Inspection and Testing Peel Test Shown in the
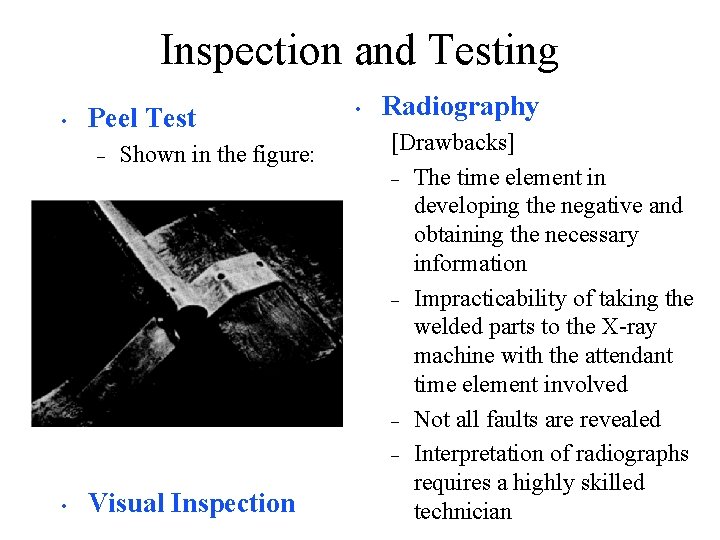
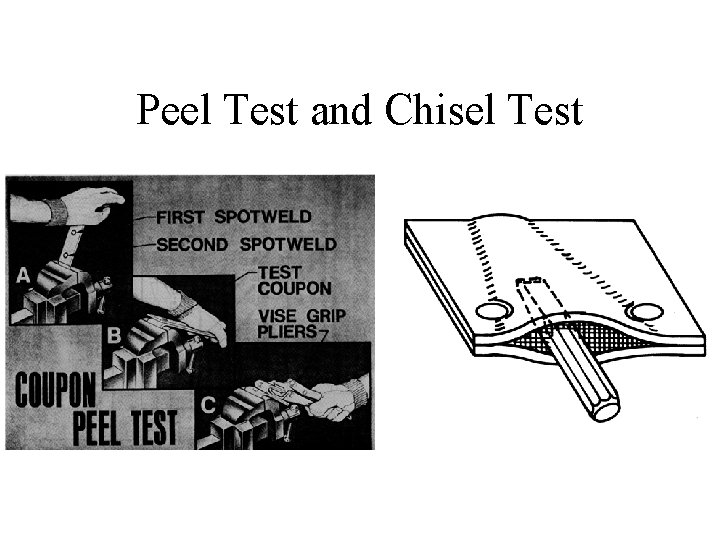
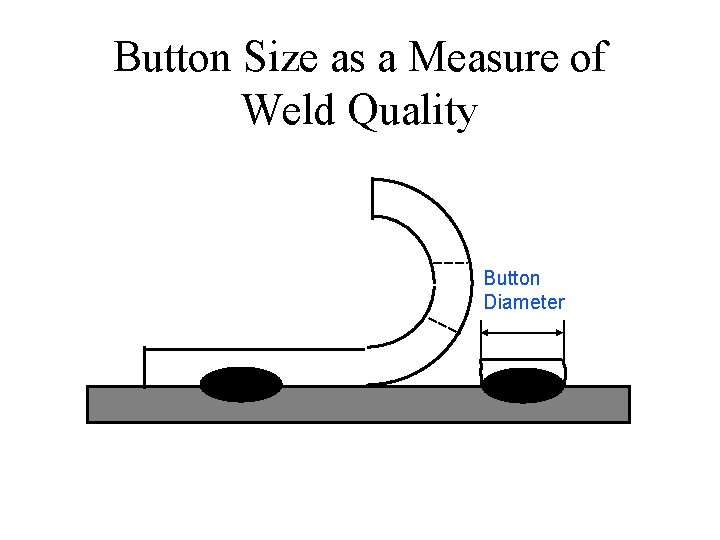
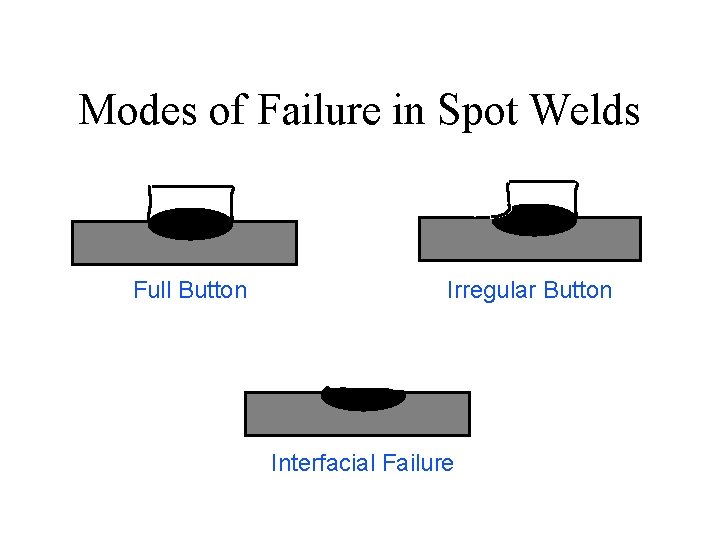
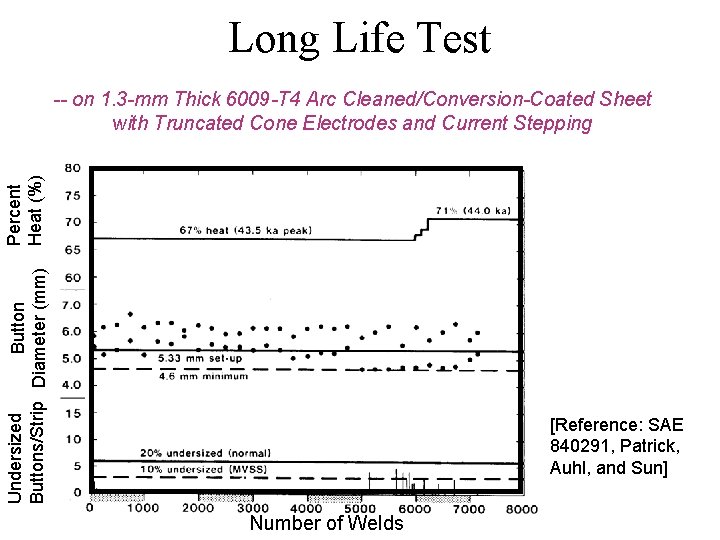
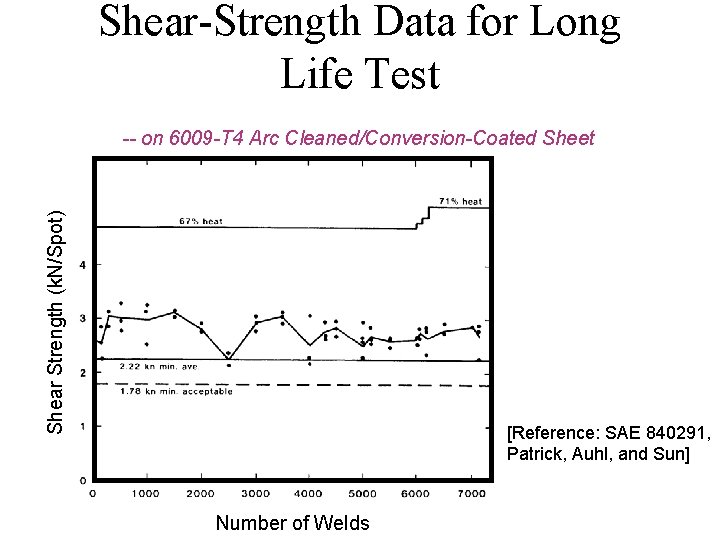
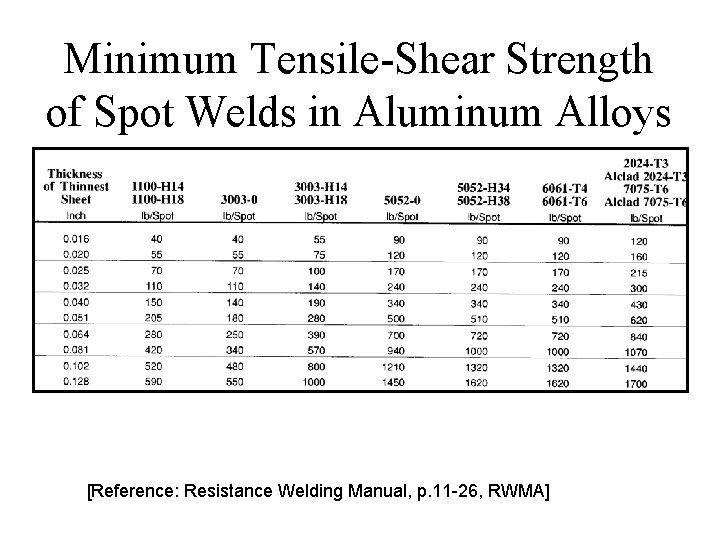
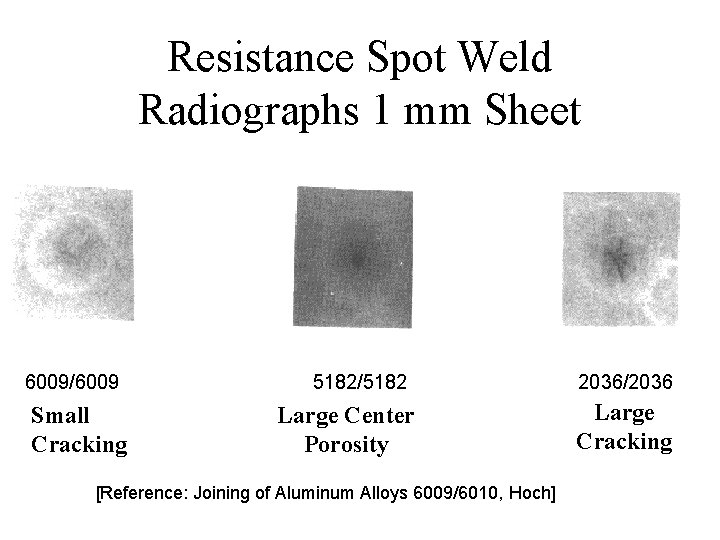
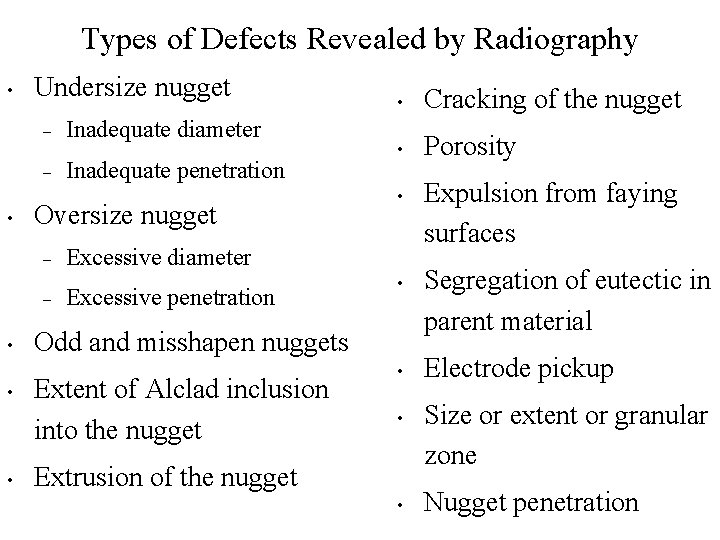
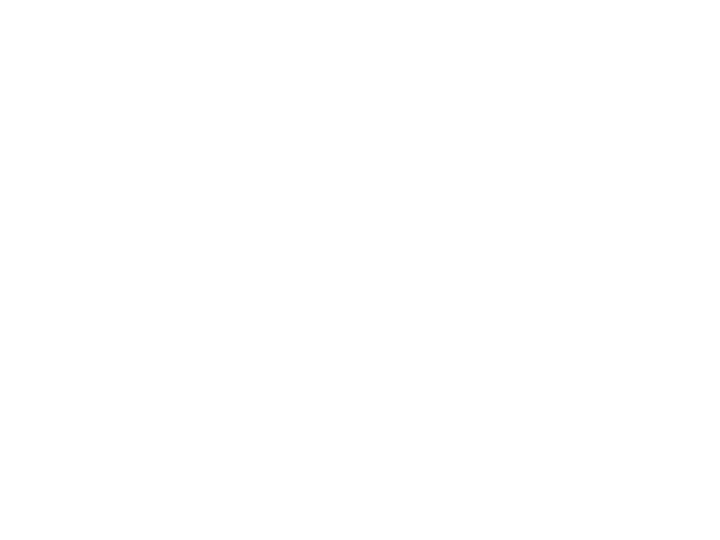
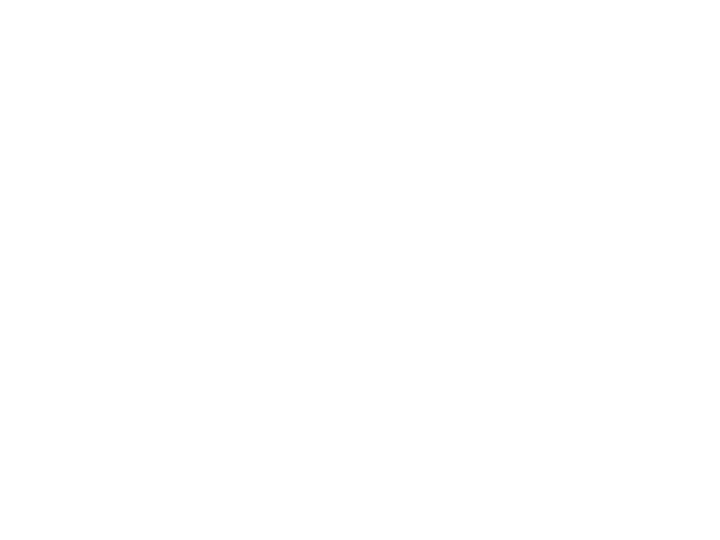
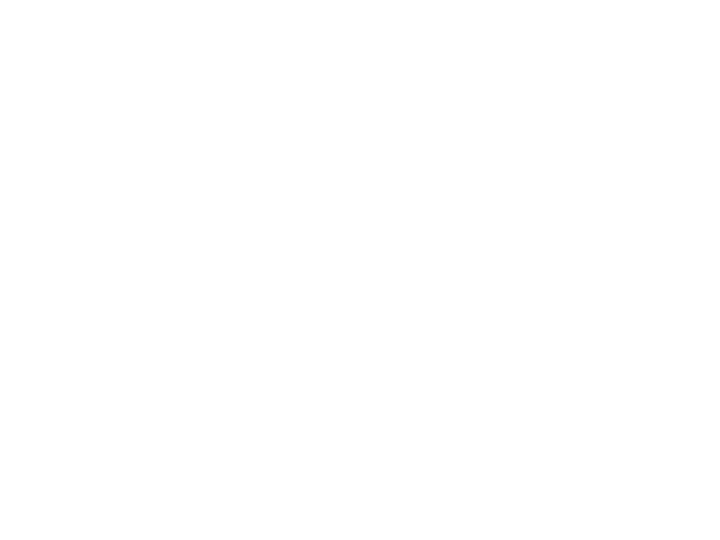
![Setup Procedures and Suggested Schedules • • • [Step 1] Insert electrode of • Setup Procedures and Suggested Schedules • • • [Step 1] Insert electrode of •](https://slidetodoc.com/presentation_image_h/0a32e26c02eaeb78a89123abf8556387/image-13.jpg)
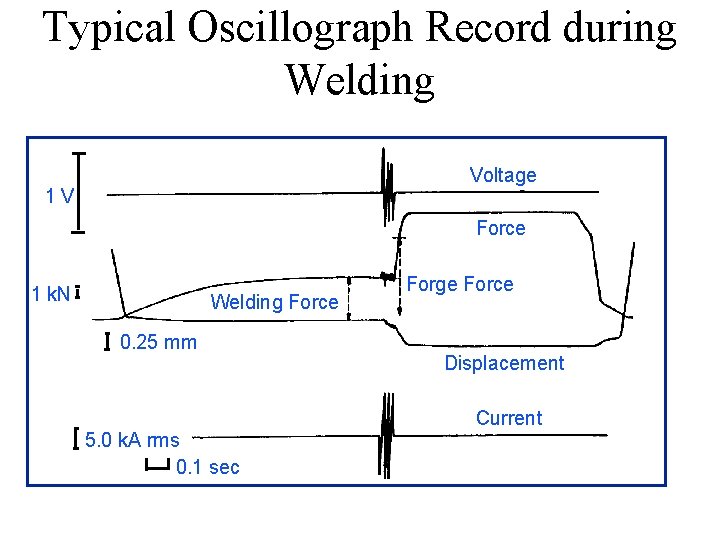
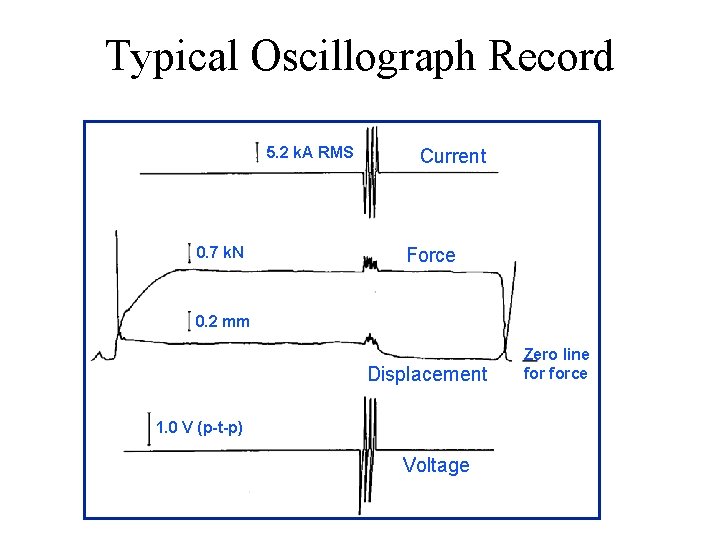
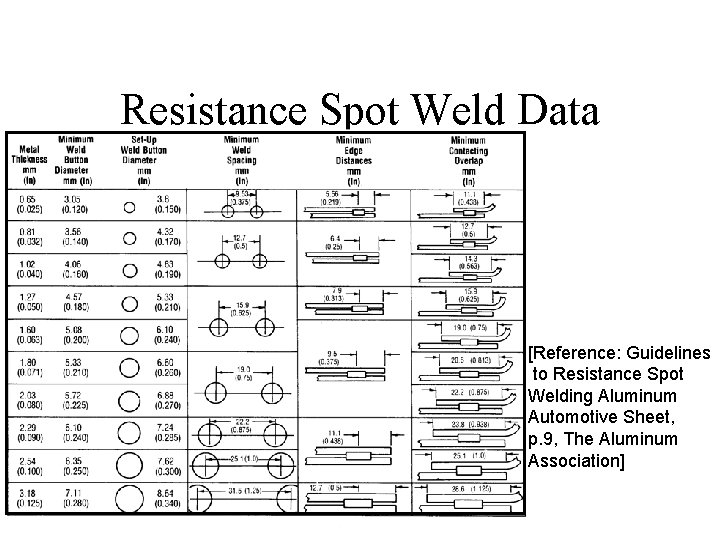
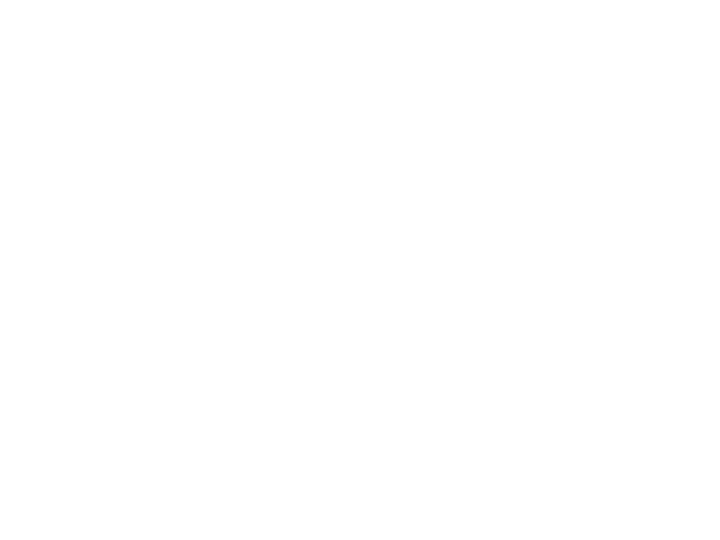
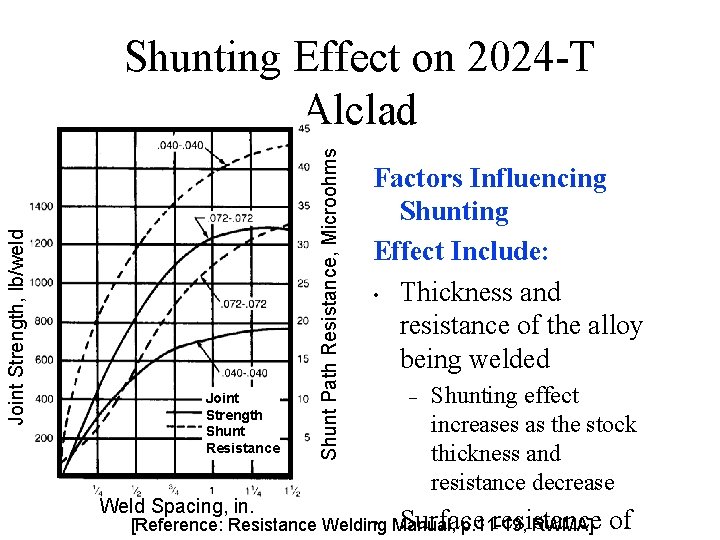
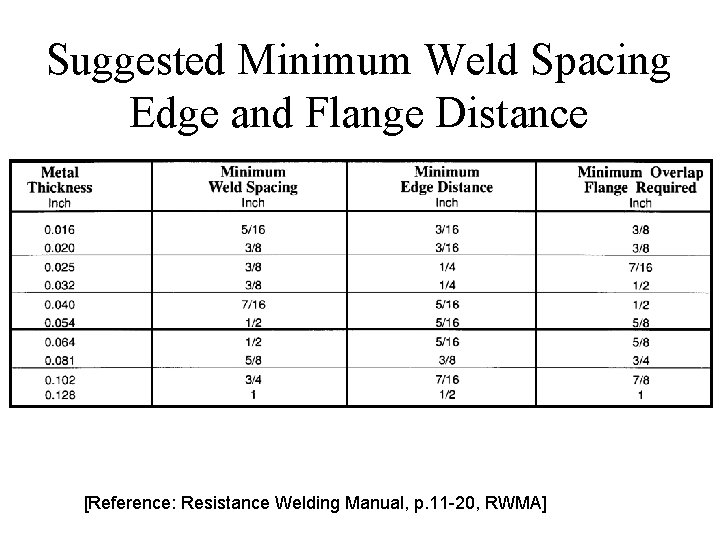
- Slides: 19
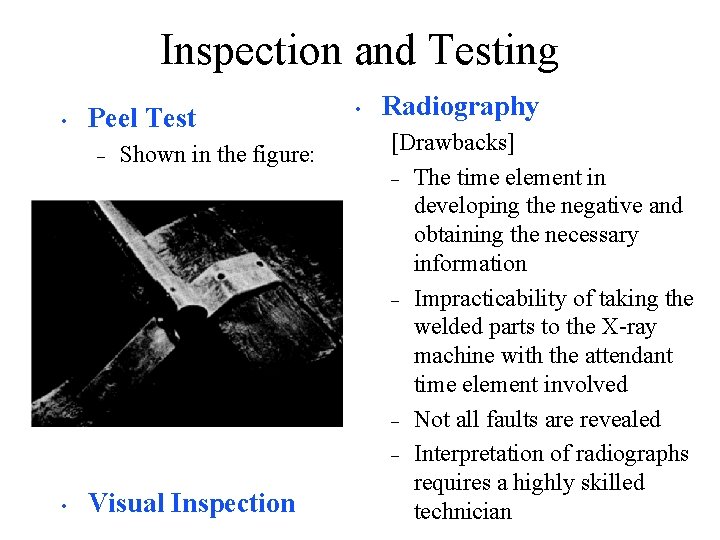
Inspection and Testing • Peel Test – • Shown in the figure: Visual Inspection • Radiography [Drawbacks] – The time element in developing the negative and obtaining the necessary information – Impracticability of taking the welded parts to the X-ray machine with the attendant time element involved – Not all faults are revealed – Interpretation of radiographs requires a highly skilled technician
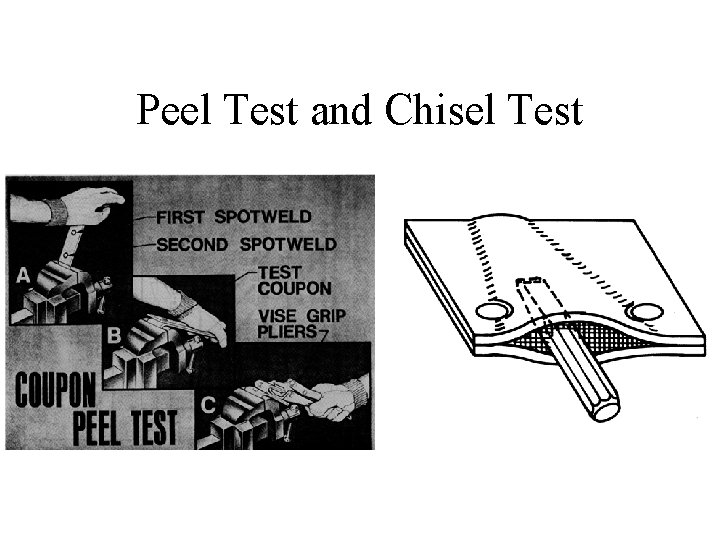
Peel Test and Chisel Test
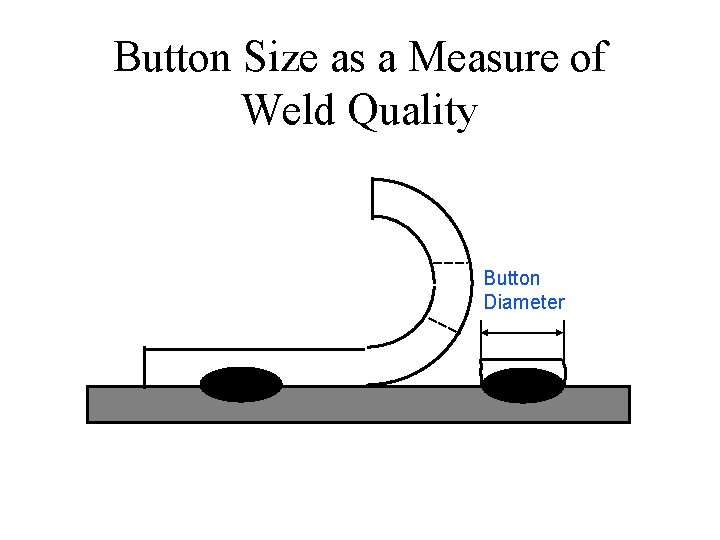
Button Size as a Measure of Weld Quality Button Diameter
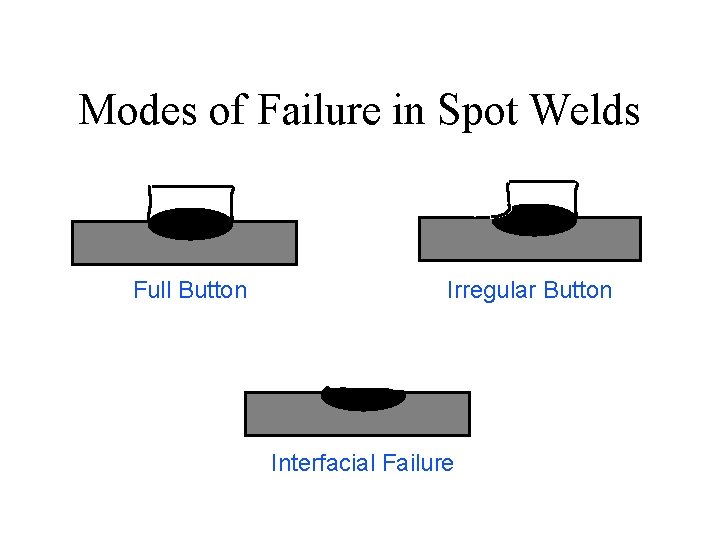
Modes of Failure in Spot Welds Full Button Irregular Button Interfacial Failure
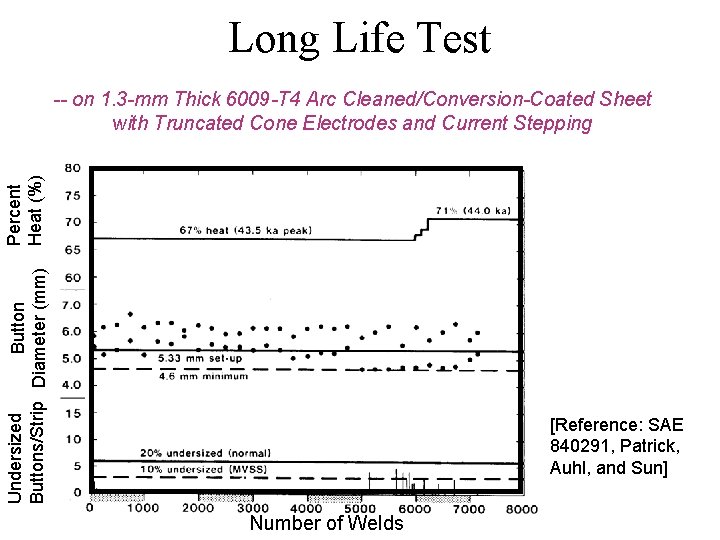
Long Life Test Undersized Buttons/Strip Diameter (mm) Percent Heat (%) -- on 1. 3 -mm Thick 6009 -T 4 Arc Cleaned/Conversion-Coated Sheet with Truncated Cone Electrodes and Current Stepping [Reference: SAE 840291, Patrick, Auhl, and Sun] Number of Welds
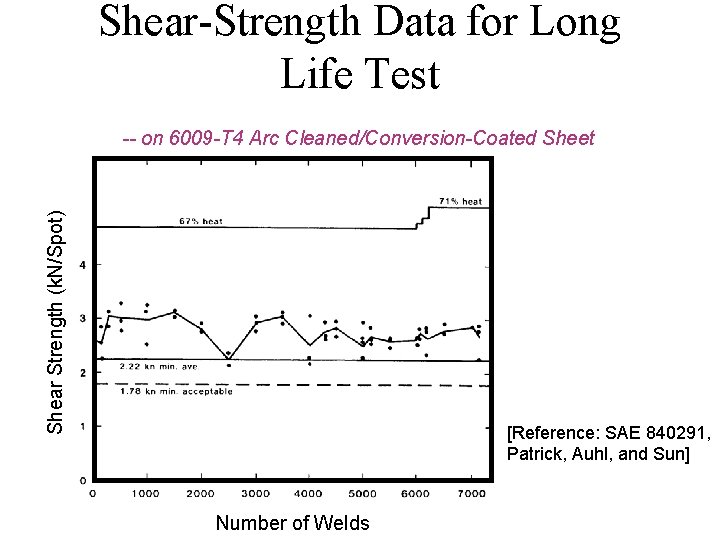
Shear-Strength Data for Long Life Test Shear Strength (k. N/Spot) -- on 6009 -T 4 Arc Cleaned/Conversion-Coated Sheet [Reference: SAE 840291, Patrick, Auhl, and Sun] Number of Welds
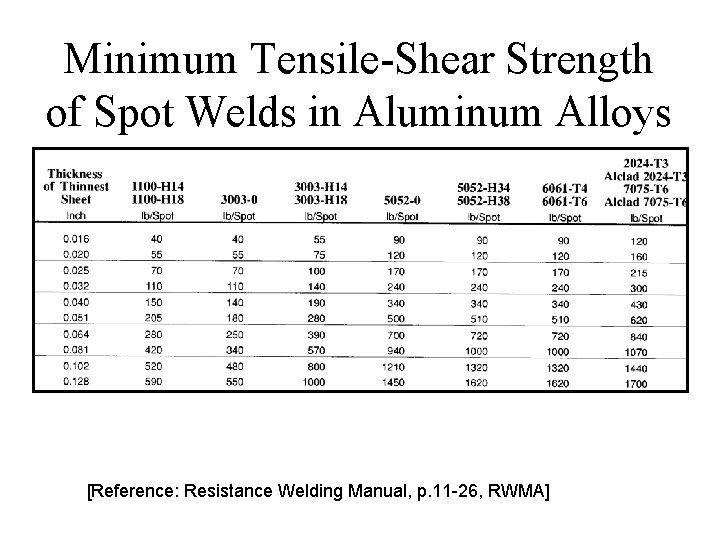
Minimum Tensile-Shear Strength of Spot Welds in Aluminum Alloys [Reference: Resistance Welding Manual, p. 11 -26, RWMA]
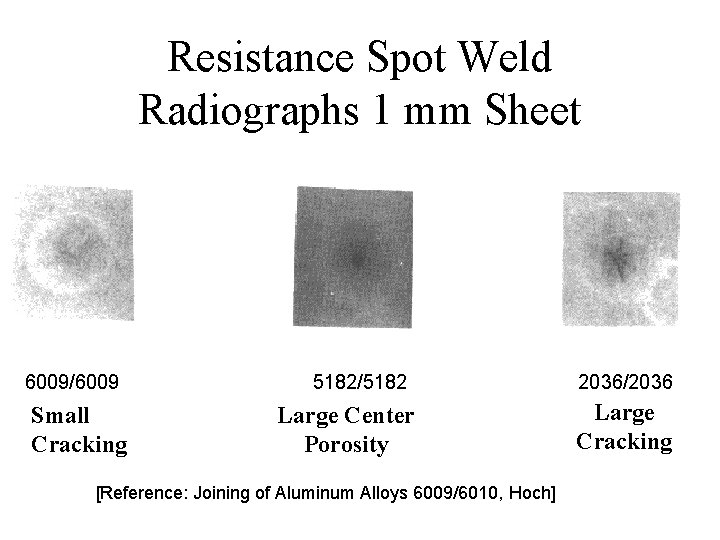
Resistance Spot Weld Radiographs 1 mm Sheet 6009/6009 Small Cracking 5182/5182 Large Center Porosity [Reference: Joining of Aluminum Alloys 6009/6010, Hoch] 2036/2036 Large Cracking
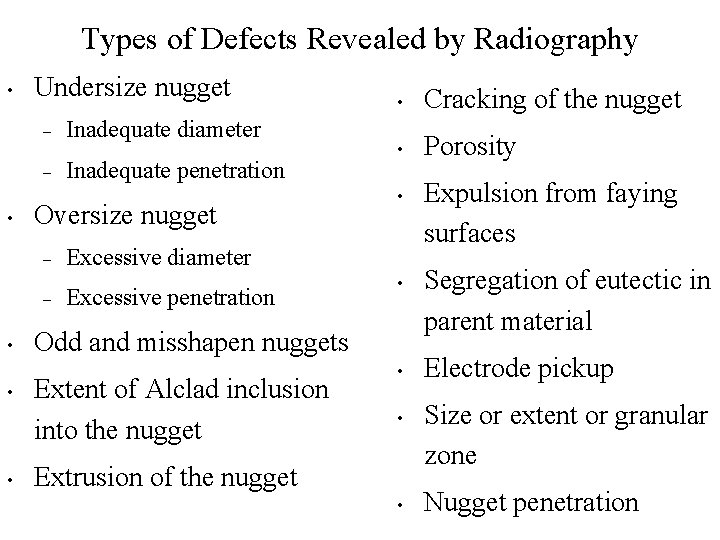
Types of Defects Revealed by Radiography • • Undersize nugget – Inadequate diameter – Inadequate penetration Oversize nugget – – • • Cracking of the nugget • Porosity • Excessive diameter Excessive penetration • Odd and misshapen nuggets Extent of Alclad inclusion into the nugget • • Extrusion of the nugget • Expulsion from faying surfaces Segregation of eutectic in parent material Electrode pickup Size or extent or granular zone Nugget penetration
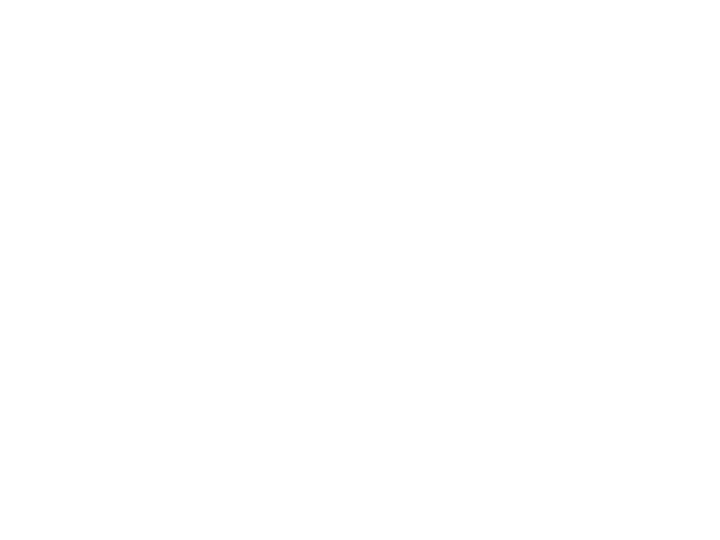
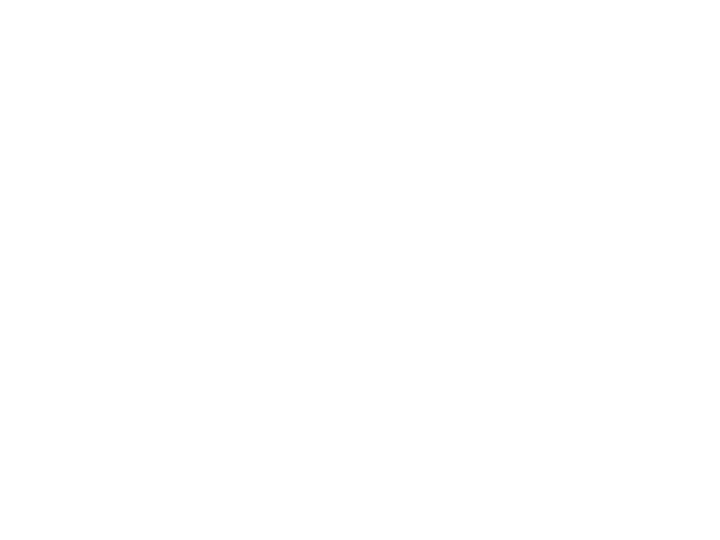
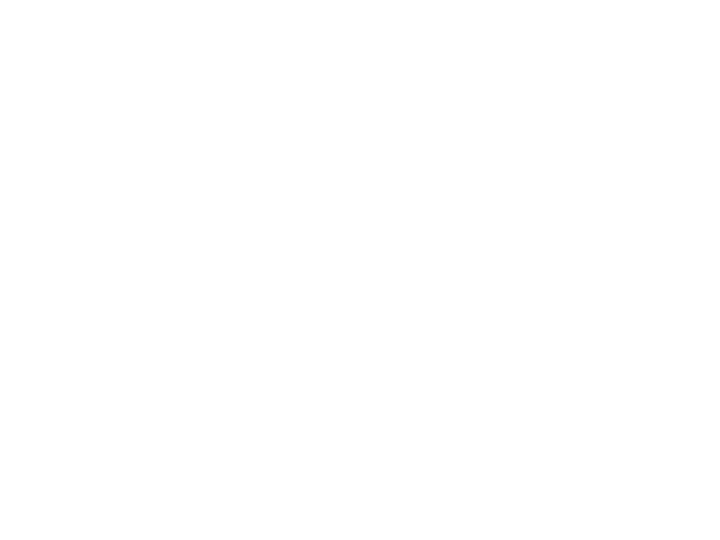
![Setup Procedures and Suggested Schedules Step 1 Insert electrode of Setup Procedures and Suggested Schedules • • • [Step 1] Insert electrode of •](https://slidetodoc.com/presentation_image_h/0a32e26c02eaeb78a89123abf8556387/image-13.jpg)
Setup Procedures and Suggested Schedules • • • [Step 1] Insert electrode of • proper size and tip contour for the gauge combination. Align electrodes. [Step 2] Set pressure gage for suggested welding force, and check with an electrode force gauge. • [Step 3] Adjust the control to provide the approximate suggested weld and “postheat time”. [Step 4] The welding currents shown are approximate and intended to be a guide. The magnitude of the welding current is usually controlled by a heat dial or phase-shift control. [Step 5] Check the machine for consistency of operation by making and testing twenty single spot tension-shear specimens and five macroscopic examination specimens.
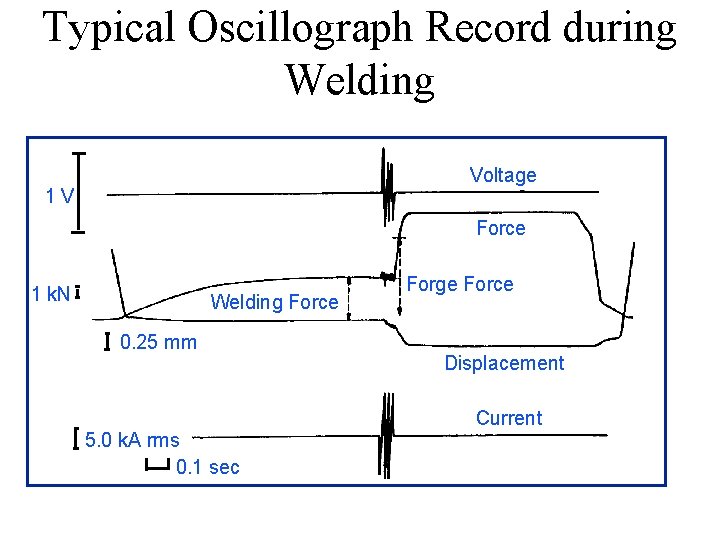
Typical Oscillograph Record during Welding Voltage 1 V Force 1 k. N Welding Force 0. 25 mm 5. 0 k. A rms 0. 1 sec Forge Force Displacement Current
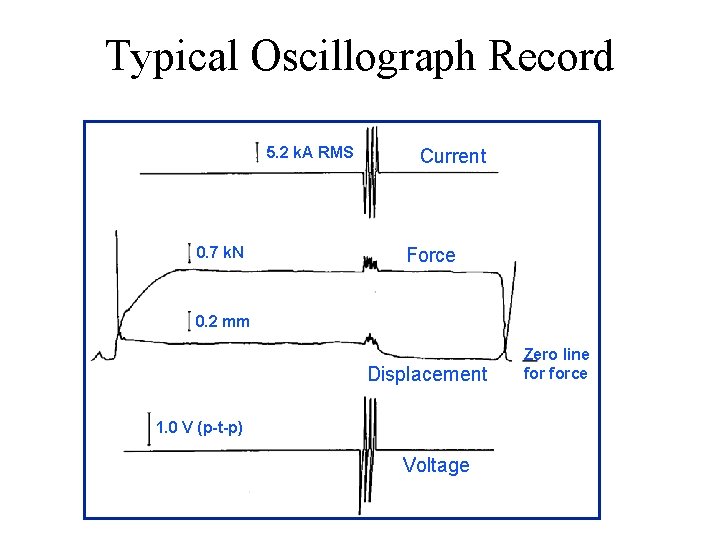
Typical Oscillograph Record 5. 2 k. A RMS 0. 7 k. N Current Force 0. 2 mm Displacement 1. 0 V (p-t-p) Voltage Zero line force
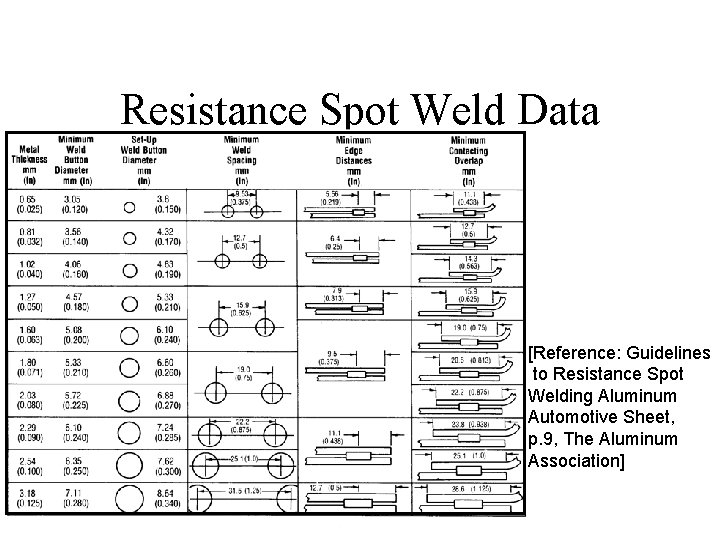
Resistance Spot Weld Data [Reference: Guidelines to Resistance Spot Welding Aluminum Automotive Sheet, p. 9, The Aluminum Association]
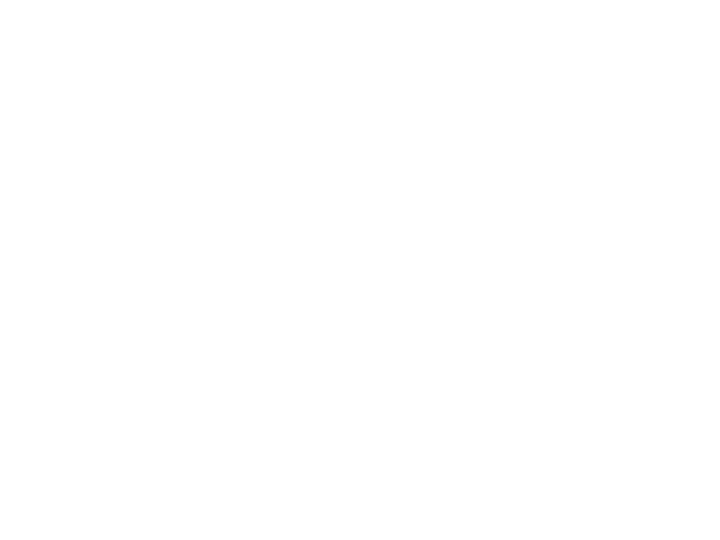
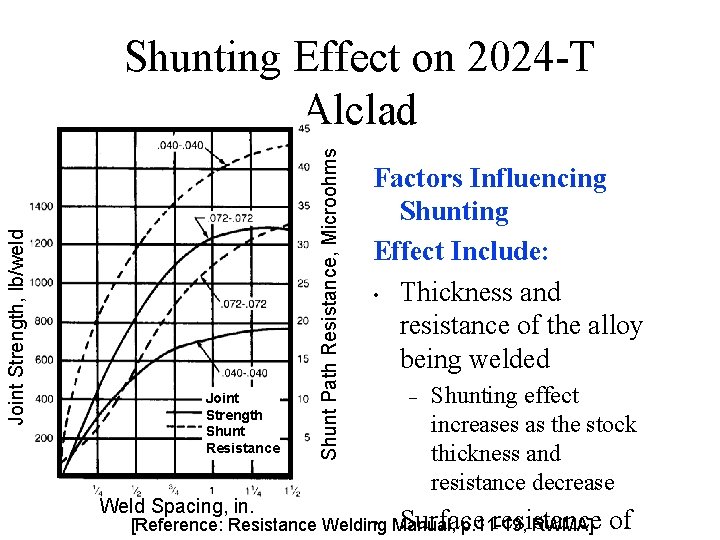
Joint Strength Shunt Resistance Weld Spacing, in. Shunt Path Resistance, Microohms Joint Strength, lb/weld Shunting Effect on 2024 -T Alclad Factors Influencing Shunting Effect Include: • Thickness and resistance of the alloy being welded – Shunting effect increases as the stock thickness and resistance decrease • Manual, Surface resistance [Reference: Resistance Welding p. 11 -19, RWMA] of
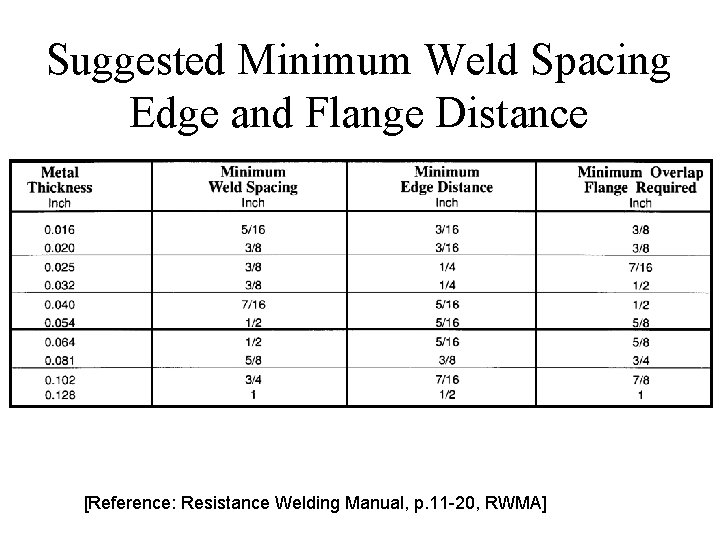
Suggested Minimum Weld Spacing Edge and Flange Distance [Reference: Resistance Welding Manual, p. 11 -20, RWMA]
Peer review walkthrough and inspection in software testing
Test lll
Rohacell hero
Peel test welding
Positive vs negative testing
Cs3250
What is domain test
Motivational overview in software testing
Data flow testing strategies in software testing
What is globalization testing
Functional testing vs unit testing
Decision table testing in software testing
Control structure testing in software engineering
Decision table testing in software testing
Advantages and disadvantages of decision table
Metode black box
Behavioral testing adalah
Decision table testing is white box
Rigorous testing in software testing
Testing blindness in software testing