ME 612 Metal Forming and Theory of Plasticity
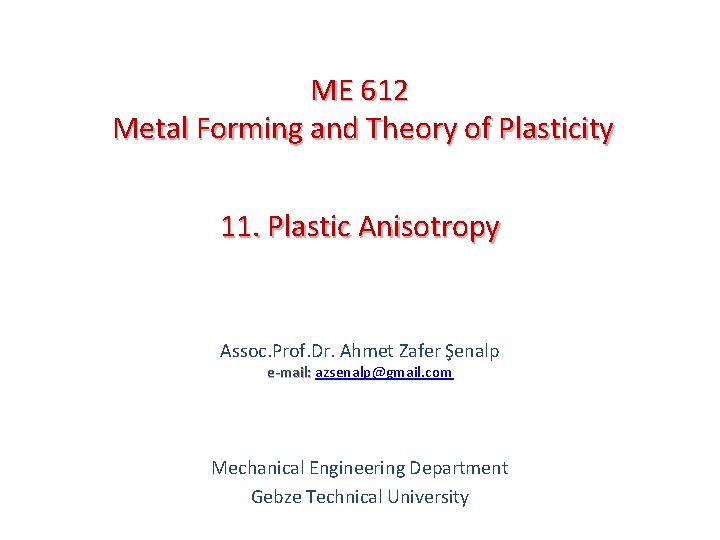
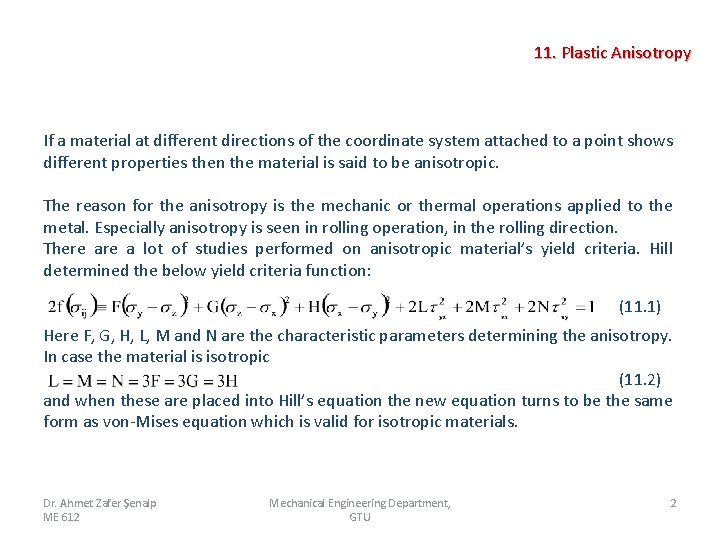
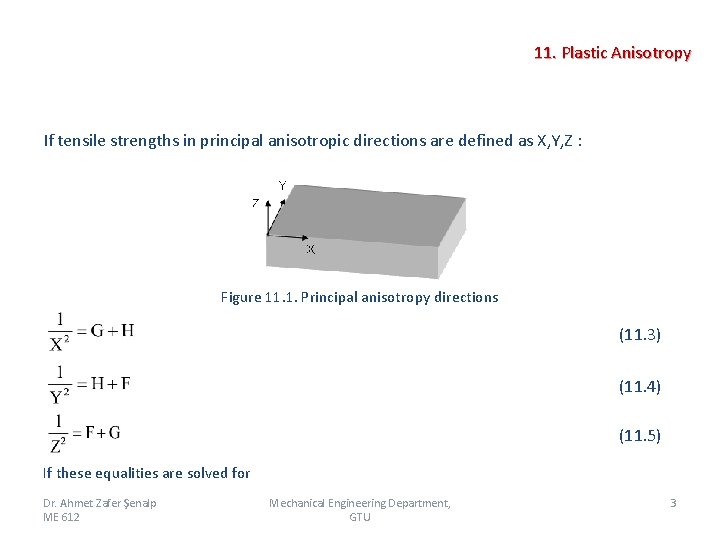
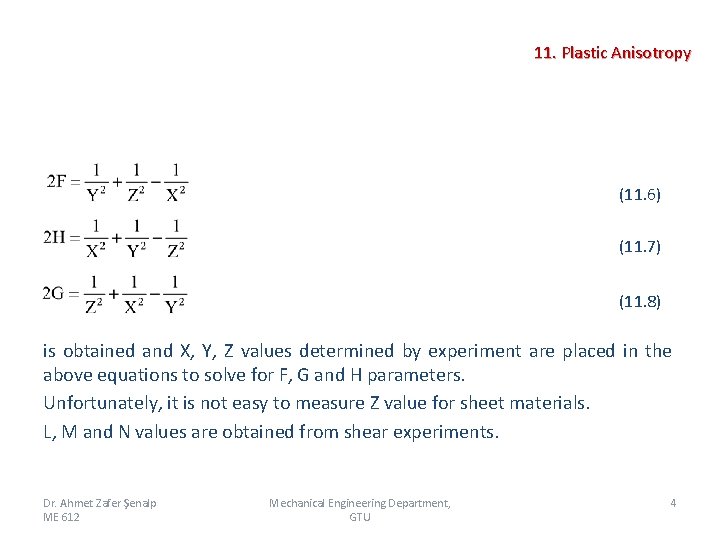
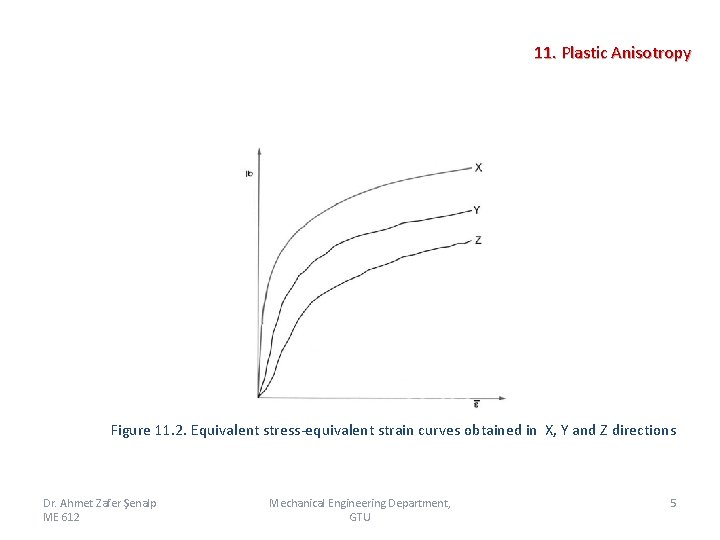
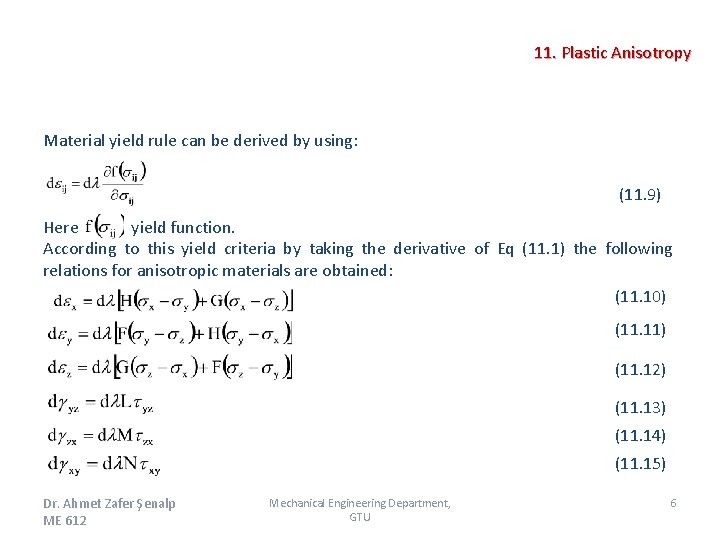
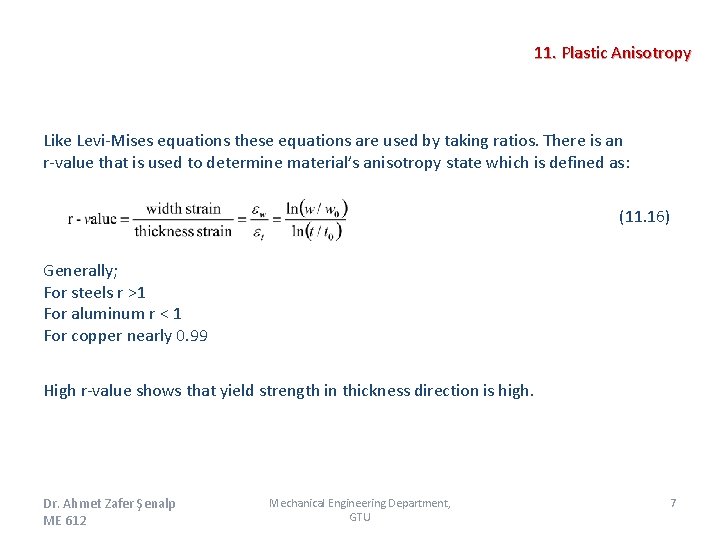
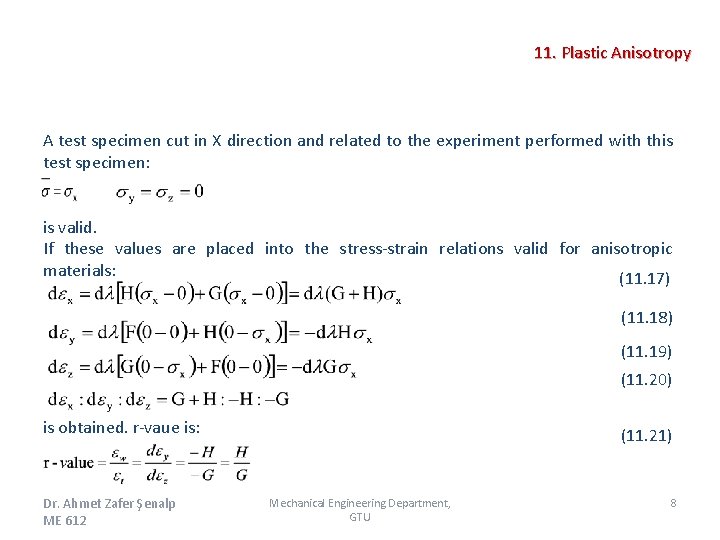
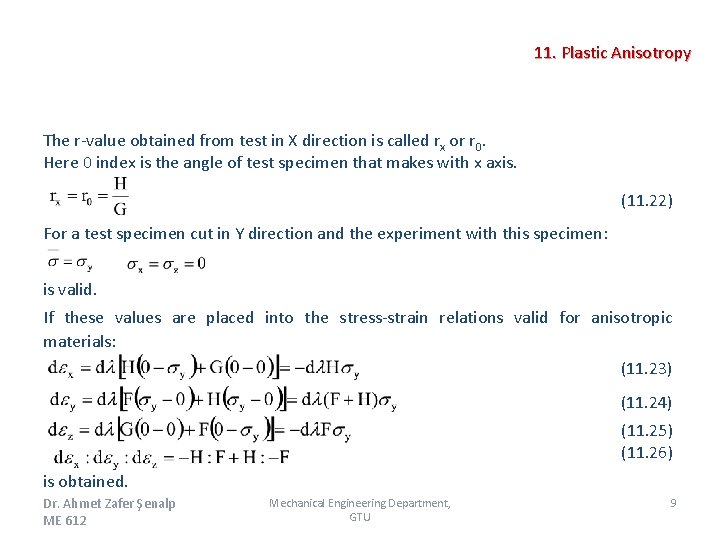
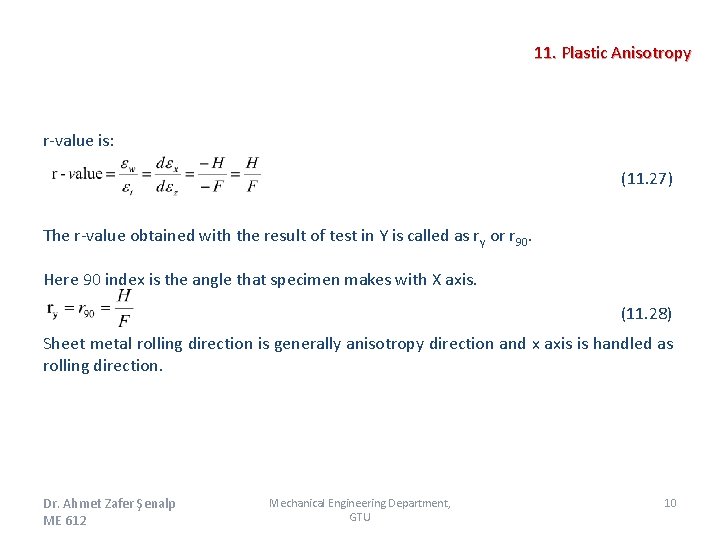
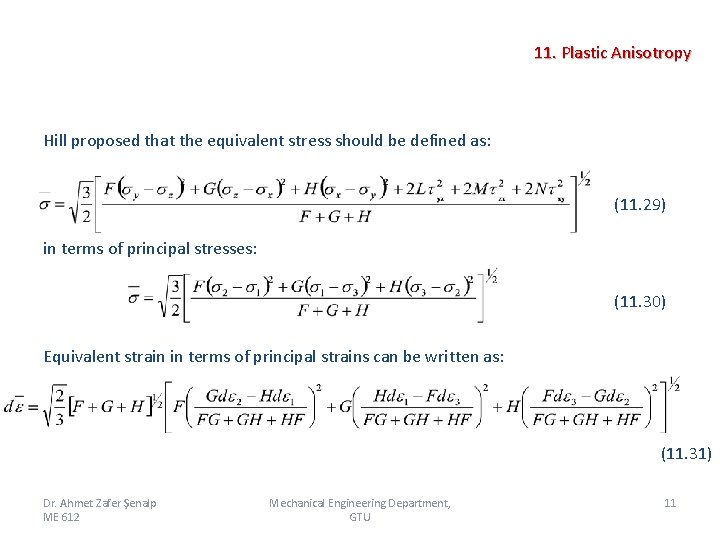
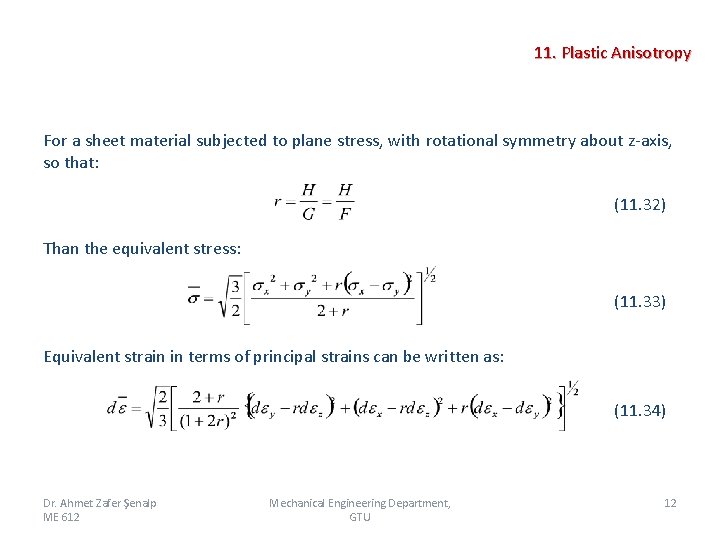
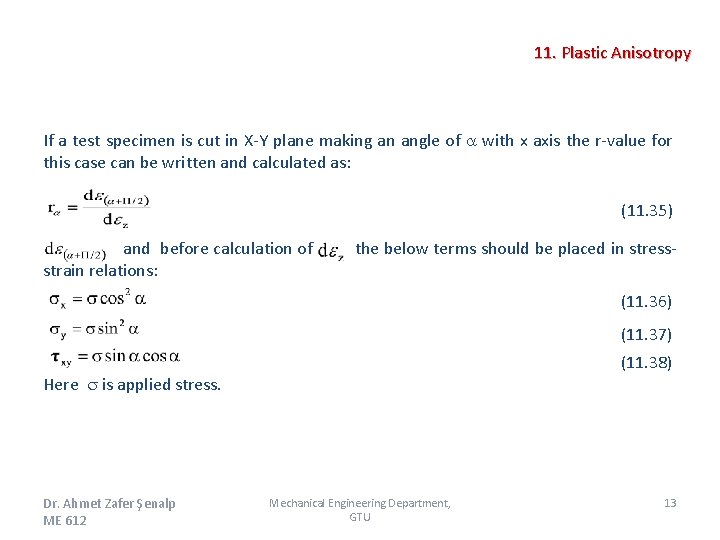
- Slides: 13
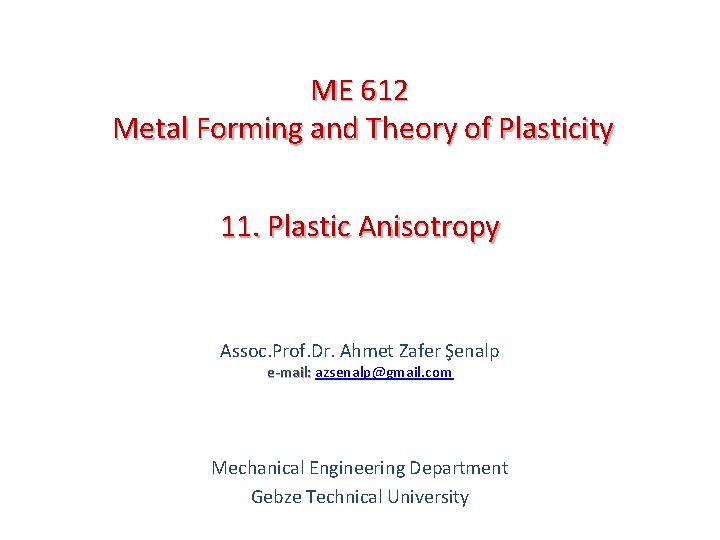
ME 612 Metal Forming and Theory of Plasticity 11. Plastic Anisotropy Assoc. Prof. Dr. Ahmet Zafer Şenalp e-mail: azsenalp@gmail. com Mechanical Engineering Department Gebze Technical University
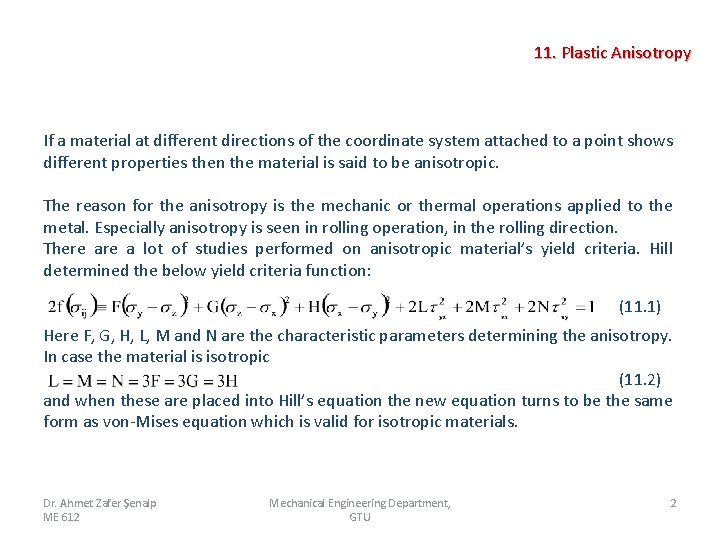
11. Plastic Anisotropy If a material at different directions of the coordinate system attached to a point shows different properties then the material is said to be anisotropic. The reason for the anisotropy is the mechanic or thermal operations applied to the metal. Especially anisotropy is seen in rolling operation, in the rolling direction. There a lot of studies performed on anisotropic material’s yield criteria. Hill determined the below yield criteria function: (11. 1) Here F, G, H, L, M and N are the characteristic parameters determining the anisotropy. In case the material is isotropic (11. 2) and when these are placed into Hill’s equation the new equation turns to be the same form as von-Mises equation which is valid for isotropic materials. Dr. Ahmet Zafer Şenalp ME 612 Mechanical Engineering Department, GTU 2
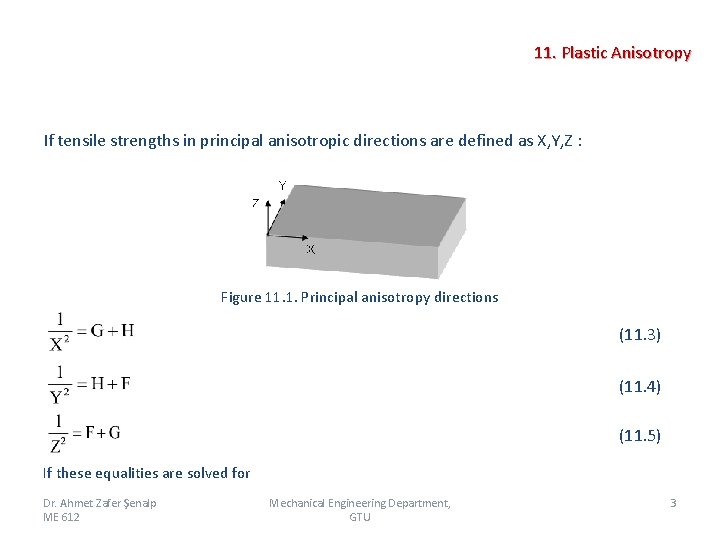
11. Plastic Anisotropy If tensile strengths in principal anisotropic directions are defined as X, Y, Z : Figure 11. 1. Principal anisotropy directions (11. 3) (11. 4) (11. 5) If these equalities are solved for Dr. Ahmet Zafer Şenalp ME 612 Mechanical Engineering Department, GTU 3
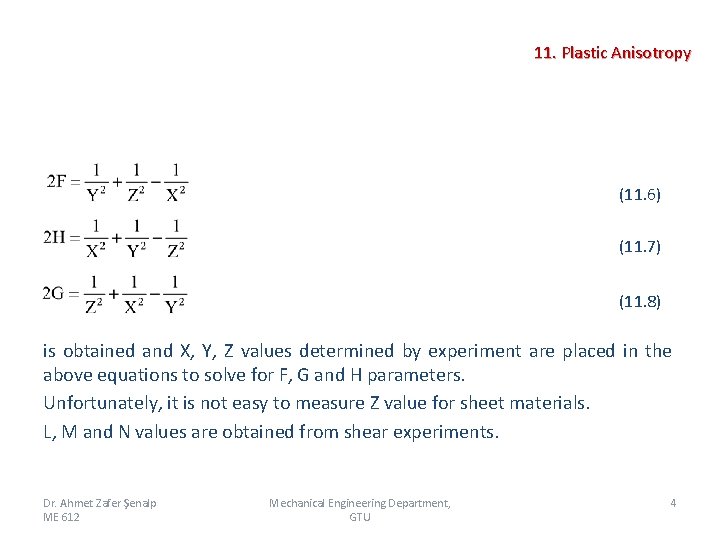
11. Plastic Anisotropy (11. 6) (11. 7) (11. 8) is obtained and X, Y, Z values determined by experiment are placed in the above equations to solve for F, G and H parameters. Unfortunately, it is not easy to measure Z value for sheet materials. L, M and N values are obtained from shear experiments. Dr. Ahmet Zafer Şenalp ME 612 Mechanical Engineering Department, GTU 4
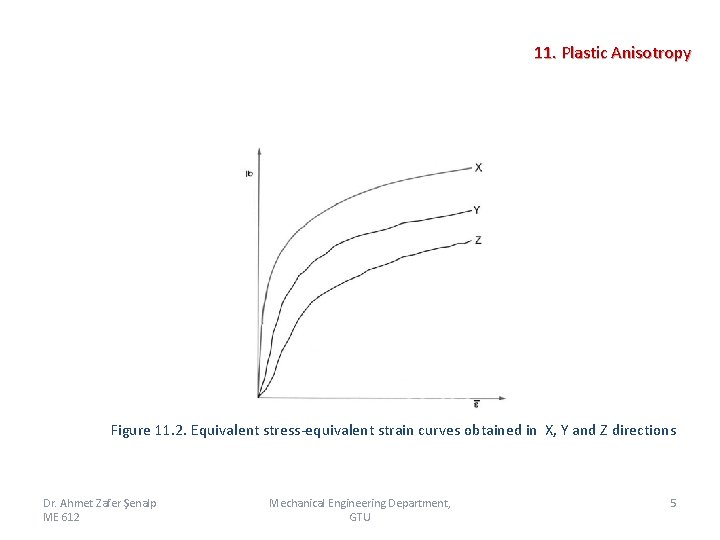
11. Plastic Anisotropy Figure 11. 2. Equivalent stress-equivalent strain curves obtained in X, Y and Z directions Dr. Ahmet Zafer Şenalp ME 612 Mechanical Engineering Department, GTU 5
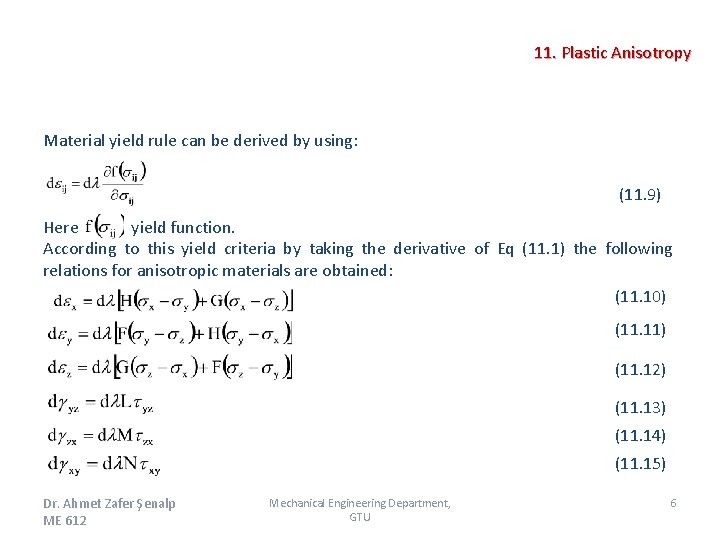
11. Plastic Anisotropy Material yield rule can be derived by using: (11. 9) Here yield function. According to this yield criteria by taking the derivative of Eq (11. 1) the following relations for anisotropic materials are obtained: (11. 10) (11. 11) (11. 12) (11. 13) (11. 14) (11. 15) Dr. Ahmet Zafer Şenalp ME 612 Mechanical Engineering Department, GTU 6
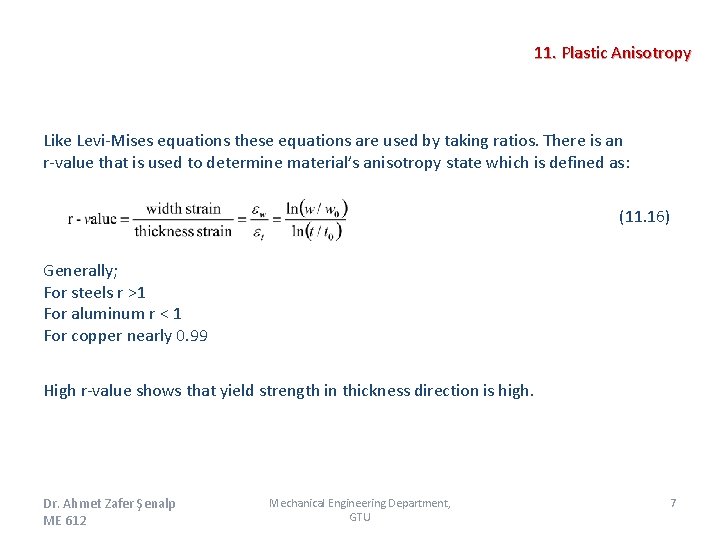
11. Plastic Anisotropy Like Levi-Mises equations these equations are used by taking ratios. There is an r-value that is used to determine material’s anisotropy state which is defined as: (11. 16) Generally; For steels r >1 For aluminum r < 1 For copper nearly 0. 99 High r-value shows that yield strength in thickness direction is high. Dr. Ahmet Zafer Şenalp ME 612 Mechanical Engineering Department, GTU 7
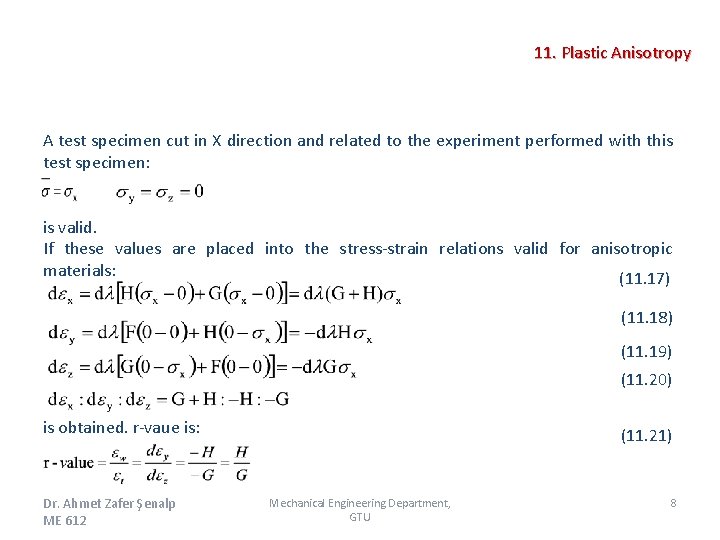
11. Plastic Anisotropy A test specimen cut in X direction and related to the experiment performed with this test specimen: is valid. If these values are placed into the stress-strain relations valid for anisotropic materials: (11. 17) (11. 18) (11. 19) (11. 20) is obtained. r-vaue is: Dr. Ahmet Zafer Şenalp ME 612 (11. 21) Mechanical Engineering Department, GTU 8
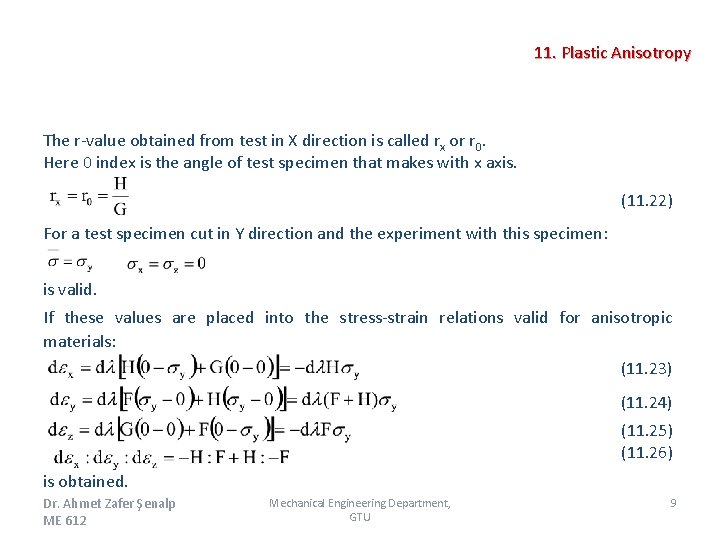
11. Plastic Anisotropy The r-value obtained from test in X direction is called rx or r 0. Here 0 index is the angle of test specimen that makes with x axis. (11. 22) For a test specimen cut in Y direction and the experiment with this specimen: is valid. If these values are placed into the stress-strain relations valid for anisotropic materials: (11. 23) (11. 24) (11. 25) (11. 26) is obtained. Dr. Ahmet Zafer Şenalp ME 612 Mechanical Engineering Department, GTU 9
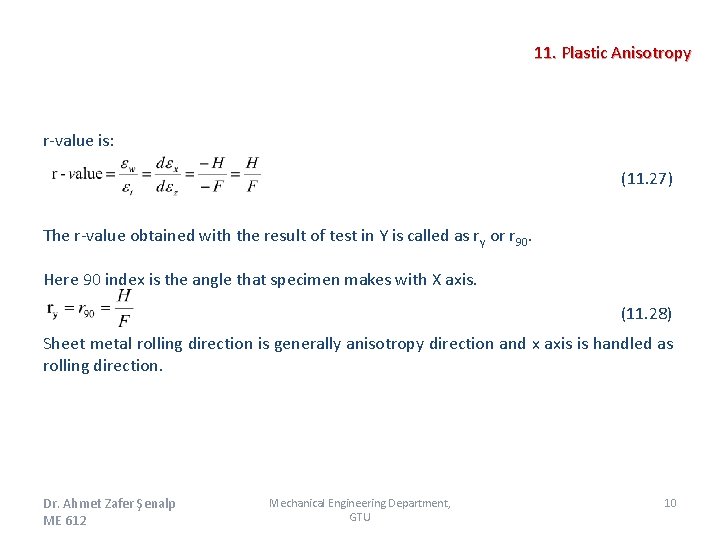
11. Plastic Anisotropy r-value is: (11. 27) The r-value obtained with the result of test in Y is called as ry or r 90. Here 90 index is the angle that specimen makes with X axis. (11. 28) Sheet metal rolling direction is generally anisotropy direction and x axis is handled as rolling direction. Dr. Ahmet Zafer Şenalp ME 612 Mechanical Engineering Department, GTU 10
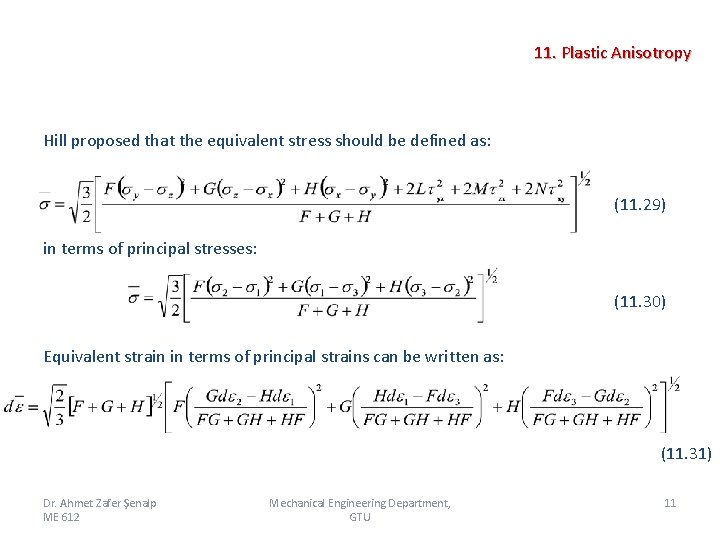
11. Plastic Anisotropy Hill proposed that the equivalent stress should be defined as: (11. 29) in terms of principal stresses: (11. 30) Equivalent strain in terms of principal strains can be written as: (11. 31) Dr. Ahmet Zafer Şenalp ME 612 Mechanical Engineering Department, GTU 11
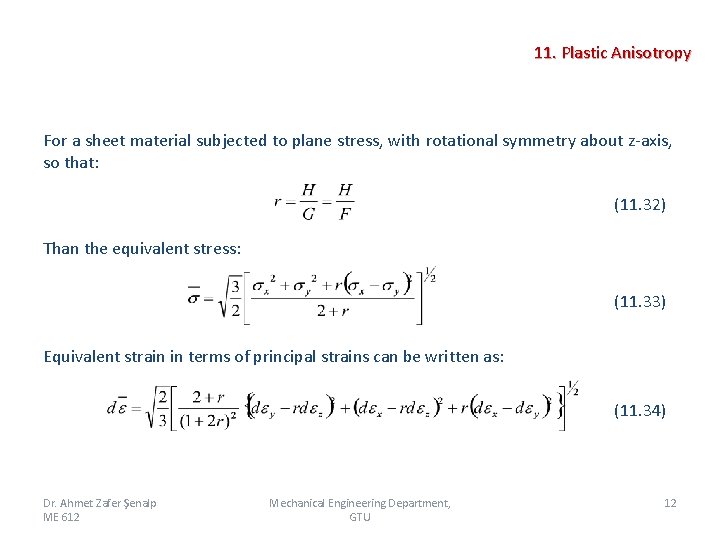
11. Plastic Anisotropy For a sheet material subjected to plane stress, with rotational symmetry about z-axis, so that: (11. 32) Than the equivalent stress: (11. 33) Equivalent strain in terms of principal strains can be written as: (11. 34) Dr. Ahmet Zafer Şenalp ME 612 Mechanical Engineering Department, GTU 12
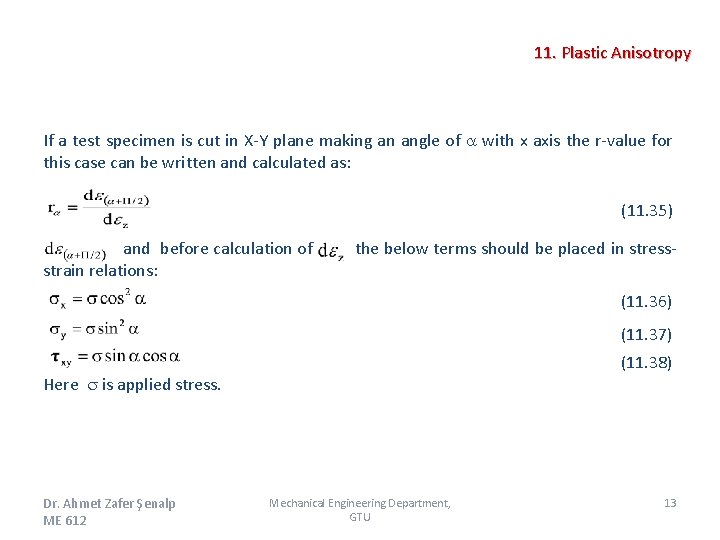
11. Plastic Anisotropy If a test specimen is cut in X-Y plane making an angle of a with x axis the r-value for this case can be written and calculated as: (11. 35) and before calculation of strain relations: the below terms should be placed in stress(11. 36) (11. 37) (11. 38) Here s is applied stress. Dr. Ahmet Zafer Şenalp ME 612 Mechanical Engineering Department, GTU 13
Metal forming analysis gtu
Sheet metal fundamentals
26-612
Stamp duty(amendment) proclamation no. 612/2008
Who were the babylonians
Solomon's temple location
2017:612
Cs 612
Sheet metal working
Cold working processes
Draw bead
Forming process in sheet metal
Advantages of explosive forming
Mcq on sheet metal forming