Changes to S 2 Lifting Equipment Changes to
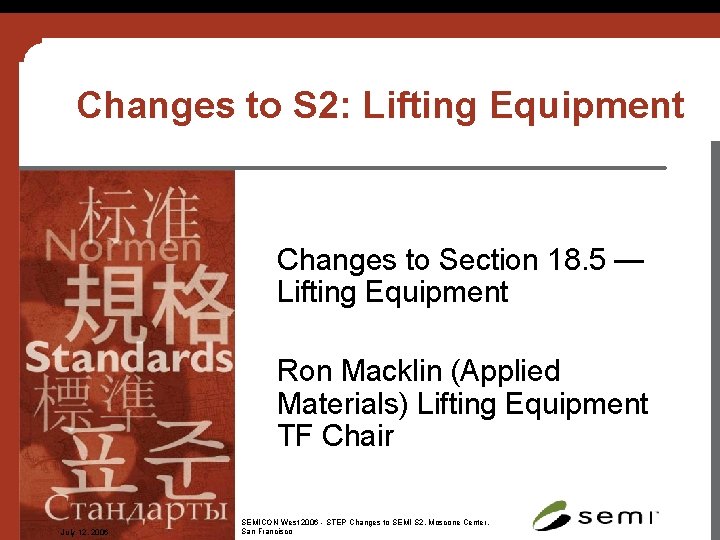
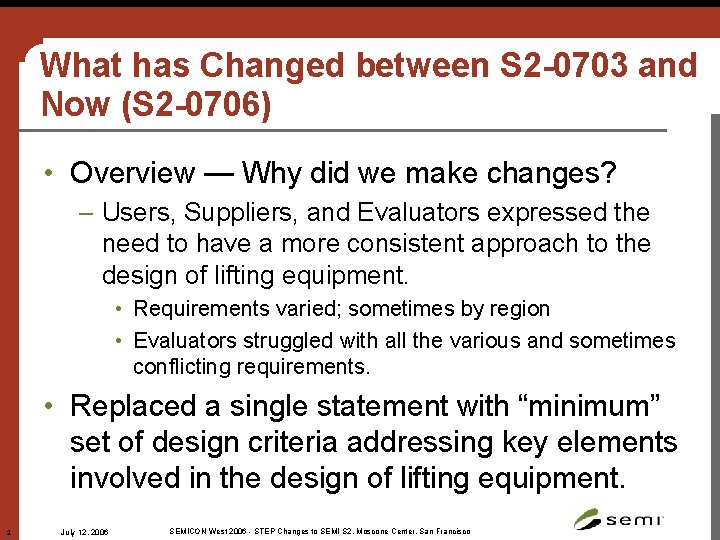
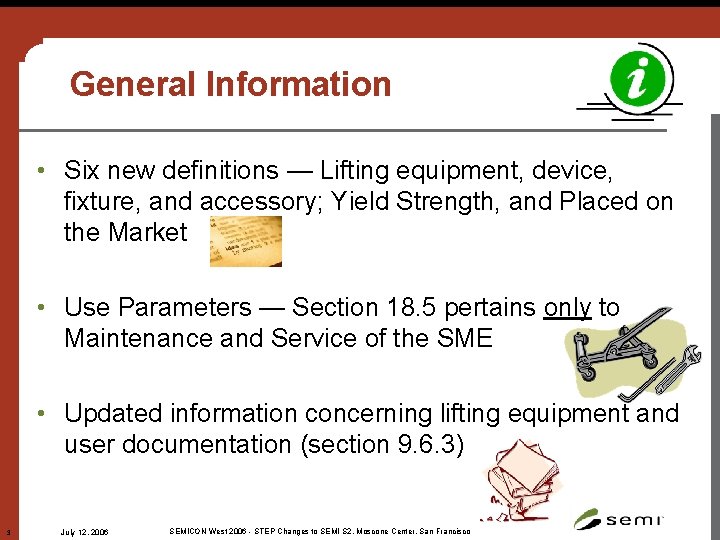
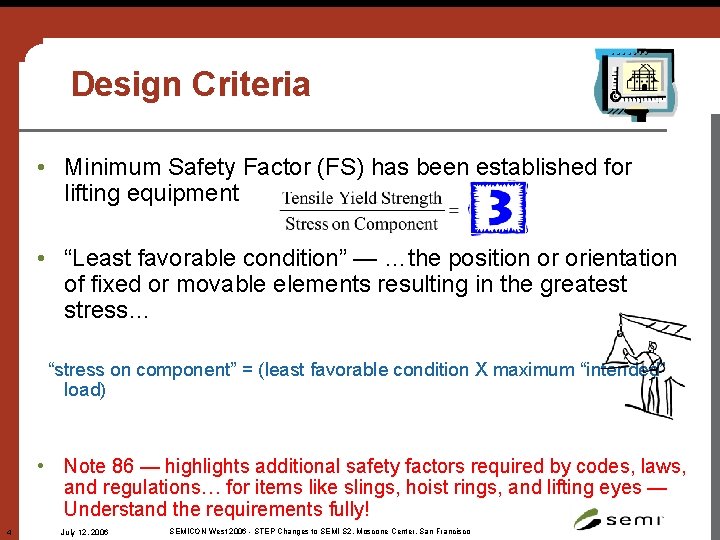
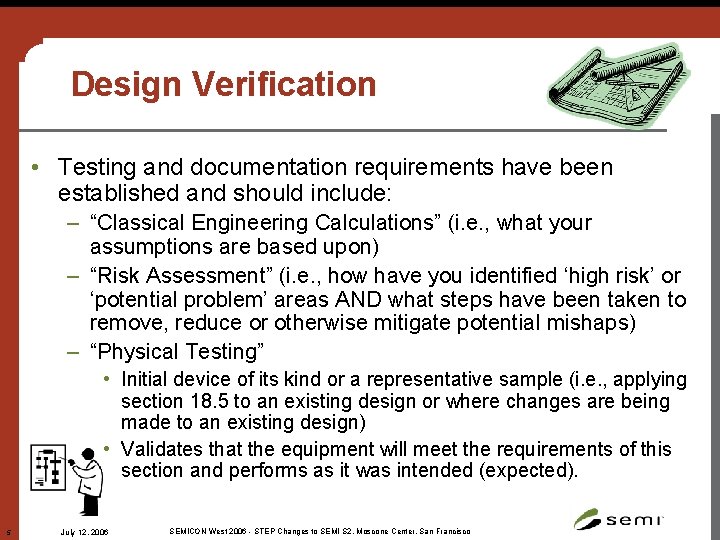
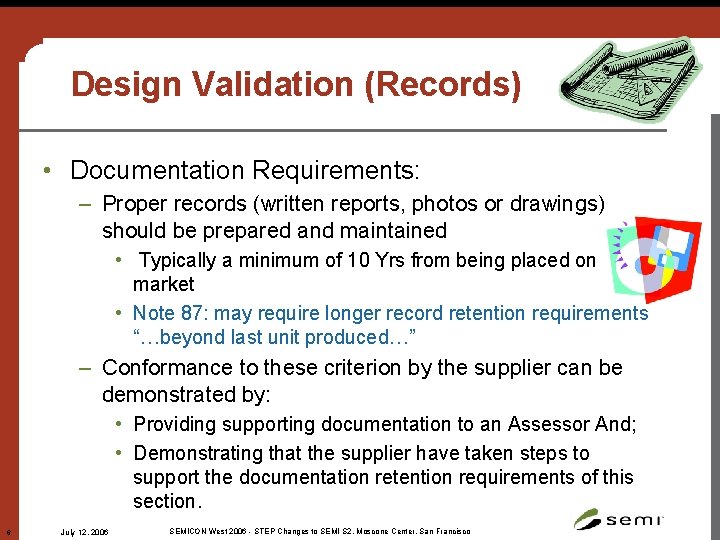
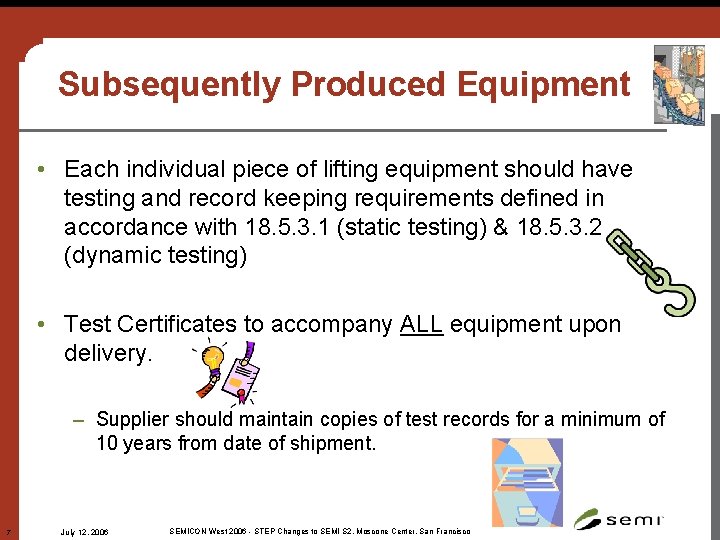
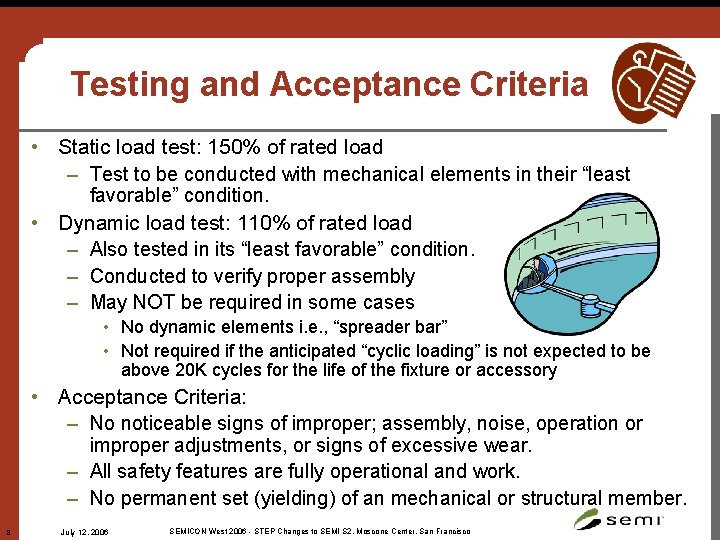
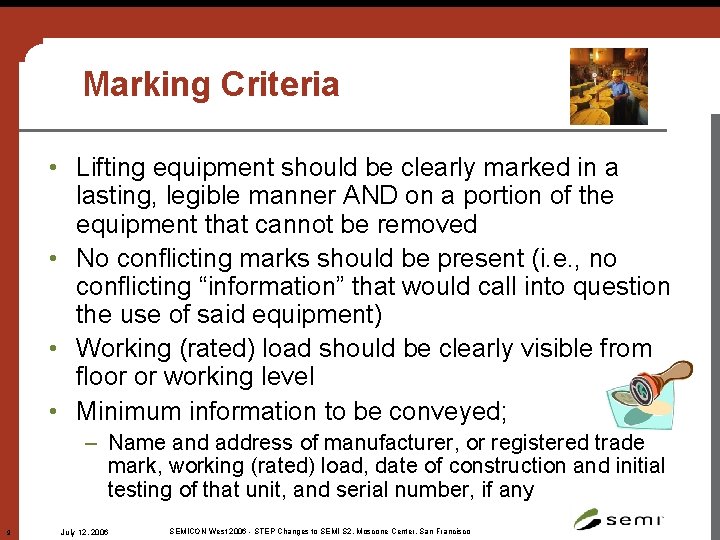
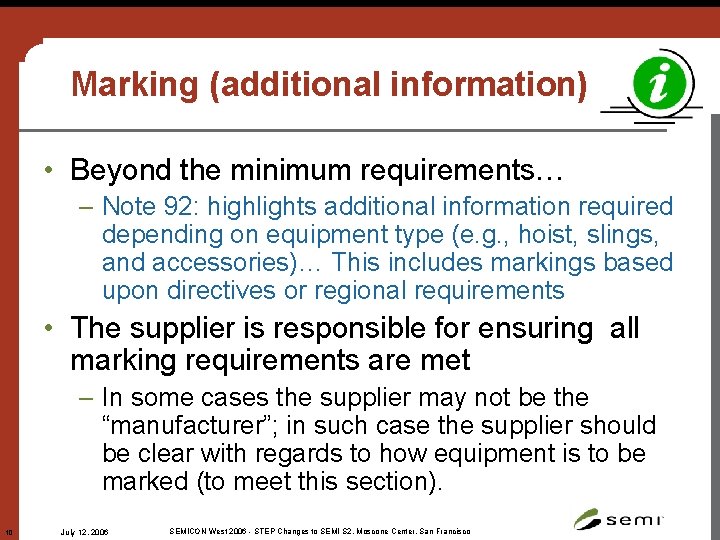
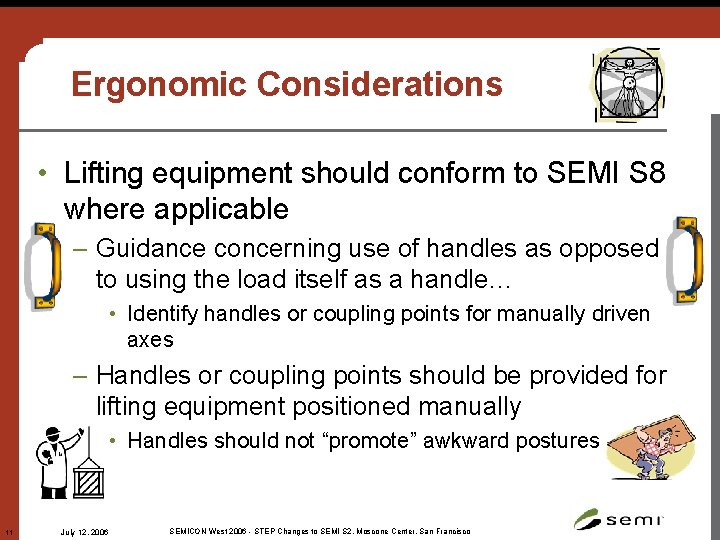
- Slides: 11
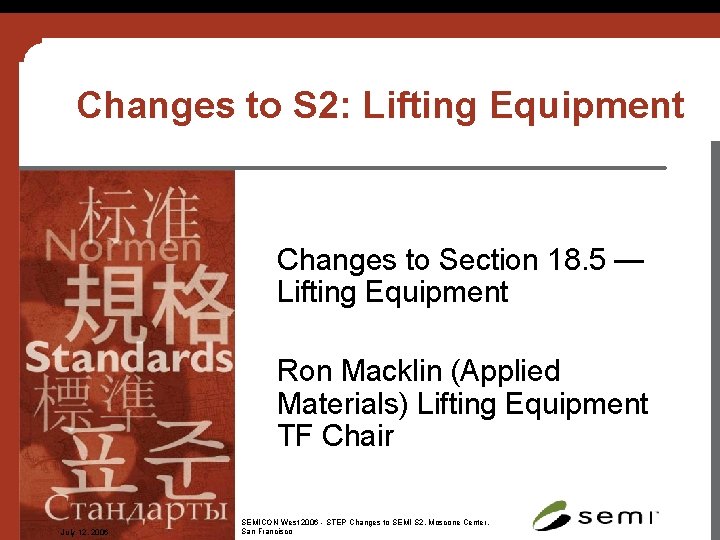
Changes to S 2: Lifting Equipment Changes to Section 18. 5 — Lifting Equipment Ron Macklin (Applied Materials) Lifting Equipment TF Chair July 12, 2006 SEMICON West 2006 - STEP Changes to SEMI S 2, Moscone Center, San Francisco
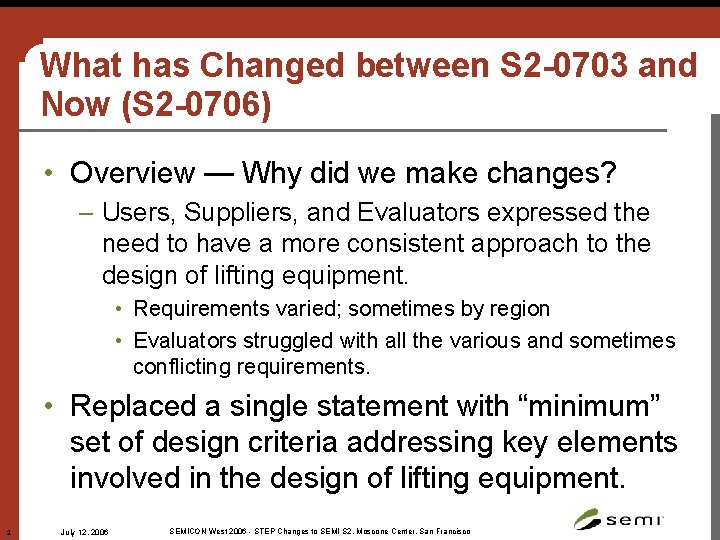
What has Changed between S 2 -0703 and Now (S 2 -0706) • Overview — Why did we make changes? – Users, Suppliers, and Evaluators expressed the need to have a more consistent approach to the design of lifting equipment. • Requirements varied; sometimes by region • Evaluators struggled with all the various and sometimes conflicting requirements. • Replaced a single statement with “minimum” set of design criteria addressing key elements involved in the design of lifting equipment. 2 July 12, 2006 SEMICON West 2006 - STEP Changes to SEMI S 2, Moscone Center, San Francisco
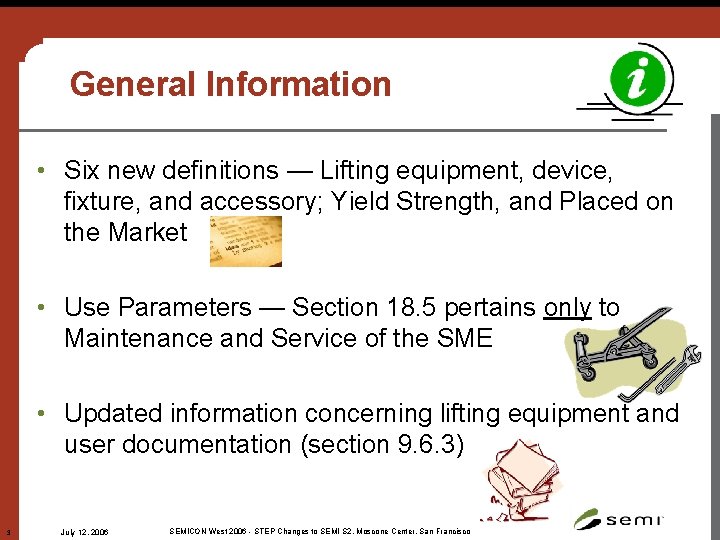
General Information • Six new definitions — Lifting equipment, device, fixture, and accessory; Yield Strength, and Placed on the Market • Use Parameters — Section 18. 5 pertains only to Maintenance and Service of the SME • Updated information concerning lifting equipment and user documentation (section 9. 6. 3) 3 July 12, 2006 SEMICON West 2006 - STEP Changes to SEMI S 2, Moscone Center, San Francisco
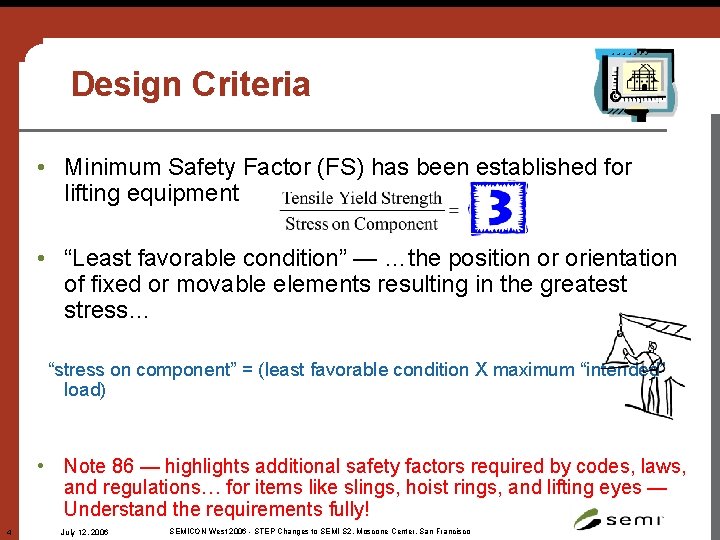
Design Criteria • Minimum Safety Factor (FS) has been established for lifting equipment • “Least favorable condition” — …the position or orientation of fixed or movable elements resulting in the greatest stress… “stress on component” = (least favorable condition X maximum “intended” load) • Note 86 — highlights additional safety factors required by codes, laws, and regulations… for items like slings, hoist rings, and lifting eyes — Understand the requirements fully! 4 July 12, 2006 SEMICON West 2006 - STEP Changes to SEMI S 2, Moscone Center, San Francisco
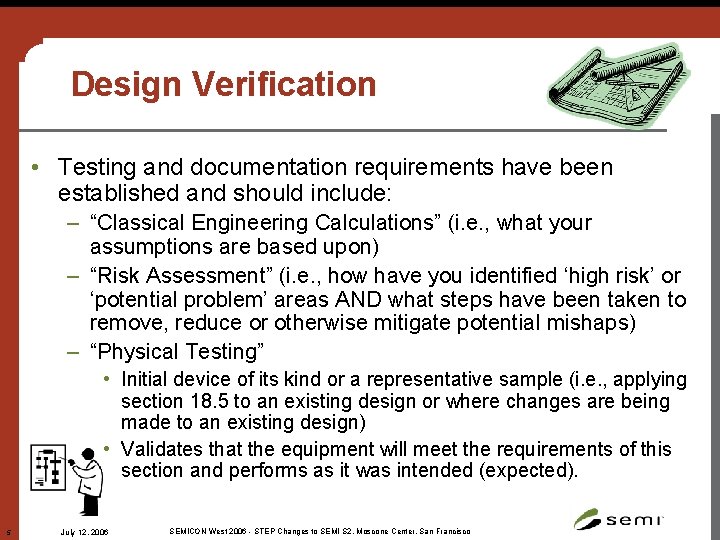
Design Verification • Testing and documentation requirements have been established and should include: – “Classical Engineering Calculations” (i. e. , what your assumptions are based upon) – “Risk Assessment” (i. e. , how have you identified ‘high risk’ or ‘potential problem’ areas AND what steps have been taken to remove, reduce or otherwise mitigate potential mishaps) – “Physical Testing” • Initial device of its kind or a representative sample (i. e. , applying section 18. 5 to an existing design or where changes are being made to an existing design) • Validates that the equipment will meet the requirements of this section and performs as it was intended (expected). 5 July 12, 2006 SEMICON West 2006 - STEP Changes to SEMI S 2, Moscone Center, San Francisco
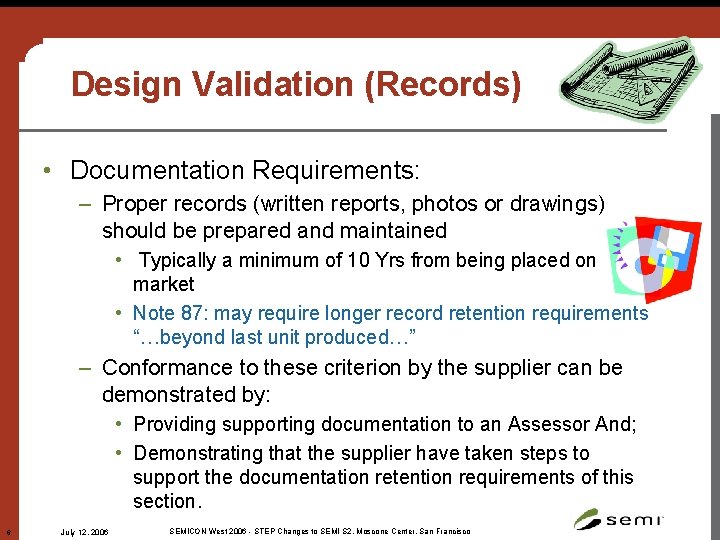
Design Validation (Records) • Documentation Requirements: – Proper records (written reports, photos or drawings) should be prepared and maintained • Typically a minimum of 10 Yrs from being placed on market • Note 87: may require longer record retention requirements “…beyond last unit produced…” – Conformance to these criterion by the supplier can be demonstrated by: • Providing supporting documentation to an Assessor And; • Demonstrating that the supplier have taken steps to support the documentation retention requirements of this section. 6 July 12, 2006 SEMICON West 2006 - STEP Changes to SEMI S 2, Moscone Center, San Francisco
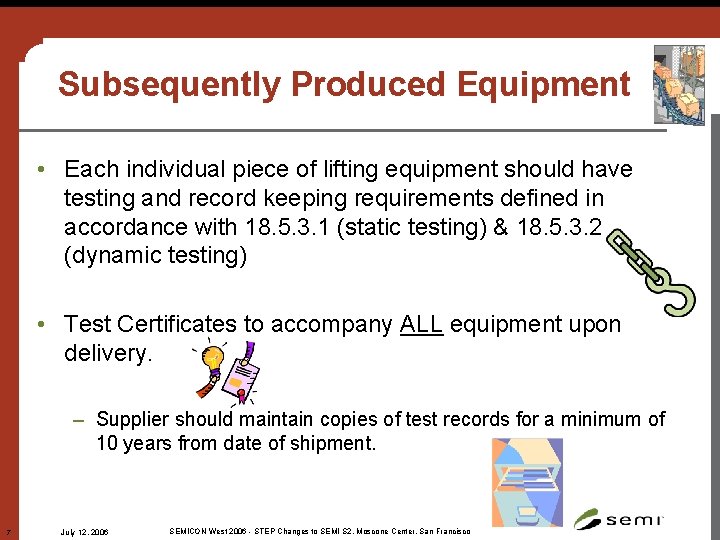
Subsequently Produced Equipment • Each individual piece of lifting equipment should have testing and record keeping requirements defined in accordance with 18. 5. 3. 1 (static testing) & 18. 5. 3. 2 (dynamic testing) • Test Certificates to accompany ALL equipment upon delivery. – Supplier should maintain copies of test records for a minimum of 10 years from date of shipment. 7 July 12, 2006 SEMICON West 2006 - STEP Changes to SEMI S 2, Moscone Center, San Francisco
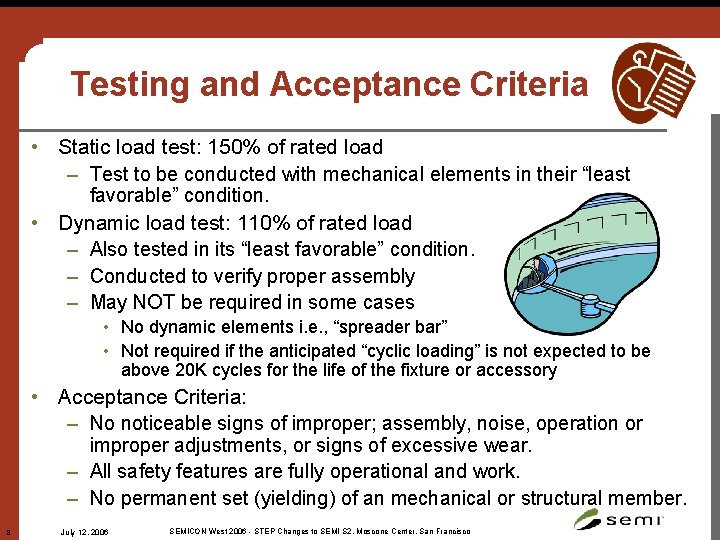
Testing and Acceptance Criteria • Static load test: 150% of rated load – Test to be conducted with mechanical elements in their “least favorable” condition. • Dynamic load test: 110% of rated load – Also tested in its “least favorable” condition. – Conducted to verify proper assembly – May NOT be required in some cases • No dynamic elements i. e. , “spreader bar” • Not required if the anticipated “cyclic loading” is not expected to be above 20 K cycles for the life of the fixture or accessory • Acceptance Criteria: – No noticeable signs of improper; assembly, noise, operation or improper adjustments, or signs of excessive wear. – All safety features are fully operational and work. – No permanent set (yielding) of an mechanical or structural member. 8 July 12, 2006 SEMICON West 2006 - STEP Changes to SEMI S 2, Moscone Center, San Francisco
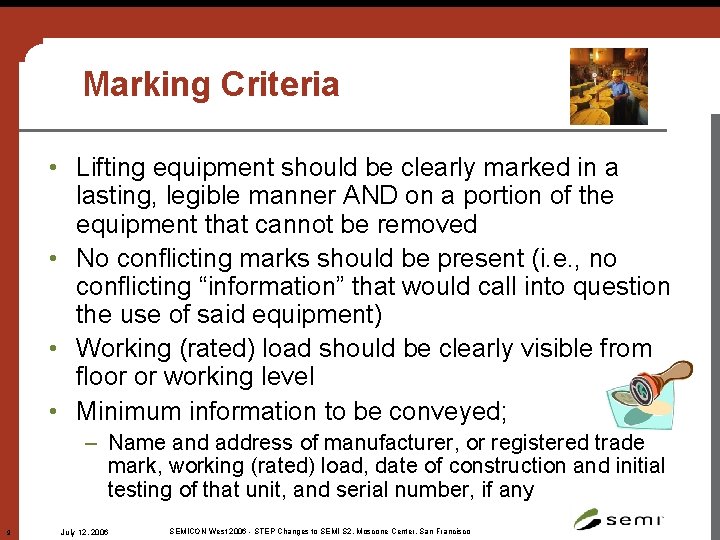
Marking Criteria • Lifting equipment should be clearly marked in a lasting, legible manner AND on a portion of the equipment that cannot be removed • No conflicting marks should be present (i. e. , no conflicting “information” that would call into question the use of said equipment) • Working (rated) load should be clearly visible from floor or working level • Minimum information to be conveyed; – Name and address of manufacturer, or registered trade mark, working (rated) load, date of construction and initial testing of that unit, and serial number, if any 9 July 12, 2006 SEMICON West 2006 - STEP Changes to SEMI S 2, Moscone Center, San Francisco
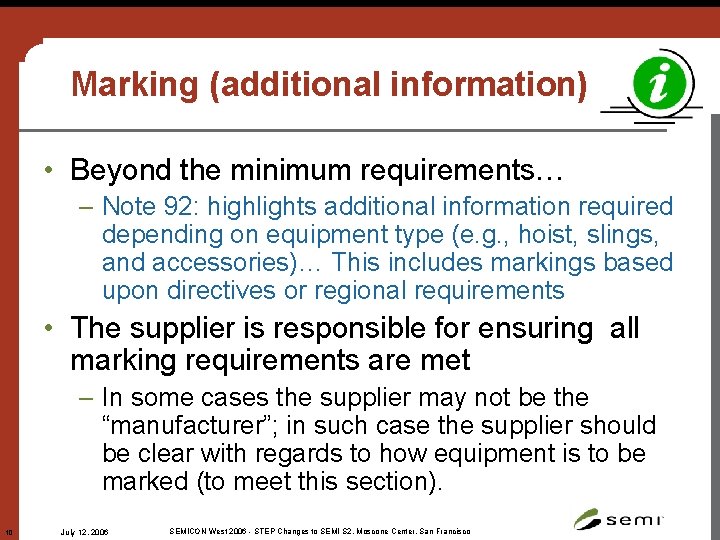
Marking (additional information) • Beyond the minimum requirements… – Note 92: highlights additional information required depending on equipment type (e. g. , hoist, slings, and accessories)… This includes markings based upon directives or regional requirements • The supplier is responsible for ensuring all marking requirements are met – In some cases the supplier may not be the “manufacturer”; in such case the supplier should be clear with regards to how equipment is to be marked (to meet this section). 10 July 12, 2006 SEMICON West 2006 - STEP Changes to SEMI S 2, Moscone Center, San Francisco
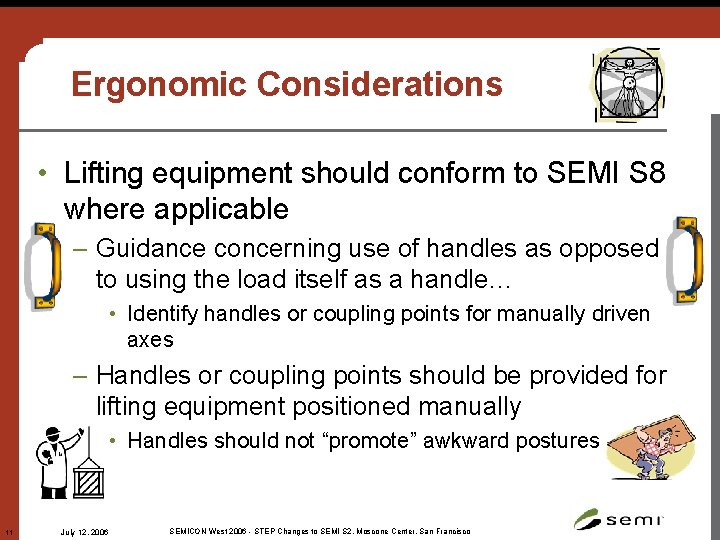
Ergonomic Considerations • Lifting equipment should conform to SEMI S 8 where applicable – Guidance concerning use of handles as opposed to using the load itself as a handle… • Identify handles or coupling points for manually driven axes – Handles or coupling points should be provided for lifting equipment positioned manually • Handles should not “promote” awkward postures 11 July 12, 2006 SEMICON West 2006 - STEP Changes to SEMI S 2, Moscone Center, San Francisco
Lifting tools and tackles list
6bcy
Elektrotechnisch materiaal
Elizabeth mulroney
Examples of chemical changes
The limited access zone of a masonry wall must be
Orographic lifting
Convergent lifting
A pump of 200w power is lifting 2kg water
Slings safety training
No bending lifting twisting
Transfer belt definition