Ptype thermoelectric properties of stoichiometric fullHeusler alloy Fe
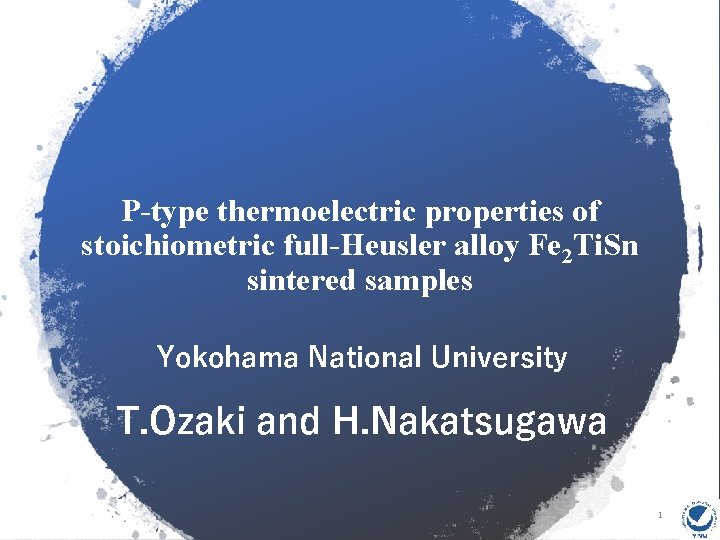
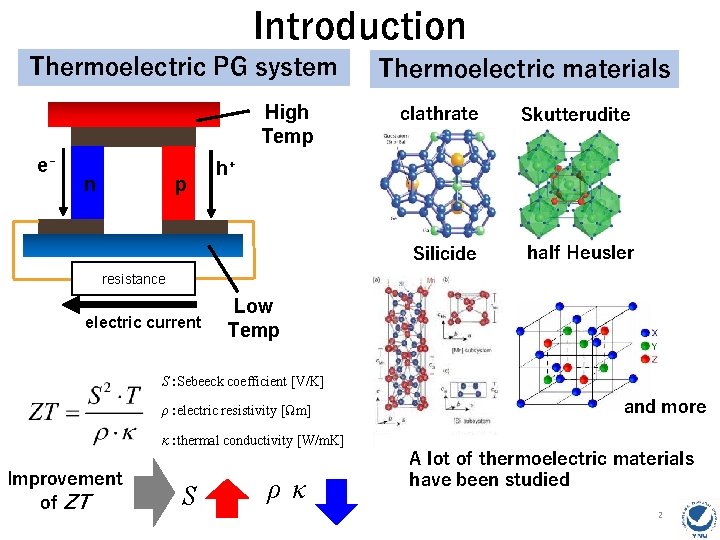
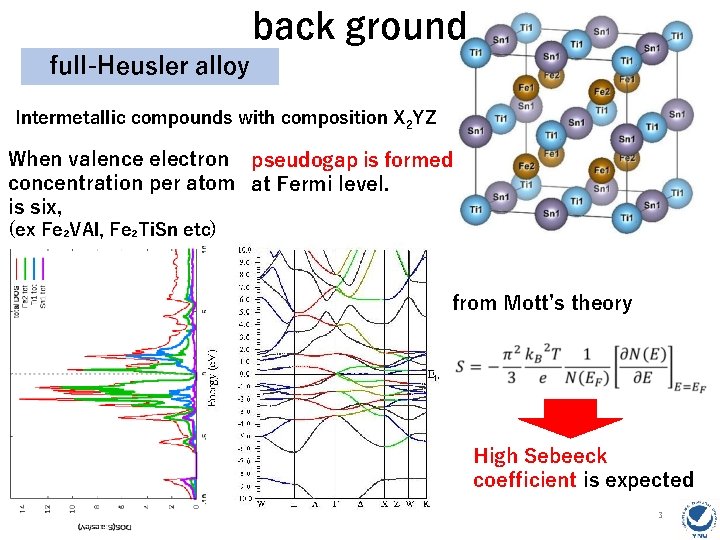
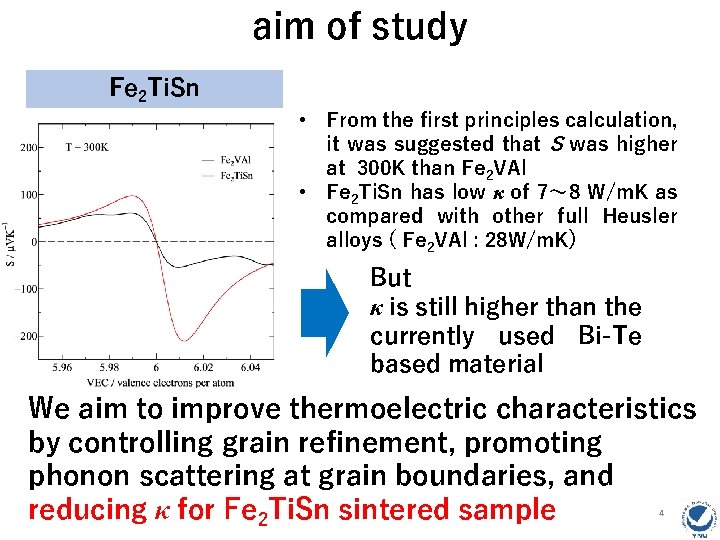
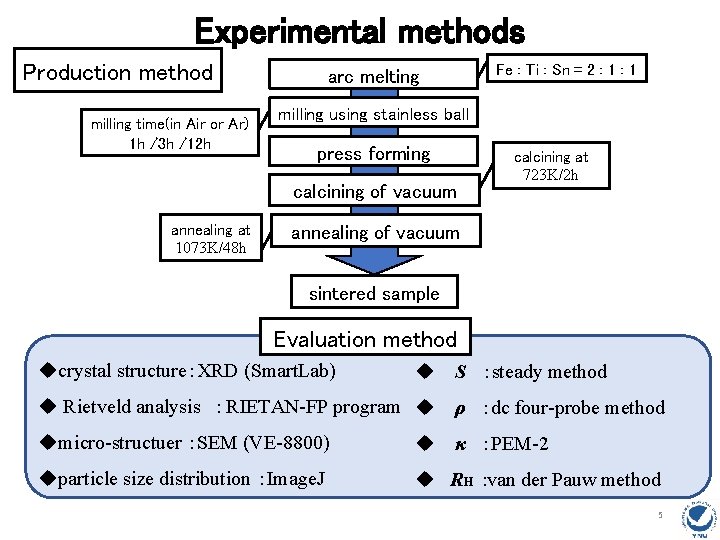
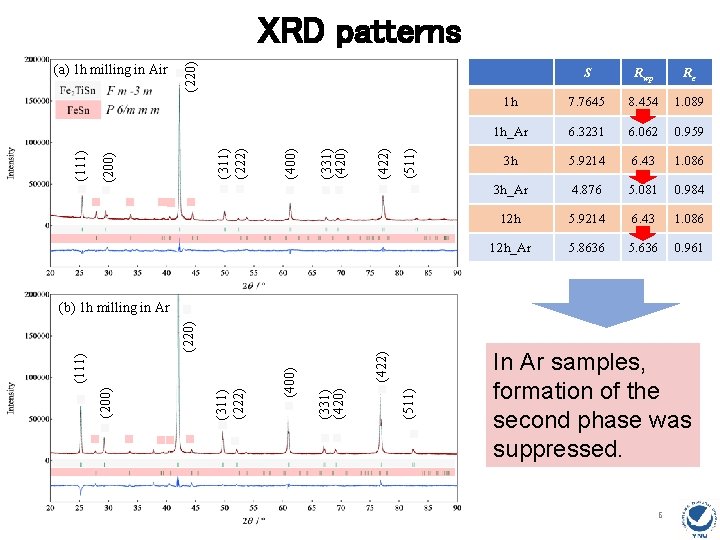
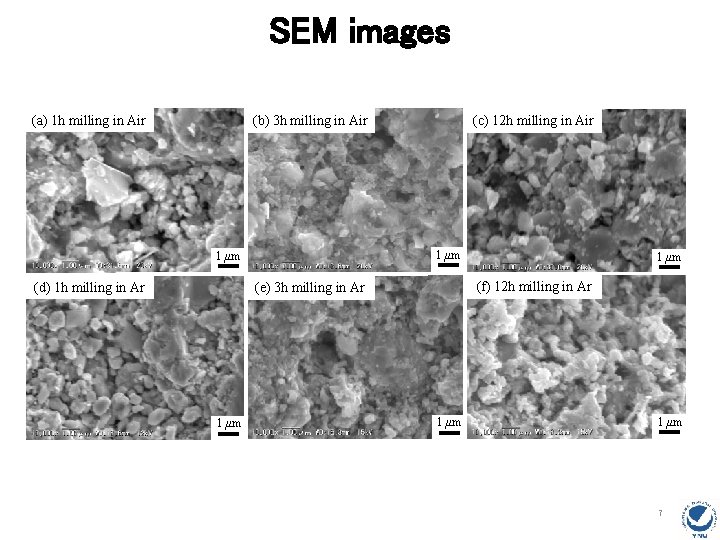
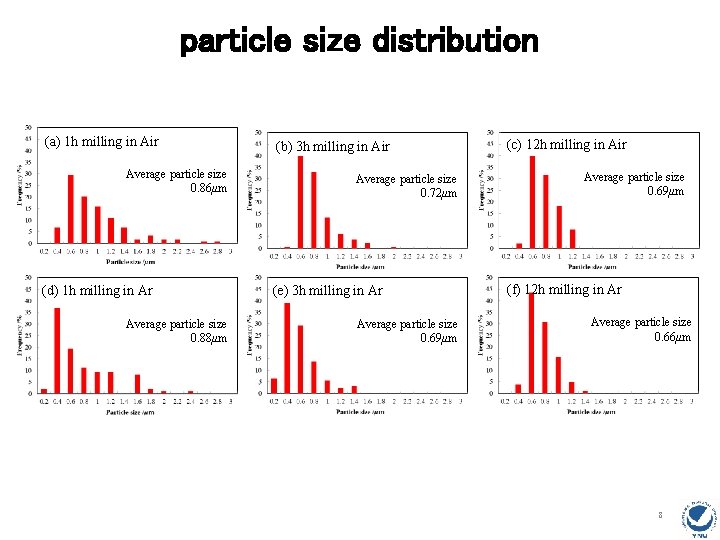
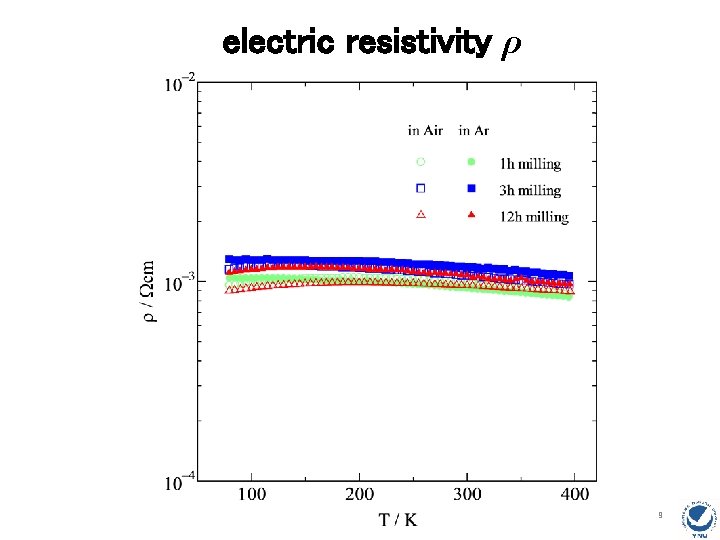
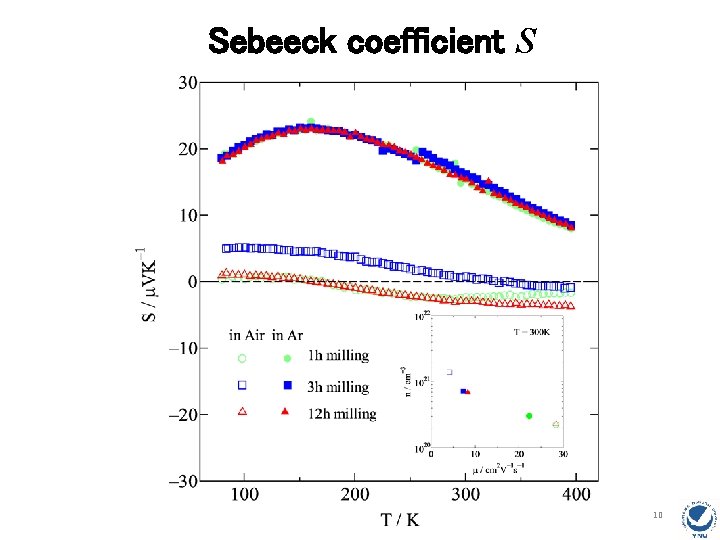
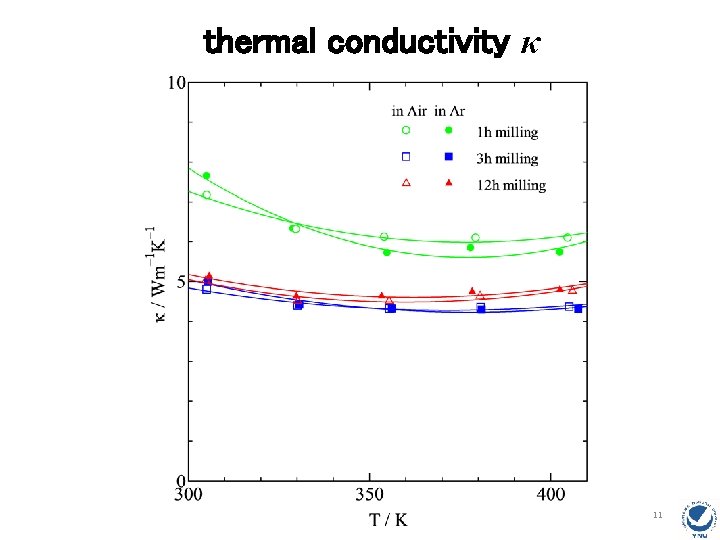
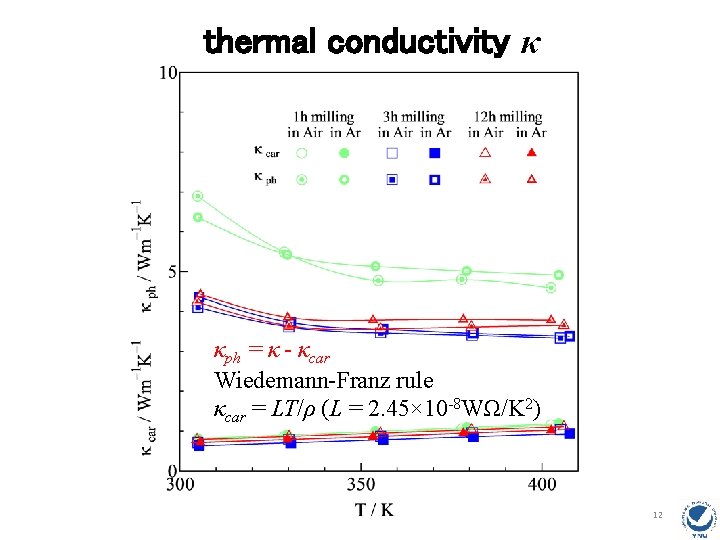
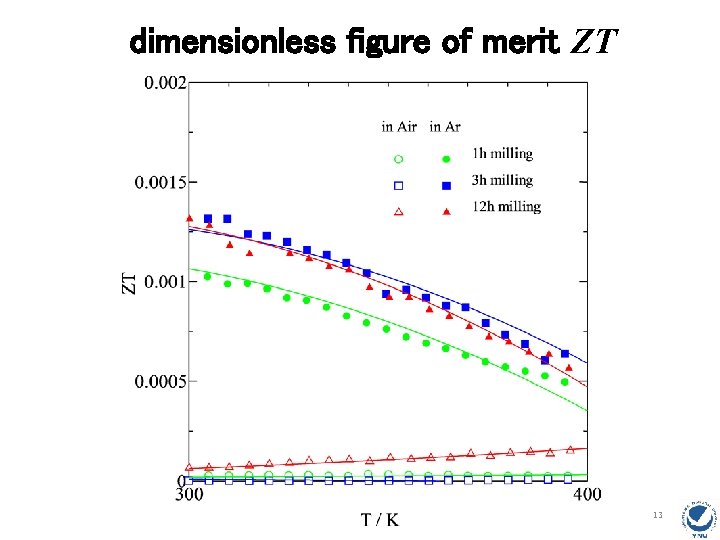
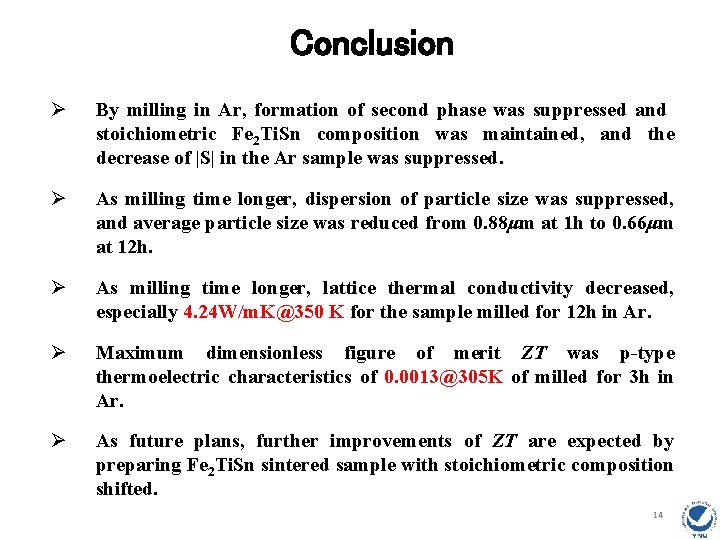
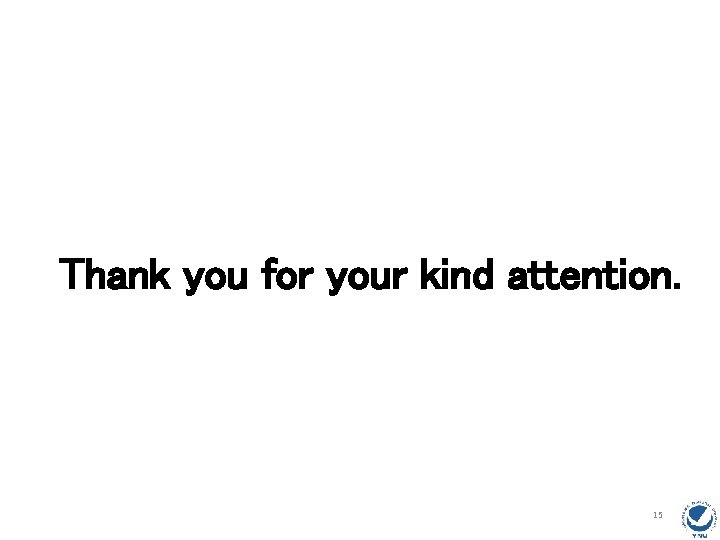
- Slides: 15
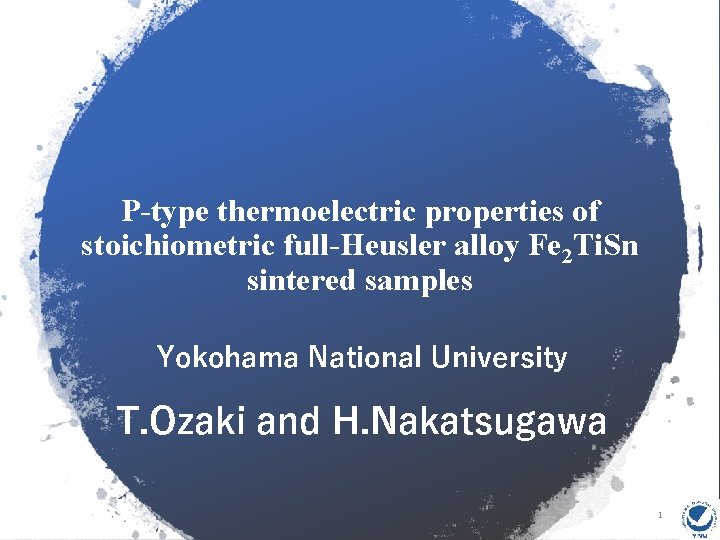
P-type thermoelectric properties of stoichiometric full-Heusler alloy Fe 2 Ti. Sn sintered samples Yokohama National University T. Ozaki and H. Nakatsugawa 1
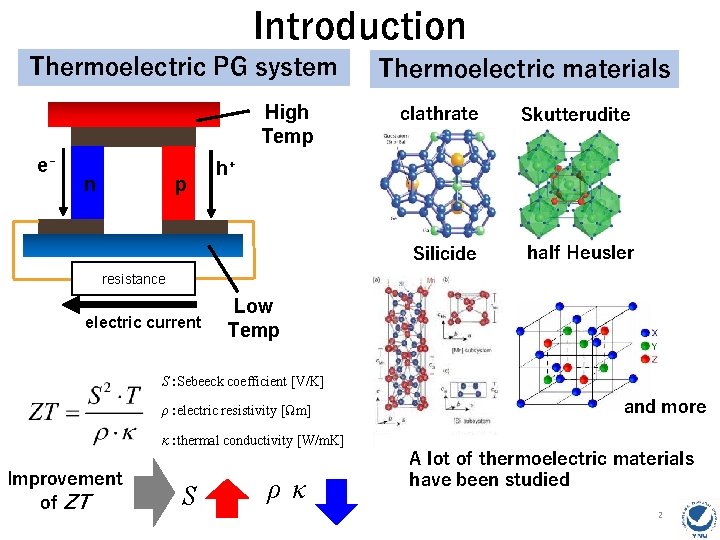
Introduction Thermoelectric PG system High Temp e⁻ n p Thermoelectric materials clathrate Skutterudite Silicide half Heusler h⁺ resistance electric current Low Temp S : Sebeeck coefficient [V/K] ρ : electric resistivity [Ωm] κ : thermal conductivity [W/m. K] Improvement of ZT S ρ κ and more A lot of thermoelectric materials have been studied 2
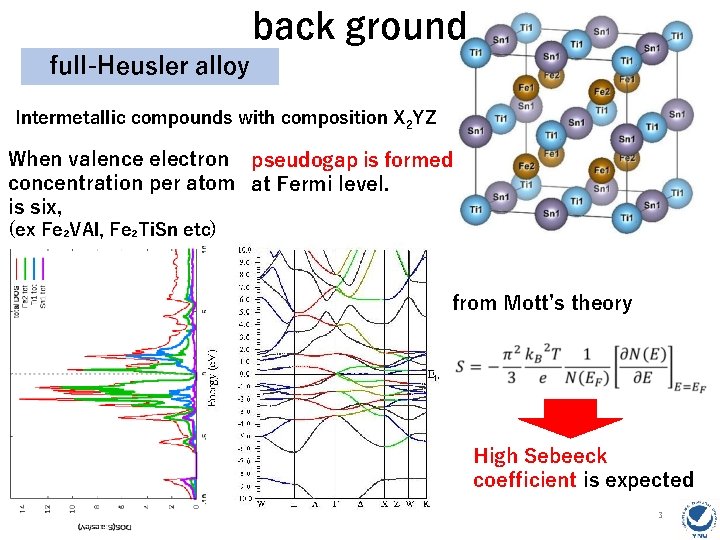
back ground full-Heusler alloy Intermetallic compounds with composition X 2 YZ When valence electron pseudogap is formed concentration per atom at Fermi level. is six, (ex Fe₂VAl, Fe₂Ti. Sn etc) from Mott’s theory High Sebeeck coefficient is expected 3
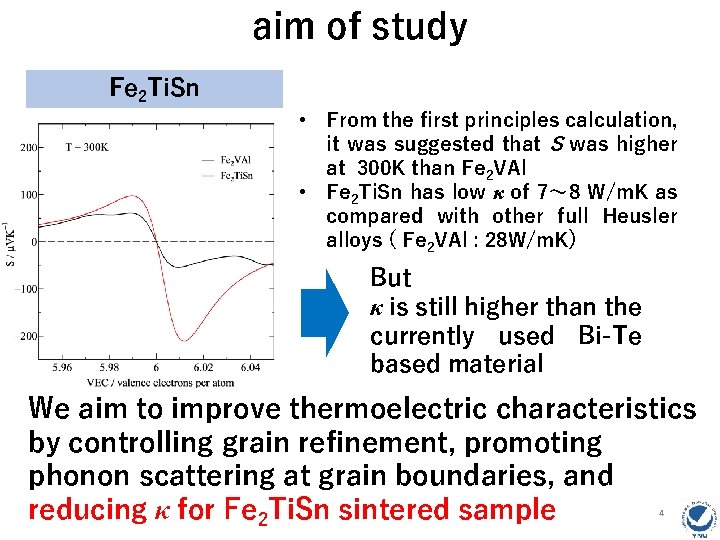
aim of study Fe 2 Ti. Sn • From the first principles calculation, it was suggested that S was higher at 300 K than Fe 2 VAl • Fe 2 Ti. Sn has low κ of 7~ 8 W/m. K as compared with other full Heusler alloys ( Fe 2 VAl : 28 W/m. K) But κ is still higher than the currently used Bi-Te based material We aim to improve thermoelectric characteristics by controlling grain refinement, promoting phonon scattering at grain boundaries, and reducing κ for Fe 2 Ti. Sn sintered sample 4
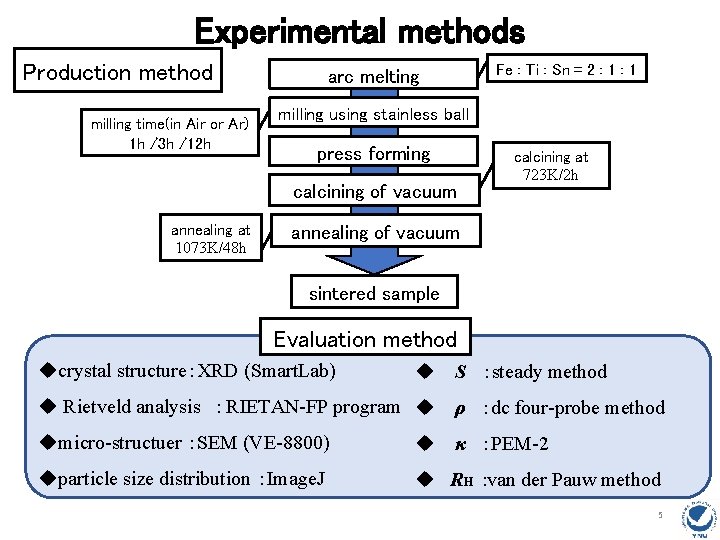
Experimental methods Production method milling time(in Air or Ar) 1 h /3 h /12 h arc melting milling using stainless ball press forming calcining of vacuum annealing at 1073 K/48 h Fe : Ti : Sn = 2 : 1 calcining at 723 K/2 h annealing of vacuum sintered sample Evaluation method ucrystal structure:XRD (Smart. Lab) u S :steady method u Rietveld analysis : RIETAN-FP program u ρ :dc four-probe method umicro-structuer :SEM (VE-8800) u κ :PEM-2 uparticle size distribution :Image. J u RH : van der Pauw method 5
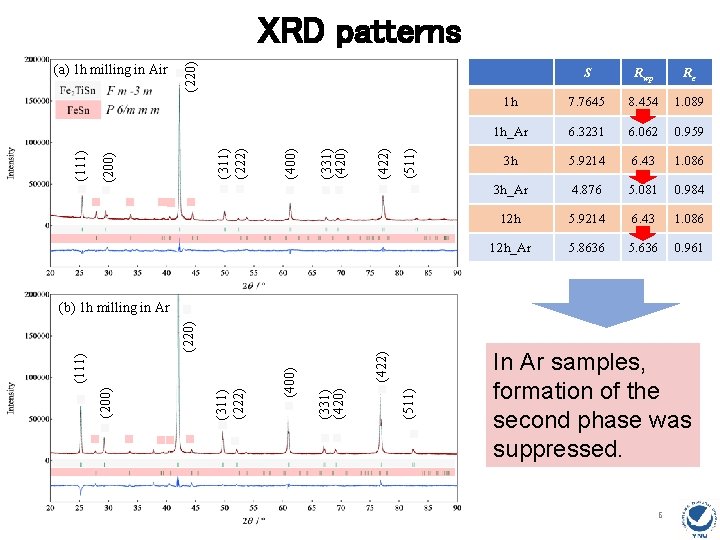
(511) (422) (331) (420) (400) (311) (222) (200) (111) (a) 1 h milling in Air (220) XRD patterns S Rwp Re 1 h 7. 7645 8. 454 1. 089 1 h_Ar 6. 3231 6. 062 0. 959 3 h 5. 9214 6. 43 1. 086 3 h_Ar 4. 876 5. 081 0. 984 12 h 5. 9214 6. 43 1. 086 12 h_Ar 5. 8636 5. 636 0. 961 (511) (422) (331) (420) (400) (311) (222) (200) (111) (220) (b) 1 h milling in Ar In Ar samples, formation of the second phase was suppressed. 6
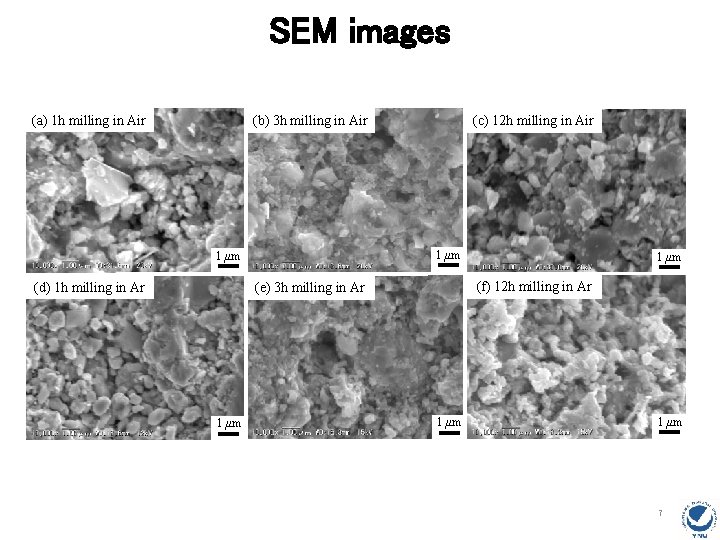
SEM images (a) 1 h milling in Air (b) 3 h milling in Air 1 μm (d) 1 h milling in Ar (c) 12 h milling in Air (f) 12 h milling in Ar (e) 3 h milling in Ar 1 μm 7
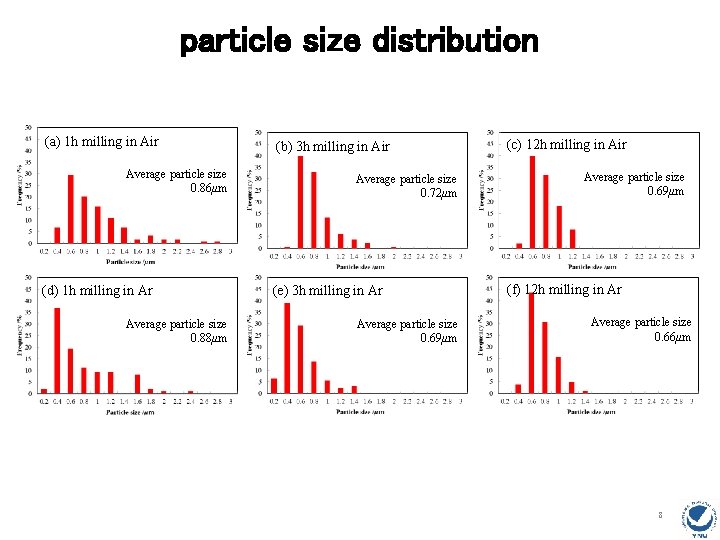
particle size distribution (a) 1 h milling in Air Average particle size 0. 86μm (d) 1 h milling in Ar Average particle size 0. 88μm (b) 3 h milling in Air Average particle size 0. 72μm (e) 3 h milling in Ar Average particle size 0. 69μm (c) 12 h milling in Air Average particle size 0. 69μm (f) 12 h milling in Ar Average particle size 0. 66μm 8
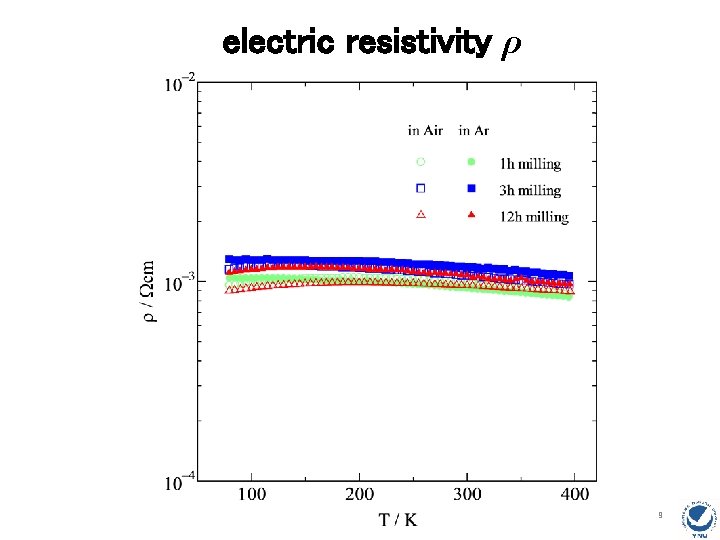
electric resistivity ρ 9
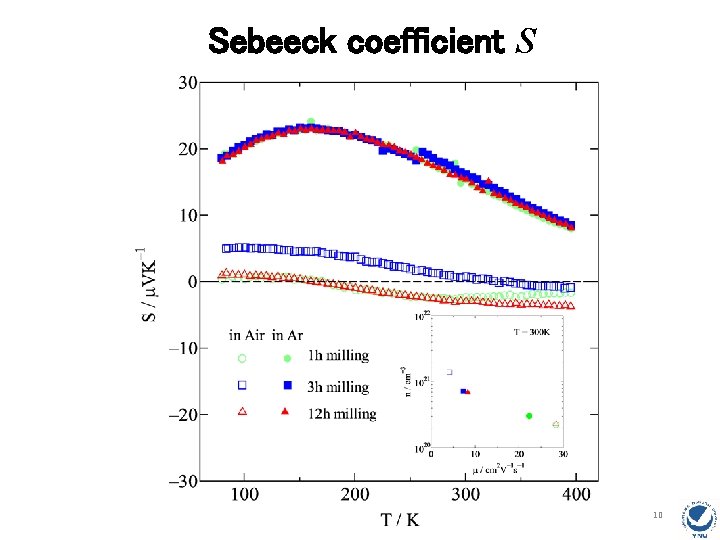
Sebeeck coefficient S 10
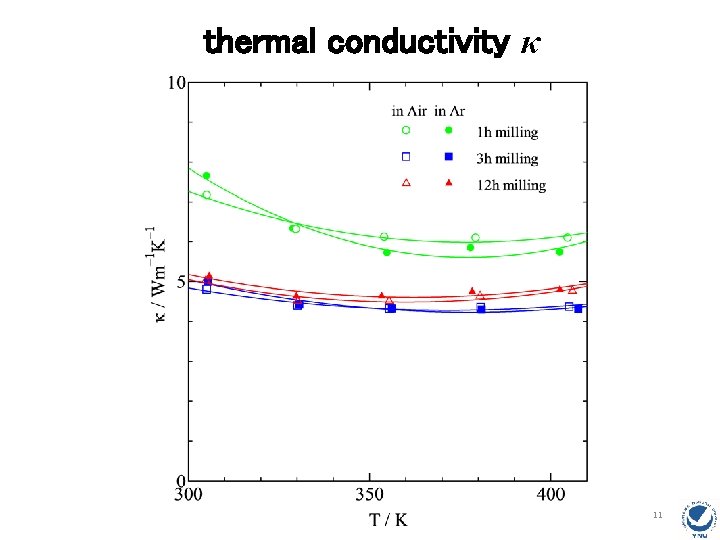
thermal conductivity κ 11
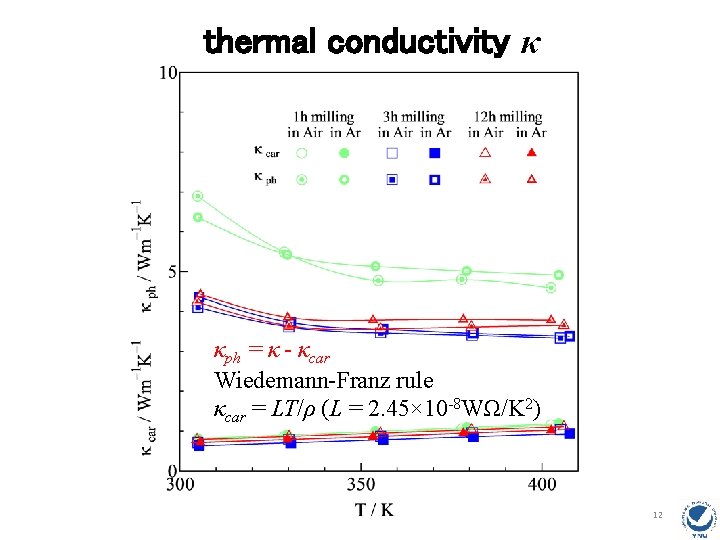
thermal conductivity κ κph = κ - κcar Wiedemann-Franz rule κcar = LT/ρ (L = 2. 45× 10 -8 WΩ/K 2) 12
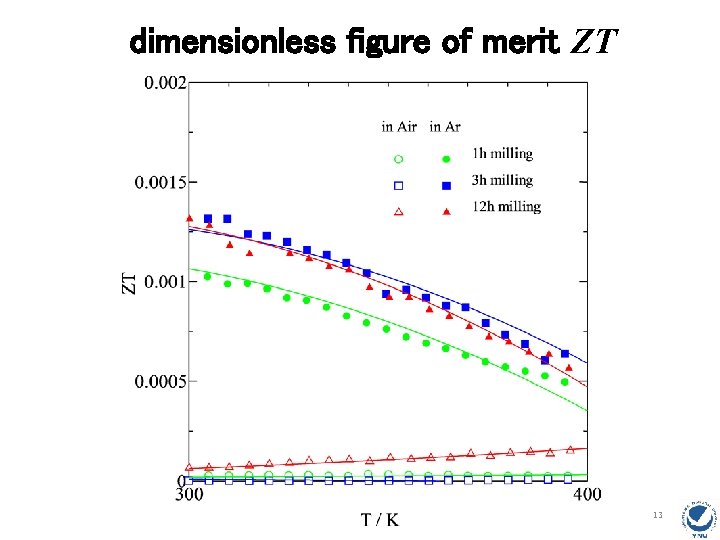
dimensionless figure of merit ZT 13
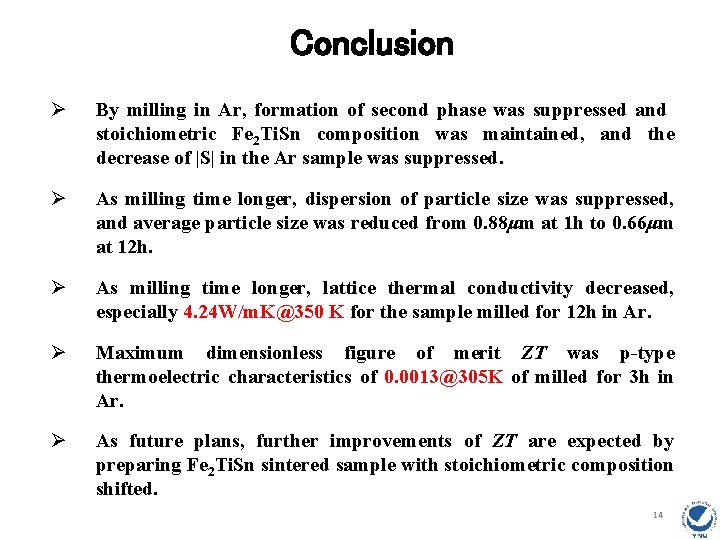
Conclusion Ø By milling in Ar, formation of second phase was suppressed and stoichiometric Fe 2 Ti. Sn composition was maintained, and the decrease of |S| in the Ar sample was suppressed. Ø As milling time longer, dispersion of particle size was suppressed, and average particle size was reduced from 0. 88μm at 1 h to 0. 66μm at 12 h. Ø As milling time longer, lattice thermal conductivity decreased, especially 4. 24 W/m. K@350 K for the sample milled for 12 h in Ar. Ø Maximum dimensionless figure of merit ZT was p-type thermoelectric characteristics of 0. 0013@305 K of milled for 3 h in Ar. Ø As future plans, further improvements of ZT are expected by preparing Fe 2 Ti. Sn sintered sample with stoichiometric composition shifted. 14
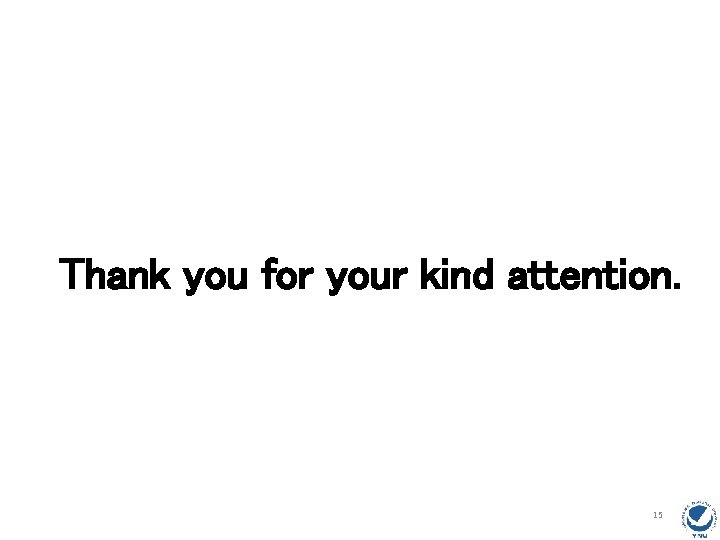
Thank you for your kind attention. 15
Ptype
Guided by and submitted by
Melcor tec
Dangling bond in fullerene
Thermoelectric
Incopetency
Stoichiometric table for flow system
Stoichiometric calculations
Stoichiometric table
Basic stoichiometry
Stoichiometric gasoline
Stoichiometric table for reversible reaction
Mass to mass formula
What is stoichiometry?
Stoichiometric
Stoichiometric table for flow system