Safety Leadership for Front Line Supervisors FLS Milestones
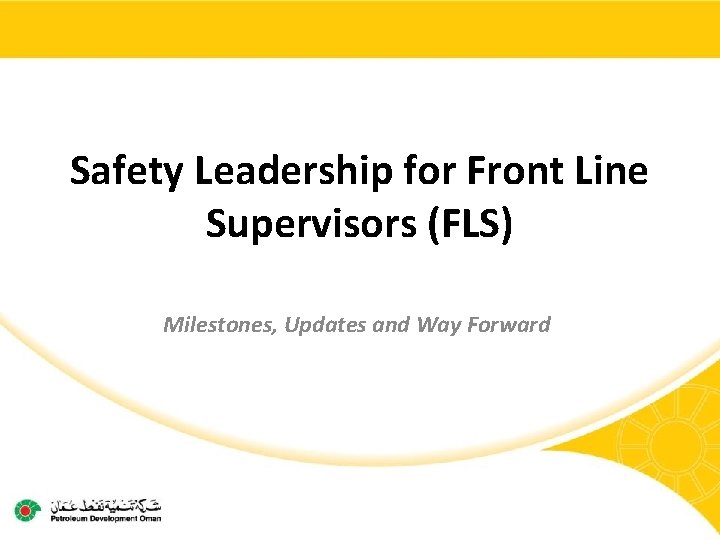
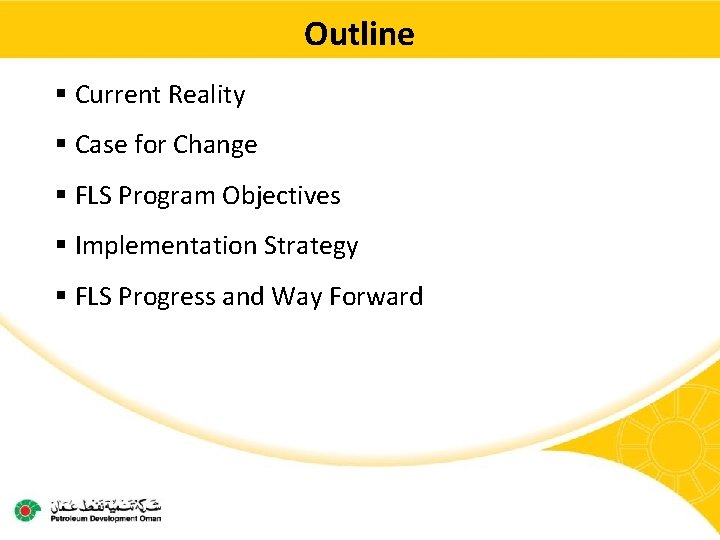
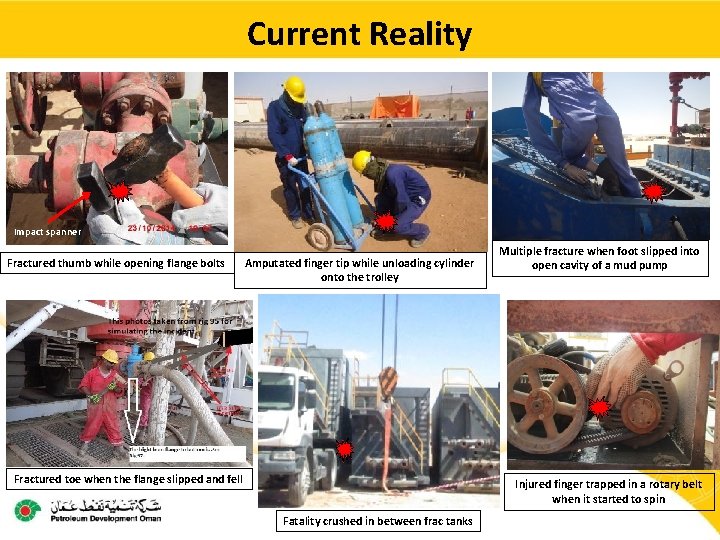
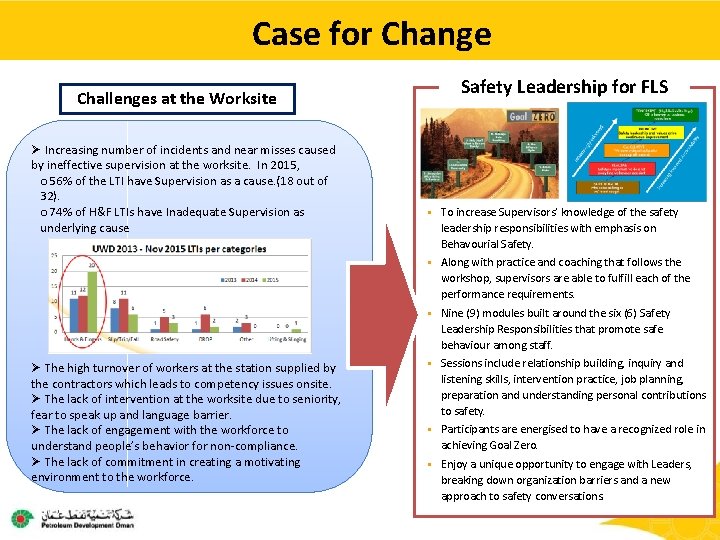
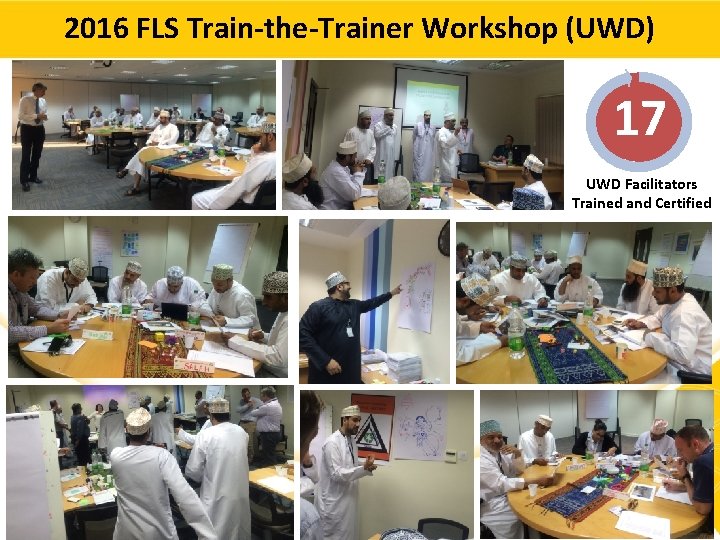
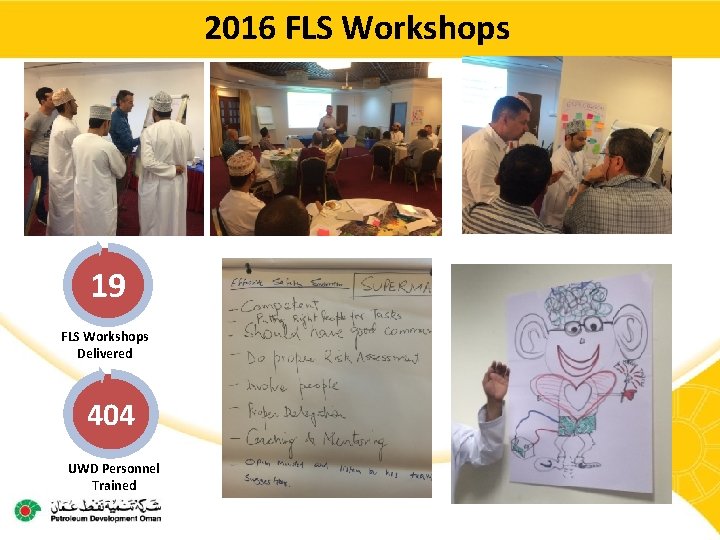
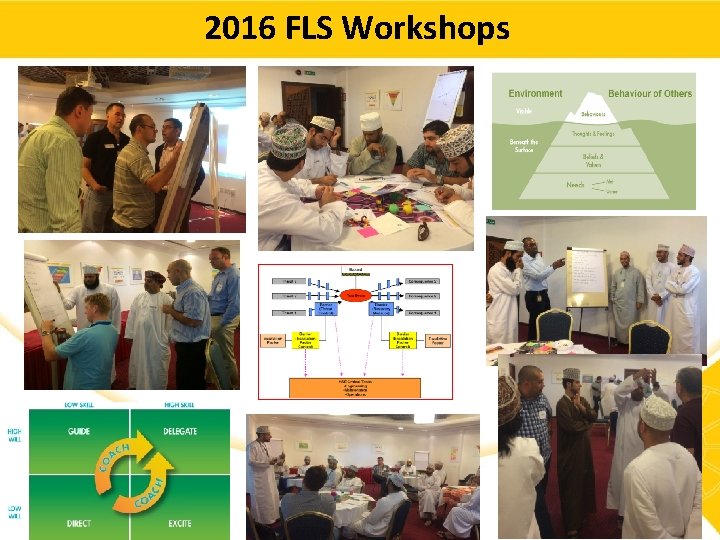
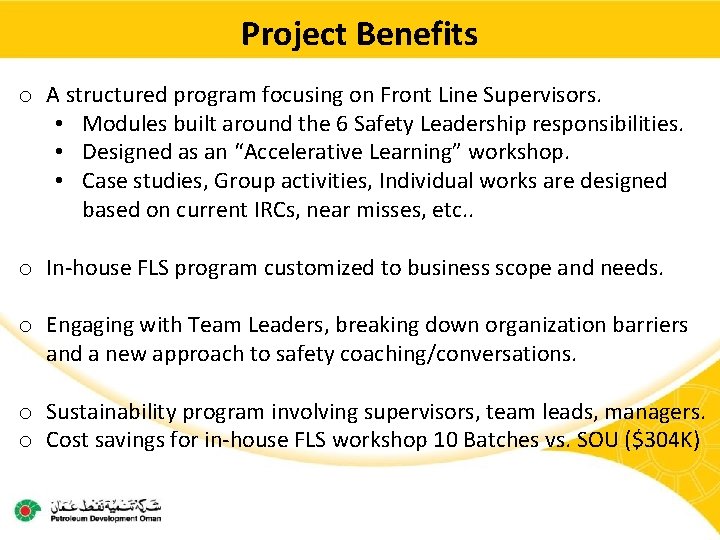
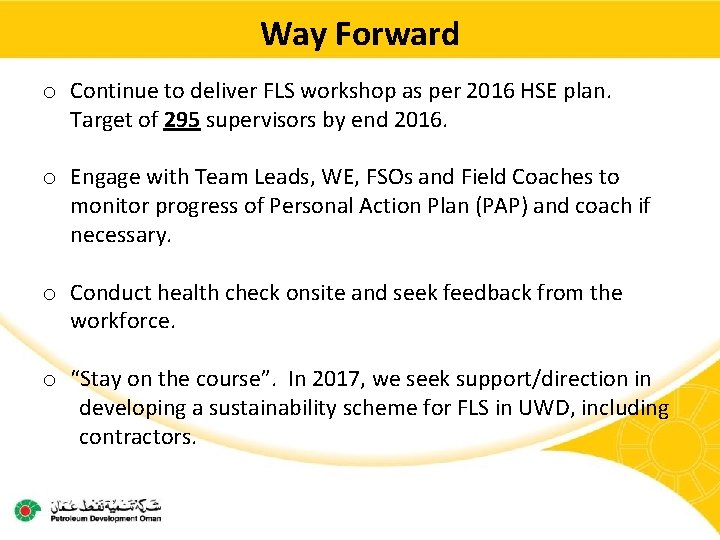
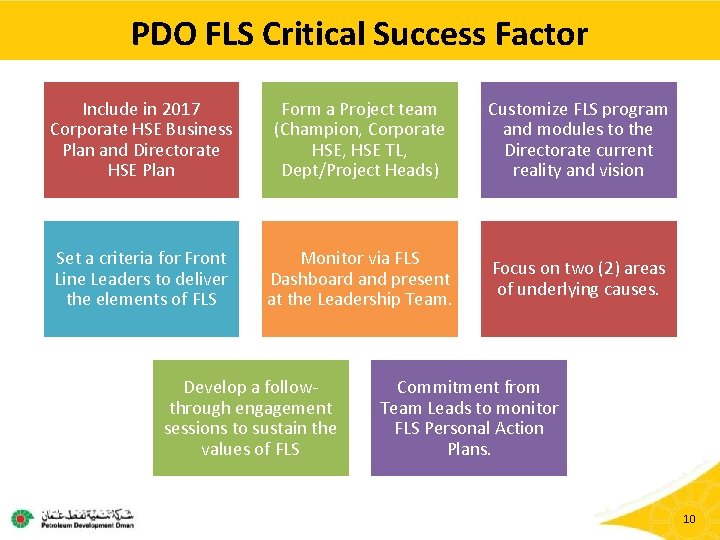
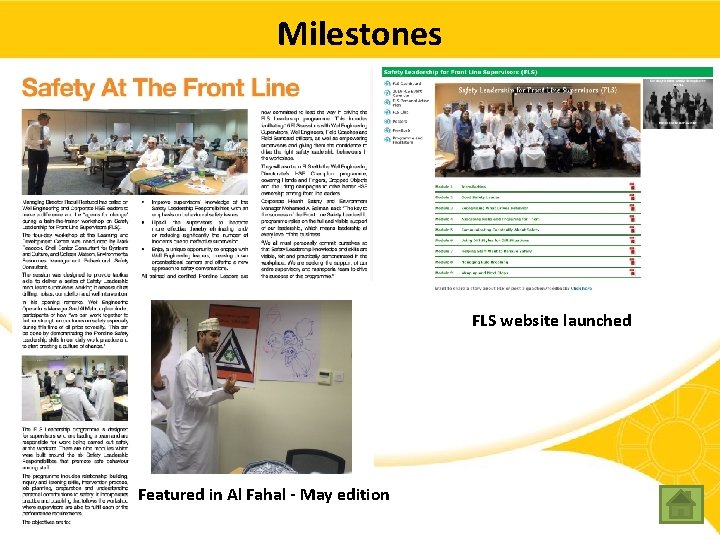
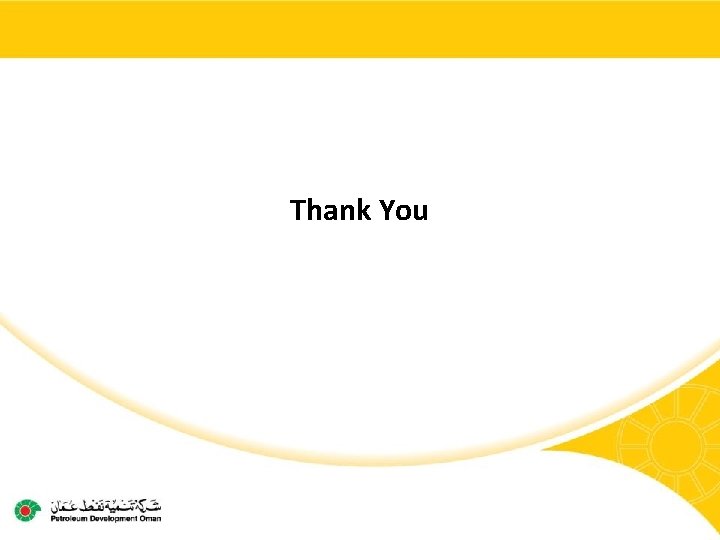
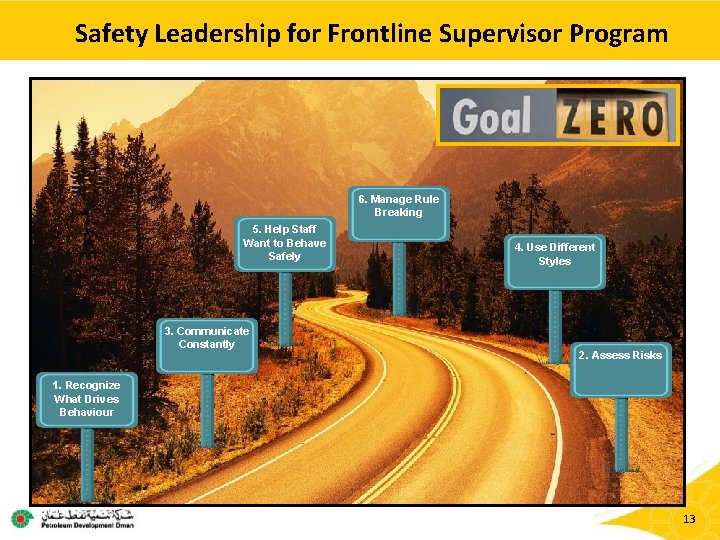
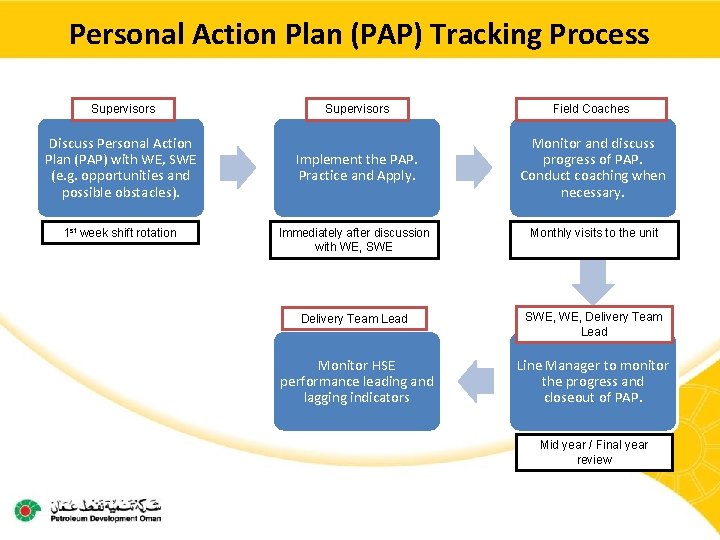
- Slides: 14
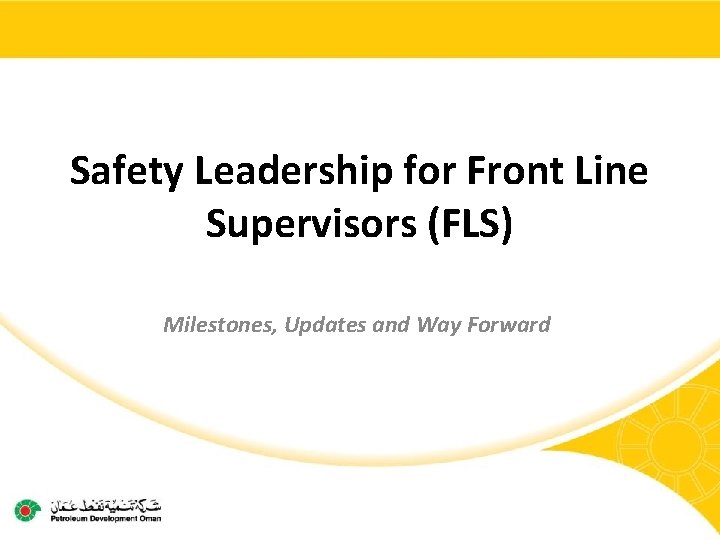
Safety Leadership for Front Line Supervisors (FLS) Milestones, Updates and Way Forward
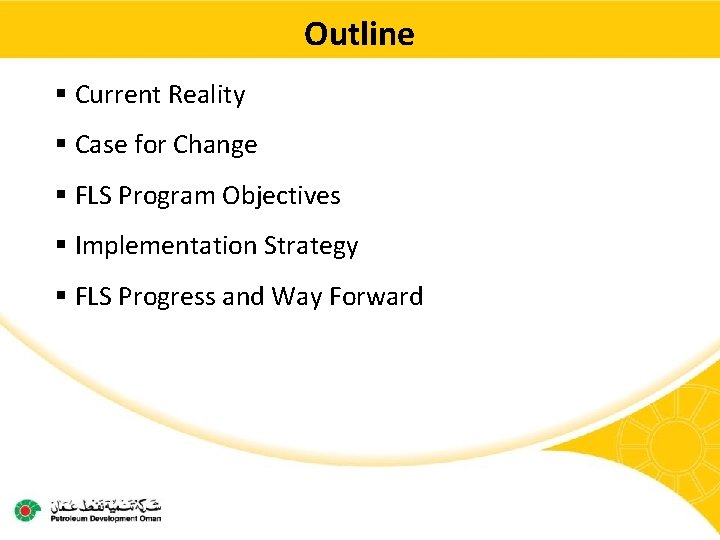
Outline § Current Reality § Case for Change § FLS Program Objectives § Implementation Strategy § FLS Progress and Way Forward
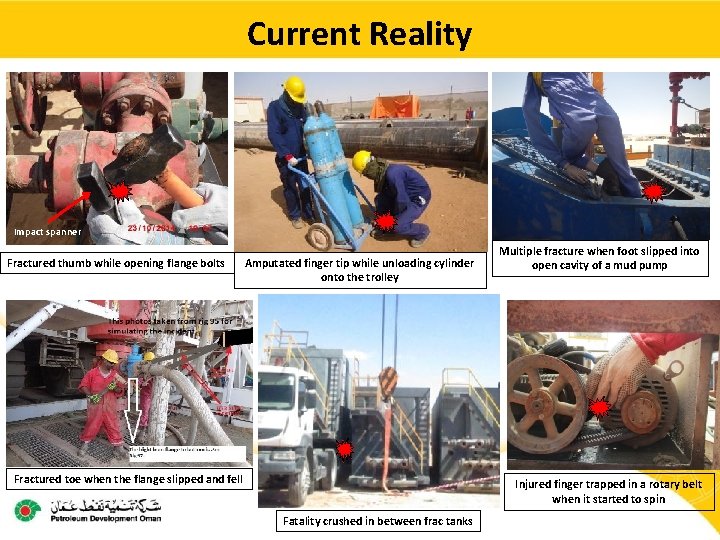
Current Reality Impact spanner Fractured thumb while opening flange bolts Amputated finger tip while unloading cylinder onto the trolley Fractured toe when the flange slipped and fell Multiple fracture when foot slipped into open cavity of a mud pump Injured finger trapped in a rotary belt when it started to spin Fatality crushed in between frac tanks
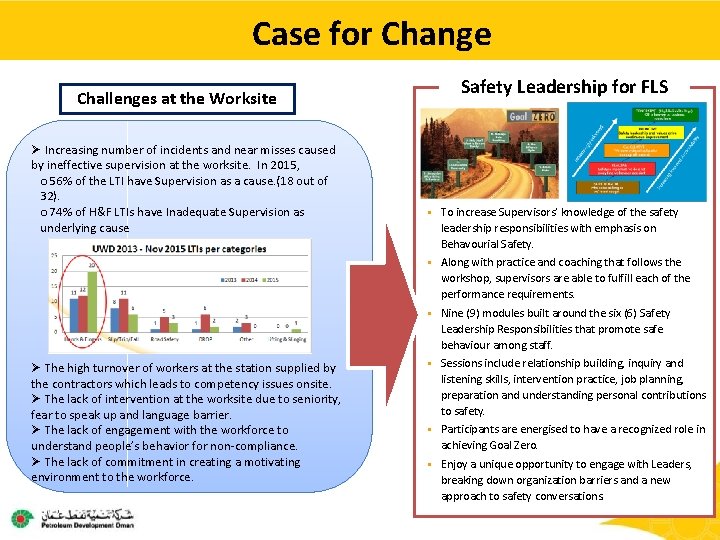
Case for Change Challenges at the Worksite Ø Increasing number of incidents and near misses caused by ineffective supervision at the worksite. In 2015, o 56% of the LTI have Supervision as a cause. (18 out of 32). o 74% of H&F LTIs have Inadequate Supervision as underlying cause Safety Leadership for FLS § To increase Supervisors’ knowledge of the safety leadership responsibilities with emphasis on Behavourial Safety. § Along with practice and coaching that follows the workshop, supervisors are able to fulfill each of the performance requirements. § Nine (9) modules built around the six (6) Safety Leadership Responsibilities that promote safe behaviour among staff. Ø The high turnover of workers at the station supplied by the contractors which leads to competency issues onsite. Ø The lack of intervention at the worksite due to seniority, fear to speak up and language barrier. Ø The lack of engagement with the workforce to understand people’s behavior for non-compliance. Ø The lack of commitment in creating a motivating environment to the workforce. § Sessions include relationship building, inquiry and listening skills, intervention practice, job planning, preparation and understanding personal contributions to safety. § Participants are energised to have a recognized role in achieving Goal Zero. § Enjoy a unique opportunity to engage with Leaders, breaking down organization barriers and a new approach to safety conversations.
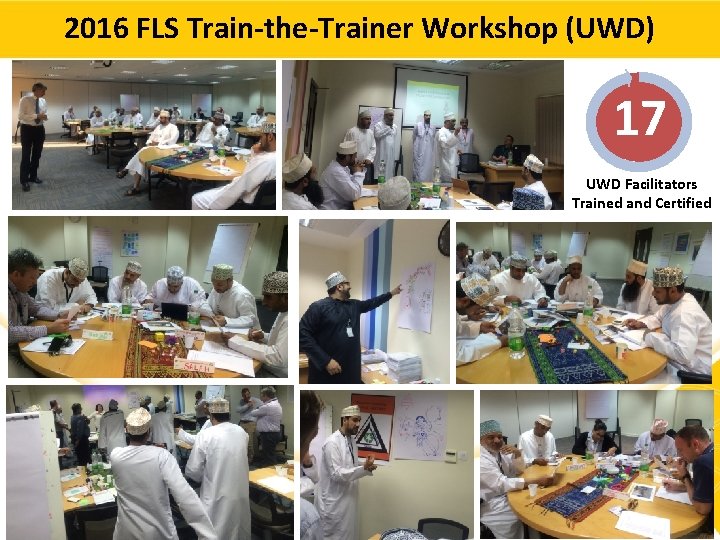
2016 FLS Train-the-Trainer Workshop (UWD) 17 UWD Facilitators Trained and Certified
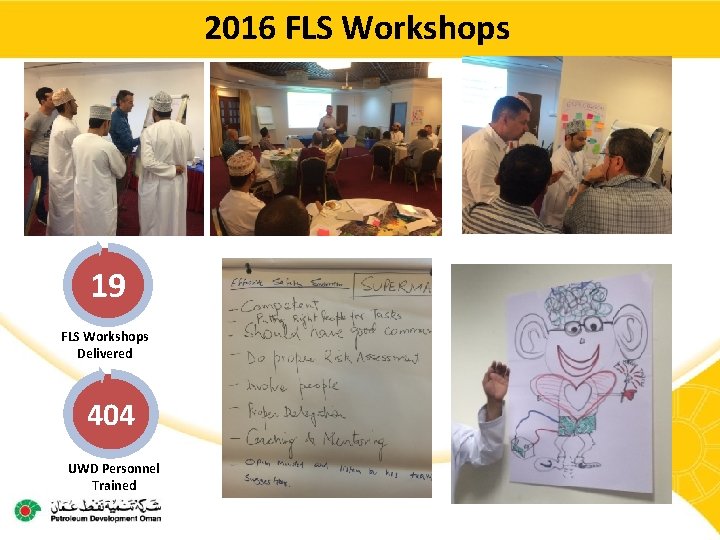
2016 FLS Workshops 19 FLS Workshops Delivered 404 UWD Personnel Trained
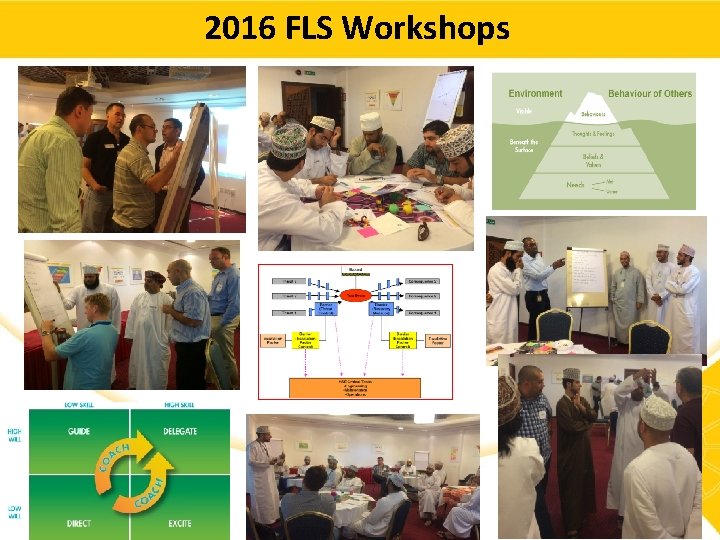
2016 FLS Workshops
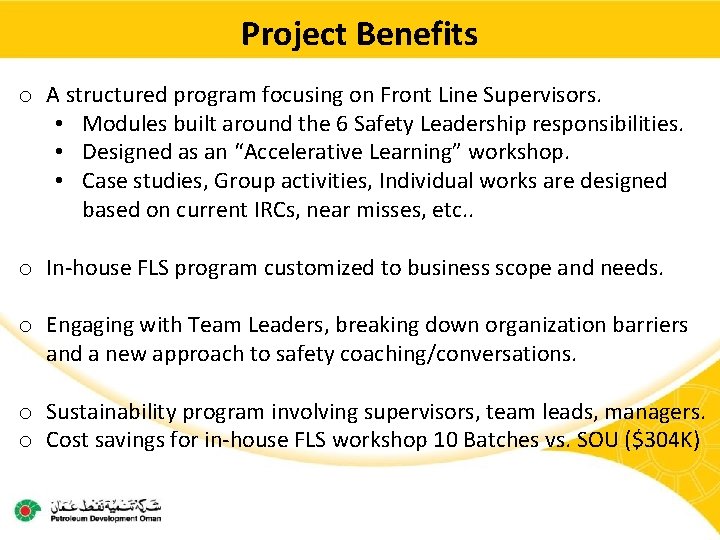
Project Benefits o A structured program focusing on Front Line Supervisors. • Modules built around the 6 Safety Leadership responsibilities. • Designed as an “Accelerative Learning” workshop. • Case studies, Group activities, Individual works are designed based on current IRCs, near misses, etc. . o In-house FLS program customized to business scope and needs. o Engaging with Team Leaders, breaking down organization barriers and a new approach to safety coaching/conversations. o Sustainability program involving supervisors, team leads, managers. o Cost savings for in-house FLS workshop 10 Batches vs. SOU ($304 K)
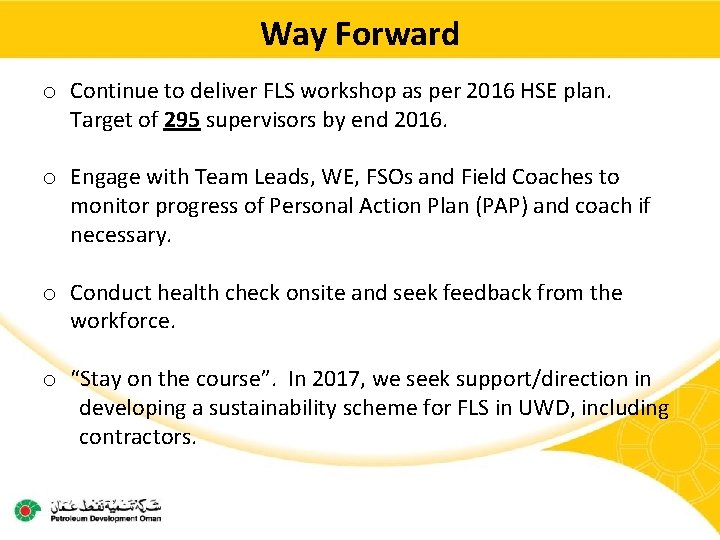
Way Forward o Continue to deliver FLS workshop as per 2016 HSE plan. Target of 295 supervisors by end 2016. o Engage with Team Leads, WE, FSOs and Field Coaches to monitor progress of Personal Action Plan (PAP) and coach if necessary. o Conduct health check onsite and seek feedback from the workforce. o “Stay on the course”. In 2017, we seek support/direction in developing a sustainability scheme for FLS in UWD, including contractors.
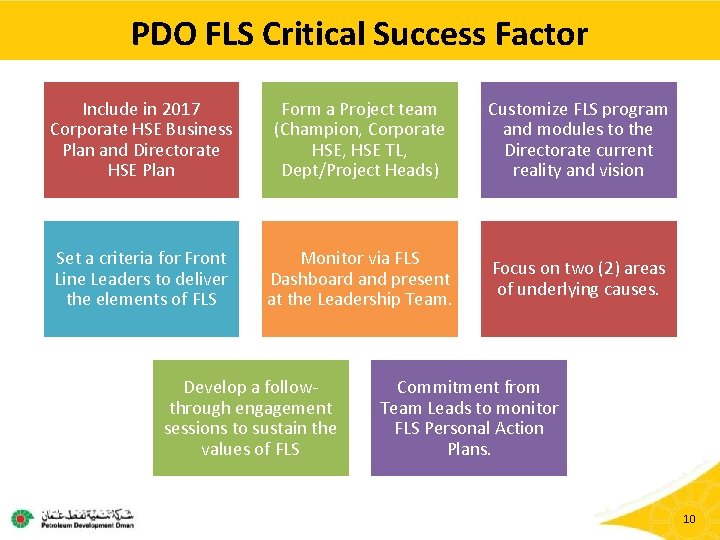
PDO FLS Critical Success Factor Include in 2017 Corporate HSE Business Plan and Directorate HSE Plan Form a Project team (Champion, Corporate HSE, HSE TL, Dept/Project Heads) Customize FLS program and modules to the Directorate current reality and vision Set a criteria for Front Line Leaders to deliver the elements of FLS Monitor via FLS Dashboard and present at the Leadership Team. Focus on two (2) areas of underlying causes. Develop a followthrough engagement sessions to sustain the values of FLS Commitment from Team Leads to monitor FLS Personal Action Plans. 10
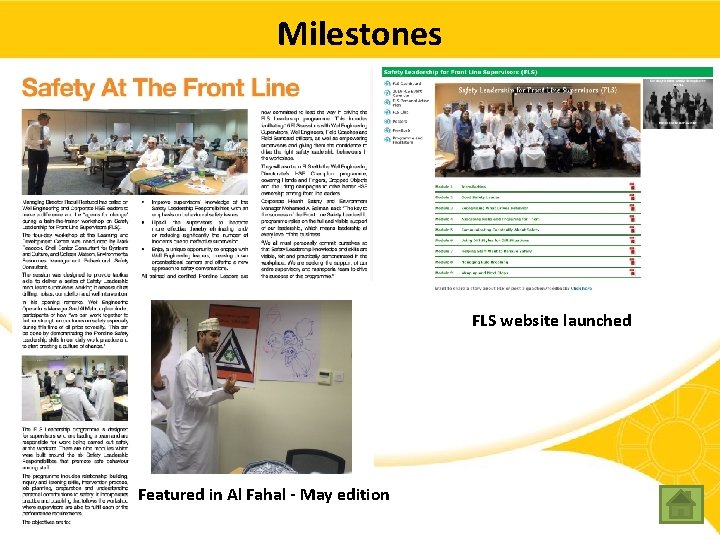
Milestones FLS website launched Featured in Al Fahal - May edition
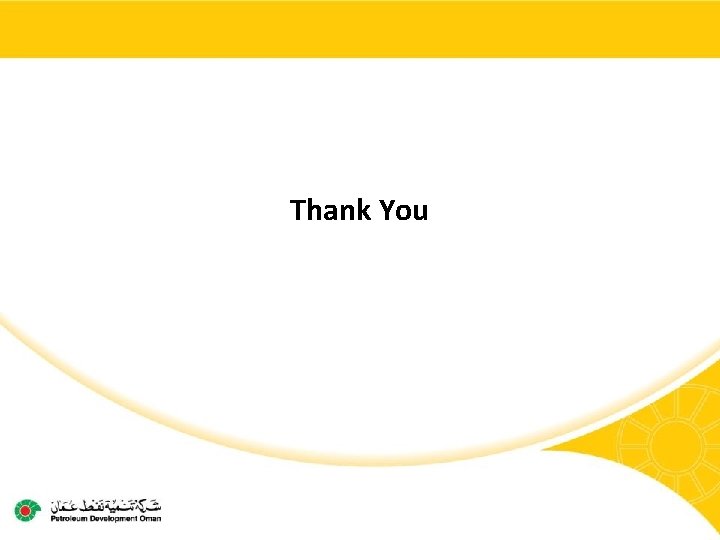
Thank You
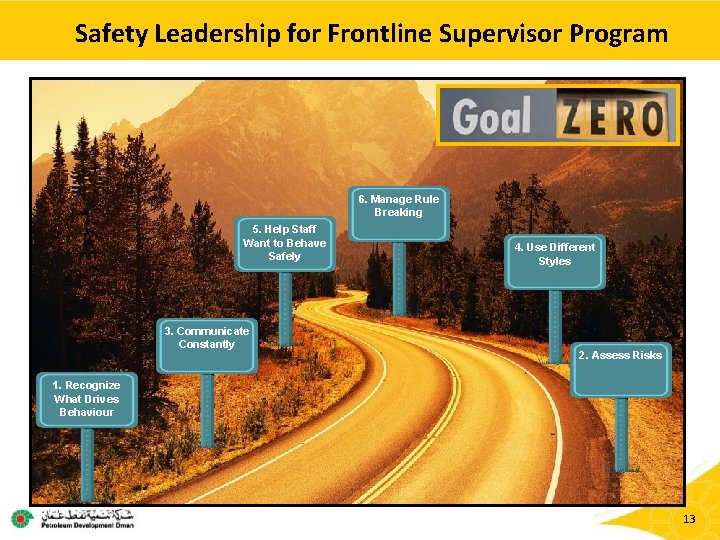
Safety Leadership for Frontline Supervisor Program 6. Manage Rule Breaking 5. Help Staff Want to Behave Safely 3. Communicate Constantly 4. Use Different Styles 2. Assess Risks 1. Recognize What Drives Behaviour 13
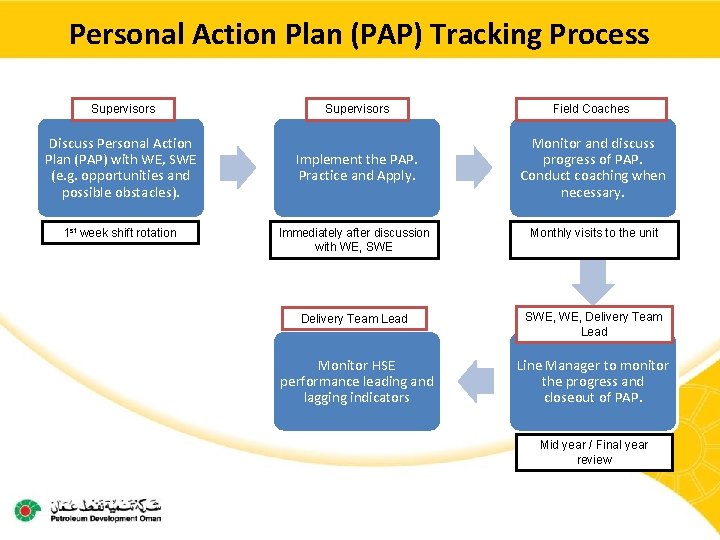
Personal Action Plan (PAP) Tracking Process Supervisors Discuss Personal Action Plan (PAP) with WE, SWE (e. g. opportunities and possible obstacles). 1 st week shift rotation Supervisors Field Coaches Implement the PAP. Practice and Apply. Monitor and discuss progress of PAP. Conduct coaching when necessary. Immediately after discussion with WE, SWE Monthly visits to the unit Delivery Team Lead SWE, Delivery Team Lead Monitor HSE performance leading and lagging indicators Line Manager to monitor the progress and closeout of PAP. Mid year / Final year review
Hse culture ladder
Fls
Fls 1993
Carecapture
Fls 2581
Amaya casnav
Tn attendance supervisors conference
Eeo training for managers
Ounces of ice cream in a large milkshake
Ergonomics awareness training for supervisors
Ergonomics awareness training for supervisors
Eeo compliance training for managers and supervisors
Danger zones for supervisors
Trinity county board of supervisors meeting
Bath county board of supervisors