MDIC CAPA Process Pilot Program Chair Kathryn Merrill
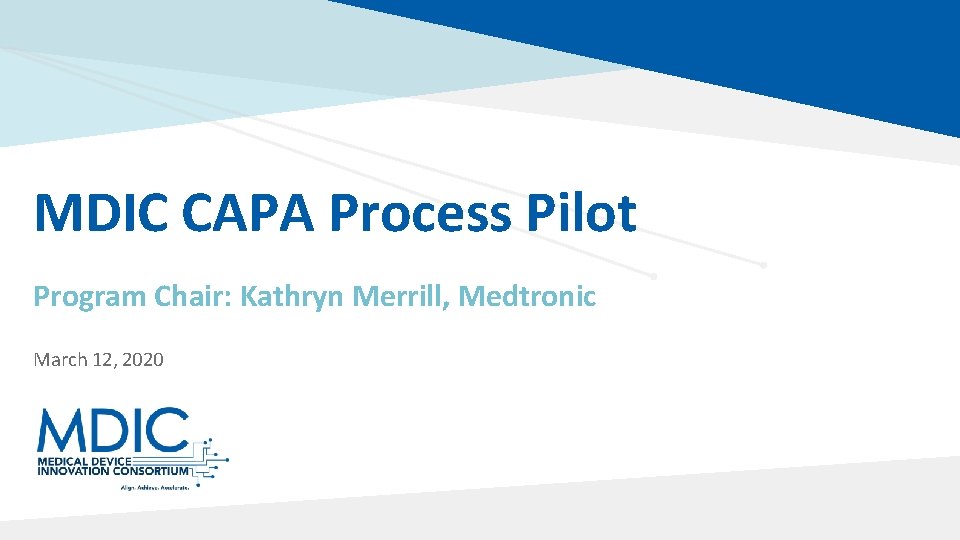
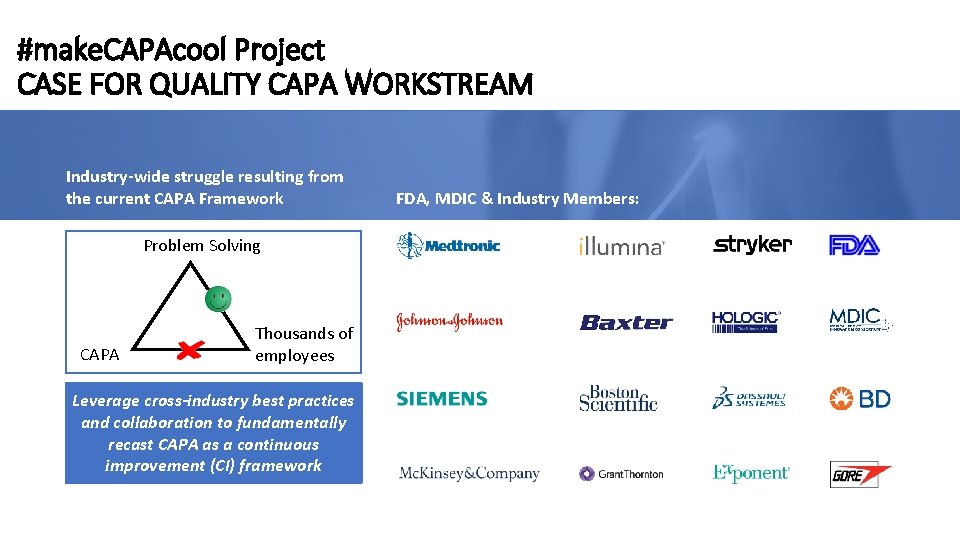
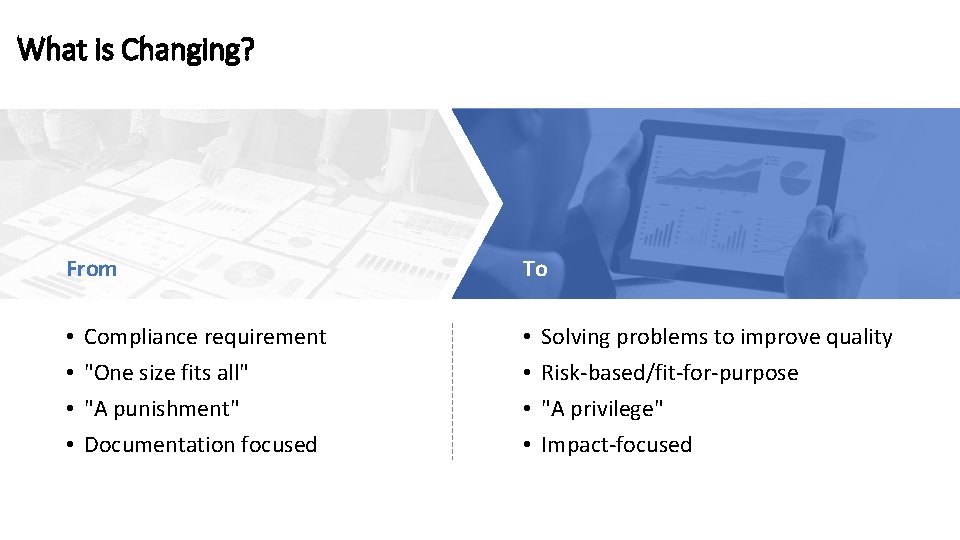
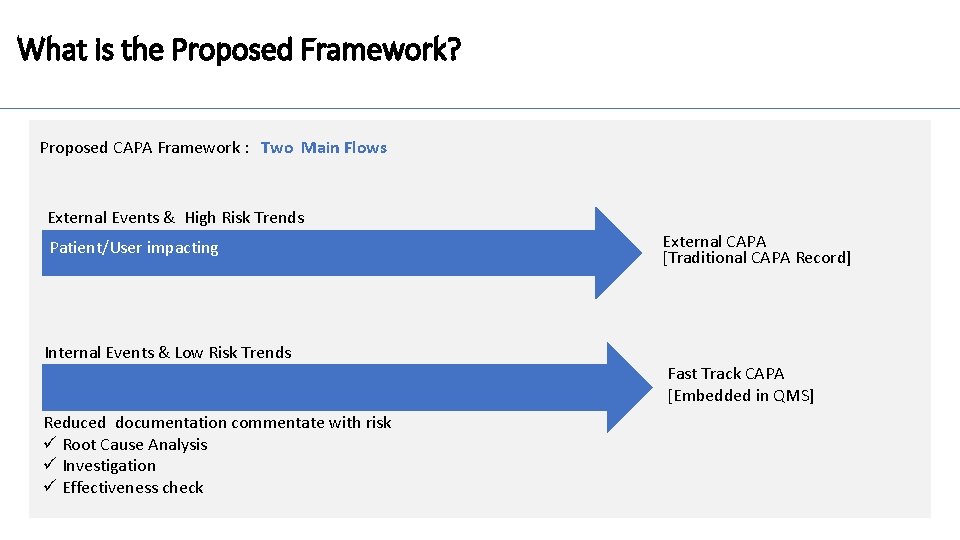
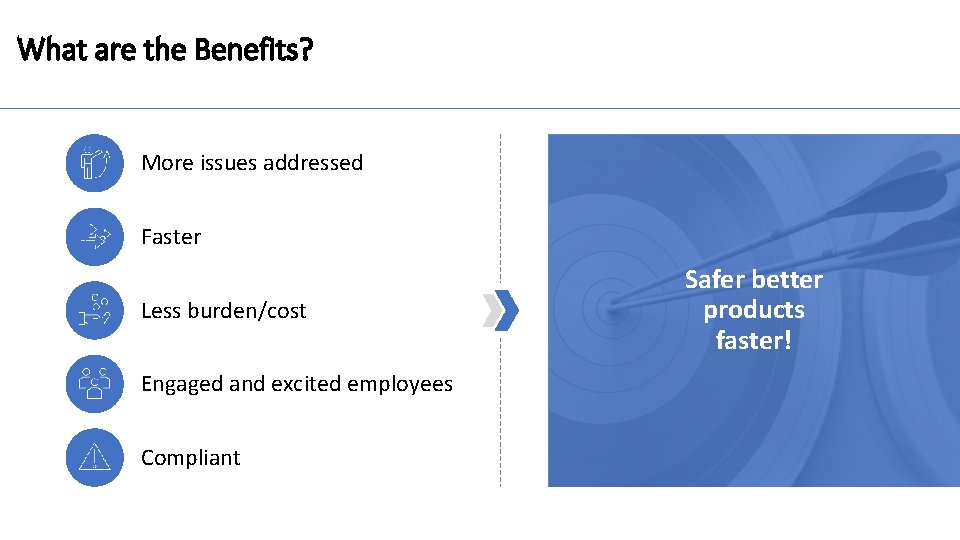
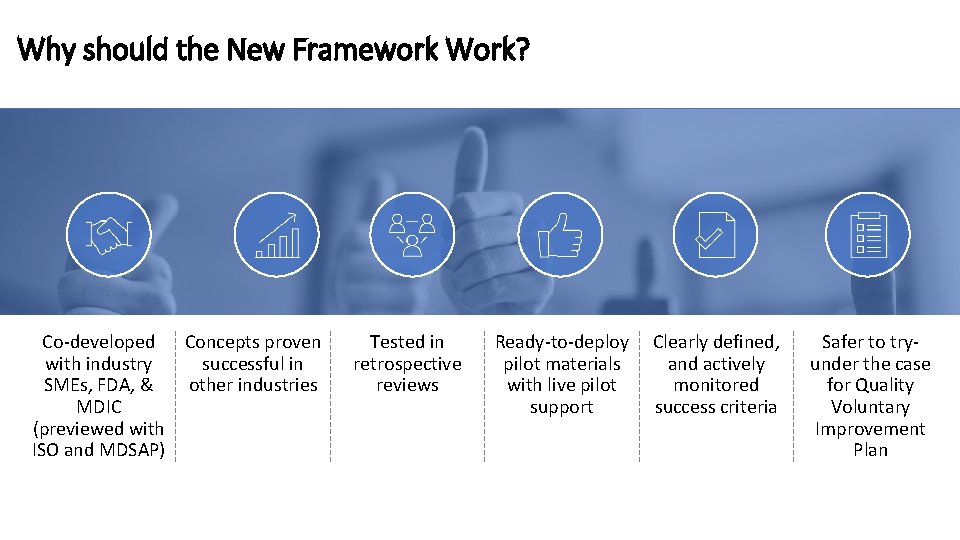
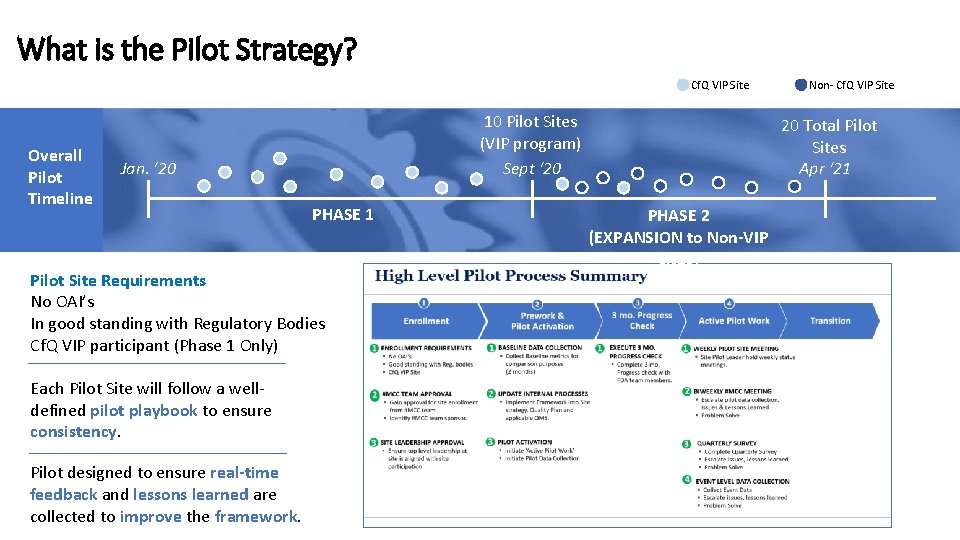


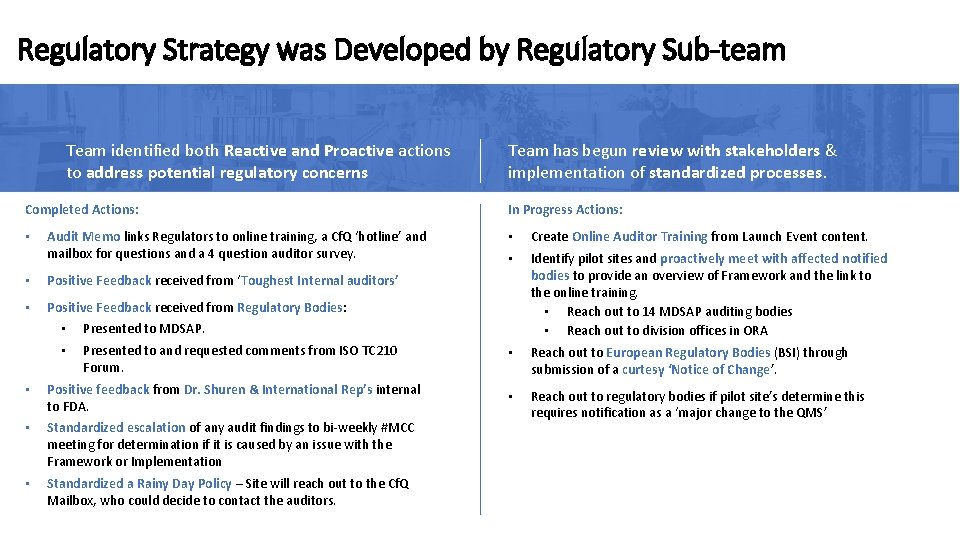
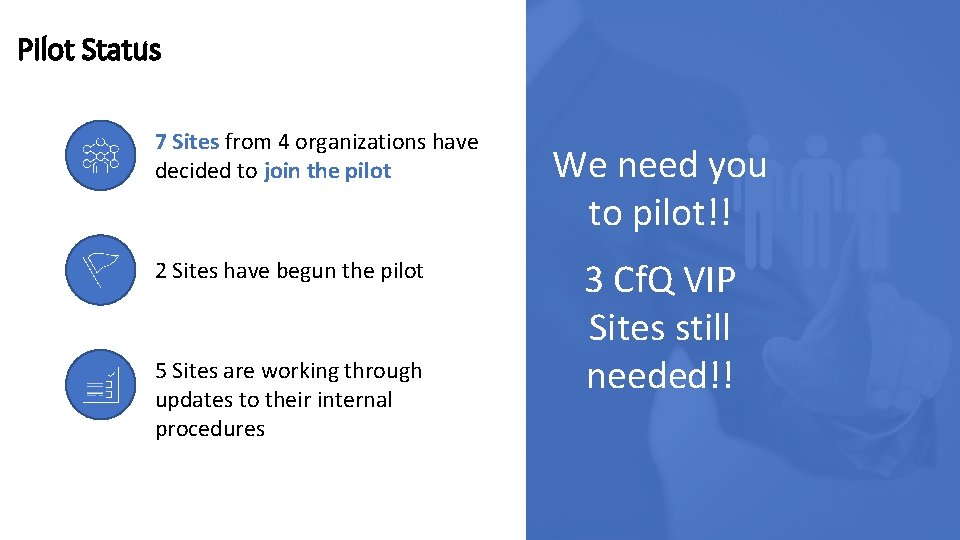
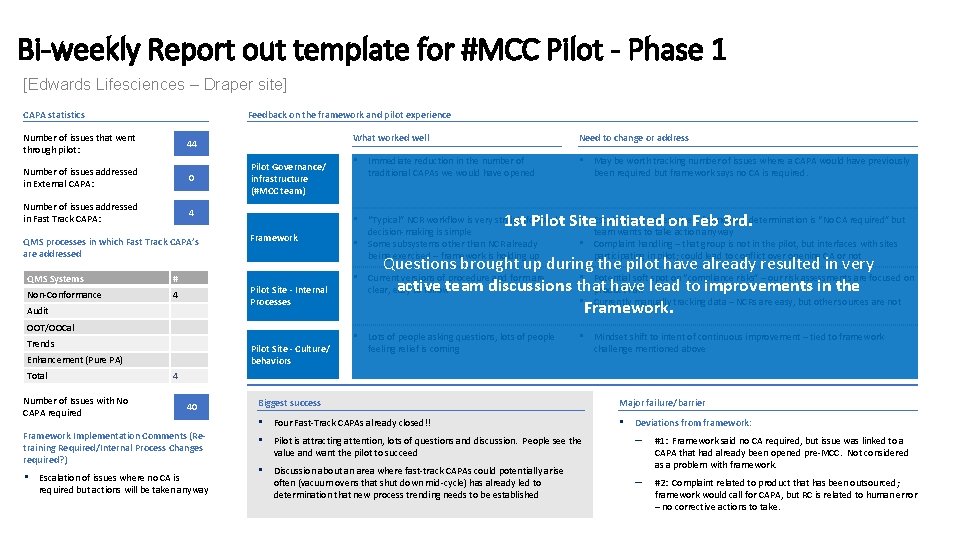
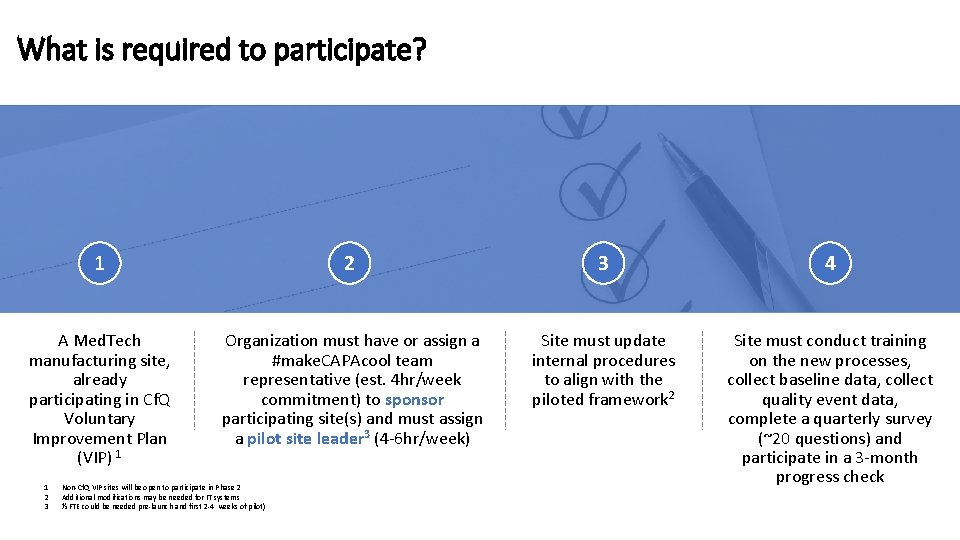
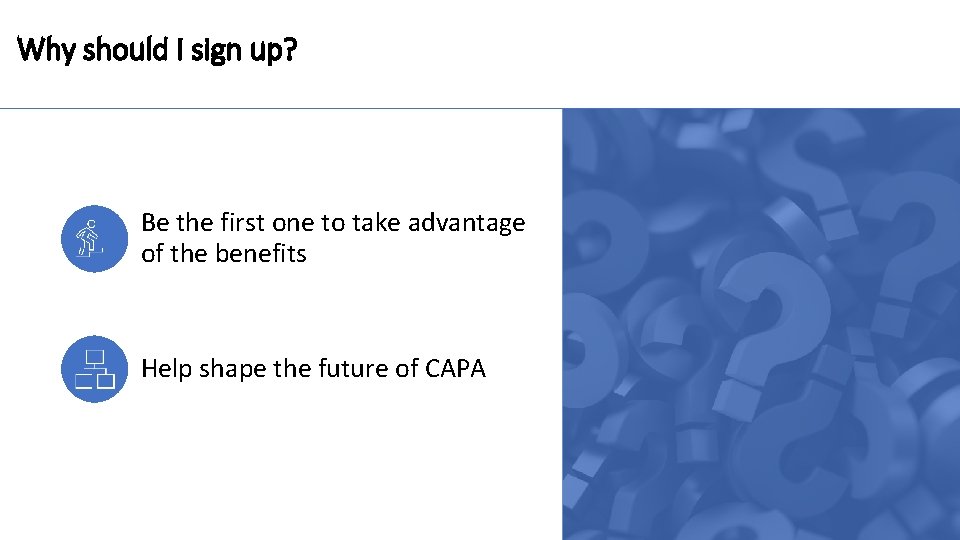
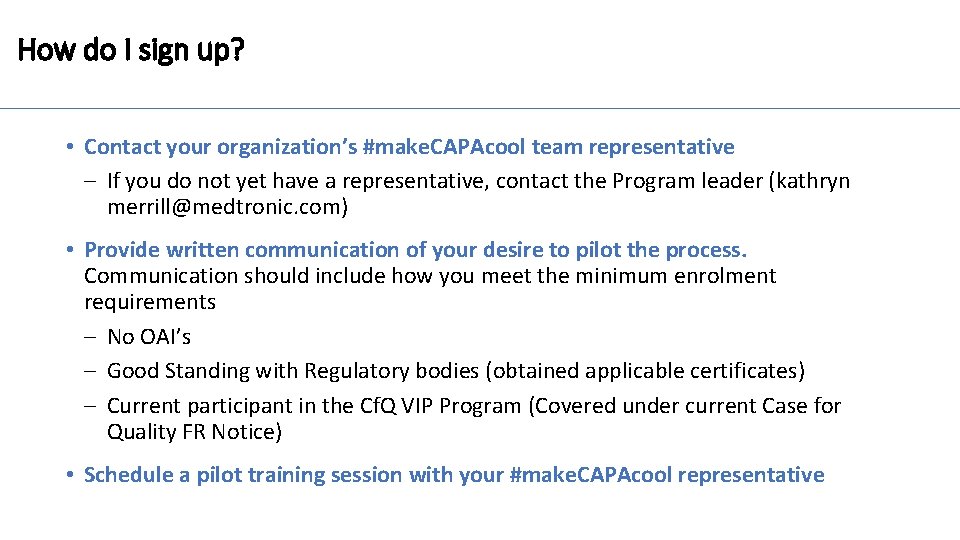
- Slides: 15
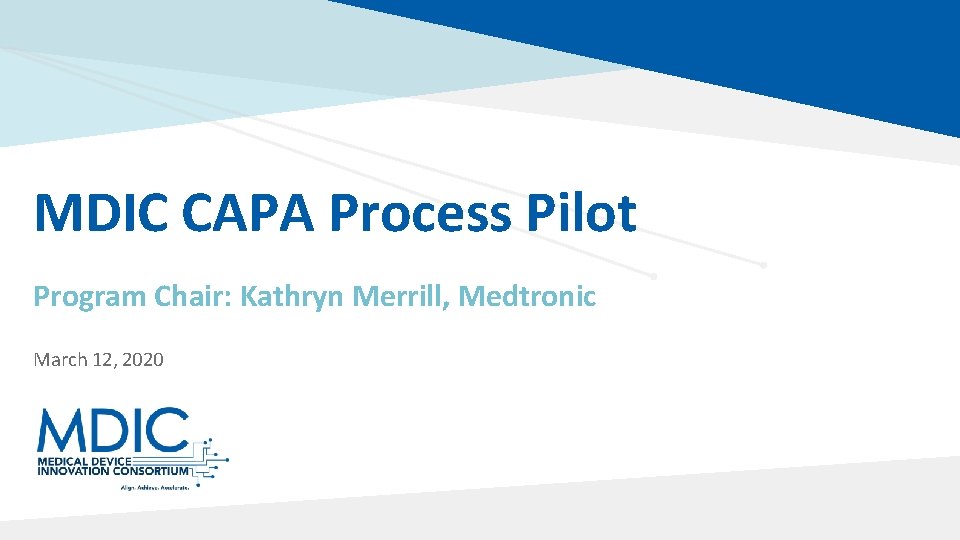
MDIC CAPA Process Pilot Program Chair: Kathryn Merrill, Medtronic March 12, 2020
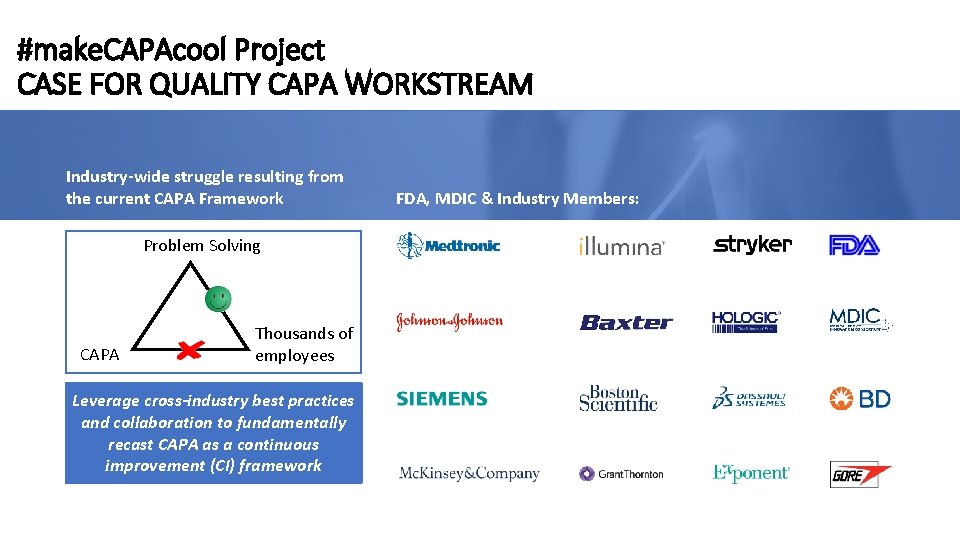
#make. CAPAcool Project CASE FOR QUALITY CAPA WORKSTREAM Industry-wide struggle resulting from the current CAPA Framework Solvingbest practices Leverage Problem cross-industry and collaboration to fundamentally recast CAPA as a continuous improvement (CI) framework Thousands of CAPA employees Leverage cross-industry best practices and collaboration to fundamentally recast CAPA as a continuous improvement (CI) framework FDA, MDIC & Industry Members:
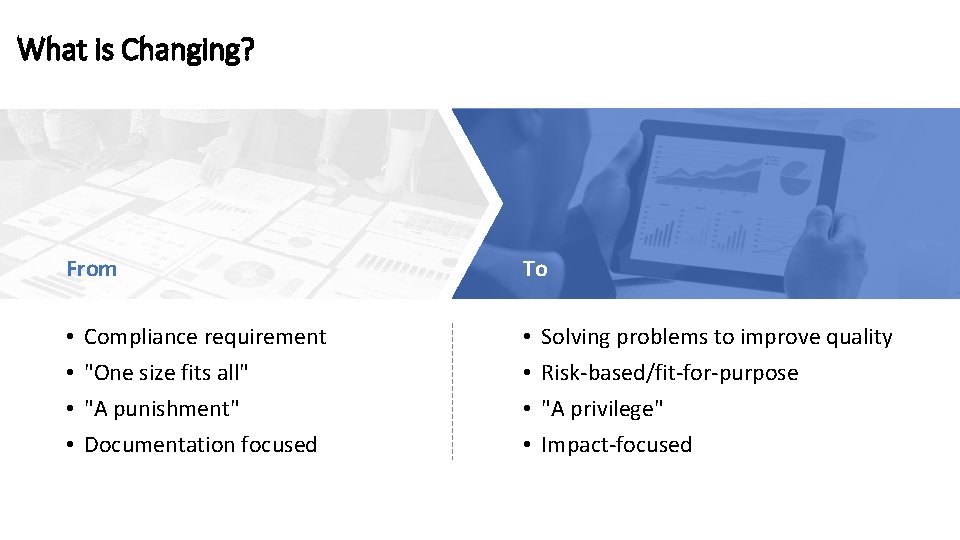
What is Changing? From • • Compliance requirement "One size fits all" "A punishment" Documentation focused To • • Solving problems to improve quality Risk-based/fit-for-purpose "A privilege" Impact-focused
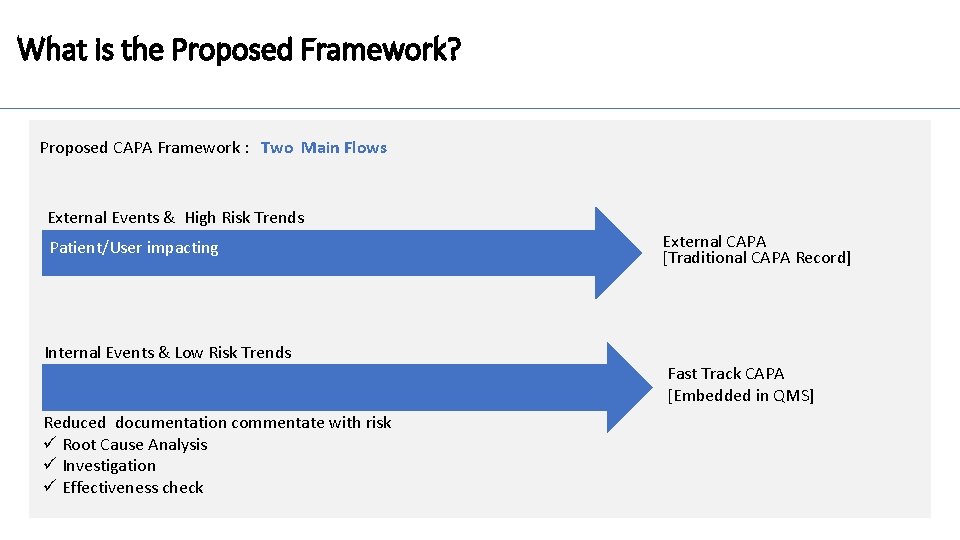
What is the Proposed Framework? Proposed CAPA Framework : Two Main Flows External Events & High Risk Trends Patient/User impacting Internal Events & Low Risk Trends Reduced documentation commentate with risk ü Root Cause Analysis ü Investigation ü Effectiveness check External CAPA [Traditional CAPA Record] Fast Track CAPA [Embedded in QMS]
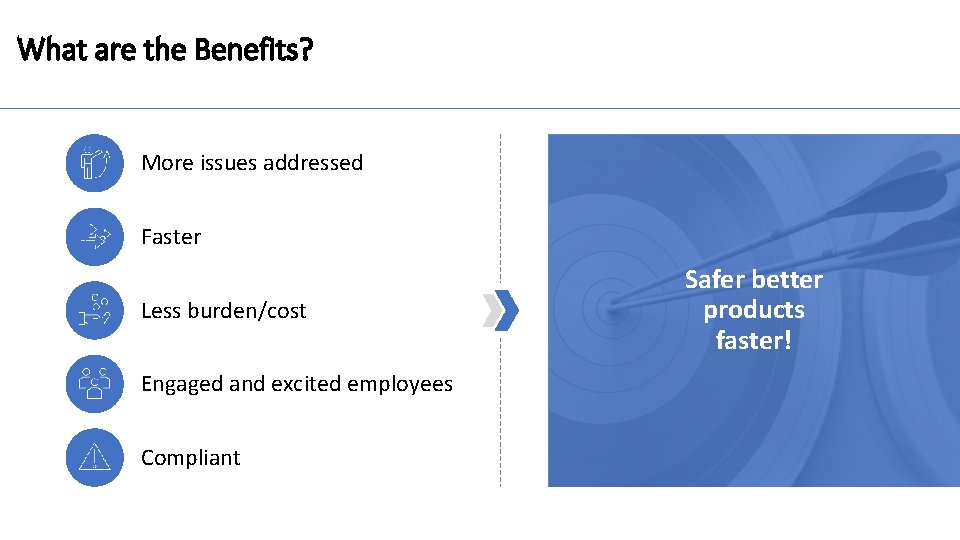
What are the Benefits? More issues addressed Faster Less burden/cost Engaged and excited employees Compliant Safer better products faster!
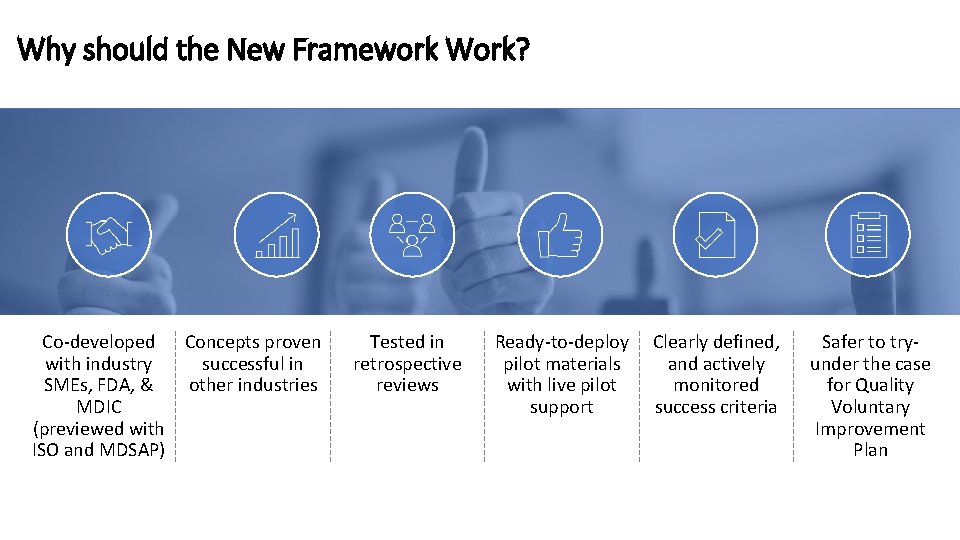
Why should the New Framework Work? Co-developed Concepts proven with industry successful in SMEs, FDA, & other industries MDIC (previewed with ISO and MDSAP) Tested in retrospective reviews Ready-to-deploy pilot materials with live pilot support Clearly defined, and actively monitored success criteria Safer to tryunder the case for Quality Voluntary Improvement Plan
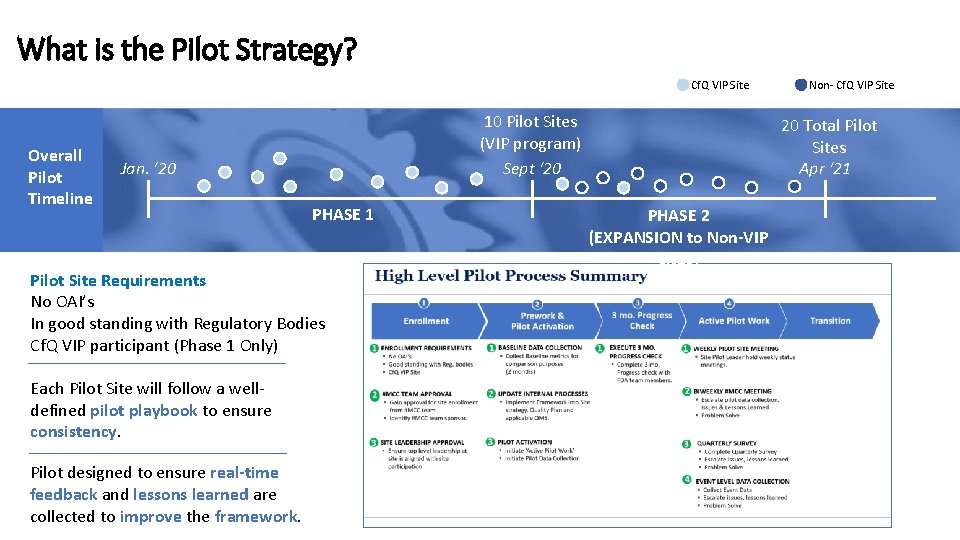
What is the Pilot Strategy? Cf. Q VIP Site Overall Pilot Timeline 10 Pilot Sites (VIP program) Sept ‘ 20 Jan. ‘ 20 PHASE 1 Pilot Site Requirements No OAI’s In good standing with Regulatory Bodies Cf. Q VIP participant (Phase 1 Only) Each Pilot Site will follow a welldefined pilot playbook to ensure consistency. Pilot designed to ensure real-time feedback and lessons learned are collected to improve the framework. Non- Cf. Q VIP Site 20 Total Pilot Sites Apr ‘ 21 PHASE 2 (EXPANSION to Non-VIP sites)

#make. CAPAcool Pilot Launch Event at Mc. Kinsey #MCC team members & Pilot Site leaders attended a 2 Day Launch Event hosted by Mc. Kinsey. Goals • • Onboard new pilot sites quickly. Standardize pilot process Outcomes: • Provided detailed training on the Pilot Materials • Lead participants through a workshop to help them develop their change story & to identify levers to effective change. • Provided time for teams to begin working on a change strategy for their individual sites.

#make. CAPAcool Pilot Launch Event at Mc. Kinsey Pilot materials: • Whitepaper • Training overview slide deck • Playbook • Examples • Data Collection Sites & Surveys • Audit Memo
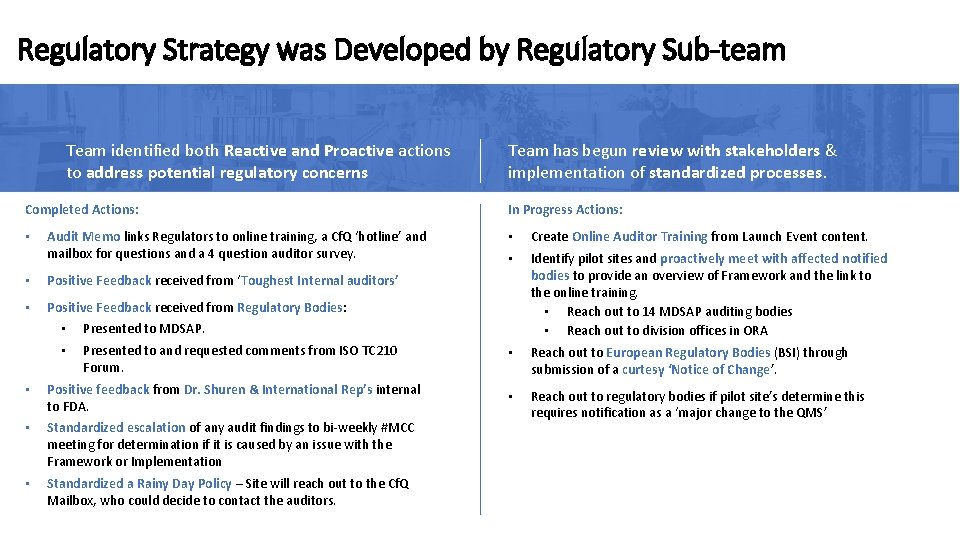
Regulatory Strategy was Developed by Regulatory Sub-team Team identified both Reactive and Proactive actions to address potential regulatory concerns Completed Actions: • Audit Memo links Regulators to online training, a Cf. Q ‘hotline’ and mailbox for questions and a 4 question auditor survey. • Positive Feedback received from ‘Toughest Internal auditors’ • Positive Feedback received from Regulatory Bodies: • Presented to MDSAP. • Presented to and requested comments from ISO TC 210 Forum. • Positive feedback from Dr. Shuren & International Rep’s internal to FDA. • Standardized escalation of any audit findings to bi-weekly #MCC meeting for determination if it is caused by an issue with the Framework or Implementation • Standardized a Rainy Day Policy – Site will reach out to the Cf. Q Mailbox, who could decide to contact the auditors. Team has begun review with stakeholders & implementation of standardized processes. In Progress Actions: • Create Online Auditor Training from Launch Event content. • Identify pilot sites and proactively meet with affected notified bodies to provide an overview of Framework and the link to the online training. • Reach out to 14 MDSAP auditing bodies • Reach out to division offices in ORA • Reach out to European Regulatory Bodies (BSI) through submission of a curtesy ‘Notice of Change’. • Reach out to regulatory bodies if pilot site’s determine this requires notification as a ‘major change to the QMS’
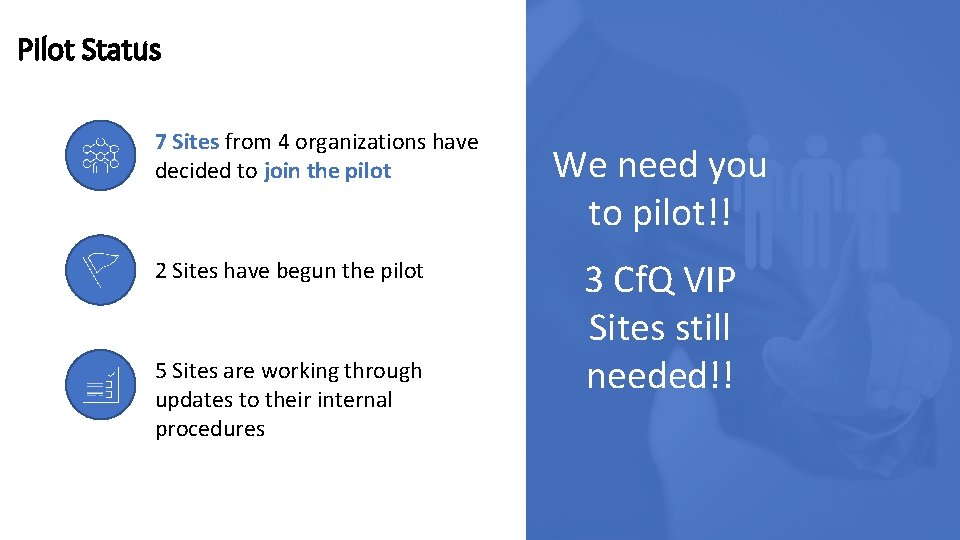
Pilot Status 7 Sites from 4 organizations have decided to join the pilot 2 Sites have begun the pilot 5 Sites are working through updates to their internal procedures We need you to pilot!! 3 Cf. Q VIP Sites still needed!!
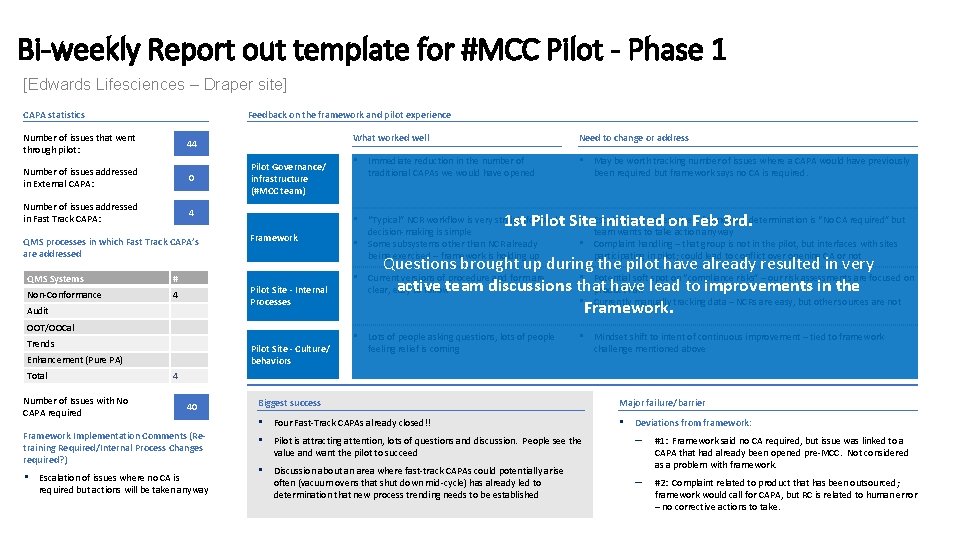
Bi-weekly Report out template for #MCC Pilot - Phase 1 [Edwards Lifesciences – Draper site] Feedback on the framework and pilot experience CAPA statistics Number of issues that went through pilot: 44 Number of issues addressed in External CAPA: 0 Number of issues addressed in Fast Track CAPA: 4 QMS processes in which Fast Track CAPA’s are addressed QMS Systems # Non-Conformance 4 Pilot Governance/ infrastructure (#MCC team) Framework Pilot Site - Internal Processes Audit OOT/OOCal Trends Pilot Site - Culture/ behaviors Enhancement (Pure PA) Total Number of Issues with No CAPA required Need to change or address • Immediate reduction in the number of traditional CAPAs we would have opened • • “Typical” NCR workflow is very straightforward; decision-making is simple Some subsystems other than NCR already being exercised – framework is holding up • May be worth tracking number of issues where a CAPA would have previously been required but framework says no CA is required. • Escalation of issueson where framework 1 st Pilot Site initiated Feb 3 rd. determination is “No CA required” but team wants to take action anyway • Complaint handling – that group is not in the pilot, but interfaces with sites participating in pilot; could lead to conflict over opening CA or not Questions brought up during the pilot have already resulted in very • Potential soft spot on “compliance risks” – our risk assessments are focused on active team discussions that have product risk lead to improvements in the • Currently manually tracking data – NCRs are easy, but other sources are not Framework. • Current versions of procedure and form are clear, easy to follow • Lots of people asking questions, lots of people feeling relief is coming • Mindset shift to intent of continuous improvement – tied to framework challenge mentioned above 4 40 Framework Implementation Comments (Retraining Required/Internal Process Changes required? ) ▪ What worked well Escalation of issues where no CA is required but actions will be taken anyway Biggest success Major failure/barrier • • Four Fast-Track CAPAs already closed!! • • Discussion about an area where fast-track CAPAs could potentially arise often (vacuum ovens that shut down mid-cycle) has already led to determination that new process trending needs to be established Pilot is attracting attention, lots of questions and discussion. People see the value and want the pilot to succeed Deviations from framework: – #1: Framework said no CA required, but issue was linked to a CAPA that had already been opened pre-MCC. Not considered as a problem with framework. – #2: Complaint related to product that has been outsourced; framework would call for CAPA, but RC is related to human error – no corrective actions to take.
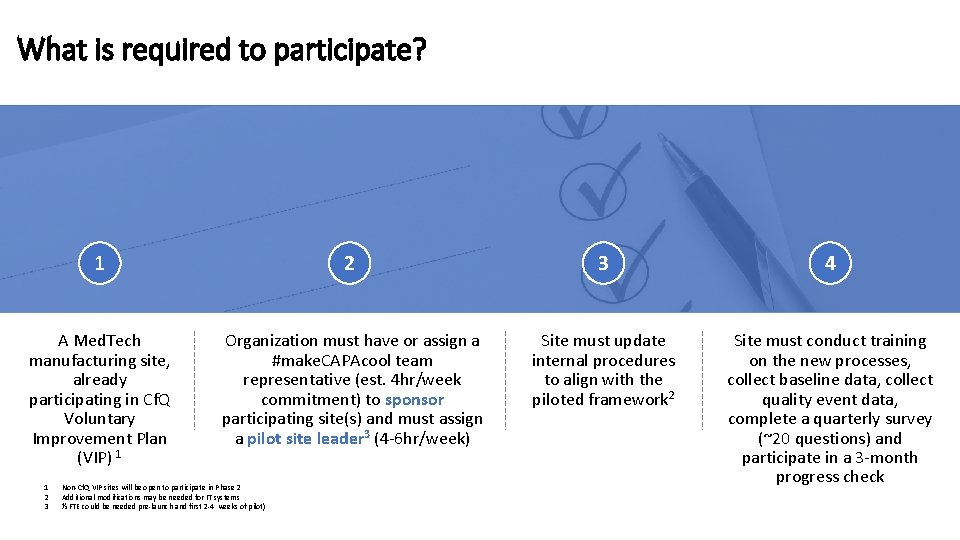
What is required to participate? 1 2 3 4 A Med. Tech manufacturing site, already participating in Cf. Q Voluntary Improvement Plan (VIP) 1 Organization must have or assign a #make. CAPAcool team representative (est. 4 hr/week commitment) to sponsor participating site(s) and must assign a pilot site leader 3 (4 -6 hr/week) Site must update internal procedures to align with the piloted framework 2 Site must conduct training on the new processes, collect baseline data, collect quality event data, complete a quarterly survey (~20 questions) and participate in a 3 -month progress check 1 2 3 Non-Cf. Q VIP sites will be open to participate in Phase 2 Additional modifications may be needed for IT systems ½ FTE could be needed pre-launch and first 2 -4 weeks of pilot)
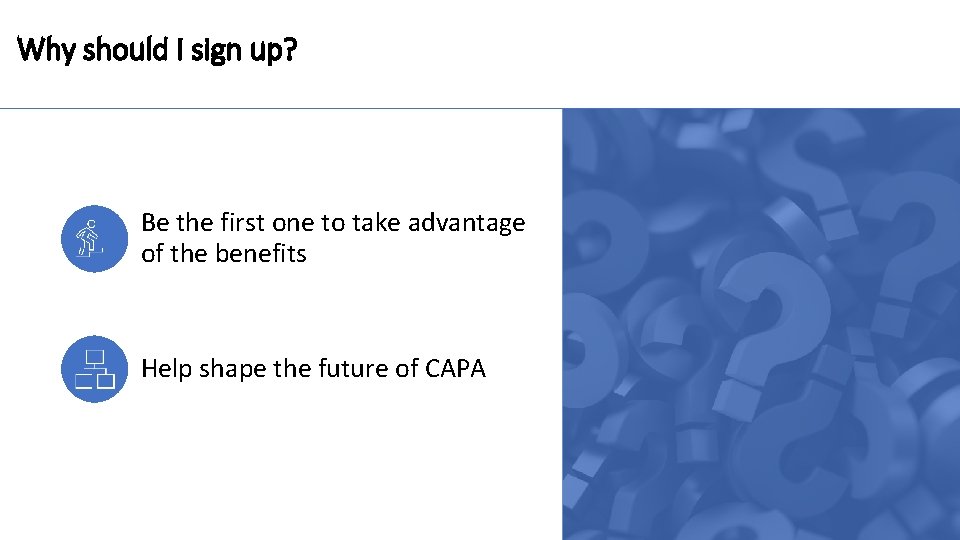
Why should I sign up? Be the first one to take advantage of the benefits Help shape the future of CAPA
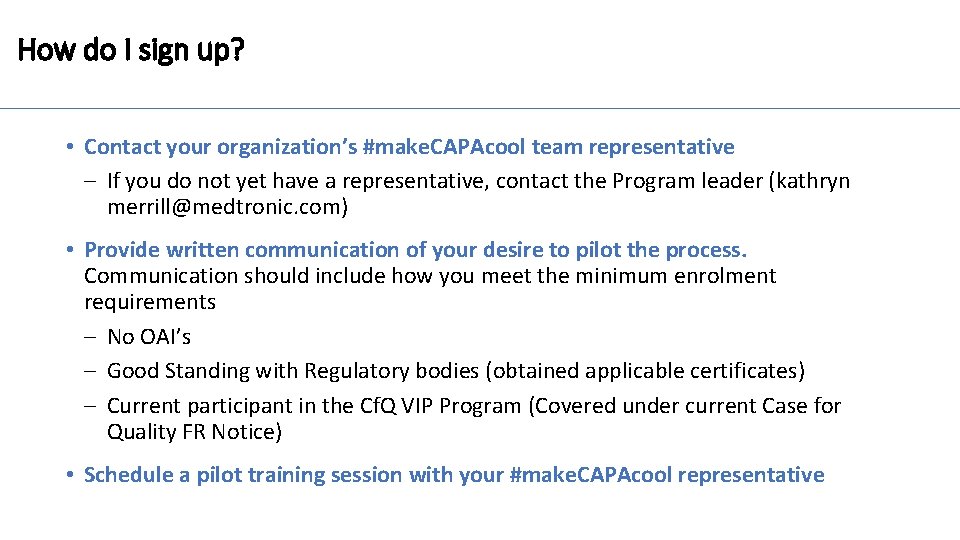
How do I sign up? • Contact your organization’s #make. CAPAcool team representative – If you do not yet have a representative, contact the Program leader (kathryn merrill@medtronic. com) • Provide written communication of your desire to pilot the process. Communication should include how you meet the minimum enrolment requirements – No OAI’s – Good Standing with Regulatory bodies (obtained applicable certificates) – Current participant in the Cf. Q VIP Program (Covered under current Case for Quality FR Notice) • Schedule a pilot training session with your #make. CAPAcool representative
Capacoo
Faa wings pilot proficiency program
Wings pilot proficiency program
Section 502 guaranteed rural housing loan program
First action interview
Lion pilot program
Dr merrill barry
Merrill's first principles of instruction
Dr. sonya merrill
Modelo merril
Merrill lynch strategic balanced index
Bradley merrill thompson
Merrill winston
Sonya merrill
Dr sonya merrill
Dr barry merrill