Fusion is our Future Readiness of the Fusion
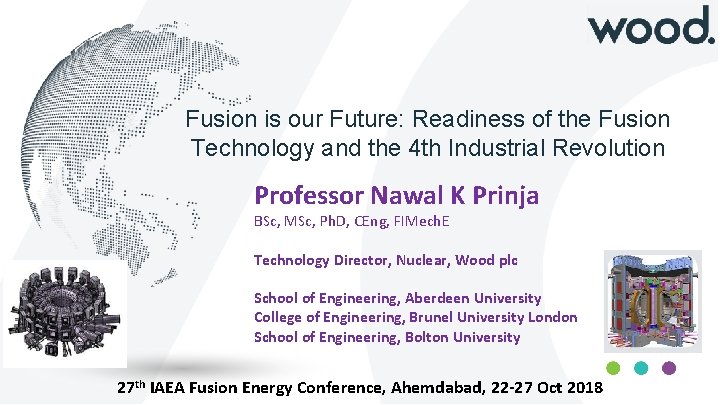
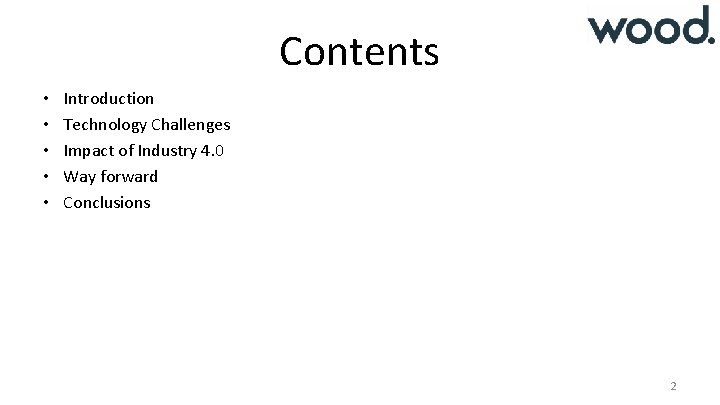
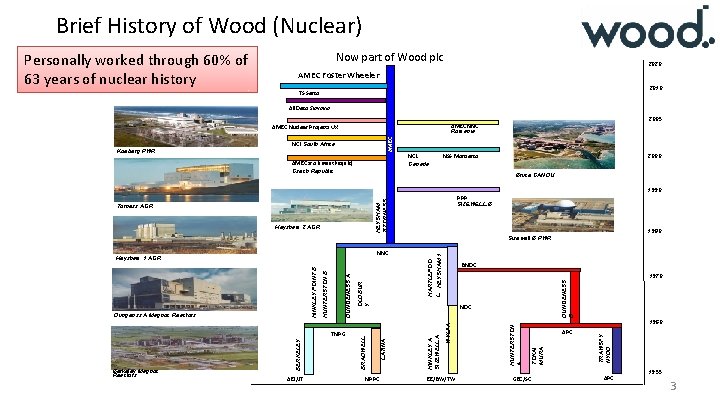
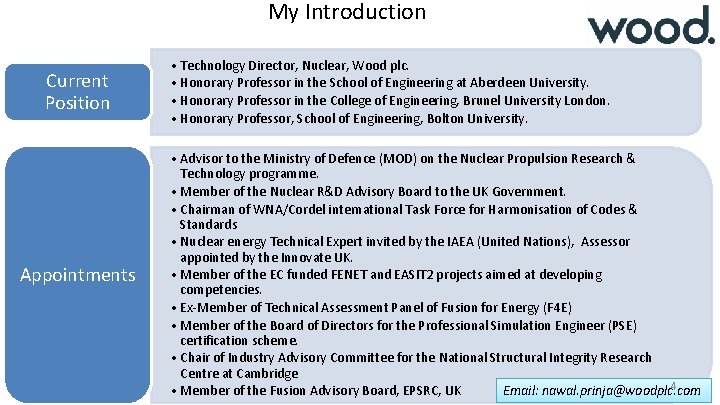
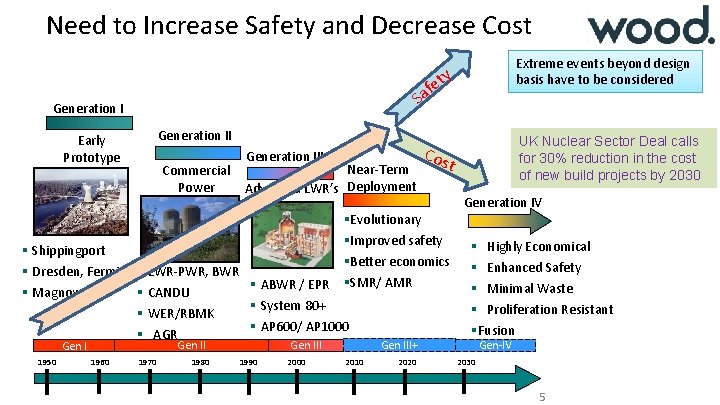
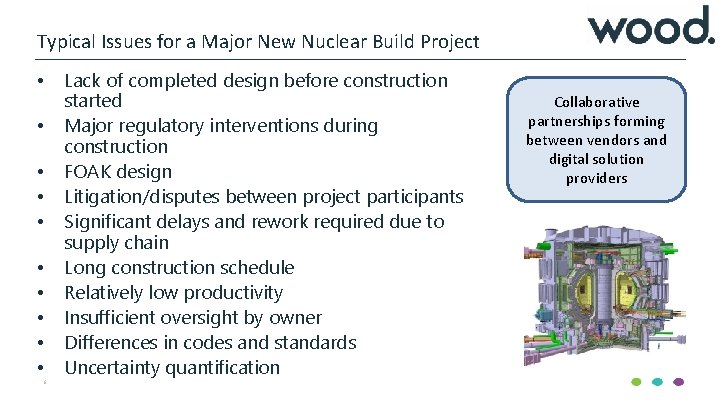
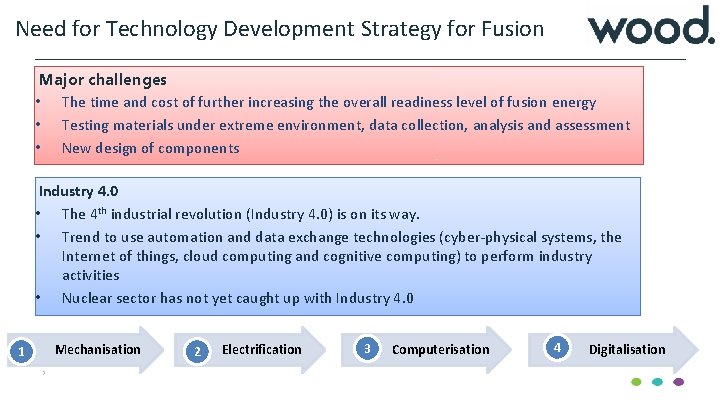
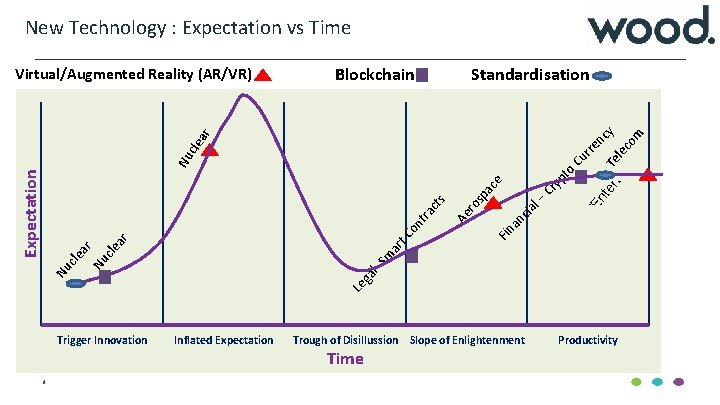
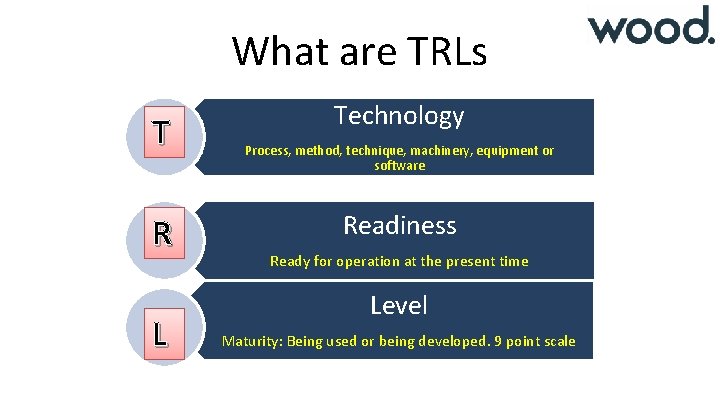
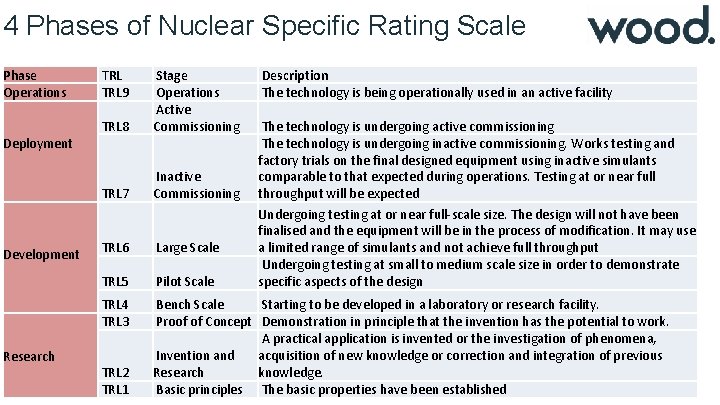
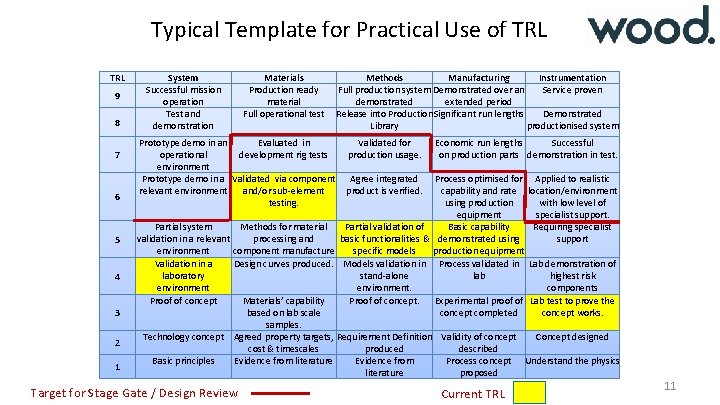
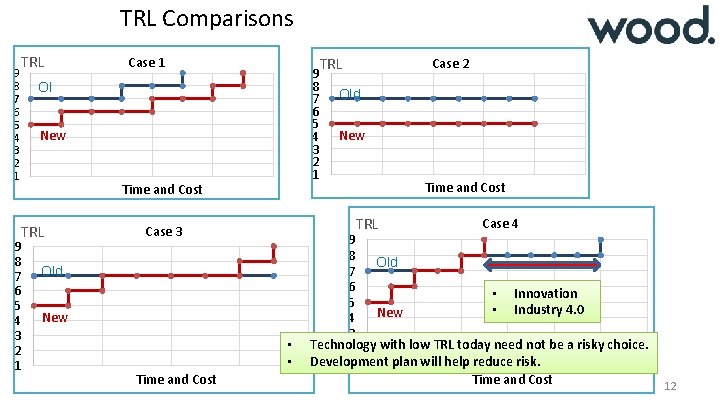
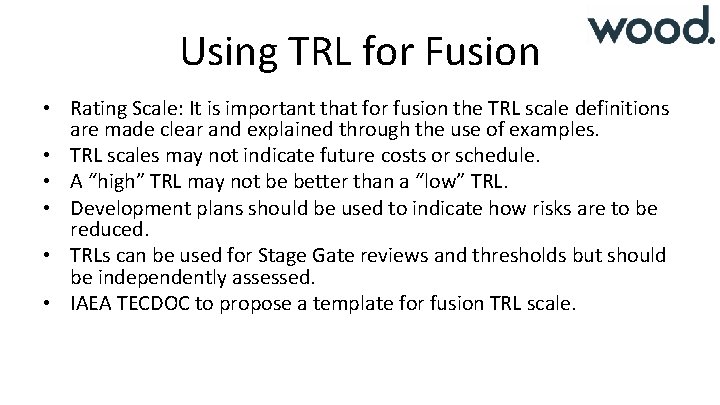
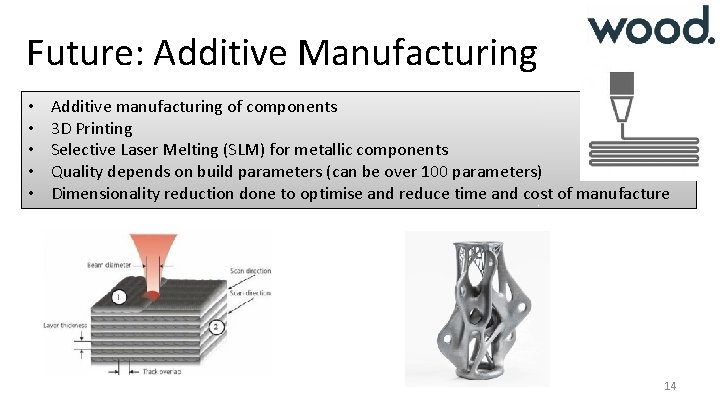
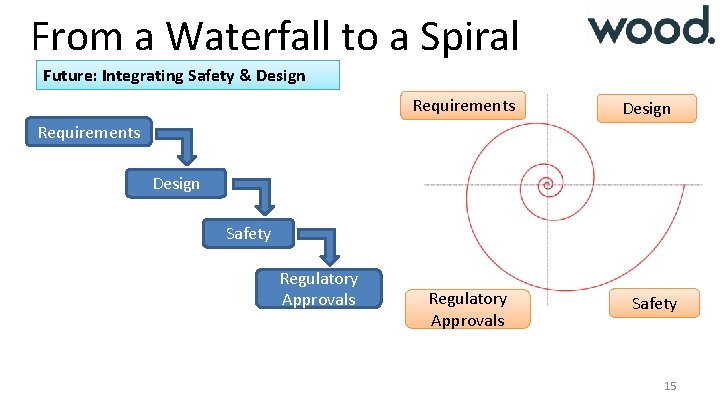
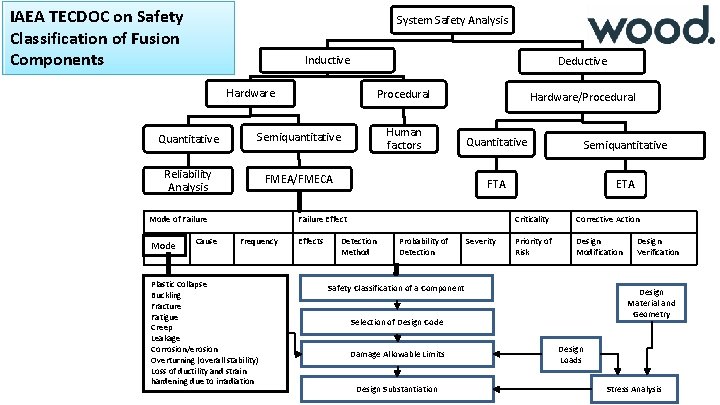
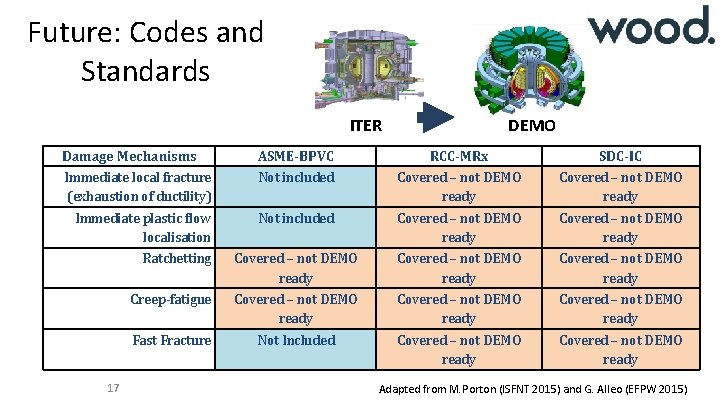
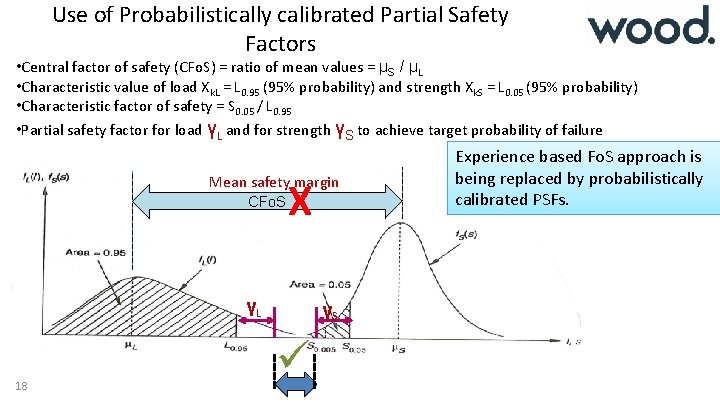
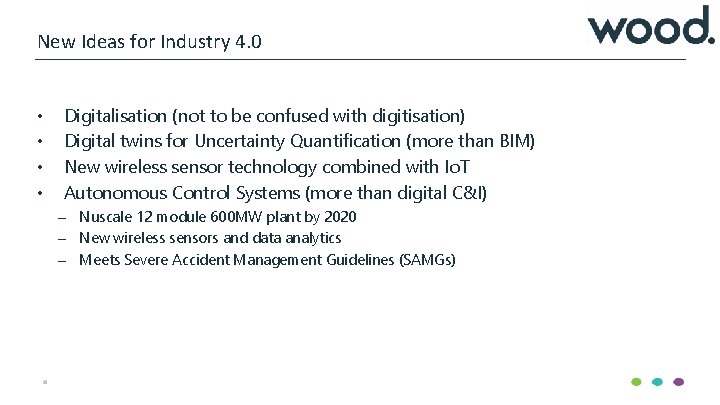
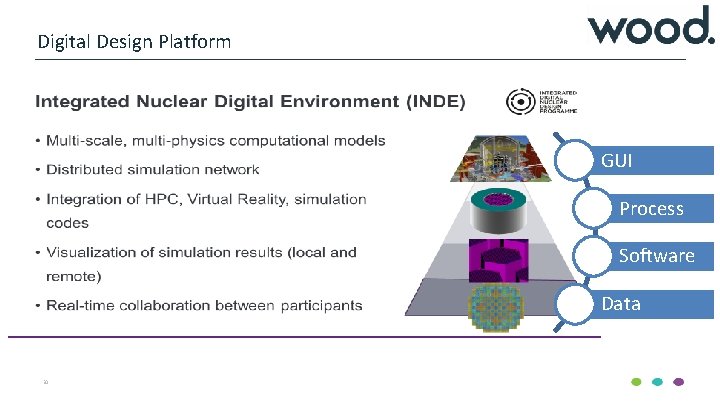
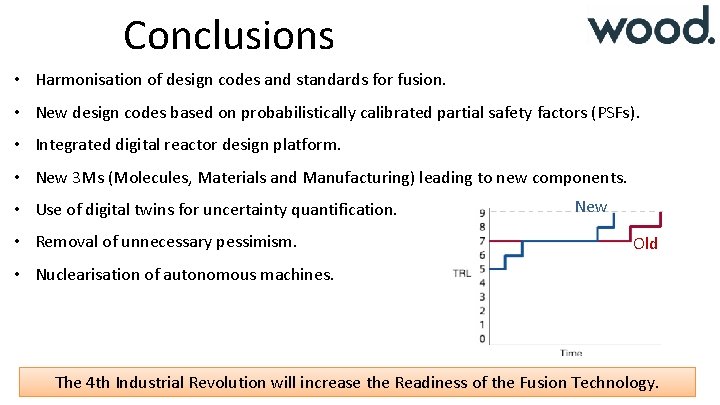
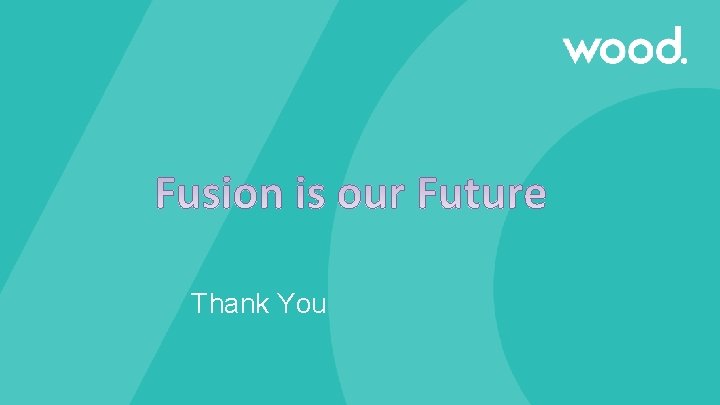
- Slides: 22
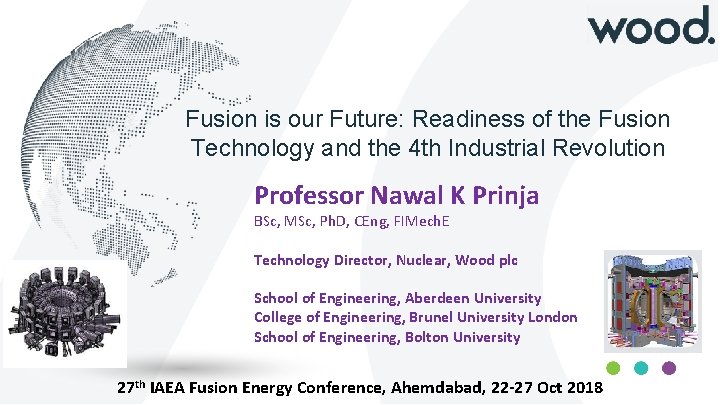
Fusion is our Future: Readiness of the Fusion Technology and the 4 th Industrial Revolution Professor Nawal K Prinja BSc, MSc, Ph. D, CEng, FIMech. E Technology Director, Nuclear, Wood plc School of Engineering, Aberdeen University College of Engineering, Brunel University London School of Engineering, Bolton University 27 th IAEA Fusion Energy Conference, Ahemdabad, 22 -27 Oct 2018
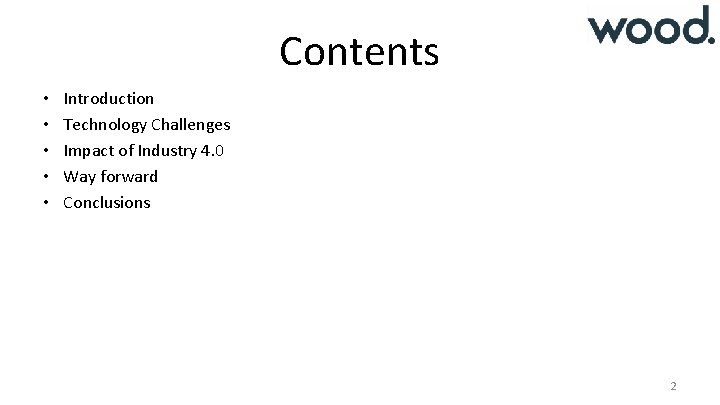
Contents • • • Introduction Technology Challenges Impact of Industry 4. 0 Way forward Conclusions 2
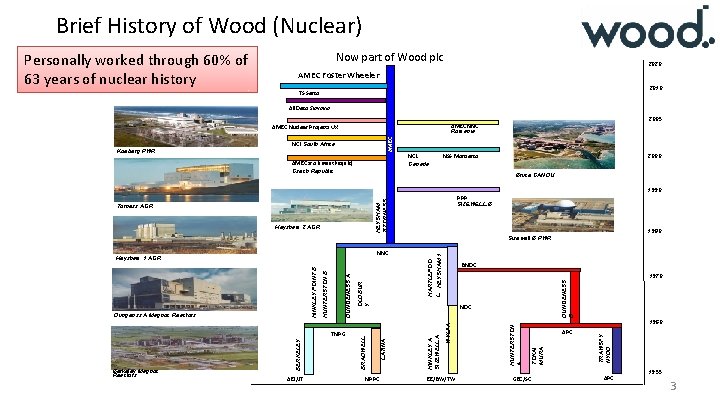
Brief History of Wood (Nuclear) Personally worked through 60% of 63 years of nuclear history Now part of Wood plc 2020 AMEC Foster Wheeler 2010 TS Serco All. Deco Slovakia AMEC Koeberg PWR 2005 AMEC NNC Romania AMEC Nuclear Projects UK NCI South Africa NCL Canada AMEC sro (Invest. Projekt) Czech Republic 2000 NSS Monserco Bruce CANDU 1990 HEYSHAM 2/TORNESS PPP SIZEWELL B Torness AGR Heysham 2 AGR 1980 AEI/JT TOKAI MURA HUNTERSTON A LATINA WYLFA EE/BW/TW 1960 APC GEC/SC TRAWSFY NYDD OLDBUR Y NPPC 1970 NDC HINKLEY A SIZEWELL A Berkeley Magnox Reactors BERKELEY TNPG BRADWELL DUNGENESS A HUNTERSTON B HINKLEY POINT B Dungenss A Magnox Reactors BNDC DUNGENESS B NNC Heysham 1 AGR HARTLEPOO L HEYSHAM 1 Sizewell B PWR APC 1955 3
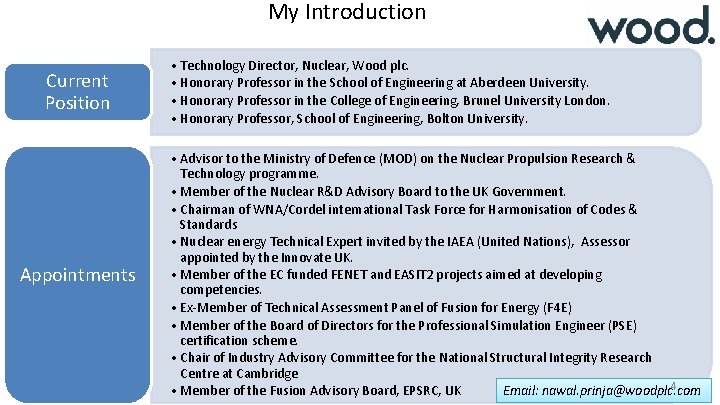
My Introduction Current Position Appointments • Technology Director, Nuclear, Wood plc. • Honorary Professor in the School of Engineering at Aberdeen University. • Honorary Professor in the College of Engineering, Brunel University London. • Honorary Professor, School of Engineering, Bolton University. • Advisor to the Ministry of Defence (MOD) on the Nuclear Propulsion Research & Technology programme. • Member of the Nuclear R&D Advisory Board to the UK Government. • Chairman of WNA/Cordel international Task Force for Harmonisation of Codes & Standards • Nuclear energy Technical Expert invited by the IAEA (United Nations), Assessor appointed by the Innovate UK. • Member of the EC funded FENET and EASIT 2 projects aimed at developing competencies. • Ex-Member of Technical Assessment Panel of Fusion for Energy (F 4 E) • Member of the Board of Directors for the Professional Simulation Engineer (PSE) certification scheme. • Chair of Industry Advisory Committee for the National Structural Integrity Research Centre at Cambridge 4 Email: nawal. prinja@woodplc. com • Member of the Fusion Advisory Board, EPSRC, UK
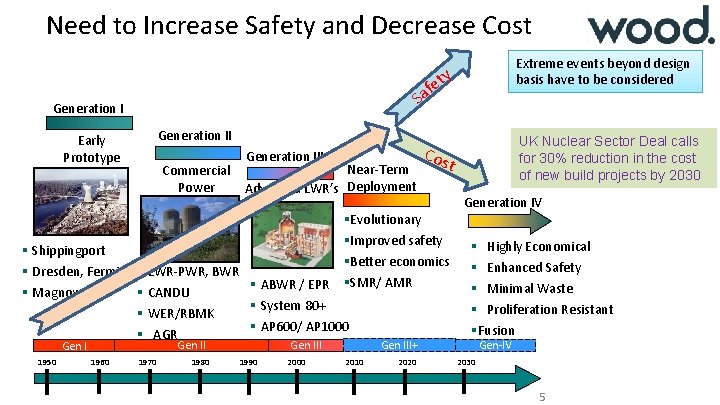
Need to Increase Safety and Decrease Cost ty e af S Generation II Early Prototype Reactors Commercial Power Reactors Generation III Near-Term Advanced LWR’s Deployment Gen II Gen I 1960 1970 1980 Gen III+ Gen III 1990 2000 2010 2020 UK Nuclear Sector Deal calls for 30% reduction in the cost of new build projects by 2030 Cos t §Evolutionary §Improved safety § Shippingport §Better economics § Dresden, Fermi I § LWR-PWR, BWR § ABWR / EPR §SMR/ AMR § Magnox § CANDU § System 80+ § WER/RBMK § AP 600/ AP 1000 § AGR 1950 Extreme events beyond design basis have to be considered Generation IV § Highly Economical § Enhanced Safety § Minimal Waste § Proliferation Resistant §Fusion Gen-IV 2030 5
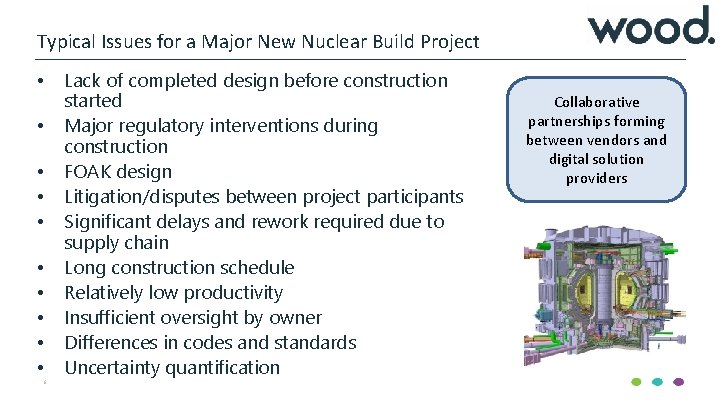
Typical Issues for a Major New Nuclear Build Project • • • 6 Lack of completed design before construction started Major regulatory interventions during construction FOAK design Litigation/disputes between project participants Significant delays and rework required due to supply chain Long construction schedule Relatively low productivity Insufficient oversight by owner Differences in codes and standards Uncertainty quantification Collaborative partnerships forming between vendors and digital solution providers
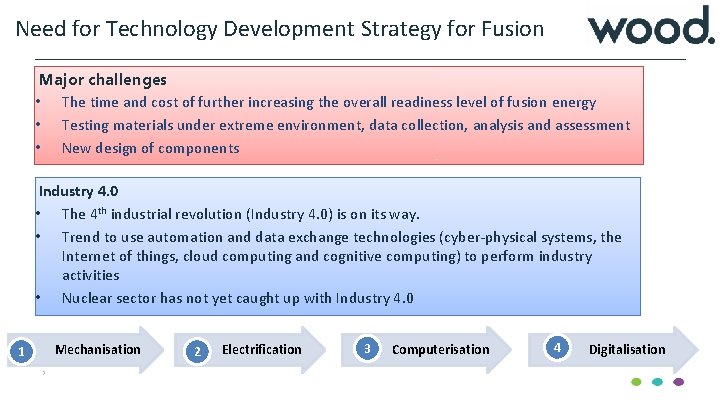
Need for Technology Development Strategy for Fusion Major challenges • The time and cost of further increasing the overall readiness level of fusion energy • Testing materials under extreme environment, data collection, analysis and assessment • New design of components Industry 4. 0 • The 4 th industrial revolution (Industry 4. 0) is on its way. • Trend to use automation and data exchange technologies (cyber-physical systems, the Internet of things, cloud computing and cognitive computing) to perform industry activities • Nuclear sector has not yet caught up with Industry 4. 0 Mechanisation 1 7 2 Electrification 3 Computerisation 4 Digitalisation
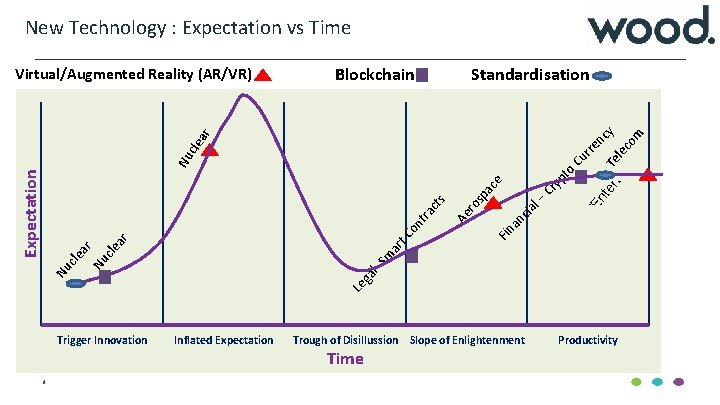
New Technology : Expectation vs Time Blockchain Standardisation y cle rr Nu to te C g/ in am Sm G Fi Cu En pa os Ae r – ial p ry c n na ar cle a Le ga l- Nu Nu cle ar r t. C on tra ct s ce Expectation c en rta Tele in co m m en t ar Virtual/Augmented Reality (AR/VR) Trigger Innovation 8 Inflated Expectation Trough of Disillussion Slope of Enlightenment Time Productivity
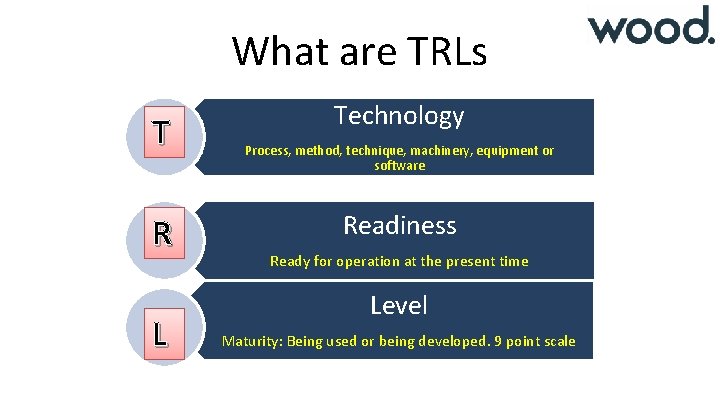
What are TRLs T R L Technology Process, method, technique, machinery, equipment or software Readiness Ready for operation at the present time Level Maturity: Being used or being developed. 9 point scale
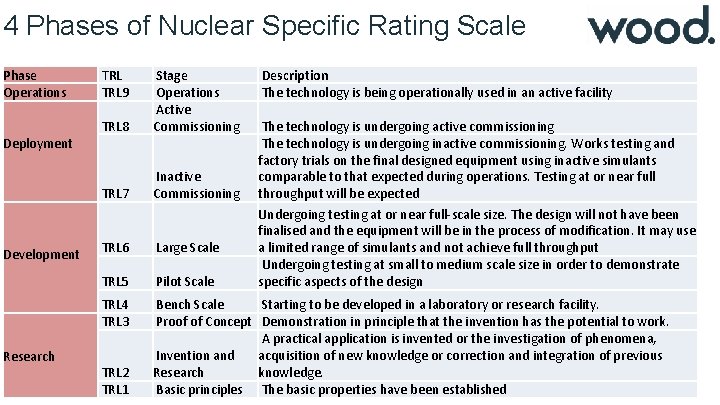
4 Phases of Nuclear Specific Rating Scale Phase Operations Deployment Development TRL 9 TRL 8 Stage Operations Active Commissioning TRL 7 Inactive Commissioning TRL 6 Large Scale TRL 5 Pilot Scale TRL 4 TRL 3 Research 10 Description The technology is being operationally used in an active facility The technology is undergoing active commissioning The technology is undergoing inactive commissioning. Works testing and factory trials on the final designed equipment using inactive simulants comparable to that expected during operations. Testing at or near full throughput will be expected Undergoing testing at or near full-scale size. The design will not have been finalised and the equipment will be in the process of modification. It may use a limited range of simulants and not achieve full throughput Undergoing testing at small to medium scale size in order to demonstrate specific aspects of the design Bench Scale Starting to be developed in a laboratory or research facility. Proof of Concept Demonstration in principle that the invention has the potential to work. A practical application is invented or the investigation of phenomena, Invention and acquisition of new knowledge or correction and integration of previous TRL 2 Research knowledge. Technology in Nuclear N Prinja TRL 1 Basic principles The basic properties have been established
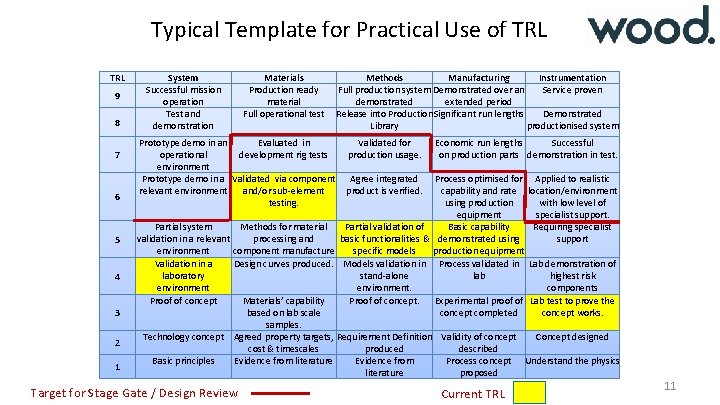
Typical Template for Practical Use of TRL 9 8 7 6 5 4 3 2 1 System Successful mission operation Test and demonstration Materials Production ready material Full operational test Prototype demo in an Evaluated in operational development rig tests environment Prototype demo in a Validated via component relevant environment and/or sub-element testing. Methods Manufacturing Instrumentation Full production system Demonstrated over an Service proven demonstrated extended period Release into Production Significant run lengths Demonstrated Library productionised system Validated for production usage. Economic run lengths Successful on production parts demonstration in test. Process optimised for Applied to realistic capability and rate location/environment using production with low level of equipment specialist support. Partial system Methods for material Partial validation of Basic capability Requiring specialist validation in a relevant processing and basic functionalities & demonstrated using support environment component manufacture specific models production equipment Validation in a Design curves produced. Models validation in Process validated in Lab demonstration of laboratory stand-alone lab highest risk environment. components Proof of concept Materials’ capability Proof of concept. Experimental proof of Lab test to prove the based on lab scale concept completed concept works. samples. Technology concept Agreed property targets, Requirement Definition Validity of concept Concept designed cost & timescales produced described Basic principles Evidence from literature Evidence from Process concept Understand the physics literature proposed Target for Stage Gate / Design Review Agree integrated product is verified. Current TRL 11
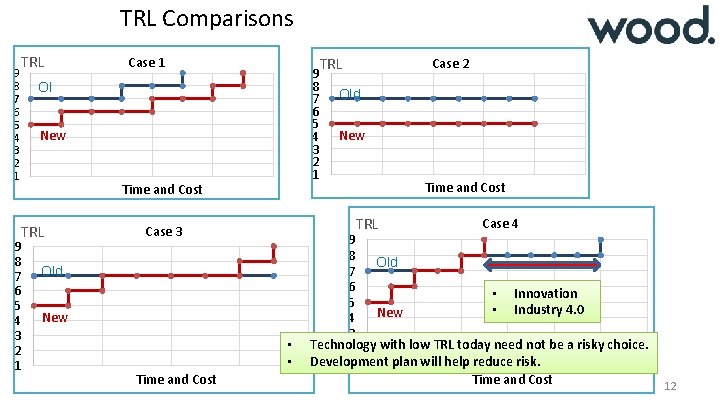
TRL Comparisons 9 8 7 6 5 4 3 2 1 TRL Case 1 9 8 7 6 5 4 3 2 1 Ol New Time and Cost TRL 9 8 7 6 5 4 3 2 1 Case 2 Old New Time and Cost TRL Case 3 Old New • • Time and Cost TRL Case 4 9 8 Old 7 6 • Innovation 5 • Industry 4. 0 New 4 3 Technology with low TRL today need not be a risky choice. 2 Development plan will help reduce risk. 1 Time and Cost 12
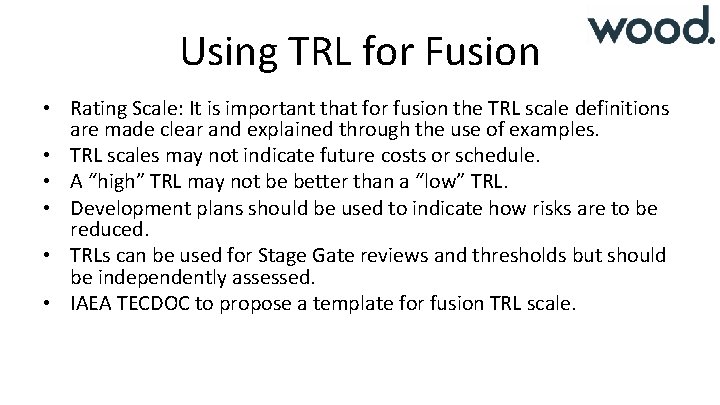
Using TRL for Fusion • Rating Scale: It is important that for fusion the TRL scale definitions are made clear and explained through the use of examples. • TRL scales may not indicate future costs or schedule. • A “high” TRL may not be better than a “low” TRL. • Development plans should be used to indicate how risks are to be reduced. • TRLs can be used for Stage Gate reviews and thresholds but should be independently assessed. • IAEA TECDOC to propose a template for fusion TRL scale.
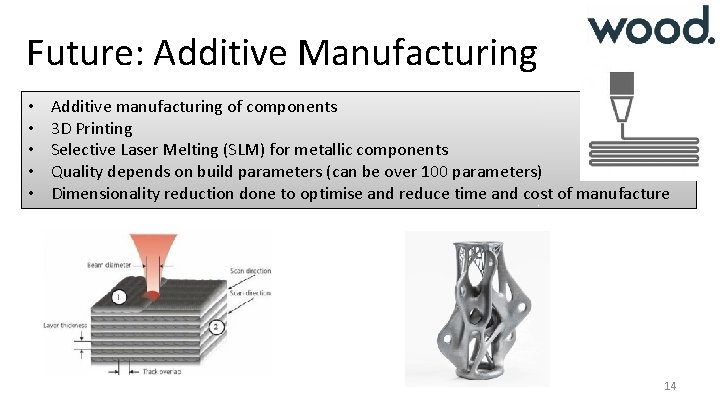
Future: Additive Manufacturing • • • Additive manufacturing of components 3 D Printing Selective Laser Melting (SLM) for metallic components Quality depends on build parameters (can be over 100 parameters) Dimensionality reduction done to optimise and reduce time and cost of manufacture 14
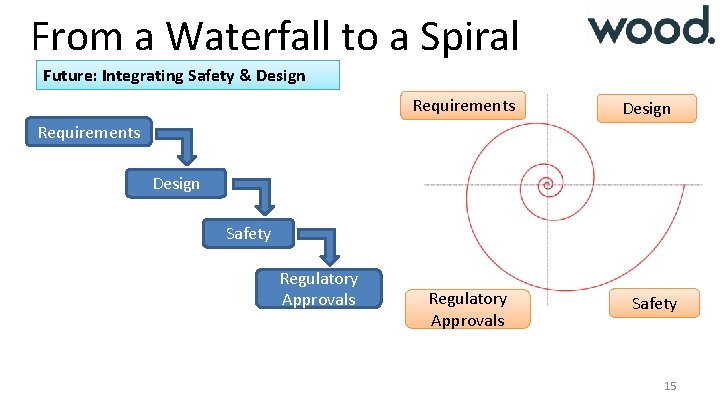
From a Waterfall to a Spiral Future: Integrating Safety & Design Requirements Design Safety Regulatory Approvals Safety 15
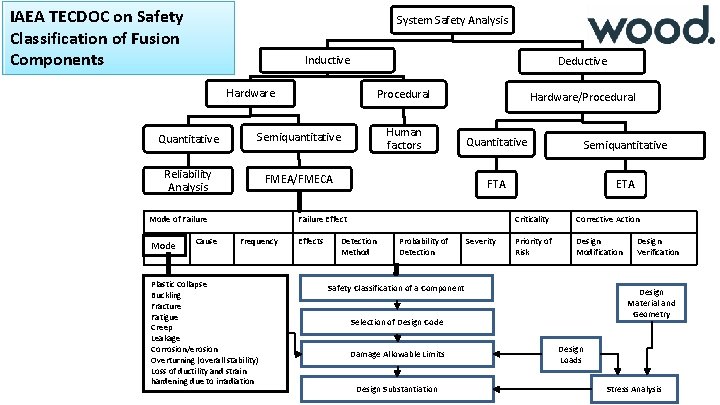
IAEA TECDOC on Safety Classification of Fusion Components System Safety Analysis Inductive Deductive Hardware Procedural Quantitative Semiquantitative Reliability Analysis FMEA/FMECA Mode of Failure Mode Cause Human factors Hardware/Procedural Quantitative Semiquantitative FTA ETA Failure Effect Frequency Plastic Collapse Buckling Fracture Fatigue Creep Leakage Corrosion/erosion Overturning (overall stability) Loss of ductility and strain hardening due to irradiation Effects Detection Method Probability of Detection Severity Criticality Corrective Action Priority of Risk Design Modification Safety Classification of a Component Design Material and Geometry Selection of Design Code Damage Allowable Limits Design Substantiation Design Verification Design Loads Stress Analysis
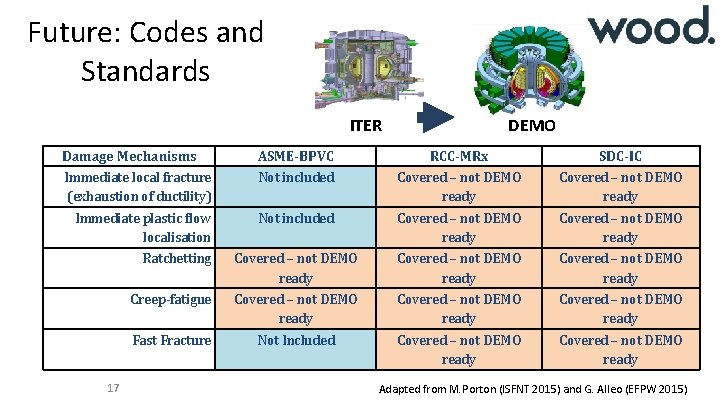
Future: Codes and Standards ITER DEMO Damage Mechanisms Immediate local fracture (exhaustion of ductility) ASME-BPVC Not included RCC-MRx Covered – not DEMO ready SDC-IC Covered – not DEMO ready Immediate plastic flow localisation Not included Covered – not DEMO ready Ratchetting Covered – not DEMO ready Creep-fatigue Covered – not DEMO ready Fast Fracture Not Included Covered – not DEMO ready 17 Adapted from M. Porton (ISFNT 2015) and G. Alleo (EFPW 2015)
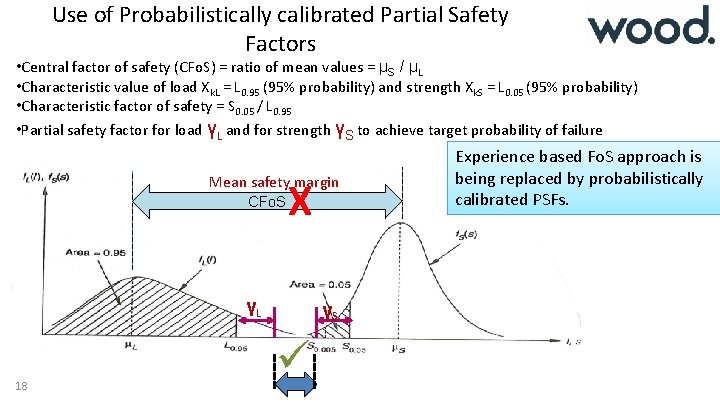
Use of Probabilistically calibrated Partial Safety Factors • Central factor of safety (CFo. S) = ratio of mean values = μS / μL • Characteristic value of load Xk. L = L 0. 95 (95% probability) and strength Xk. S = L 0. 05 (95% probability) • Characteristic factor of safety = S 0. 05 / L 0. 95 • Partial safety factor for load γL and for strength γS to achieve target probability of failure Mean safety margin CFo. S X γL 18 γS Experience based Fo. S approach is being replaced by probabilistically calibrated PSFs.
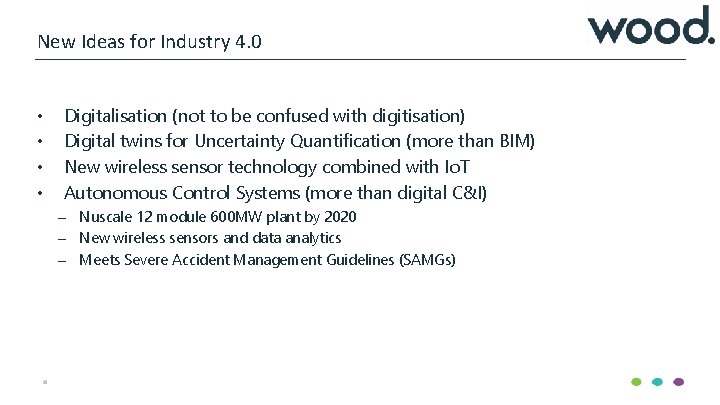
New Ideas for Industry 4. 0 • • Digitalisation (not to be confused with digitisation) Digital twins for Uncertainty Quantification (more than BIM) New wireless sensor technology combined with Io. T Autonomous Control Systems (more than digital C&I) – Nuscale 12 module 600 MW plant by 2020 – New wireless sensors and data analytics – Meets Severe Accident Management Guidelines (SAMGs) 19
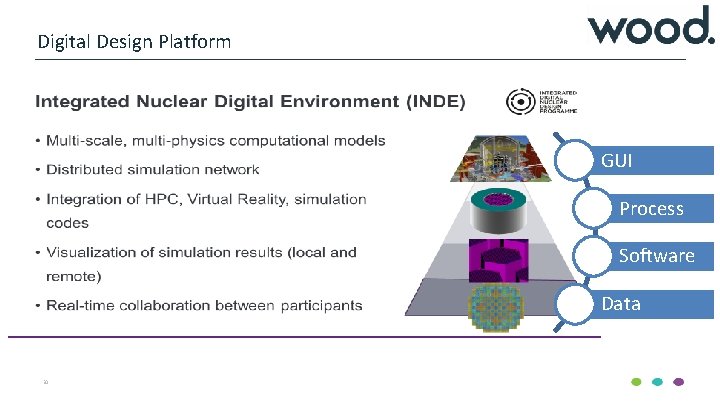
Digital Design Platform GUI Process Software Data 20
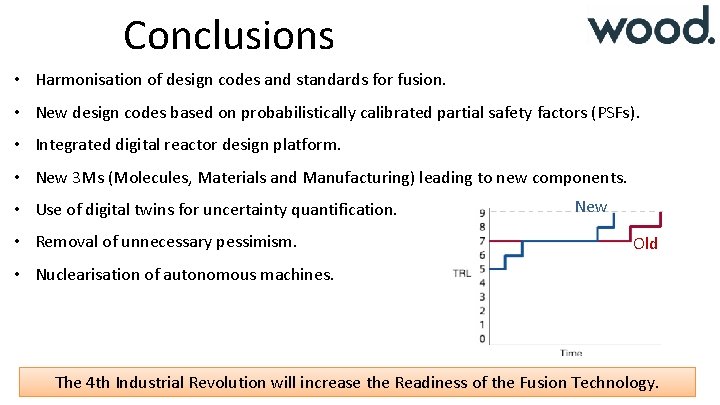
Conclusions • Harmonisation of design codes and standards for fusion. • New design codes based on probabilistically calibrated partial safety factors (PSFs). • Integrated digital reactor design platform. • New 3 Ms (Molecules, Materials and Manufacturing) leading to new components. • Use of digital twins for uncertainty quantification. • Removal of unnecessary pessimism. New Old • Nuclearisation of autonomous machines. The 4 th Industrial Revolution will increase the Readiness of the Fusion Technology. 21
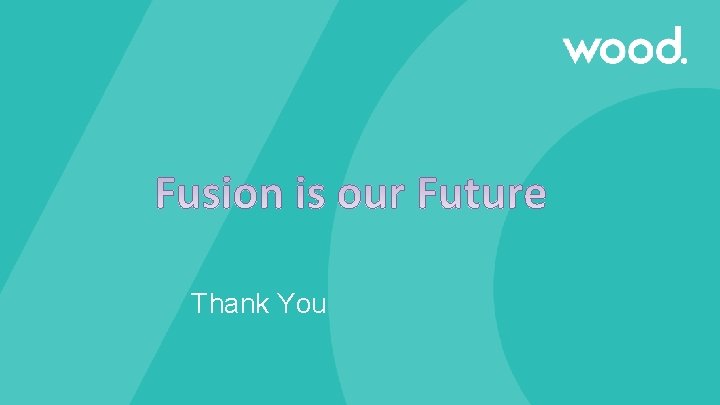
Thank You
Our census our future
Our future is in our hands quotes
Our census our future
Future perfect simple and future continuous exercises
Future perfect or future continuous
Our readiness to perceive ourselves favorably
Our collective madness is for *
Awareness of ourselves and our environment is:
Marcus aurelius our life is what our thoughts make it
Awareness of ourselves and our environment is:
We bow our hearts we bend our knees
Awareness of ourselves and our environment is:
Thinking language and intelligence
Our life is what our thoughts make it
Awareness of ourselves and our environment is
God our father christ our brother
Words to christ be our light
Powering our future
Our future hope
A future not our own poem
Future nurse programme
Future plans and finished future actions
Future perfect