Wearable Ergonomic Sensor Technology Neil Chetney MSSE Newport
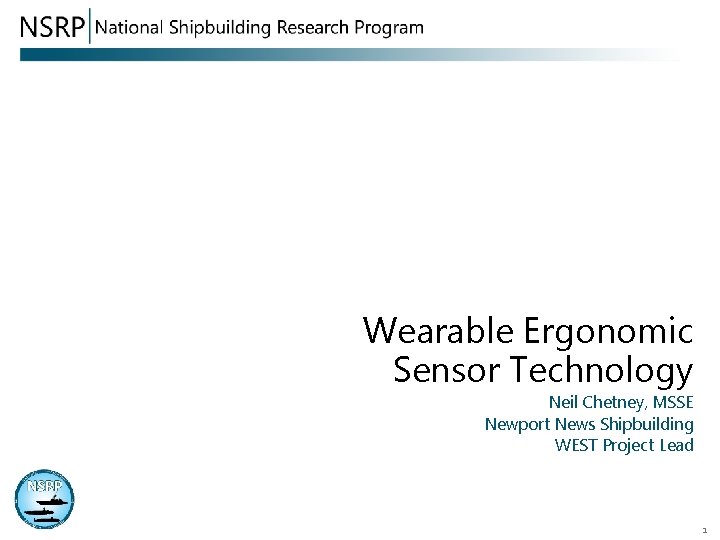
Wearable Ergonomic Sensor Technology Neil Chetney, MSSE Newport News Shipbuilding WEST Project Lead 1
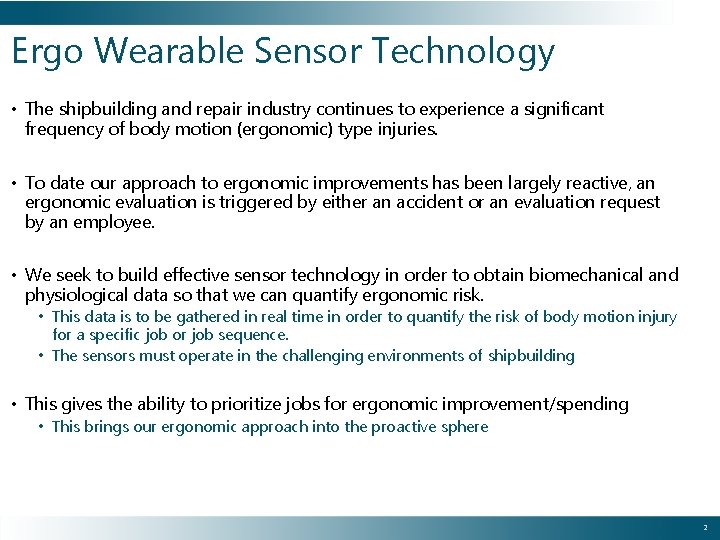
Ergo Wearable Sensor Technology • The shipbuilding and repair industry continues to experience a significant frequency of body motion (ergonomic) type injuries. • To date our approach to ergonomic improvements has been largely reactive, an ergonomic evaluation is triggered by either an accident or an evaluation request by an employee. • We seek to build effective sensor technology in order to obtain biomechanical and physiological data so that we can quantify ergonomic risk. • This data is to be gathered in real time in order to quantify the risk of body motion injury for a specific job or job sequence. • The sensors must operate in the challenging environments of shipbuilding • This gives the ability to prioritize jobs for ergonomic improvement/spending • This brings our ergonomic approach into the proactive sphere 2
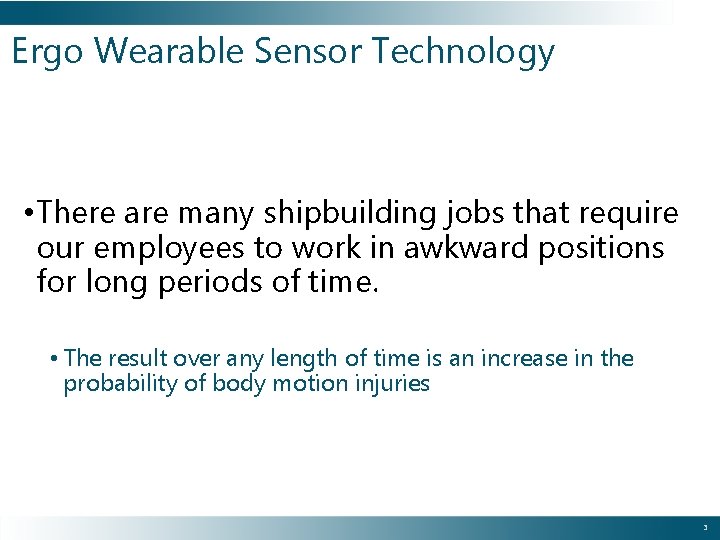
Ergo Wearable Sensor Technology • There are many shipbuilding jobs that require our employees to work in awkward positions for long periods of time. • The result over any length of time is an increase in the probability of body motion injuries 3
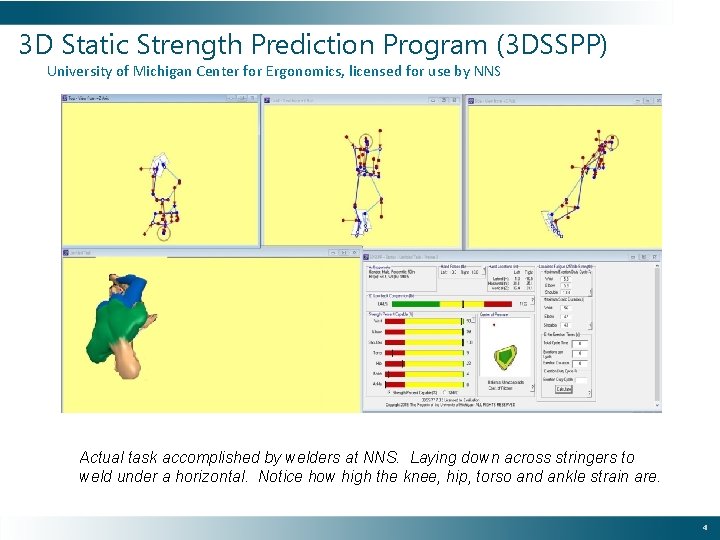
3 D Static Strength Prediction Program (3 DSSPP) University of Michigan Center for Ergonomics, licensed for use by NNS Actual task accomplished by welders at NNS. Laying down across stringers to weld under a horizontal. Notice how high the knee, hip, torso and ankle strain are. 4
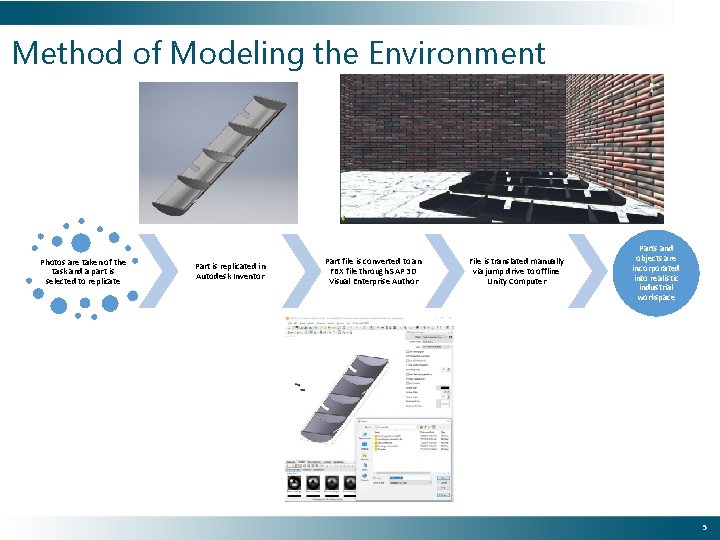
Method of Modeling the Environment Photos are taken of the task and a part is selected to replicate Part is replicated in Autodesk Inventor Part file is converted to an FBX file through SAP 3 D Visual Enterprise Author File is translated manually via jump drive to offline Unity Computer Parts and objects are incorporated into realistic industrial workspace 5
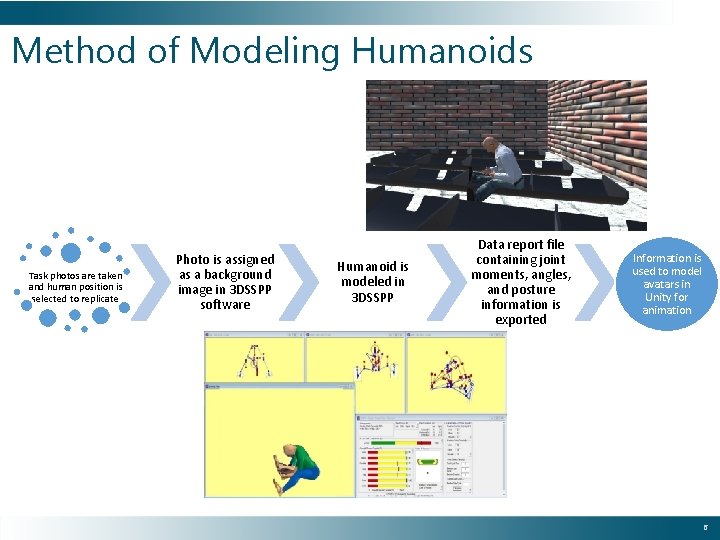
Method of Modeling Humanoids Task photos are taken and human position is selected to replicate Photo is assigned as a background image in 3 DSSPP software Humanoid is modeled in 3 DSSPP Data report file containing joint moments, angles, and posture information is exported Information is used to model avatars in Unity for animation 6
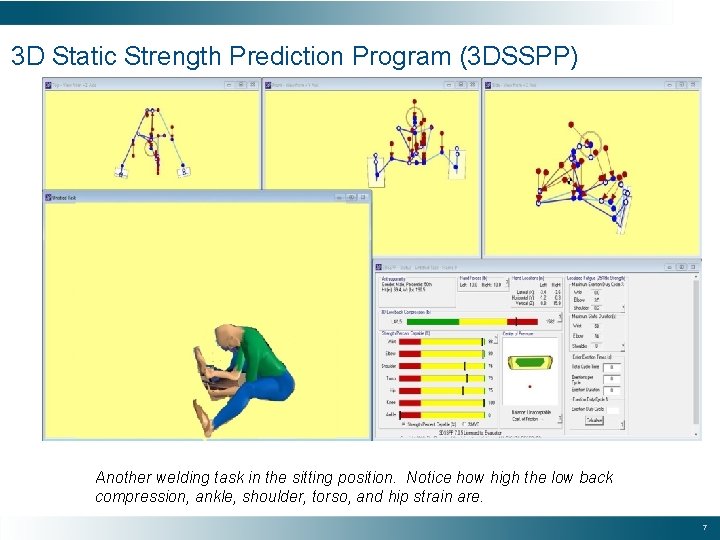
3 D Static Strength Prediction Program (3 DSSPP) Another welding task in the sitting position. Notice how high the low back compression, ankle, shoulder, torso, and hip strain are. 7
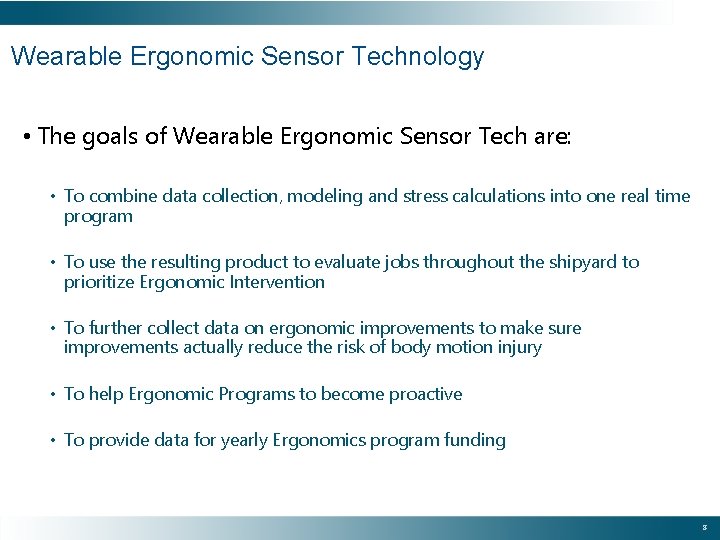
Wearable Ergonomic Sensor Technology • The goals of Wearable Ergonomic Sensor Tech are: • To combine data collection, modeling and stress calculations into one real time program • To use the resulting product to evaluate jobs throughout the shipyard to prioritize Ergonomic Intervention • To further collect data on ergonomic improvements to make sure improvements actually reduce the risk of body motion injury • To help Ergonomic Programs to become proactive • To provide data for yearly Ergonomics program funding 8
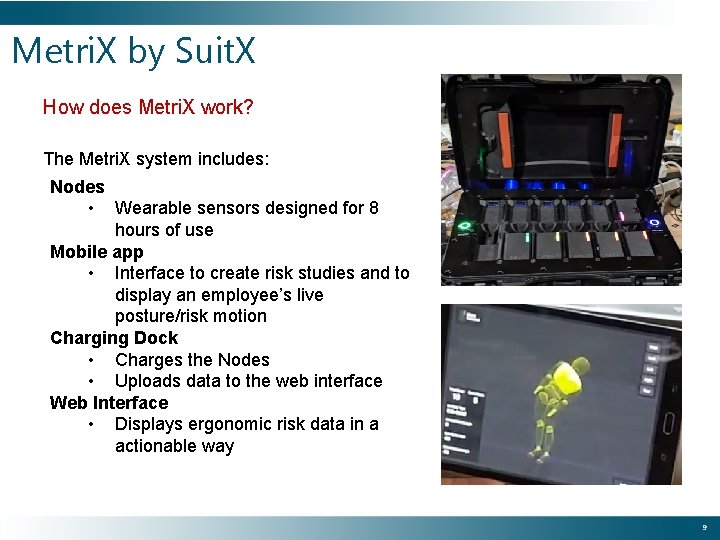
Metri. X by Suit. X How does Metri. X work? The Metri. X system includes: Nodes • Wearable sensors designed for 8 hours of use Mobile app • Interface to create risk studies and to display an employee’s live posture/risk motion Charging Dock • Charges the Nodes • Uploads data to the web interface Web Interface • Displays ergonomic risk data in a actionable way 9
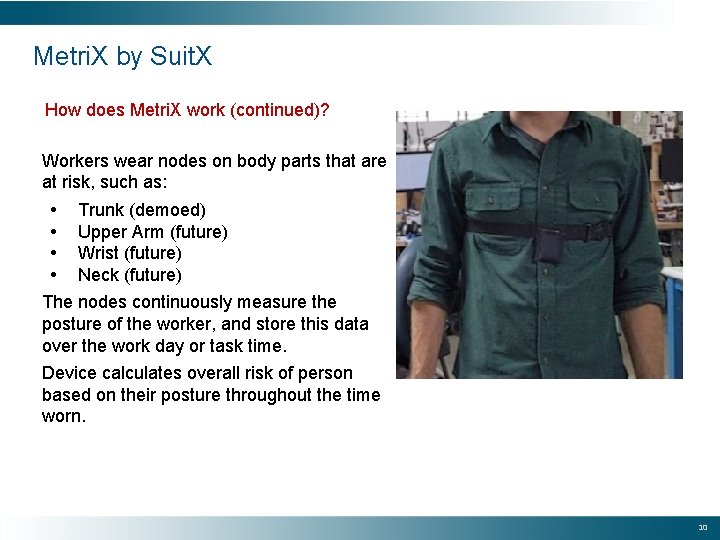
Metri. X by Suit. X How does Metri. X work (continued)? Workers wear nodes on body parts that are at risk, such as: • • Trunk (demoed) Upper Arm (future) Wrist (future) Neck (future) The nodes continuously measure the posture of the worker, and store this data over the work day or task time. Device calculates overall risk of person based on their posture throughout the time worn. 10
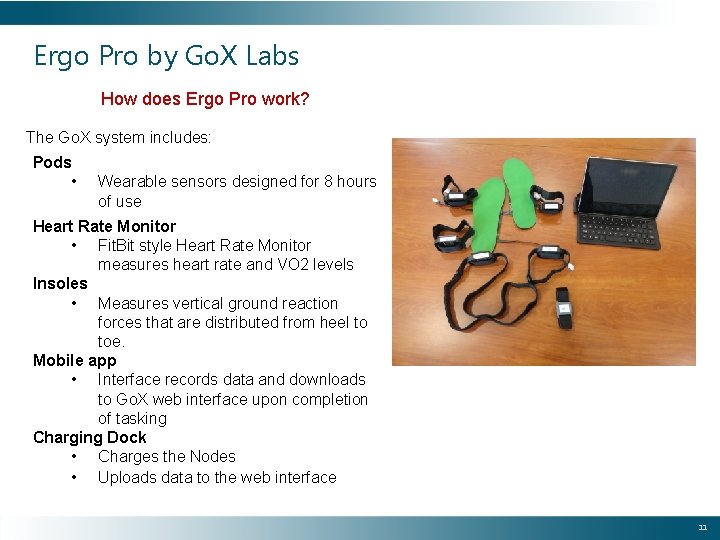
Ergo Pro by Go. X Labs How does Ergo Pro work? The Go. X system includes: Pods • Wearable sensors designed for 8 hours of use Heart Rate Monitor • Fit. Bit style Heart Rate Monitor measures heart rate and VO 2 levels Insoles • Measures vertical ground reaction forces that are distributed from heel to toe. Mobile app • Interface records data and downloads to Go. X web interface upon completion of tasking Charging Dock • Charges the Nodes • Uploads data to the web interface 11
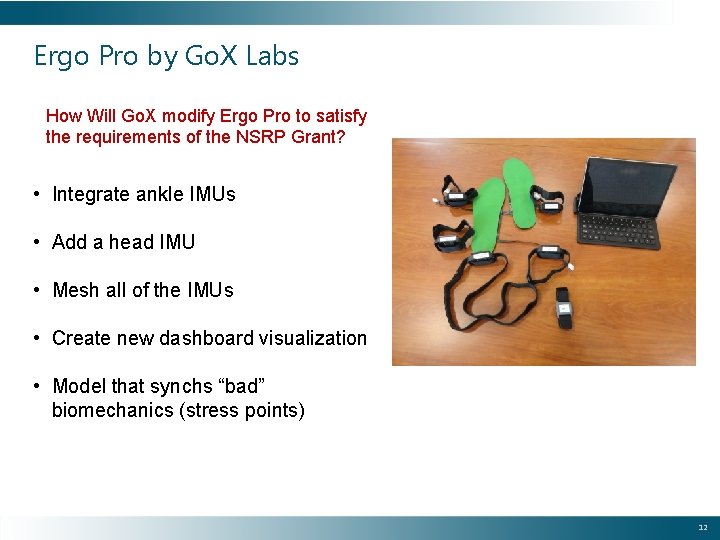
Ergo Pro by Go. X Labs How Will Go. X modify Ergo Pro to satisfy the requirements of the NSRP Grant? • Integrate ankle IMUs • Add a head IMU • Mesh all of the IMUs • Create new dashboard visualization • Model that synchs “bad” biomechanics (stress points) 12
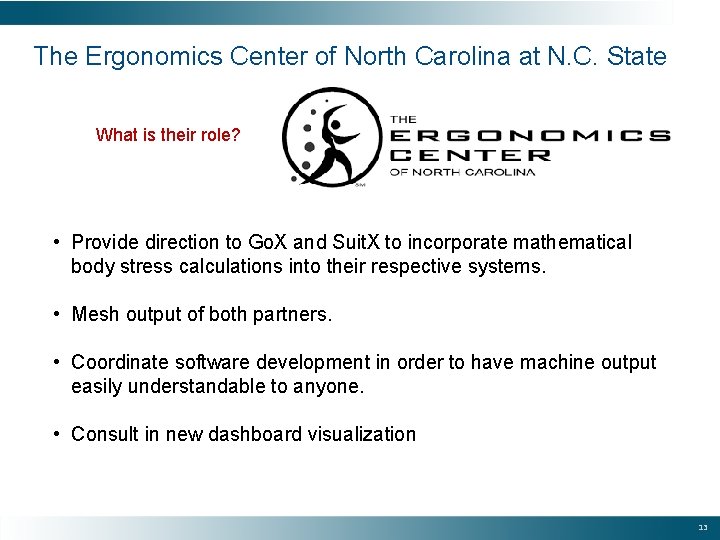
The Ergonomics Center of North Carolina at N. C. State What is their role? • Provide direction to Go. X and Suit. X to incorporate mathematical body stress calculations into their respective systems. • Mesh output of both partners. • Coordinate software development in order to have machine output easily understandable to anyone. • Consult in new dashboard visualization 13
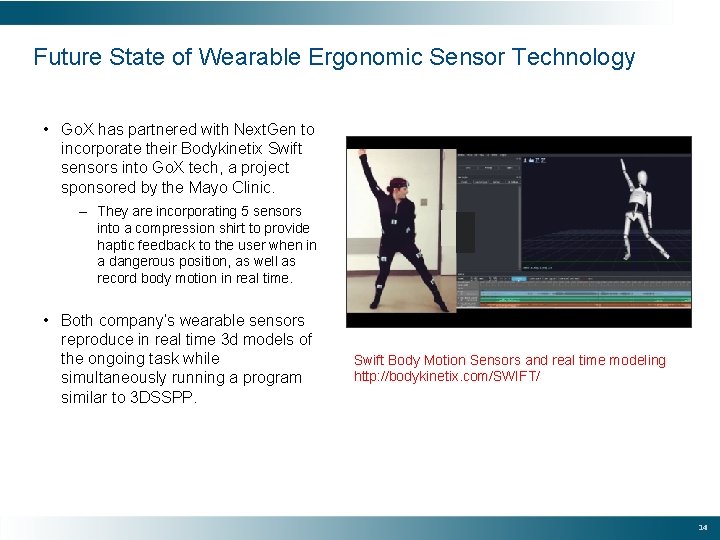
Future State of Wearable Ergonomic Sensor Technology • Go. X has partnered with Next. Gen to incorporate their Bodykinetix Swift sensors into Go. X tech, a project sponsored by the Mayo Clinic. – They are incorporating 5 sensors into a compression shirt to provide haptic feedback to the user when in a dangerous position, as well as record body motion in real time. • Both company’s wearable sensors reproduce in real time 3 d models of the ongoing task while simultaneously running a program similar to 3 DSSPP. Swift Body Motion Sensors and real time modeling http: //bodykinetix. com/SWIFT/ 14
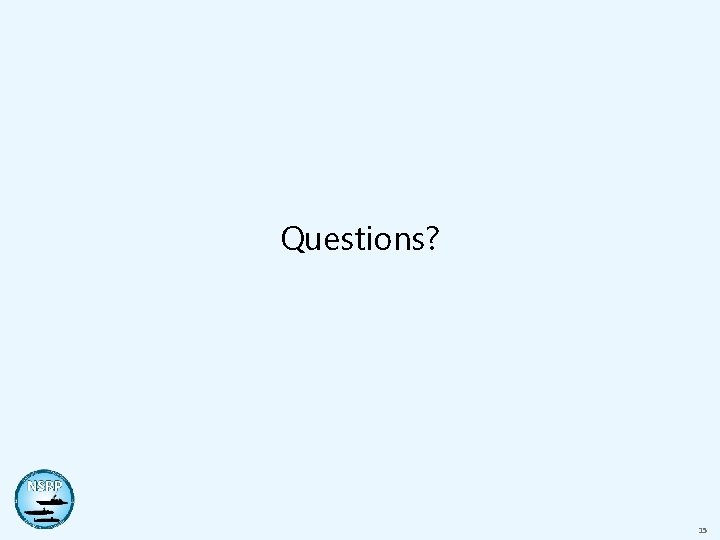
Questions? 15
- Slides: 15