Feedforward Ratio Control CSE 425 Industrial Process Control
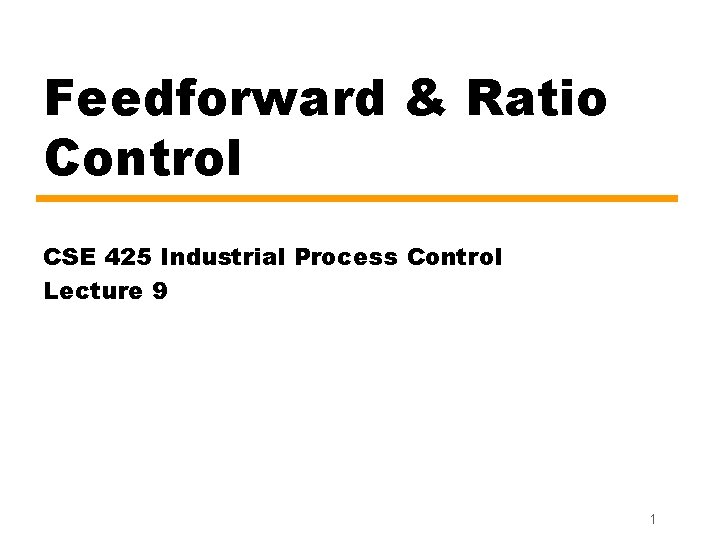
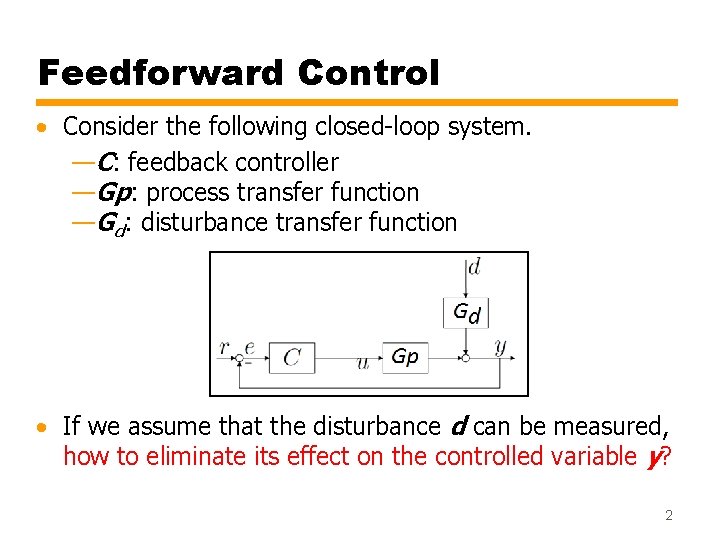
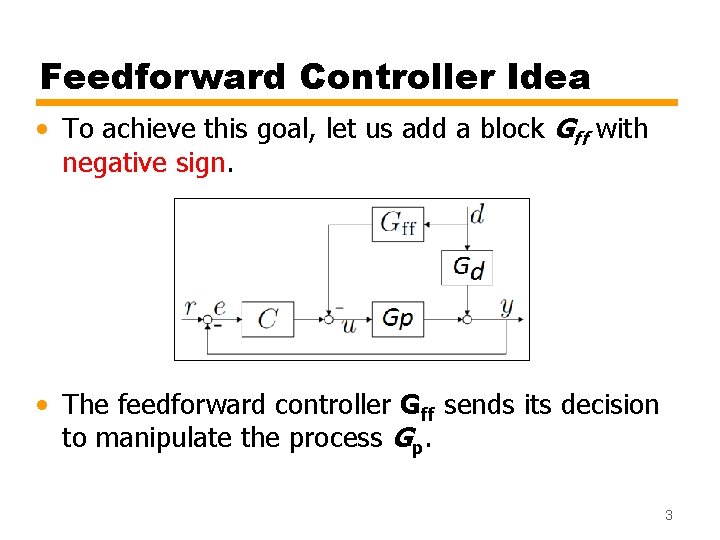
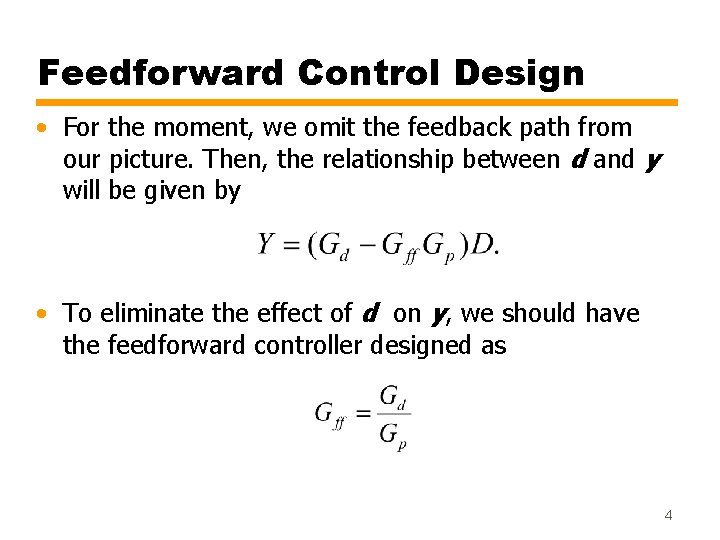
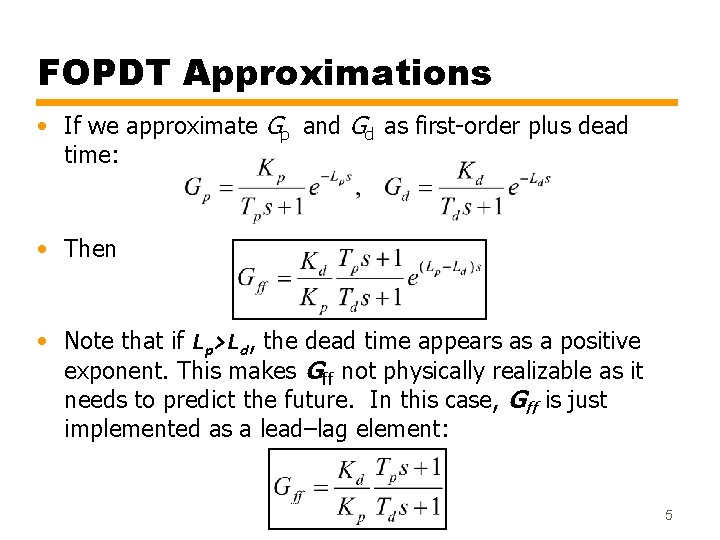
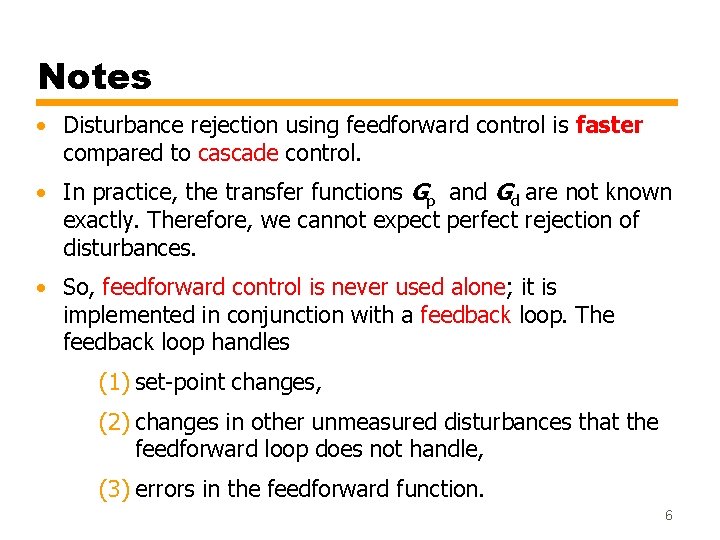
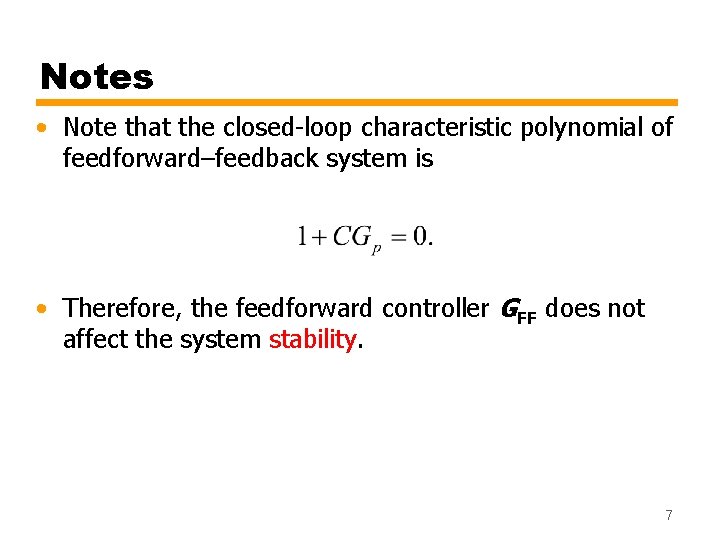
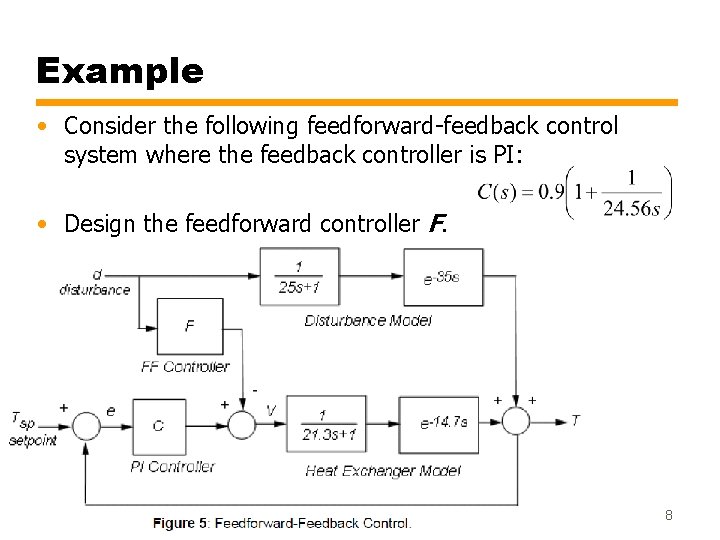
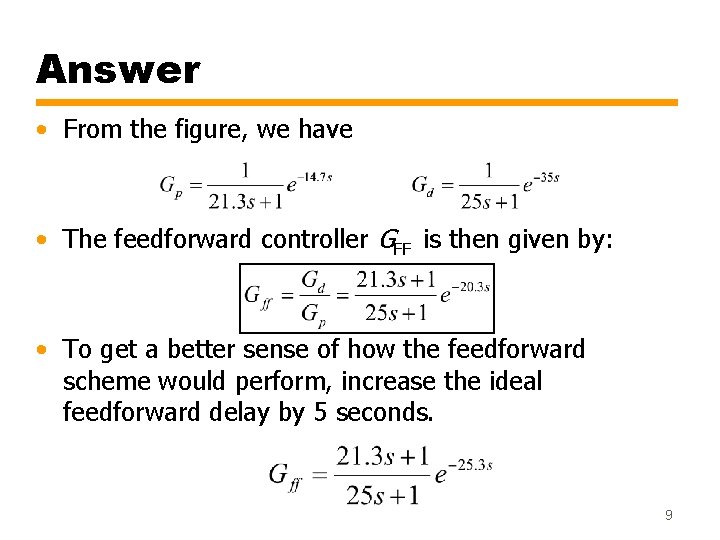
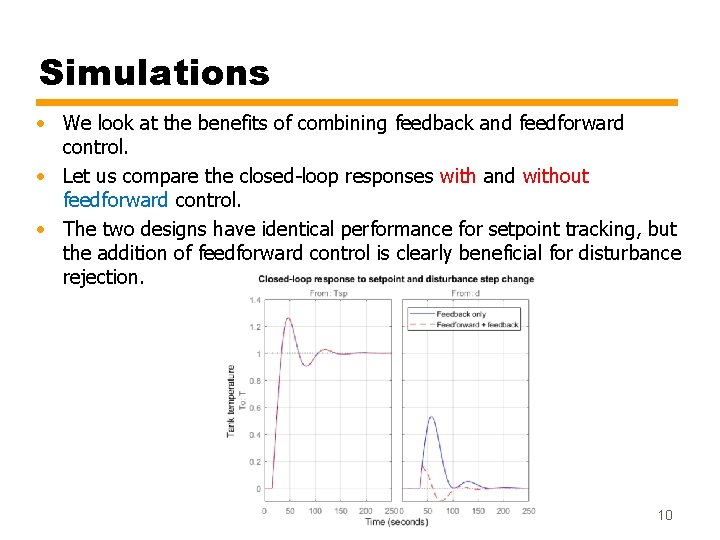
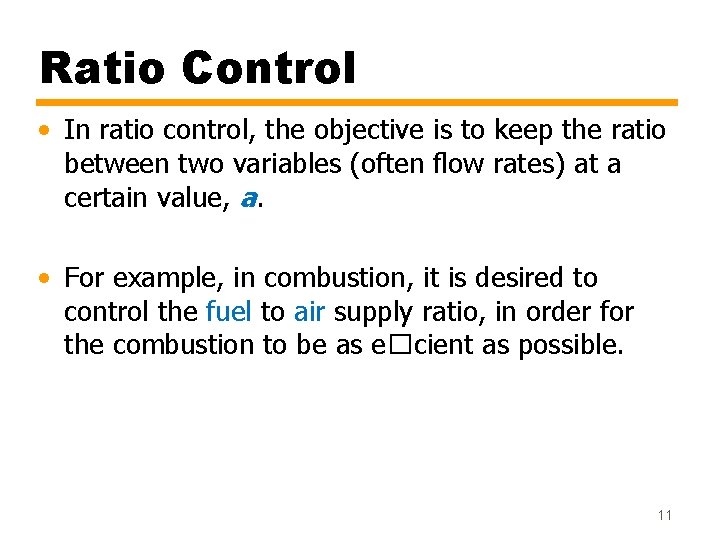
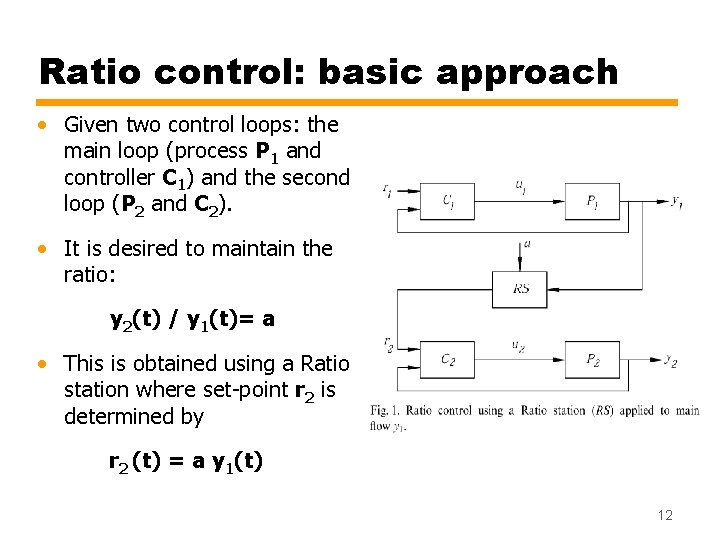
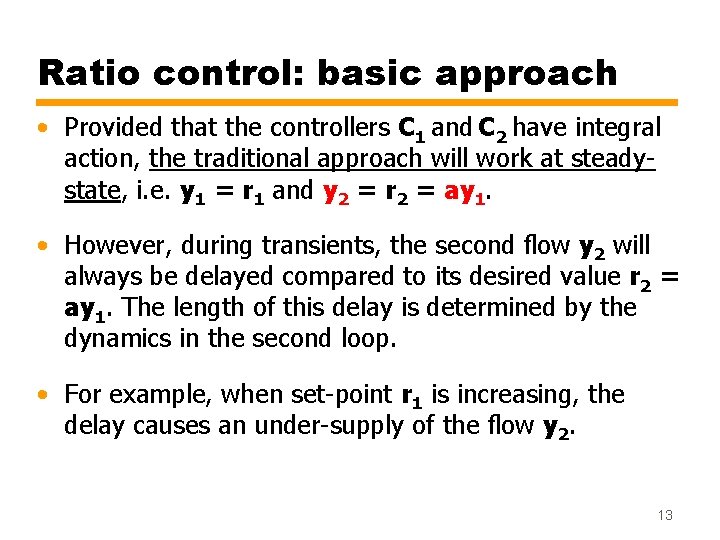
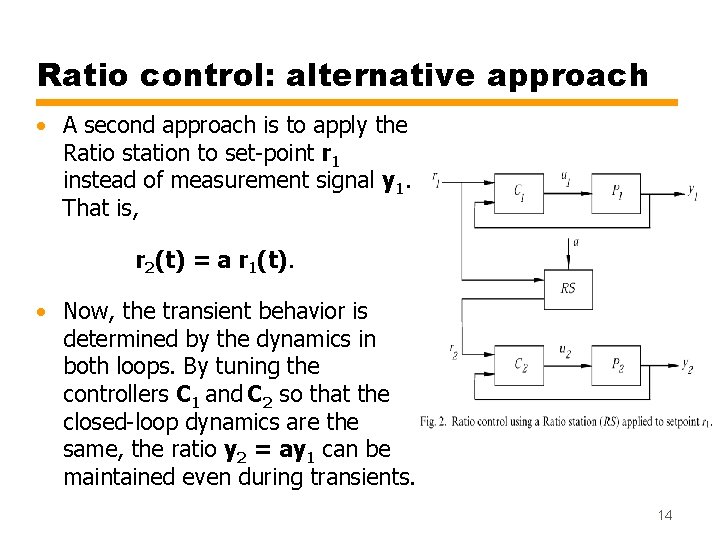
- Slides: 14
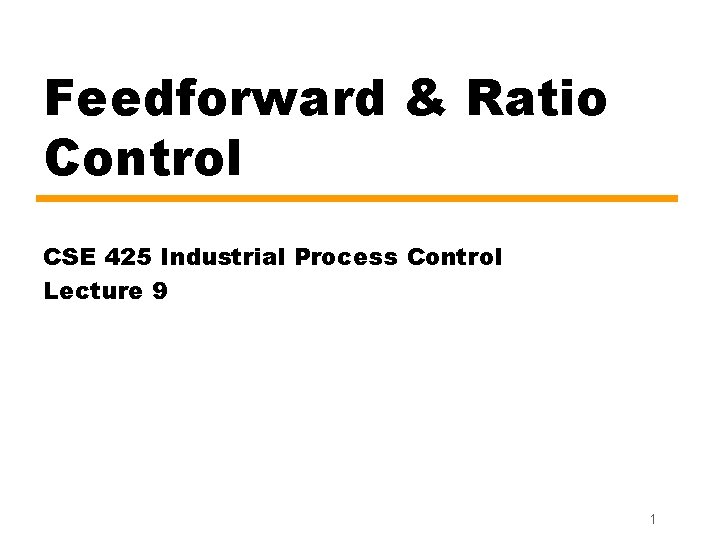
Feedforward & Ratio Control CSE 425 Industrial Process Control Lecture 9 1
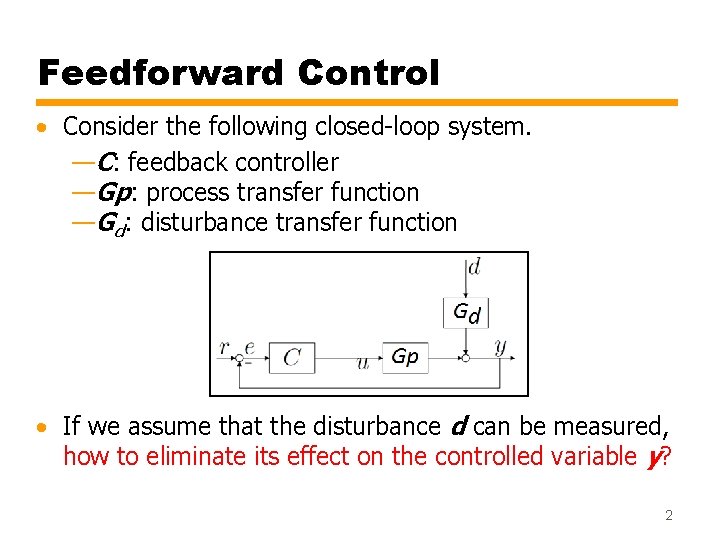
Feedforward Control • Consider the following closed-loop system. —C: feedback controller —Gp: process transfer function —Gd: disturbance transfer function • If we assume that the disturbance d can be measured, how to eliminate its effect on the controlled variable y? 2
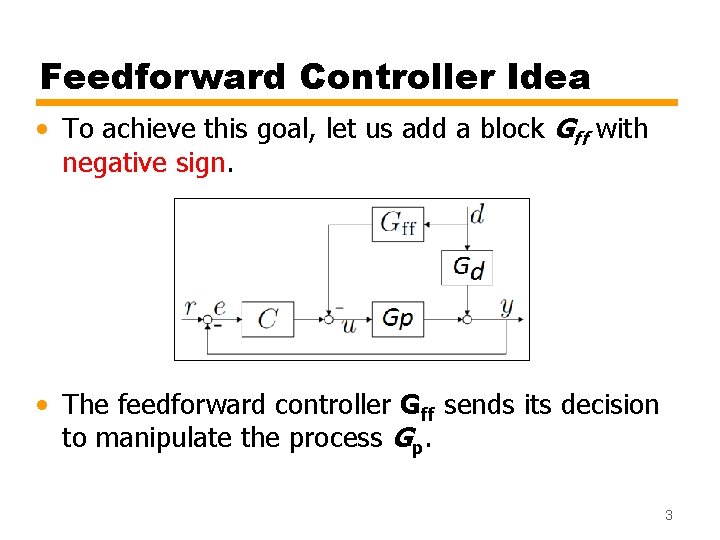
Feedforward Controller Idea • To achieve this goal, let us add a block Gff with negative sign. • The feedforward controller Gff sends its decision to manipulate the process Gp. 3
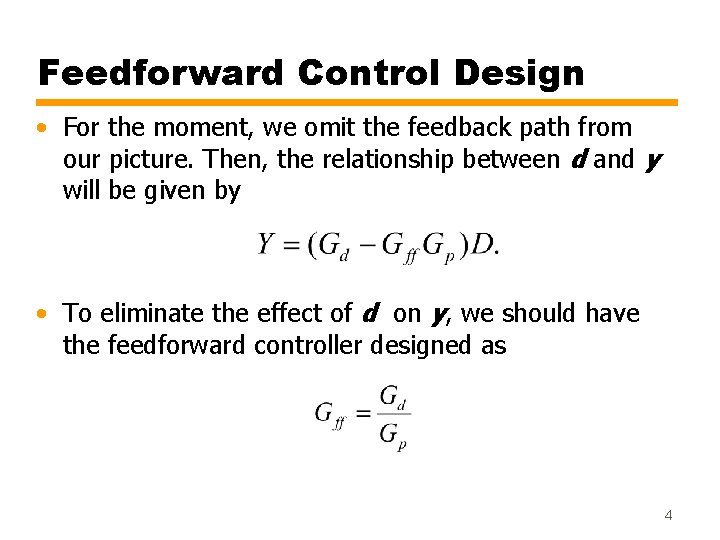
Feedforward Control Design • For the moment, we omit the feedback path from our picture. Then, the relationship between d and y will be given by • To eliminate the effect of d on y, we should have the feedforward controller designed as 4
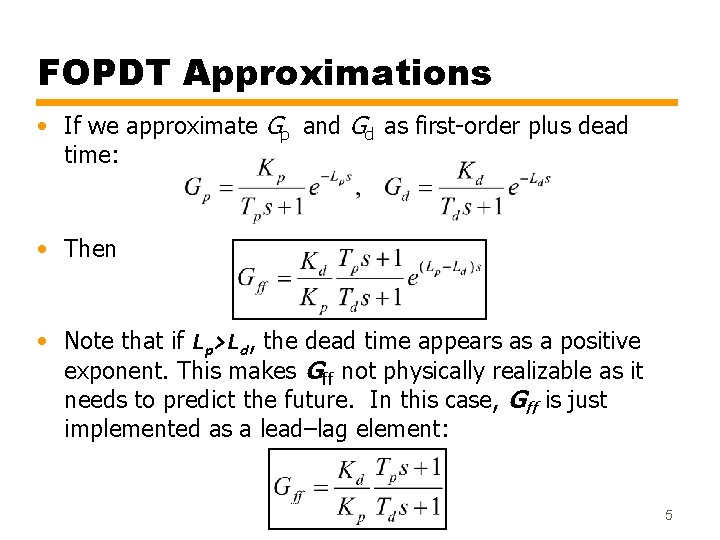
FOPDT Approximations • If we approximate Gp and Gd as first-order plus dead time: • Then • Note that if Lp>Ld, the dead time appears as a positive exponent. This makes Gff not physically realizable as it needs to predict the future. In this case, Gff is just implemented as a lead–lag element: 5
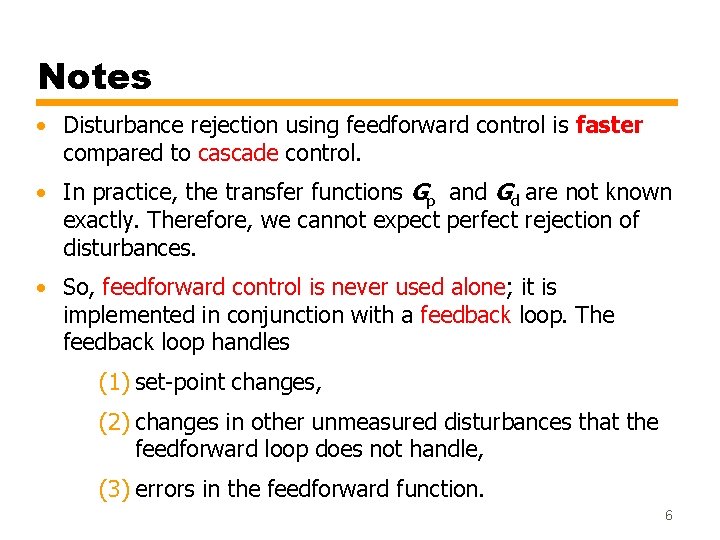
Notes • Disturbance rejection using feedforward control is faster compared to cascade control. • In practice, the transfer functions Gp and Gd are not known exactly. Therefore, we cannot expect perfect rejection of disturbances. • So, feedforward control is never used alone; it is implemented in conjunction with a feedback loop. The feedback loop handles (1) set-point changes, (2) changes in other unmeasured disturbances that the feedforward loop does not handle, (3) errors in the feedforward function. 6
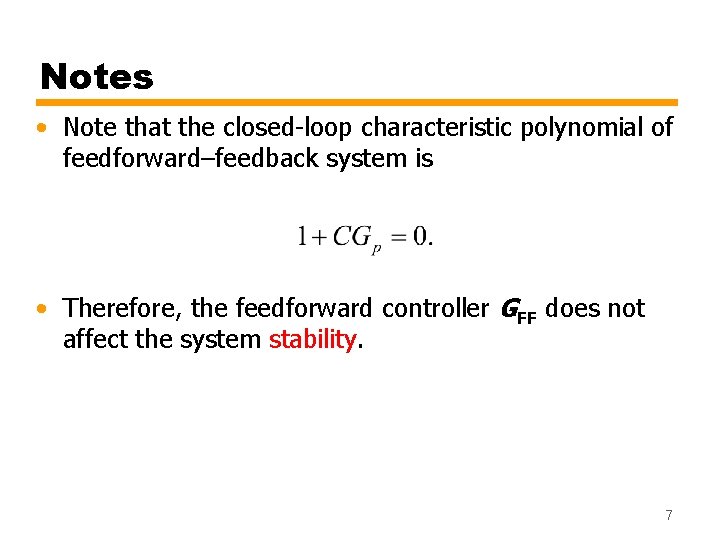
Notes • Note that the closed-loop characteristic polynomial of feedforward–feedback system is • Therefore, the feedforward controller GFF does not affect the system stability. 7
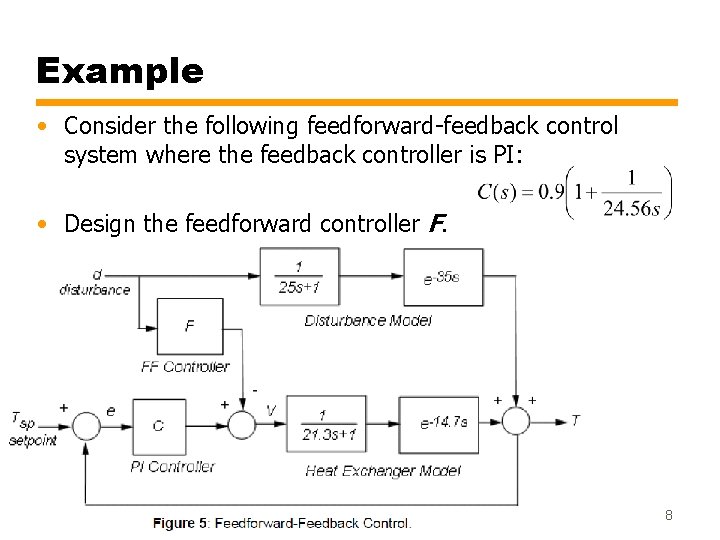
Example • Consider the following feedforward-feedback control system where the feedback controller is PI: • Design the feedforward controller F. 8
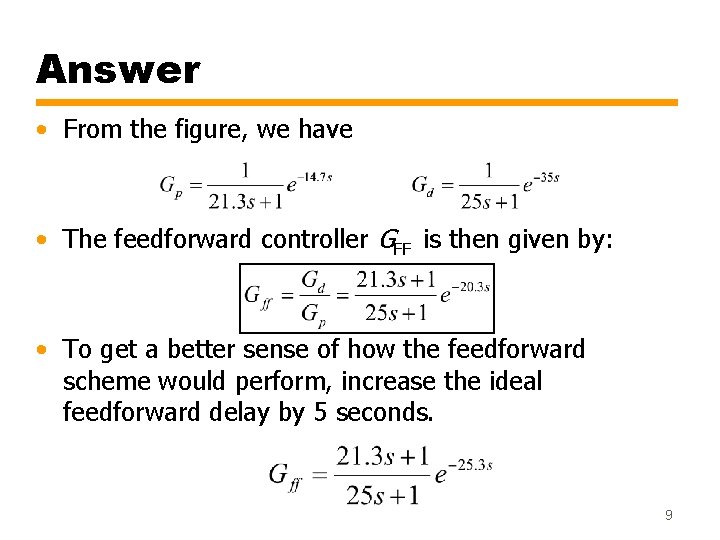
Answer • From the figure, we have • The feedforward controller GFF is then given by: • To get a better sense of how the feedforward scheme would perform, increase the ideal feedforward delay by 5 seconds. 9
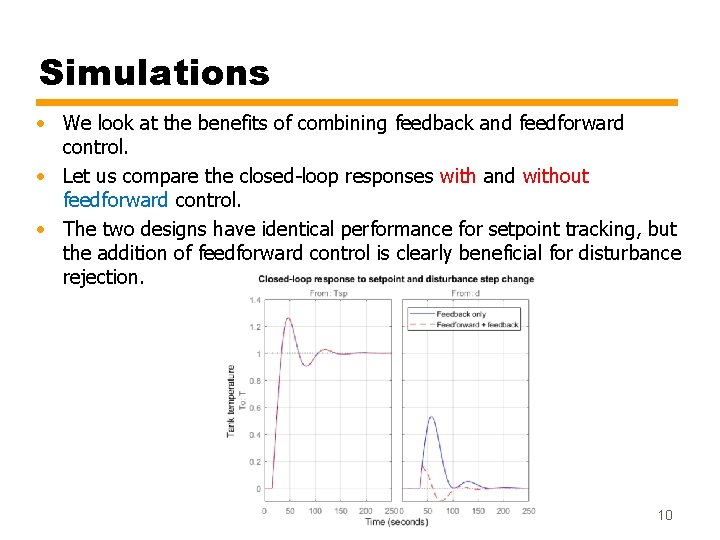
Simulations • We look at the benefits of combining feedback and feedforward control. • Let us compare the closed-loop responses with and without feedforward control. • The two designs have identical performance for setpoint tracking, but the addition of feedforward control is clearly beneficial for disturbance rejection. 10
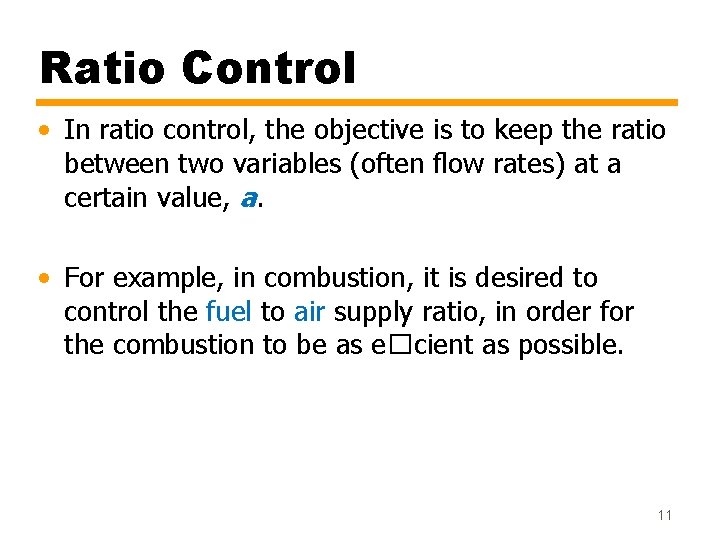
Ratio Control • In ratio control, the objective is to keep the ratio between two variables (often flow rates) at a certain value, a. • For example, in combustion, it is desired to control the fuel to air supply ratio, in order for the combustion to be as e�cient as possible. 11
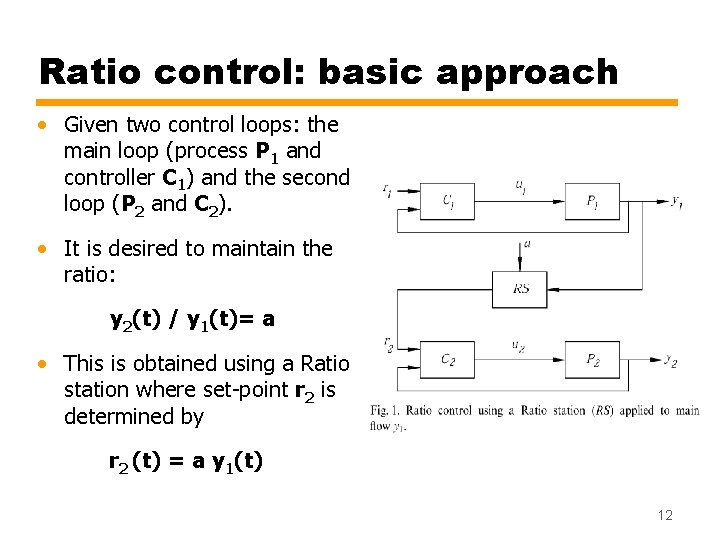
Ratio control: basic approach • Given two control loops: the main loop (process P 1 and controller C 1) and the second loop (P 2 and C 2). • It is desired to maintain the ratio: y 2(t) / y 1(t)= a • This is obtained using a Ratio station where set-point r 2 is determined by r 2 (t) = a y 1(t) 12
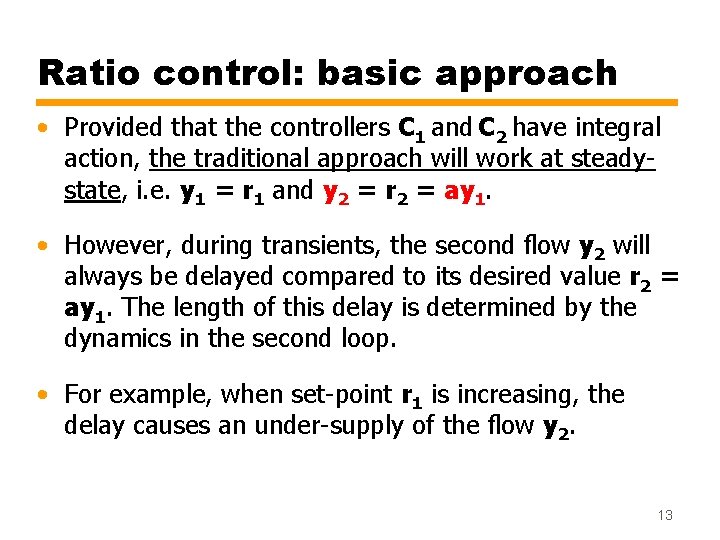
Ratio control: basic approach • Provided that the controllers C 1 and C 2 have integral action, the traditional approach will work at steadystate, i. e. y 1 = r 1 and y 2 = r 2 = ay 1. • However, during transients, the second flow y 2 will always be delayed compared to its desired value r 2 = ay 1. The length of this delay is determined by the dynamics in the second loop. • For example, when set-point r 1 is increasing, the delay causes an under-supply of the flow y 2. 13
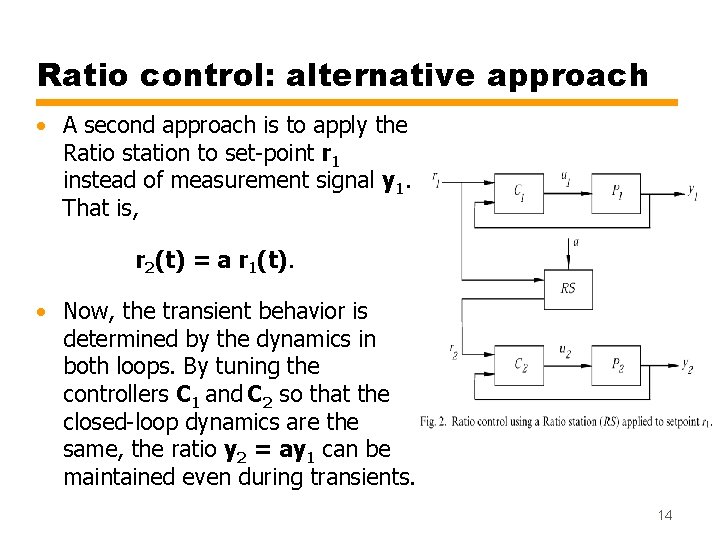
Ratio control: alternative approach • A second approach is to apply the Ratio station to set-point r 1 instead of measurement signal y 1. That is, r 2(t) = a r 1(t). • Now, the transient behavior is determined by the dynamics in both loops. By tuning the controllers C 1 and C 2 so that the closed-loop dynamics are the same, the ratio y 2 = ay 1 can be maintained even during transients. 14