Coil EM Loads and Stresses Analyzed with ANSYS
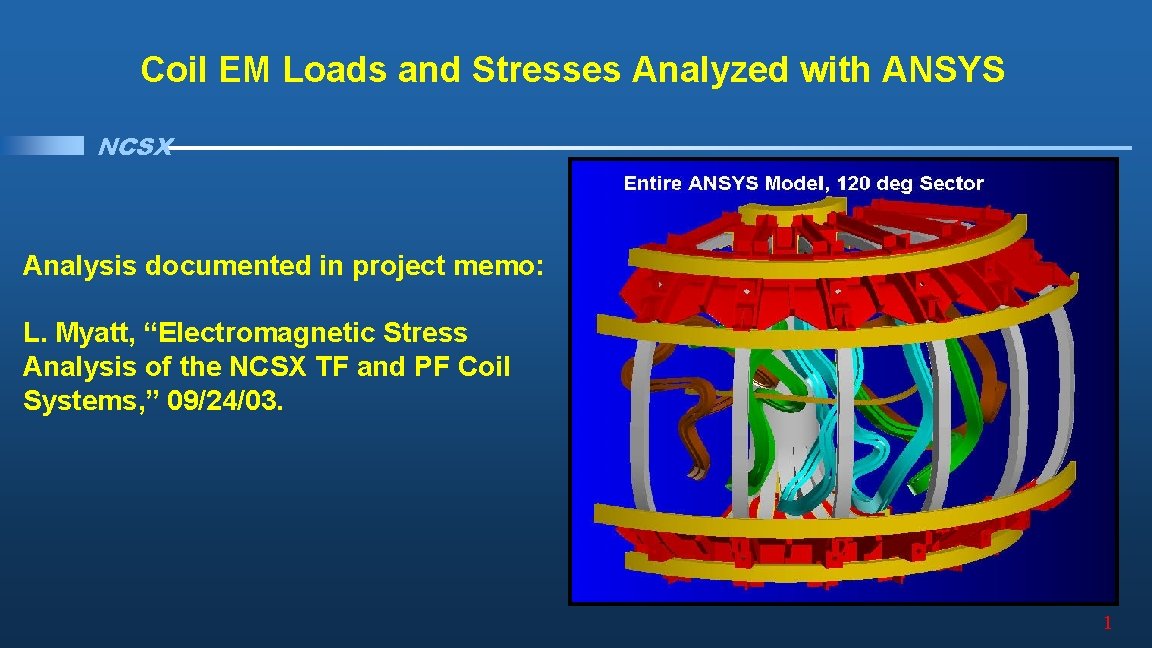
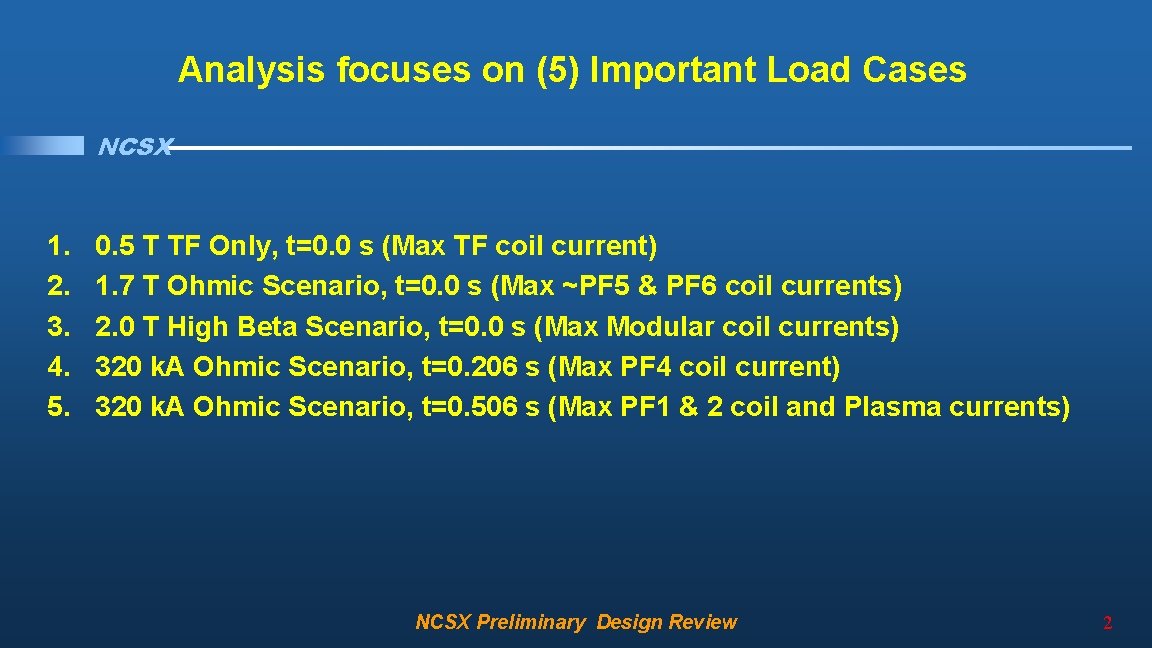
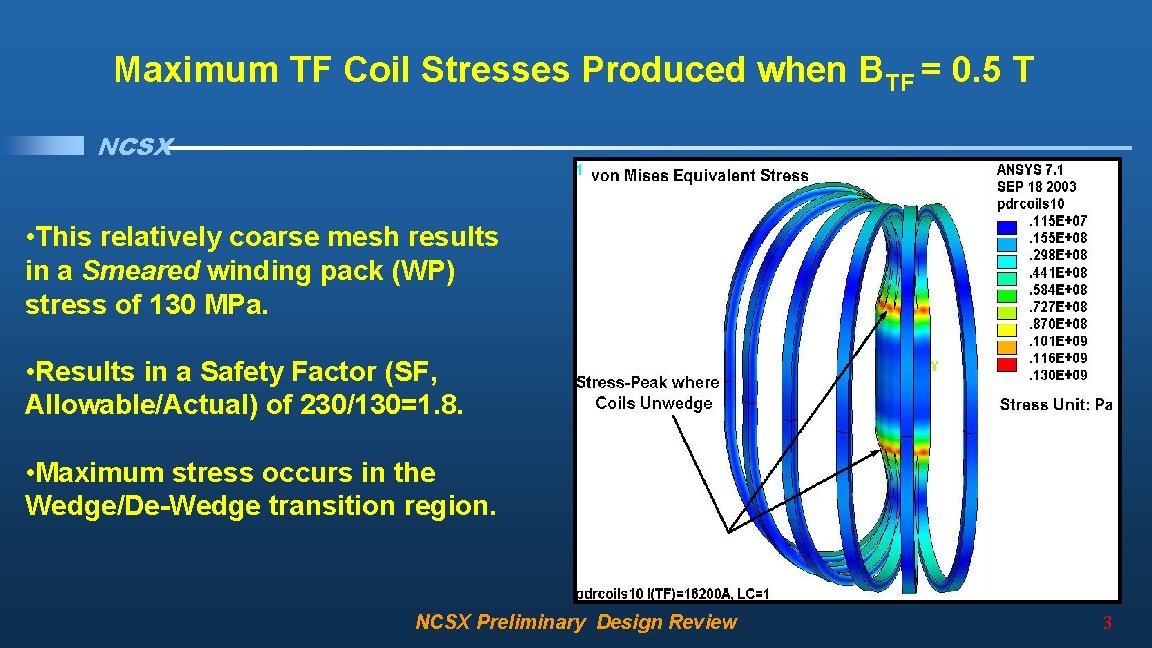
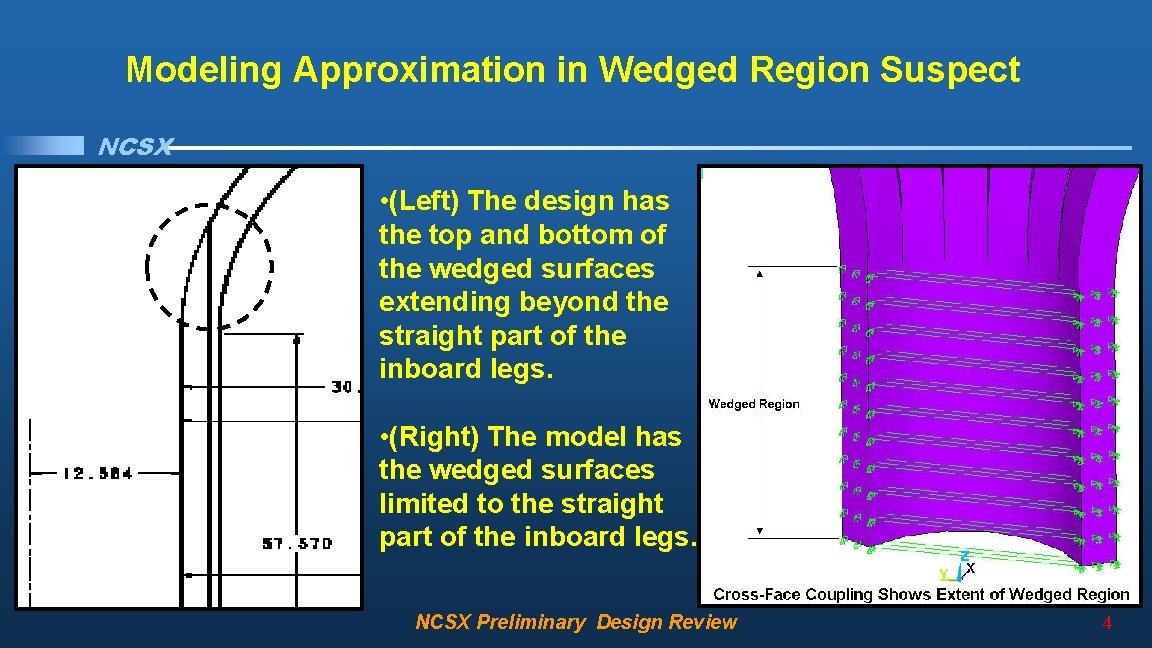
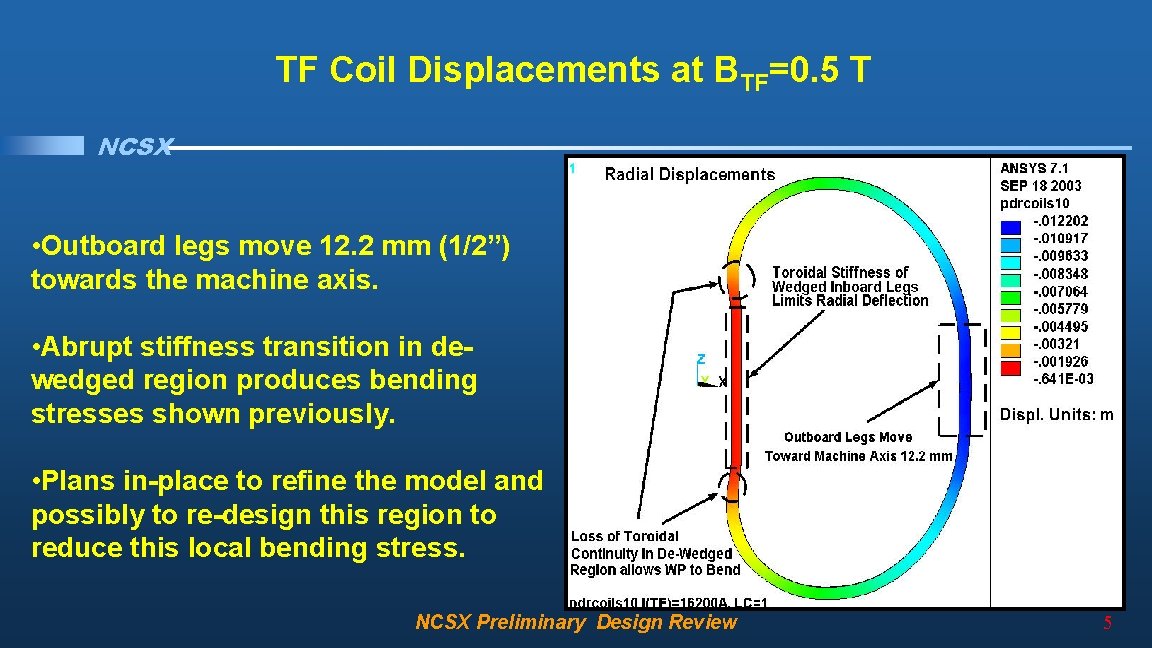
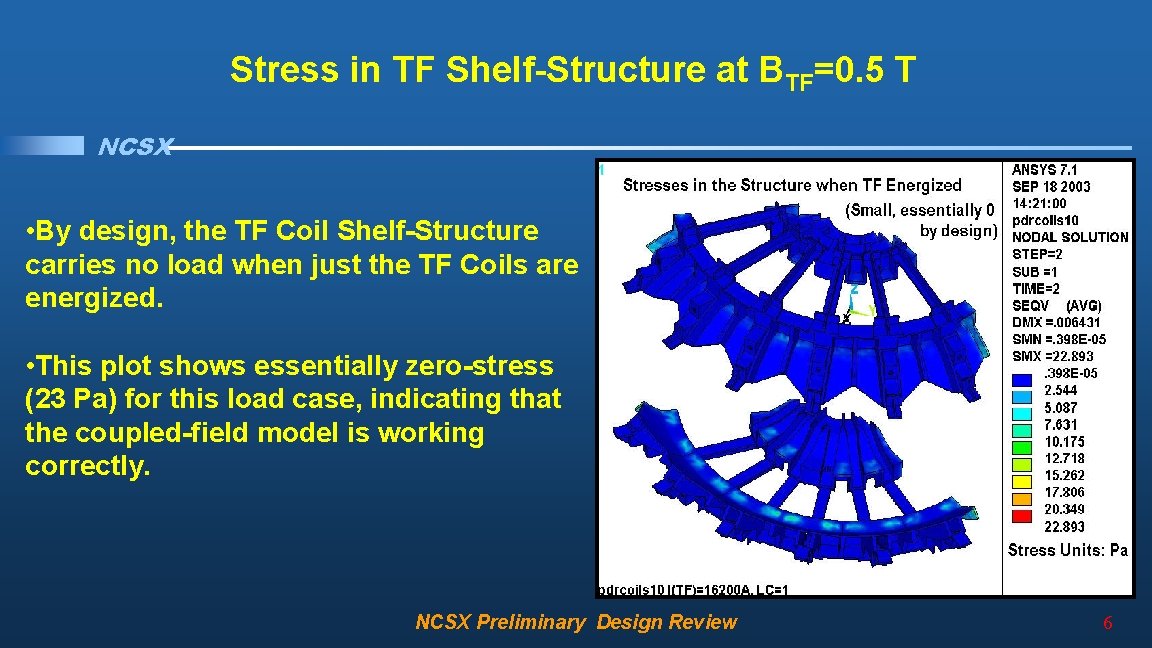
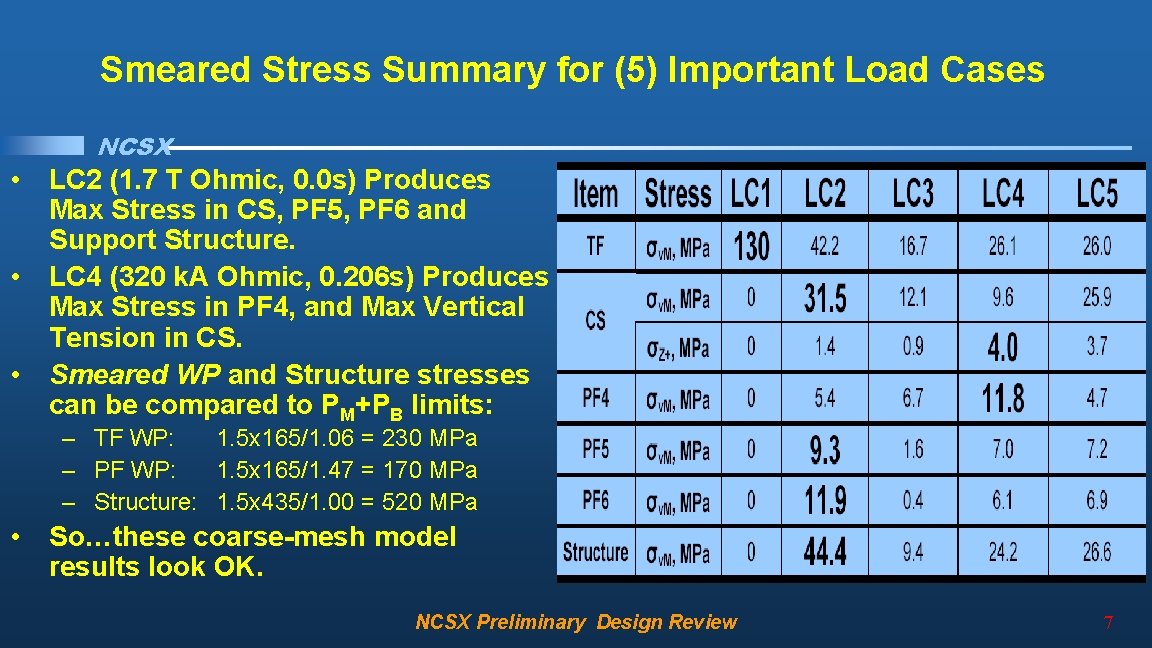
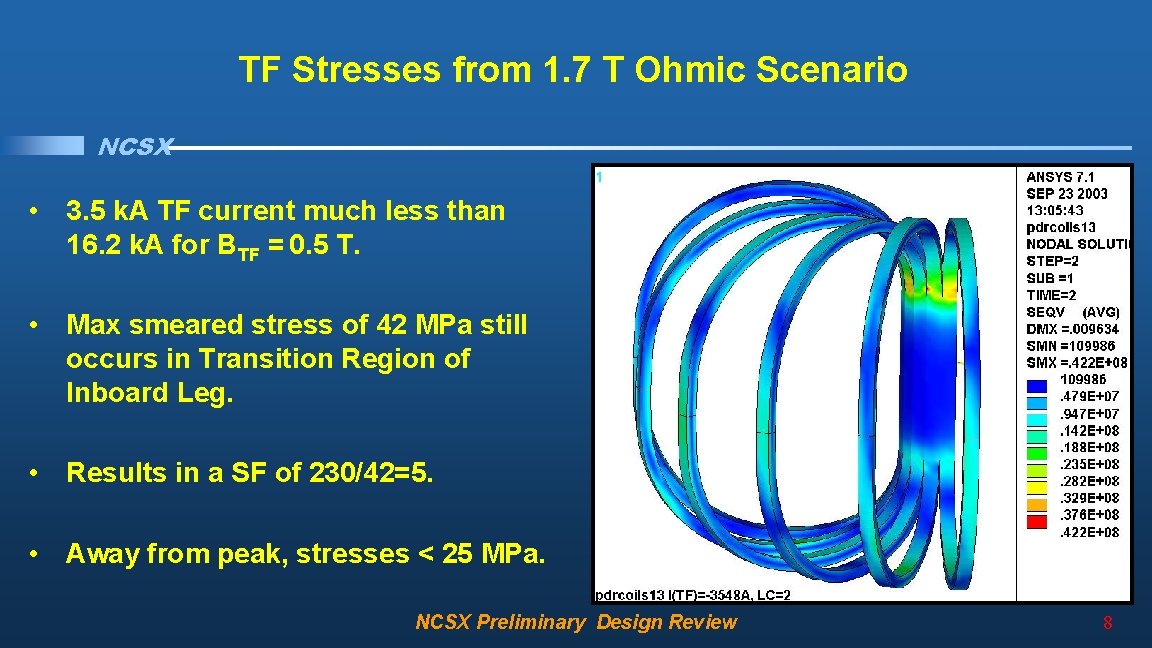
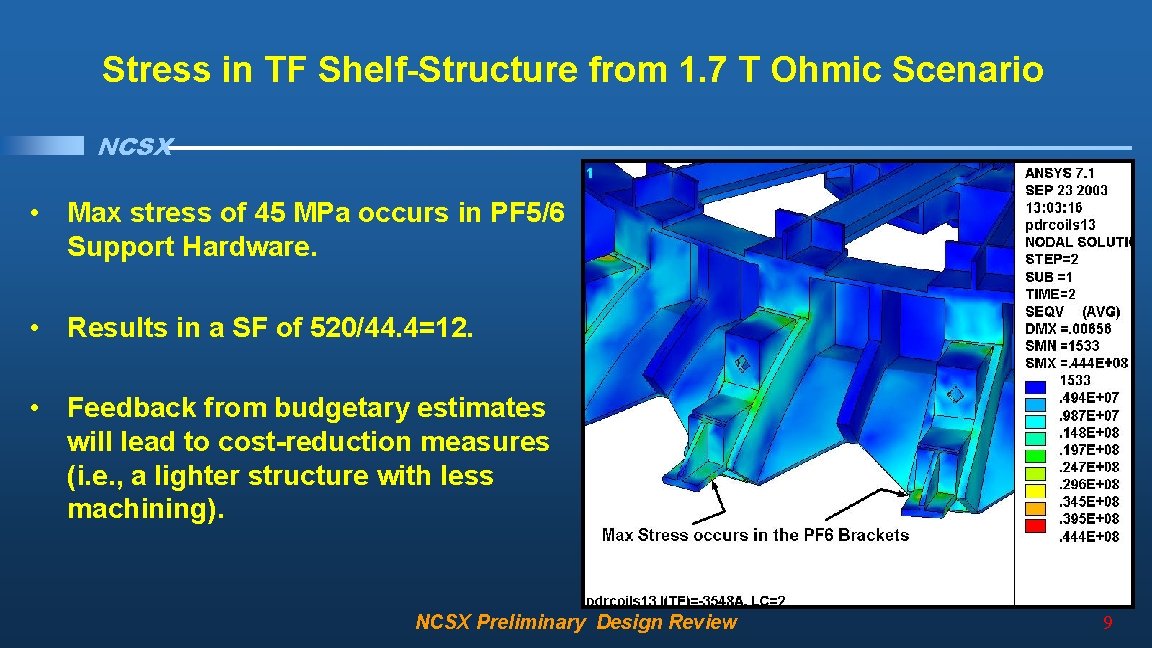
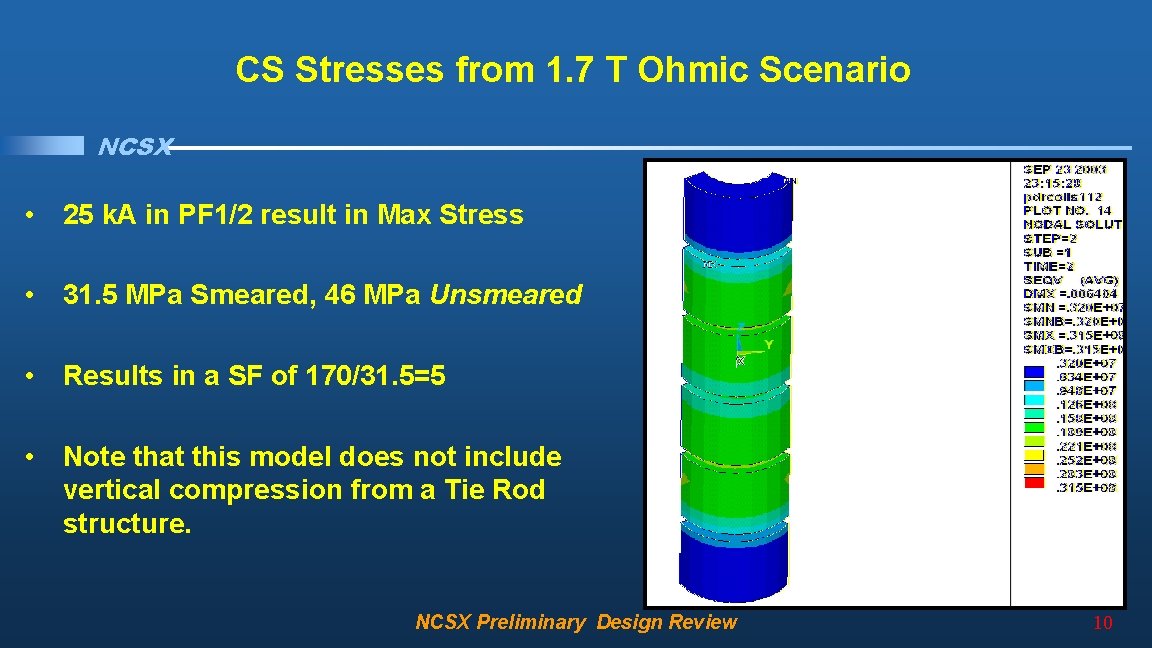
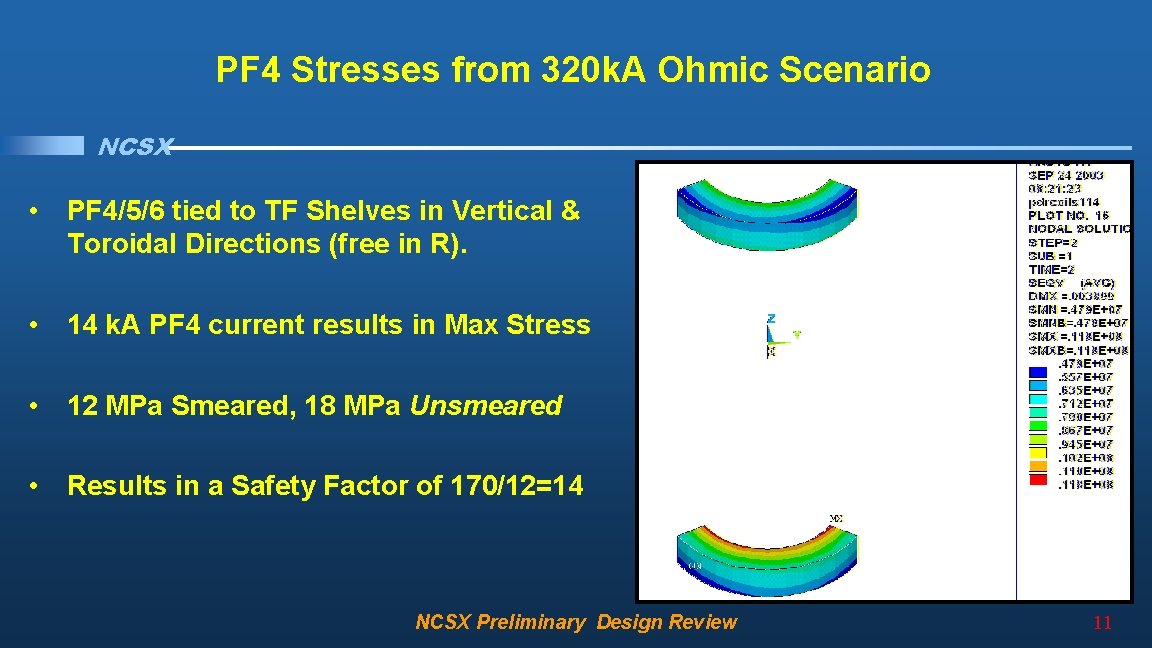
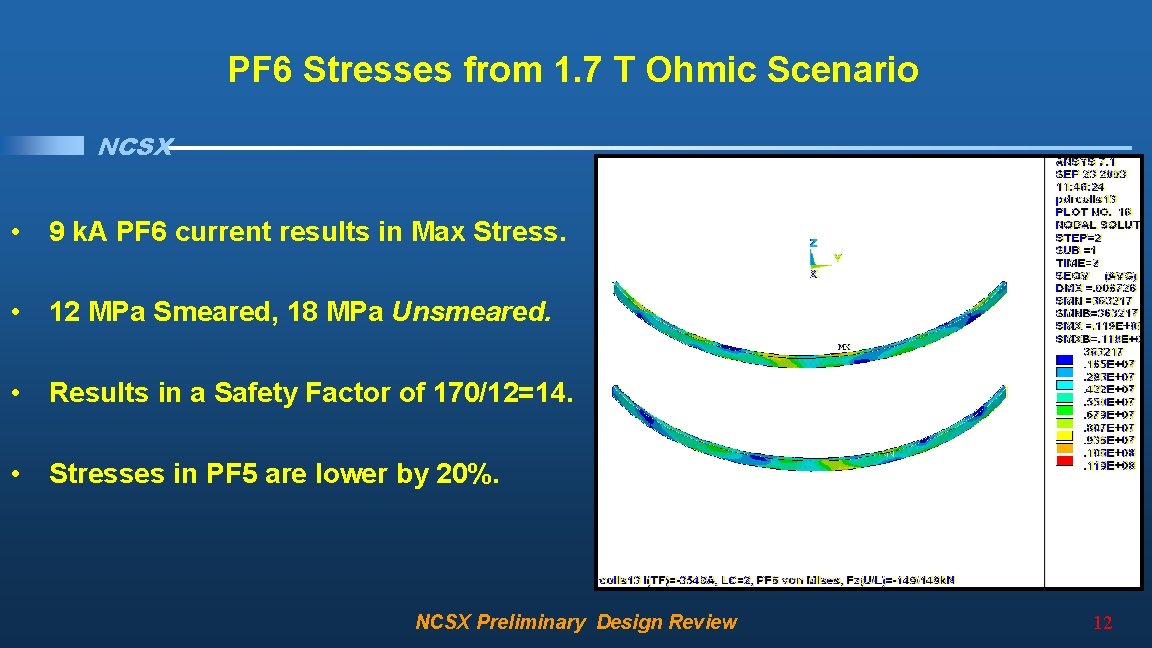
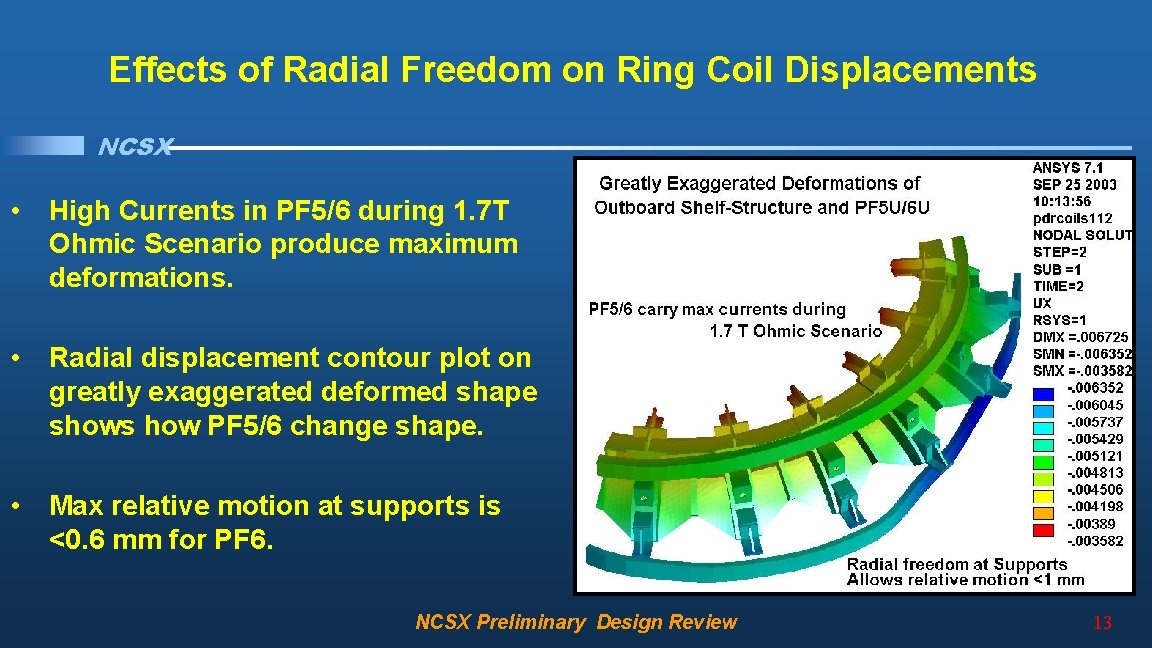
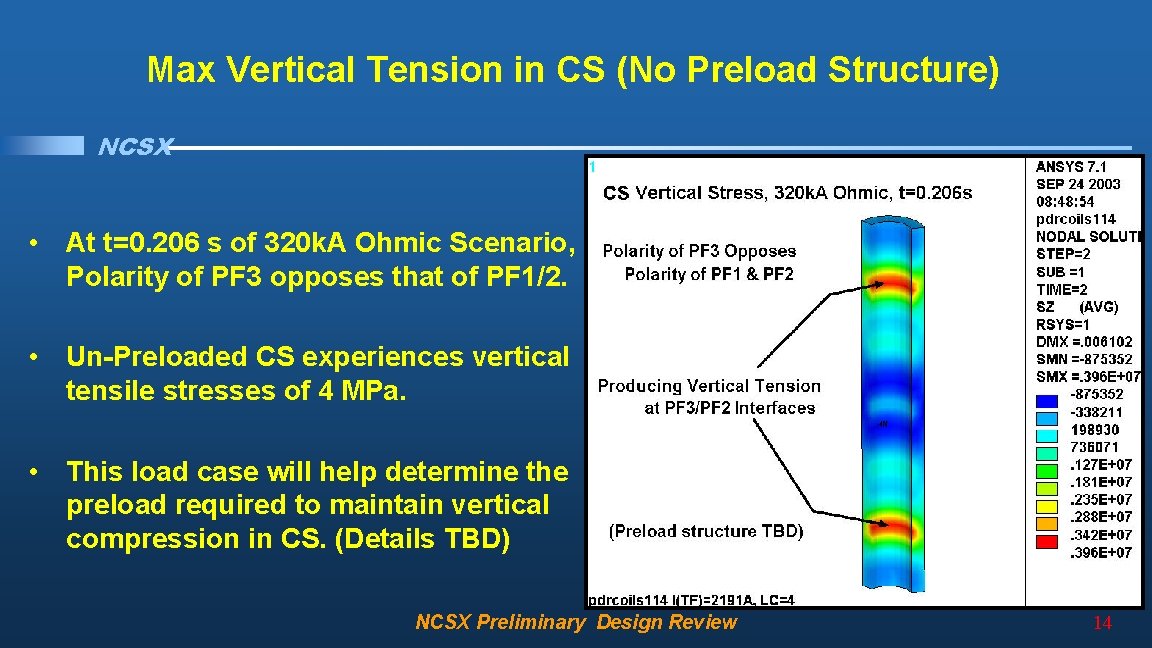
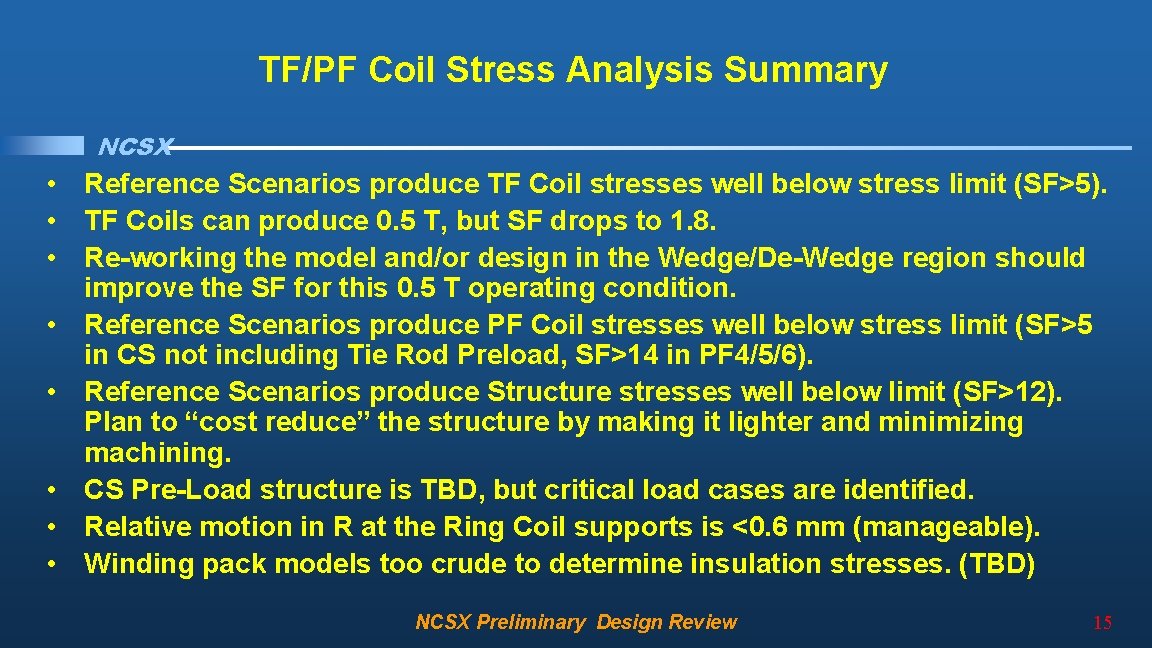
- Slides: 15
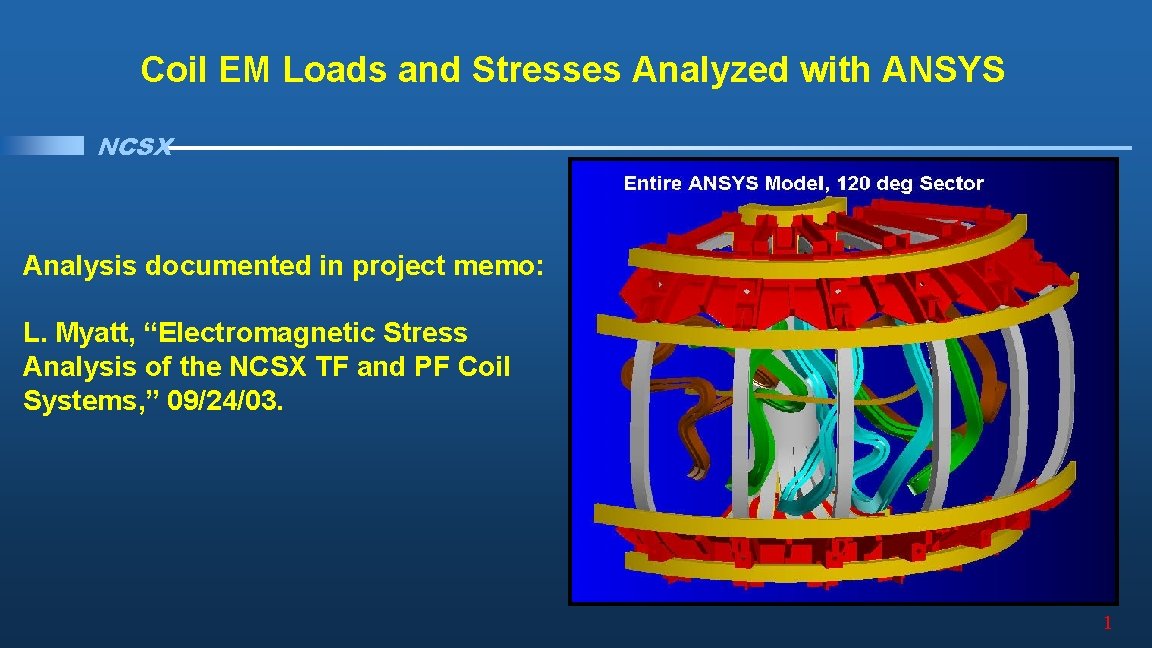
Coil EM Loads and Stresses Analyzed with ANSYS NCSX Analysis documented in project memo: L. Myatt, “Electromagnetic Stress Analysis of the NCSX TF and PF Coil Systems, ” 09/24/03. 1
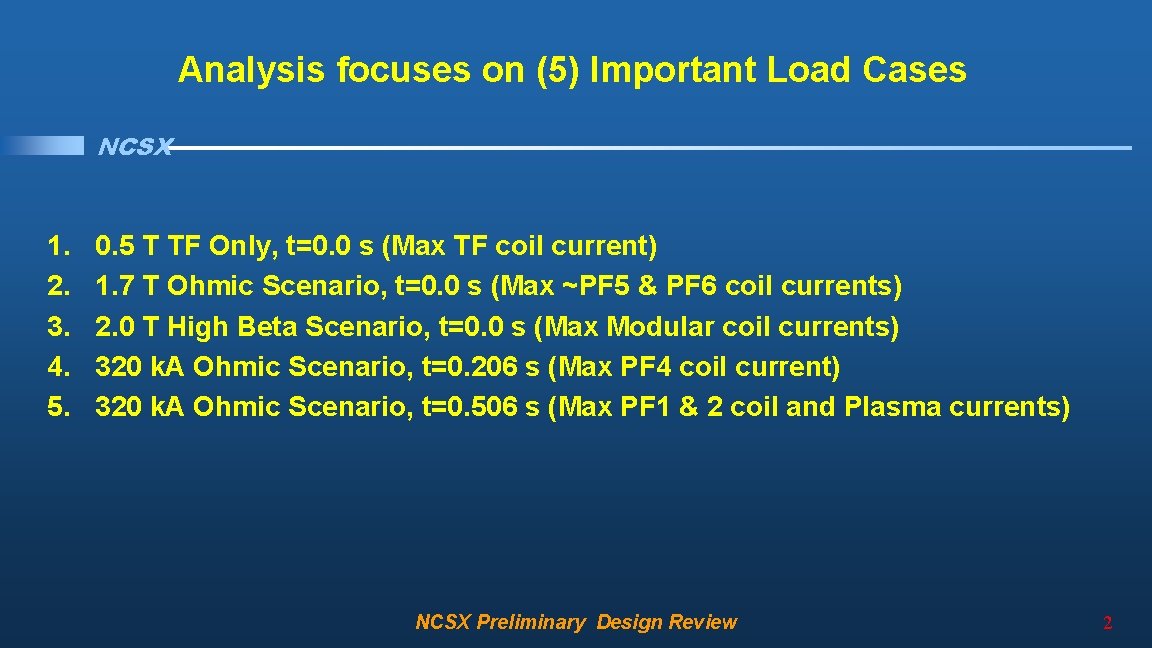
Analysis focuses on (5) Important Load Cases NCSX 1. 2. 3. 4. 5. 0. 5 T TF Only, t=0. 0 s (Max TF coil current) 1. 7 T Ohmic Scenario, t=0. 0 s (Max ~PF 5 & PF 6 coil currents) 2. 0 T High Beta Scenario, t=0. 0 s (Max Modular coil currents) 320 k. A Ohmic Scenario, t=0. 206 s (Max PF 4 coil current) 320 k. A Ohmic Scenario, t=0. 506 s (Max PF 1 & 2 coil and Plasma currents) NCSX Preliminary Design Review 2
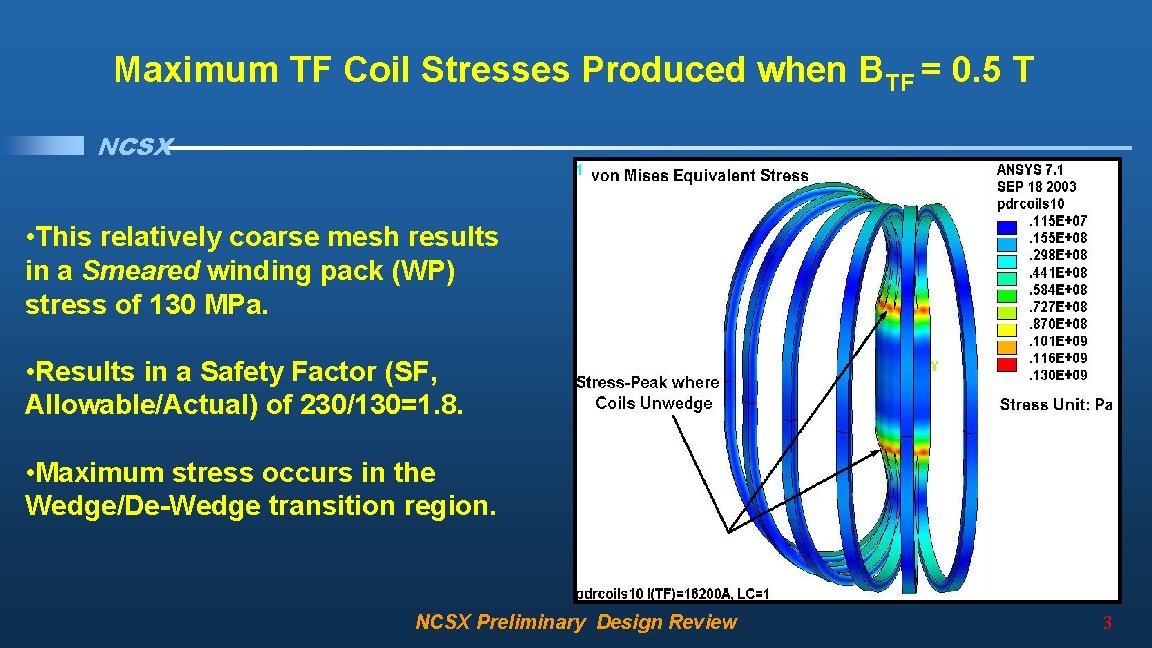
Maximum TF Coil Stresses Produced when BTF = 0. 5 T NCSX • This relatively coarse mesh results in a Smeared winding pack (WP) stress of 130 MPa. • Results in a Safety Factor (SF, Allowable/Actual) of 230/130=1. 8. • Maximum stress occurs in the Wedge/De-Wedge transition region. NCSX Preliminary Design Review 3
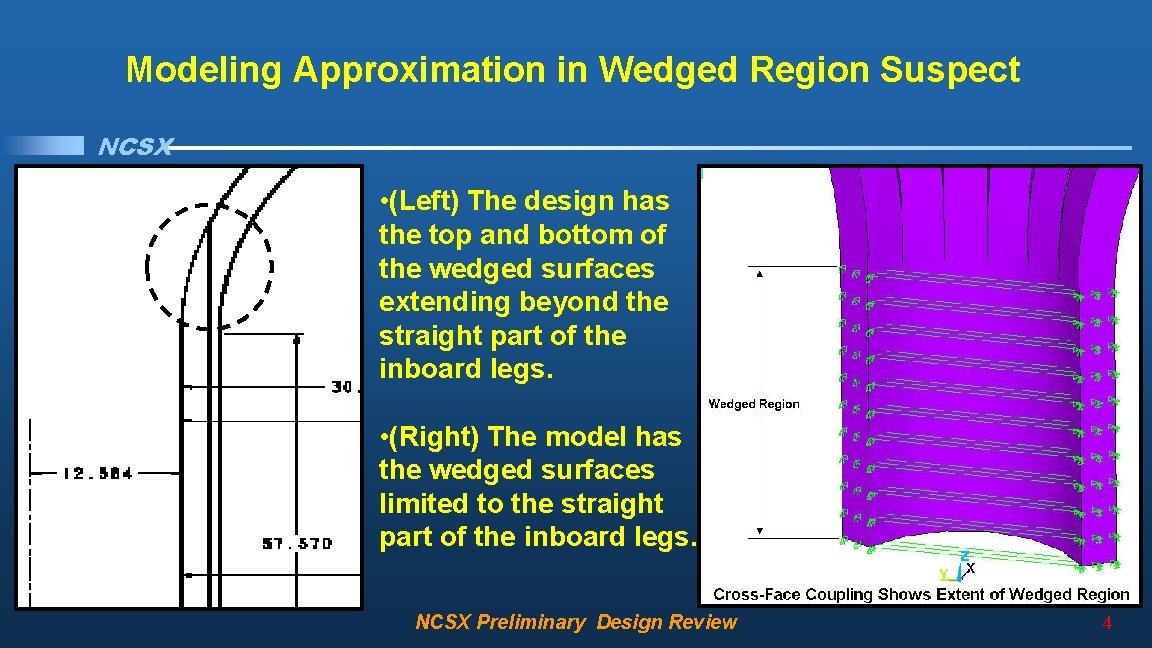
Modeling Approximation in Wedged Region Suspect NCSX • (Left) The design has the top and bottom of the wedged surfaces extending beyond the straight part of the inboard legs. • (Right) The model has the wedged surfaces limited to the straight part of the inboard legs. NCSX Preliminary Design Review 4
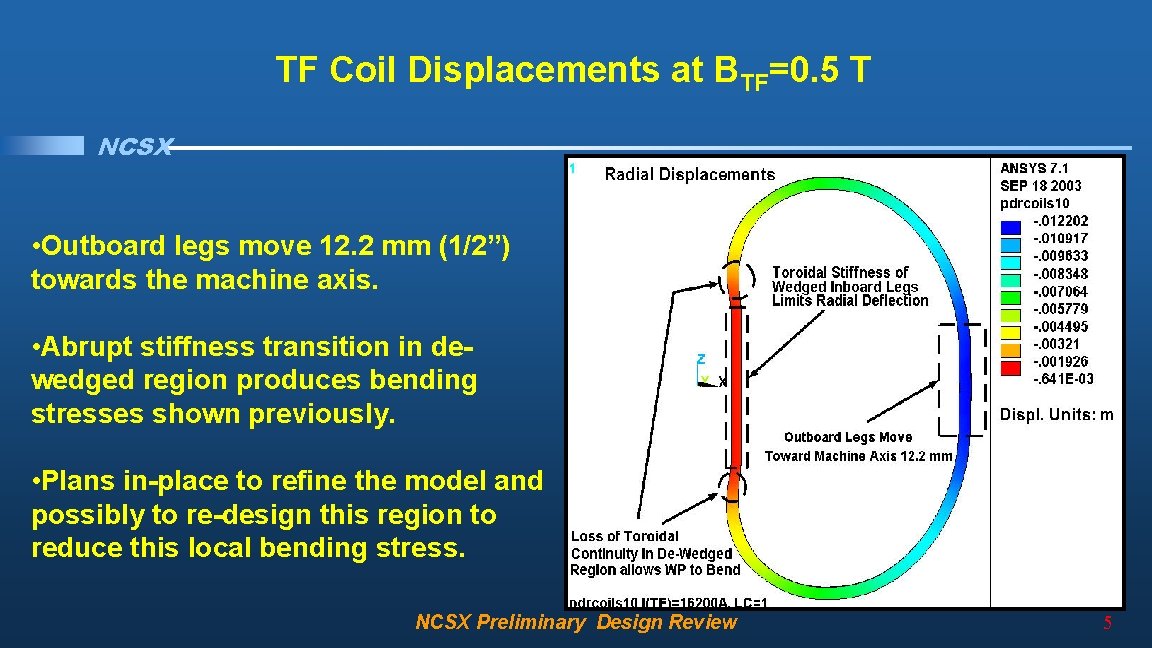
TF Coil Displacements at BTF=0. 5 T NCSX • Outboard legs move 12. 2 mm (1/2”) towards the machine axis. • Abrupt stiffness transition in dewedged region produces bending stresses shown previously. • Plans in-place to refine the model and possibly to re-design this region to reduce this local bending stress. NCSX Preliminary Design Review 5
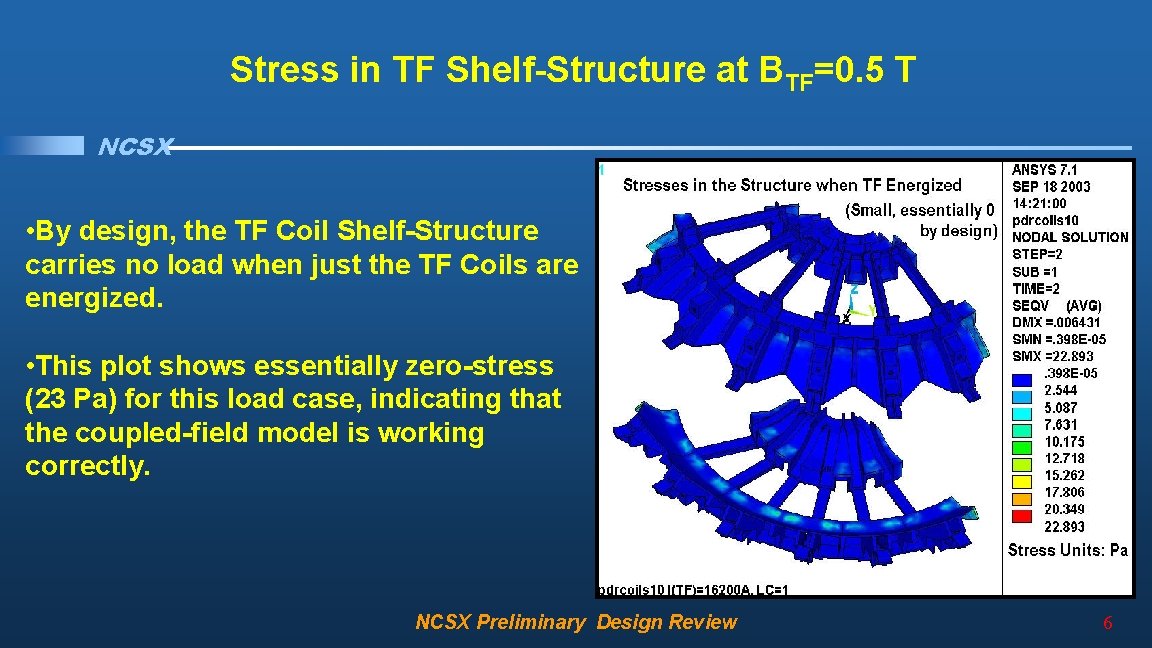
Stress in TF Shelf-Structure at BTF=0. 5 T NCSX • By design, the TF Coil Shelf-Structure carries no load when just the TF Coils are energized. • This plot shows essentially zero-stress (23 Pa) for this load case, indicating that the coupled-field model is working correctly. NCSX Preliminary Design Review 6
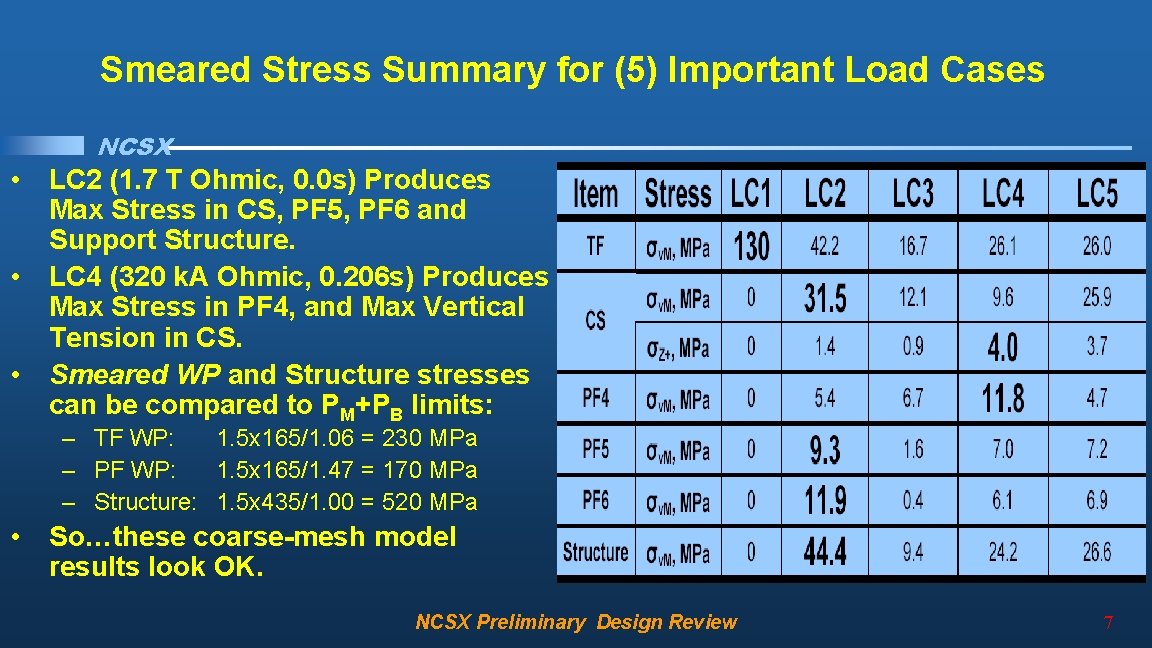
Smeared Stress Summary for (5) Important Load Cases NCSX • • • LC 2 (1. 7 T Ohmic, 0. 0 s) Produces Max Stress in CS, PF 5, PF 6 and Support Structure. LC 4 (320 k. A Ohmic, 0. 206 s) Produces Max Stress in PF 4, and Max Vertical Tension in CS. Smeared WP and Structure stresses can be compared to PM+PB limits: – TF WP: 1. 5 x 165/1. 06 = 230 MPa – PF WP: 1. 5 x 165/1. 47 = 170 MPa – Structure: 1. 5 x 435/1. 00 = 520 MPa • So…these coarse-mesh model results look OK. NCSX Preliminary Design Review 7
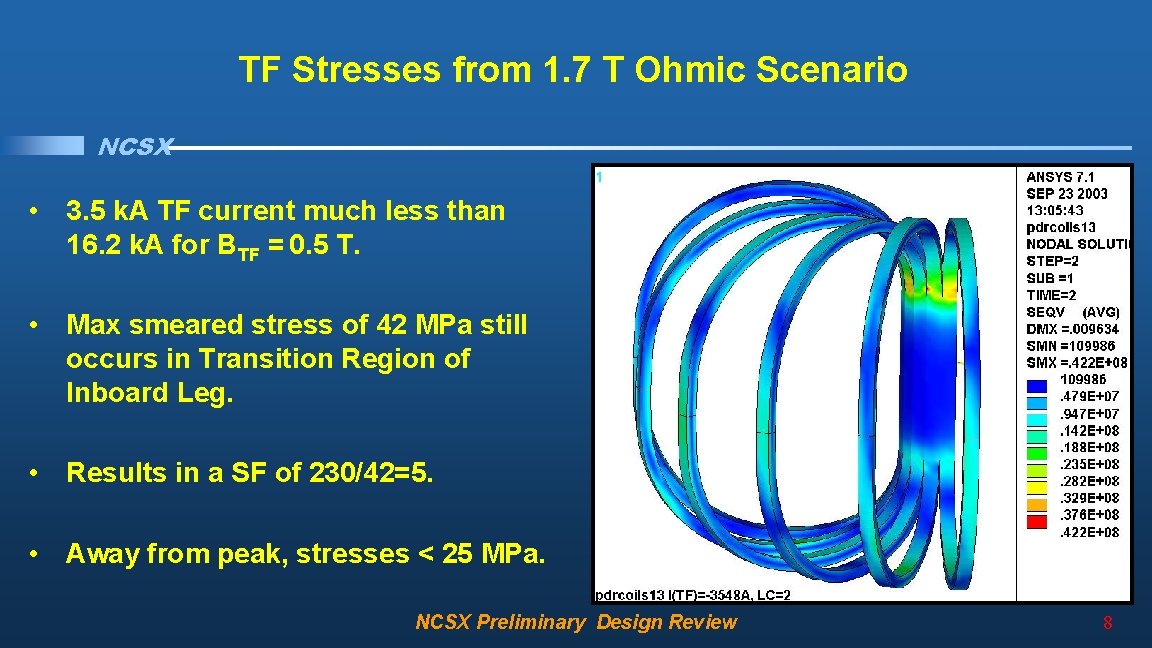
TF Stresses from 1. 7 T Ohmic Scenario NCSX • 3. 5 k. A TF current much less than 16. 2 k. A for BTF = 0. 5 T. • Max smeared stress of 42 MPa still occurs in Transition Region of Inboard Leg. • Results in a SF of 230/42=5. • Away from peak, stresses < 25 MPa. Solenoid at 1. 7 T Ohmic scenario; t=0 NCSX Preliminary Design Review 8
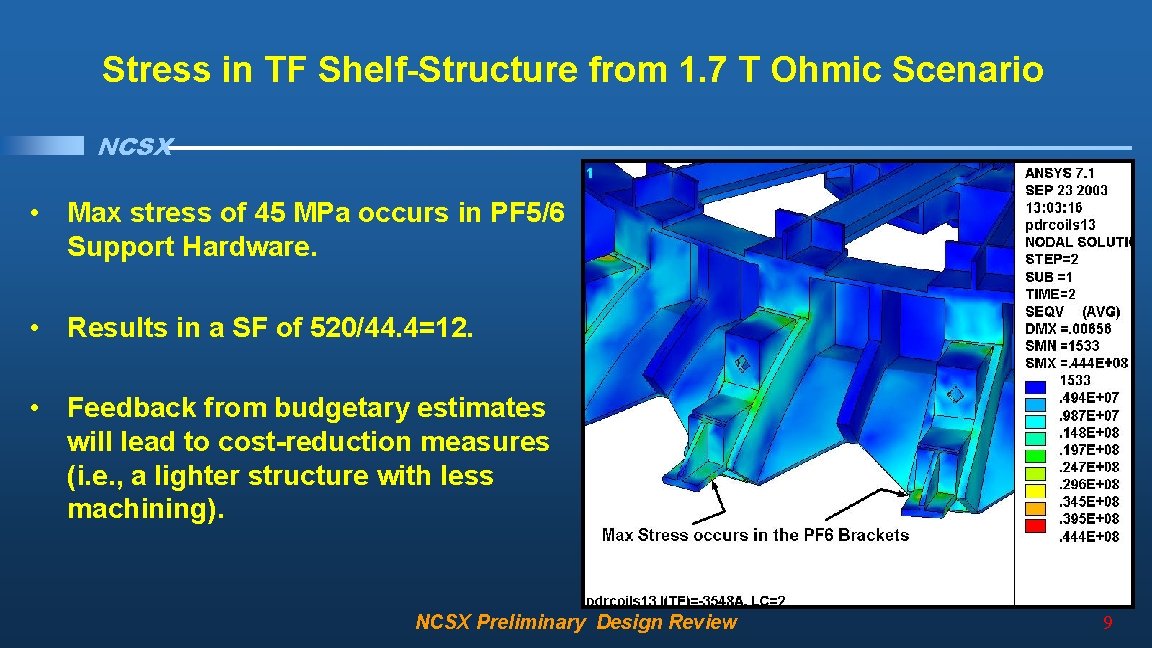
Stress in TF Shelf-Structure from 1. 7 T Ohmic Scenario NCSX • Max stress of 45 MPa occurs in PF 5/6 Support Hardware. • Results in a SF of 520/44. 4=12. • Feedback from budgetary estimates will lead to cost-reduction measures (i. e. , a lighter structure with less machining). NCSX Preliminary Design Review 9
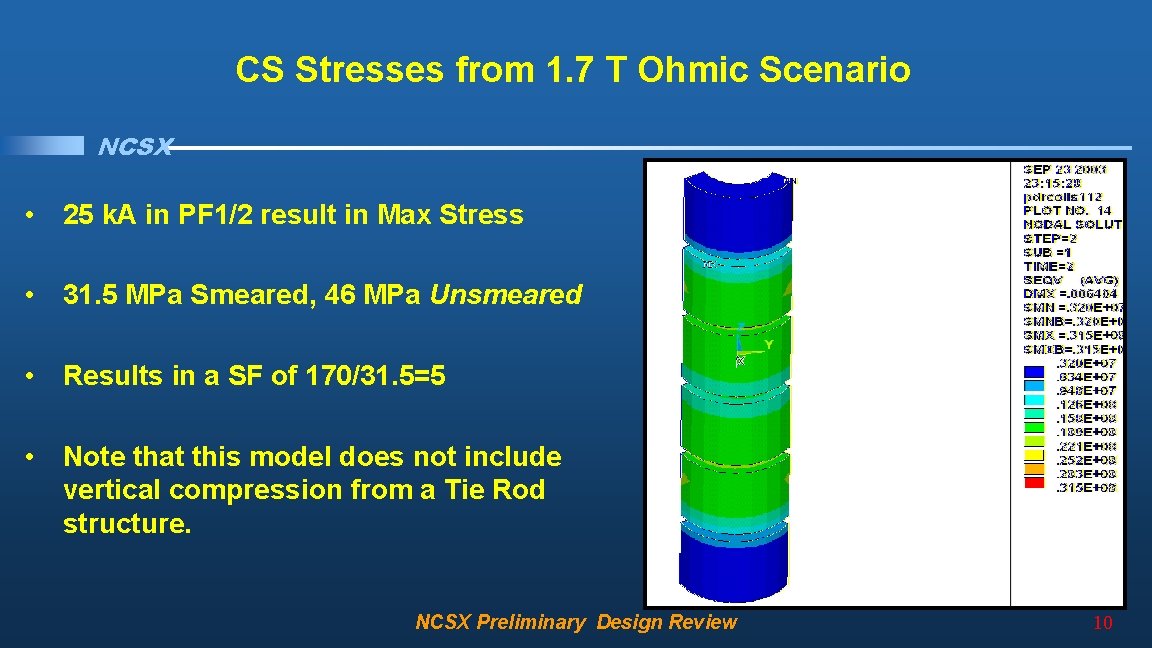
CS Stresses from 1. 7 T Ohmic Scenario NCSX • 25 k. A in PF 1/2 result in Max Stress • 31. 5 MPa Smeared, 46 MPa Unsmeared • Results in a SF of 170/31. 5=5 • Note that this model does not include vertical compression from a Tie Rod structure. NCSX Preliminary Design Review 10
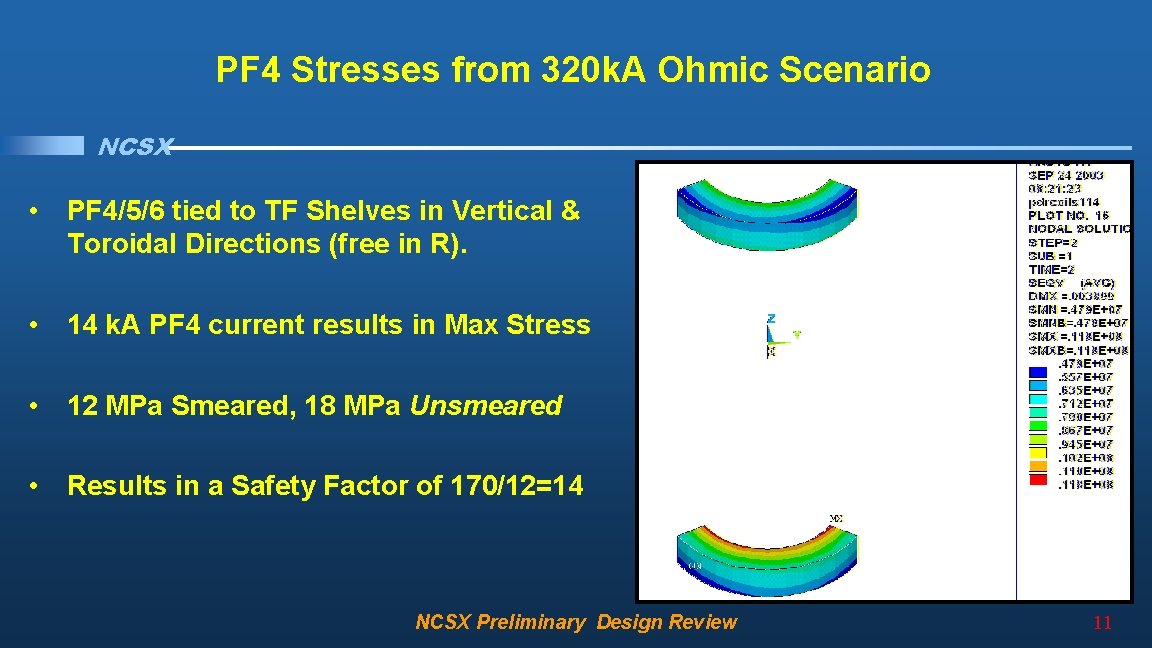
PF 4 Stresses from 320 k. A Ohmic Scenario NCSX • PF 4/5/6 tied to TF Shelves in Vertical & Toroidal Directions (free in R). • 14 k. A PF 4 current results in Max Stress • 12 MPa Smeared, 18 MPa Unsmeared • Results in a Safety Factor of 170/12=14 NCSX Preliminary Design Review 11
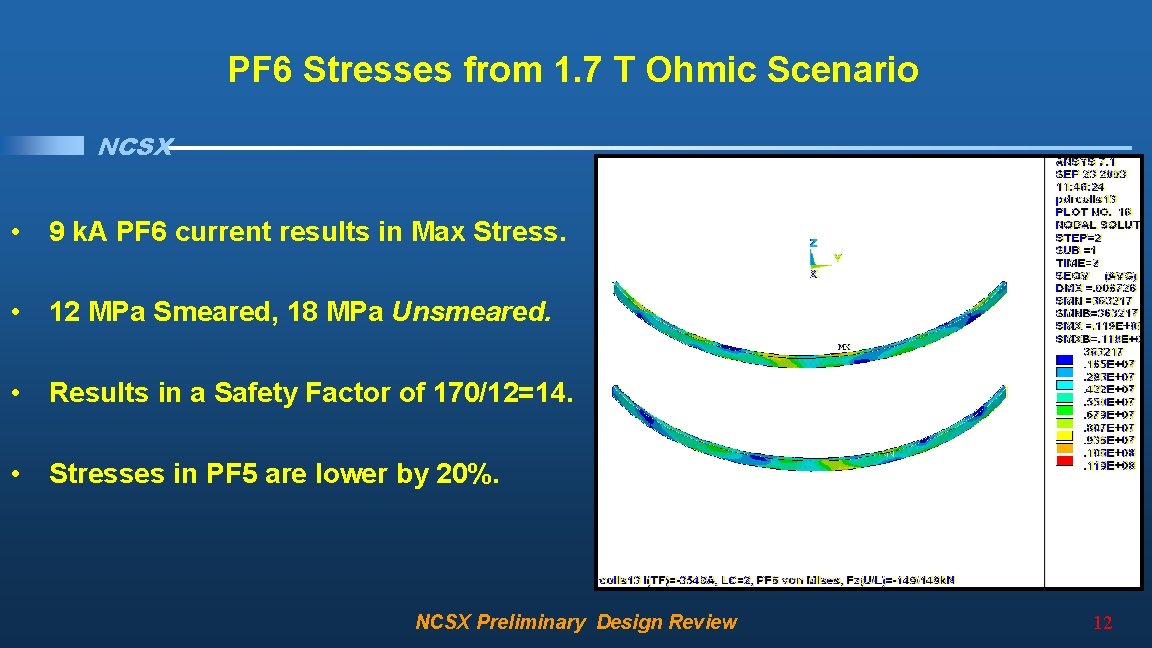
PF 6 Stresses from 1. 7 T Ohmic Scenario NCSX • 9 k. A PF 6 current results in Max Stress. • 12 MPa Smeared, 18 MPa Unsmeared. • Results in a Safety Factor of 170/12=14. • Stresses in PF 5 are lower by 20%. NCSX Preliminary Design Review 12
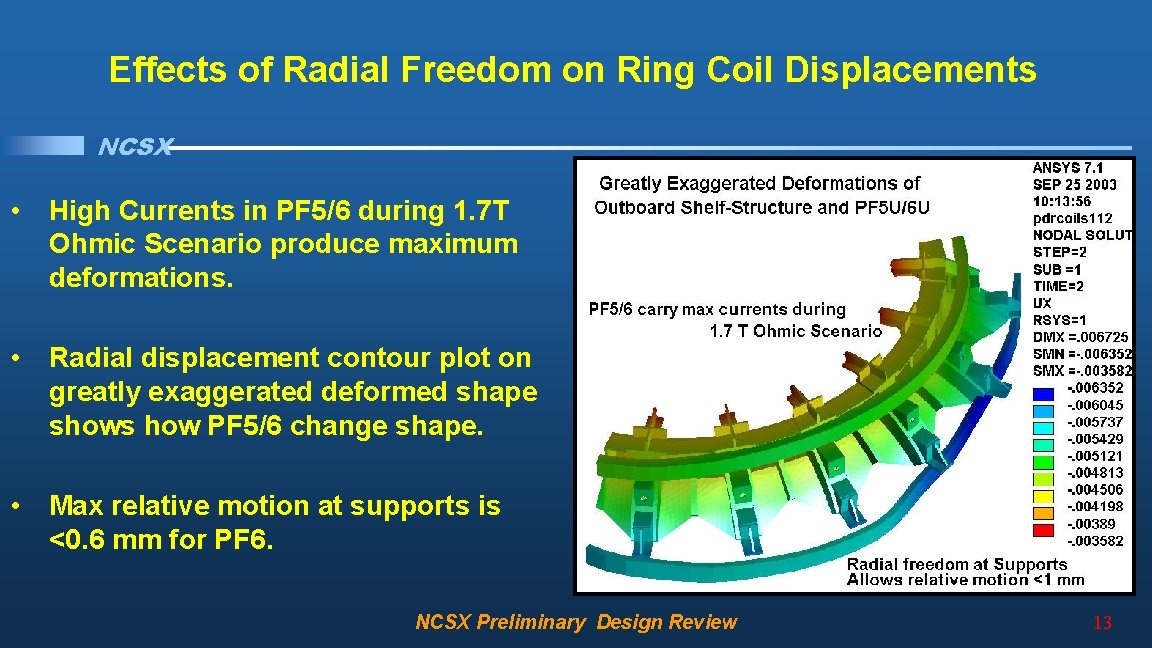
Effects of Radial Freedom on Ring Coil Displacements NCSX • High Currents in PF 5/6 during 1. 7 T Ohmic Scenario produce maximum deformations. • Radial displacement contour plot on greatly exaggerated deformed shape shows how PF 5/6 change shape. • Max relative motion at supports is <0. 6 mm for PF 6. NCSX Preliminary Design Review 13
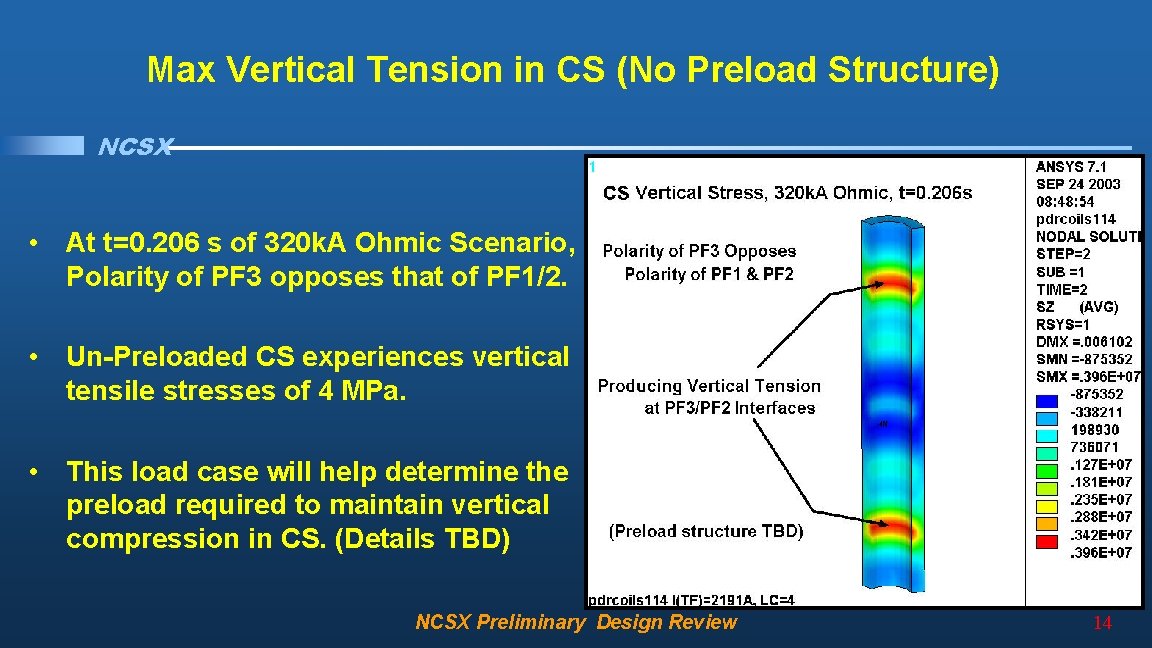
Max Vertical Tension in CS (No Preload Structure) NCSX • At t=0. 206 s of 320 k. A Ohmic Scenario, Polarity of PF 3 opposes that of PF 1/2. • Un-Preloaded CS experiences vertical tensile stresses of 4 MPa. • This load case will help determine the preload required to maintain vertical compression in CS. (Details TBD) NCSX Preliminary Design Review 14
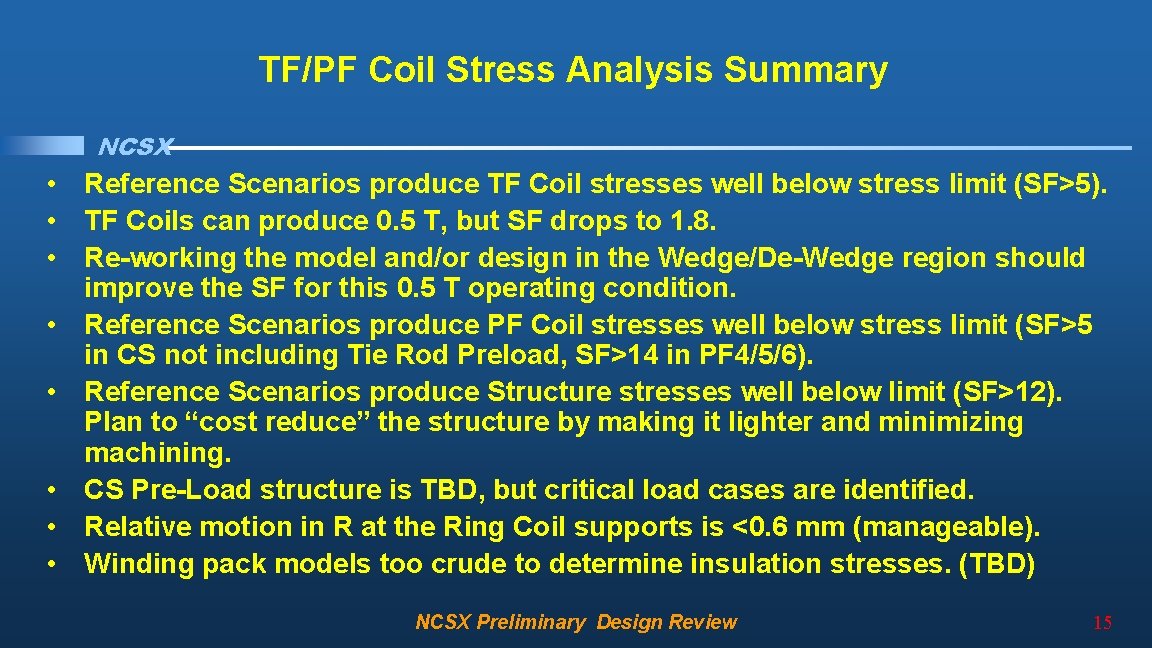
TF/PF Coil Stress Analysis Summary NCSX • • Reference Scenarios produce TF Coil stresses well below stress limit (SF>5). TF Coils can produce 0. 5 T, but SF drops to 1. 8. Re-working the model and/or design in the Wedge/De-Wedge region should improve the SF for this 0. 5 T operating condition. Reference Scenarios produce PF Coil stresses well below stress limit (SF>5 in CS not including Tie Rod Preload, SF>14 in PF 4/5/6). Reference Scenarios produce Structure stresses well below limit (SF>12). Plan to “cost reduce” the structure by making it lighter and minimizing machining. CS Pre-Load structure is TBD, but critical load cases are identified. Relative motion in R at the Ring Coil supports is <0. 6 mm (manageable). Winding pack models too crude to determine insulation stresses. (TBD) NCSX Preliminary Design Review 15
Series coil and multi-turn coil
Types of forces in technology
What jenra is it
Characteristics of system
Lake enclosure fingerprint
Time domain analysis of control system
Analyzing data and drawing conclusions
How to analyze a community problem?
Limitations of item analysis
Probability learning objectives
Hair design elements
Pipe network analysis example
Sensible loads
Forms and shores must not be removed until
Protruding reinforced steel must be guarded
Fire hose appliances