. Cl solution saturated with Mg(OH)2 for 7 days and after removal of the corrosion products: (a) a secondary electron micrograph showing the corrosion morphology comprised areas of localised corrosion with shallow and deep cavities, and isolated cavities outside of these areas. Some of the cavities were aligned (top right hand corner), (b) a backscattered electron micrograph showing that the Mg 24 Y 5 or Mg 12(RE Y) particles (marked by the arrows) remained intact, i. e. not corroded.
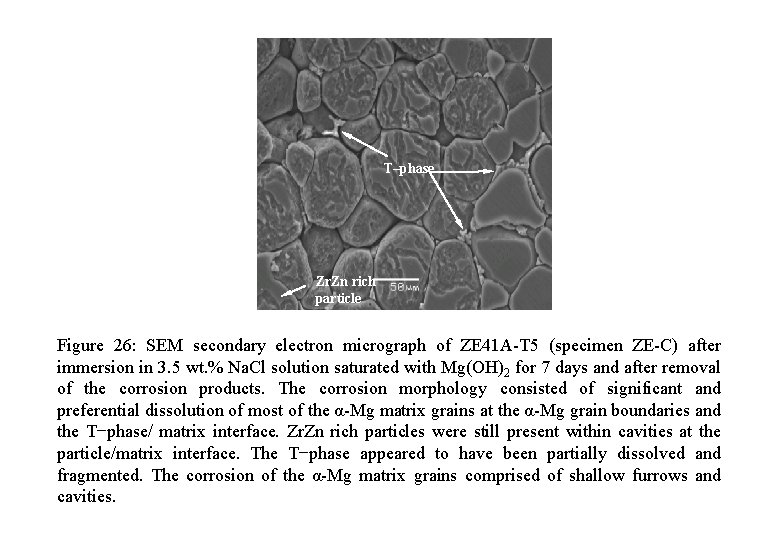
T‒phase Zr. Zn rich particle Figure 26: SEM secondary electron micrograph of ZE 41 A-T 5 (specimen ZE-C) after immersion in 3. 5 wt. % Na. Cl solution saturated with Mg(OH)2 for 7 days and after removal of the corrosion products. The corrosion morphology consisted of significant and preferential dissolution of most of the α-Mg matrix grains at the α-Mg grain boundaries and the T−phase/ matrix interface. Zr. Zn rich particles were still present within cavities at the particle/matrix interface. The T−phase appeared to have been partially dissolved and fragmented. The corrosion of the α-Mg matrix grains comprised of shallow furrows and cavities.
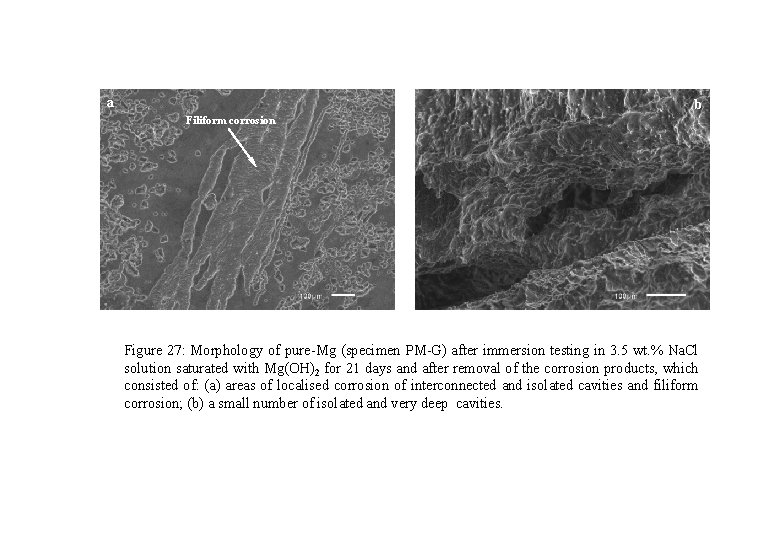
a b Filiform corrosion Figure 27: Morphology of pure-Mg (specimen PM-G) after immersion testing in 3. 5 wt. % Na. Cl solution saturated with Mg(OH)2 for 21 days and after removal of the corrosion products, which consisted of: (a) areas of localised corrosion of interconnected and isolated cavities and filiform corrosion; (b) a small number of isolated and very deep cavities.
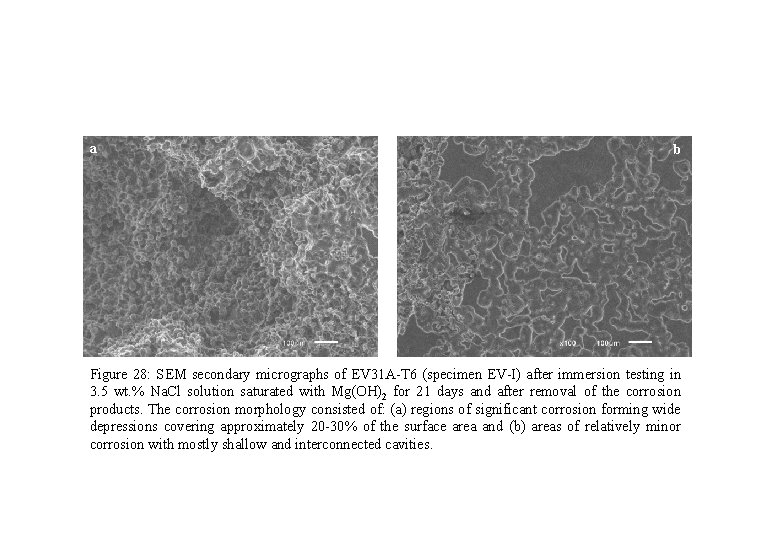
a b Figure 28: SEM secondary micrographs of EV 31 A-T 6 (specimen EV-I) after immersion testing in 3. 5 wt. % Na. Cl solution saturated with Mg(OH)2 for 21 days and after removal of the corrosion products. The corrosion morphology consisted of: (a) regions of significant corrosion forming wide depressions covering approximately 20 -30% of the surface area and (b) areas of relatively minor corrosion with mostly shallow and interconnected cavities.
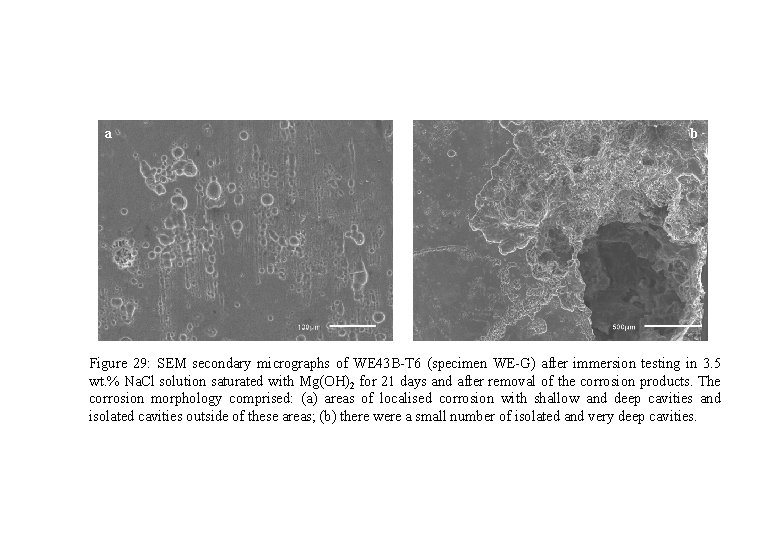
a b Figure 29: SEM secondary micrographs of WE 43 B-T 6 (specimen WE-G) after immersion testing in 3. 5 wt. % Na. Cl solution saturated with Mg(OH)2 for 21 days and after removal of the corrosion products. The corrosion morphology comprised: (a) areas of localised corrosion with shallow and deep cavities and isolated cavities outside of these areas; (b) there were a small number of isolated and very deep cavities.
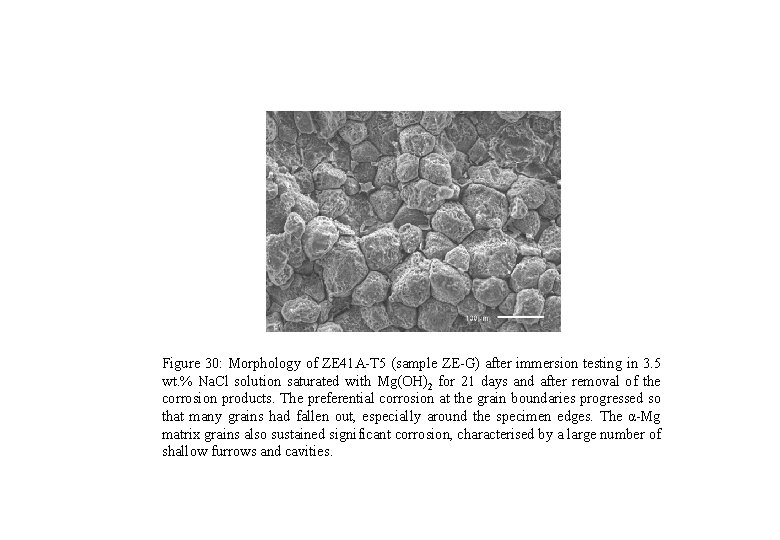
Figure 30: Morphology of ZE 41 A-T 5 (sample ZE-G) after immersion testing in 3. 5 wt. % Na. Cl solution saturated with Mg(OH)2 for 21 days and after removal of the corrosion products. The preferential corrosion at the grain boundaries progressed so that many grains had fallen out, especially around the specimen edges. The α-Mg matrix grains also sustained significant corrosion, characterised by a large number of shallow furrows and cavities.
Is oxidation corrosion
Filiform corrosion example
Differentiate between dry corrosion and wet corrosion
Difference between wet corrosion and dry corrosion
Sanitary well definition
Iceberg model surface and deep culture
Shallow and deep foundation
Contoh shallow knowledge dan deep knowledge
Shallow latch vs deep latch