LCLSII Prototype Vacuum Vessel VV and Helium Gas

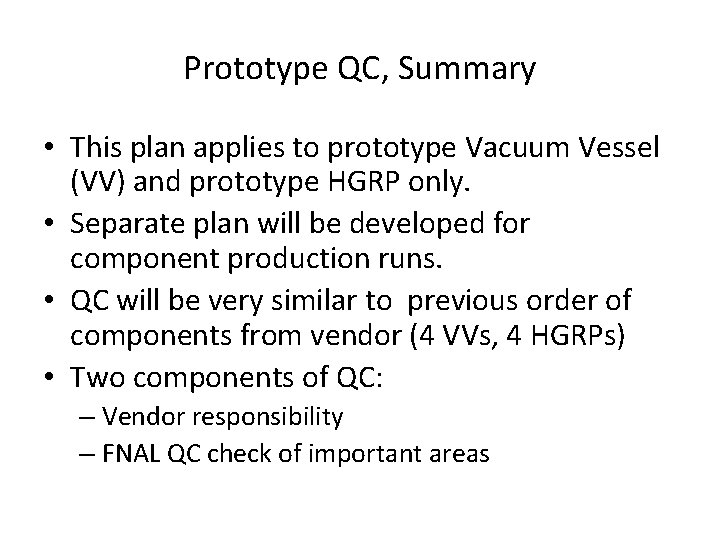
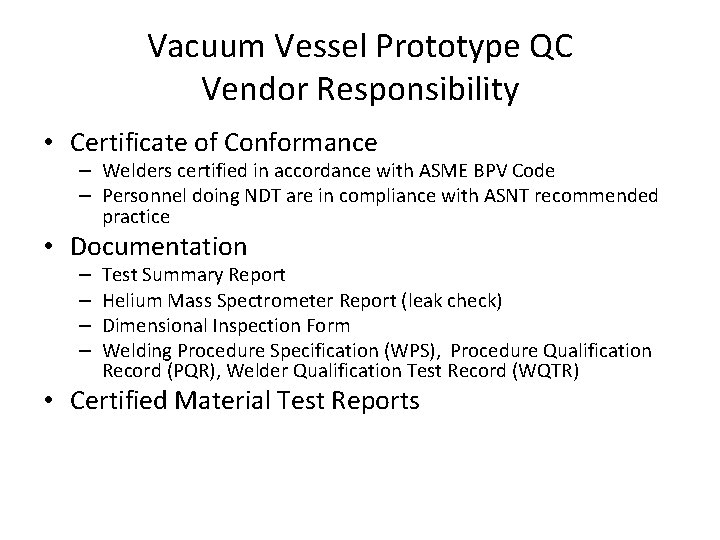
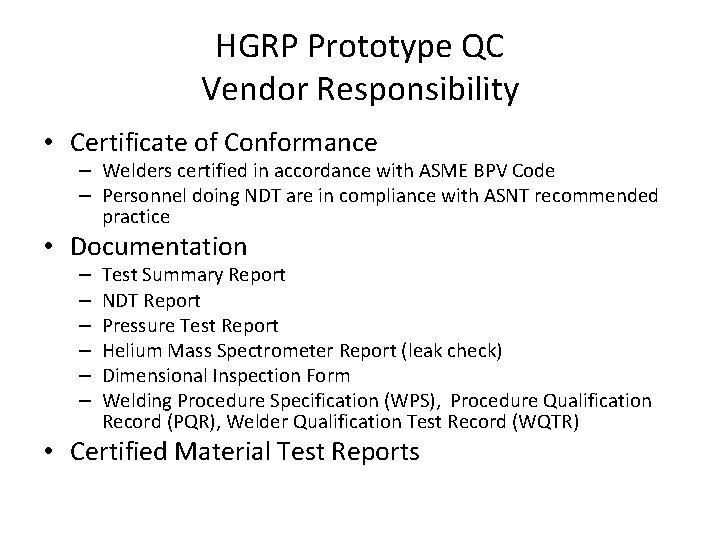
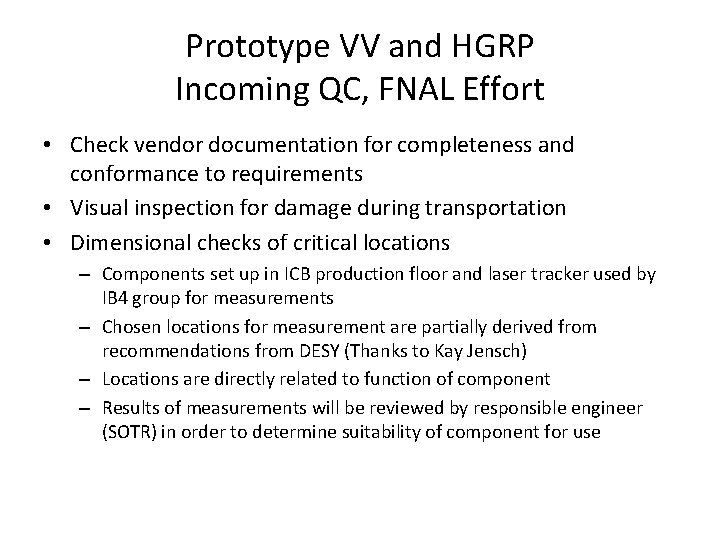
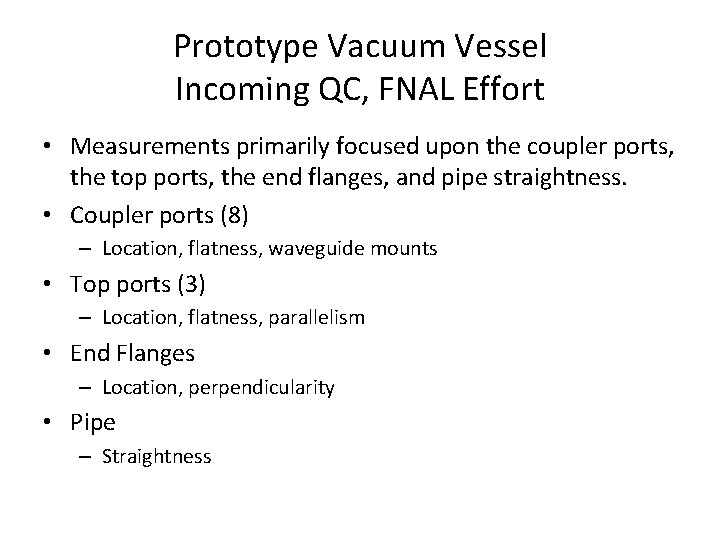
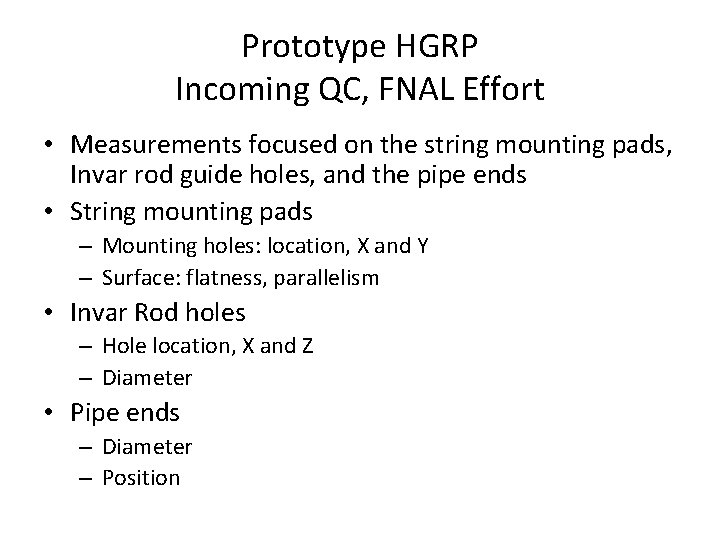

- Slides: 8

LCLS-II Prototype Vacuum Vessel (VV) and Helium Gas Return Pipe (HGRP) FDR Planned Quality Control Effort (QC) Ken Premo 12/04/14
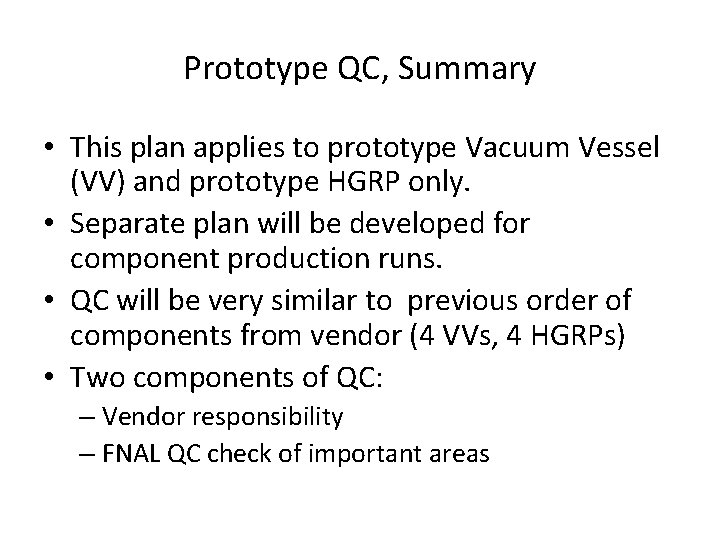
Prototype QC, Summary • This plan applies to prototype Vacuum Vessel (VV) and prototype HGRP only. • Separate plan will be developed for component production runs. • QC will be very similar to previous order of components from vendor (4 VVs, 4 HGRPs) • Two components of QC: – Vendor responsibility – FNAL QC check of important areas
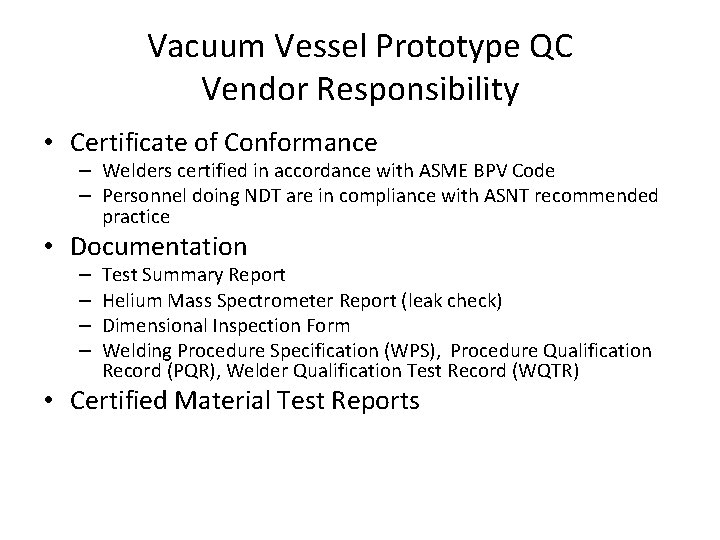
Vacuum Vessel Prototype QC Vendor Responsibility • Certificate of Conformance – Welders certified in accordance with ASME BPV Code – Personnel doing NDT are in compliance with ASNT recommended practice • Documentation – – Test Summary Report Helium Mass Spectrometer Report (leak check) Dimensional Inspection Form Welding Procedure Specification (WPS), Procedure Qualification Record (PQR), Welder Qualification Test Record (WQTR) • Certified Material Test Reports
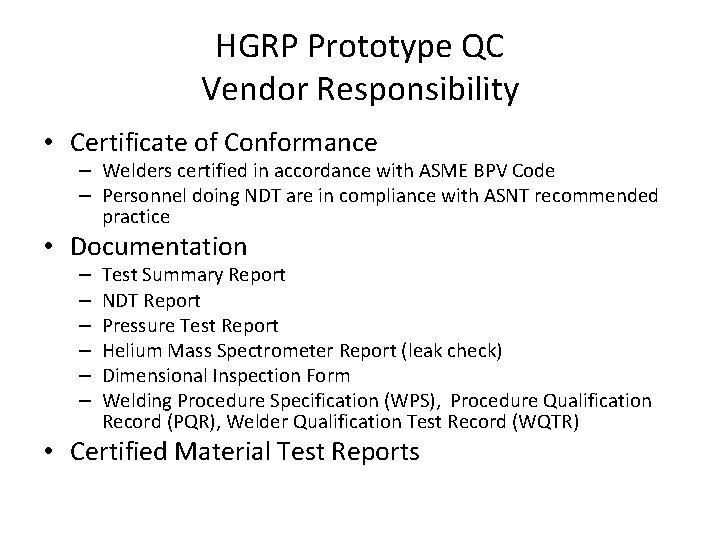
HGRP Prototype QC Vendor Responsibility • Certificate of Conformance – Welders certified in accordance with ASME BPV Code – Personnel doing NDT are in compliance with ASNT recommended practice • Documentation – – – Test Summary Report NDT Report Pressure Test Report Helium Mass Spectrometer Report (leak check) Dimensional Inspection Form Welding Procedure Specification (WPS), Procedure Qualification Record (PQR), Welder Qualification Test Record (WQTR) • Certified Material Test Reports
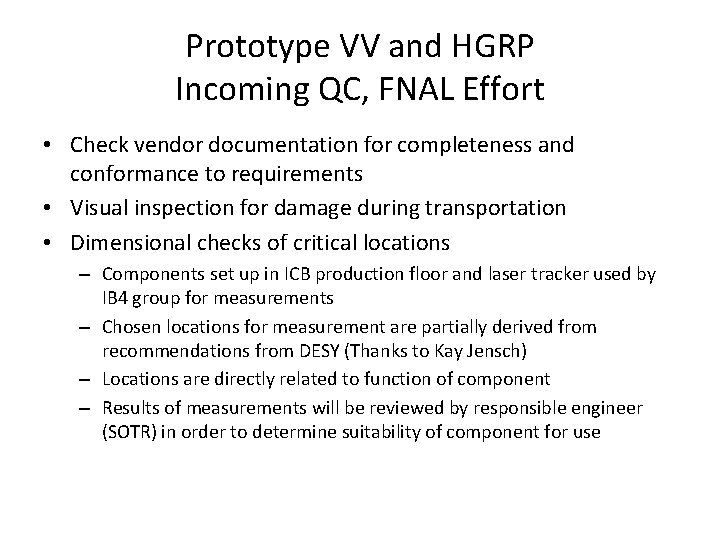
Prototype VV and HGRP Incoming QC, FNAL Effort • Check vendor documentation for completeness and conformance to requirements • Visual inspection for damage during transportation • Dimensional checks of critical locations – Components set up in ICB production floor and laser tracker used by IB 4 group for measurements – Chosen locations for measurement are partially derived from recommendations from DESY (Thanks to Kay Jensch) – Locations are directly related to function of component – Results of measurements will be reviewed by responsible engineer (SOTR) in order to determine suitability of component for use
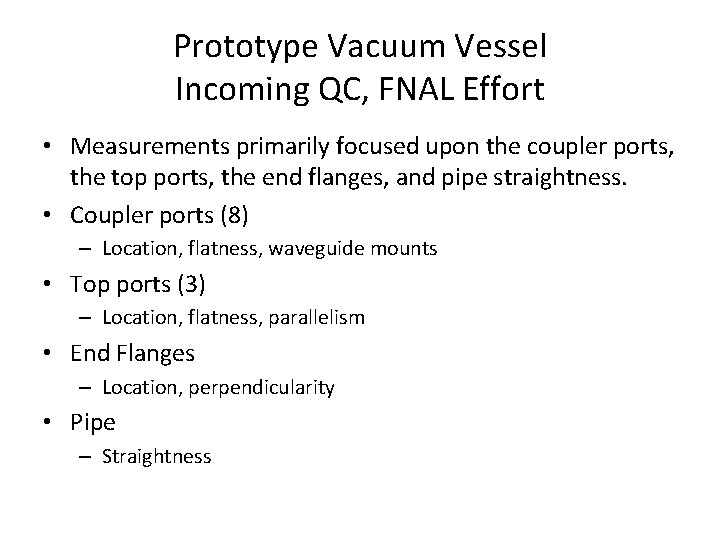
Prototype Vacuum Vessel Incoming QC, FNAL Effort • Measurements primarily focused upon the coupler ports, the top ports, the end flanges, and pipe straightness. • Coupler ports (8) – Location, flatness, waveguide mounts • Top ports (3) – Location, flatness, parallelism • End Flanges – Location, perpendicularity • Pipe – Straightness
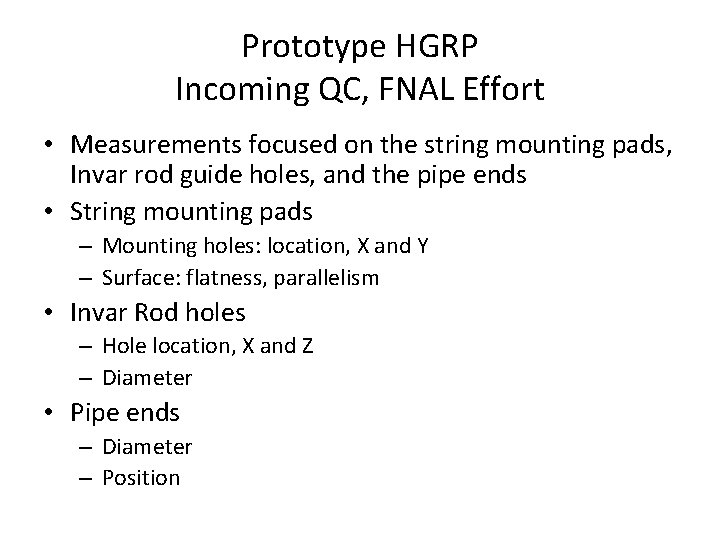
Prototype HGRP Incoming QC, FNAL Effort • Measurements focused on the string mounting pads, Invar rod guide holes, and the pipe ends • String mounting pads – Mounting holes: location, X and Y – Surface: flatness, parallelism • Invar Rod holes – Hole location, X and Z – Diameter • Pipe ends – Diameter – Position

Prototype VV and HGRP Incoming QC, FNAL Effort • Work to be done: – Define serialization scheme for VV and HGRP – Measurement traveler to be developed for QC measurements – Drawings detailing QC measurements required, datum, etc. will be developed; draft QC prints for HGRP currently being reviewed by QC – Summary report of measurement results • Travelers and summary reports will be stored in Vector database (vector. fnal. gov) • Based on experience from prototypes, the initial traveler, drawings, & summary report could be revised prior to production quantities