OSHA 10 Adding Value and Competitive Advantage James
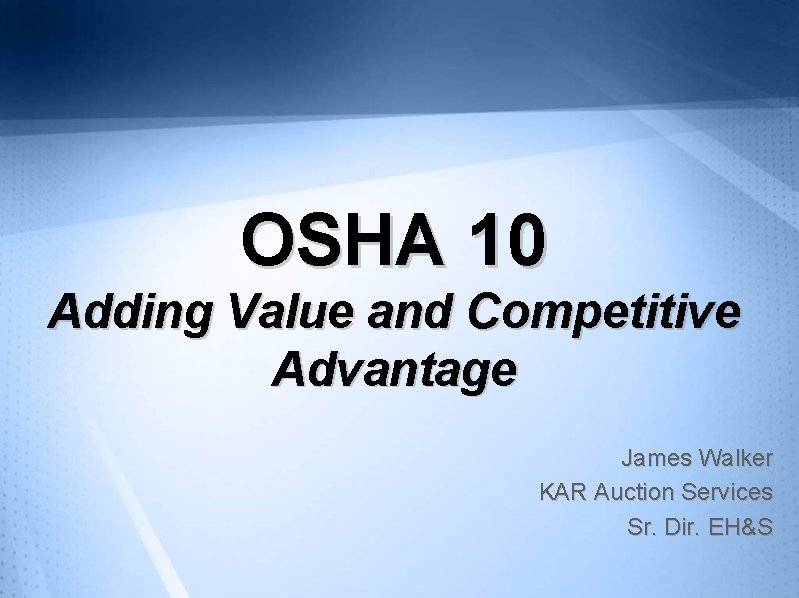
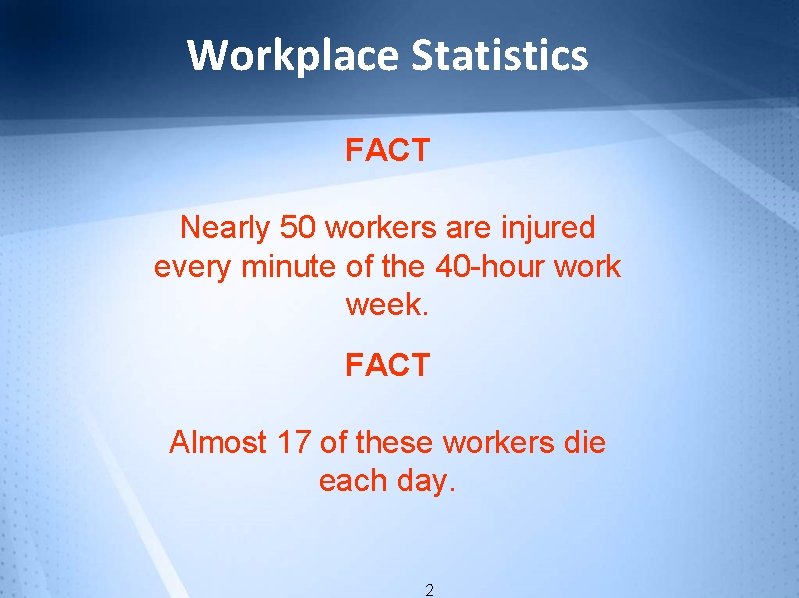
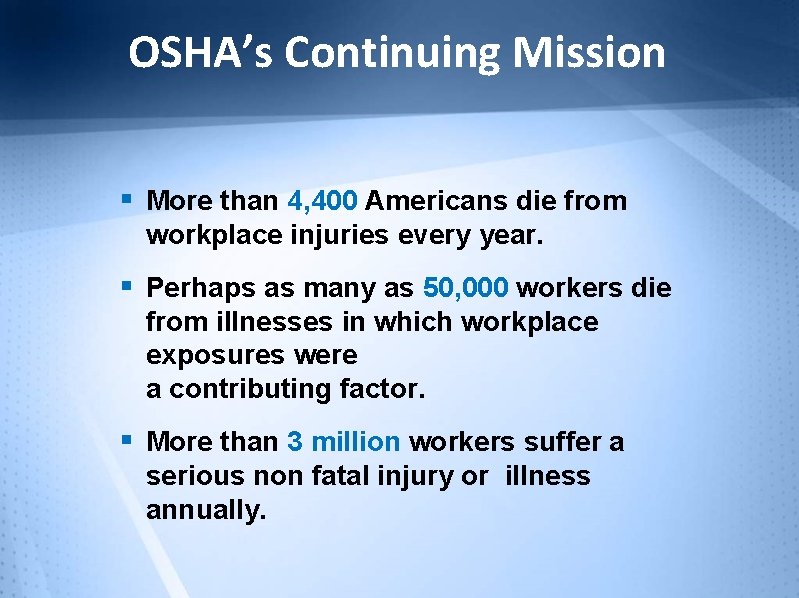
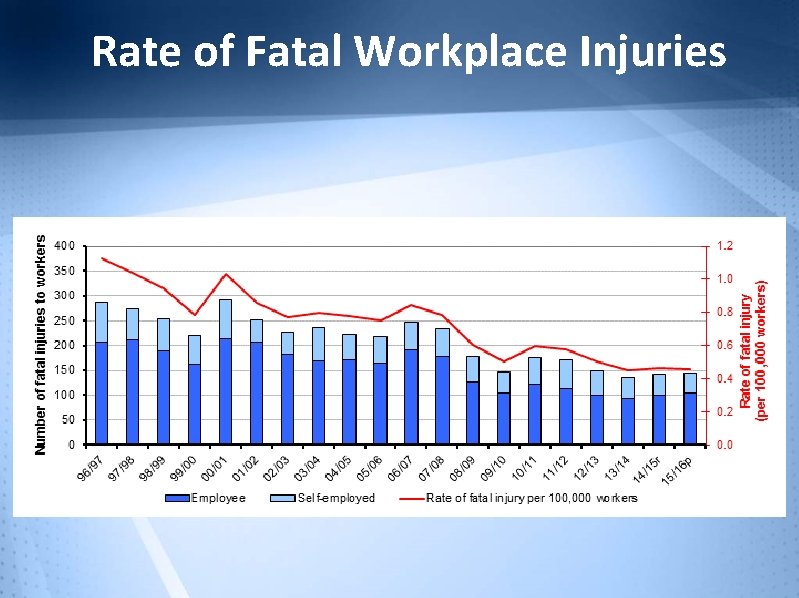
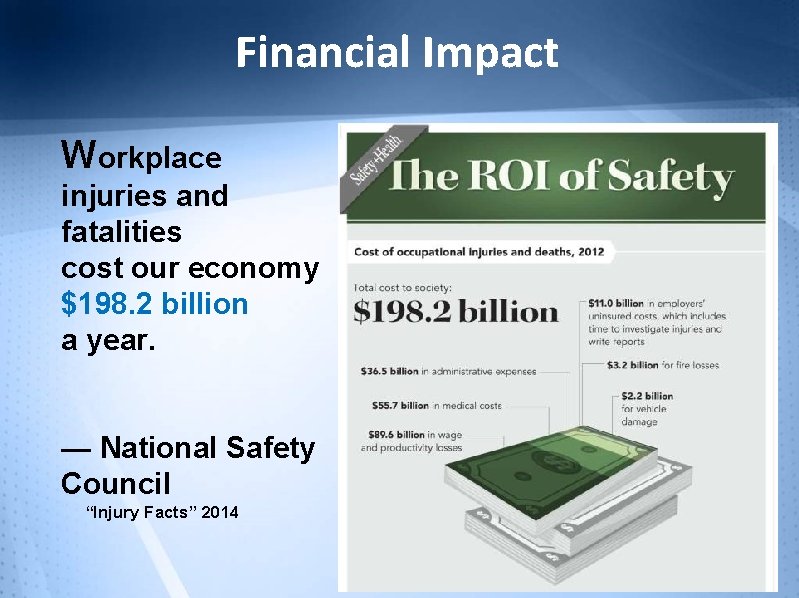
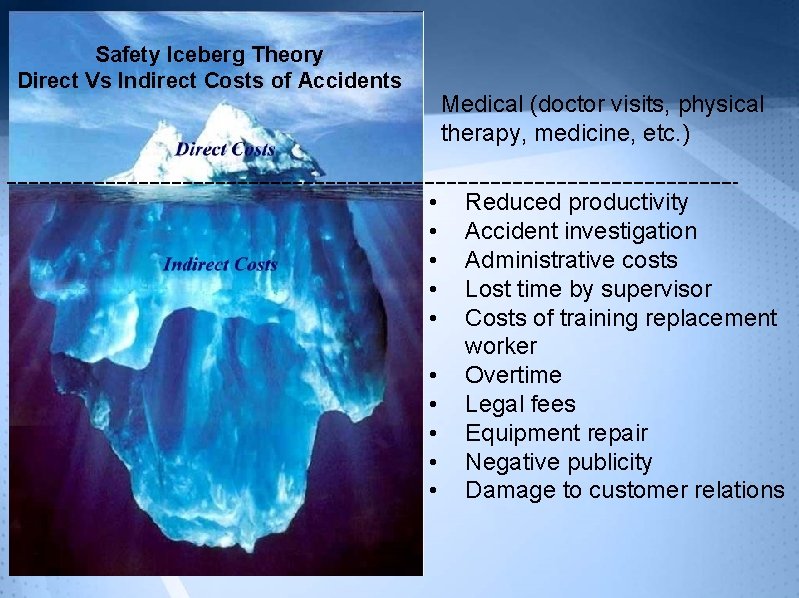

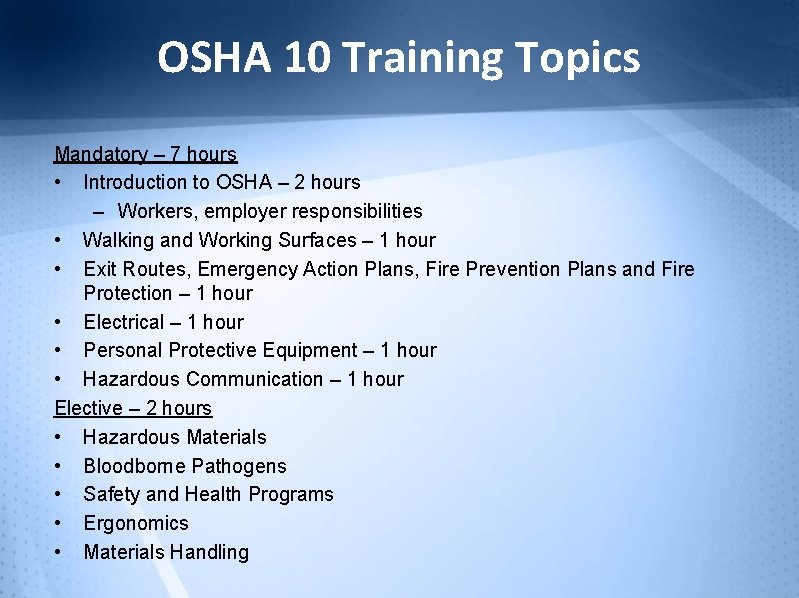
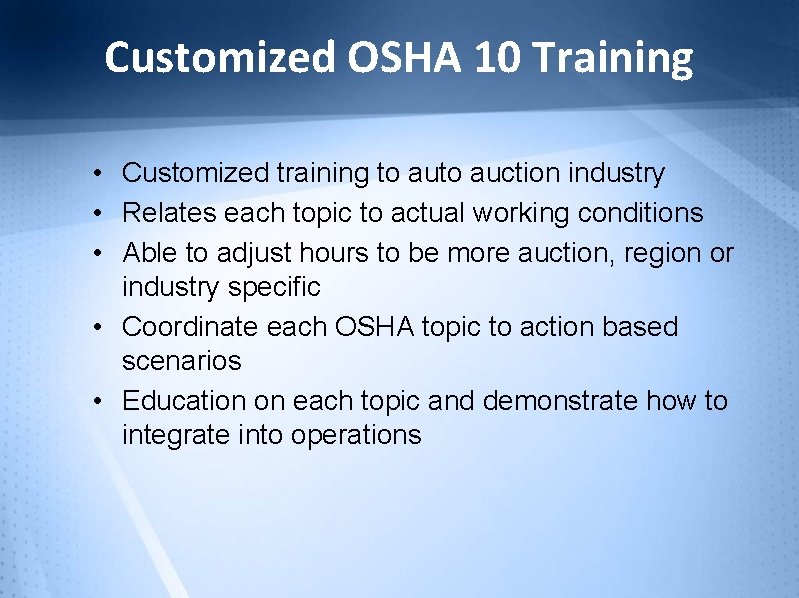
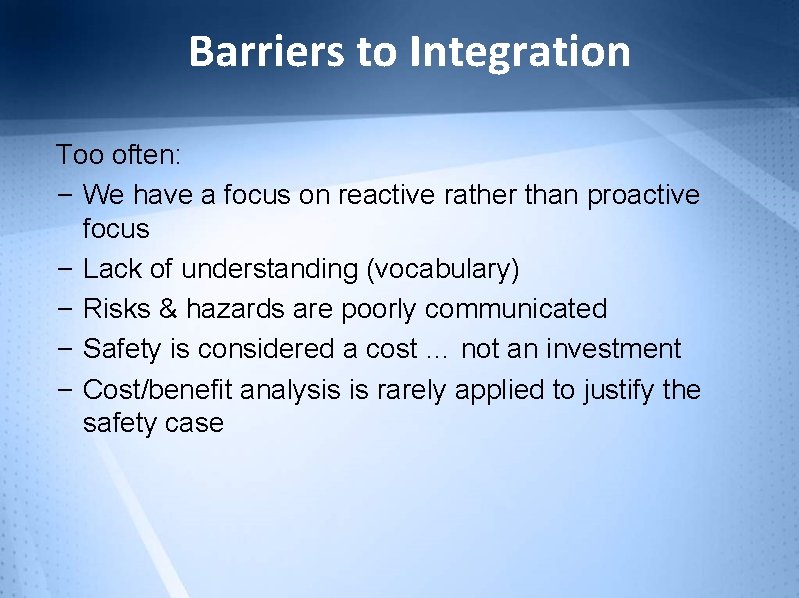
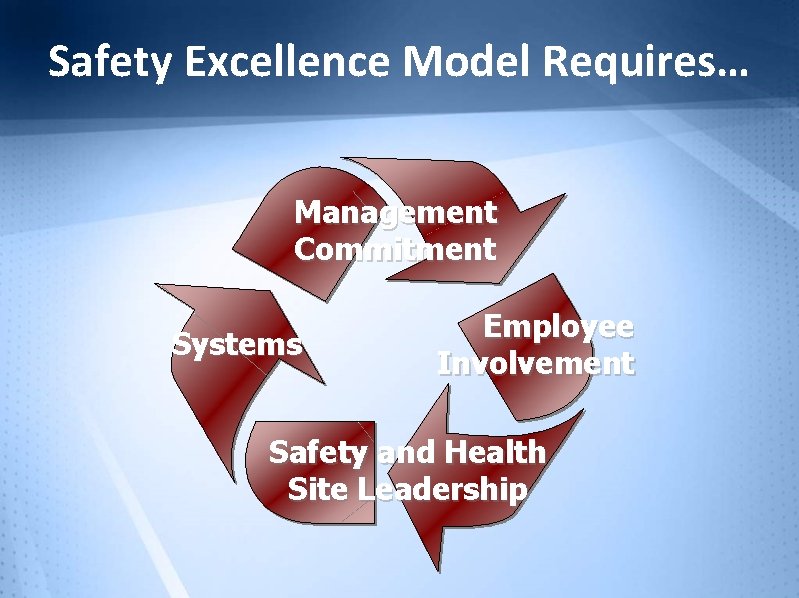
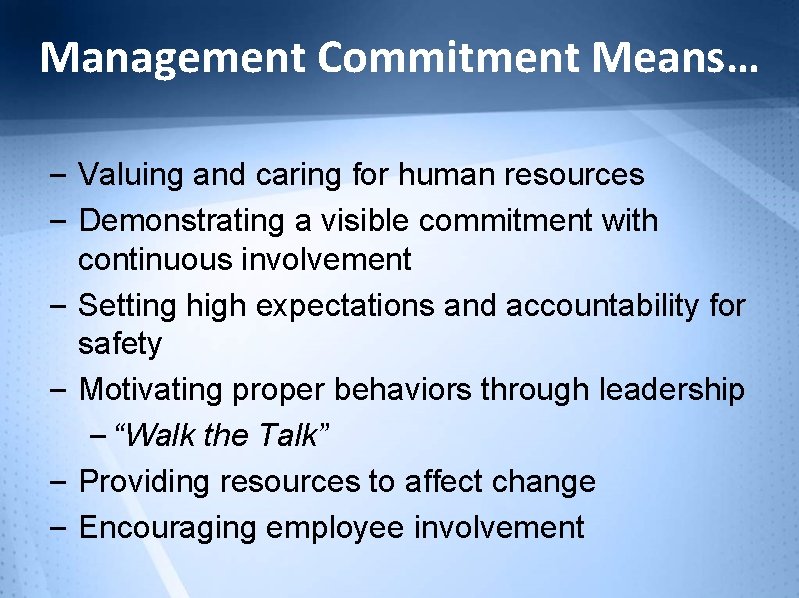
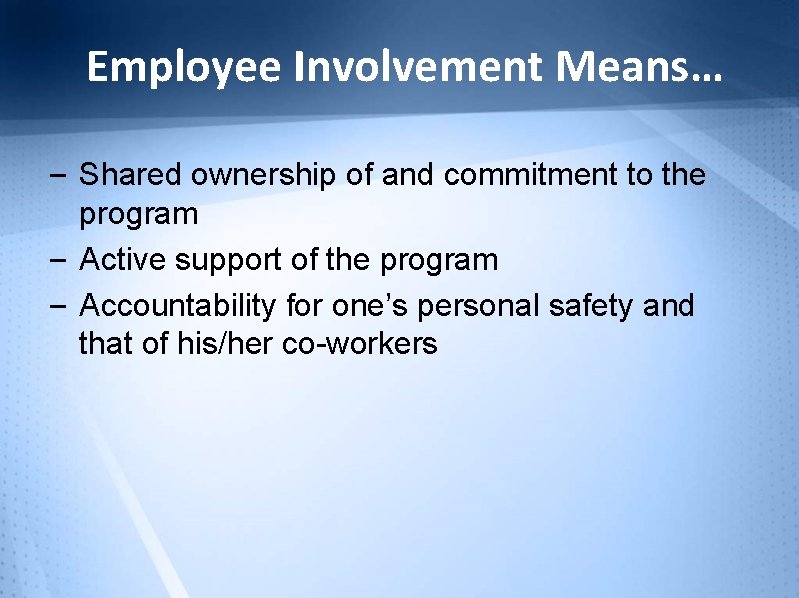
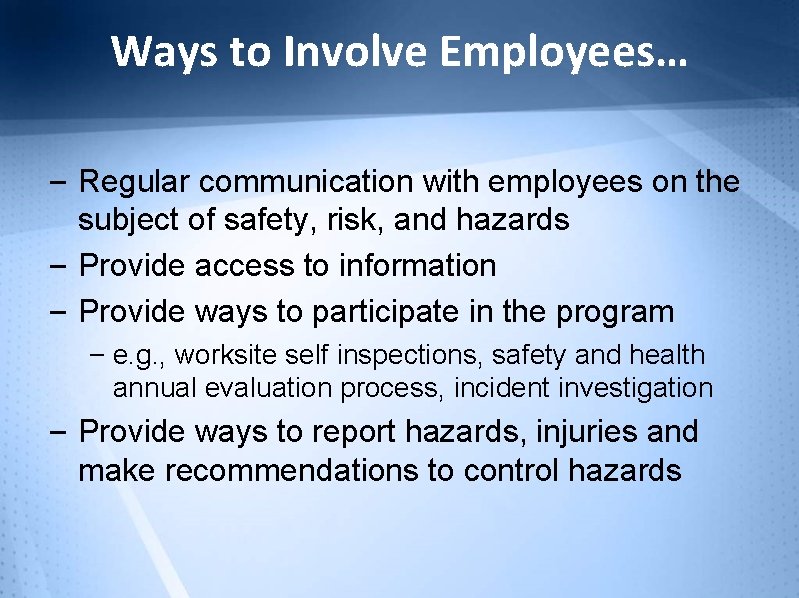
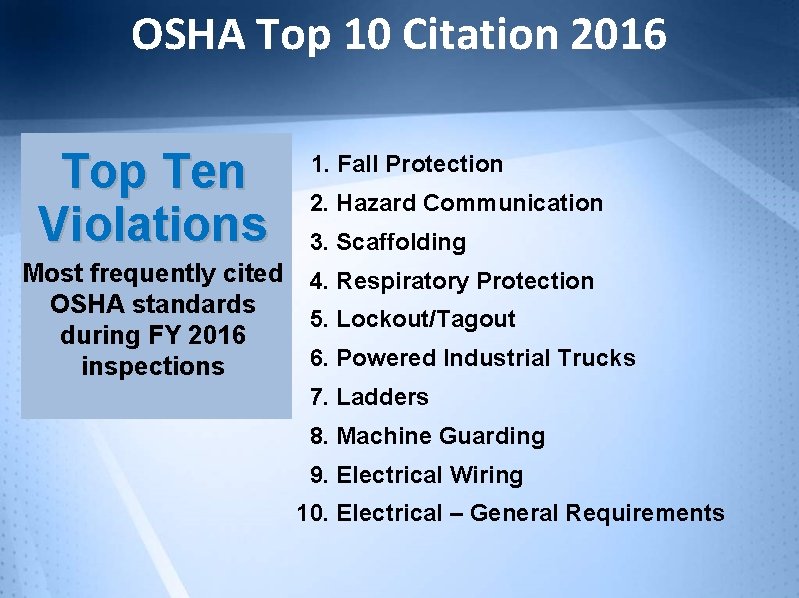
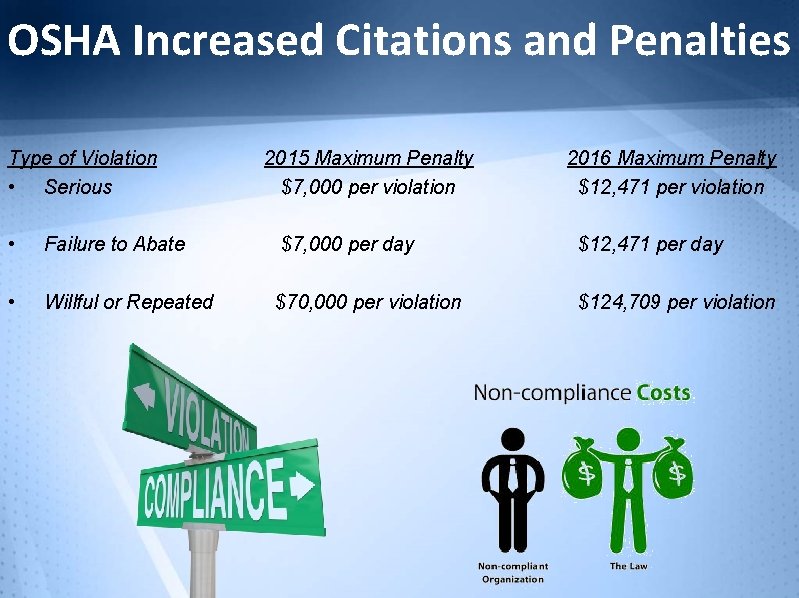
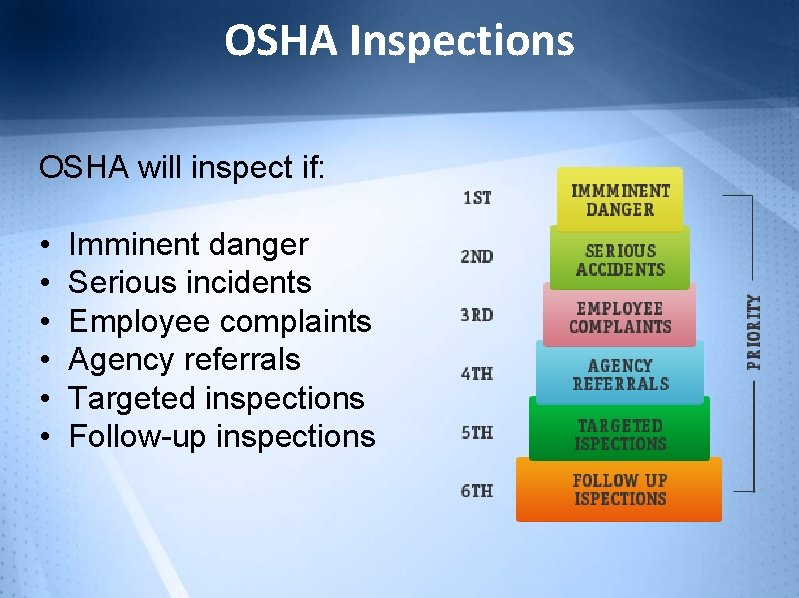
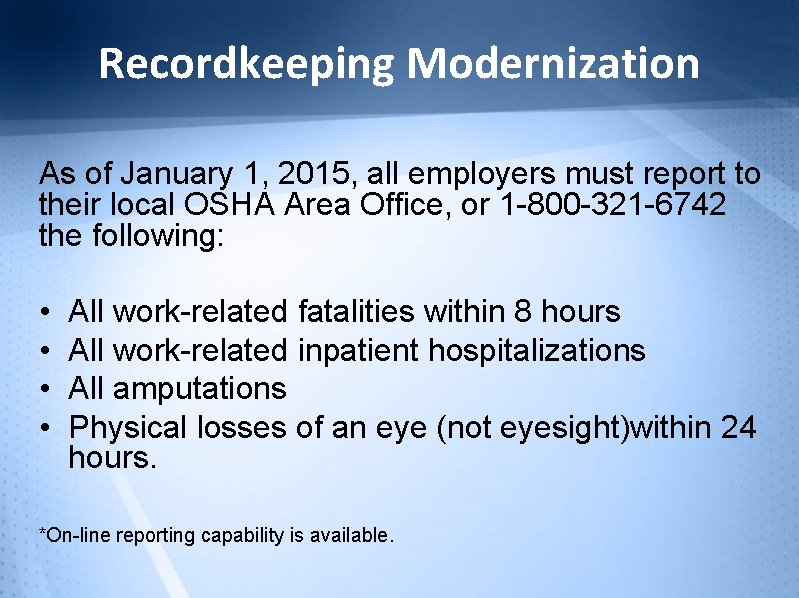
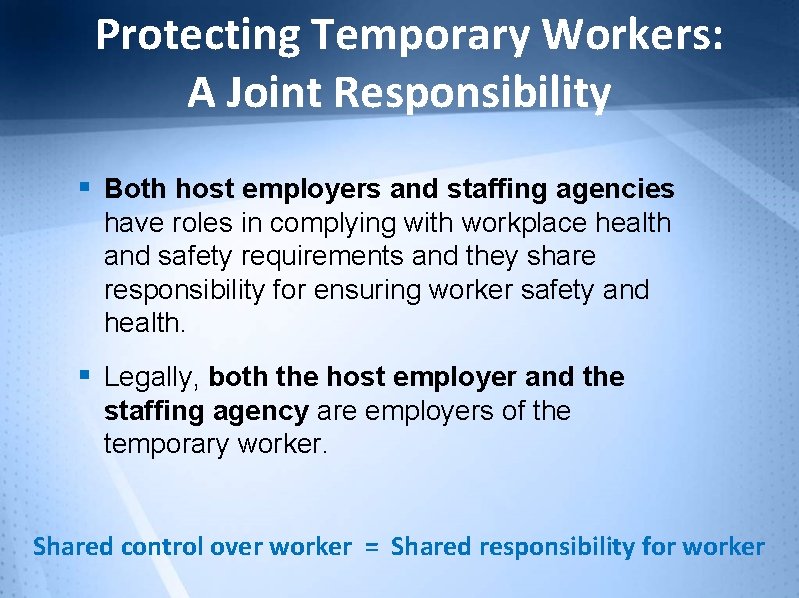
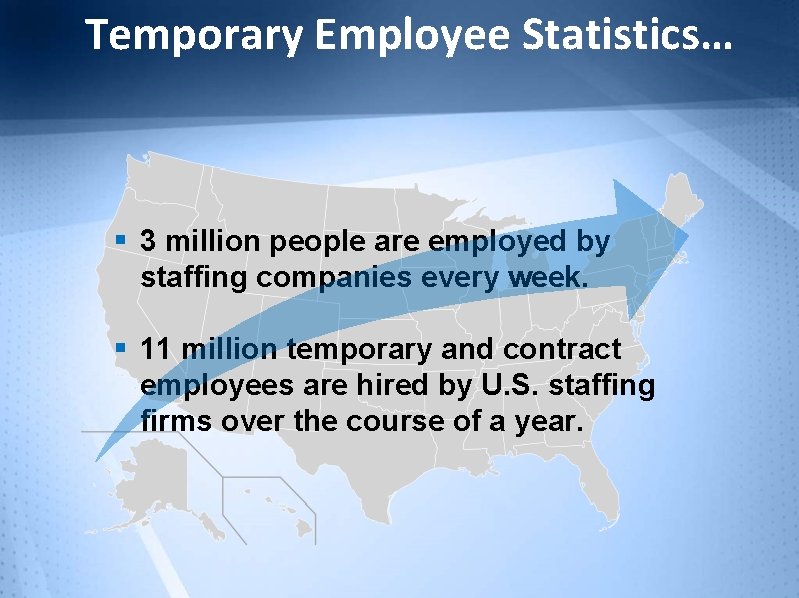
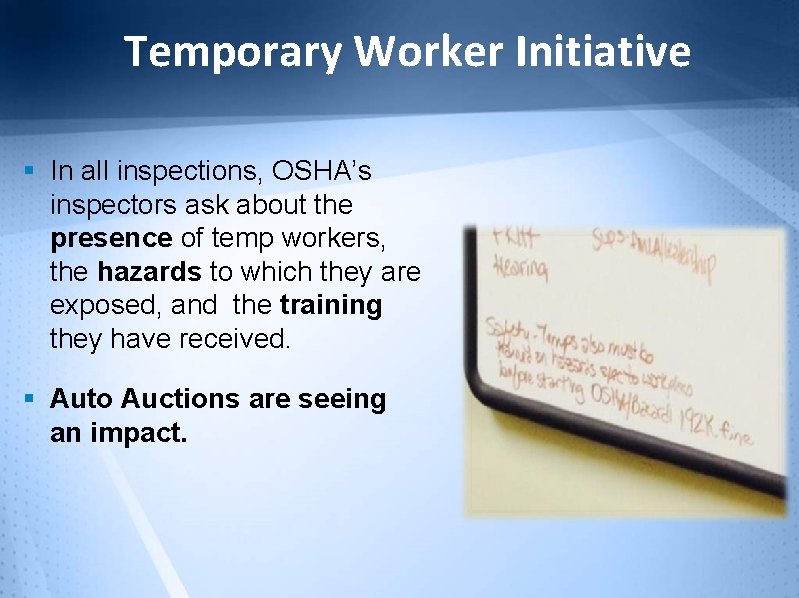
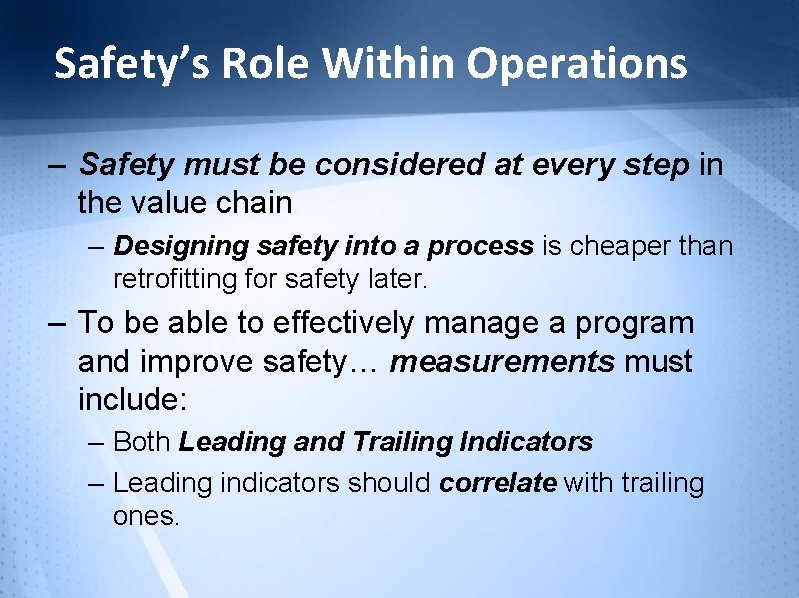
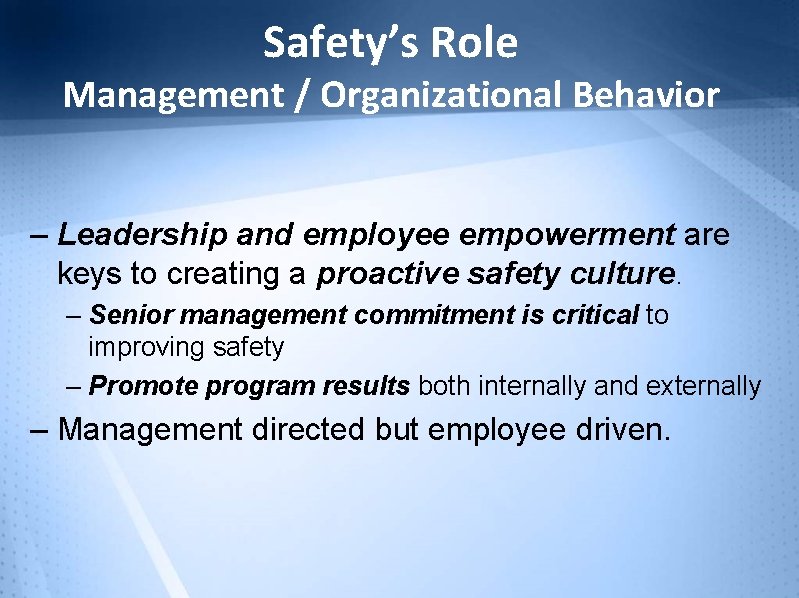
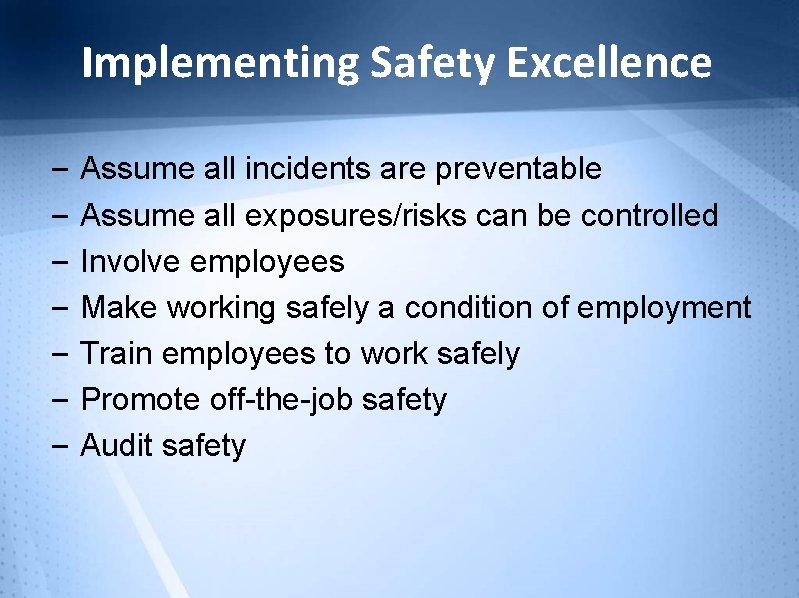
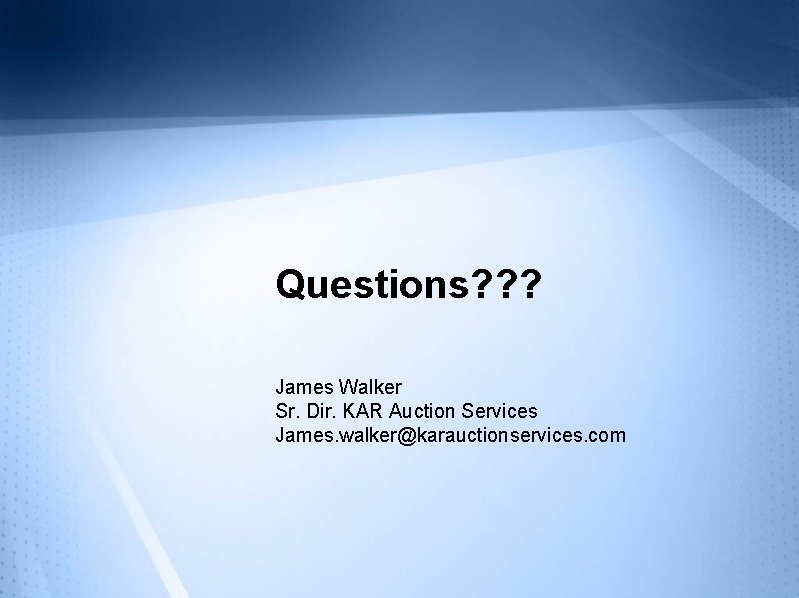
- Slides: 25
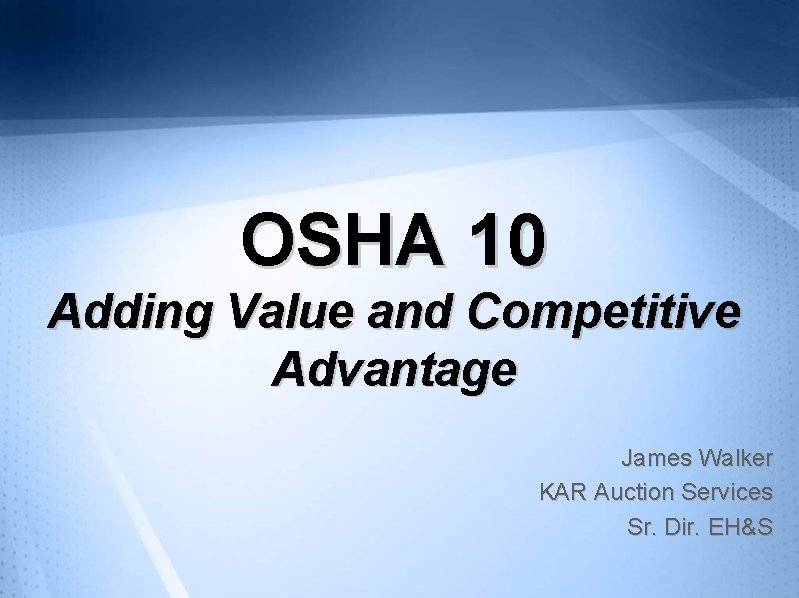
OSHA 10 Adding Value and Competitive Advantage James Walker KAR Auction Services Sr. Dir. EH&S
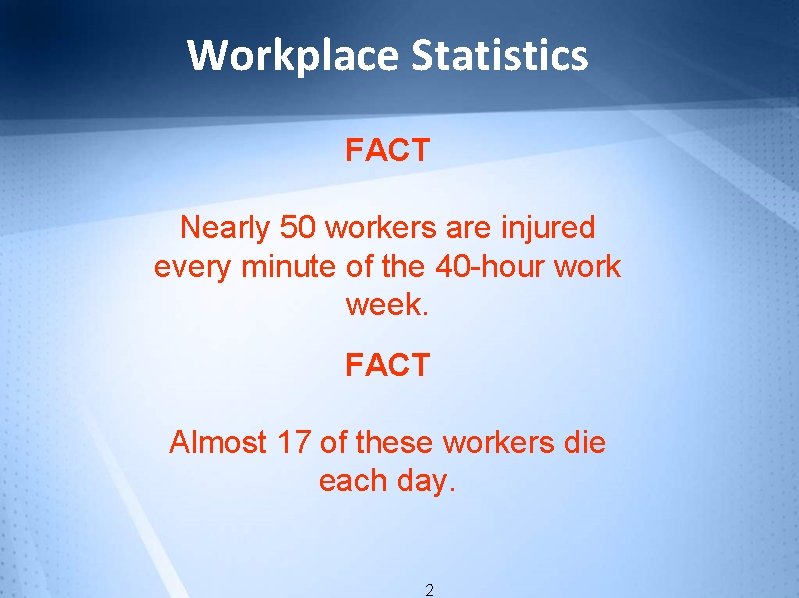
Workplace Statistics FACT Nearly 50 workers are injured every minute of the 40 -hour work week. FACT Almost 17 of these workers die each day. 2
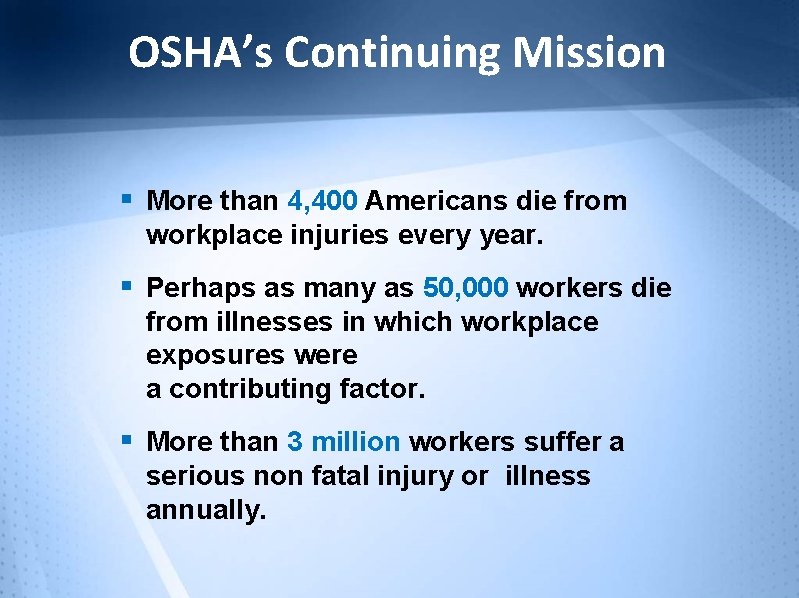
OSHA’s Continuing Mission § More than 4, 400 Americans die from workplace injuries every year. § Perhaps as many as 50, 000 workers die from illnesses in which workplace exposures were a contributing factor. § More than 3 million workers suffer a serious non fatal injury or illness annually.
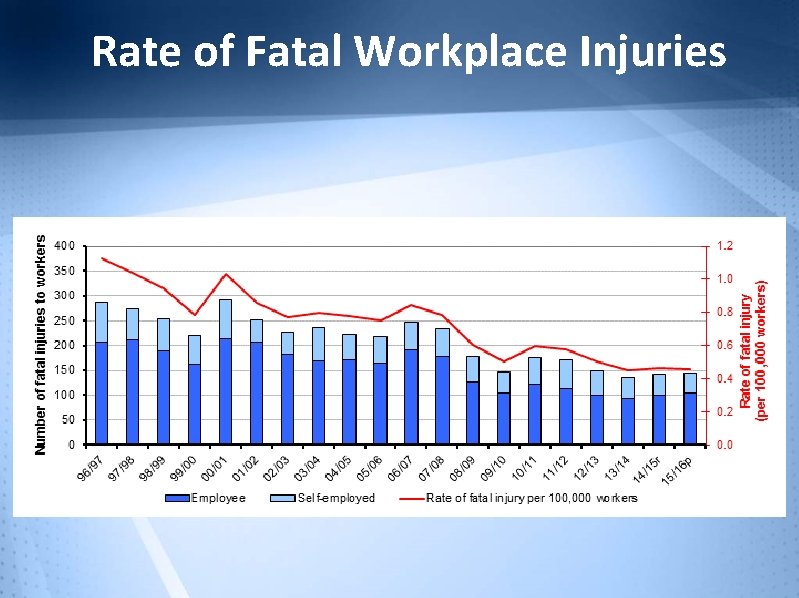
Rate of Fatal Workplace Injuries
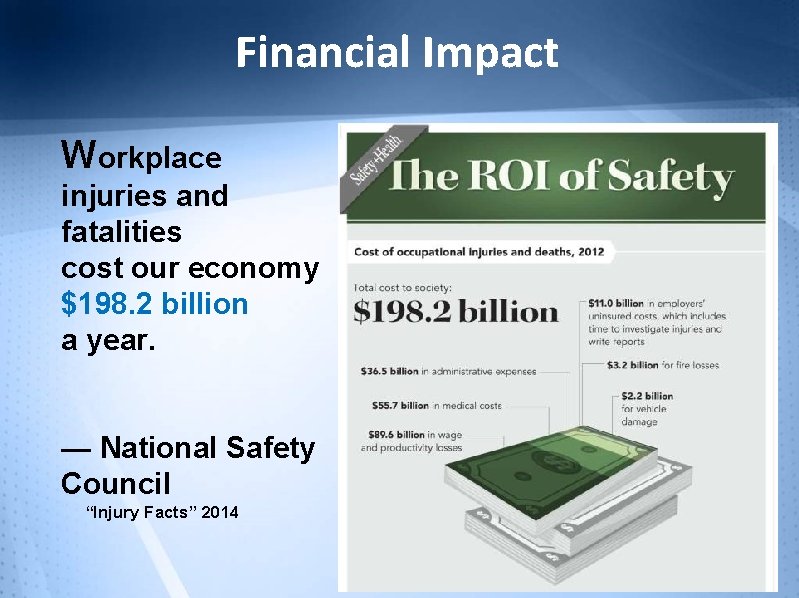
Financial Impact Workplace injuries and fatalities cost our economy $198. 2 billion a year. — National Safety Council “Injury Facts” 2014
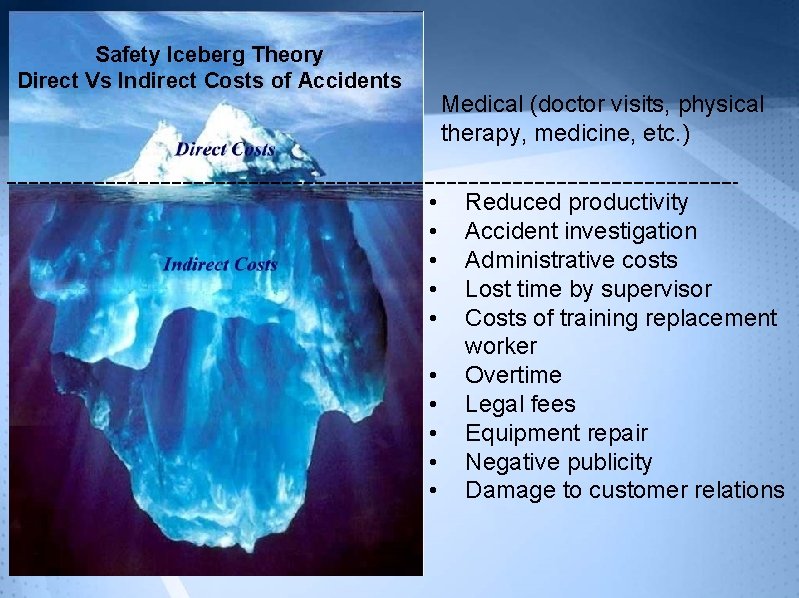
Safety Iceberg Theory Direct Vs Indirect Costs of Accidents Medical (doctor visits, physical therapy, medicine, etc. ) • • • Reduced productivity Accident investigation Administrative costs Lost time by supervisor Costs of training replacement worker Overtime Legal fees Equipment repair Negative publicity Damage to customer relations

Benefits of Effective Safety and Health Programs OSHA 10 can help: • Reduce work related injuries and illnesses • Improve morale and productivity • Reduce workers’ compensation costs • Help avoid litigation and costly incident claims • Employ a safe working atmosphere 7
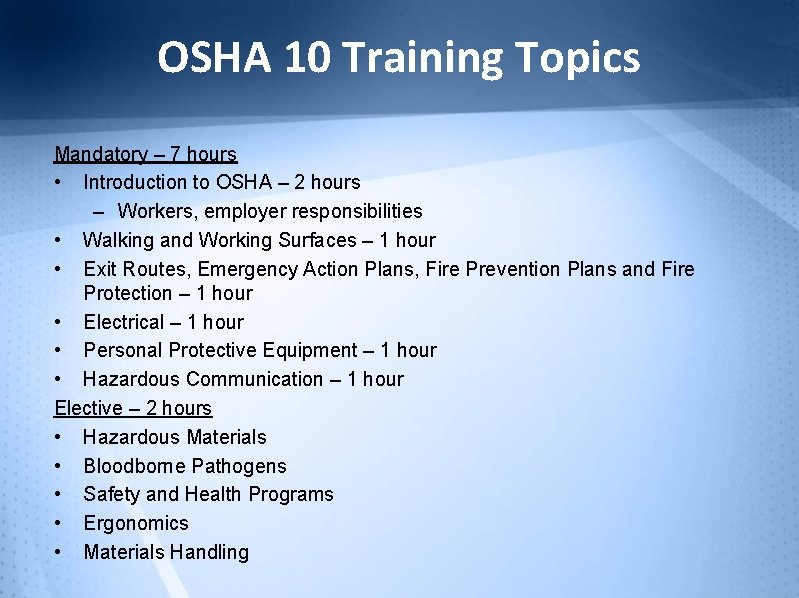
OSHA 10 Training Topics Mandatory – 7 hours • Introduction to OSHA – 2 hours – Workers, employer responsibilities • Walking and Working Surfaces – 1 hour • Exit Routes, Emergency Action Plans, Fire Prevention Plans and Fire Protection – 1 hour • Electrical – 1 hour • Personal Protective Equipment – 1 hour • Hazardous Communication – 1 hour Elective – 2 hours • Hazardous Materials • Bloodborne Pathogens • Safety and Health Programs • Ergonomics • Materials Handling
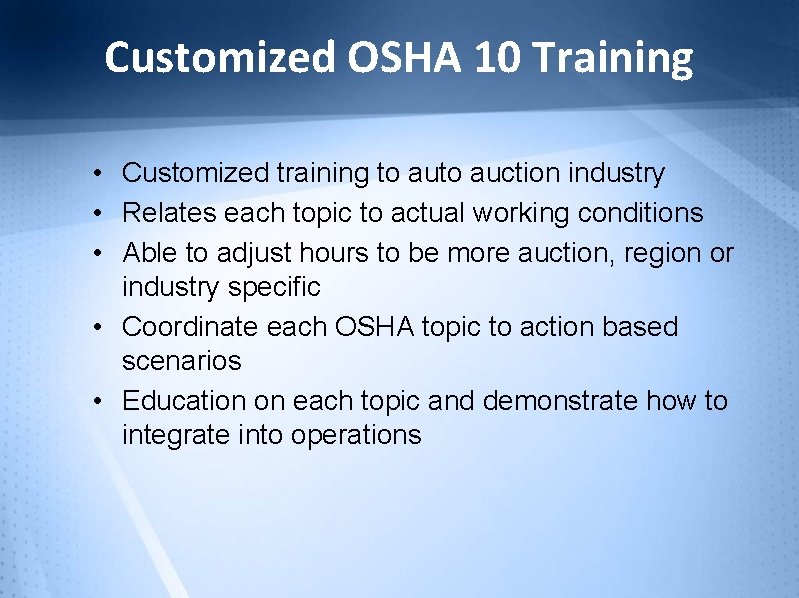
Customized OSHA 10 Training • Customized training to auction industry • Relates each topic to actual working conditions • Able to adjust hours to be more auction, region or industry specific • Coordinate each OSHA topic to action based scenarios • Education on each topic and demonstrate how to integrate into operations
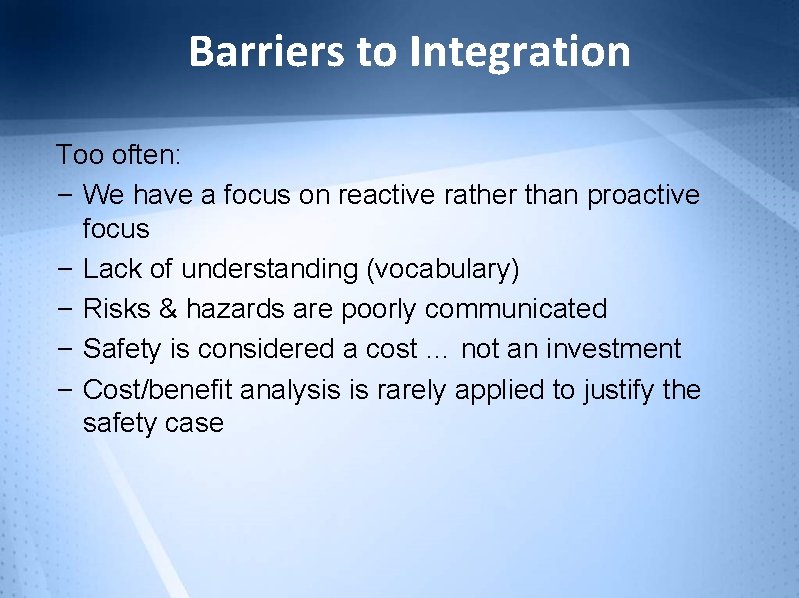
Barriers to Integration Too often: – We have a focus on reactive rather than proactive focus – Lack of understanding (vocabulary) – Risks & hazards are poorly communicated – Safety is considered a cost … not an investment – Cost/benefit analysis is rarely applied to justify the safety case
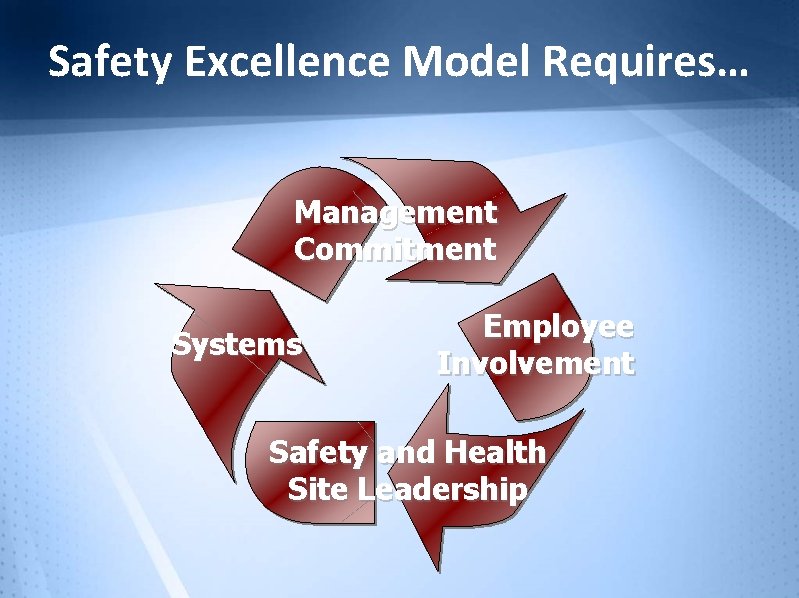
Safety Excellence Model Requires… Management Commitment Systems Employee Involvement Safety and Health Site Leadership
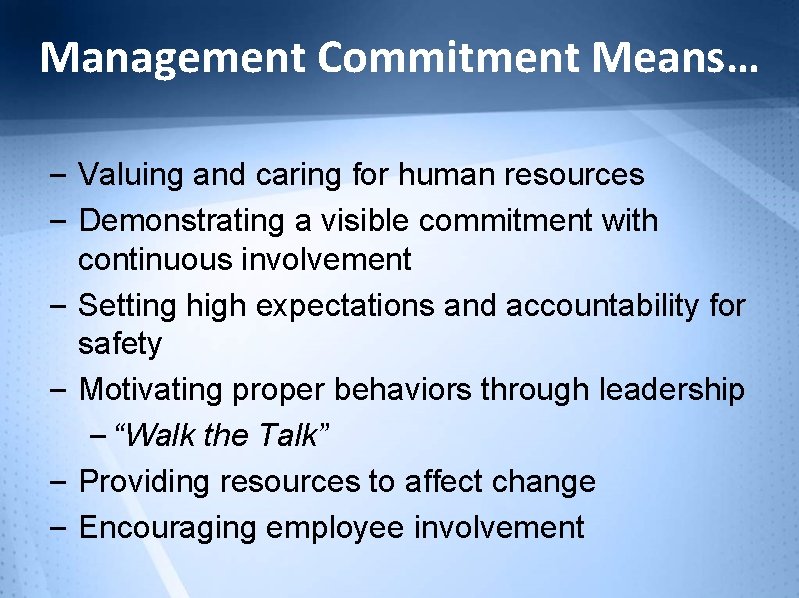
Management Commitment Means… – Valuing and caring for human resources – Demonstrating a visible commitment with continuous involvement – Setting high expectations and accountability for safety – Motivating proper behaviors through leadership – “Walk the Talk” – Providing resources to affect change – Encouraging employee involvement
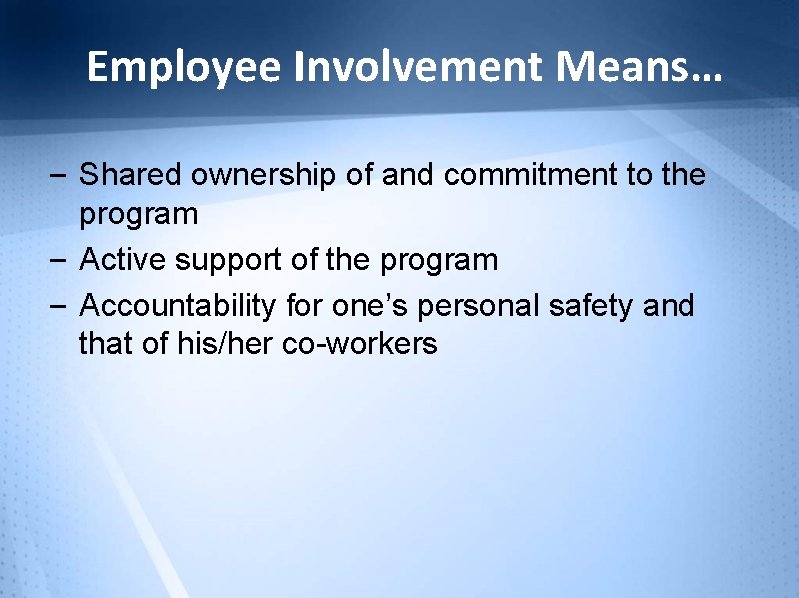
Employee Involvement Means… – Shared ownership of and commitment to the program – Active support of the program – Accountability for one’s personal safety and that of his/her co-workers
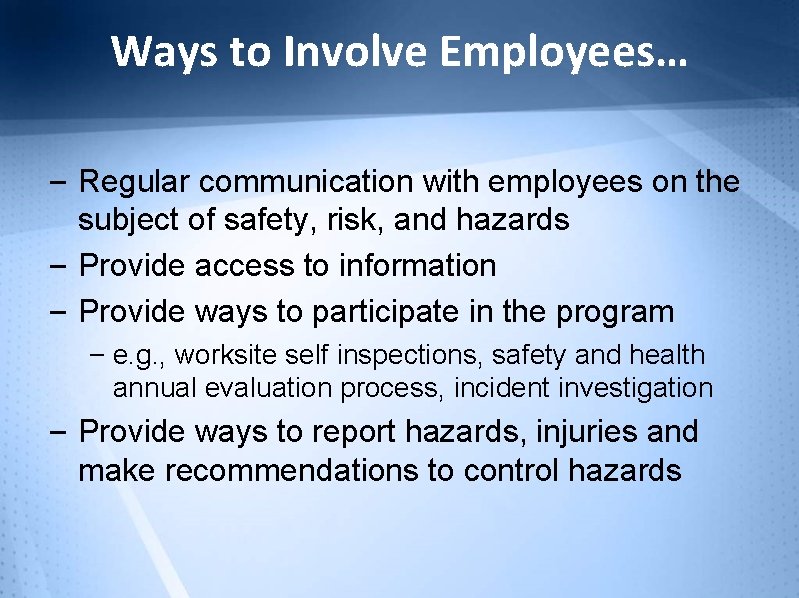
Ways to Involve Employees… – Regular communication with employees on the subject of safety, risk, and hazards – Provide access to information – Provide ways to participate in the program – e. g. , worksite self inspections, safety and health annual evaluation process, incident investigation – Provide ways to report hazards, injuries and make recommendations to control hazards
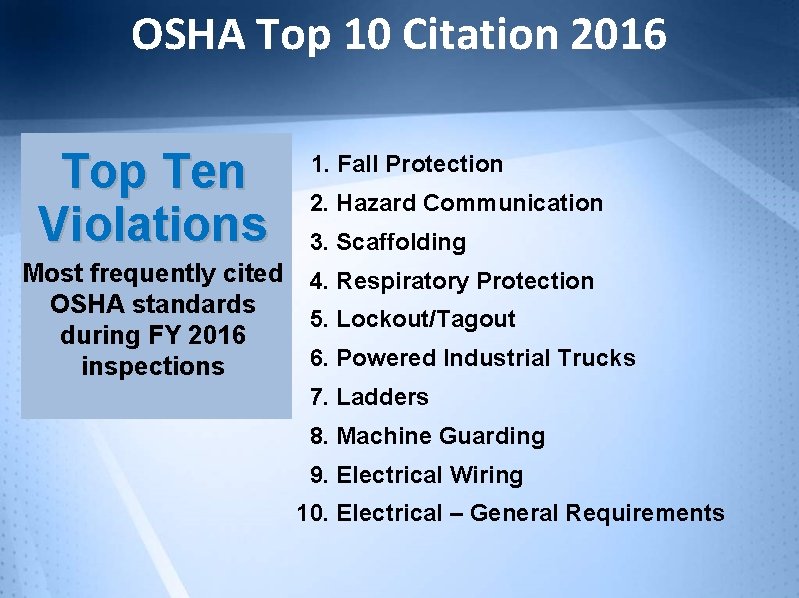
OSHA Top 10 Citation 2016 Top Ten Violations Most frequently cited OSHA standards during FY 2016 inspections 1. Fall Protection 2. Hazard Communication 3. Scaffolding 4. Respiratory Protection 5. Lockout/Tagout 6. Powered Industrial Trucks 7. Ladders 8. Machine Guarding 9. Electrical Wiring 10. Electrical – General Requirements
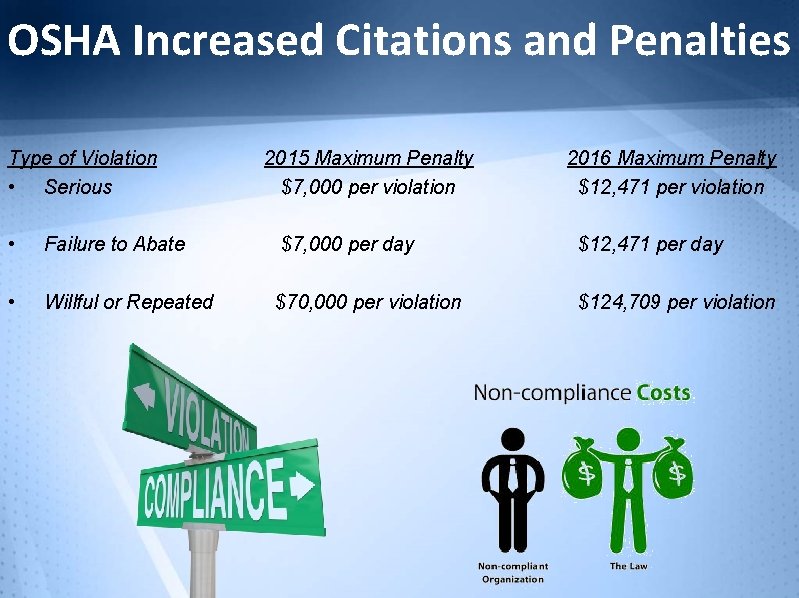
OSHA Increased Citations and Penalties Type of Violation • Serious 2015 Maximum Penalty $7, 000 per violation 2016 Maximum Penalty $12, 471 per violation • Failure to Abate $7, 000 per day $12, 471 per day • Willful or Repeated $70, 000 per violation $124, 709 per violation
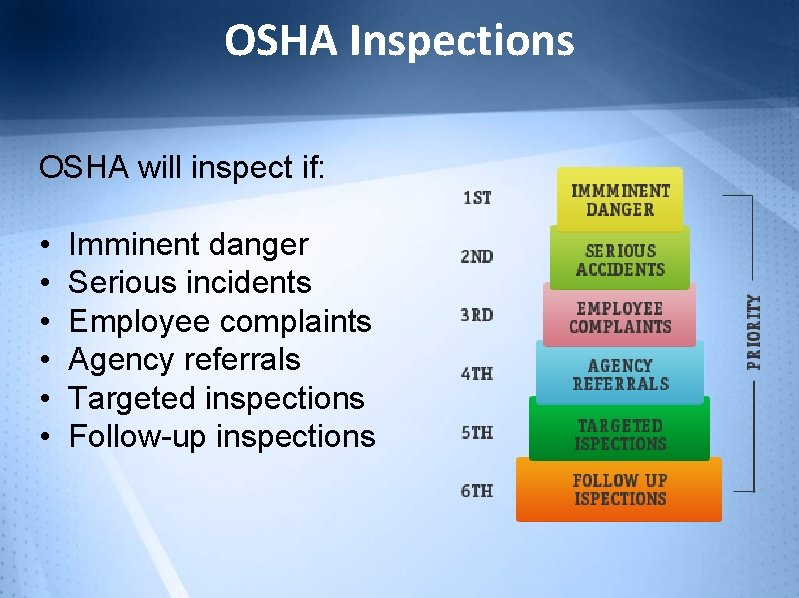
OSHA Inspections OSHA will inspect if: • • • Imminent danger Serious incidents Employee complaints Agency referrals Targeted inspections Follow-up inspections
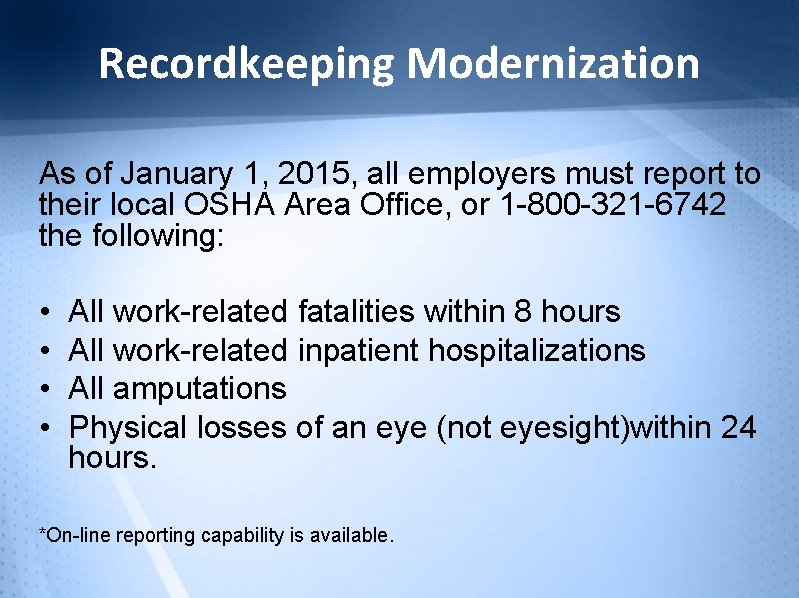
Recordkeeping Modernization As of January 1, 2015, all employers must report to their local OSHA Area Office, or 1 -800 -321 -6742 the following: • • All work-related fatalities within 8 hours All work-related inpatient hospitalizations All amputations Physical losses of an eye (not eyesight)within 24 hours. *On-line reporting capability is available.
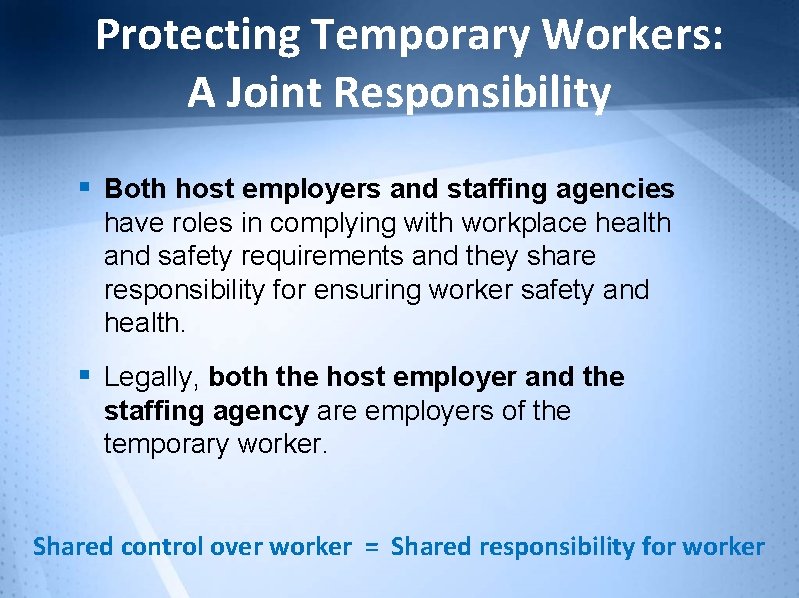
Protecting Temporary Workers: A Joint Responsibility § Both host employers and staffing agencies have roles in complying with workplace health and safety requirements and they share responsibility for ensuring worker safety and health. § Legally, both the host employer and the staffing agency are employers of the temporary worker. Shared control over worker = Shared responsibility for worker
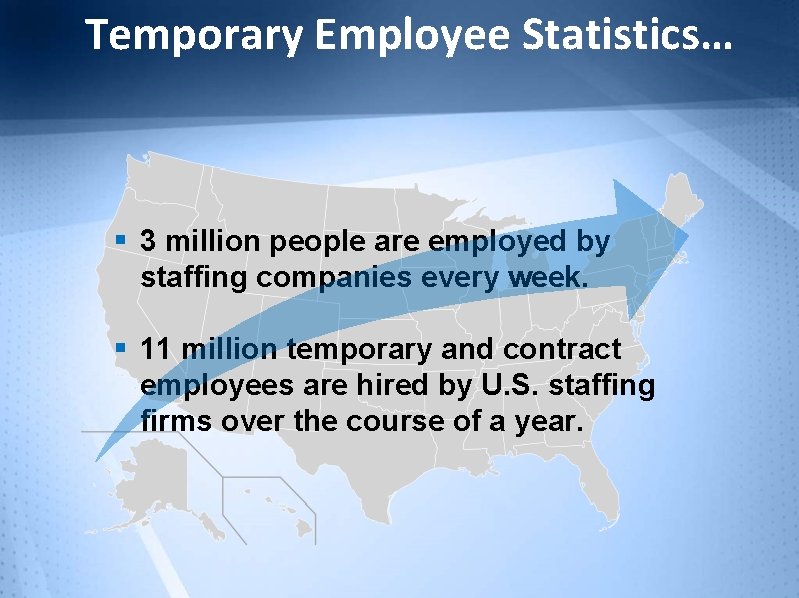
Temporary Employee Statistics… § 3 million people are employed by staffing companies every week. § 11 million temporary and contract employees are hired by U. S. staffing firms over the course of a year.
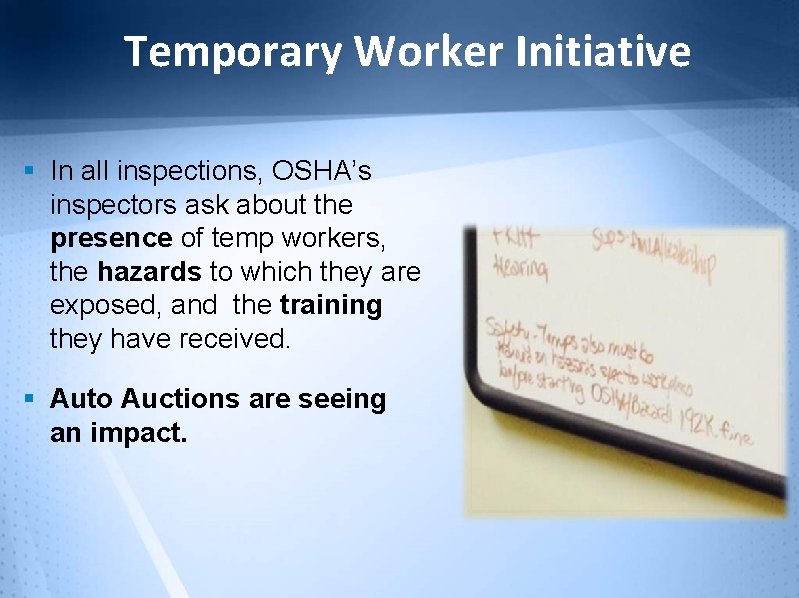
Temporary Worker Initiative § In all inspections, OSHA’s inspectors ask about the presence of temp workers, the hazards to which they are exposed, and the training they have received. § Auto Auctions are seeing an impact.
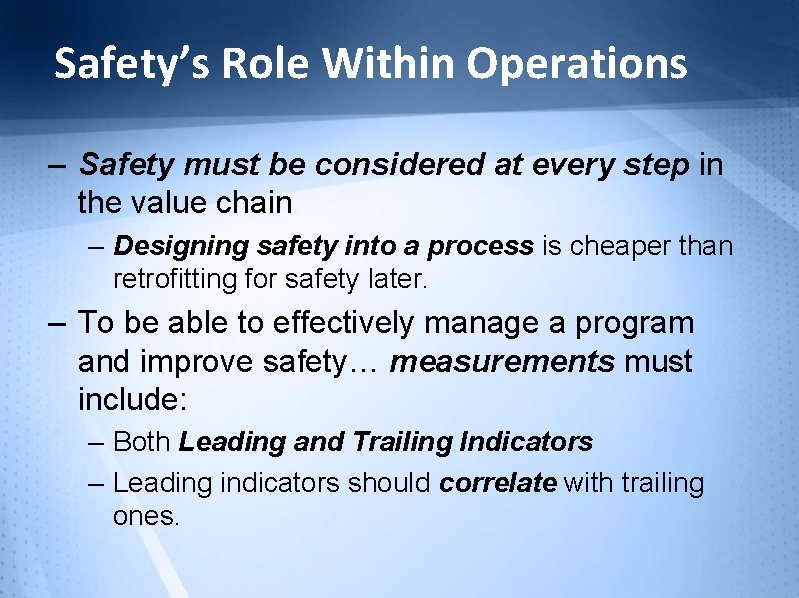
Safety’s Role Within Operations – Safety must be considered at every step in the value chain – Designing safety into a process is cheaper than retrofitting for safety later. – To be able to effectively manage a program and improve safety… measurements must include: – Both Leading and Trailing Indicators – Leading indicators should correlate with trailing ones.
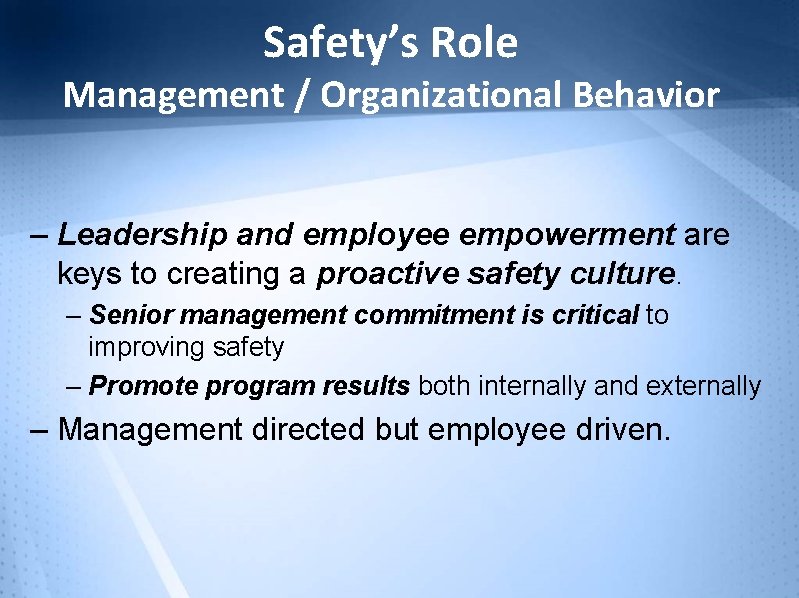
Safety’s Role Management / Organizational Behavior – Leadership and employee empowerment are keys to creating a proactive safety culture. – Senior management commitment is critical to improving safety – Promote program results both internally and externally – Management directed but employee driven.
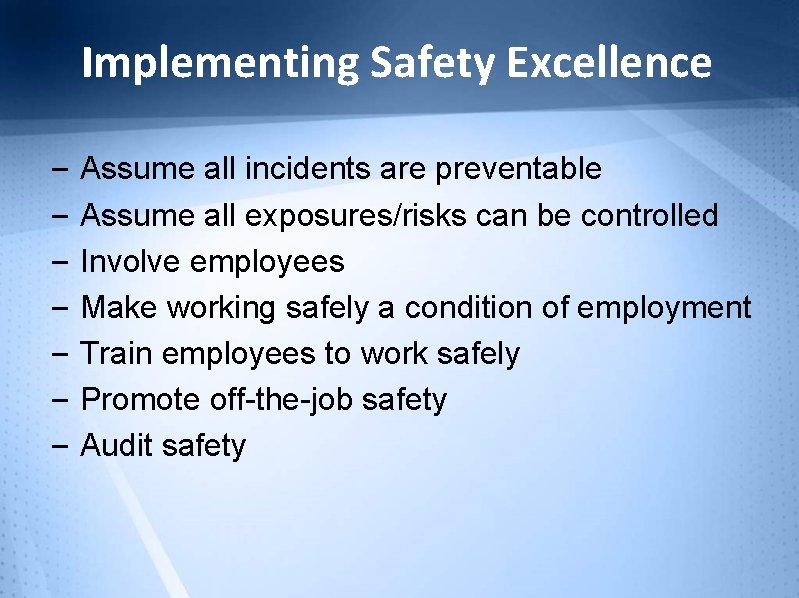
Implementing Safety Excellence – Assume all incidents are preventable – Assume all exposures/risks can be controlled – Involve employees – Make working safely a condition of employment – Train employees to work safely – Promote off-the-job safety – Audit safety
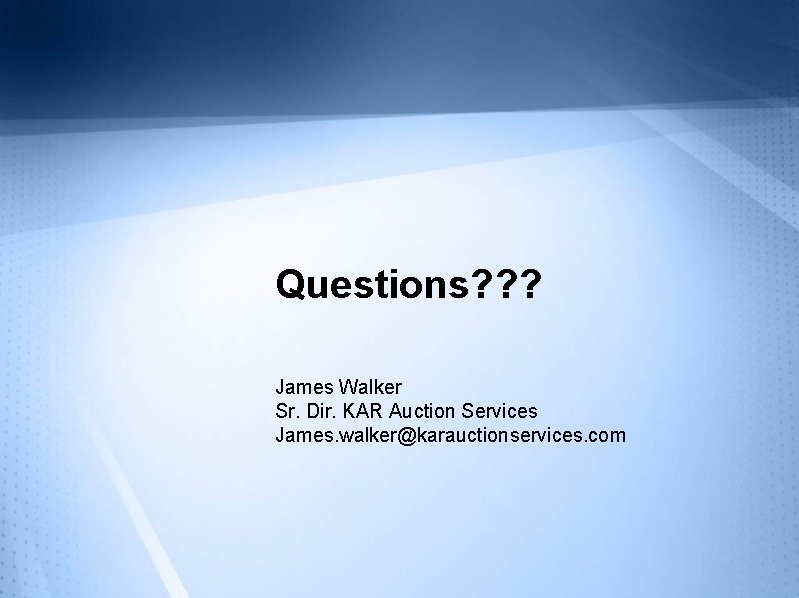
Questions? ? ? James Walker Sr. Dir. KAR Auction Services James. walker@karauctionservices. com
Competitive antagonist
Chapter 5 competitive rivalry and competitive dynamics
What is the least competitive market structure
Firm resources and sustained competitive advantage barney
Developing a firm's strategy canvas focuses on
Creating and sustaining competitive advantage
A company's strategy can be considered ethical
Benefits of hpw
Chapter 18 creating competitive advantage
Chapter 18 creating competitive advantage
Jay barney competitive advantage
Competitive advantage of starbucks
What is starbucks competitive advantage
Human resource management gaining a competitive advantage
Human resource management gaining a competitive advantage
Human resource management gaining a competitive advantage
Levi's competitive advantage
Quotes on competitive advantage
Bases of competitive advantage
Four building blocks of competitive advantage
Achieving competitive advantage with information systems
Searching for loose bricks
Advantage of mis
Strategic planning for competitive advantage
Competitive advantage pada koperasi
Competitive advantage of kfc