A Complete ClosedLoop CCATreated Wood Recycling System ChungYun
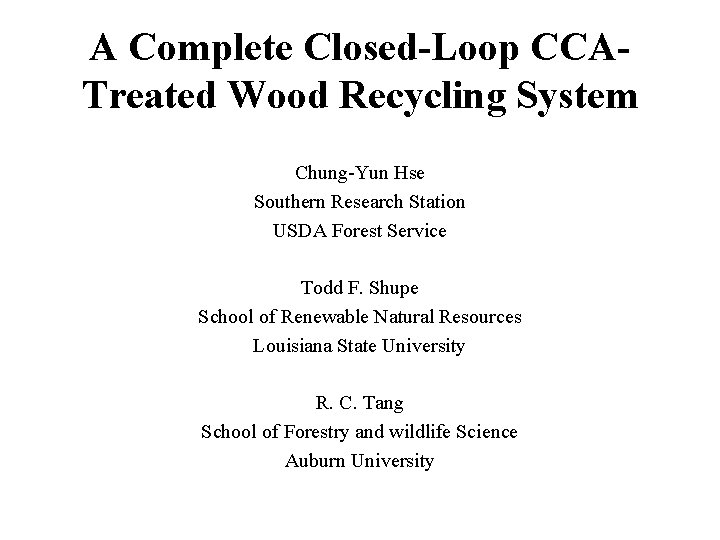
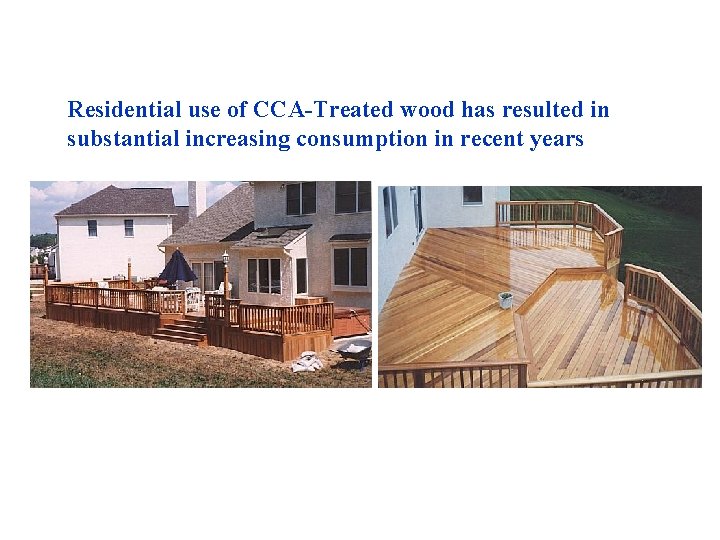
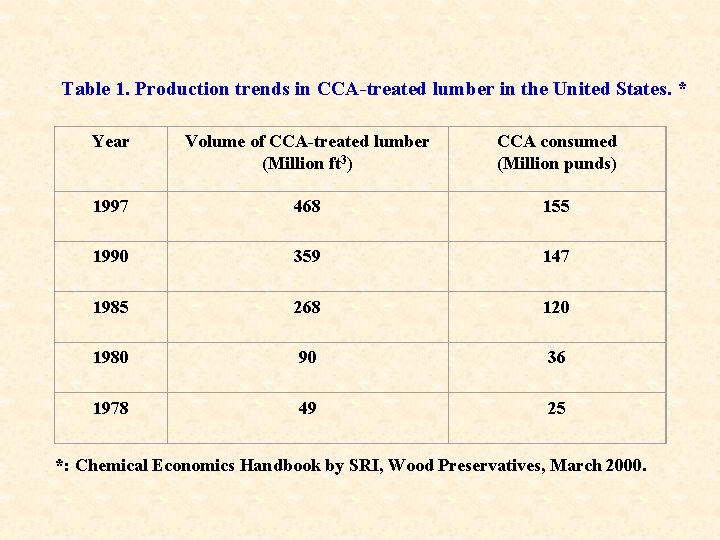
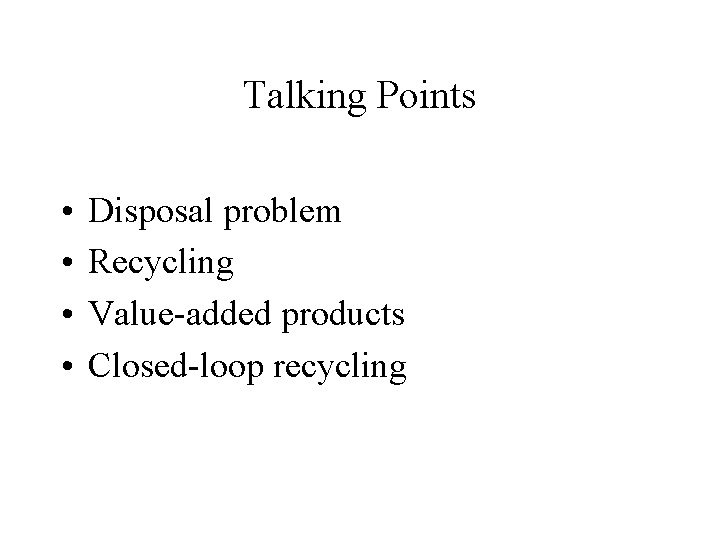
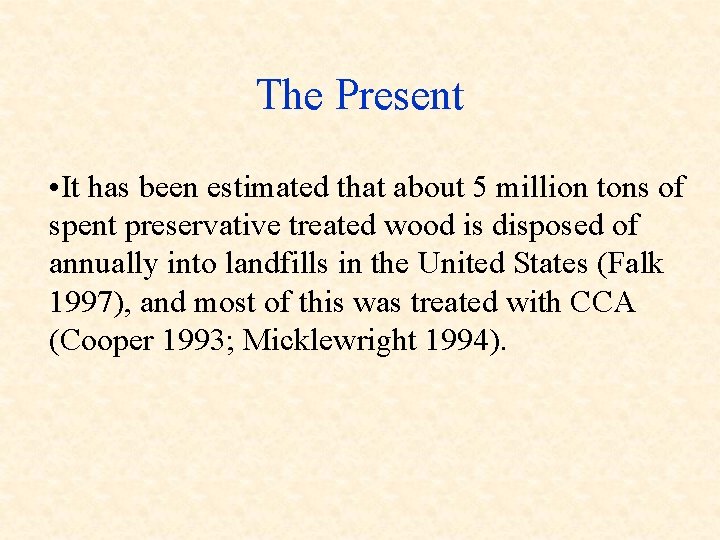
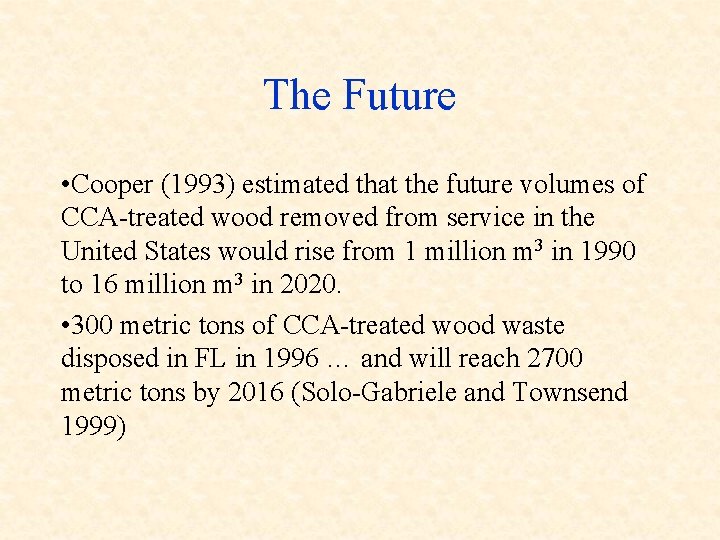
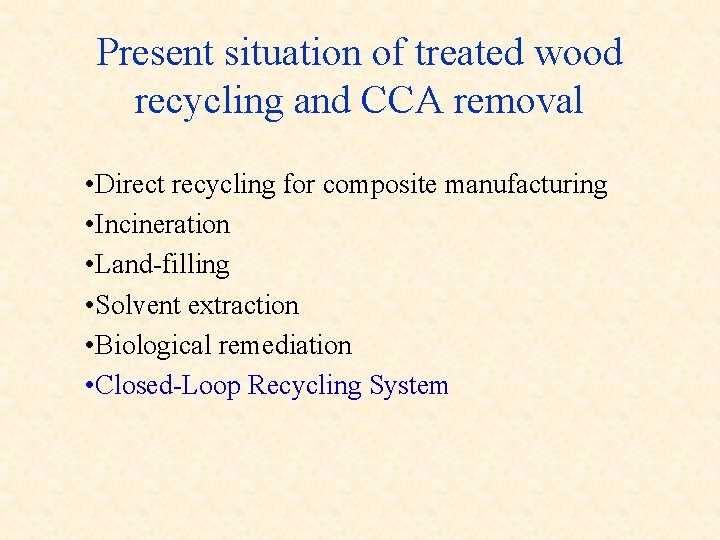
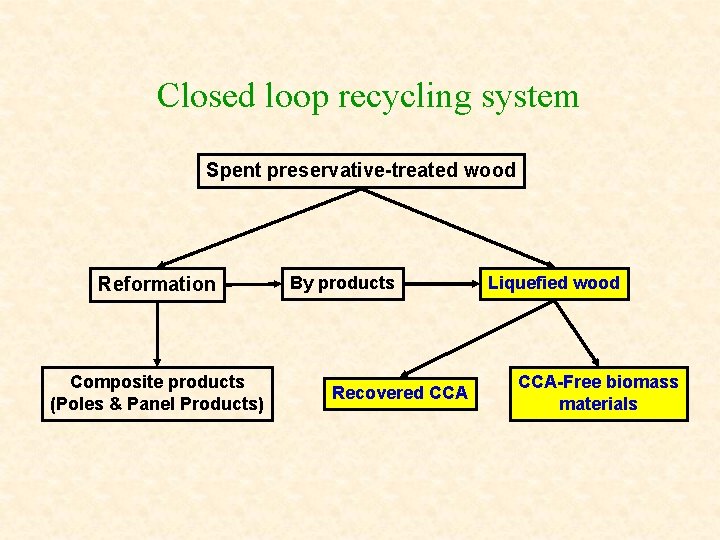
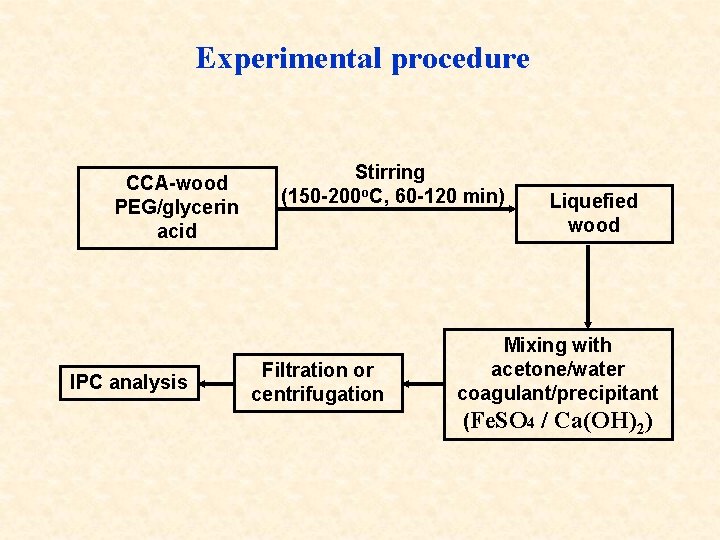
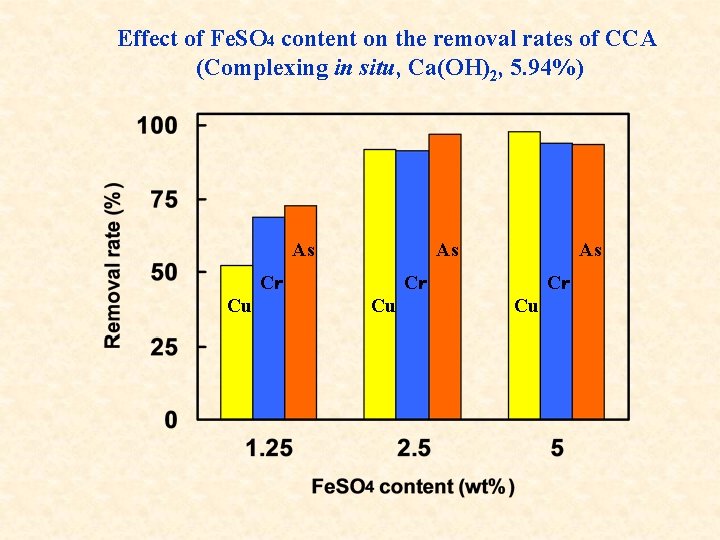
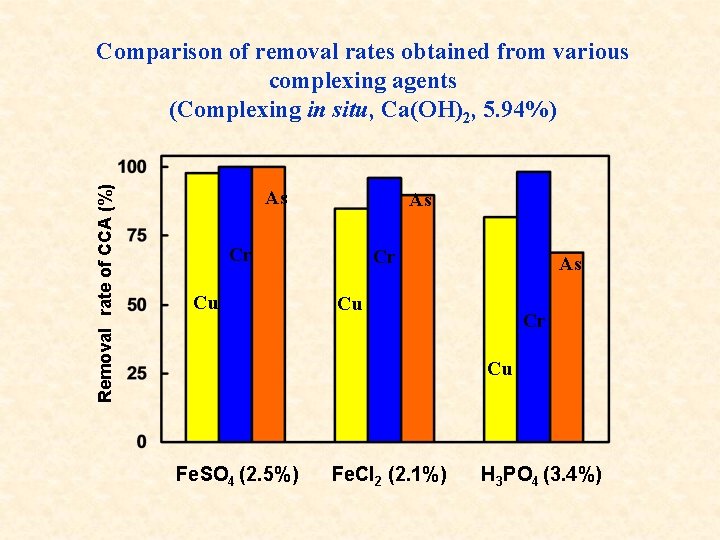
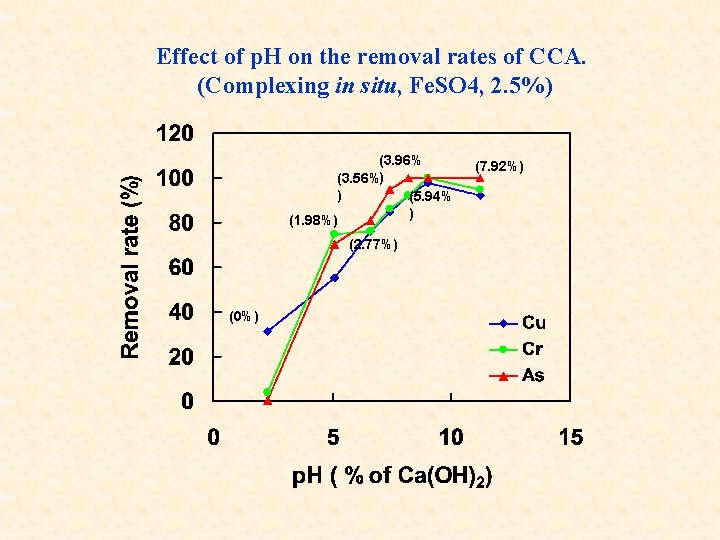
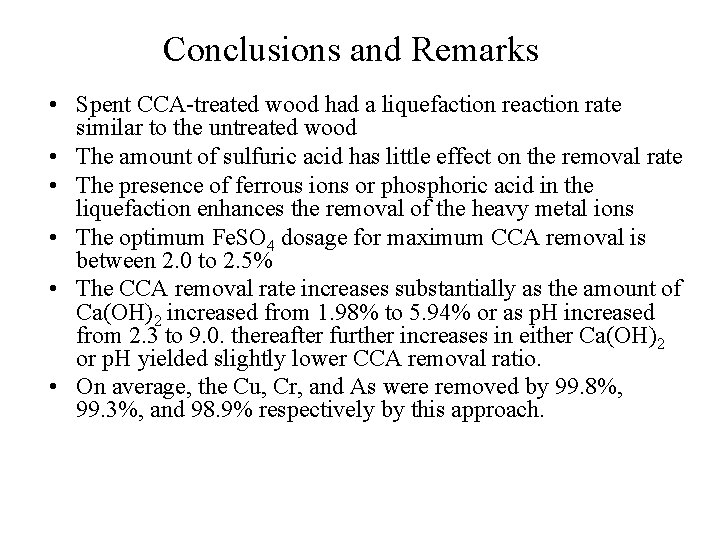
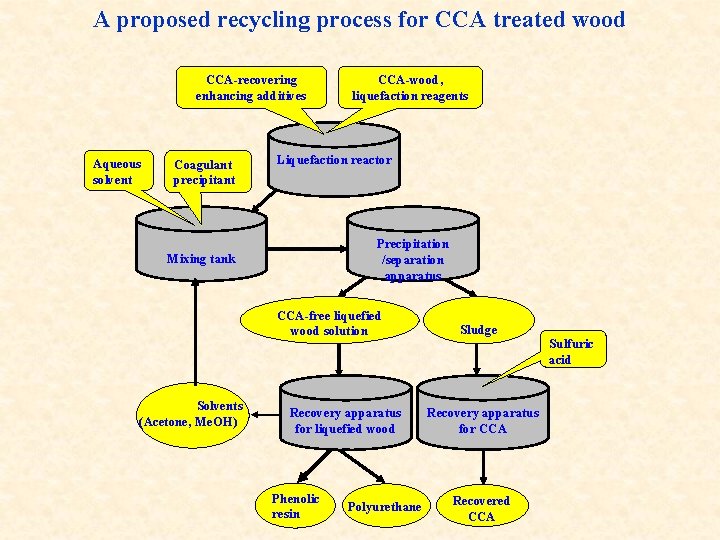
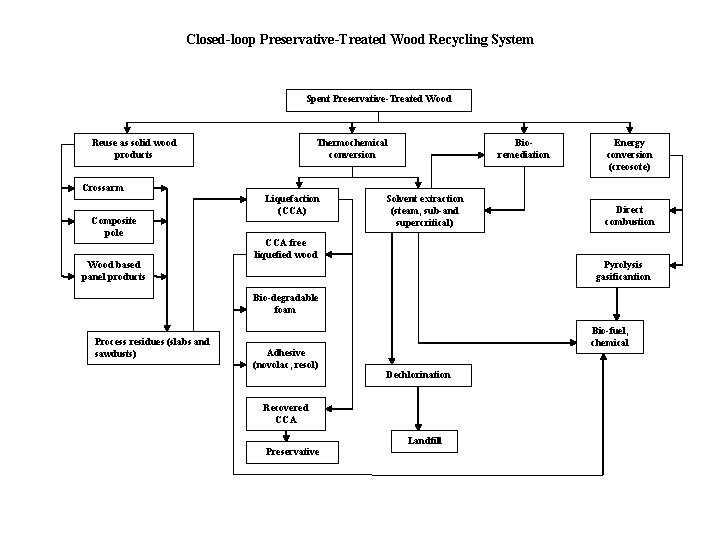
- Slides: 15
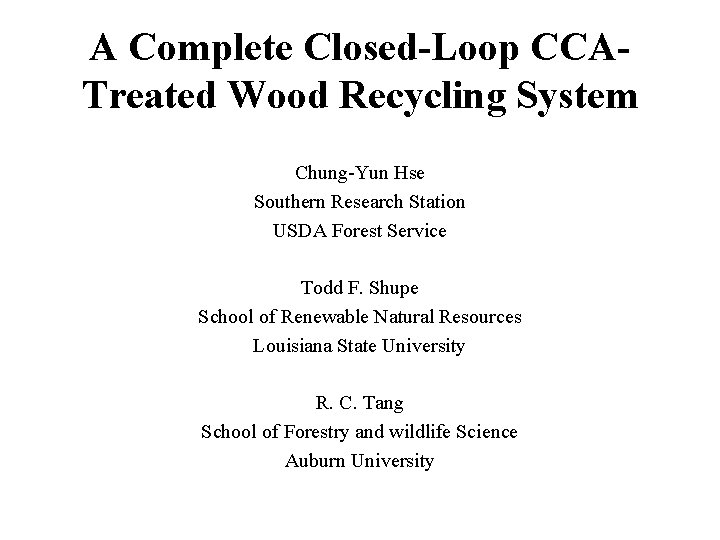
A Complete Closed-Loop CCATreated Wood Recycling System Chung-Yun Hse Southern Research Station USDA Forest Service Todd F. Shupe School of Renewable Natural Resources Louisiana State University R. C. Tang School of Forestry and wildlife Science Auburn University
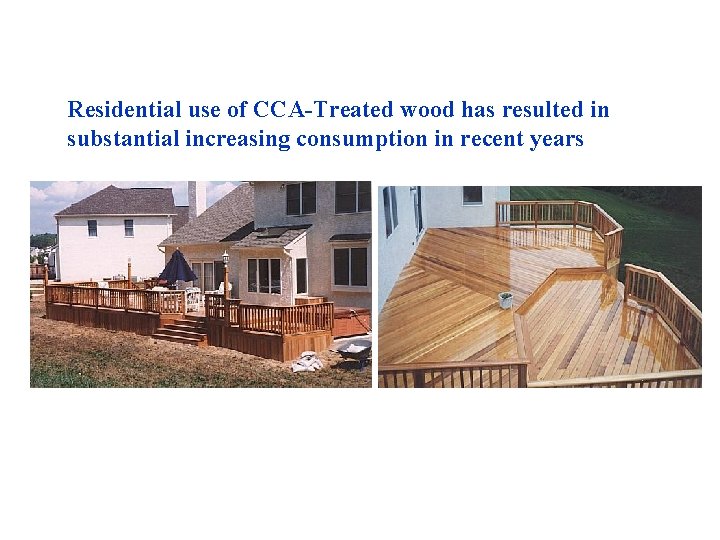
Residential use of CCA-Treated wood has resulted in substantial increasing consumption in recent years
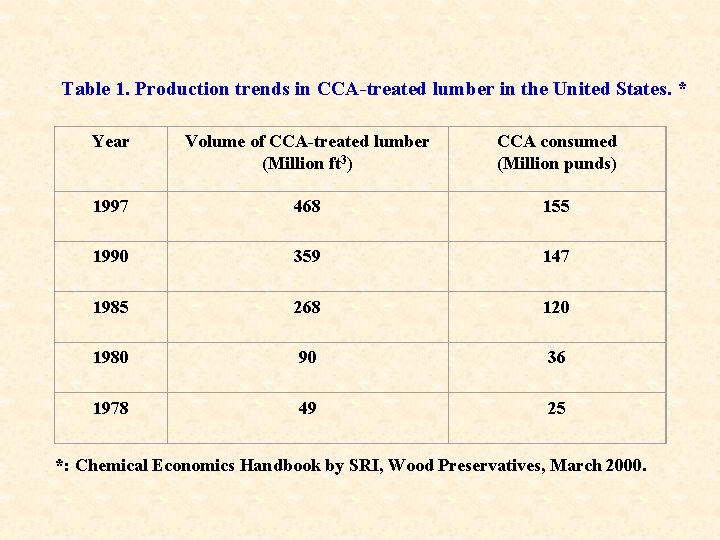
Table 1. Production trends in CCA-treated lumber in the United States. * Year Volume of CCA-treated lumber (Million ft 3) CCA consumed (Million punds) 1997 468 155 1990 359 147 1985 268 120 1980 90 36 1978 49 25 *: Chemical Economics Handbook by SRI, Wood Preservatives, March 2000.
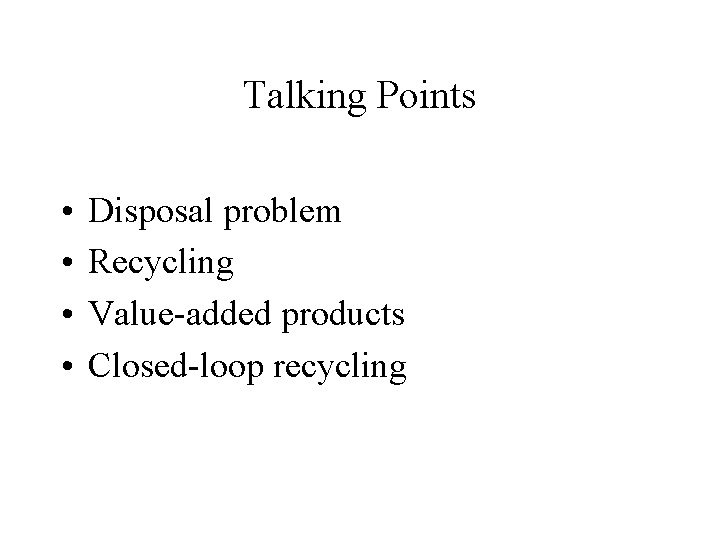
Talking Points • • Disposal problem Recycling Value-added products Closed-loop recycling
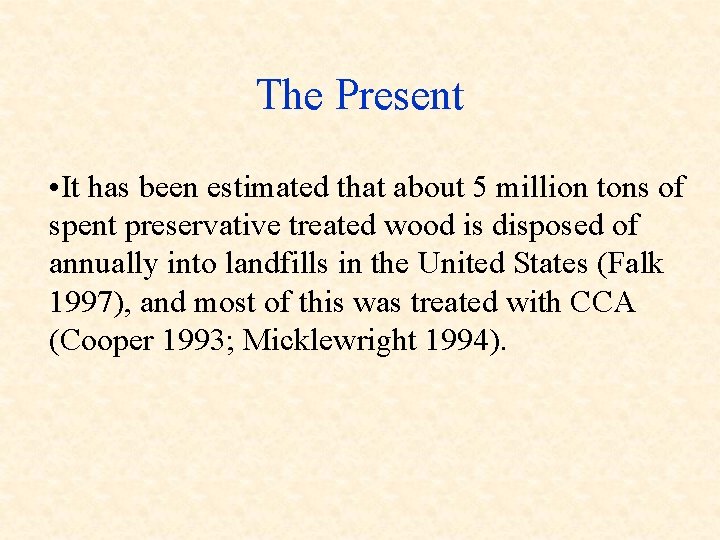
The Present • It has been estimated that about 5 million tons of spent preservative treated wood is disposed of annually into landfills in the United States (Falk 1997), and most of this was treated with CCA (Cooper 1993; Micklewright 1994).
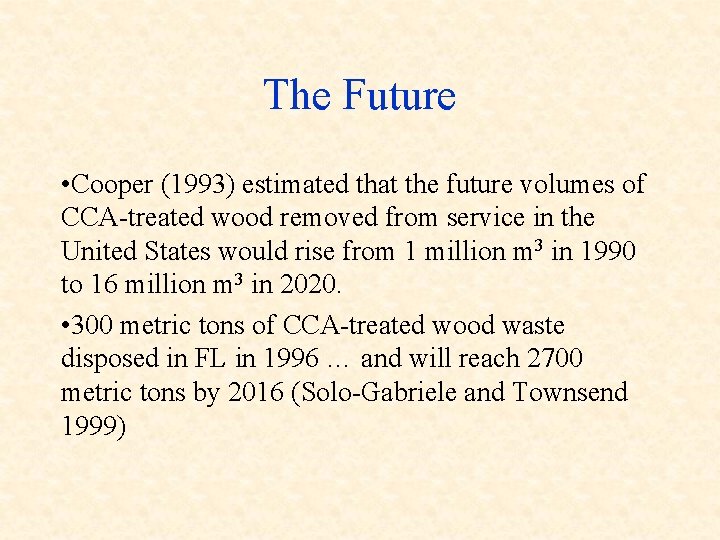
The Future • Cooper (1993) estimated that the future volumes of CCA-treated wood removed from service in the United States would rise from 1 million m 3 in 1990 to 16 million m 3 in 2020. • 300 metric tons of CCA-treated wood waste disposed in FL in 1996 … and will reach 2700 metric tons by 2016 (Solo-Gabriele and Townsend 1999)
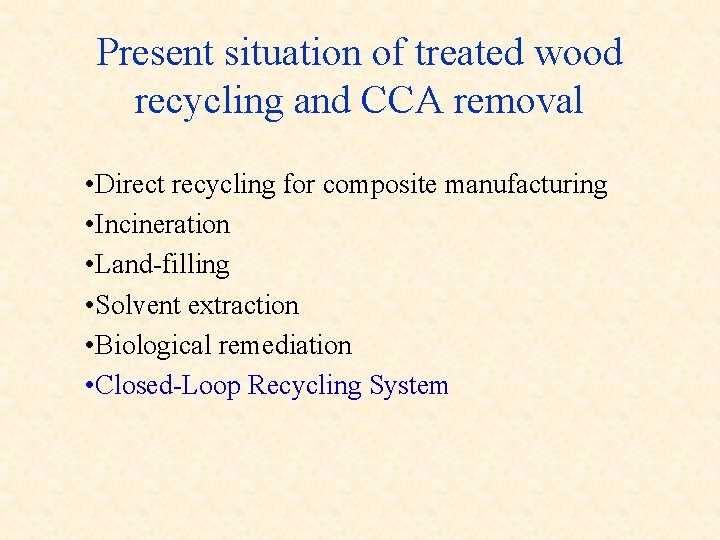
Present situation of treated wood recycling and CCA removal • Direct recycling for composite manufacturing • Incineration • Land-filling • Solvent extraction • Biological remediation • Closed-Loop Recycling System
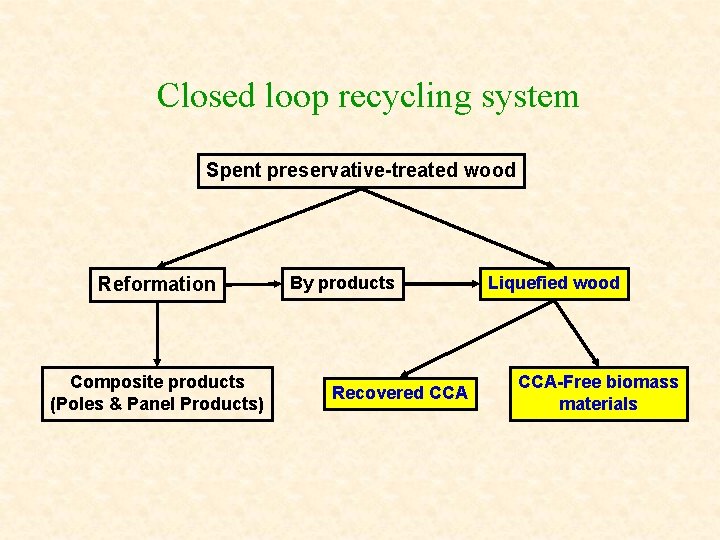
Closed loop recycling system Spent preservative-treated wood Reformation Composite products (Poles & Panel Products) By products Recovered CCA Liquefied wood CCA-Free biomass materials
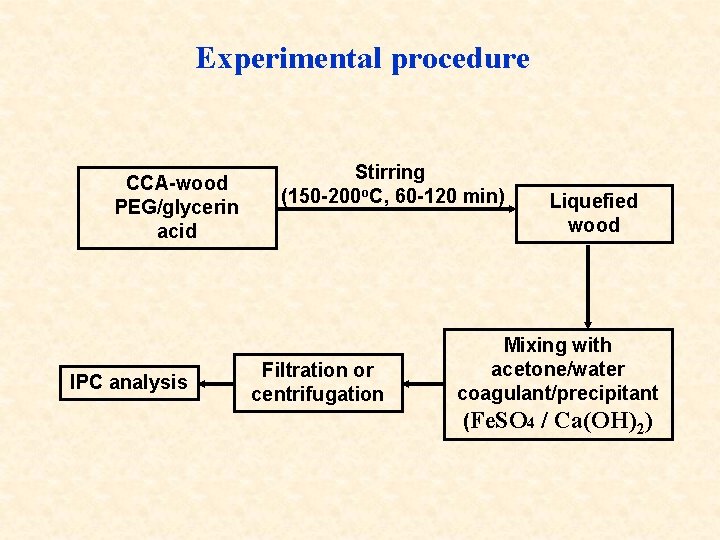
Experimental procedure CCA-wood PEG/glycerin acid IPC analysis Stirring (150 -200 o. C, 60 -120 min) Filtration or centrifugation Liquefied wood Mixing with acetone/water coagulant/precipitant (Fe. SO 4 / Ca(OH)2)
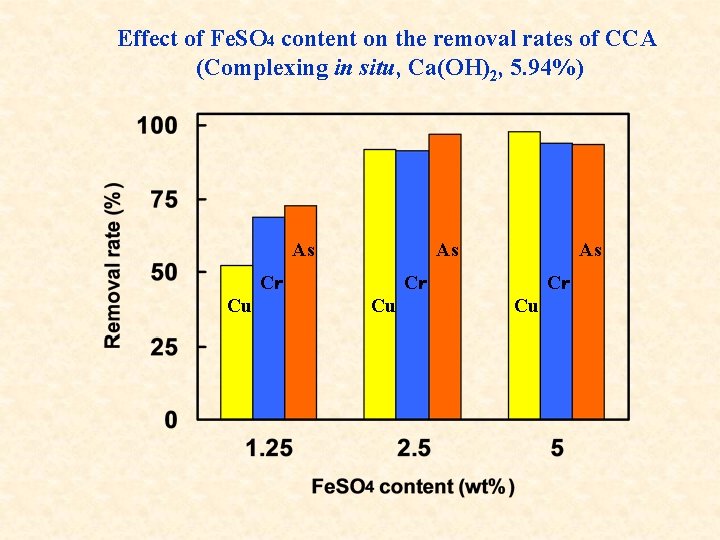
Effect of Fe. SO 4 content on the removal rates of CCA (Complexing in situ, Ca(OH)2, 5. 94%) As As Cr Cu
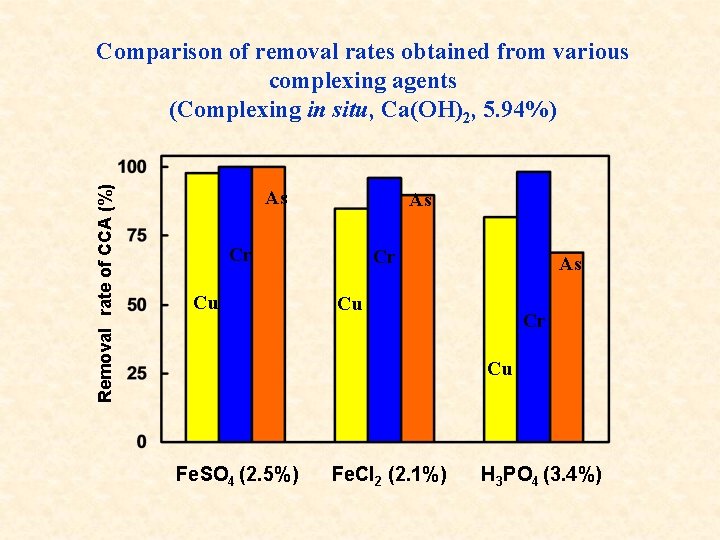
Removal rate of CCA (%) Comparison of removal rates obtained from various complexing agents (Complexing in situ, Ca(OH)2, 5. 94%) As As Cr Cu Cr As Cu Cr Cu Fe. SO 4 (2. 5%) Fe. Cl 2 (2. 1%) H 3 PO 4 (3. 4%)
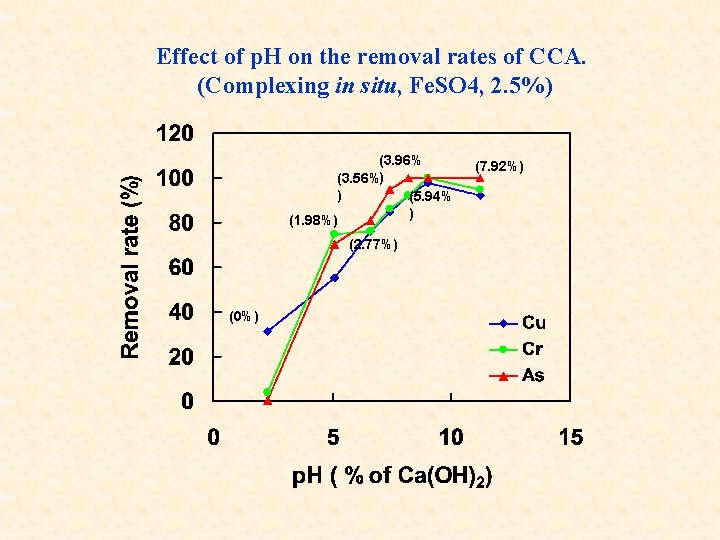
Effect of p. H on the removal rates of CCA. (Complexing in situ, Fe. SO 4, 2. 5%) (3. 96% (3. 56%) ) (5. 94% ) (1. 98%) (2. 77%) (0%) (7. 92%)
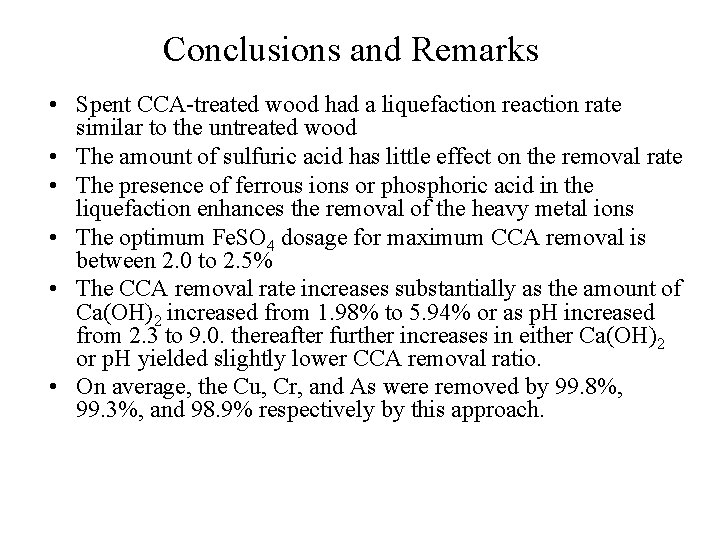
Conclusions and Remarks • Spent CCA-treated wood had a liquefaction reaction rate similar to the untreated wood • The amount of sulfuric acid has little effect on the removal rate • The presence of ferrous ions or phosphoric acid in the liquefaction enhances the removal of the heavy metal ions • The optimum Fe. SO 4 dosage for maximum CCA removal is between 2. 0 to 2. 5% • The CCA removal rate increases substantially as the amount of Ca(OH)2 increased from 1. 98% to 5. 94% or as p. H increased from 2. 3 to 9. 0. thereafter further increases in either Ca(OH)2 or p. H yielded slightly lower CCA removal ratio. • On average, the Cu, Cr, and As were removed by 99. 8%, 99. 3%, and 98. 9% respectively by this approach.
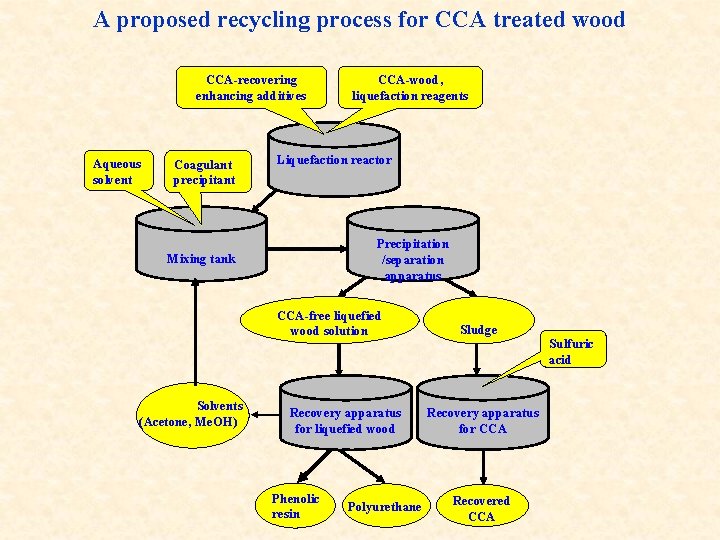
A proposed recycling process for CCA treated wood CCA-recovering enhancing additives Aqueous solvent Coagulant precipitant CCA-wood, liquefaction reagents Liquefaction reactor Precipitation /separation apparatus Mixing tank CCA-free liquefied wood solution Solvents (Acetone, Me. OH) Recovery apparatus for liquefied wood Phenolic resin Polyurethane Sludge Recovery apparatus for CCA Recovered CCA Sulfuric acid
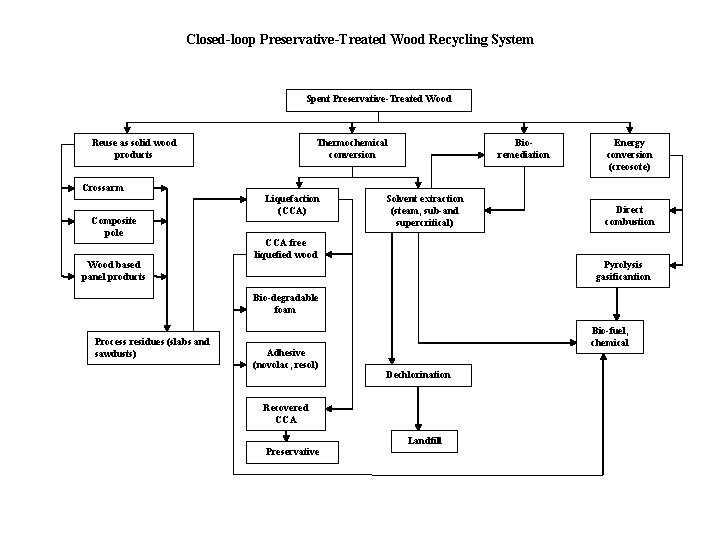
Closed-loop Preservative-Treated Wood Recycling System Spent Preservative-Treated Wood Reuse as solid wood products Crossarm Composite pole Wood based panel products Thermochemical conversion Liquefaction (CCA) Bioremediation Solvent extraction (steam, sub-and supercritical) CCA free liquefied wood Energy conversion (creosote) Direct combustion Pyrolysis gasificantion Bio-degradable foam Process residues (slabs and sawdusts) Adhesive (novolac, resol) Bio-fuel, chemical Dechlorination Recovered CCA Preservative Landfill
Wood recycling swansea
Early wood and late wood
Roots vegetative propagation
Gymnosperm structure
Wood sawed wood old tongue twister
Wood wood teenager
Gersmehl nutrient cycle
Complete the missing word to complete the three key words
The complete subject
Wood frame system components
Breton wood system
Sustainable barbados recycling centre
Stafford county recycling
What are the cons of recycling
Thermoset recycling
3 benefits of recycling