QXF WindingCuring Tooling and Curing Mold Miao Yu
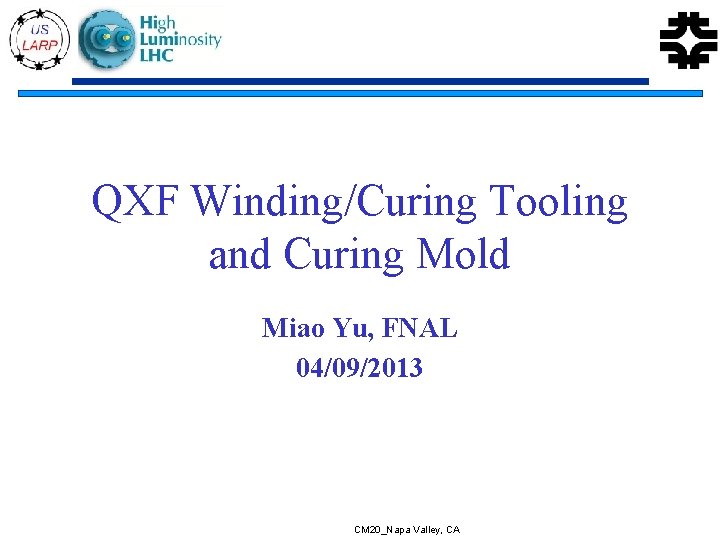
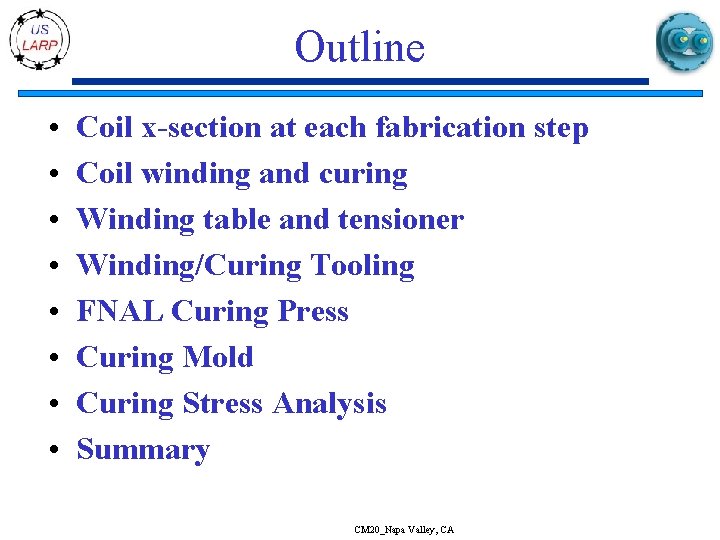
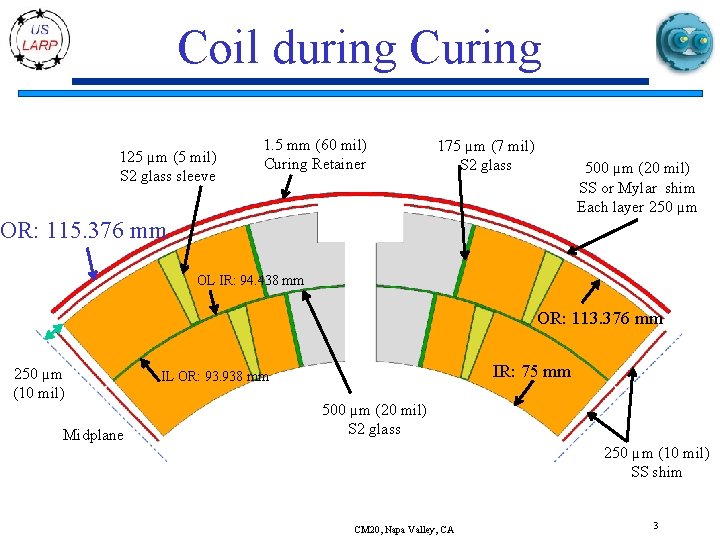
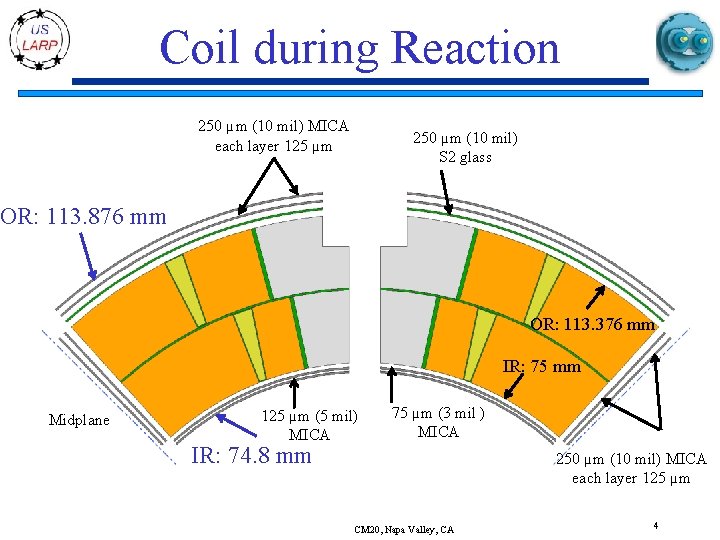
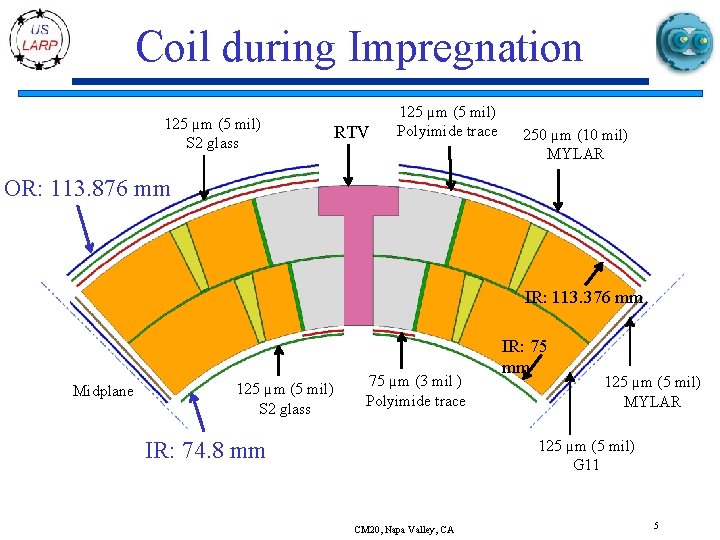
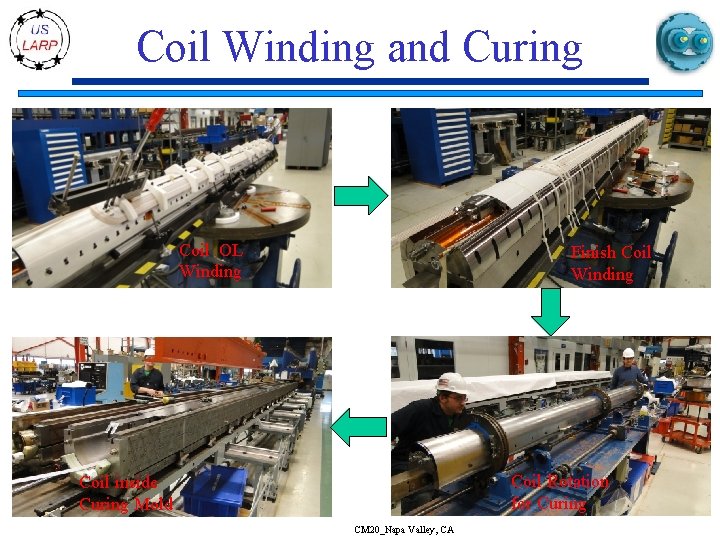
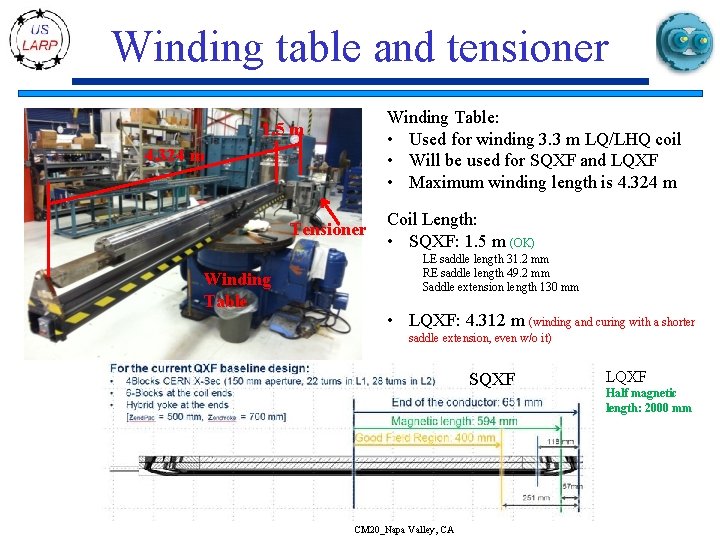
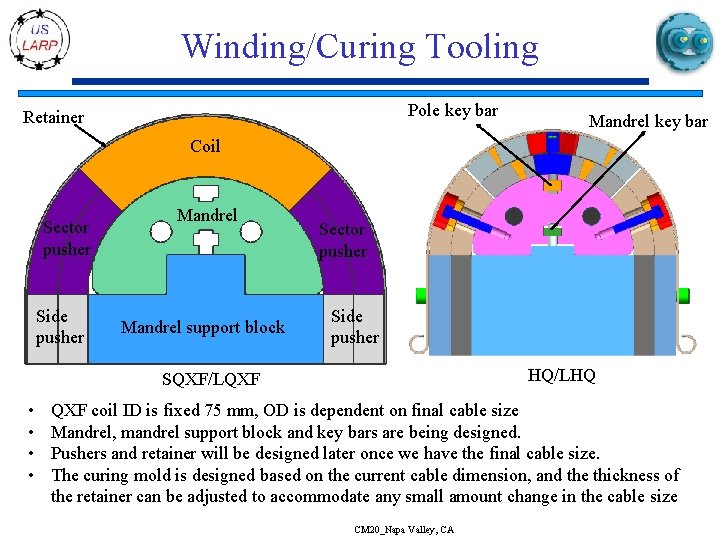
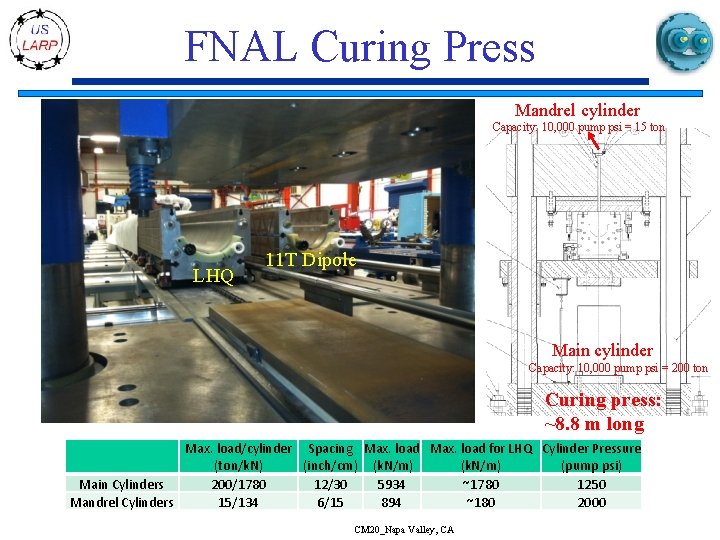
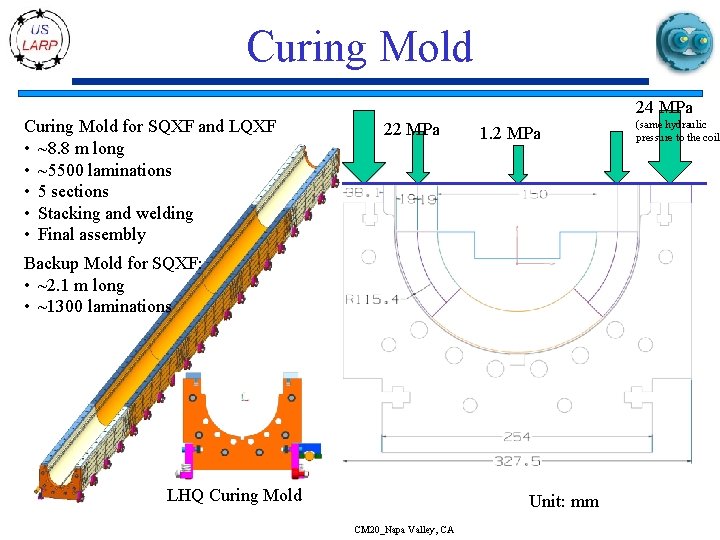
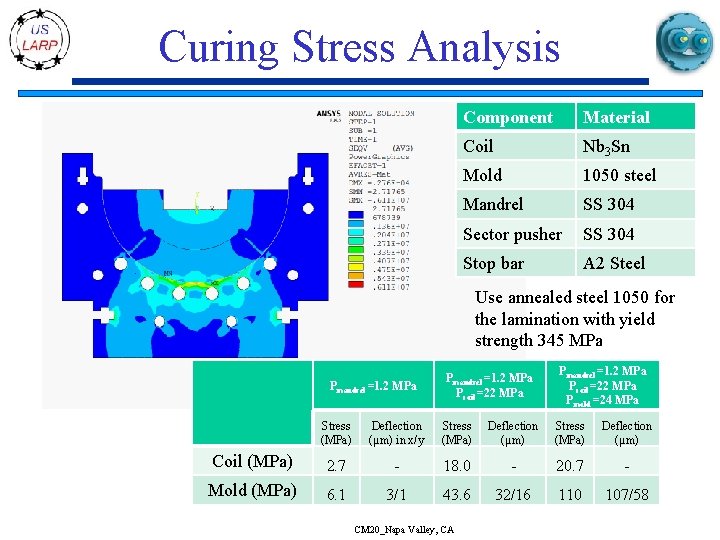
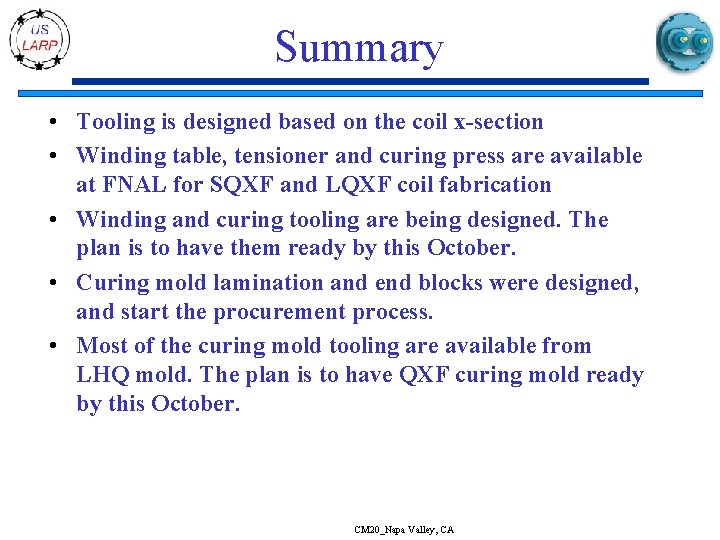
- Slides: 12
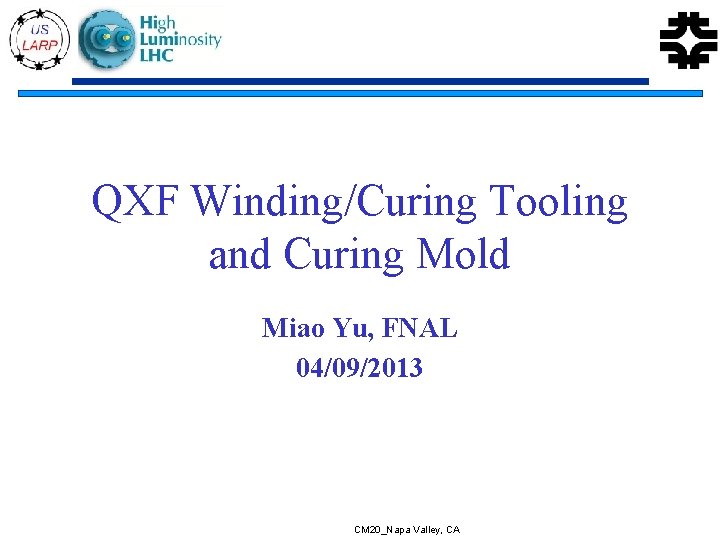
QXF Winding/Curing Tooling and Curing Mold Miao Yu, FNAL 04/09/2013 CM 20_Napa Valley, CA
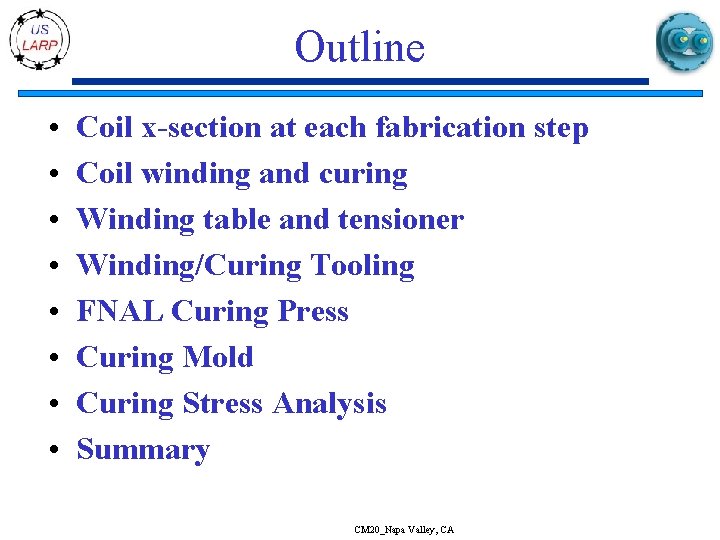
Outline • • Coil x-section at each fabrication step Coil winding and curing Winding table and tensioner Winding/Curing Tooling FNAL Curing Press Curing Mold Curing Stress Analysis Summary CM 20_Napa Valley, CA
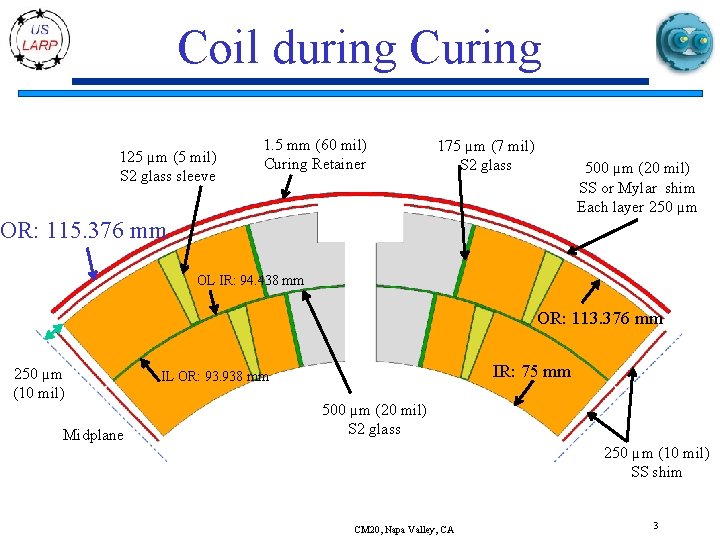
Coil during Curing 125 µm (5 mil) S 2 glass sleeve 1. 5 mm (60 mil) Curing Retainer 175 µm (7 mil) S 2 glass 500 µm (20 mil) SS or Mylar shim Each layer 250 µm OR: 115. 376 mm OL IR: 94. 438 mm OR: 113. 376 mm 250 µm (10 mil) Midplane IR: 75 mm IL OR: 93. 938 mm 500 µm (20 mil) S 2 glass 250 µm (10 mil) SS shim CM 20, Napa Valley, CA 3
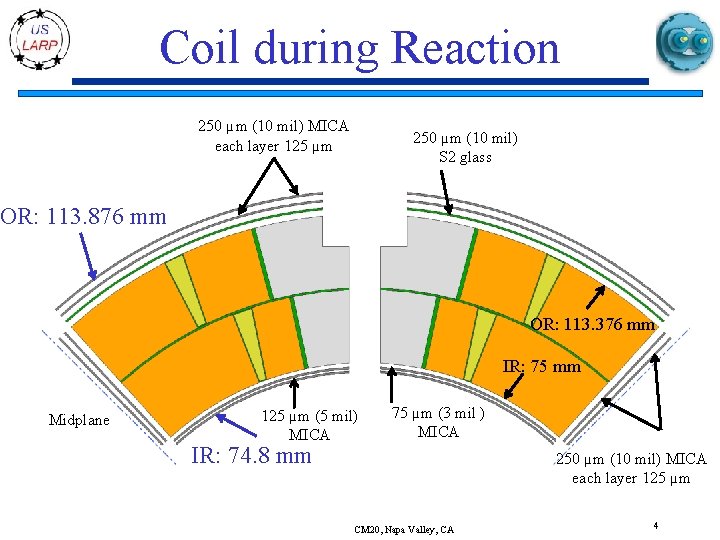
Coil during Reaction 250 µm (10 mil) MICA each layer 125 µm 250 µm (10 mil) S 2 glass OR: 113. 876 mm OR: 113. 376 mm IR: 75 mm Midplane 125 µm (5 mil) MICA 75 µm (3 mil ) MICA IR: 74. 8 mm 250 µm (10 mil) MICA each layer 125 µm CM 20, Napa Valley, CA 4
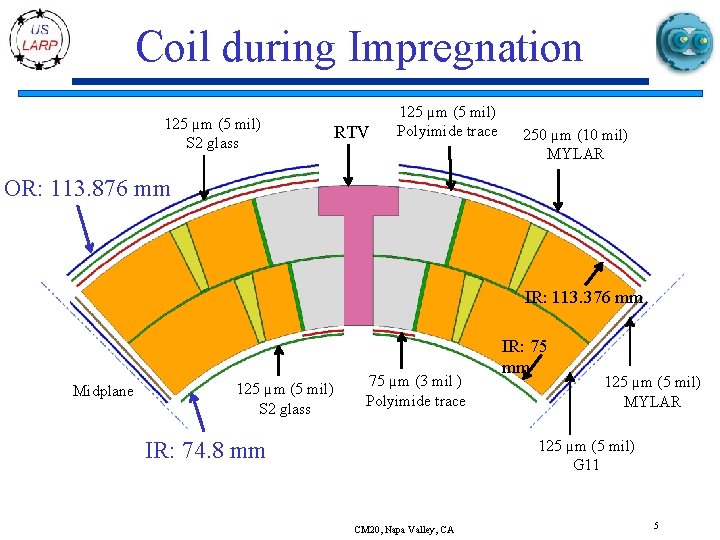
Coil during Impregnation 125 µm (5 mil) S 2 glass RTV 125 µm (5 mil) Polyimide trace 250 µm (10 mil) MYLAR OR: 113. 876 mm IR: 113. 376 mm Midplane 125 µm (5 mil) S 2 glass 75 µm (3 mil ) Polyimide trace IR: 74. 8 mm IR: 75 mm 125 µm (5 mil) MYLAR 125 µm (5 mil) G 11 CM 20, Napa Valley, CA 5
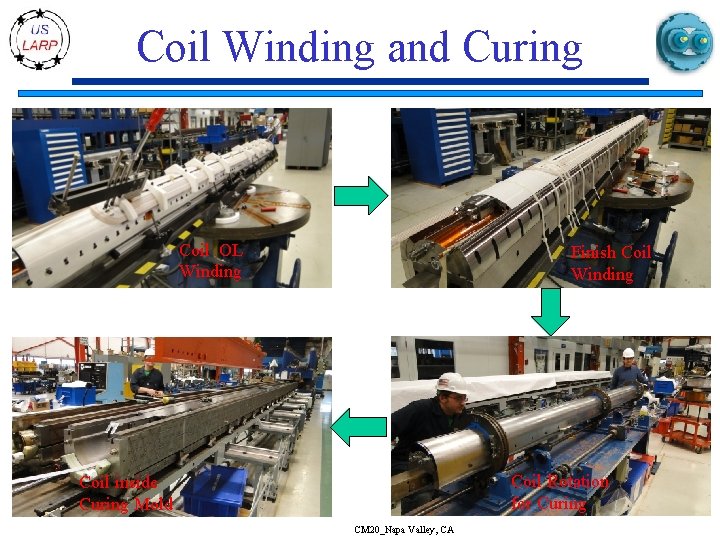
Coil Winding and Curing Coil OL Winding Finish Coil Winding Coil Rotation for Curing Coil inside Curing Mold CM 20_Napa Valley, CA
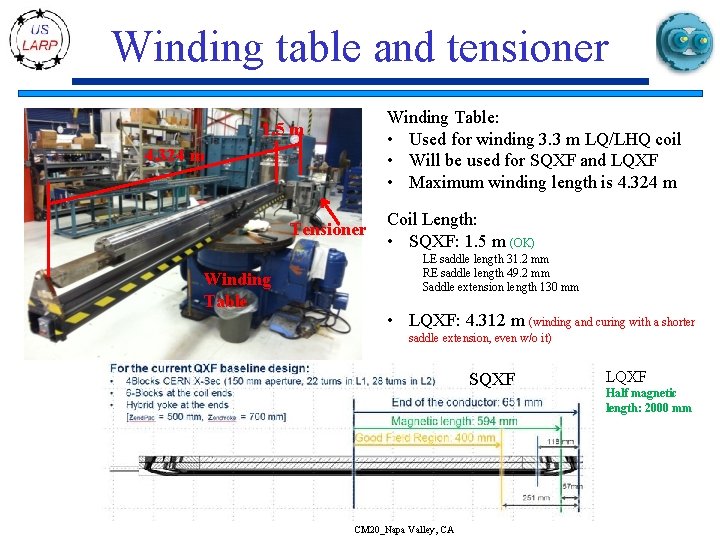
Winding table and tensioner Winding Table: • Used for winding 3. 3 m LQ/LHQ coil • Will be used for SQXF and LQXF • Maximum winding length is 4. 324 m 1. 5 m 4. 324 m Tensioner Winding Table Coil Length: • SQXF: 1. 5 m (OK) LE saddle length 31. 2 mm RE saddle length 49. 2 mm Saddle extension length 130 mm • LQXF: 4. 312 m (winding and curing with a shorter saddle extension, even w/o it) SQXF CM 20_Napa Valley, CA LQXF Half magnetic length: 2000 mm
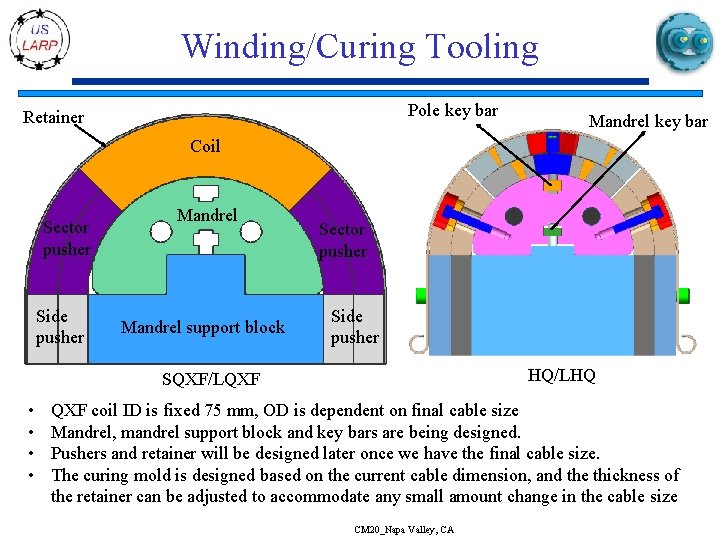
Winding/Curing Tooling Pole key bar Retainer Mandrel key bar Coil Sector pusher Side pusher Mandrel support block Sector pusher Side pusher HQ/LHQ SQXF/LQXF • • QXF coil ID is fixed 75 mm, OD is dependent on final cable size Mandrel, mandrel support block and key bars are being designed. Pushers and retainer will be designed later once we have the final cable size. The curing mold is designed based on the current cable dimension, and the thickness of the retainer can be adjusted to accommodate any small amount change in the cable size CM 20_Napa Valley, CA
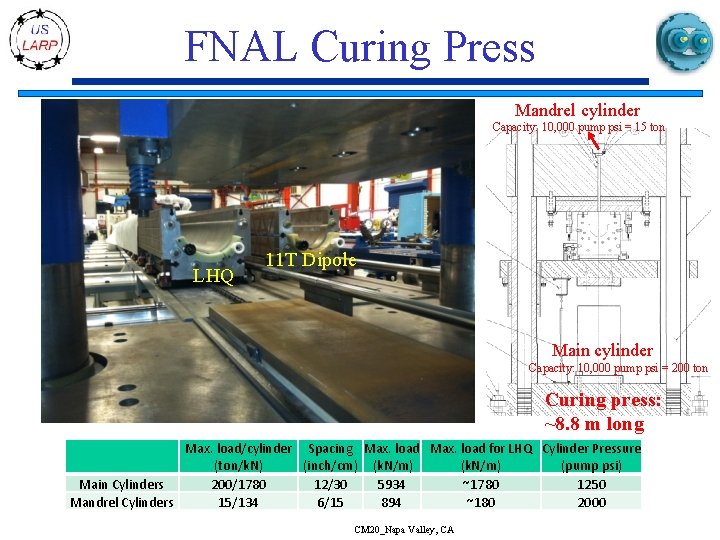
FNAL Curing Press Mandrel cylinder Capacity: 10, 000 pump psi = 15 ton LHQ 11 T Dipole Main cylinder Capacity: 10, 000 pump psi = 200 ton Curing press: ~8. 8 m long Max. load/cylinder Spacing Max. load for LHQ Cylinder Pressure (ton/k. N) (inch/cm) (k. N/m) (pump psi) Main Cylinders 200/1780 12/30 5934 ~1780 1250 Mandrel Cylinders 15/134 6/15 894 ~180 2000 CM 20_Napa Valley, CA
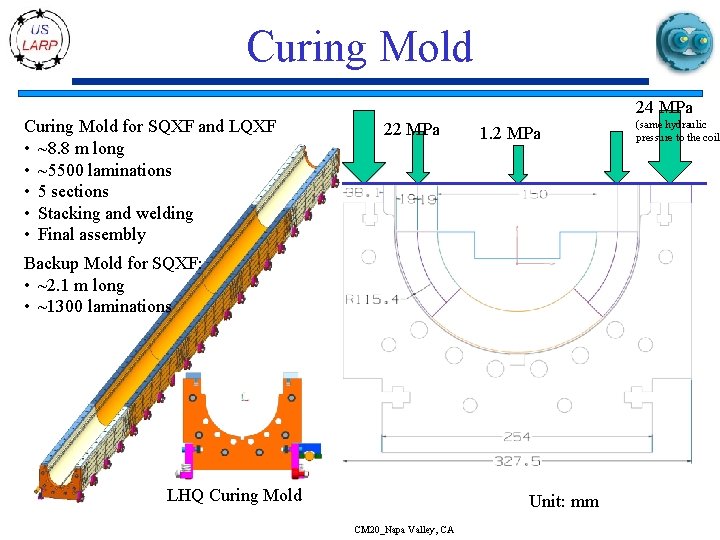
Curing Mold for SQXF and LQXF • ~8. 8 m long • ~5500 laminations • 5 sections • Stacking and welding • Final assembly 24 MPa 22 MPa 1. 2 MPa Backup Mold for SQXF: • ~2. 1 m long • ~1300 laminations LHQ Curing Mold Unit: mm CM 20_Napa Valley, CA (same hydraulic pressure to the coil)
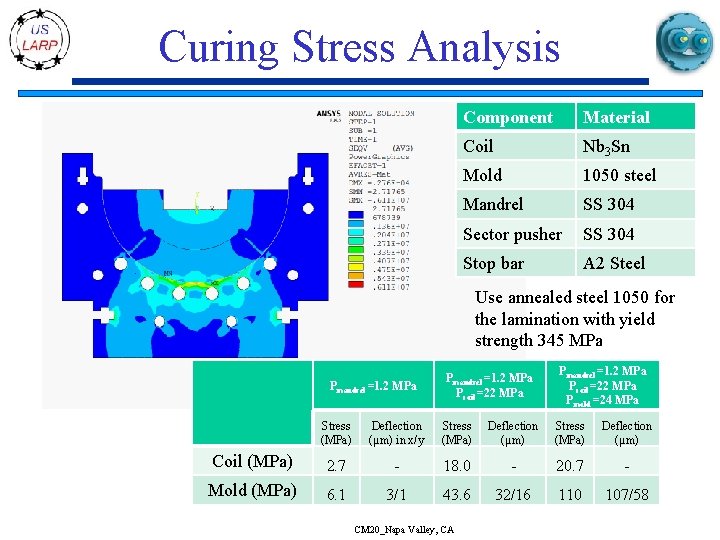
Curing Stress Analysis Component Material Coil Nb 3 Sn Mold 1050 steel Mandrel SS 304 Sector pusher SS 304 Stop bar A 2 Steel Use annealed steel 1050 for the lamination with yield strength 345 MPa Pmandrel =1. 2 MPa Pcoil =22 MPa Pmold =24 MPa Stress (MPa) Deflection (µm) in x/y Stress (MPa) Deflection (µm) Coil (MPa) 2. 7 - 18. 0 - 20. 7 - Mold (MPa) 6. 1 3/1 43. 6 32/16 110 107/58 CM 20_Napa Valley, CA
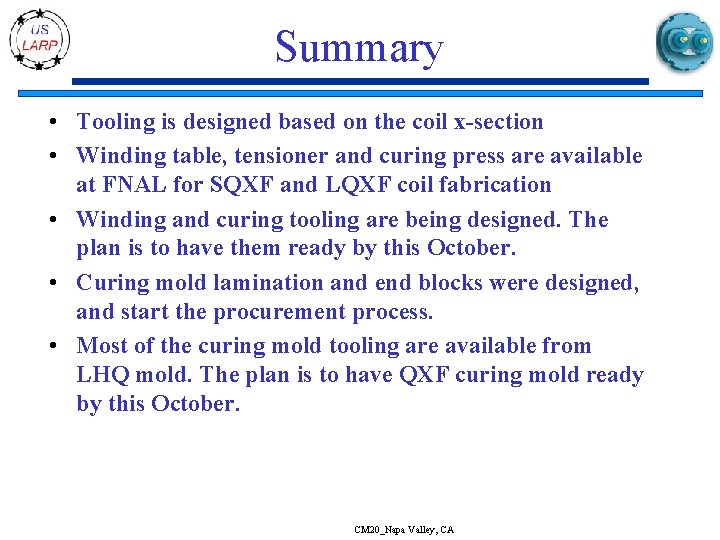
Summary • Tooling is designed based on the coil x-section • Winding table, tensioner and curing press are available at FNAL for SQXF and LQXF coil fabrication • Winding and curing tooling are being designed. The plan is to have them ready by this October. • Curing mold lamination and end blocks were designed, and start the procurement process. • Most of the curing mold tooling are available from LHQ mold. The plan is to have QXF curing mold ready by this October. CM 20_Napa Valley, CA
Rossini's cat duet
Soft tooling vs hard tooling
Are algae plants or protists
Bulk factor in compression moulding
Pot type mold & plunger type mold are the classification of
Yajie miao
Peter miao
Concrete constructing forms and curing vocabulary
Impervious paper curing
Concrete cure curve
Chapter 46 impression materials
Syneresis impression material
Solid ground curing