Preliminary examination of highvelocity metalshaping with electrical wire
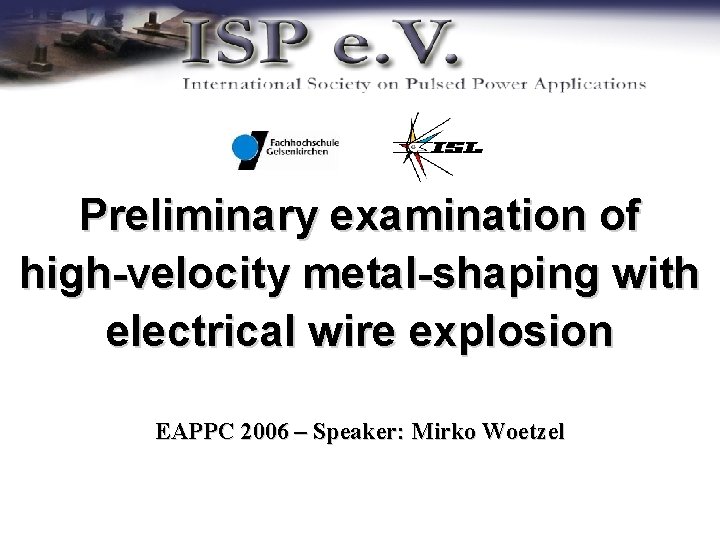
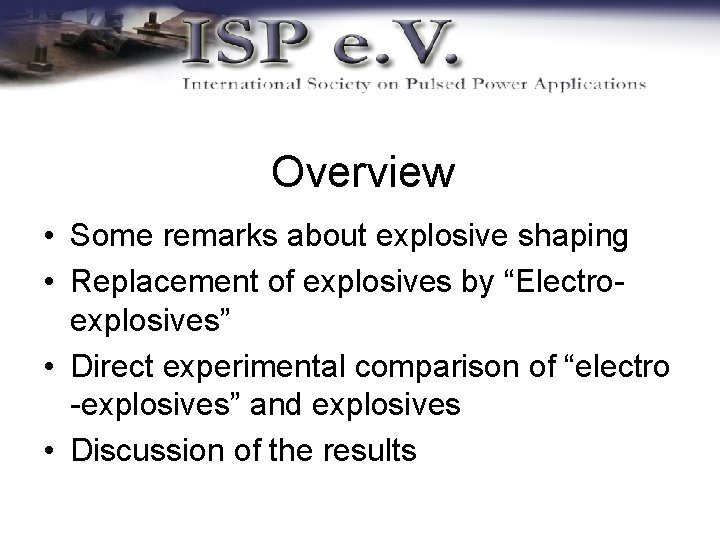
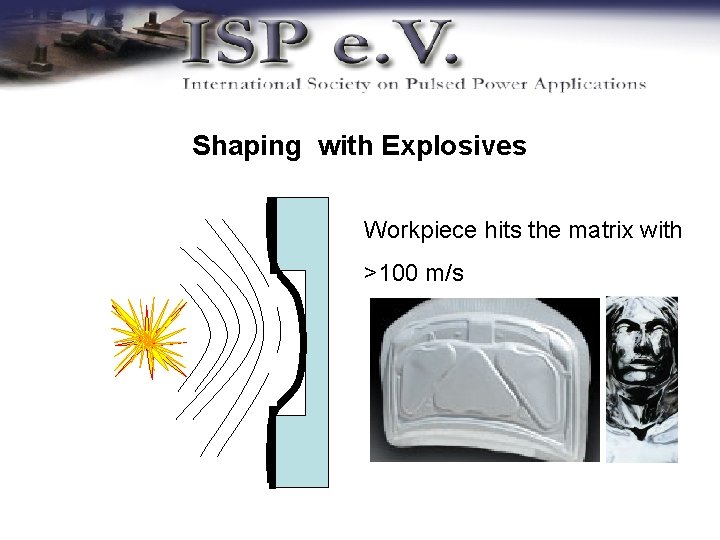
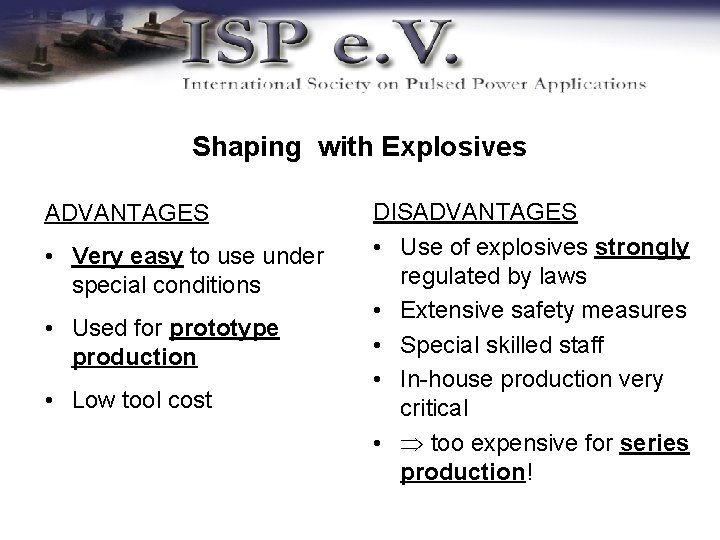
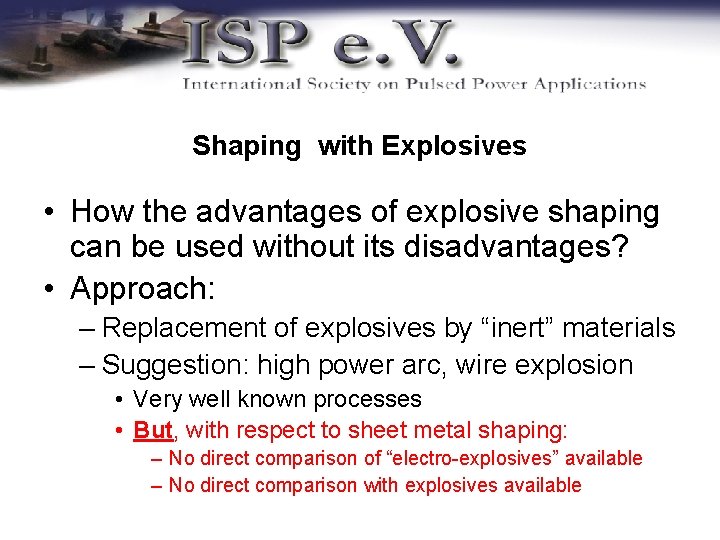
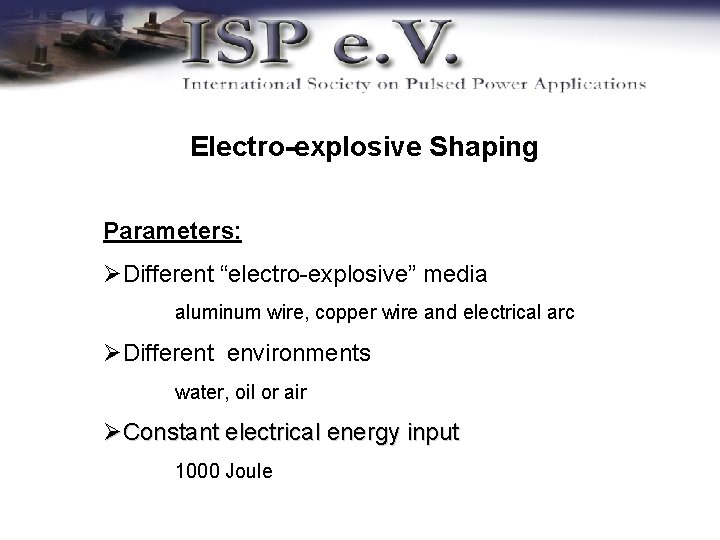
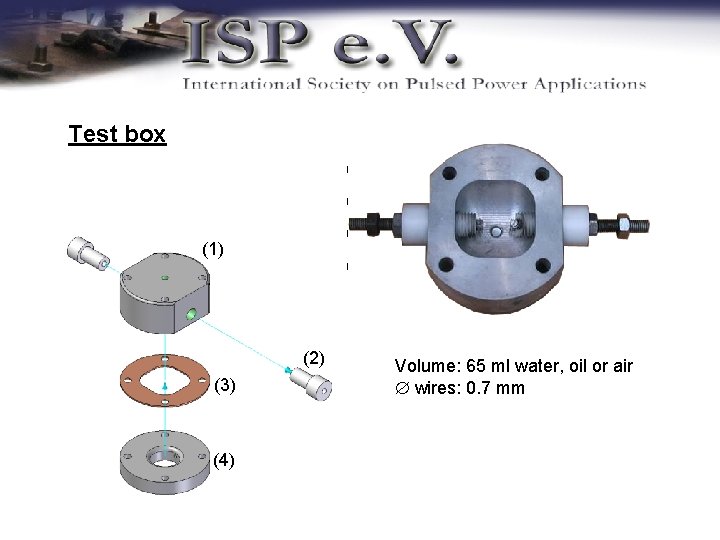
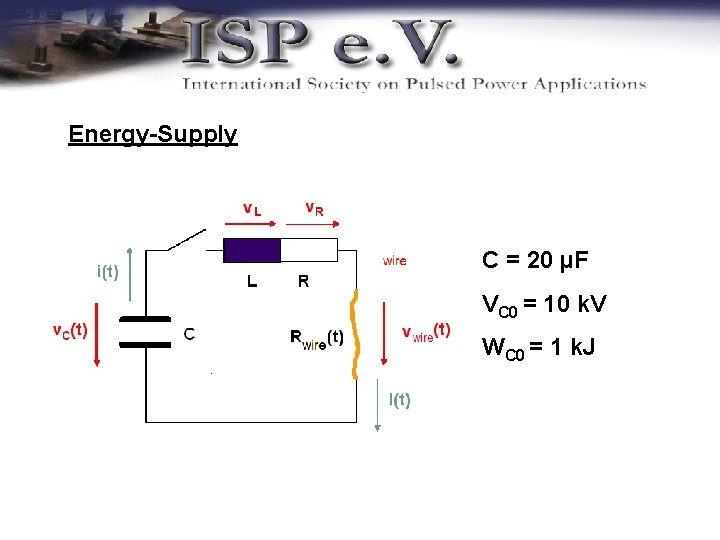
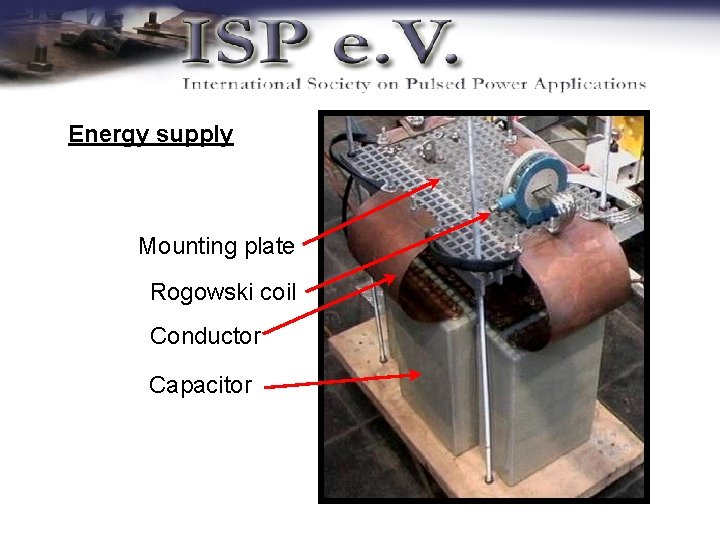
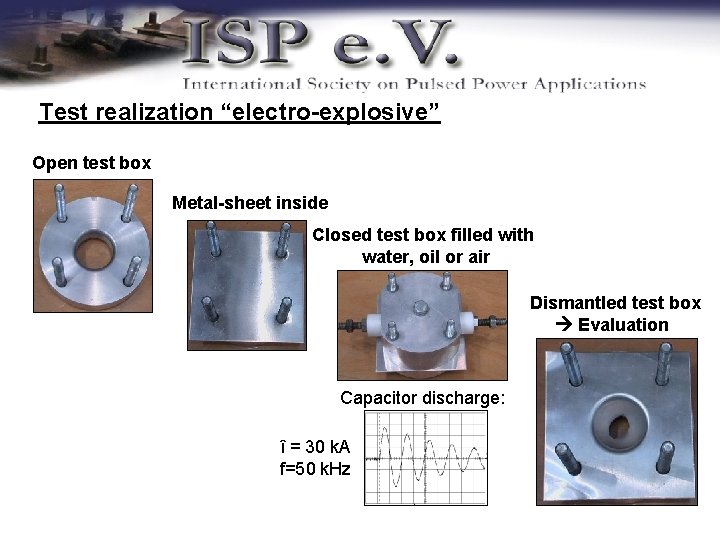
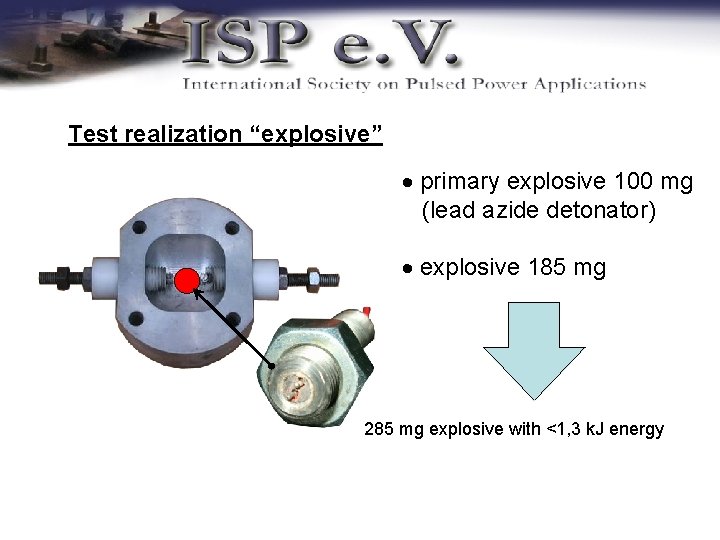
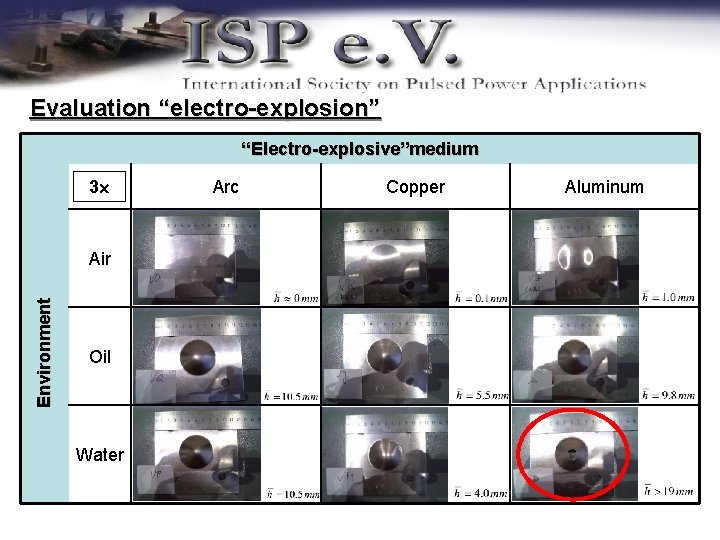
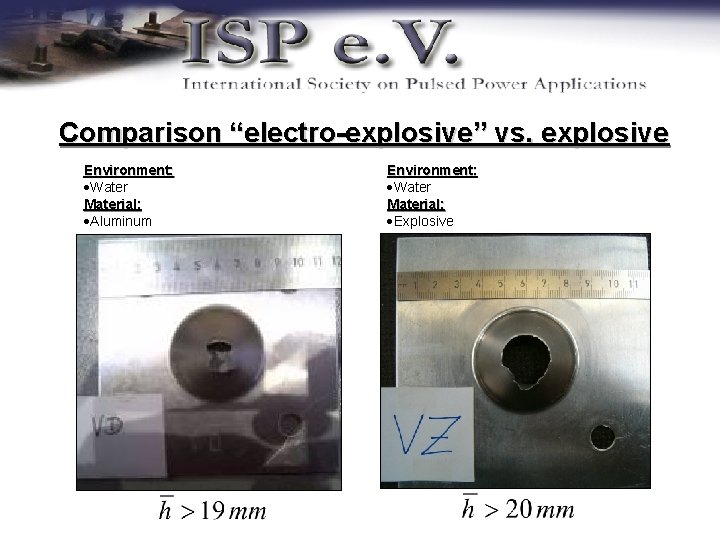
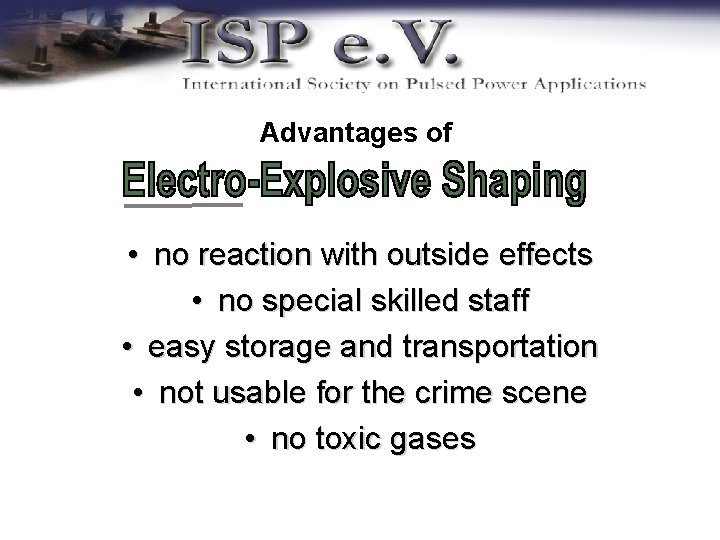
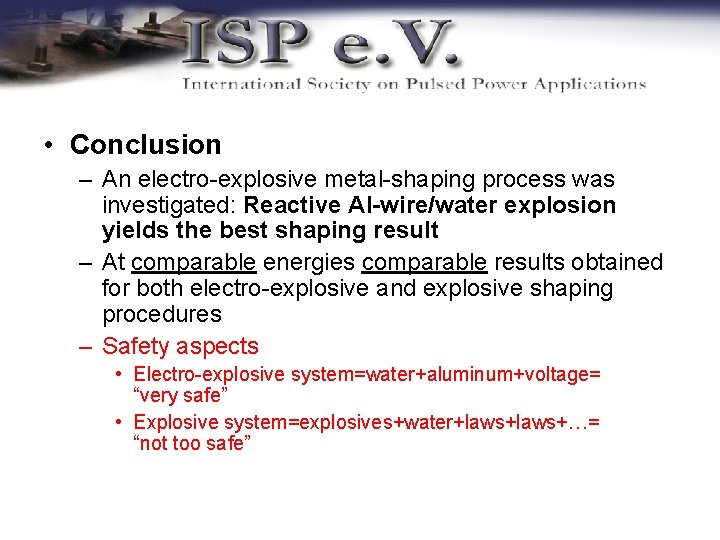
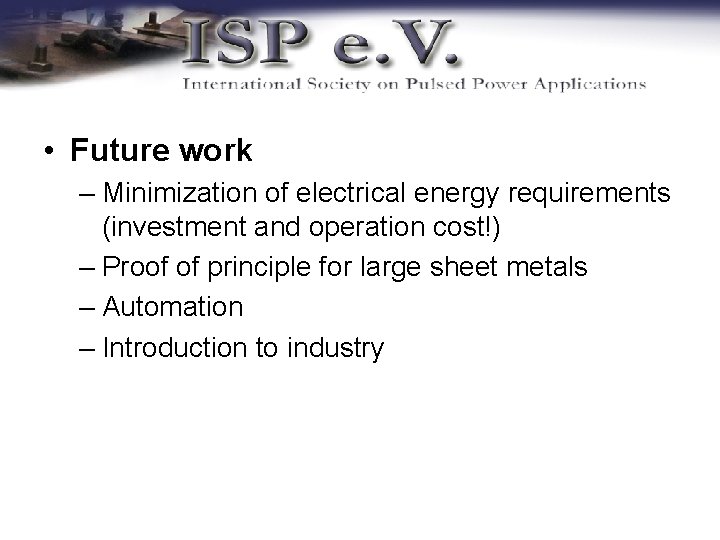
- Slides: 16
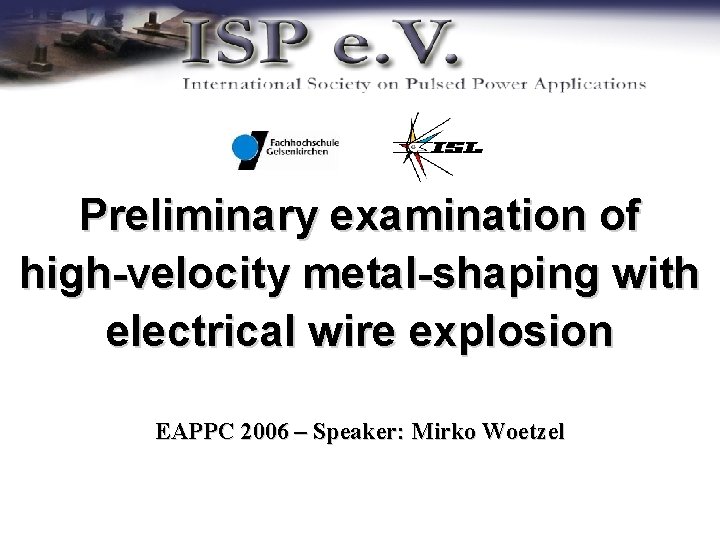
Preliminary examination of high-velocity metal-shaping with electrical wire explosion EAPPC 2006 – Speaker: Mirko Woetzel
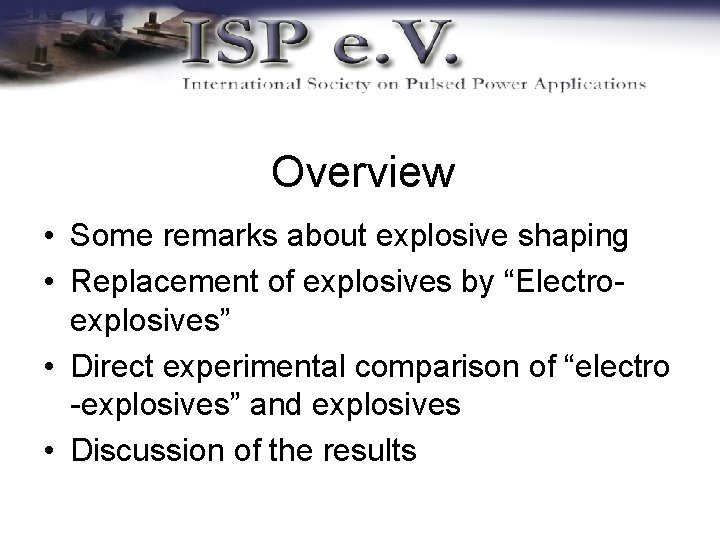
Overview • Some remarks about explosive shaping • Replacement of explosives by “Electroexplosives” • Direct experimental comparison of “electro -explosives” and explosives • Discussion of the results
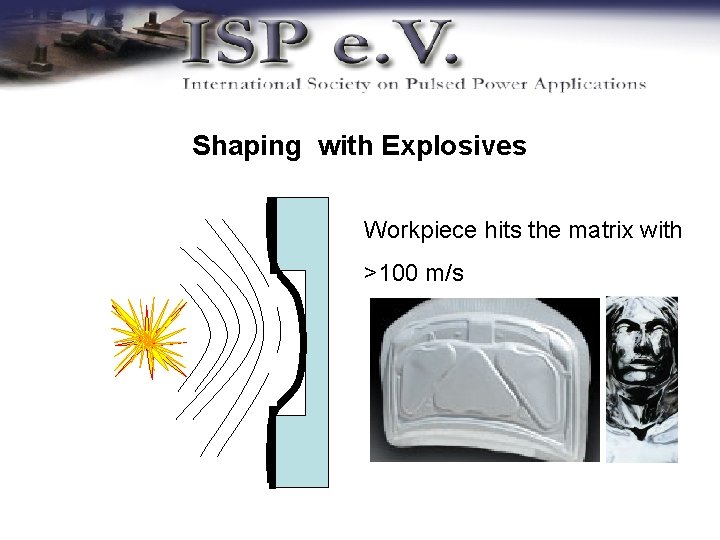
Shaping with Explosives Workpiece hits the matrix with >100 m/s
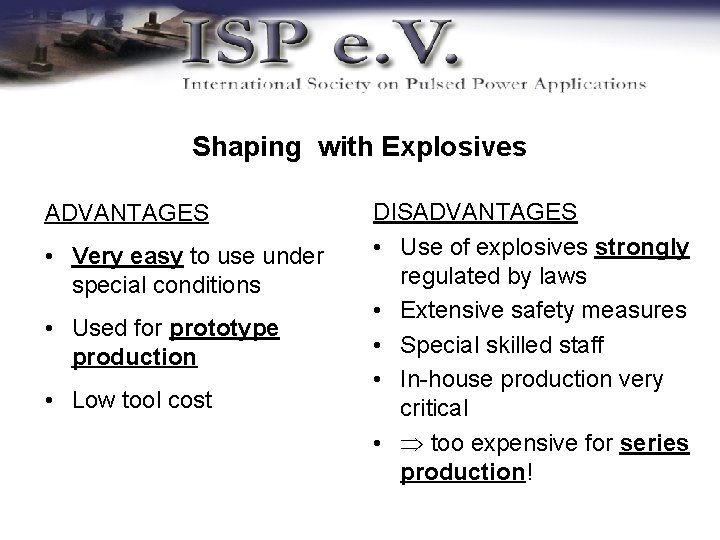
Shaping with Explosives ADVANTAGES • Very easy to use under special conditions • Used for prototype production • Low tool cost DISADVANTAGES • Use of explosives strongly regulated by laws • Extensive safety measures • Special skilled staff • In-house production very critical • too expensive for series production!
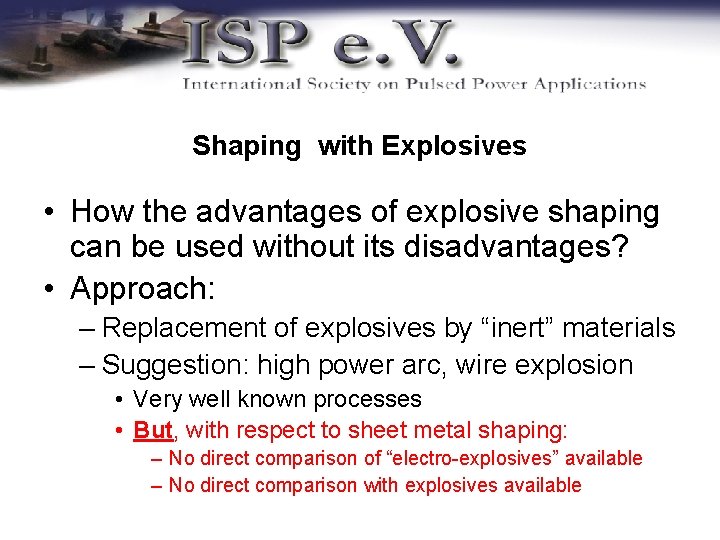
Shaping with Explosives • How the advantages of explosive shaping can be used without its disadvantages? • Approach: – Replacement of explosives by “inert” materials – Suggestion: high power arc, wire explosion • Very well known processes • But, with respect to sheet metal shaping: – No direct comparison of “electro-explosives” available – No direct comparison with explosives available
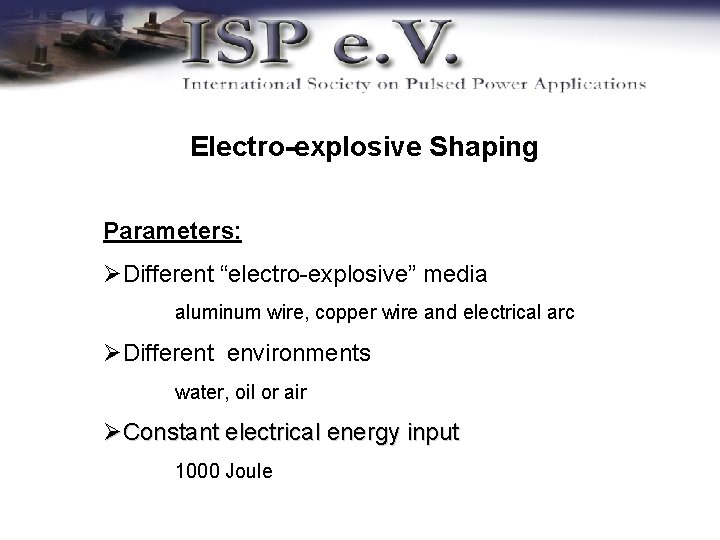
Electro-explosive Shaping Parameters: ØDifferent “electro-explosive” media aluminum wire, copper wire and electrical arc ØDifferent environments water, oil or air ØConstant electrical energy input 1000 Joule
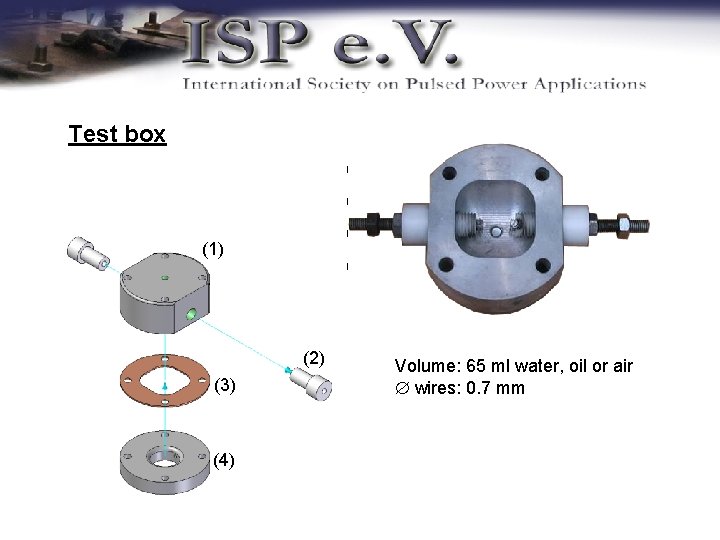
Test box (1) Aluminium – Master-Frame 20 mm (2) Teflon – Isolator of electrodes (3) Smooth Copper – Seal (1) (4) Aluminium – Shaping Matrix (2) (3) (4) Volume: 65 ml water, oil or air wires: 0. 7 mm
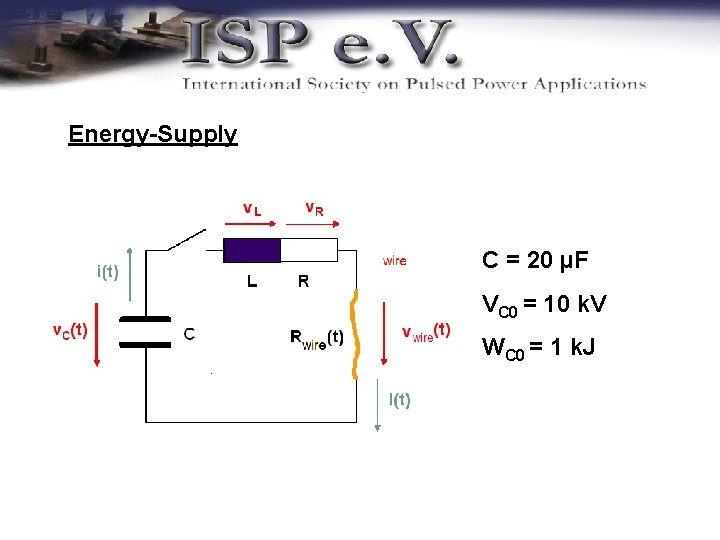
Energy-Supply C = 20 µF VC 0 = 10 k. V WC 0 = 1 k. J
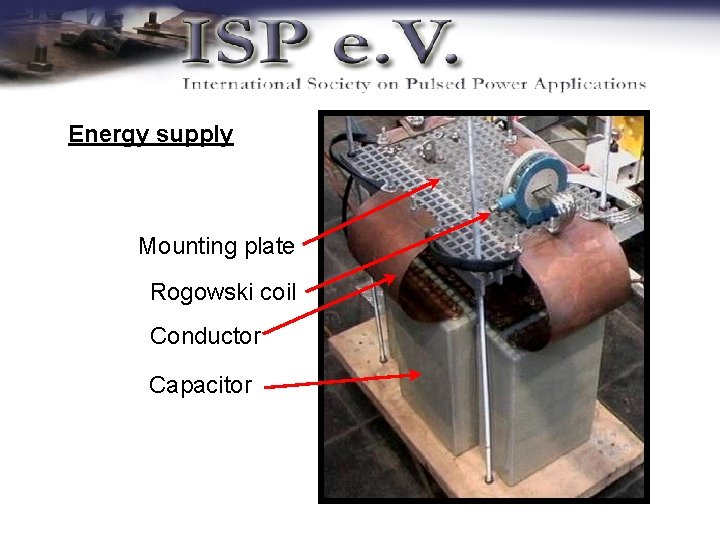
Energy supply Mounting plate Rogowski coil Conductor Capacitor
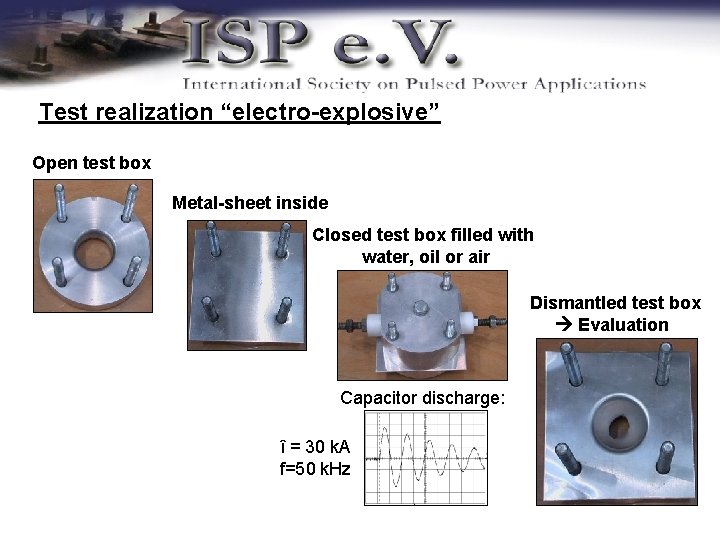
Test realization “electro-explosive” Open test box Metal-sheet inside Closed test box filled with water, oil or air Dismantled test box Evaluation Capacitor discharge: î = 30 k. A f=50 k. Hz
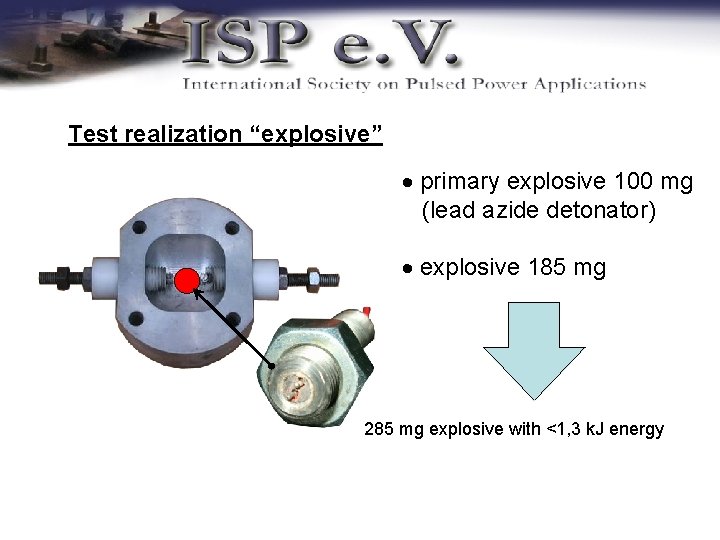
Test realization “explosive” primary explosive 100 mg (lead azide detonator) explosive 185 mg 285 mg explosive with <1, 3 k. J energy
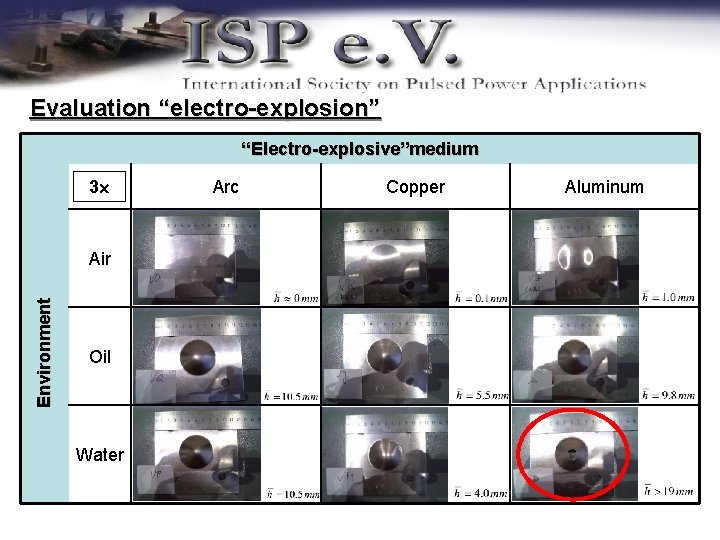
Evaluation “electro-explosion” “Electro-explosive”medium 3 Environment Air Oil Water Arc Copper Aluminum
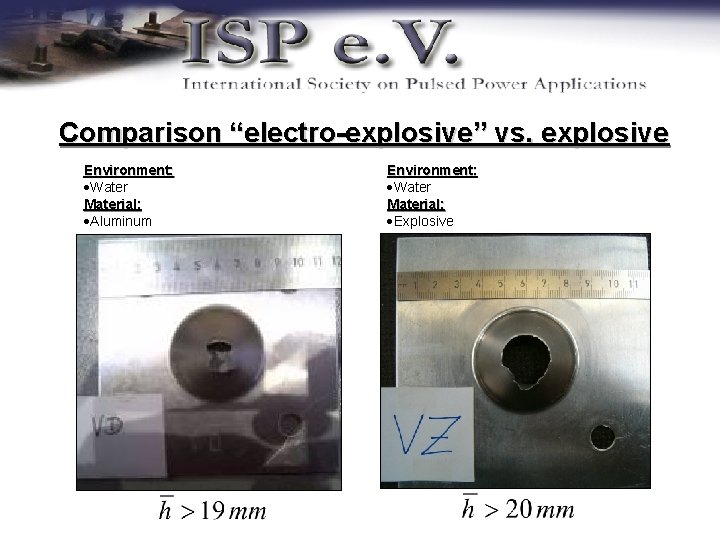
Comparison “electro-explosive” vs. explosive Environment: Water Material: Aluminum Environment: Water Material: Explosive
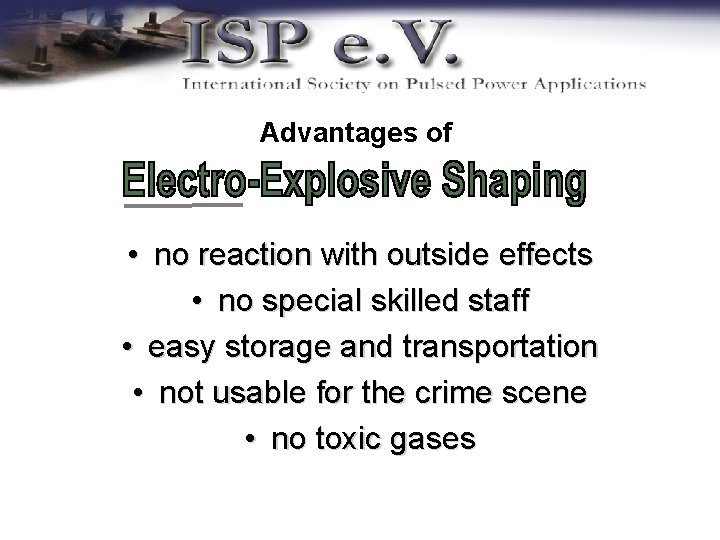
Advantages of • no reaction with outside effects • no special skilled staff • easy storage and transportation • not usable for the crime scene • no toxic gases
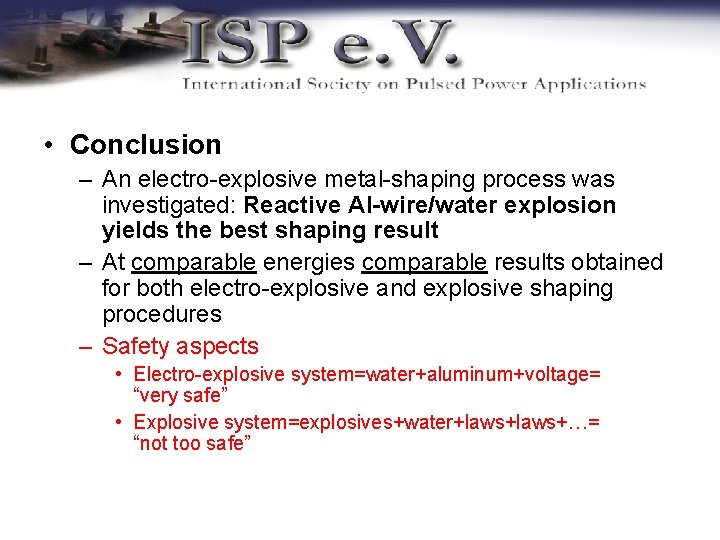
• Conclusion – An electro-explosive metal-shaping process was investigated: Reactive Al-wire/water explosion yields the best shaping result – At comparable energies comparable results obtained for both electro-explosive and explosive shaping procedures – Safety aspects • Electro-explosive system=water+aluminum+voltage= “very safe” • Explosive system=explosives+water+laws+…= “not too safe”
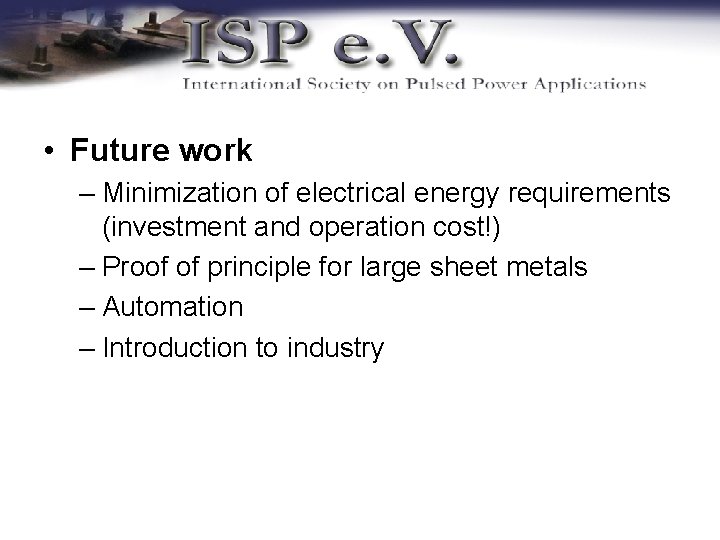
• Future work – Minimization of electrical energy requirements (investment and operation cost!) – Proof of principle for large sheet metals – Automation – Introduction to industry
A circular loop of wire is in a region of spatially uniform
Why do magnets repel
Mga pahinang preliminari kahulugan
Preliminary steps of haccp
Preliminary audit procedures
P 波
Arrt preliminary score
Preliminary assessment
Thesis statement formula
Components of effective pre-departure training programs
Preliminary interview
Preliminary statement definition
Chemical texture services
Preliminary budget
Preliminary results example
Preliminary works cited
3 p's of communication