New LED driver Preliminary tests G Mitev E
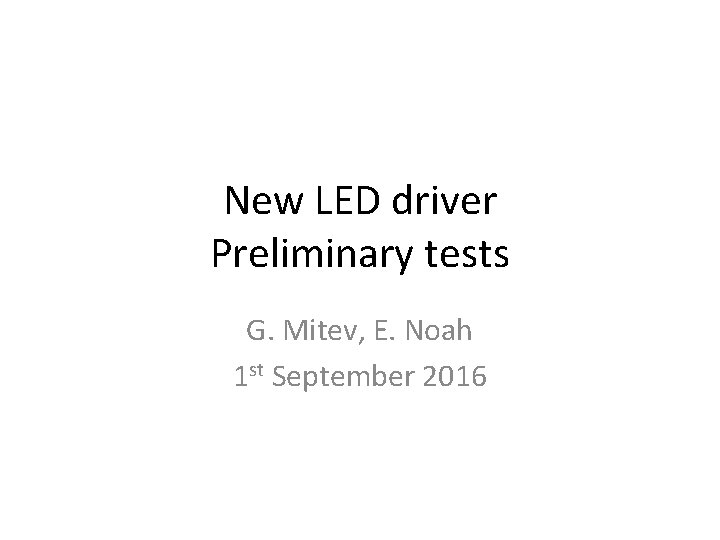
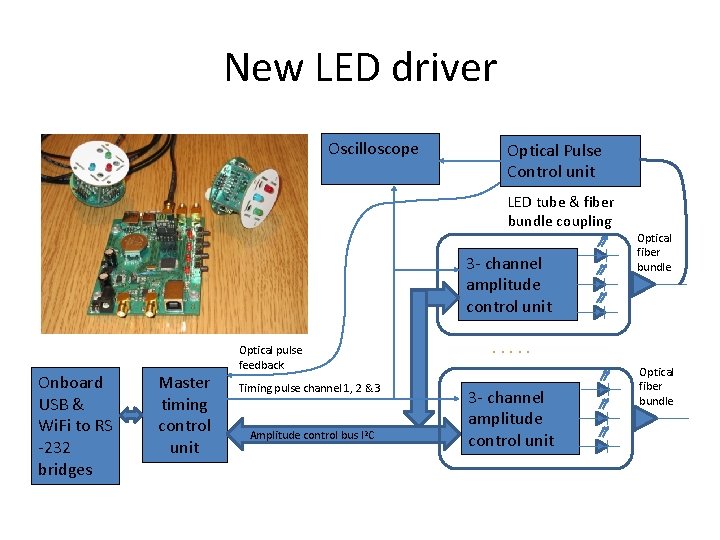
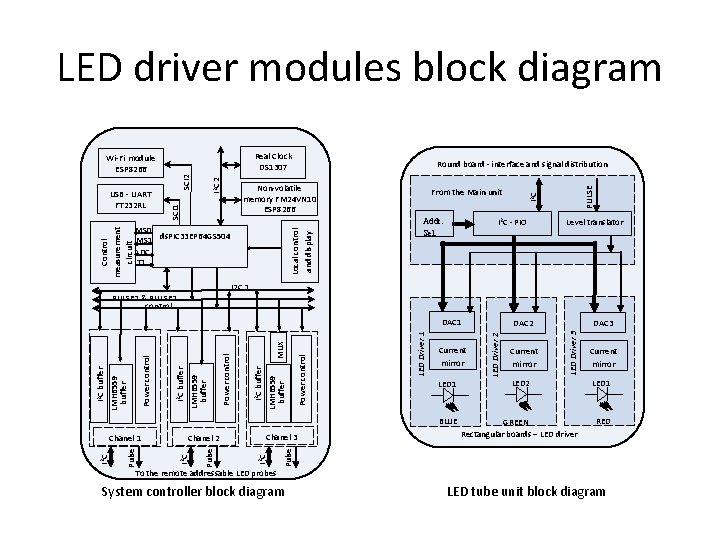
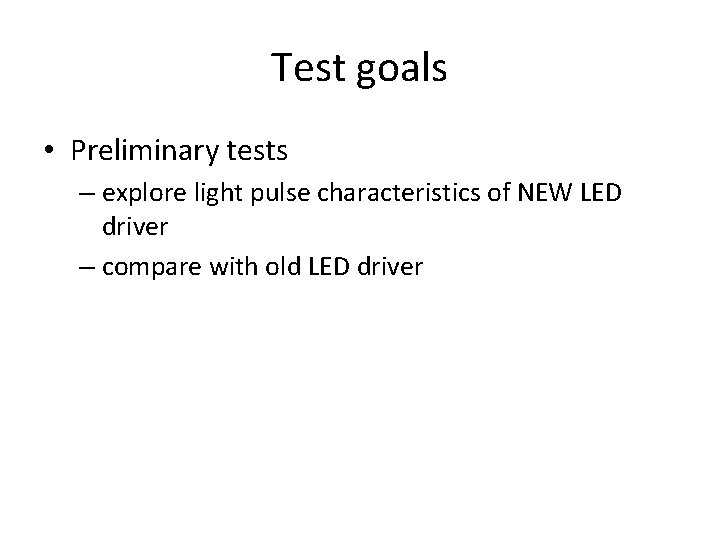
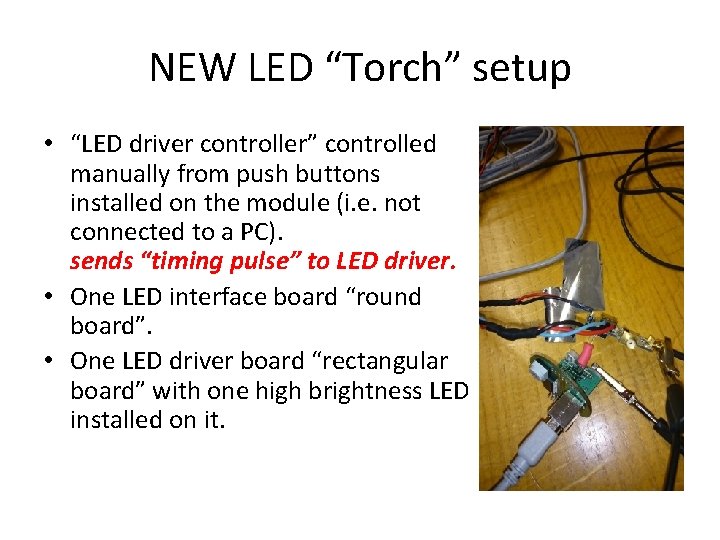
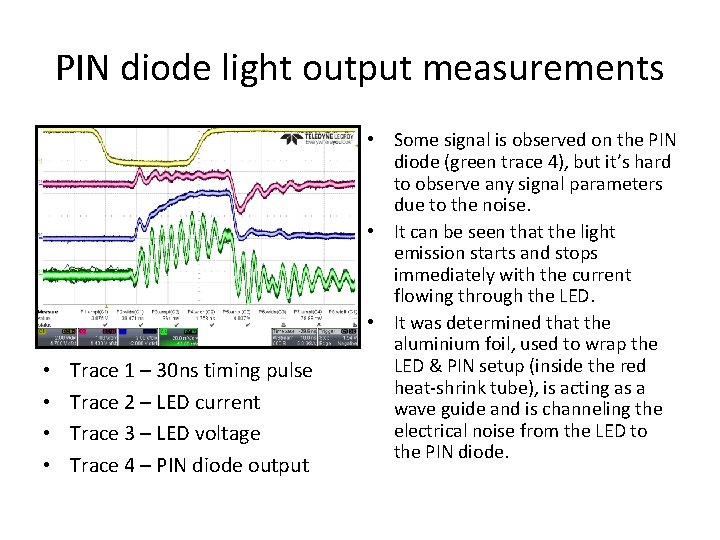
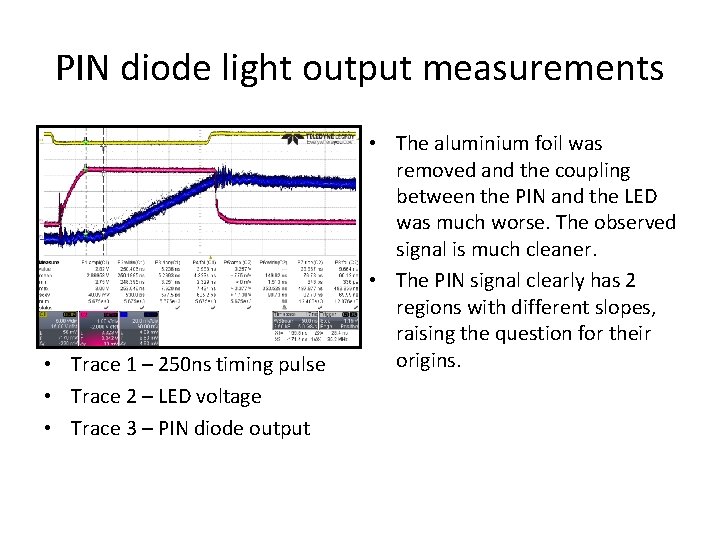
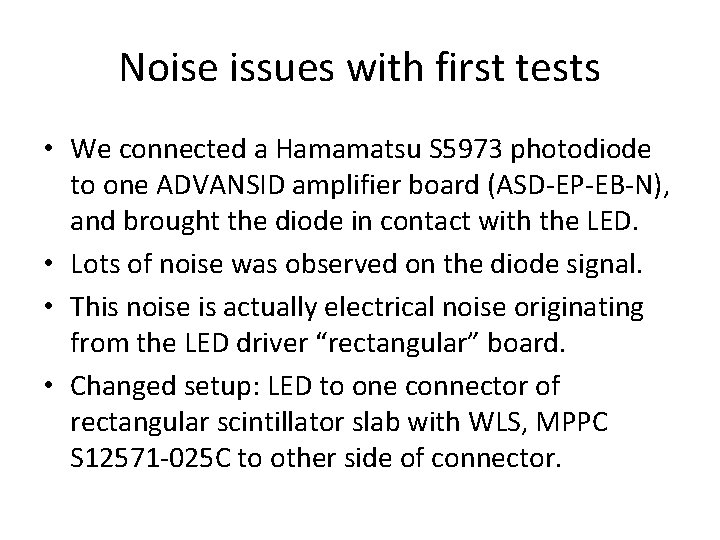
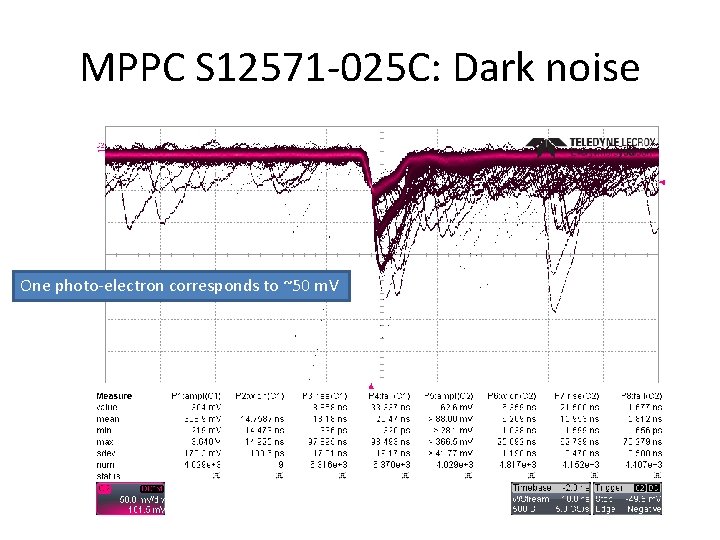
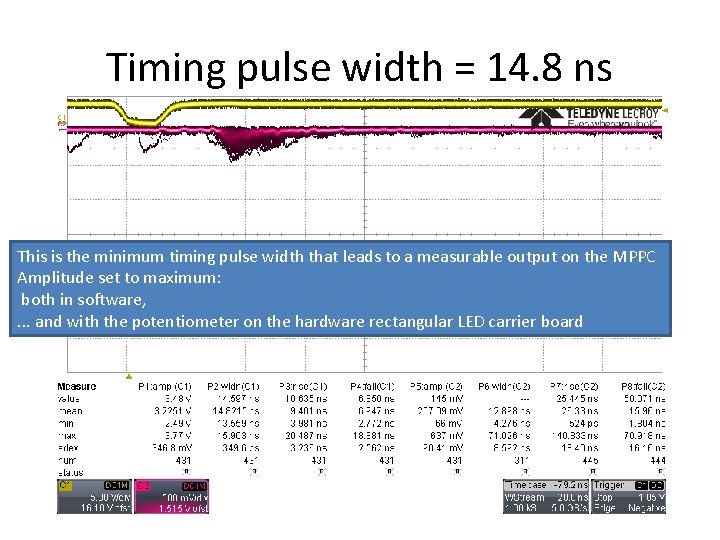
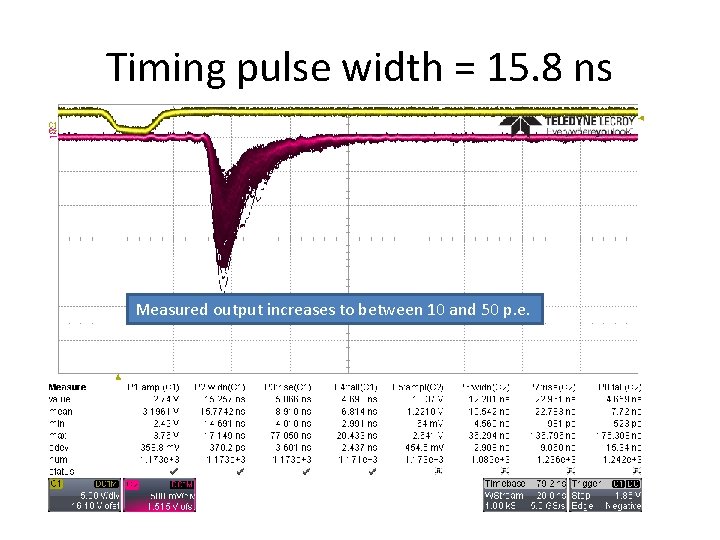
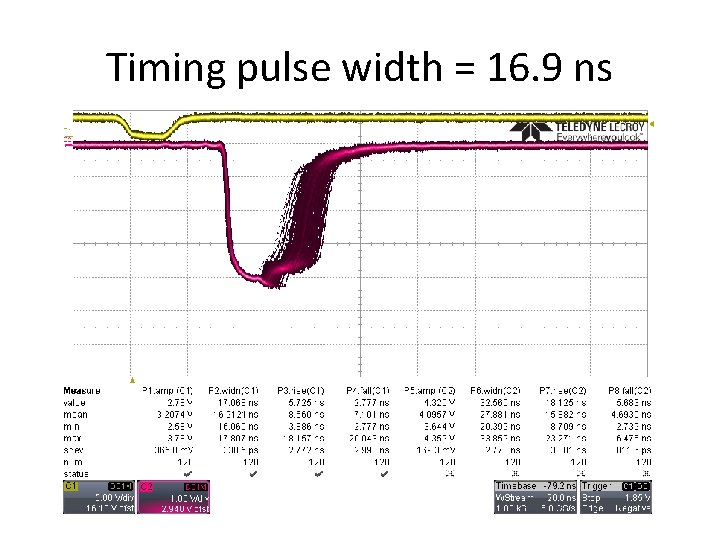
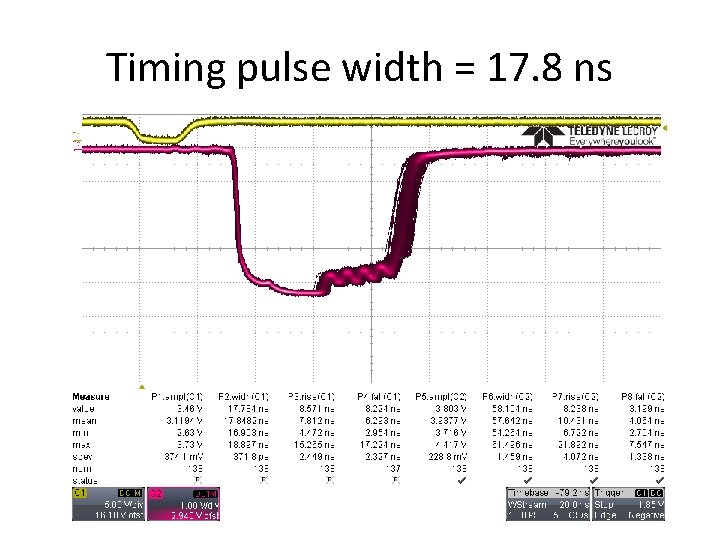
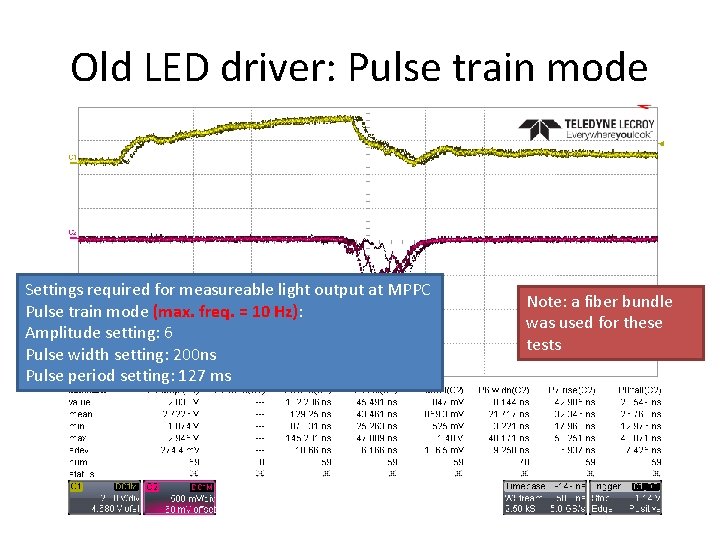
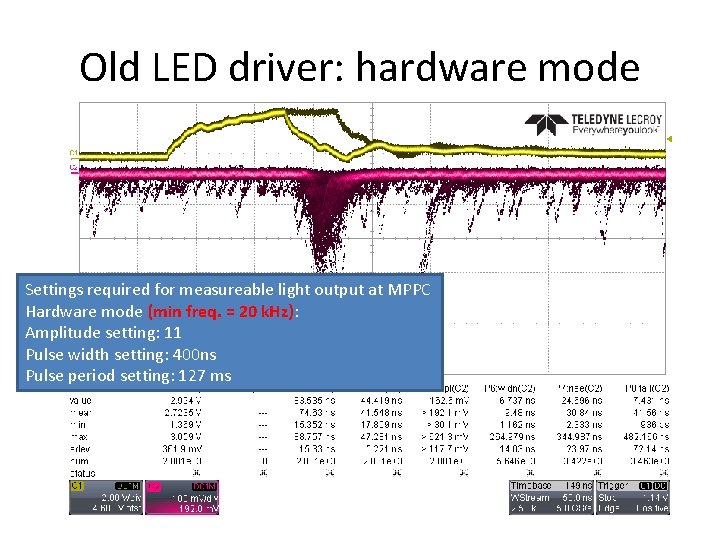
- Slides: 15
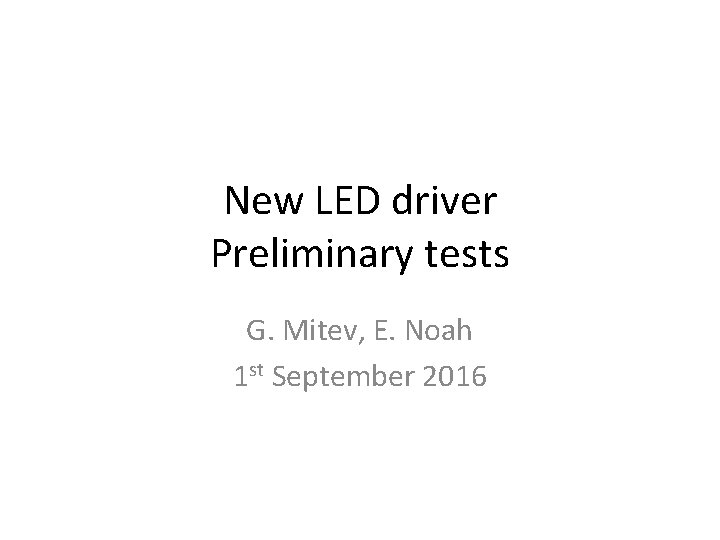
New LED driver Preliminary tests G. Mitev, E. Noah 1 st September 2016
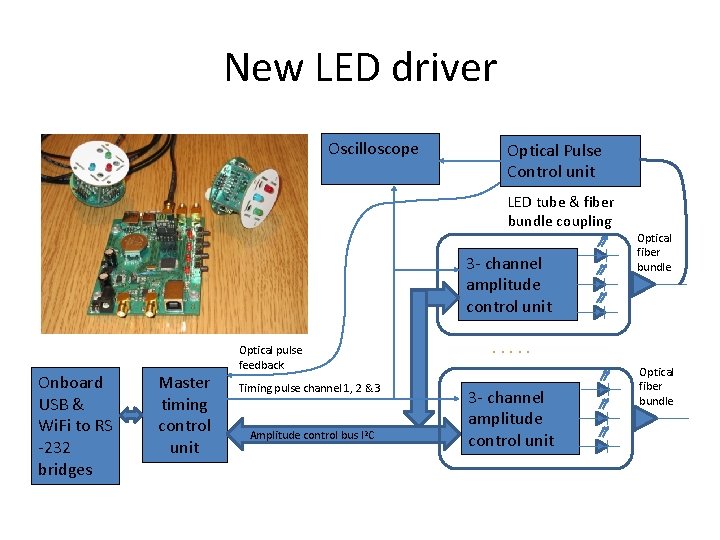
New LED driver Oscilloscope Optical Pulse Control unit LED tube & fiber bundle coupling 3 - channel amplitude control unit Onboard USB & Wi. Fi to RS -232 bridges Master timing control unit Optical pulse feedback Timing pulse channel 1, 2 & 3 Amplitude control bus I 2 C Optical fiber bundle . . . 3 - channel amplitude control unit Optical fiber bundle
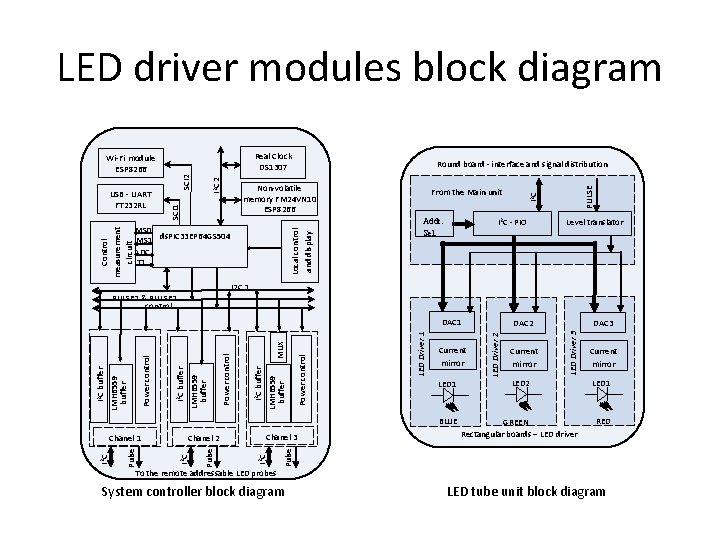
LED driver modules block diagram Real Clock DS 1307 MS 0 MS 1 ds. PIC 33 EP 64 GS 504 ADC T 1 From the Main unit Addr. Sel. I 2 C - PIO Current mirror LED Driver 3 LED Driver 2 Current mirror DAC 3 DAC 2 Current mirror LED 1 LED 2 LED 1 BLUE GREEN Rectangular boards – LED driver RED Pulse LED Driver 1 Power control MUX LMH 6559 buffer I 2 C buffer Chanel 3 I 2 C Power control I 2 C buffer LMH 6559 buffer Pulse Chanel 2 I 2 C Power control LMH 6559 buffer I 2 C buffer DAC 1 I 2 C Level translator I 2 C 1 PULSE 1 & PULSE 2 control Chanel 1 PULSE SCI 1 Non-volatile memory FM 24 VN 10 ESP 8266 I 2 C 2 Round board - interface and signal distribution Local control and display Control measurement circuit USB - UART FT 232 RL SCI 2 Wi-Fi module ESP 8266 To the remote addressable LED probes System controller block diagram LED tube unit block diagram
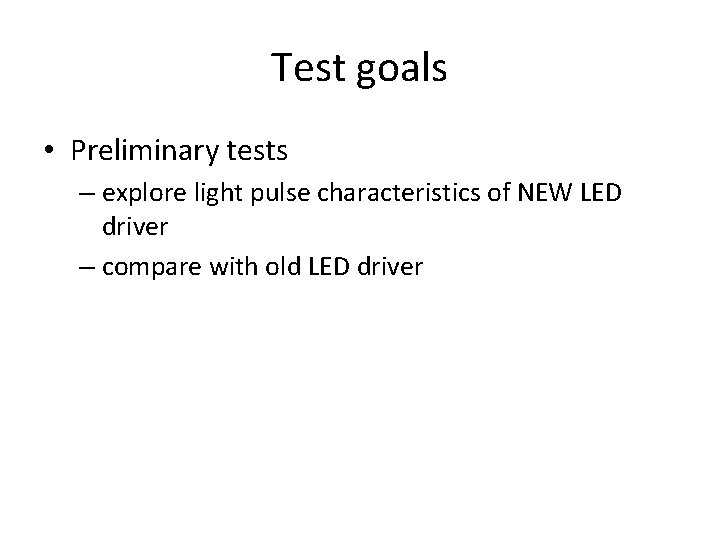
Test goals • Preliminary tests – explore light pulse characteristics of NEW LED driver – compare with old LED driver
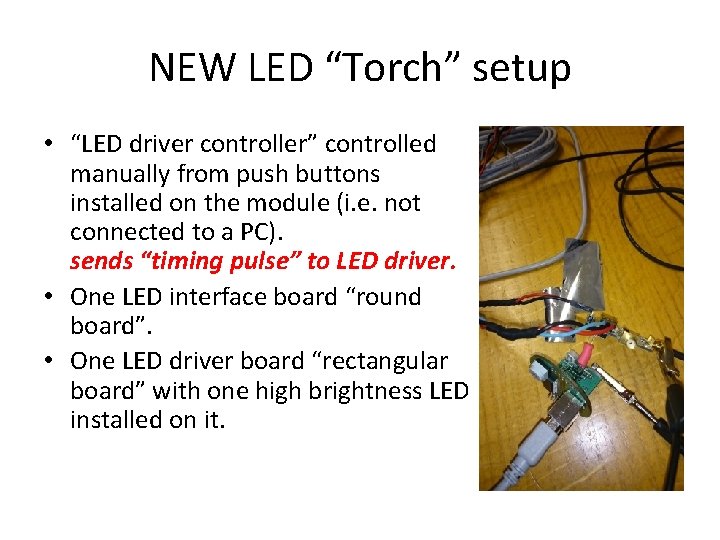
NEW LED “Torch” setup • “LED driver controller” controlled manually from push buttons installed on the module (i. e. not connected to a PC). sends “timing pulse” to LED driver. • One LED interface board “round board”. • One LED driver board “rectangular board” with one high brightness LED installed on it.
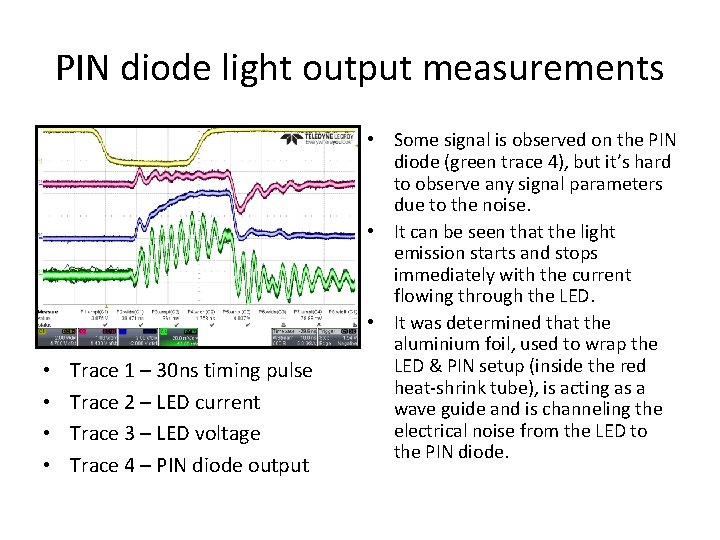
PIN diode light output measurements • • Trace 1 – 30 ns timing pulse Trace 2 – LED current Trace 3 – LED voltage Trace 4 – PIN diode output • Some signal is observed on the PIN diode (green trace 4), but it’s hard to observe any signal parameters due to the noise. • It can be seen that the light emission starts and stops immediately with the current flowing through the LED. • It was determined that the aluminium foil, used to wrap the LED & PIN setup (inside the red heat-shrink tube), is acting as a wave guide and is channeling the electrical noise from the LED to the PIN diode.
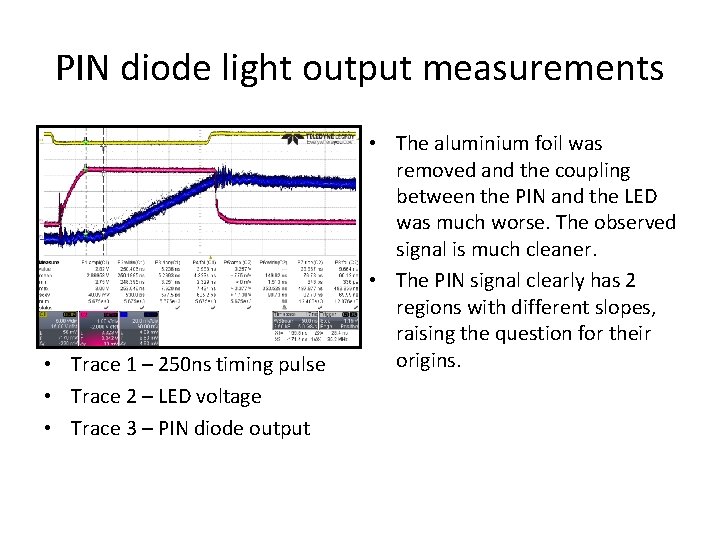
PIN diode light output measurements • Trace 1 – 250 ns timing pulse • Trace 2 – LED voltage • Trace 3 – PIN diode output • The aluminium foil was removed and the coupling between the PIN and the LED was much worse. The observed signal is much cleaner. • The PIN signal clearly has 2 regions with different slopes, raising the question for their origins.
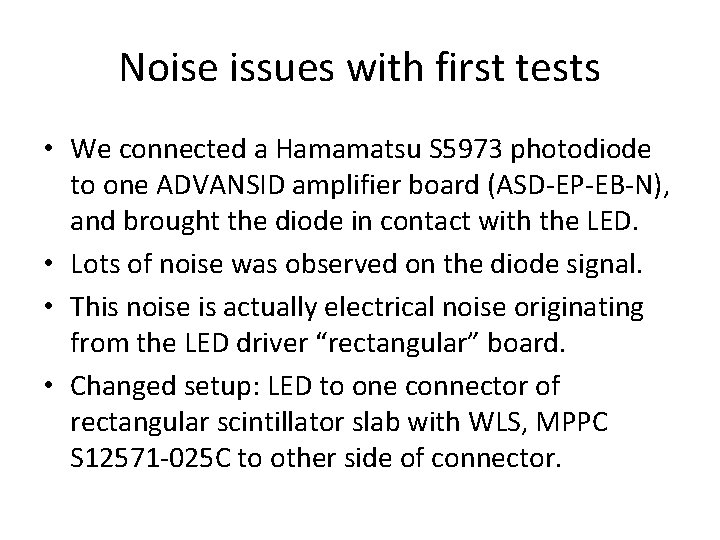
Noise issues with first tests • We connected a Hamamatsu S 5973 photodiode to one ADVANSID amplifier board (ASD-EP-EB-N), and brought the diode in contact with the LED. • Lots of noise was observed on the diode signal. • This noise is actually electrical noise originating from the LED driver “rectangular” board. • Changed setup: LED to one connector of rectangular scintillator slab with WLS, MPPC S 12571 -025 C to other side of connector.
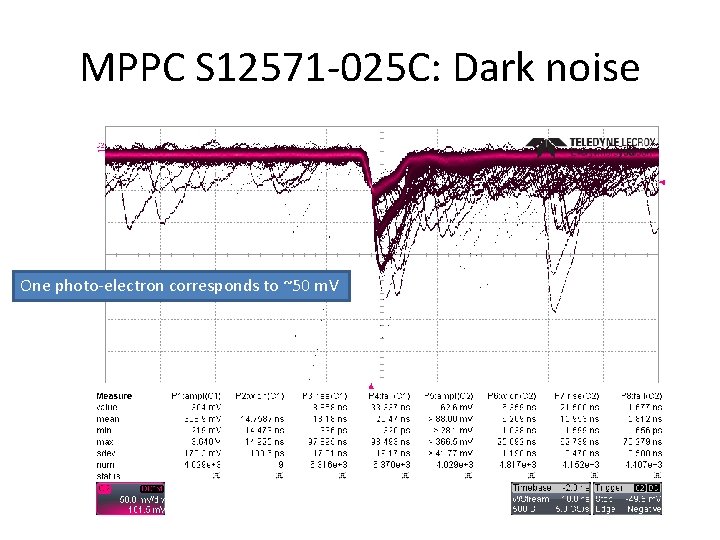
MPPC S 12571 -025 C: Dark noise One photo-electron corresponds to ~50 m. V
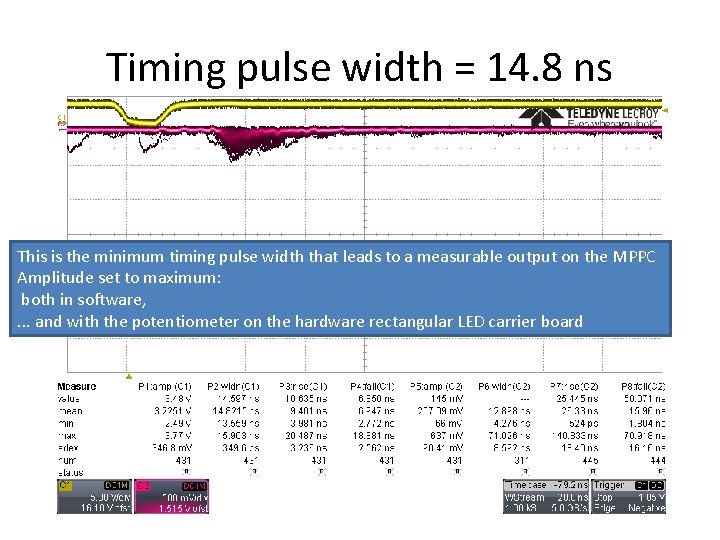
Timing pulse width = 14. 8 ns This is the minimum timing pulse width that leads to a measurable output on the MPPC Amplitude set to maximum: both in software, . . . and with the potentiometer on the hardware rectangular LED carrier board
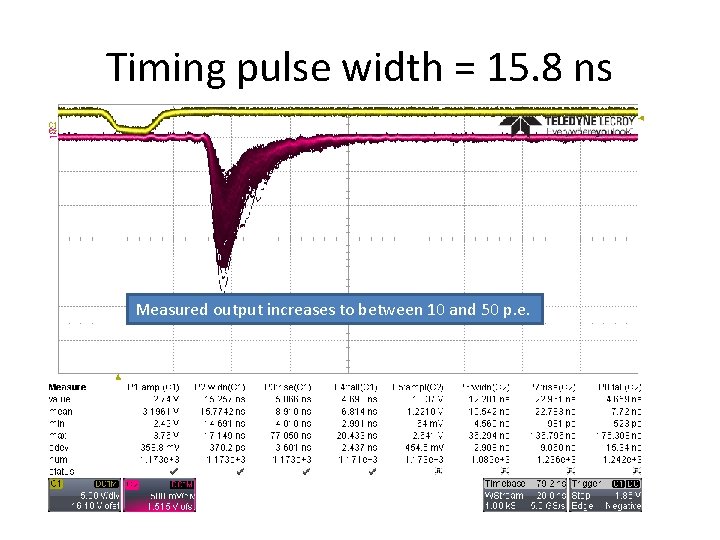
Timing pulse width = 15. 8 ns Measured output increases to between 10 and 50 p. e.
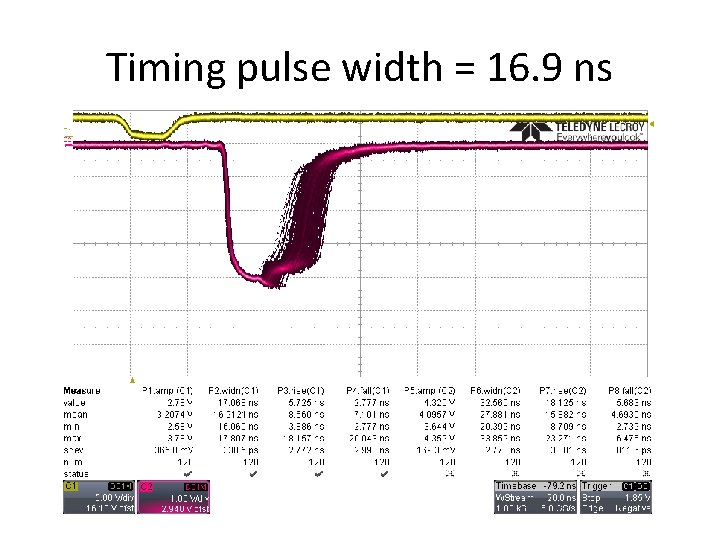
Timing pulse width = 16. 9 ns
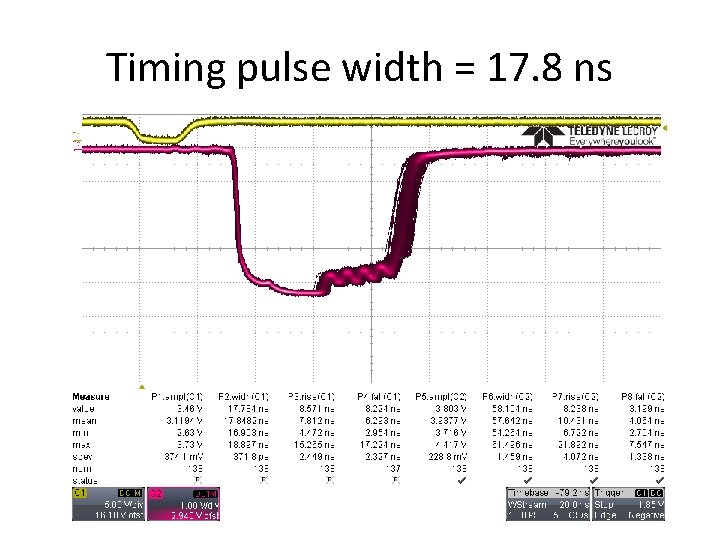
Timing pulse width = 17. 8 ns
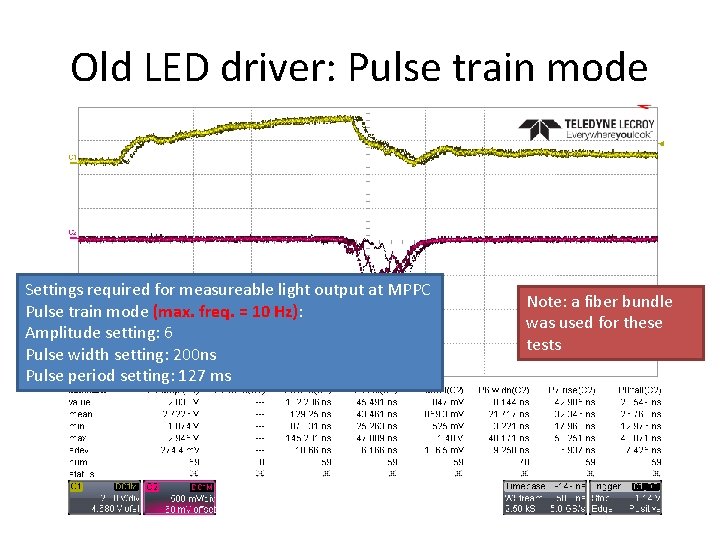
Old LED driver: Pulse train mode Settings required for measureable light output at MPPC Pulse train mode (max. freq. = 10 Hz): Amplitude setting: 6 Pulse width setting: 200 ns Pulse period setting: 127 ms Note: a fiber bundle was used for these tests
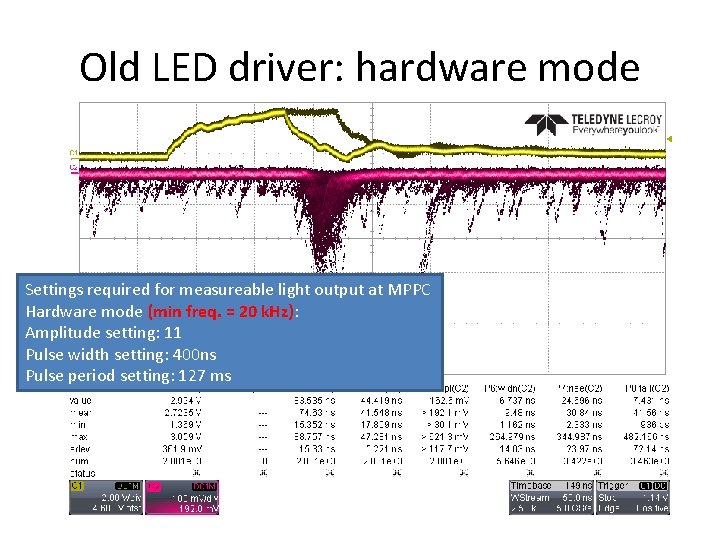
Old LED driver: hardware mode Settings required for measureable light output at MPPC Hardware mode (min freq. = 20 k. Hz): Amplitude setting: 11 Pulse width setting: 400 ns Pulse period setting: 127 ms
Ace different tests help iq still
User-mode driver framework
New zealands tests positive
New jersey drivers manual
Getting a driver license illegally may result in
Chapter 1 the new jersey driver license system answers
Nj road test requirements
Chapter 1 the new jersey driver license system answers
Preliminary budget
Preliminary treatment adalah
Preliminary survey audit
P 波
Preliminary design review example
Preliminary materials
Mla thesis example
Preliminary interview