Outline n n Introduce PCINSFCPF DSDM Research Effort
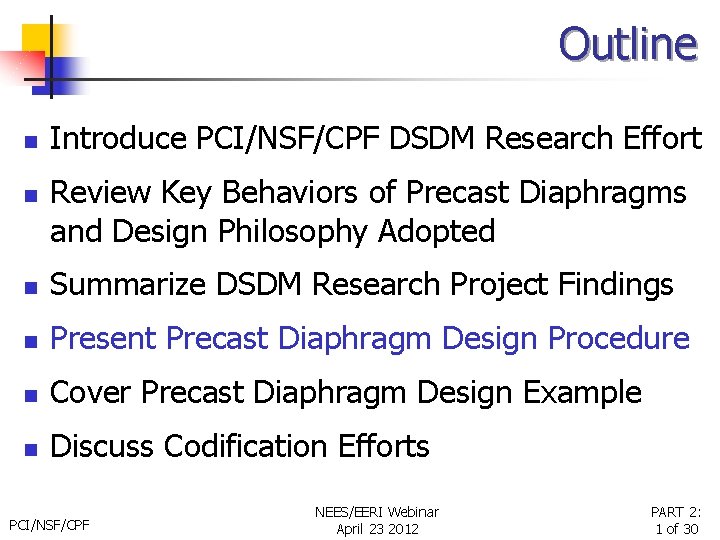
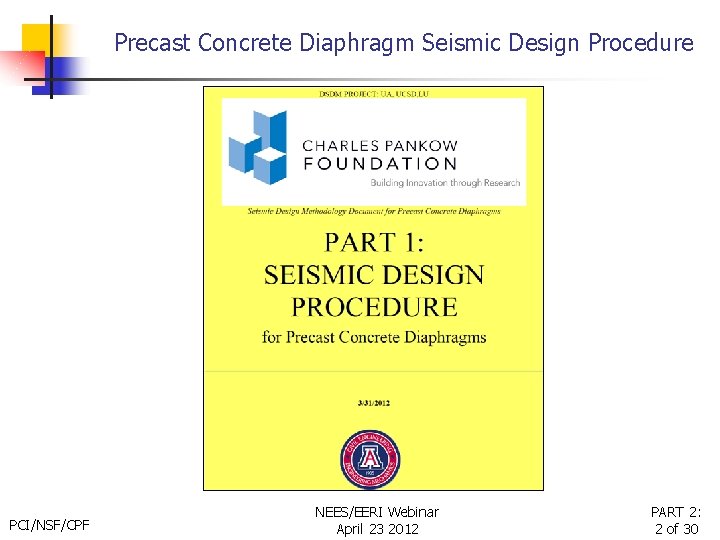
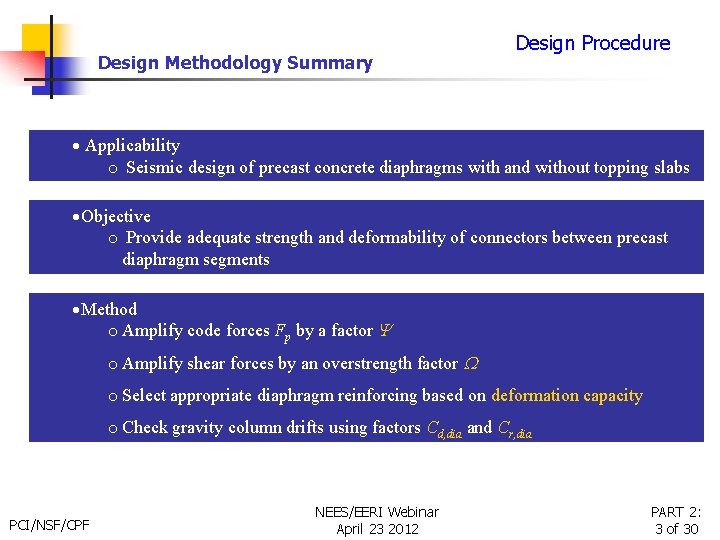
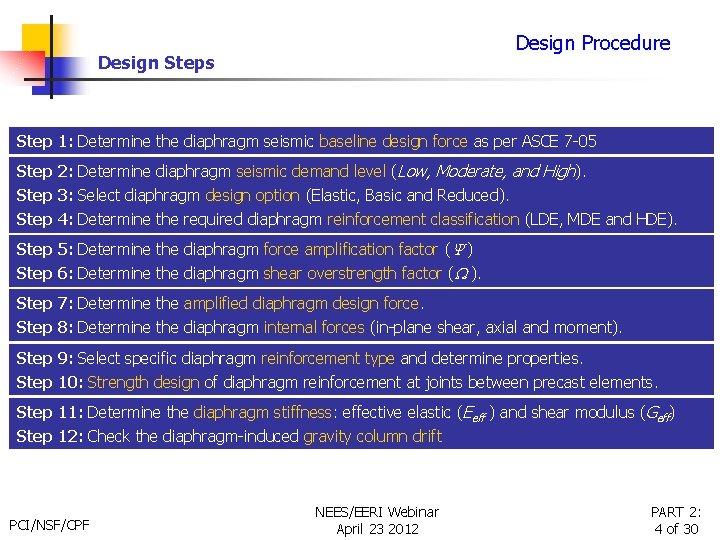
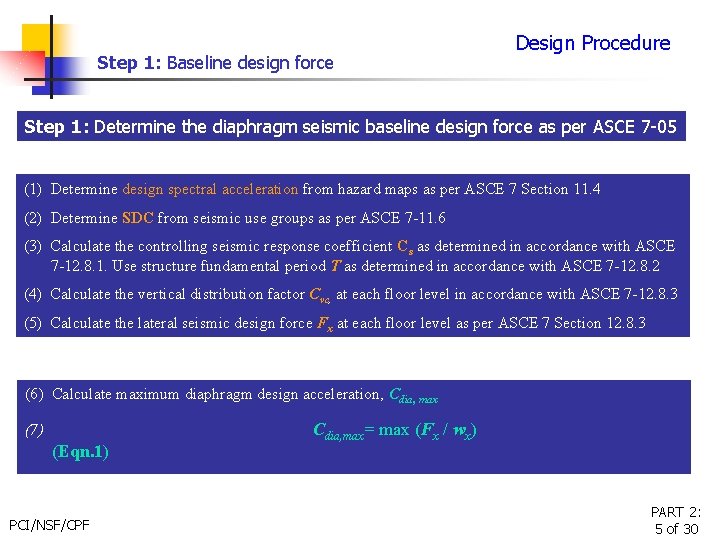
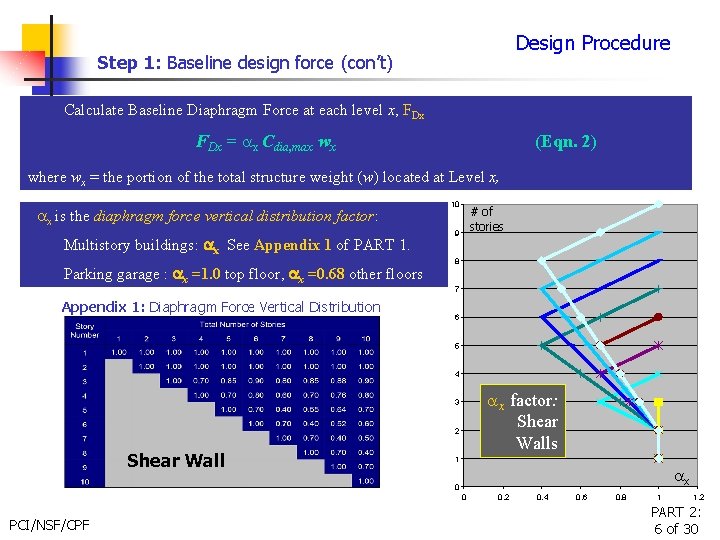
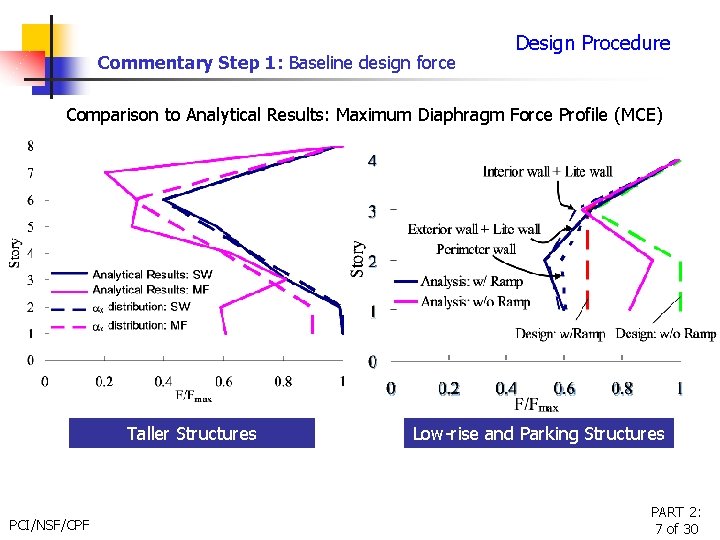
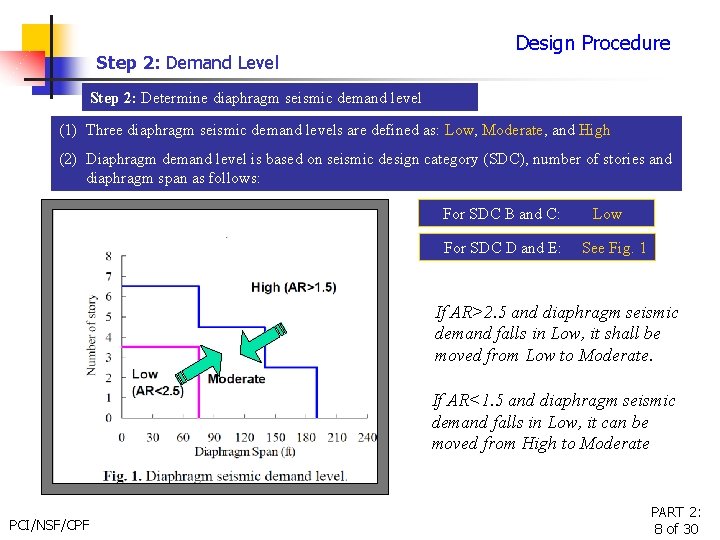
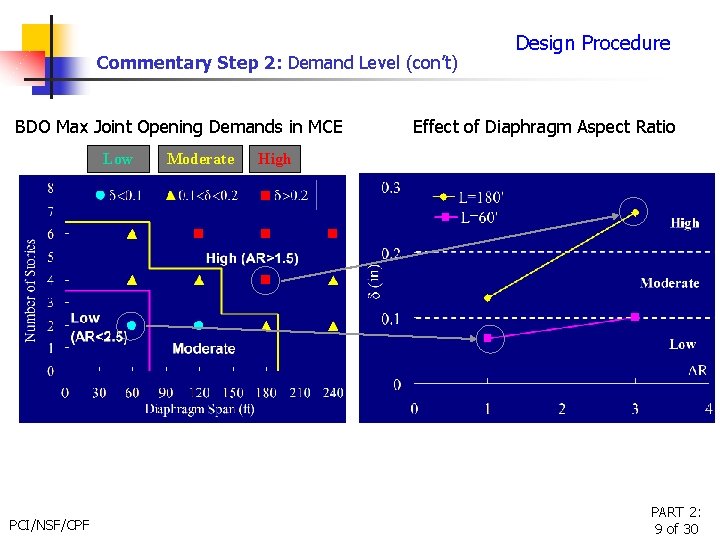
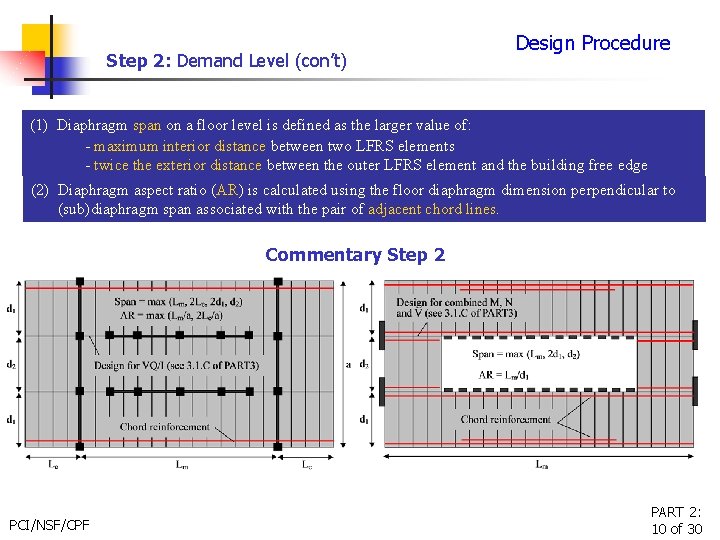
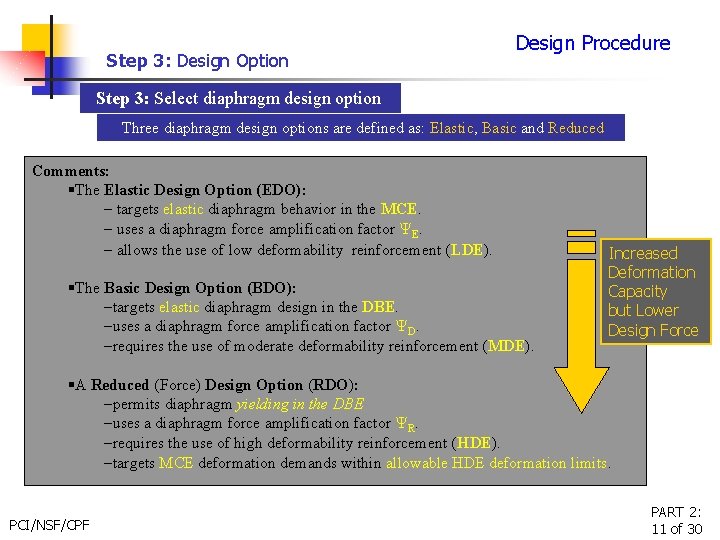
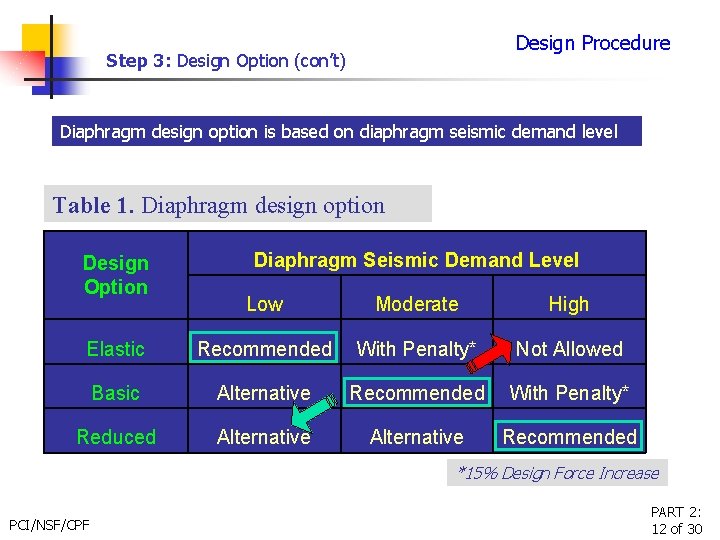
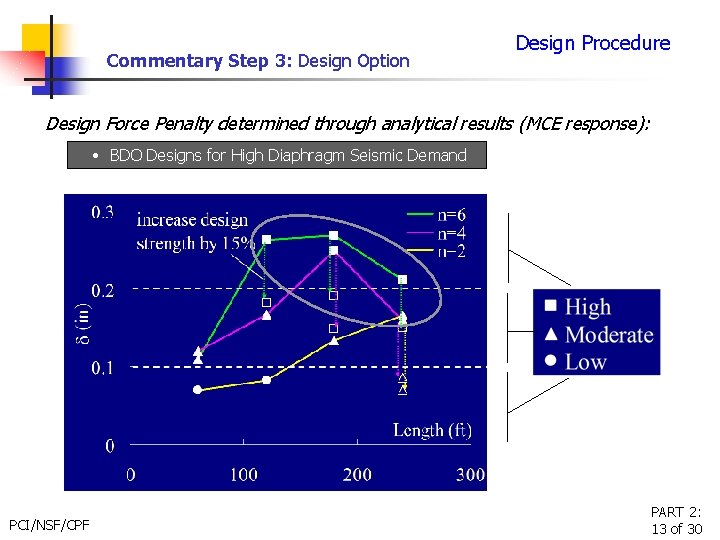
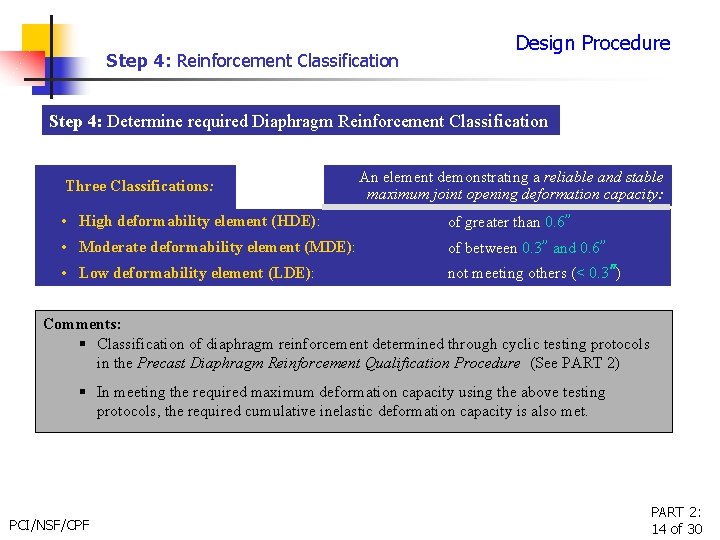
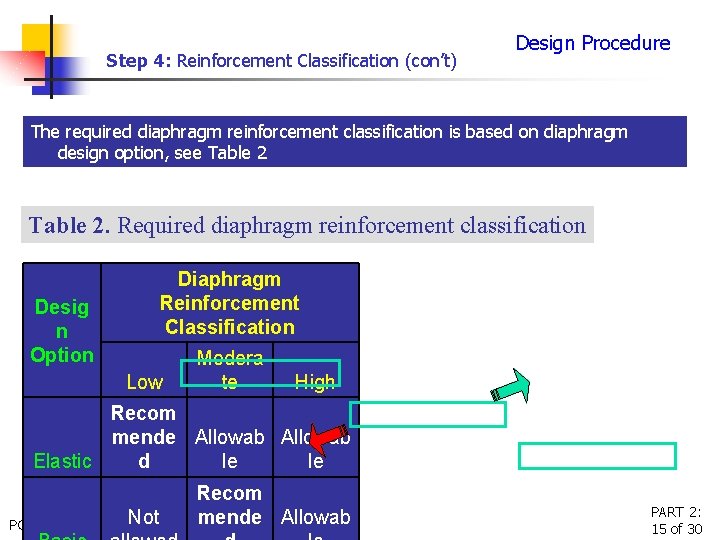
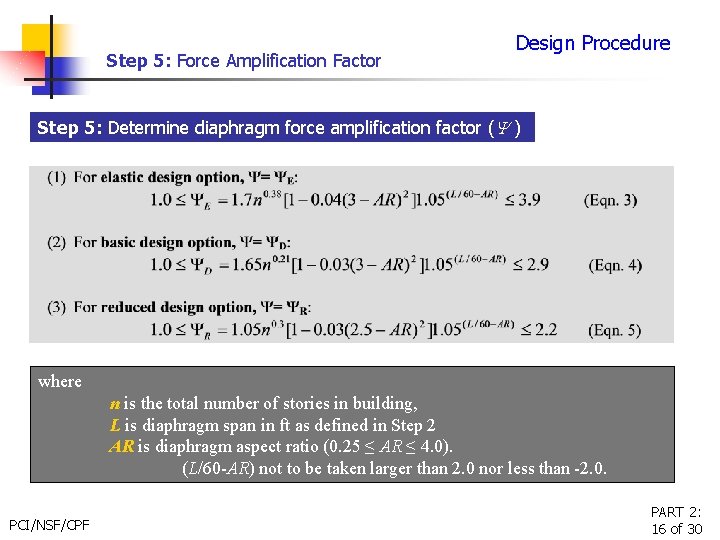
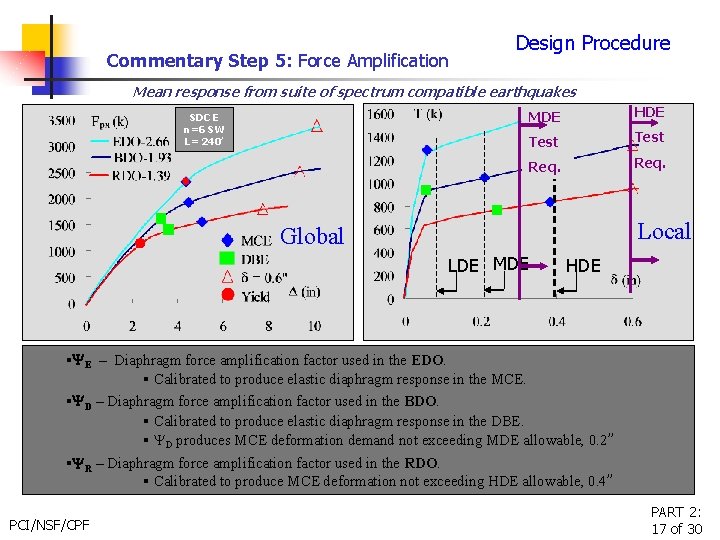
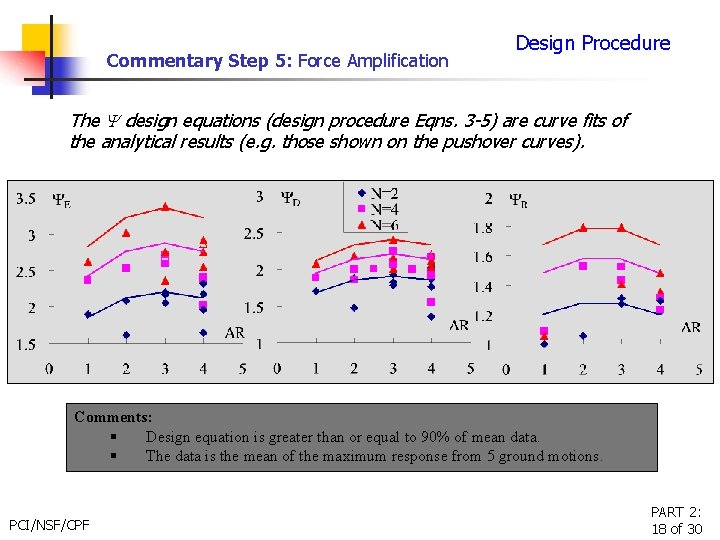
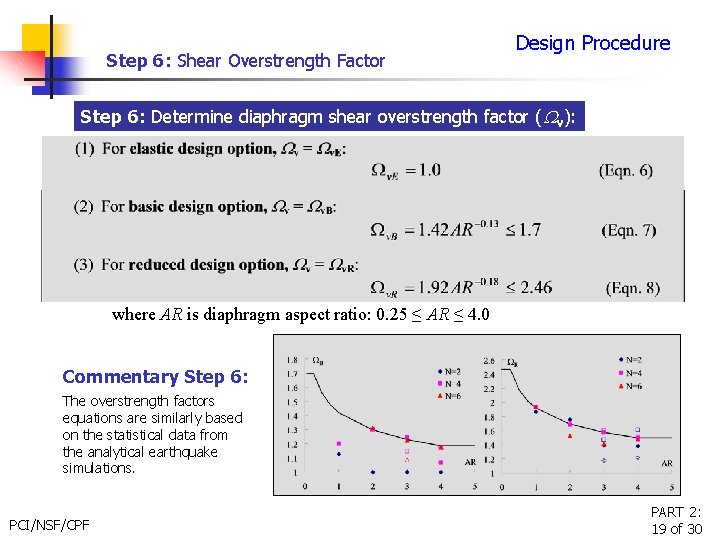
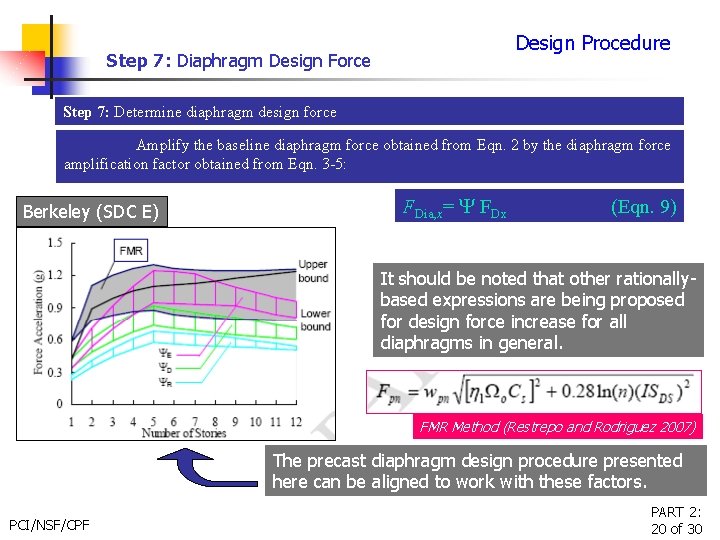
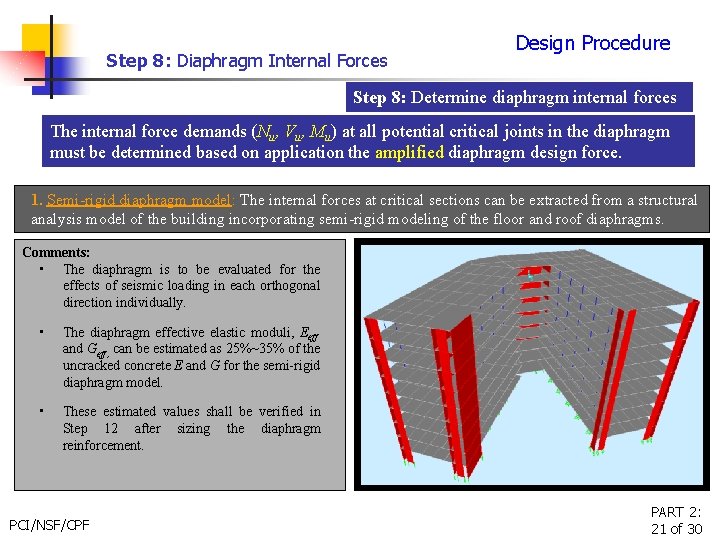
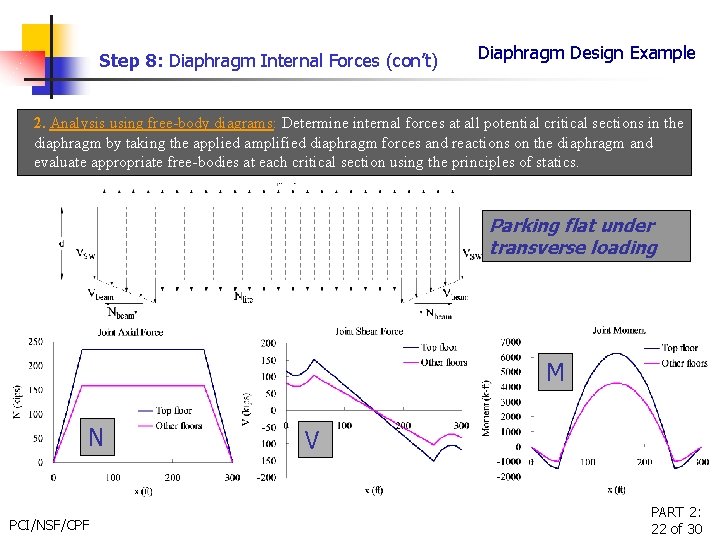
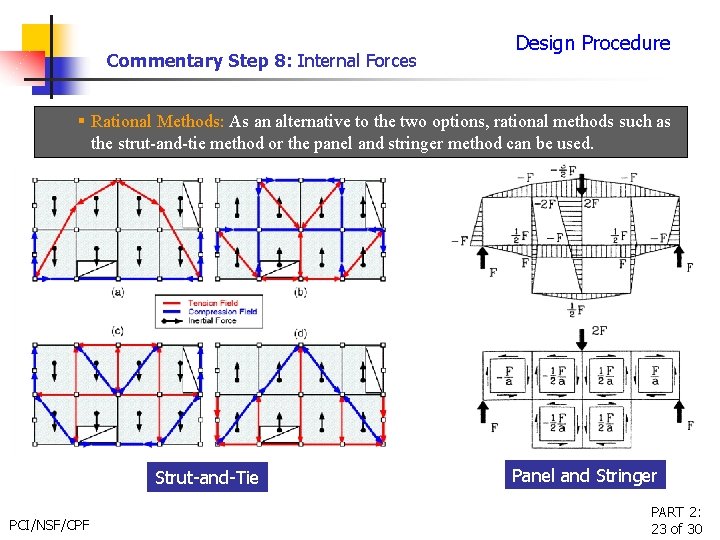
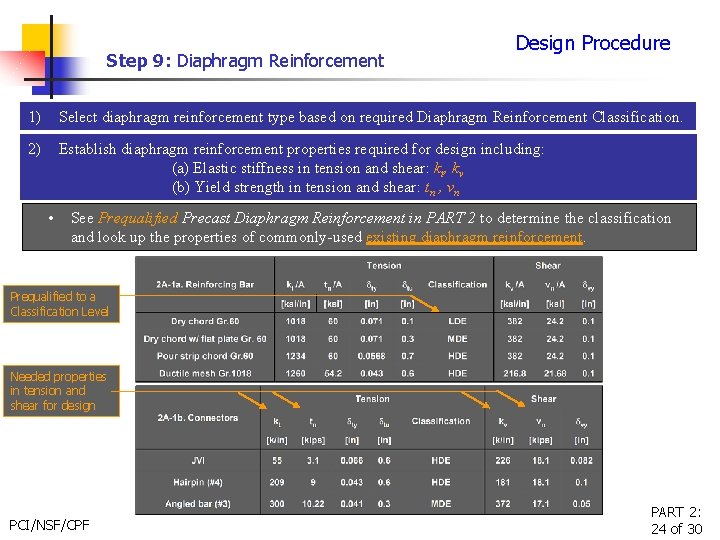
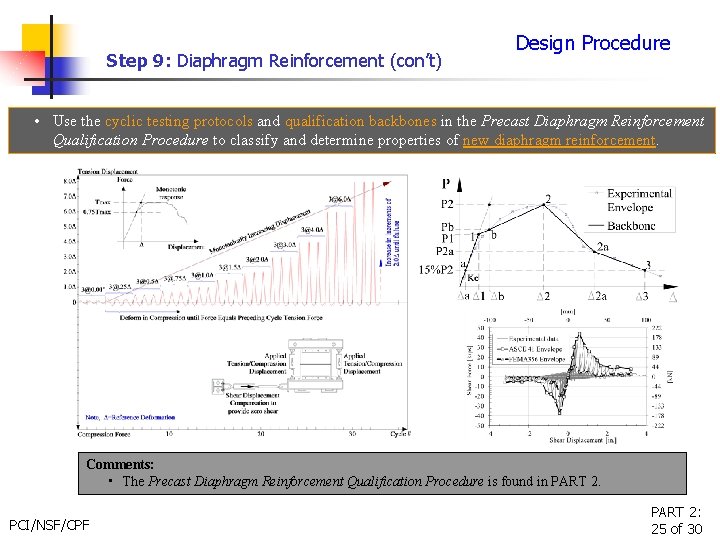
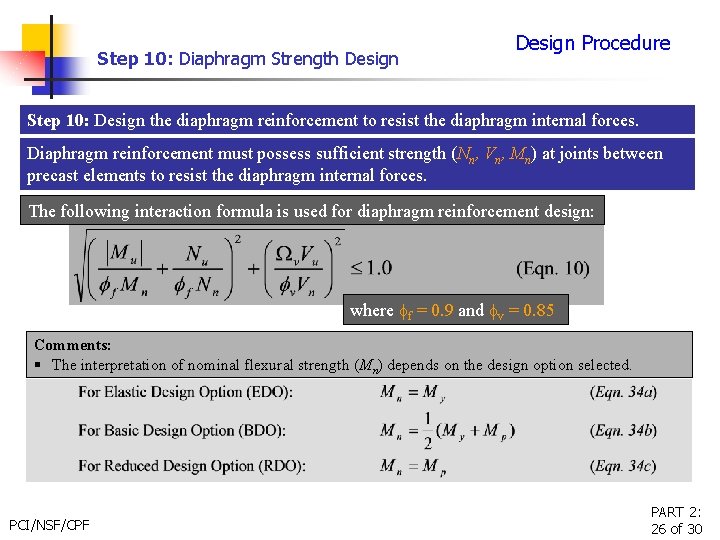
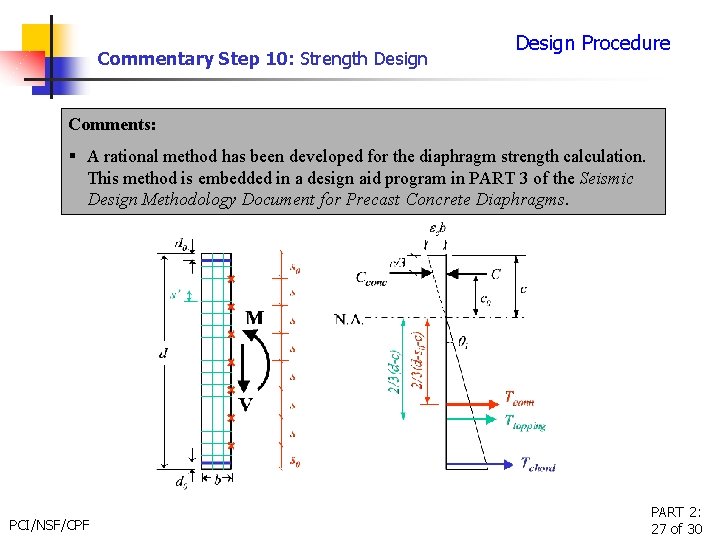
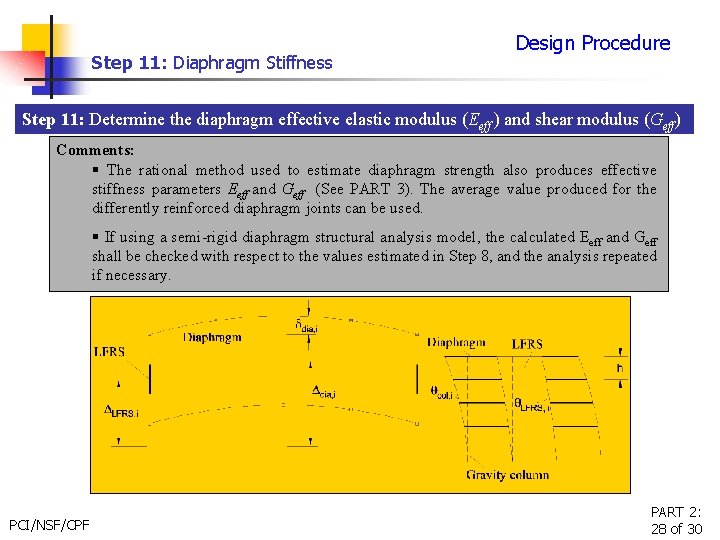
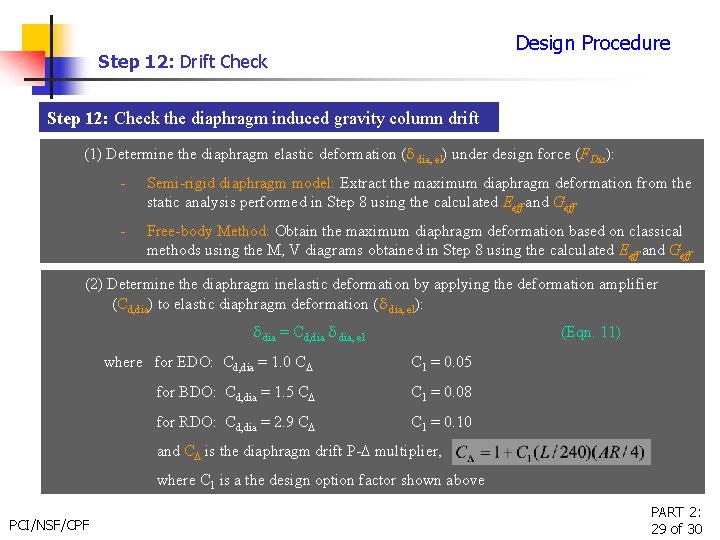
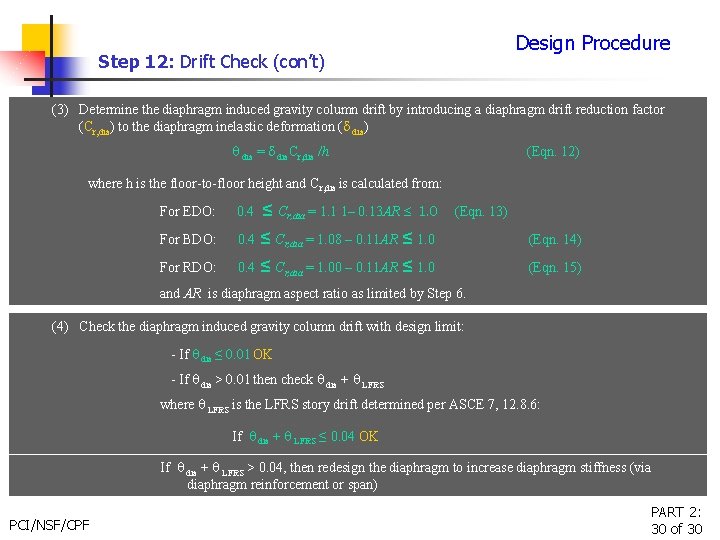
- Slides: 30
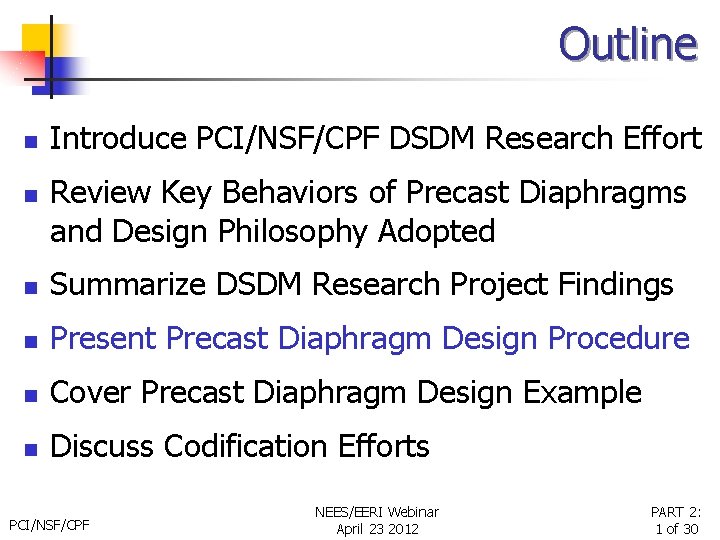
Outline n n Introduce PCI/NSF/CPF DSDM Research Effort Review Key Behaviors of Precast Diaphragms and Design Philosophy Adopted n Summarize DSDM Research Project Findings n Present Precast Diaphragm Design Procedure n Cover Precast Diaphragm Design Example n Discuss Codification Efforts PCI/NSF/CPF NEES/EERI Webinar April 23 2012 PART 2: 1 of 30
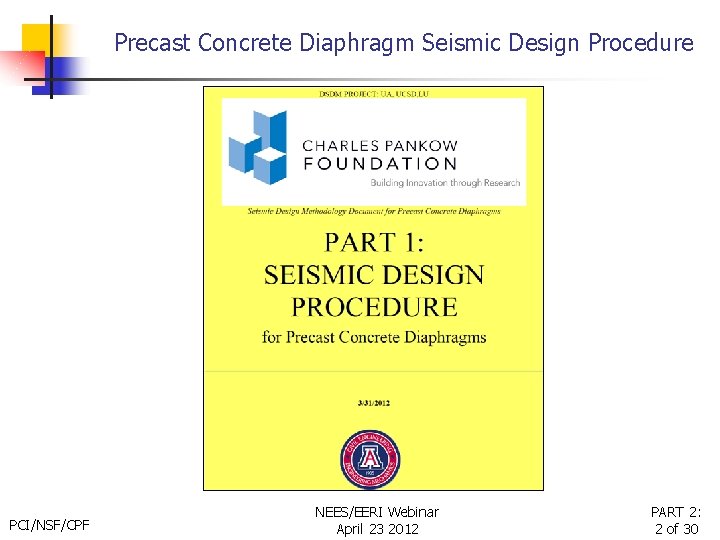
Precast Concrete Diaphragm Seismic Design Procedure PCI/NSF/CPF NEES/EERI Webinar April 23 2012 PART 2: 2 of 30
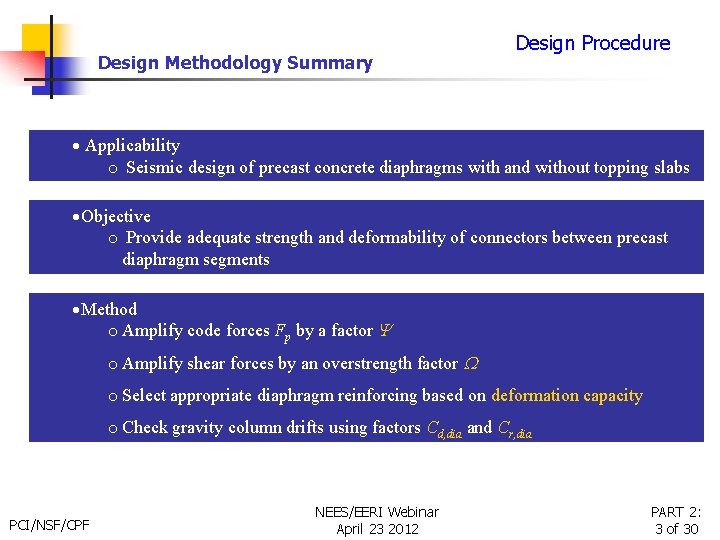
Design Methodology Summary Design Procedure · Applicability o Seismic design of precast concrete diaphragms with and without topping slabs ·Objective o Provide adequate strength and deformability of connectors between precast diaphragm segments ·Method o Amplify code forces Fp by a factor Y o Amplify shear forces by an overstrength factor W o Select appropriate diaphragm reinforcing based on deformation capacity o Check gravity column drifts using factors Cd, dia and Cr, dia PCI/NSF/CPF NEES/EERI Webinar April 23 2012 PART 2: 3 of 30
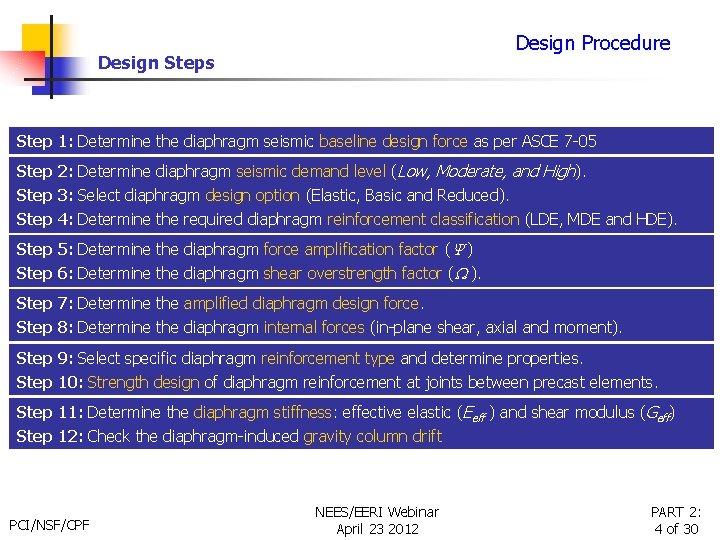
Design Procedure Design Steps Step 1: Determine the diaphragm seismic baseline design force as per ASCE 7 -05 Step 2: Determine diaphragm seismic demand level (Low, Moderate, and High). Step 3: Select diaphragm design option (Elastic, Basic and Reduced). Step 4: Determine the required diaphragm reinforcement classification (LDE, MDE and HDE). Step 5: Determine the diaphragm force amplification factor (Y ) Step 6: Determine the diaphragm shear overstrength factor (W ). Step 7: Determine the amplified diaphragm design force. Step 8: Determine the diaphragm internal forces (in-plane shear, axial and moment). Step 9: Select specific diaphragm reinforcement type and determine properties. Step 10: Strength design of diaphragm reinforcement at joints between precast elements. Step 11: Determine the diaphragm stiffness: effective elastic (Eeff ) and shear modulus (Geff) Step 12: Check the diaphragm-induced gravity column drift PCI/NSF/CPF NEES/EERI Webinar April 23 2012 PART 2: 4 of 30
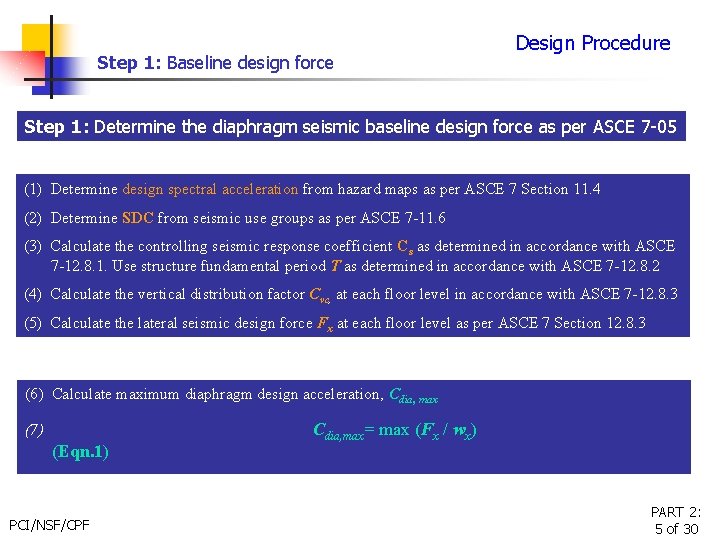
Step 1: Baseline design force Design Procedure Step 1: Determine the diaphragm seismic baseline design force as per ASCE 7 -05 (1) Determine design spectral acceleration from hazard maps as per ASCE 7 Section 11. 4 (2) Determine SDC from seismic use groups as per ASCE 7 -11. 6 (3) Calculate the controlling seismic response coefficient Cs as determined in accordance with ASCE 7 -12. 8. 1. Use structure fundamental period T as determined in accordance with ASCE 7 -12. 8. 2 (4) Calculate the vertical distribution factor Cvc, at each floor level in accordance with ASCE 7 -12. 8. 3 (5) Calculate the lateral seismic design force Fx at each floor level as per ASCE 7 Section 12. 8. 3 (6) Calculate maximum diaphragm design acceleration, Cdia, max (7) (Eqn. 1) PCI/NSF/CPF Cdia, max= max (Fx / wx) PART 2: 5 of 30
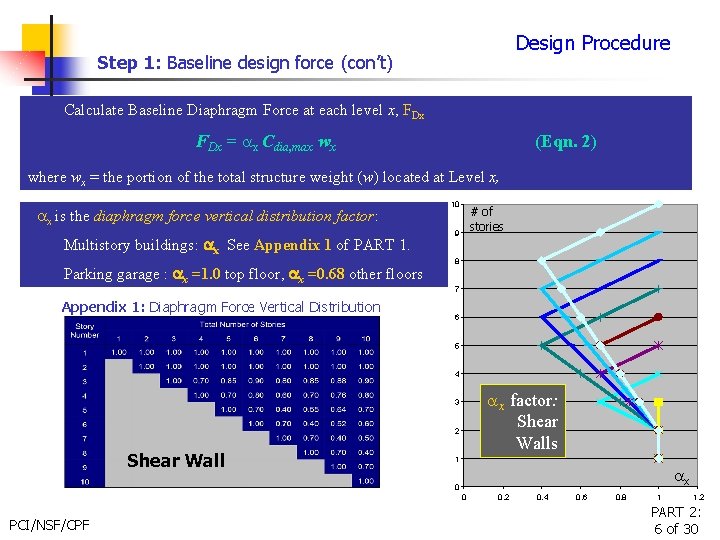
Design Procedure Step 1: Baseline design force (con’t) Calculate Baseline Diaphragm Force at each level x, FDx = ax Cdia, max wx (Eqn. 2) where wx = the portion of the total structure weight (w) located at Level x, ax is the diaphragm force vertical distribution factor: Multistory buildings: ax See Appendix 1 of PART 1. Parking garage : ax =1. 0 top floor, ax =0. 68 other floors Appendix 1: Diaphragm Force Vertical Distribution 10 # of stories 9 8 7 Shear Wall 6 5 4 ax factor: Shear Walls 3 2 Shear Wall 1 ax 0 0 PCI/NSF/CPF 0. 2 0. 4 0. 6 0. 8 1 1. 2 PART 2: 6 of 30
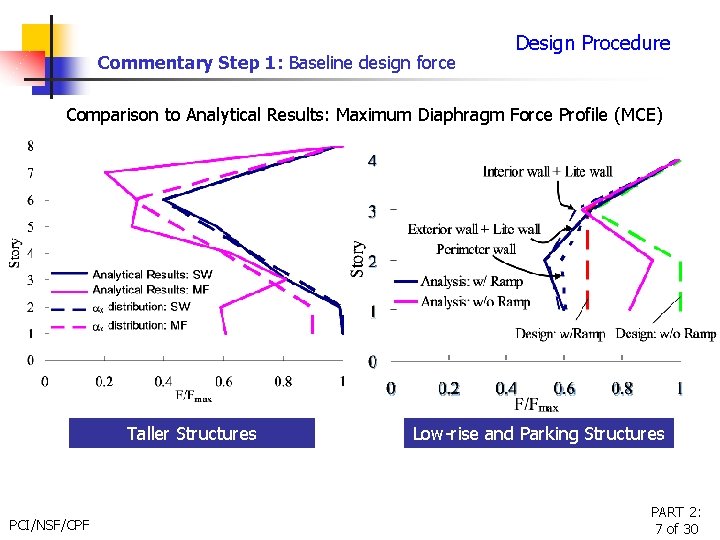
Commentary Step 1: Baseline design force Design Procedure Comparison to Analytical Results: Maximum Diaphragm Force Profile (MCE) Taller Structures PCI/NSF/CPF Low-rise and Parking Structures PART 2: 7 of 30
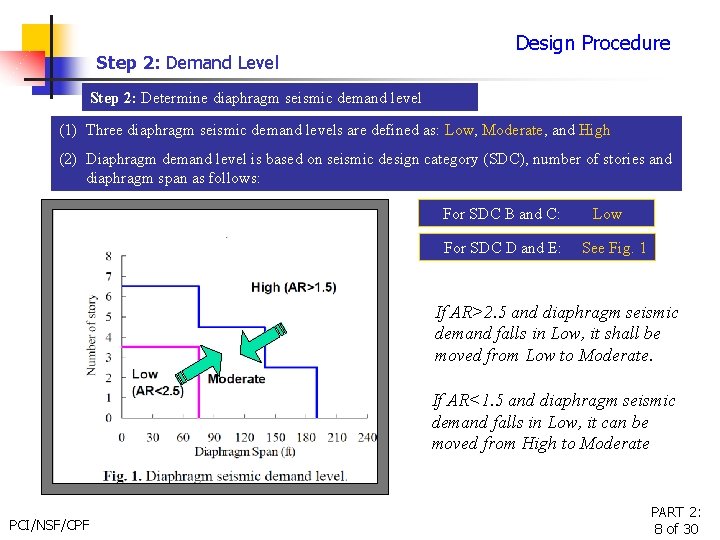
Step 2: Demand Level Design Procedure Step 2: Determine diaphragm seismic demand level (1) Three diaphragm seismic demand levels are defined as: Low, Moderate, and High (2) Diaphragm demand level is based on seismic design category (SDC), number of stories and diaphragm span as follows: For SDC B and C: For SDC D and E: Low See Fig. 1 If AR>2. 5 and diaphragm seismic demand falls in Low, it shall be moved from Low to Moderate. If AR<1. 5 and diaphragm seismic demand falls in Low, it can be moved from High to Moderate PCI/NSF/CPF PART 2: 8 of 30
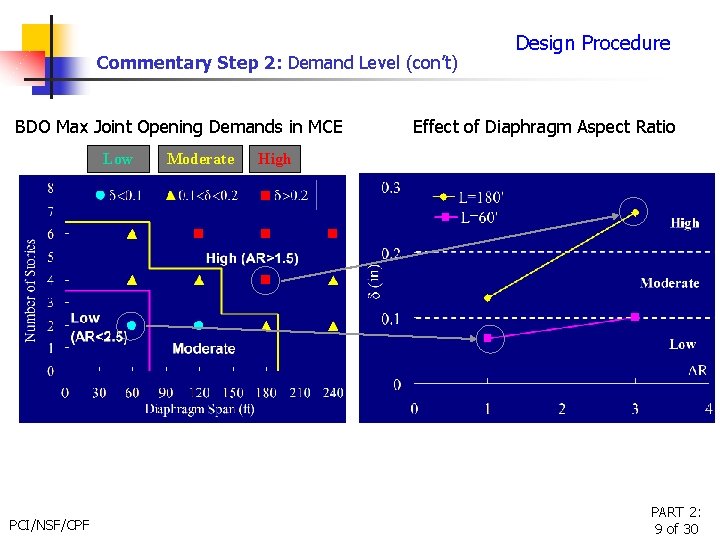
Commentary Step 2: Demand Level (con’t) BDO Max Joint Opening Demands in MCE Low PCI/NSF/CPF Moderate Design Procedure Effect of Diaphragm Aspect Ratio High PART 2: 9 of 30
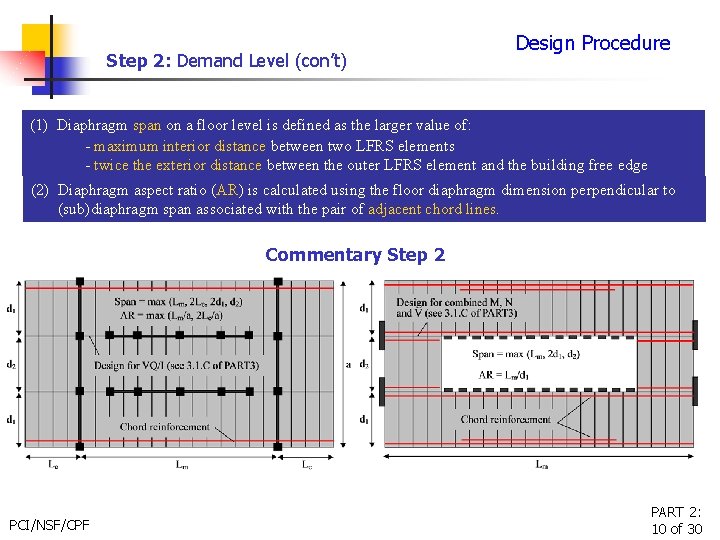
Step 2: Demand Level (con’t) Design Procedure (1) Diaphragm span on a floor level is defined as the larger value of: - maximum interior distance between two LFRS elements - twice the exterior distance between the outer LFRS element and the building free edge (2) Diaphragm aspect ratio (AR) is calculated using the floor diaphragm dimension perpendicular to (sub)diaphragm span associated with the pair of adjacent chord lines. Commentary Step 2 PCI/NSF/CPF PART 2: 10 of 30
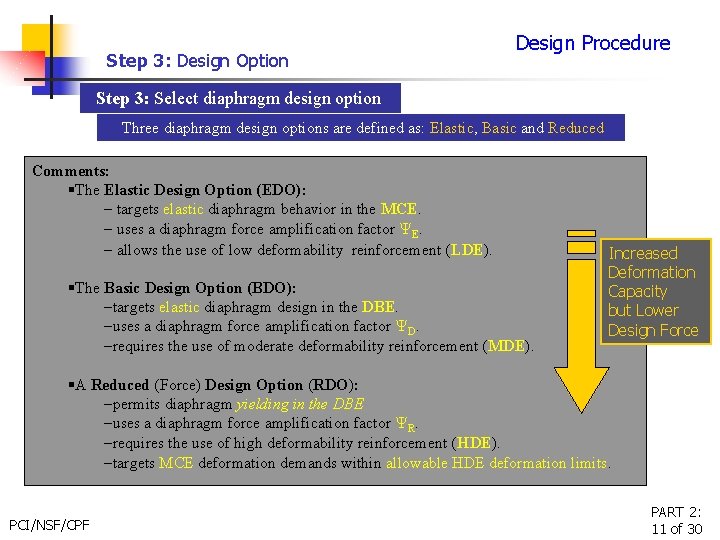
Step 3: Design Option Design Procedure Step 3: Select diaphragm design option Three diaphragm design options are defined as: Elastic, Basic and Reduced Comments: §The Elastic Design Option (EDO): - targets elastic diaphragm behavior in the MCE. - uses a diaphragm force amplification factor YE. - allows the use of low deformability reinforcement (LDE). §The Basic Design Option (BDO): -targets elastic diaphragm design in the DBE. -uses a diaphragm force amplification factor YD. -requires the use of moderate deformability reinforcement (MDE). Increased Deformation Capacity but Lower Design Force §A Reduced (Force) Design Option (RDO): -permits diaphragm yielding in the DBE -uses a diaphragm force amplification factor YR. -requires the use of high deformability reinforcement (HDE). -targets MCE deformation demands within allowable HDE deformation limits. PCI/NSF/CPF PART 2: 11 of 30
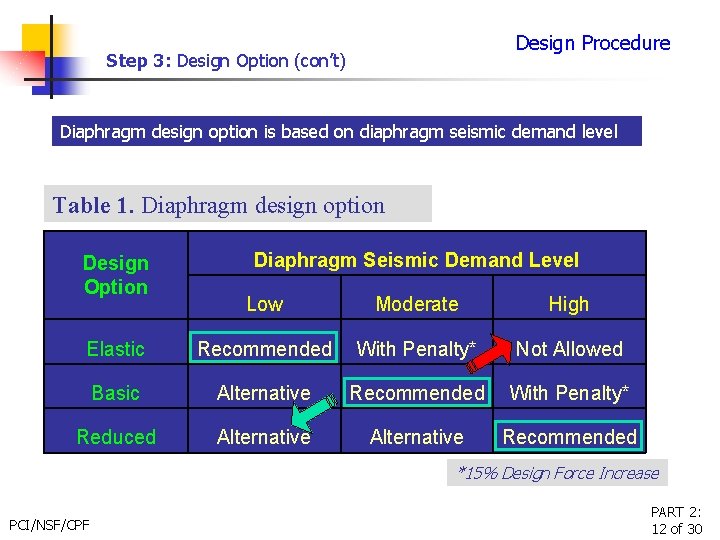
Design Procedure Step 3: Design Option (con’t) Diaphragm design option is based on diaphragm seismic demand level Table 1. Diaphragm design option Design Option Diaphragm Seismic Demand Level Low Moderate High Elastic Recommended With Penalty* Not Allowed Basic Alternative Recommended With Penalty* Reduced Alternative Recommended *15% Design Force Increase PCI/NSF/CPF PART 2: 12 of 30
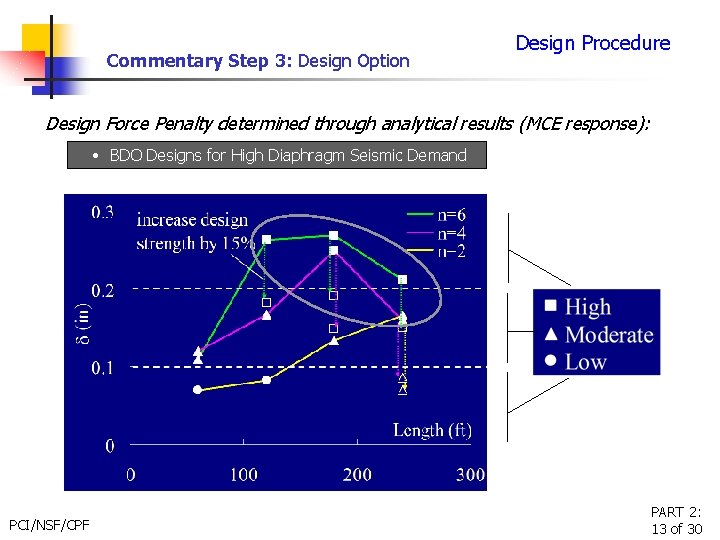
Commentary Step 3: Design Option Design Procedure Design Force Penalty determined through analytical results (MCE response): • BDO Designs for High Diaphragm Seismic Demand PCI/NSF/CPF PART 2: 13 of 30
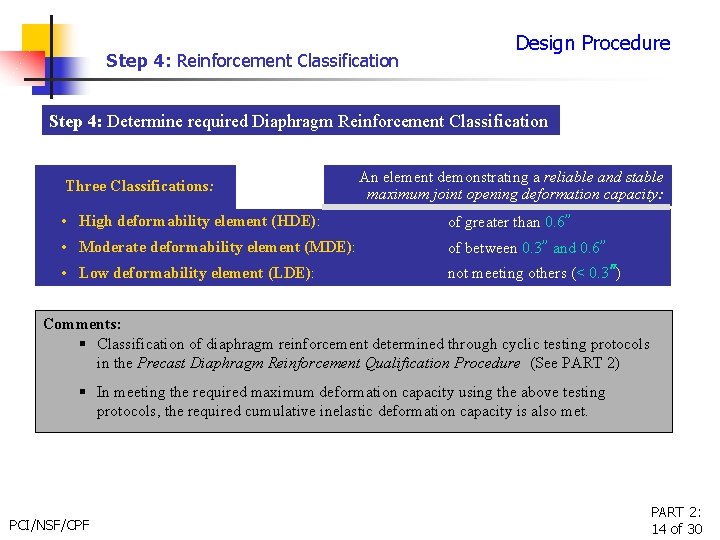
Step 4: Reinforcement Classification Design Procedure Step 4: Determine required Diaphragm Reinforcement Classification Three Classifications: An element demonstrating a reliable and stable maximum joint opening deformation capacity: • High deformability element (HDE): of greater than 0. 6” • Moderate deformability element (MDE): of between 0. 3” and 0. 6” • Low deformability element (LDE): not meeting others (< 0. 3”) Comments: § Classification of diaphragm reinforcement determined through cyclic testing protocols in the Precast Diaphragm Reinforcement Qualification Procedure (See PART 2) § In meeting the required maximum deformation capacity using the above testing protocols, the required cumulative inelastic deformation capacity is also met. PCI/NSF/CPF PART 2: 14 of 30
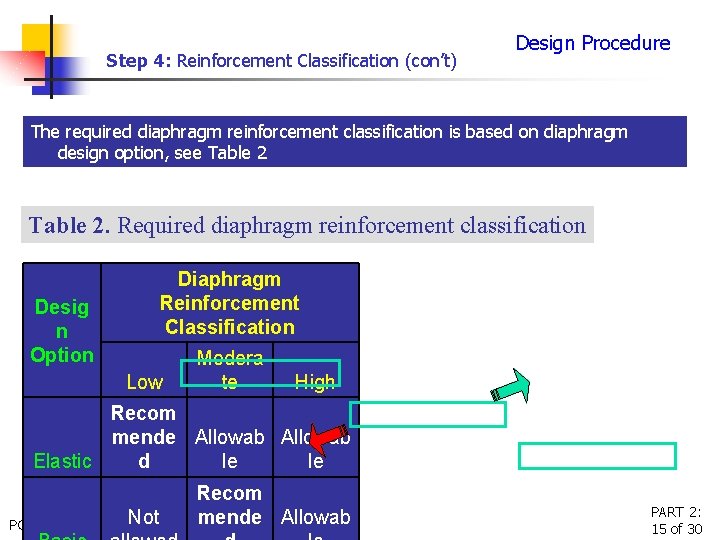
Step 4: Reinforcement Classification (con’t) Design Procedure The required diaphragm reinforcement classification is based on diaphragm design option, see Table 2. Required diaphragm reinforcement classification Diaphragm Reinforcement Classification Desig n Option Low Modera te High Recom mende Allowab Elastic d le le PCI/NSF/CPF Not Recom mende Allowab PART 2: 15 of 30
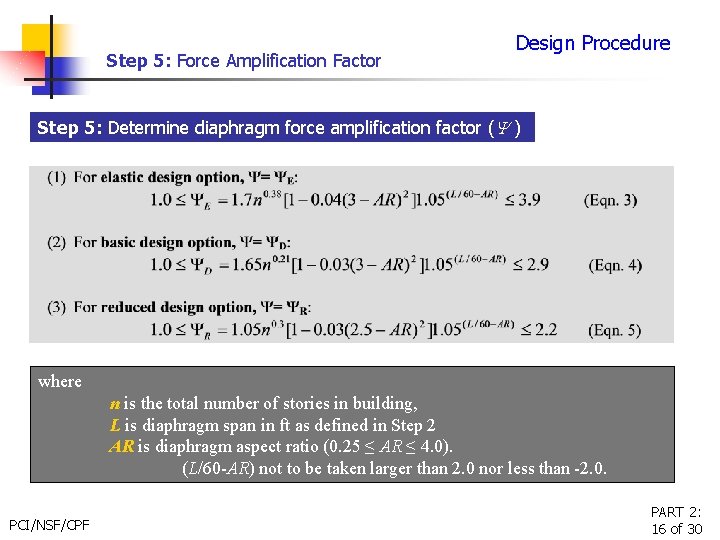
Step 5: Force Amplification Factor Design Procedure Step 5: Determine diaphragm force amplification factor (Y ) where n is the total number of stories in building, L is diaphragm span in ft as defined in Step 2 AR is diaphragm aspect ratio (0. 25 ≤ AR ≤ 4. 0). (L/60 -AR) not to be taken larger than 2. 0 nor less than -2. 0. PCI/NSF/CPF PART 2: 16 of 30
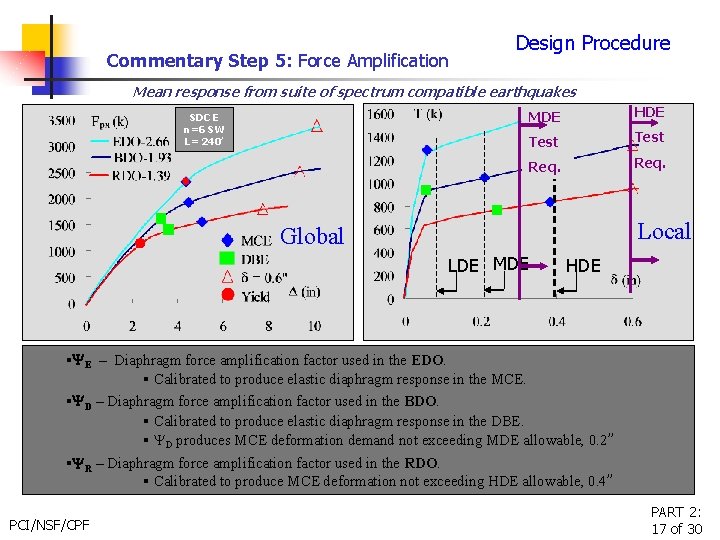
Commentary Step 5: Force Amplification Design Procedure Mean response from suite of spectrum compatible earthquakes SDC E n=6 SW L= 240’ MDE HDE Test Req. Local Global LDE MDE HDE §YE – Diaphragm force amplification factor used in the EDO. § Calibrated to produce elastic diaphragm response in the MCE. §YD – Diaphragm force amplification factor used in the BDO. § Calibrated to produce elastic diaphragm response in the DBE. § YD produces MCE deformation demand not exceeding MDE allowable, 0. 2” §YR – Diaphragm force amplification factor used in the RDO. § Calibrated to produce MCE deformation not exceeding HDE allowable, 0. 4” PCI/NSF/CPF PART 2: 17 of 30
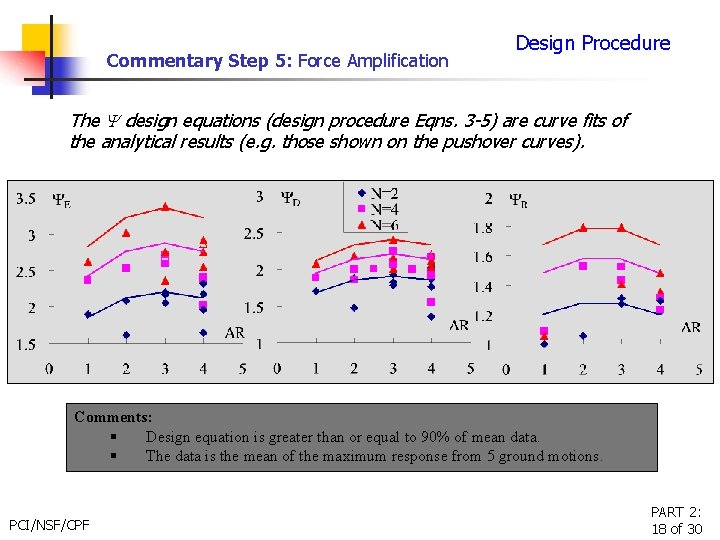
Commentary Step 5: Force Amplification Design Procedure The Y design equations (design procedure Eqns. 3 -5) are curve fits of the analytical results (e. g. those shown on the pushover curves). Comments: § Design equation is greater than or equal to 90% of mean data. § The data is the mean of the maximum response from 5 ground motions. PCI/NSF/CPF PART 2: 18 of 30
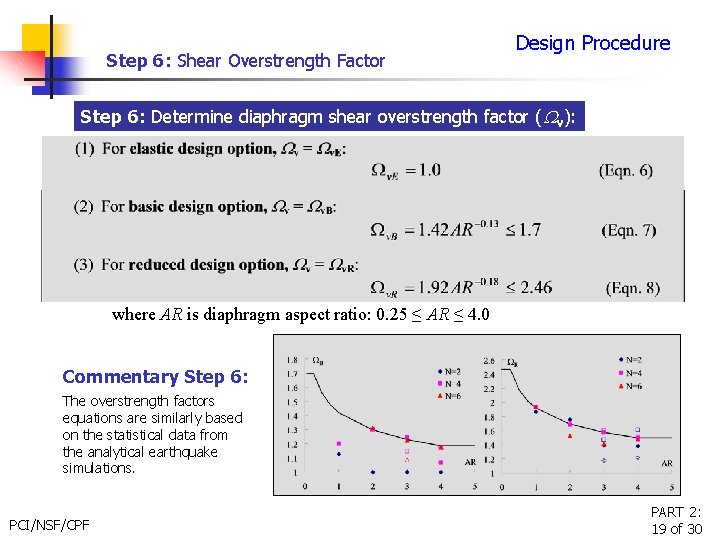
Step 6: Shear Overstrength Factor Design Procedure Step 6: Determine diaphragm shear overstrength factor (Wv): where AR is diaphragm aspect ratio: 0. 25 ≤ AR ≤ 4. 0 Commentary Step 6: The overstrength factors equations are similarly based on the statistical data from the analytical earthquake simulations. PCI/NSF/CPF PART 2: 19 of 30
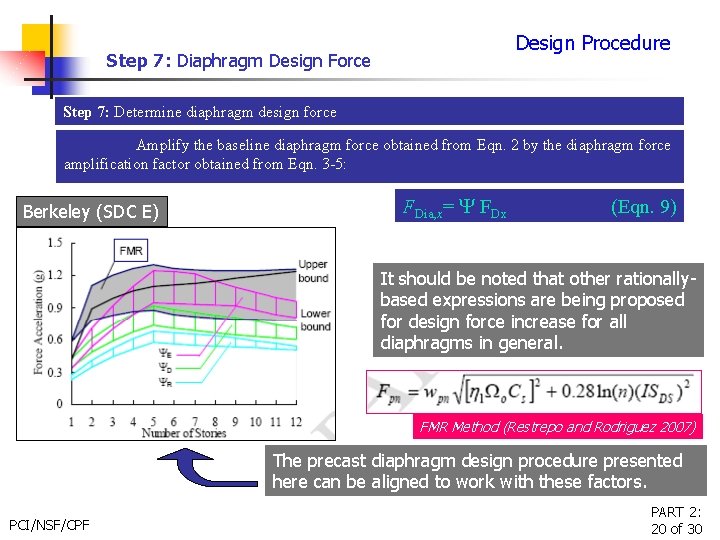
Design Procedure Step 7: Diaphragm Design Force Step 7: Determine diaphragm design force Amplify the baseline diaphragm force obtained from Eqn. 2 by the diaphragm force amplification factor obtained from Eqn. 3 -5: Berkeley (SDC E) FDia, x= Y FDx (Eqn. 9) It should be noted that other rationallybased expressions are being proposed for design force increase for all diaphragms in general. FMR Method (Restrepo and Rodriguez 2007) The precast diaphragm design procedure presented here can be aligned to work with these factors. PCI/NSF/CPF PART 2: 20 of 30
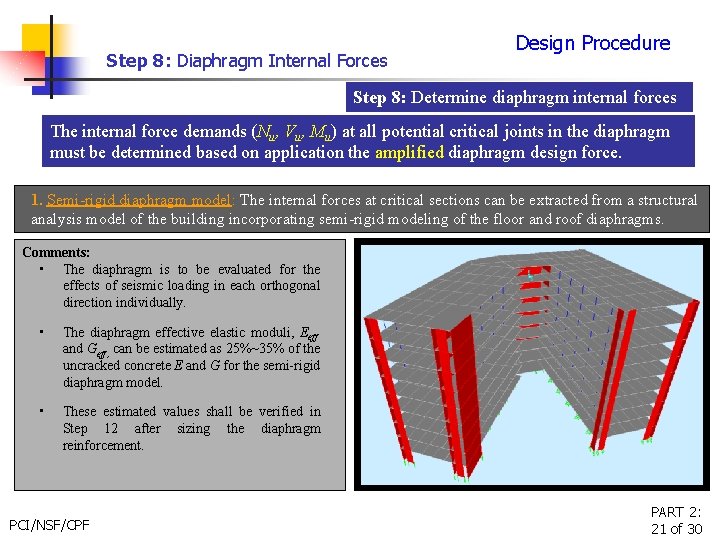
Step 8: Diaphragm Internal Forces Design Procedure Step 8: Determine diaphragm internal forces The internal force demands (Nu, Vu, Mu) at all potential critical joints in the diaphragm must be determined based on application the amplified diaphragm design force. 1. Semi-rigid diaphragm model: The internal forces at critical sections can be extracted from a structural analysis model of the building incorporating semi-rigid modeling of the floor and roof diaphragms. Comments: • The diaphragm is to be evaluated for the effects of seismic loading in each orthogonal direction individually. • The diaphragm effective elastic moduli, Eeff and Geff , can be estimated as 25%~35% of the uncracked concrete E and G for the semi-rigid diaphragm model. • These estimated values shall be verified in Step 12 after sizing the diaphragm reinforcement. PCI/NSF/CPF PART 2: 21 of 30
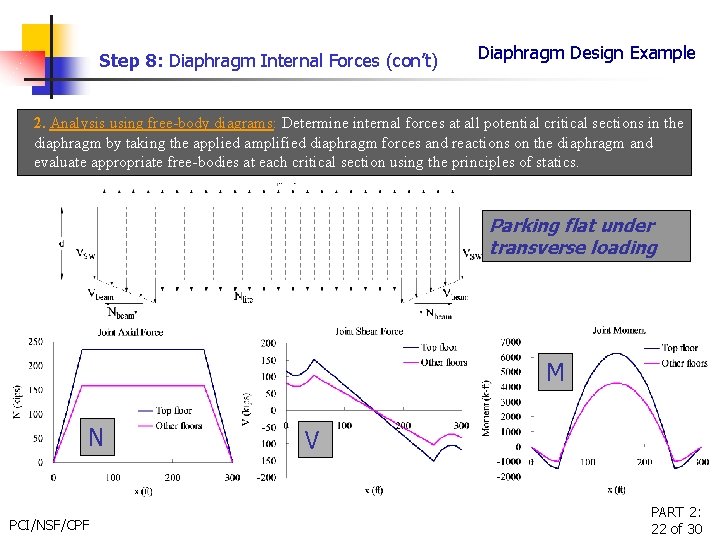
Step 8: Diaphragm Internal Forces (con’t) Diaphragm Design Example 2. Analysis using free-body diagrams: Determine internal forces at all potential critical sections in the diaphragm by taking the applied amplified diaphragm forces and reactions on the diaphragm and evaluate appropriate free-bodies at each critical section using the principles of statics. Parking flat under transverse loading M N PCI/NSF/CPF V PART 2: 22 of 30
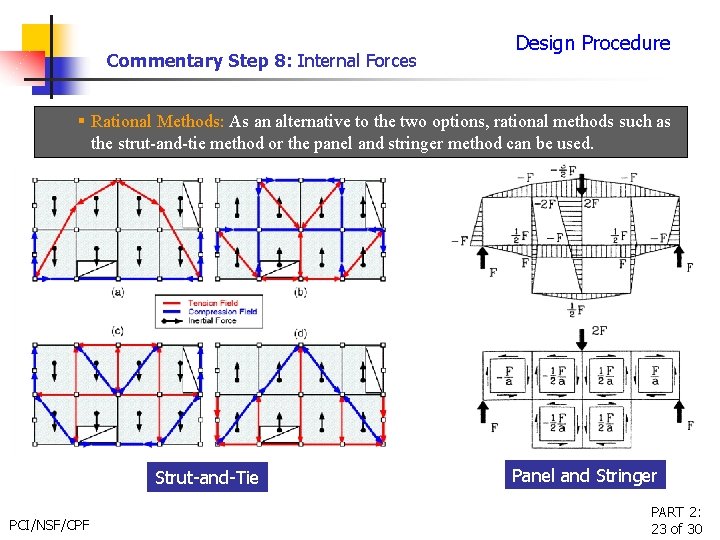
Commentary Step 8: Internal Forces Design Procedure § Rational Methods: As an alternative to the two options, rational methods such as the strut-and-tie method or the panel and stringer method can be used. Strut-and-Tie PCI/NSF/CPF Panel and Stringer PART 2: 23 of 30
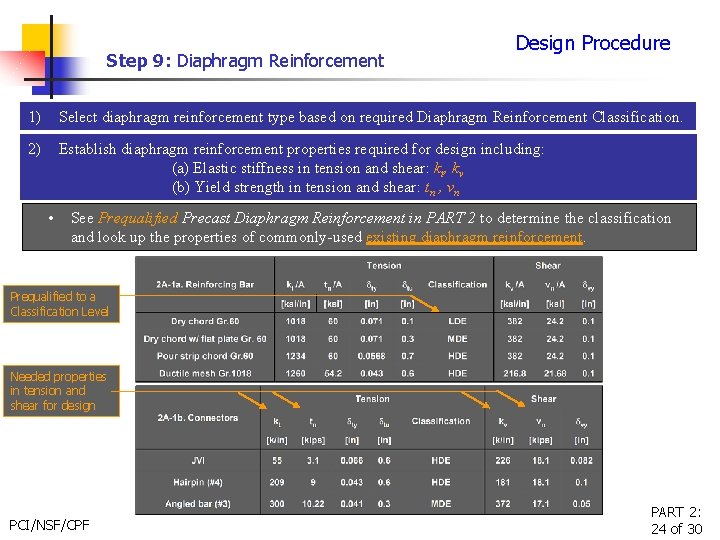
Step 9: Diaphragm Reinforcement Design Procedure 1) Select diaphragm reinforcement type based on required Diaphragm Reinforcement Classification. 2) Establish diaphragm reinforcement properties required for design including: (a) Elastic stiffness in tension and shear: kt, kv (b) Yield strength in tension and shear: tn , vn • See Prequalified Precast Diaphragm Reinforcement in PART 2 to determine the classification and look up the properties of commonly-used existing diaphragm reinforcement. Prequalified to a Classification Level Needed properties in tension and shear for design PCI/NSF/CPF PART 2: 24 of 30
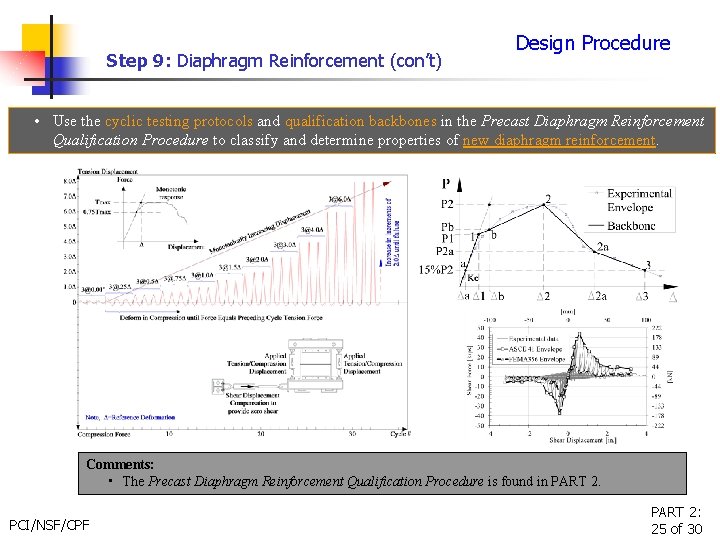
Step 9: Diaphragm Reinforcement (con’t) Design Procedure • Use the cyclic testing protocols and qualification backbones in the Precast Diaphragm Reinforcement Qualification Procedure to classify and determine properties of new diaphragm reinforcement. Comments: • The Precast Diaphragm Reinforcement Qualification Procedure is found in PART 2. PCI/NSF/CPF PART 2: 25 of 30
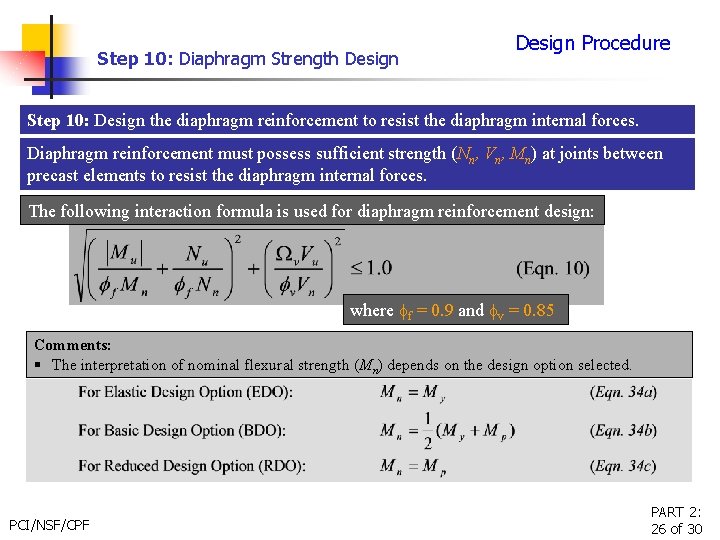
Step 10: Diaphragm Strength Design Procedure Step 10: Design the diaphragm reinforcement to resist the diaphragm internal forces. Diaphragm reinforcement must possess sufficient strength (Nn, Vn, Mn) at joints between precast elements to resist the diaphragm internal forces. The following interaction formula is used for diaphragm reinforcement design: where ff = 0. 9 and fv = 0. 85 Comments: § The interpretation of nominal flexural strength (Mn) depends on the design option selected. PCI/NSF/CPF PART 2: 26 of 30
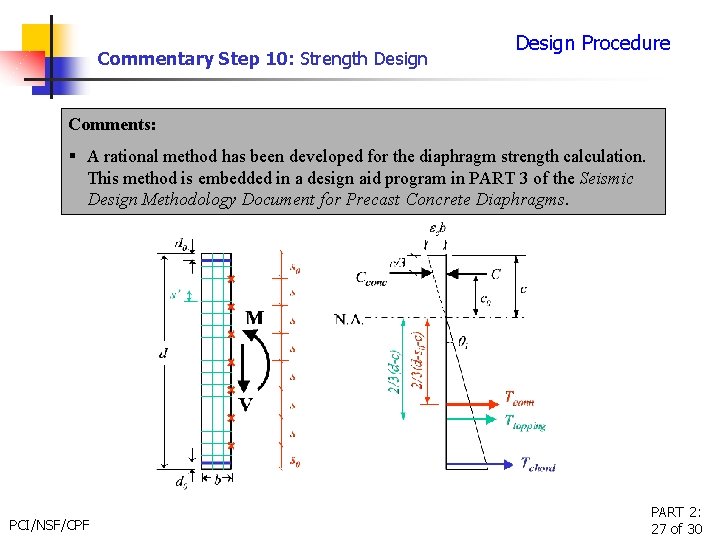
Commentary Step 10: Strength Design Procedure Comments: § A rational method has been developed for the diaphragm strength calculation. This method is embedded in a design aid program in PART 3 of the Seismic Design Methodology Document for Precast Concrete Diaphragms. PCI/NSF/CPF PART 2: 27 of 30
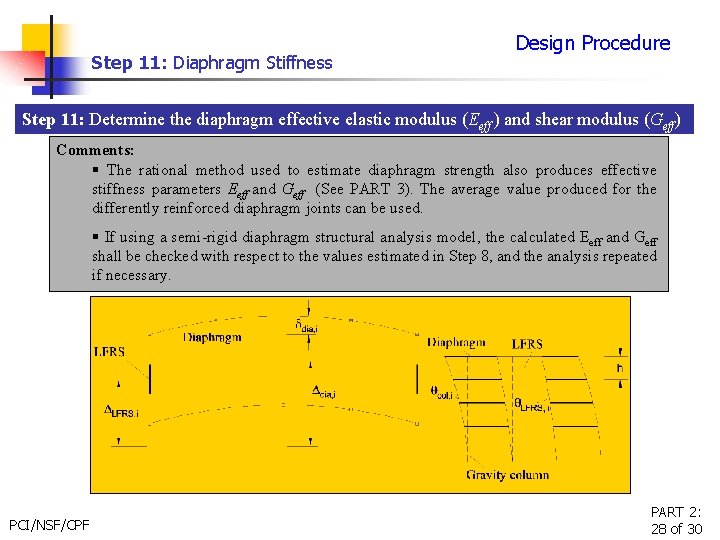
Step 11: Diaphragm Stiffness Design Procedure Step 11: Determine the diaphragm effective elastic modulus (Eeff ) and shear modulus (Geff) Comments: § The rational method used to estimate diaphragm strength also produces effective stiffness parameters Eeff and Geff (See PART 3). The average value produced for the differently reinforced diaphragm joints can be used. § If using a semi-rigid diaphragm structural analysis model, the calculated Eeff and Geff shall be checked with respect to the values estimated in Step 8, and the analysis repeated if necessary. PCI/NSF/CPF PART 2: 28 of 30
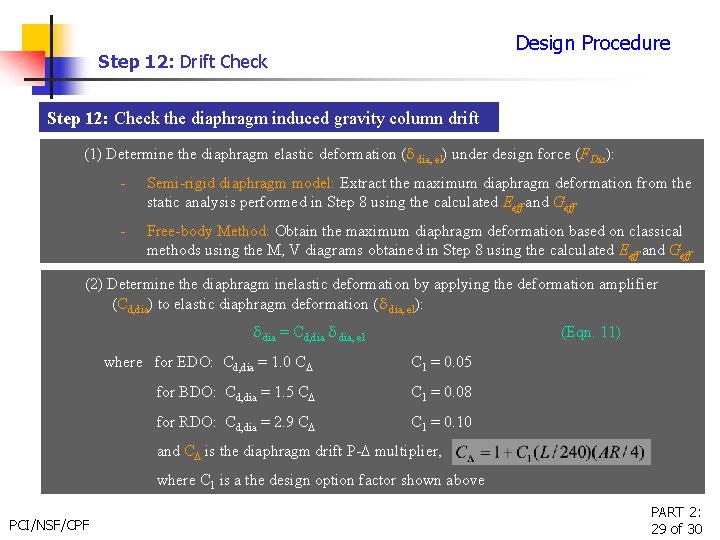
Design Procedure Step 12: Drift Check Step 12: Check the diaphragm induced gravity column drift (1) Determine the diaphragm elastic deformation (d dia, el) under design force (FDia): - Semi-rigid diaphragm model: Extract the maximum diaphragm deformation from the static analysis performed in Step 8 using the calculated Eeff and Geff - Free-body Method: Obtain the maximum diaphragm deformation based on classical methods using the M, V diagrams obtained in Step 8 using the calculated Eeff and Geff (2) Determine the diaphragm inelastic deformation by applying the deformation amplifier (Cd, dia) to elastic diaphragm deformation (d dia, el): d dia = Cd, dia d dia, el (Eqn. 11) where for EDO: Cd, dia = 1. 0 CD C 1 = 0. 05 for BDO: Cd, dia = 1. 5 CD C 1 = 0. 08 for RDO: Cd, dia = 2. 9 CD C 1 = 0. 10 and CD is the diaphragm drift P-D multiplier, where C 1 is a the design option factor shown above PCI/NSF/CPF PART 2: 29 of 30
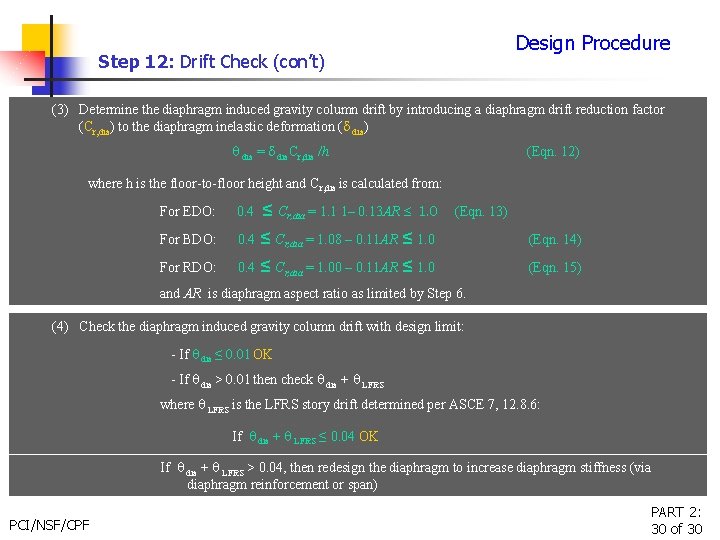
Design Procedure Step 12: Drift Check (con’t) (3) Determine the diaphragm induced gravity column drift by introducing a diaphragm drift reduction factor (Cr, dia) to the diaphragm inelastic deformation (d dia) q dia = d dia. Cr, dia /h (Eqn. 12) where h is the floor-to-floor height and Cr, dia is calculated from: ≤ Cr, dia = 1. 1 1– 0. 13 AR ≤ 1. 0 For EDO: 0. 4 (Eqn. 13) For BDO: 0. 4 ≤ Cr, dia = 1. 08 – 0. 11 AR ≤ 1. 0 (Eqn. 14) For RDO: 0. 4 ≤ Cr, dia = 1. 00 – 0. 11 AR ≤ 1. 0 (Eqn. 15) and AR is diaphragm aspect ratio as limited by Step 6. (4) Check the diaphragm induced gravity column drift with design limit: - If q dia ≤ 0. 01 OK - If q dia > 0. 01 then check q dia + q LFRS where q LFRS is the LFRS story drift determined per ASCE 7, 12. 8. 6: If q dia + q LFRS ≤ 0. 04 OK If q dia + q LFRS > 0. 04, then redesign the diaphragm to increase diaphragm stiffness (via diaphragm reinforcement or span) PCI/NSF/CPF PART 2: 30 of 30
Metodología dsdm
Dsdm structured timebox
Politie cognitieve test vrijstelling
Usdp methodology
Dsdm
Dsdm
Dsdm consortium
Extreme programming agile
Software life cycle
Adaptive sdlc
Dsdm models
Dsdm
Quotation sandwich example
Research paper body paragraph outline
Mla format thesis
Serial killer research project
Outline of presentation
Secara garis besar, laporan penelitian terdiri dari ....
Research question outline
Type of research design
Operational definition of anger
Legal research outline
Research design is a blueprint outline and a plan
Topical outline of quantitative research design
Operational definition psychology examples
Research paper outline example
Analytical paragraph writing
5 sentences about house
Ice quote method
Introducing quotes with signal phrases
Disposition romeo and juliet