Sensor Systems for CPI Sensor temperature sensors flow
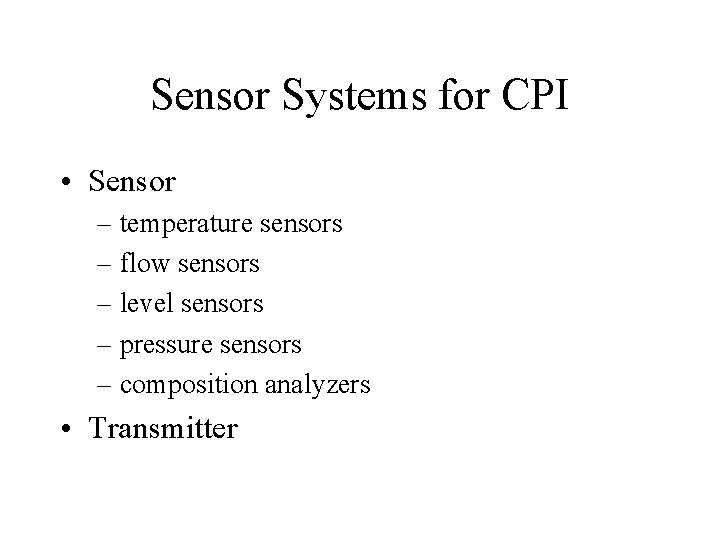
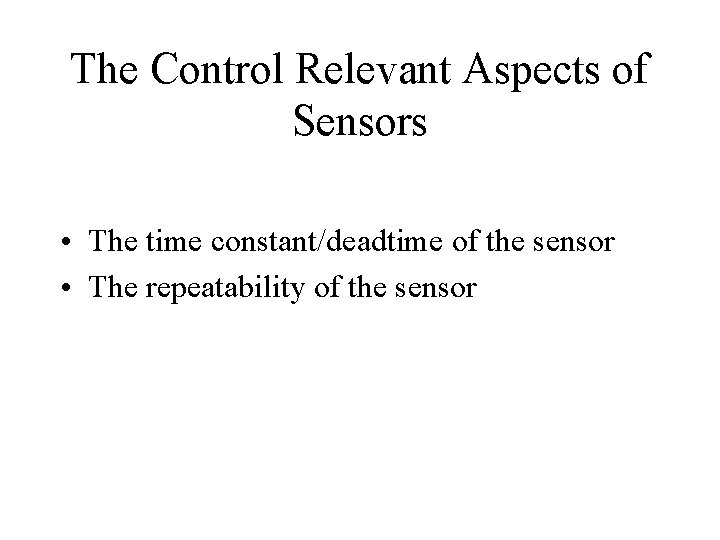
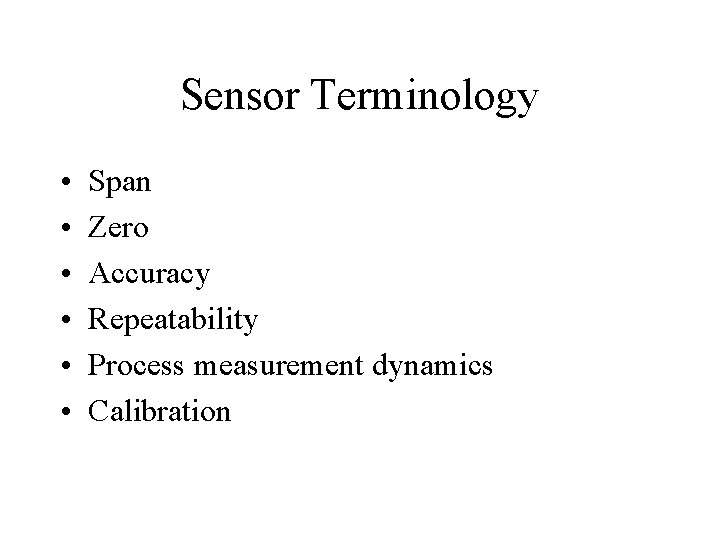
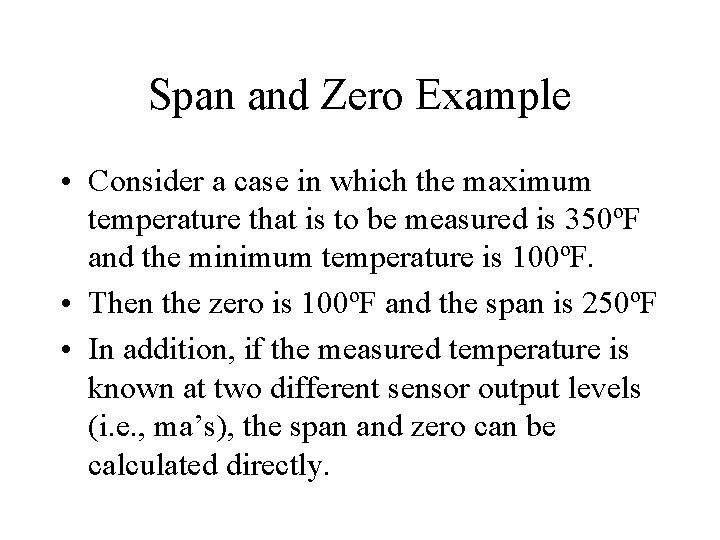
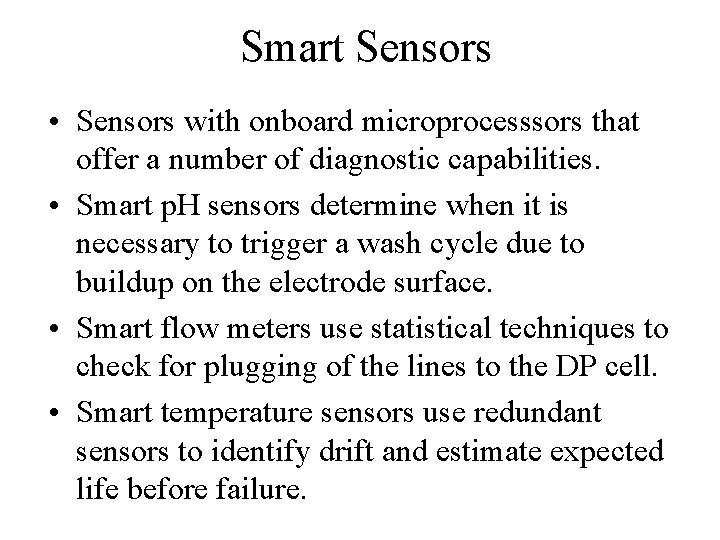
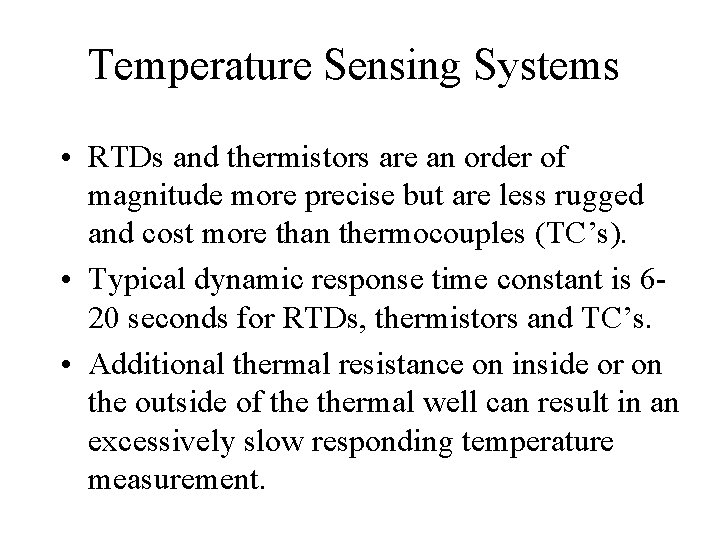
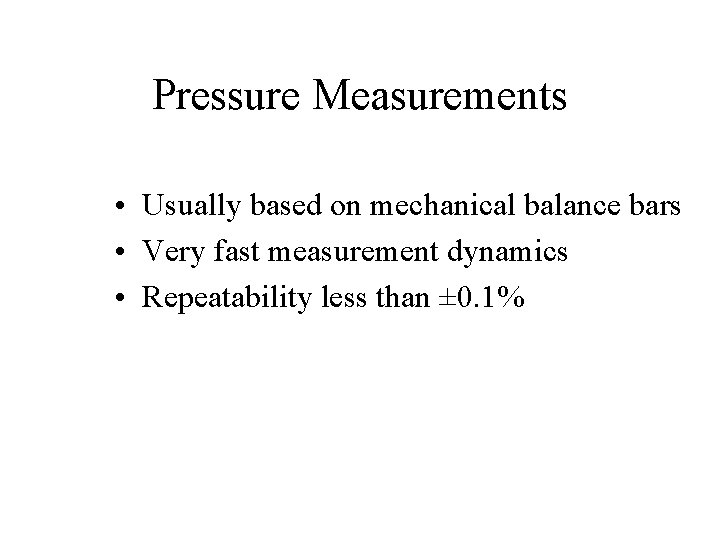

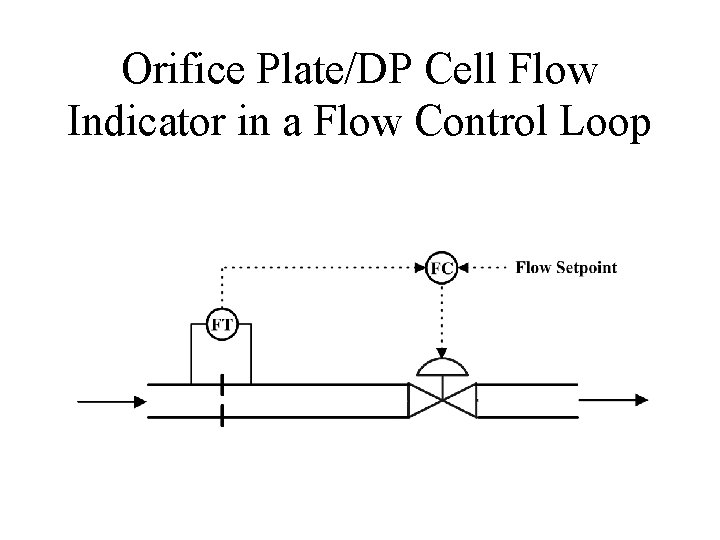
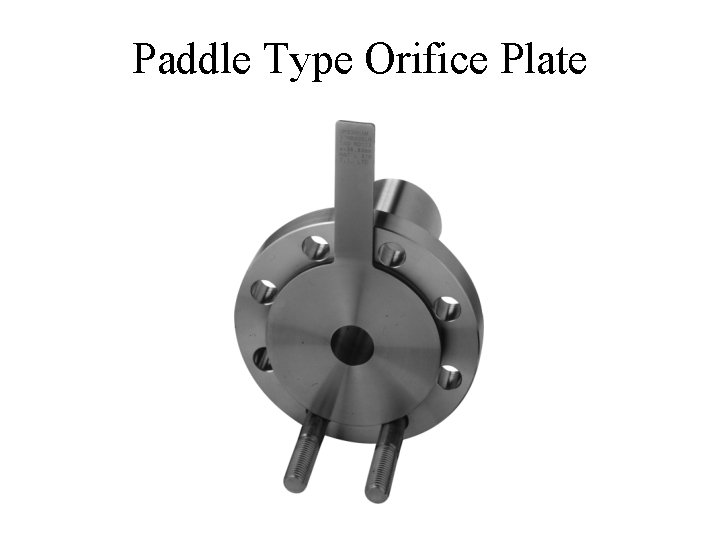
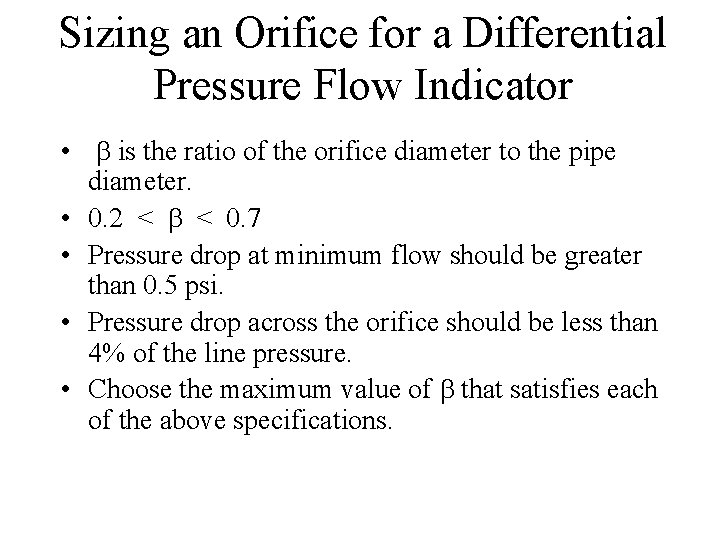
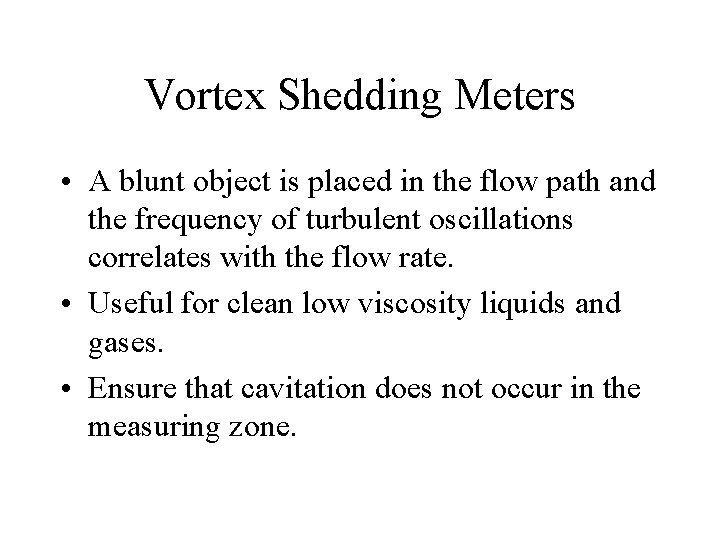
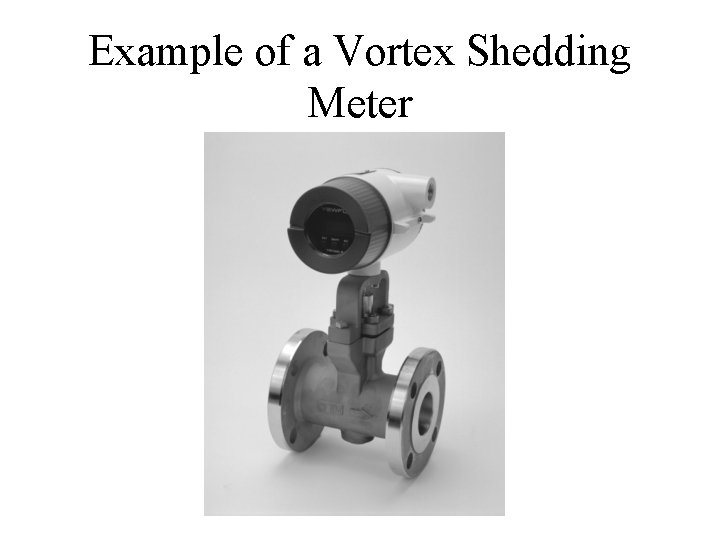

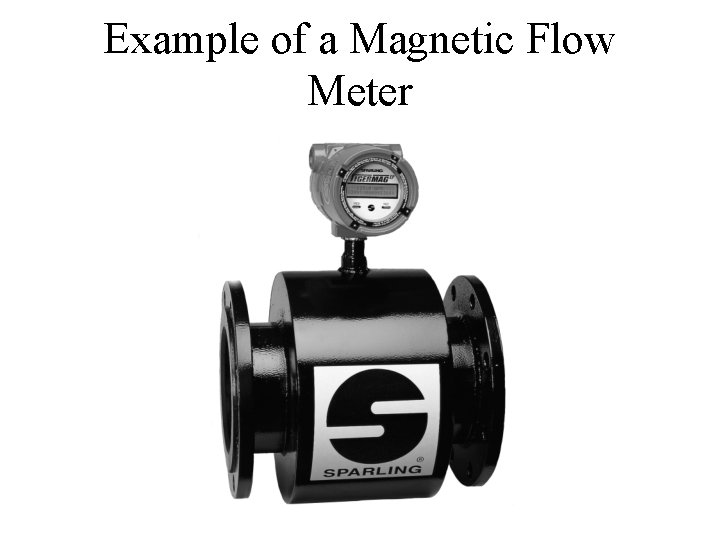
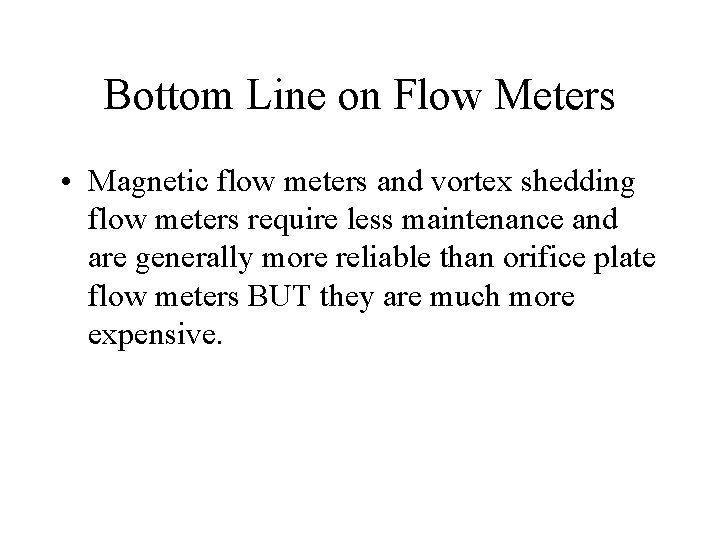
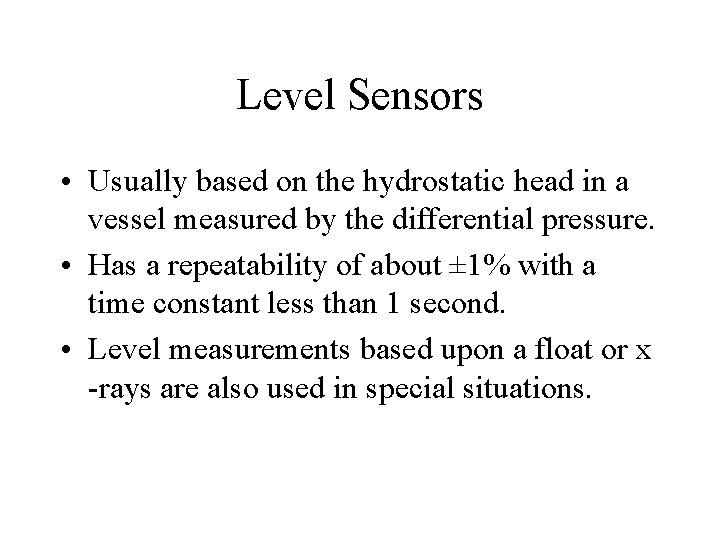
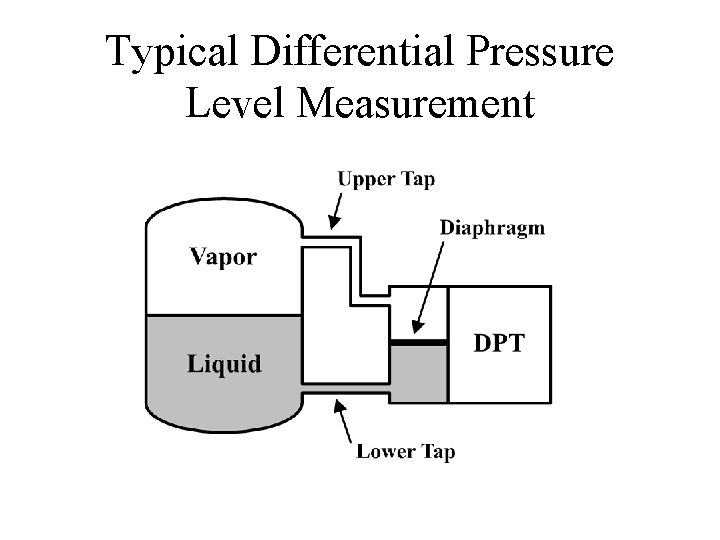
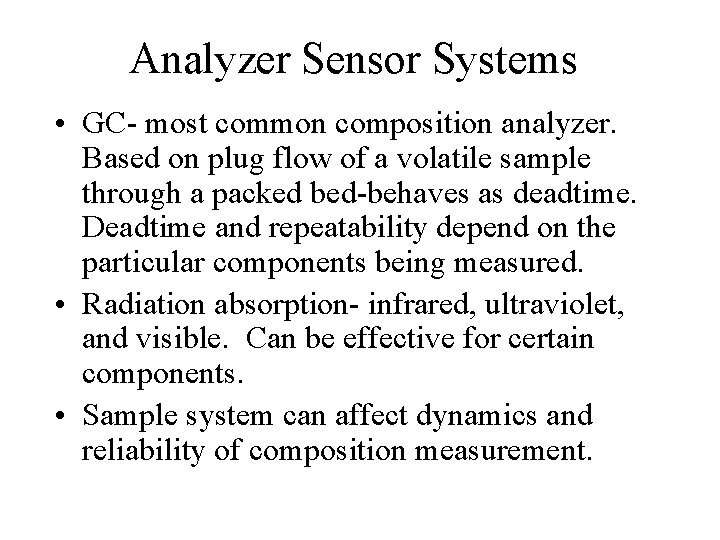
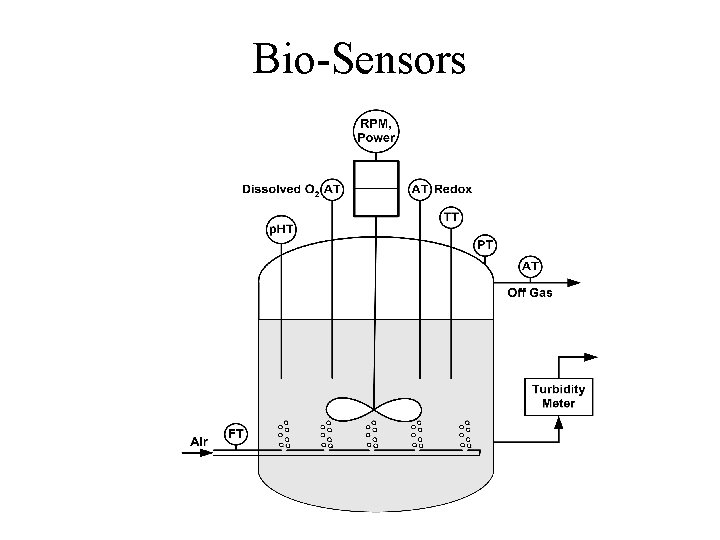
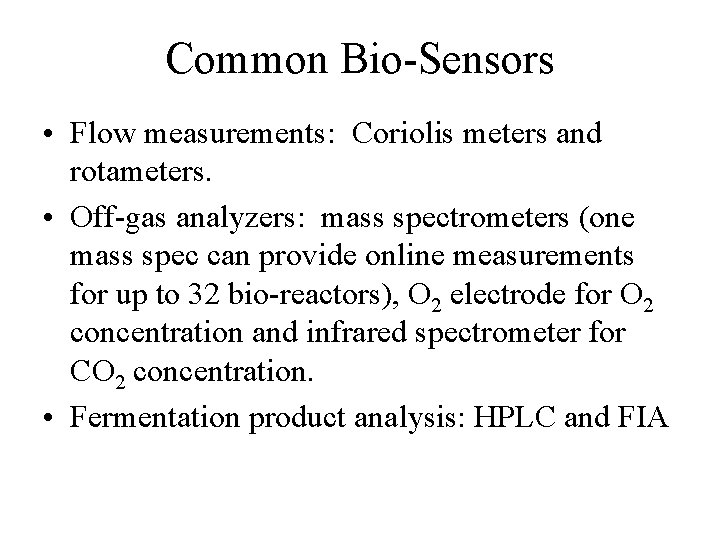
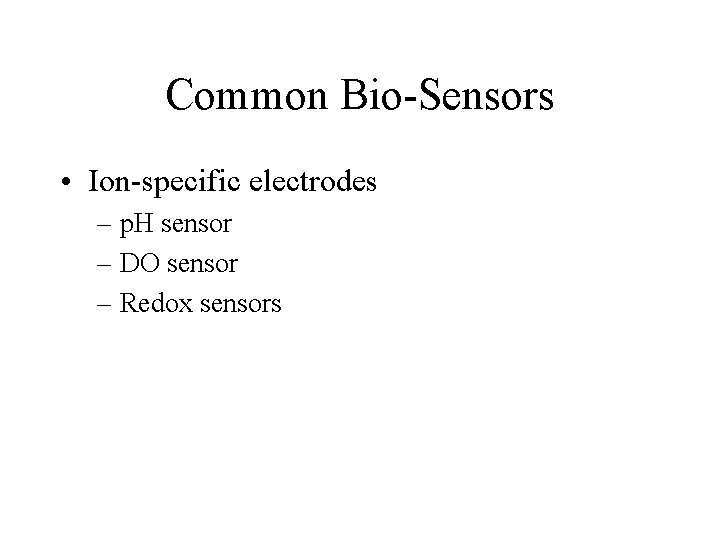
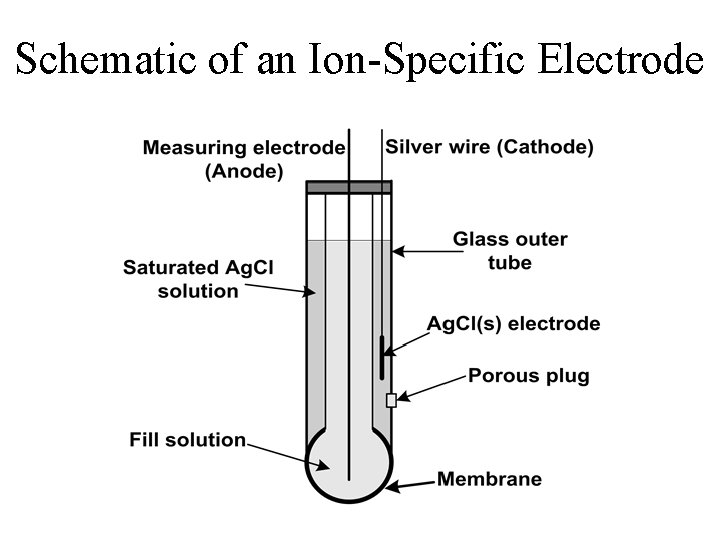
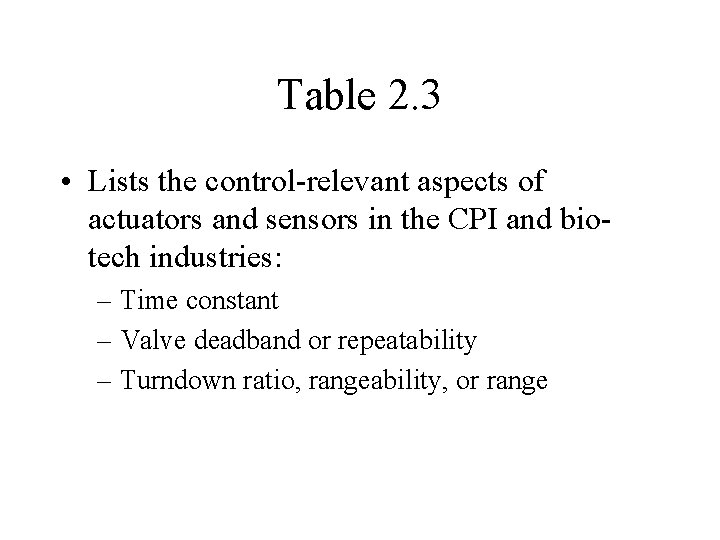
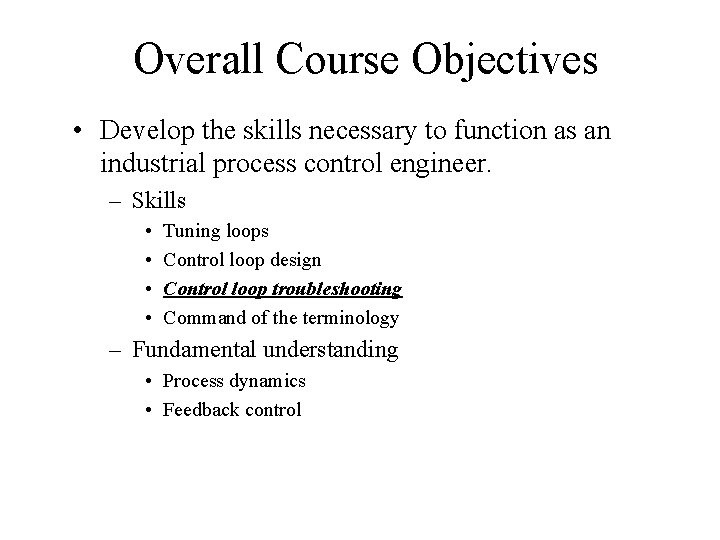
- Slides: 25
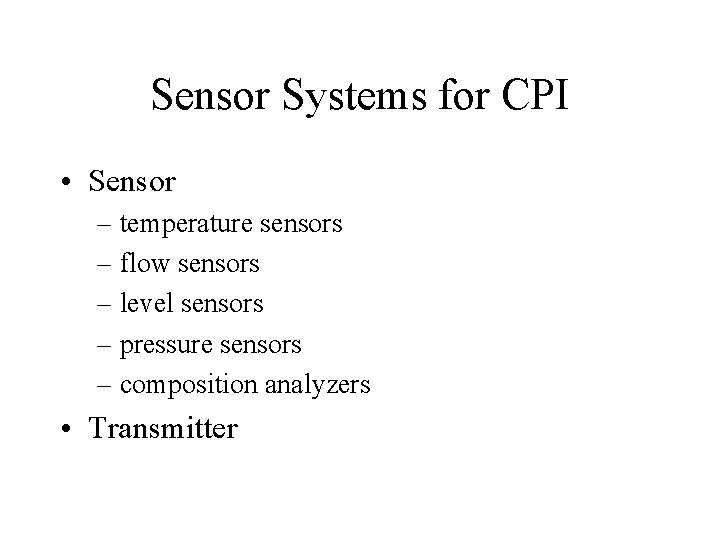
Sensor Systems for CPI • Sensor – temperature sensors – flow sensors – level sensors – pressure sensors – composition analyzers • Transmitter
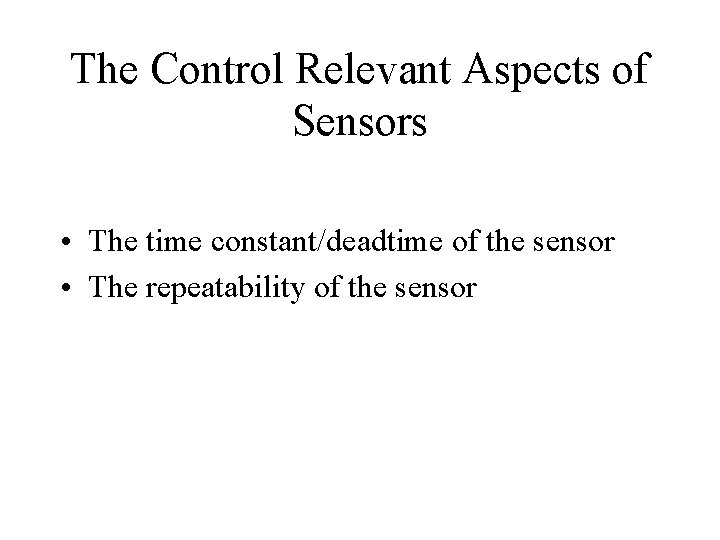
The Control Relevant Aspects of Sensors • The time constant/deadtime of the sensor • The repeatability of the sensor
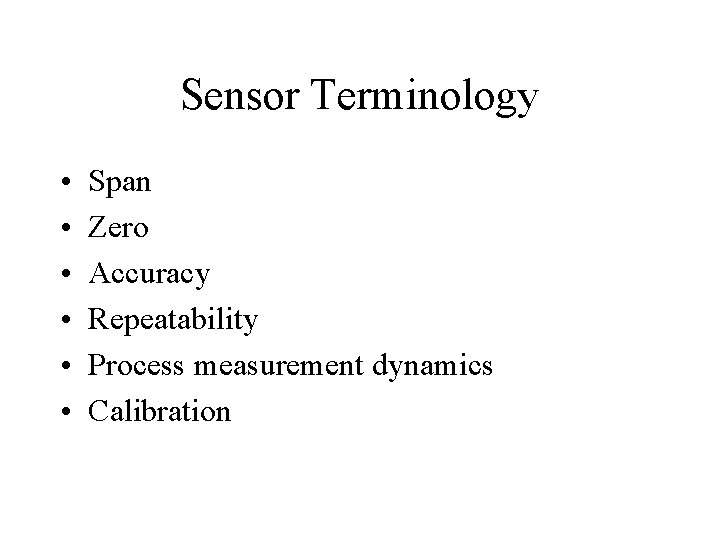
Sensor Terminology • • • Span Zero Accuracy Repeatability Process measurement dynamics Calibration
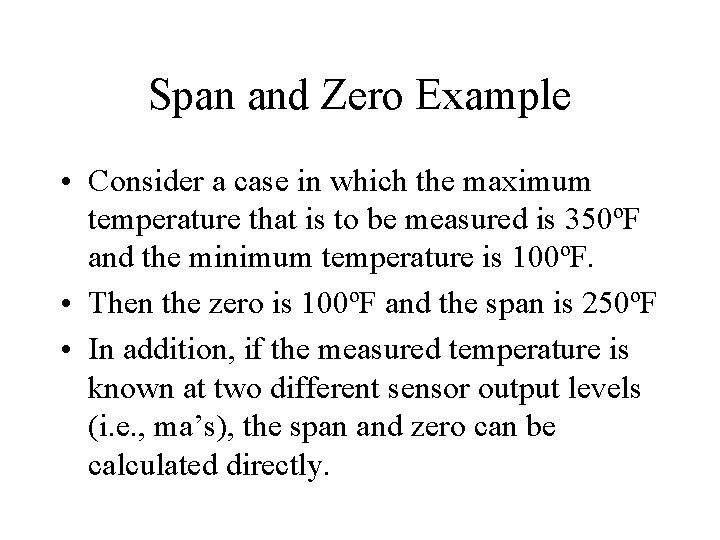
Span and Zero Example • Consider a case in which the maximum temperature that is to be measured is 350ºF and the minimum temperature is 100ºF. • Then the zero is 100ºF and the span is 250ºF • In addition, if the measured temperature is known at two different sensor output levels (i. e. , ma’s), the span and zero can be calculated directly.
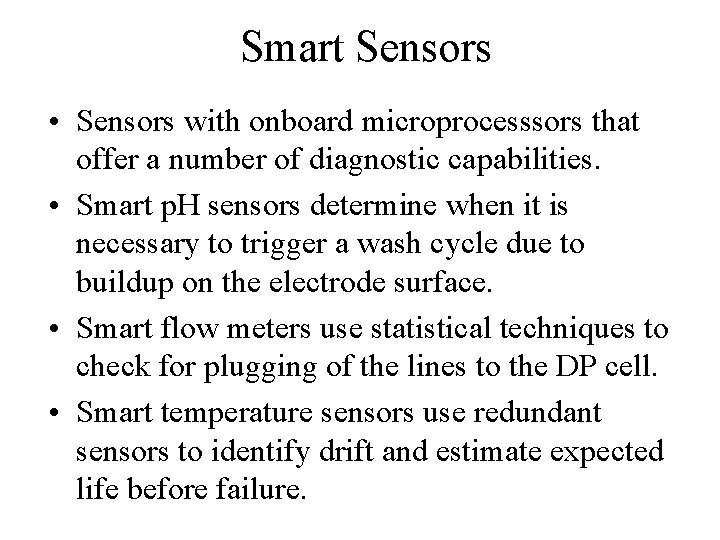
Smart Sensors • Sensors with onboard microprocesssors that offer a number of diagnostic capabilities. • Smart p. H sensors determine when it is necessary to trigger a wash cycle due to buildup on the electrode surface. • Smart flow meters use statistical techniques to check for plugging of the lines to the DP cell. • Smart temperature sensors use redundant sensors to identify drift and estimate expected life before failure.
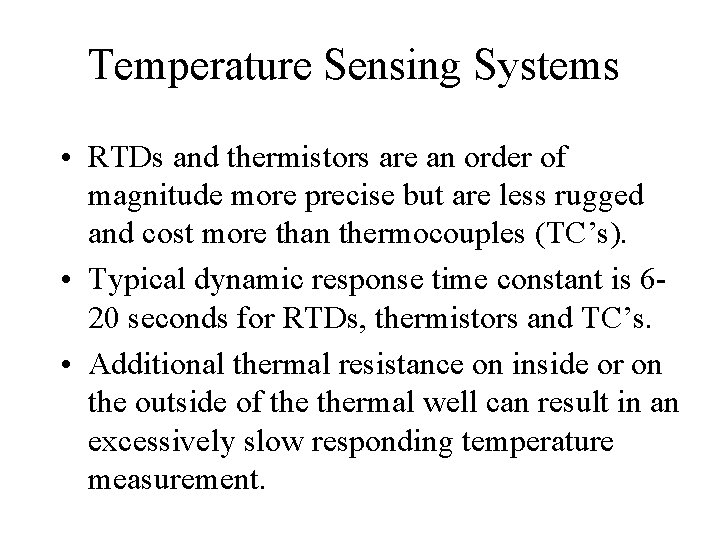
Temperature Sensing Systems • RTDs and thermistors are an order of magnitude more precise but are less rugged and cost more than thermocouples (TC’s). • Typical dynamic response time constant is 620 seconds for RTDs, thermistors and TC’s. • Additional thermal resistance on inside or on the outside of thermal well can result in an excessively slow responding temperature measurement.
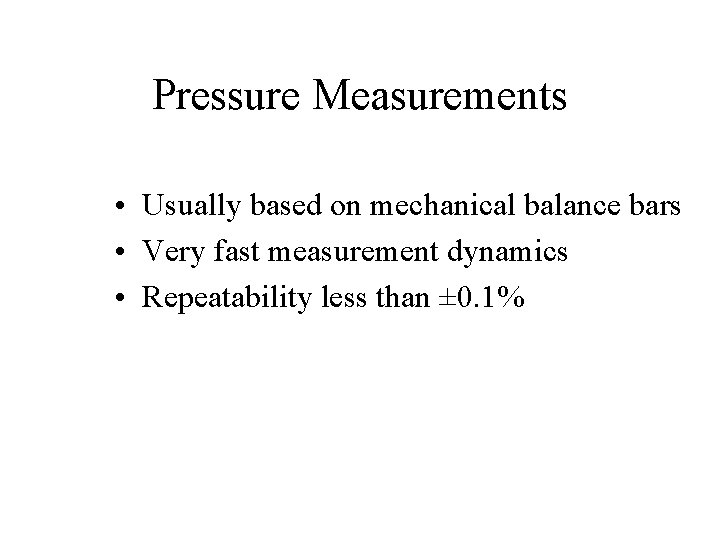
Pressure Measurements • Usually based on mechanical balance bars • Very fast measurement dynamics • Repeatability less than ± 0. 1%

Flow Measurements • Orifice plate/DP cell most common approach. Good repeatability and fast dynamic response. • Magnetic flow meters and vortex shedding flow meters are also used in certain situations. They are more expensive but more reliable and require less maintenance. • A straight run of pipe required for good accuracy for all flow meters.
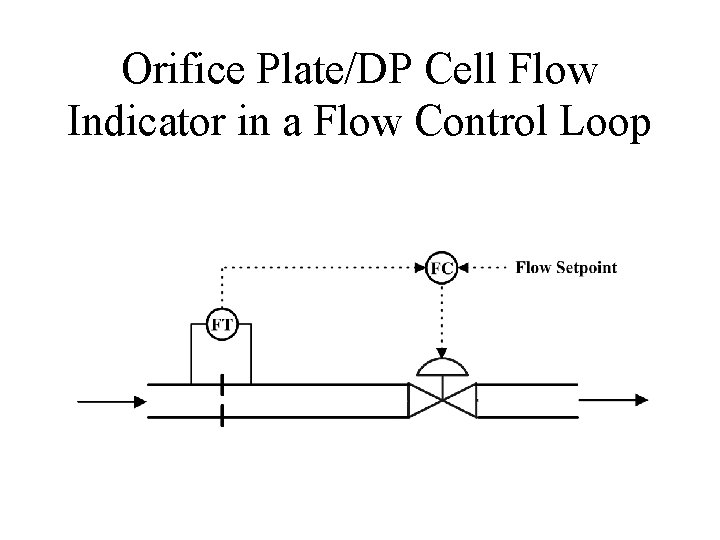
Orifice Plate/DP Cell Flow Indicator in a Flow Control Loop
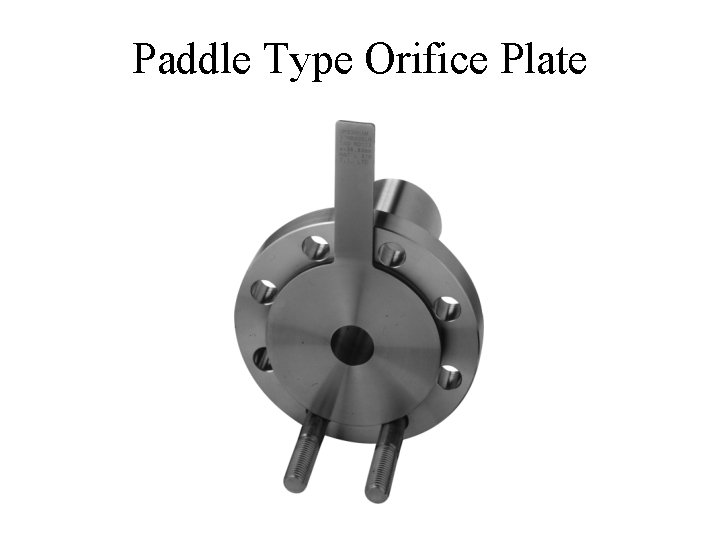
Paddle Type Orifice Plate
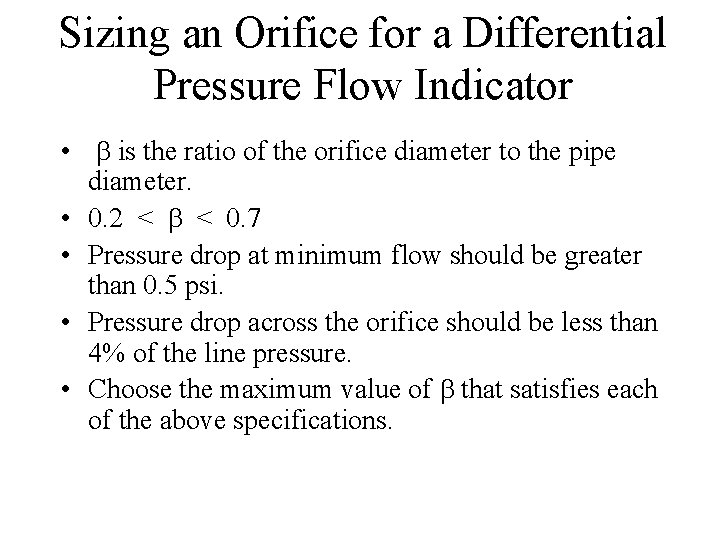
Sizing an Orifice for a Differential Pressure Flow Indicator • b is the ratio of the orifice diameter to the pipe diameter. • 0. 2 < b < 0. 7 • Pressure drop at minimum flow should be greater than 0. 5 psi. • Pressure drop across the orifice should be less than 4% of the line pressure. • Choose the maximum value of b that satisfies each of the above specifications.
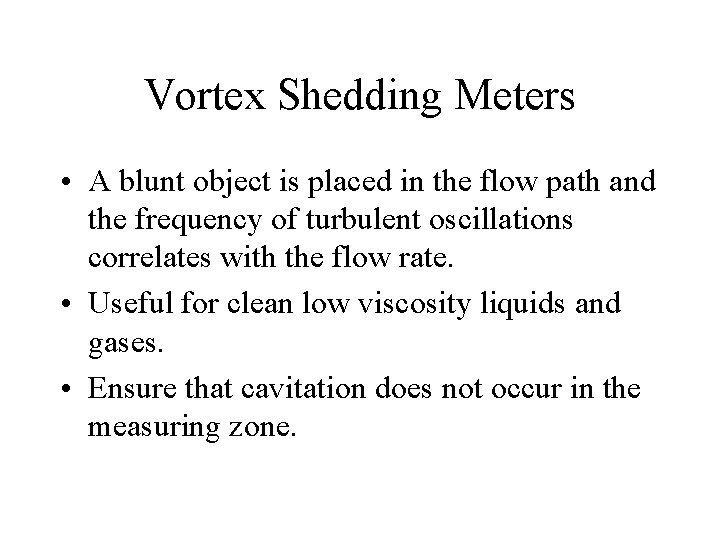
Vortex Shedding Meters • A blunt object is placed in the flow path and the frequency of turbulent oscillations correlates with the flow rate. • Useful for clean low viscosity liquids and gases. • Ensure that cavitation does not occur in the measuring zone.
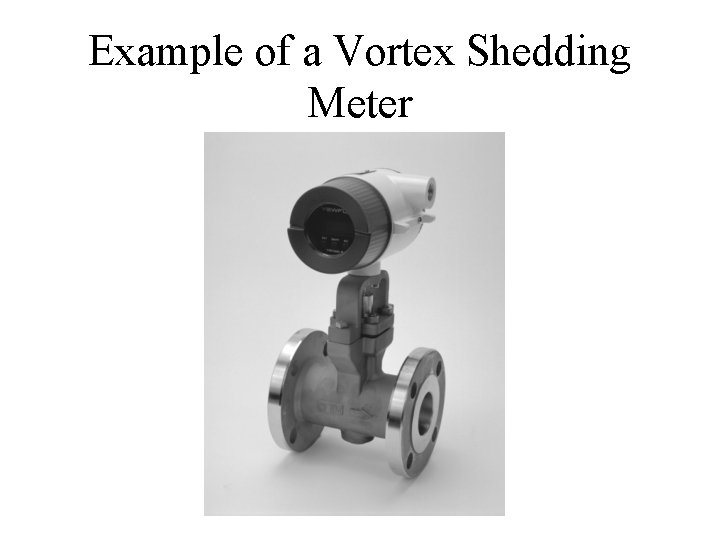
Example of a Vortex Shedding Meter

Magnetic Flow Meters • Based on measuring the current generated by the flow a conducting fluid through a magnetic field. • Have low pressure drop associated with them. • Are applied to conductive fluid (tap water is conductive enough) • Deposition on the electrodes is a limitation. • See picture in text.
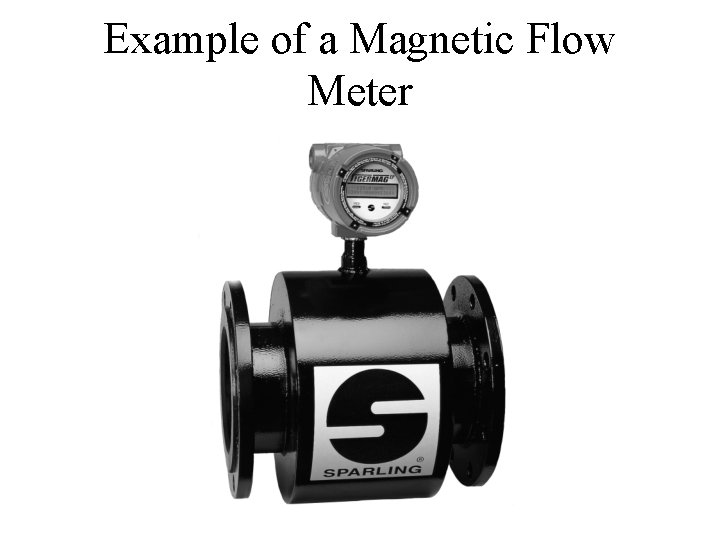
Example of a Magnetic Flow Meter
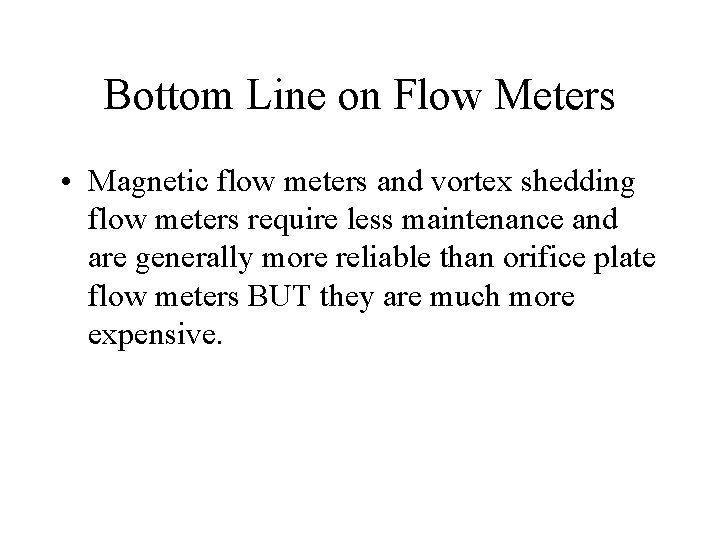
Bottom Line on Flow Meters • Magnetic flow meters and vortex shedding flow meters require less maintenance and are generally more reliable than orifice plate flow meters BUT they are much more expensive.
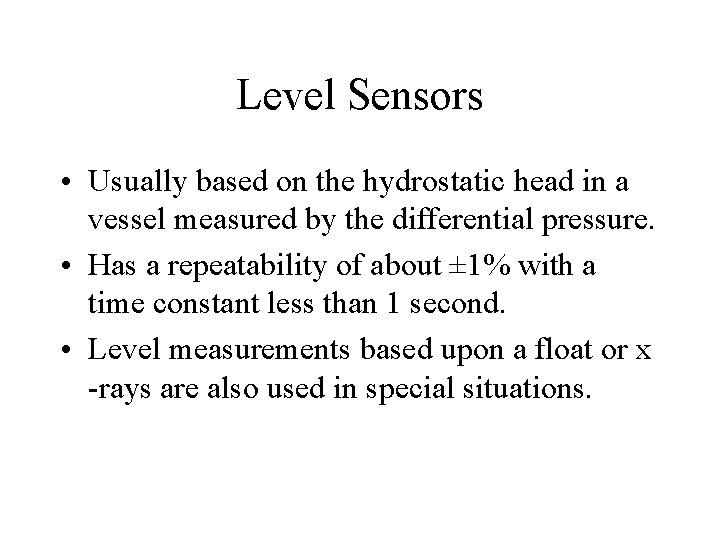
Level Sensors • Usually based on the hydrostatic head in a vessel measured by the differential pressure. • Has a repeatability of about ± 1% with a time constant less than 1 second. • Level measurements based upon a float or x -rays are also used in special situations.
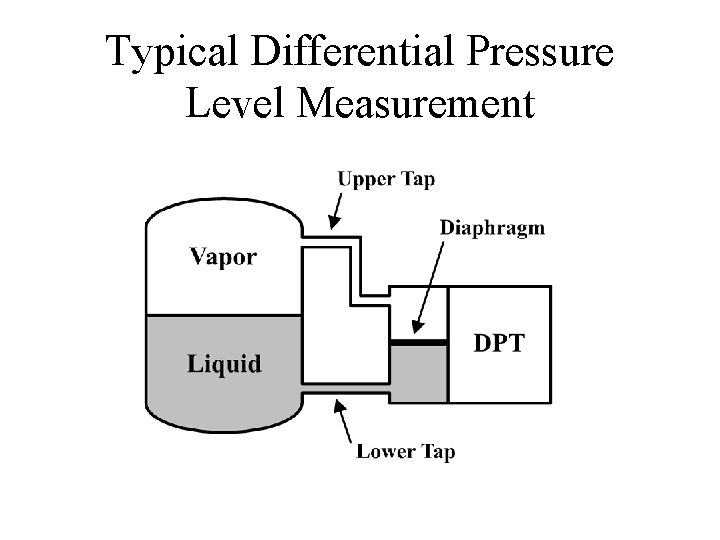
Typical Differential Pressure Level Measurement
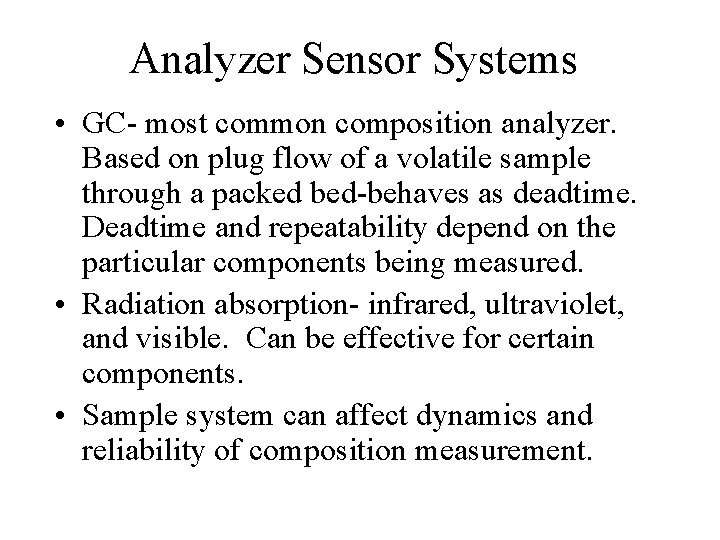
Analyzer Sensor Systems • GC- most common composition analyzer. Based on plug flow of a volatile sample through a packed bed-behaves as deadtime. Deadtime and repeatability depend on the particular components being measured. • Radiation absorption- infrared, ultraviolet, and visible. Can be effective for certain components. • Sample system can affect dynamics and reliability of composition measurement.
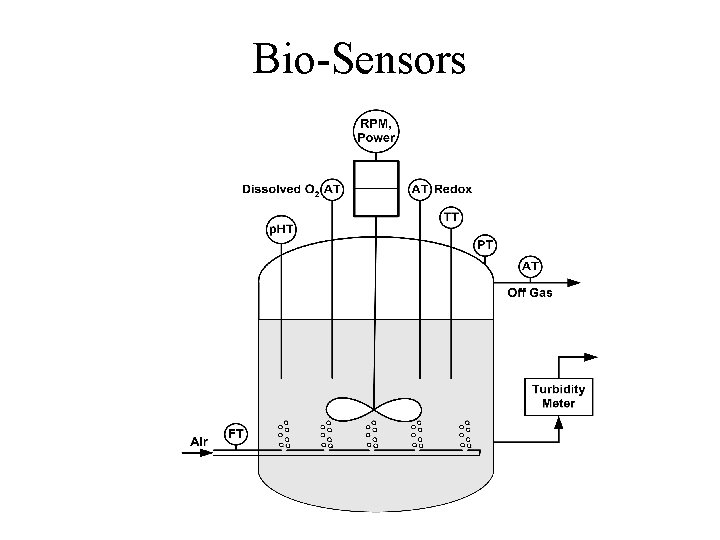
Bio-Sensors
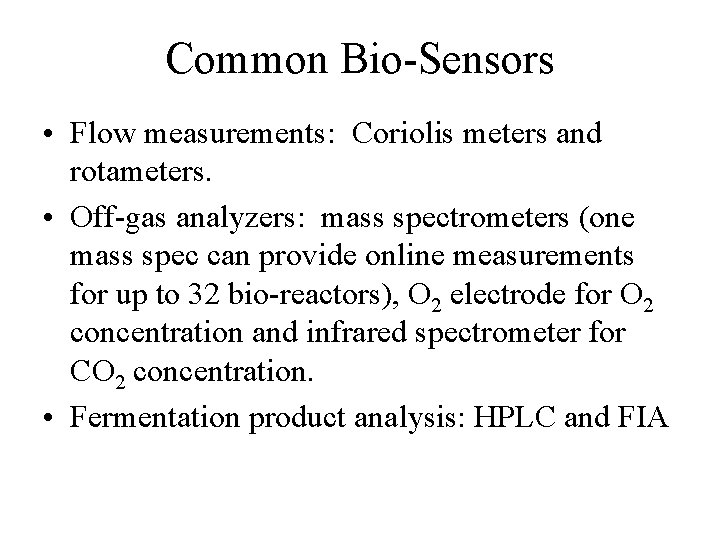
Common Bio-Sensors • Flow measurements: Coriolis meters and rotameters. • Off-gas analyzers: mass spectrometers (one mass spec can provide online measurements for up to 32 bio-reactors), O 2 electrode for O 2 concentration and infrared spectrometer for CO 2 concentration. • Fermentation product analysis: HPLC and FIA
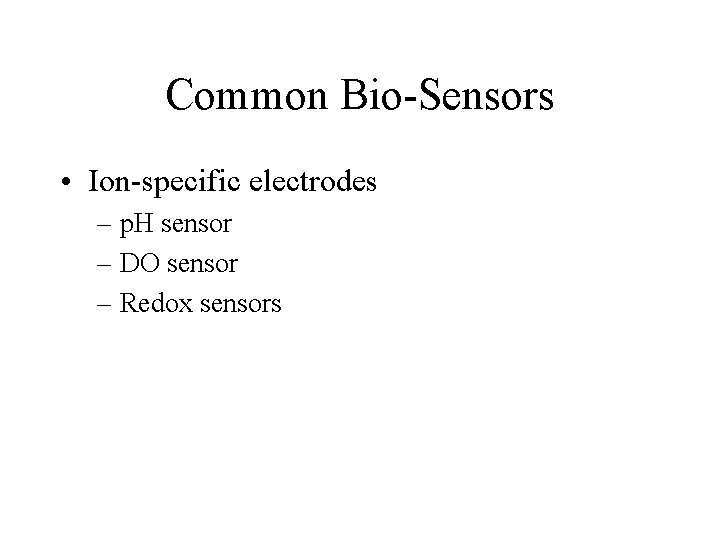
Common Bio-Sensors • Ion-specific electrodes – p. H sensor – DO sensor – Redox sensors
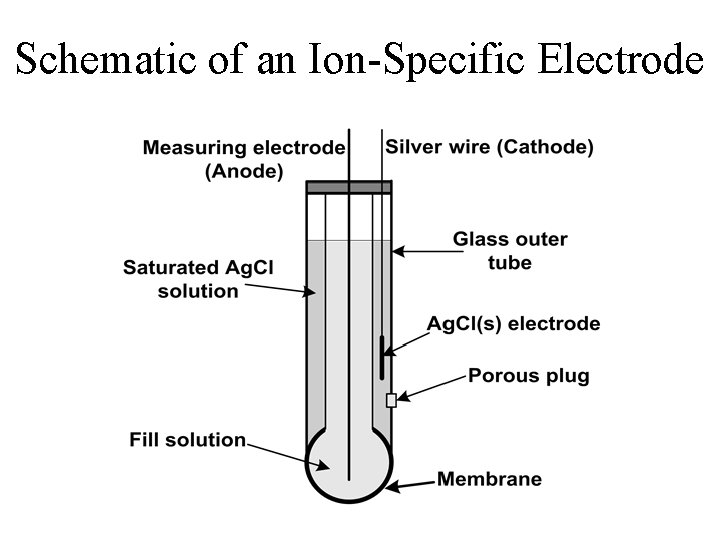
Schematic of an Ion-Specific Electrode
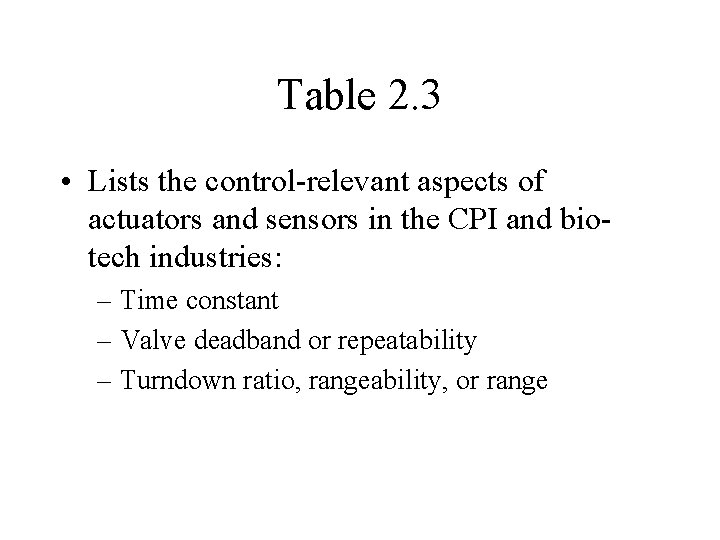
Table 2. 3 • Lists the control-relevant aspects of actuators and sensors in the CPI and biotech industries: – Time constant – Valve deadband or repeatability – Turndown ratio, rangeability, or range
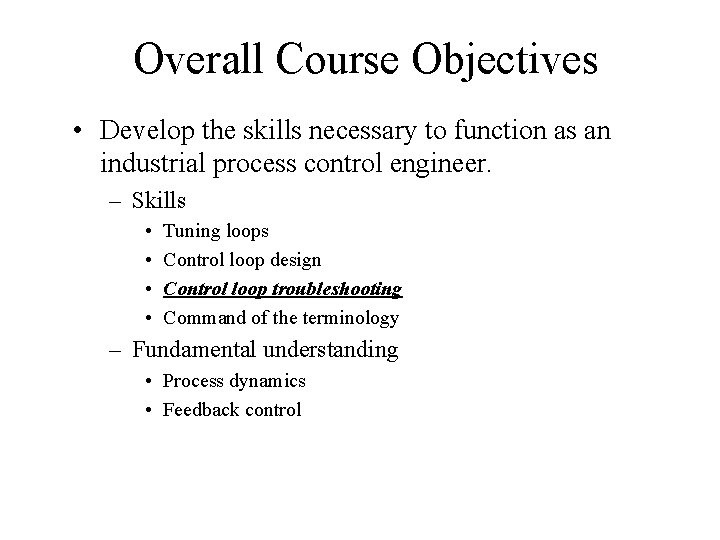
Overall Course Objectives • Develop the skills necessary to function as an industrial process control engineer. – Skills • • Tuning loops Control loop design Control loop troubleshooting Command of the terminology – Fundamental understanding • Process dynamics • Feedback control
Aplikasi sensor suhu
Difference between curie temperature and neel temperature
Difference between curie temperature and neel temperature
Difference between curie temperature and neel temperature
Flow control symbol
Static characteristics of sensors
Wearable inertial sensors
Ergonomic sensors
Smart washroom management system
Conclusion of smart sensors
Oil debris monitoring system
Types of negotiations
Peas vacuum cleaner
Water density sensors
Ieee sensor journal impact factor
Gds sensors
Kmz10b
Chemical sensors ppt
Definition of sensors
Types of electrochemical sensors
How to beat a motion sensor
Exteroceptive sensors examples
System architecture directions for networked sensors
Data nugget streams as sensors answers
Types of sensors in android
Smart sensor networks using bluetooth