CHAPTER 4 CONVEYOR SYSTEM PLT 423 Material Handling
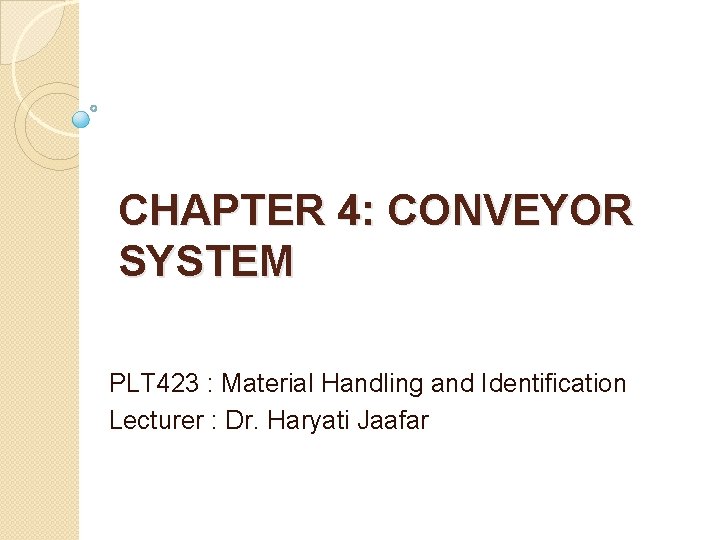
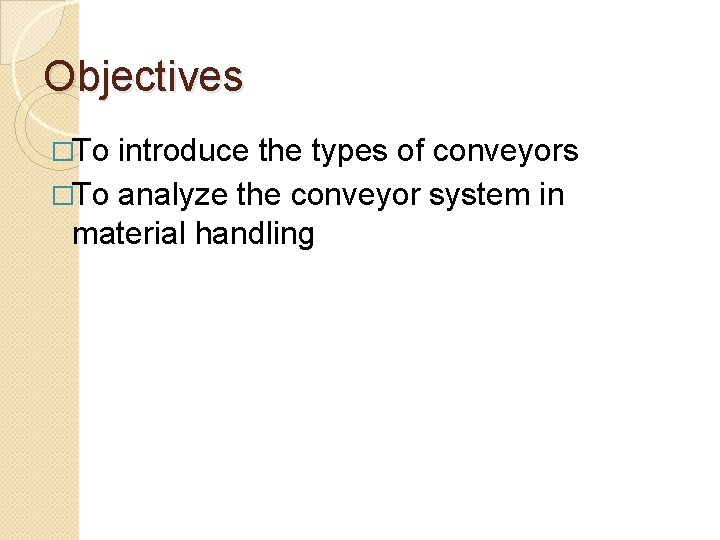
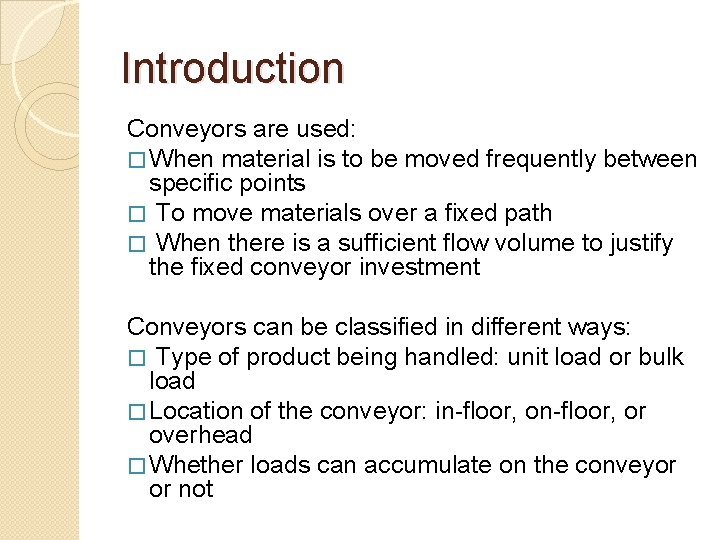
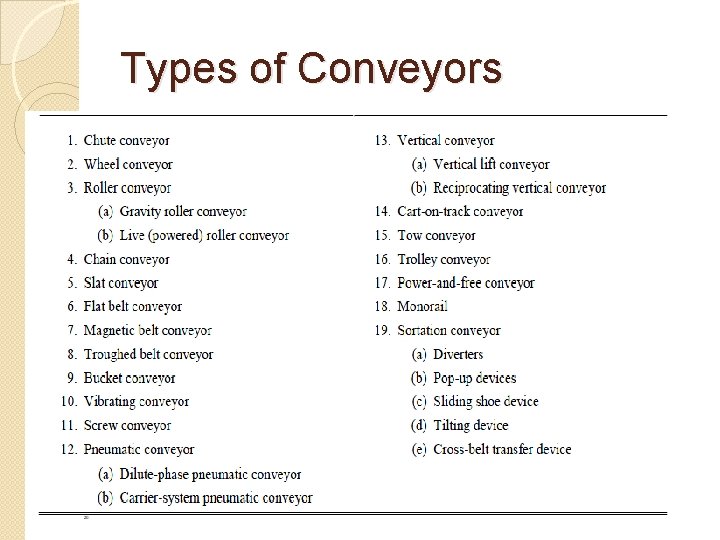
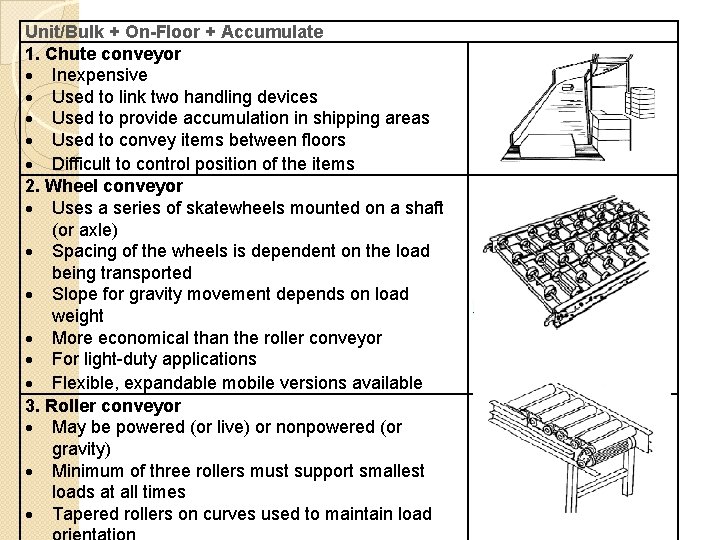
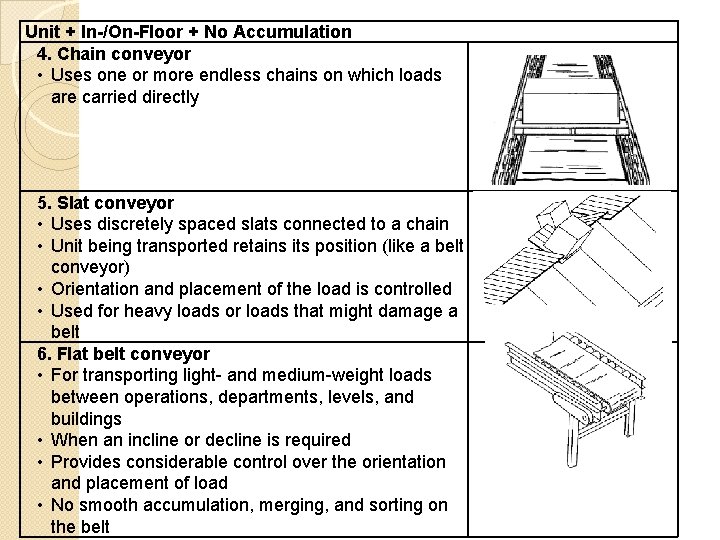
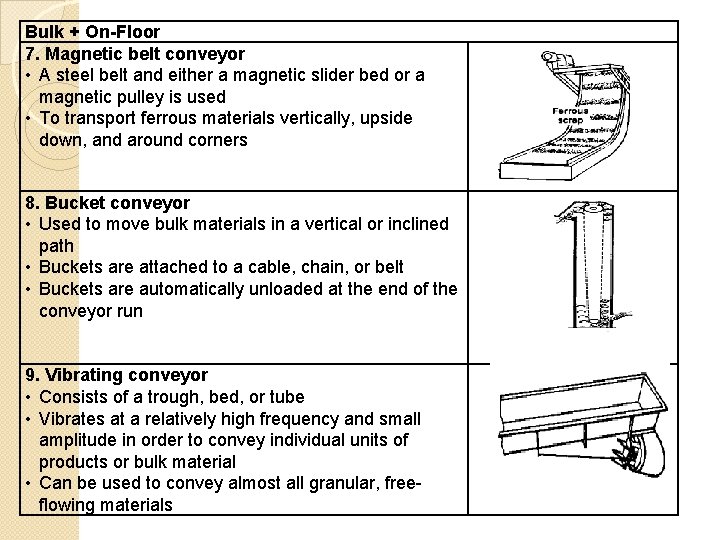
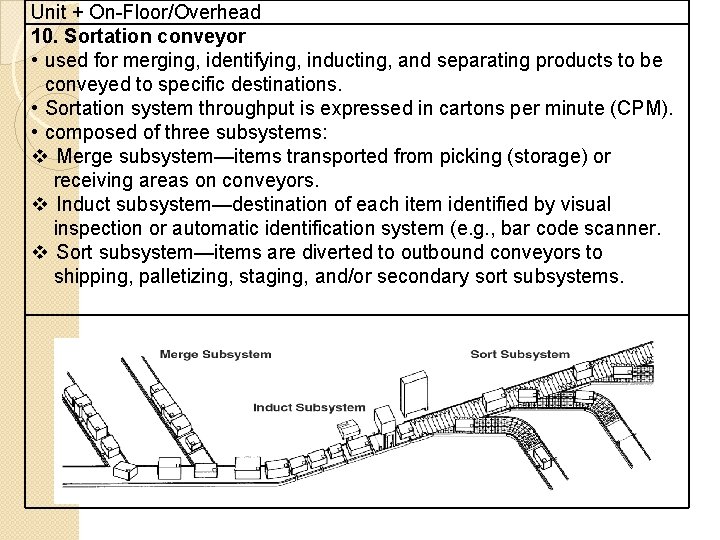

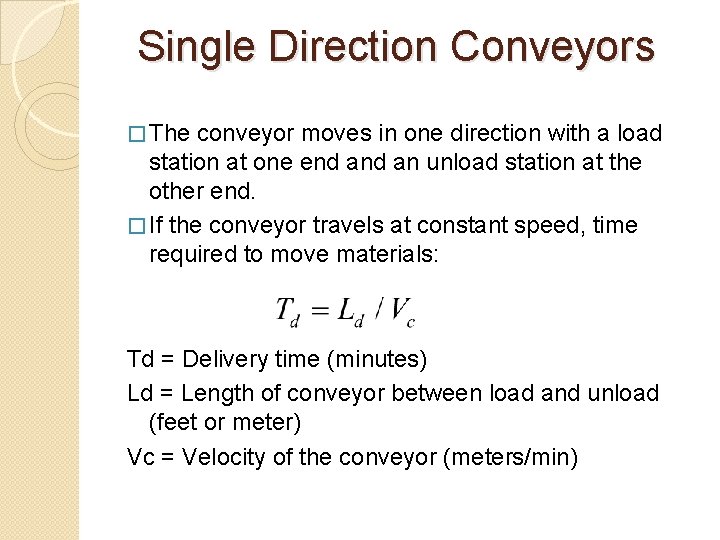
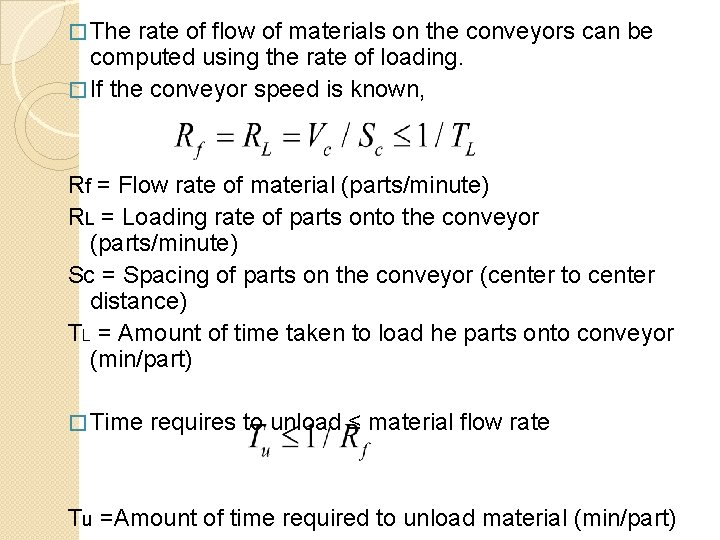
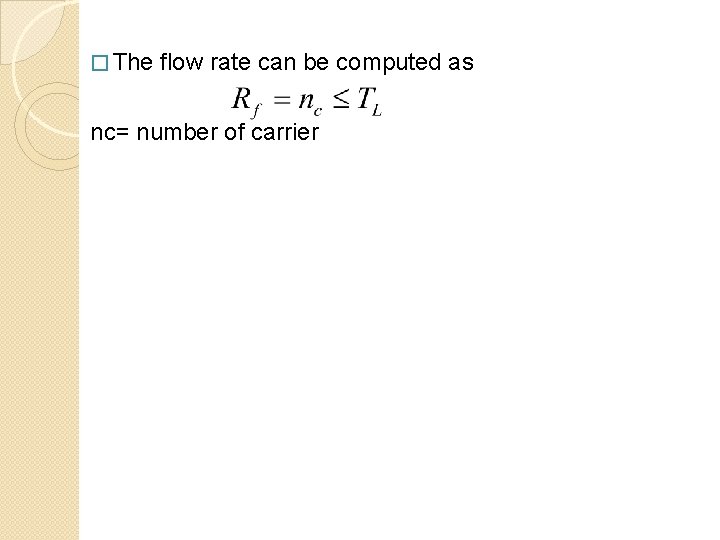
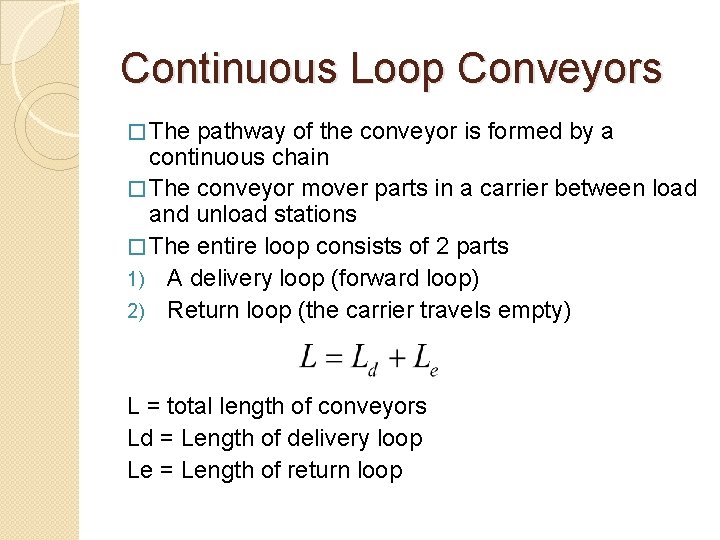
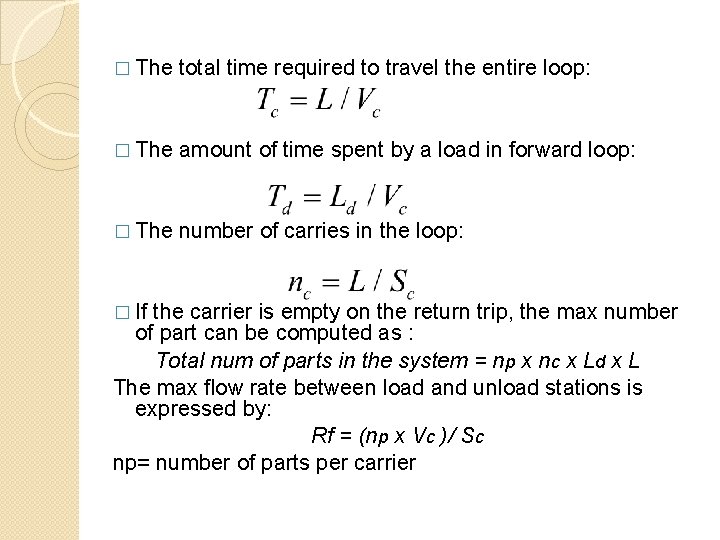
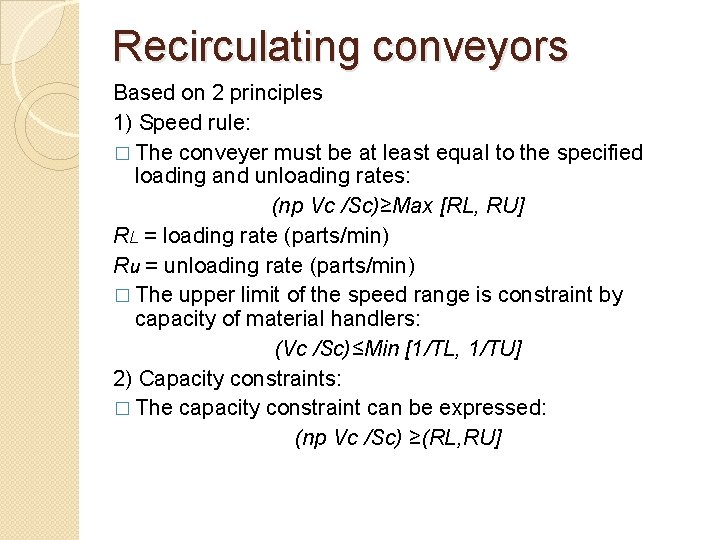
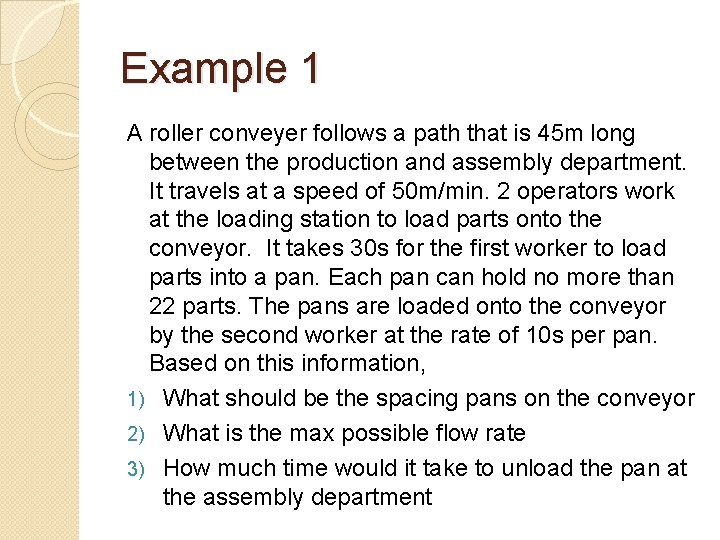
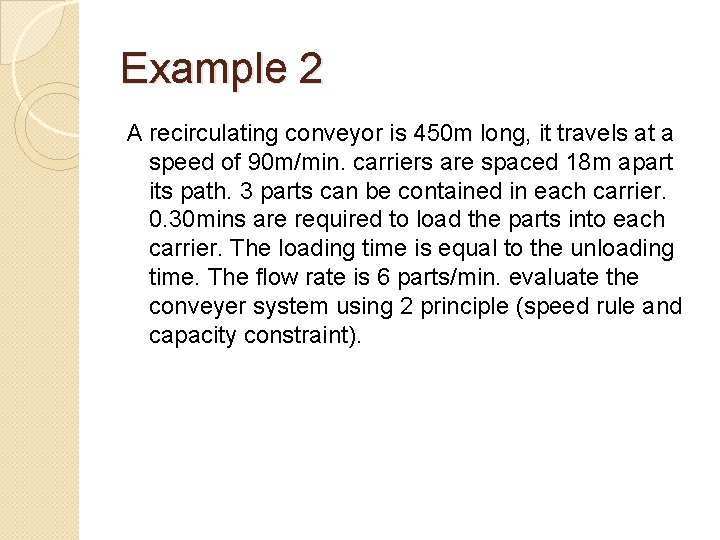
- Slides: 17
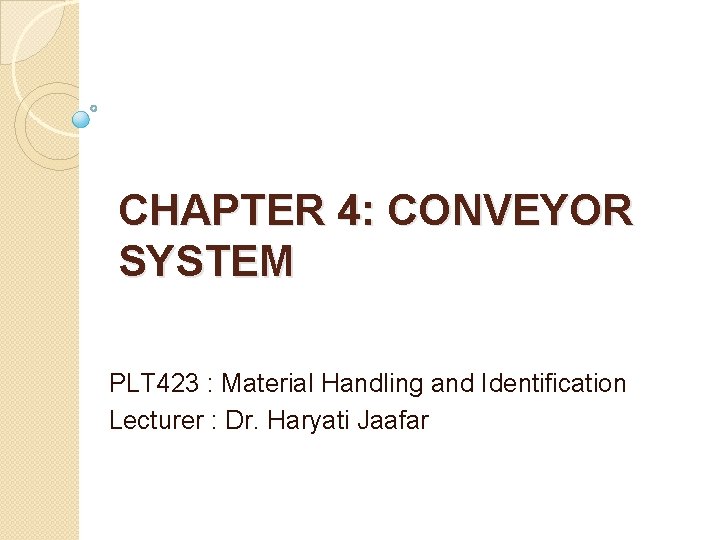
CHAPTER 4: CONVEYOR SYSTEM PLT 423 : Material Handling and Identification Lecturer : Dr. Haryati Jaafar
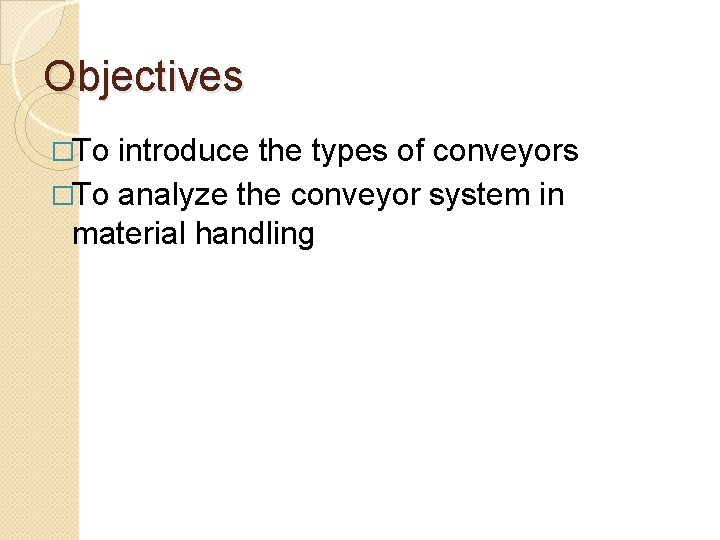
Objectives �To introduce the types of conveyors �To analyze the conveyor system in material handling
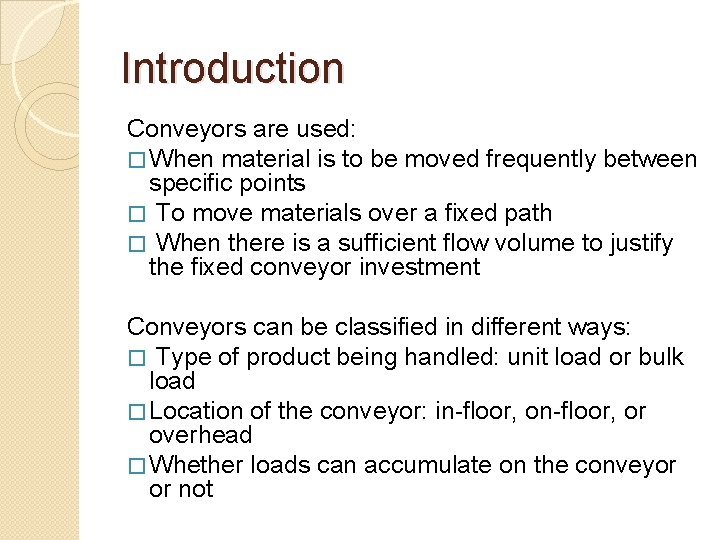
Introduction Conveyors are used: � When material is to be moved frequently between specific points � To move materials over a fixed path � When there is a sufficient flow volume to justify the fixed conveyor investment Conveyors can be classified in different ways: � Type of product being handled: unit load or bulk load � Location of the conveyor: in-floor, or overhead � Whether loads can accumulate on the conveyor or not
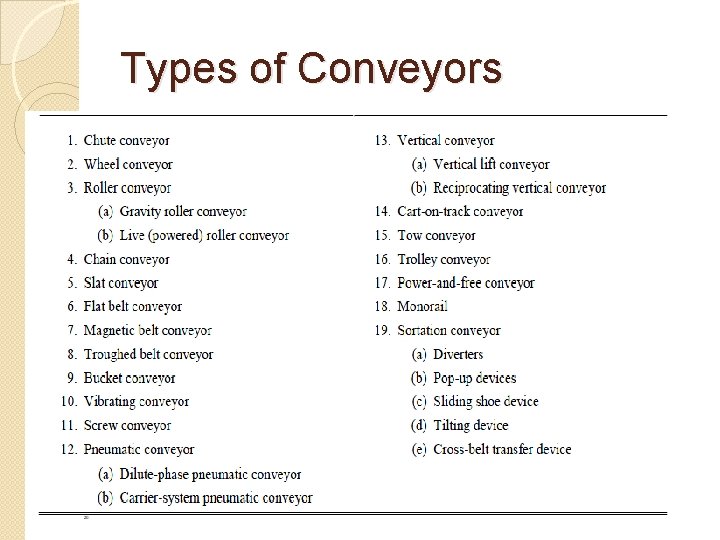
Types of Conveyors
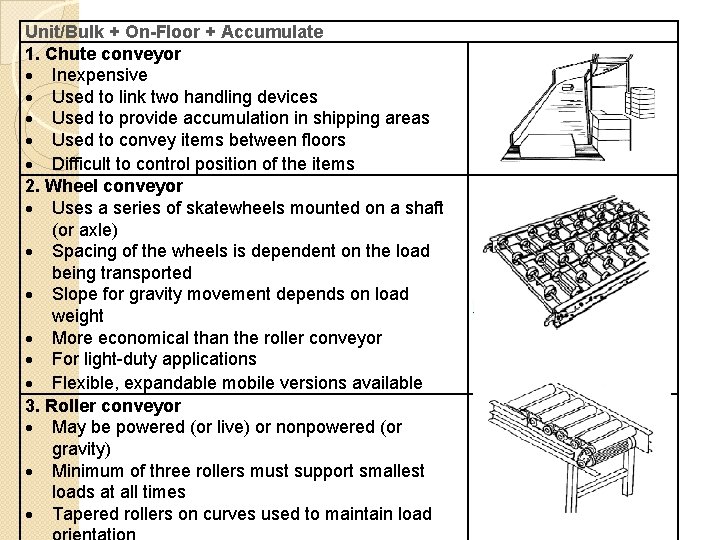
Unit/Bulk + On-Floor + Accumulate 1. Chute conveyor Inexpensive Used to link two handling devices Used to provide accumulation in shipping areas Used to convey items between floors Difficult to control position of the items 2. Wheel conveyor Uses a series of skatewheels mounted on a shaft (or axle) Spacing of the wheels is dependent on the load being transported Slope for gravity movement depends on load weight More economical than the roller conveyor For light-duty applications Flexible, expandable mobile versions available 3. Roller conveyor May be powered (or live) or nonpowered (or gravity) Minimum of three rollers must support smallest loads at all times Tapered rollers on curves used to maintain load
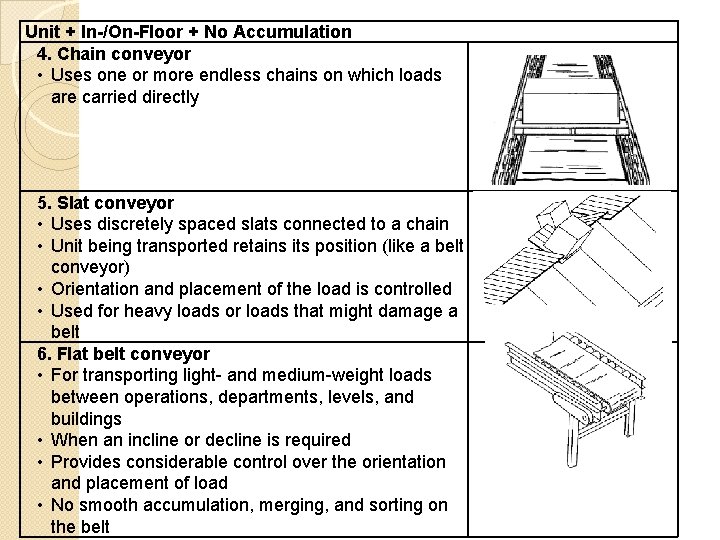
Unit + In-/On-Floor + No Accumulation 4. Chain conveyor • Uses one or more endless chains on which loads are carried directly 5. Slat conveyor • Uses discretely spaced slats connected to a chain • Unit being transported retains its position (like a belt conveyor) • Orientation and placement of the load is controlled • Used for heavy loads or loads that might damage a belt 6. Flat belt conveyor • For transporting light- and medium-weight loads between operations, departments, levels, and buildings • When an incline or decline is required • Provides considerable control over the orientation and placement of load • No smooth accumulation, merging, and sorting on the belt
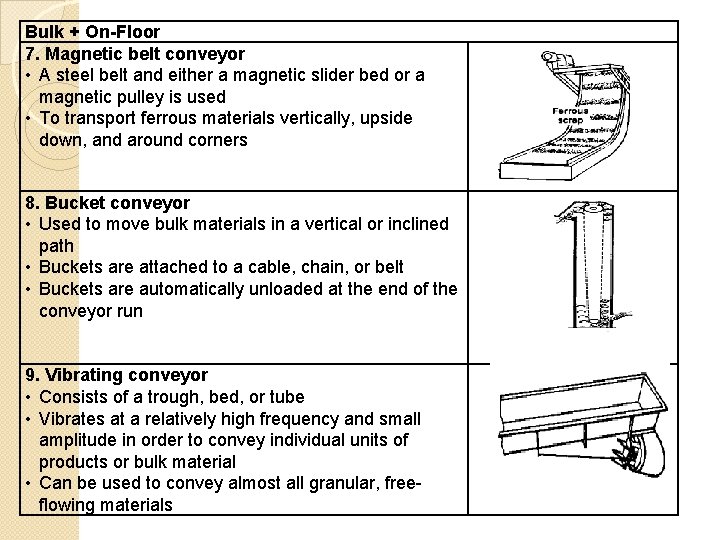
Bulk + On-Floor 7. Magnetic belt conveyor • A steel belt and either a magnetic slider bed or a magnetic pulley is used • To transport ferrous materials vertically, upside down, and around corners 8. Bucket conveyor • Used to move bulk materials in a vertical or inclined path • Buckets are attached to a cable, chain, or belt • Buckets are automatically unloaded at the end of the conveyor run 9. Vibrating conveyor • Consists of a trough, bed, or tube • Vibrates at a relatively high frequency and small amplitude in order to convey individual units of products or bulk material • Can be used to convey almost all granular, freeflowing materials
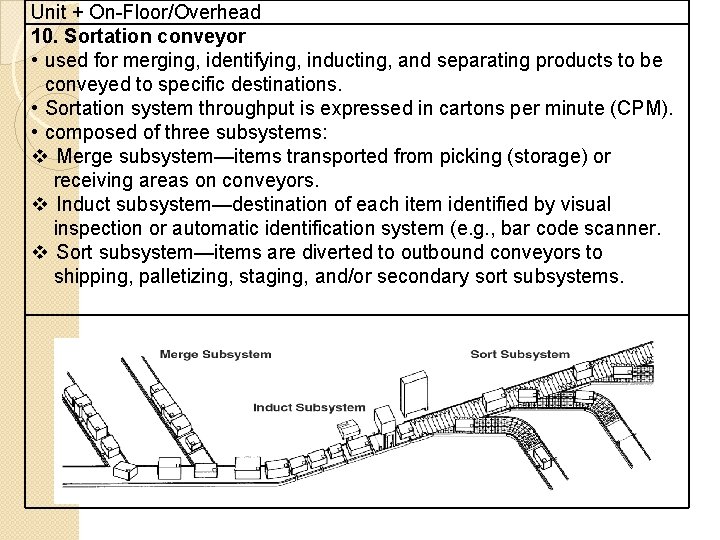
Unit + On-Floor/Overhead 10. Sortation conveyor • used for merging, identifying, inducting, and separating products to be conveyed to specific destinations. • Sortation system throughput is expressed in cartons per minute (CPM). • composed of three subsystems: v Merge subsystem—items transported from picking (storage) or receiving areas on conveyors. v Induct subsystem—destination of each item identified by visual inspection or automatic identification system (e. g. , bar code scanner. v Sort subsystem—items are diverted to outbound conveyors to shipping, palletizing, staging, and/or secondary sort subsystems.

Analysis of Conveyor System Three types of conveyors �Single direction conveyors �Continuous loop conveyors �Recirculating conveyors
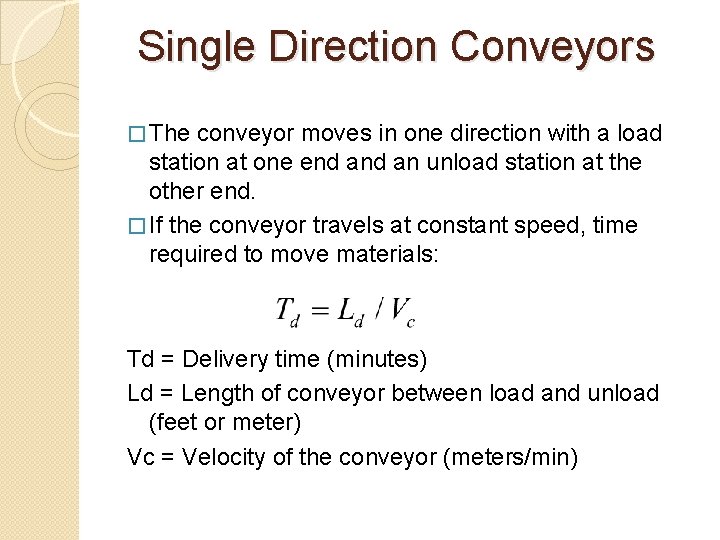
Single Direction Conveyors � The conveyor moves in one direction with a load station at one end an unload station at the other end. � If the conveyor travels at constant speed, time required to move materials: Td = Delivery time (minutes) Ld = Length of conveyor between load and unload (feet or meter) Vc = Velocity of the conveyor (meters/min)
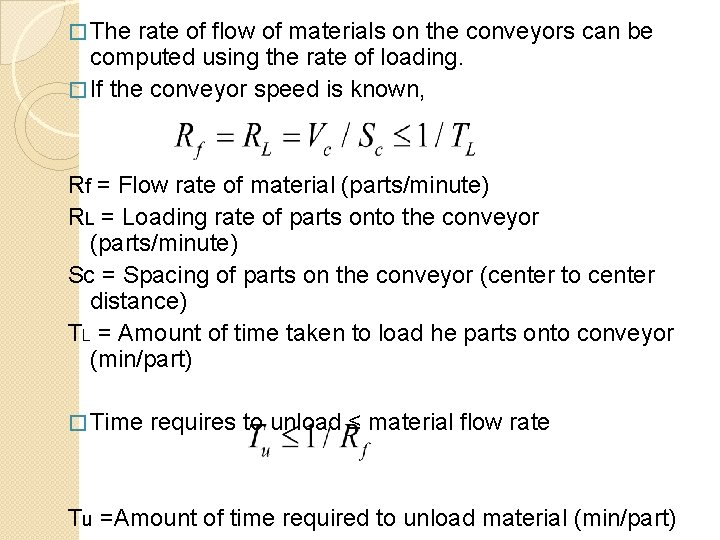
� The rate of flow of materials on the conveyors can be computed using the rate of loading. � If the conveyor speed is known, Rf = Flow rate of material (parts/minute) RL = Loading rate of parts onto the conveyor (parts/minute) Sc = Spacing of parts on the conveyor (center to center distance) TL = Amount of time taken to load he parts onto conveyor (min/part) � Time requires to unload ≤ material flow rate Tu =Amount of time required to unload material (min/part)
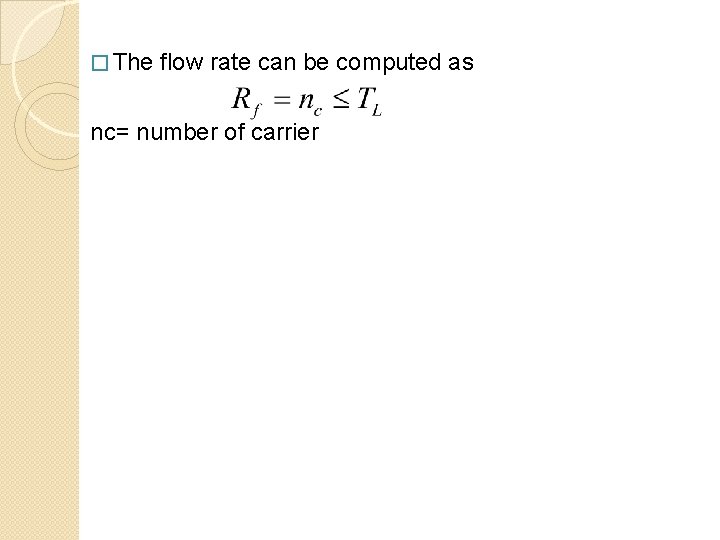
� The flow rate can be computed as nc= number of carrier
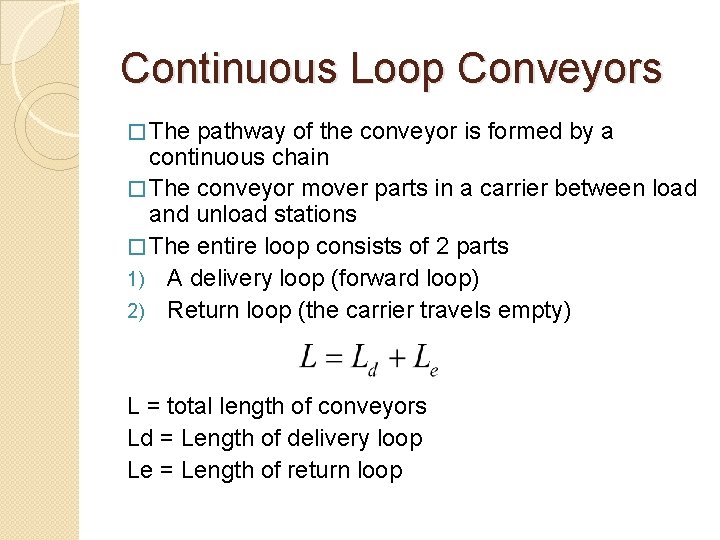
Continuous Loop Conveyors � The pathway of the conveyor is formed by a continuous chain � The conveyor mover parts in a carrier between load and unload stations � The entire loop consists of 2 parts 1) A delivery loop (forward loop) 2) Return loop (the carrier travels empty) L = total length of conveyors Ld = Length of delivery loop Le = Length of return loop
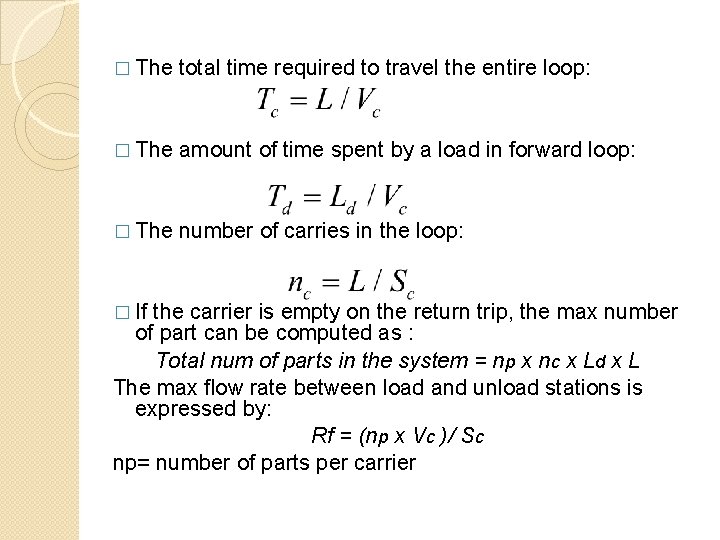
� The total time required to travel the entire loop: � The amount of time spent by a load in forward loop: � The number of carries in the loop: � If the carrier is empty on the return trip, the max number of part can be computed as : Total num of parts in the system = np x nc x Ld x L The max flow rate between load and unload stations is expressed by: Rf = (np x Vc )/ Sc np= number of parts per carrier
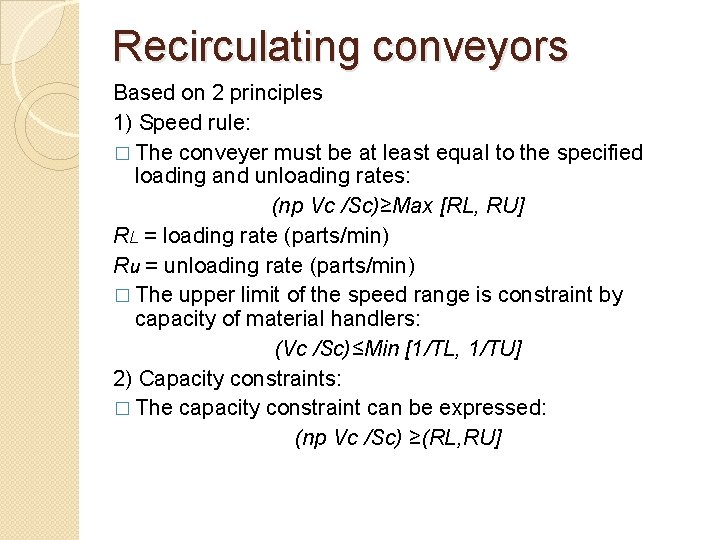
Recirculating conveyors Based on 2 principles 1) Speed rule: � The conveyer must be at least equal to the specified loading and unloading rates: (np Vc /Sc)≥Max [RL, RU] RL = loading rate (parts/min) Ru = unloading rate (parts/min) � The upper limit of the speed range is constraint by capacity of material handlers: (Vc /Sc)≤Min [1/TL, 1/TU] 2) Capacity constraints: � The capacity constraint can be expressed: (np Vc /Sc) ≥(RL, RU]
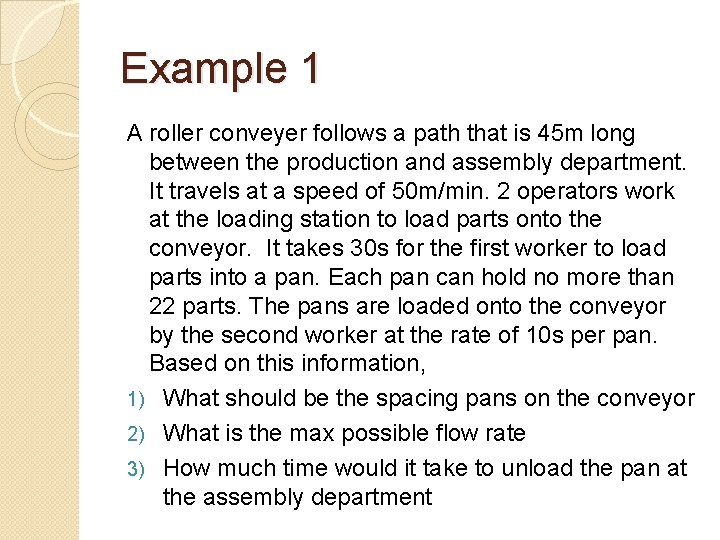
Example 1 A roller conveyer follows a path that is 45 m long between the production and assembly department. It travels at a speed of 50 m/min. 2 operators work at the loading station to load parts onto the conveyor. It takes 30 s for the first worker to load parts into a pan. Each pan can hold no more than 22 parts. The pans are loaded onto the conveyor by the second worker at the rate of 10 s per pan. Based on this information, 1) What should be the spacing pans on the conveyor 2) What is the max possible flow rate 3) How much time would it take to unload the pan at the assembly department
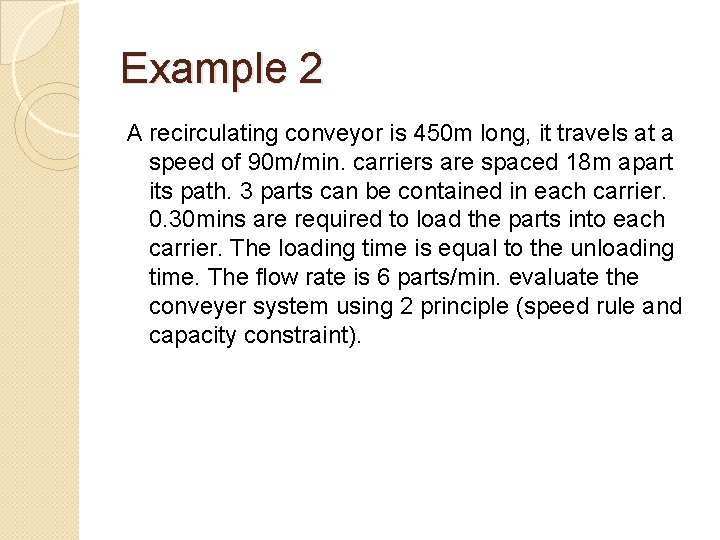
Example 2 A recirculating conveyor is 450 m long, it travels at a speed of 90 m/min. carriers are spaced 18 m apart its path. 3 parts can be contained in each carrier. 0. 30 mins are required to load the parts into each carrier. The loading time is equal to the unloading time. The flow rate is 6 parts/min. evaluate the conveyer system using 2 principle (speed rule and capacity constraint).
Introduction to materials handling
Material handling principle
Pertanyaan tentang tata letak fasilitas pabrik
A way to prevent materials handling hazards is to ___.
Unit load
Manajemen industri perikanan
Material handling introduction
Material handling costs
Dilip lift truck
Riekes material handling
Tines
Material handling efficiency
Principles of material handling
Material handling objectives
Material handling and facilities planning
Dilip material handling equipment
Industrial robotics ppt
Tines