1 ATLAS Upgrade WP 4 Face to Face
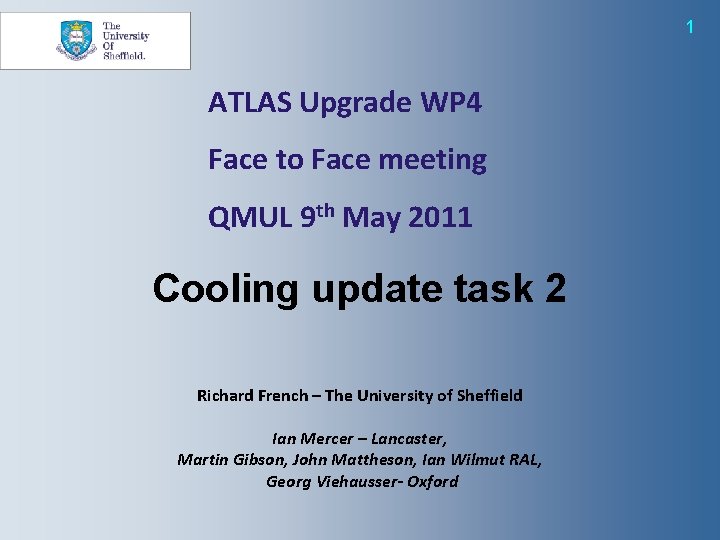
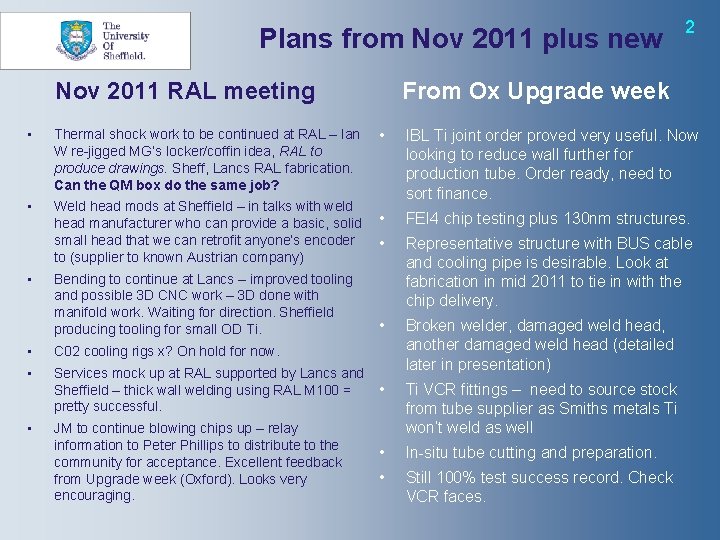
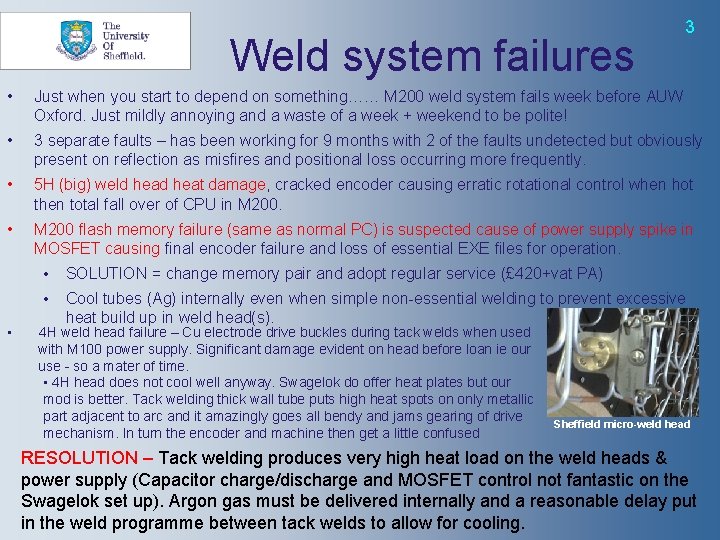
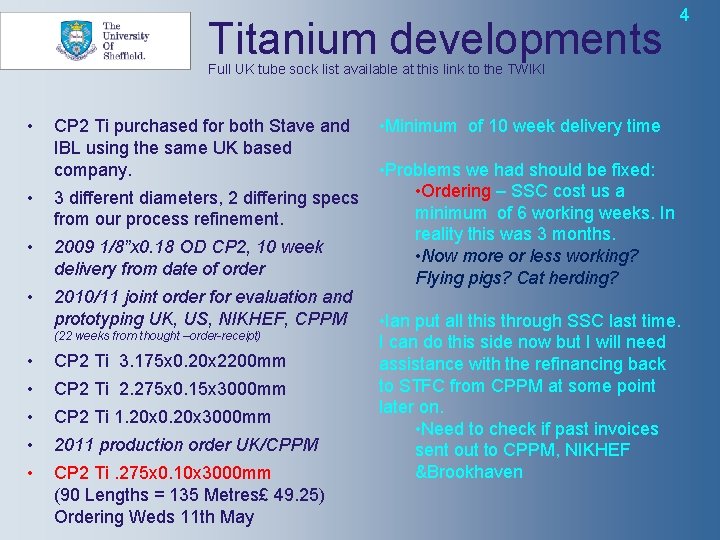
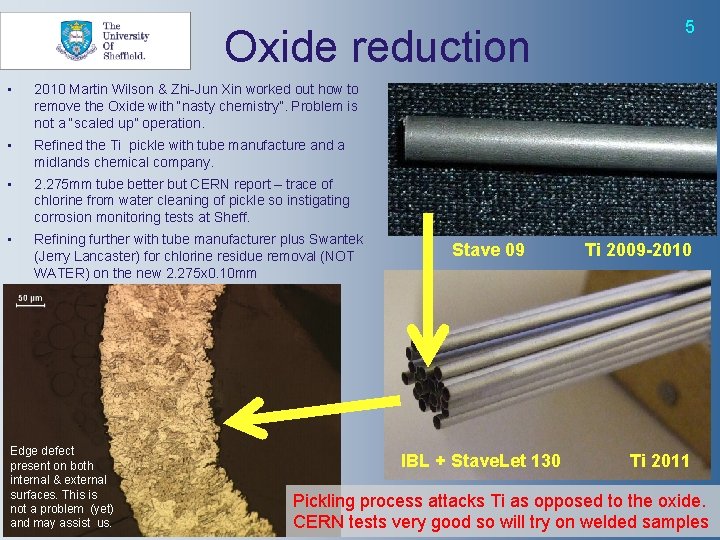
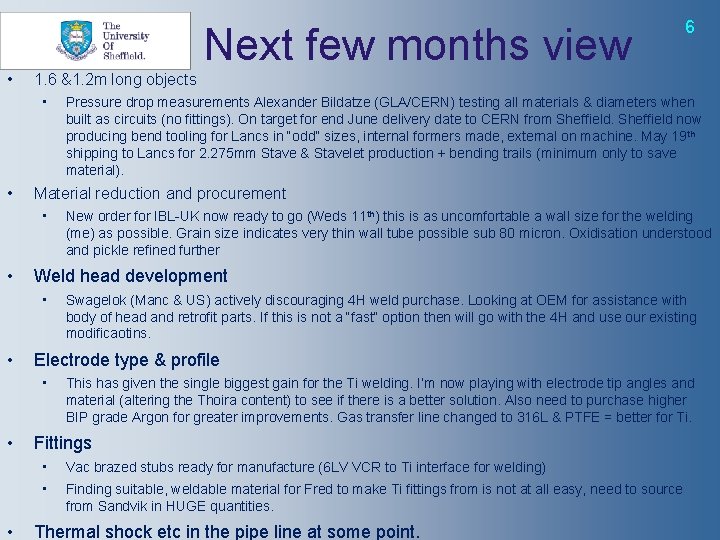
- Slides: 6
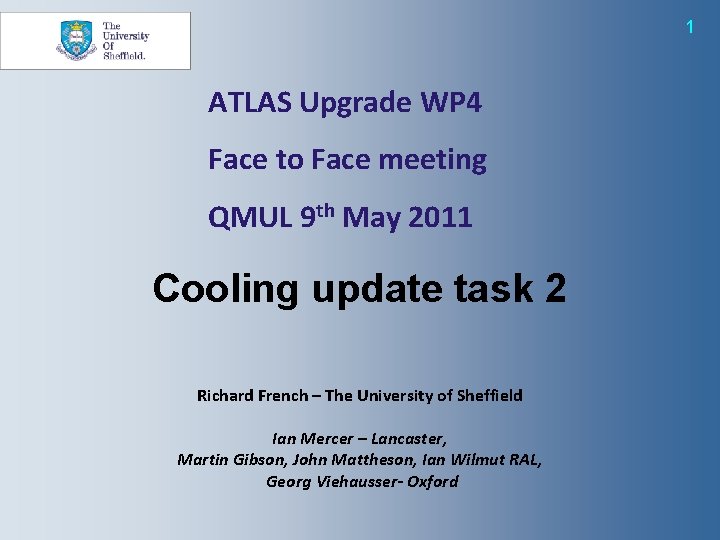
1 ATLAS Upgrade WP 4 Face to Face meeting QMUL 9 th May 2011 Cooling update task 2 Richard French – The University of Sheffield Ian Mercer – Lancaster, Martin Gibson, John Mattheson, Ian Wilmut RAL, Georg Viehausser- Oxford
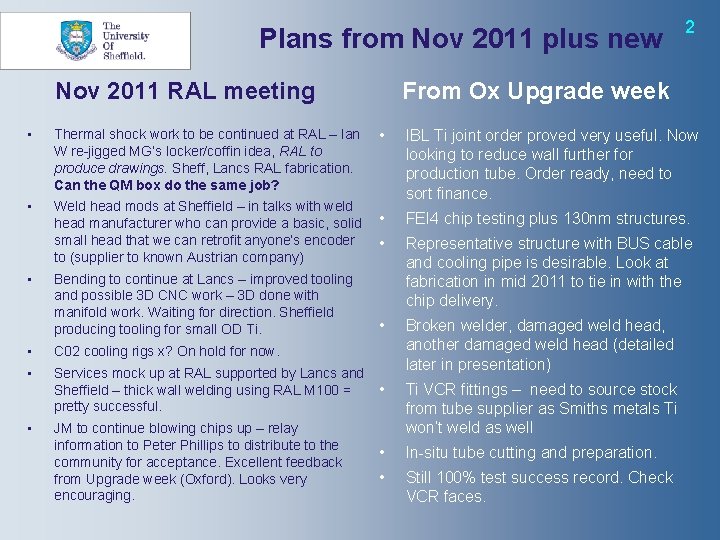
Plans from Nov 2011 plus new Nov 2011 RAL meeting • Thermal shock work to be continued at RAL – Ian W re-jigged MG’s locker/coffin idea, RAL to produce drawings. Sheff, Lancs RAL fabrication. Can the QM box do the same job? • Weld head mods at Sheffield – in talks with weld head manufacturer who can provide a basic, solid small head that we can retrofit anyone’s encoder to (supplier to known Austrian company) • Bending to continue at Lancs – improved tooling and possible 3 D CNC work – 3 D done with manifold work. Waiting for direction. Sheffield producing tooling for small OD Ti. • C 02 cooling rigs x? On hold for now. • Services mock up at RAL supported by Lancs and Sheffield – thick wall welding using RAL M 100 = pretty successful. • JM to continue blowing chips up – relay information to Peter Phillips to distribute to the community for acceptance. Excellent feedback from Upgrade week (Oxford). Looks very encouraging. 2 From Ox Upgrade week • IBL Ti joint order proved very useful. Now looking to reduce wall further for production tube. Order ready, need to sort finance. • FEI 4 chip testing plus 130 nm structures. • Representative structure with BUS cable and cooling pipe is desirable. Look at fabrication in mid 2011 to tie in with the chip delivery. • Broken welder, damaged weld head, another damaged weld head (detailed later in presentation) • Ti VCR fittings – need to source stock from tube supplier as Smiths metals Ti won’t weld as well • In-situ tube cutting and preparation. • Still 100% test success record. Check VCR faces.
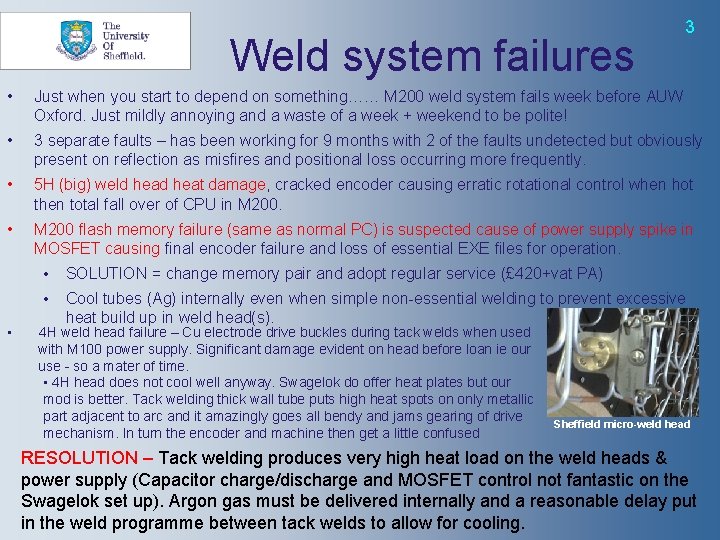
Weld system failures 3 • Just when you start to depend on something…… M 200 weld system fails week before AUW Oxford. Just mildly annoying and a waste of a week + weekend to be polite! • 3 separate faults – has been working for 9 months with 2 of the faults undetected but obviously present on reflection as misfires and positional loss occurring more frequently. • 5 H (big) weld heat damage, cracked encoder causing erratic rotational control when hot then total fall over of CPU in M 200. • M 200 flash memory failure (same as normal PC) is suspected cause of power supply spike in MOSFET causing final encoder failure and loss of essential EXE files for operation. • • SOLUTION = change memory pair and adopt regular service (£ 420+vat PA) • Cool tubes (Ag) internally even when simple non-essential welding to prevent excessive heat build up in weld head(s). 4 H weld head failure – Cu electrode drive buckles during tack welds when used with M 100 power supply. Significant damage evident on head before loan ie our use - so a mater of time. • 4 H head does not cool well anyway. Swagelok do offer heat plates but our mod is better. Tack welding thick wall tube puts high heat spots on only metallic part adjacent to arc and it amazingly goes all bendy and jams gearing of drive mechanism. In turn the encoder and machine then get a little confused Sheffield micro-weld head RESOLUTION – Tack welding produces very high heat load on the weld heads & power supply (Capacitor charge/discharge and MOSFET control not fantastic on the Swagelok set up). Argon gas must be delivered internally and a reasonable delay put in the weld programme between tack welds to allow for cooling.
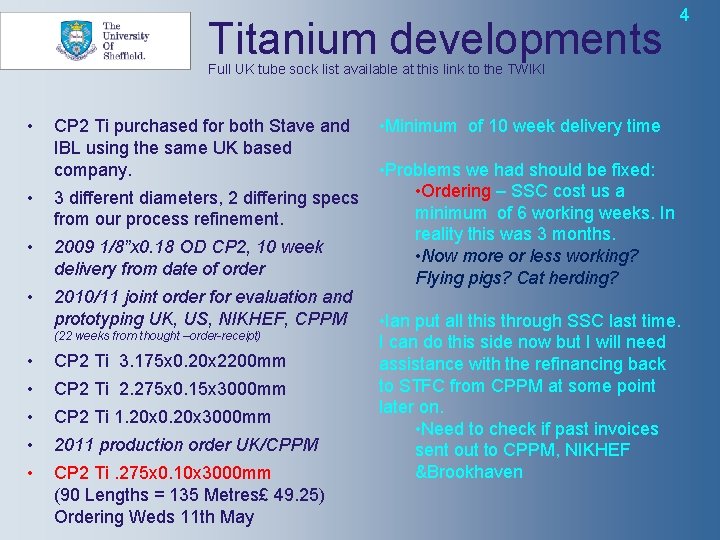
Titanium developments 4 Full UK tube sock list available at this link to the TWIKI • CP 2 Ti purchased for both Stave and IBL using the same UK based company. • 3 different diameters, 2 differing specs from our process refinement. • 2009 1/8”x 0. 18 OD CP 2, 10 week delivery from date of order • 2010/11 joint order for evaluation and prototyping UK, US, NIKHEF, CPPM (22 weeks from thought –order-receipt) • CP 2 Ti 3. 175 x 0. 20 x 2200 mm • CP 2 Ti 2. 275 x 0. 15 x 3000 mm • CP 2 Ti 1. 20 x 0. 20 x 3000 mm • 2011 production order UK/CPPM • CP 2 Ti. 275 x 0. 10 x 3000 mm (90 Lengths = 135 Metres£ 49. 25) Ordering Weds 11 th May • Minimum of 10 week delivery time • Problems we had should be fixed: • Ordering – SSC cost us a minimum of 6 working weeks. In reality this was 3 months. • Now more or less working? Flying pigs? Cat herding? • Ian put all this through SSC last time. I can do this side now but I will need assistance with the refinancing back to STFC from CPPM at some point later on. • Need to check if past invoices sent out to CPPM, NIKHEF &Brookhaven
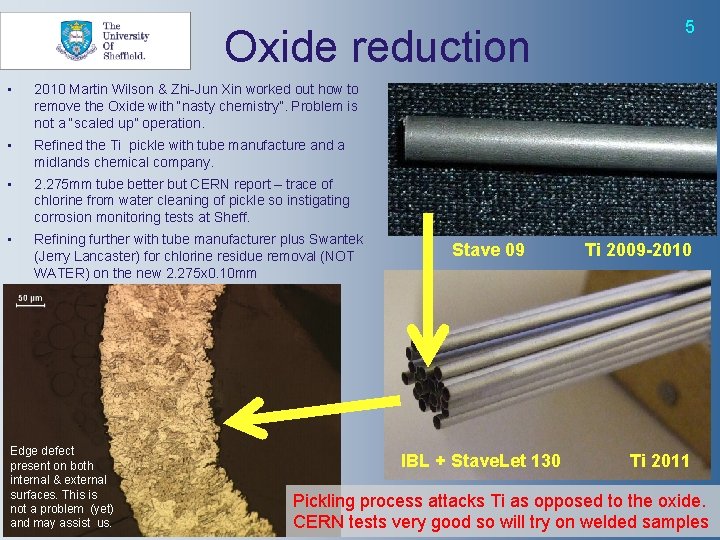
Oxide reduction • 2010 Martin Wilson & Zhi-Jun Xin worked out how to remove the Oxide with “nasty chemistry”. Problem is not a “scaled up” operation. • Refined the Ti pickle with tube manufacture and a midlands chemical company. • 2. 275 mm tube better but CERN report – trace of chlorine from water cleaning of pickle so instigating corrosion monitoring tests at Sheff. • Refining further with tube manufacturer plus Swantek (Jerry Lancaster) for chlorine residue removal (NOT WATER) on the new 2. 275 x 0. 10 mm Edge defect present on both internal & external surfaces. This is not a problem (yet) and may assist us. Stave 09 IBL + Stave. Let 130 5 Ti 2009 -2010 Ti 2011 Pickling process attacks Ti as opposed to the oxide. CERN tests very good so will try on welded samples
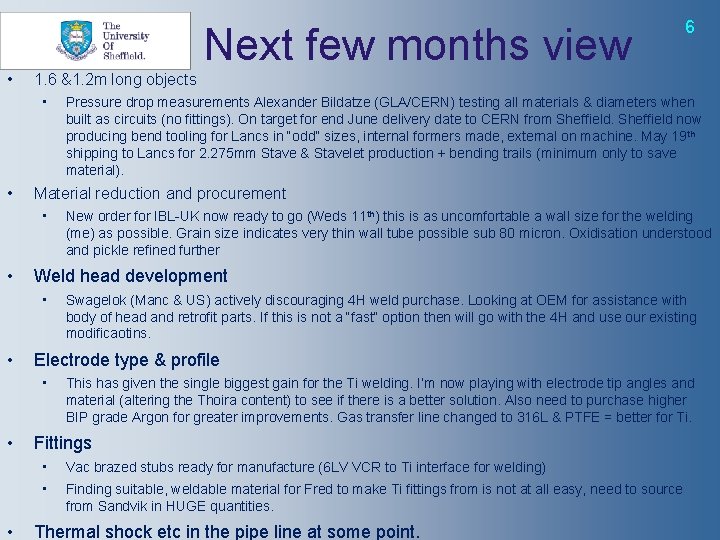
Next few months view • 1. 6 &1. 2 m long objects • • • Swagelok (Manc & US) actively discouraging 4 H weld purchase. Looking at OEM for assistance with body of head and retrofit parts. If this is not a “fast” option then will go with the 4 H and use our existing modificaotins. Electrode type & profile • • New order for IBL-UK now ready to go (Weds 11 th) this is as uncomfortable a wall size for the welding (me) as possible. Grain size indicates very thin wall tube possible sub 80 micron. Oxidisation understood and pickle refined further Weld head development • • Pressure drop measurements Alexander Bildatze (GLA/CERN) testing all materials & diameters when built as circuits (no fittings). On target for end June delivery date to CERN from Sheffield now producing bend tooling for Lancs in “odd” sizes, internal formers made, external on machine. May 19 th shipping to Lancs for 2. 275 mm Stave & Stavelet production + bending trails (minimum only to save material). Material reduction and procurement • • 6 This has given the single biggest gain for the Ti welding. I’m now playing with electrode tip angles and material (altering the Thoira content) to see if there is a better solution. Also need to purchase higher BIP grade Argon for greater improvements. Gas transfer line changed to 316 L & PTFE = better for Ti. Fittings • Vac brazed stubs ready for manufacture (6 LV VCR to Ti interface for welding) • Finding suitable, weldable material for Fred to make Ti fittings from is not at all easy, need to source from Sandvik in HUGE quantities. Thermal shock etc in the pipe line at some point.