Standard Cost Variance Analysis MANUFACTURING FIRMS USE STANDARD
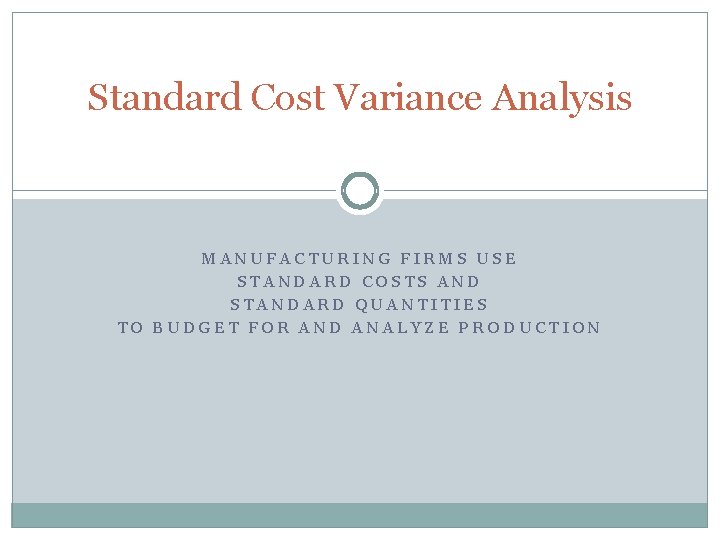
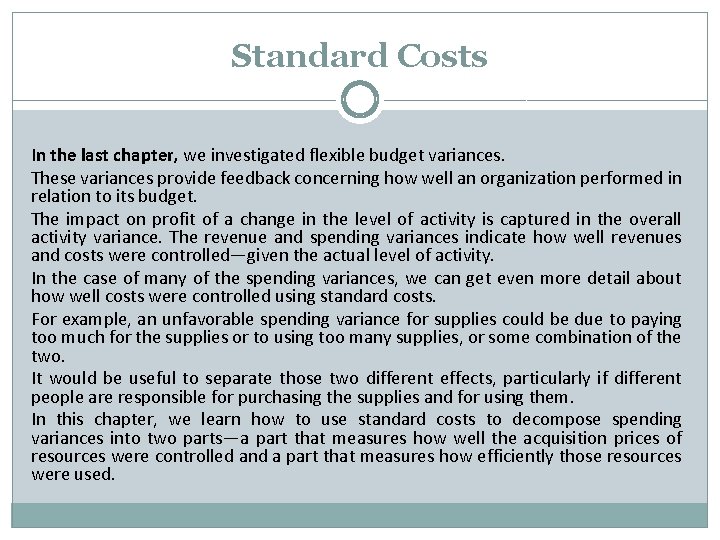
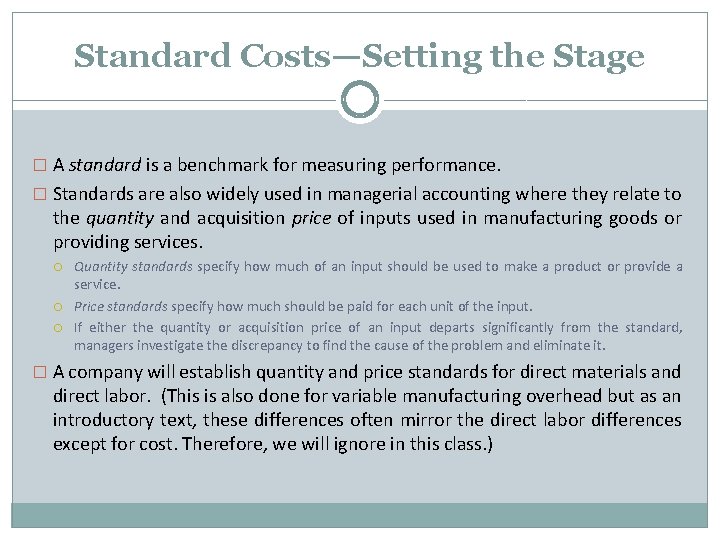
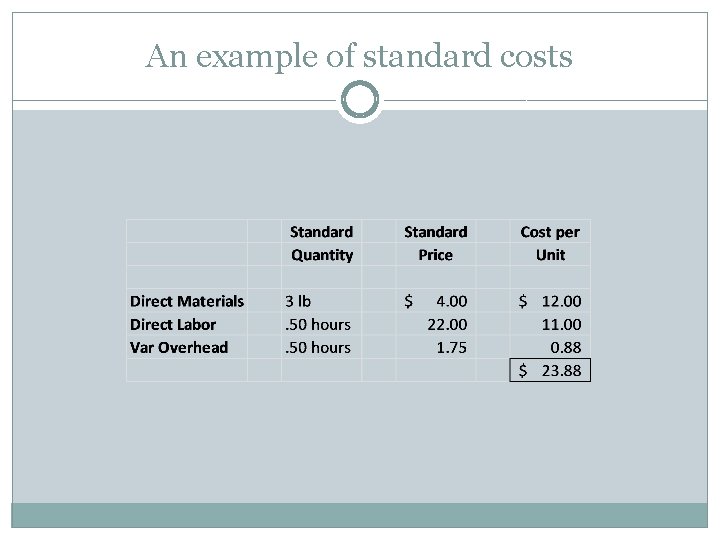
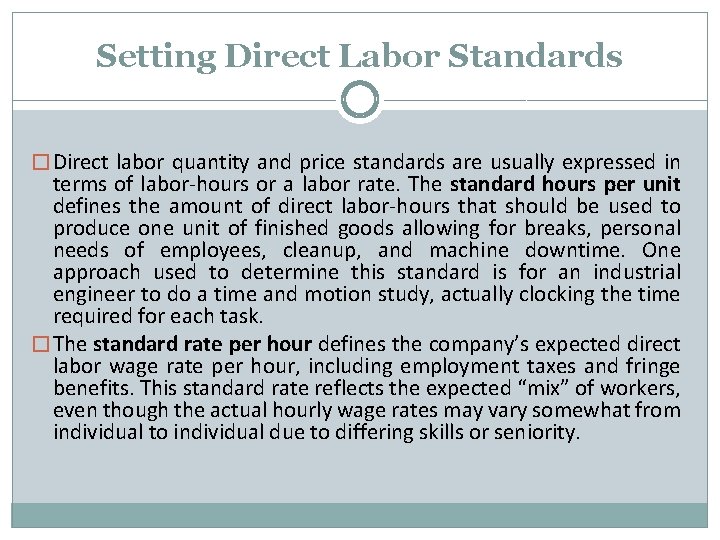
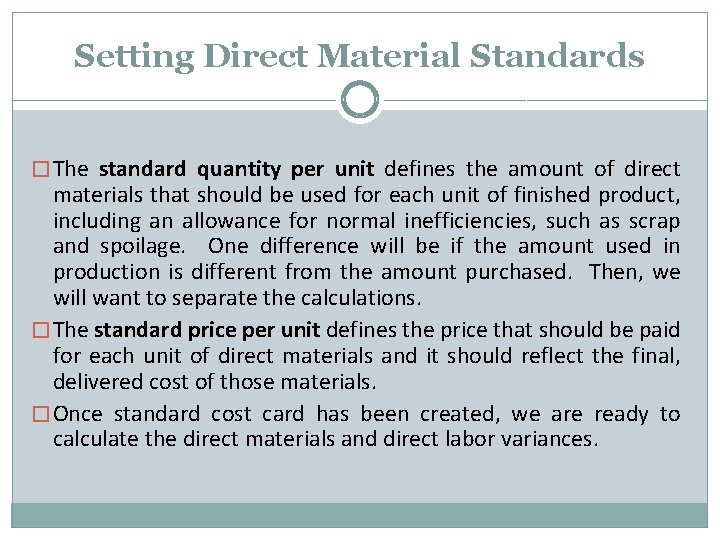
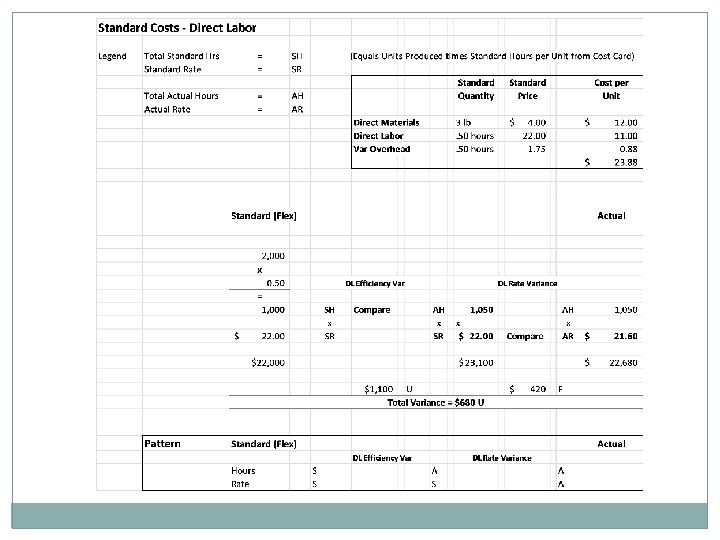
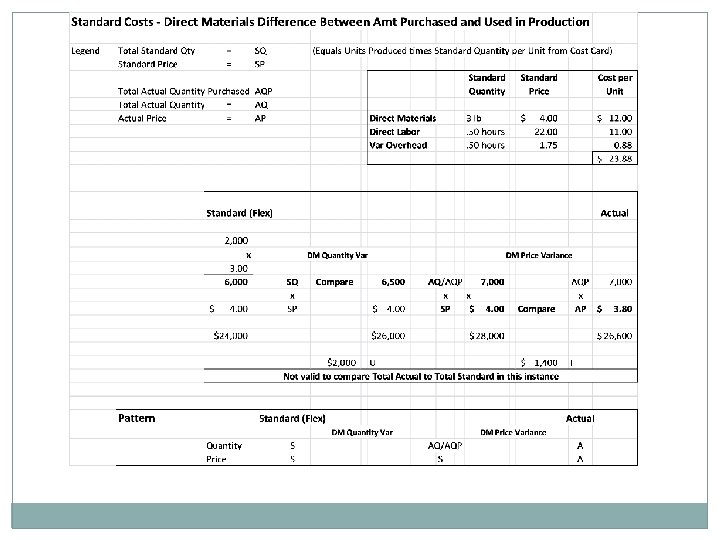
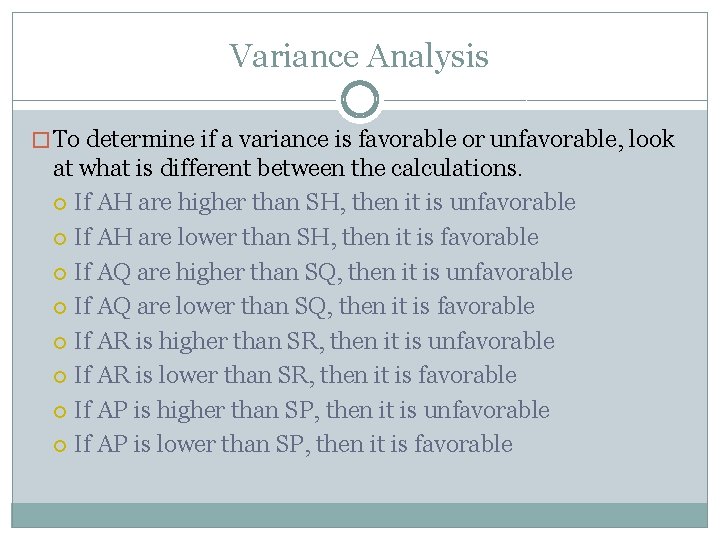
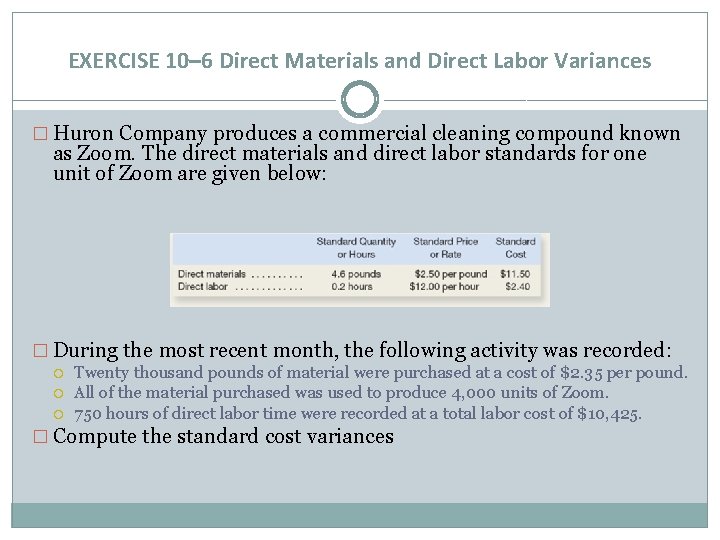
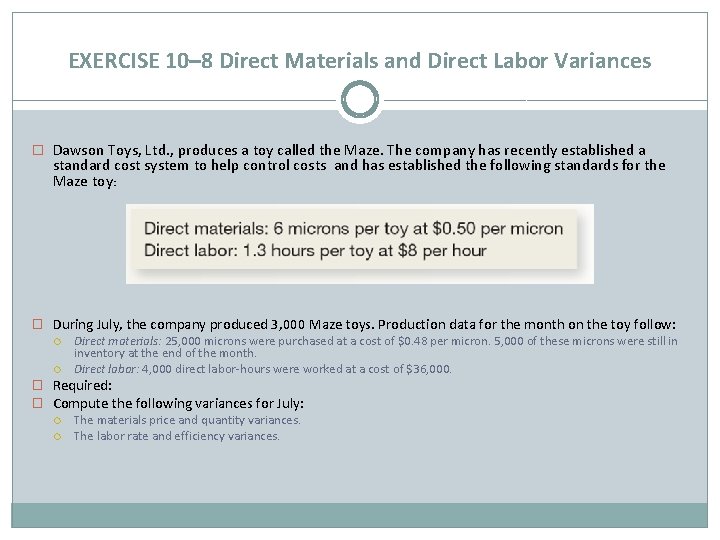
- Slides: 11
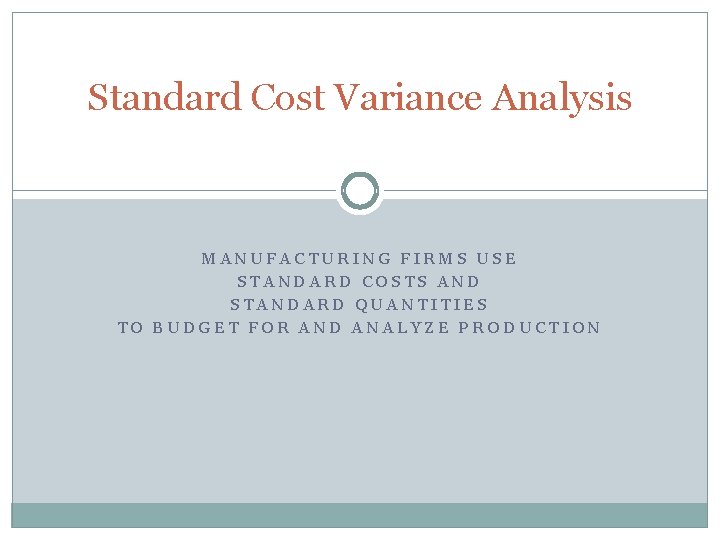
Standard Cost Variance Analysis MANUFACTURING FIRMS USE STANDARD COSTS AND STANDARD QUANTITIES TO BUDGET FOR AND ANALYZE PRODUCTION
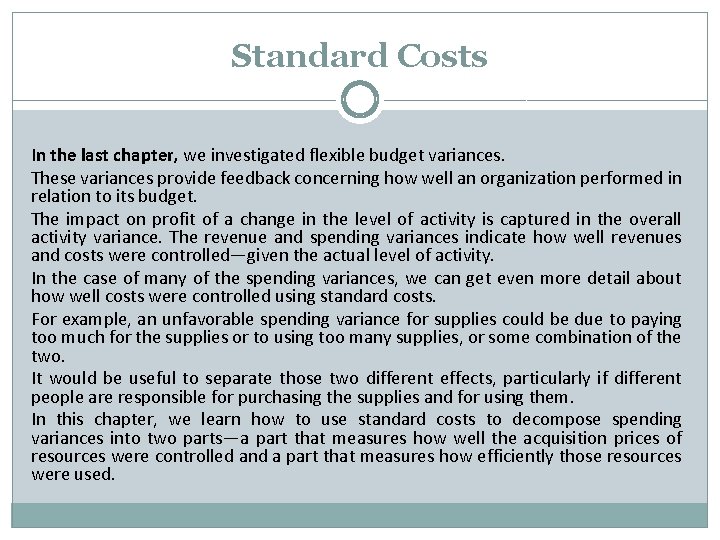
Standard Costs In the last chapter, we investigated flexible budget variances. These variances provide feedback concerning how well an organization performed in relation to its budget. The impact on profit of a change in the level of activity is captured in the overall activity variance. The revenue and spending variances indicate how well revenues and costs were controlled—given the actual level of activity. In the case of many of the spending variances, we can get even more detail about how well costs were controlled using standard costs. For example, an unfavorable spending variance for supplies could be due to paying too much for the supplies or to using too many supplies, or some combination of the two. It would be useful to separate those two different effects, particularly if different people are responsible for purchasing the supplies and for using them. In this chapter, we learn how to use standard costs to decompose spending variances into two parts—a part that measures how well the acquisition prices of resources were controlled and a part that measures how efficiently those resources were used.
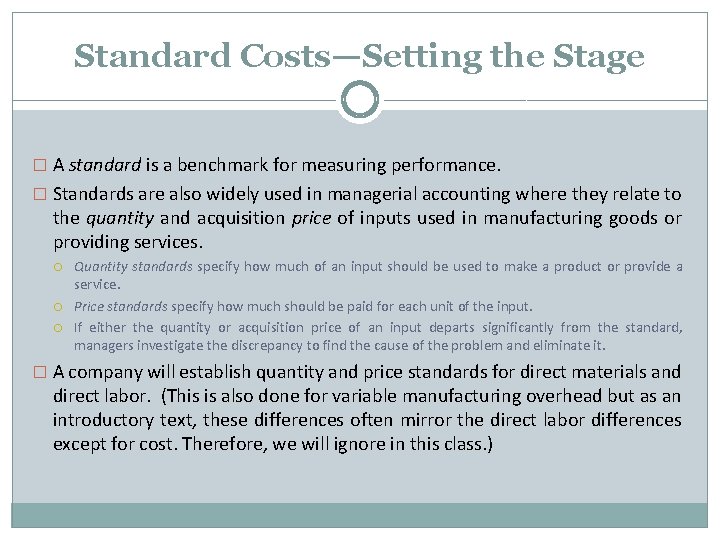
Standard Costs—Setting the Stage � A standard is a benchmark for measuring performance. � Standards are also widely used in managerial accounting where they relate to the quantity and acquisition price of inputs used in manufacturing goods or providing services. Quantity standards specify how much of an input should be used to make a product or provide a service. Price standards specify how much should be paid for each unit of the input. If either the quantity or acquisition price of an input departs significantly from the standard, managers investigate the discrepancy to find the cause of the problem and eliminate it. � A company will establish quantity and price standards for direct materials and direct labor. (This is also done for variable manufacturing overhead but as an introductory text, these differences often mirror the direct labor differences except for cost. Therefore, we will ignore in this class. )
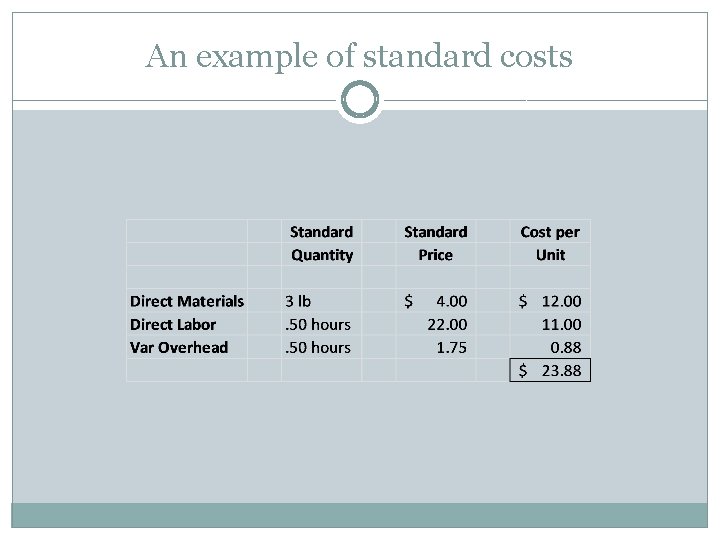
An example of standard costs
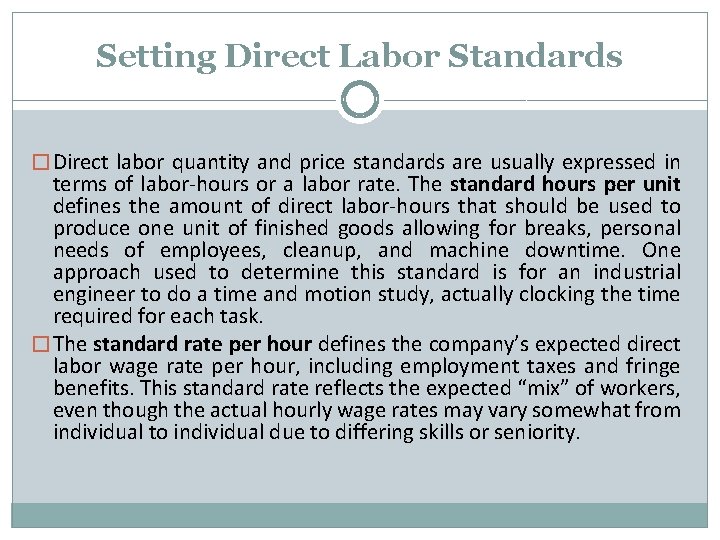
Setting Direct Labor Standards � Direct labor quantity and price standards are usually expressed in terms of labor-hours or a labor rate. The standard hours per unit defines the amount of direct labor-hours that should be used to produce one unit of finished goods allowing for breaks, personal needs of employees, cleanup, and machine downtime. One approach used to determine this standard is for an industrial engineer to do a time and motion study, actually clocking the time required for each task. � The standard rate per hour defines the company’s expected direct labor wage rate per hour, including employment taxes and fringe benefits. This standard rate reflects the expected “mix” of workers, even though the actual hourly wage rates may vary somewhat from individual to individual due to differing skills or seniority.
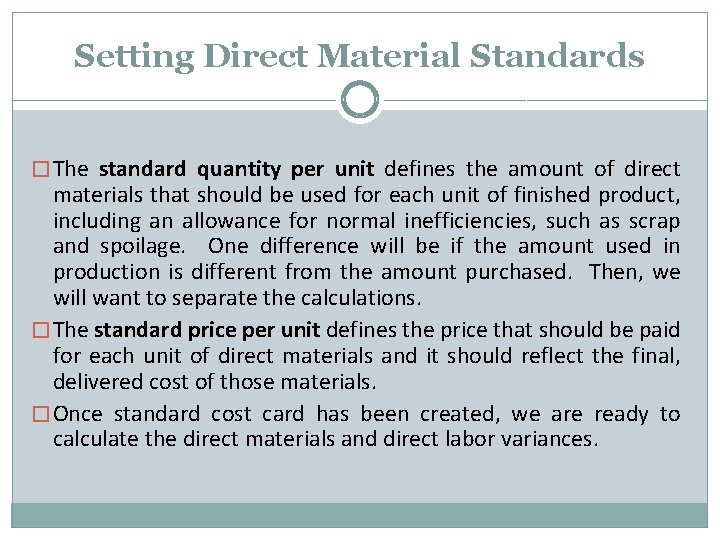
Setting Direct Material Standards � The standard quantity per unit defines the amount of direct materials that should be used for each unit of finished product, including an allowance for normal inefficiencies, such as scrap and spoilage. One difference will be if the amount used in production is different from the amount purchased. Then, we will want to separate the calculations. � The standard price per unit defines the price that should be paid for each unit of direct materials and it should reflect the final, delivered cost of those materials. � Once standard cost card has been created, we are ready to calculate the direct materials and direct labor variances.
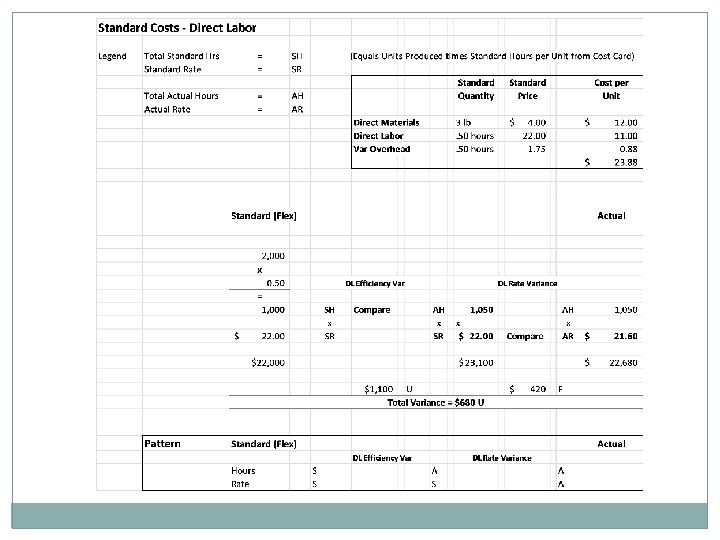
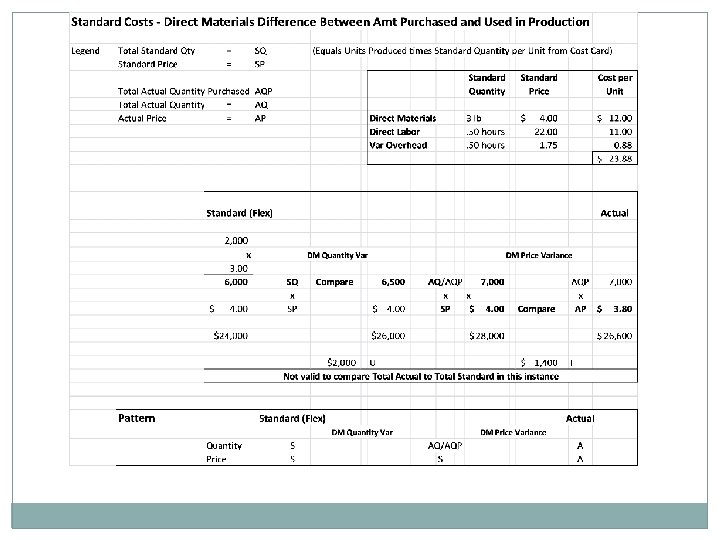
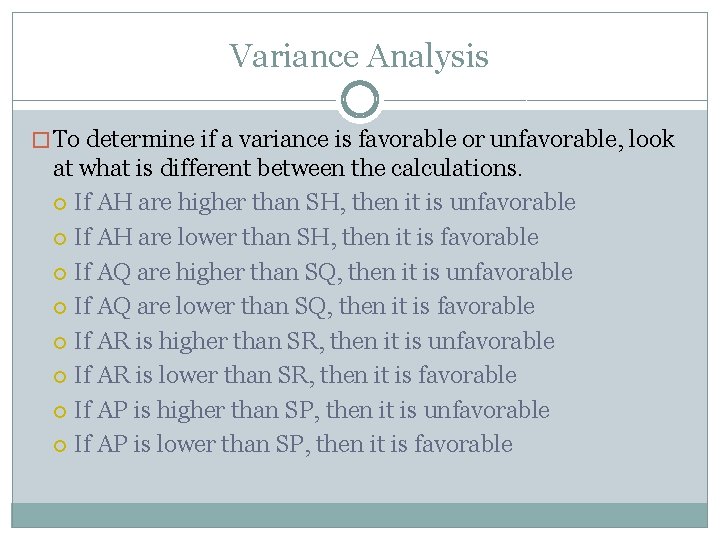
Variance Analysis � To determine if a variance is favorable or unfavorable, look at what is different between the calculations. If AH are higher than SH, then it is unfavorable If AH are lower than SH, then it is favorable If AQ are higher than SQ, then it is unfavorable If AQ are lower than SQ, then it is favorable If AR is higher than SR, then it is unfavorable If AR is lower than SR, then it is favorable If AP is higher than SP, then it is unfavorable If AP is lower than SP, then it is favorable
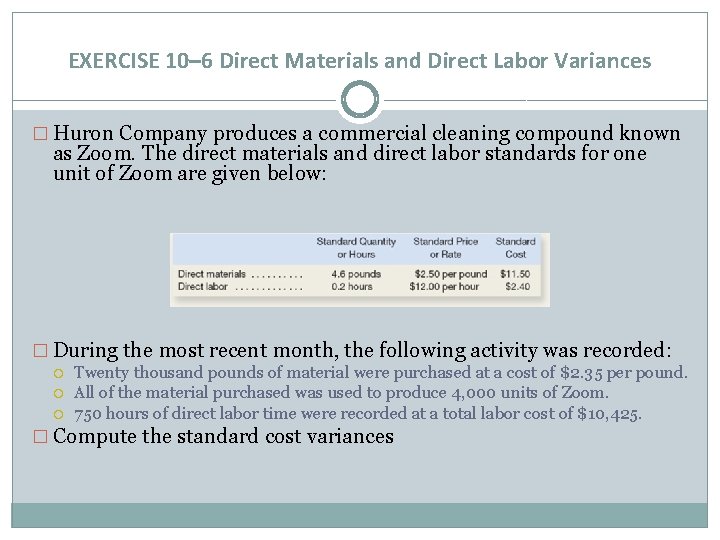
EXERCISE 10– 6 Direct Materials and Direct Labor Variances � Huron Company produces a commercial cleaning compound known as Zoom. The direct materials and direct labor standards for one unit of Zoom are given below: � During the most recent month, the following activity was recorded: Twenty thousand pounds of material were purchased at a cost of $2. 35 per pound. All of the material purchased was used to produce 4, 000 units of Zoom. 750 hours of direct labor time were recorded at a total labor cost of $10, 425. � Compute the standard cost variances
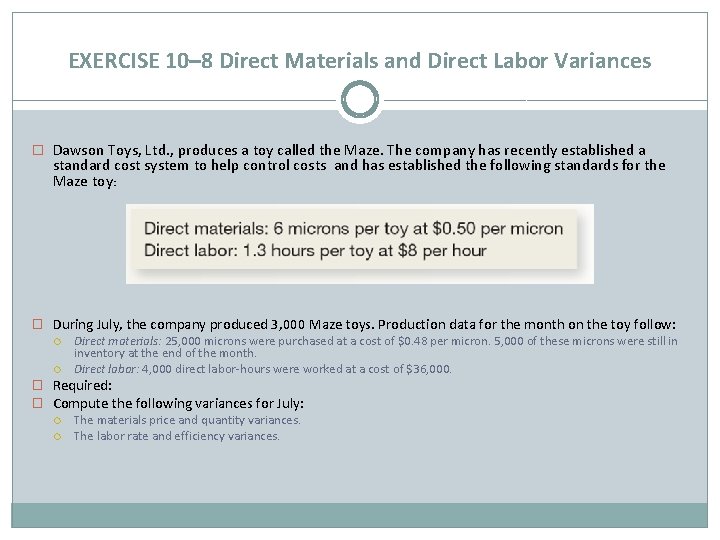
EXERCISE 10– 8 Direct Materials and Direct Labor Variances � Dawson Toys, Ltd. , produces a toy called the Maze. The company has recently established a standard cost system to help control costs and has established the following standards for the Maze toy: � During July, the company produced 3, 000 Maze toys. Production data for the month on the toy follow: Direct materials: 25, 000 microns were purchased at a cost of $0. 48 per micron. 5, 000 of these microns were still in inventory at the end of the month. Direct labor: 4, 000 direct labor-hours were worked at a cost of $36, 000. � Required: � Compute the following variances for July: The materials price and quantity variances. The labor rate and efficiency variances.
Manufacturing cost vs non manufacturing cost
Process costing definition
Controllable expenses examples
Manufacturing cost vs non manufacturing cost
When setting direct labor standards
Voh cost
Material yield variance arises due to change in the
Fixed overhead budget variance formula
Material price variance
Additively
Disadvantages of standard costing system
Cost behavior and cost-volume-profit analysis