Micromechanics Computational Cell Microstructure idealization Modeling idealization Ductile
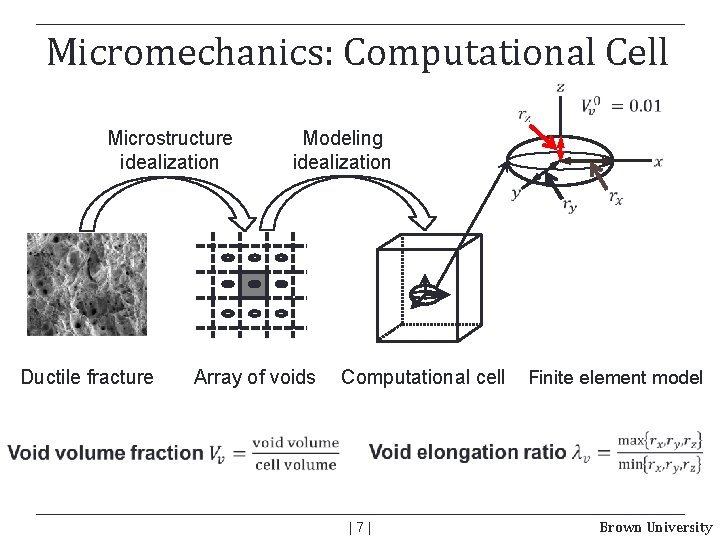
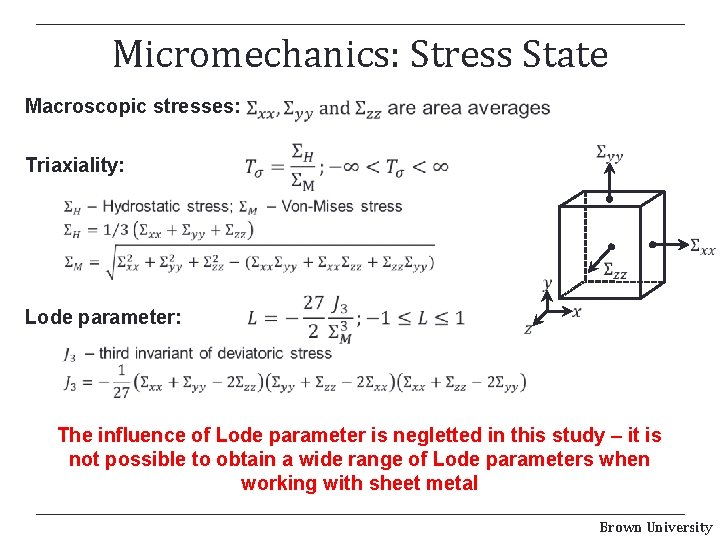
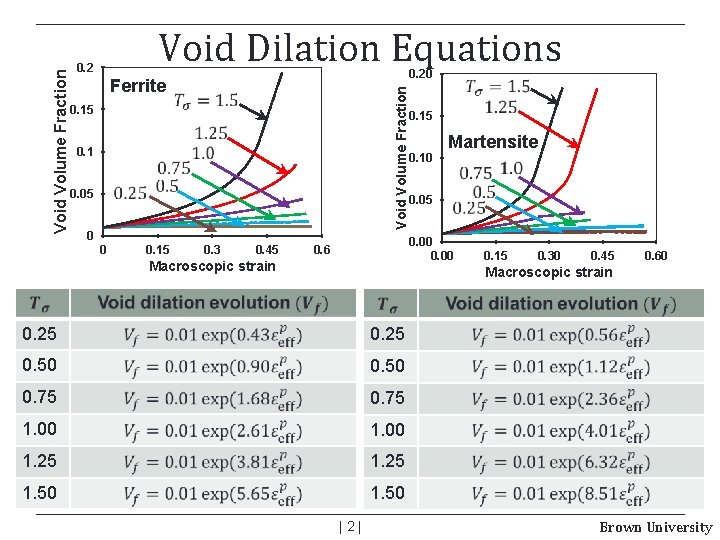
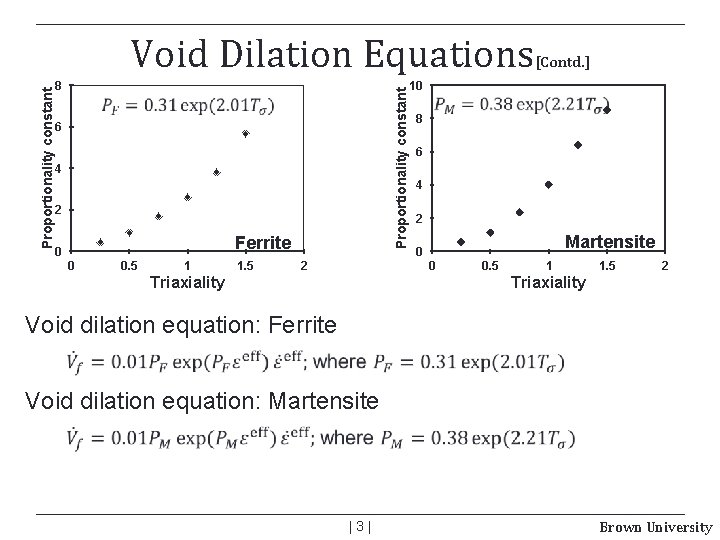
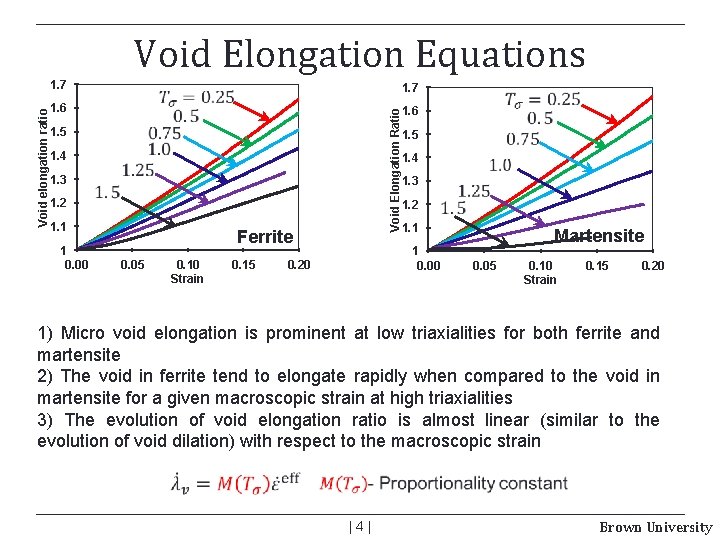
![Void Elongation Equations 4 Proportionality Constant 4 [Contd. ] 3 2 1 Ferrite 0 Void Elongation Equations 4 Proportionality Constant 4 [Contd. ] 3 2 1 Ferrite 0](https://slidetodoc.com/presentation_image_h/0d15b8e392bc062389ed0d73f8877616/image-6.jpg)
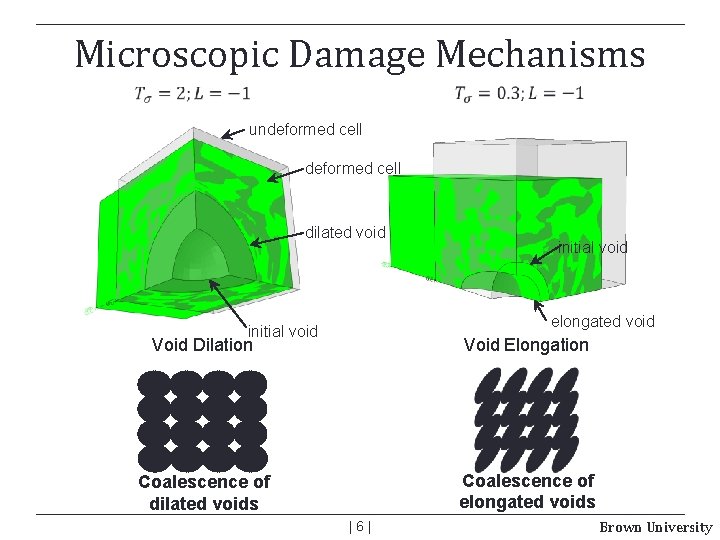
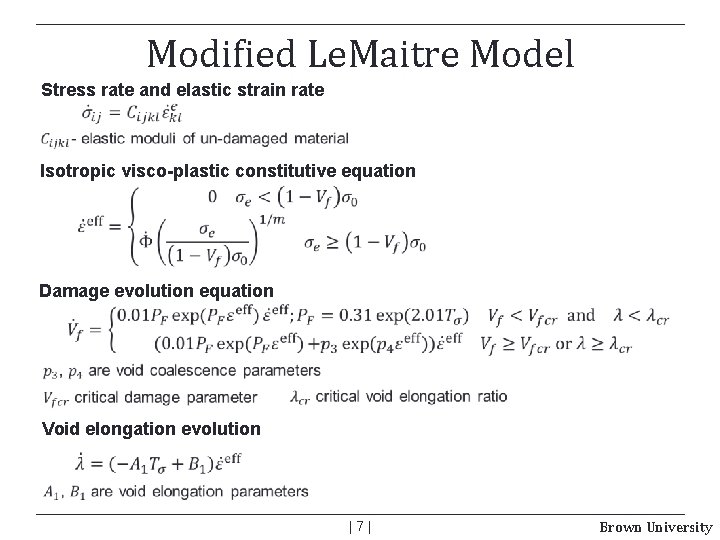
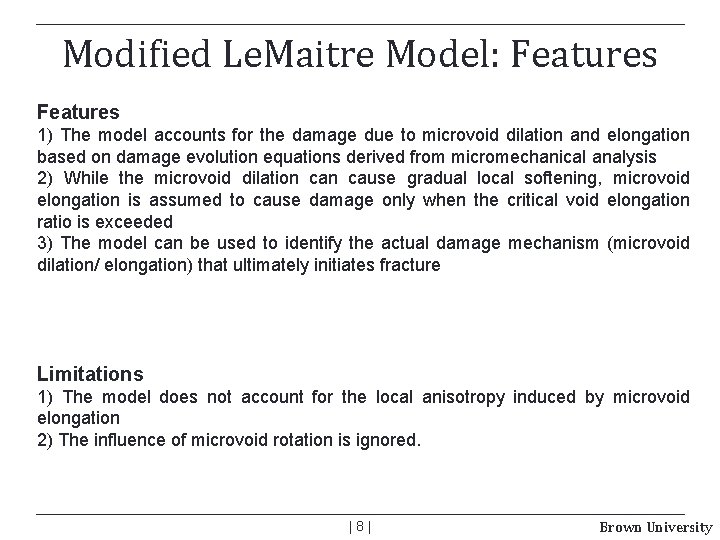
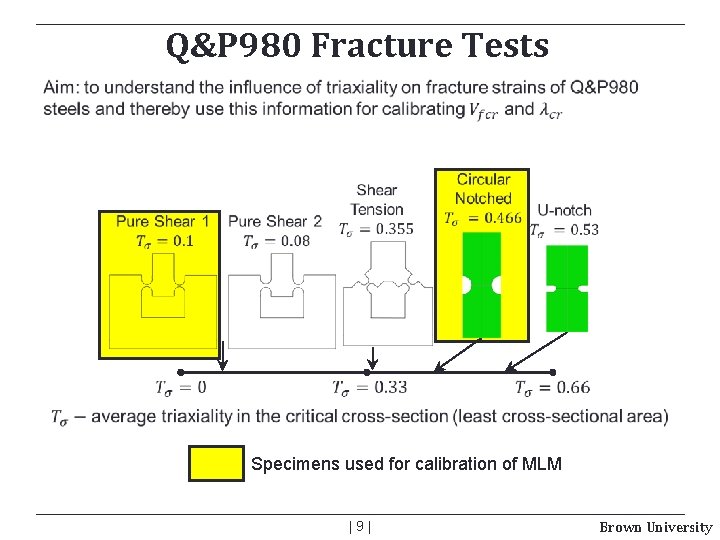
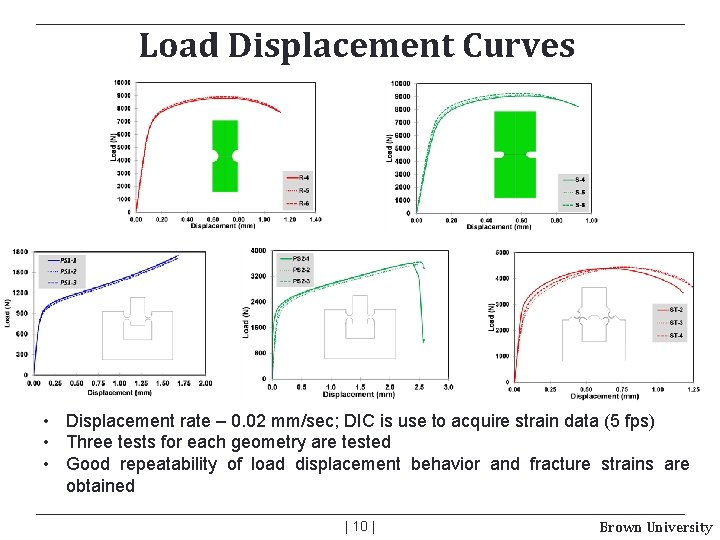
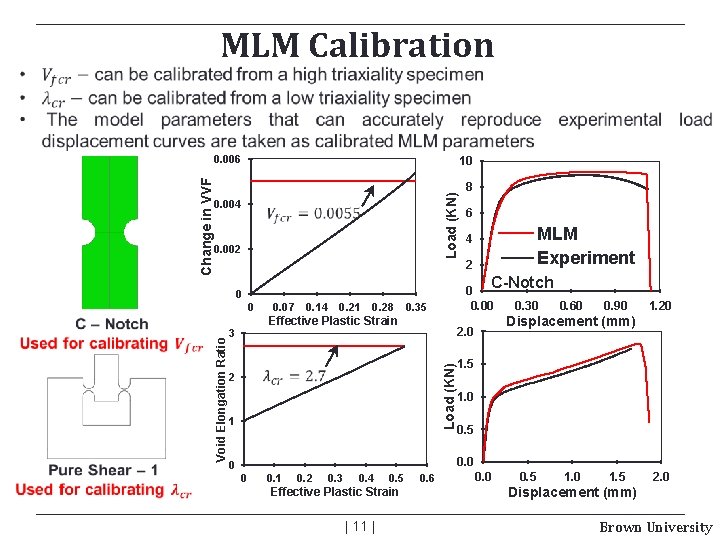
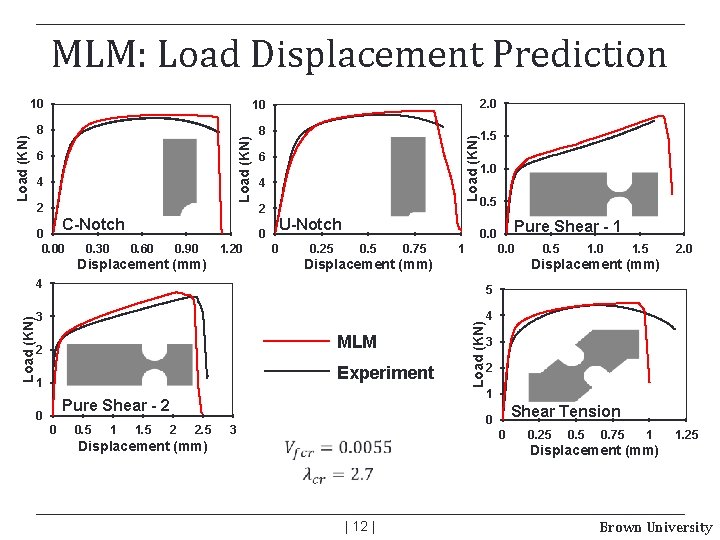
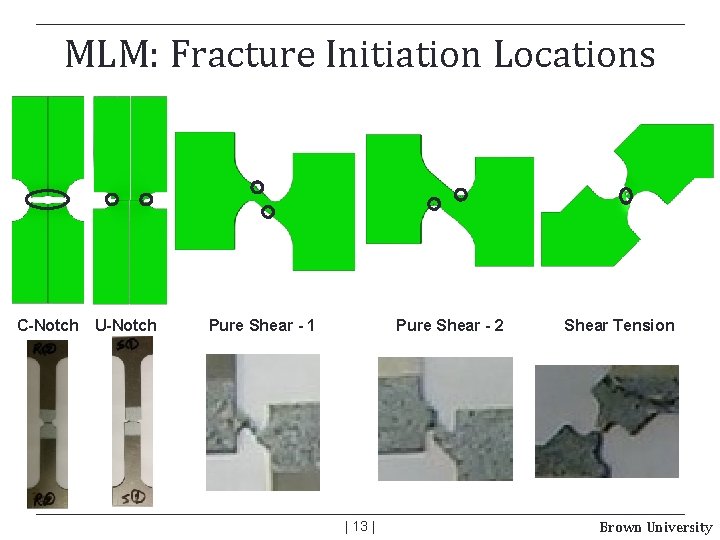
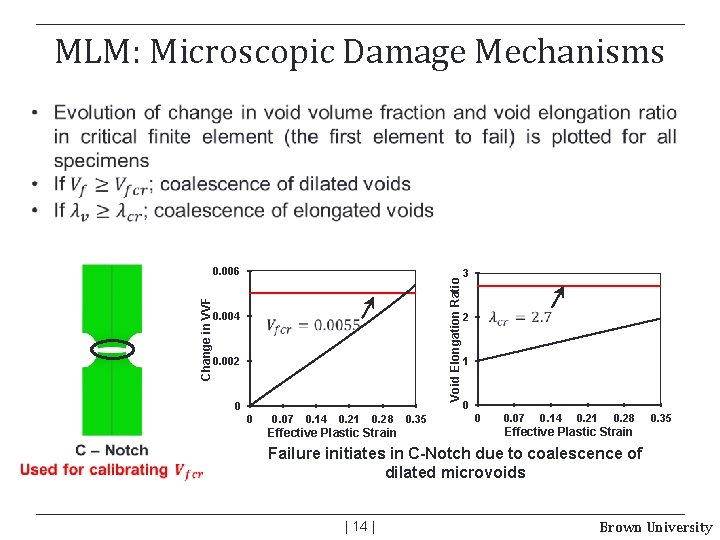
![MLM: Microscopic Damage Mechanisms[Contd. ] Void Elongation Ratio Change in VVF 0. 006 0. MLM: Microscopic Damage Mechanisms[Contd. ] Void Elongation Ratio Change in VVF 0. 006 0.](https://slidetodoc.com/presentation_image_h/0d15b8e392bc062389ed0d73f8877616/image-16.jpg)
![MLM: Microscopic Damage Mechanisms[Contd. ] Void Elongation Ratio Change in VVF 0. 008 0. MLM: Microscopic Damage Mechanisms[Contd. ] Void Elongation Ratio Change in VVF 0. 008 0.](https://slidetodoc.com/presentation_image_h/0d15b8e392bc062389ed0d73f8877616/image-17.jpg)
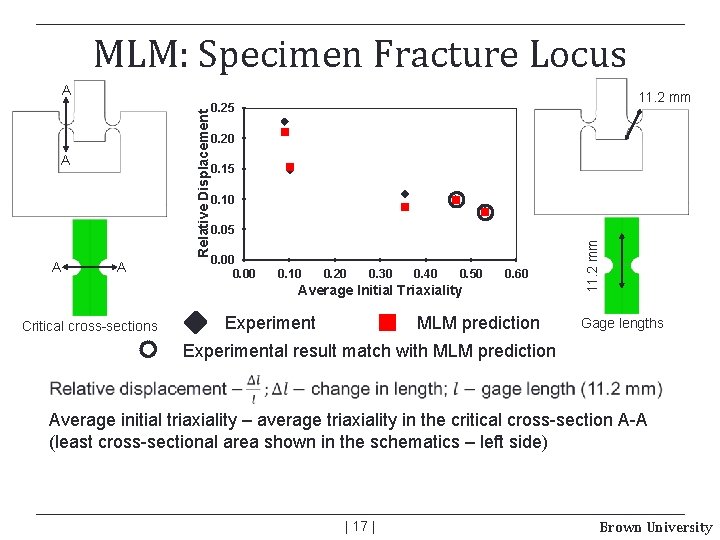
- Slides: 18
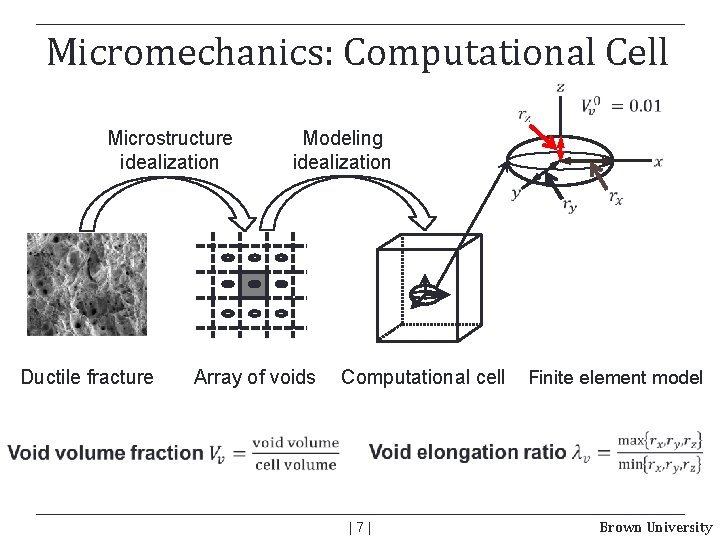
Micromechanics: Computational Cell Microstructure idealization Modeling idealization Ductile fracture Array of voids Computational cell Finite element model | 7 | Brown University
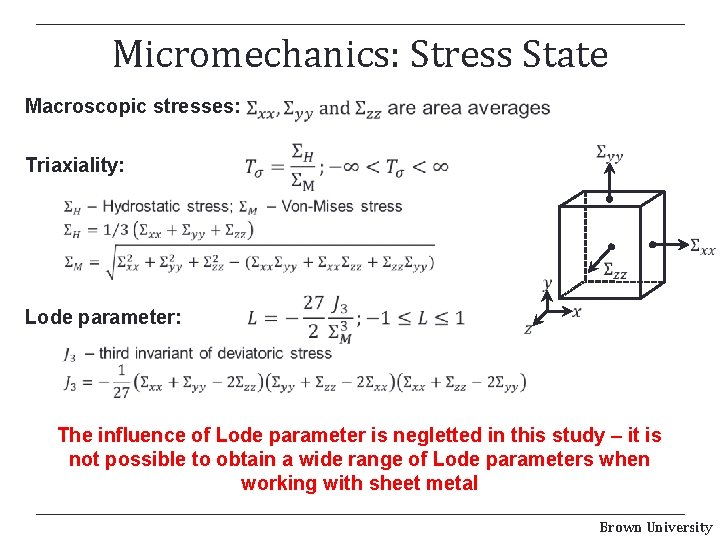
Micromechanics: Stress State Macroscopic stresses: Triaxiality: Lode parameter: The influence of Lode parameter is negletted in this study – it is not possible to obtain a wide range of Lode parameters when working with sheet metal Brown University
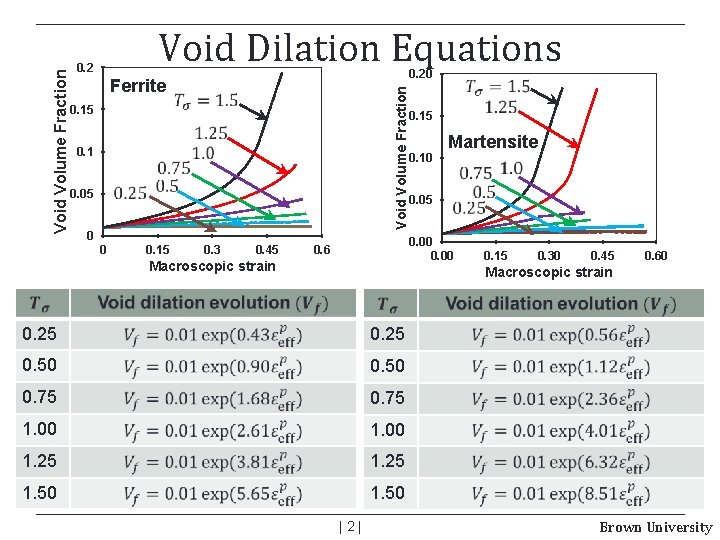
Ferrite 0. 15 0. 1 0. 05 0. 20 Void Volume Fraction Void Dilation Equations 0. 2 0 0 0. 15 0. 3 0. 45 0. 15 Martensite 0. 05 0. 10 0. 00 0. 6 Macroscopic strain 0. 15 0. 30 0. 45 0. 60 Macroscopic strain 0. 25 0. 50 0. 75 1. 00 1. 25 1. 50 | 2 | Brown University
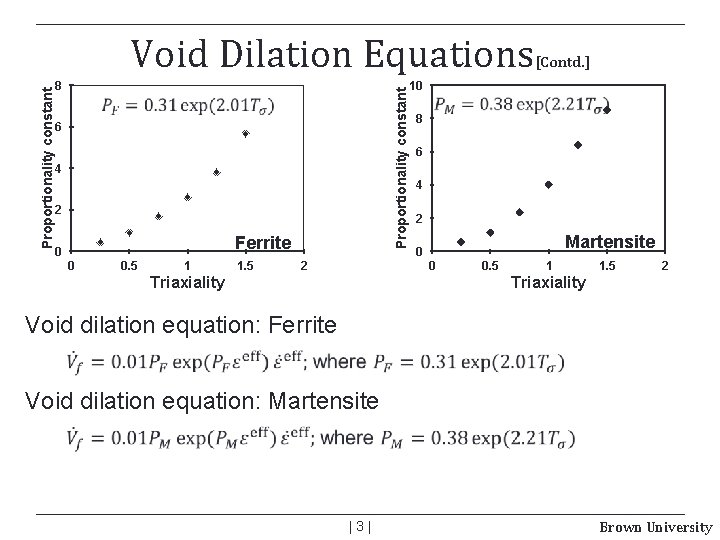
8 Proportionality constant Void Dilation Equations 6 4 2 Ferrite 0 0 0. 5 1 1. 5 2 10 8 6 4 2 Martensite 0 0 Triaxiality [Contd. ] 0. 5 1 1. 5 2 Triaxiality Void dilation equation: Ferrite Void dilation equation: Martensite | 3 | Brown University
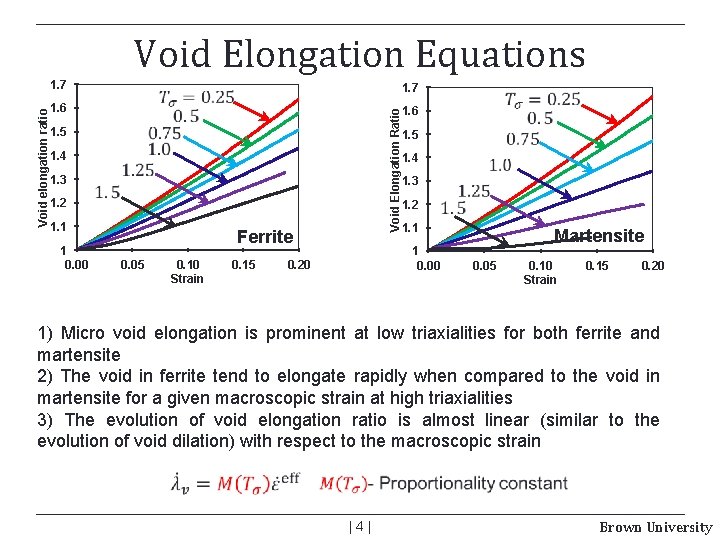
Void Elongation Equations 1. 6 1. 5 1. 4 1. 3 1. 2 1. 7 Void Elongation Ratio Void elongation ratio 1. 7 1. 1 1 0. 00 Ferrite 0. 05 0. 10 Strain 0. 15 1. 6 1. 5 1. 4 1. 3 1. 2 1. 1 1 0. 00 0. 20 Martensite 0. 05 0. 10 Strain 0. 15 0. 20 1) Micro void elongation is prominent at low triaxialities for both ferrite and martensite 2) The void in ferrite tend to elongate rapidly when compared to the void in martensite for a given macroscopic strain at high triaxialities 3) The evolution of void elongation ratio is almost linear (similar to the evolution of void dilation) with respect to the macroscopic strain | 4 | Brown University
![Void Elongation Equations 4 Proportionality Constant 4 Contd 3 2 1 Ferrite 0 Void Elongation Equations 4 Proportionality Constant 4 [Contd. ] 3 2 1 Ferrite 0](https://slidetodoc.com/presentation_image_h/0d15b8e392bc062389ed0d73f8877616/image-6.jpg)
Void Elongation Equations 4 Proportionality Constant 4 [Contd. ] 3 2 1 Ferrite 0 0 0. 5 1 Triaxiality 1. 5 3 2 1 Martensite 0 2 0 0. 5 1 Triaxiality 1. 5 2 Evaluating proportionality functions The proportionality functions are obtained by plotting slopes of void elongation evolution curves with respect to the triaxialities at which they are obtained | 5 | Brown University
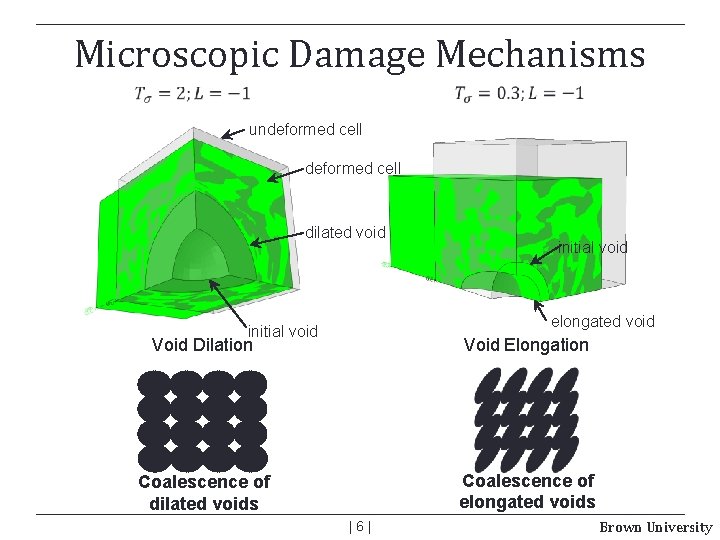
Microscopic Damage Mechanisms undeformed cell dilated void initial void elongated void initial void Void Dilation Void Elongation Coalescence of dilated voids Coalescence of elongated voids | 6 | Brown University
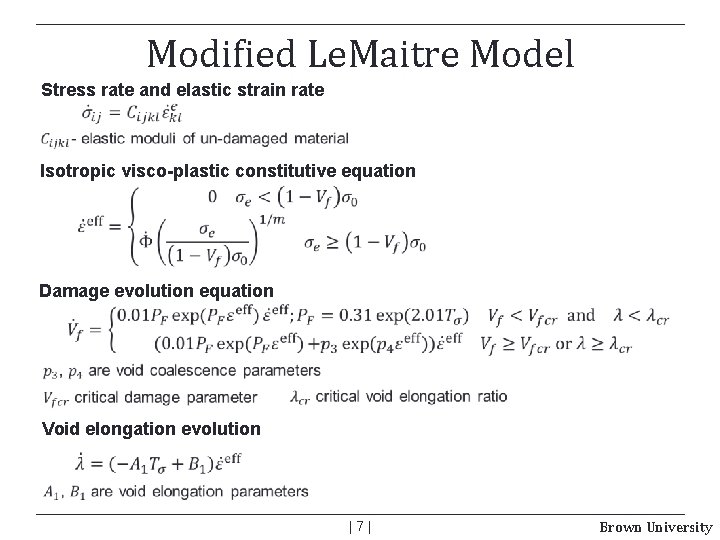
Modified Le. Maitre Model Stress rate and elastic strain rate Isotropic visco-plastic constitutive equation Damage evolution equation Void elongation evolution | 7 | Brown University
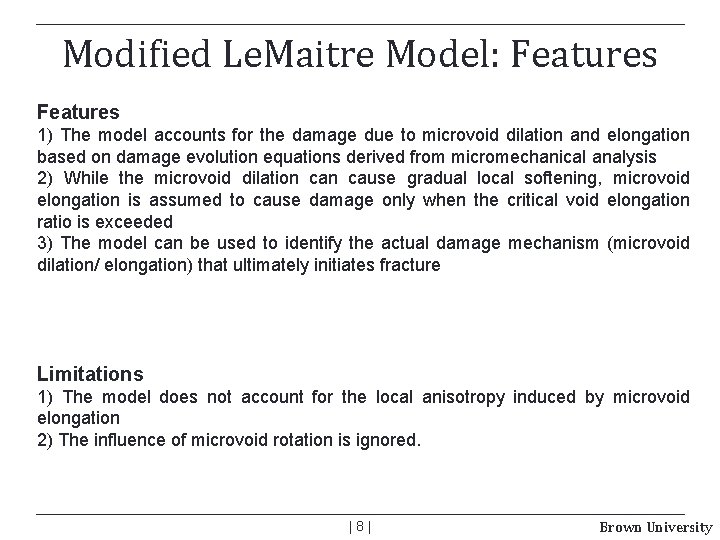
Modified Le. Maitre Model: Features 1) The model accounts for the damage due to microvoid dilation and elongation based on damage evolution equations derived from micromechanical analysis 2) While the microvoid dilation cause gradual local softening, microvoid elongation is assumed to cause damage only when the critical void elongation ratio is exceeded 3) The model can be used to identify the actual damage mechanism (microvoid dilation/ elongation) that ultimately initiates fracture Limitations 1) The model does not account for the local anisotropy induced by microvoid elongation 2) The influence of microvoid rotation is ignored. | 8 | Brown University
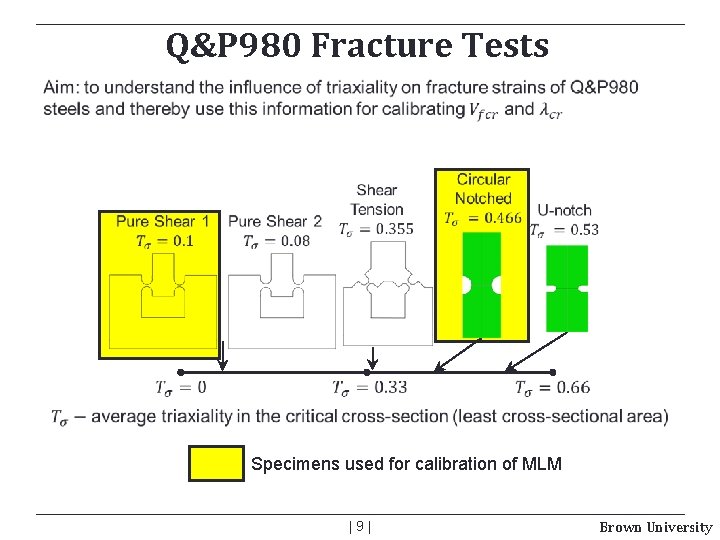
Q&P 980 Fracture Tests Specimens used for calibration of MLM | 9 | Brown University
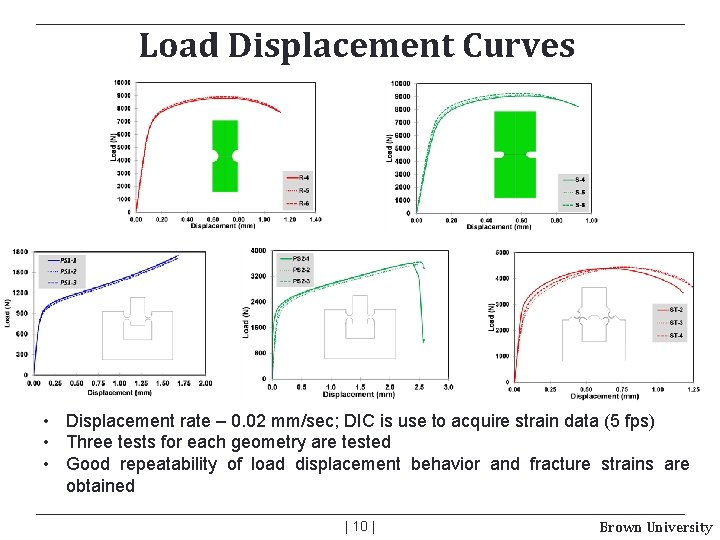
Load Displacement Curves • Displacement rate – 0. 02 mm/sec; DIC is use to acquire strain data (5 fps) • Three tests for each geometry are tested • Good repeatability of load displacement behavior and fracture strains are obtained | 10 | Brown University
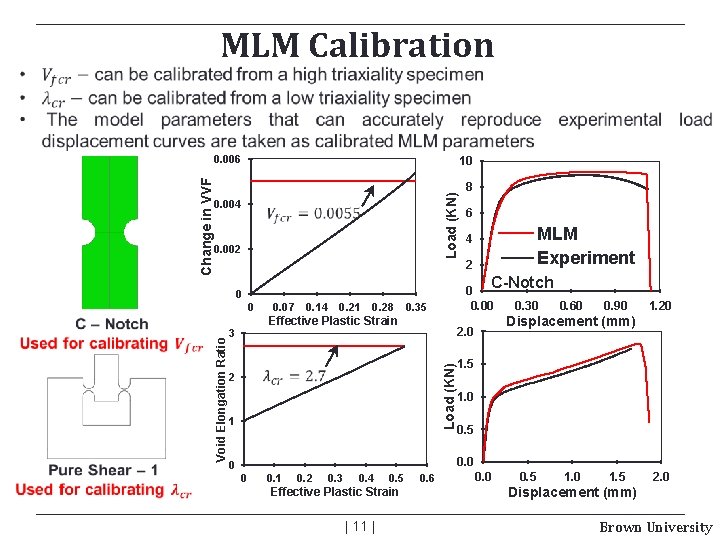
MLM Calibration 10 0. 004 Load (KN) Change in VVF 0. 006 0. 002 0. 07 0. 14 0. 21 0. 28 0. 35 Effective Plastic Strain 3 2 1 0. 30 0. 60 0. 90 1. 20 Displacement (mm) 2. 0 Load (KN) Void Elongation Ratio MLM Experiment 4 C-Notch 0 2 6 0 0. 00 0 8 1. 5 1. 0 0. 5 0. 0 0. 1 0. 2 0. 3 0. 4 0. 5 Effective Plastic Strain | 11 | 0. 6 0. 0 0. 5 1. 0 1. 5 2. 0 Displacement (mm) Brown University
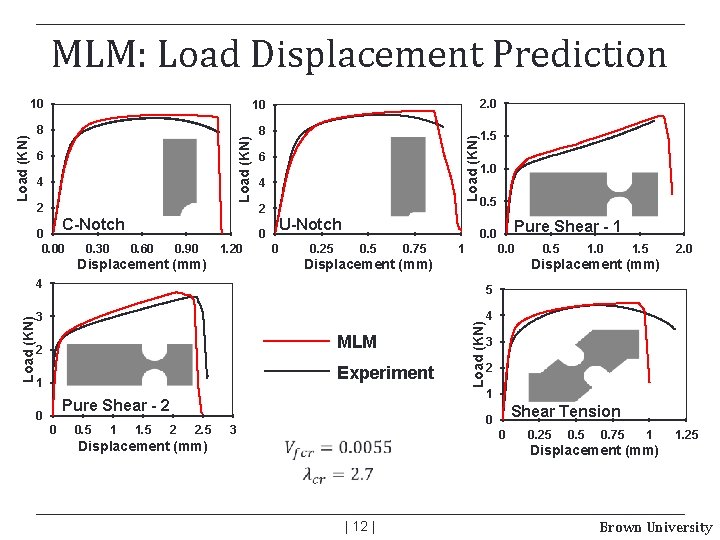
8 8 Load (KN) 10 6 4 2 0 0. 00 6 4 2 0 0. 30 0. 60 0. 90 0 0. 25 0. 75 1 Displacement (mm) Load (KN) Displacement (mm) 1. 20 Displacement (mm) | 12 | Brown University
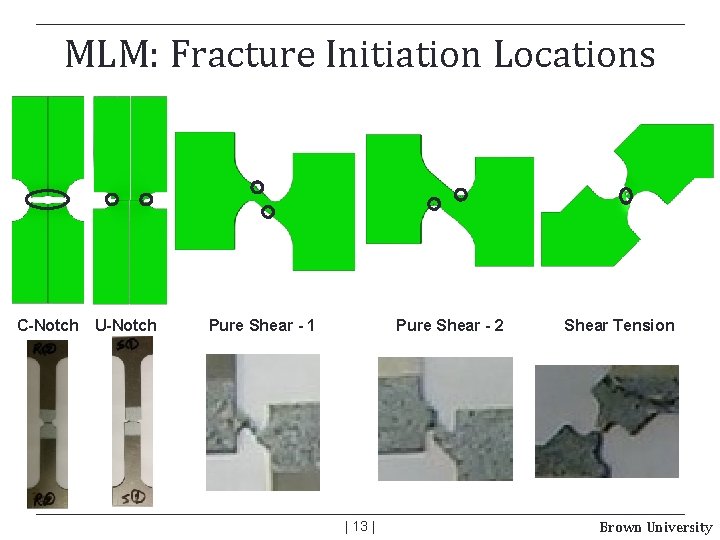
MLM: Fracture Initiation Locations C-Notch U-Notch Pure Shear - 1 Pure Shear - 2 | 13 | Shear Tension Brown University
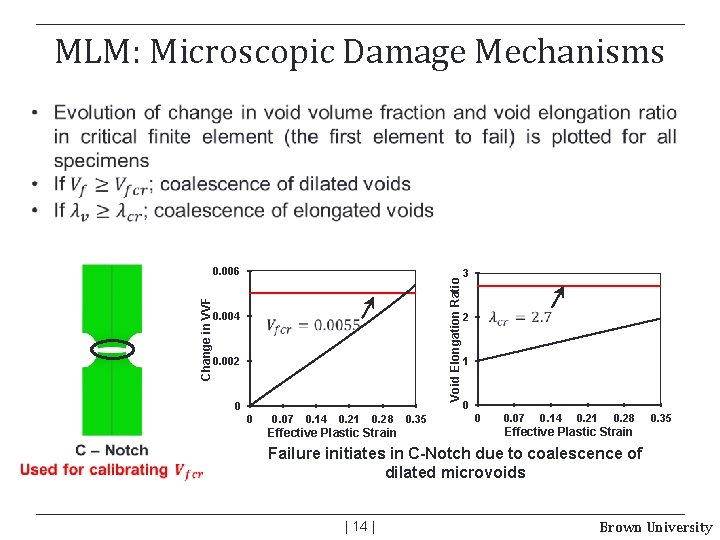
MLM: Microscopic Damage Mechanisms 0. 004 Void Elongation Ratio Change in VVF 0. 006 0. 002 0 0 0. 07 0. 14 0. 21 0. 28 Effective Plastic Strain 0. 35 3 2 1 0 0 0. 07 0. 14 0. 21 0. 28 0. 35 Effective Plastic Strain Failure initiates in C-Notch due to coalescence of dilated microvoids | 14 | Brown University
![MLM Microscopic Damage MechanismsContd Void Elongation Ratio Change in VVF 0 006 0 MLM: Microscopic Damage Mechanisms[Contd. ] Void Elongation Ratio Change in VVF 0. 006 0.](https://slidetodoc.com/presentation_image_h/0d15b8e392bc062389ed0d73f8877616/image-16.jpg)
MLM: Microscopic Damage Mechanisms[Contd. ] Void Elongation Ratio Change in VVF 0. 006 0. 004 0. 002 0 0 0. 1 0. 2 0. 3 0. 4 0. 5 0. 6 3 1 0 0 Effective Plastic Strain 0. 1 0. 2 0. 3 0. 4 0. 5 0. 6 Effective Plastic Strain Failure initiates in U-Notch due to coalescence of dilated and elongated microvoids U-Notch Void Elongation Ratio Change in VVF 0. 006 0. 004 0. 002 0 0. 1 0. 2 0. 3 0. 4 0. 5 Effective Plastic Strain 0. 6 3 2 1 0 0 0. 1 0. 2 0. 3 0. 4 0. 5 0. 6 Effective Plastic Strain Failure initiates in PS-1 due to coalescence of elongated microvoids | 15 | Brown University
![MLM Microscopic Damage MechanismsContd Void Elongation Ratio Change in VVF 0 008 0 MLM: Microscopic Damage Mechanisms[Contd. ] Void Elongation Ratio Change in VVF 0. 008 0.](https://slidetodoc.com/presentation_image_h/0d15b8e392bc062389ed0d73f8877616/image-17.jpg)
MLM: Microscopic Damage Mechanisms[Contd. ] Void Elongation Ratio Change in VVF 0. 008 0. 006 0. 004 0. 002 0 0 Pure Shear - 2 0. 1 0. 2 0. 3 0. 4 0. 5 3 2 1 0 0 Effective Plastic Strain 0. 1 0. 2 0. 3 0. 4 0. 5 Effective Plastic Strain Failure initiates in PS-1 due to coalescence of elongated microvoids Void Elongation Ratio Change in VVF 0. 006 0. 004 0. 002 0 Shear Tension 0 0. 1 0. 2 0. 3 0. 4 0. 5 Effective Plastic Strain 0. 6 3 2 1 0 0 0. 1 0. 2 0. 3 0. 4 0. 5 0. 6 Effective Plastic Strain Failure initiates in U-Notch due to coalescence of dilated and elongated microvoids | 16 | Brown University
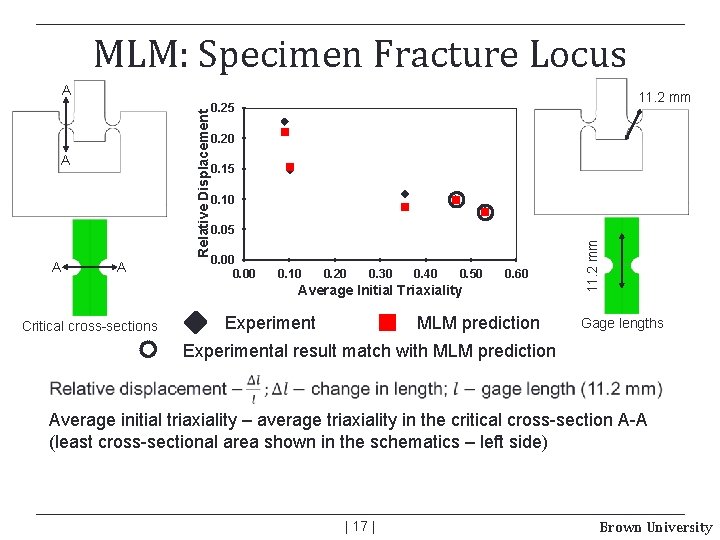
MLM: Specimen Fracture Locus A A A 11. 2 mm 0. 25 0. 20 0. 15 0. 10 0. 05 0. 00 0. 10 0. 20 0. 30 0. 40 0. 50 0. 60 Average Initial Triaxiality Critical cross-sections Experiment MLM prediction 11. 2 mm Relative Displacement A Gage lengths Experimental result match with MLM prediction Average initial triaxiality – average triaxiality in the critical cross-section A-A (least cross-sectional area shown in the schematics – left side) | 17 | Brown University
Computational engineering and physical modeling
Eutectic and eutectoid reaction
High frequency market microstructure
Development of microstructure in isomorphous alloys
Empirical market microstructure
Market microstructure trading strategies
Microstructure of a dictionary
Microstructure of ferrous metals
Devaluation and idealization
Erickson nursing theory
Relational modeling vs dimensional modeling
Audio compression test
Convergent boundary with subduction
Ductile and malleable
Is magnesium brittle
Horizontal
Moderately ductile fracture
Definiton of ductile
Brittle or ductile