Lockheed Martin Additive Manufacturing Introduction to Engineering Design
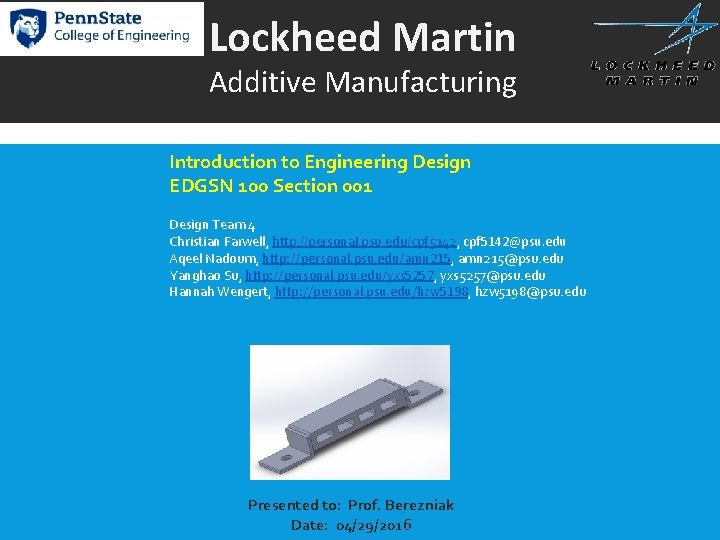
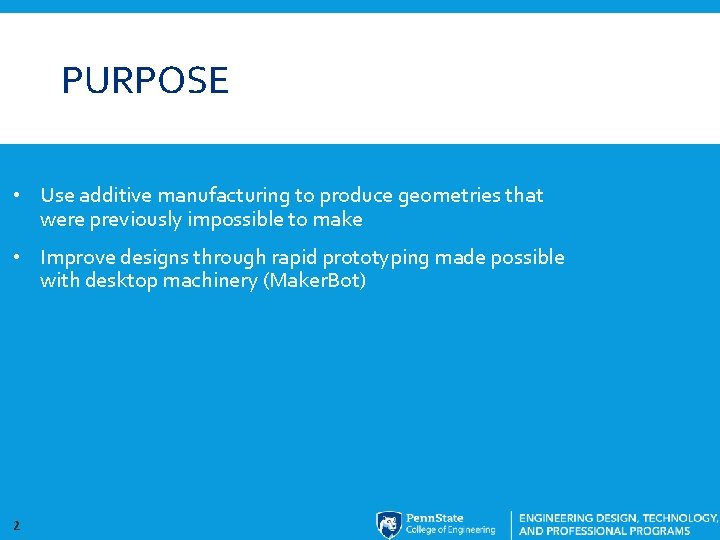
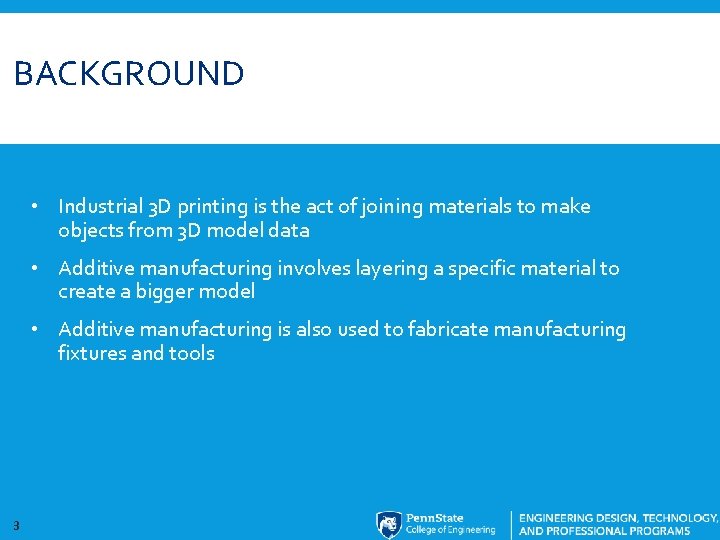
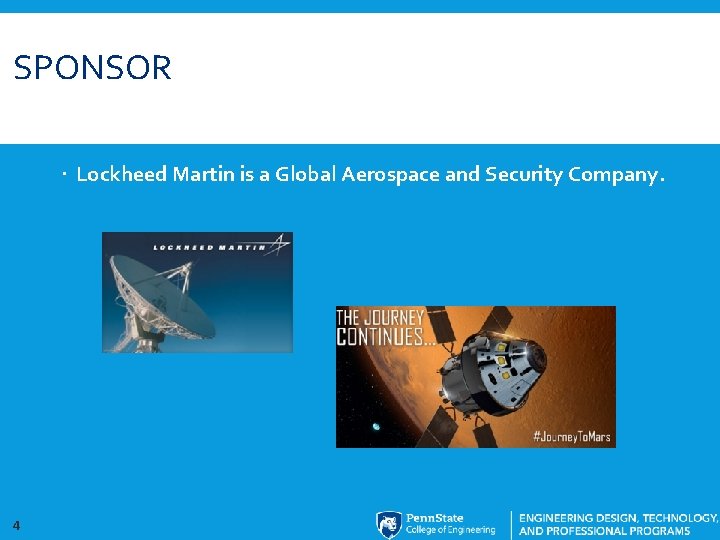
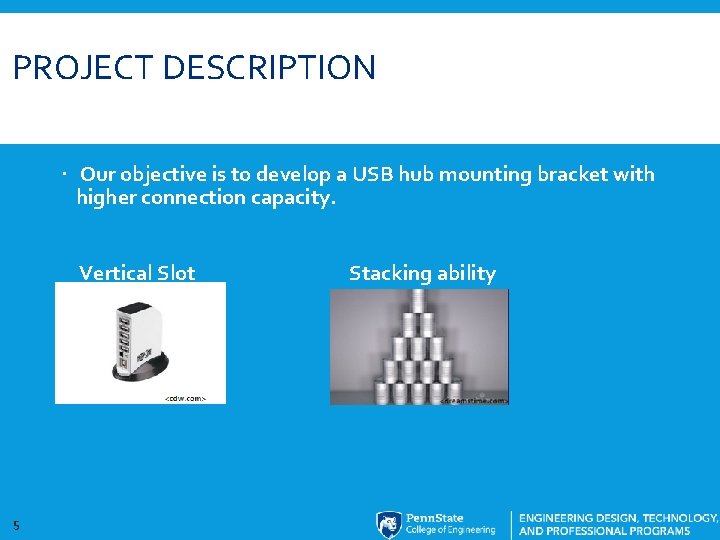
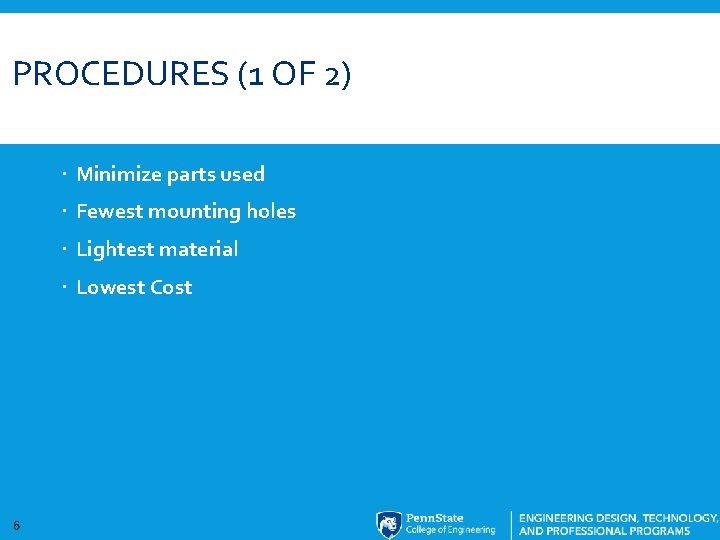
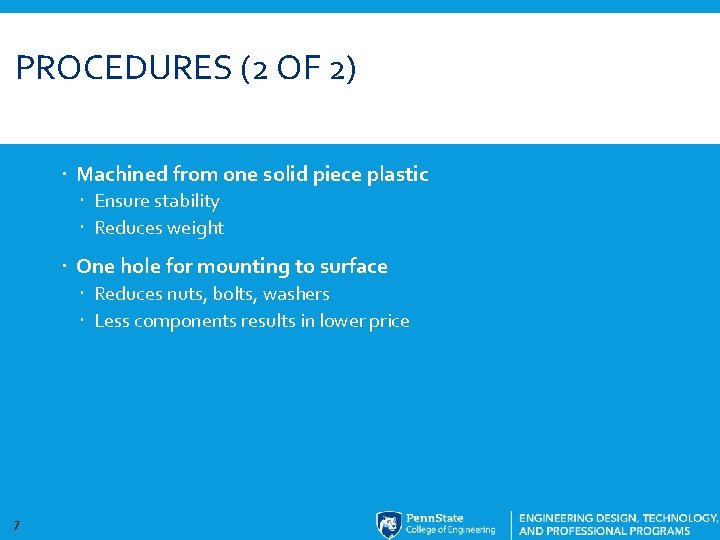
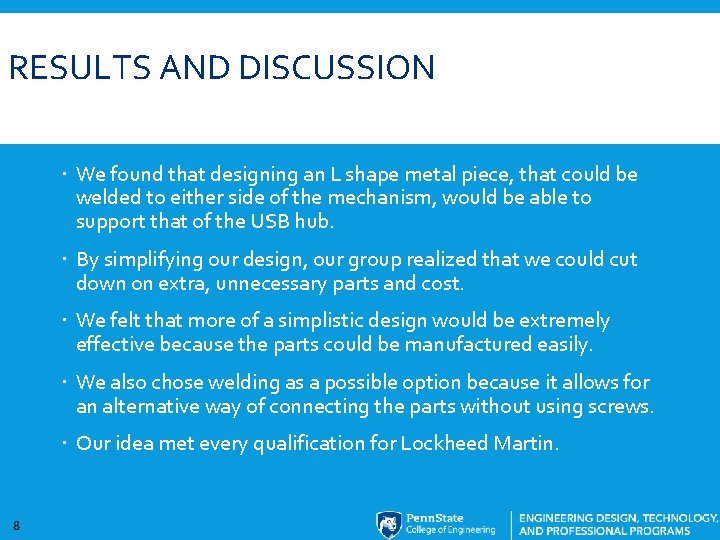
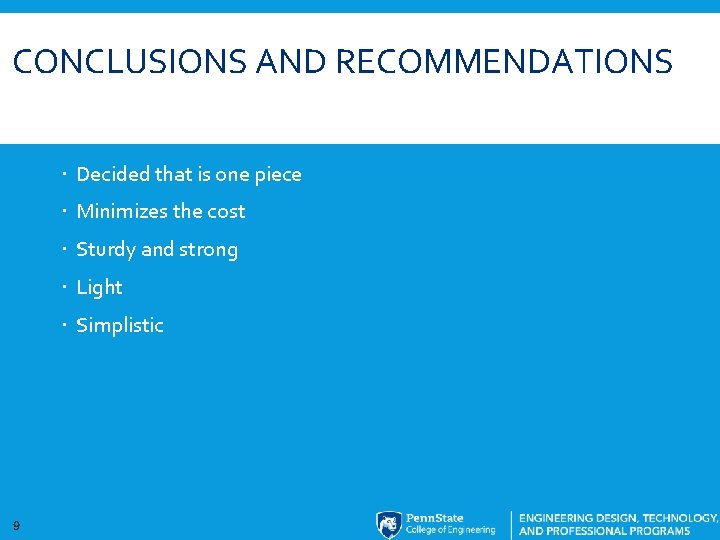
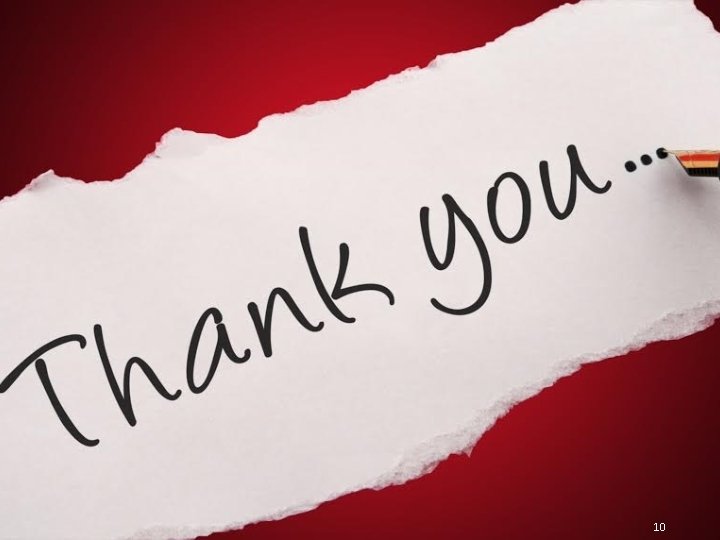
- Slides: 10
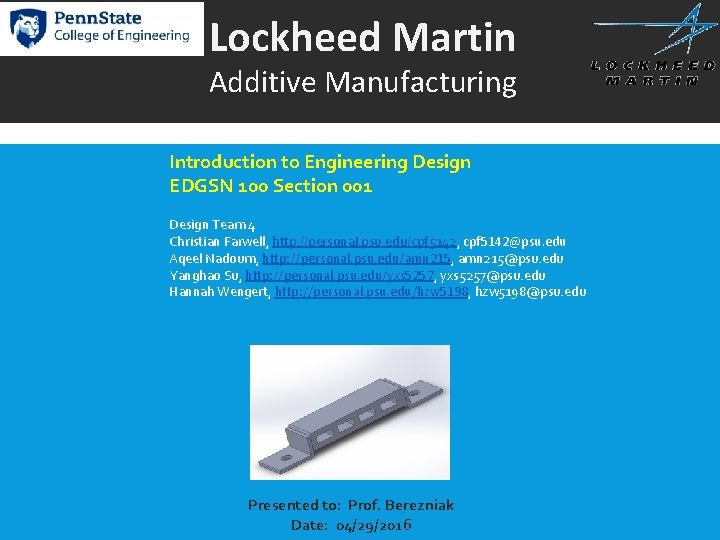
Lockheed Martin Additive Manufacturing Introduction to Engineering Design EDGSN 100 Section 001 Design Team 4 Christian Farwell, http: //personal. psu. edu/cpf 5142, cpf 5142@psu. edu Aqeel Nadoum, http: //personal. psu. edu/amn 215, amn 215@psu. edu Yanghao Su, http: //personal. psu. edu/yxs 5257, yxs 5257@psu. edu Hannah Wengert, http: //personal. psu. edu/hzw 5198, hzw 5198@psu. edu Presented to: Prof. Berezniak Date: 04/29/2016
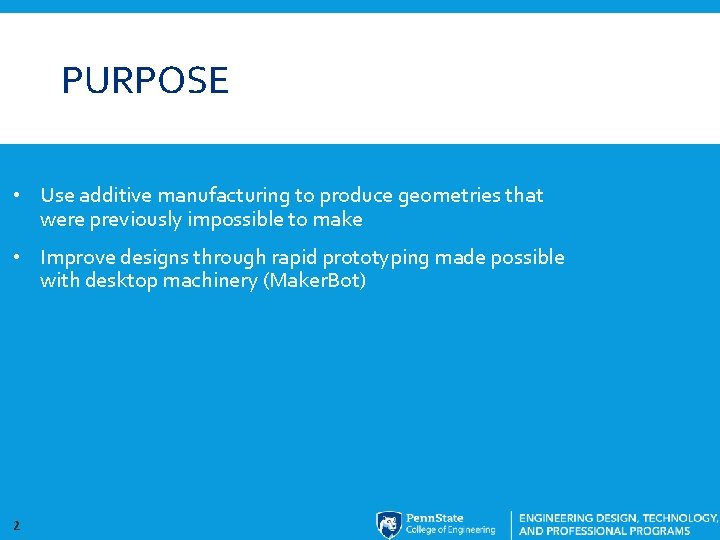
PURPOSE • Use additive manufacturing to produce geometries that were previously impossible to make • Improve designs through rapid prototyping made possible with desktop machinery (Maker. Bot) 2
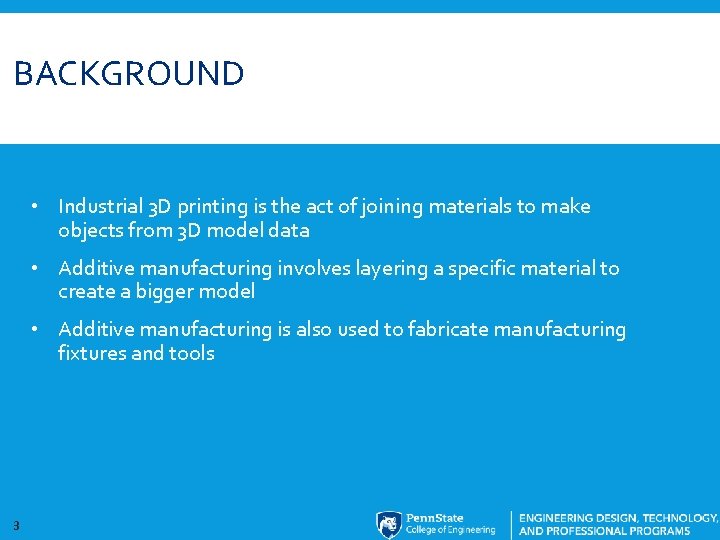
BACKGROUND • Industrial 3 D printing is the act of joining materials to make objects from 3 D model data • Additive manufacturing involves layering a specific material to create a bigger model • Additive manufacturing is also used to fabricate manufacturing fixtures and tools 3
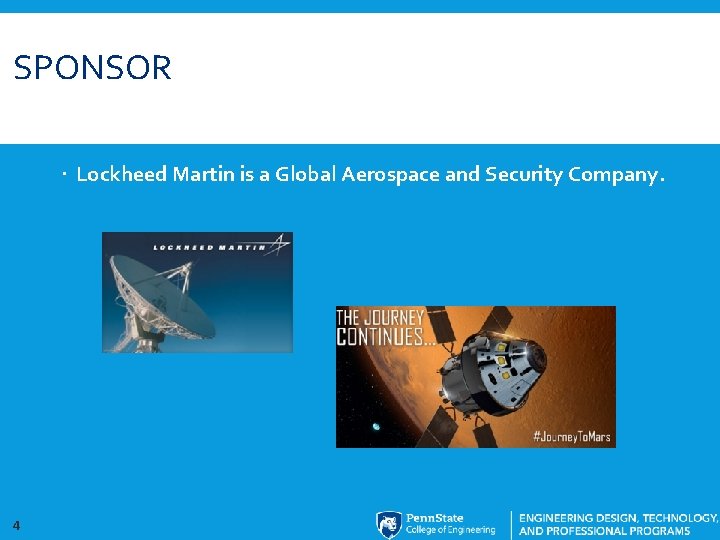
SPONSOR Lockheed Martin is a Global Aerospace and Security Company. 4
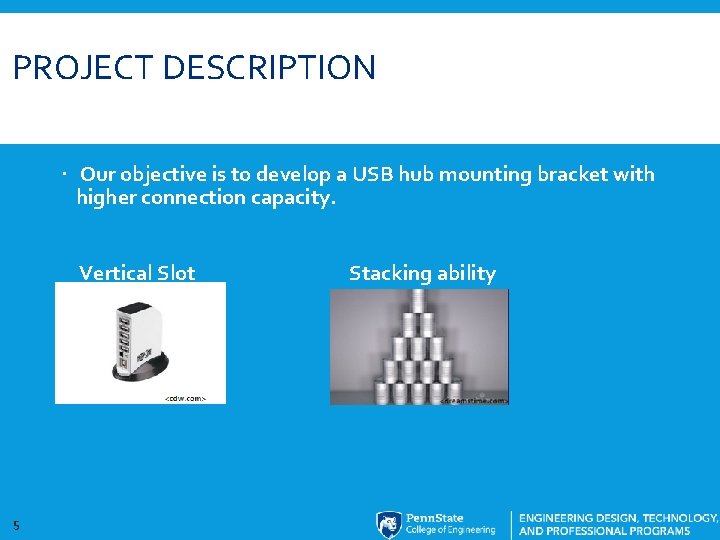
PROJECT DESCRIPTION Our objective is to develop a USB hub mounting bracket with higher connection capacity. Vertical Slot 5 Stacking ability
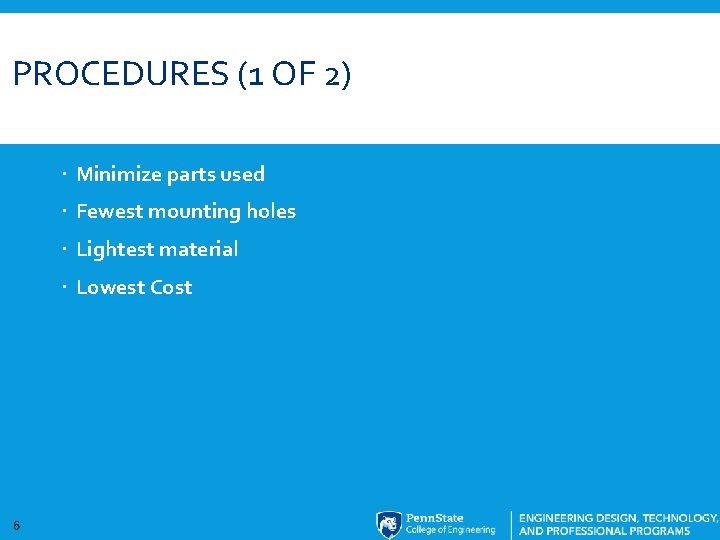
PROCEDURES (1 OF 2) Minimize parts used Fewest mounting holes Lightest material Lowest Cost 6
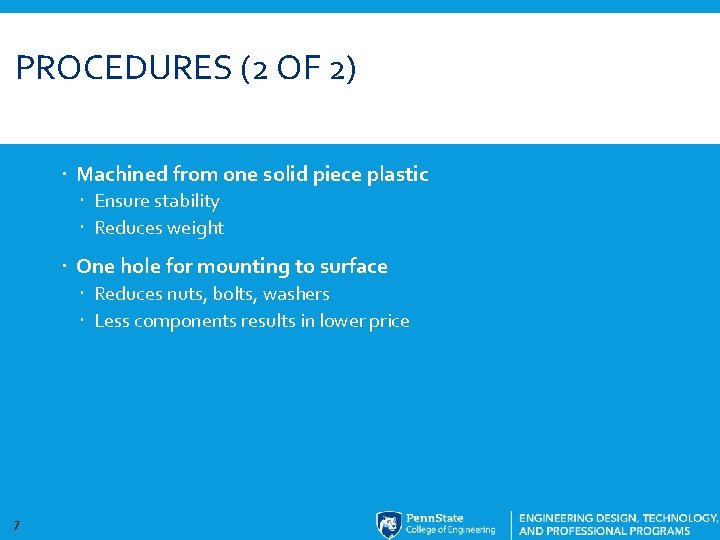
PROCEDURES (2 OF 2) Machined from one solid piece plastic Ensure stability Reduces weight One hole for mounting to surface Reduces nuts, bolts, washers Less components results in lower price 7
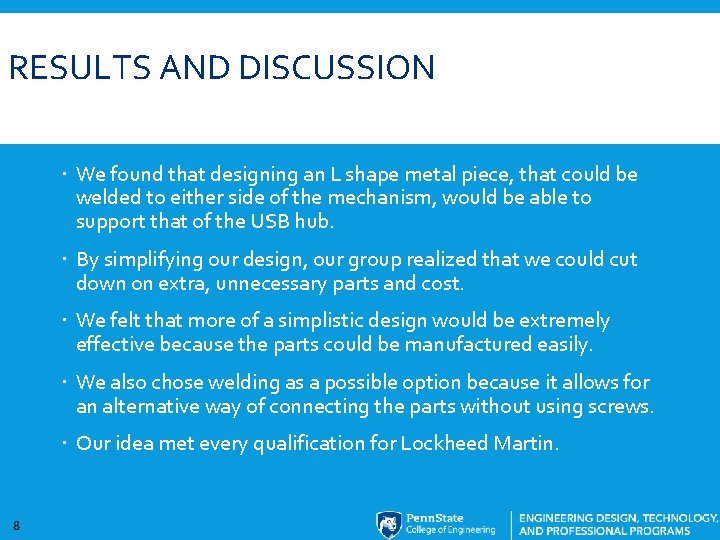
RESULTS AND DISCUSSION We found that designing an L shape metal piece, that could be welded to either side of the mechanism, would be able to support that of the USB hub. By simplifying our design, our group realized that we could cut down on extra, unnecessary parts and cost. We felt that more of a simplistic design would be extremely effective because the parts could be manufactured easily. We also chose welding as a possible option because it allows for an alternative way of connecting the parts without using screws. Our idea met every qualification for Lockheed Martin. 8
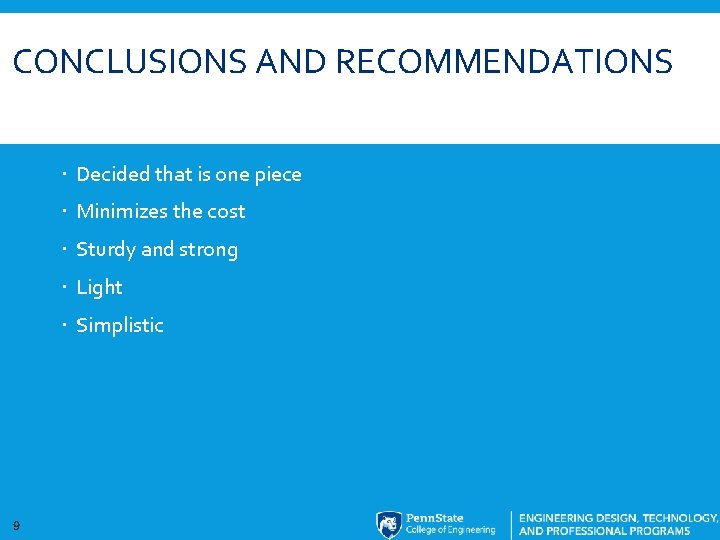
CONCLUSIONS AND RECOMMENDATIONS Decided that is one piece Minimizes the cost Sturdy and strong Light Simplistic 9
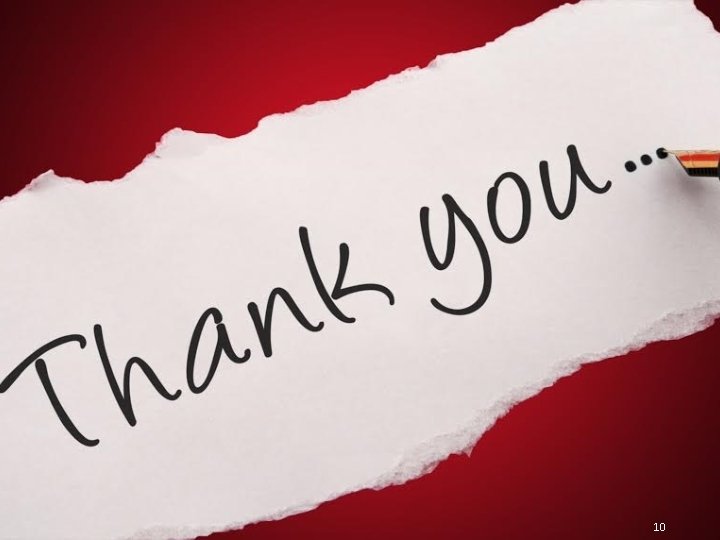
10