Mechanisms and Applications mr Can ZGNEY Mechanisms A
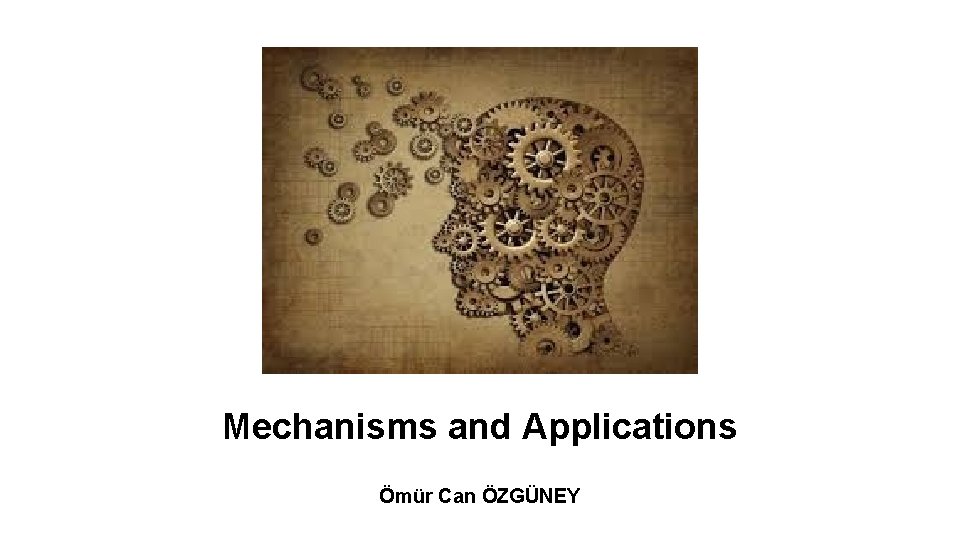
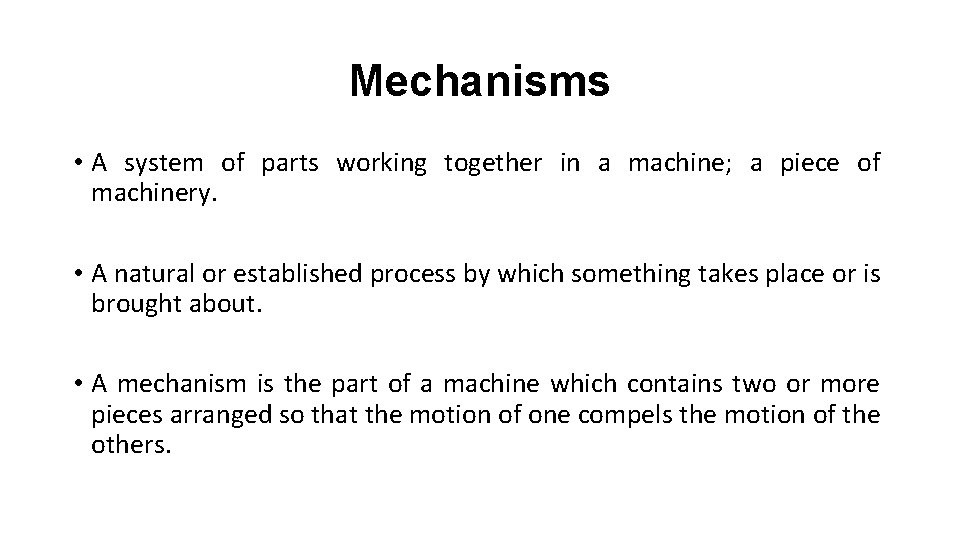
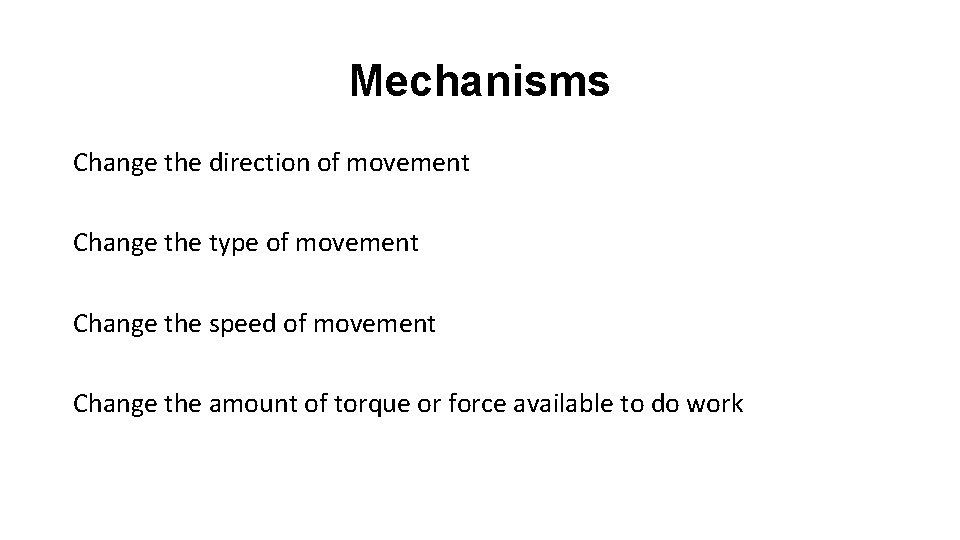
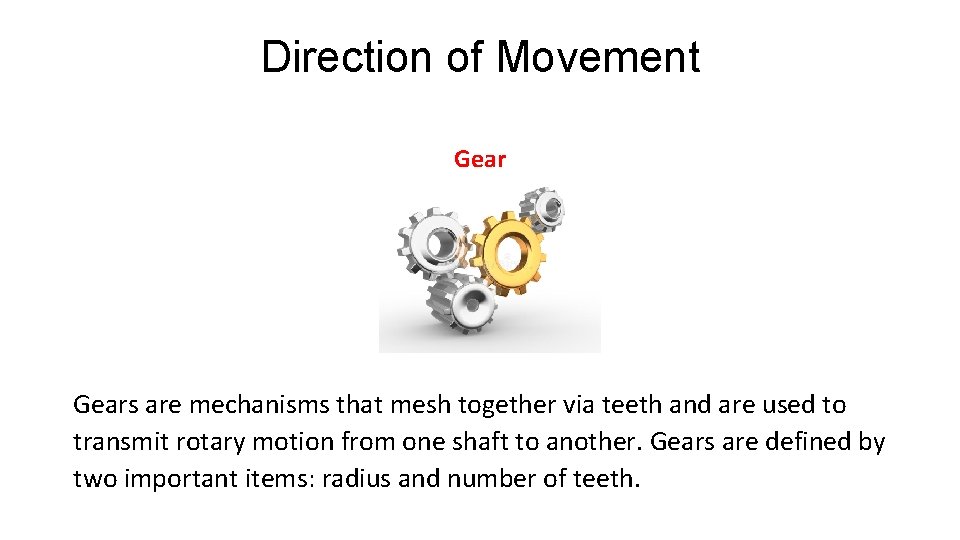
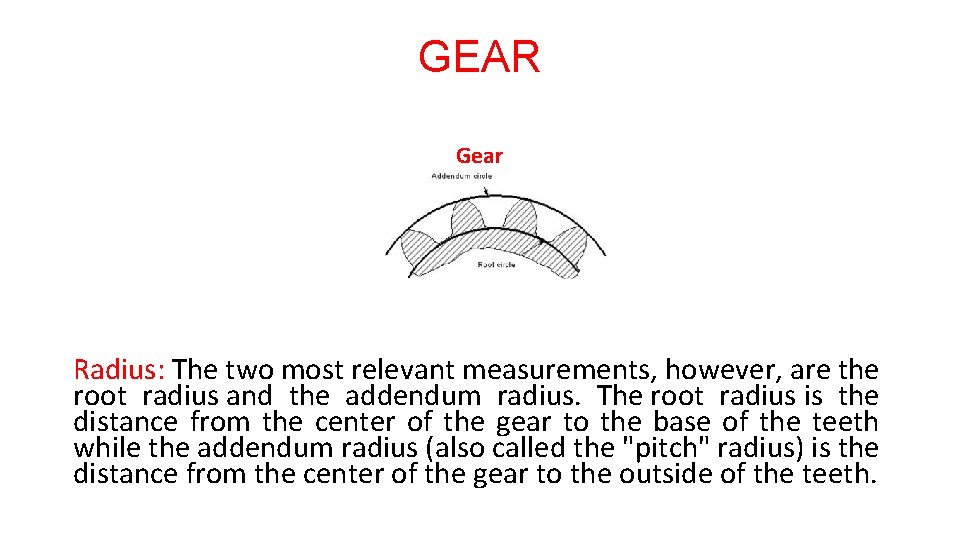
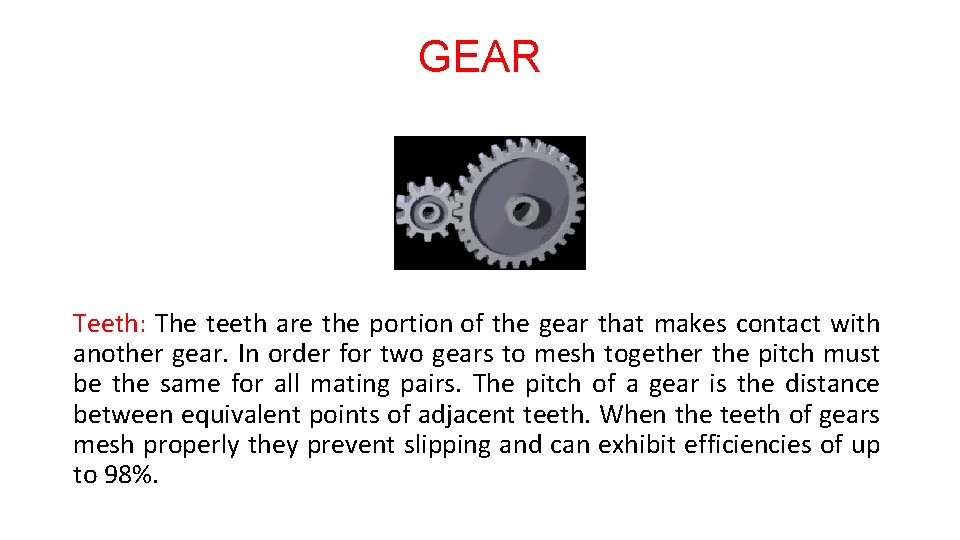
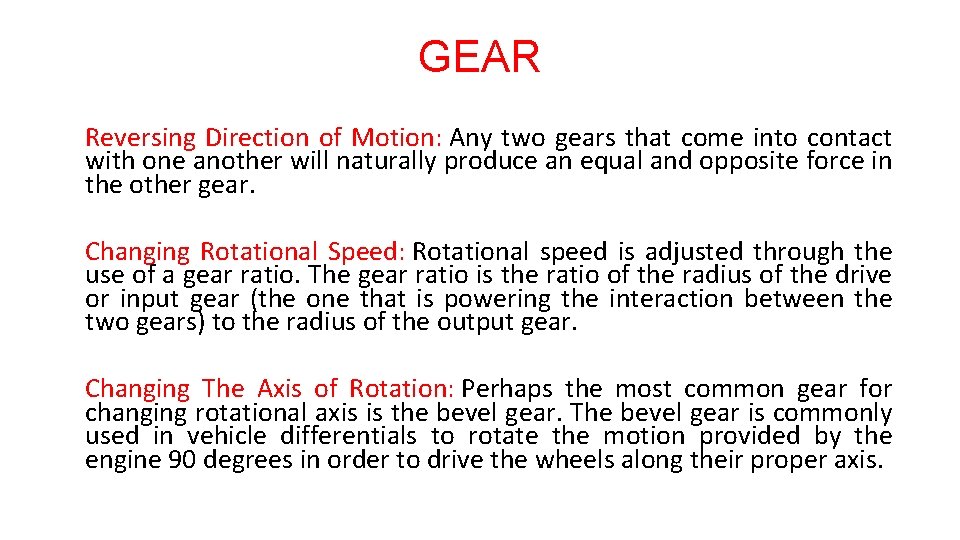
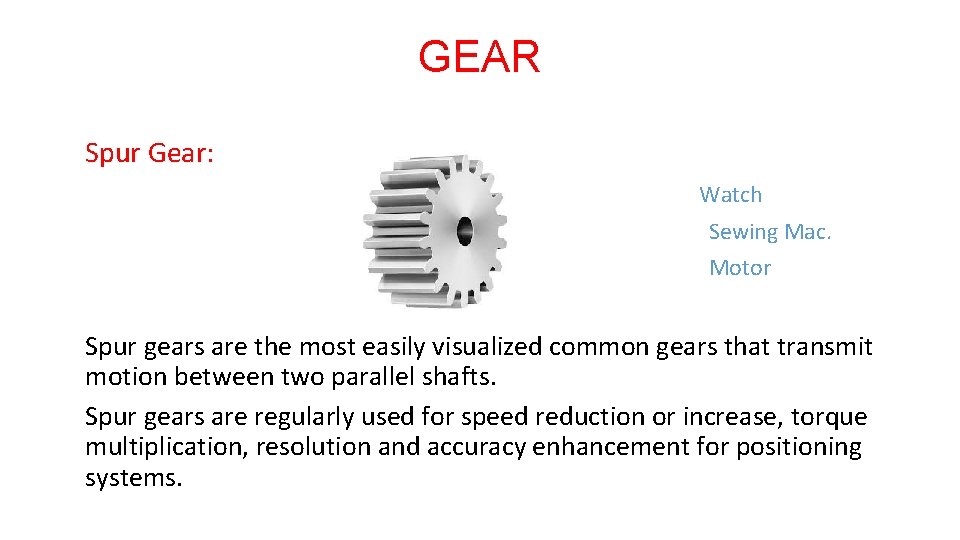
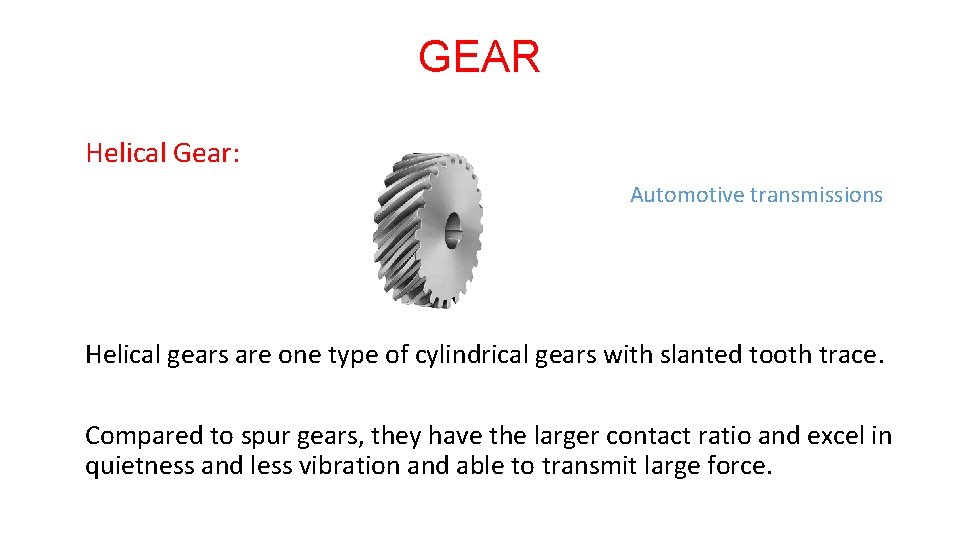
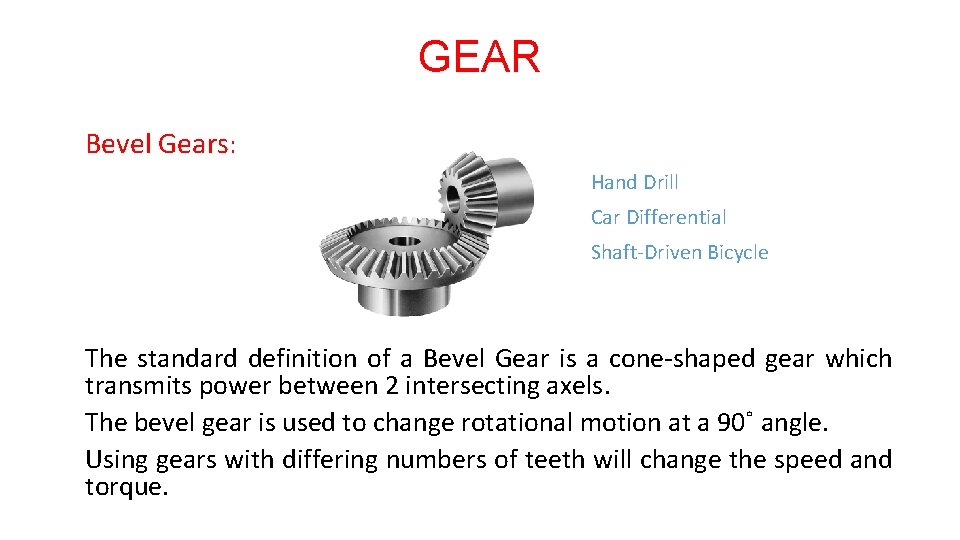
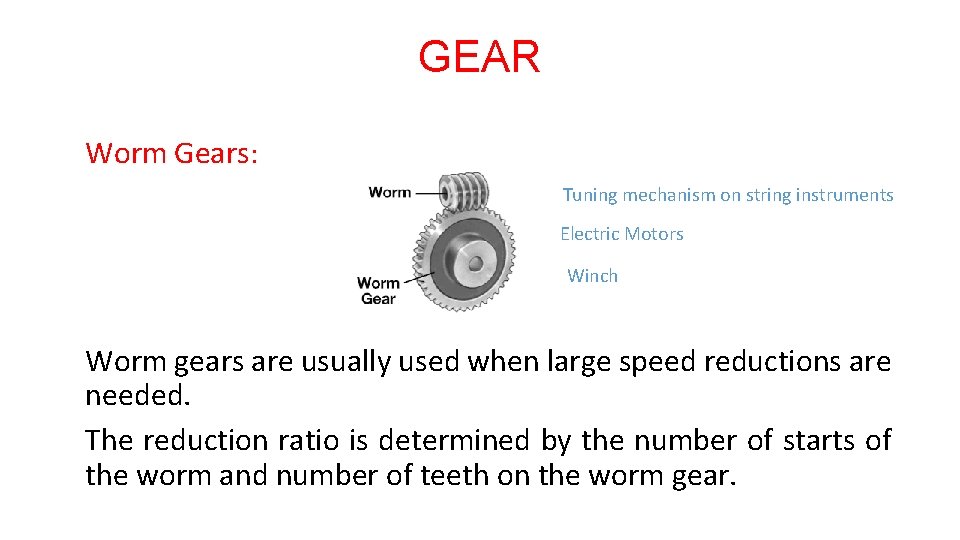
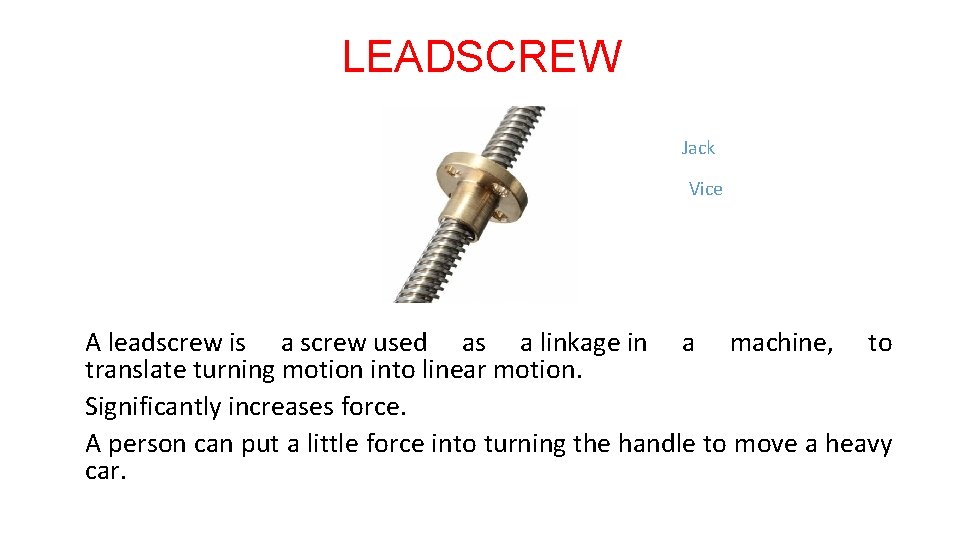
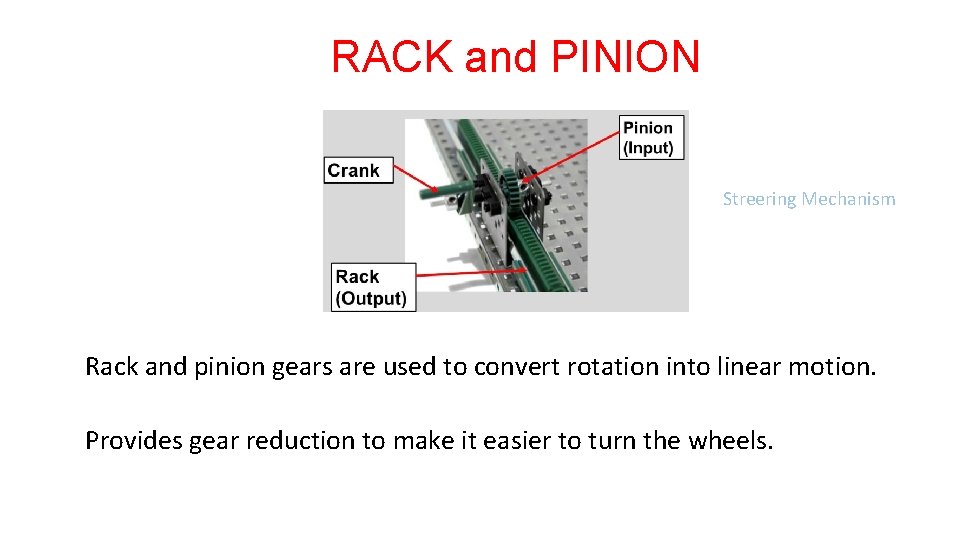
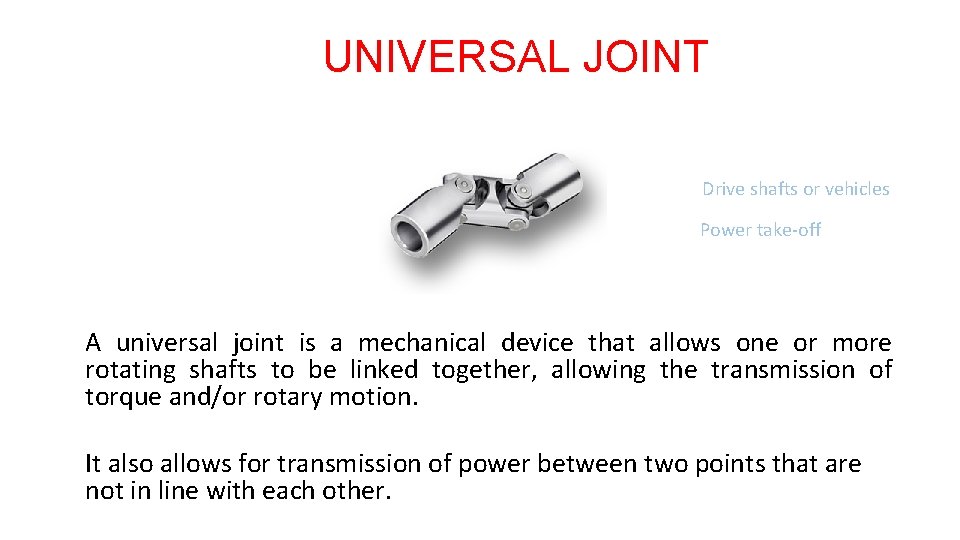
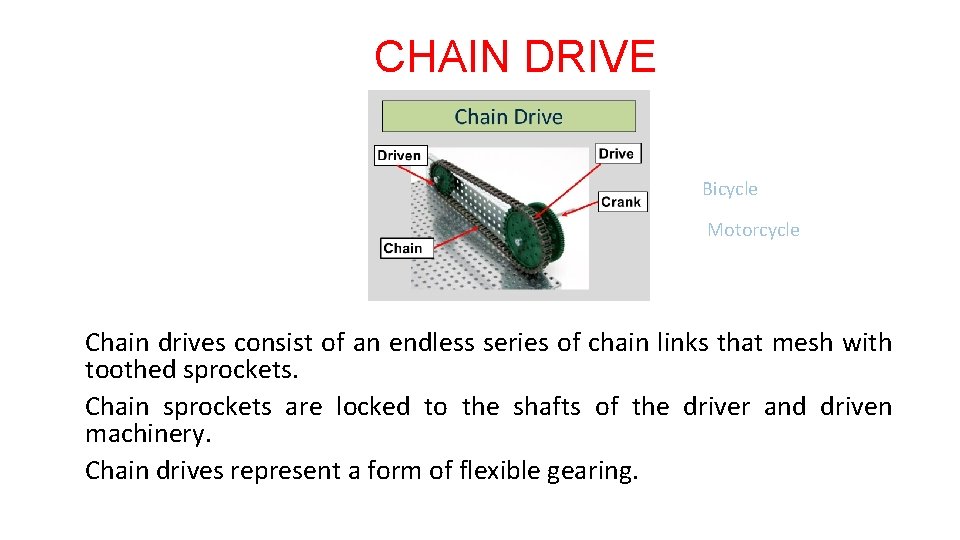
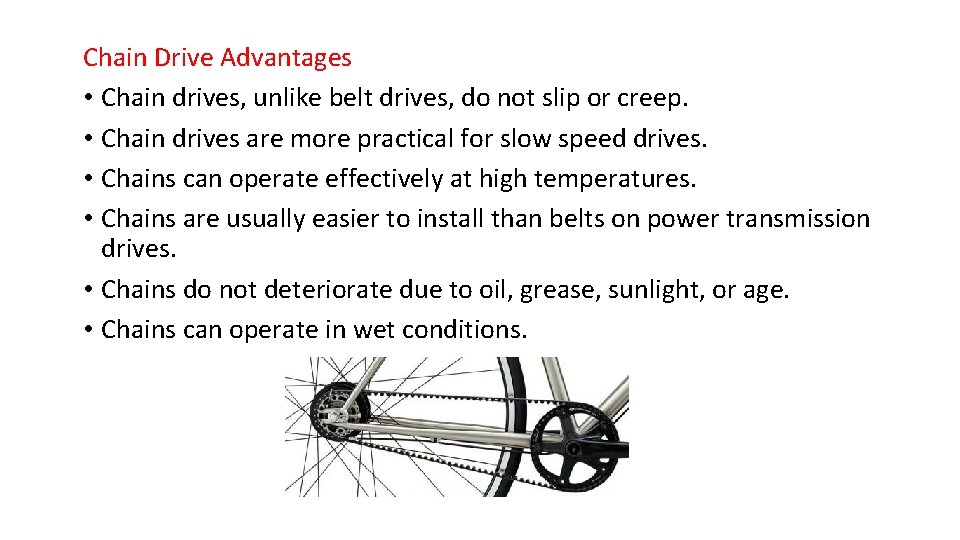
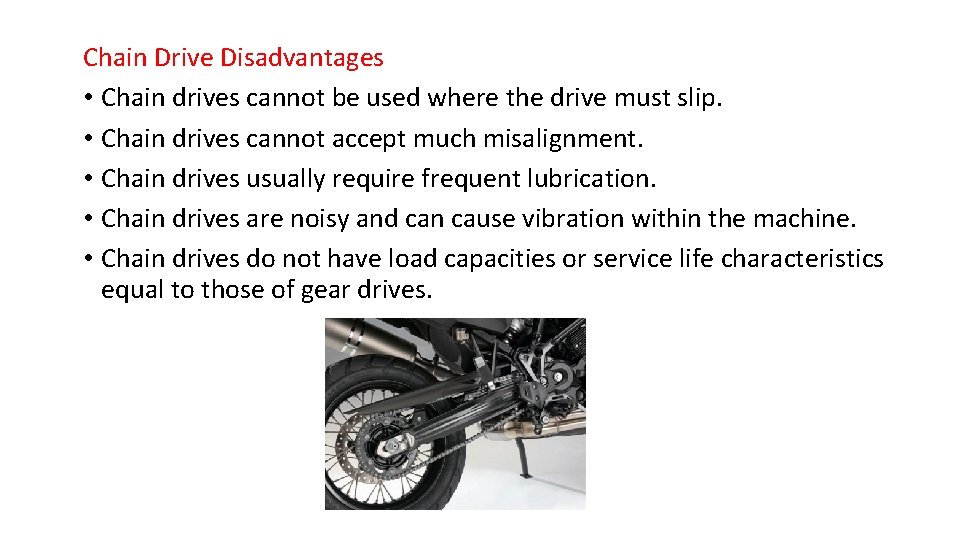

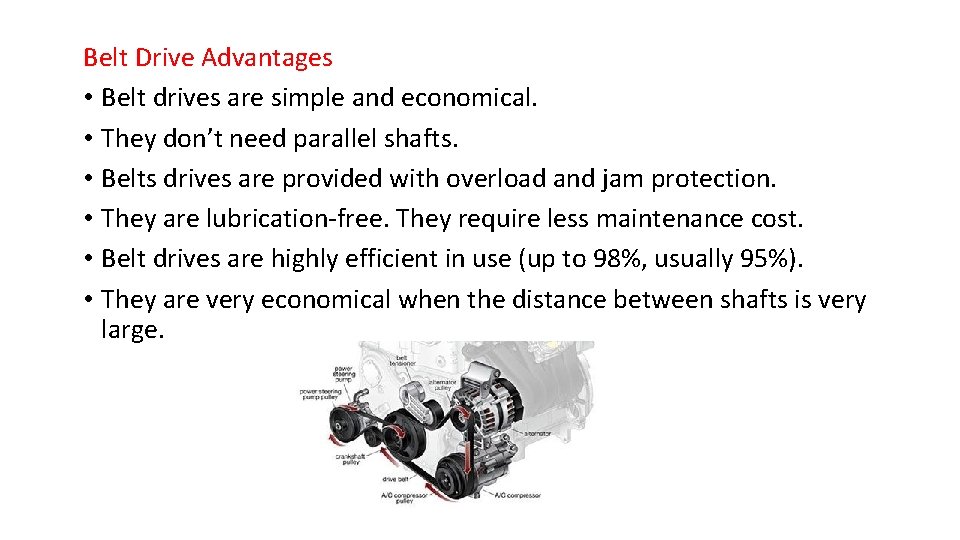
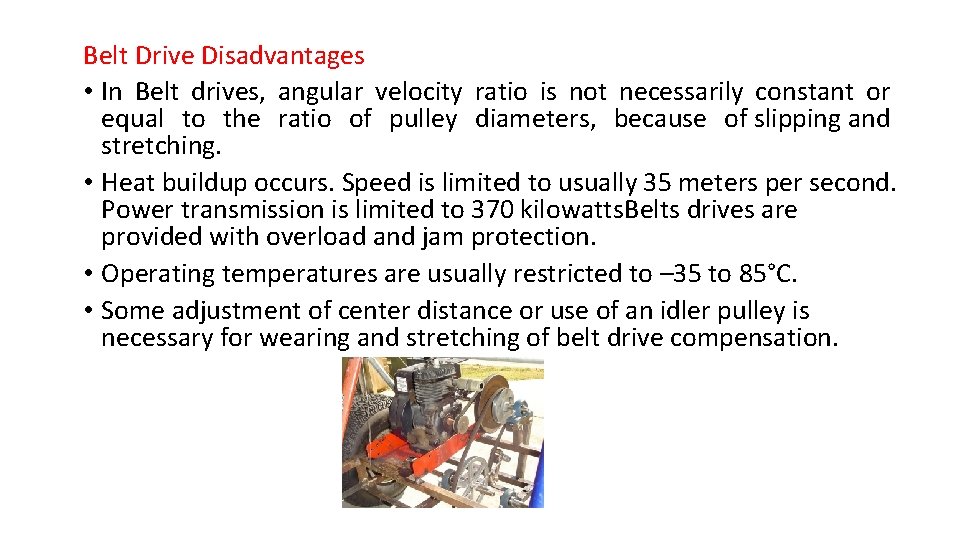
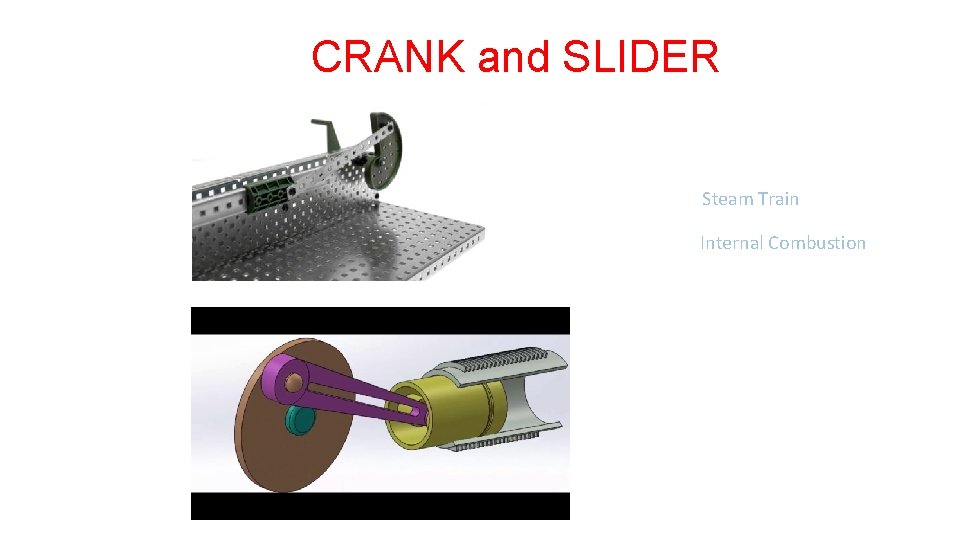
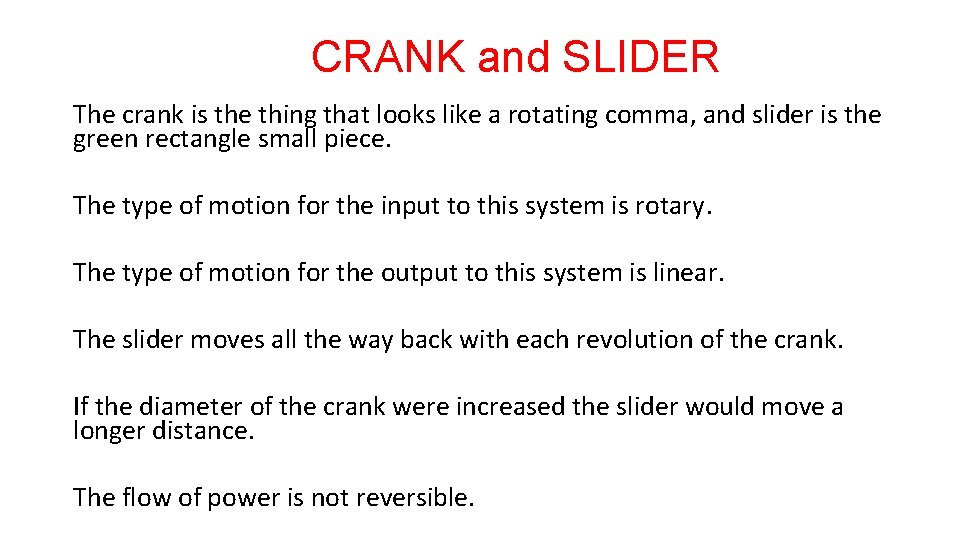
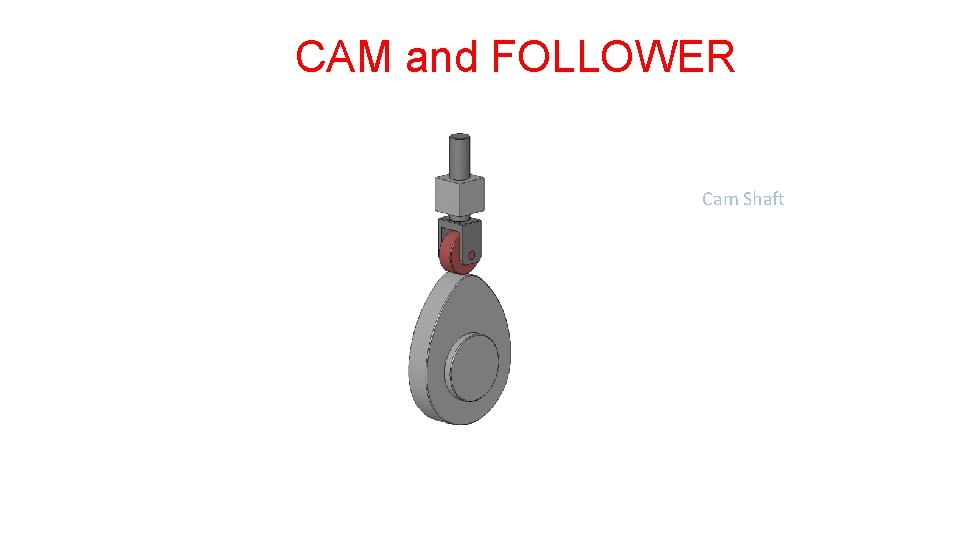
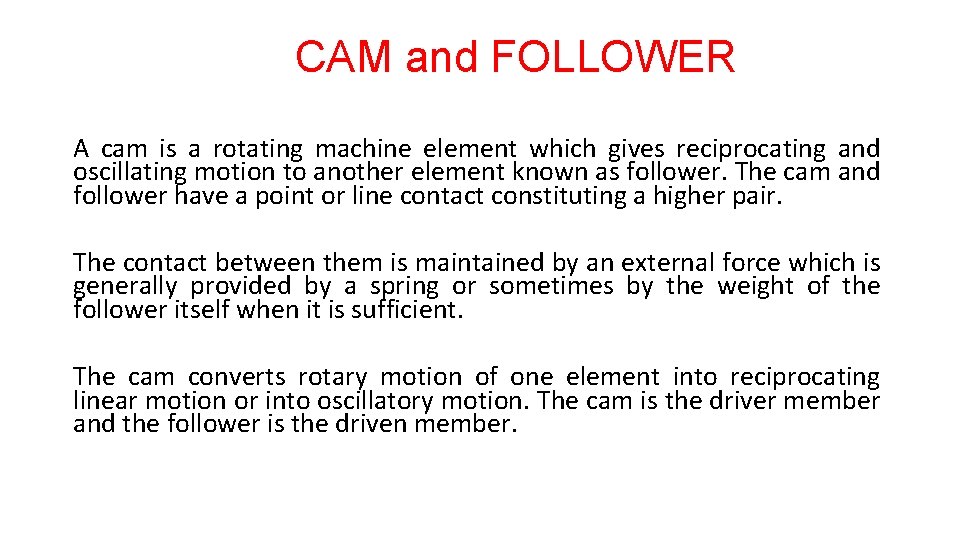
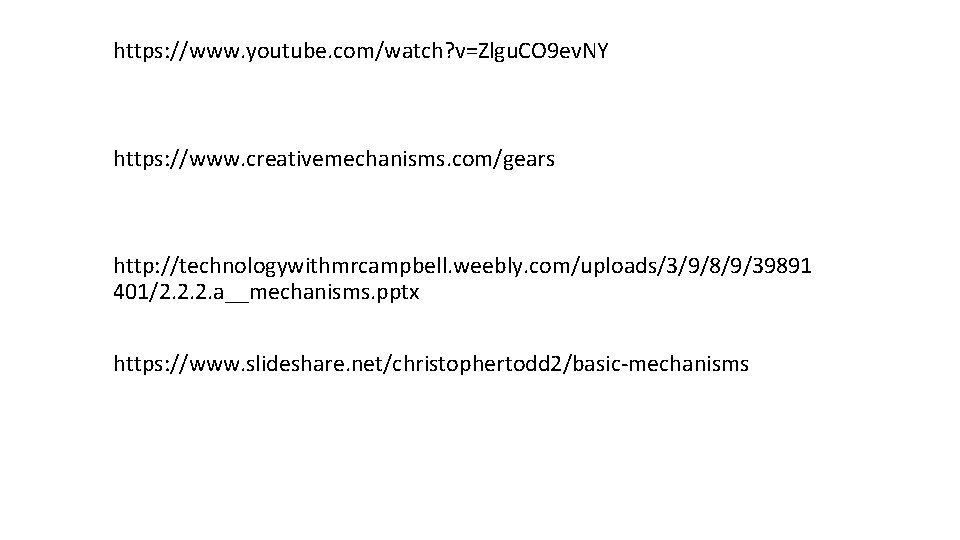
- Slides: 25
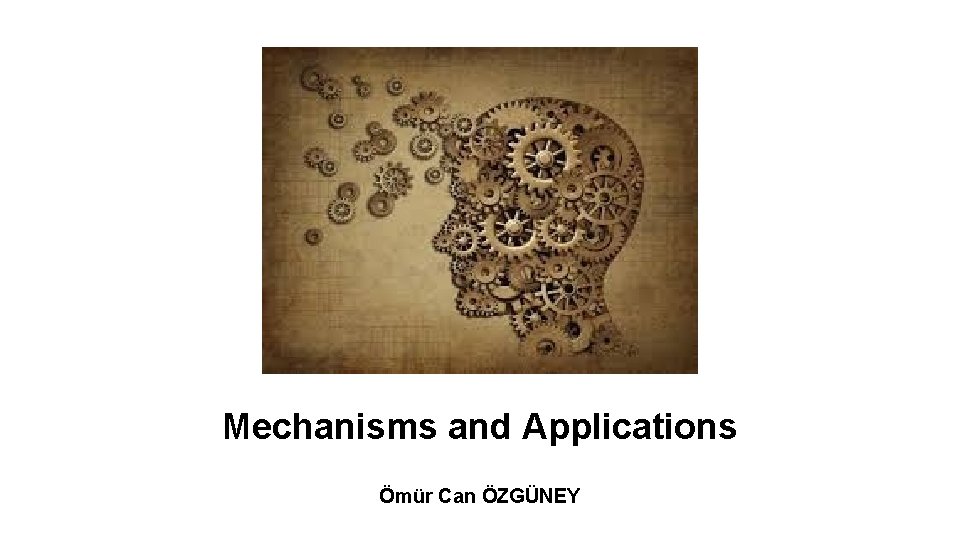
Mechanisms and Applications Ömür Can ÖZGÜNEY
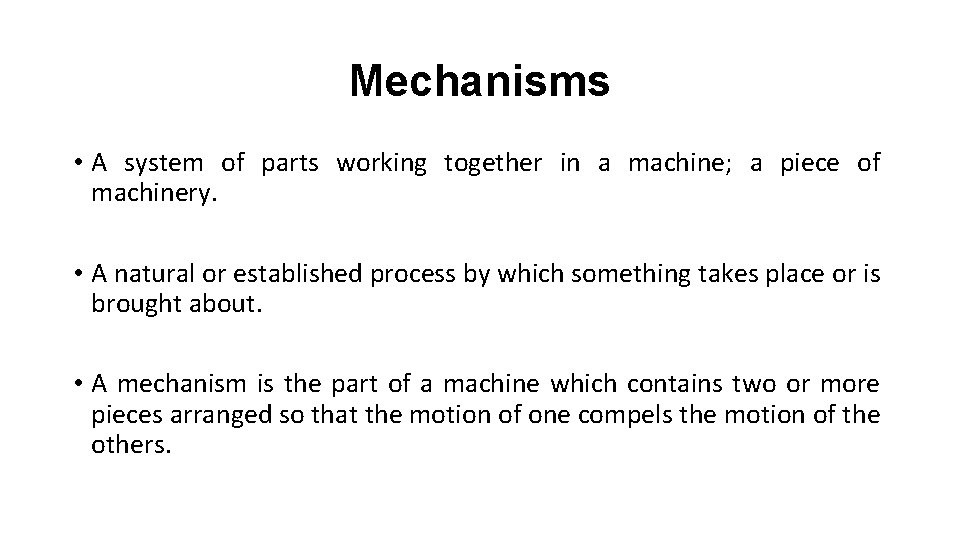
Mechanisms • A system of parts working together in a machine; a piece of machinery. • A natural or established process by which something takes place or is brought about. • A mechanism is the part of a machine which contains two or more pieces arranged so that the motion of one compels the motion of the others.
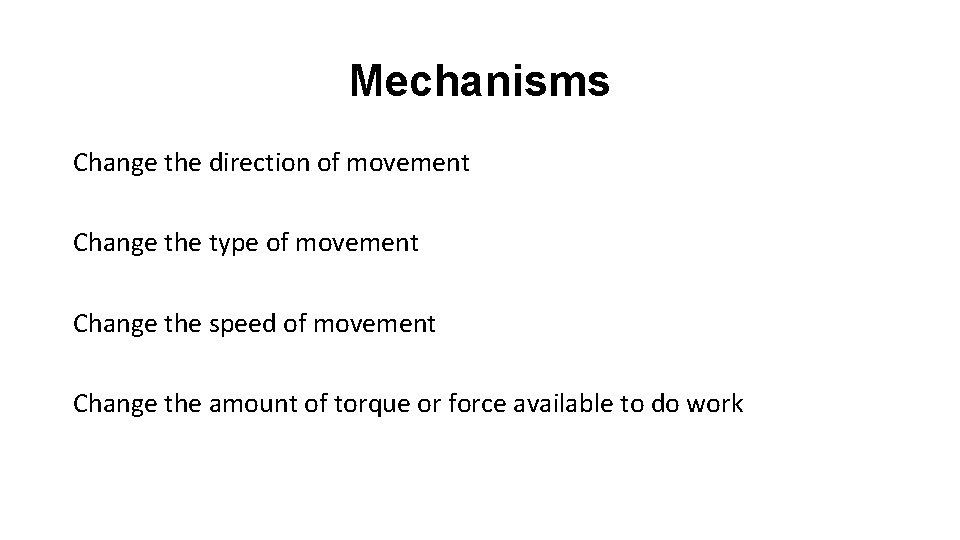
Mechanisms Change the direction of movement Change the type of movement Change the speed of movement Change the amount of torque or force available to do work
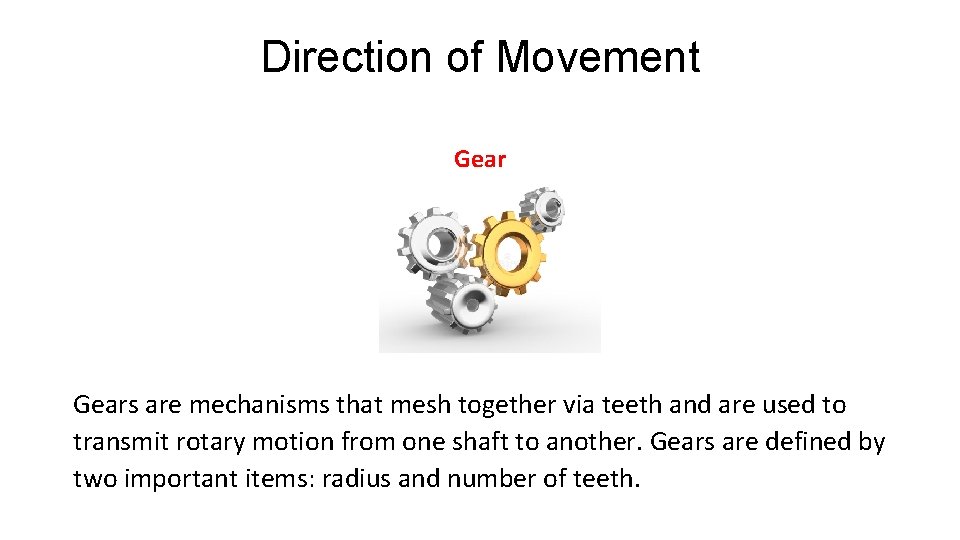
Direction of Movement Gears are mechanisms that mesh together via teeth and are used to transmit rotary motion from one shaft to another. Gears are defined by two important items: radius and number of teeth.
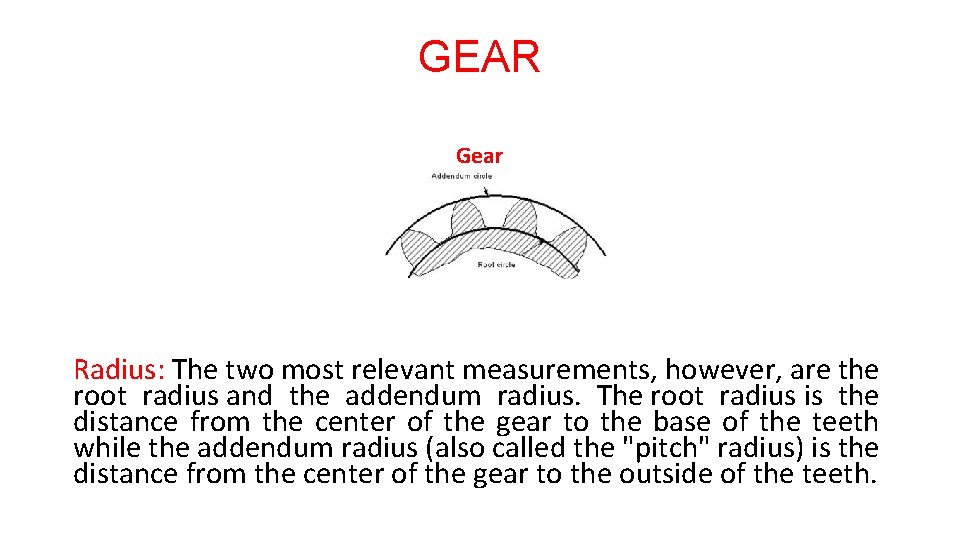
GEAR Gear Radius: The two most relevant measurements, however, are the root radius and the addendum radius. The root radius is the distance from the center of the gear to the base of the teeth while the addendum radius (also called the "pitch" radius) is the distance from the center of the gear to the outside of the teeth.
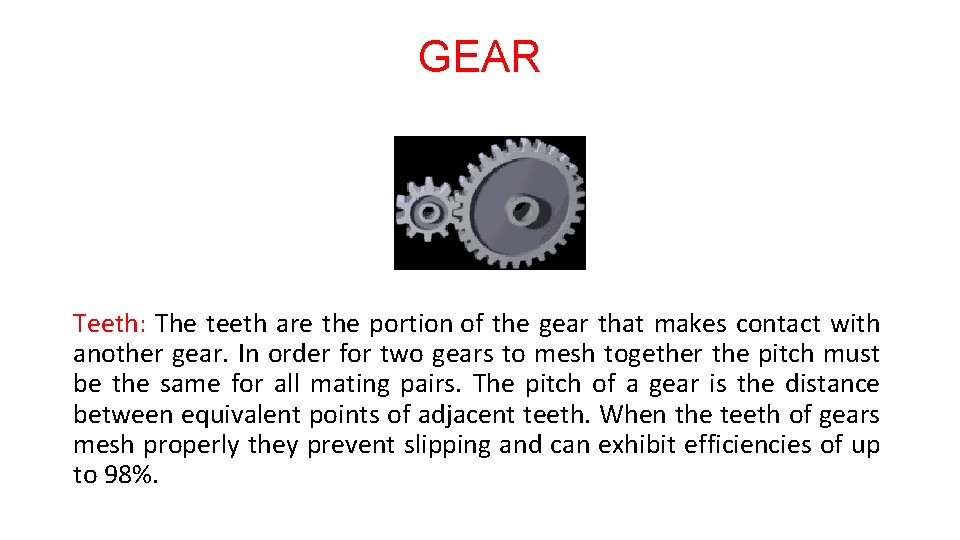
GEAR Teeth: The teeth are the portion of the gear that makes contact with another gear. In order for two gears to mesh together the pitch must be the same for all mating pairs. The pitch of a gear is the distance between equivalent points of adjacent teeth. When the teeth of gears mesh properly they prevent slipping and can exhibit efficiencies of up to 98%.
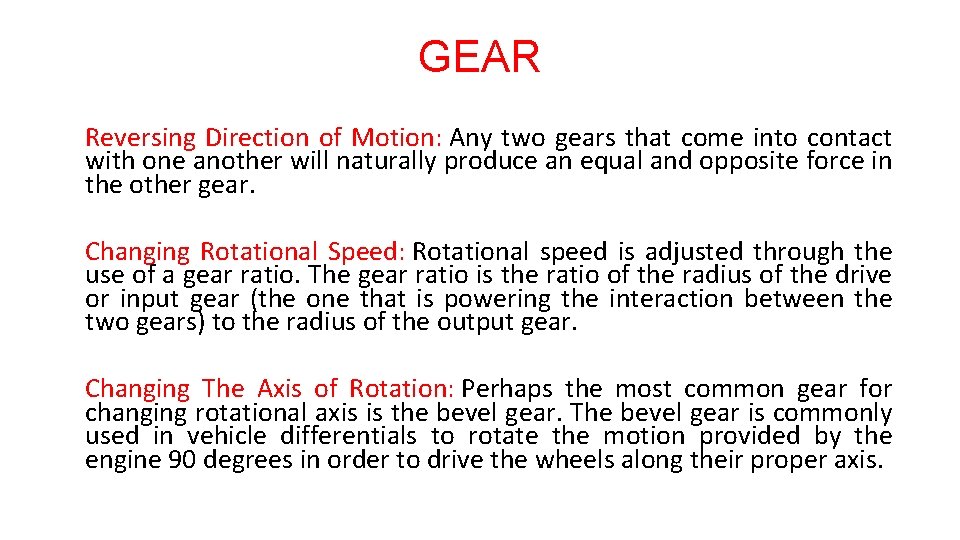
GEAR Reversing Direction of Motion: Any two gears that come into contact with one another will naturally produce an equal and opposite force in the other gear. Changing Rotational Speed: Rotational speed is adjusted through the use of a gear ratio. The gear ratio is the ratio of the radius of the drive or input gear (the one that is powering the interaction between the two gears) to the radius of the output gear. Changing The Axis of Rotation: Perhaps the most common gear for changing rotational axis is the bevel gear. The bevel gear is commonly used in vehicle differentials to rotate the motion provided by the engine 90 degrees in order to drive the wheels along their proper axis.
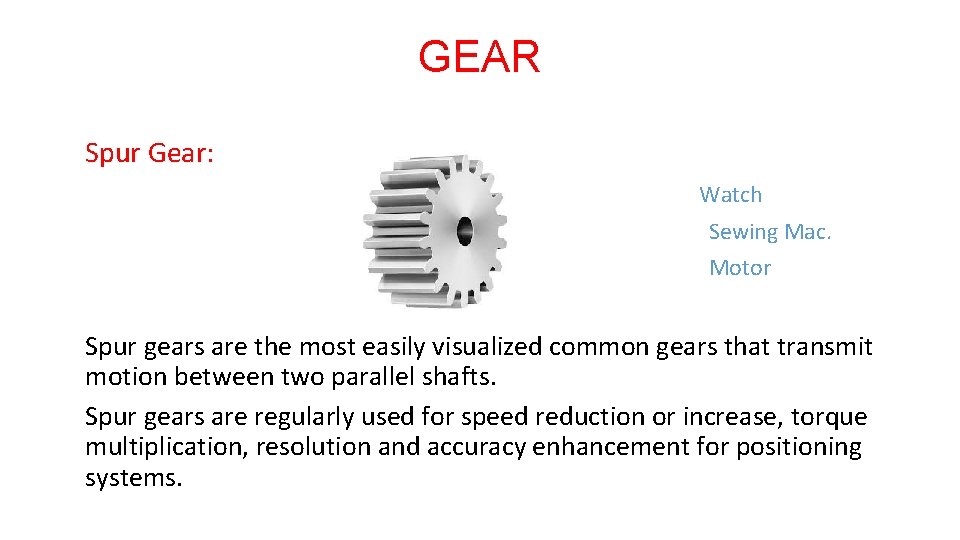
GEAR Spur Gear: Watch Sewing Mac. Motor Spur gears are the most easily visualized common gears that transmit motion between two parallel shafts. Spur gears are regularly used for speed reduction or increase, torque multiplication, resolution and accuracy enhancement for positioning systems.
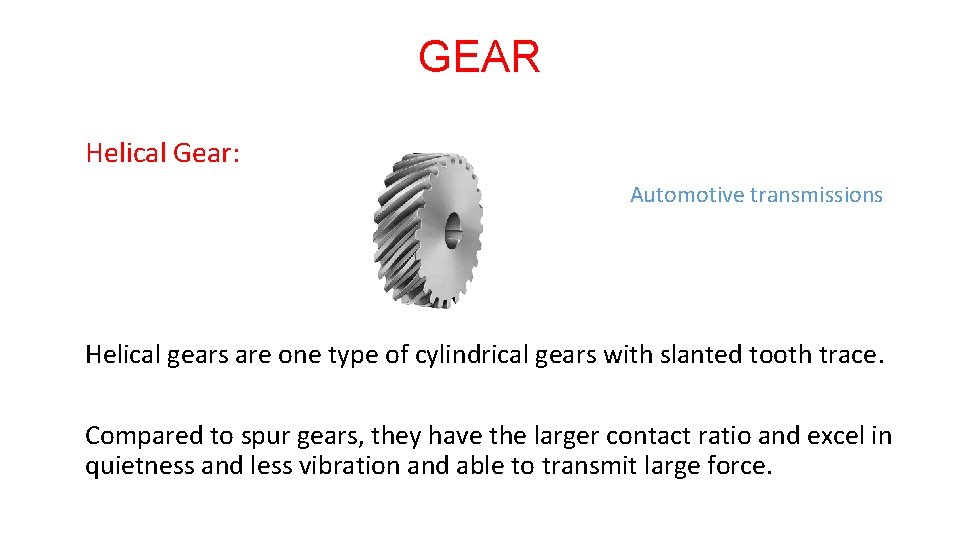
GEAR Helical Gear: Automotive transmissions Helical gears are one type of cylindrical gears with slanted tooth trace. Compared to spur gears, they have the larger contact ratio and excel in quietness and less vibration and able to transmit large force.
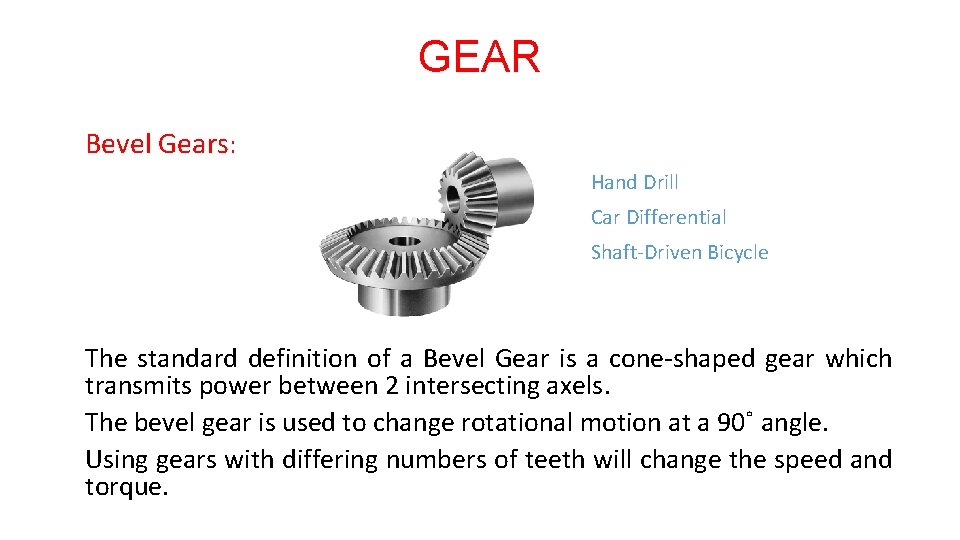
GEAR Bevel Gears: Hand Drill Car Differential Shaft-Driven Bicycle The standard definition of a Bevel Gear is a cone-shaped gear which transmits power between 2 intersecting axels. The bevel gear is used to change rotational motion at a 90˚ angle. Using gears with differing numbers of teeth will change the speed and torque.
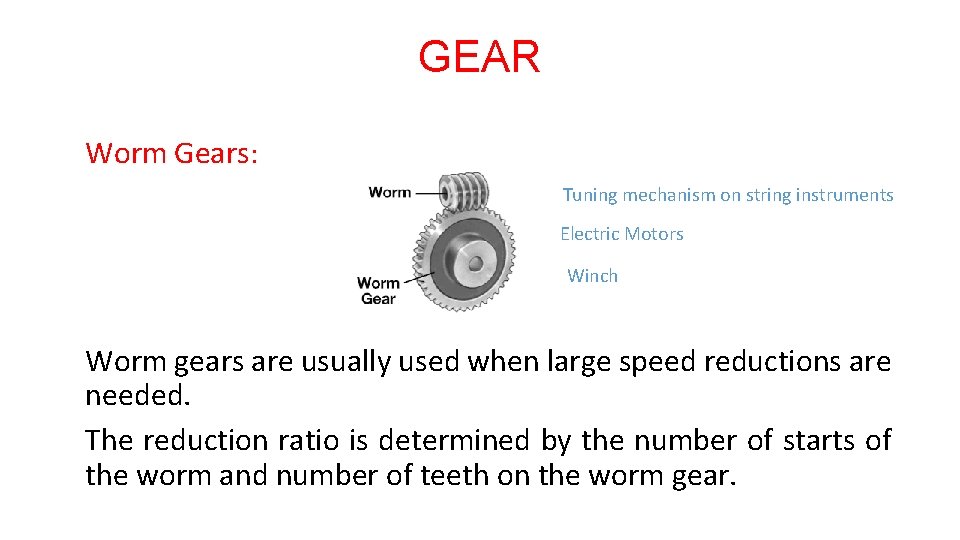
GEAR Worm Gears: Tuning mechanism on string instruments Electric Motors Winch Worm gears are usually used when large speed reductions are needed. The reduction ratio is determined by the number of starts of the worm and number of teeth on the worm gear.
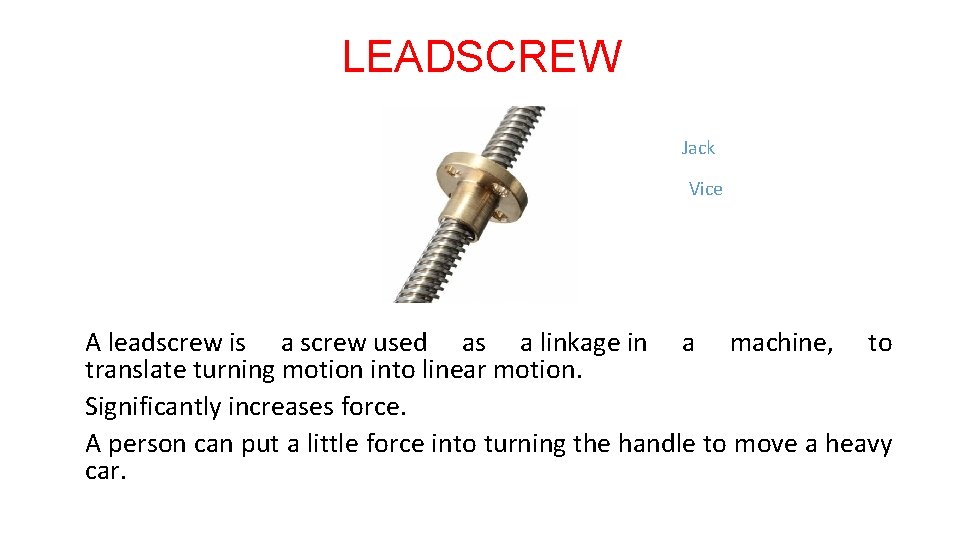
LEADSCREW Jack Vice A leadscrew is a screw used as a linkage in a machine, to translate turning motion into linear motion. Significantly increases force. A person can put a little force into turning the handle to move a heavy car.
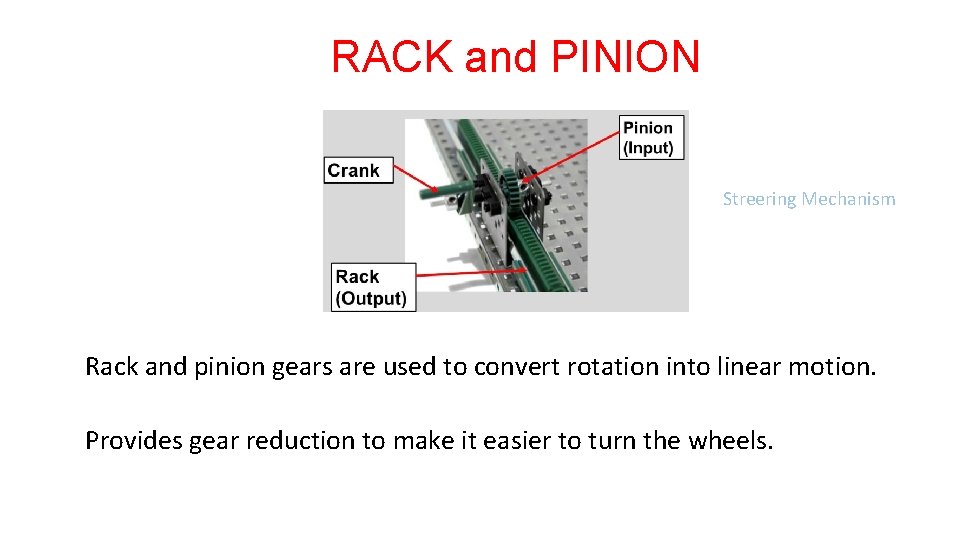
RACK and PINION Streering Mechanism Rack and pinion gears are used to convert rotation into linear motion. Provides gear reduction to make it easier to turn the wheels.
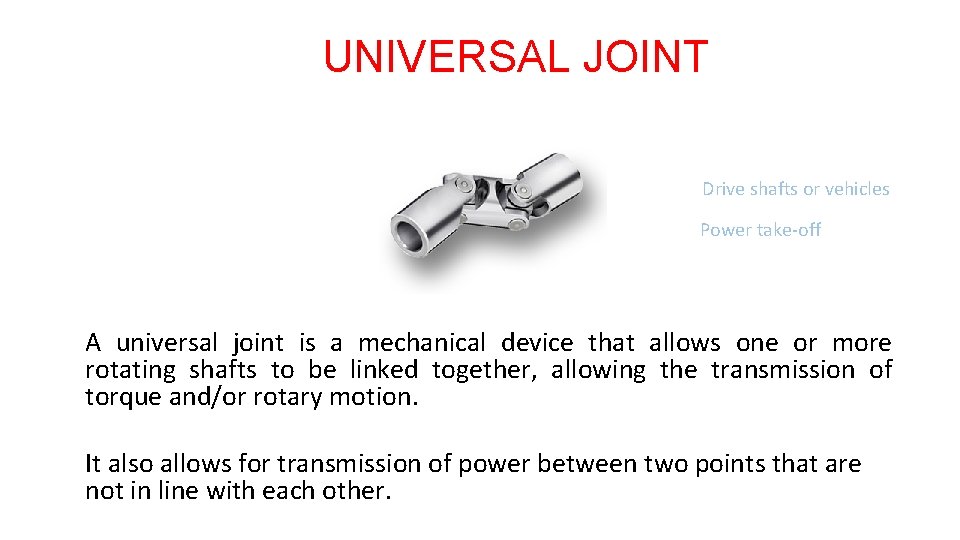
UNIVERSAL JOINT Drive shafts or vehicles Power take-off A universal joint is a mechanical device that allows one or more rotating shafts to be linked together, allowing the transmission of torque and/or rotary motion. It also allows for transmission of power between two points that are not in line with each other.
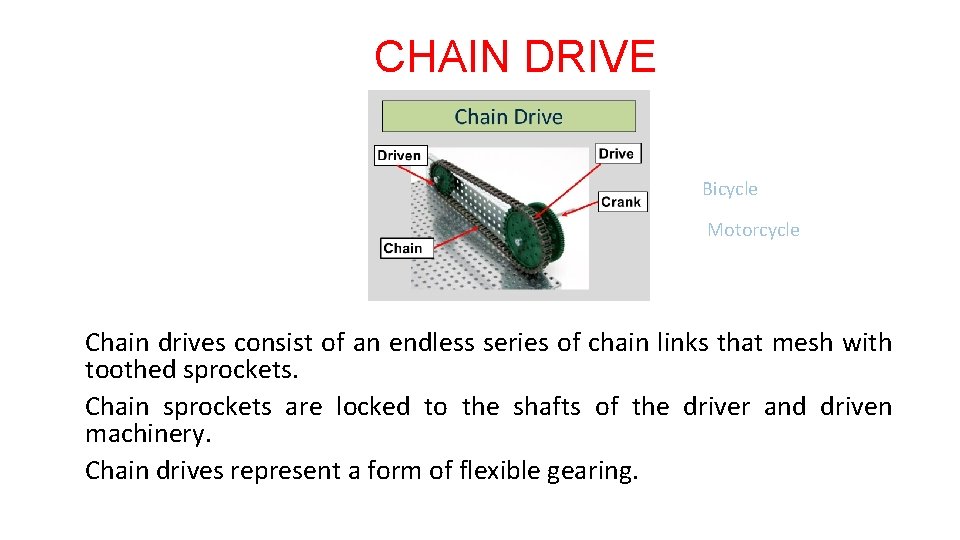
CHAIN DRIVE Bicycle Motorcycle Chain drives consist of an endless series of chain links that mesh with toothed sprockets. Chain sprockets are locked to the shafts of the driver and driven machinery. Chain drives represent a form of flexible gearing.
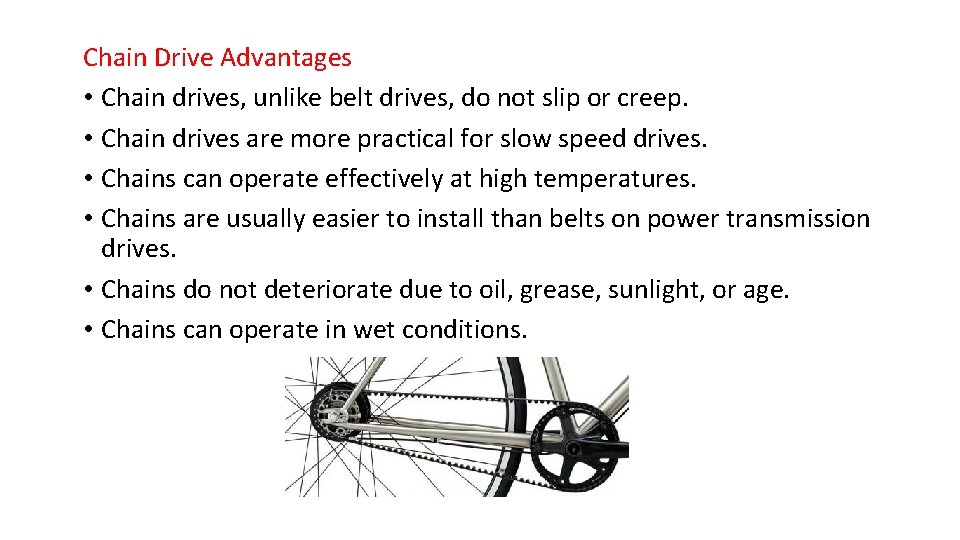
Chain Drive Advantages • Chain drives, unlike belt drives, do not slip or creep. • Chain drives are more practical for slow speed drives. • Chains can operate effectively at high temperatures. • Chains are usually easier to install than belts on power transmission drives. • Chains do not deteriorate due to oil, grease, sunlight, or age. • Chains can operate in wet conditions.
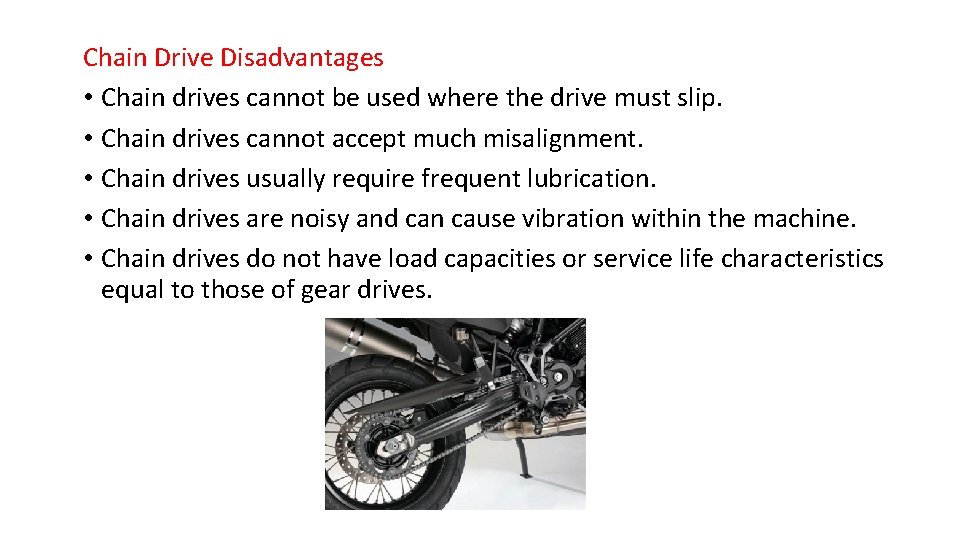
Chain Drive Disadvantages • Chain drives cannot be used where the drive must slip. • Chain drives cannot accept much misalignment. • Chain drives usually require frequent lubrication. • Chain drives are noisy and can cause vibration within the machine. • Chain drives do not have load capacities or service life characteristics equal to those of gear drives.

BELT DRIVE Lawn Mower Car Engine A belt is a looped strip of flexible material used to mechanically link two or more rotating shafts. A belt drive offers smooth transmission of power between shafts at a considerable distance. Belt drives are used as the source of motion to transfer to efficiently transmit power or to track relative movement.
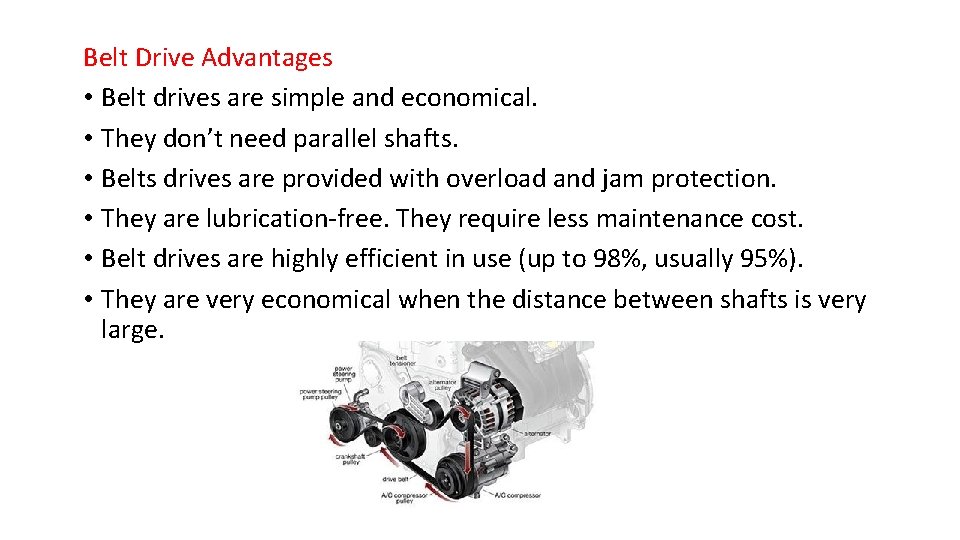
Belt Drive Advantages • Belt drives are simple and economical. • They don’t need parallel shafts. • Belts drives are provided with overload and jam protection. • They are lubrication-free. They require less maintenance cost. • Belt drives are highly efficient in use (up to 98%, usually 95%). • They are very economical when the distance between shafts is very large.
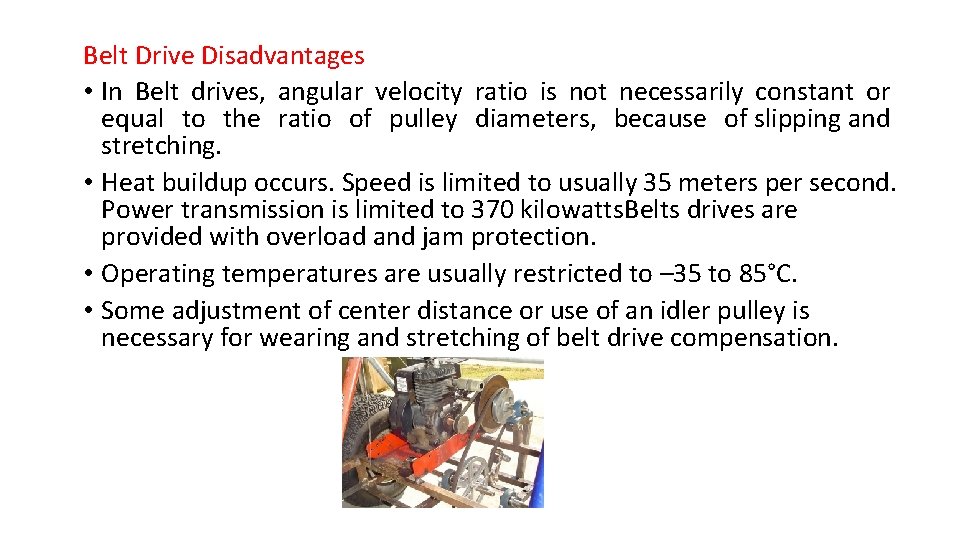
Belt Drive Disadvantages • In Belt drives, angular velocity ratio is not necessarily constant or equal to the ratio of pulley diameters, because of slipping and stretching. • Heat buildup occurs. Speed is limited to usually 35 meters per second. Power transmission is limited to 370 kilowatts. Belts drives are provided with overload and jam protection. • Operating temperatures are usually restricted to – 35 to 85°C. • Some adjustment of center distance or use of an idler pulley is necessary for wearing and stretching of belt drive compensation.
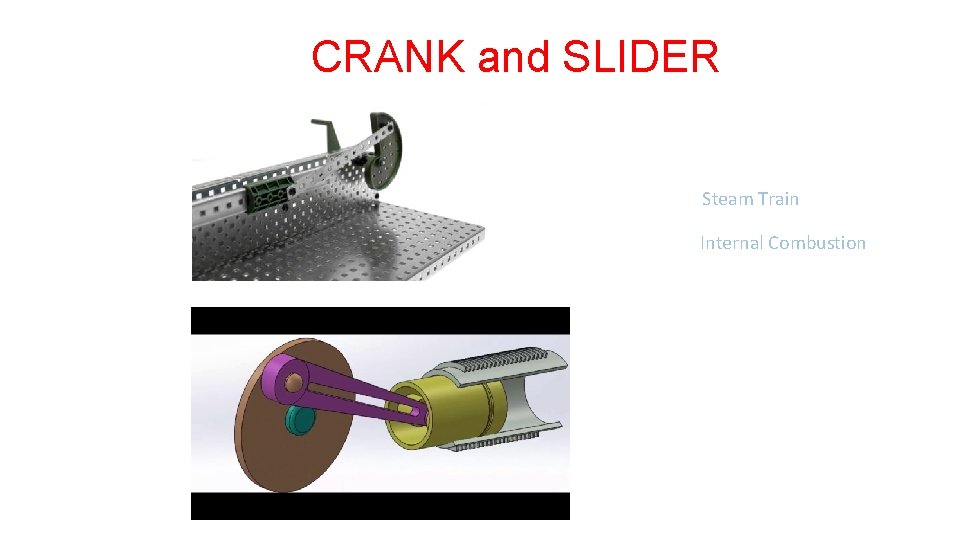
CRANK and SLIDER Steam Train Internal Combustion
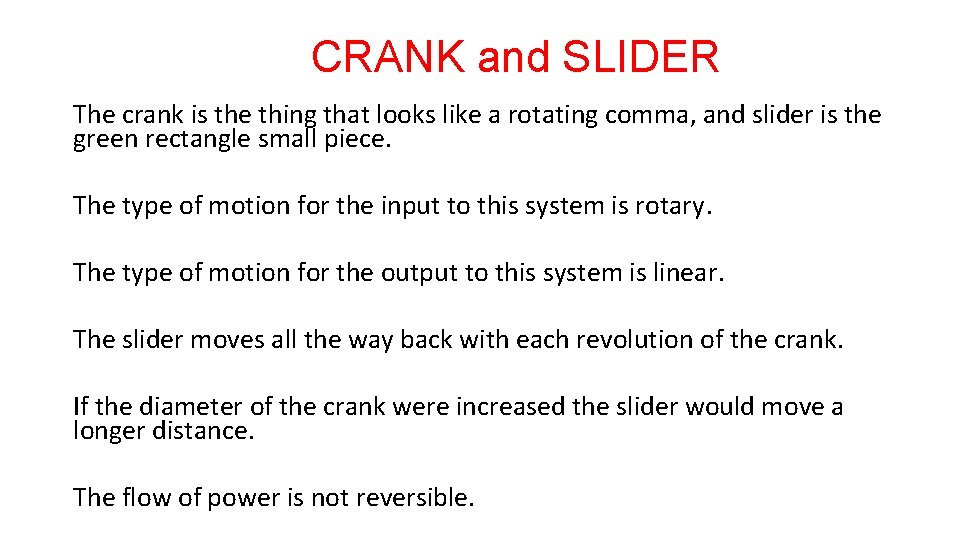
CRANK and SLIDER The crank is the thing that looks like a rotating comma, and slider is the green rectangle small piece. The type of motion for the input to this system is rotary. The type of motion for the output to this system is linear. The slider moves all the way back with each revolution of the crank. If the diameter of the crank were increased the slider would move a longer distance. The flow of power is not reversible.
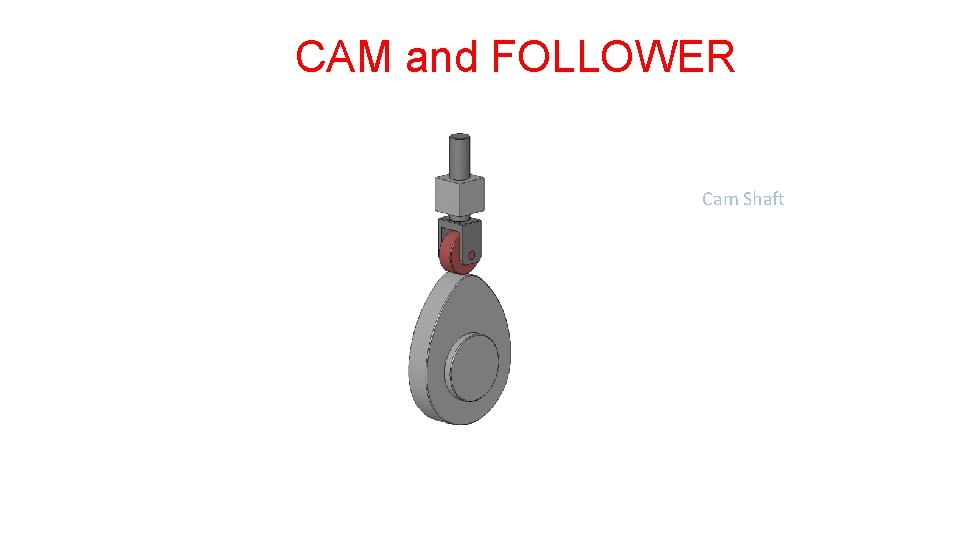
CAM and FOLLOWER Cam Shaft
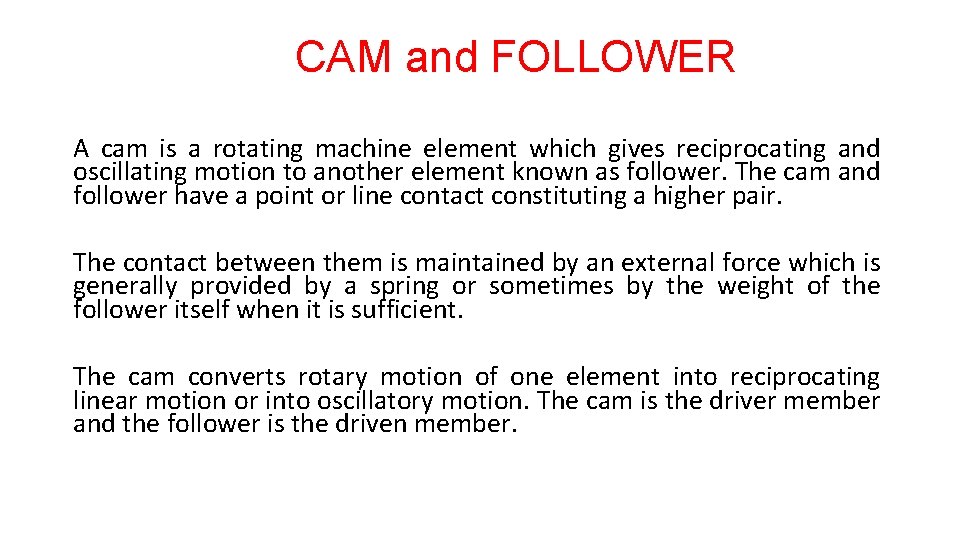
CAM and FOLLOWER A cam is a rotating machine element which gives reciprocating and oscillating motion to another element known as follower. The cam and follower have a point or line contact constituting a higher pair. The contact between them is maintained by an external force which is generally provided by a spring or sometimes by the weight of the follower itself when it is sufficient. The cam converts rotary motion of one element into reciprocating linear motion or into oscillatory motion. The cam is the driver member and the follower is the driven member.
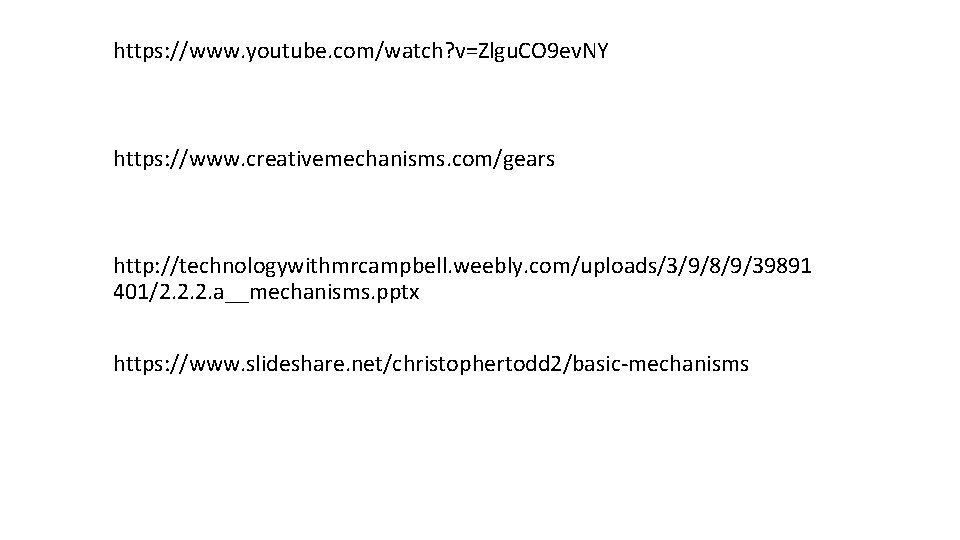
https: //www. youtube. com/watch? v=Zlgu. CO 9 ev. NY https: //www. creativemechanisms. com/gears http: //technologywithmrcampbell. weebly. com/uploads/3/9/8/9/39891 401/2. 2. 2. a__mechanisms. pptx https: //www. slideshare. net/christophertodd 2/basic-mechanisms
Look at the pictures and complete with can or can't
Virtualization ppt
Structures and mechanisms
Optical disk
Basic mechanisms underlying seizures and epilepsy
Sensory and motor mechanisms
Security services in cryptography
Internal service delivery mechanisms
Security attacks services and mechanisms
Managing weight and eating behaviors
National mechanism for reporting and follow-up
Heat transfer
Fuzzy sets and fuzzy logic theory and applications
If you can imagine it you can achieve it
You can tell harris about it just ____(easily) as i can.
If you think you can you can poem
If you can't measure it it does not exist
If you can't measure it, you can't manage it
Can can body percussion
The arrangement of the element of curriculum is
You can tell harris about it just ____(easily) as i can.
Positive degree examples
You can speak english
Cool bear hunt
I know nothing is impossible
If you cant measure it you can't manage it