L 05 C Surface defects Defects arise in
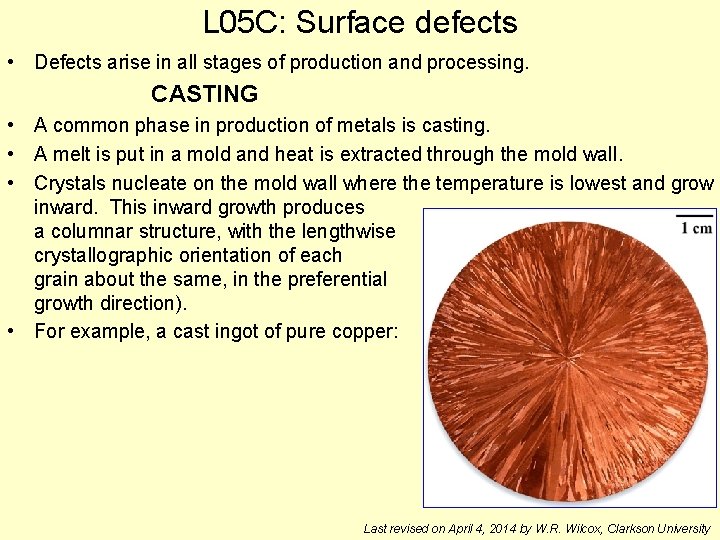
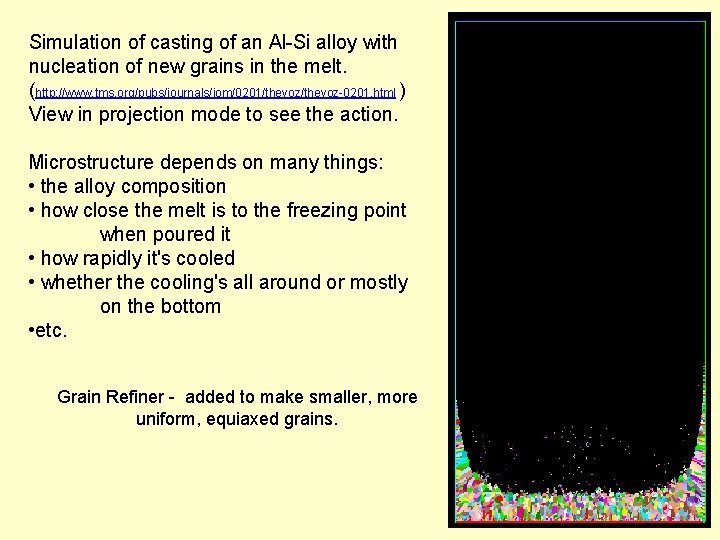
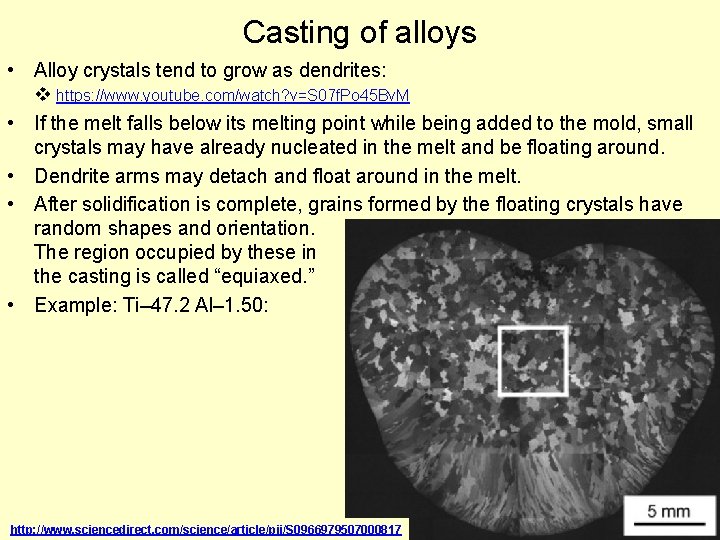
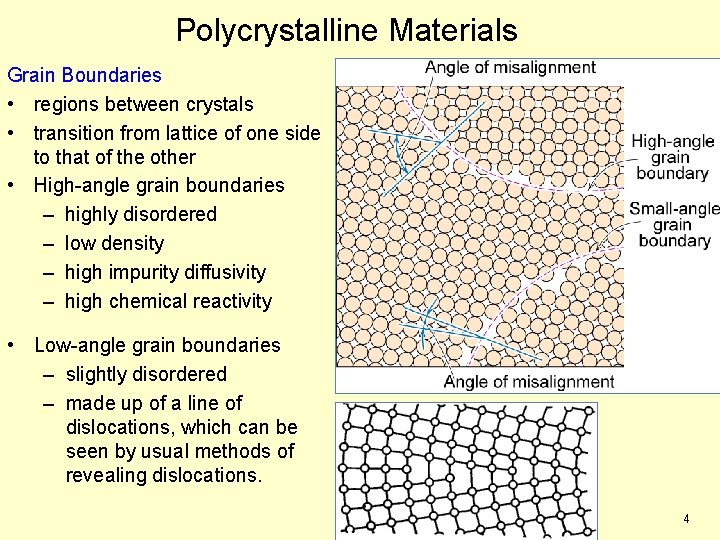
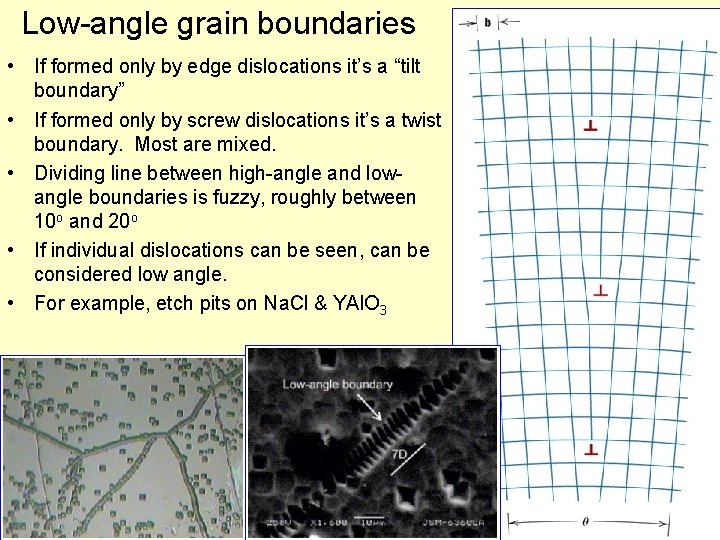
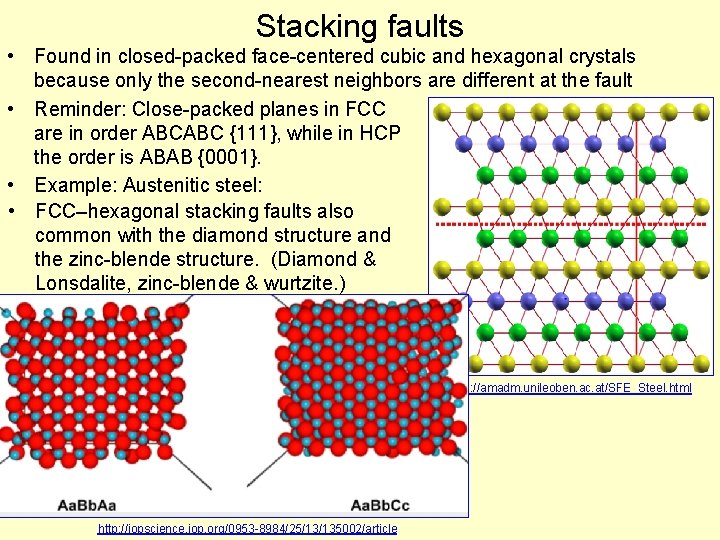
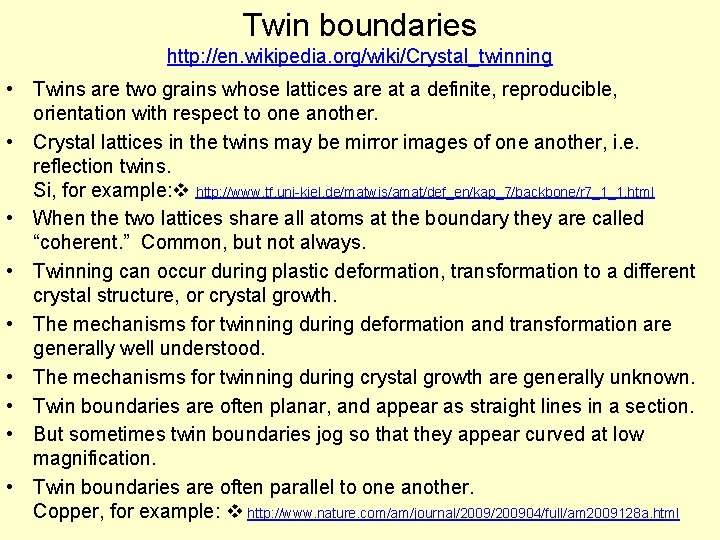
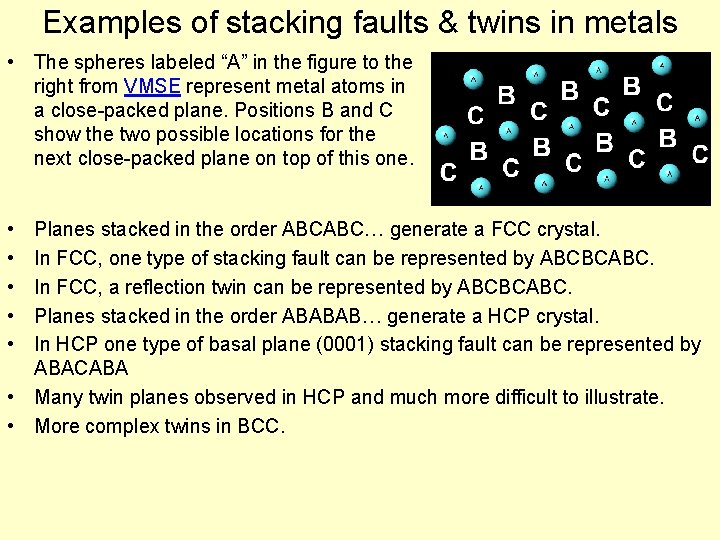
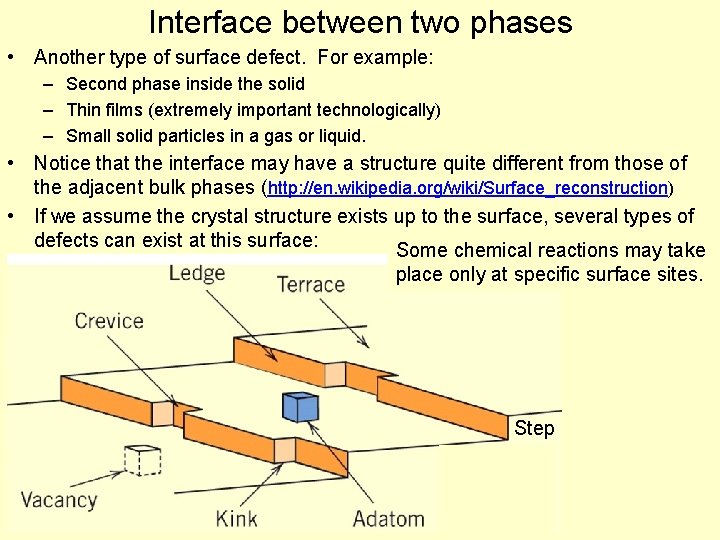
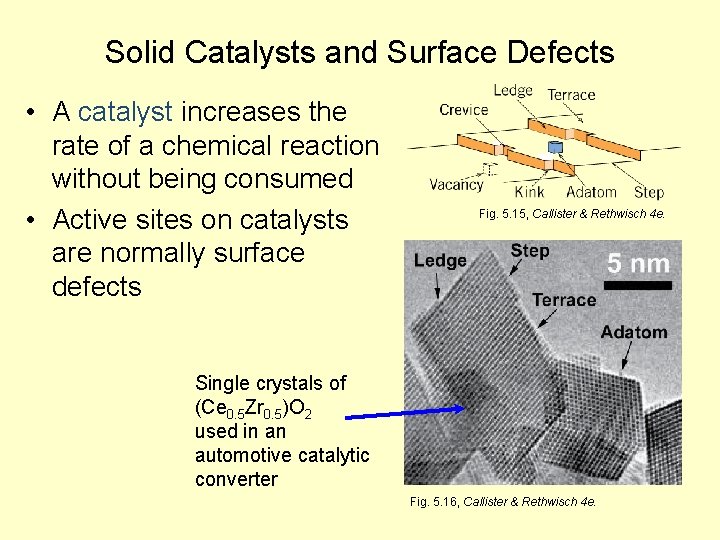
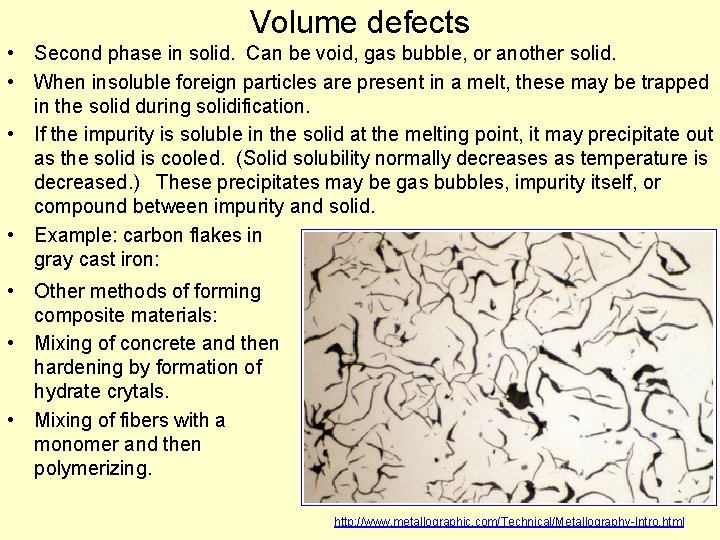
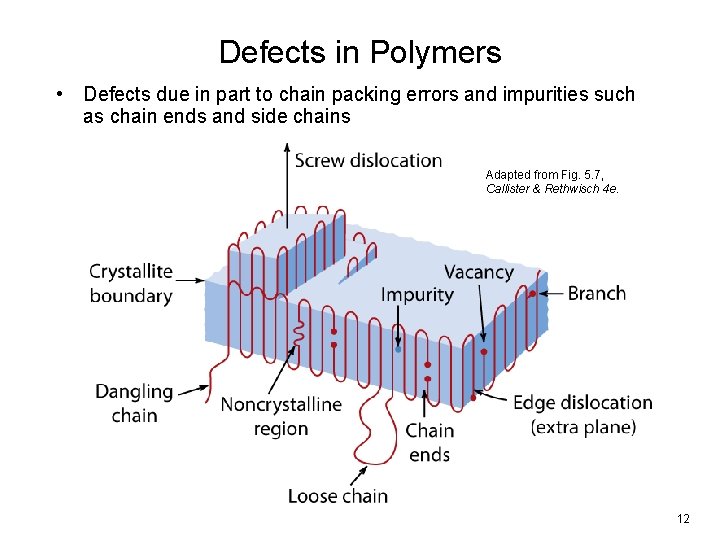
- Slides: 12
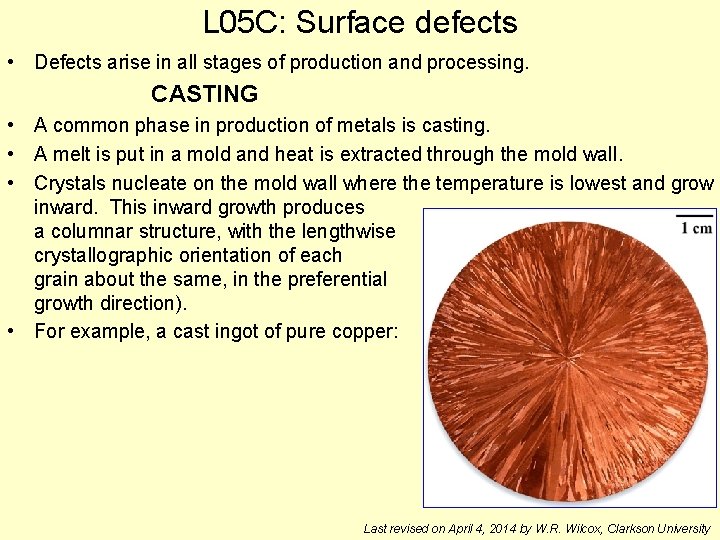
L 05 C: Surface defects • Defects arise in all stages of production and processing. CASTING • A common phase in production of metals is casting. • A melt is put in a mold and heat is extracted through the mold wall. • Crystals nucleate on the mold wall where the temperature is lowest and grow inward. This inward growth produces a columnar structure, with the lengthwise crystallographic orientation of each grain about the same, in the preferential growth direction). • For example, a cast ingot of pure copper: Last revised on April 4, 2014 by W. R. Wilcox, Clarkson University
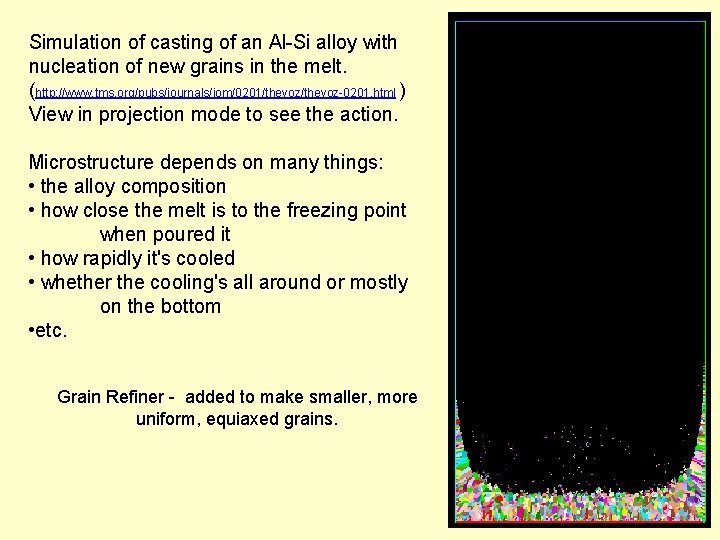
Simulation of casting of an Al-Si alloy with nucleation of new grains in the melt. (http: //www. tms. org/pubs/journals/jom/0201/thevoz-0201. html ) View in projection mode to see the action. Microstructure depends on many things: • the alloy composition • how close the melt is to the freezing point when poured it • how rapidly it's cooled • whether the cooling's all around or mostly on the bottom • etc. Grain Refiner - added to make smaller, more uniform, equiaxed grains.
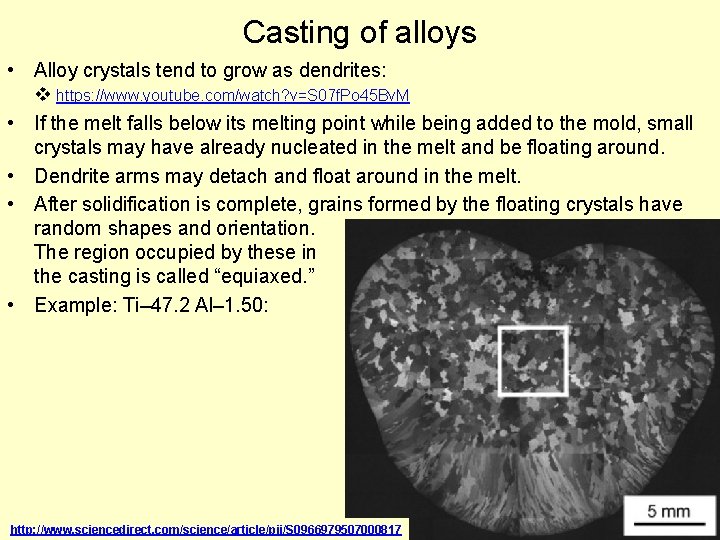
Casting of alloys • Alloy crystals tend to grow as dendrites: https: //www. youtube. com/watch? v=S 07 f. Po 45 Bv. M • If the melt falls below its melting point while being added to the mold, small crystals may have already nucleated in the melt and be floating around. • Dendrite arms may detach and float around in the melt. • After solidification is complete, grains formed by the floating crystals have random shapes and orientation. The region occupied by these in the casting is called “equiaxed. ” • Example: Ti– 47. 2 Al– 1. 50: http: //www. sciencedirect. com/science/article/pii/S 0966979507000817
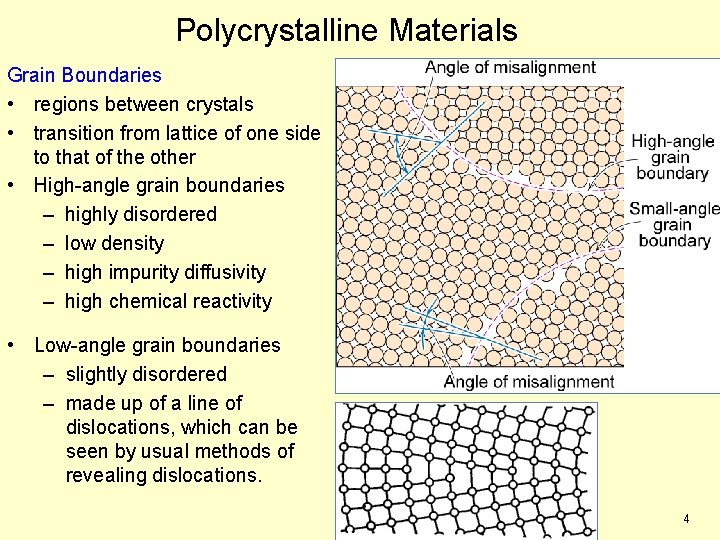
Polycrystalline Materials Grain Boundaries • regions between crystals • transition from lattice of one side to that of the other • High-angle grain boundaries – highly disordered – low density – high impurity diffusivity – high chemical reactivity • Low-angle grain boundaries – slightly disordered – made up of a line of dislocations, which can be seen by usual methods of revealing dislocations. 4
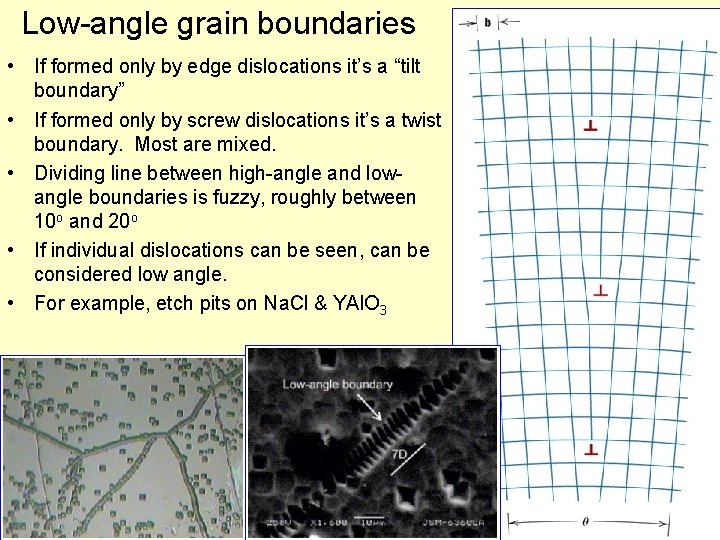
Low-angle grain boundaries • If formed only by edge dislocations it’s a “tilt boundary” • If formed only by screw dislocations it’s a twist boundary. Most are mixed. • Dividing line between high-angle and lowangle boundaries is fuzzy, roughly between 10 o and 20 o • If individual dislocations can be seen, can be considered low angle. • For example, etch pits on Na. Cl & YAl. O 3
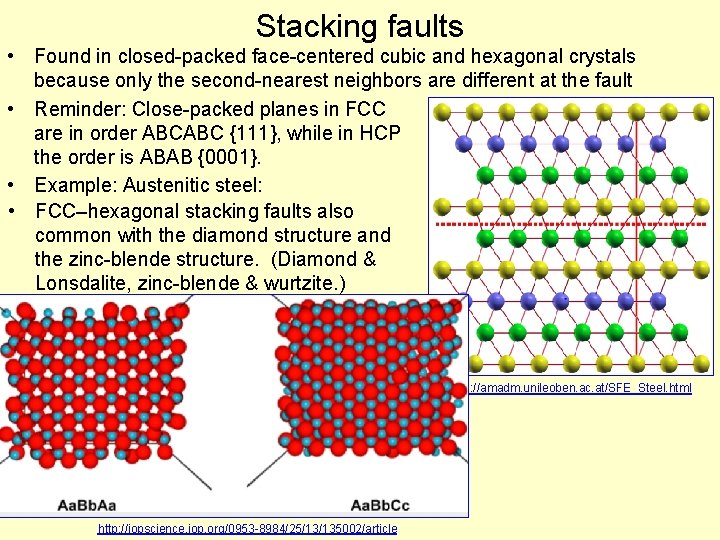
Stacking faults • Found in closed-packed face-centered cubic and hexagonal crystals because only the second-nearest neighbors are different at the fault • Reminder: Close-packed planes in FCC are in order ABCABC {111}, while in HCP the order is ABAB {0001}. • Example: Austenitic steel: • FCC–hexagonal stacking faults also common with the diamond structure and the zinc-blende structure. (Diamond & Lonsdalite, zinc-blende & wurtzite. ) http: //amadm. unileoben. ac. at/SFE_Steel. html http: //iopscience. iop. org/0953 -8984/25/13/135002/article
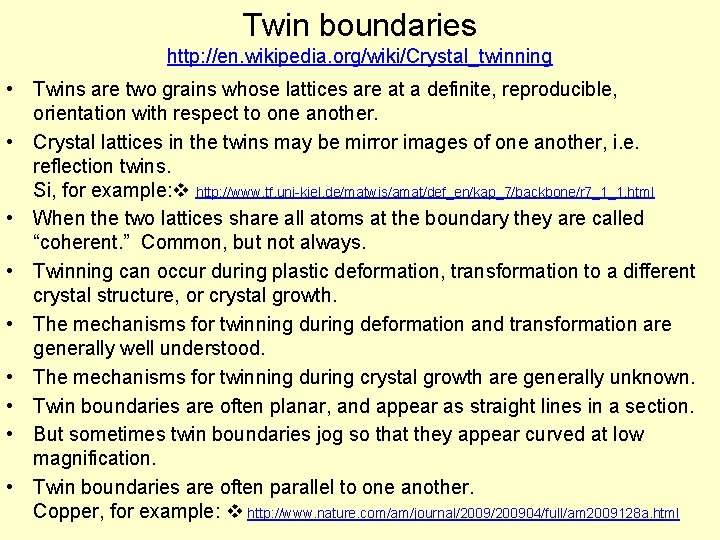
Twin boundaries http: //en. wikipedia. org/wiki/Crystal_twinning • Twins are two grains whose lattices are at a definite, reproducible, orientation with respect to one another. • Crystal lattices in the twins may be mirror images of one another, i. e. reflection twins. Si, for example: http: //www. tf. uni-kiel. de/matwis/amat/def_en/kap_7/backbone/r 7_1_1. html • When the two lattices share all atoms at the boundary they are called “coherent. ” Common, but not always. • Twinning can occur during plastic deformation, transformation to a different crystal structure, or crystal growth. • The mechanisms for twinning during deformation and transformation are generally well understood. • The mechanisms for twinning during crystal growth are generally unknown. • Twin boundaries are often planar, and appear as straight lines in a section. • But sometimes twin boundaries jog so that they appear curved at low magnification. • Twin boundaries are often parallel to one another. Copper, for example: http: //www. nature. com/am/journal/200904/full/am 2009128 a. html
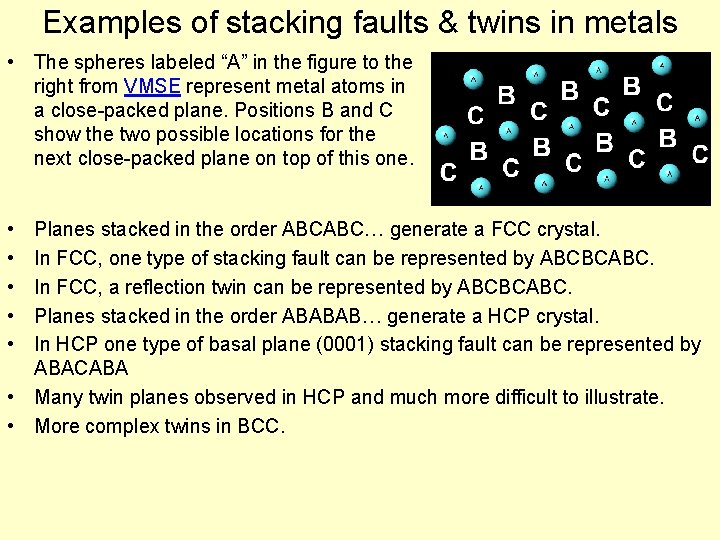
Examples of stacking faults & twins in metals • The spheres labeled “A” in the figure to the right from VMSE represent metal atoms in a close-packed plane. Positions B and C show the two possible locations for the next close-packed plane on top of this one. • • • Planes stacked in the order ABCABC… generate a FCC crystal. In FCC, one type of stacking fault can be represented by ABCBCABC. In FCC, a reflection twin can be represented by ABCBCABC. Planes stacked in the order ABABAB… generate a HCP crystal. In HCP one type of basal plane (0001) stacking fault can be represented by ABACABA • Many twin planes observed in HCP and much more difficult to illustrate. • More complex twins in BCC.
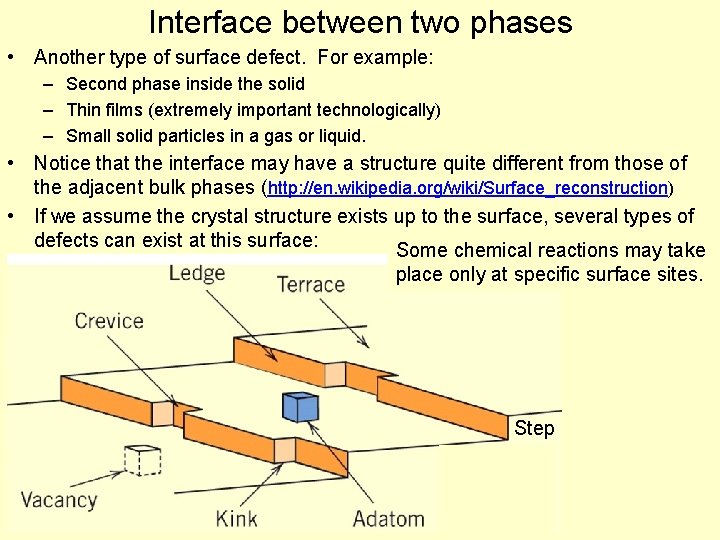
Interface between two phases • Another type of surface defect. For example: – Second phase inside the solid – Thin films (extremely important technologically) – Small solid particles in a gas or liquid. • Notice that the interface may have a structure quite different from those of the adjacent bulk phases (http: //en. wikipedia. org/wiki/Surface_reconstruction) • If we assume the crystal structure exists up to the surface, several types of defects can exist at this surface: Some chemical reactions may take place only at specific surface sites. Step
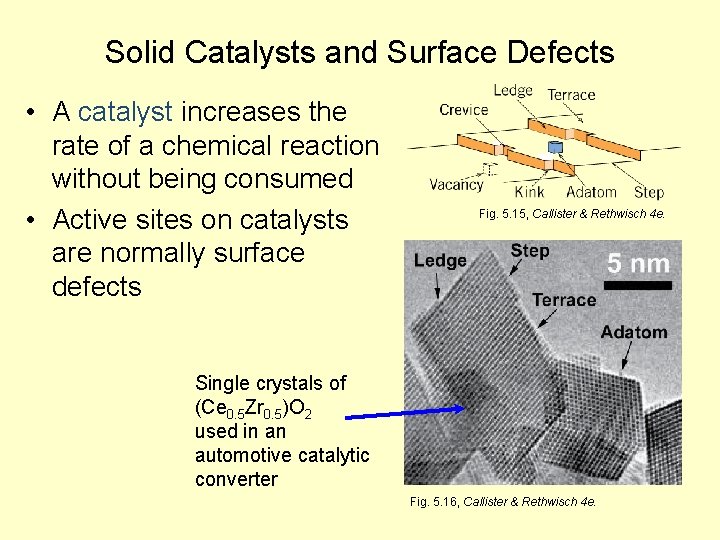
Solid Catalysts and Surface Defects • A catalyst increases the rate of a chemical reaction without being consumed • Active sites on catalysts are normally surface defects Fig. 5. 15, Callister & Rethwisch 4 e. Single crystals of (Ce 0. 5 Zr 0. 5)O 2 used in an automotive catalytic converter Fig. 5. 16, Callister & Rethwisch 4 e.
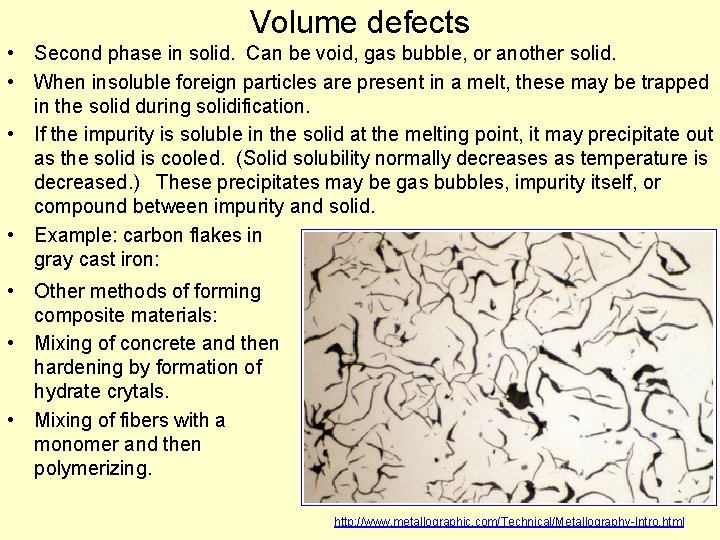
Volume defects • Second phase in solid. Can be void, gas bubble, or another solid. • When insoluble foreign particles are present in a melt, these may be trapped in the solid during solidification. • If the impurity is soluble in the solid at the melting point, it may precipitate out as the solid is cooled. (Solid solubility normally decreases as temperature is decreased. ) These precipitates may be gas bubbles, impurity itself, or compound between impurity and solid. • Example: carbon flakes in gray cast iron: • Other methods of forming composite materials: • Mixing of concrete and then hardening by formation of hydrate crytals. • Mixing of fibers with a monomer and then polymerizing. http: //www. metallographic. com/Technical/Metallography-Intro. html
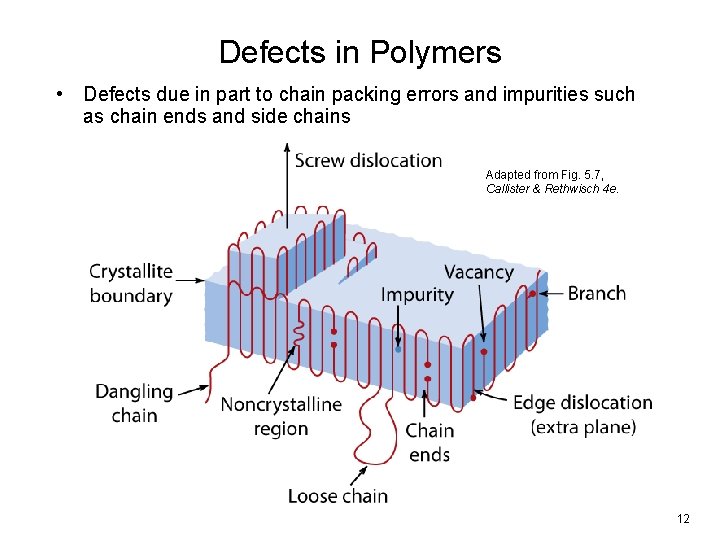
Defects in Polymers • Defects due in part to chain packing errors and impurities such as chain ends and side chains Adapted from Fig. 5. 7, Callister & Rethwisch 4 e. 12
Surface defects examples
Arise to greet the lord of light
Why do territorial conflicts arise among religious groups
Panchal cast
How did the ottoman safavid and mughal empires arise
Arise due to
Why might fishing disputes arise in the region
Summary of the lake isle of innisfree
How does monopoly arise?
Oh church arise
Describe the conditions under which new species may arise.
Aristate antennae
Infinitive simple past and past participle