ENERGY CONVERSION ES 832 a Eric Savory www
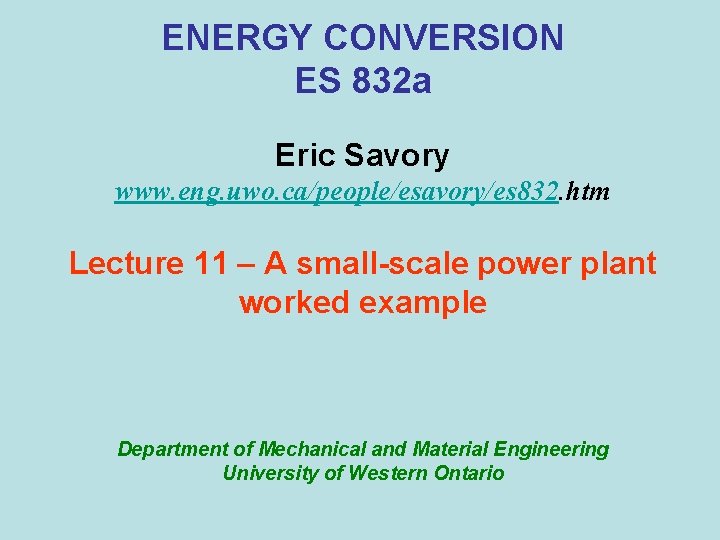
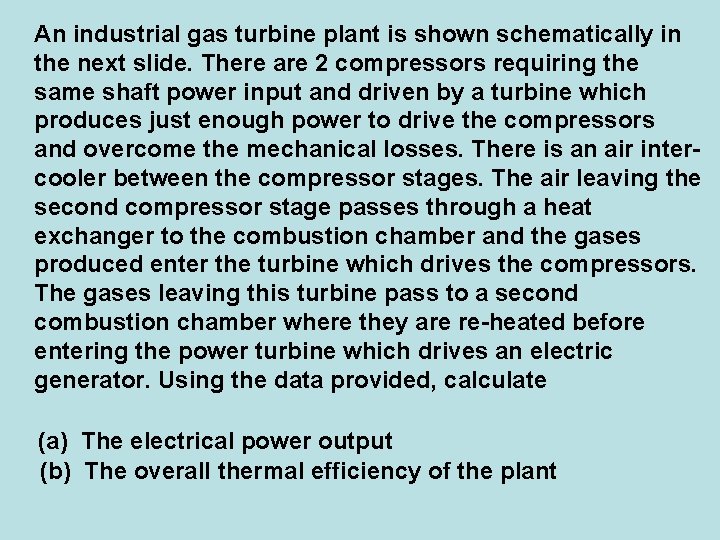
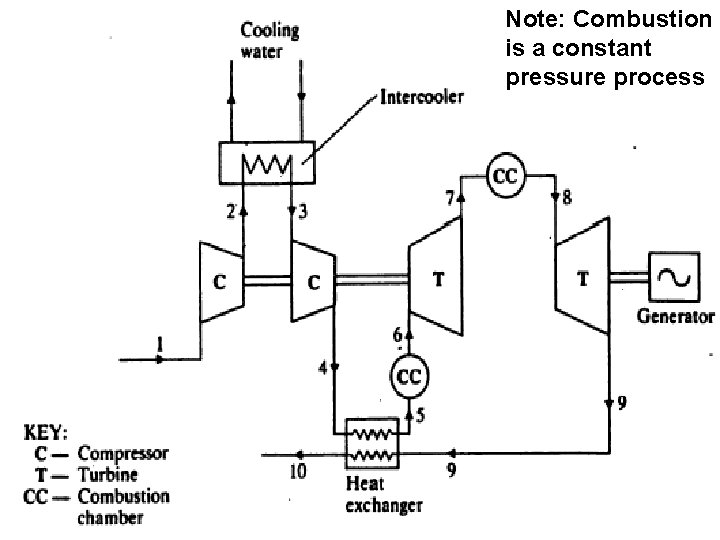
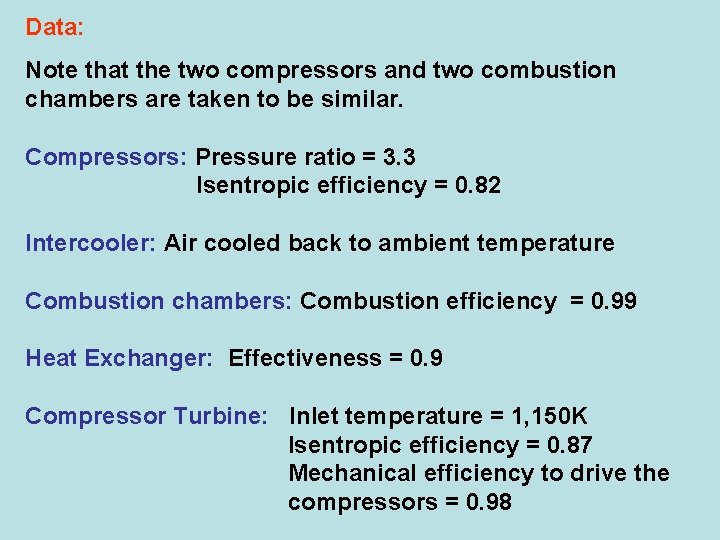
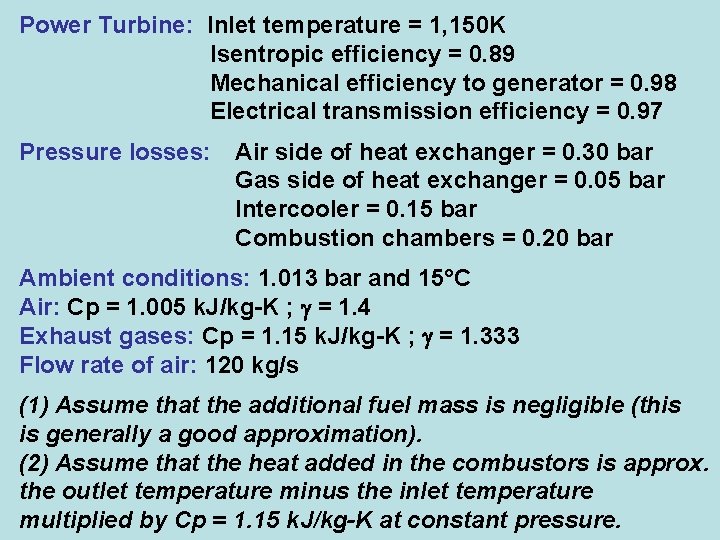
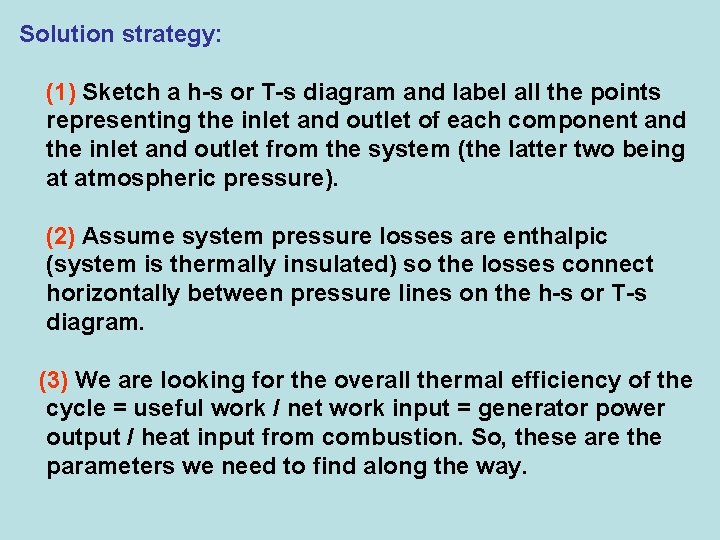
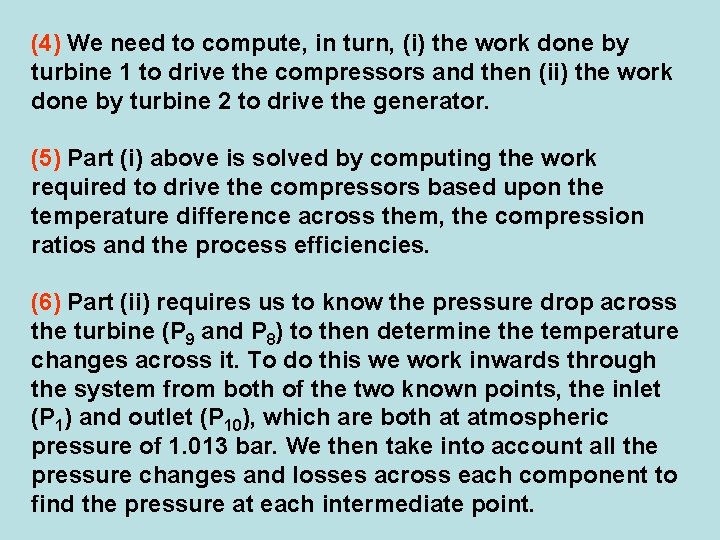
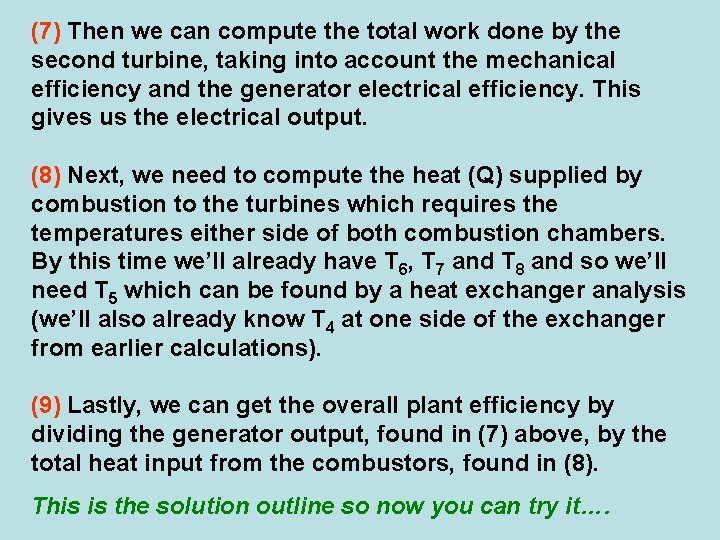
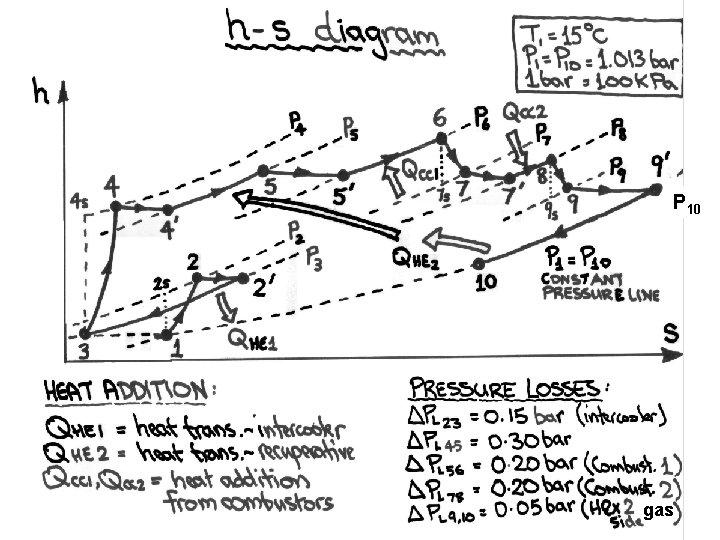
- Slides: 9
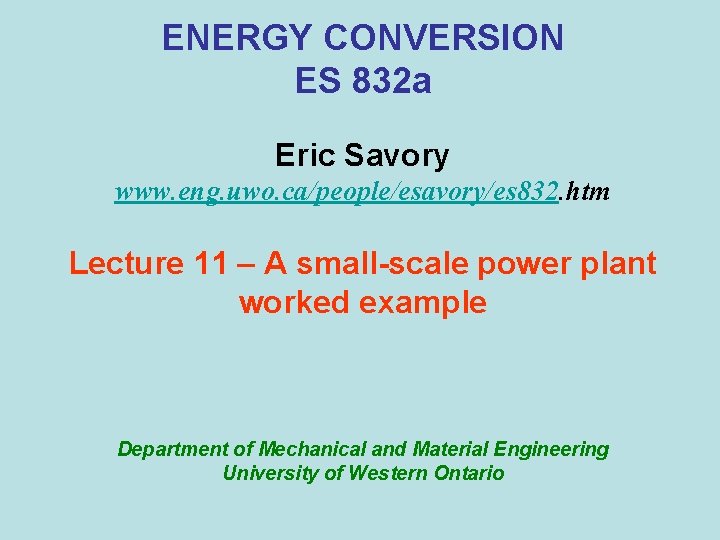
ENERGY CONVERSION ES 832 a Eric Savory www. eng. uwo. ca/people/esavory/es 832. htm Lecture 11 – A small-scale power plant worked example Department of Mechanical and Material Engineering University of Western Ontario
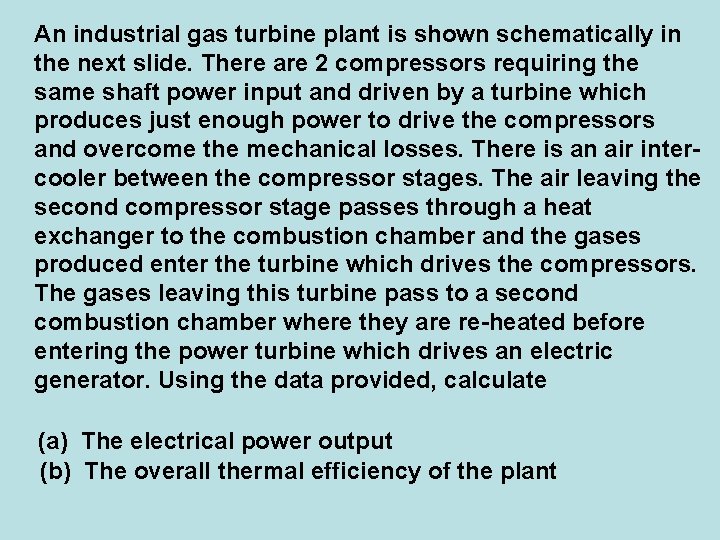
An industrial gas turbine plant is shown schematically in the next slide. There are 2 compressors requiring the same shaft power input and driven by a turbine which produces just enough power to drive the compressors and overcome the mechanical losses. There is an air intercooler between the compressor stages. The air leaving the second compressor stage passes through a heat exchanger to the combustion chamber and the gases produced enter the turbine which drives the compressors. The gases leaving this turbine pass to a second combustion chamber where they are re-heated before entering the power turbine which drives an electric generator. Using the data provided, calculate (a) The electrical power output (b) The overall thermal efficiency of the plant
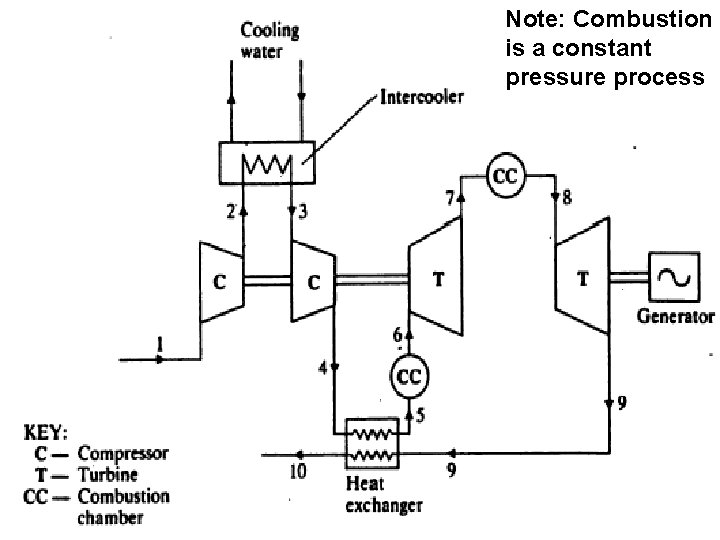
Note: Combustion is a constant pressure process
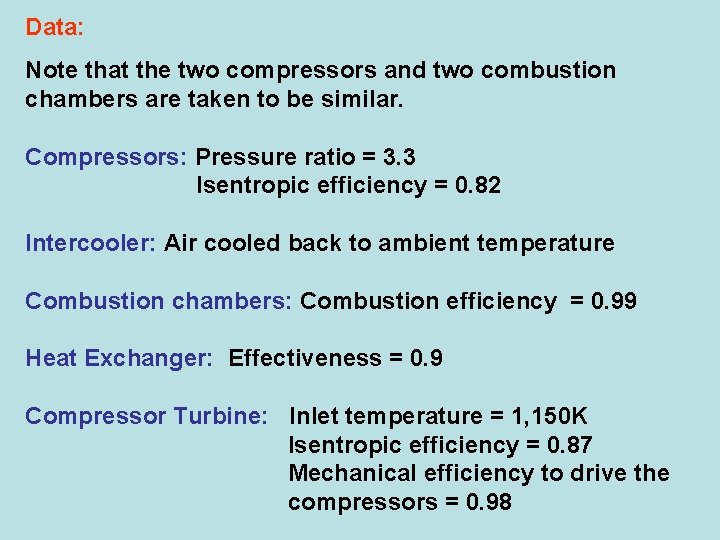
Data: Note that the two compressors and two combustion chambers are taken to be similar. Compressors: Pressure ratio = 3. 3 Isentropic efficiency = 0. 82 Intercooler: Air cooled back to ambient temperature Combustion chambers: Combustion efficiency = 0. 99 Heat Exchanger: Effectiveness = 0. 9 Compressor Turbine: Inlet temperature = 1, 150 K Isentropic efficiency = 0. 87 Mechanical efficiency to drive the compressors = 0. 98
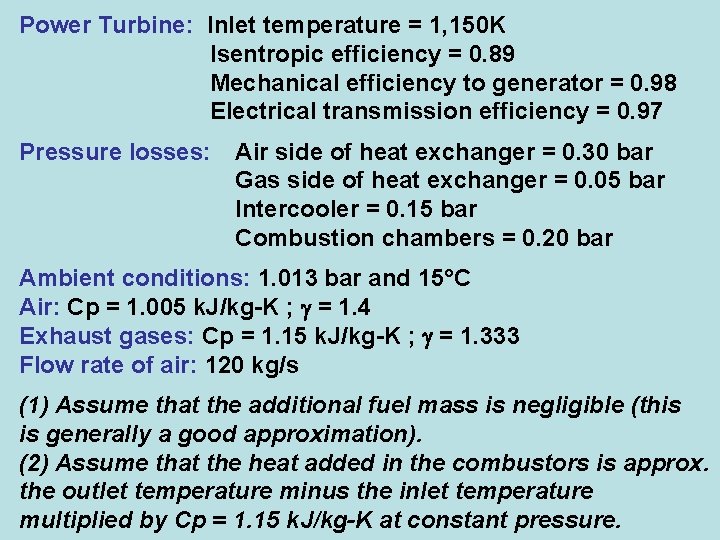
Power Turbine: Inlet temperature = 1, 150 K Isentropic efficiency = 0. 89 Mechanical efficiency to generator = 0. 98 Electrical transmission efficiency = 0. 97 Pressure losses: Air side of heat exchanger = 0. 30 bar Gas side of heat exchanger = 0. 05 bar Intercooler = 0. 15 bar Combustion chambers = 0. 20 bar Ambient conditions: 1. 013 bar and 15°C Air: Cp = 1. 005 k. J/kg-K ; = 1. 4 Exhaust gases: Cp = 1. 15 k. J/kg-K ; = 1. 333 Flow rate of air: 120 kg/s (1) Assume that the additional fuel mass is negligible (this is generally a good approximation). (2) Assume that the heat added in the combustors is approx. the outlet temperature minus the inlet temperature multiplied by Cp = 1. 15 k. J/kg-K at constant pressure.
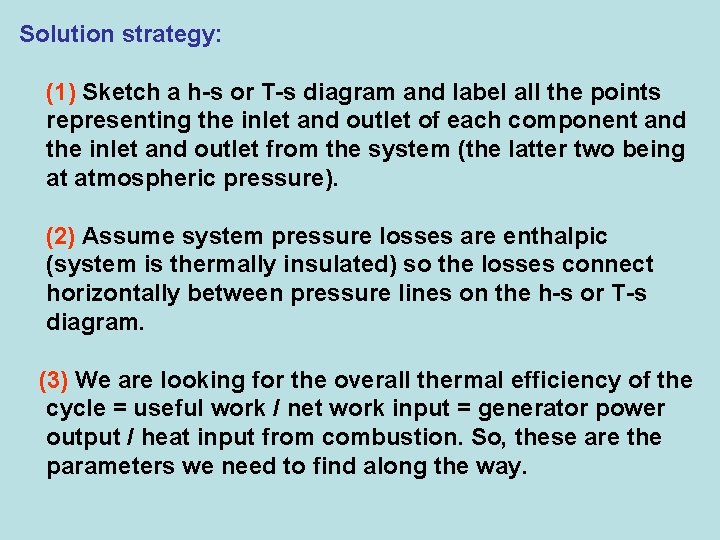
Solution strategy: (1) Sketch a h-s or T-s diagram and label all the points representing the inlet and outlet of each component and the inlet and outlet from the system (the latter two being at atmospheric pressure). (2) Assume system pressure losses are enthalpic (system is thermally insulated) so the losses connect horizontally between pressure lines on the h-s or T-s diagram. (3) We are looking for the overall thermal efficiency of the cycle = useful work / net work input = generator power output / heat input from combustion. So, these are the parameters we need to find along the way.
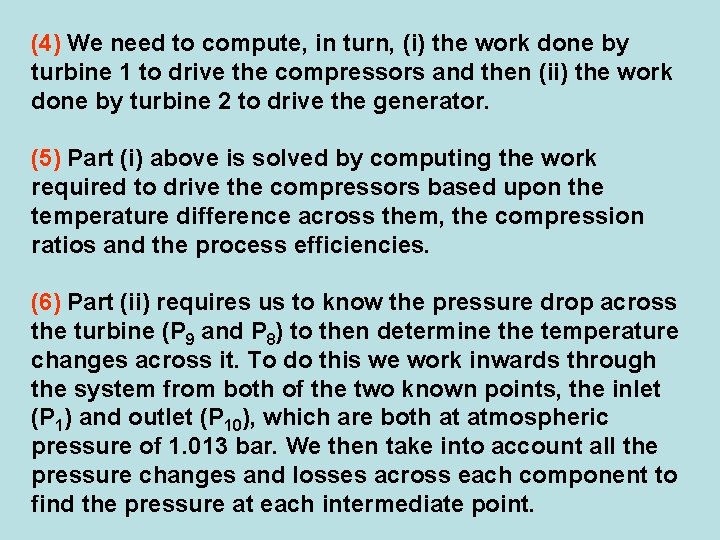
(4) We need to compute, in turn, (i) the work done by turbine 1 to drive the compressors and then (ii) the work done by turbine 2 to drive the generator. (5) Part (i) above is solved by computing the work required to drive the compressors based upon the temperature difference across them, the compression ratios and the process efficiencies. (6) Part (ii) requires us to know the pressure drop across the turbine (P 9 and P 8) to then determine the temperature changes across it. To do this we work inwards through the system from both of the two known points, the inlet (P 1) and outlet (P 10), which are both at atmospheric pressure of 1. 013 bar. We then take into account all the pressure changes and losses across each component to find the pressure at each intermediate point.
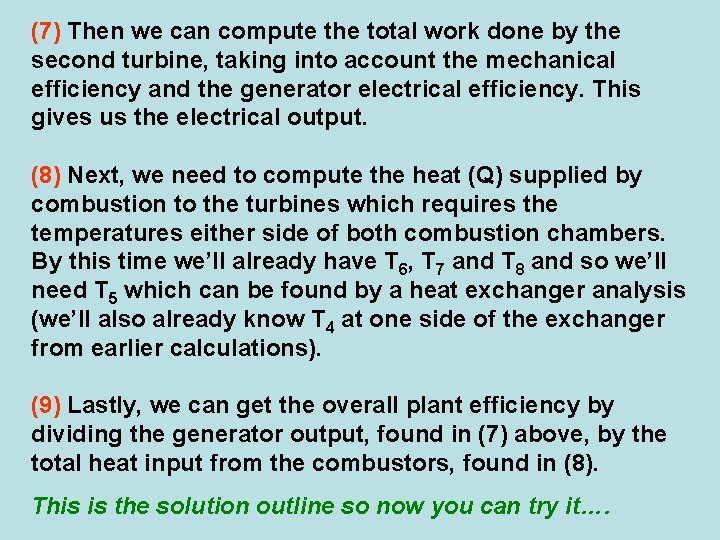
(7) Then we can compute the total work done by the second turbine, taking into account the mechanical efficiency and the generator electrical efficiency. This gives us the electrical output. (8) Next, we need to compute the heat (Q) supplied by combustion to the turbines which requires the temperatures either side of both combustion chambers. By this time we’ll already have T 6, T 7 and T 8 and so we’ll need T 5 which can be found by a heat exchanger analysis (we’ll also already know T 4 at one side of the exchanger from earlier calculations). (9) Lastly, we can get the overall plant efficiency by dividing the generator output, found in (7) above, by the total heat input from the combustors, found in (8). This is the solution outline so now you can try it….
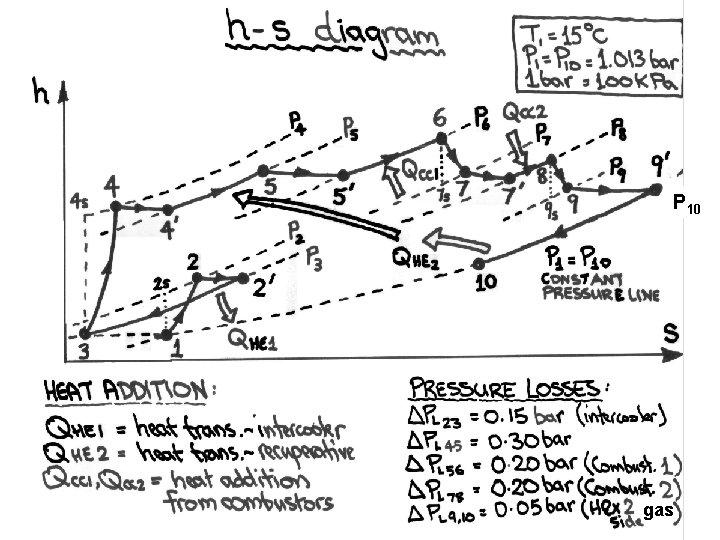
P 10 gas