MCW 8 Endoscopic Optical Coherence Tomography Using TwoAxis
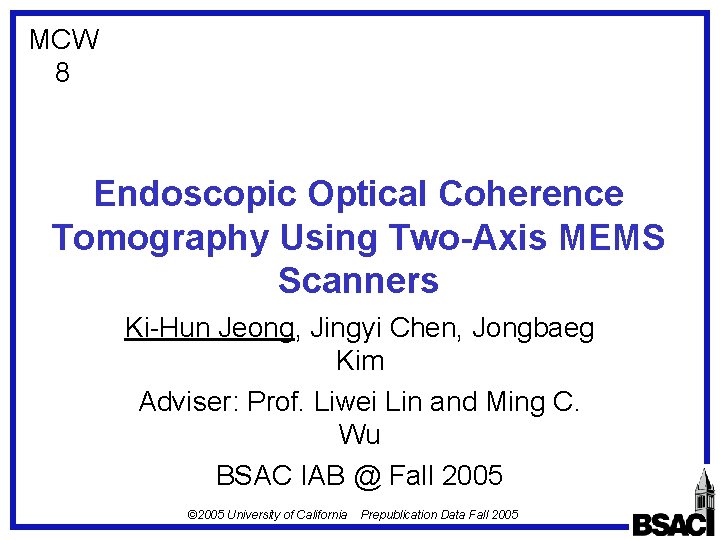
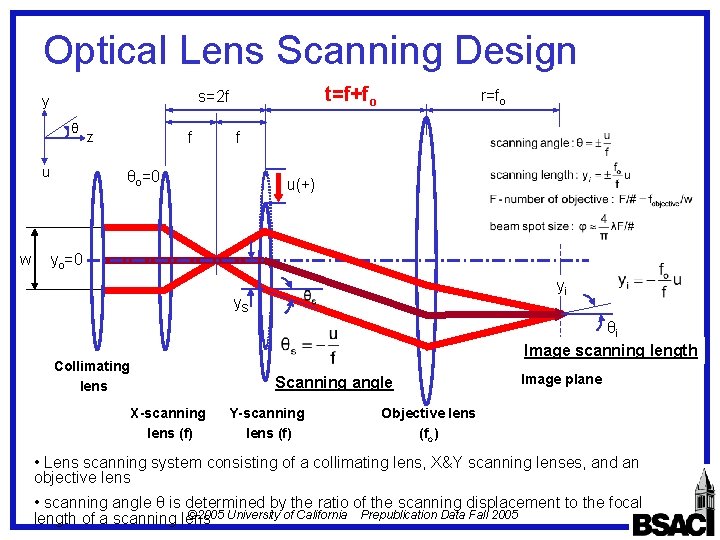
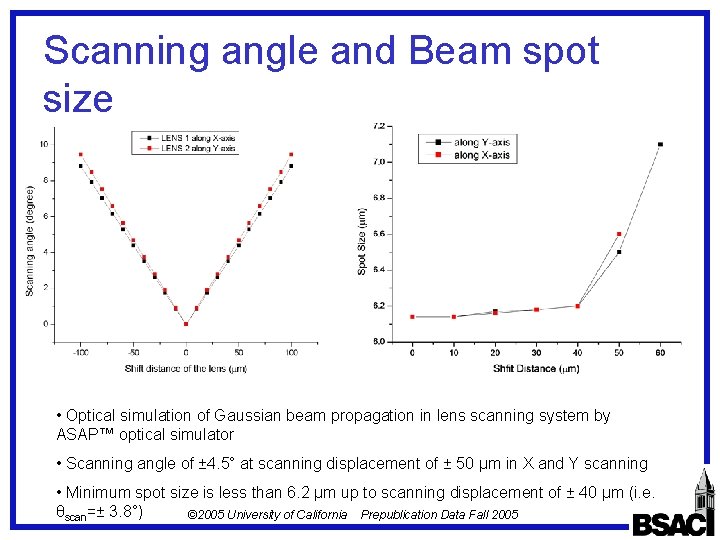
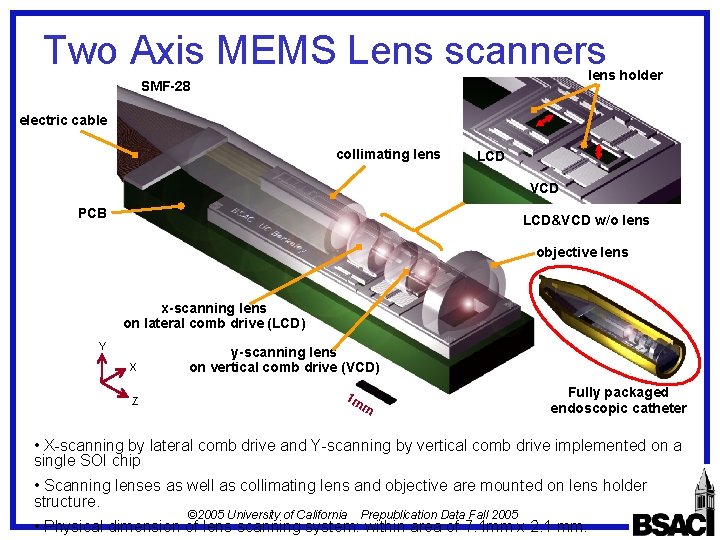
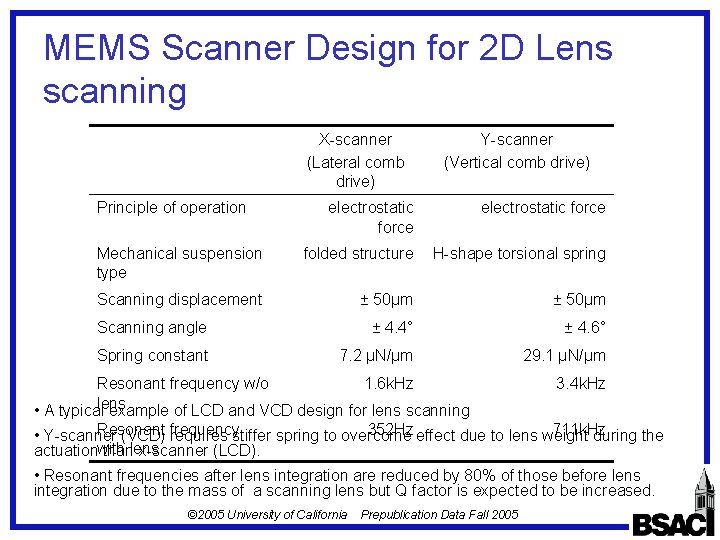
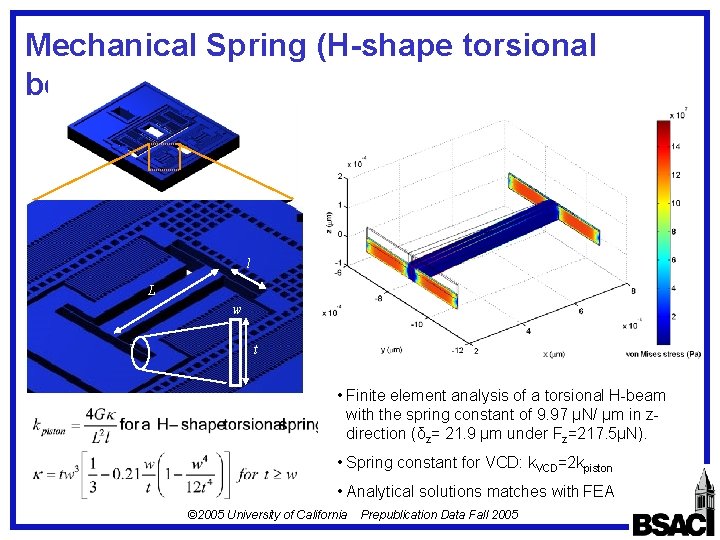
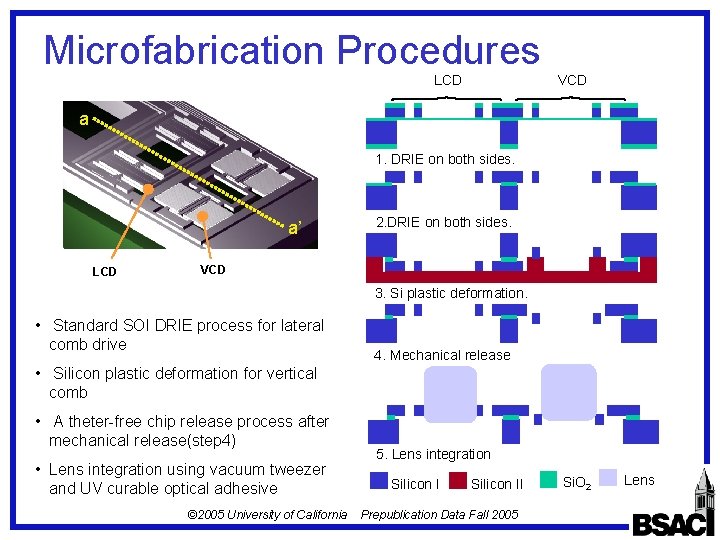
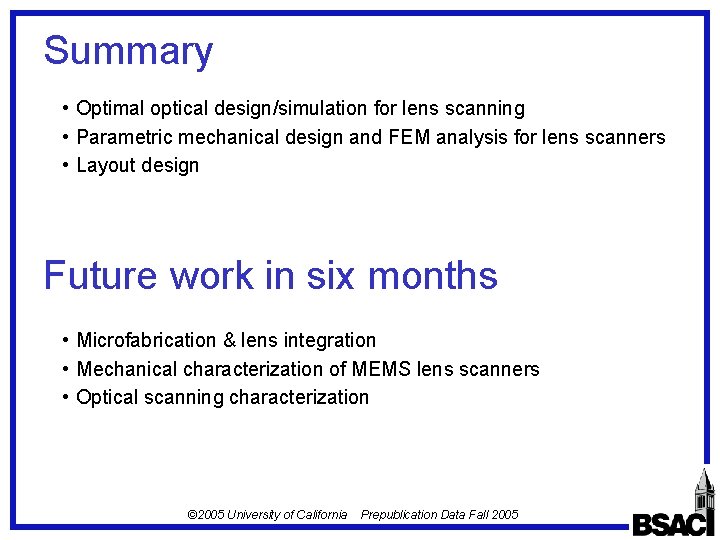
- Slides: 8
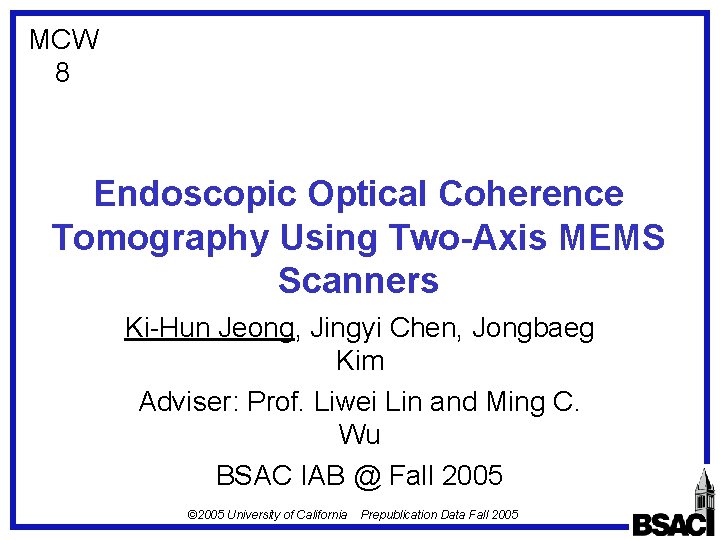
MCW 8 Endoscopic Optical Coherence Tomography Using Two-Axis MEMS Scanners Ki-Hun Jeong, Jingyi Chen, Jongbaeg Kim Adviser: Prof. Liwei Lin and Ming C. Wu BSAC IAB @ Fall 2005 © 2005 University of California Prepublication Data Fall 2005
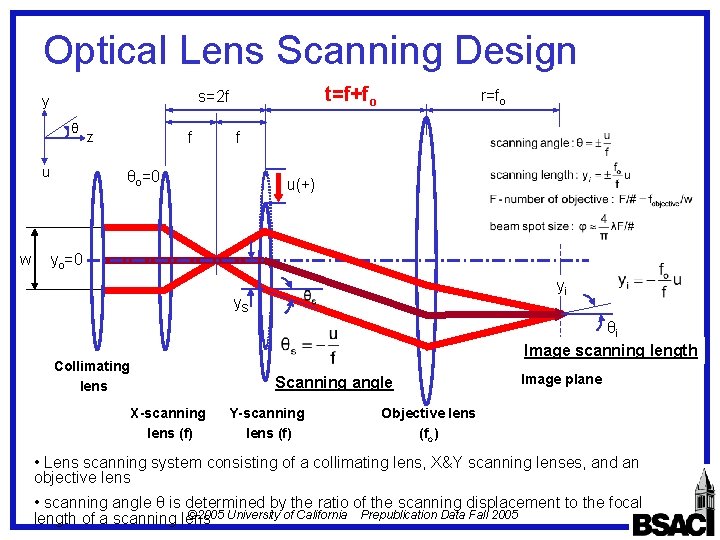
Optical Lens Scanning Design θ u w t=f+fo s=2 f y f z r=fo f θo=0 u(+) yo=0 yi y. S θi Image scanning length Collimating lens Scanning angle X-scanning lens (f) Y-scanning lens (f) Image plane Objective lens (fo) • Lens scanning system consisting of a collimating lens, X&Y scanning lenses, and an objective lens • scanning angle θ is determined by the ratio of the scanning displacement to the focal © 2005 University of California Prepublication Data Fall 2005 length of a scanning lens
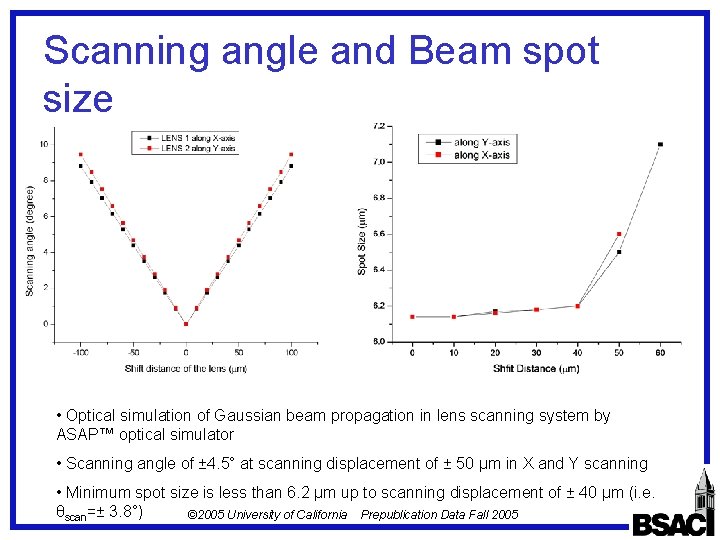
Scanning angle and Beam spot size • Optical simulation of Gaussian beam propagation in lens scanning system by ASAP™ optical simulator • Scanning angle of ± 4. 5° at scanning displacement of ± 50 μm in X and Y scanning • Minimum spot size is less than 6. 2 μm up to scanning displacement of ± 40 μm (i. e. θscan=± 3. 8°) © 2005 University of California Prepublication Data Fall 2005
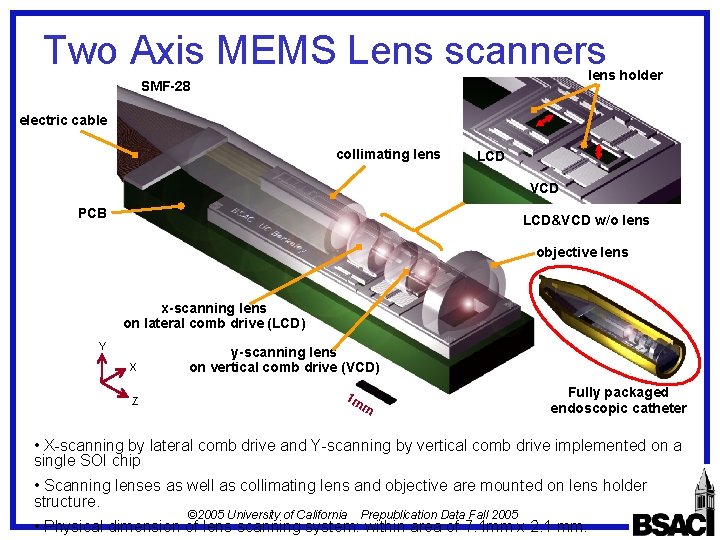
Two Axis MEMS Lens scanners lens holder SMF-28 electric cable collimating lens LCD VCD PCB LCD&VCD w/o lens objective lens x-scanning lens on lateral comb drive (LCD) Y X Z y-scanning lens on vertical comb drive (VCD) 1 m m Fully packaged endoscopic catheter • X-scanning by lateral comb drive and Y-scanning by vertical comb drive implemented on a single SOI chip • Scanning lenses as well as collimating lens and objective are mounted on lens holder structure. © 2005 University of California Prepublication Data Fall 2005 • Physical dimension of lens scanning system: within area of 7. 1 mm x 2. 1 mm.
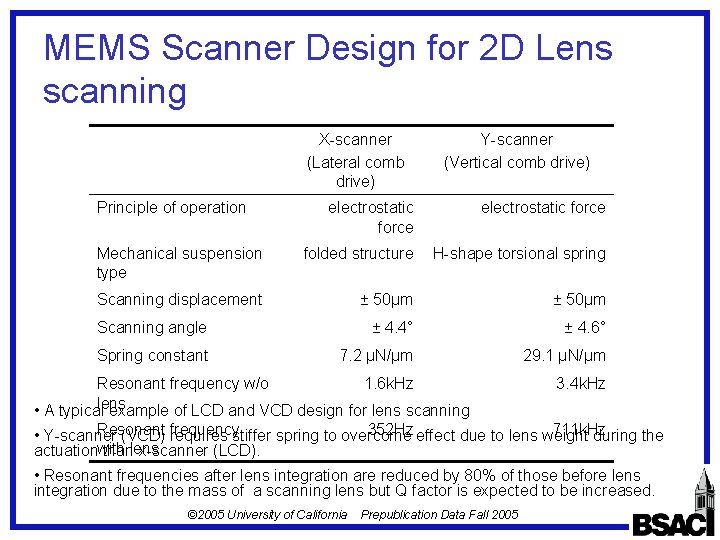
MEMS Scanner Design for 2 D Lens scanning X-scanner (Lateral comb drive) Principle of operation Y-scanner (Vertical comb drive) electrostatic force Mechanical suspension type folded structure H-shape torsional spring Scanning displacement ± 50μm Scanning angle ± 4. 4° ± 4. 6° Spring constant 7. 2 μN/μm 29. 1 μN/μm Resonant frequency w/o 1. 6 k. Hz • A typicallens example of LCD and VCD design for lens scanning 3. 4 k. Hz Resonant 352 Hz effect due to lens weight 711 k. Hz • Y-scanner (VCD) frequency requires stiffer spring to overcome during the actuationwith thanlens x-scanner (LCD). • Resonant frequencies after lens integration are reduced by 80% of those before lens integration due to the mass of a scanning lens but Q factor is expected to be increased. © 2005 University of California Prepublication Data Fall 2005
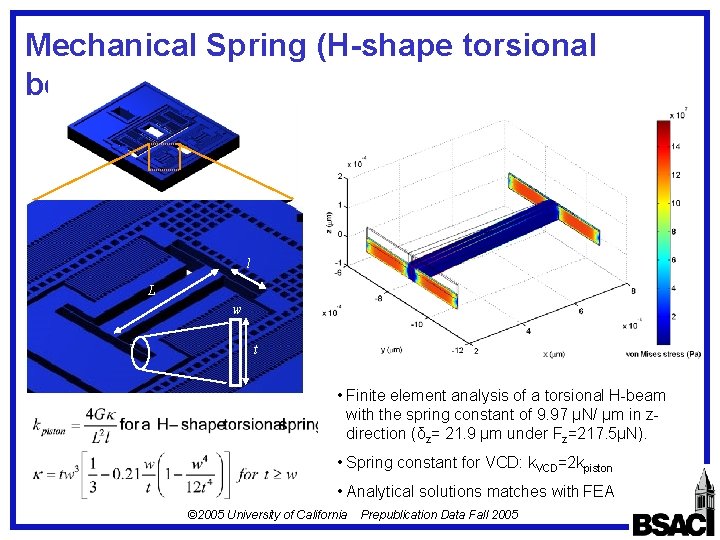
Mechanical Spring (H-shape torsional beam) of VCD l L w t • Finite element analysis of a torsional H-beam with the spring constant of 9. 97 μN/ μm in zdirection (δz= 21. 9 μm under Fz=217. 5μN). • Spring constant for VCD: k. VCD=2 kpiston • Analytical solutions matches with FEA © 2005 University of California Prepublication Data Fall 2005
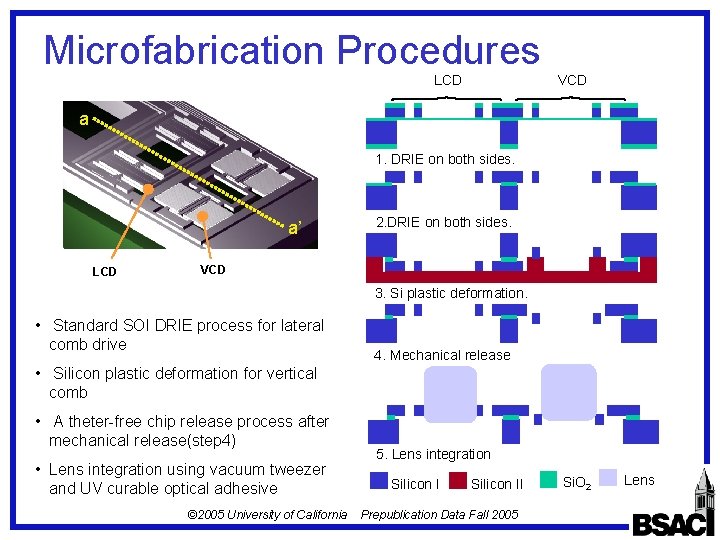
Microfabrication Procedures LCD VCD a 1. DRIE on both sides. a’ LCD 2. DRIE on both sides. VCD 3. Si plastic deformation. • Standard SOI DRIE process for lateral comb drive 4. Mechanical release • Silicon plastic deformation for vertical comb • A theter-free chip release process after mechanical release(step 4) • Lens integration using vacuum tweezer and UV curable optical adhesive © 2005 University of California 5. Lens integration Silicon II Prepublication Data Fall 2005 Si. O 2 Lens
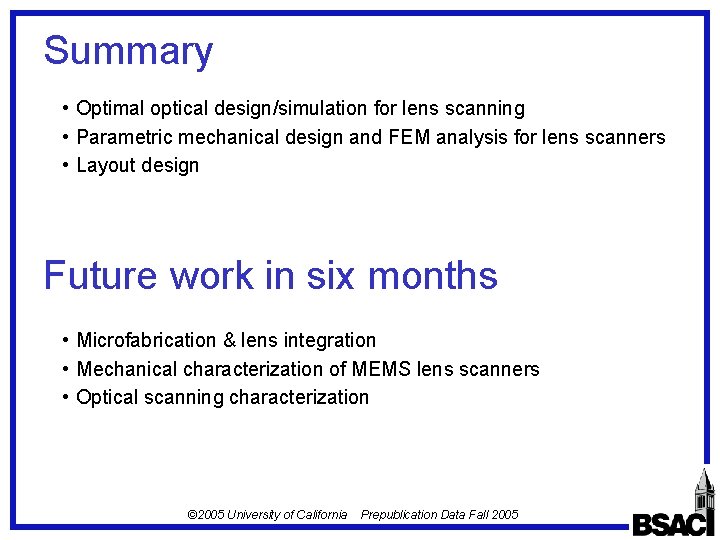
Summary • Optimal optical design/simulation for lens scanning • Parametric mechanical design and FEM analysis for lens scanners • Layout design Future work in six months • Microfabrication & lens integration • Mechanical characterization of MEMS lens scanners • Optical scanning characterization © 2005 University of California Prepublication Data Fall 2005