COMETa 2020 5 th INTERNATIONAL SCIENTIFIC CONFERENCE Conference
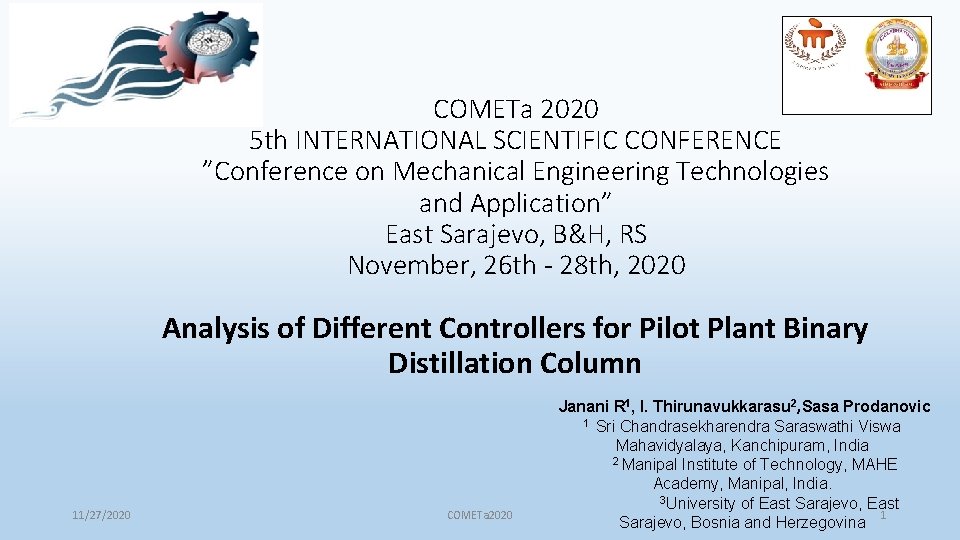
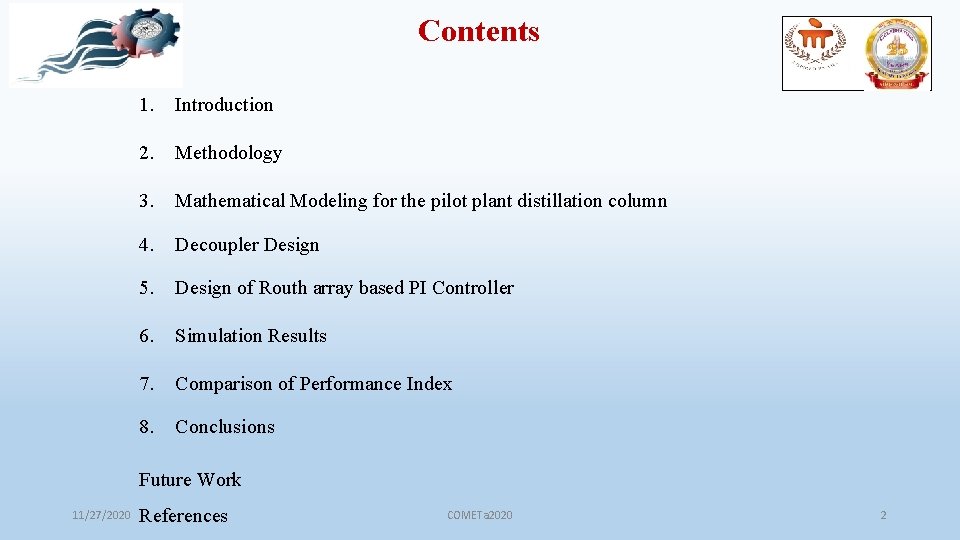
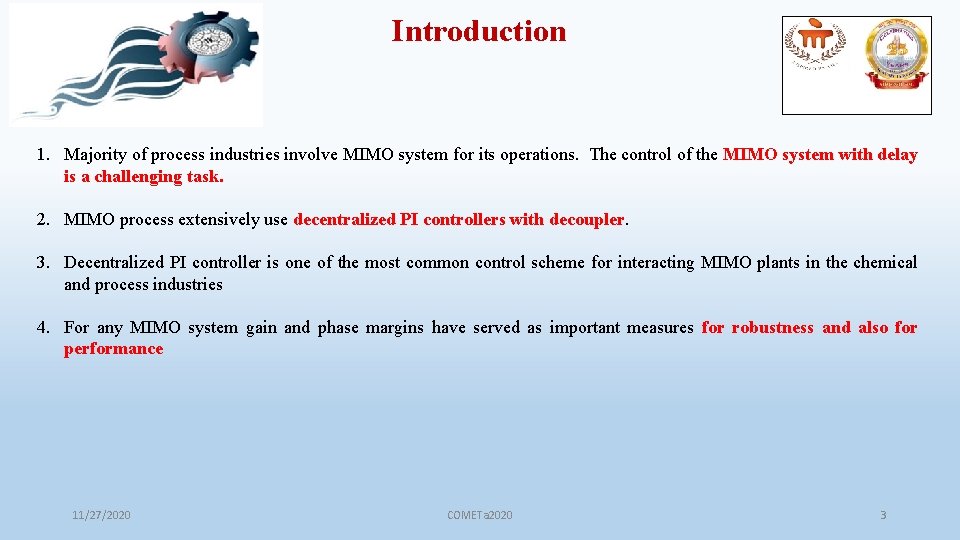
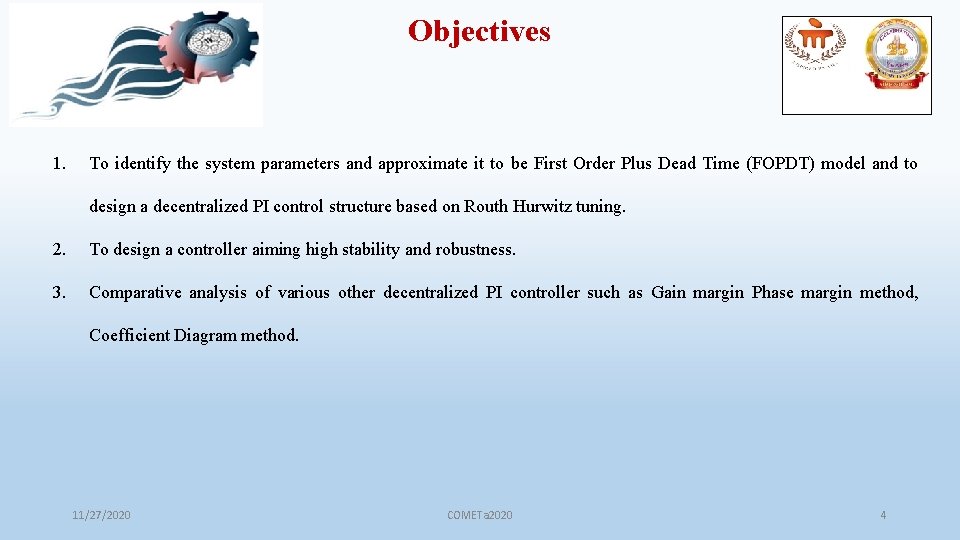
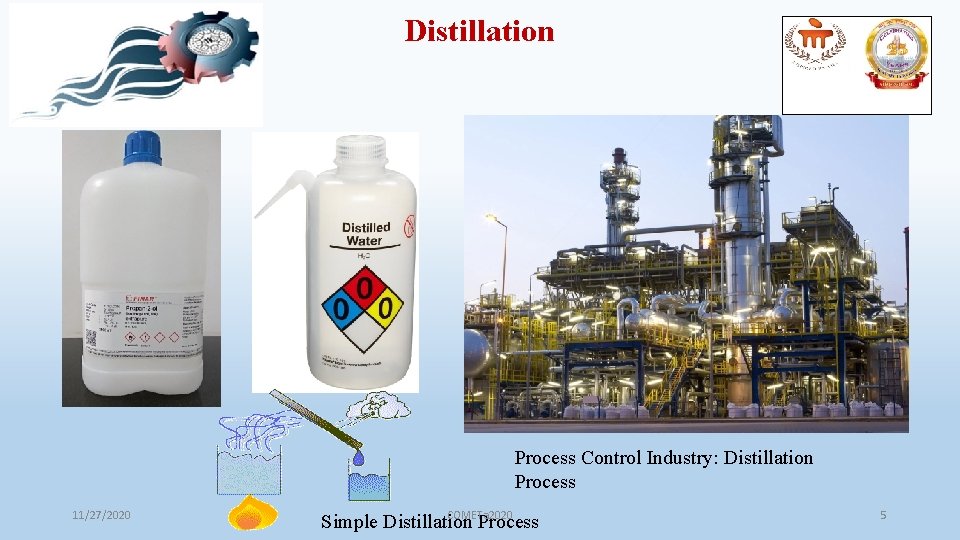
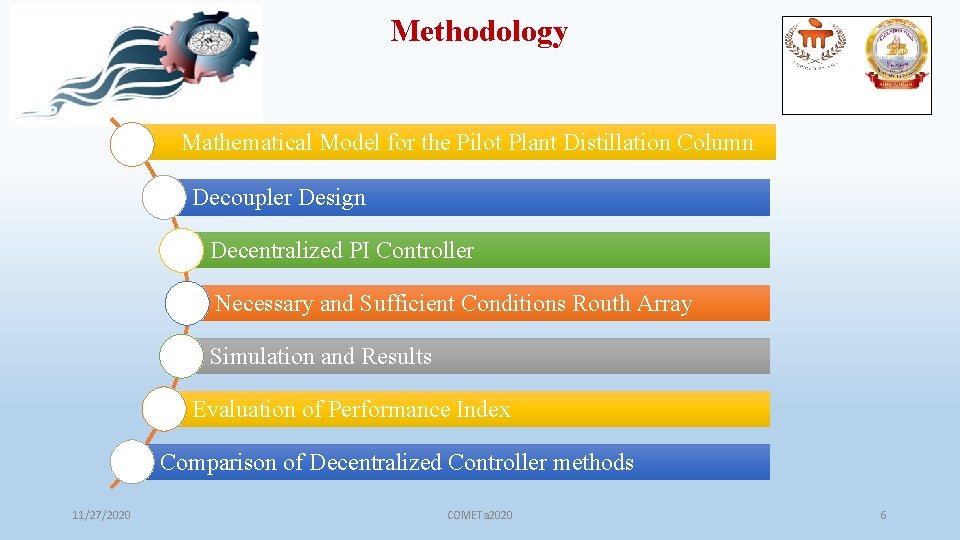
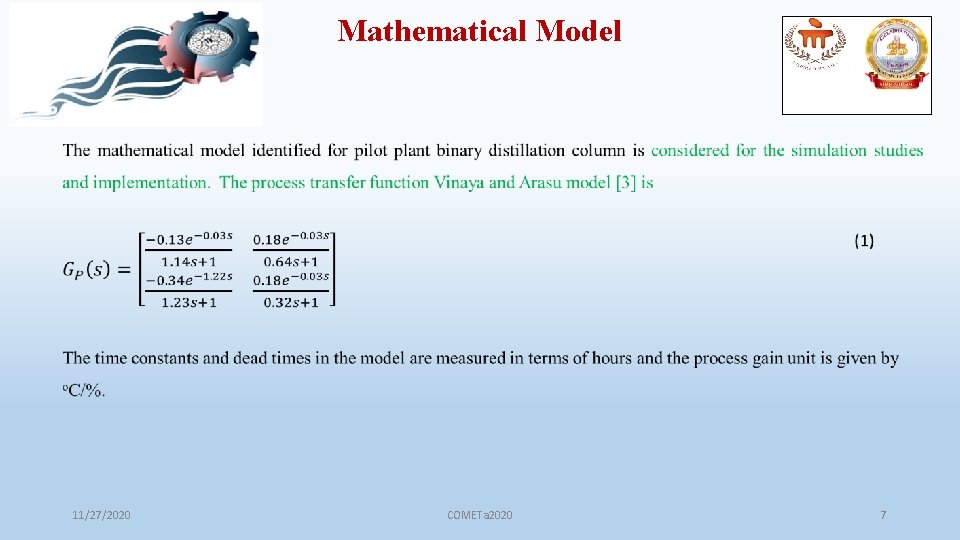
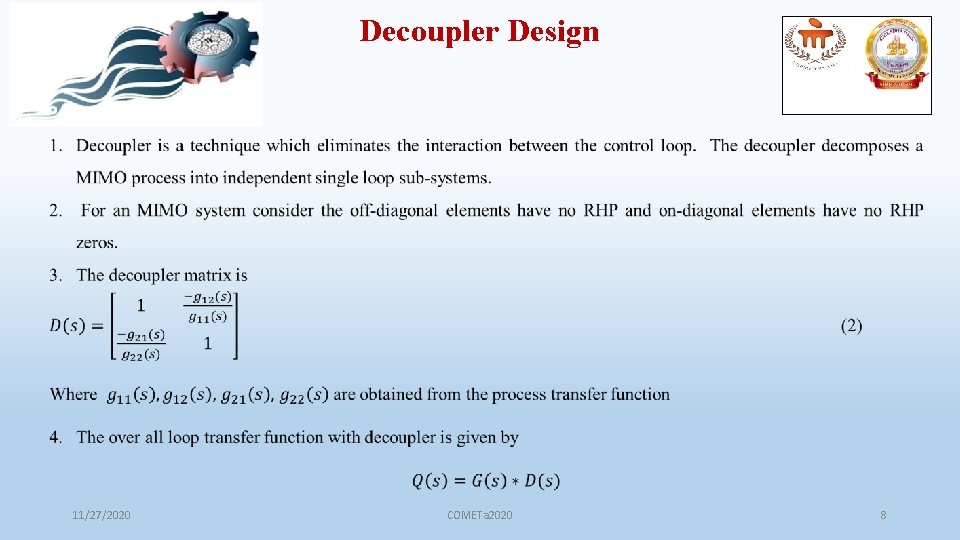
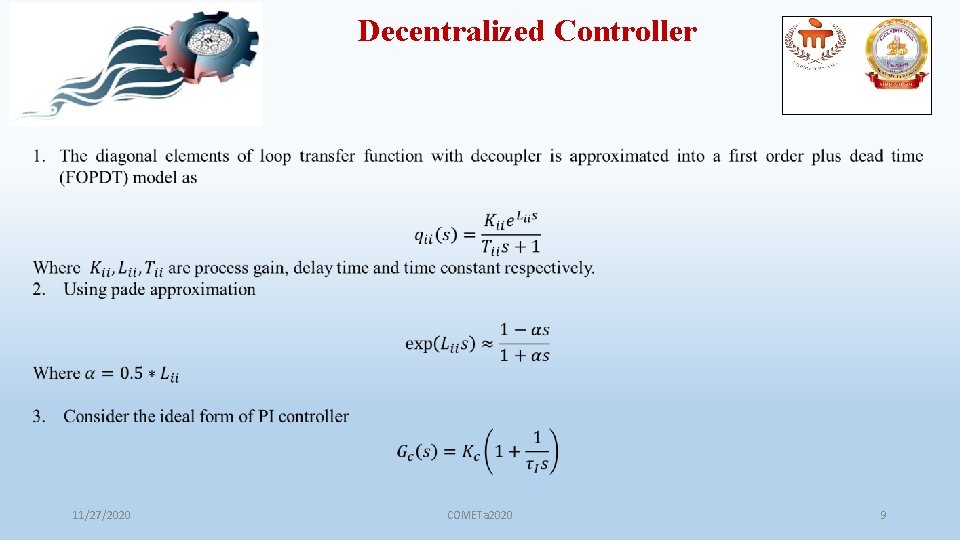
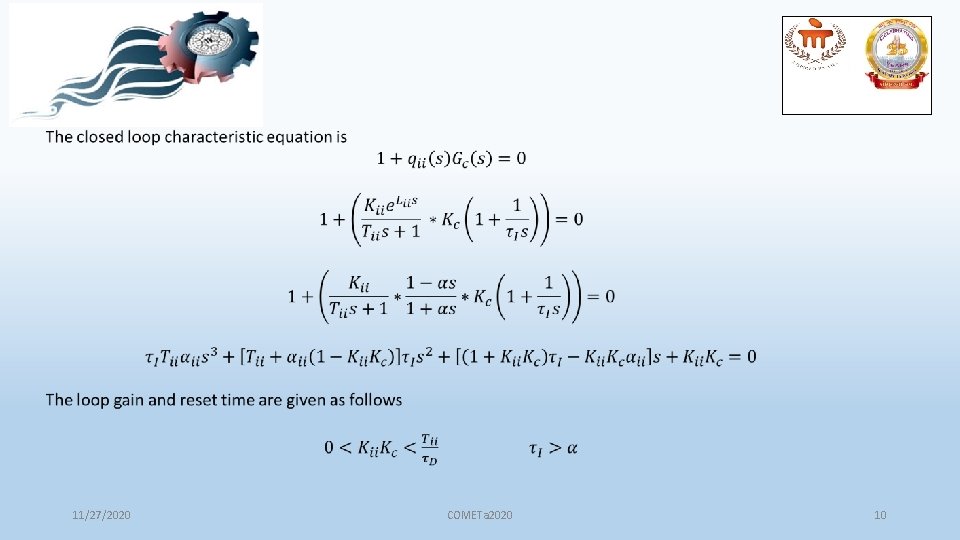
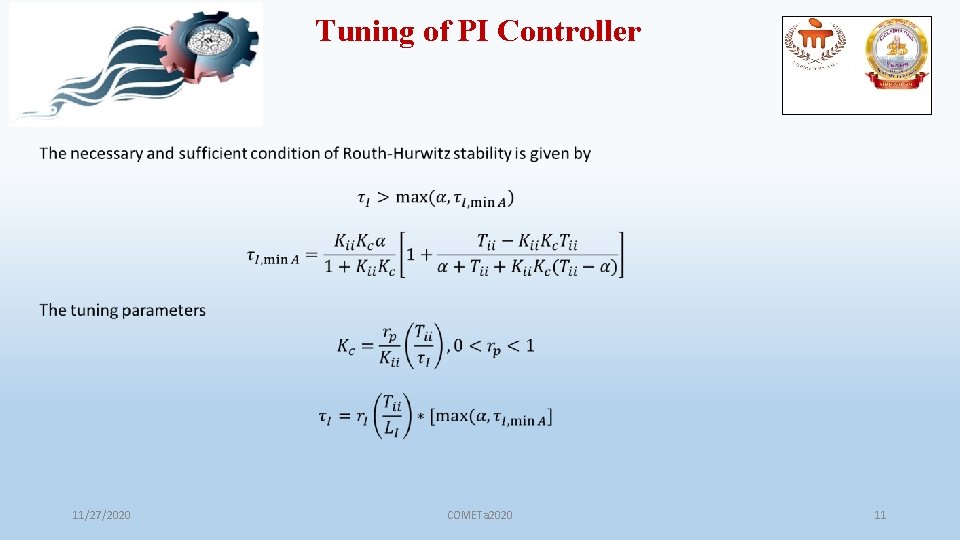
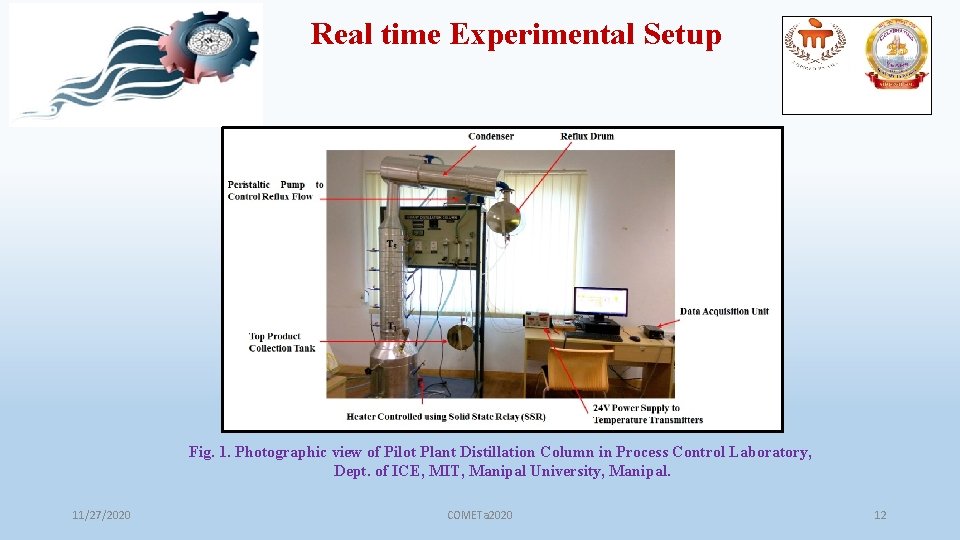
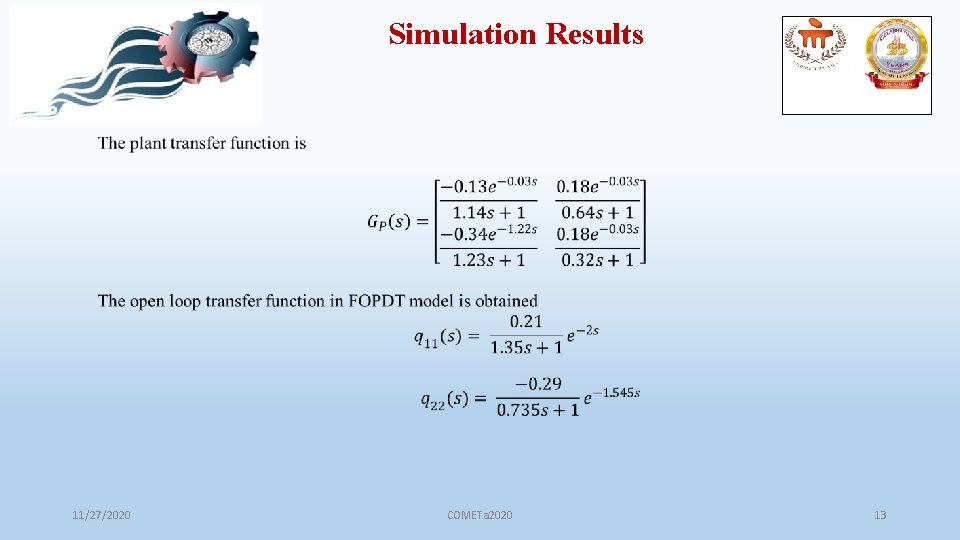
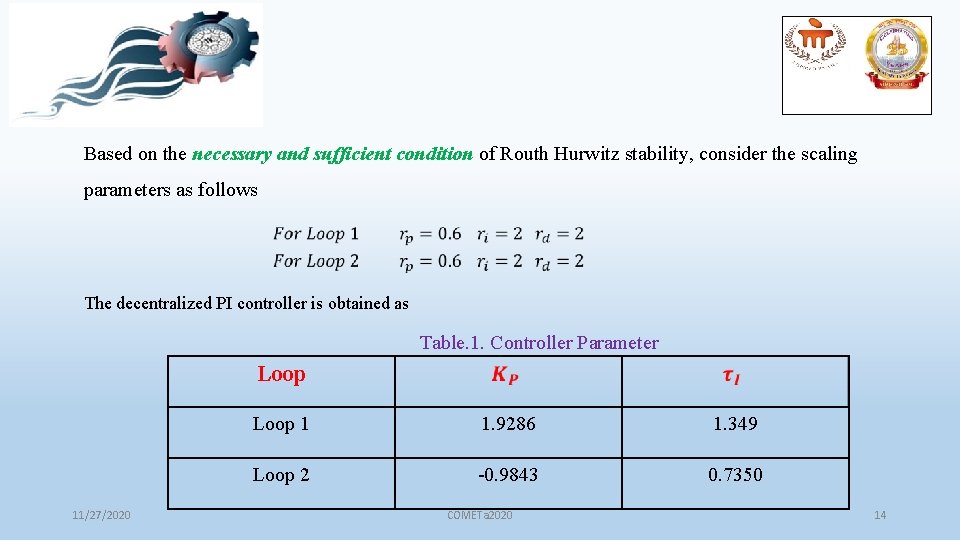
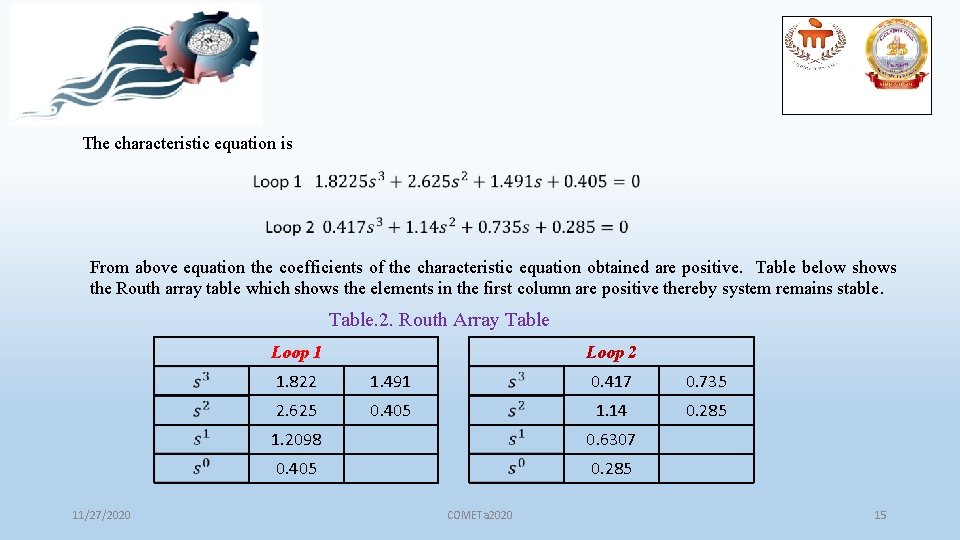
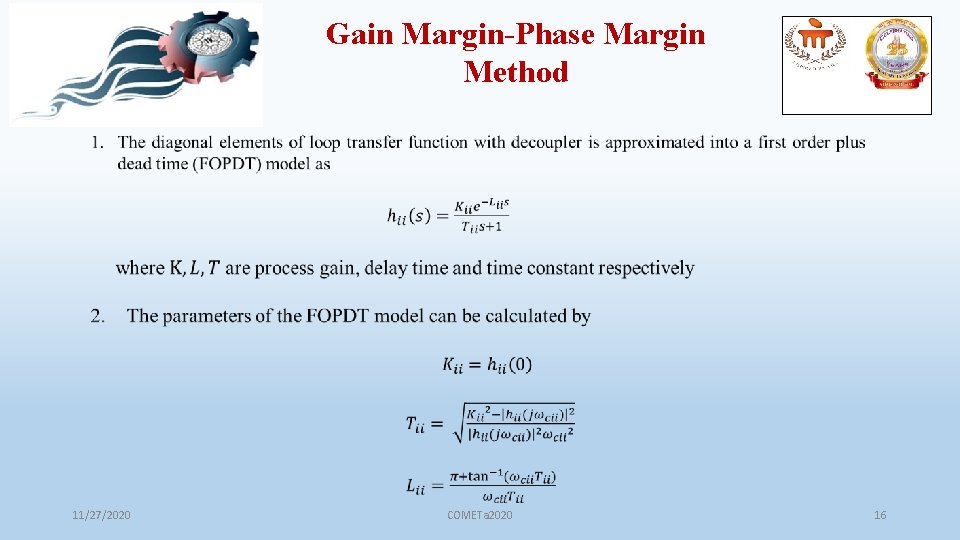
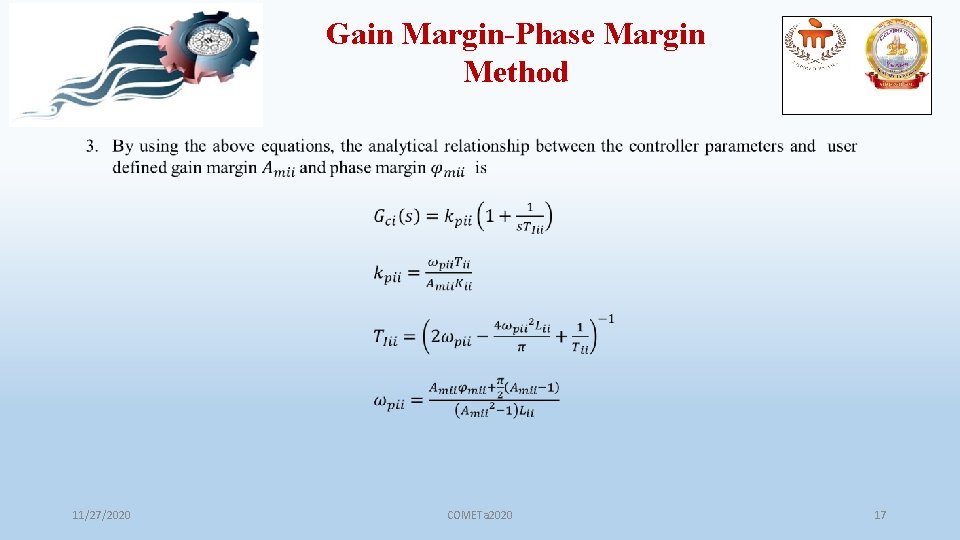
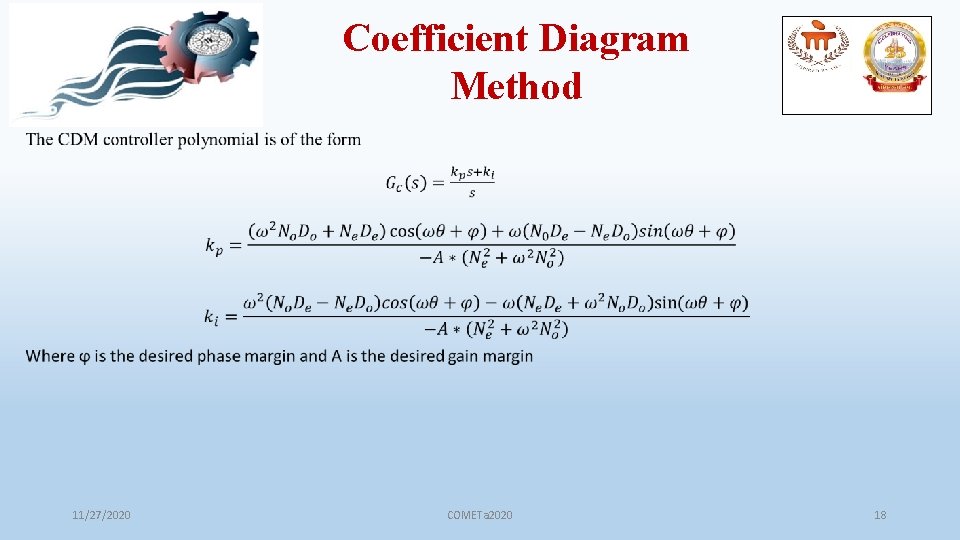
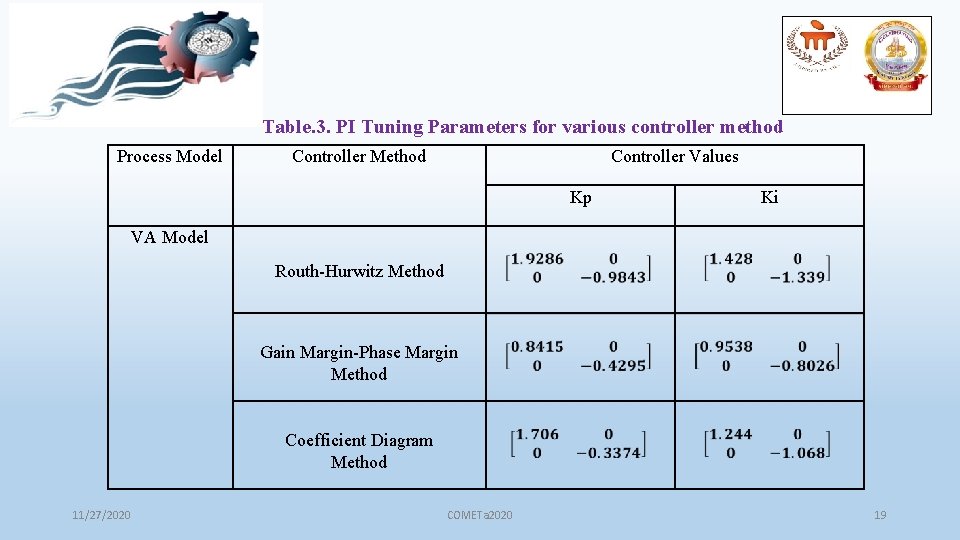
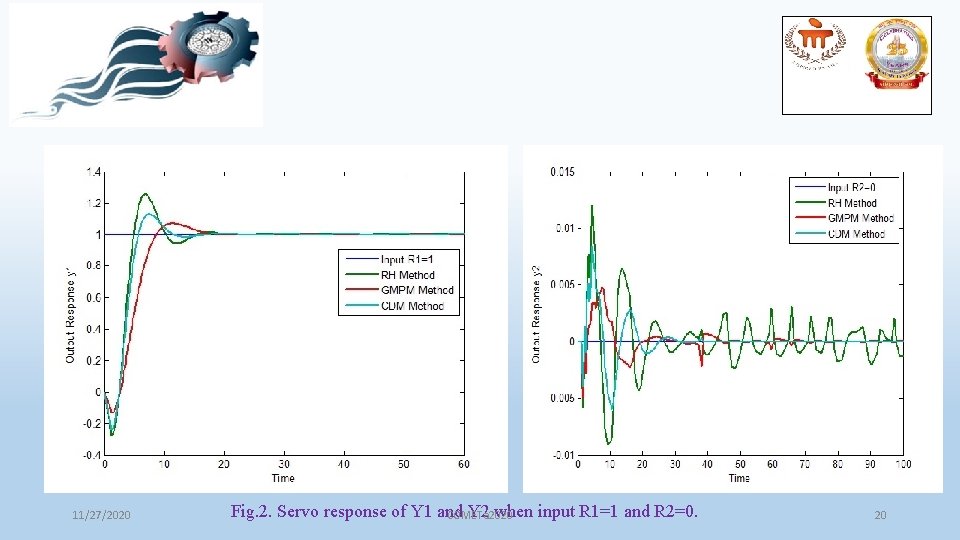
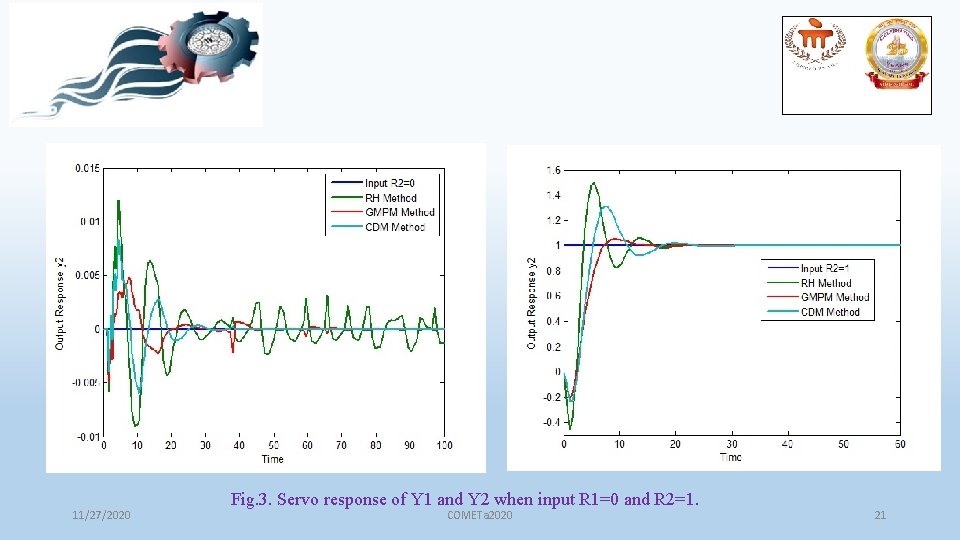
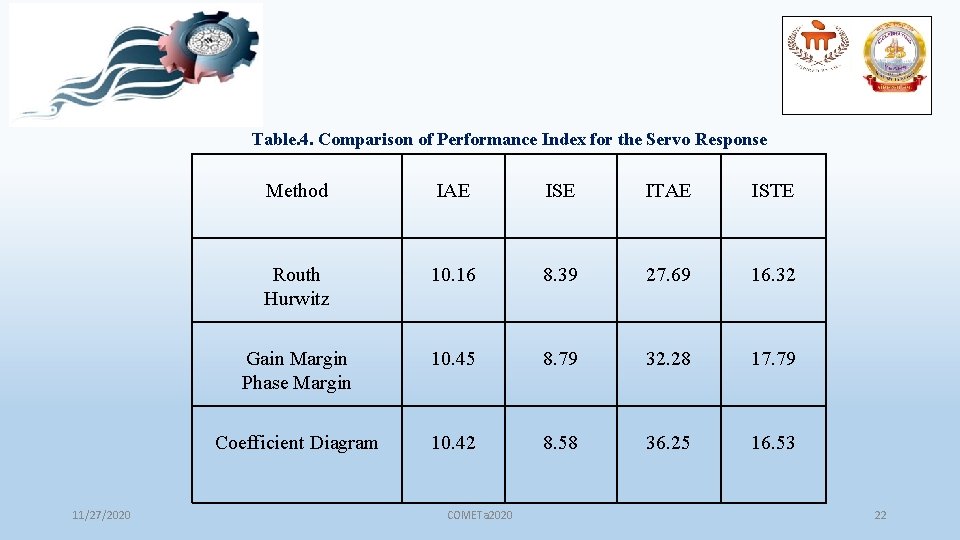
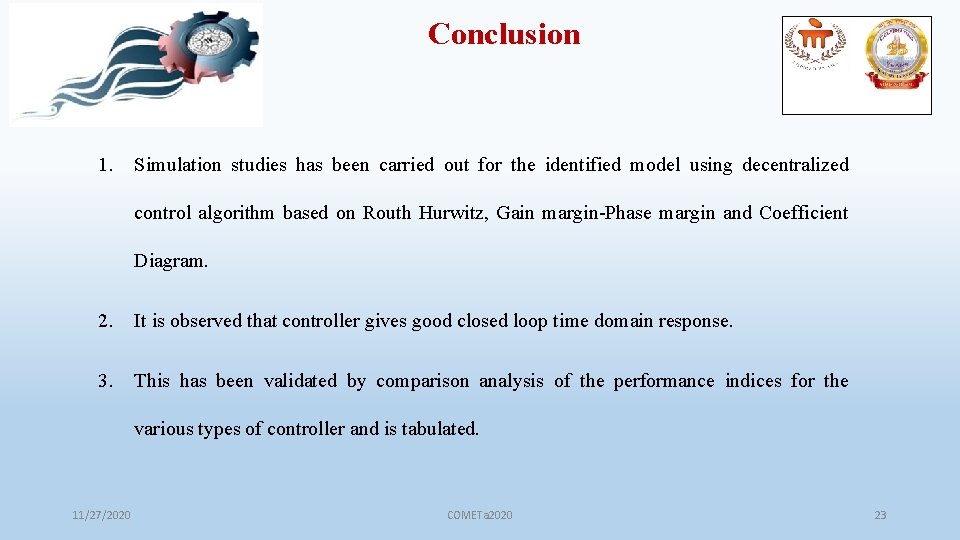
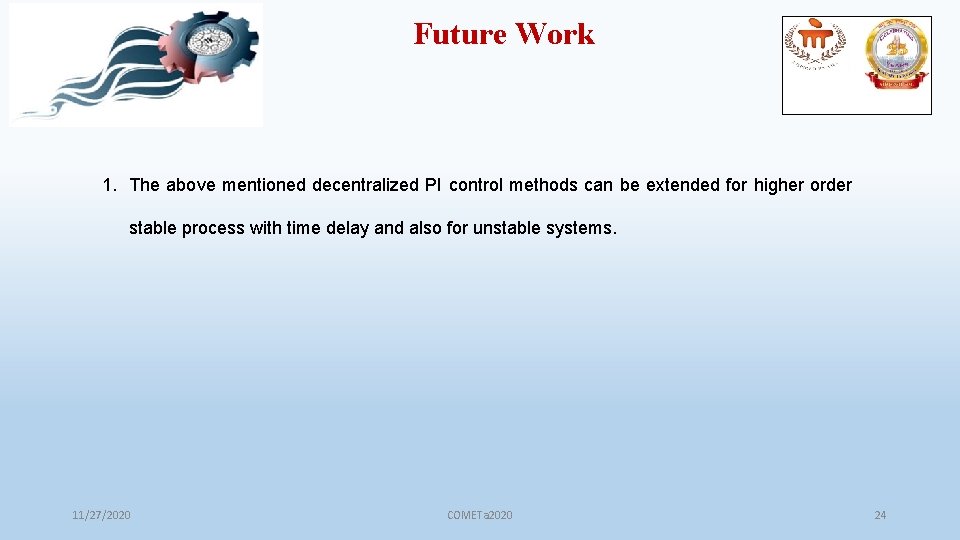
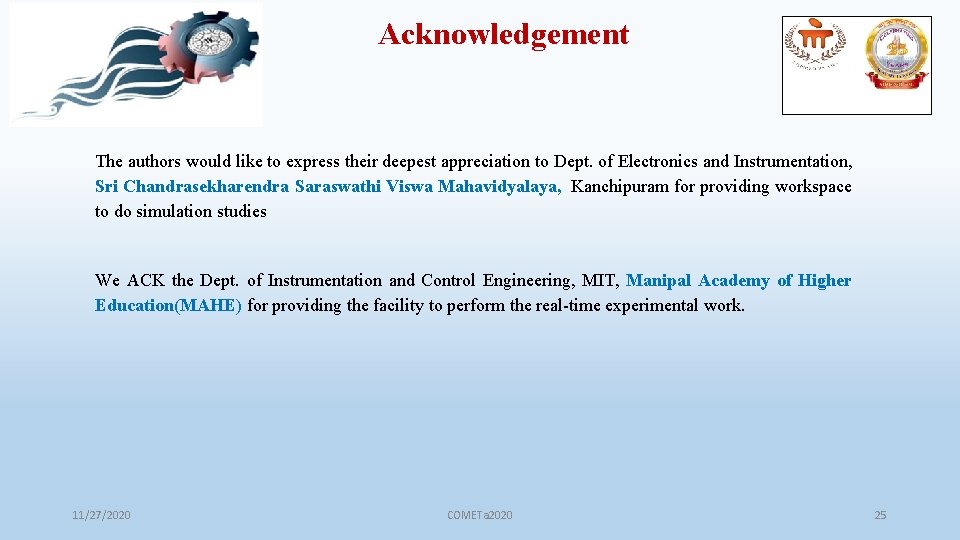
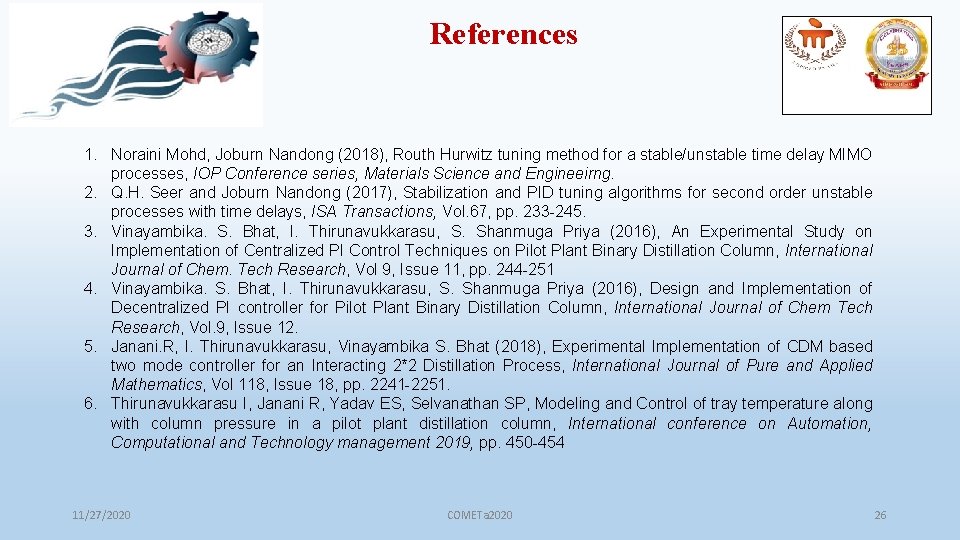
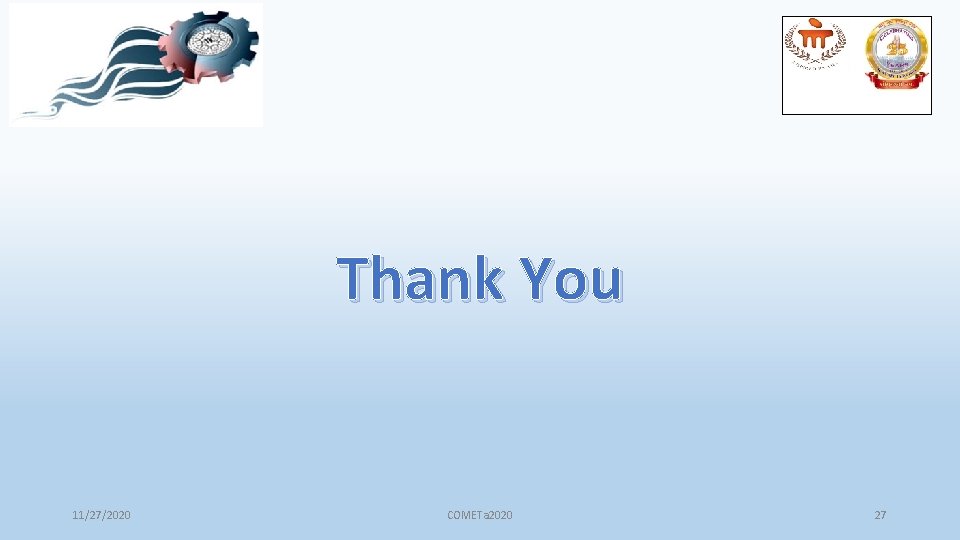
- Slides: 27
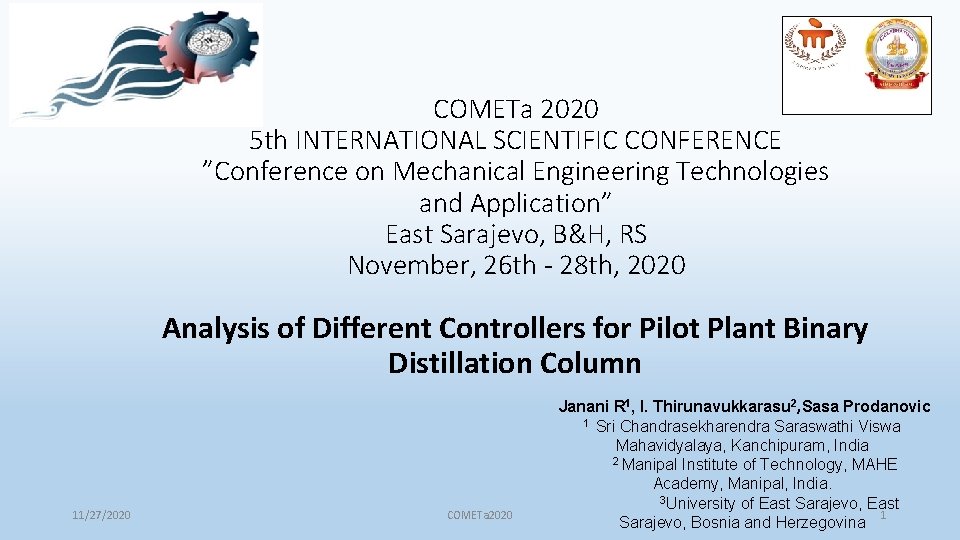
COMETa 2020 5 th INTERNATIONAL SCIENTIFIC CONFERENCE ”Conference on Mechanical Engineering Technologies and Application” East Sarajevo, B&H, RS November, 26 th - 28 th, 2020 Analysis of Different Controllers for Pilot Plant Binary Distillation Column 11/27/2020 COMETa 2020 Janani R 1, I. Thirunavukkarasu 2, Sasa Prodanovic 1 Sri Chandrasekharendra Saraswathi Viswa Mahavidyalaya, Kanchipuram, India 2 Manipal Institute of Technology, MAHE Academy, Manipal, India. 3 University of East Sarajevo, East 1 Sarajevo, Bosnia and Herzegovina
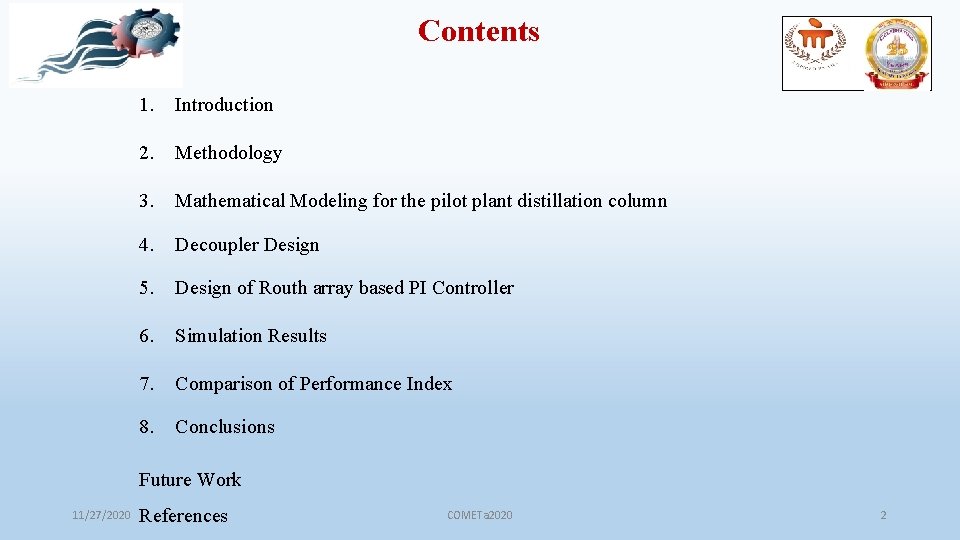
Contents 1. Introduction 2. Methodology 3. Mathematical Modeling for the pilot plant distillation column 4. Decoupler Design 5. Design of Routh array based PI Controller 6. Simulation Results 7. Comparison of Performance Index 8. Conclusions Future Work 11/27/2020 References COMETa 2020 2
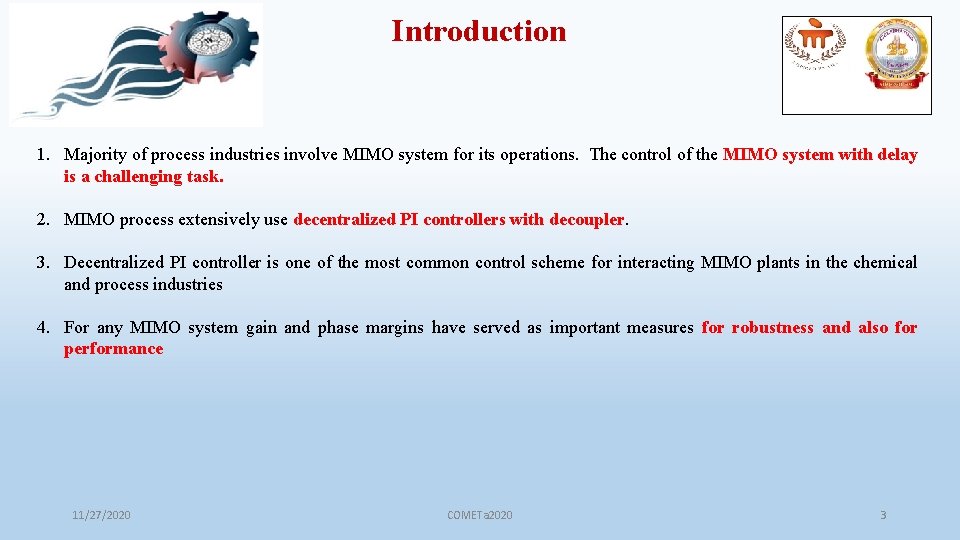
Introduction 1. Majority of process industries involve MIMO system for its operations. The control of the MIMO system with delay is a challenging task. 2. MIMO process extensively use decentralized PI controllers with decoupler. 3. Decentralized PI controller is one of the most common control scheme for interacting MIMO plants in the chemical and process industries 4. For any MIMO system gain and phase margins have served as important measures for robustness and also for performance 11/27/2020 COMETa 2020 3
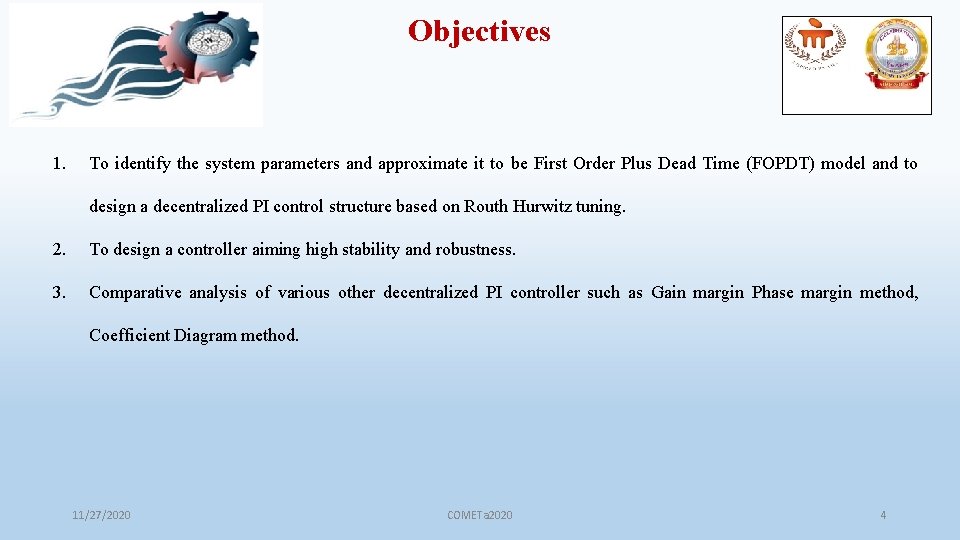
Objectives 1. To identify the system parameters and approximate it to be First Order Plus Dead Time (FOPDT) model and to design a decentralized PI control structure based on Routh Hurwitz tuning. 2. To design a controller aiming high stability and robustness. 3. Comparative analysis of various other decentralized PI controller such as Gain margin Phase margin method, Coefficient Diagram method. 11/27/2020 COMETa 2020 4
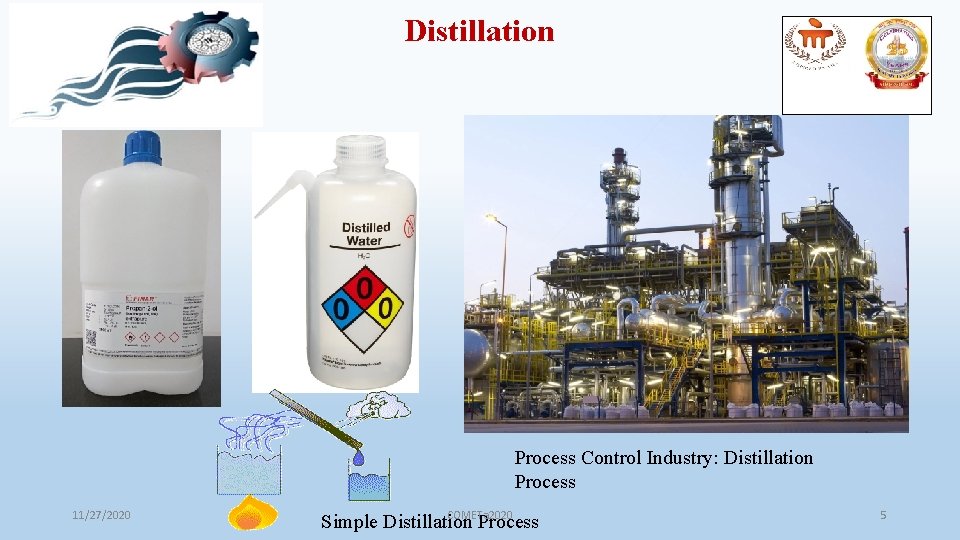
Distillation Process Control Industry: Distillation Process 11/27/2020 COMETa 2020 Simple Distillation Process 5
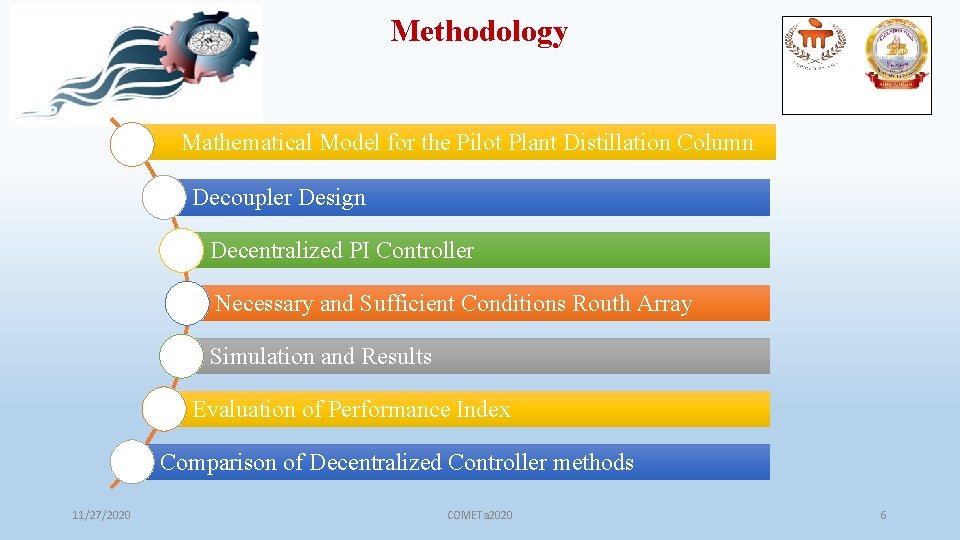
Methodology Mathematical Model for the Pilot Plant Distillation Column Decoupler Design Decentralized PI Controller Necessary and Sufficient Conditions Routh Array Simulation and Results Evaluation of Performance Index Comparison of Decentralized Controller methods 11/27/2020 COMETa 2020 6
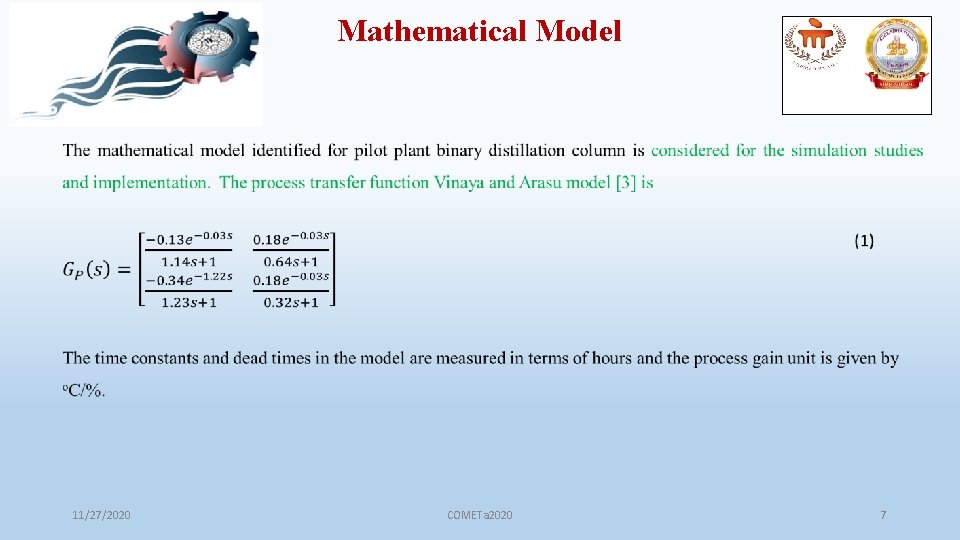
Mathematical Model 11/27/2020 COMETa 2020 7
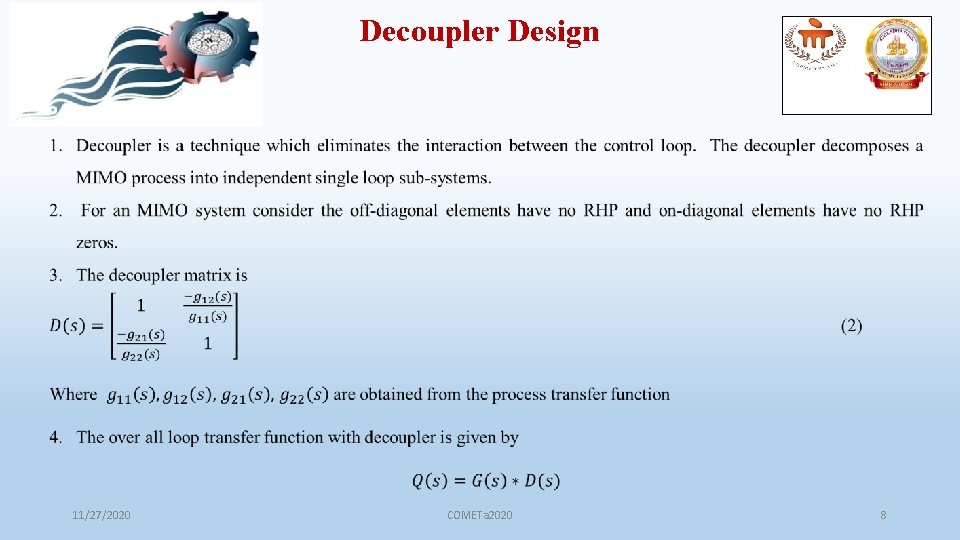
Decoupler Design 11/27/2020 COMETa 2020 8
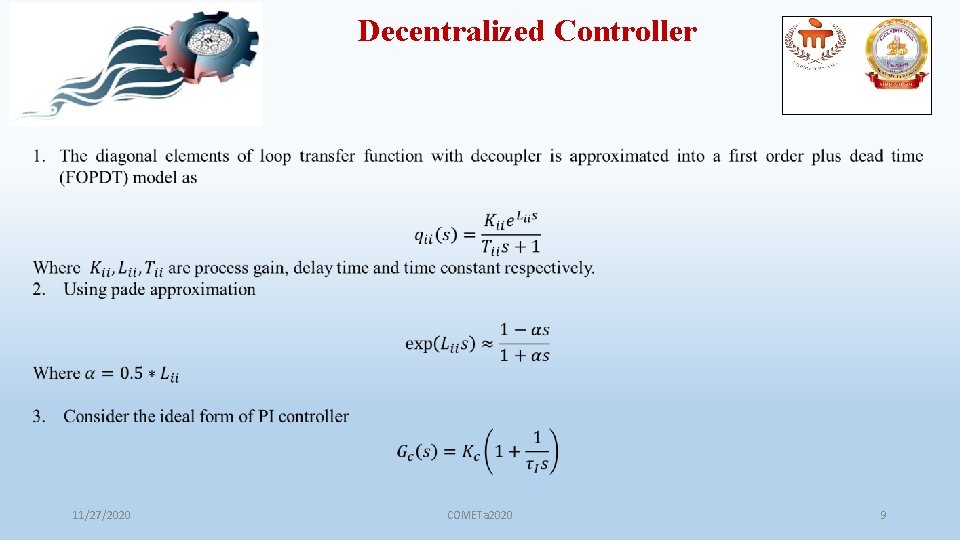
Decentralized Controller 11/27/2020 COMETa 2020 9
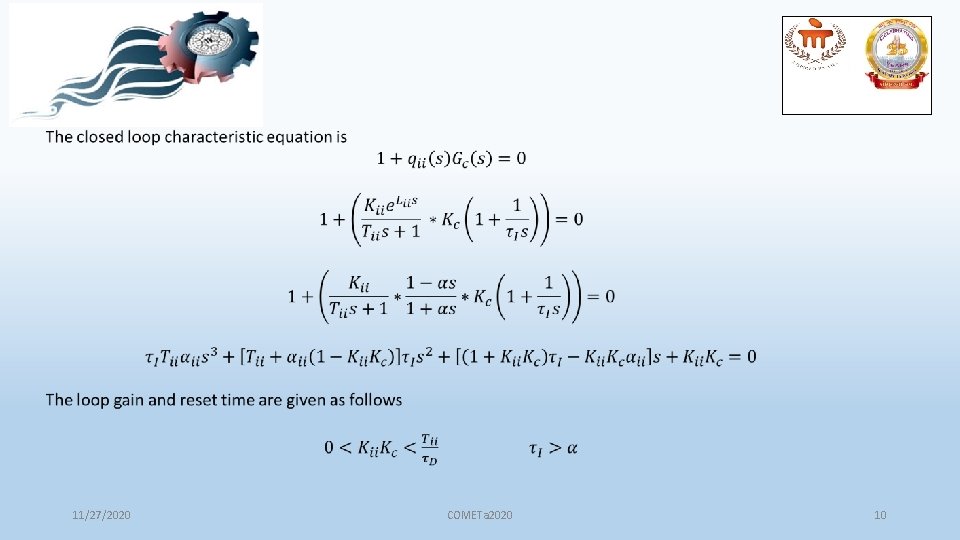
11/27/2020 COMETa 2020 10
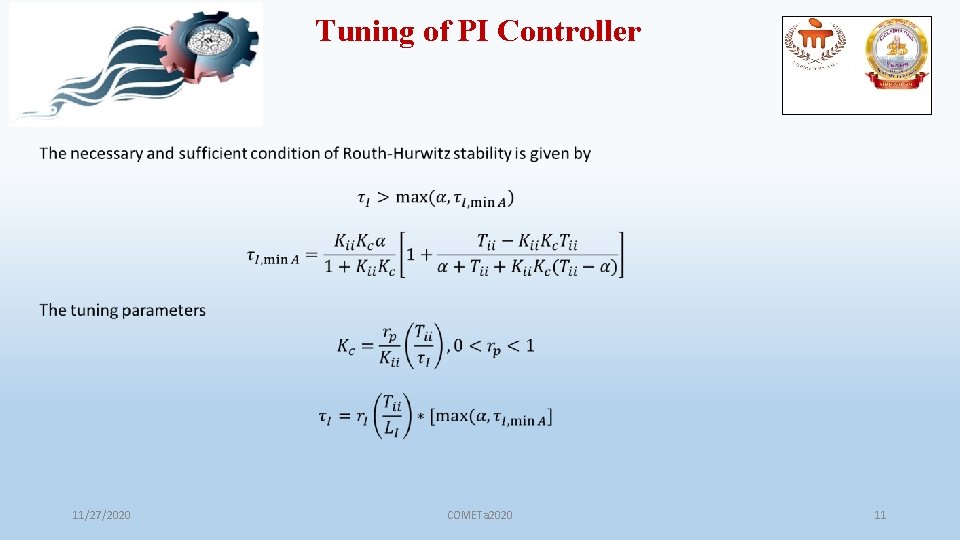
Tuning of PI Controller 11/27/2020 COMETa 2020 11
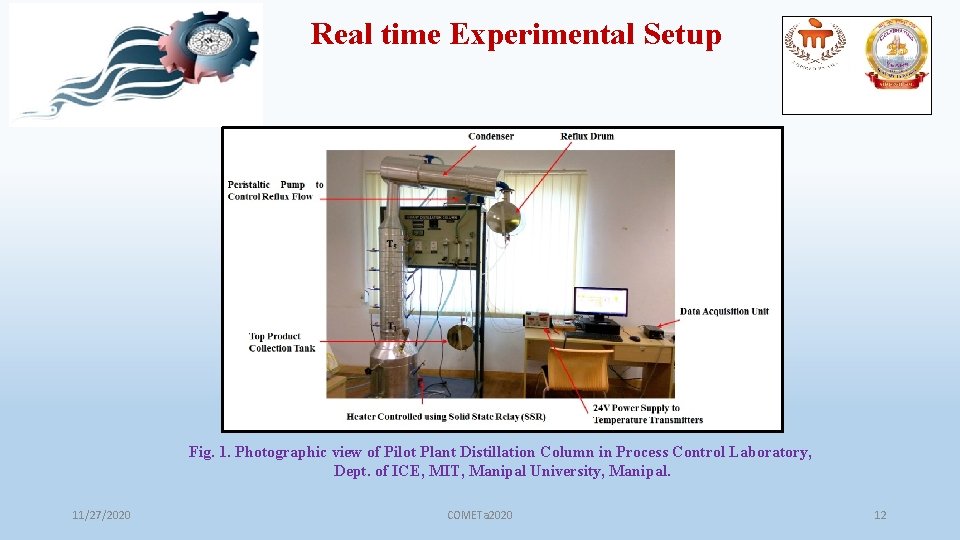
Real time Experimental Setup Fig. 1. Photographic view of Pilot Plant Distillation Column in Process Control Laboratory, Dept. of ICE, MIT, Manipal University, Manipal. 11/27/2020 COMETa 2020 12
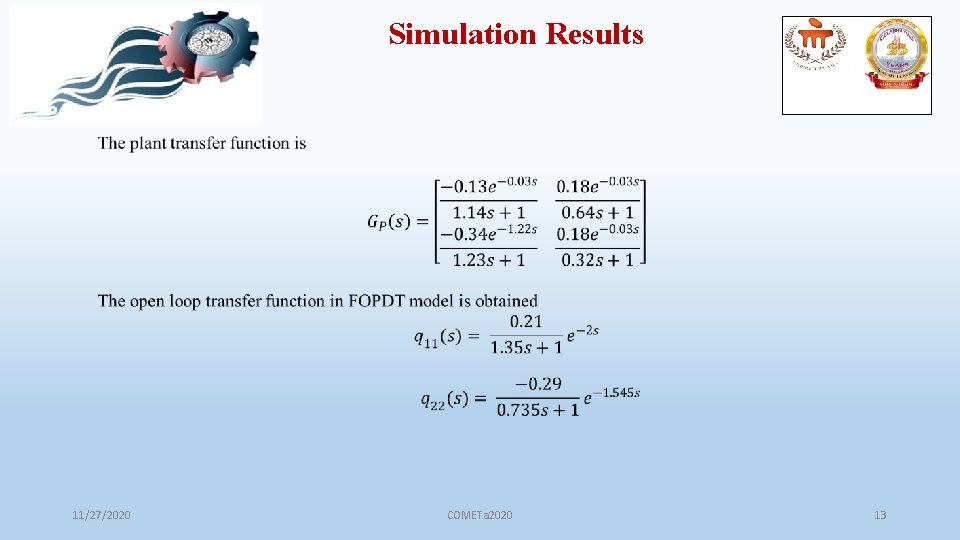
Simulation Results 11/27/2020 COMETa 2020 13
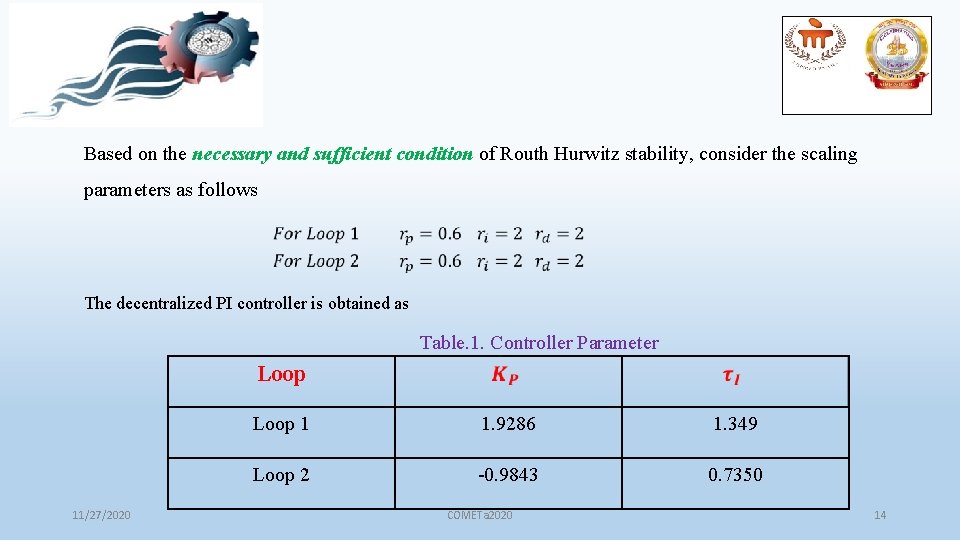
Based on the necessary and sufficient condition of Routh Hurwitz stability, consider the scaling parameters as follows The decentralized PI controller is obtained as Table. 1. Controller Parameter Loop 11/27/2020 Loop 1 1. 9286 1. 349 Loop 2 -0. 9843 0. 7350 COMETa 2020 14
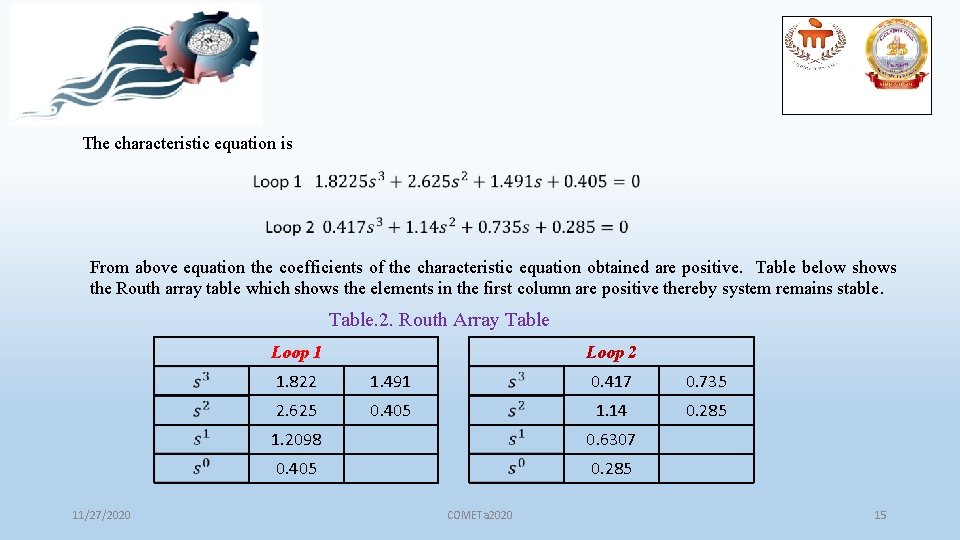
The characteristic equation is From above equation the coefficients of the characteristic equation obtained are positive. Table below shows the Routh array table which shows the elements in the first column are positive thereby system remains stable. Table. 2. Routh Array Table Loop 1 11/27/2020 Loop 2 1. 822 1. 491 0. 417 0. 735 2. 625 0. 405 1. 14 0. 285 1. 2098 0. 6307 0. 405 0. 285 COMETa 2020 15
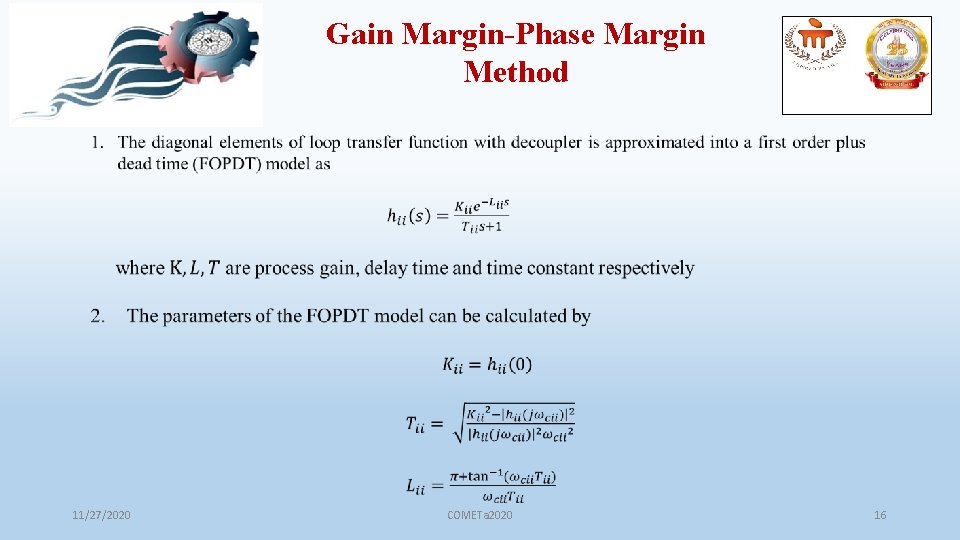
Gain Margin-Phase Margin Method 11/27/2020 COMETa 2020 16
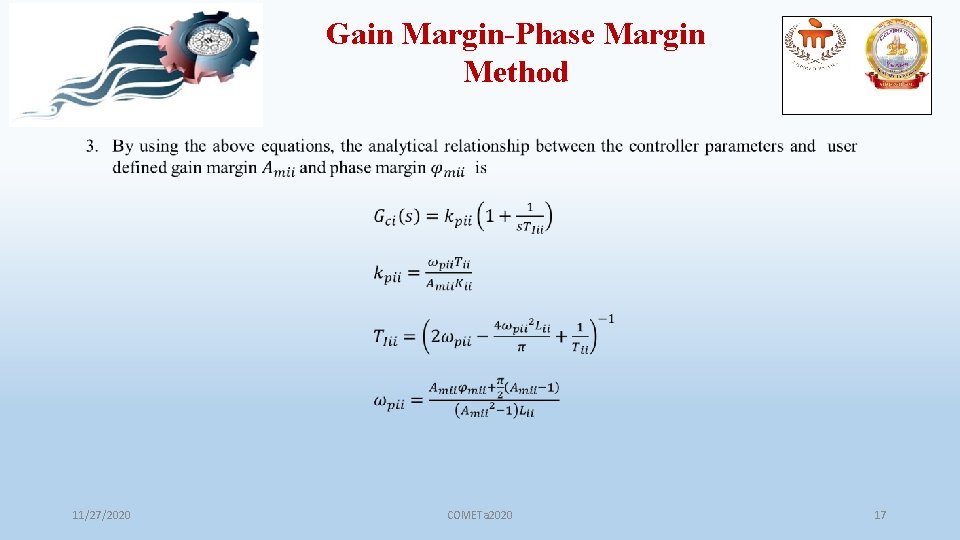
Gain Margin-Phase Margin Method 11/27/2020 COMETa 2020 17
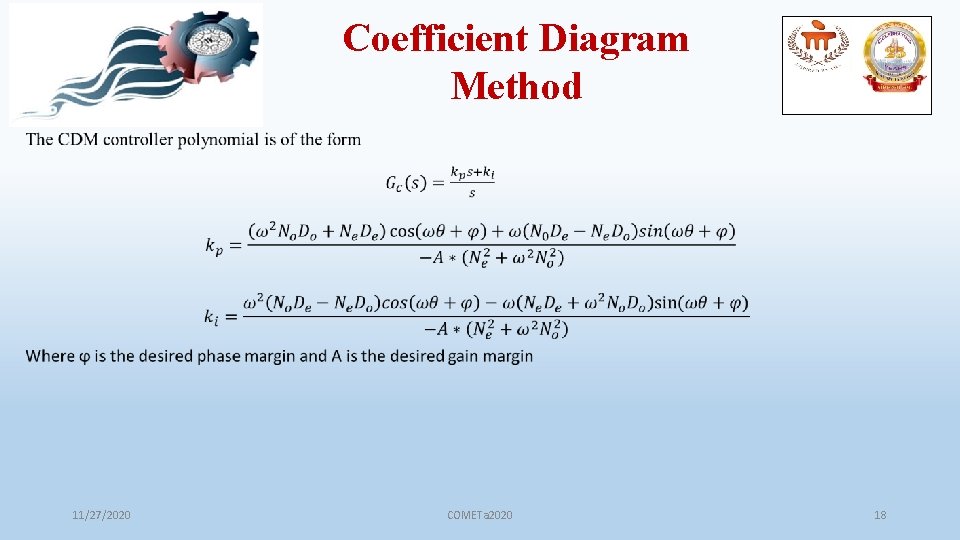
Coefficient Diagram Method 11/27/2020 COMETa 2020 18
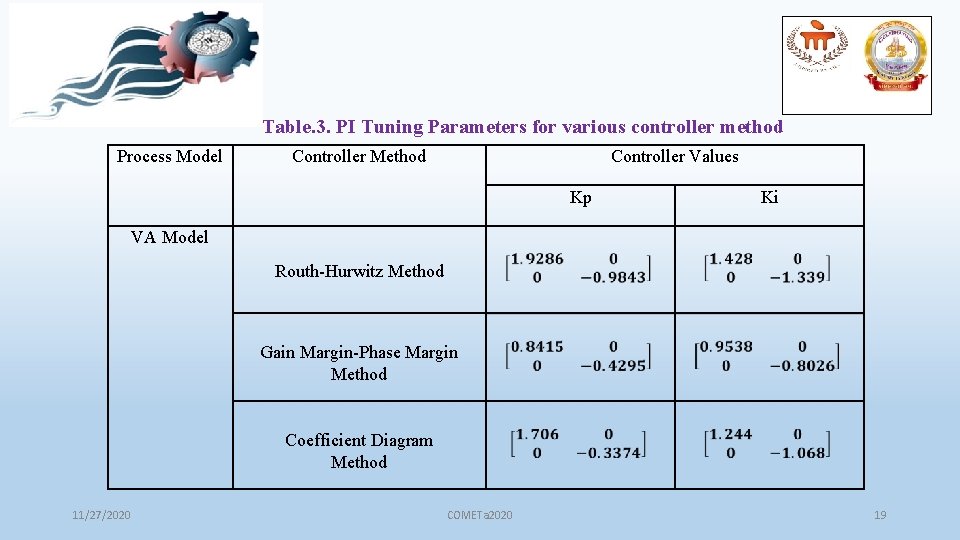
Table. 3. PI Tuning Parameters for various controller method Process Model Controller Method Controller Values Kp Ki VA Model Routh-Hurwitz Method Gain Margin-Phase Margin Method Coefficient Diagram Method 11/27/2020 COMETa 2020 19
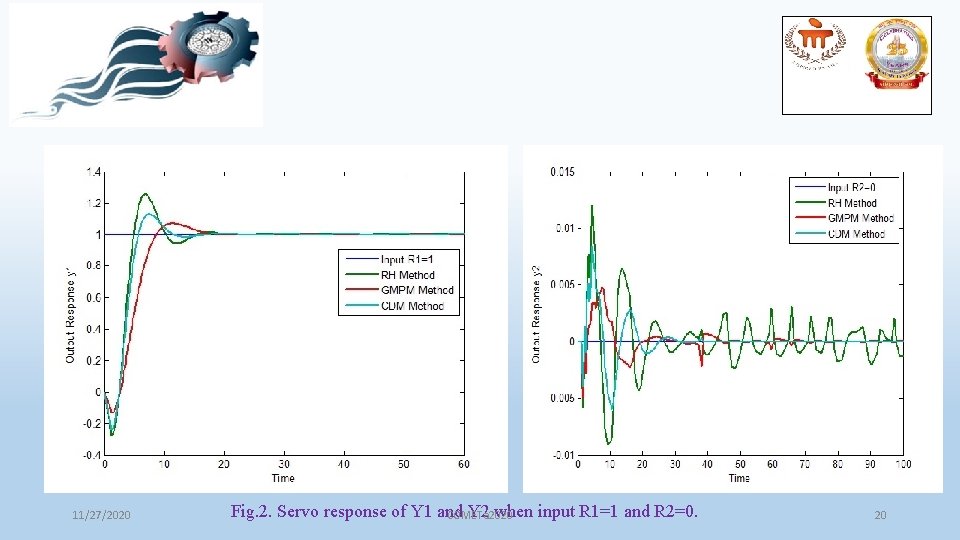
11/27/2020 Fig. 2. Servo response of Y 1 and Y 2 when input R 1=1 and R 2=0. COMETa 2020 20
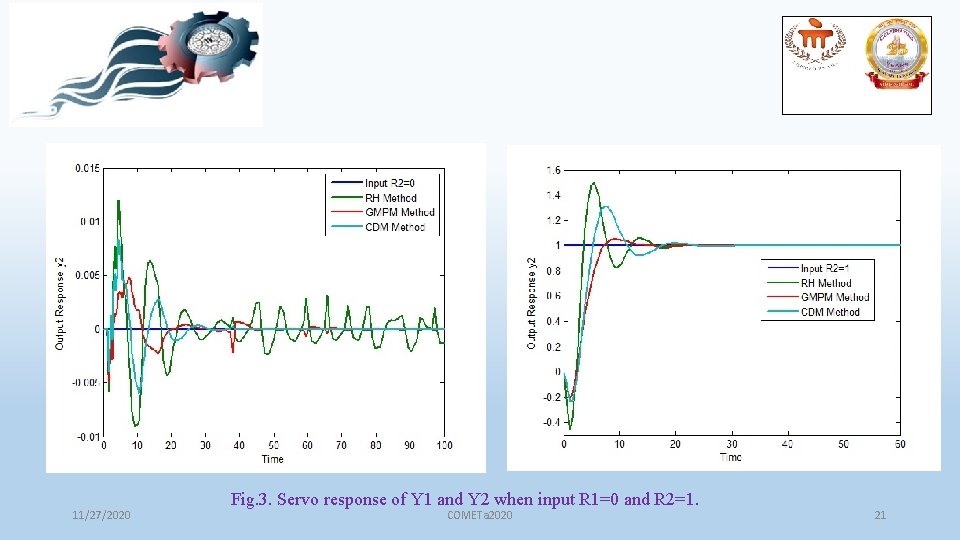
11/27/2020 Fig. 3. Servo response of Y 1 and Y 2 when input R 1=0 and R 2=1. COMETa 2020 21
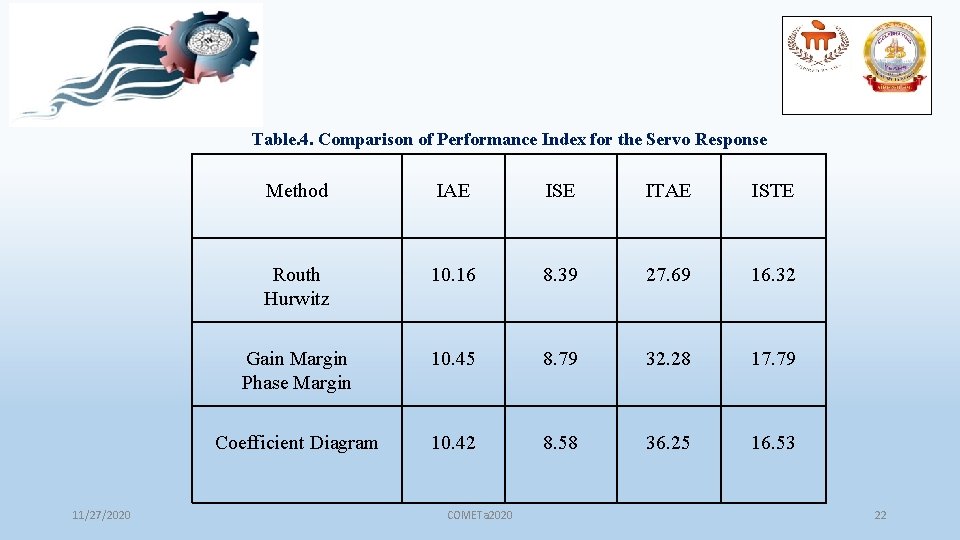
Table. 4. Comparison of Performance Index for the Servo Response 11/27/2020 Method IAE ISE ITAE ISTE Routh Hurwitz 10. 16 8. 39 27. 69 16. 32 Gain Margin Phase Margin 10. 45 8. 79 32. 28 17. 79 Coefficient Diagram 10. 42 8. 58 36. 25 16. 53 COMETa 2020 22
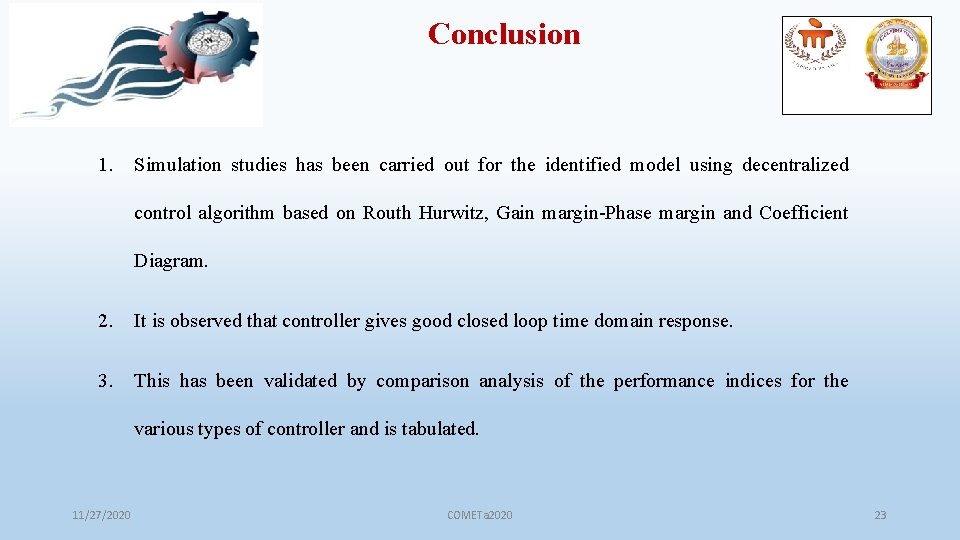
Conclusion 1. Simulation studies has been carried out for the identified model using decentralized control algorithm based on Routh Hurwitz, Gain margin-Phase margin and Coefficient Diagram. 2. It is observed that controller gives good closed loop time domain response. 3. This has been validated by comparison analysis of the performance indices for the various types of controller and is tabulated. 11/27/2020 COMETa 2020 23
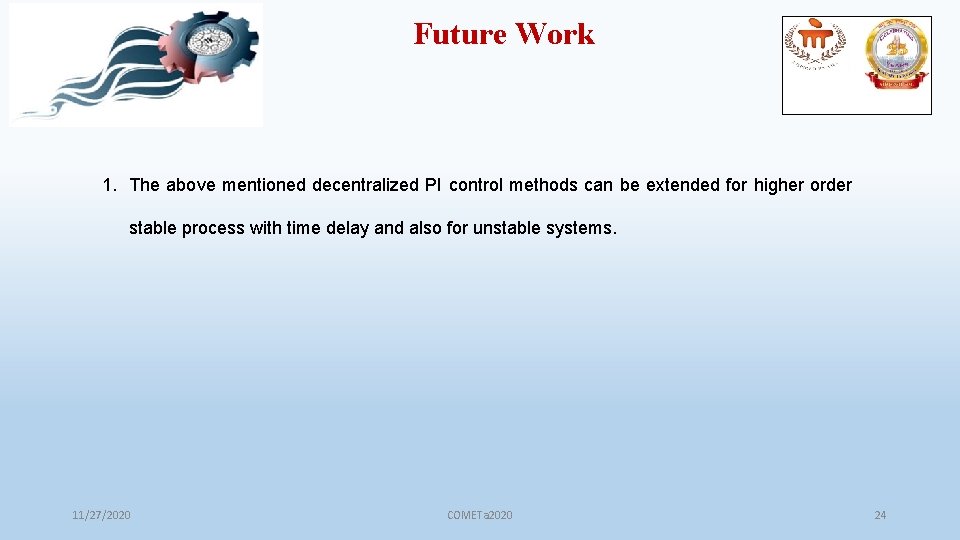
Future Work 1. The above mentioned decentralized PI control methods can be extended for higher order stable process with time delay and also for unstable systems. 11/27/2020 COMETa 2020 24
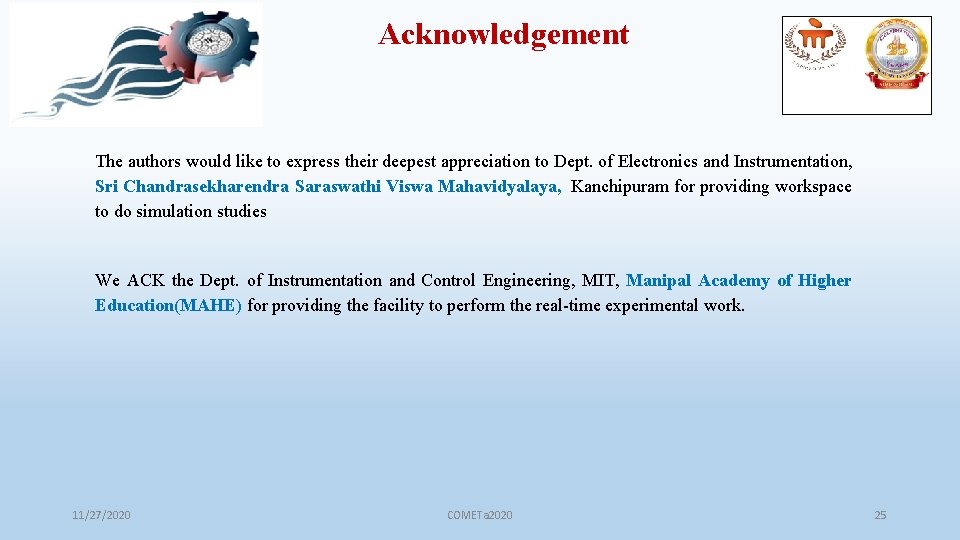
Acknowledgement The authors would like to express their deepest appreciation to Dept. of Electronics and Instrumentation, Sri Chandrasekharendra Saraswathi Viswa Mahavidyalaya, Kanchipuram for providing workspace to do simulation studies We ACK the Dept. of Instrumentation and Control Engineering, MIT, Manipal Academy of Higher Education(MAHE) for providing the facility to perform the real-time experimental work. 11/27/2020 COMETa 2020 25
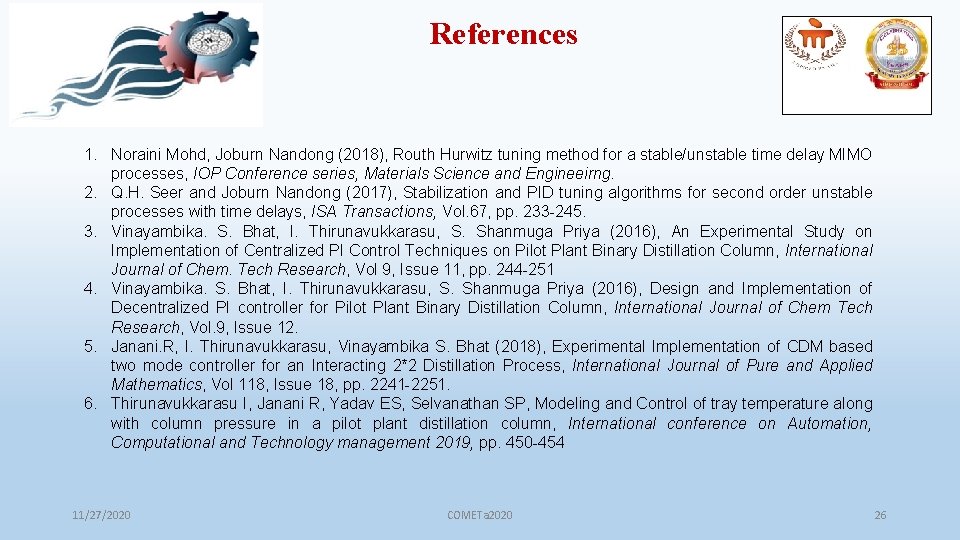
References 1. Noraini Mohd, Joburn Nandong (2018), Routh Hurwitz tuning method for a stable/unstable time delay MIMO processes, IOP Conference series, Materials Science and Engineeirng. 2. Q. H. Seer and Joburn Nandong (2017), Stabilization and PID tuning algorithms for second order unstable processes with time delays, ISA Transactions, Vol. 67, pp. 233 -245. 3. Vinayambika. S. Bhat, I. Thirunavukkarasu, S. Shanmuga Priya (2016), An Experimental Study on Implementation of Centralized PI Control Techniques on Pilot Plant Binary Distillation Column, International Journal of Chem. Tech Research, Vol 9, Issue 11, pp. 244 -251 4. Vinayambika. S. Bhat, I. Thirunavukkarasu, S. Shanmuga Priya (2016), Design and Implementation of Decentralized PI controller for Pilot Plant Binary Distillation Column, International Journal of Chem Tech Research, Vol. 9, Issue 12. 5. Janani. R, I. Thirunavukkarasu, Vinayambika S. Bhat (2018), Experimental Implementation of CDM based two mode controller for an Interacting 2*2 Distillation Process, International Journal of Pure and Applied Mathematics, Vol 118, Issue 18, pp. 2241 -2251. 6. Thirunavukkarasu I, Janani R, Yadav ES, Selvanathan SP, Modeling and Control of tray temperature along with column pressure in a pilot plant distillation column, International conference on Automation, Computational and Technology management 2019, pp. 450 -454 11/27/2020 COMETa 2020 26
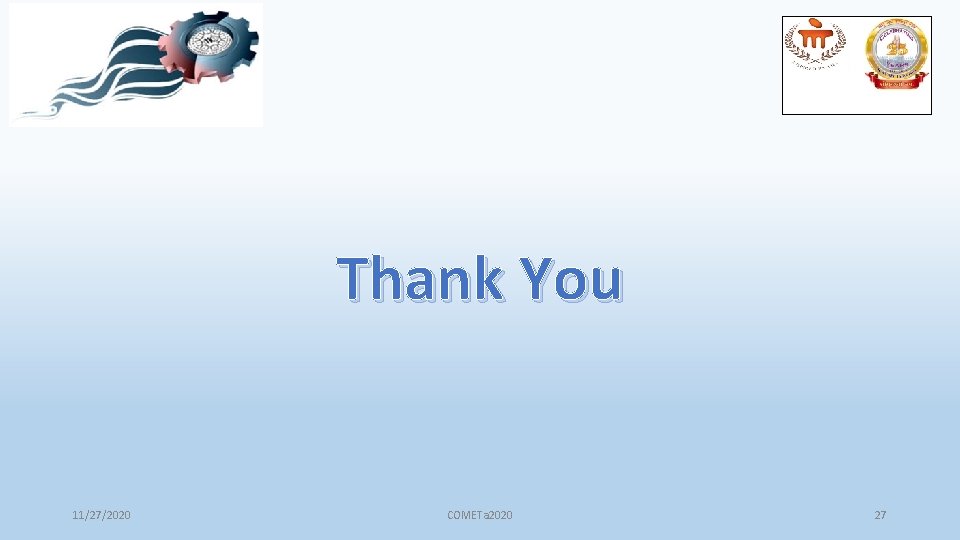
Thank You 11/27/2020 COMETa 2020 27
Cometa 2020
Cometa 2020
Cometa caronte
Dos hermanas fueron a comprar una cuerda de saltar
La longitud del hilo que sostiene una cometa es de 250
Cometa di halley ultimo passaggio
Cometa west
Solicitud
Astronomo muñoz ferrada
Cometa 1970
Polisemicas
Stella cometa che brilli lassù testo
Fórmula del perímetro del trapecio
Geipan rapport cometa
Information gathered during an experiment
How is a scientific law different from a scientific theory?
Afp annual conference 2020
Spring io conference 2020
Mip conference 2020
Ansys innovation conference
Alzheimers nz conference 2020
National conference for rabi campaign 2020
H2fc supergen conference 2020
Imcat conference 2020
Junior science olympiad
Semiconductor
International cryogenic engineering conference
International gambling conference