TwoStage Cost Systems Agenda Traditional cost systems Twostage
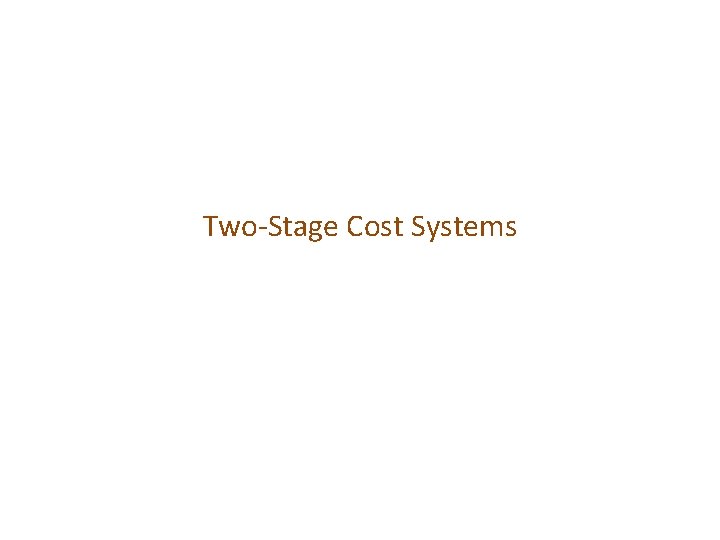
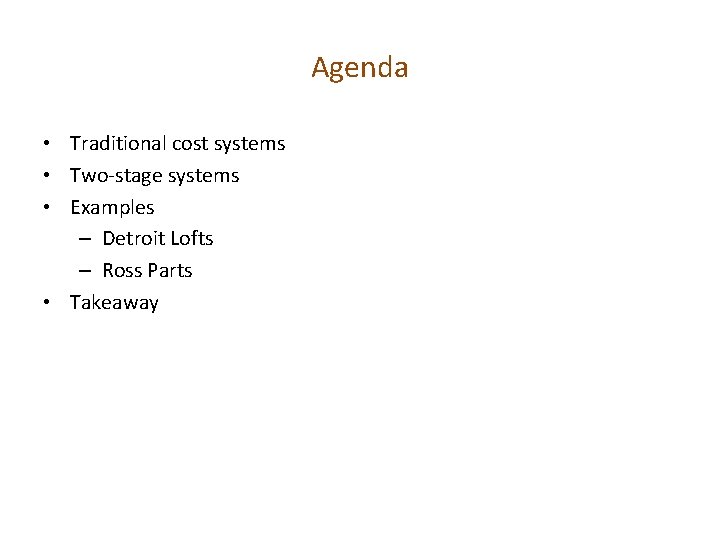
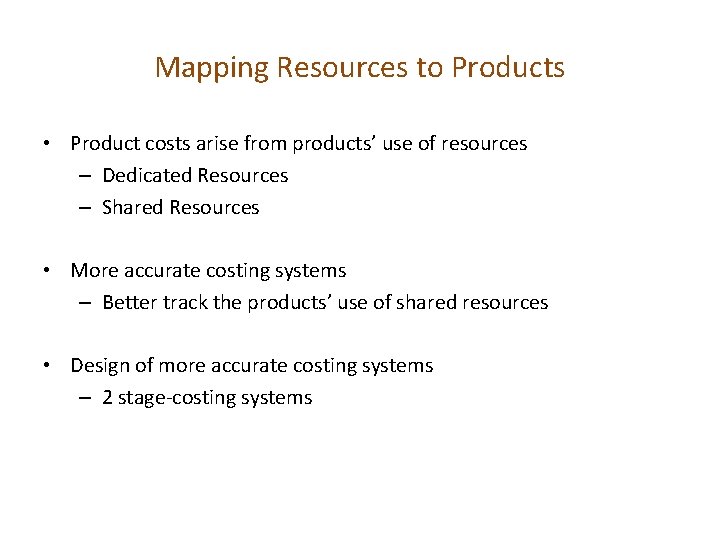
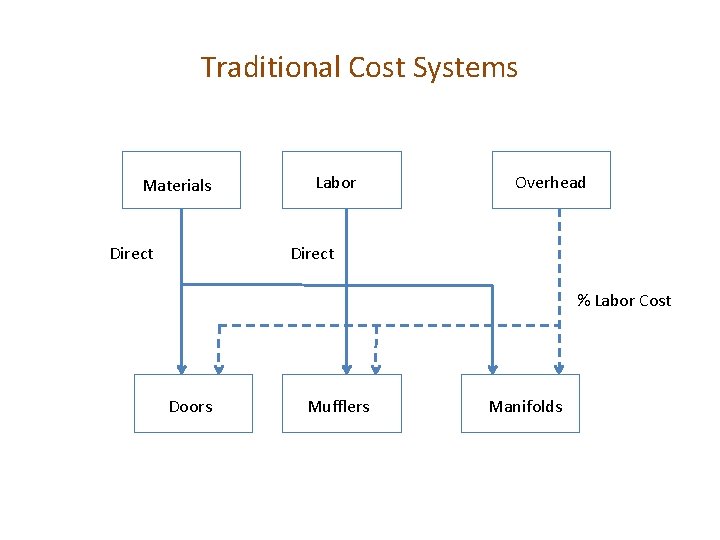
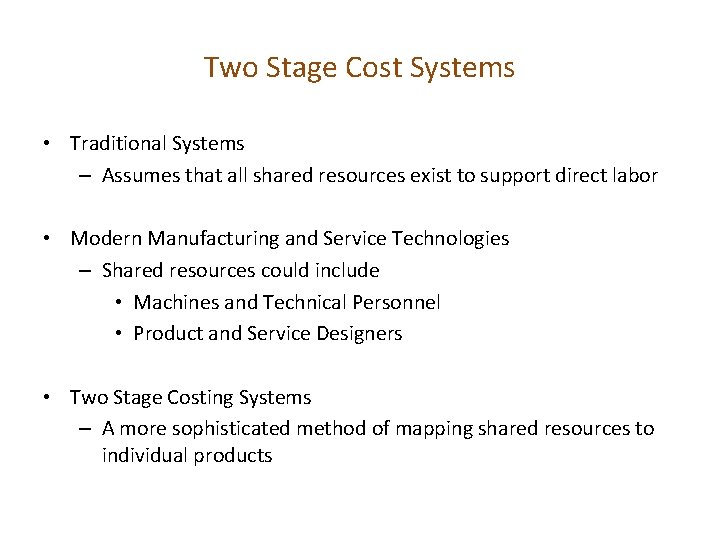
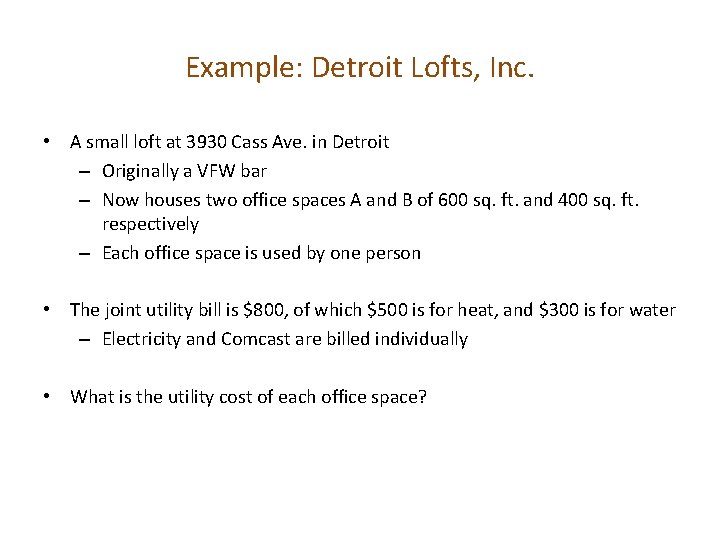
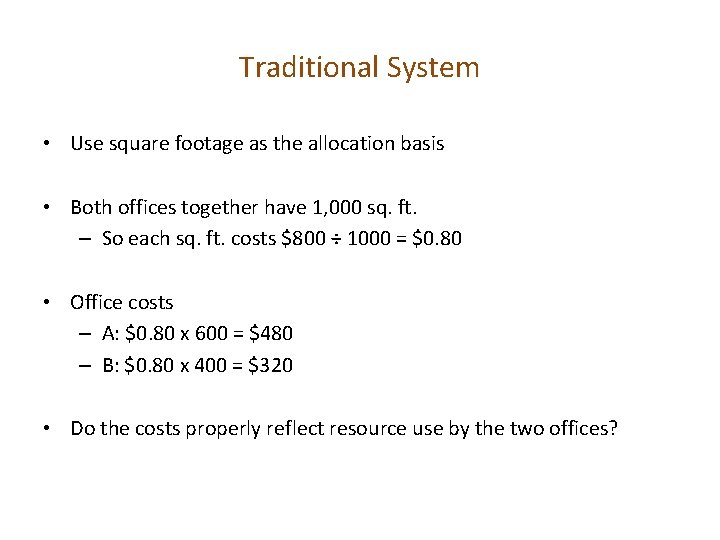

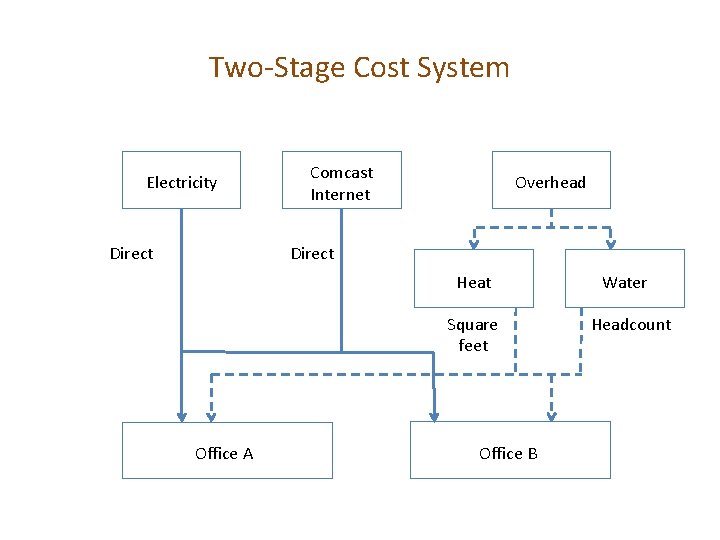
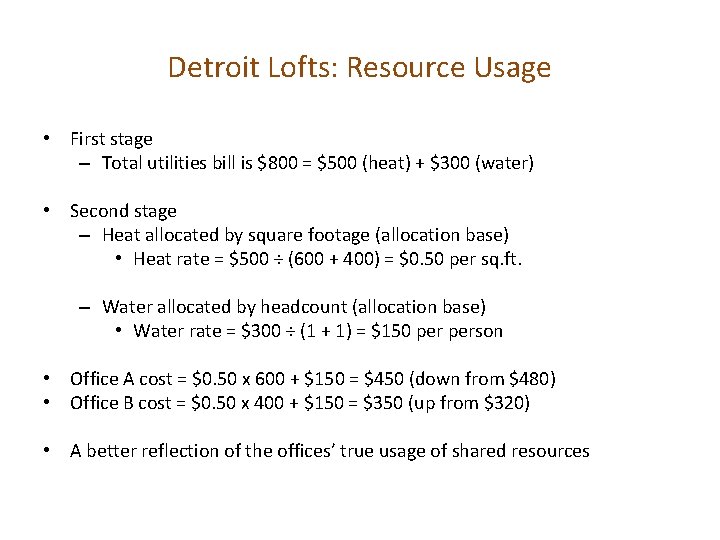
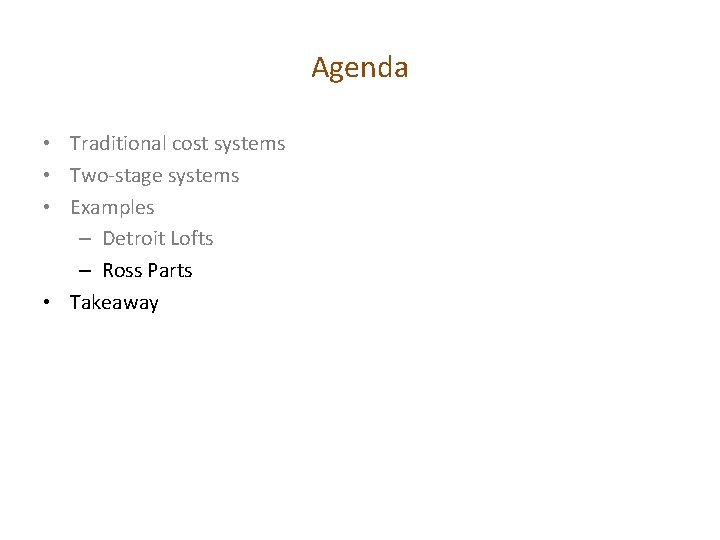
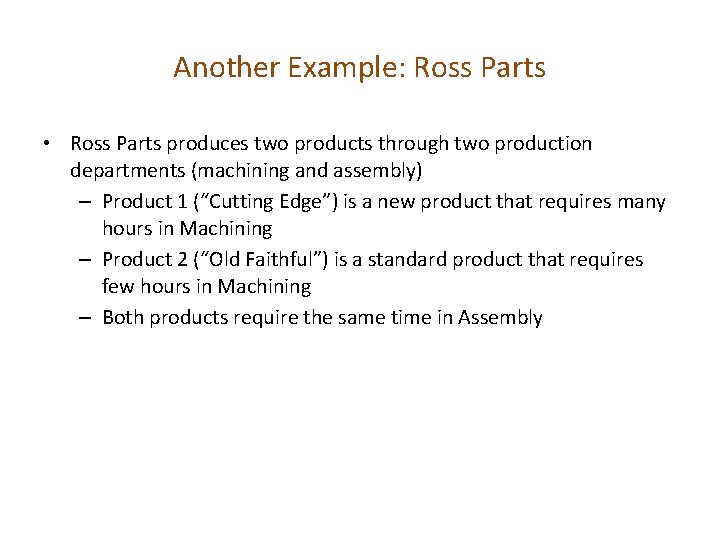
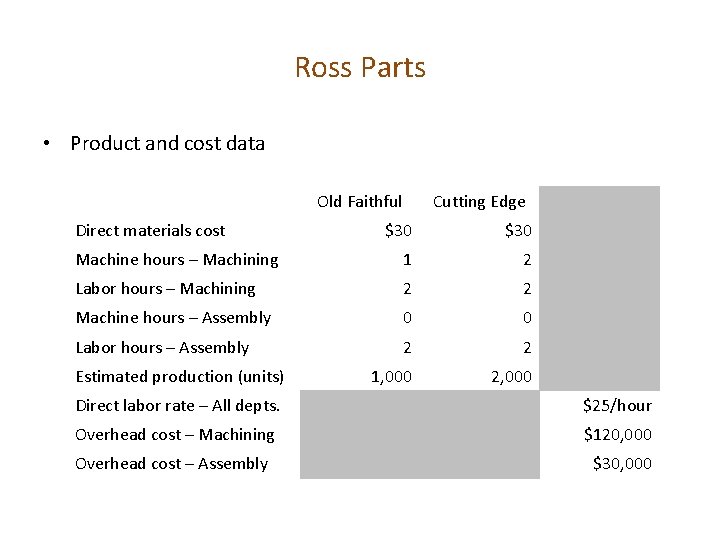
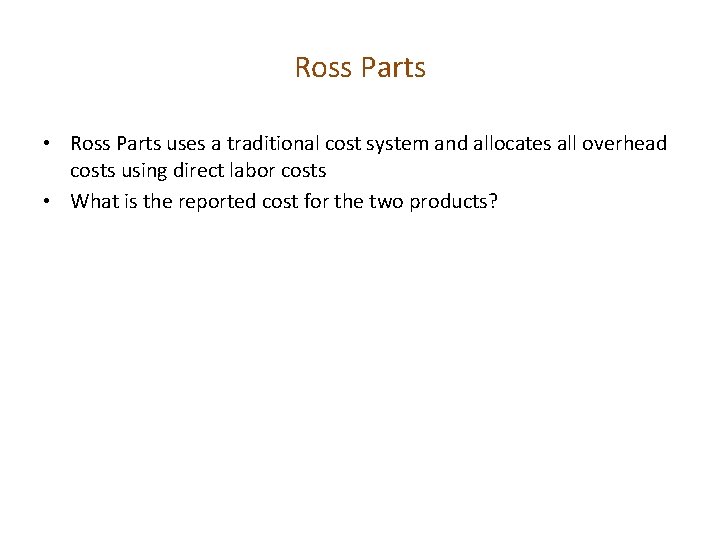
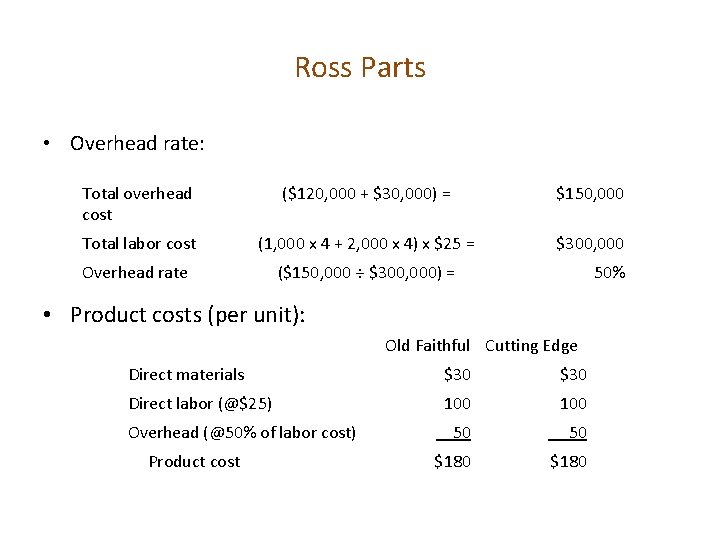
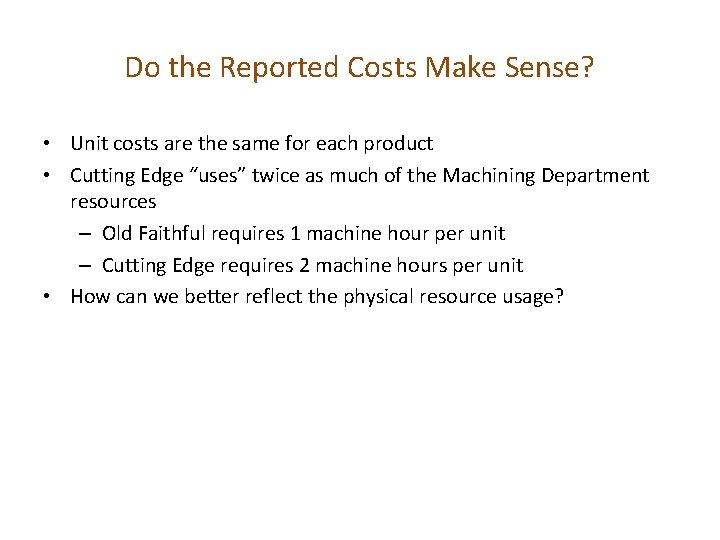
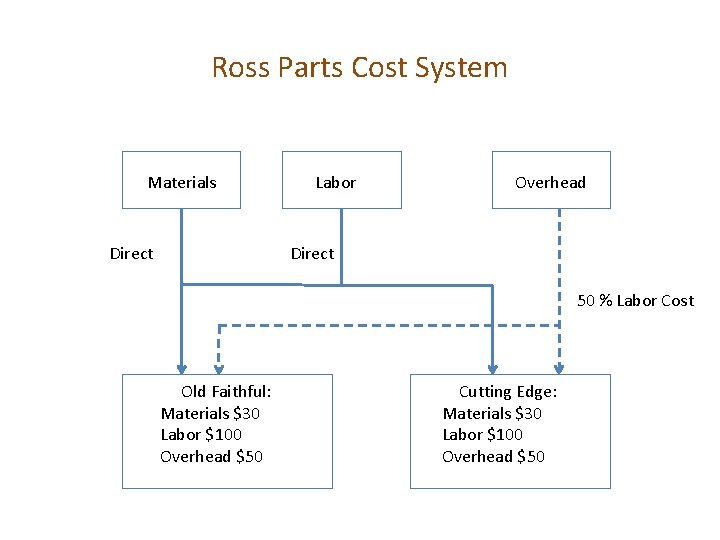
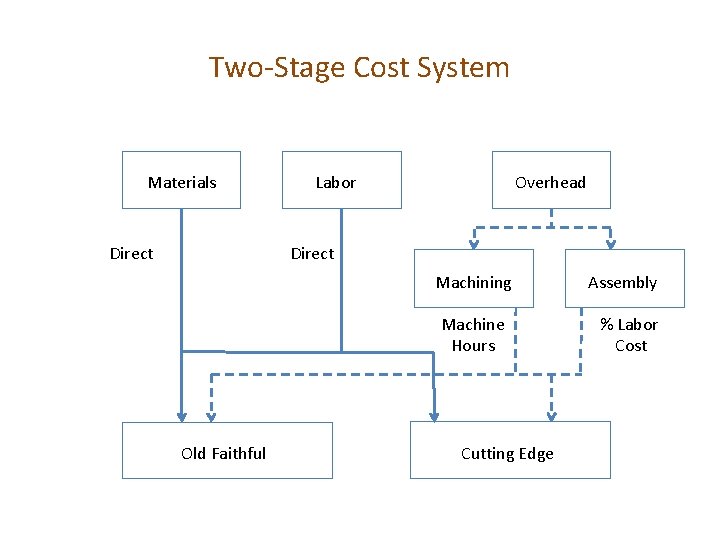
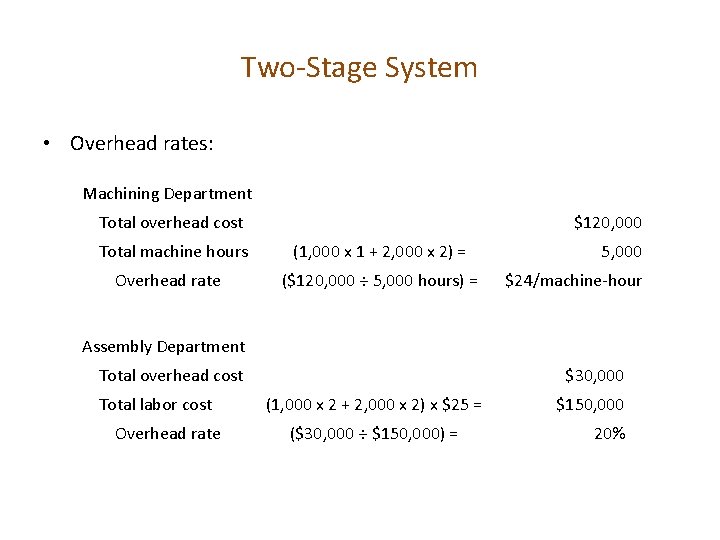
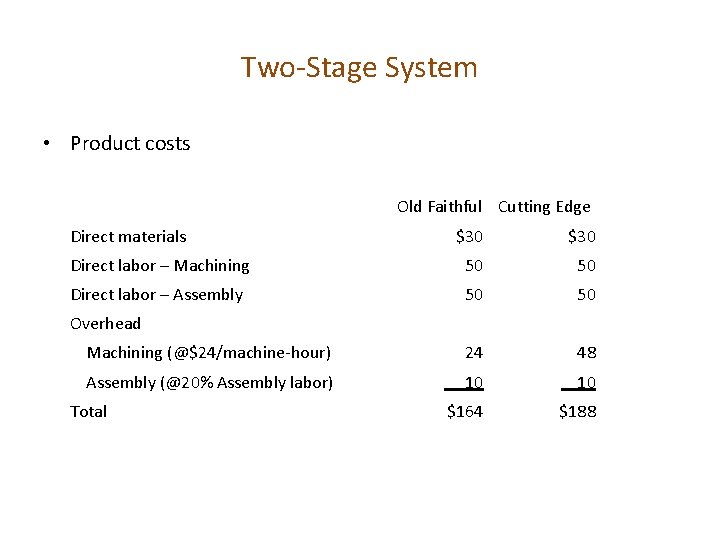
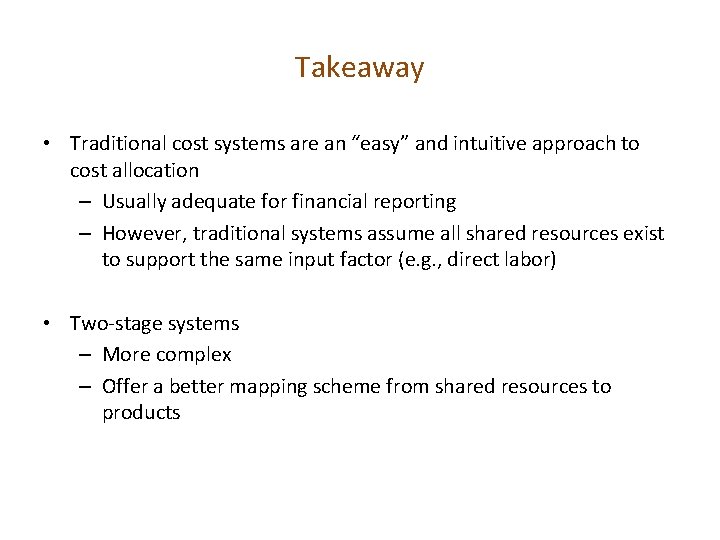
- Slides: 21
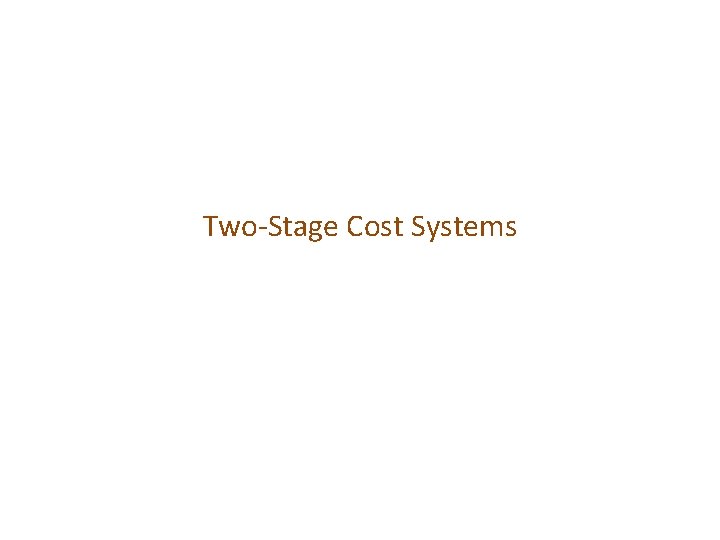
Two-Stage Cost Systems
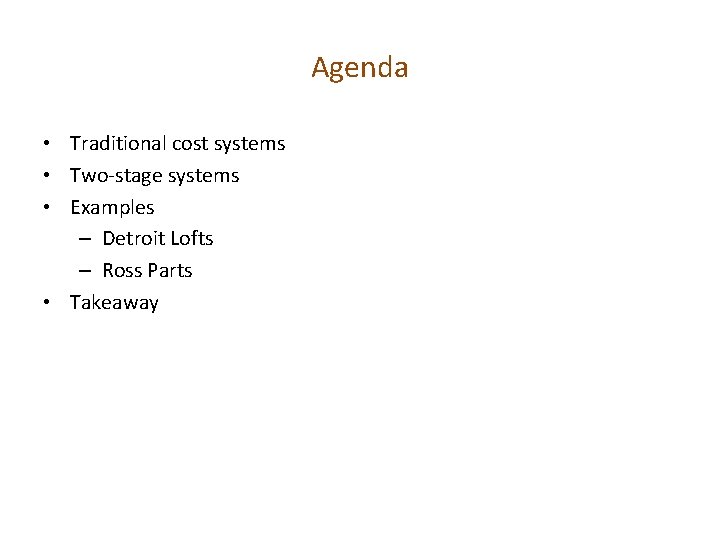
Agenda • Traditional cost systems • Two-stage systems • Examples – Detroit Lofts – Ross Parts • Takeaway
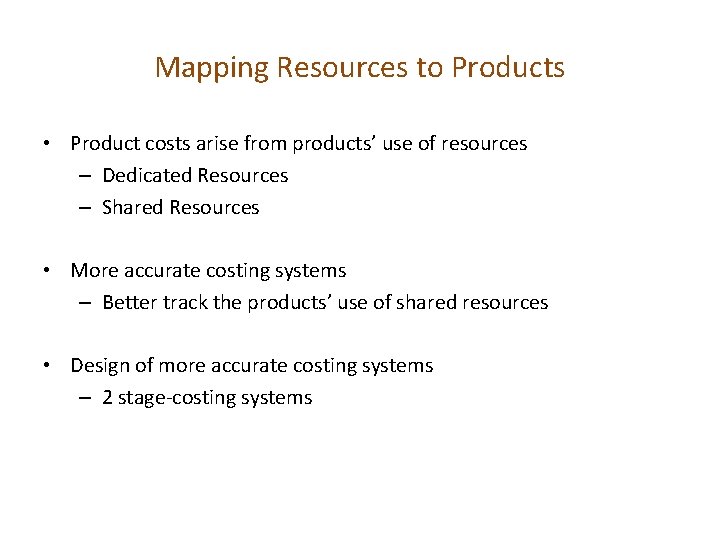
Mapping Resources to Products • Product costs arise from products’ use of resources – Dedicated Resources – Shared Resources • More accurate costing systems – Better track the products’ use of shared resources • Design of more accurate costing systems – 2 stage-costing systems
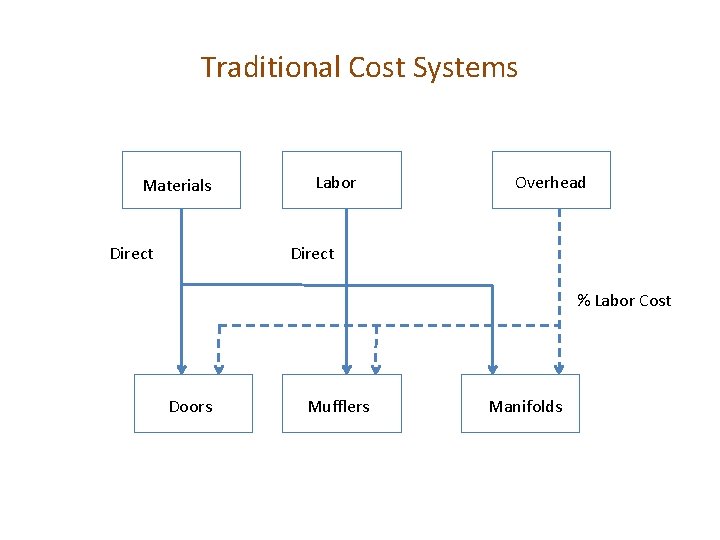
Traditional Cost Systems Materials Direct Labor Overhead Direct % Labor Cost Doors Mufflers Manifolds
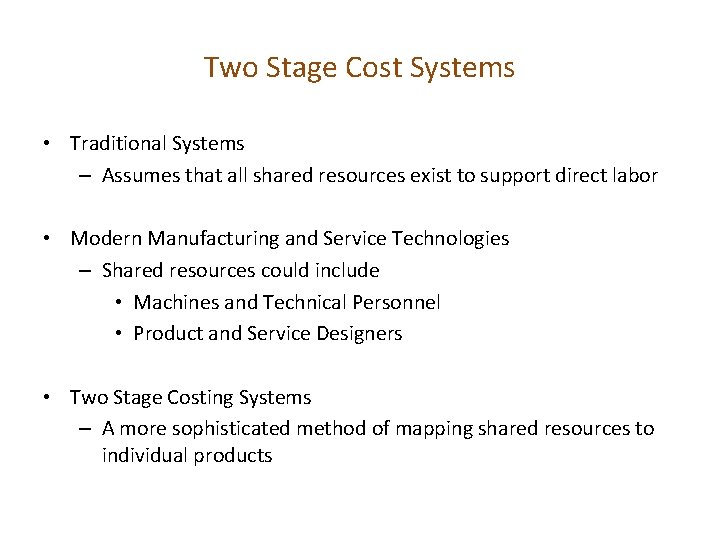
Two Stage Cost Systems • Traditional Systems – Assumes that all shared resources exist to support direct labor • Modern Manufacturing and Service Technologies – Shared resources could include • Machines and Technical Personnel • Product and Service Designers • Two Stage Costing Systems – A more sophisticated method of mapping shared resources to individual products
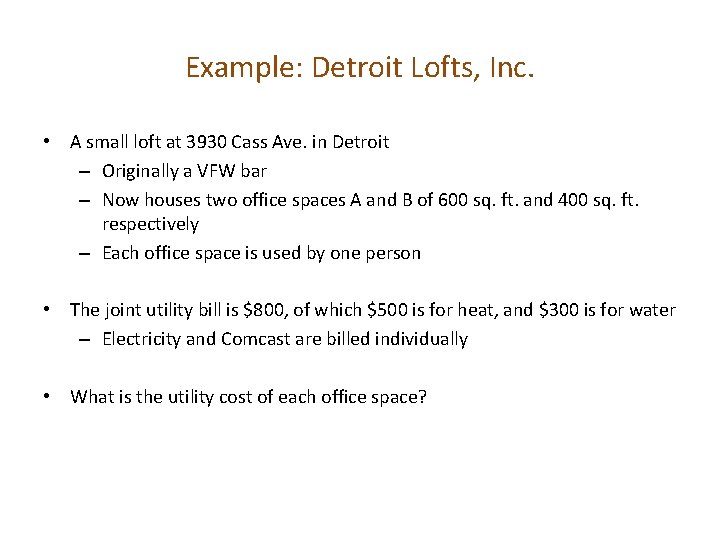
Example: Detroit Lofts, Inc. • A small loft at 3930 Cass Ave. in Detroit – Originally a VFW bar – Now houses two office spaces A and B of 600 sq. ft. and 400 sq. ft. respectively – Each office space is used by one person • The joint utility bill is $800, of which $500 is for heat, and $300 is for water – Electricity and Comcast are billed individually • What is the utility cost of each office space?
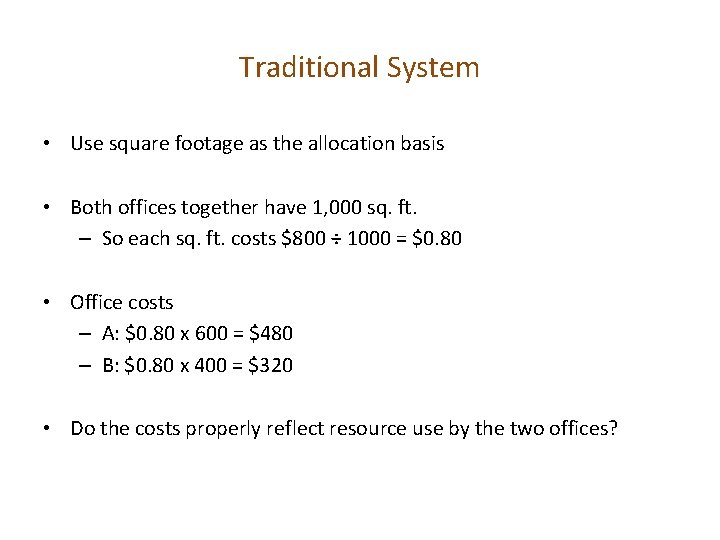
Traditional System • Use square footage as the allocation basis • Both offices together have 1, 000 sq. ft. – So each sq. ft. costs $800 ÷ 1000 = $0. 80 • Office costs – A: $0. 80 x 600 = $480 – B: $0. 80 x 400 = $320 • Do the costs properly reflect resource use by the two offices?

Two-Stage Costing System • One approach is to adopt a “two-stage” cost system – First stage • Split overhead into the two departments (heat and water) – Second stage • Calculate separate overhead rates using different allocation bases (cost drivers) Note: use allocation base levels that combine all offices’ usage • Calculate individual office costs using the new rates
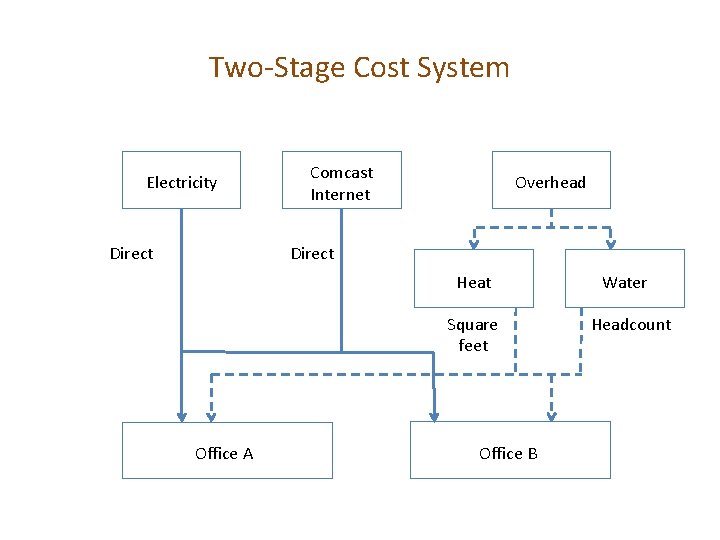
Two-Stage Cost System Electricity Direct Comcast Internet Overhead Direct Heat Square feet Office A Office B Water Headcount
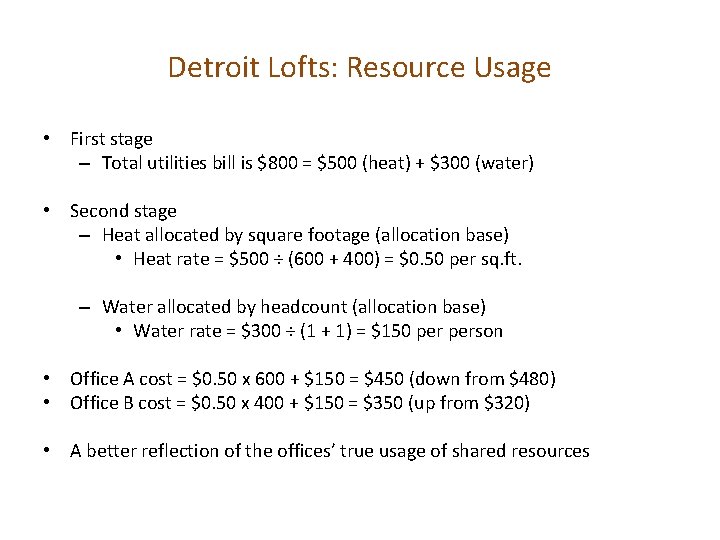
Detroit Lofts: Resource Usage • First stage – Total utilities bill is $800 = $500 (heat) + $300 (water) • Second stage – Heat allocated by square footage (allocation base) • Heat rate = $500 ÷ (600 + 400) = $0. 50 per sq. ft. – Water allocated by headcount (allocation base) • Water rate = $300 ÷ (1 + 1) = $150 person • Office A cost = $0. 50 x 600 + $150 = $450 (down from $480) • Office B cost = $0. 50 x 400 + $150 = $350 (up from $320) • A better reflection of the offices’ true usage of shared resources
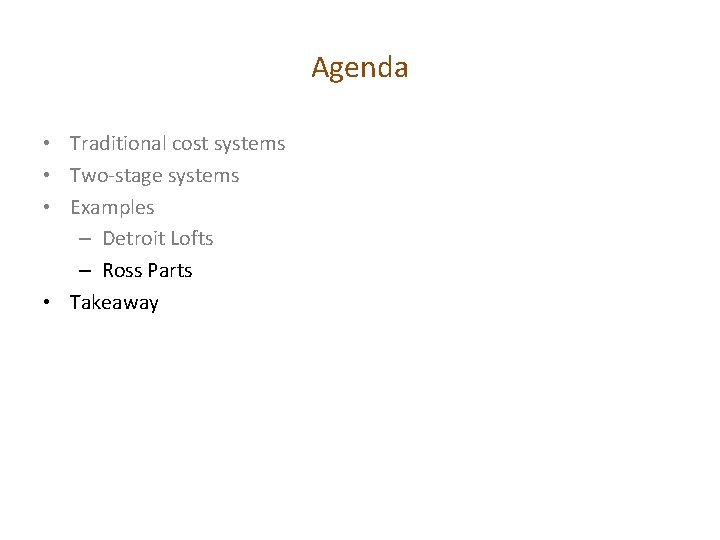
Agenda • Traditional cost systems • Two-stage systems • Examples – Detroit Lofts – Ross Parts • Takeaway
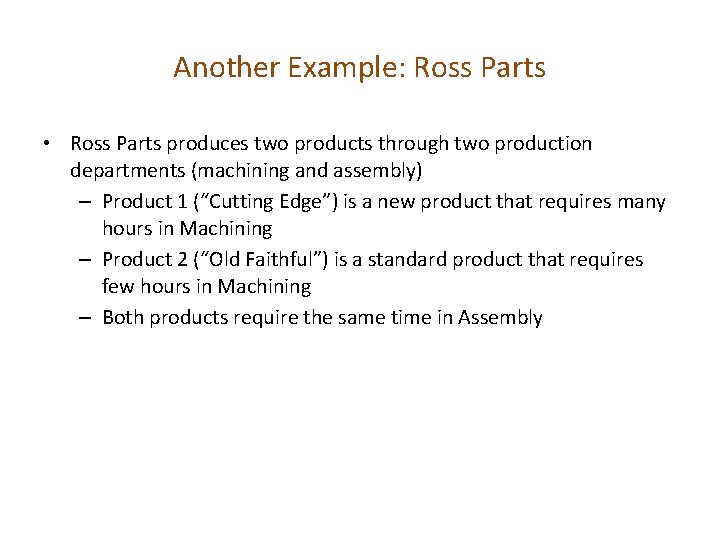
Another Example: Ross Parts • Ross Parts produces two products through two production departments (machining and assembly) – Product 1 (“Cutting Edge”) is a new product that requires many hours in Machining – Product 2 (“Old Faithful”) is a standard product that requires few hours in Machining – Both products require the same time in Assembly
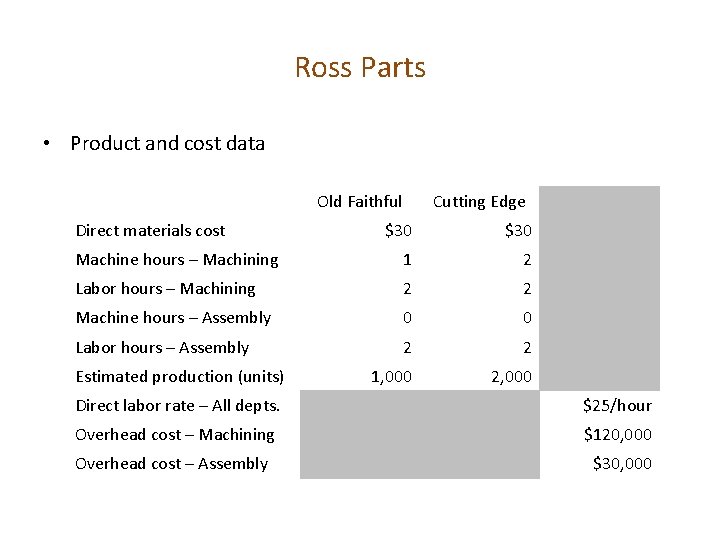
Ross Parts • Product and cost data Old Faithful Direct materials cost Cutting Edge $30 Machine hours – Machining 1 2 Labor hours – Machining 2 2 Machine hours – Assembly 0 0 Labor hours – Assembly 2 2 1, 000 2, 000 Estimated production (units) Direct labor rate – All depts. $25/hour Overhead cost – Machining $120, 000 Overhead cost – Assembly $30, 000
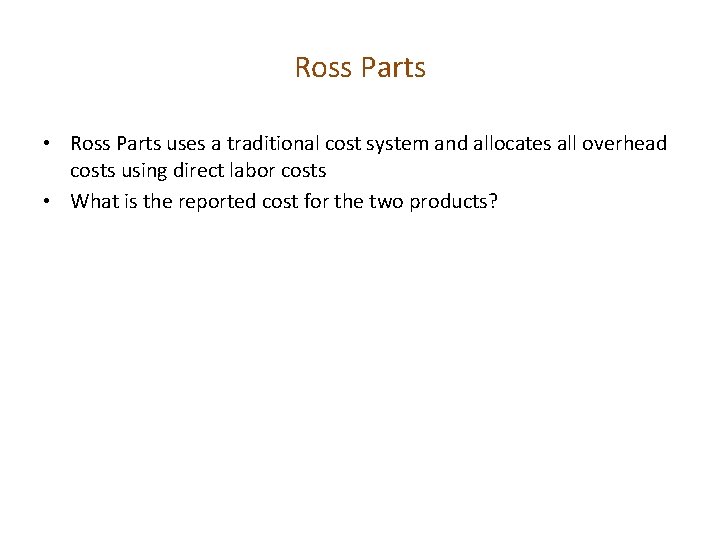
Ross Parts • Ross Parts uses a traditional cost system and allocates all overhead costs using direct labor costs • What is the reported cost for the two products?
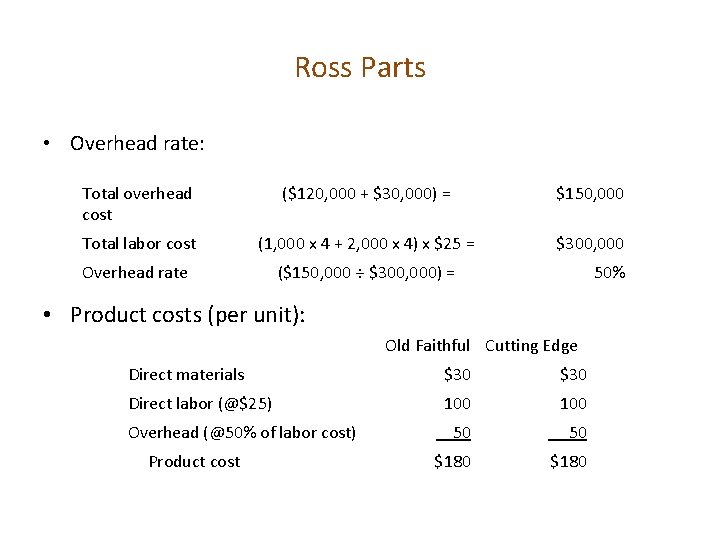
Ross Parts • Overhead rate: Total overhead cost ($120, 000 + $30, 000) = $150, 000 Total labor cost (1, 000 x 4 + 2, 000 x 4) x $25 = $300, 000 Overhead rate ($150, 000 ÷ $300, 000) = 50% • Product costs (per unit): Old Faithful Cutting Edge Direct materials $30 Direct labor (@$25) 100 50 50 $180 Overhead (@50% of labor cost) Product cost
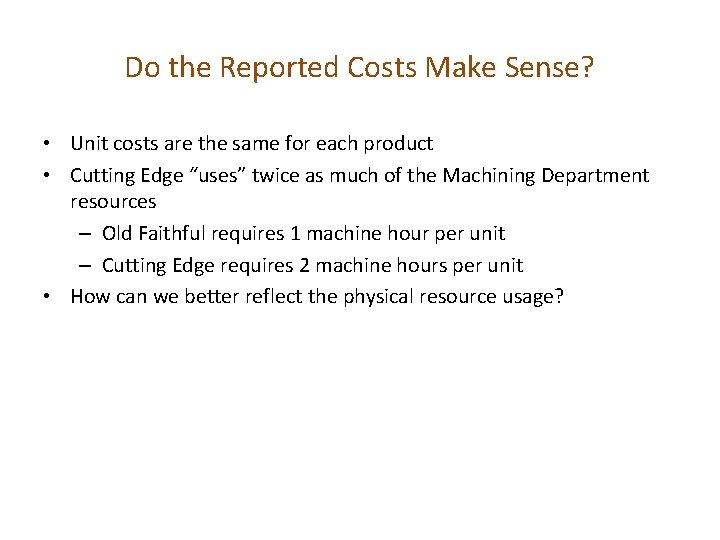
Do the Reported Costs Make Sense? • Unit costs are the same for each product • Cutting Edge “uses” twice as much of the Machining Department resources – Old Faithful requires 1 machine hour per unit – Cutting Edge requires 2 machine hours per unit • How can we better reflect the physical resource usage?
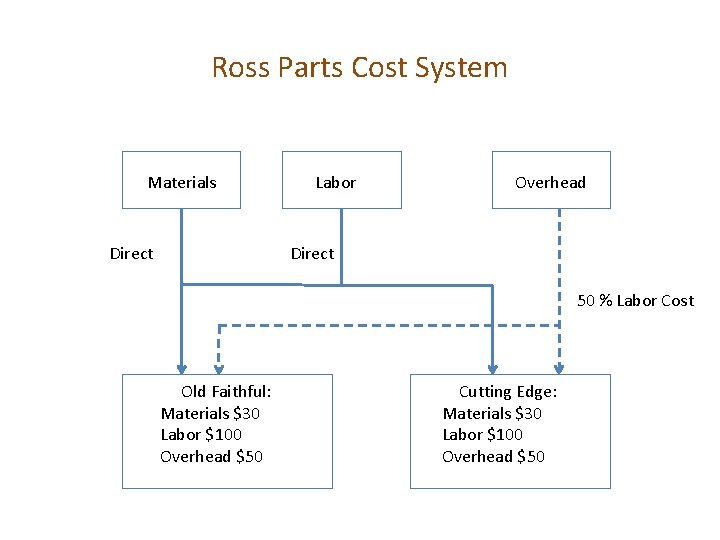
Ross Parts Cost System Materials Direct Labor Overhead Direct 50 % Labor Cost Old Faithful: Materials $30 Labor $100 Overhead $50 Cutting Edge: Materials $30 Labor $100 Overhead $50
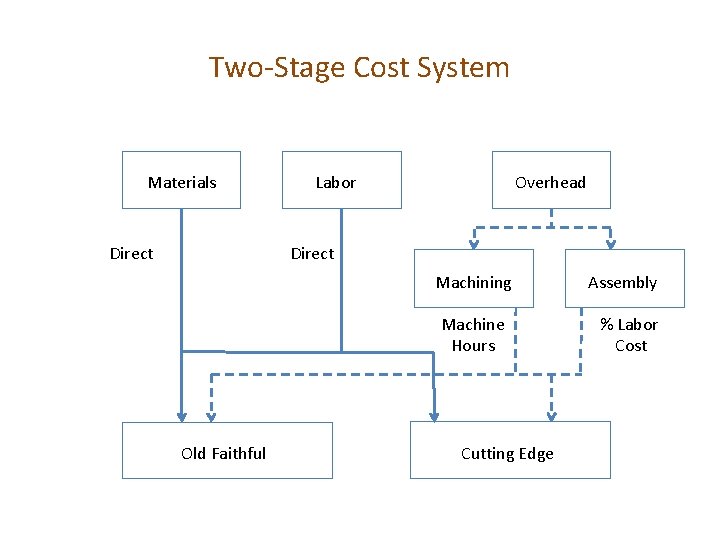
Two-Stage Cost System Materials Direct Overhead Labor Direct Machining Machine Hours Old Faithful Cutting Edge Assembly % Labor Cost
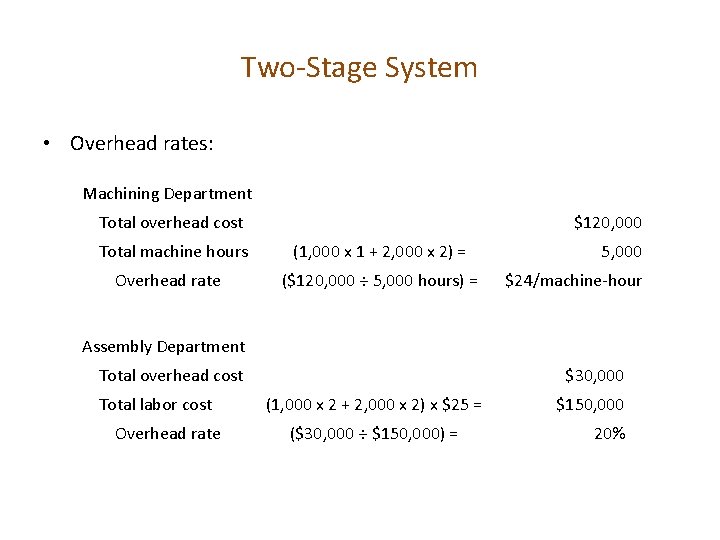
Two-Stage System • Overhead rates: Machining Department Total overhead cost Total machine hours Overhead rate $120, 000 (1, 000 x 1 + 2, 000 x 2) = ($120, 000 ÷ 5, 000 hours) = 5, 000 $24/machine-hour Assembly Department Total overhead cost Total labor cost Overhead rate $30, 000 (1, 000 x 2 + 2, 000 x 2) x $25 = ($30, 000 ÷ $150, 000) = $150, 000 20%
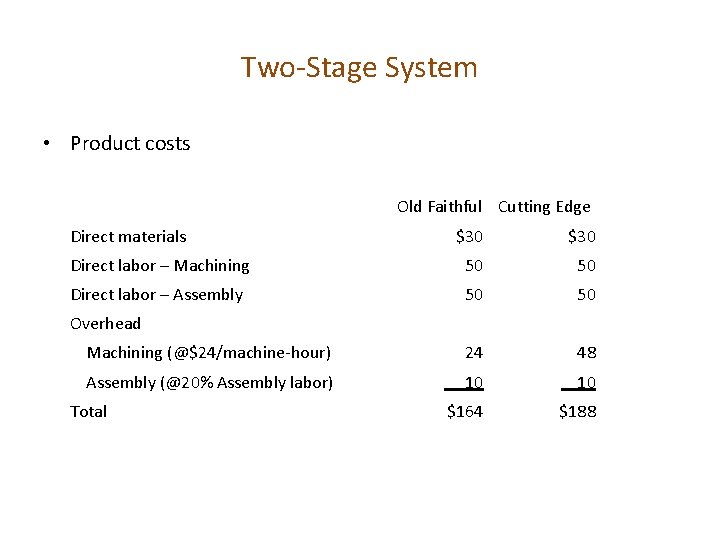
Two-Stage System • Product costs Old Faithful Cutting Edge Direct materials $30 Direct labor – Machining 50 50 Direct labor – Assembly 50 50 Machining (@$24/machine-hour) 24 48 Assembly (@20% Assembly labor) 10 10 $164 $188 Overhead Total
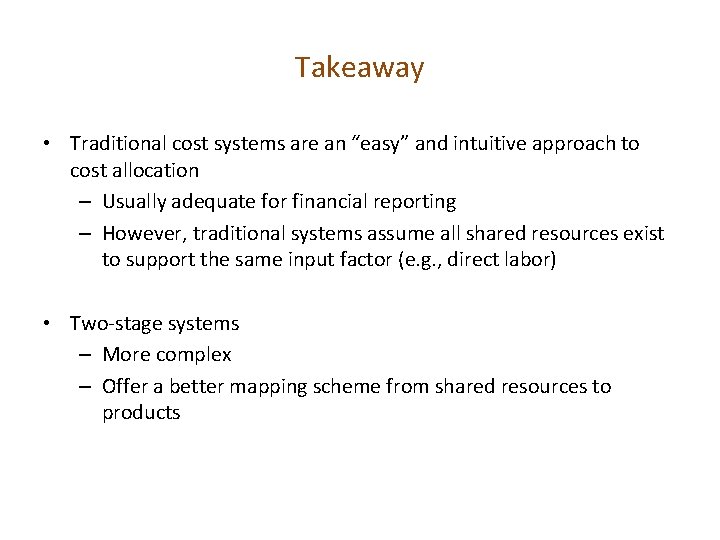
Takeaway • Traditional cost systems are an “easy” and intuitive approach to cost allocation – Usually adequate for financial reporting – However, traditional systems assume all shared resources exist to support the same input factor (e. g. , direct labor) • Two-stage systems – More complex – Offer a better mapping scheme from shared resources to products
Agenda sistemica y agenda institucional
Job wr53 at nw fab
Linear cost function
Traditional net cost method
Agenda management systems
Agenda open systems
Traditional systems development
Traditional approach to systems implementation
Traditional systems development life cycle
Cost accumulation and cost assignment
Cost accumulation and cost assignment
Manufacturing cost vs non manufacturing cost
Job costing vs process costing
Flotation cost in cost of equity
Controllable costs
Cost pools
Manufacturing cost vs non manufacturing cost
Manufacturing variance analysis
Book value of debt
What is a period cost on the income statement
Cost control and cost reduction difference
Meaning of standard costing in cost accounting