Distortion Compensation for Lightweight Additive Manufacturing DISCOAM RISE
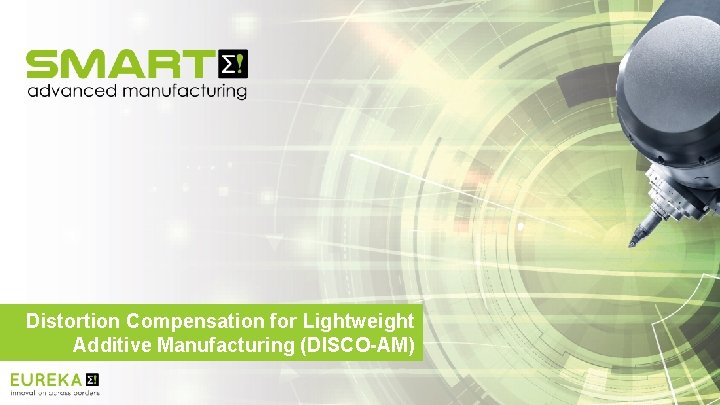
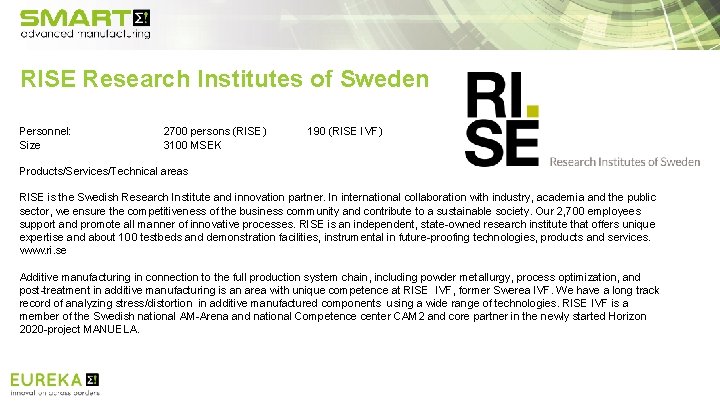
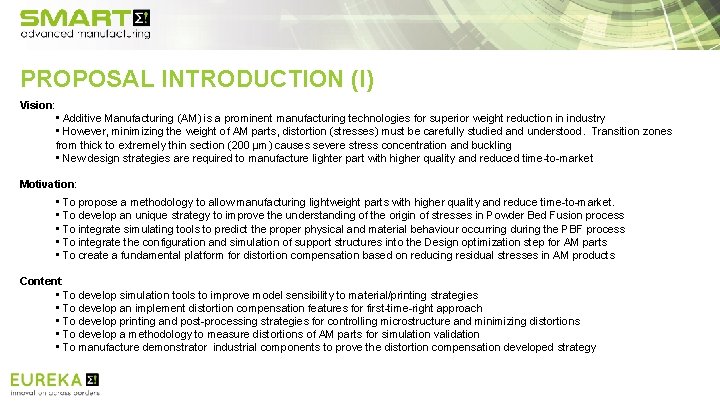
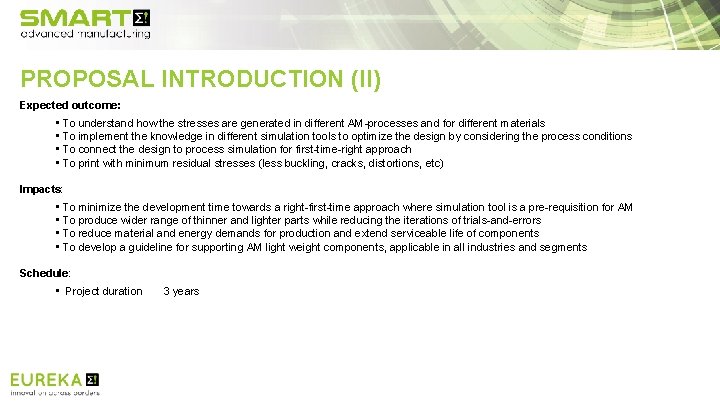
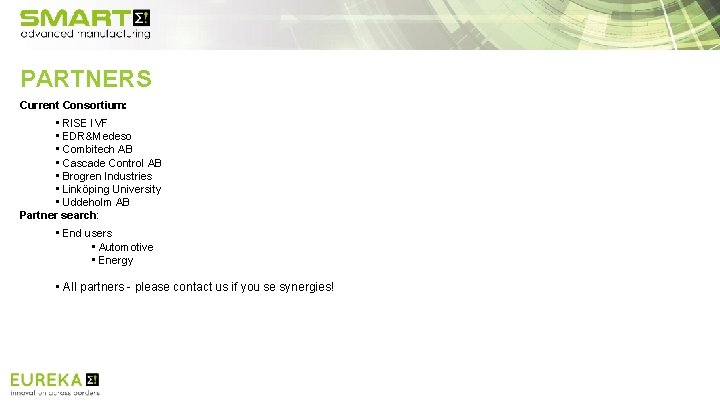
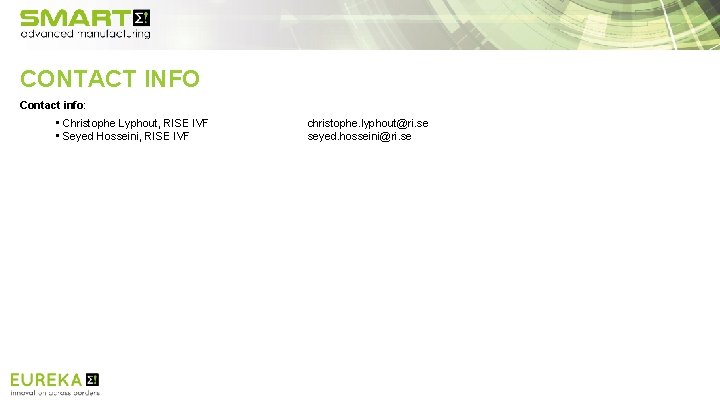
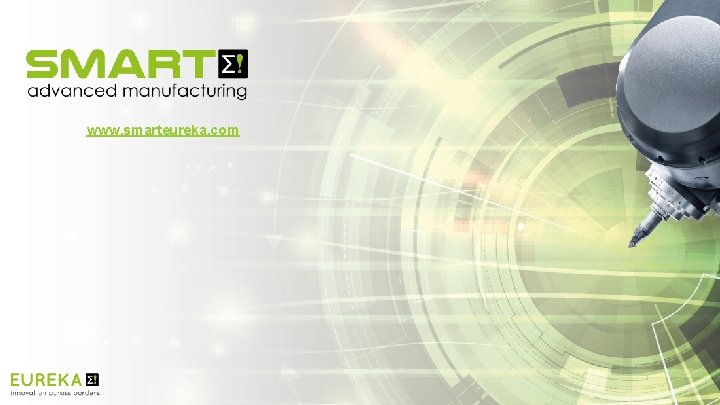
- Slides: 7
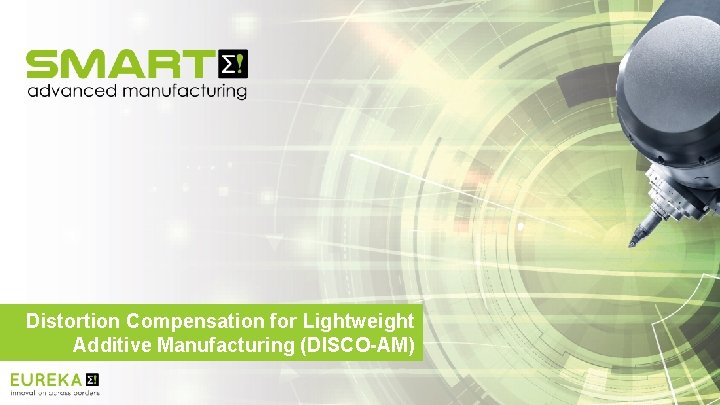
Distortion Compensation for Lightweight Additive Manufacturing (DISCO-AM)
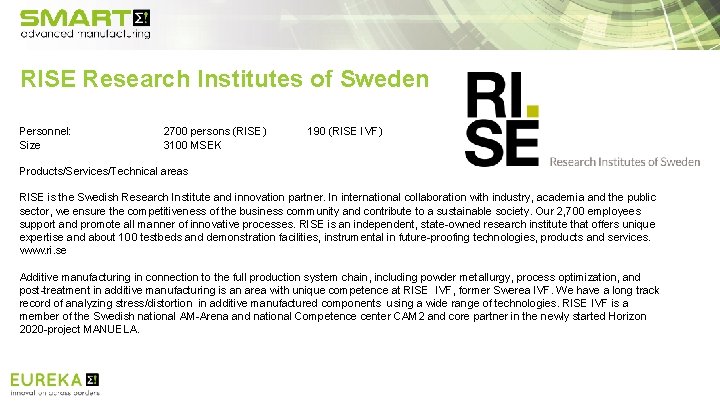
RISE Research Institutes of Sweden Personnel: Size 2700 persons (RISE) 3100 MSEK 190 (RISE IVF) Products/Services/Technical areas RISE is the Swedish Research Institute and innovation partner. In international collaboration with industry, academia and the public sector, we ensure the competitiveness of the business community and contribute to a sustainable society. Our 2, 700 employees support and promote all manner of innovative processes. RISE is an independent, state-owned research institute that offers unique expertise and about 100 testbeds and demonstration facilities, instrumental in future-proofing technologies, products and services. www. ri. se Additive manufacturing in connection to the full production system chain, including powder metallurgy, process optimization, and post-treatment in additive manufacturing is an area with unique competence at RISE IVF, former Swerea IVF. We have a long track record of analyzing stress/distortion in additive manufactured components using a wide range of technologies. RISE IVF is a member of the Swedish national AM-Arena and national Competence center CAM 2 and core partner in the newly started Horizon 2020 -project MANUELA.
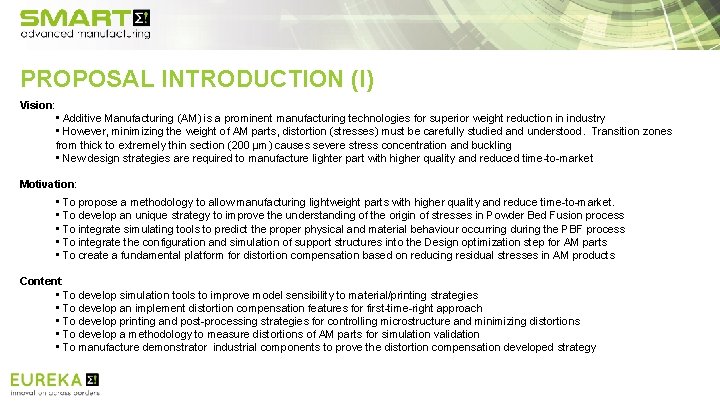
PROPOSAL INTRODUCTION (I) Vision: • Additive Manufacturing (AM) is a prominent manufacturing technologies for superior weight reduction in industry • However, minimizing the weight of AM parts, distortion (stresses) must be carefully studied and understood. Transition zones from thick to extremely thin section (200 µm) causes severe stress concentration and buckling • New design strategies are required to manufacture lighter part with higher quality and reduced time-to-market Motivation: • To propose a methodology to allow manufacturing lightweight parts with higher quality and reduce time-to-market. • To develop an unique strategy to improve the understanding of the origin of stresses in Powder Bed Fusion process • To integrate simulating tools to predict the proper physical and material behaviour occurring during the PBF process • To integrate the configuration and simulation of support structures into the Design optimization step for AM parts • To create a fundamental platform for distortion compensation based on reducing residual stresses in AM products Content: • To develop simulation tools to improve model sensibility to material/printing strategies • To develop an implement distortion compensation features for first-time-right approach • To develop printing and post-processing strategies for controlling microstructure and minimizing distortions • To develop a methodology to measure distortions of AM parts for simulation validation • To manufacture demonstrator industrial components to prove the distortion compensation developed strategy
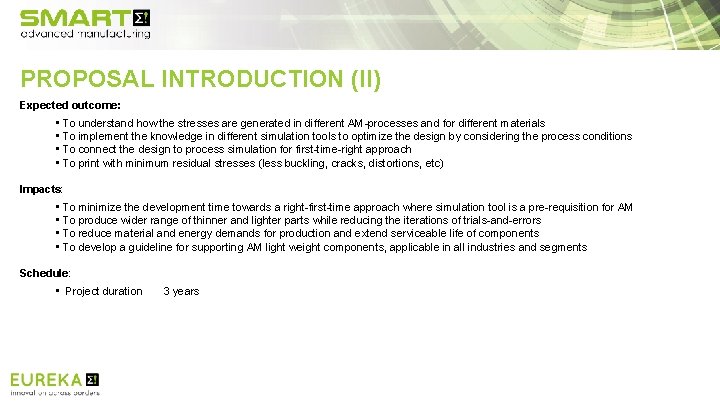
PROPOSAL INTRODUCTION (II) Expected outcome: • To understand how the stresses are generated in different AM-processes and for different materials • To implement the knowledge in different simulation tools to optimize the design by considering the process conditions • To connect the design to process simulation for first-time-right approach • To print with minimum residual stresses (less buckling, cracks, distortions, etc) Impacts: • To minimize the development time towards a right-first-time approach where simulation tool is a pre-requisition for AM • To produce wider range of thinner and lighter parts while reducing the iterations of trials-and-errors • To reduce material and energy demands for production and extend serviceable life of components • To develop a guideline for supporting AM light weight components, applicable in all industries and segments Schedule: • Project duration 3 years
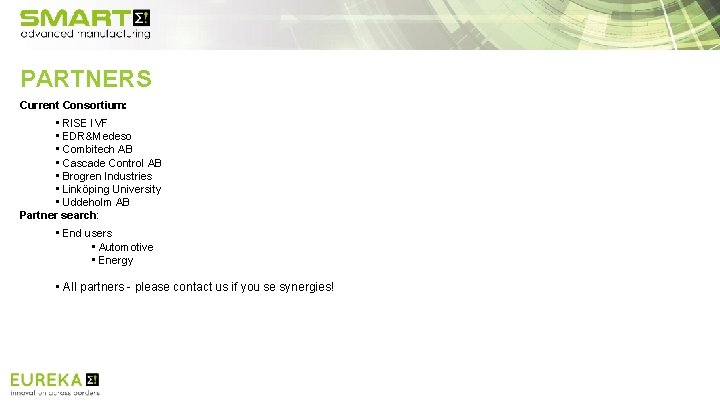
PARTNERS Current Consortium: • RISE IVF • EDR&Medeso • Combitech AB • Cascade Control AB • Brogren Industries • Linköping University • Uddeholm AB Partner search: • End users • Automotive • Energy • All partners - please contact us if you se synergies!
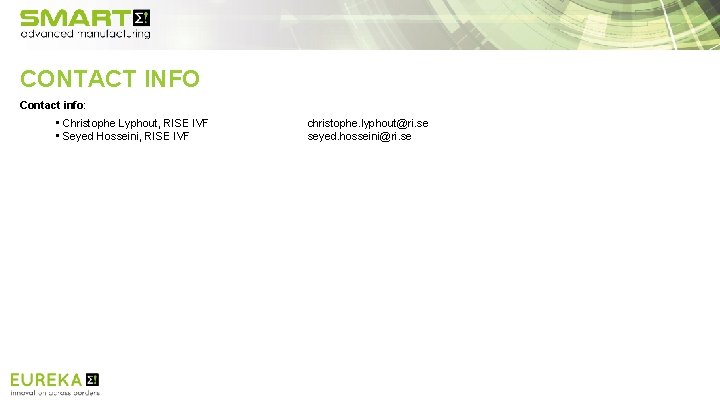
CONTACT INFO Contact info: • Christophe Lyphout, RISE IVF • Seyed Hosseini, RISE IVF christophe. lyphout@ri. se seyed. hosseini@ri. se
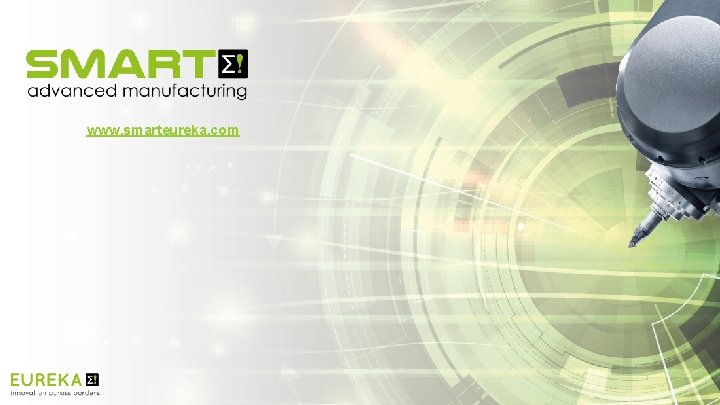
www. smarteureka. com